机械加工余量表
磨削加工余量标准

·机械加工余量标准25EQY—19-1999 1.主题内容与适用范围本标准规定了磨削加工的加工余量。
本标准适用于磨削各类材料时的加工余量。
2.技术内容加工余量表(一)厚度4以上的平面磨削余量(单面)说明:1.二次平面磨削余量乘系数1.52.三次平面磨削余量乘系数23.厚度4以上者单面余量不小于0.5-0.84.橡胶模平板单面余量不小于0.7毛坯加工余量表(二)3.2I:园棒类:(1)工件的最大外径无公差要求,光洁度在▽以下,例:不磨外圆的凹模带台肩的凸模、凹模、凸凹模以及推杆、推销、限制器、托杆、各种螺钉、螺栓、螺塞、螺帽外径必须滚花者。
(毫米)1.6当D<36时并不适应于调头夹加工,在加工单个工件时,应在L上加夹头量10-15。
(2)工件的最大外径有公差配合要求,光洁度在▽以上,例如:外圆须磨加工的凹模,挡料销、肩台须磨加工的凸模或凸凹模等。
(毫米)当D<36时,不适合调头加工,在加工单个零件时,应加夹头量10-15。
毛坯加工余量表(三)3.2Ⅱ:圆形锻件类(不需锻件图)(1)不淬火钢表面粗糙度在▽以下无公差配合要求者,例如:固定板、退料板等。
(毫米)注:表中的加工余量为最小余量,其最大余量不得超过厂规定标准。
毛坯加工余量表(四)Ⅲ:矩形锻件类:表内的加工余量为最小余量,其最大余量不得超过厂规定标准。
平面、端面磨削加工余量表(五)一、平面平面每面磨量二、端面端面每面磨量注:3.2本表适用于淬火零件,不淬火零件应适当减少20-40%粗加工的表面粗糙度不应低于▽如需磨两次的零件,其磨量应适当增加10-20%环形工件磨削加工余量表(六)注:φ50以下,壁厚10以上者,或长度为100-300者,用上限φ50-φ100,壁厚20以下者,或长度为200-500者,用上限φ100以上者,壁厚30以下者,或长度为300-600者,用上限6.4长度超过以上界线者,上限乘以系数1.3加工粗糙度不低于▽,端面留磨量0.5φ6以下小孔研磨量表(七)注:本表只适用于淬火件1.6应按孔的最小极限尺寸来留研磨量淬火前小孔需占铰粗糙度▽以上当长度e小于15毫米时,表内数值应加大20-30%导柱衬套磨削加工余量表(八)镗孔加工余量表(九)附注:当一次镗削时,加工余量应该是粗加工余量加工精加工余量。
第13章 工序间加工余量
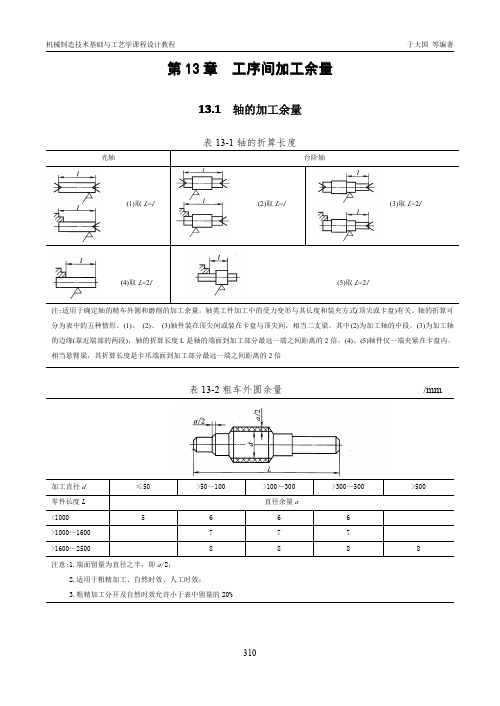
2.表中的公差系指尺寸 L 的公差,当原公差大于该公差时,尺寸公差为原公差值;
3.加工套类零件时余量值可适当增加
13.2 孔、槽的加工余量
表 13-10 精车(铣、刨)槽余量
于大国 等编著 1.2 1.4 1.5 1.7 -0.8
/mm
>500 0.6 0.6 0.6 0.7 0.7 0.8 -0.5
/mm
加工 孔的 直径
钻 第一次 第二次
直径
用车刀 扩孔钻
镗以后
粗铰
精铰 H7 或 H8、H9
加工 孔的 直径
直径
钻 用车刀 扩孔
第一次 第二次 镗以后 钻
粗铰
精铰 H7 或 H8,
H9
3
2.9
-
-
-
-
3
24 22.0
-
23.8 23.8 23.94 24
4
3.9
-
-
-
-
4
25 23.0
-
24.8 24.8 24.94 25
0.3
0.3
0.4
0.5
0.6
>120~260
0.4
0.4
0.5
0.5
0.6
>260~500
0.5
0.5
0.5
0.6
0.7
>500
0.6
0.6
0.6
0.7
0.8
长度公差
-0.12
-0.17
-0.23
-0.3
-0.4
注: 1.加工有台阶的轴时,每个台阶的加工余量应根据该台阶直径 d 及零件的全长 L 分别选用;
≤100
0.2 0.3 0.2 0.3 0.2 0.3 0.2 0.3 0.3 0.3 0.3 0.3 0.3 0.4
机械加工工序间余量

3.2机械加工工序间余量本章规定的常见工序间加工留量作为本公司编制机械加工工序及有关单位确定加工余量的依据,如有特殊情况可由工艺部门另作规定。
3.2.1切料头时留芯部安全尺寸如图3.2-1所示,当工件材料σs=400~450MPa时,切料头留芯部安全尺寸d按表3.2-1选取。
表3.2-1 中数据用公式d3≈5Q l/σs计算,式中的σs材料屈服极限。
如为其它材料时,应根据其σs大小将安全尺寸d应乘上修正系数K,K值按表3.2-2选取。
表3.2-1 mm注:①、切料头安全尺寸d应按h13级精度加工。
②、切料头当接近安全尺寸时严禁啃刀。
③、切料头前床面上必须垫适当数量的枕木,在架中心架或托辊切断时,直径可以适当缩小。
表3.2-23.2.2 各类锯片及铣刀切口宽度及切割规格各类锯片及铣刀宽度及切割规格见表3.2-3。
表3.2-3 mm注:圆锯能切割方料的最大尺寸为圆料的70%。
3.2.3 车床切断刀及插床切口刀的切口宽度及切割深度车床切断刀及插床切口刀的切口宽度及切割深度见表3.2-4。
表3.2-4 mm注:车床、插床的刀具宽度可以适当磨小。
如果设计专用切断刀时宽度可以适当减少。
3.2.4箱体、架体零件粗加工后人工时效余量箱体、架体零件粗加工后人工时效余量见表3.2-5 。
表3.2-5 mm注:①、适用于铸铁件粗加工后人工时效及粗精加工分开如床身、立柱、工作台、箱体等,不适用于容易变形的薄板。
②、自然时效余量为表中数值的0.5~0.6倍。
③、铸钢件可按表中数值增加1~2mm。
3.2.5 平键修配余量平键修配余量见表3.2-6。
表3.2-6 mm注:①、间隙配合的导向键及切向键不留修配余量。
②、斜健的两侧不留修配余量,斜面上一般情况设计时已留有0.3~0.5mm的修配量,如图纸上未留量时,工艺上应留量。
3.2.6 孔的钻、扩、铰余量孔的钻、扩、铰余量见表3.2-7.表3.2-7 mm注:①、大于Φ30mm的孔,可在二次走刀中钻出,先用较小钻头预钻孔。
机械制造工艺-加工余量、工序尺寸及公差
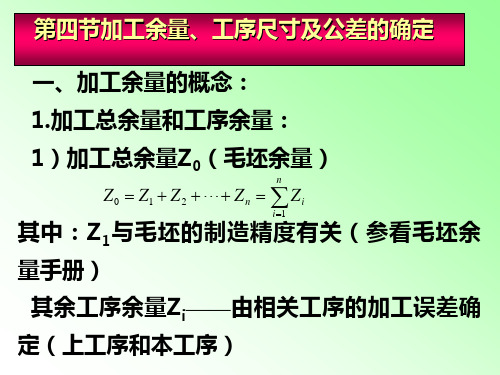
例题: 某轴直径φ50mm,其尺寸精度为IT5,表
面粗糙度为Ra0.04μm,并要求高频淬火,毛 坯为锻件。其工艺路线为:粗车-半精车 -高频淬火-粗磨-精磨-研磨,计算轴 的各工序尺寸及公差 解:
加工余量:由工艺手册确定。 工序尺寸:研磨工序尺寸即零件的设计 尺寸50-0.011 、Ra0.04μm
n1
T0 Ti i1
注: 公差的值大小——应按国标规定各公
差等级标准选取。 当T0一定时,各环公差Ti随n增加而减小。
3、封闭环的上偏差ES0
m
n1
ES0 ESp EIq
p1
qm1
ESP——增环上偏差 EIq——减环下偏差 m——增环环数
4、封闭环的下偏差EI0
m
n1
EI0 EIp ESq
1)基准不重合(待加工表面为工序基准) 2)待加工表面留有余量Z
解:画工艺尺寸链图(图1-45) (方法:从一个尺寸出发,到尺寸的基准后转
入相接的下一个尺寸链,通过所有相关联尺寸, 最终返回出发点。)P53 其中,键槽深为由本工序和终工序而间接获得, 为封闭环。 解得:L2=53.7(本工序工序尺寸及公差)
例:图4-22轴线弯曲造成的余量不均匀误差。 各项位置误差造成的影响参看表4-11
4)本工序的装夹误差εb 包括定位误差、夹紧误差。
5)余量计算公式 由于空间位置误差和装夹误差的
方向性,所以用矢量相加表示。 单边余量
Zmin Ta Ry Ha ea b
双边余量
Zmin Ta / 2 Ry Ha ea b
求:本工序工序尺寸L2(渗碳深度) 分析:渗碳层保留深度L0 —单边值(图面尺寸)
渗碳深度L2—单边值。 按尺寸链图,代入公式求解得:L2=0.7+0.025
表1盘、柱类自由锻件机械加工余量与公差mm

零件尺寸!(或",#)大于#$#%&!##!%#’##’(#&!($##(##至$#%&!##!%#’##’(#&!($##(##%&#加工余量%,&与极限偏差%&%&%&%&%&%&%&%&%&%&大于至锻件精度等级)%&!##%*’%*’%*’%*’+*’+*’,*&,*&-*&-*&!#*$!#*$!##!%#+*’%*’+*’%*’,*&+*’,*&,*&-*&-*&!#*$!#*$!’*(!’*(!$*%!$*%!%#’##,*&%*’,*&+*’,*&-*&-*&!#*$!#*$!!*$!!*$!’*(!’*(!$*%!$*%!%*+!%*+’##’(#-*&+*’-*&+*’-*&,*&!#*$-*&!!*$!#*$!’*(!’*(!&*(!&*(!(*%!(*%!,*,!,*,’#*,’#*,’(#&!(!#*$,*&!#*$,*&!#*$-*&!!*$!#*$!’*(!!*$!&*(!’*(!$*%!$*%!%*+!%*+!-*,!-*,’’*-’’*-&!($##!’*(-*&!’*(-*&!’*(!#*$!&*(!!*$!$*%!’*(!(*%!&*(!%*+!(*%!,*,!,*,’!*-’!*-’$*!#’$*!# $##(##!$*%!#*$!$*%!!*$!(*%!’*(!%*+!$*%!+*+!(*%!,*,!+*+’#*-!-*,’&*!#’&*!#’+*!’’+*!’(##%&#!+*+!&*(!,*,!$*%!-*,!(*%’#*,!%*+’!*-!+*+’’*-!-*,’&*!#’’*-’%*!!’(*!!&#*!&&#*!&大于至锻件精度等级.%&!##$*’$*’$*’(*’(*’%*’%*’+*’+*’,*&,*&,*&!##!%#(*’$*’(*’(*’%*’%*’%*’+*’+*’,*&,*&!#*$!#*$!#*$!’*(!’*(!%#’##%*’(*’%*’%*’%*’+*’+*’,*&,*&-*&-*&!#*$!!*$!’*(!&*(!&*(!$*%!(*%’##’(#%*’%*’+*’%*’+*’+*’,*&,*&-*&!#*$!#*$!!*$!!*$!’*(!&*(!$*%!(*%!%*+!,*,!,*,’(#&!(,*&+*’,*&,*&,*&,*&-*&-*&!#*$!#*$!!*$!’*(!’*(!&*(!$*%!(*%!+*+!,*,’#*,’#*, &!($##!#*$,*&!#*$,*&!#*$-*&!!*$!!*$!’*(!’*(!&*(!&*(!$*%!$*%!%*+!+*+!-*,’#*,’&*!#’$*!# $##(##!’*(!#*$!’*(!!*$!&*(!’*(!$*%!&*(!(*%!$*%!%*%!%*+!-*,!,*,’’*-’’*-’%*!!’%*!! (##%&#!%*+!’*(!%*+!&*(!+*+!$*%!,*,!(*%!-*,!+*+’#*,!-*,’&*!#’’*-’%*!!’(*!!&#*!&&#*!&零件直径!大于#$#%&!##!%#至$#%&!##!%#’##加工余量#,$,%与极限偏差#$%#$%#$%#$%#$%大于至锻件精度等级(%&!##%)’%)’*)&%)’%)’*)&+)’+)’!!)$,)&,)&!’)-!##!%#+)’%)’!!)$+)’%)’!!)$,)&+)’!’)-,)&,)&!’)-*)&*)&!$)%!%#’##,)&%)’!’)-,)&+)’!’)-,)&,)&!’)-*)&*)&!$)%!#)$!#)$!-)%’##’-#*)&+)’!$)%*)&+)’!$)%*)&,)&!$)%!#)$*)&!-)%!!)$!#)$!+)+’-#&!-!#)$,)&!-)%!#)$,)&!-)%!#)$*)&!-)%!!)$!#)$!+)+!’)-!!)$!,),&!-$##!’)-*)&!,),!’)-*)&!,),!’)-!#)$!,),!&)-!!)$’#),!$)%!’)-’!)*$##-##!$)%!#)$’!)*!$)%!!)$’!)*!-)%!’)-’&)!#!%)+!$)%’$)!#-##%&#!+)+!&)-’%)!!!,),!$)%’+)!’!*),!-)!!!!!!!!!!!!!!!!!!!!!!!!!!!!!!!!!!!!!!!!!!!!!!!!!!!!!!!!!!!!!!!!!!!!!!!!!!!!!%’*)!&’#),!%)+&#)!&零件直径!零件高度"’##’-#&!-$##-##’-#&!-$##-##%&#加工余量#,$,%与极限偏差#$%#$%#$%#$%#$%大于至锻件精度等级(%&!##!##!%#!!)$!!)$!+)+!%#’##!’)-!’)-!,),!&)-!&)-’#),’##’-#!’)-!’)-!,),!$)%!$)%’!)*!%)+%)+’$)!#’-#&!-!&)-!’)-’#),!$)%!$)%’!)*!%)+!%)+’$)!#!,),!,),’+)!’&!-$##!-)%!&)-’&)!#!%)+!-)%’$)!#!,),!,),’+)!’’#),’#),&#)!&’&)!#’&)!#&-)!-$##-##!+)+!-)%’%)!!!,),!+)+’+)!’’#)*!*),&#)!&’&)!#’&)!#&-)!-’%)!!’%)!!&*)!+-##%&#’!)*!+)+&’)!$’’)*!*),&&)!$’&)!#’’)*&-)!-’%)!!’-)!!&*)!+&#)!&&#)!&$-)’#零件直径!零件高度"大于!"!#$%!!%#!至"!#$%!!%#!&!!加工余量#,$,%与极限偏差#$%#$%#$%#$%#$%大于至锻件精度等级’#$%!!"(&"(&#(&"(&"(&#(&)(&)(&*($+(&+(&%%("%!!%#!)(&"(&*($)(&)(&*($#(&#(&,($#(&+(&,($*($*($%&()%#!&!!#(&)(&,($#(&#(&,($#(&+(&,($+(&*($%%("*($,($%&()&!!&)!#(&#(&,($+(&#(&%%("+(&+(&%%("*($*($%&(),($%!("%"(#&)!$%)*($+(&%&()*($*($%&()*($*($%&(),($,($%"(#%!("%!("%)(#$%)"!!%!("*($%)(#%!("*($%)(#%!(",($%)(#%%("%!("%+(+%&()%&()%*(*"!!)!!%&()%!("%*(*%&()%%("%*(*%$()%&()&!(*%"(#%$()&%(,)!!#$!%#(+%&()&"(%!%#(+%$()&"(%!%+(+%"(!!!!!!!!!!!!!!!!!!!!!!!!!!!!!!!!!!!!!!!!!!!!!!!!!!!!!!!!!!!!!!!!!!!!!!!!!!!!!#&#(%%%*(*%)(#&+(%&零件直径!零件高度"&!!&)!$%)"!!)!!&)!$%)"!!)!!#$!加工余量#,$,%与极限偏差#$%#$%#$%#$%#$%大于至锻件精度等级’#$%!!%!!%#!%!("%!("%)(#%#!&!!%!("%!("%)(#%&()%&()%*(*&!!&)!%!("%%("%)(#%&()%&()%*(*%"(#%"(#&%(,&)!$%)%%("%&()%+(+%&()%$()%*(*%)(#%)(#&$(%!%+(+%+(+&#(%%$%)"!!%$()%$()&!(*%"(#%"(#&%(,%#(+%+(+&"(%!%,(*%,(*&,(%$&&(,&&(,$$(%""!!)!!%)(#%"(#&$(%!%#(+%#(+&"(%!%,(*%*(*&,(%+&&(,&&(,$$(%"&)(%%&)(%%$*(%+)!!#$!%*(*%+(+&,(%$&!(*%,(*$!(%$&$(%!&&(,$)(%)&#(%%&)(%%$,(%+$!(%$$!(%$")(&!表!圆环类自由锻件机械加工余量与公差零件直径!""零件高度",""大于#$#%&!##!%#’##至$#%&!##!%#’##’(#加工余量#、$、%与极限偏差,""#$%#$%#$%#$%#$%#$%大于至锻件精度等级)%&!##*+’%+’,+&*+’%+’,+&-+&*+’!#+$!##!%#-+&%+’!#+$-+&%+’!#+$,+&*+’!’+(!#+$-+&!&+(!%#’##,+&%+’!’+(,+&%+’!’+(!#+$*+’!&+(!!+$-+&!$+%!’+(!#+$!%+*’##’(#!#+$%+’!&+(!!+$%+’!$+%!!+$*+’!$+%!’+(-+&!%+*!&+(!#+$!*+*!$+%!’+(!-+-’(#&!(!!+$%+’!$+%!’+(*+’!%+*!&+(*+’!*+*!$+%-+&!-+-!(+%!#+$’#+-!%+*!’+(’!+,&!($##!&+(-+&!*+*!$+%-+&!-+-!(+%,+&’#+-!%+*!#+$’!+,!*+*!!+$’’+,!-+-!&+(’&+!#$##(##!%+*,+&’!+,!*+*!#+$’’+,!-+-!!+$’&+!#!,+-!’+(’(+!!’#+-!&+(’%+!!’!+,!$+%’*+!!(##%&#’#+-!’+(’%+!!’!+,!&+(’*+!’’’+,!$+!!!!!!!!!!!!!!!!!!!!!!!!!!!!!!!!!!!!!!!!!!!!!!!!!!!!!!!!!!!!!!!!!!!!!!!!!!!!!%’,+!&’&+!#!(+%&#+!&’$+!#!%+*&!+!&零件直径!""零件高度",""’(#&!($##(##&!($##(##%&#加工余量#、$、%与极限偏差,""#$%#$%#$%#$%零件壁厚!.&’,""大于#$%/&!#!%’(至$%/&!#!%’($#大于至锻件精度等级)余量增值系数’%&!##!/$!/&!##!%#!/%!/&!/’!%#’##!/%!/$!/&!/’’##’(#!/%!/$!/&!/’’(#&!(!*+*!$+%’’+,!/*!/%!/$!/&!/’&!($##!,+-!(+%’(+!!’!+,!-+-’*+!!!/*!/%!/$!/&!/’$##(##’’+,!%+*’,+!’’$+!#!,+-&!+!&’%+!!’&+!#&$+!$!/,!/*!/%!/$!/&!/’(##%&#’%+!!!-+-&$+!$’*+!’’!+,&(+!%’,+!&’$+!#&-+!*&’+!$&#+!&$’+!-!/,!/*!/%!/$!/&!/’零件直径!!!零件高度",!!大于"#"$%&""&$"’""至#"$%&""&$"’""’("加工余量#、$、%与极限偏差,!!#$%#$%#$%#$%#$%#$%大于至锻件精度等级)$%&""(*’(*’(*’(*’(*’(*’$*’$*’$*’&""&$"$*’(*’$*’$*’(*’$*’+*’$*’+*’,*%+*’,*%&$"’""+*’(*’+*’+*’(*’+*’,*%$*’,*%-*%+*’-*%&"*#-*%&"*#’""’(",*%$*’,*%,*%$*’,*%-*%$*’-*%&"*#+*’&"*#&&*#-*%&&*#&’*(&&*#&’*(’("%&(-*%$*’-*%&"*#$*’&"*#&"*#+*’&"*#&’*(,*%&’*(&%*(-*%&%*(&#*$&&*#&#*$%&(#""&&*#+*’&&*#&’*(,*%&’*(&%*(,*%&%*(&#*$-*%&#*$&(*$&"*#&(*$&+*+&’*(&+*+#""(""&%*(-*%&%*(&#*$-*%&#*$&(*$&"*#&(*$&$*+&&*#&$*+&,*,&’*(&,*,&-*,&%*(&-*,(""$%"&+*+&&*#&+*+&,*,&’*(&,*,&-*,&%*(&!!!!!!!!!!!!!!!!!!!!!!!!!!!!!!!!!!!!!!!!!!!!!!!!!!!!!!!!!!!!!!!!!!!!!!!!!!!!!-*,’&*-&#*$’&*-’’*-&(*$’’*-零件直径!!!零件高度",!!’("%&(#""(""%&(#""(""$%"加工余量#、$、%与极限偏差,!!#$%#$%#$%#$%零件壁厚!.&’,!!大于"#$/%&"&$’(至#$/%&"&$’(#"大于至锻件精度等级0余量增值系数’$%&""&/#&/%&""&$"&/(&/%&/’&$"’""&/(&/#&/%&/’’""’("&/(&/#&/%&/’’("%&(&(*$&%*(&(*$&/$&/(&/#&/%&/’%&(#""&,*,&#*$&,*,’"*,&+*+’"*,&/$&/(&/#&/%&/’#""(""’"*,&(*$’"*,’’*-&,*,’’*-’(*&&’%*&"’(*&&&/+&/$&/(&/#&/%&/’(""$%"’#*&"&+*+’#*&"’(*&&’"*,’(*&&’+*&’’#*&"’+*&’%&*&#%"*&%%&*&#&/+&/$&/(&/#&/%&/’表!套筒类自由锻件机械加工余量与公差零件直径!""零件高度",""大于!##!$#%##%&#’!&(##&##至!$#%##%&#’!&(##&##$’#加工余量#、$、%与极限偏差,""#$%#$%#$%#$%#$%#$%#$%零件壁厚!)&%,""大于#($*’!#!$%&至($*’!#!$%&(#大于至锻件精度等级+余量增值系数’!##!$#!#,(-,’!’,&!#,(!%,&!’,&!!,(!$,.!(,$!%,&%’,!#!$,.!’,&’’,!&!.,.!*/!*$!*’!*!!$#%##!%,&!#,(!$,.!’,&!’,&!.,.!(,$!-,-!-,-!&,$%.,!%%#,-%!*.!*(!*%%##%&#!(,$!%,&!-,-!&,$!$,.%#,-!.,.%’,!#%%,/!-,-’’,!&%’,!#%!*.!*(!*%%&#’!&!.,.!(,$%%,/!/,-%#,-%&,!!%#,-%-,!%%$,!!%’,!#’-,!.’#,!’%*%!*/!*$!*’!*!’!&(##%!,/!-,-%.,!%%’,!#%(,!#’#,!’%$,!!’(,!&’(,!&%*%!*/!*$!*’!*! (##&##%$,!!%’,!#’(,!&%/,!’’#,!’’-,!.%*’%!*/!*$!*’!*! &##$’#’%,!(’#,!’(%,!-%*’%*%!*/!*$!*’!*%大于至锻件精度等级0余量增值系数’!##!$#-,’.,%-,’-,’!!,(-,’/,’!$,./,’!#,(%’,!#!#,(!%,&’’,!&!%,&!*.!*&!*’!*!!$#%##!#,(/,’!#,(!!,(!’,&!!,(!%,&!-,-!%,&!(,$%.,!%!(,$!*-!*$!*(!*%%##%&#!%,&!!,(!%,&!(,$!$,.!(,$!&,$%’,!#!&,$!.,.’’,!&!.,.!*-!*$!*(!*%%&#’!&!&,$!’,&!&,$!.,.%#,-!.,.!/,-%-,!%!/,-%!,/’-,!.%!,/!*/!*.!*&!*’!*!’!&(##%#,-!.,-%#,-%%,/%(,!#%%,/%(,!#’(,!&%(,!#!*/!*.!*&!*’!*! (##&##%&,!!%’,!#%&,!!%.,!%’#,!’%.,!%%!*-!*.!*&!*’!*! &##$’#’!,!(’#,!’’!,!(%!*/!*.!*&!*’!*%表!模锻件材料消耗工艺定额明细表工厂、车间名称产品名称、型号模锻件材料消耗工艺定额明细表年月计量单位"#$$共页第页序号零件号零件名称每台件数工艺要求的原材料坯料下料工艺必需要的损单件重量每台产品重量材料利用率%钢号来料规格断面尺寸!长度尺寸"标准编号特殊要求长度尺寸#可制锻件数$修整端头损耗%&切断损耗%’压头或不成倍数损耗%(下料损耗合计&)零件&锻件&*坯料&+消耗定额&,零件!&锻件!&*坯料!&+消耗定额!&,零件’锻件’*下料’-利用哪个零件的废料及可利用百分数允许代用的材料备注.!/012345.6...!./.0.1.2.3.4.5!6!.!!!/!0!1!2!3!4!5工厂、车间名称产品名称、型号模锻件材料消耗工艺定额明细表年月计量单位!"##共页第页修改标记工艺员技术科长工艺科长修改通知单号定额员车间主任科长。
加工余量

(1)、加工尾座体的底平面,粗糙度要求为Ra=1.6,采用粗铣—精铣—刮研。
粗铣余量2.7mm,精铣余量0.9mm,刮研余量0.15mm。
(2)、加工尾座体的两侧孔端面,粗糙度要求为Ra=3.2,采用粗铣—半精铣。
采用两次铣加工(粗、精铣)可以满足,粗铣余量取2mm,精铣余量取1mm。
(3)、加工尾座体的前侧面阶梯孔端面,粗糙度要求为Ra=6.3,采用粗铣—半精铣。
加工方法同上。
粗铣深度取1.5mm。
(4)、加工右侧小凸台,粗糙度要求为Ra=3.2,采用粗铣—半精铣。
粗铣余量取1mm,精铣余量取0.7mm。
(5)、加工Φ40H6孔,粗糙度要求Ra=0.4,采用粗镗—半精镗—精镗—浮动镗刀块精镗。
采用粗镗和半精镗、精镗和浮动镗刀块精镗的方式,故考虑分四次进行镗加工。
取粗镗双边余量3mm,半精镗双边余量1.5mm,精镗单边余量0.5mm,浮动镗刀块精镗的双边余量0.2。
(6)、加工肩Φ20H7的孔,粗糙度要求Ra=1.6,采用钻—扩—铰。
钻的单边余量为9mm,扩的单边余量为0.9mm,铰的单边余量为0.1mm。
(7)、加工Φ20H9的凸台孔,粗糙度要求Ra=3.2,采用钻—扩—铰。
钻的单边余量为9mm,扩的单边余量为0.9mm,铰的单边余量为0.1mm。
(8)、加工前侧面Φ10H9孔,粗糙度要求Ra=3.2,采用钻—铰。
采用钻—铰的加工方式,钻的单边余量为4.9mm,再铰加工即可满足要求。
(9)、加工两个阶梯孔,孔内壁粗糙度要求均为Ra=12.5,,采用钻Φ14大孔—钻Φ10小孔,锪出阶梯的加工方式。
(10)、加工Φ6H7后侧面孔和Φ6H7下表面底孔,粗糙度要求Ra=1.6,采用钻—铰。
一次钻不能满足要求,故采用钻—铰的加工方式,钻至直径Φ5.8,再铰加工。
(11)、加工M8和M5螺纹孔,由【7】213页M8螺纹孔:首先选用Φ7的麻花钻头进行钻加工,再用丝锥攻M8螺纹。
M5螺纹孔:首先选用Φ4.2的麻花钻头进行钻加工,再用丝锥攻M5螺纹。
机械加工余量等级大全【详述】

机械加工余量等级内容来源网络,由“深圳机械展(11万㎡,1100多家展商,超10万观众)”收集整理!更多cnc加工中心、车铣磨钻床、线切割、数控刀具工具、工业机器人、非标自动化、数字化无人工厂、精密测量、3D打印、激光切割、钣金冲压折弯、精密零件加工等展示,就在深圳机械展.机械加工余量标准,25EQY—19-19991.主题内容与适用范围本标准规定了磨削加工的加工余量。
本标准适用于磨削各类材料时的加工余量。
2.技术内容加工余量表(一)厚度4以上的平面磨削余量(单面)平面长度平面宽度200以下平面宽度200以上小于100 0.3 100-250 0.45 251-500 0.5 0.6 500-800 0.6 0.65 说明:1.二次平面磨削余量乘系数1.5 2.三次平面磨削余量乘系数2 3.厚度4以上者单面余量不小于0.5-0.8 4.橡胶模平板单面余量不小于0.7 毛坯加工余量表(二)3.2I:园棒类: (1)工件的大外径无公差要求,光洁度在▽以下,例:不磨外圆的凹模带台肩的凸模、凹模、凸凹模以及推杆、推销、限制器、托杆、各种螺钉、螺栓、螺塞、螺帽外径必须滚花者。
(毫米)工件直径(D)工件长度L 车刃的割刀量和车削二端面的余量(每件) <70 71-120 121-200 201-300 301-450 直径上加工余量≤32 1 2 2 3 4 5-10 33-60 2 3 3 4 5 4-6 61-100 3 4 4 4 5 4-6 101-200 4 5 5 5 6 4-6 1.6当D<36时并不适应于调头夹加工,在加工单个工件时,应在L上加夹头量10-15。
(2)工件的大外径有公差配合要求,光洁度在▽以上,例如:外圆须磨加工的凹模,挡料销、肩台须磨加工的凸模或凸凹模等。
(毫米)工件直径(D)工件长度L 车刃的割刀量和车削二端面的余量(每件) <50 51-80 81-150 151-250 251-420 直径上加工余量≤15 3 3 4 4 5 5-10 16-32 3 4 4 5 6 5-10 33-60 4 4 5 6 6 5-8 61-100 5 5 5 6 7 5-8 101-200 6 6 6 7 7 5-8 当D<36时,不适合调头加工,在加工单个零件时,应加夹头量10-15。
自由锻造水压机锻件机械加工余量和公差标准

25 −13 27 −14 31 −16
+10
+9Βιβλιοθήκη +827 −14 31 −16
+10
+9
31 −16 34 −17
+10
34 −17 38 −19
+11
38 −19
+13
42 − 21 45 − 23 50 − 25 54 − 27 60 −30
+20 +15
+14
45 − 23 50 − 25 55 − 27 60 −30 65 −32
2.1 圆轴类锻件机械加工余量和公差
2.1.1 小型轴类锻件机械加工余量和公差表
零 件 直 径 D 零件长度 L ≤ 200 201~ 250 251~ 320 321~ 400 401~ 500 501~ 650 651~ 800 801~ 1000
余量 a 及公差 ≤1500 19 −10 21 −11 23 −12 25 −13 29 −15 32 −16
130 − 65 100 − 50
+33
+43
筒节轧机出成品
<3700
注:⑴两端取样时,长度余量等同直径余量和公差,不足 100 的为 100;单端取样时,长度余量为 2 倍 直径余量和公差。
2.4.2 其他圆筒形锻件机械加工余量和公差表。
零 件 外 径 D 零件长度 L ≤ 500 501~ 650 651~ 800 801~ 1000 1001~ 1300 1301~ 1600 1601~ 2000 2001~ 2500 > 2500
零 件 直 径 D 零件长度 L 1001~ 1500 1501~ 2000 2001~ 2500 2501~ 3000
机械加工工序间余量

4、轴类零件粗加工余量
表9
加工直径 零件长度 ≤30 >30-50 >50-120 >120-250 >250-500 >500-800 >800-1200 3 3.5 4 4 5 6 7 3.5 4 4 5 5 6 7 ≤18 >18-30 >30-50 >50-120 >120-250 >250-500 直 4 5 5 5 6 7 7 径 余 5 5 5 6 7 7 8 量 5 5 6 6 7 8 8 a 5 5 6 6 7 8 8
说明:本表摘自《一般工艺规定及指导资料》P10 剪耗规定表
三、轴的加工余量 1、外圆柱表面加工路线及所能达到的精度和表面粗糙度 表6
加工路线
尺寸精度
表面粗糙度 Ra μm
粗车 粗车,半精车 粗车,半精车, 精车 磨 粗车,半精车, 精车,细车(适用于有色金 属及合金) 粗磨,精磨 精车,滚压 粗车,半精车,粗磨,精磨, 镜面磨削 研磨 超精加工 抛光 粗车,半精车,粗磨,精磨, 镜面磨削 精研磨 粗研磨 超精加工 抛光
3、轴类零件采用热轧棒料时外径的选用 表8
零件的长度与公称直径之比 零件的 公称直 径 毛坏直径 5 6 8 10 11 12 14 16 17 18 19 20 零件的 公称直 径 ≤4 >4-8 >8-12 >12-20 7 8 10 12 14 14 16 18 19 20 21 22 14 16 18 19 20 21 22 7 8 10 12 14 8 8 10 13 14 15 17 18 20 21 22 23 8 8 11 13 14 15 18 19 21 22 23 24 21 22 25 27 28 30 32 33 35 36 37 38 零件的 公称直 径 毛坏直径 ≤4 >4-8 >8-12 >12-20 24 25 28 30 32 33 35 36 38 39 40 42 24 25 28 30 32 33 35 38 38 40 42 42 ≤4 >4-8 >8-12 >12-20 零件的 公称直 径 毛坏直径 24 26 28 32 32 34 36 38 39 40 42 42 25 26 30 32 32 34 36 38 39 40 42 43 ≤4 零件的长度与公称直径之比 >4-8 >8-12 >12-20
加工余量查询
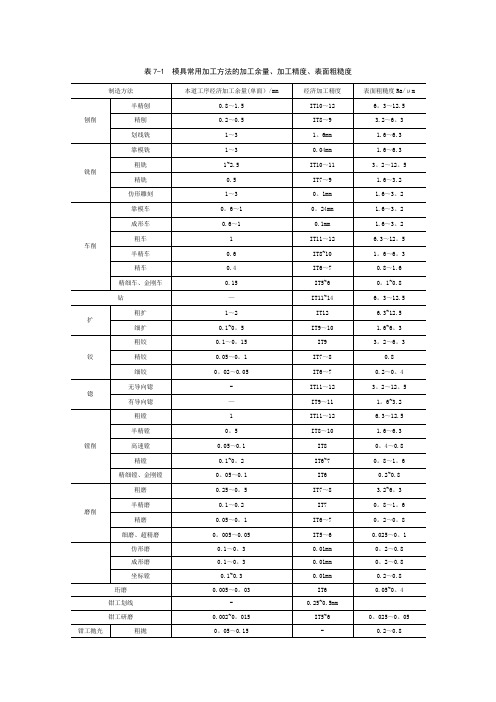
表7-1 模具常用加工方法的加工余量、加工精度、表面粗糙度细抛、镜面抛0。
005~0.01 —0.001~0.1 电火花成形加工—0.05~0。
1mm 1.25~2.5电火花线切割—0。
005~0.01mm 1.25~2.5电解成形加工—±0。
05~0。
2mm 0。
8~3.2 电解抛光0.1~0.15 —0.025~0.8电解磨削0。
1~0。
15 IT6~7 0.025~0.8照相腐蚀0.1~0.4 - 0。
1~0.8超声抛光0.02~0。
1 —0.01~0.1 磨料流动抛光0.02~0。
1 —0.01~0.1 冷挤压—IT7~8 0.08~0。
32注:经济加工余量是指本道工序的比较合理、经济的加工余量。
本道工序加工余量要视加工基本尺寸、工件材料、热处理状况、前道工序的加工结果等具体情况而定。
1。
加工总余量的确定(1)加工总余量和工序余量加工总余量(毛坯余量)—毛坯尺寸与零件图设计尺寸之差。
工序余量—相邻两工序的工序尺寸之差。
某个表面加工余量Z∑为该表面各加工工序的工序余量Zi之和,即式中n—该表面的加工工序数。
(2)影响加工余量的因素1)加工表面上的表面粗糙度和表面缺陷层深度。
2)加工前或上工序的尺寸公差。
3)加工前或上工序各表面相互位置的空间偏差。
4)本工序加工时的装夹误差.(3)查表法确定机械加工余量,总余量和半精加工、精加工工序余量可参考有关标准或工艺手册查得,并应结合实际情况加以修正。
粗加工工序余量减去半精加工和精加工工序余量而得到。
2. 工序尺寸及公差计算对于各种工序的定位基准与设计基准重合时的表面的多次加工(如外圆和内孔的加工),工序尺寸可由后续加工的工序尺寸加工上(对被包容面)或减去(对包容面)公称工序余量而求得;工序尺寸公差按所用加工方法的经济精度选定。
图4—2 表示外圆加工时加工余量、工序尺寸及其公差的分布,图中Z1、Z2、Z3为粗加工、半精加工、精加工的公称余量;To为毛坯公差.T1 、T2、T3为粗加工、半精加工、精加工的工序尺寸公差。
机械加工余量选择表

φ100 以上者,壁厚 30 以下者,或长度为 300-600 者,用上限
长度超过以上界线6者.4 ,上限乘以系数 1.3 加工粗糙度不低于▽,端面留磨量 0.5
φ6 以下小孔研磨量表(七)
材料 钢 45 T10A Cr12MoV
直径上留研磨量(毫米) 0.05-0.06
0.015-0.025 0.01-0.02
工件直径
工件长度L
(D)
≤ 101-25 251-32 321-45 451-60 601-800
100
0
0
0
0
长度上加工余量 2e
5
6
6
7
8
10
工件截面上加工余量(2a=2b)
≤10
4
4
5
5
6
6
11-25
4
4
5
5
6
6
26-50
4
5
5
6
7
7
51-100 5
5
6
7
7
7
101-200 5
5
7
7
8
8
201-300 6
7
7
8
8
9
301-450 7
7
8
8
9
9
451-600 8
8
9
9
10
10
平面、端面磨削加工余量表(五)
一、平面
宽度 厚度
<18 < 19-30 200 31-50
平面每面磨量
<100 0.3 0.3 0.4
工件长度 L
101-250 251-400
0.4
0.4
0.45
磨削加工余量标准

·机械加工余量标准25EQY—19-19991.主题内容与适用范围本标准规定了磨削加工的加工余量。
本标准适用于磨削各类材料时的加工余量。
2.技术内容加工余量表(一)厚度4以上的平面磨削余量(单面)平面长度平面宽度200以下平面宽度200以上小于100 0.3100-250 0.45251-500 0.5 0.6500-800 0.6 0.65说明:1.二次平面磨削余量乘系数1.52.三次平面磨削余量乘系数23.厚度4以上者单面余量不小于0.5-0.84.橡胶模平板单面余量不小于0.7毛坯加工余量表(二)3.2I:园棒类:(1)工件的最大外径无公差要求,光洁度在▽以下,例:不磨外圆的凹模带台肩的凸模、凹模、凸凹模以及推杆、推销、限制器、托杆、各种螺钉、螺栓、螺塞、螺帽外径必须滚花者。
(毫米)工件直径(D)工件长度 L 车刃的割刀量和车削二端面的余量(每件)<70 71-120 121-200 201-300 301-450直径上加工余量≤32 1 2 2 3 4 5-1033-60 2 3 3 4 5 4-661-100 3 4 4 4 5 4-6101-200 4 5 5 5 6 4-61.6当D<36时并不适应于调头夹加工,在加工单个工件时,应在L上加夹头量10-15。
(2)工件的最大外径有公差配合要求,光洁度在▽以上,例如:外圆须磨加工的凹模,挡料销、肩台须磨加工的凸模或凸凹模等。
(毫米)工件直径(D)工件长度 L 车刃的割刀量和车削二端面的余量(每件)<50 51-80 81-150 151-250 251-420直径上加工余量≤15 3 3 4 4 5 5-1016-32 3 4 4 5 6 5-1033-60 4 4 5 6 6 5-861-100 5 5 5 6 7 5-8101-200 6 6 6 7 7 5-8当D<36时,不适合调头加工,在加工单个零件时,应加夹头量10-15。
毛坯余量制定标准

毛坯余量制定标准毛坯余量的制定,必须结合零件的材料、结构尺寸、加工精度及下料成形方式、热处理方法、机械加工方案综合考虑。
合理的毛坯余量,不仅能有效地确保产品质量,而且可以最大限度地降低材料消耗和加工成本,提高生产效率。
现就工作中经常遇到的毛坯余量留放办法提出我们初步意见供大家讨论,欢迎各位领导及专家提出宝贵意见。
1 棒材毛坯余量1.1棒材毛坯外径机械加工余量见表1表1:轧制棒材外径机械加工余量单位:mm注: (1) 台阶轴,大外圆近中部者适用表值,大外圆近端部或凸肩很窄可适当减少;(2) 需要粗加工后去应力回火的零件,应适当增加余量;(3) 长度与直径之比大于20者,按工艺要求规定酌情增加余量。
1.1棒材毛坯长度及余量1.1.1 对于φ≤36mm的棒材毛坯,采用多件下料。
在制造BOM中,毛坯尺寸1按单个零件长度+10mm往上取整计算,毛坯尺寸2为15mm,每件制数为l。
在此,毛坯尺寸2里面的15具有双重意义,一是多件下料,二是留有15mm夹头余量。
1.1.2 对于φ>36mm的棒材毛坯,毛坯尺寸写成“L”形式,可制件数一栏注明可制件数。
对于切深不超过20mm、工件长度不超过60mm(除>M30或11/4″的高温螺母、带槽螺母和罩螺母单件下料)的中空零件,在备注栏内注明:允许多件下料。
根据规定,允许多件下料的零件,毛坯尺寸为单个零件长度+10mm,每件制数为l,坯料总长控制在200mm之内。
1.1.3 可调头加工外圆的单件下料零件,毛坯长度L=单个零件长度+10mm。
1.1.4 不能调头加工外圆的单件下料零件,应根据零件加工所需的夹头量、是否带Ⅳ试样、是否留热处理吊头、是否留顶尖孔余量决定。
1.1.4.1 夹头量见表3注:1.自动和半自动车床夹头留量一般为40mm;2.压花零件、车外螺纹、磨削外圆夹头余量一般留25mm。
1.1.4.2 杆状零件长度大于等于1200mm的均安排在井式炉中热处理(螺栓除外)。
- 1、下载文档前请自行甄别文档内容的完整性,平台不提供额外的编辑、内容补充、找答案等附加服务。
- 2、"仅部分预览"的文档,不可在线预览部分如存在完整性等问题,可反馈申请退款(可完整预览的文档不适用该条件!)。
- 3、如文档侵犯您的权益,请联系客服反馈,我们会尽快为您处理(人工客服工作时间:9:00-18:30)。
的钻头勺话E
中
*
2. 0-2.6
3. 5-4.5
平面长度
平 面 宽 度
C1Q0
>100 〜200
>200
《100
0.6-0. 7
>100 〜25C
0. 6〜0.8
0. 7-0.9
—
>250—50C
0. 7—L0
0. 75-1.0
X 8-1.1
>500
0- 8〜1.0
0. 9〜L2
0.9-12
荒
貌 后 粗
ft
柜
后
半
宽度W2,)O
注=加工带凸台的零件时,其加匚余量要检推零件的#大直筷来确定.
表5-45平面第一次粗加工余量
(mm)
平面JR大尺寸
毛 坯 制
员 方
法
停 件
格冲压
冷神压
«造
青«
可嫂铸快
<50
1.0〜1.3
0. 8〜1.0
0. 8 〜” 1
0.6〜0.8
1.0-1.4
>50 〜120
】.5〜2.0
L 3〜1.7
1.0-L1
镯孔加工余量表(九)
加工孔
的直径(mm)
材料
轻合金
巴氏合金
青铜及铸铁
钢件
细镯 前加工精度 为4级
加工
性质
粗
加工
精
加工
粗
加工
精
加工
粗
加工
精
加工
粗
加工
精
加工
直径余量(mm)
< 30
0.2
0.1
0.3
0.1
0.2
0.1
0.2
0.1
0.045
31-50
0.3
0.1
0.4
0.1
0.3
0.1
0.2
0.1
0.05
4。
25.0
38
39.7
3, 75
4OH6
10
9. »
—
—
—
EH8
42
25. Q
40
417
41-75
4油
12
1L 8
—
—
—
ISHft
IS
25. D
■13
心7
4475
45H8
}3
12^8
—
—
F™-
13H8
4B
漏0
46
47*7
47,75
48HB
U
H.&
—
—
— |
HH&1
50
2>0
花
49,7
49.7S
5OHS
51-80
0.4
0.1
0.5
0.1
0.3
0.1
0.2
0.1
0.06
81-120
0.4
0.1
0.5
0.1
0.3
0.1
0.3
0.1
0.07
121-180
0.5
0.1
0.6
0.2
0.4
0.1
0.3
0.1
0.08
181-260
0.5
0.1
0.6
0.2
0.4
0.1
0.3
0.1
0.09
261-360
0.5
0.1
15
34. 8
—
―
—
15H6
60
30.0
55
59.S
f
60H8
16
1 15.0
W■-
——
]&酥
16HB
70
33 0
65
69.5
—
70H8
18
17-0
—
—
17. 86/
18H8
80
30.0
75
79.5
—
S0H8
20
id. 0
—
1* 3
】头
踽H8
so
30-ft
flfJ-C
曲3
—
90H8
!2
ZtLO
—
21-8,
L0
1.0
>30~50
1.0
1.5
L7
1.5
1.5
2.0
1.0
1.0
1.2
10
1.2
1.2
>50
1.5 -
1.7
2.0
1.7
2.0
2.5
1.0
1.3
1.5
13
1.5
15
盘5-31星孔斌8级绮度(H8)孔内加工
(mm)
直 径宜 控
年件基
本尺寸
帖
册刀
ftw后
扩孔is
*
军忤基
衣兄寸
用帽〃
理以后
酒孔站
第一次
ei.s
22H8
100
30.0
80.0
觥3
—
L0UH8
24
22-0
一
2、3
23. g
UHU
”0
30.0
SO. 0
】19, 3
—
I20HA
£5
23*0
—
24.3
24.8
25HB
140
300
80.0
L39. 3
—
I40HS
76
210
—
25.8
踣.9
26X8
ISO
30. U
80. 0
159. 3
—
ISOHE
0. 5
1. 0
h 3
L4
1.0
L3
1-5
SA
10
L3
L 3
L5
U3
l.5
L.5
1.9
1—30
—0, 3S
-a 43
-a 52
-0- 62
-Ou 13*-—fl. IS一"15〜一制巽-D. IS0. 27
一汰21〜」』83-0l25 〜一0.39
>50-^80
>前〜1的>120-180 >180-250>及0〜3上5
28
m 0
27.*
ZMt
2SH8
180
10.0
80.0
179. 3
-
1A0H8
在坤费上加J■直程为30mm与33iwn胸乱时由用鼻田常28mm与30mm的话头香粘一次.
2-钻未直代大于用稣R留,
7级孔
m
47 rU
V
*1F・*
■ r-j
rr. h#
、,■ir
48
25.0
46・Q
47.7
*7,75
47.93
1.3〜1.8
0. 8-1-1
1.4~】.8
>120 〜260
2.0〜2.7
1.7〜2.2
1.4〜1.8
1.5~1.8
1.0-1.4
1.5-2. 5
>260〜50C
2.7〜3.5
2.2~3.0
2. 0〜2.5
1.8-2. 2
1.3〜1.8
2.2〜3.0
>500
4.6.0
3.5〜妃5
3.。〜4.0
2.4〜3.0
0.6
0.2
0.4
0.1
0.3
0.1
0.1
表
,件暴率尺寸
宜 程 余量
宜 橙 伯 茬
经威未经格处理
零件的里羊
未经斡牡理
经偈处蓬
竟车
心4)
粗车
(hlZ ⑶
1 te A
,湖〜湖
<300
>200—400
4 zoo
>m-400
3〜6 >6-10 >10-18
>30—50
1,5 1-5 2.0 2.0
L7
2^2
Z.3
Z.5
2. S蓼
2.5
2,8
3.Q
3, 3
1.5
1-5
2.0
2-0
1-8
1.8
3.P
2.3
*3
L8
L8
2-0
W.3
% 3
2.0
2. 0
5- 3
2* 5
25
-0. 74 f 87
-1.00 -bl5
-L 30
f 30Q.4S
-0+洗C. 54
—0* 4。〜一C-63
-&■460. 72
一0,52〜T.81
#8117
50
25.0
4氐0
49-7
49.75
«. 93
S0H7
60
30
5$.Q
59.5
59-5
S9.9
A0H7
70
30
孙。
69・§
阁・5
6小
7DH7
80
30
75.0
79-5
7$. 5
79.9
flOH7
90
3。
叫9
89.3
—
B9.S
WH7
tw
30
80.0
99.3
—
盼8
1WH7
LZO
30
an.a
,财
—
宽度〉200-400