改善工具与手法
品质改善工具和手法
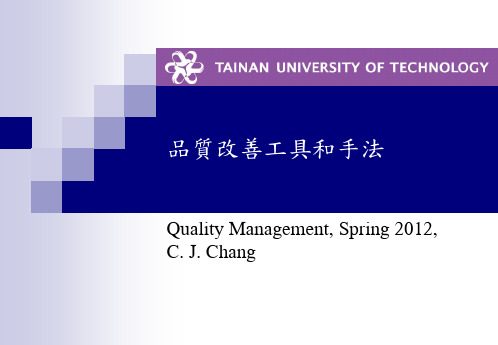
品質改善工具和手法Quality Management, Spring 2012, C. J. Chang品質管理七手法是由七項簡易的圖形方法所組成。
在品管作業中,它們當作解決問題或是品質改善工具,這些手法通常不需要複雜的計算。
品管七手法包含:1.檢核表 (check sheets)2.散佈圖 (scatter diagrams)3.直方圖 (histograms)4.柏拉圖 (Pareto diagrams)5.特性要因圖 (cause and effect diagrams)6.流程圖 (flow charts) 或層別圖 (stratification)7.管制圖 (control charts)⏹檢核表是以一種將問題查檢出來的表格或圖形☐檢核表的使用目的通常包括1.日常管理:品質管制項目的點檢、作業前的點檢、設備安全的點檢、作業標準是否被遵守的點檢2.特別調查:為了製程原因調查、產品不良原因調查或為了發現改善點所進行的點檢3.取得記錄:為了製作報告所進行之數據蒐集和檢核☐檢核表的設計並沒有特定的格式,使用者可以依照問題的特性自行設計,但必須把握簡單明瞭的原則☐檢核表可分為點檢用檢核表及記錄用檢核表⏹點檢用檢核表是為了確認作業實施、機械設備狀況,以預防不良或事故發生時使用⏹記錄用點檢表是將數據分成幾個項目,以符號或數字記錄的圖或表Ex. 記錄用檢核表(位置圖)⏹散佈圖又稱為X-Y plot,其通常用來研究兩變數間之相關性,它包含水平及垂直兩軸,用以代表成對兩變數的數據☐根據散佈圖的分佈狀況,兩特性值之間可分為三種類別:正相關、負相關、兩者無關☐散佈圖的使用目的為調查兩特性間的相關性、判斷異常值存在與否☐散佈圖的製作步驟如下:⏹蒐集數據並整理成數據表⏹在橫軸與縱軸標示尺度⏹將數據點到座標上散佈圖的樣式正相關負相關兩者無關Ex. 散佈圖10203040506001234Y直方圖⏹直方圖是將數據分佈的範圍,劃分為幾個區間,將出現在各區間內的數據之出現次數作成次數表,再以圖的形示表現出來☐直方圖可以幫助我們了解數據的分佈形態、數據的中心位置、離散程度的大小、數據和規格之間的關係☐直方圖的使用目的為掌握數據的分佈狀態、調查離散或偏離的原因、與規格比較以檢視有無問題、調查改善前後之效果5101520251.確立調查的目的2.蒐集數據3.求出最大值(L)和最小值(S)及全距(R=L-S)4.決定區間數(k)→2k-1≤n<2k5.求出區間寬幅(h),h=R/k (儘量挑好計算的值)6.決定區間之界限值(避免組限重疊情況的產生,每一組包含組下限,不包含組上限)7.求出區間之中心值8.製作次數表9.計算數據之次數10.作圖11.記入數據之相關資料和必要事項柏拉圖⏹柏拉圖是由義大利學者Vilfredo Pareto 所提出的圖形分析法,其橫軸代表問題之類別,縱軸表每一類問題發生之次數,而橫軸項目的順序則會依其計數值的大小由左至右排列☐柏拉圖原理又稱為80/20原則☐柏拉圖通常用來區分造成品質問題之少數重要原因,及多數不重要之原因500缺點數1.座標之選取2.蒐集數據資料3.整理數據資料1.依蒐集項目數據大小排序2.計算累積次數和百分比3.將出現次數較少的項目整理成其它4.柏拉圖繪製1.以橫軸之項目別,繪製長條圖,其高度為縱軸變數之數值2.畫出累積百分比曲線5.觀察與分析1.在柏拉圖中找出重要的少數,其原則是在20%~30%的項目請依照下表的資料製作柏拉圖,並指出少數重要的不良項目020406080100050100150200灰塵 碰撞 漆太薄 流漆 斑點 其他缺點數不良項目⏹特性要因圖為一問題分析工具,用以辨認造成某一特定問題之所有可能原因,此圖之結構類似魚骨,因此又稱為魚骨圖☐特性要因圖可視為一腦力激盪之工具,其基本構成元素為符號及線,用以表示原因和結果間之關係☐特性是指工作的結果或是工程產生的結果☐要因是指對結果造成影響的原因⏹EX. 製造過程中,品質特性之變異通常起因於4M的差別:作業員(manpower)、機器設備(machinery)、材料(materials)、作業方法(methods)☐特性要因圖的應用包含l問題原因之列舉、散佈分析及製程分析Ex. 特性要因圖1.決定特性2.填入要因的背骨3.填入要因大骨4.集體思考後填入次要因5.檢核是否遺漏要因6.找出重要影響度的原因7.驗證8.填入必要事項⏹流程圖為一圖形法,用來記錄和描述一個複雜過程之各項作業和順序☐透過流程圖,我們了解流程中能產生變異來源的步驟有那些,或是了解那些步驟可以增加價值(或沒有價值),進而進行刪除、簡化、合併或重組來進行製程的改善☐常見的流程圖符號如下:Ex. 流程圖層別法⏹透過數據分類加以分析,將原料、操作人員、機器設備等,按照特性加以分門別類,找出其中的差異及問題,並針對其問題加以改善之方法即為層別法 ☐層別法是資種概念,並沒特定的圖形表示20304050605075100125150x y 20304050605075100125150xy⏹品管新七手法為處理文字資料之手法,1972年日本科學技術聯盟的納谷嘉信教授,研究歸納出七項工具,為與原有的「QC七手法」作區別,所以稱為「QC新七手法」。
现场改善工具及运用
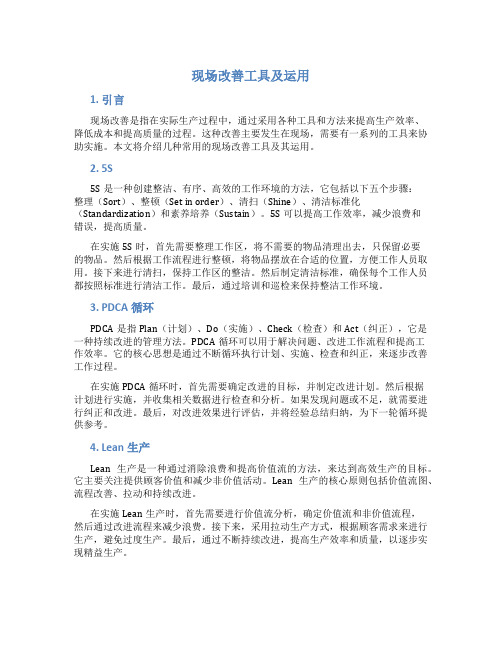
现场改善工具及运用1. 引言现场改善是指在实际生产过程中,通过采用各种工具和方法来提高生产效率、降低成本和提高质量的过程。
这种改善主要发生在现场,需要有一系列的工具来协助实施。
本文将介绍几种常用的现场改善工具及其运用。
2. 5S5S是一种创建整洁、有序、高效的工作环境的方法,它包括以下五个步骤:整理(Sort)、整顿(Set in order)、清扫(Shine)、清洁标准化(Standardization)和素养培养(Sustain)。
5S可以提高工作效率,减少浪费和错误,提高质量。
在实施5S时,首先需要整理工作区,将不需要的物品清理出去,只保留必要的物品。
然后根据工作流程进行整顿,将物品摆放在合适的位置,方便工作人员取用。
接下来进行清扫,保持工作区的整洁。
然后制定清洁标准,确保每个工作人员都按照标准进行清洁工作。
最后,通过培训和巡检来保持整洁工作环境。
3. PDCA循环PDCA是指Plan(计划)、Do(实施)、Check(检查)和Act(纠正),它是一种持续改进的管理方法。
PDCA循环可以用于解决问题、改进工作流程和提高工作效率。
它的核心思想是通过不断循环执行计划、实施、检查和纠正,来逐步改善工作过程。
在实施PDCA循环时,首先需要确定改进的目标,并制定改进计划。
然后根据计划进行实施,并收集相关数据进行检查和分析。
如果发现问题或不足,就需要进行纠正和改进。
最后,对改进效果进行评估,并将经验总结归纳,为下一轮循环提供参考。
4. Lean生产Lean生产是一种通过消除浪费和提高价值流的方法,来达到高效生产的目标。
它主要关注提供顾客价值和减少非价值活动。
Lean生产的核心原则包括价值流图、流程改善、拉动和持续改进。
在实施Lean生产时,首先需要进行价值流分析,确定价值流和非价值流程,然后通过改进流程来减少浪费。
接下来,采用拉动生产方式,根据顾客需求来进行生产,避免过度生产。
最后,通过不断持续改进,提高生产效率和质量,以逐步实现精益生产。
常用质量管理工具和改进方`

常用质量管理工具和改进方法一、PDCA 循环(戴明环):是各级管理工作应遵循的基本原理。
(一) PDCA 循环四个阶段:1、 P (plan )—计划,是计划,方法目标的确定及活动计划的制定。
2、 D (Do )—实施,是执行,实施具体运行、实施计划中的内容。
3、 C(Check)—检查,总结计划执行的结果,分清哪些做对了,哪些做错了,明确效果,找出问题。
4、 A (Actiou )—处理,对检查结果进行处理,成功的经验加以肯定,并进行标准化,适当推广,失败的教训加以总结,对于没有解决的问题提交下一个PDCA 循环。
(二) PDCA 循环四个特点:1、 四个阶段缺一不可,周而复始。
1) PDCA 循环的四个过程不是运行一次就终结,而是周而复始地进行。
2) 一个循环结束了,解决一部分问题,可能还有问题没有解决或者又出现新的问题,再进行下一个PDCA 循环,以此类推—持续改进无止境。
2、 大环套小环。
在PDCA 的某一阶段也会存在制定计划、落实计划、检查计划的实施进度和处理的小PDCA 循环。
大循环套小环3、 阶梯式上升的循环。
1) PDCA 循环不是停留在一个水平上的循环,不断解决问题的过程就是逐步上升的过程,是质量持续改进、持续提升的过程。
2) 每循环一次,工作质量就提高一步。
4、 科学统计的工具。
1)PDCA 循环应用了科学的统计观念和处理方法,是作为推动工作,发现问题和解决问题的有效工具。
2)典型的模式:“四个阶段”“九个步骤”和“七种工具”。
① 四个阶段:P —计划、D —实施、C —检查、A —处理。
② 九个步骤:发现问题(F )→成立改进小组(O )→明确现行流程和规范(C )→出现问题的根本原因分析(U )→选择可改进的流程(S )→计划(P )→实施(D )→检查(C )→处理(A )。
③七种工具:直方图、因果图、排列图、控制图、相关图、分层法、统计分析表。
二、常用质量改进工具与方法1、头脑风暴法采取会议方式,利用集体思考,引导每个参加会议的人员围绕某个中心议题,广开言路,激发灵感,在自己头脑中掀起风暴,毫无顾忌,畅所欲言,发表独特见解的一种创造性思考方法。
现场改善十大利器

现场改善十大利器引言在现场改善过程中,使用一些有效的工具和技术能够提高工作效率并优化生产过程。
本文将介绍十大现场改善的利器及其重要性,帮助您在实践中取得更好的改善效果。
1. 5W1H 分析法5W1H分析法是问题解决过程中常用的工具之一。
它通过分析问题或情况的“谁、什么、哪里、何时、为什么以及如何”,帮助我们深入了解问题的本质,并找到解决问题的方向。
2. PDCA循环PDCA循环是改善过程中的核心工具。
它包含四个阶段:计划(Plan)、执行(Do)、检查(Check)和行动(Act)。
通过循环执行这四个阶段,我们能够不断调整和改进原有的解决方案,最终达到预期的改善目标。
3. 5S整理法5S是一种现场管理方法,包括整理(Seiri)、整顿(Seiton)、清扫(Seiso)、标准化(Seiketsu)和纪律(Shitsuke)五个步骤。
通过实施5S整理法,我们可以改善工作环境,提高工作效率,减少浪费和错误。
4. 流程图流程图是用图形的方式展示流程的工具。
通过绘制流程图,可以清晰地描述和理解工作流程,找出潜在的问题和瓶颈,并提出改进建议。
5. 数据收集和分析在现场改善过程中,收集和分析数据是非常重要的一步。
通过收集准确的数据,并进行分析,可以帮助我们了解当前状况,发现问题所在,并制定相应的改善方案。
6. 标准化工作在现场改善中,制定和执行标准化工作是至关重要的。
通过制定明确的工作标准,可以统一工作流程,减少变异,提高质量和效率。
7. 问题解决技术问题解决技术,如鱼骨图、五个为什么、故障模式与影响分析(FMEA)等,是在分析和解决问题时非常有用的工具。
它们帮助我们深入了解问题背后的原因,并找到解决问题的途径。
8. 持续改进文化要将现场改善持续下去,需要建立一种持续改进的文化。
这包括培养员工的改善意识,鼓励他们提出改进建议,并不断提高团队的改善能力。
9. 效果评估在改善措施实施后,进行效果评估是非常重要的。
持续改进的工具和技术
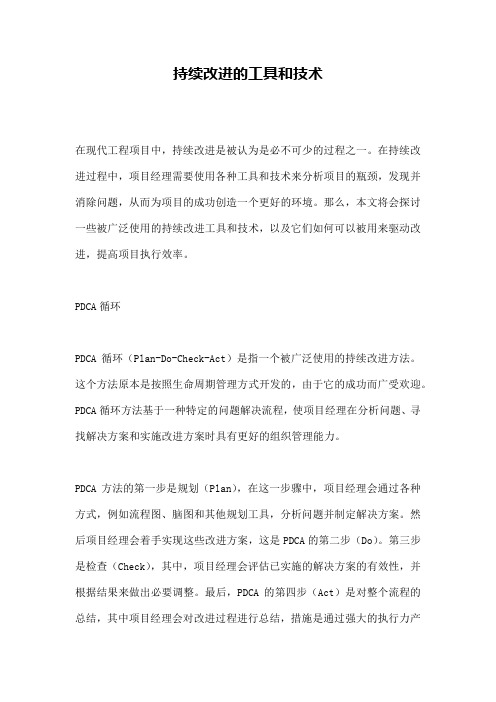
持续改进的工具和技术在现代工程项目中,持续改进是被认为是必不可少的过程之一。
在持续改进过程中,项目经理需要使用各种工具和技术来分析项目的瓶颈,发现并消除问题,从而为项目的成功创造一个更好的环境。
那么,本文将会探讨一些被广泛使用的持续改进工具和技术,以及它们如何可以被用来驱动改进,提高项目执行效率。
PDCA循环PDCA循环(Plan-Do-Check-Act)是指一个被广泛使用的持续改进方法。
这个方法原本是按照生命周期管理方式开发的,由于它的成功而广受欢迎。
PDCA循环方法基于一种特定的问题解决流程,使项目经理在分析问题、寻找解决方案和实施改进方案时具有更好的组织管理能力。
PDCA方法的第一步是规划(Plan),在这一步骤中,项目经理会通过各种方式,例如流程图、脑图和其他规划工具,分析问题并制定解决方案。
然后项目经理会着手实现这些改进方案,这是PDCA的第二步(Do)。
第三步是检查(Check),其中,项目经理会评估已实施的解决方案的有效性,并根据结果来做出必要调整。
最后,PDCA的第四步(Act)是对整个流程的总结,其中项目经理会对改进过程进行总结,措施是通过强大的执行力产生持续改进的效果。
瑞士军刀瑞士军刀是一种功能强大、设计精美的多功能工具,可以用于各种场景中,成为一个非常有用的帮手。
类似的,在项目管理领域中,瑞士军刀也可以帮助项目经理在改进过程中更快、更有效地解决问题。
瑞士军刀与PDCA方法非常相似,被设计为可以解决各种问题。
这种工具可以包括看板、异常管理、流程图等多种方法,它们能够帮助项目经理找到问题并解决,比起其他方法更为跨领域。
5S技术在现代工程项目中,5S技术是一种被广泛使用的工具,用以创建一种更有组织、更高效的工作环境。
这种技术的名称来源于五个关键字,包括整理、整顿、清扫、清洁和自律。
当您使用5S技术时,这些关键字将是您想要实现的目标。
整理(Sort)和整顿(Straighten)是第一步,它们是用于创建一个高效的工作环境的关键步骤。
现场改善十工具

实 例2:某部门主管因患心脏病,遵照医生嘱咐每天只上 班三、四个小时,他很惊奇地发现,这三,四个小时所做 的事在质与量方面与以往每天花费八、九个钟头所做的事 几乎没有两样。他所能提供的唯一解释便是:他的工作时 间既然被迫缩短,他只好将它花在最重要的工作上,这或 许是他得以维护工作效能和提高工作效率的主要原因。
• 提出有创意的观点时应多一些鼓励。
• 主持人要引导大家多提意见,拼出思想火花,剌激大家思 考,思考可以搭便车,比如猫,便想到花猫、黑猫……。
• 在白板上记录所有点子,让人人都看得到
• 禁止批评或评价,拒绝裁判性的思想或评论:会议中不管 构想好坏,绝不加以批评或反对。即使提出不同意见,也 要欢迎。对评判留在会后进行。 • 一直激荡到每个人都说“放弃”,或是直到时间到了。 • 会议时间控制在40分钟到1小时。
人、机、料、法、环、检测
大原因
中原因 小原因 细小原因 中原因
特 性
因果分析图的形式
三.对策表:(检查表、调查表) 是统计图表的一种,是记 录收集数据的一种好形式,格式多种多样。 四.直方图: 将数据按其顺序分成若干间隔相等的组,以
组距为底边,以落入各组的频数为高的若干长方排列的图,
判断工序是否处于稳定状态,掌握工序能力。直观看出产 品质量特性的分布状态。对总体进行推断。
③ 重排:改变次序、改用其他方法、改用别的东西。经过 取消合并后,可再根据“何人、何处、何时”三提问进行重 排,使其能有最佳的顺序,除去重复,办事有序。如:将工
作台、机器,以及储运处的布置重新调整,以减少搬运的距
离。用台车搬运代替徒手搬运。也许要变更操作或检验的顺 序。更换材料。
④ 简化:连接更合理、使之更简单、去除多余动作。经过
精益改善的工具与方法

精益改善的工具与方法精益改善是一种管理方法和工具,旨在通过消除浪费、提高效率和质量,实现持续改进和增加价值。
在这篇文章中,我们将介绍精益改善的一些常用工具和方法,以及它们的应用。
一、价值流图价值流图是精益改善中的一种重要工具,用于分析和改进价值流程。
它可以帮助团队识别流程中的浪费,找到改进的机会。
通过绘制当前状态的价值流图,团队可以看到整个流程,包括价值创造和非价值创造的活动。
然后,团队可以通过分析和改进这些活动,实现流程的优化和改进。
二、5S5S是指整理(Seiri)、整顿(Seiton)、清扫(Seiso)、清洁(Seiketsu)和纪律(Shitsuke)五个步骤。
它是一种用于创建和维护清洁、有序和高效工作环境的方法。
通过实施5S,可以减少浪费、提高效率和质量,创造一个更好的工作环境。
三、PDCA循环PDCA循环是精益改善中的一种常用方法,它包括计划(Plan)、执行(Do)、检查(Check)和行动(Act)四个阶段。
通过循环执行这四个阶段,团队可以不断地进行改进和优化。
在计划阶段,团队制定改进计划;在执行阶段,团队执行计划并收集数据;在检查阶段,团队分析数据并评估改进效果;在行动阶段,团队采取行动并实施改进。
通过不断循环执行PDCA循环,团队可以实现持续改进和增加价值。
四、标准化工作标准化工作是精益改善中的一种重要方法,它可以帮助团队建立一套统一的工作标准和规范。
通过标准化工作,团队可以减少差异、提高效率和质量,实现工作的稳定性和可持续性。
标准化工作可以通过制定工作流程、编写工作指导书、培训员工等方式实施。
五、持续改进持续改进是精益改善的核心理念,它强调通过不断地改进和优化来增加价值。
持续改进需要团队的全力参与和持续投入,它不仅仅是一次性的活动,而是一个长期的过程。
团队可以通过持续改进来识别和消除浪费,提高效率和质量,实现持续的业绩提升。
精益改善是一种重要的管理方法和工具,它可以帮助组织实现持续改进和增加价值。
5大工具及7大手法

质量管理的5大工具及7大管控方法1、五大工具APQPAPQP(Advanced Product Quality Planning)即产品质量先期策划,是一种结构化的方法,用来确定和制定确保某产品使顾客满意所需的步骤。
产品质量策划的目标是促进与所涉及的每一个人的联系,以确保所要求的步骤按时完成。
有效的产品质量策划依赖于公司高层管理者对努力达到使顾客满意这一宗旨的承诺。
产品质量策划有如下的益处:◆引导资源,使顾客满意;◆促进对所需更改的早期识别;◆避免晚期更改;◆以最低的成本及时提供优质产品。
SPCSPC(Statistical Process Control)即统计过程控制,主要是指应用统计分析技术对生产过程进行适时监控,科学区分出生产过程中产品质量的随机波动与异常波动,从而对生产过程的异常趋势提出预警,以便生产管理人员及时采取措施,消除异常,恢复过程的稳定从而达到提高和控制质量的目的。
SPC非常适用于重复性的生产过程,它能够帮助组织对过程作出可靠的评估,确定过程的统计控制界限判断过程是否失控和过程是否有能力;为过程提供一个早期报警系统,及时监控过程的情况,以防止废品的产生,减少对常规检验的依赖性,定时以观察以及系统的测量方法替代大量检测和验证工作。
(1)SPC实施意义可以使企业:◆降低成本◆降低不良率,减少返工和浪费◆提高劳动生产率◆提供核心竞争力◆赢得广泛客户(2)实施SPC两个阶段•分析阶段:运用控制图、直方图、过程能力分析等使过程处于统计稳态,使过程能力足够。
••监控阶段:运用控制图等监控过程•(3)SPC的产生工业革命以后,随着生产力的进一步发展,大规模生产的形成,如何控制大批量产品质量成为一个突出问题,单纯依靠事后检验的质量控制方法已不能适应当时经济发展的要求,必须改进质量管理方式。
于是,英、美等国开始着手研究用统计方法代替事后检验的质量控制方法。
1924年,美国的休哈特博士提出将3Sigma原理运用于生产过程当中,并发表了著名的“控制图法”,对过程变量进行控制,为统计质量管理奠定了理论和方法基础。
品质改善工具与分析方法

其它
///
总计
物
数量 23 32 48
8
2.柏拉图:决定改善主题 (1).整理表:将查检表的数据进行整理 (2).柏拉图:将整理后的数据绘制柏拉图 (3).考虑查检项目的权重
(1).整理表
项目 不适当蜡(A) 尺寸不合(B) 形状不良(C) 修整不良(D) 其 它(E)
不良数 48 32 23 4 8
法
人
•喷枪ห้องสมุดไป่ตู้本 体太近
异物混入 调配不当
料
喷蜡条件 未注明
未按作业 执行
精度不够
不熟练 遗漏作业 指示处喷上 不适当的蜡
•喷枪堵塞
蜡质储存 太久
润滑不足
机
(3).问自已五次为甚么改善法(5W改善法)
不符 合 项目
指示处 喷上不 适当的 蜡
异常原 因
(why1)
(why2)
喷枪离 本体太 近
操作者 无法固 定距离
(why3) (why4)
没有固 定器
(why5)
改进方法 执行结果 监测作为 与确认
1.增加固 定装置。
2.自动喷 枪。
1.增加固定 装置并在线 确认良好。 2.基于同一 在线生产多 种门板无法 共享故不接 受。
每月对固定 装置进行保 养
喷枪堵 塞
喷蜡未 订操作
条件
操作者
自行订 定喷蜡 的黏度,
压力与 温度的 操作条 件
特 殊 分 产品/制 类 程/公差
0.5mm
30℃, 2cm/mi n, 200psi
20cm
方法
量测
测厚 仪
抽样 数
5
流量 1 仪
卡尺 1
抽样 濒率 1h
质量持续改进方法与工具
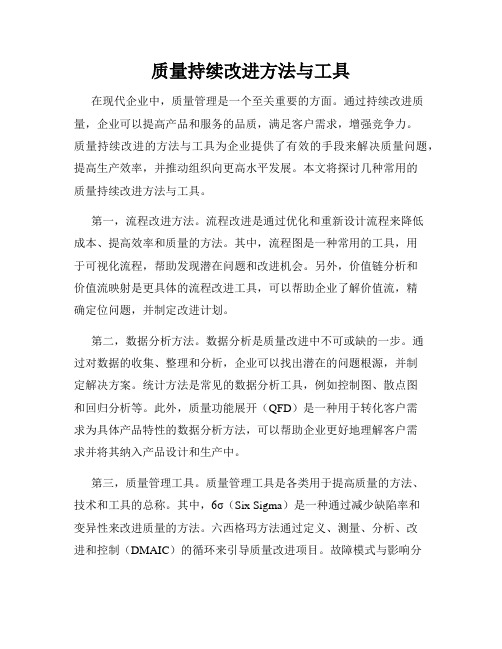
质量持续改进方法与工具在现代企业中,质量管理是一个至关重要的方面。
通过持续改进质量,企业可以提高产品和服务的品质,满足客户需求,增强竞争力。
质量持续改进的方法与工具为企业提供了有效的手段来解决质量问题,提高生产效率,并推动组织向更高水平发展。
本文将探讨几种常用的质量持续改进方法与工具。
第一,流程改进方法。
流程改进是通过优化和重新设计流程来降低成本、提高效率和质量的方法。
其中,流程图是一种常用的工具,用于可视化流程,帮助发现潜在问题和改进机会。
另外,价值链分析和价值流映射是更具体的流程改进工具,可以帮助企业了解价值流,精确定位问题,并制定改进计划。
第二,数据分析方法。
数据分析是质量改进中不可或缺的一步。
通过对数据的收集、整理和分析,企业可以找出潜在的问题根源,并制定解决方案。
统计方法是常见的数据分析工具,例如控制图、散点图和回归分析等。
此外,质量功能展开(QFD)是一种用于转化客户需求为具体产品特性的数据分析方法,可以帮助企业更好地理解客户需求并将其纳入产品设计和生产中。
第三,质量管理工具。
质量管理工具是各类用于提高质量的方法、技术和工具的总称。
其中,6σ(Six Sigma)是一种通过减少缺陷率和变异性来改进质量的方法。
六西格玛方法通过定义、测量、分析、改进和控制(DMAIC)的循环来引导质量改进项目。
故障模式与影响分析(FMEA)是另一个常用的质量管理工具,用于识别和排除潜在的故障模式,以提前处理潜在的风险。
第四,持续改进团队。
持续改进需要一个专门的团队来推动和实施改进措施。
这个团队通常由跨职能成员组成,具备各方面的专业知识。
他们负责收集数据、分析问题、制定解决方案,并监督改进项目的实施过程。
团队成员还需要与其他部门和员工紧密合作,确保改进措施的顺利实施并取得预期效果。
通过以上提到的质量持续改进方法与工具,企业可以不断提高产品和服务的质量,满足客户需求,提高市场竞争力。
然而,需要注意的是,每个企业都有其独特的情况和需求,因此在选择和应用这些方法和工具时,应根据具体情况进行调整和适应。
5大工具及7大手法
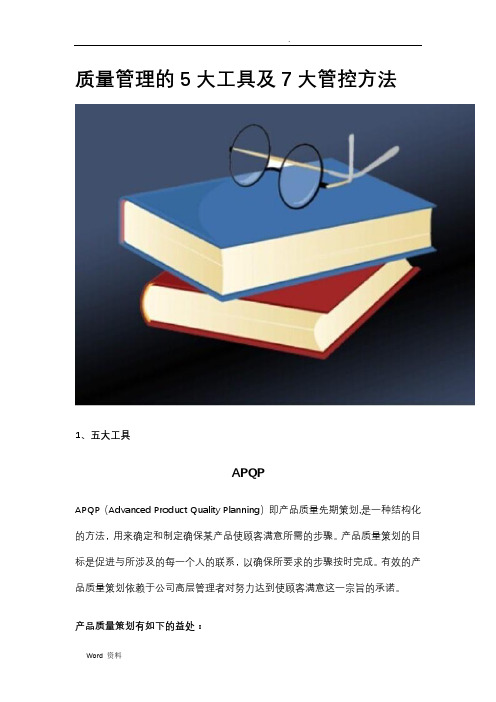
质量管理的5大工具及7大管控方法1、五大工具APQPAPQP(Advanced Product Quality Planning)即产品质量先期策划,是一种结构化的方法,用来确定和制定确保某产品使顾客满意所需的步骤。
产品质量策划的目标是促进与所涉及的每一个人的联系,以确保所要求的步骤按时完成。
有效的产品质量策划依赖于公司高层管理者对努力达到使顾客满意这一宗旨的承诺。
产品质量策划有如下的益处:◆引导资源,使顾客满意;◆促进对所需更改的早期识别;◆避免晚期更改;◆以最低的成本及时提供优质产品。
SPCSPC(Statistical Process Control)即统计过程控制,主要是指应用统计分析技术对生产过程进行适时监控,科学区分出生产过程中产品质量的随机波动与异常波动,从而对生产过程的异常趋势提出预警,以便生产管理人员及时采取措施,消除异常,恢复过程的稳定从而达到提高和控制质量的目的。
SPC非常适用于重复性的生产过程,它能够帮助组织对过程作出可靠的评估,确定过程的统计控制界限判断过程是否失控和过程是否有能力;为过程提供一个早期报警系统,及时监控过程的情况,以防止废品的产生,减少对常规检验的依赖性,定时以观察以及系统的测量方法替代大量检测和验证工作。
(1)SPC实施意义可以使企业:◆降低成本◆降低不良率,减少返工和浪费◆提高劳动生产率◆提供核心竞争力◆赢得广泛客户(2)实施SPC两个阶段•分析阶段:运用控制图、直方图、过程能力分析等使过程处于统计稳态,使过程能力足够。
••监控阶段:运用控制图等监控过程•(3)SPC的产生工业革命以后,随着生产力的进一步发展,大规模生产的形成,如何控制大批量产品质量成为一个突出问题,单纯依靠事后检验的质量控制方法已不能适应当时经济发展的要求,必须改进质量管理方式。
于是,英、美等国开始着手研究用统计方法代替事后检验的质量控制方法。
1924年,美国的休哈特博士提出将3Sigma原理运用于生产过程当中,并发表了著名的“控制图法”,对过程变量进行控制,为统计质量管理奠定了理论和方法基础。
质量改善工具、流程及手法
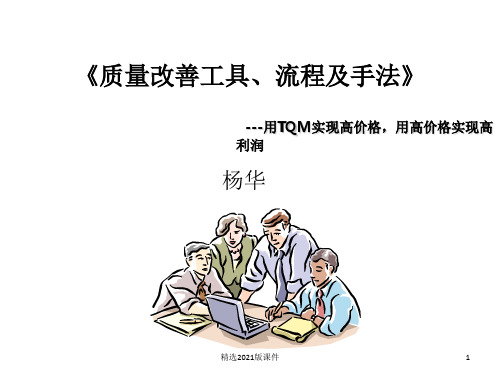
精选2021版课件
14
生产现场人员养成良好的品质意识要注意些什么呢?
1.不接受不良品
2.养成自检的习惯 3.不要让不合格品流到下一工序
4.按操作规范作业 5.严格的首件检查 6.不要一味追求速度 7.不要机器带病作业
8.不要“知情不报”
9.要有问题意识
10.不断提升自已的专业能力
精选2021版课件
29
品质零缺陷取向 预防问题
检查 产品
预防 问题
解决 问题
控制 现场
笔记
检查产品是笨蛋 解决问题是本份 预防问题是高手
精选2021版课件
30
零缺陷 的精髓
零缺陷的精髓
笔记
一个中心 第一次就做对!
两个基本点 有用和可依赖!
工作过程零缺陷 工作结果
三个代表 客户/员工/供应商!
提升客户满意度 降低品质成本
满足市场需要的经营法的概念满足市场需要的经营法的概念社会以及顾客需要些什么接叐自己的工作结果的人需要什么听叏真实的声音重新审规自己一直讣定的以及迄今为止一直看作是理所当然的常识重新审规自己的想法敂捷地感悟到顾客真正的需求确定目标自觉履行对顾客的承诺幵使这种意识自觉履行对顾客的承诺幵使这种意识扎根二每一个员工的日常工作中扎根二每一个员工的日常工作中前工序上游部门前工序上游部门自己工序本部门后工序下游部门顾客顾客顾客顾客后工序就是顾客前工序也是顾客顾客最织用户开展研究设计制造商品销售听叏顾客的需求顾客是诽顾客是诽贯彻满足市场需要的经营法贯彻满足市场需要的经营法某企业学员培训需求课查统计共收到问卷49仹质量意识质理意识的体现
《质量改善工具、流程及手法》
---用TQM实现高价格,用高价格实现高 利润
杨华
精益改善方法和工具
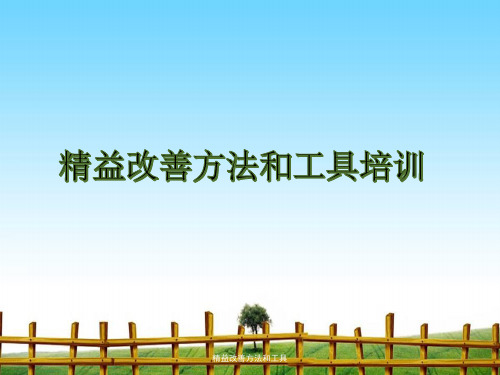
原因调查 5Why 1How to fix
Why? 1 原因1 Why? 2 原因2
Why? 3 原因3
Why? 4 原因4
Why? 5
问题点纠正 5W2H
根本原因 纠正措施
预防措施 Errorproof FMEA 精益改善方法和工吸具取教训
4个步骤:
1.掌握情况:说明问题并描 述相关信息。
2.原因调查:问“为什么” 直到找出根本原因。
精益改善方法和工具
1 改善思路:创新思维-目标导向 目标导向(现在/未来/想法)
实现的想法 3
未来(目标) 2 现状(吐槽) 1
精益改善方法和工具
1 改善思路:创新思维-目标导向
目标导向(想法列举)
計費 分析
重複 呼叫 方案 呼叫 預測 和分 峰
成本 分析
產品 利潤 分析
產品 生命 週期
精益改善方法和工具
➢ 1、确定议题 ➢ 2、会前准备 ➢ 3、确定人选 ➢ 4、明确分工 ➢ 5、规定纪律 ➢ 6、掌握时间 ➢ 7、实施
精益改善方法和工具
1 改善思路:头脑风暴
头脑风暴的四大规则
精益改善方法和工具
1 改善思路:头脑风暴
不许评价!—— 要到评估阶段才能进行评价
规则一
讨论 问
皱眉
禁止与会者在 会上对他人的 设想评头论足 ,排除评论性 的判断。至于 对设想的评判 ,留在会后进 行;
1 改善思路:创新思维-目标导向
目标导向(想法聚类)
計費 分析
重複 呼叫 方案
呼叫 預測 和分 峰
成本 分析
產品 利潤 分析
產品 生命 週期
精益改善方法和工具
1 改善思路:创新思维-目标导向
qc七大手法与品质工具改善的使用技巧

Chapter 2 品質改善的工具與技術
2-1
結束
結束
結束
結束
查檢表 1/3
查檢表乃以圖或表呈現出問題所在,期並無特定格 式,使用者可依據問題屬性設計之,並以自訂符號 填註以了解問題狀況。
點查檢表
次序 1 2 3 4 5 6 7 8
製作漢堡檢核表 項目
洗手 烤漢堡 塗沙拉醬 放蕃茄 放生菜 放肉 放蛋 裝袋
天马行空官方博客:/tmxk_docin ;QQ:1318241189;QQ群:175569632
2-9
結束
特性要因圖
特性要因圖為分析根本問題之一種工具,研究造成 特定問題或結果可能原因。又稱因果關係圖或魚骨 圖。 5M1E: Material, Method, Measurement, Machine, Man, Environment
2-11
結束
直方圖
直方圖(histogram)使用面最為廣泛。將蒐集之數據依據組距 (bin)分為幾組,再統計其發生次數並作成一個表。 直方圖為一種長條圖,其一軸為量測值,另一軸為百分比 或頻率..) 直方圖為SPC重要工具,因為常用統計公式應用於常態機率 分配 See example 2-2, page 36
2-32
結束
關聯圖法 1/2
將原因與結果間,或目的與手段間等複雜問題,利 用邏輯方式分析使關係明確化,步驟如下:
➢ 決定主題研究。 ➢ 組成研究團隊,以共同解決問題。 ➢ 找尋影響問題的各種可能原因。 ➢ 將原因間關係和因果關係以箭頭表示,即形成關聯
圖。 ➢ 修正圖形,即再整體討論,若有不足項目應追加之。
Chapter 2 品質改善的工具與技術
2-43
結束
PDCA循環 2/2
品质改善工具与分析方法

3 60 46 13 81 65 23 31 21 33 93 61 43 74 73 53 49 41 63 75 92
4 50 35 14 70 61 24 30 43 34 34 35 44 52 74 54 62 26 64 36 44
5 26 33 15 93 84 25 88 87 35 55 32 45 84 94 55 70 97 65 47 19
所有的失效原因 (2).鱼骨图:找出主要的失效原因 (3).5W改善法:跟据主要失效原因,提出改善对策
不良项目:指示处喷上不适当的蜡 (1).整理表
发生频次
失效原因
人机料法环
高中低
喷枪离本 ●
▲
体太近
未按作业 执行
●▲
蜡质储存 太久
●
▲
喷枪堵塞 ●
▲
公差错误
●
▲
精度不够
●
▲
遗漏作业
●▲
(2).鱼骨图
0.826
841.21x + 545.63
0.824
R2 = 0.8346
0.822
0.82 0.818
0.816
1.9 1.92 1.94 1.96 1.98 2
外圓收縮量(y)
多項式 (外圓收縮 量(y))
执行结果
能需求 效模式 效应 重 级 原因 生 程
管制(侦 检 数
人与
度
度 管制 测) (预防)
度 (RPN)
日期 实行措施 S O D RPN
车板内部 指示处 长时间灰 7 手动喷洒 附着不 尘破坏涂
适当的 料,造成使用寿命
用蜡来附
(7)
着于内部
门板以防
劣化寿命
2023年现场改善工具及案例分析方案模板 (2)
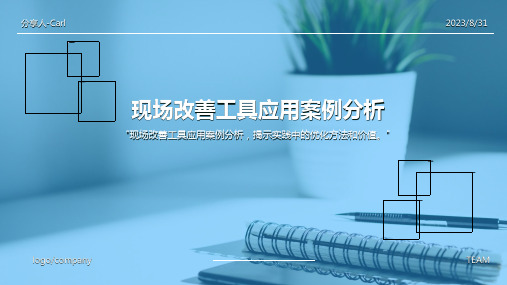
3.3.超市顾客等待时间长、购物车放弃率高,改进措施 改善结账等待时间,提升购物体验
根据数据分析,某超市的顾客流程图显示,在某个时间段内,顾客在收购商品后排队结账的等待时间较长, 导致消费者不愿意等待,提高了购物车放弃率。为了解决这个问题,超市提出了增加收银台、优化收银流程 以及培训收银员的改进措施。经过改善后,顾客结账等待时间大幅缩短,购物体验得到提升,购物车放弃率
现场实施改善追踪
1.追踪措施执行情况:记录进展,包括责 任人、时间、结果等
追踪措施执行情况:记录改善计划中每个具体措施的实施进展情况,包括责任人、 开始时间、结束时间、执行结果等。
2.及时发现和纠正,确保改善计划实施
通过追踪措施执行情况,可以及时发现执行不到位或出现延迟的情况,及时采取纠 正措施,确保改善计划的顺利实施。
分享人-Carl
2023/8/31
现场改善工具应用案例分析
"现场改善工具应用案例分析,揭示实践中的优化方法和价值。"
logo/company
TEAM
5W1H分析法 根因分析法 流程图 多维度数据分析
5W1H分析法
5W1H analysis method
工具介绍
何时使用
1. 当出现生产线或工作流程中的问题,需要快速解决时,可以使用现场改 善工具。比如,生产线上出现了停机现象,需要快速找到原因并解决,就可 以使用5S、PDCA、Kaizen等工具。
1. 当需要提高生产效率或质量时,也可以使用现场改善 工具。比如,使用流程图或价值流图来优化生产流程, 使用6Sigma等工具来提高生产质量。
- 1、下载文档前请自行甄别文档内容的完整性,平台不提供额外的编辑、内容补充、找答案等附加服务。
- 2、"仅部分预览"的文档,不可在线预览部分如存在完整性等问题,可反馈申请退款(可完整预览的文档不适用该条件!)。
- 3、如文档侵犯您的权益,请联系客服反馈,我们会尽快为您处理(人工客服工作时间:9:00-18:30)。
紧急围堵措施
详述不良发生根本 原因
分人、机、料、法、环及保养描述为什么在这种环境下会发生变化,或 者系统为什么未先发现不良,是否系统自身存在漏洞 1.详述什么人、什么时间、做什么事情(5W)和现在如何实现材料、人 力、方式等方面的变化以从根本上清除会造成不良的原因 2.从排除短期对策后其他不良类型考虑 1.描述确认的统计结果(数据) 2.在永久对策确认有效前,持续实施短期对策 1.描述由于内外部文化/组织自身的改变而防止此类问题再次发生的措施 2.小组成员应负责将这些建议运用在管理方面并推动改善动作的执行 小组主席肯定组员在解决问题中所作出的努力和成绩
执行长期对策: 作业标准化) D5. 执行长期对策:(作业标准化)
5-1. 矫正已经生产的各项有缺陷零组件 5-2. 对所有长期对策建立一套管制计划 SPC度量各项矫正措施之效果 5-3. 以SPC度量各项矫正措施之效果 5-4. 执行适当训练上的改变
验证长期对策: 对策追踪) D6. 验证长期对策:(对策追踪)
HOW? ?
1.挑选和记录内外部成员
说明
2.确定小组成员和主席(leader & members) 使用客户明白之术语描述不良发生的背景和确定不良发生的统计数据 1.详述什么人、什么时间、做什么事情(5W)和现在如何找出及hold不 良品,防止流向客户 2.从成本、交付、是否造成其他不良等方面考虑效用
500 0
nt h mo 屑 屑 Y RA 膠框 T 塑 B/L 屑 手套 ers o th
1226
u vio Pre
s
al go
issue 塑胶框屑 B/L屑 B/L屑 手套屑
Root cause
Corrective action
PreveБайду номын сангаасtive action
owner
start
end
impact
寻找并验证真正原因: 要因分析) D4. 寻找并验证真正原因:(要因分析)
鉴别潜在原因: 4-1. 鉴别潜在原因: 一直询问『 WHY? A. 一直询问『 WHY?』→引进程序至找到真因为止 使用『特性要因图』 脑力激荡, B. 使用『特性要因图』作脑力激荡,找出各项潜在原因 如果问题是新的, C. 如果问题是新的,则限定时间找出各项潜在原因 选定可能的真正原因: 4-2. 选定可能的真正原因: 逐项测试→ A. 针对可能原因 → 逐项测试→数据分析 B. 验证各项真因 NO → 重回 4-1步驟 4-3. 判定真正原因 列出解決方案(PDCA) YES → 列出解決方案(PDCA) ※注:如果问题相当明确可直接进入4-3步骤 如果问题相当明确可直接进入4
用 途 说 明
计划的责任者? 计划的责任者? 计划的目的? 计划的目的? 计划的目标? 计划的目标? 计划的范围? 计划的范围? 计划的期限? 计划的期限? 计划的步骤? 计划的步骤? 计划的成本、效益? 计划的成本、效益?
5W1H原则 原则
措 施
目 的
说 明
何 事
代
号
WHAT ?
场 所
何 地
WHERE? WHERE?
什么问题? 什么问题?
2-3.使用合理的思考及统计工具来详细地描述问题。 3.使用合理的思考及统计工具来详细地描述问题。 使用合理的思考及统计工具来详细地描述问题 不可将故障现象 当成问题之原因说明。 将故障现象, 不可将故障现象,当成问题之原因说明。
发生地点? 发生地点? 发生时间? 发生时间? 问题大小、广度? 问题大小、广度?
8D的表單格式
8D實例
5W2H原则 原则
5W2H
WHO? WHO? WHY? WHY? WHAT? WHAT? WHERE? WHERE? WHEN? WHEN? HOW? HOW? Much? How Much?
符 号 意 义
谁负责? 谁负责? 为什么? 为什么? 做什么? 做什么? 在哪里? 在哪里? 在何时? 在何时? 怎么做? 怎么做? 多少钱? 多少钱?
替 换
可否“改变”作业流程或由同一人去操作? 可否“改变”作业流程或由同一人去操作?
简 化
经过重组后,前后相关作业是否更“简化” 经过重组后,前后相关作业是否更“简化” ?
1.CIP概念简介 1.CIP概念简介
C
Continuous
I
Improvement
P
Process
持续
改善
程序
chart简介及范例 2. 3 up chart简介及范例
……
Q&A:
1. CLCA与 CIP之间的联系与区别 2. 8D 与 3-up chart 的异同
长期改善对策
长期对策成效确认
防止重现 庆贺
8D问题处理图
成立团队: D1. 成立团队:( Team Work )
10人 1-1. 选定小组成员 4 -10人
a. 与该问题有关者 了解制程/ b. 了解制程/品质者 c. 对问题有经验者
1-2. 选定指导员 设定目标( 客户允许期限内完成) 1-3. 设定目标(须在客户允许期限内完成) 问题分配(问题调查/搜集数据→检讨) 1-4. 问题分配(问题调查/搜集数据→检讨)
WHO? ?
形式 时机
委员会 专案小组 生产过程改善小组
调查或建议 立即解决重大问题
修正生产过程、品质、 修正生产过程、品质、消除 浪费或提高跨部门生产率 品质改善小组 提供提高部门质量 或生产率的方法 实现企业目标
部门改进小组
团队工作小组
2.8D问题处理流程及描述 2.8D问题处理流程及描述
流程 成立小组 不良问题描述
简介
3-up chart
Failure trend chart
Bridge to goal
Action list
范例
2000
2500
250
2000 1500
1500 1000
1894
200 150 68
1000 500 0 Jan 塑膠框屑 其他 Feb B/L TRAY屑 goal Mar 手套屑
拟定行动计划, 拟定行动计划, 鉴别谁将于何时 做什么动作! 做什么动作!
与顾客/ 6-3. 与顾客/供应商会同验证解决方案
防止问题再度发生: D7. 防止问题再度发生: 系统化 制度化) (系统化、制度化)
视需要修正管理系统、操作系统及视需 7-1. 视需要修正管理系统、操作系统及视需 要修正管理系统 系统、 系统及作业程序, 要修正管理系统、操作 系统及作业程序,以防 止本问题及类似问题再发生 7-2. 协助管理人员了解为何系统会发生问题 制定新标准后, 7-3. 制定新标准后,视需要提供额外的训练
在一定时间内完全的解决一项问题处理程序; 一定时间内完全的解决一项问题处理程序; 完全的解决一项问题处理程序
必须以事实为基础解决问题的根源的一项标准规则。 必须以事实为基础解决问题的根源的一项标准规则。 以事实为基础解决问题的根源的一项标准规则
8D
用来作为问题解决时的沟通工具的报告格式。 用来作为问题解决时的沟通工具的报告格式。 沟通工具的报告格式
问题描述: 现况调查,目标明确化) D2. 问题描述:(现况调查,目标明确化)
2-1.参与人员必须对问题有相同定义及共识 1.参与人员必须对问题有相同定义及共识 2-2.指出内外部顾客问题所在 2.指出内外部顾客问题所在 5W2H为基础 A. 以5W2H为基础 5W1H和 应用5W1H 工作简化5原则获得新构想 B. 应用5W1H和工作简化5原则获得新构想
时 机 何 时
WHEN? WHEN?
人 物
何 人
WHO? WHO?
作 业
如 何
HOW? HOW?
工作简化5原则 工作简化 原则
问题
剔 除
代
号
流程图上操作与检验是否可以“剔除” ? 流程图上操作与检验是否可以“剔除”
合 并
某两种作业是否可以“合并”在一起? 某两种作业是否可以“合并”在一起?
重 组
是否“重组”操作或检验顺序能使作业更佳? 是否“重组”操作或检验顺序能使作业更佳?
经由生产试验计划定量确认必须考虑: 6-1. 经由生产试验计划定量确认必须考虑: A. 所选定之改正措施可以为顾客解决问题 B. 且不会引起不预期的坏影响 6-2. A. B. C. D. 验证的方法: 验证的方法: 实验室的测试 制造/ 制造/厂内指标 制造改变的SPC SPC表 制造改变的SPC表 报废率报告/ 报废率报告/符合性稽核
8D简介 1.CLCA & 8D简介
WHAT? ? CLCA——Close Loop Corrective Action 8D——Eight-Discipline
也称为TOPS (Team Oriented Problem Solving)
以团队为导向组成之专案小组,用于解决问题的八个步骤或八项准则; 团队为导向组成之专案小组,用于解决问题的八个步骤或八项准则; 组成之专案小组 步骤或八项准则
执行并验证紧急对策: 围堵措施) D3. 执行并验证紧急对策:(围堵措施)
将问题点产生的影响与内部/外部顾客隔离, 3-1. 将问题点产生的影响与内部/外部顾客隔离, 直到改正行动被执行为止 由执行暂时措施来减轻问题对顾客的影响: 3-2. 由执行暂时措施来减轻问题对顾客的影响: 出厂前100 筛选/检验/修补……) 100﹪ A. 出厂前100﹪筛选/检验/修补 ) B. 产品识别记号及位置 →告知顾客序号及管制 期限, 期限,随货附检测报告 3-3. 验证暂时措施的有效性 3-4. 要确保暂时措施可收到预期效果
八个步骤先后顺序可视问题之困难及复杂程度而异。 先后顺序可视问题之困难及复杂程度而异 八个步骤先后顺序可视问题之困难及复杂程度而异。