压铸工艺详细介绍
压铸件工艺流程
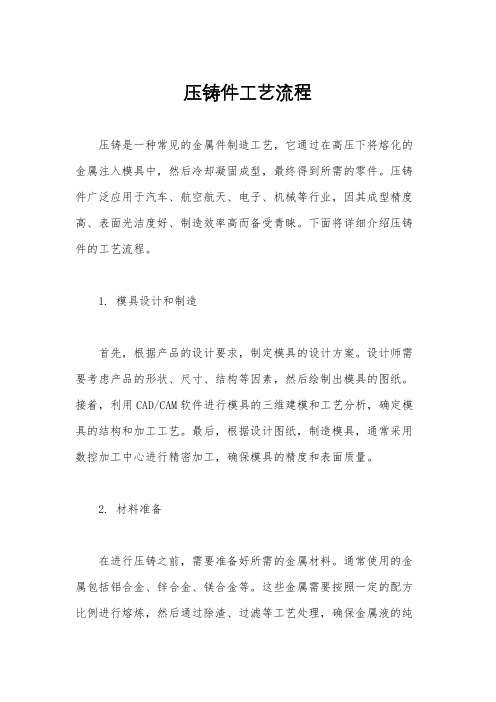
压铸件工艺流程压铸是一种常见的金属件制造工艺,它通过在高压下将熔化的金属注入模具中,然后冷却凝固成型,最终得到所需的零件。
压铸件广泛应用于汽车、航空航天、电子、机械等行业,因其成型精度高、表面光洁度好、制造效率高而备受青睐。
下面将详细介绍压铸件的工艺流程。
1. 模具设计和制造首先,根据产品的设计要求,制定模具的设计方案。
设计师需要考虑产品的形状、尺寸、结构等因素,然后绘制出模具的图纸。
接着,利用CAD/CAM软件进行模具的三维建模和工艺分析,确定模具的结构和加工工艺。
最后,根据设计图纸,制造模具,通常采用数控加工中心进行精密加工,确保模具的精度和表面质量。
2. 材料准备在进行压铸之前,需要准备好所需的金属材料。
通常使用的金属包括铝合金、锌合金、镁合金等。
这些金属需要按照一定的配方比例进行熔炼,然后通过除渣、过滤等工艺处理,确保金属液的纯净度和稳定性。
3. 熔炼和保温将准备好的金属材料加入熔炉中进行熔炼,直至达到所需的温度和流动性。
然后将熔融金属倒入保温炉中进行保温,以保持金属液的温度和流动性,为后续的压铸工艺做准备。
4. 压铸成型在保温炉中保持金属液的温度和流动性后,将金属液注入压铸机的射出室。
通过高压注射系统,将金属液压入模具腔内,填充整个模腔。
在一定的压力和温度下,金属液在模具中凝固成型,形成所需的压铸件。
5. 冷却和固化在金属液填充模腔后,需要等待一定时间,让压铸件在模具中冷却和固化。
冷却时间的长短取决于金属的种类和厚度等因素。
在固化完成后,打开模具,取出成型的压铸件。
6. 修磨和处理取出的压铸件通常会存在一些毛刺、气孔等缺陷,需要进行修磨和处理。
通过去毛刺、抛光、喷砂等工艺,使压铸件的表面光洁度达到要求。
同时,还可以进行热处理、表面处理等工艺,提高压铸件的性能和表面质量。
7. 检验和包装最后,对成型的压铸件进行检验,包括尺寸、外观、化学成分等方面的检测。
合格后,对压铸件进行包装,通常采用防震防潮的包装方式,以确保产品的质量和运输安全。
压铸工艺详解
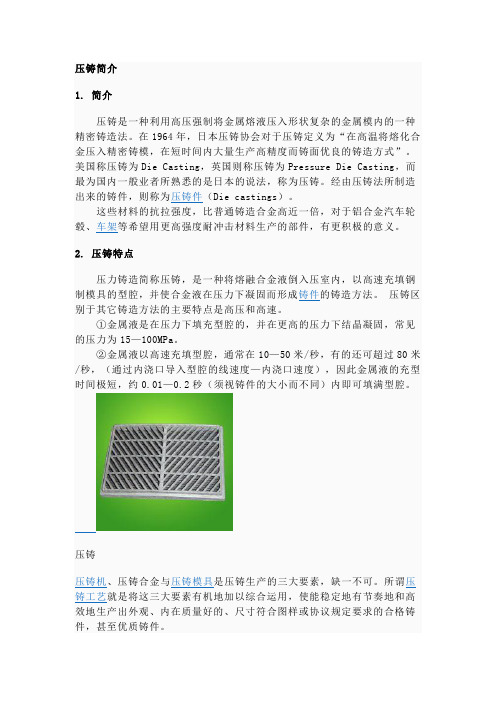
压铸简介1. 简介压铸是一种利用高压强制将金属熔液压入形状复杂的金属模内的一种精密铸造法。
在1964年,日本压铸协会对于压铸定义为“在高温将熔化合金压入精密铸模,在短时间内大量生产高精度而铸面优良的铸造方式”。
美国称压铸为Die Casting,英国则称压铸为Pressure Die Casting,而最为国内一般业者所熟悉的是日本的说法,称为压铸。
经由压铸法所制造出来的铸件,则称为压铸件(Die castings)。
这些材料的抗拉强度,比普通铸造合金高近一倍,对于铝合金汽车轮毂、车架等希望用更高强度耐冲击材料生产的部件,有更积极的意义。
2. 压铸特点压力铸造简称压铸,是一种将熔融合金液倒入压室内,以高速充填钢制模具的型腔,并使合金液在压力下凝固而形成铸件的铸造方法。
压铸区别于其它铸造方法的主要特点是高压和高速。
①金属液是在压力下填充型腔的,并在更高的压力下结晶凝固,常见的压力为15—100MPa。
②金属液以高速充填型腔,通常在10—50米/秒,有的还可超过80米/秒,(通过内浇口导入型腔的线速度—内浇口速度),因此金属液的充型时间极短,约0.01—0.2秒(须视铸件的大小而不同)内即可填满型腔。
压铸压铸机、压铸合金与压铸模具是压铸生产的三大要素,缺一不可。
所谓压铸工艺就是将这三大要素有机地加以综合运用,使能稳定地有节奏地和高效地生产出外观、内在质量好的、尺寸符合图样或协议规定要求的合格铸件,甚至优质铸件。
压铸是一种精密的铸造方法,经由压铸而铸成的压铸件之尺寸公差甚小,表面精度甚高,在大多数的情况下,压铸件不需再车削加工即可装配应用,有螺纹的零件亦可直接铸出。
从一般的照相机件、打字机件、电子计算器件及装饰品等小零件,以及汽车、机车、飞机等交通工具的复杂零件大多是利用压铸法制造的。
压铸法也有下列缺点:· (1)压铸合金受限制目前的压铸合金只有锌、锡、铅、铜、镁、铝等六种,其中以铜合金的熔点最高、铝合金压铸应用广泛。
压力铸造工艺介绍
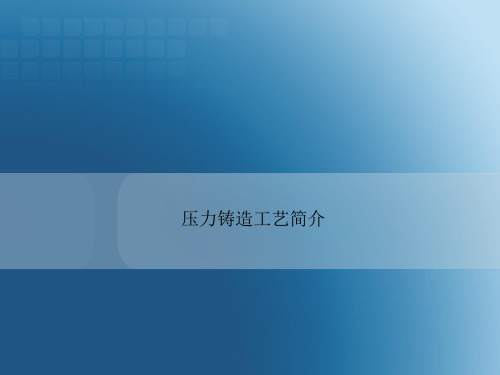
卧式压铸机
热压室压铸机
3.压铸工艺三大要素 3.2.1 卧式压铸机工作原理
3.压铸工艺三大要素 3.2.2 立式压铸机工作原理
640~680℃
200℃左右 900~980℃
1. 密度低,比强度高 2. 流动性好 3. 减震性、磁屏蔽性能好
1.熔点低,流动性好,收缩小 2.可塑性好 3.铸件表面光滑,易做各种表面处理
因熔点高,模具寿命低,应减少使用
3.2 压铸机 3.压铸工艺三大要素
压铸机一般分为冷压室压铸机和热压室压铸机两大类。 冷压室压铸机按其压室结构和布置方式分为卧式压铸机和立式压铸机两种。
3.1 压铸合金
压铸合金应具备的特性: 易于压铸:流动性、收缩性、出模性等尽可能满足压铸的要求。 机械性能:强度、延伸性、脆性等满足产品的设计要求。 机械加工性:易于加工及加工表面的质量能达到产品设计的要求。 表面处理性:抛光、电镀、喷漆、氧化等要求能达到产品设计的要求。 抗腐蚀性:产品在最终的使用环境下具有一定的抗腐蚀性。
4.1 压铸各阶段4.压铸工艺的工艺参数
t1:金属液在压室中未承受压力的时间 t2:金属液于压室中在压射冲头的作用下,通过内 浇口充填型腔的时间 t3:充填刚刚结束时的瞬间 t4.压铸工艺的工艺参数
4.2 工艺参数的选4择.压铸工艺的工艺参数
影响充型的主要因素包括:压力、速度、温度、时间,而各个因素是相互影响和制约的。调整某一 因素,其他因素也会随之变化,因此需对这些工艺参数进行正确选择和调整才能保证生产。
2.1 定义
压铸工艺

4.全立式冷压室压铸机的压铸过程
(1)冲头上压式
2
3
4 5 6
7
1
1—压射冲头 2—熔融合金 3—压室 4—动模 5—定模 6—型腔 7—余料
a)熔融合金浇入压室 c)开模→冲头上升推出余料
b)合模→压射→熔融合金充填型腔 d)推出压铸件→冲头复位
8
<压铸模、锻模及其他模具>
4.全立式冷压室压铸机的压铸过程
面的形状和位置精度,同时,压铸件的变形也是不可忽略的 影响因素。
表1-5 压铸件平行度和垂直度公差;
表1-6 压铸件同轴度和对称度公差。
18
<压铸模、锻模及其他模具>
二.压铸件的表面质量
压铸件的表面粗糙度值,一般比模具成型表面的粗糙度 值低两级。新模具可获得Ra值为0.8μm的压铸件。
模具在正常使用寿命内: 锌合金铸件Ra=1.6-3.2μm 铝、镁合金铸件Ra=3.2μm 铜合金铸件受模具龟裂的影响表面质量最差。
6.经济效益好。
11
<压铸模、锻模及其他模具>
但是压铸生产也存在一些缺点: 1.压铸件易出现气孔和缩松; 2.不适合小批量生产; 3.模具的寿命低; 4.受压铸件结构和合金种类所限。
目前主要压铸锌合金、铝合金及铜合金,黑色合金压铸生产尚不普遍。
12
压铸模、锻模与其他模具
第一章
压铸工艺
Chapter2 The technology of die casting
<压铸模、锻模及其他模具>
四.压铸件的结构工艺性
1.压铸件的壁厚
厚壁压铸件中心层晶粒较大,易产生气孔、缩孔等缺陷,使其强度 和致密性随壁厚的增大而下降。 因此,在保证强度和刚度的前提下,应尽量减小壁厚,通常工艺条 件下以不超过4.5mm为宜。同时,要尽量使各截面壁厚均匀,在较厚部 分采用设加强肋的方法防止铸件缺陷。 需要注意的是,铸件壁厚太薄将会导致欠铸、冷隔现象的产生。
压铸工艺

1.压力铸造:液态金属在较高的压力作用下,以较高的速度充填型腔,并在压力下凝固成型而获得铸件的一种工艺方法。
2.压射比压:压射比压是充填型腔时压室内金属液单位面积上所受的压力。
3.充填时间:液态金属从开始进入型腔起到充满型腔为止所需的时间。
4.充氧压铸:在压铸前将氧气充入型腔,置换出型腔的空气再进行压铸,适用于铝合金压铸。
5.浇注温度:指液态金属从压室进入型腔时的平均温度,一般用保温炉内的温度表示。
6.模具预热温度:为使压铸模能正常工作而在压铸前将压铸模预先加热到一定的温度。
7.活动型芯:用来成型压铸件上与开模方向不一致的侧凹或侧孔,可以抽芯的成型零件。
8.导柱、导套:确保动、定模在安装和合模时精确定位,防止动、定模错位的导向零件。
9.收缩率:压铸件在成型、冷却过程中体积收缩的程度,有实际收缩率和计算收缩率。
10.压铸模CAD:利用计算机技术完成压铸工艺和压铸模设计过程中的信息检索、方案构思、分析计算、工程绘图和文件编制等工作。
1.压铸工艺过程是由压铸机来完成的,压铸机根据压室的工作条件分为冷压室压铸机和热压室压铸机两大类。
各种压铸机的压铸基本过程都为合模、压射、增压-持压和开模。
2.斜导柱抽芯机构是侧抽芯机构中应用最广泛的抽芯机构,其结构主要由活动型芯、斜导柱、滑块、楔紧块、限位块等组成。
3.普通压铸件常有气孔和疏松等缺陷,不能进行热处理,而真空压铸、充氧压铸、精密压铸等压铸新工艺技术能有效的避免或减少疏松、气孔,提高压铸件质量。
4.压铸模成型零件的成型尺寸分为三类:型腔尺寸,即磨损后变大的尺寸;型芯尺寸,即磨损后变小的尺寸和中心距尺寸,即磨损后不变的尺寸。
什么是持压时间?试分析持压时间对压铸件质量和压铸生产效率的影响。
持压时间是指增压开始到结束的这一段时间。
其作用是使型腔中的液态金属在压实压力的持续作用下完成凝固,从而获得组织致密的主见。
持压时间不足,容易造成疏松,尤其是如果内浇口处金属伤胃完全凝固,则将在成压铸冲头退回时金属液被反吸出来而产生铸件内部空洞缺陷。
压铸工艺ppt课件

压铸工艺可获得高精度 、高质量的金属零件, 尺寸精度可达IT6-IT8级 。
压铸机生产效率高,可 实现自动化生产,提高 生产效率。
压铸工艺可节约原材料 ,减少加工余量,降低 生产成本。
压铸工艺可应用于各种 金属材料的成型,如铝 合金、锌合金、铜合金 等。
压铸工艺发展历程
01 早期阶段
压铸工艺起源于19世纪初,最初用于制造印刷机 零件和钟表零件等小型精密零件。
采用真空压铸、挤压铸造等先进压铸技术 ,提高金属液的充型能力和补缩能力,减 少气孔、缩松等缺陷的产生。
提高压铸件质量途径
加强原材料控制
选用优质合金材料,严格控制金属液的化学成分和物理性能,确保原 材料质量符合要求。
优化压铸工艺设计
根据压铸件的结构和性能要求,合理设计浇注系统、排气系统和冷却 系统等,确保金属液在型腔内的流动和凝固过程稳定可靠。
冷却系统设计
根据模具温度和产品要求,设计合理的冷 却水道和冷却方式
模具材料及热处理
01 常用模具材料
热作模具钢、冷作模具钢、塑料模具钢等
02 热处理工艺
淬火、回火、表面强化处理等,提高模具的硬度 、耐磨性和抗疲劳性能
03 模具寿命与维护
通过合理的使用和维护,延长模具使用寿命,降 低生产成本
03
压铸合金与熔炼
强化过程监控和检验
采用先进的检测手段和工艺控制方法,对压铸过程中的关键参数进行 实时监控和调整,确保压铸件质量稳定可靠。
加强人员培训和管理
提高压铸操作人员的技能水平和质量意识,加强生产现场的管理和调 度,确保生产过程的顺利进行和产品质量的有效控制。
06
压铸工艺发展趋势与展望
新型压铸技术及应用前景
02 中期阶段
压铸工艺
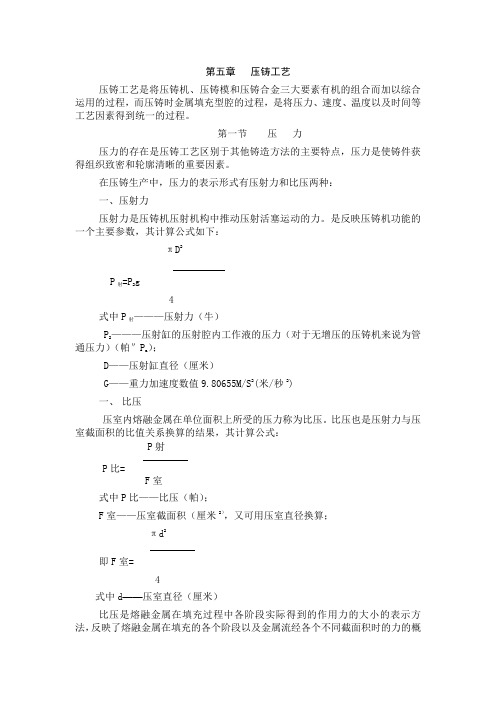
第五章压铸工艺压铸工艺是将压铸机、压铸模和压铸合金三大要素有机的组合而加以综合运用的过程,而压铸时金属填充型腔的过程,是将压力、速度、温度以及时间等工艺因素得到统一的过程。
第一节压力压力的存在是压铸工艺区别于其他铸造方法的主要特点,压力是使铸件获得组织致密和轮廓清晰的重要因素。
在压铸生产中,压力的表示形式有压射力和比压两种:一、压射力压射力是压铸机压射机构中推动压射活塞运动的力。
是反映压铸机功能的一个主要参数,其计算公式如下:πD2P射=P2g4式中P射———压射力(牛)P2———压射缸的压射腔内工作液的压力(对于无增压的压铸机来说为管通压力)(帕″Pa);D——压射缸直径(厘米)G——重力加速度数值9.80655M/S2(米/秒2)一、比压压室内熔融金属在单位面积上所受的压力称为比压。
比压也是压射力与压室截面积的比值关系换算的结果,其计算公式:P射P比=F室式中P比——比压(帕);F室——压室截面积(厘米2),又可用压室直径换算;πd2即F室=4式中d——压室直径(厘米)比压是熔融金属在填充过程中各阶段实际得到的作用力的大小的表示方法,反映了熔融金属在填充的各个阶段以及金属流经各个不同截面积时的力的概念。
将填充阶段的比压称为填充比压(又称压射比压,以P比压表示;增压阶段的比压,称为增压比压,以P比增表示。
填充比压用来克服浇注系统和型腔中的流动阻力,而增压比压则是决定了正在凝固的金属所受到的压力以及这时所形成的胀型力的大小。
三、压力的作用和影响⑴比压对铸件机械性能的影响比压增大,结晶细,结晶层增厚,由于填充特性改善,表面质量提高,会孔影响减轻,从而抗拉强度提高,但延伸率有所降低。
⑵对填充条件的影响。
合金熔液在高比压作用下填充型腔,合金温度升高,流动性改善。
有利于铸件质量的提高。
四、影响压力的因素⑴压铸合金的特性,如熔点、流动性等,熔点高,有效比压越大。
⑵合金浇注温度和模具温度,温度过低,压力损耗增大。
压铸工艺

第三部分压铸工艺一、工艺参数1、压力参数:①压射力用压射压力和压射比压来表示,是获得组织致密、轮廓清晰的压铸件的主要因素,在压铸机上其大小可以调节。
②压射压力压射时压射油缸内的油压,可以从压力表上直接读出,是一个变量,当压铸机进入压射动作时产生压射压力,按照压射动作分段对应的称为一级压射压力(慢压射压力)、二级压射压力(快压射压力)等;增压阶段后转变为增压压力,此时的压射压力达到极大值。
③压射比压压射时压室内金属液在单位面积上所受的压力,简称比压。
可通过改变压射力或更换不同直径的压室及冲头来进行调整。
计算公式为:比压=压射力÷(冲头直径)²×4/π2、速度参数:①压射速度压射时冲头移动的速度。
按照压射过程的不同阶段,压射速度分为慢压射速度(低速压射速度)和快压射速度(高速压射速度)。
一般慢压射速度的选择根据“压室充满度”(即压室内金属液的多少,用百分比快压射速度,是在一定填充时间条件下确定的。
根据铸件的结构特征确定其填充时间后,可用以下公式进行计算:快压射速度=坯件重量/合金比重/压室内截面积/填充时间×[1+(N-1)+0.1]式中“坯件重量”含浇冒系统;“N”为型腔穴数;“填充时间”可查表得到。
按此公式计算出来的快压射速度,是获得优质铸件的理论速度,实际生产中选其1.2倍;对有较大镶嵌件的铸件时可选1.5~2倍。
②内浇口速度金属液在压力作用下通过内浇道导入型腔时的线速度,称为内浇口速度。
内浇口速度对铸件质量有着重要影响,主要是表面光洁度、强度和塑性等方面。
内浇口速度的大小可通过查表得到,调节的方法有:调整压射速度、改变压室直径、调整比压、改变内浇口截面积。
铸件平均壁厚、填充时间、内浇口速度对照表3、时间参数:①填充时间金属液自开始进入型腔到充满铸型的过程所需要的时间。
影响填充时间的因素有:金属液的过热度、浇注温度、模具温度、涂料性能与用量、排气效果等。
压铸过程原理及压铸工艺参数确定

压铸过程原理及压铸工艺参数确定压铸是将熔融的金属注入到铸模中并进行压力加固,使其凝固形成一种金属铸件的工艺过程。
压铸是金属铸造中最常用的一种方法,广泛应用于汽车制造、航空航天、电子电器等工业领域。
下面将详细介绍压铸过程的原理以及压铸工艺参数的确定。
1.压铸模具的设计与制造:压铸模具是压铸过程中至关重要的一环。
它根据铸件的形状和要求,设计并制造出铸型腔、浇注系统、引手等组成部分。
通过压铸模具,可以将熔融金属注入到铸型腔中,形成铸件的形状。
2.熔炼和注射金属:在压铸过程中,首先需要将金属材料熔化,然后通过注射机将熔融金属注入到铸型腔中。
注射机通常由一个熔融金属锅和一个压力室组成。
3.压力加固:当熔融金属注入到铸型腔中后,需要施加一定的压力进行加固。
通过施加压力,可以使熔融金属充分填充铸型腔,并确保金属凝固成一体的铸件。
4.压铸过程:压铸过程是由注射、封着、冷却、开露和脱模等步骤组成的。
在注射阶段,熔融金属被注射机注入铸型腔中。
在封着阶段,注射机的活塞会施加压力,确保金属填充完全,并避免金属的逆流。
在冷却阶段,熔融金属开始凝固。
在开露阶段,模具中的冷却液被排出,并准备下一次注射。
在脱模阶段,铸件从模具中取出。
压铸工艺参数确定:1.注射速度:注射速度是指熔融金属注入铸型腔的速度。
注射速度过快可能导致金属的冲击和气泡产生,而注射速度过慢则会延长制造周期。
注射速度的选择应该根据铸件的形状、厚度和尺寸来确定。
2.注射压力:注射压力是指压铸过程中施加在熔融金属上的压力。
注射压力的选择应该保证金属充分填充铸型腔,并防止金属气泡和缺陷的产生。
3.注射温度:注射温度是指熔融金属注入铸型腔时的温度。
注射温度的选择应该保证熔融金属的流动性,在填充铸型腔的同时尽量减少金属的气泡和缩孔。
4.压力时间:压力时间是指施加在熔融金属上的压力的持续时间。
压力时间的选择应该保证金属充分填充铸型腔,并确保金属在凝固过程中不产生缩孔和缺陷。
压铸件工艺
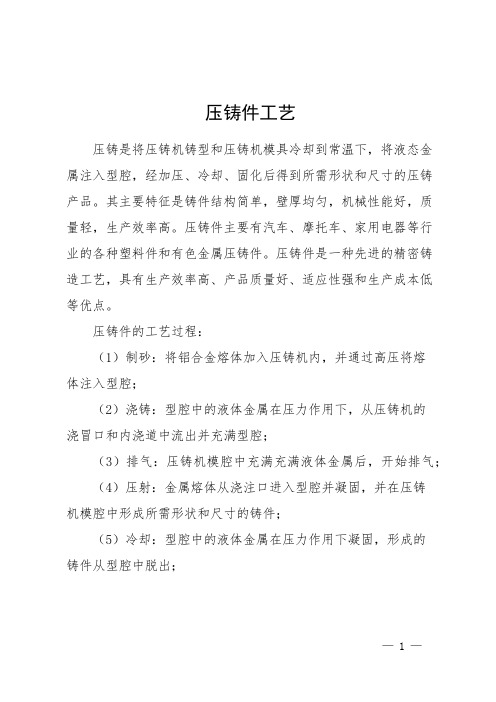
压铸件工艺
压铸是将压铸机铸型和压铸机模具冷却到常温下,将液态金属注入型腔,经加压、冷却、固化后得到所需形状和尺寸的压铸产品。
其主要特征是铸件结构简单,壁厚均匀,机械性能好,质量轻,生产效率高。
压铸件主要有汽车、摩托车、家用电器等行业的各种塑料件和有色金属压铸件。
压铸件是一种先进的精密铸造工艺,具有生产效率高、产品质量好、适应性强和生产成本低等优点。
压铸件的工艺过程:
(1)制砂:将铝合金熔体加入压铸机内,并通过高压将熔
体注入型腔;
(2)浇铸:型腔中的液体金属在压力作用下,从压铸机的
浇冒口和内浇道中流出并充满型腔;
(3)排气:压铸机模腔中充满充满液体金属后,开始排气;
(4)压射:金属熔体从浇注口进入型腔并凝固,并在压铸
机模腔中形成所需形状和尺寸的铸件;
(5)冷却:型腔中的液体金属在压力作用下凝固,形成的
铸件从型腔中脱出;
— 1 —
(6)固化:压铸件经过冷却和固化后,得到所需形状和尺寸的压铸产品。
— 2 —。
压铸成型工艺

定义与特点高效率生产周期短,适用于大批量生产。
高精度压铸成型工艺能够实现较高的尺寸精度和表面光洁度。
定义压铸成型是一种金属铸造工艺,通过高压将熔融金属注入金属模具中,快速冷却凝固后得到所需形状的零件或产品。
优良力学性能压铸件具有优良的力学性能和耐磨性。
广泛适应性可用于铸造各种合金,如铝合金、锌合金、铜合金等。
压铸成型工艺的应用领域电子工业建筑五金散热器、外壳、连接器等。
门窗五金、卫浴五金等。
汽车工业家用电器其他领域发动机零件、车身结构件、传动系统零件等。
洗衣机零件、电视机零件、空调零件等。
航空航天、军事、医疗器械等。
发展历程及现状发展历程压铸成型工艺起源于19世纪末,随着工业革命的推进和金属加工技术的发展,逐渐成为一种重要的金属成型方法。
20世纪中期以后,随着压铸机和模具制造技术的进步,压铸成型工艺得到了快速发展。
现状目前,压铸成型工艺已经成为一种成熟的制造技术,广泛应用于各个领域。
随着新材料、新工艺的不断涌现,压铸成型工艺也在不断发展和完善,向着更高精度、更高效率、更环保的方向发展。
同时,随着数字化、智能化技术的应用,压铸成型工艺的自动化和智能化水平也在不断提高。
03在压铸过程中,金属液在高压下快速充填模具型腔,确保金属液充分占据型腔并复制模具表面的细节。
高压充填原理金属液在凝固过程中会产生收缩,压铸工艺通过控制压射压力和速度,以及模具温度等因素,实现对凝固收缩的补偿。
凝固收缩补偿当金属液完全凝固后,通过开模机构将模具分型面打开,利用顶出机构将压铸件从模具中顶出。
压铸件脱模压铸成型工艺原理压铸机类型及结构热室压铸机主要用于锌、镁等低熔点合金的压铸。
其压室直接浸在保温坩埚的金属液中,结构简单、紧凑、易于维护。
冷室压铸机适用于铝、铜等高熔点合金的压铸。
其压室与保温炉分开,通过给汤机将金属液浇入压室。
冷室压铸机分为卧式和立式两种结构。
压铸机主要部件包括合模机构、压射机构、液压系统、电气控制系统等。
其中,合模机构用于实现模具的开合和锁紧;压射机构用于提供金属液的充填压力和速度;液压系统为压铸机提供动力;电气控制系统负责整个压铸过程的自动化控制。
压铸工艺详细介绍

压铸工艺详细介绍压铸工艺是一种通过将熔融金属注入到模具中,在模具中冷却并固化得出零件的制造方法。
它是现代工业中常用的工艺之一,广泛应用于汽车、航空航天、电子、通讯等领域的零部件制造。
下面详细介绍压铸工艺的步骤和特点。
压铸工艺包含以下几个主要步骤:1.模具设计和制造:首先,根据零件的形状和尺寸要求,设计和制造适用的模具。
模具通常由两部分组成,上模和下模,分别用于顶出零件和固化零件。
2.材料准备:选择适合的铸造合金材料,并按照比例混合和加热。
常用的铸造合金包括铝合金、锌合金和镁合金等。
3.熔融和注入:将预先加热好的合金材料投入到熔炉中进行熔化。
当材料达到适当的熔点后,使用注射机将熔融金属注入到模具中。
4.冷却和固化:熔融金属经过注射后,进入到模具中冷却和固化。
冷却时间通常通过模具温度和冷却系统来控制。
在固化过程中,熔融金属会逐渐凝固成为固体零件。
5.顶出和清理:当零件完全固化后,使用顶子或其他设备顶出零件。
然后对零件进行清理和去除多余的材料,以获得所需的最终产品。
压铸工艺的特点如下:1.高生产效率:压铸工艺可以在短时间内生产大批量的零件。
注射速度快,冷却时间短,可以实现高效的生产。
2.良好的表面质量:由于模具的高精度和压力施加,压铸零件的表面质量通常很好,可以直接用于装配和使用,无需额外加工。
3.复杂形状的制造:压铸工艺可以制造一些复杂形状的零件,如薄壁结构、镂空结构和细小的细节部件等。
4.材料节约:相比其他金属加工方法,压铸工艺可以在加工过程中最大限度地利用金属材料,减少浪费和成本。
5.自动化程度高:压铸工艺可以通过自动化设备和控制系统实现高度自动化的生产,提高生产效率和质量稳定性。
总之,压铸工艺是一项重要的金属加工工艺,广泛应用于各个领域的零件制造。
它具有高效、精确、可靠的特点,能够满足复杂零件的制造需求。
随着科技的不断进步,压铸工艺也将继续发展和创新,为工业制造带来更多的可能性。
压力铸造工艺介绍
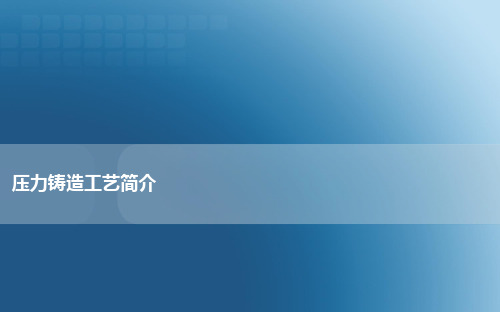
•
8、业余生活要有意义,不要越轨。20 20年12 月13日 星期日 5时39 分40秒0 5:39:40 13 December 2020
•
9、一个人即使已登上顶峰,也仍要自 强不息 。上午 5时39 分40秒 上午5时 39分05 :39:402 0.12.13
• 10、你要做多大的事情,就该承受多大的压力。12/13/
2020 5:39:40 AM05:39:402020/12/13
• 11、自己要先看得起自己,别人才会看得起你。12/13/
谢 谢 大 家 2020 5:39 AM12/13/2020 5:39 AM20.12.1320.12.13
4
3.压铸工艺三大要素
主要压铸合金 铝合金
锌合金
镁合金 铅锡合金 铜合金
浇铸温度 650~680℃
420~440℃
640~680℃ 200℃左右 900~980℃
特点及性能
1. 密度低,可生产要求减轻质量的零部件 2. 强度高,塑性好 3. 抗氧化腐蚀性能好
1. 良好的压铸特性:容易压铸形状复杂,尺寸精度高的产品 2. 抗拉强度高和硬度高,冲击韧性和伸长率较好 3. 良好的加工性能:产品表面,容易做各种表面处理 4. 生产高效
1. 密度低,比强度高 2. 流动性好 3. 减震性、磁屏蔽性能好
1.熔点低,流动性好,收缩小 2.可塑性好 3.铸件表面光滑,易做各种表面处理 因熔点高,模具寿命低,应减少使用
5
3.压铸工艺三大要素
3.2 压铸机
压铸机一般分为冷压室压铸机和热压室压铸机两大类。 冷压室压铸机按其压室结构和布置方式分为卧式压铸机和立式压铸机两种。
2
2.压力铸造
2.1 定义
压铸企业基本工艺流程及知识简介
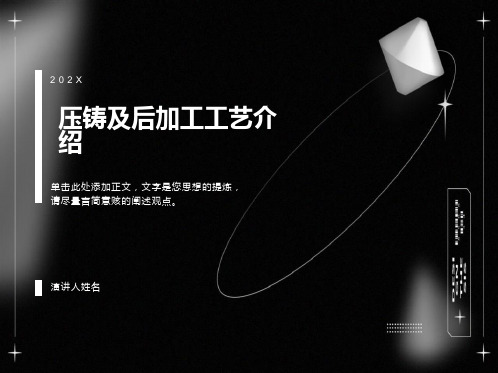
压铸制品 工艺流程
压铸模具
压铸模具必须用热作模具钢制作,常用的钢材有: H13, 2344, 8407, 8418, SKD61, DAC, FDAC等。
模具的结构:(后模,前模)模架,模仁,导柱, 导套顶针,司筒,分流子,浇口套,滑块,斜导柱, 油压抽芯。
3,模具的加工设备:铣床, CNC加工中心,线切 割(慢走丝),(镜面)火花机,磨床,车床,焊 补设备 。
压铸金属材 料
压铸镁合金
镁合金是以镁为基加入其他元素组成的合金。其 特点是:密度小,比强度高,比弹性模量大,散 热好,消震性好,承受冲击载荷能力比铝合金大, 耐有机物和碱的腐蚀性能好。镁的比重大约是铝 的2/3,是铁的1/4。所以在手机,通讯设备等 电子器材,汽车配件,医疗器械上使用广泛。
目前使用最广的是镁铝合金,其次是镁锰合金和 镁锌锆合金。使用的牌号常见的有AZ91D, AM60B,AM50A,AS41B等。
压铸铝合金
铝合金密度低,但强度比较高,接近或超过优质钢, 塑性好,可加工成各种型材,具有优良的导电性、导 热性和抗蚀性,工业上广泛使用,使用量仅次于钢。 铝合金的比重量只有铁的约1/3,所以在目前各行各 业中用途十分重要,尤其是在飞机,船舶,汽车,电 子仪器等的轻量化过程中发辉不可或缺的作用。
常用的有Al-Si-Cu系,常见的有ADC12(A383), ADC10(A380)等。另外还有Al-Si系,Al-Si-Mg系, Al-Mg系。另目前称作铝钛合金的是在上述材料加入 钛金属改良而成,加入钛金属可以显著提高产品的机 械性能。
后加工工艺及设备
热整形加工
○ 在压铸,冲压,机加工,表面处理 等各制程中,尤其是薄壁件,都会 产生形变,所以需要热整形加工来 纠正。
压铸的工艺流程
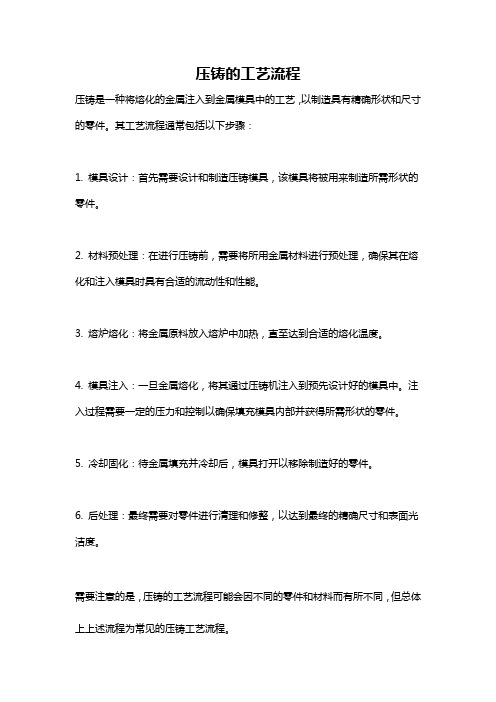
压铸的工艺流程
压铸是一种将熔化的金属注入到金属模具中的工艺,以制造具有精确形状和尺寸的零件。
其工艺流程通常包括以下步骤:
1. 模具设计:首先需要设计和制造压铸模具,该模具将被用来制造所需形状的零件。
2. 材料预处理:在进行压铸前,需要将所用金属材料进行预处理,确保其在熔化和注入模具时具有合适的流动性和性能。
3. 熔炉熔化:将金属原料放入熔炉中加热,直至达到合适的熔化温度。
4. 模具注入:一旦金属熔化,将其通过压铸机注入到预先设计好的模具中。
注入过程需要一定的压力和控制以确保填充模具内部并获得所需形状的零件。
5. 冷却固化:待金属填充并冷却后,模具打开以移除制造好的零件。
6. 后处理:最终需要对零件进行清理和修整,以达到最终的精确尺寸和表面光洁度。
需要注意的是,压铸的工艺流程可能会因不同的零件和材料而有所不同,但总体上上述流程为常见的压铸工艺流程。
压铸成型工艺
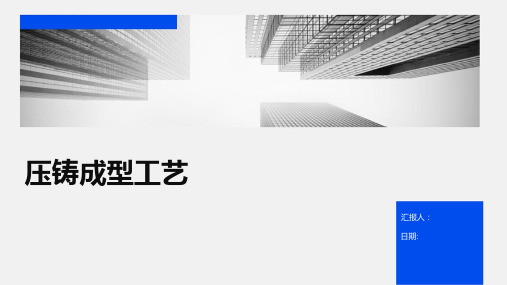
VS
节能降耗
通过优化工艺流程、使用高效设备、余热 回收等技术手段,降低能源消耗和生产成 本。
智能化和自动化生产
智能化控制
采用智能传感器、控制器和执行器等设备,实现生产过程的智能化控制,提高生产效率和产品质量。
自动化生产
。
03
持压时间
金属液注入模具后,需要保持一定的压力一段时间,以确保产品内部质
量和致密度的稳定。持压时间过短会影响产品内部质量,过长则可能导
致模具损坏。
温度参数
模具温度
模具的温度对于压铸成型的质量影响非常大。模具温度过低 会导致金属液流动性下降,过高则可能导致金属液在填充过 程中产生气孔、缩孔等缺陷。
05
压铸成型工艺发展趋 势和挑战
技术创新和发展趋势
高效压铸技术
随着高效压铸设备的研发,压铸 速度大幅提高,生产效率也得到
了显著提升。
精密压铸技术
通过高精度模具和成型工艺,实 现铸件的高精度、高质量生产。
复合材料压铸技术
采用多种材料的组合,发挥各自 优势,提高铸件的综合性能。
环保和节能要求
环保生产
分类
根据所用材料和工艺要求的不同,压铸成型可分为铝合金压铸、锌合金压铸、 镁合金压铸等。
工作原理
高压注入
将熔融金属在高压作用下通过浇 道注入模具中,填满模具的型腔
。
冷却凝固
在模具内冷却凝固后打开模具,取 出铸件。
脱模
将铸件从模具中脱出,进行后续处 理。
应用领域
汽车工业
铝合金压铸件广泛应用于汽车工业中,如发 动机缸体、缸盖等。
对压铸件进行检测,确保其符合质量要求 。
铁压铸工艺

铁压铸工艺铁压铸工艺是一种常用的铸造工艺,它通过将熔化的金属注入到铸型中,然后使用压力将金属填充到整个铸型中。
这种工艺可以生产出具有精密形状和高质量的铸件。
下面将详细介绍铁压铸工艺的工作原理、优点和应用。
铁压铸工艺的工作原理是在铸造过程中施加高压力,以促进金属液的充填和凝固。
首先,将金属加热到熔点,然后将其注入到预先设计好的铸型中。
在注入过程中,使用压力将金属液填充到整个铸型中,确保铸件内部没有气孔和缺陷。
随后,金属开始凝固,在凝固过程中继续施加压力,以保持铸件的形状和密度。
最后,冷却后的铸件从铸型中取出,进行后续的加工和处理。
铁压铸工艺具有一些显著的优点。
首先,由于施加了高压力,铁压铸工艺可以实现铸件的高充填率和高密度,从而保证铸件的强度和耐久性。
其次,铁压铸工艺可以制造复杂形状的铸件,包括薄壁结构和细节部件,这在其他铸造工艺中很难实现。
此外,铁压铸工艺还可以提供良好的表面质量和尺寸精度,减少后续加工的需求。
最后,铁压铸工艺适用于各种铁基合金,如灰铁、球墨铸铁和铸钢等,具有广泛的应用范围。
铁压铸工艺在许多领域都有着广泛的应用。
首先,在汽车工业中,铁压铸工艺可以制造车身结构件、发动机零部件和悬挂系统等关键零部件。
这些铸件需要具有高强度和精确的尺寸,以确保汽车的性能和安全性。
其次,在机械工业中,铁压铸工艺可以制造各种机械零部件,如齿轮、减振器和连接件等。
这些零部件需要具有高密度和精密的形状,以确保机械设备的稳定性和可靠性。
此外,铁压铸工艺还可以应用于电力工业、冶金工业和航空航天工业等领域,制造各种复杂的铸件。
铁压铸工艺是一种常用的铸造工艺,通过施加高压力促进金属液的充填和凝固,可以制造出具有精密形状和高质量的铸件。
它具有高充填率、高密度、复杂形状、良好表面质量和广泛应用等优点。
铁压铸工艺在汽车工业、机械工业和电力工业等领域都有着重要的应用。
随着技术的不断发展,铁压铸工艺将在未来的铸造领域中发挥更加重要的作用。
铁压铸工艺

铁压铸工艺铁压铸工艺是一种常见的金属铸造工艺,广泛应用于制造行业。
本文将介绍铁压铸工艺的定义、特点、应用、优势和发展趋势。
一、定义铁压铸工艺是指将铁水注入到预先设计好的铸型中,然后通过压力使铁水充分填充整个铸型腔体,并在一定时间内冷却凝固,最终得到所需的铸件。
这种工艺通常使用铸铁作为原材料,通过机械设备进行压力施加。
二、特点1. 精度高:铁压铸工艺可以制造出形状复杂、尺寸精确的铸件,满足不同行业的要求。
2. 生产效率高:相比传统的铸造工艺,铁压铸工艺具有生产效率高、生产周期短的优势。
3. 材料利用率高:铁压铸工艺可以减少材料浪费,降低生产成本。
4. 可塑性强:铁压铸工艺适用于各种不同形状、大小的铸件制造,具有较大的可塑性。
三、应用铁压铸工艺广泛应用于汽车制造、工程机械、农机设备、航空航天等行业。
在汽车制造中,铁压铸工艺常用于发动机缸体、曲轴箱、曲轴等零部件的制造。
在工程机械领域,铁压铸工艺常用于挖掘机铲斗、铲刀等零部件的生产。
在航空航天领域,铁压铸工艺常用于飞机发动机零部件的制造。
四、优势1. 节约成本:铁压铸工艺可以减少材料浪费,降低生产成本。
2. 提高产品质量:铁压铸工艺可以制造出精度高、质量稳定的铸件。
3. 降低环境污染:铁压铸工艺相较于传统铸造工艺,能够减少废气、废水和废渣的排放,对环境污染较小。
五、发展趋势1. 自动化:随着科技的进步,铁压铸工艺将逐渐实现自动化生产,提高生产效率和产品质量。
2. 新材料应用:随着新材料的不断发展,铁压铸工艺将拓展到更多的材料领域,如铝合金、镁合金等。
3. 精益生产:铁压铸工艺将更加注重生产过程的精益化管理,提高生产效率和产品质量。
铁压铸工艺作为一种先进的金属铸造工艺,具有精度高、生产效率高、材料利用率高等优点,在各个行业得到广泛应用。
随着技术的不断进步,铁压铸工艺将进一步发展壮大,为制造行业的发展做出更大的贡献。
- 1、下载文档前请自行甄别文档内容的完整性,平台不提供额外的编辑、内容补充、找答案等附加服务。
- 2、"仅部分预览"的文档,不可在线预览部分如存在完整性等问题,可反馈申请退款(可完整预览的文档不适用该条件!)。
- 3、如文档侵犯您的权益,请联系客服反馈,我们会尽快为您处理(人工客服工作时间:9:00-18:30)。
压铸工艺详细介绍
压铸工艺是一种常用的铸造工艺,它在制造各种金属制品中起着重要
的作用。
下面将详细介绍压铸工艺的相关内容。
首先,压铸工艺是一种利用金属熔融状态下的高压力进行模具充填和
冷却的工艺。
它采用金属材料加热熔化后,注入模具中,在模具内部形成
所需产品的形状,并通过压力将金属充分填充到模具的每个角落。
然后经
过冷却凝固,最终获得具有一定形状和尺寸的铸件。
压铸工艺具有以下几个特点:
1.高效性:压铸工艺可以实现高速生产,并且相对于其他铸造工艺,
其生产效率更高。
2.精度高:由于模具的准确度高,所以压铸工艺可以生产出精确的尺
寸和形状的铸件。
3.表面质量好:压铸工艺可以生产出光滑并且不需要进一步表面处理
的铸件。
4.兼容性强:压铸工艺可以处理各种金属材料,如铝合金、锌合金、
镁合金等。
压铸工艺主要包括以下几个步骤:
1.准备工作:包括确定产品的设计要求和模具的制造。
2.材料准备:根据产品的要求选择合适的金属材料,并进行加热熔化。
3.充填:将熔化的金属注入模具中,确保充填均匀并填满整个模具腔体。
4.冷却:待金属充填完成后,模具会进行冷却以凝固金属,并保持所
需形状。
5.脱模:冷却后,打开模具并取出铸件。
6.修整:对铸件进行必要的修整和整形,以满足产品的要求。
7.表面处理:根据产品的要求进行表面处理,如喷漆、电镀等。
8.检验和包装:对铸件进行质量检验,并进行包装。
在压铸工艺中,模具是一个关键的部分。
模具的制造需要对产品的设
计要求有一定的了解,并采用精密的制造工艺,以保证模具的精确度和耐
用性。
压铸工艺在各个领域都有广泛的应用,特别是在汽车行业、家电行业
和机械制造行业中更为常见。
通过压铸工艺,可以生产出各种复杂形状的
铸件,并且可以实现大规模、高效率的生产。
总之,压铸工艺是一种非常重要的铸造工艺,它具有高效性、精度高、表面质量好等特点,并在各个领域都有广泛应用。
压铸工艺的成功实施需
要准备工作、材料准备、充填、冷却、脱模、修整、表面处理、检验和包
装等多个步骤的协调配合。
通过不断的改进和创新,压铸工艺将继续为各
行各业的金属制品生产提供可靠的技术支持。