烧结节能降耗
烧结车间节能降耗心得体会
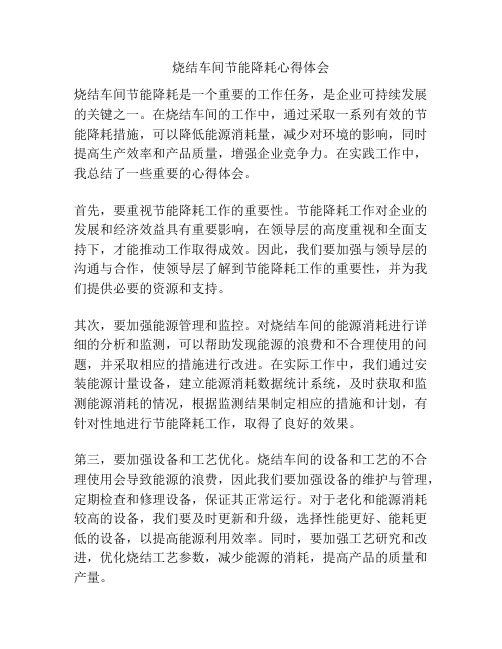
烧结车间节能降耗心得体会烧结车间节能降耗是一个重要的工作任务,是企业可持续发展的关键之一。
在烧结车间的工作中,通过采取一系列有效的节能降耗措施,可以降低能源消耗量,减少对环境的影响,同时提高生产效率和产品质量,增强企业竞争力。
在实践工作中,我总结了一些重要的心得体会。
首先,要重视节能降耗工作的重要性。
节能降耗工作对企业的发展和经济效益具有重要影响,在领导层的高度重视和全面支持下,才能推动工作取得成效。
因此,我们要加强与领导层的沟通与合作,使领导层了解到节能降耗工作的重要性,并为我们提供必要的资源和支持。
其次,要加强能源管理和监控。
对烧结车间的能源消耗进行详细的分析和监测,可以帮助发现能源的浪费和不合理使用的问题,并采取相应的措施进行改进。
在实际工作中,我们通过安装能源计量设备,建立能源消耗数据统计系统,及时获取和监测能源消耗的情况,根据监测结果制定相应的措施和计划,有针对性地进行节能降耗工作,取得了良好的效果。
第三,要加强设备和工艺优化。
烧结车间的设备和工艺的不合理使用会导致能源的浪费,因此我们要加强设备的维护与管理,定期检查和修理设备,保证其正常运行。
对于老化和能源消耗较高的设备,我们要及时更新和升级,选择性能更好、能耗更低的设备,以提高能源利用效率。
同时,要加强工艺研究和改进,优化烧结工艺参数,减少能源的消耗,提高产品的质量和产量。
第四,要加强人员培训和宣传教育。
人是企业的第一生产力,只有人员具备了节能降耗的相关知识和意识,才能更好地参与和推动工作。
我们要加强人员的培训,使其了解节能降耗的重要性和方法,并将其融入到工作中。
同时,要通过宣传和教育活动,提高全员的节能降耗意识,营造良好的节能降耗的氛围和环境。
最后,要加强经验交流和合作。
节能降耗工作是一个长期的过程,需要不断总结和完善。
我们要开展经验交流活动,邀请相关领域的专家和企业进行交流和分享,借鉴先进的经验和做法,使自身的工作不断提升和改进。
浅谈降低烧结工序能耗的措施
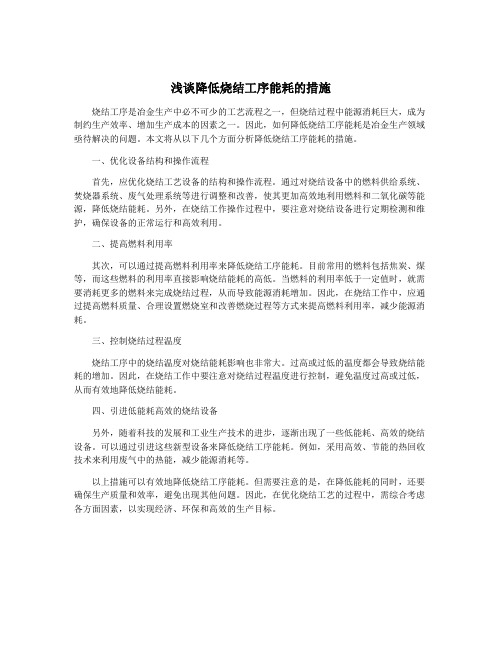
浅谈降低烧结工序能耗的措施烧结工序是冶金生产中必不可少的工艺流程之一,但烧结过程中能源消耗巨大,成为制约生产效率、增加生产成本的因素之一。
因此,如何降低烧结工序能耗是冶金生产领域亟待解决的问题。
本文将从以下几个方面分析降低烧结工序能耗的措施。
一、优化设备结构和操作流程首先,应优化烧结工艺设备的结构和操作流程。
通过对烧结设备中的燃料供给系统、焚烧器系统、废气处理系统等进行调整和改善,使其更加高效地利用燃料和二氧化碳等能源,降低烧结能耗。
另外,在烧结工作操作过程中,要注意对烧结设备进行定期检测和维护,确保设备的正常运行和高效利用。
二、提高燃料利用率其次,可以通过提高燃料利用率来降低烧结工序能耗。
目前常用的燃料包括焦炭、煤等,而这些燃料的利用率直接影响烧结能耗的高低。
当燃料的利用率低于一定值时,就需要消耗更多的燃料来完成烧结过程,从而导致能源消耗增加。
因此,在烧结工作中,应通过提高燃料质量、合理设置燃烧室和改善燃烧过程等方式来提高燃料利用率,减少能源消耗。
三、控制烧结过程温度烧结工序中的烧结温度对烧结能耗影响也非常大。
过高或过低的温度都会导致烧结能耗的增加。
因此,在烧结工作中要注意对烧结过程温度进行控制,避免温度过高或过低,从而有效地降低烧结能耗。
四、引进低能耗高效的烧结设备另外,随着科技的发展和工业生产技术的进步,逐渐出现了一些低能耗、高效的烧结设备。
可以通过引进这些新型设备来降低烧结工序能耗。
例如,采用高效、节能的热回收技术来利用废气中的热能,减少能源消耗等。
以上措施可以有效地降低烧结工序能耗。
但需要注意的是,在降低能耗的同时,还要确保生产质量和效率,避免出现其他问题。
因此,在优化烧结工艺的过程中,需综合考虑各方面因素,以实现经济、环保和高效的生产目标。
烧结降低点火煤气单耗的措施
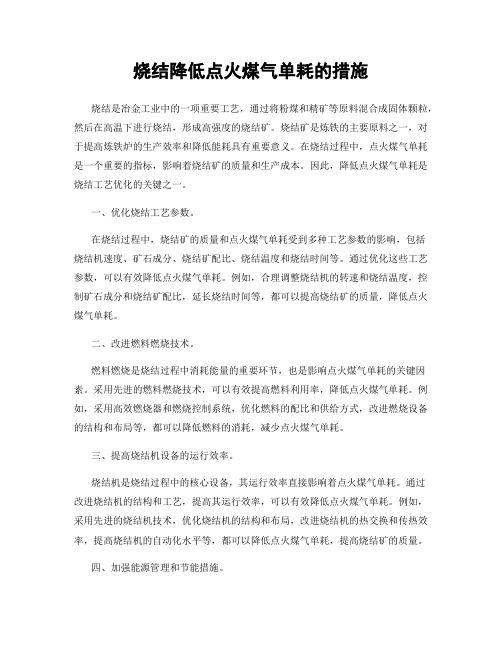
烧结降低点火煤气单耗的措施烧结是冶金工业中的一项重要工艺,通过将粉煤和精矿等原料混合成固体颗粒,然后在高温下进行烧结,形成高强度的烧结矿。
烧结矿是炼铁的主要原料之一,对于提高炼铁炉的生产效率和降低能耗具有重要意义。
在烧结过程中,点火煤气单耗是一个重要的指标,影响着烧结矿的质量和生产成本。
因此,降低点火煤气单耗是烧结工艺优化的关键之一。
一、优化烧结工艺参数。
在烧结过程中,烧结矿的质量和点火煤气单耗受到多种工艺参数的影响,包括烧结机速度、矿石成分、烧结矿配比、烧结温度和烧结时间等。
通过优化这些工艺参数,可以有效降低点火煤气单耗。
例如,合理调整烧结机的转速和烧结温度,控制矿石成分和烧结矿配比,延长烧结时间等,都可以提高烧结矿的质量,降低点火煤气单耗。
二、改进燃料燃烧技术。
燃料燃烧是烧结过程中消耗能量的重要环节,也是影响点火煤气单耗的关键因素。
采用先进的燃料燃烧技术,可以有效提高燃料利用率,降低点火煤气单耗。
例如,采用高效燃烧器和燃烧控制系统,优化燃料的配比和供给方式,改进燃烧设备的结构和布局等,都可以降低燃料的消耗,减少点火煤气单耗。
三、提高烧结机设备的运行效率。
烧结机是烧结过程中的核心设备,其运行效率直接影响着点火煤气单耗。
通过改进烧结机的结构和工艺,提高其运行效率,可以有效降低点火煤气单耗。
例如,采用先进的烧结机技术,优化烧结机的结构和布局,改进烧结机的热交换和传热效率,提高烧结机的自动化水平等,都可以降低点火煤气单耗,提高烧结矿的质量。
四、加强能源管理和节能措施。
能源管理和节能是降低点火煤气单耗的重要手段。
通过加强能源管理,优化能源结构,提高能源利用率,可以有效降低点火煤气单耗。
例如,采用高效节能设备,改进能源供应和利用系统,加强能源监测和控制,实施能源管理和节能政策等,都可以降低能耗,降低点火煤气单耗。
五、加强运行管理和技术培训。
运行管理和技术培训是保证烧结工艺稳定运行和降低点火煤气单耗的重要保障。
烧结机节能降耗措施

烧结机节能降耗措施在建筑材料、化工等行业中,烧结机是一种常用的设备,用于将粉状或粒状原料加热至一定温度后烘干、烧结成固体,制成块状产品。
然而,烧结机的运行过程中会产生大量的能源消耗和环境污染。
因此,烧结机节能降耗已经成为了当前行业中的一个重要问题。
本文将介绍烧结机节能降耗的几种措施。
1. 采用高效热交换技术烧结机内部的热量分布不均,导致了很大一部分热量的浪费。
此时,可以采用高效的热交换技术,将一部分废热收集起来,用于预热后续的原料,从而提高了热能的利用率。
例如,可以在烧结机的烟囱上安装烟囱热交换器,将烟气中的热量通过水的循环来直接回收利用。
另外,还可以在烧结机的废气出口处安装余热回收设备,将排放的热量再利用起来。
2. 降低热损失烧结机在运行过程中会产生大量的热损失,这也是造成能源浪费的重要因素。
因此,降低热损失是节能降耗的重要措施之一。
可以在烧结机的内部加装热防护材料,减少热量的散失,从而提高了热能的利用效率。
此外,还可以在烧结机的内部加装隔热板,减少热量的传导和散失,降低能源的消耗。
3. 优化燃料燃烧燃料燃烧是烧结机中能源消耗的主要来源之一。
因此,优化燃料燃烧也是节能降耗的重要措施。
可以采用合理的燃烧方式,如改善燃烧空气调节和混合方式,从而提高燃烧效率。
此外,还可以采用节能型的燃烧设备,例如采用带有预热功能的燃烧系统,利用废气回收设备对未燃烧的燃料进行再次燃烧,从而降低了能源的消耗。
4. 减少机械损失烧结机在运行过程中,机械损失也会导致能源消耗。
因此,减少机械损失也是节能降耗的重要措施。
可以采用精密的机件和材料,提高烧结机的精度和韧性。
此外,还可以加强运行维护和保养,定期检查和更换机件,避免机件的磨损和损坏,从而降低了运行时的能源消耗。
5. 提高运行效率在烧结机的运行过程中,提高运行效率也是一种节能降耗的重要措施。
可以采取以下方法:•加强设备的操作培训和技能提升,提高员工对设备的理解和操作技能;•采用自动化控制系统,利用先进技术对烧结机的运行进行监测和控制,提高了运行效率;•合理规划烧结机的生产计划,避免重复性操作和浪费。
探究降低烧结工艺能耗的措施
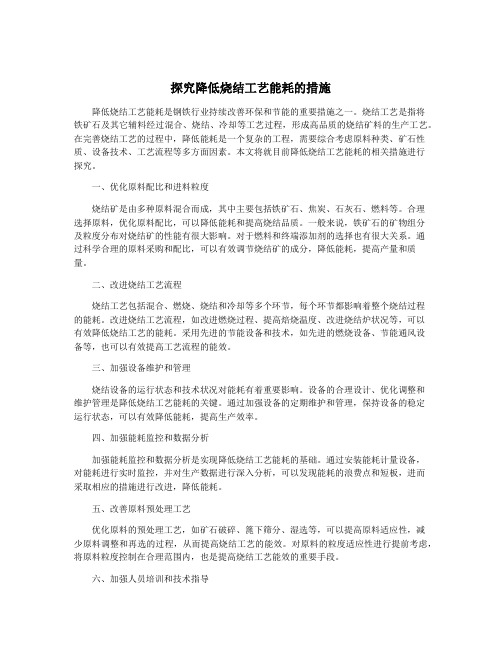
探究降低烧结工艺能耗的措施降低烧结工艺能耗是钢铁行业持续改善环保和节能的重要措施之一。
烧结工艺是指将铁矿石及其它辅料经过混合、烧结、冷却等工艺过程,形成高品质的烧结矿料的生产工艺。
在完善烧结工艺的过程中,降低能耗是一个复杂的工程,需要综合考虑原料种类、矿石性质、设备技术、工艺流程等多方面因素。
本文将就目前降低烧结工艺能耗的相关措施进行探究。
一、优化原料配比和进料粒度烧结矿是由多种原料混合而成,其中主要包括铁矿石、焦炭、石灰石、燃料等。
合理选择原料,优化原料配比,可以降低能耗和提高烧结品质。
一般来说,铁矿石的矿物组分及粒度分布对烧结矿的性能有很大影响。
对于燃料和终端添加剂的选择也有很大关系。
通过科学合理的原料采购和配比,可以有效调节烧结矿的成分,降低能耗,提高产量和质量。
二、改进烧结工艺流程烧结工艺包括混合、燃烧、烧结和冷却等多个环节,每个环节都影响着整个烧结过程的能耗。
改进烧结工艺流程,如改进燃烧过程、提高焙烧温度、改进烧结炉状况等,可以有效降低烧结工艺的能耗。
采用先进的节能设备和技术,如先进的燃烧设备、节能通风设备等,也可以有效提高工艺流程的能效。
三、加强设备维护和管理烧结设备的运行状态和技术状况对能耗有着重要影响。
设备的合理设计、优化调整和维护管理是降低烧结工艺能耗的关键。
通过加强设备的定期维护和管理,保持设备的稳定运行状态,可以有效降低能耗,提高生产效率。
四、加强能耗监控和数据分析加强能耗监控和数据分析是实现降低烧结工艺能耗的基础。
通过安装能耗计量设备,对能耗进行实时监控,并对生产数据进行深入分析,可以发现能耗的浪费点和短板,进而采取相应的措施进行改进,降低能耗。
五、改善原料预处理工艺优化原料的预处理工艺,如矿石破碎、篦下筛分、湿选等,可以提高原料适应性,减少原料调整和再选的过程,从而提高烧结工艺的能效。
对原料的粒度适应性进行提前考虑,将原料粒度控制在合理范围内,也是提高烧结工艺能效的重要手段。
浅谈降低烧结工序能耗的措施

浅谈降低烧结工序能耗的措施1. 引言1.1 烧结工序对能源消耗的重要性烧结工序是冶金工业重要的炼铁生产工序之一,其能源消耗对整个生产过程的能耗影响极为重要。
烧结工序主要是通过将铁矿石等原料在高温下加热,使其在烧结炉中发生一系列物理化学反应,最终形成高强度的铁制品。
烧结工序的能源消耗占据了整个冶金生产的重要比重,对于企业的生产成本和环境影响都具有重要的意义。
烧结工序所需能源包括燃料能源和电力能源,其中以燃料消耗较大。
在烧结工序中,煤炭、焦炭等燃料被用来提供高温热能,使原料得以烧结。
传统的烧结工序存在能源利用率低、排放浪费等问题,导致能源消耗较高。
降低烧结工序的能源消耗具有重要意义。
通过优化烧结工艺参数、采用先进的设备和技术、加强热能回收利用、提高烧结燃料的利用率以及应用节能技术等措施,可以有效降低烧结工序的能源消耗,提高生产效率,减少生产成本,实现可持续发展。
节能减排也是当前社会发展的重要趋势,降低烧结工序的能源消耗,不仅符合环保要求,也能提升企业的竞争力。
2. 正文2.1 优化烧结工艺参数优化烧结工艺参数是降低烧结工序能耗的重要措施之一。
通过调整烧结工艺中的各项参数,可以实现更高效的烧结过程,减少能源的消耗。
优化烧结工艺参数可以提高烧结的热效率。
合理调节烧结温度、烧结时间等参数,可以使烧结过程中的热能更加充分利用,减少能源的浪费。
优化参数还可以提高烧结矿的燃烧效率,减少燃料的使用量,降低能耗。
优化烧结工艺参数还可以改善产品质量。
通过精确控制烧结过程中的各项参数,可以确保产品的成分和性能达到要求,避免因为工艺参数不合理导致的质量问题,减少了产品的废品率,提高了资源利用率。
优化烧结工艺参数还可以减少设备运行时的能耗。
通过合理设置烧结设备的工作参数,有效控制能源的消耗,延长设备的使用寿命,减少了能源的浪费,降低了生产成本。
优化烧结工艺参数是降低烧结工序能耗的有效途径之一,可以提高烧结热效率,改善产品质量,减少设备能耗,从而实现节能减排的目标。
烧结降能耗具体方式分析
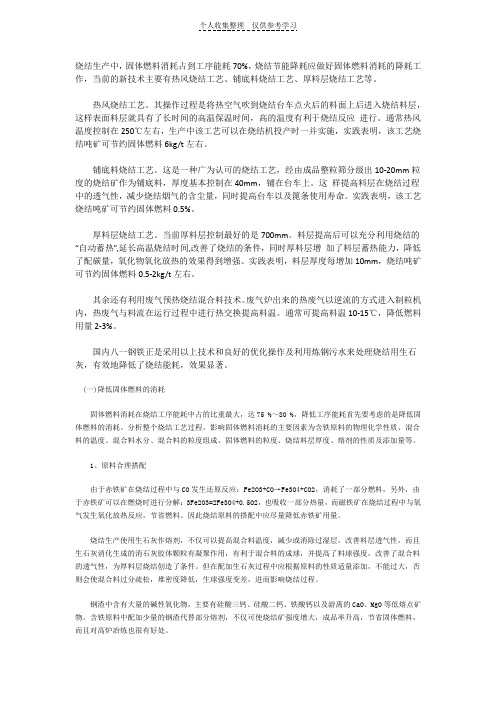
烧结生产中,固体燃料消耗占到工序能耗70%,烧结节能降耗应做好固体燃料消耗的降耗工作,当前的新技术主要有热风烧结工艺、铺底料烧结工艺、厚料层烧结工艺等。
热风烧结工艺。
其操作过程是将热空气吹到烧结台车点火后的料面上后进入烧结料层,这样表面料层就具有了长时间的高温保温时间,高的温度有利于烧结反应进行。
通常热风温度控制在250℃左右,生产中该工艺可以在烧结机投产时一并实施,实践表明,该工艺烧结吨矿可节约固体燃料6kg/t左右。
铺底料烧结工艺。
这是一种广为认可的烧结工艺,经由成品整粒筛分级出10-20mm粒度的烧结矿作为铺底料,厚度基本控制在40mm,铺在台车上。
这样提高料层在烧结过程中的透气性,减少烧结烟气的含尘量,同时提高台车以及篦条使用寿命。
实践表明,该工艺烧结吨矿可节约固体燃料0.5%。
厚料层烧结工艺。
当前厚料层控制最好的是700mm。
料层提高后可以充分利用烧结的“自动蓄热”,延长高温烧结时间,改善了烧结的条件,同时厚料层增加了料层蓄热能力,降低了配碳量,氧化物氧化放热的效果得到增强。
实践表明,料层厚度每增加10mm,烧结吨矿可节约固体燃料0.5-2kg/t左右。
其余还有利用废气预热烧结混合料技术。
废气炉出来的热废气以逆流的方式进入制粒机内,热废气与料流在运行过程中进行热交换提高料温。
通常可提高料温10-15℃,降低燃料用量2-3%。
国内八一钢铁正是采用以上技术和良好的优化操作及利用炼钢污水来处理烧结用生石灰,有效地降低了烧结能耗,效果显著。
(一)降低固体燃料的消耗固体燃料消耗在烧结工序能耗中占的比重最大,达75 %~80 %,降低工序能耗首先要考虑的是降低固体燃料的消耗。
分析整个烧结工艺过程,影响固体燃料消耗的主要因素为含铁原料的物理化学性质、混合料的温度、混合料水分、混合料的粒度组成、固体燃料的粒度、烧结料层厚度、熔剂的性质及添加量等。
1、原料合理搭配由于赤铁矿在烧结过程中与CO发生还原反应:Fe2O3+CO→Fe3O4+CO2,消耗了一部分燃料,另外,由于赤铁矿可以在燃烧时进行分解:3Fe2O3=2Fe3O4+0.5O2,也吸收一部分热量,而磁铁矿在烧结过程中与氧气发生氧化放热反应,节省燃料。
探究降低烧结工艺能耗的措施
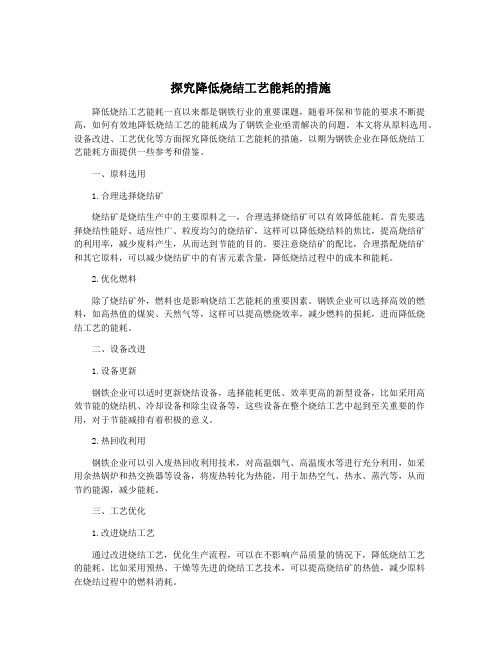
探究降低烧结工艺能耗的措施降低烧结工艺能耗一直以来都是钢铁行业的重要课题,随着环保和节能的要求不断提高,如何有效地降低烧结工艺的能耗成为了钢铁企业亟需解决的问题。
本文将从原料选用、设备改进、工艺优化等方面探究降低烧结工艺能耗的措施,以期为钢铁企业在降低烧结工艺能耗方面提供一些参考和借鉴。
一、原料选用1.合理选择烧结矿烧结矿是烧结生产中的主要原料之一,合理选择烧结矿可以有效降低能耗。
首先要选择烧结性能好、适应性广、粒度均匀的烧结矿,这样可以降低烧结料的焦比,提高烧结矿的利用率,减少废料产生,从而达到节能的目的。
要注意烧结矿的配比,合理搭配烧结矿和其它原料,可以减少烧结矿中的有害元素含量,降低烧结过程中的成本和能耗。
2.优化燃料除了烧结矿外,燃料也是影响烧结工艺能耗的重要因素。
钢铁企业可以选择高效的燃料,如高热值的煤炭、天然气等,这样可以提高燃烧效率,减少燃料的损耗,进而降低烧结工艺的能耗。
二、设备改进1.设备更新钢铁企业可以适时更新烧结设备,选择能耗更低、效率更高的新型设备,比如采用高效节能的烧结机、冷却设备和除尘设备等,这些设备在整个烧结工艺中起到至关重要的作用,对于节能减排有着积极的意义。
2.热回收利用钢铁企业可以引入废热回收利用技术,对高温烟气、高温废水等进行充分利用,如采用余热锅炉和热交换器等设备,将废热转化为热能,用于加热空气、热水、蒸汽等,从而节约能源,减少能耗。
三、工艺优化1.改进烧结工艺通过改进烧结工艺,优化生产流程,可以在不影响产品质量的情况下,降低烧结工艺的能耗。
比如采用预热、干燥等先进的烧结工艺技术,可以提高烧结矿的热值,减少原料在烧结过程中的燃料消耗。
2.控制炉温合理控制烧结炉的温度是降低烧结工艺能耗的关键。
通过优化燃烧工艺、合理设置冷却系统等措施,可以控制烧结炉的温度,避免能量的过度消耗,从而降低烧结工艺的能耗。
以上就是关于降低烧结工艺能耗的措施的一些探讨和建议,希望对于钢铁企业在降低烧结工艺能耗方面有所帮助。
浅谈降低烧结工序能耗的措施

浅谈降低烧结工序能耗的措施
烧结是粉煤灰等煤屑燃烧后生成的产物,具有一定的热值和热能,因此在其烧结过程中能耗较高。
为了降低烧结工序的能耗,需要采取以下措施:
1. 优化燃料选择和使用:燃料的选择和使用在烧结过程中起着重要作用。
合理选择和使用高热值、低硫、低灰分的燃料,以减少燃料消耗,降低烟气排放,提高烧结效率。
2. 热能回收利用:在烧结过程中,热能可以通过余热锅炉等方式回收利用,以减少能量损失,提高能源利用率。
3. 优化烧结过程控制参数:通过优化烧结温度、温度梯度、气体流速等控制参数,可以提高烧结质量,降低能耗。
4. 选用高效节能设备:采用高效节能设备,如高效烧结机、省电烘干设备等,可以有效降低能耗,提高工艺效率和产品质量。
5. 建立能源管理体系:建立能源管理体系,对能源消耗进行监测和管理,对关键环节进行能耗分析和优化,制定科学合理的能源管理措施,可以有效降低烧结工序的能耗。
综上所述,通过优化燃料选择和使用、热能回收利用、优化烧结过程控制参数、选用高效节能设备以及建立能源管理体系等措施,可以有效降低烧结工序的能耗,提高能源利用效率和企业经济效益。
浅谈烧结节能降耗的技术途径和措施
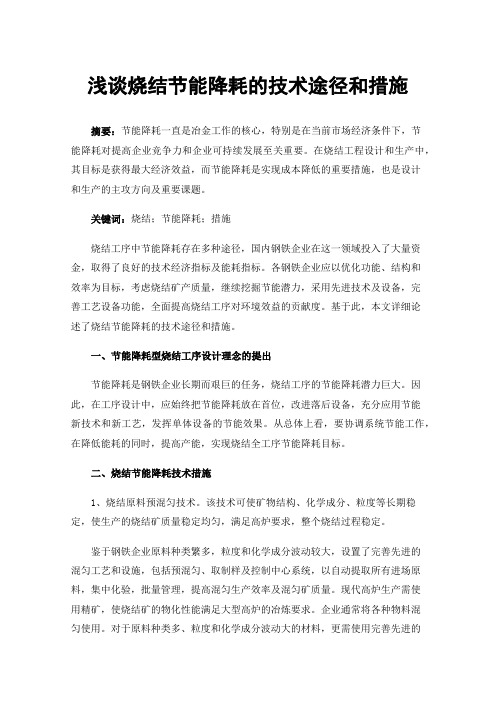
浅谈烧结节能降耗的技术途径和措施摘要:节能降耗一直是冶金工作的核心,特别是在当前市场经济条件下,节能降耗对提高企业竞争力和企业可持续发展至关重要。
在烧结工程设计和生产中,其目标是获得最大经济效益,而节能降耗是实现成本降低的重要措施,也是设计和生产的主攻方向及重要课题。
关键词:烧结;节能降耗;措施烧结工序中节能降耗存在多种途径,国内钢铁企业在这一领域投入了大量资金,取得了良好的技术经济指标及能耗指标。
各钢铁企业应以优化功能、结构和效率为目标,考虑烧结矿产质量,继续挖掘节能潜力,采用先进技术及设备,完善工艺设备功能,全面提高烧结工序对环境效益的贡献度。
基于此,本文详细论述了烧结节能降耗的技术途径和措施。
一、节能降耗型烧结工序设计理念的提出节能降耗是钢铁企业长期而艰巨的任务,烧结工序的节能降耗潜力巨大。
因此,在工序设计中,应始终把节能降耗放在首位,改进落后设备,充分应用节能新技术和新工艺,发挥单体设备的节能效果。
从总体上看,要协调系统节能工作,在降低能耗的同时,提高产能,实现烧结全工序节能降耗目标。
二、烧结节能降耗技术措施1、烧结原料预混匀技术。
该技术可使矿物结构、化学成分、粒度等长期稳定,使生产的烧结矿质量稳定均匀,满足高炉要求,整个烧结过程稳定。
鉴于钢铁企业原料种类繁多,粒度和化学成分波动较大,设置了完善先进的混匀工艺和设施,包括预混匀、取制样及控制中心系统,以自动提取所有进场原料,集中化验,批量管理,提高混匀生产效率及混匀矿质量。
现代高炉生产需使用精矿,使烧结矿的物化性能满足大型高炉的冶炼要求。
企业通常将各种物料混匀使用。
对于原料种类多、粒度和化学成分波动大的材料,更需使用完善先进的混匀工艺和设施作为技术支持,通过自动制样系统,对所有进场原料进行自动取料及集中化验,并根据不同品种、成分和定量进行堆放,实现原料的批次管理。
2、超厚料层烧结自动蓄热技术。
在烧结工艺中,蓄热量会随着料层厚度的不断增加而逐渐积累,当厚度达到180~220mm时,蓄热率为35~45%,厚度为400mm,蓄热率可达65%。
烧结厂降低固体燃耗的研究与实践

烧结厂降低固体燃耗的研究与实践
烧结厂是钢铁生产过程中不可或缺的重要环节,但同时也是一个能源消耗量较大的环节。
其中固体燃料是烧结过程中能源消耗的主要来源。
因此,降低固体燃料的消耗量,是烧结厂节能减排的重要措施。
以下是烧结厂降低固体燃耗的研究与实践:
1.提高烧结热效率。
对于烧结工艺中的热能损失,可以通过提高烧结热效率来减少固体燃耗。
其中一种有效的方法是采用先进的热交换技术,将热能回收用于制热或发电。
2.优化烧结原料。
烧结原料中的品位高低、组成结构等因素都会影响其热值,因此在烧结原料的选择和配比方面,可以优化烧结原料的组成和品位,从而减少固体燃料的消耗量。
3.制定科学的烧结参数。
在烧结过程中,通过调节烧结参数来控制烧结过程中的不同阶段,可以减少固体燃料的消耗。
例如,在烧结的初期阶段,通过增加还原气体的流量,可以提高还原反应的速率和效率,从而减少固体燃料的消耗。
4.加强热工装备的维护和改造。
在烧结厂的热工装备中,存在一定的能源浪费或能源利用不充分的情况。
例如,在热风炉的运行中,热能的回收利用率不高,通过加强热工装备的维护和改造,可以提高热能的利用率,从而减少固体燃料的消耗。
综上所述,烧结厂的固体燃料消耗问题,需要采取多方面的措施来解决。
随着技术的进步和工艺的不断完善,相信在未来,烧结厂的能耗将实现更加高效、节能和环保的目标。
浅谈降低烧结工序能耗的措施
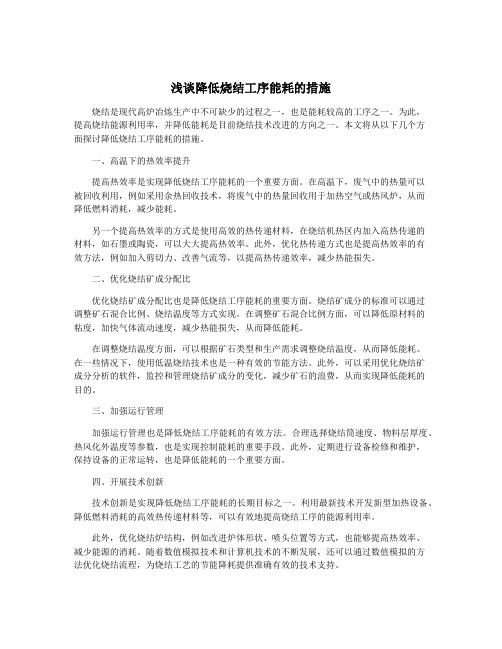
浅谈降低烧结工序能耗的措施烧结是现代高炉冶炼生产中不可缺少的过程之一,也是能耗较高的工序之一。
为此,提高烧结能源利用率,并降低能耗是目前烧结技术改进的方向之一。
本文将从以下几个方面探讨降低烧结工序能耗的措施。
一、高温下的热效率提升提高热效率是实现降低烧结工序能耗的一个重要方面。
在高温下,废气中的热量可以被回收利用,例如采用余热回收技术,将废气中的热量回收用于加热空气或热风炉,从而降低燃料消耗,减少能耗。
另一个提高热效率的方式是使用高效的热传递材料,在烧结机热区内加入高热传递的材料,如石墨或陶瓷,可以大大提高热效率。
此外,优化热传递方式也是提高热效率的有效方法,例如加入剪切力、改善气流等,以提高热传递效率,减少热能损失。
二、优化烧结矿成分配比优化烧结矿成分配比也是降低烧结工序能耗的重要方面。
烧结矿成分的标准可以通过调整矿石混合比例、烧结温度等方式实现。
在调整矿石混合比例方面,可以降低原材料的粘度,加快气体流动速度,减少热能损失,从而降低能耗。
在调整烧结温度方面,可以根据矿石类型和生产需求调整烧结温度,从而降低能耗。
在一些情况下,使用低温烧结技术也是一种有效的节能方法。
此外,可以采用优化烧结矿成分分析的软件,监控和管理烧结矿成分的变化,减少矿石的浪费,从而实现降低能耗的目的。
三、加强运行管理加强运行管理也是降低烧结工序能耗的有效方法。
合理选择烧结筒速度、物料层厚度、热风化外温度等参数,也是实现控制能耗的重要手段。
此外,定期进行设备检修和维护,保持设备的正常运转,也是降低能耗的一个重要方面。
四、开展技术创新技术创新是实现降低烧结工序能耗的长期目标之一。
利用最新技术开发新型加热设备、降低燃料消耗的高效热传递材料等,可以有效地提高烧结工序的能源利用率。
此外,优化烧结炉结构,例如改进炉体形状、喷头位置等方式,也能够提高热效率、减少能源的消耗。
随着数值模拟技术和计算机技术的不断发展,还可以通过数值模拟的方法优化烧结流程,为烧结工艺的节能降耗提供准确有效的技术支持。
浅谈降低烧结工序能耗的措施
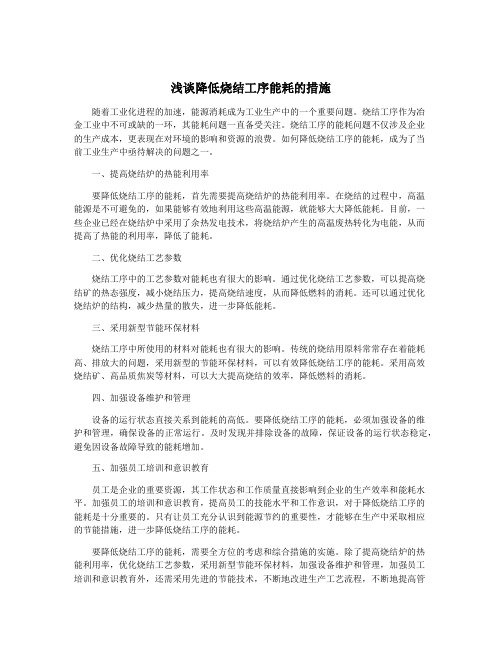
浅谈降低烧结工序能耗的措施随着工业化进程的加速,能源消耗成为工业生产中的一个重要问题。
烧结工序作为冶金工业中不可或缺的一环,其能耗问题一直备受关注。
烧结工序的能耗问题不仅涉及企业的生产成本,更表现在对环境的影响和资源的浪费。
如何降低烧结工序的能耗,成为了当前工业生产中亟待解决的问题之一。
一、提高烧结炉的热能利用率要降低烧结工序的能耗,首先需要提高烧结炉的热能利用率。
在烧结的过程中,高温能源是不可避免的,如果能够有效地利用这些高温能源,就能够大大降低能耗。
目前,一些企业已经在烧结炉中采用了余热发电技术,将烧结炉产生的高温废热转化为电能,从而提高了热能的利用率,降低了能耗。
二、优化烧结工艺参数烧结工序中的工艺参数对能耗也有很大的影响。
通过优化烧结工艺参数,可以提高烧结矿的热态强度,减小烧结压力,提高烧结速度,从而降低燃料的消耗。
还可以通过优化烧结炉的结构,减少热量的散失,进一步降低能耗。
三、采用新型节能环保材料烧结工序中所使用的材料对能耗也有很大的影响。
传统的烧结用原料常常存在着能耗高、排放大的问题,采用新型的节能环保材料,可以有效降低烧结工序的能耗。
采用高效烧结矿、高品质焦炭等材料,可以大大提高烧结的效率,降低燃料的消耗。
四、加强设备维护和管理设备的运行状态直接关系到能耗的高低。
要降低烧结工序的能耗,必须加强设备的维护和管理,确保设备的正常运行。
及时发现并排除设备的故障,保证设备的运行状态稳定,避免因设备故障导致的能耗增加。
五、加强员工培训和意识教育员工是企业的重要资源,其工作状态和工作质量直接影响到企业的生产效率和能耗水平。
加强员工的培训和意识教育,提高员工的技能水平和工作意识,对于降低烧结工序的能耗是十分重要的。
只有让员工充分认识到能源节约的重要性,才能够在生产中采取相应的节能措施,进一步降低烧结工序的能耗。
要降低烧结工序的能耗,需要全方位的考虑和综合措施的实施。
除了提高烧结炉的热能利用率,优化烧结工艺参数,采用新型节能环保材料,加强设备维护和管理,加强员工培训和意识教育外,还需采用先进的节能技术,不断地改进生产工艺流程,不断地提高管理水平,从而才能够全面降低烧结工序的能耗,实现可持续发展的目标。
浅谈降低烧结工序能耗的措施
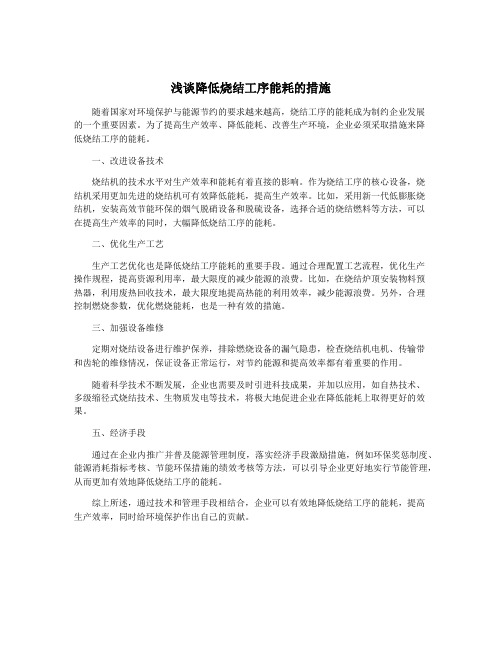
浅谈降低烧结工序能耗的措施随着国家对环境保护与能源节约的要求越来越高,烧结工序的能耗成为制约企业发展的一个重要因素。
为了提高生产效率、降低能耗、改善生产环境,企业必须采取措施来降低烧结工序的能耗。
一、改进设备技术烧结机的技术水平对生产效率和能耗有着直接的影响。
作为烧结工序的核心设备,烧结机采用更加先进的烧结机可有效降低能耗,提高生产效率。
比如,采用新一代低膨胀烧结机,安装高效节能环保的烟气脱硝设备和脱硫设备,选择合适的烧结燃料等方法,可以在提高生产效率的同时,大幅降低烧结工序的能耗。
二、优化生产工艺生产工艺优化也是降低烧结工序能耗的重要手段。
通过合理配置工艺流程,优化生产操作规程,提高资源利用率,最大限度的减少能源的浪费。
比如,在烧结炉顶安装物料预热器,利用废热回收技术,最大限度地提高热能的利用效率,减少能源浪费。
另外,合理控制燃烧参数,优化燃烧能耗,也是一种有效的措施。
三、加强设备维修定期对烧结设备进行维护保养,排除燃烧设备的漏气隐患,检查烧结机电机、传输带和齿轮的维修情况,保证设备正常运行,对节约能源和提高效率都有着重要的作用。
随着科学技术不断发展,企业也需要及时引进科技成果,并加以应用,如自热技术、多级缩径式烧结技术、生物质发电等技术,将极大地促进企业在降低能耗上取得更好的效果。
五、经济手段通过在企业内推广并普及能源管理制度,落实经济手段激励措施,例如环保奖惩制度、能源消耗指标考核、节能环保措施的绩效考核等方法,可以引导企业更好地实行节能管理,从而更加有效地降低烧结工序的能耗。
综上所述,通过技术和管理手段相结合,企业可以有效地降低烧结工序的能耗,提高生产效率,同时给环境保护作出自己的贡献。
浅谈降低烧结工序能耗的措施
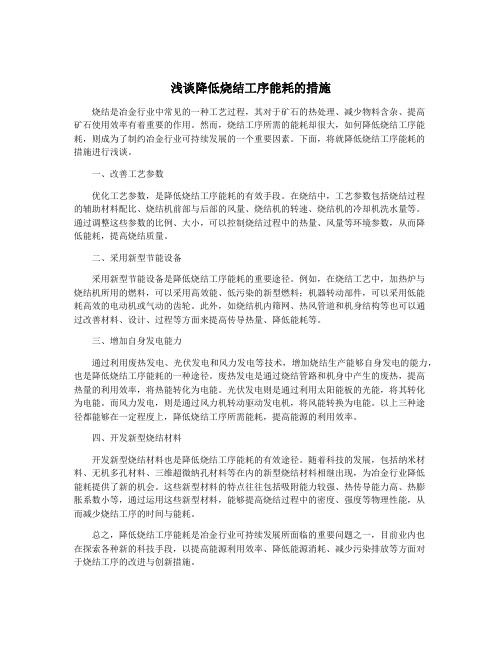
浅谈降低烧结工序能耗的措施烧结是冶金行业中常见的一种工艺过程,其对于矿石的热处理、减少物料含杂、提高矿石使用效率有着重要的作用。
然而,烧结工序所需的能耗却很大,如何降低烧结工序能耗,则成为了制约冶金行业可持续发展的一个重要因素。
下面,将就降低烧结工序能耗的措施进行浅谈。
一、改善工艺参数优化工艺参数,是降低烧结工序能耗的有效手段。
在烧结中,工艺参数包括烧结过程的辅助材料配比、烧结机前部与后部的风量、烧结机的转速、烧结机的冷却机洗水量等。
通过调整这些参数的比例、大小,可以控制烧结过程中的热量、风量等环境参数,从而降低能耗,提高烧结质量。
二、采用新型节能设备采用新型节能设备是降低烧结工序能耗的重要途径。
例如,在烧结工艺中,加热炉与烧结机所用的燃料,可以采用高效能、低污染的新型燃料;机器转动部件,可以采用低能耗高效的电动机或气动的齿轮。
此外,如烧结机内筛网、热风管道和机身结构等也可以通过改善材料、设计、过程等方面来提高传导热量、降低能耗等。
三、增加自身发电能力通过利用废热发电、光伏发电和风力发电等技术,增加烧结生产能够自身发电的能力,也是降低烧结工序能耗的一种途径。
废热发电是通过烧结管路和机身中产生的废热,提高热量的利用效率,将热能转化为电能。
光伏发电则是通过利用太阳能板的光能,将其转化为电能。
而风力发电,则是通过风力机转动驱动发电机,将风能转换为电能。
以上三种途径都能够在一定程度上,降低烧结工序所需能耗,提高能源的利用效率。
四、开发新型烧结材料开发新型烧结材料也是降低烧结工序能耗的有效途径。
随着科技的发展,包括纳米材料、无机多孔材料、三维超微纳孔材料等在内的新型烧结材料相继出现,为冶金行业降低能耗提供了新的机会。
这些新型材料的特点往往包括吸附能力较强、热传导能力高、热膨胀系数小等,通过运用这些新型材料,能够提高烧结过程中的密度、强度等物理性能,从而减少烧结工序的时间与能耗。
总之,降低烧结工序能耗是冶金行业可持续发展所面临的重要问题之一,目前业内也在探索各种新的科技手段,以提高能源利用效率、降低能源消耗、减少污染排放等方面对于烧结工序的改进与创新措施。
探究降低烧结工艺能耗的措施

探究降低烧结工艺能耗的措施降低烧结工艺能耗一直是炼铁行业的重要课题之一。
烧结是指将粉煤灰和水泥等材料混合后,在高温条件下烧结成不同尺寸的块状颗粒,烧结技术在炼铁生产中占有重要地位。
烧结工艺能耗一直是制约烧结生产的一个重要因素,如何降低烧结工艺能耗一直是炼铁企业和科研人员们关注的焦点。
本文将探讨降低烧结工艺能耗的相关措施。
对于烧结工艺能耗的控制,需要从原材料的选择上做文章。
优化原料的配比,选择合适的矿石和助熔剂,可以降低烧结过程中的能耗。
对原料的粒度和配比进行合理的控制,可以提高烧结矿的透气性和块度,从而减少烧结矿在料层中的堵塞现象,降低烧结工艺的能耗。
烧结工艺中的燃料选择也对能耗有着重要的影响。
燃料的选择直接关系到整个烧结工艺的燃烧效率和烧结品质。
采用高效率的清洁能源代替传统的燃煤烧结,如采用天然气、生物质燃料等清洁能源,可以有效降低烧结工艺的能耗,同时减少对环境的污染。
控制烧结过程中的热能流失也是降低能耗的重要措施之一。
通过合理的烧结炉结构设计和热力系统优化,降低烧结工艺中热能的散失,提高热能的利用效率,可以有效降低烧结工艺的能耗。
采用先进的节能技术也是降低烧结工艺能耗的重要手段。
采用高效热交换设备、节能型热风炉、集中控制系统等节能设备,可以有效地降低烧结工艺的能耗。
采用先进的自动化控制系统,实现烧结工艺的智能化管理,提高生产效率,减少能耗。
降低烧结工艺的能耗是炼铁企业和科研人员们一直在探讨和研究的课题,通过优化原料选择、合理控制燃料选择、控制热能流失和采用先进的节能技术等措施,可以有效地降低烧结工艺的能耗,提高企业的经济效益和环保效益。
希望未来炼铁行业能够在降低烧结工艺能耗方面取得更多的创新突破,为绿色炼铁产业的发展做出更大的贡献。
探究降低烧结工艺能耗的措施
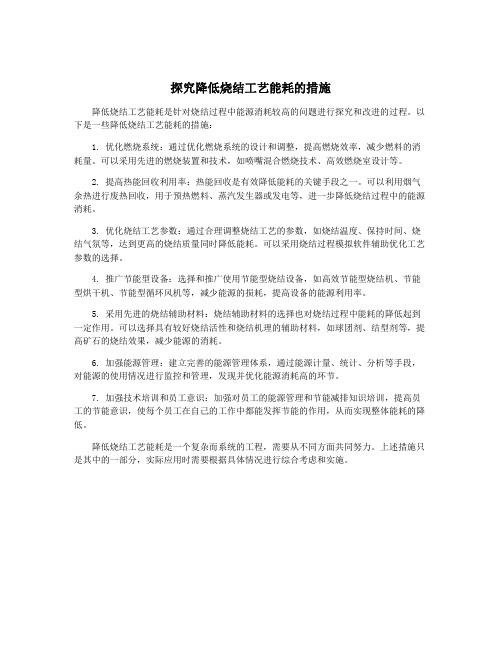
探究降低烧结工艺能耗的措施
降低烧结工艺能耗是针对烧结过程中能源消耗较高的问题进行探究和改进的过程。
以下是一些降低烧结工艺能耗的措施:
1. 优化燃烧系统:通过优化燃烧系统的设计和调整,提高燃烧效率,减少燃料的消耗量。
可以采用先进的燃烧装置和技术,如喷嘴混合燃烧技术、高效燃烧室设计等。
2. 提高热能回收利用率:热能回收是有效降低能耗的关键手段之一。
可以利用烟气余热进行废热回收,用于预热燃料、蒸汽发生器或发电等,进一步降低烧结过程中的能源消耗。
3. 优化烧结工艺参数:通过合理调整烧结工艺的参数,如烧结温度、保持时间、烧结气氛等,达到更高的烧结质量同时降低能耗。
可以采用烧结过程模拟软件辅助优化工艺参数的选择。
4. 推广节能型设备:选择和推广使用节能型烧结设备,如高效节能型烧结机、节能型烘干机、节能型循环风机等,减少能源的损耗,提高设备的能源利用率。
5. 采用先进的烧结辅助材料:烧结辅助材料的选择也对烧结过程中能耗的降低起到一定作用。
可以选择具有较好烧结活性和烧结机理的辅助材料,如球团剂、结型剂等,提高矿石的烧结效果,减少能源的消耗。
6. 加强能源管理:建立完善的能源管理体系,通过能源计量、统计、分析等手段,对能源的使用情况进行监控和管理,发现并优化能源消耗高的环节。
7. 加强技术培训和员工意识:加强对员工的能源管理和节能减排知识培训,提高员工的节能意识,使每个员工在自己的工作中都能发挥节能的作用,从而实现整体能耗的降低。
降低烧结工艺能耗是一个复杂而系统的工程,需要从不同方面共同努力。
上述措施只是其中的一部分,实际应用时需要根据具体情况进行综合考虑和实施。
烧结工序节能降耗的技术措施
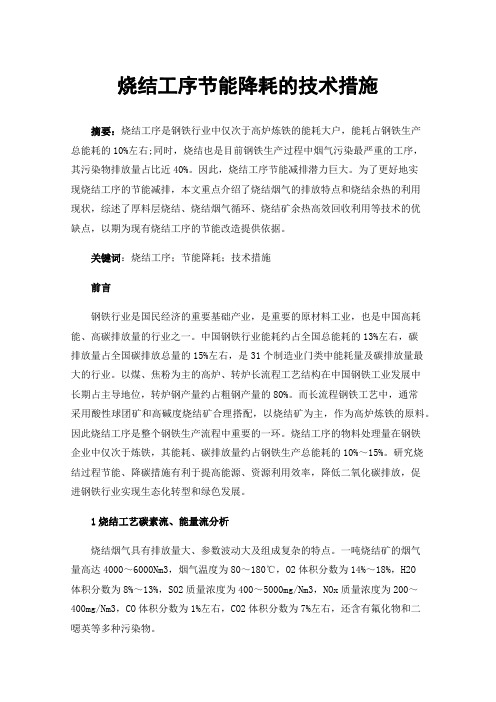
烧结工序节能降耗的技术措施摘要:烧结工序是钢铁行业中仅次于高炉炼铁的能耗大户,能耗占钢铁生产总能耗的10%左右;同时,烧结也是目前钢铁生产过程中烟气污染最严重的工序,其污染物排放量占比近40%。
因此,烧结工序节能减排潜力巨大。
为了更好地实现烧结工序的节能减排,本文重点介绍了烧结烟气的排放特点和烧结余热的利用现状,综述了厚料层烧结、烧结烟气循环、烧结矿余热高效回收利用等技术的优缺点,以期为现有烧结工序的节能改造提供依据。
关键词:烧结工序;节能降耗;技术措施前言钢铁行业是国民经济的重要基础产业,是重要的原材料工业,也是中国高耗能、高碳排放量的行业之一。
中国钢铁行业能耗约占全国总能耗的13%左右,碳排放量占全国碳排放总量的15%左右,是31个制造业门类中能耗量及碳排放量最大的行业。
以煤、焦粉为主的高炉、转炉长流程工艺结构在中国钢铁工业发展中长期占主导地位,转炉钢产量约占粗钢产量的80%。
而长流程钢铁工艺中,通常采用酸性球团矿和高碱度烧结矿合理搭配,以烧结矿为主,作为高炉炼铁的原料。
因此烧结工序是整个钢铁生产流程中重要的一环。
烧结工序的物料处理量在钢铁企业中仅次于炼铁,其能耗、碳排放量约占钢铁生产总能耗的10%~15%。
研究烧结过程节能、降碳措施有利于提高能源、资源利用效率,降低二氧化碳排放,促进钢铁行业实现生态化转型和绿色发展。
1烧结工艺碳素流、能量流分析烧结烟气具有排放量大、参数波动大及组成复杂的特点。
一吨烧结矿的烟气量高达4000~6000Nm3,烟气温度为80~180℃,O2体积分数为14%~18%,H2O体积分数为8%~13%,SO2质量浓度为400~5000mg/Nm3,NOx质量浓度为200~400mg/Nm3,CO体积分数为1%左右,CO2体积分数为7%左右,还含有氟化物和二噁英等多种污染物。
1.1烧结工艺主要功能烧结的生产过程是把精矿粉、燃料(焦粉、无烟煤)和熔剂(石灰石、白云石、生石灰)按一定比例配料混匀后,在烧结机上点火燃烧,利用燃料和铁氧化物氧化反应放出热量,使混合料局部熔化,并将散粒颗粒黏结成块状烧结矿,作为炼铁原料。
超厚料层烧结降耗减碳技术
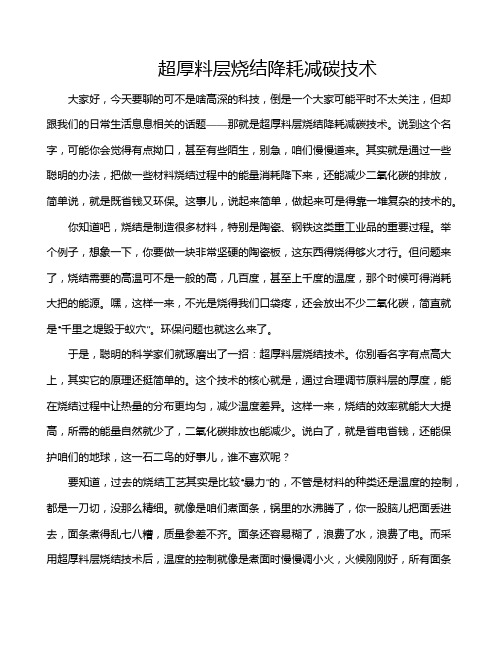
超厚料层烧结降耗减碳技术大家好,今天要聊的可不是啥高深的科技,倒是一个大家可能平时不太关注,但却跟我们的日常生活息息相关的话题——那就是超厚料层烧结降耗减碳技术。
说到这个名字,可能你会觉得有点拗口,甚至有些陌生,别急,咱们慢慢道来。
其实就是通过一些聪明的办法,把做一些材料烧结过程中的能量消耗降下来,还能减少二氧化碳的排放,简单说,就是既省钱又环保。
这事儿,说起来简单,做起来可是得靠一堆复杂的技术的。
你知道吧,烧结是制造很多材料,特别是陶瓷、钢铁这类重工业品的重要过程。
举个例子,想象一下,你要做一块非常坚硬的陶瓷板,这东西得烧得够火才行。
但问题来了,烧结需要的高温可不是一般的高,几百度,甚至上千度的温度,那个时候可得消耗大把的能源。
嘿,这样一来,不光是烧得我们口袋疼,还会放出不少二氧化碳,简直就是“千里之堤毁于蚁穴”。
环保问题也就这么来了。
于是,聪明的科学家们就琢磨出了一招:超厚料层烧结技术。
你别看名字有点高大上,其实它的原理还挺简单的。
这个技术的核心就是,通过合理调节原料层的厚度,能在烧结过程中让热量的分布更均匀,减少温度差异。
这样一来,烧结的效率就能大大提高,所需的能量自然就少了,二氧化碳排放也能减少。
说白了,就是省电省钱,还能保护咱们的地球,这一石二鸟的好事儿,谁不喜欢呢?要知道,过去的烧结工艺其实是比较“暴力”的,不管是材料的种类还是温度的控制,都是一刀切,没那么精细。
就像是咱们煮面条,锅里的水沸腾了,你一股脑儿把面丢进去,面条煮得乱七八糟,质量参差不齐。
面条还容易糊了,浪费了水,浪费了电。
而采用超厚料层烧结技术后,温度的控制就像是煮面时慢慢调小火,火候刚刚好,所有面条都煮得恰到好处,不仅省了能源,还能保证每一根面条都劲道十足。
看似简单,其实是经过了无数次的实验和调整,才有了现在的成果。
再说了,大家应该也知道,现在环保问题越来越严峻,特别是碳排放这一块,简直是全球范围的大难题。
很多国家都在喊着“碳中和”的口号,纷纷开始推动各行各业减排二氧化碳。
- 1、下载文档前请自行甄别文档内容的完整性,平台不提供额外的编辑、内容补充、找答案等附加服务。
- 2、"仅部分预览"的文档,不可在线预览部分如存在完整性等问题,可反馈申请退款(可完整预览的文档不适用该条件!)。
- 3、如文档侵犯您的权益,请联系客服反馈,我们会尽快为您处理(人工客服工作时间:9:00-18:30)。
降低烧结工序能耗的措施(一)降低固体燃料的消耗固体燃料消耗在烧结工序能耗中占的比重最大,达75 %~80 %,降低工序能耗首先要考虑的是降低固体燃料的消耗。
分析整个烧结工艺过程,影响固体燃料消耗的主要因素为含铁原料的物理化学性质、混合料的温度、混合料水分、混合料的粒度组成、固体燃料的粒度、烧结料层厚度、熔剂的性质及添加量等。
1、原料合理搭配由于赤铁矿在烧结过程中与CO发生还原反应:Fe2O3+CO→Fe3O4+CO2,消耗了一部分燃料,另外,由于赤铁矿可以在燃烧时进行分解:3Fe2O3=2Fe3O4+0.5O2,也吸收一部分热量,而磁铁矿在烧结过程中与氧气发生氧化放热反应,节省燃料。
因此烧结原料的搭配中应尽量降低赤铁矿用量。
烧结生产使用生石灰作熔剂,不仅可以提高混合料温度,减少或消除过湿层,改善料层透气性,而且生石灰消化生成的消石灰胶体颗粒有凝聚作用,有利于混合料的成球,并提高了料球强度,改善了混合料的透气性,为厚料层烧结创造了条件。
但在配加生石灰过程中应根据原料的性质适量添加,不能过大,否则会使混合料过分疏松,堆密度降低,生球强度变差,进而影响烧结过程。
钢渣中含有大量的碱性氧化物,主要有硅酸三钙、硅酸二钙、铁酸钙以及游离的CaO、MgO 等低熔点矿物。
含铁原料中配加少量的钢渣代替部分熔剂,不仅可使烧结矿强度增大,成品率升高,节省固体燃料,而且对高炉冶炼也很有好处。
轧一烧结厂目前所用的含铁原料以河北精矿为主,配加少量澳矿、印度矿、巴西矿、墨西哥矿、高炉返矿、筛下自返矿,另外还配加少量炼钢红泥。
熔剂大部分采用生石灰、高镁灰、石灰石。
2、控制燃料粒度及粒度组成烧结所用固体燃料的粒度与混合料的特性有关,一般应由实验确定。
但实验室和实际生产都证明了在精矿烧结时,固体燃料的最好粒度范围是0.5~3 mm,大于3 mm和小于0.5 mm粒级的存在都是不希望的,这部分粒级含量的增加均会使固体燃耗增加,烧结矿成品率降低。
设法控制固体燃料的粒度及组成是所有的烧结厂为高产、优质、低耗而应采取的一项重要措施。
3、提高混合料温度(1)当烧结混合料温度较低时,水汽在料层中冷凝,形成过湿现象,使烧结料层透气性变坏。
提高混合料的温度,使其达到露点以上,可以显著减少或消除水汽在料层中的冷凝量,降低过湿层对气流的阻力,从而改善了料层透气性,使抽过料层的空气量增加,为料层内的热交换创造了良好的条件,燃烧速度加快,提高台时产量,节约固体燃料。
(2)提高混合料温度的措施主要有:生石灰预热、热水预热、热返矿预热、蒸汽预热及烧结废气预热等。
(3)另外使用生石灰作为强化烧结与节能的重要措施,并用80 ℃左右的热水消化生石灰,使混合料的温度提高了20 ℃左右。
同时,改一次混合加冷水为加热水工艺。
另外,由于我厂采用的热返矿不直接参加配料工艺,热振筛筛下的小于5 mm的热返矿直接用链板输送机送到预热滚筒和部分一次混合料混匀、润湿,使混合料温度提高了50 ℃以上。
通过这些方法,使送往烧结机的烧结料温度可达70 ℃左右,为节能降耗、提高产量创造了条件。
迁安轧一联成烧结厂在生产过程中,配加适量的烧结剂,因为烧结剂在节能降耗中的作用也是不可忽视的。
4、强化烧结剂的合理搭配(1)TYS烧结强效剂产品性能及作用①降低固体燃料消耗烧结料中的配碳量决定着烧结温度、气氛性质及烧结速度。
因本产品含有增氧、助燃物质,可催化加快固体燃料的燃烧反应速度,特别是对固体燃料中非碳物质的催化作用更强,激活混合料中可燃元素及固体燃料的反应活性,加上烧结剂固有的强力可燃、助燃放热物质,使料层总热量大大增加,温度升高,固定燃耗相对降低。
②提高烧结矿强度,提高成品率,降低粉化率,提高烧结矿品质由于增强剂和稳定剂的加入,改善增加了生成液相的数量和性质,增加了湿润性良好的胶结相。
同时,抑制了正硅酸钙的晶型转化(晶型转化时,体积增大10%,发生体积膨胀,导致烧结矿冷却时的自行粉碎)。
同时由于FeO的降低,烧结气氧的改善减少了难还原的铁橄榄石和正硅酸钙的形成(CaO与SiO3及FeO的化学亲和力比CaO 和Fe2O3的亲和力大得多),利于赤铁矿和铁酸钙的形成,抑制了粉化现象,提高了烧结矿的强度,粒级趋于优化合理,同时改善了烧结矿的还原性,成品率上升,返矿量下降。
③提高烧结矿产量、垂直烧结速度是决定产量的重要因素,与产量基本成正比关系。
而垂直烧结速度是燃料的燃烧速度和传热速度决定的,当配碳量适宜或较高时,烧结过程总速度取决于碳的燃烧速度,燃烧速度与供氧强度成正比,强效剂中的富氧离子加快了碳的燃烧速度,提高了燃烧效率,同时高温使料层中水的气化速度变快,过湿层透气性变好,气体的传热速度加快,垂直烧结速度提高,产量提升,同时含粉率降低,强度的提高,使成品率上升,返矿下降,产量相应提高。
④降低燃料消耗燃料消耗的降低是FeO含量降低的重要因素,同时由于烧结剂的加入给烧结料层增加了适量氧离子,缓解了碳粒附近的供氧不足,降低了CO浓度,减少了还原气氛,增强扩大了氧化气氛,抑制降低了FeO的生成。
⑤提高生铁产量,降低焦比由于烧结强效剂的加入,改善了烧结矿的粒度组成和矿物组成,提高了烧结矿的冶金性能,还原性提高,FeO下降,铁产量增加,焦比同步降低。
⑥降低烧结废气中硫含量,利于环境保护由于烧结强效剂的增氧、助燃和催化作用降低了烧结固体燃料的配加量,减少了烧结废气中硫的含量,降低了环境污染,有利于环境保护。
综上所述,TYS烧结强效剂是烧结和煤燃烧及环境保护领域不可或缺的新产品,它以低温烧结和燃气化理论为基础,是该领域的前端技术,它是由燃气化剂、增氧剂、助燃剂、增强剂和阻凝剂等多种元素组成,在烧结混合料中添加少量的该产品后,对燃料气化反应,燃烧反应起到了一定的催化助燃作用,使燃料的反应活性大大提高,反应过程为气—固——液相传热,传质条件改善,使部位液相反应可在低于1300℃以下完成,同时由于烧结料层中燃烧速度加快,反应完全,相对放出热量多,烧结带的温度水平高,生成的CF2和C2F等降低熔点的CF液相向FeO晶粒很快渗透,Ca2+扩散到Fe2O3和Fe3O4晶体中,形成钙质固熔体,使二者的熔点很快下降,最后形成的低熔点的液相,在冷却到1150—1200℃时,树枝状和柱状晶体,使烧结矿的固结强度大大的改善。
该产品用于烧结后,可以改善烧结矿的质量,加快烧结过程,提高烧成率和成品率,降低固体燃料消耗,降低烧结废气中二氧化硫排放量,减少环境污染,在烧结混合料中配加万分之三到四该产品,可以降低固体燃料5~10%,同时提高烧结机利用系数3~5%,提高烧结矿转鼓3~5%。
(2)TYS烧结强效剂配加量及配加量及配加方法①配加量本产品配加量为混合料总量的万分之三到四,根据生产实际,具体科学掌握。
②配加方法分干式和湿式良种,干式配加就是在配料室燃料皮带的后面加一个强效剂配料机,直接将强效剂加在固体燃料上面,这种方法设备简单,操作方便,配加量准确,目前使用较为广泛,湿式配加是将强效剂溶于水中,将水用蒸汽加热到80~100℃,将溶液喷洒在固体燃料上。
这种配加方法设备庞大,操作麻烦,配加量不准确,设备鼓掌多,目前已趋于淘汰。
③物理特征(1)外观:灰白色超细粉末(2)粒度(通过100目):98%(3)密度(g/cm3) :1.4(4)水分:≤3.5%(5)PH值:7.8~8.5④强化制粒工艺轧一烧结厂为了加强制粒工艺,将90m2带烧的一混筒体内壁改为螺旋装,螺旋的方向和滚筒旋转的方向相反,从而延长了制粒时间,增强了制粒效果。
在制粒过程中,还采用“一混加足水,二混雾水制粒”的技术,这样一来,混合料在一混滚筒内已加足水,且由以前的加常温水改为加热水,做到提前润湿,提高了料温,加强了白灰的消化;二混采用雾化喷头补水,雾水有助于混合料粒度长大,从而强化制粒工艺,改善混合料的粒度组成,减少混合料中小于3 mm粒级的含量,增加3~5 mm粒级的含量,使混合料粒度趋于均匀,可明显改善烧结料层的透气性,增高料层,改善烧结矿强度,为烧结矿产质量的不断提高、能耗的降低起到了很大作用。
⑤厚料层烧结在抽风烧结过程中,台车上部的烧结饼受空气急剧冷却的影响,结晶程度差,玻璃质含量高,强度差。
随着料层厚度的增加,强度差的所占的比重相应降低,成品率相应提高,返矿率下降,进而减少了固体燃料消耗。
烧结料层的自动蓄热作用随着料层高度的增加而加强,当料层高度为180~220 mm时,蓄热量只占燃烧带热量总收入的35 %~45 %,当料层厚度达到400 mm时,蓄热量达55 %~60 %。
因此,提高料层厚度,采用厚料层烧结,充分利用烧结过程的自动蓄热,可以降低烧结料中的固体燃料用量,根据实际生产情况,料层每增加10 mm,燃料消耗可降低1.5 kg/t左右。
除此之外,还可以对主抽风机进行扩容改造、加高台车挡板、加强设备维护、减少系统漏风等措施,使料层厚度有一定提高。
(二)降低电耗电耗在烧结工序能耗中是仅次于固体燃耗的第二大能耗,约占13 %~20 %,因此降低电耗也是降低烧结工序能耗的重要措施。
1、减少设备漏风率,降低电耗主抽风机容量占烧结厂总装机容量的30 %~50 %。
减少抽风系统的漏风率,增加通过料层的有效风量对节约电耗意义重大。
烧结台车和首尾风箱(密封板)、台车与滑道、台车与台车之间的漏风占烧结机总漏风量的8 0 %以上,因此改进台车与滑道之间的密封形式,特别是首尾风箱端部的密封结构形式,可以显著地减少有害漏风,增加通过料层的有效风量,提高烧结矿产量,节约电能。
另外,及时更换、维护台车,改善布料方式,减少台车挡板与混合料之间存在的边缘漏风等,都可以有效地减少有害漏风。
通过改造机头机尾密封装置,加强设备的维护、管理,使烧结机的漏风率明显降低,大大增加了通过料层的有效风量,提高了烧结矿产质量,降低了电耗。
下面将具体烧结机的漏风情况及具体解决措施:(1)对烧结漏风的原因分析:通过对烧结抽风系统研究分析,认为漏风集中在以下几点:①抽风机至风箱之间的漏风:此系统包括抽风管道(大烟道)、除尘系统、风机系统。
由于管道的磨损,热胀冷缩变形,夹带灰尘气流冲刷、管理不到位等,使之出现局部缝隙或漏洞而漏风。
此部分漏风因厂而异,但绝对漏风率均在5-10%左右。
②机头尾风箱处与台车横梁底面间的漏风:对此部位的漏风,目前各烧结厂普遍都安装了密封装置。
这些密封装置归纳起来有以下几种:螺旋弹簧式、四连杆式、杠杆式、重锤式、弹簧板式等等。
这些形式的作用是一个,即支撑活动密封板上下自由浮动。
这部分的绝对漏风率在10%左右。
此漏风部位漏风长期堵不住的原因不在于支撑浮动密封板的支撑系统,而在于其密封装置与被密封件之间的结构存在缺陷或不足造成的。
③台车与风箱两侧滑道间的漏风:此部位是烧结漏风的主要部位。