浅谈直形挡墙的筒仓滑模施工技术
筒仓滑模施工方案(1)

筒仓滑模施工方案(1)一、前言筒仓是农业生产中非常重要的设施,用于储存粮食等物品。
而筒仓的滑模施工是在筒仓建设过程中必不可少的一环。
本文将就筒仓滑模施工的具体方案进行详细阐述,以期为相关施工人员提供一定的参考。
二、施工前准备工作在进行筒仓滑模施工之前,需要做好以下准备工作:1.确定施工方案:根据实际情况确定筒仓滑模施工的具体方案,包括滑模的材料、尺寸等。
2.完成施工图纸:确保施工图纸准确无误,与实际情况相符合。
3.准备材料和设备:准备好所需的材料和设备,包括滑模材料、支撑架、工具等。
三、施工步骤1. 地面准备在进行滑模之前,需要对地面进行充分准备,确保地面平整、稳固,以便后续施工。
2. 搭建支撑架根据施工图纸,搭建支撑架,确保支撑架稳固可靠,能够承受滑模的重量。
3. 安装滑模将预先制作好的滑模安装在支撑架上,注意滑模的位置和角度,确保安装正确。
4. 调整滑模在安装完滑模后,需要进行调整,保证滑模处于水平状态,以确保筒仓建造的准确性。
5. 浇筑混凝土当滑模安装完毕并调整良好后,可以开始浇筑混凝土,填充滑模内部,等待混凝土完全干燥后进行下一步操作。
四、施工注意事项1.施工过程中需注意安全,佩戴好安全装备,做好防护措施。
2.注意施工质量,确保滑模的安装位置准确,避免施工过程中出现偏差。
五、总结筒仓滑模施工是整个筒仓建设过程中重要的一环,正确的施工方案和严谨的施工流程都是保证施工质量的关键。
希望本文对相关人员在进行筒仓滑模施工时有所帮助,确保筒仓的建设顺利进行。
以上就是筒仓滑模施工方案的简要介绍,更多细节可根据实际情况做出相应调整。
浅谈墙体滑模的一般施工工艺

浅谈墙体滑模的一般施工工艺摘要:随着液压提升机械和施工精度调整技术的不断改进和提高,滑模工艺的使用逐步向高层和超高层的民用建筑发展。
本文结合实际,浅谈墙体滑模的一般施工工艺。
关键词:墙体滑膜施工工艺Abstract: with the construction precision mechanical and hydraulic ascension adjustment technology is the constant improvement and improve, the use of technology of slide gradually to the top and super-tall civil construction development. Combining with the actual, showing the general construction technology wall sliding mode.Keywords: wall synovial construction craft1.概述近年来,随着液压提升机械和施工精度调整技术的不断改进和提高,滑模工艺发展迅速。
以前滑模工艺多用于烟囱、水塔等筒壁构筑物的施工,现在逐步向高层和超高层的民用建筑发展,成为了高层建筑施工可供选择的方法之一。
2.墙体滑模的一般施工工艺滑升模板的施工由滑模设备的组装、钢筋绑扎、混凝土浇捣、模板滑升、楼面施工和模板设备的拆除等几个部分组成。
2.1 模板的组装滑升模板的组装是个重要环节,直接影响到施工进度和质量,因此要合理组织、严格施工。
在组装前,要做好拼装场地的平整工作,检查起滑线以下已经施工好的基础或结构的标高和平面尺寸,并标出建筑物的结构轴线、墙体边线和提升架的位置线等。
2.2钢筋绑扎和预埋件埋没钢筋绑扎应与混凝土浇筑速度、模板的滑升速度相配合。
根据每个浇筑层的混凝土浇筑量,浇筑时间和钢筋量的大小,合理安排绑扎人员,划分操作区段,保证钢筋的绑扎速度。
筒仓滑模专项施工方案

筒仓滑模专项施工方案一、方案背景分析:筒仓是用于储存物料的特殊建筑结构,其施工对于筒仓的质量和安全性具有重要影响。
在筒仓滑模施工中,需要合理安排施工工序和采用科学的技术措施,以确保施工质量和安全性。
二、方案设计:1.施工前准备:在开始施工前,应进行详细的施工规划和设计,包括选址、结构设计等方面。
同时,应进行现场勘察,了解施工环境和条件,确保施工可行性。
2.施工工序:(1)基础施工:包括地基处理和基础浇筑。
地基处理应根据地质勘察结果进行,确保基础的稳定性和承载力。
基础浇筑应按照标准进行,确保基础的强度和平整度。
(2)筒仓滑模施工:筒仓滑模施工是利用滑模板进行施工,首先需要制作滑模板和滑模润滑剂。
滑模板应具有一定的强度和刚度,且表面要光滑平整。
滑模润滑剂应具有良好的润滑性能,可以提高滑模效果。
滑模板的安装需要按照设计要求,确保滑模板的平稳和牢固。
然后,通过施工机械将滑模板推动到预定位置,形成筒仓壁体。
滑模板的推动速度和力度要适中,避免对滑模板和筒仓壁体造成不良影响。
(3)顶部施工:顶部施工是筒仓滑模施工的最后一步。
在滑模施工完成后,可以进行筒仓顶部的搭设工作。
顶部的搭设需要采用相应的支撑和安全设施,确保施工的安全性。
3.安全措施:在筒仓滑模施工中,需要注意施工的安全性。
首先,应设置明显的安全警示标志,提醒施工人员注意安全。
其次,施工人员应接受必要的安全培训,了解施工的风险和安全措施。
在滑模施工过程中,需要严格遵守相关操作规程和安全操作规范。
同时,应定期检查施工设备和施工环境,确保其安全性和正常运行。
此外,应配备专门的安全监测和紧急救援设备,以应对突发情况。
4.质量控制:筒仓滑模施工中,需要进行质量控制,确保施工质量。
首先,应依据相关标准和规范进行滑模板和滑模润滑剂的制作和选择。
其次,施工过程中需要进行质量检测和质量控制,确保滑模施工的准确性和一致性。
三、项目进展和预期结果:筒仓滑模施工的进展由施工工艺和工作进度决定。
筒仓滑模建筑施工技术
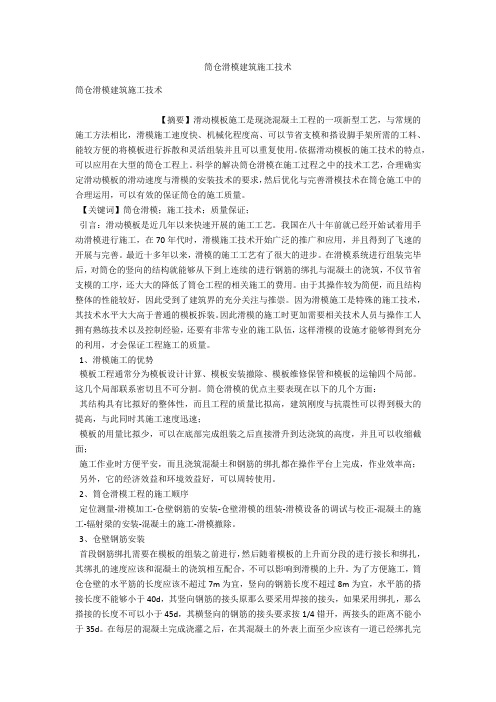
筒仓滑模建筑施工技术筒仓滑模建筑施工技术【摘要】滑动模板施工是现浇混凝土工程的一项新型工艺,与常规的施工方法相比,滑模施工速度快、机械化程度高、可以节省支模和搭设脚手架所需的工料、能较方便的将模板进行拆散和灵活组装并且可以重复使用。
依据滑动模板的施工技术的特点,可以应用在大型的筒仓工程上。
科学的解决筒仓滑模在施工过程之中的技术工艺,合理确实定滑动模板的滑动速度与滑模的安装技术的要求,然后优化与完善滑模技术在筒仓施工中的合理运用,可以有效的保证筒仓的施工质量。
【关键词】筒仓滑模;施工技术;质量保证;引言:滑动模板是近几年以来快速开展的施工工艺。
我国在八十年前就已经开始试着用手动滑模进行施工,在70年代时,滑模施工技术开始广泛的推广和应用,并且得到了飞速的开展与完善。
最近十多年以来,滑模的施工工艺有了很大的进步。
在滑模系统进行组装完毕后,对筒仓的竖向的结构就能够从下到上连续的进行钢筋的绑扎与混凝土的浇筑,不仅节省支模的工序,还大大的降低了筒仓工程的相关施工的费用。
由于其操作较为简便,而且结构整体的性能较好,因此受到了建筑界的充分关注与推崇。
因为滑模施工是特殊的施工技术,其技术水平大大高于普通的模板拆装。
因此滑模的施工时更加需要相关技术人员与操作工人拥有熟练技术以及控制经验,还要有非常专业的施工队伍,这样滑模的设施才能够得到充分的利用,才会保证工程施工的质量。
1、滑模施工的优势模板工程通常分为模板设计计算、模板安装撤除、模板维修保管和模板的运输四个局部。
这几个局部联系密切且不可分割。
筒仓滑模的优点主要表现在以下的几个方面:其结构具有比拟好的整体性,而且工程的质量比拟高,建筑刚度与抗震性可以得到极大的提高,与此同时其施工速度迅速;模板的用量比拟少,可以在底部完成组装之后直接滑升到达浇筑的高度,并且可以收缩截面;施工作业时方便平安,而且浇筑混凝土和钢筋的绑扎都在操作平台上完成,作业效率高;另外,它的经济效益和环境效益好,可以周转使用。
浅谈筒仓结构滑模施工技术

浅谈筒仓结构滑模施工技术摘要】在土木工程施工中,模板工程成本占到总成本近三分之一,模板坍塌造成的伤亡事故在建筑施工事故中也占很大份额,模板工程在建造混凝土结构构件时起到了非常重要的作用。
在滑模施工中,除建筑物易发生偏移和扭转之外,还可能发生一些其他问题。
本文重点讨论滑升模板施工的组成和构造,滑升模板的组装程序,滑升模板的施工注意要点以及施工过程。
【关键词】混凝土;滑升模板;建筑结构引言:滑升模板(简称滑模) 施工,是一种现浇混凝土工程的连续成型施工工艺。
优秀的模板工程能保证工程结构和构件的形状、尺寸和相互位置的准确、标准,并使其具有足够的强度、刚度和稳定性。
由于滑模在混凝土强度还较低的情况下脱模的,故有可能使混凝土表面出现变形或环向沟缝。
文章将从混凝土建筑结构模板的总体施工技术概况、模板结构的要求切入主题,探讨混凝土结构建筑模板施工技术要点。
1.滑升模板的组装1.1滑模组装前的准备工作:(1)滑模的组装工作,应在起滑线以下的基础或结构的混凝土达到一定强度后方可进行。
基础土方应回填平整。
(2)按照图纸,在基底上弹出结构各部位的轴线、边线、门窗等尺寸线,并标出提升架、支承杆、平台桁架等装置的位置线和标高。
(3)液压系统组装完毕后,对千斤顶逐一进行排气,并做到排气彻底;液压系统在试验油压下的液压下持压5分钟,不得渗油和漏油;(4)对滑模装置的各个部件,必须按有关制作标准检查其质量,进行除锈和刷漆等处理,核对好规格和数量并依次编号,然后妥善存放以备使用。
1.2建筑工程对混凝土模板提出的四大要求首先是保证混凝土结构和构件各部分尺寸和相互位置准确,即建筑模板的平面位置、标高、形状以及截面尺寸符合设计图纸的要求。
要求建筑模板工程能承受在正常施工和正常使用时可能出现的各种荷载。
在浇捣混凝土及其养护过程中每浇筑一层混凝土时提升一次模板,既可以加快施工进度,又能使新旧混凝土结合完整,保证新旧接缝看不出。
可以减轻劳动强度,提高工效,加快施工。
浅谈筒仓滑模施工质量控制
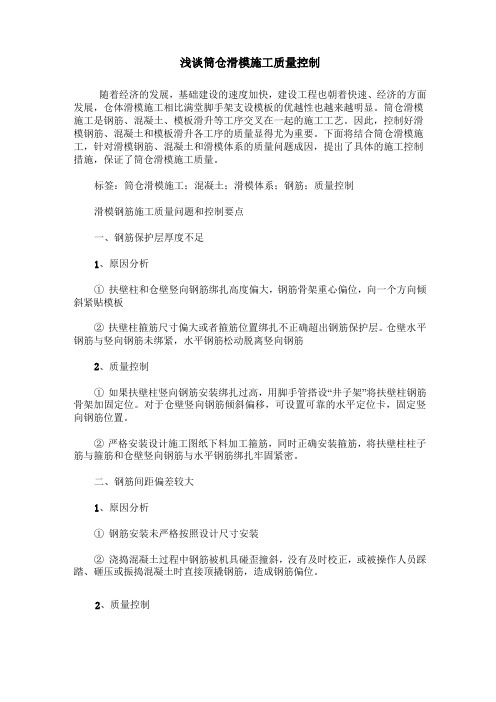
浅谈筒仓滑模施工质量控制随着经济的发展,基础建设的速度加快,建设工程也朝着快速、经济的方面发展,仓体滑模施工相比满堂脚手架支设模板的优越性也越来越明显。
筒仓滑模施工是钢筋、混凝土、模板滑升等工序交叉在一起的施工工艺。
因此,控制好滑模钢筋、混凝土和模板滑升各工序的质量显得尤为重要。
下面将结合筒仓滑模施工,针对滑模钢筋、混凝土和滑模体系的质量问题成因,提出了具体的施工控制措施,保证了筒仓滑模施工质量。
标签:筒仓滑模施工;混凝土;滑模体系;钢筋;质量控制滑模钢筋施工质量问题和控制要点一、钢筋保护层厚度不足1、原因分析①扶壁柱和仓壁竖向钢筋绑扎高度偏大,钢筋骨架重心偏位,向一个方向倾斜紧贴模板②扶壁柱箍筋尺寸偏大或者箍筋位置绑扎不正确超出钢筋保护层。
仓壁水平钢筋与竖向钢筋未绑紧,水平钢筋松动脱离竖向钢筋2、质量控制①如果扶壁柱竖向钢筋安装绑扎过高,用脚手管搭设“井子架”将扶壁柱钢筋骨架加固定位。
对于仓壁竖向钢筋倾斜偏移,可设置可靠的水平定位卡,固定竖向钢筋位置。
②严格安装设计施工图纸下料加工箍筋,同时正确安装箍筋,将扶壁柱柱子筋与箍筋和仓壁竖向钢筋与水平钢筋绑扎牢固紧密。
二、钢筋间距偏差较大1、原因分析①钢筋安装未严格按照设计尺寸安装②浇捣混凝土过程中钢筋被机具碰歪撞斜,没有及时校正,或被操作人员踩踏、砸压或振捣混凝土时直接顶撬钢筋,造成钢筋偏位。
2、质量控制①钢筋绑扎或焊接必须牢固,对水平钢筋设置可靠牢固的钢筋定位卡,底部竖向钢筋画线进行标识。
②混凝土浇捣过程中不碰撞钢筋,严禁踩踏、砸压或直接顶撬钢筋,并且钢筋工随时检查钢筋位置,及时校正。
三、水平钢筋搭接长度不够1、原因分析①钢筋工责任心不强,未严格按照设计要求搭接2、质量控制①对钢筋工进行详细的技术交底,严格按照水平钢筋搭接长度不应小于50倍钢筋直径,接头位置应错开布置,水平方向错开距离不应小于一个搭接区域,也不应小于1.0米,在竖向截面上每各三根钢筋不应多于一个接头。
浅谈水泥厂筒仓滑膜施工中的技术要点

浅谈水泥厂筒仓滑膜施工中的技术要点作者:刘钊摘要:文章对工业建筑中钢筋混凝土筒仓结构滑膜施工作了较为详细的介绍,并且对滑膜系统的构成、滑膜的组装顺序和组装要点以及滑膜施工要点作了重点阐述。
滑动模板施工是现浇混凝土工程的一项新型工艺,与常规的施工方法相比,滑膜施工速度快、机械化程度高、可以节省支模和搭设脚手架所需的工料、能较方便的将模板进行拆散和灵活组装并且可以重复使用。
本文根据滑膜施工规范要求结合新疆霍城县三山水泥厂3000t/d孰料水泥生产线工程施工经验对滑膜施工作简要阐述。
关键词:滑膜钢筋混凝土筒仓空滑提升架围圈一、工程概况:1.1新疆霍城县三山水泥厂3000t/d熟料水泥生产线为新型干法水泥生产工艺,按生产工艺流程分为原料粉磨车间、孰料制成车间、水泥制成车间及煤粉制成车间。
其中原料粉磨车间主要包括石灰石破碎及输送、辅助原料破碎及输送、原料配料库及输送、生料粉磨及废气处理、生料均化库;孰料制成车间主要包:窑尾预热器塔架、烧成窑中、窑头孰料冷却及废气处理、熟料配料库;水泥制成车间主要包括:水泥磨房、水泥库、水泥散装、水泥包装;煤粉制成车间主要包括:原煤堆棚及输送、原煤预均化堆场、煤粉制备等。
1.2在该项目施工过程中,石灰石库、生料均化库及熟料库等多处为筒仓结构,均采用滑膜施工。
其中石灰石库为2×Ф12m连体库同时滑膜,内直径均为12m,壁厚均为0.25m,滑膜施工至+4.500m 高度时停止滑膜,空滑至+5.8m位置,进行+5.72m平面梁板施工,平面标高+5.7200m,板厚800mm,环梁梁宽450mm,梁高1.2m;库内梁高1.5m,梁宽1.2m;暗梁高1.2m,梁宽2.3m。
平台板厚800mm,平面梁板施工完毕后继续进行库壁滑膜施工,滑升到高度35.5m停止滑升,拆除滑模设备;生料均化库为Ф14.3m单体库滑膜,内直径均为14.3m,9.5m以下壁厚均为0.7m,9.5m以上壁厚均为0.35m,滑升到高度47m停止滑升,拆除滑模设备;熟料库为2×Ф15m连体库同时滑膜,内径均为15m,壁厚0.35m,滑膜滑至+3.8m高度时停止滑膜,空滑至+5.2m位置进行底板施工,底板厚1.2m,带底板施工完成后继续进行库壁滑膜施工,滑升到+41m位置后停止滑升,拆除滑膜设备。
浅谈筒仓滑模工程施工技术
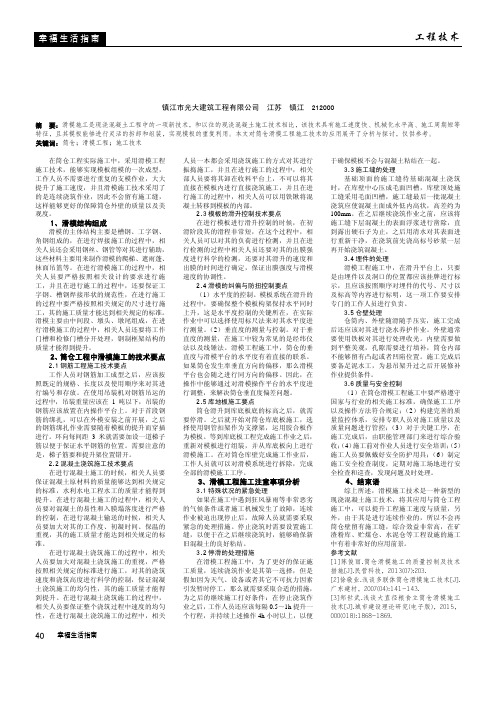
工程技术幸福生活指南40幸福生活指南浅谈筒仓滑模工程施工技术李 衡镇江市光大建筑工程有限公司 江苏 镇江 212000摘 要:滑模施工是现浇混凝土工程中的一项新技术,和以往的现浇混凝土施工技术相比,该技术具有施工速度快、机械化水平高、施工周期短等特征,且其模板能够进行灵活的拆卸和组装,实现模板的重复利用。
本文对筒仓滑模工程施工技术的应用展开了分析与探讨,仅供参考。
关键词:筒仓;滑模工程;施工技术在筒仓工程实际施工中,采用滑模工程施工技术,能够实现模板组模的一次成型,工作人员不需要进行重复的支模作业,大大提升了施工速度,并且滑模施工技术采用了的是连续浇筑作业,因此不会留有施工缝,这样能够更好的保障筒仓外壁的质量以及美观度。
1、滑模结构组成滑模的主体结构主要是槽钢、工字钢、角钢组成的,在进行焊接施工的过程中,相关人员还会采用钢丝、钢管等对其进行辅助,这些材料主要用来制作滑模的爬梯、遮雨蓬、抹面吊篮等。
在进行滑模施工的过程中,相关人员要严格按照相关设计的要求进行施工,并且在进行施工的过程中,还要保证工字钢、槽钢焊接形状的规范性,在进行施工的过程中要严格按照相关规定的尺寸进行施工,其的施工质量才能达到相关规定的标准。
滑模主要由中间段、墩头、墩尾组成,在进行滑模施工的过程中,相关人员还要将工作门槽和检修门槽分开处理,钢制框架结构的质量才能得到提升。
2、筒仓工程中滑模施工的技术要点2.1钢筋工程施工技术要点工作人员对钢筋加工成型之后,应该按照既定的规格、长度以及使用顺序来对其进行编号和存放。
在使用吊装机对钢筋吊运的过程中,吊装重量应该在1吨以下,吊装的钢筋应该放置在内操作平台上。
对于首段钢筋的绑扎,可以在外模安装之前开展,之后的钢筋绑扎作业需要随着模板的提升而穿插进行。
环向每间距3米就需要加设一道梯子筋以便于保证水平钢筋的位置。
需要注意的是,梯子筋要和提升架位置错开。
2.2混凝土浇筑施工技术要点在进行混凝土施工的时候,相关人员要保证混凝土原材料的质量能够达到相关规定的标准,水利水电工程水工的质量才能得到提升。
浅谈筒仓滑模施工技术

浅谈筒仓滑模施工技术摘要:在我国土木工程施工中,模板工程成本约为其全部成本的1/3,而由于模架倒塌而导致的伤亡事故在建筑施工事故中也占很大一大部分。
采用滑模施工,除了建筑物容易产生位移、扭曲以外,还会产生其他问题。
本文着重探讨了滑升模板施工的组成和构造,滑升模板的装配程序,滑升模板的施工注意事项,以及施工流程。
关键词:滑升模板;平台设计;滑模施工引言滑升模板(以下简称滑模)是一项对现浇混凝土进行连续成形的施工技术。
优质的模板可以确保工程结构和构件的形状、尺寸和相互位置的准确、标准,同时还可以提供足够的强度、刚度和稳定性。
因为在未达到一定水平时,采用滑升模板进行脱模,会造成混凝土表层产生扭曲或产生环状裂缝。
本文从一般施工工艺概况,模板构造的要求出发,论述了混凝土结构的施工工艺关键。
一、筒仓滑模平台设计(一)筒仓滑模平台的设计:包括刚性平台和软性平台两类,模板选用组合钢模、铝模,按照筒仓直径选用宽100mm—150mm,高1000mm-1200mm,钢模安装在内外围圆梁上,外部模框比内部模框高100mm,围圈桁架与开字架连接,开字架中部为双梁,顶部为环状槽钢承力梁,环状梁顶部安装液压千斤顶,开字架内部为放射钢桁架或放射梁,中部与钢鼓桶相连构成一个完整的滑模平台。
开字架是整个开字架的关键部件,它要承担内外模框之间的滑动摩擦,同时还要承担钢台的重量以及工程荷载,并要把这些荷载由开字架承力梁、开字架以及开字架等传递到每个顶杆上。
除此之外,开字架内、外立杆还与操作平台、后处理及维修用吊篮相连接,构成了一个完整的滑模平台结构体系,需要进行严谨的设计和计算。
1.刚性滑模平台:其优势在于其整体性好,容易进行施工,可以方便地存放所需的材料,并可以使用该平台进行仓顶混凝土梁、板等构造,但其不足之处在于其耗钢多,适用于小于16m的鼓桶仓库。
该固定式滑动模架包括:开口式框架,环形梁,内圆周圈,组合钢模板,内附设三角桁架,调整拉杆,中心鼓桶。
筒仓滑模施工技术措施
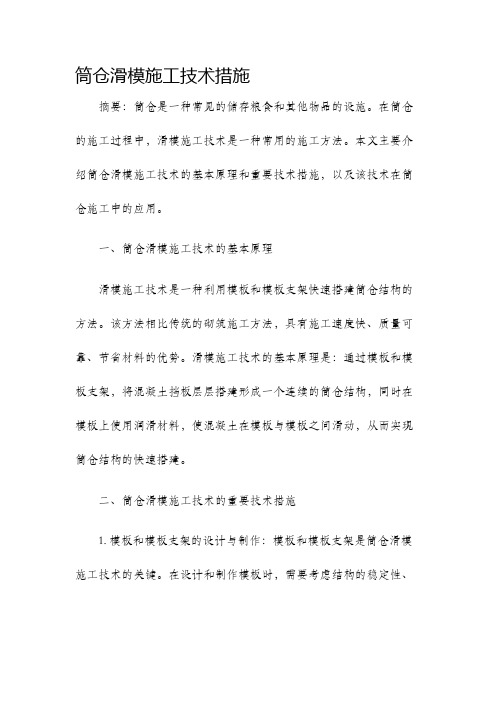
筒仓滑模施工技术措施摘要:筒仓是一种常见的储存粮食和其他物品的设施。
在筒仓的施工过程中,滑模施工技术是一种常用的施工方法。
本文主要介绍筒仓滑模施工技术的基本原理和重要技术措施,以及该技术在筒仓施工中的应用。
一、筒仓滑模施工技术的基本原理滑模施工技术是一种利用模板和模板支架快速搭建筒仓结构的方法。
该方法相比传统的砌筑施工方法,具有施工速度快、质量可靠、节省材料的优势。
滑模施工技术的基本原理是:通过模板和模板支架,将混凝土挡板层层搭建形成一个连续的筒仓结构,同时在模板上使用润滑材料,使混凝土在模板与模板之间滑动,从而实现筒仓结构的快速搭建。
二、筒仓滑模施工技术的重要技术措施1. 模板和模板支架的设计与制作:模板和模板支架是筒仓滑模施工技术的关键。
在设计和制作模板时,需要考虑结构的稳定性、承载能力以及施工的安全性。
模板支架的制作要注意支撑点的设置和支撑方式的选择,以确保筒仓结构施工过程中的稳定性和安全性。
2. 润滑材料的选择与使用:润滑材料在筒仓滑模施工技术中起着重要的作用,它可以减少混凝土与模板之间的摩擦力,使混凝土顺利地滑动。
在选择润滑材料时,需要考虑其与混凝土的相容性、润滑效果以及对环境的影响。
在使用过程中,要注意控制润滑材料的用量,以确保混凝土的质量和施工安全。
3. 混凝土的配制和施工方法:混凝土的配制和施工是筒仓滑模施工技术中的关键环节。
在配制混凝土时,要根据筒仓的设计要求和施工条件确定混凝土的配合比,同时要进行充分搅拌,保证混凝土的均匀性和流动性。
在施工过程中,要注意施工层次和均匀度的控制,以确保筒仓结构的牢固和稳定。
4. 施工过程的监控和质量控制:筒仓滑模施工技术的施工过程需要进行严密的监控和质量控制,以确保施工的准确性和质量的可靠性。
在施工过程中,要对模板和模板支架进行定期检查,确保其稳定性和安全性。
同时要监测混凝土的施工情况,包括流动性、坍落度等指标,及时调整施工参数,保证施工质量。
筒仓滑模施工工艺技术
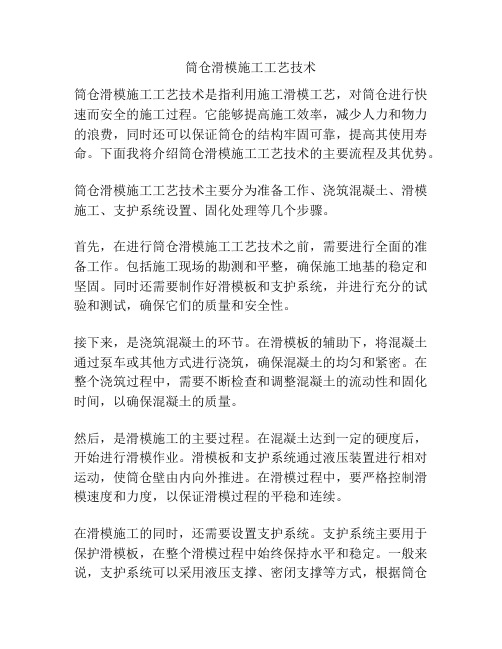
筒仓滑模施工工艺技术筒仓滑模施工工艺技术是指利用施工滑模工艺,对筒仓进行快速而安全的施工过程。
它能够提高施工效率,减少人力和物力的浪费,同时还可以保证筒仓的结构牢固可靠,提高其使用寿命。
下面我将介绍筒仓滑模施工工艺技术的主要流程及其优势。
筒仓滑模施工工艺技术主要分为准备工作、浇筑混凝土、滑模施工、支护系统设置、固化处理等几个步骤。
首先,在进行筒仓滑模施工工艺技术之前,需要进行全面的准备工作。
包括施工现场的勘测和平整,确保施工地基的稳定和坚固。
同时还需要制作好滑模板和支护系统,并进行充分的试验和测试,确保它们的质量和安全性。
接下来,是浇筑混凝土的环节。
在滑模板的辅助下,将混凝土通过泵车或其他方式进行浇筑,确保混凝土的均匀和紧密。
在整个浇筑过程中,需要不断检查和调整混凝土的流动性和固化时间,以确保混凝土的质量。
然后,是滑模施工的主要过程。
在混凝土达到一定的硬度后,开始进行滑模作业。
滑模板和支护系统通过液压装置进行相对运动,使筒仓壁由内向外推进。
在滑模过程中,要严格控制滑模速度和力度,以保证滑模过程的平稳和连续。
在滑模施工的同时,还需要设置支护系统。
支护系统主要用于保护滑模板,在整个滑模过程中始终保持水平和稳定。
一般来说,支护系统可以采用液压支撑、密闭支撑等方式,根据筒仓的具体情况和要求进行选择。
最后,是固化处理的步骤。
当筒仓滑模完全完成后,需要进行一定的固化处理,以保证混凝土的最终强度和稳定性。
通常可以通过水浸、湿度控制等方式进行固化处理,同时还需要进行相应的检测和监控,确保筒仓的质量和安全性。
筒仓滑模施工工艺技术的优势主要体现在以下几个方面。
首先,它可以有效提高施工效率,节约人力和物力资源。
相比传统的施工方法,滑模施工可以大大缩短施工周期,提高工作效率。
其次,它可以确保筒仓的结构牢固可靠,提高其使用寿命。
滑模施工可以保证筒仓壁的密实和均匀性,减少裂缝和渗漏的可能性,提高筒仓的稳定性和耐久性。
最后,滑模施工还具有灵活性强、适应性好的特点。
筒仓滑模施工方案

筒仓滑模施工方案
在工程项目中,筒仓滑模施工是一项重要的工程技术,也是保证工程质量和进度的关键环节。
本文将从筒仓滑模的施工流程、关键技术和注意事项等方面进行介绍,希望能对相关工程人员有所帮助。
一、施工准备
在进行筒仓滑模施工前,首先需要进行全面的施工准备,包括确定施工方案、准备施工材料和设备、对现场环境进行评估等。
在确定施工方案时,需要充分考虑筒仓的结构特点、承载力要求以及施工条件等因素,制定详细的施工计划和安全措施。
二、滑模施工流程
1. 地基处理
在进行筒仓滑模施工前,首先需要对地基进行处理,确保地基坚固平整,以保证滑模过程中的稳定性和安全性。
2. 模板制作
制作滑模用的模板是筒仓滑模施工的重要步骤,应根据筒仓的设计要求和尺寸制作模板,保证模板的精度和质量。
3. 浇筑混凝土
在模板制作完成后,可以开始进行混凝土的浇筑工作。
在浇筑过程中,需要注意混凝土的均匀性和密实性,以确保筒仓的强度和稳定性。
4. 滑模施工
一切准备就绪后,可以进行筒仓的滑模施工。
通过起重机和液压系统等设备,将筒仓逐渐推进到设计位置,同时注意施工过程中的水平控制和安全检查,确保滑模施工的顺利进行。
三、注意事项
在进行筒仓滑模施工时,需要注意以下几个方面:
1.安全第一,严格遵守施工安全规定,确保施工人员的安全;
2.注意施工质量,加强质量管理,保证筒仓的稳定性和耐久性;
3.严格按照设计要求和施工方案进行施工,确保筒仓滑模施工的顺利进
行。
以上是关于筒仓滑模施工方案的介绍,希望对相关工程人员在实际工程项目中有所帮助。
筒仓滑模施工方案
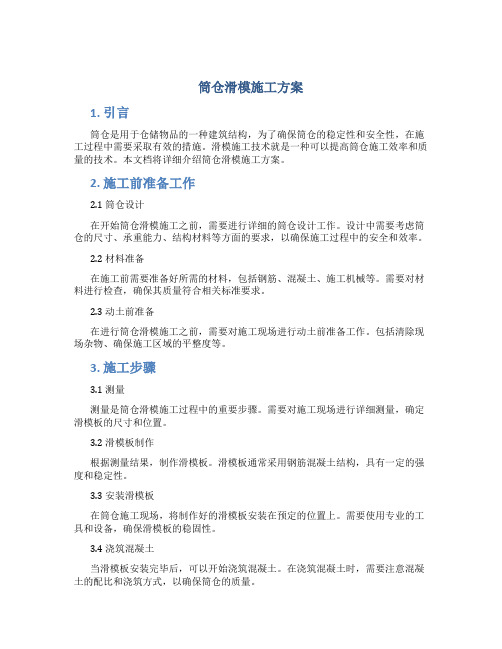
筒仓滑模施工方案1. 引言筒仓是用于仓储物品的一种建筑结构,为了确保筒仓的稳定性和安全性,在施工过程中需要采取有效的措施。
滑模施工技术就是一种可以提高筒仓施工效率和质量的技术。
本文档将详细介绍筒仓滑模施工方案。
2. 施工前准备工作2.1 筒仓设计在开始筒仓滑模施工之前,需要进行详细的筒仓设计工作。
设计中需要考虑筒仓的尺寸、承重能力、结构材料等方面的要求,以确保施工过程中的安全和效率。
2.2 材料准备在施工前需要准备好所需的材料,包括钢筋、混凝土、施工机械等。
需要对材料进行检查,确保其质量符合相关标准要求。
2.3 动土前准备在进行筒仓滑模施工之前,需要对施工现场进行动土前准备工作。
包括清除现场杂物、确保施工区域的平整度等。
3. 施工步骤3.1 测量测量是筒仓滑模施工过程中的重要步骤。
需要对施工现场进行详细测量,确定滑模板的尺寸和位置。
3.2 滑模板制作根据测量结果,制作滑模板。
滑模板通常采用钢筋混凝土结构,具有一定的强度和稳定性。
3.3 安装滑模板在筒仓施工现场,将制作好的滑模板安装在预定的位置上。
需要使用专业的工具和设备,确保滑模板的稳固性。
3.4 浇筑混凝土当滑模板安装完毕后,可以开始浇筑混凝土。
在浇筑混凝土时,需要注意混凝土的配比和浇筑方式,以确保筒仓的质量。
3.5 混凝土固化在混凝土浇筑完成后,需要等待一定的时间让混凝土固化。
固化过程中,需要保持施工现场的干燥和通风,以保证混凝土的强度和稳定性。
3.6 拆除滑模板待混凝土固化完成后,可以拆除滑模板。
在拆除滑模板之前,需要对混凝土进行检查,确保其质量符合要求。
4. 安全措施4.1 施工人员安全在施工过程中,需要确保施工人员的安全。
施工人员应穿戴好安全帽、防护鞋和手套等个人防护设备,并遵守相关施工规范和操作规程。
4.2 施工现场安全在施工现场周围设置明显的警示标志,确保施工现场的安全。
同时,对施工现场进行定期巡检,保持施工区域的整洁和安全。
4.3 设备安全在施工过程中,需要确保使用的设备的安全性能。
筒仓滑模施工技术措施

筒仓滑模施工技术措施筒仓滑模施工技术措施【关键词】筒仓滑模滑模施工筒仓新建筒仓建筑连体筒仓滑模施工组装程序筒仓滑模模板滑升控制系统1 筒仓滑模施工装置的设计1.1 筒仓滑模模板系统1)筒仓滑模模板的设计:通过验算,筒仓内外模均采用200 mm~1 200 mm钢模,为了提高筒仓滑模施工观感质量和减少筒仓滑模模板与混凝土之间的摩擦力,保证达到清水混凝土的施工质量,全部采用新筒仓滑模模板,并涂以隔离剂。
2)筒仓围圈的设计:经计算采用[10的围圈,上(下)围圈距筒仓滑模模板上(下)口径距离均为225 mm,既能保证筒仓滑模模板不致因振捣作业的影响而变形,又可保证筒仓滑模模板的锥度。
3)筒仓滑模提升架的设计:采用П型提升架,内、外立柱为[8,由δ8钢板组焊接成截面为250的格构状,横梁为[16,节点板为δ8钢板,由Φ16螺栓连接。
1.2 筒仓施工平台操作系统包括内、外操作筒仓施工平台及内、外吊脚手架,内筒仓施工平台由支撑、龙骨、铺板、钢桁架组成,供滑升时操作、临时堆放材料、机具使用;外筒仓施工平台由三角外挂架、龙骨、铺板、栏杆、密目安全网组成,并兼作电器线路布置杆。
内外吊脚手架由吊架、铺板、护栏、密目安全网组成,用于混凝土表面整修,剔出预埋件及混凝土浇水养护。
1.3 筒仓滑模施工液压提升系统包括千斤顶、液压控制台、油管、支撑杆等,是液压滑升的动力。
经过计算:每个仓筒仓施工平台总荷载为670 kN,需支撑杆个数为:n=G/30=22(个)加上不稳定系数:22×1.4=25个,采用回收式支撑杆,在提升架横梁下设置内径比支撑杆直径大2 mm~5 mm的套管。
需25个60 kN的千斤顶即可。
在 9.00 m以下每个仓需带4个壁柱及2个端柱同时滑升。
千斤顶数量可做适当调整。
油路采用等长分级方式布置,油路及千斤顶安装好后,用红铅油编号挂牌,以便滑升中纠偏使用。
线路采用并联分级方式,共设3套线路。
1.4 筒仓滑模施工精度的控制系统1.4.1 筒仓滑模施工水平度的控制采用水准仪控制,在筒仓滑模模板开始滑升前,用水准仪对整个操作筒仓施工平台各部位的千斤顶的高程进行观测、校平,并在每根支撑杆上明显标志画出水平线,当筒仓滑模模板滑升时即以此水平线作为基点,每次按250 mm的速度提升,以后每班进行两次水平度观测与检查。
浅谈直形挡墙的筒仓滑模施工技术

模板工程技术规范》GB 5 0 t l 3 的规定 ,采用 以 下计 算 方 法 : 根据仓体结构 形式和工程施 工图纸,编 制详细的 《 施工组织设计》 , 按 照 工 艺原 理 , 设计液压提升 和控制系统 。通 过荷载计算确 定所需的千斤 顶规格数量 ,根据 千斤顶的数 量选用合适 的液 压控制 台,合 理选择油路布 置方案。 3 _ 3 . 1仓体周 圈墙壁 ,液压提升系统所 需 千 斤 顶 和 支承 杆 的最 小 数 量 确 定 :
2 . 施 工工艺流程 :
简 仓滑模设计一 库壁与直形挡 墙预 留插 筋 绑扎一库底板 以下部位库壁滑模 施工一空 滑 作业一环梁及 直形挡墙施 工一 库底板施工 库壁筒体滑模施工
一
3 . 筒仓滑模 体系设计
滑 升模板体 系设计原则 :是保证施工 各 个 阶段模板体 系的整体性 、稳定性 、滑升 同 步性 ,保证模 板施工 的可控 可调和滑模体 系 与预留插 筋模板体系的无缝对接。 3 . 1滑 模体 系 选型 3 . 1 . 1 库 壁在 滑 升过 程 中 ,因 千 斤 顶本 身 性能存在偏 差 ,易造成滑 模体系整体性钢 度 在一定程度 上减小 ,因此 必须对滑模体系 进 行加强 ,滑模 系统除正 常的模板、 围檩 、提 升架 、操 作平 台等组成 外,另需加 设水 平辐 射拉杆 ( 见 水平 辐射 拉 杆 布 置 平 面 图 ) 。 3 . 1 _ 2直形挡墙滑模构造选型 :为 了便于 直形挡墙 的二次施工 ,直形挡墙与库壁 相交 处 的模板 要经过特殊处 理,在直形挡墙 与库 壁 滑模 连接 处 增 加具 有 竖 向开槽 的定型 模 板 ,以确 保滑模体系 与预留插筋模板相 交处 不漏浆不变形。 3 . 2滑模体系主要 构件形 式及构造 关系 滑模 系统 由模板 、围檩 、提升 架、提升 系统 、操作平台等组成 。 a . 模板:采用 3 am厚、高度 1 r 2 0 0 am 、 r 宽度 2 5 0 mm 的钢模板 。库壁与直形挡墙连接 处模 板 采 用 定 型 模 板 。 b 周 檩 :上 下 围檩 将 提 升 架 连 成整 体 ,其 强度 、刚度 、截面 尺寸应 由根据 计算确定 。 本工程采用『 8 槽 钢 制 作 , 上 下 围 檩 间 距 8 0 0 am,内外 各两 道 ,围檩 与模 板连接采用 r 8 撑 铅丝绑扎牢 固,围檩与 门字架连 接采用焊 接 。上 围檩距模板上 口距离不大于 2 5 0 am。 r
筒仓滑模专项施工方案
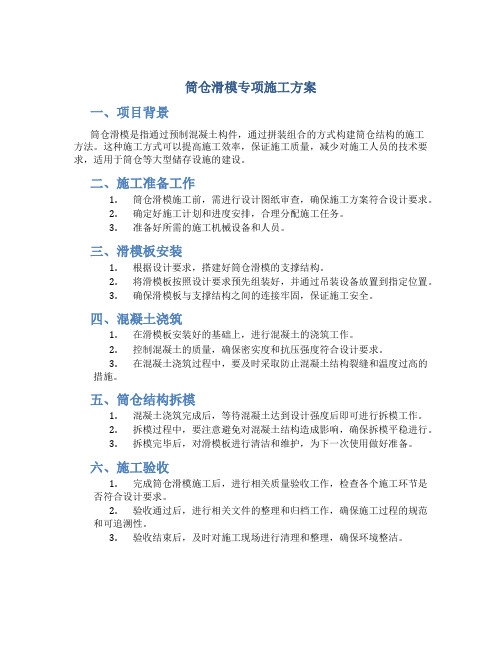
筒仓滑模专项施工方案一、项目背景筒仓滑模是指通过预制混凝土构件,通过拼装组合的方式构建筒仓结构的施工方法。
这种施工方式可以提高施工效率,保证施工质量,减少对施工人员的技术要求,适用于筒仓等大型储存设施的建设。
二、施工准备工作1.筒仓滑模施工前,需进行设计图纸审查,确保施工方案符合设计要求。
2.确定好施工计划和进度安排,合理分配施工任务。
3.准备好所需的施工机械设备和人员。
三、滑模板安装1.根据设计要求,搭建好筒仓滑模的支撑结构。
2.将滑模板按照设计要求预先组装好,并通过吊装设备放置到指定位置。
3.确保滑模板与支撑结构之间的连接牢固,保证施工安全。
四、混凝土浇筑1.在滑模板安装好的基础上,进行混凝土的浇筑工作。
2.控制混凝土的质量,确保密实度和抗压强度符合设计要求。
3.在混凝土浇筑过程中,要及时采取防止混凝土结构裂缝和温度过高的措施。
五、筒仓结构拆模1.混凝土浇筑完成后,等待混凝土达到设计强度后即可进行拆模工作。
2.拆模过程中,要注意避免对混凝土结构造成影响,确保拆模平稳进行。
3.拆模完毕后,对滑模板进行清洁和维护,为下一次使用做好准备。
六、施工验收1.完成筒仓滑模施工后,进行相关质量验收工作,检查各个施工环节是否符合设计要求。
2.验收通过后,进行相关文件的整理和归档工作,确保施工过程的规范和可追溯性。
3.验收结束后,及时对施工现场进行清理和整理,确保环境整洁。
七、总结筒仓滑模作为一种高效的施工方法,可以有效提高施工效率,保证施工质量。
在施工过程中,要严格按照设计要求执行,合理安排施工进度,保证施工安全。
只有做好施工准备工作,严格把控施工过程,才能保证筒仓滑模施工的顺利进行。
筒仓滑模施工方案
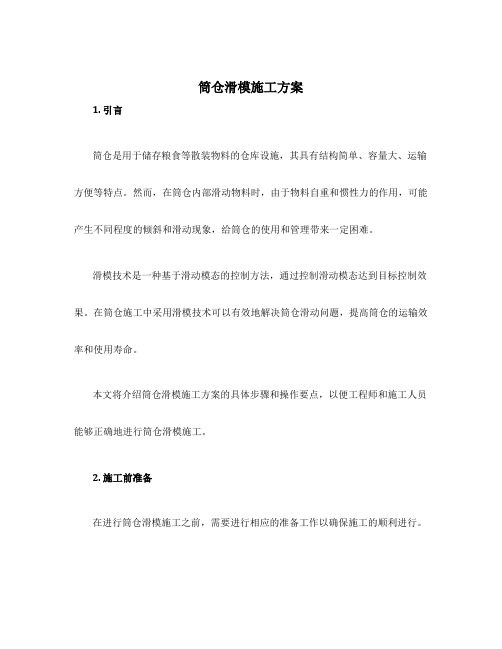
筒仓滑模施工方案1. 引言筒仓是用于储存粮食等散装物料的仓库设施,其具有结构简单、容量大、运输方便等特点。
然而,在筒仓内部滑动物料时,由于物料自重和惯性力的作用,可能产生不同程度的倾斜和滑动现象,给筒仓的使用和管理带来一定困难。
滑模技术是一种基于滑动模态的控制方法,通过控制滑动模态达到目标控制效果。
在筒仓施工中采用滑模技术可以有效地解决筒仓滑动问题,提高筒仓的运输效率和使用寿命。
本文将介绍筒仓滑模施工方案的具体步骤和操作要点,以便工程师和施工人员能够正确地进行筒仓滑模施工。
2. 施工前准备在进行筒仓滑模施工之前,需要进行相应的准备工作以确保施工的顺利进行。
•筒仓检查:首先需要对筒仓的结构进行检查,确保筒仓的主体结构完好无损,并且无明显的破损和变形。
•设备准备:准备好所需的滑模施工设备,包括滑模涂料、滑模辊等。
•人员培训:对参与施工的人员进行培训,使其了解滑模施工的基本原理和操作技巧。
3. 滑模施工步骤筒仓滑模施工的具体步骤如下:3.1 清洁筒仓内壁首先需要对筒仓内壁进行清洁,确保内壁表面干净无杂质。
可以使用刷子和清洁剂进行清洁,清洗时应注意不要刮伤内壁表面。
3.2 涂刷滑模涂料选择适当的滑模涂料,并按照说明进行搅拌和稀释。
然后使用刷子或喷枪将滑模涂料均匀地涂刷在筒仓内壁上。
涂刷时应注意涂料的厚度和均匀性,避免出现涂刷不均匀、厚度不一致的情况。
3.3 使用滑模辊进行压实在涂刷滑模涂料后,需要使用滑模辊对涂料进行压实,以提高涂料的附着力和平整度。
使用滑模辊时应注意力度的适度,避免过度压实导致涂层破裂或剥落。
3.4 干燥和固化涂刷完滑模涂料并进行压实后,需要等待涂料干燥和固化。
根据涂料的类型和环境条件,通常需要等待24小时以上,待涂料完全干燥和固化后才能进行下一步操作。
3.5 定期检查和维护筒仓滑模施工完成后,需要定期检查和维护。
定期检查涂层的完整性和附着力,如发现涂层有破损或剥落时,及时进行修补。
4. 操作要点在进行筒仓滑模施工时,需要注意以下操作要点:•涂刷滑模涂料时,要保持较为恒定的速度和力度,避免涂刷过快或过慢导致涂层不均匀。
筒仓滑模施工方案
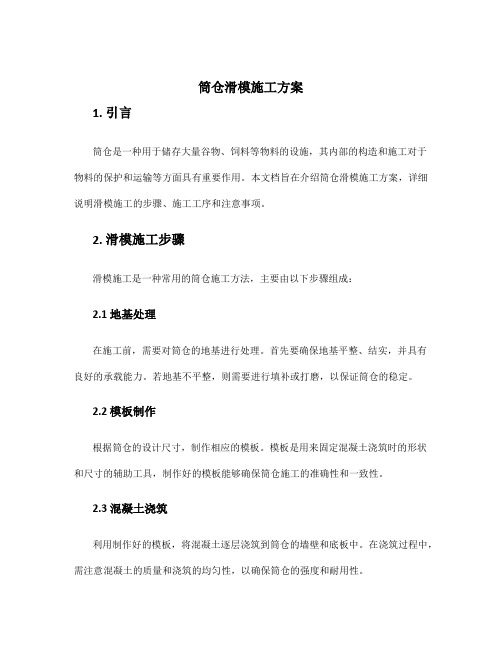
筒仓滑模施工方案1. 引言筒仓是一种用于储存大量谷物、饲料等物料的设施,其内部的构造和施工对于物料的保护和运输等方面具有重要作用。
本文档旨在介绍筒仓滑模施工方案,详细说明滑模施工的步骤、施工工序和注意事项。
2. 滑模施工步骤滑模施工是一种常用的筒仓施工方法,主要由以下步骤组成:2.1 地基处理在施工前,需要对筒仓的地基进行处理。
首先要确保地基平整、结实,并具有良好的承载能力。
若地基不平整,则需要进行填补或打磨,以保证筒仓的稳定。
2.2 模板制作根据筒仓的设计尺寸,制作相应的模板。
模板是用来固定混凝土浇筑时的形状和尺寸的辅助工具,制作好的模板能够确保筒仓施工的准确性和一致性。
2.3 混凝土浇筑利用制作好的模板,将混凝土逐层浇筑到筒仓的墙壁和底板中。
在浇筑过程中,需注意混凝土的质量和浇筑的均匀性,以确保筒仓的强度和耐用性。
2.4 构造施工混凝土浇筑完成后,需进行筒仓的构造施工。
主要包括安装筒仓的顶部和底部结构,并进行密封处理、通风设备的安装等工作。
在构造施工中,需要根据设计图纸严格执行,确保施工的准确性和符合安全规范。
2.5 其他工序除了上述步骤外,还有一些其他的工序需要完成。
例如,对筒仓外墙进行涂刷防腐涂料、安装负荷传递装置等。
这些工序需要根据实际情况和设计要求进行。
3. 施工工序注意事项在进行筒仓滑模施工时,需要注意以下事项:3.1 安全防护在施工过程中,应严格遵守安全操作规范,佩戴好安全防护用具,如安全帽、安全鞋等。
同时,保证施工现场的通风和安全疏散通道的设置,确保工人的安全。
3.2 施工质量控制对于每一个施工步骤,都需要严格按照设计要求和施工规范进行,确保施工质量。
在混凝土浇筑时,要特别注意浇注的均匀性和混凝土的质量,防止出现空鼓、裂缝等问题。
3.3 施工进度控制在开始施工前,应制定合理的施工计划,并根据实际情况进行控制。
确保施工进度的合理安排,并根据需要及时调整计划。
3.4 管理与验收在施工过程中,应有专人进行施工现场的管理,确保材料的质量和施工的准确性。
研究筒仓结构滑模施工技术
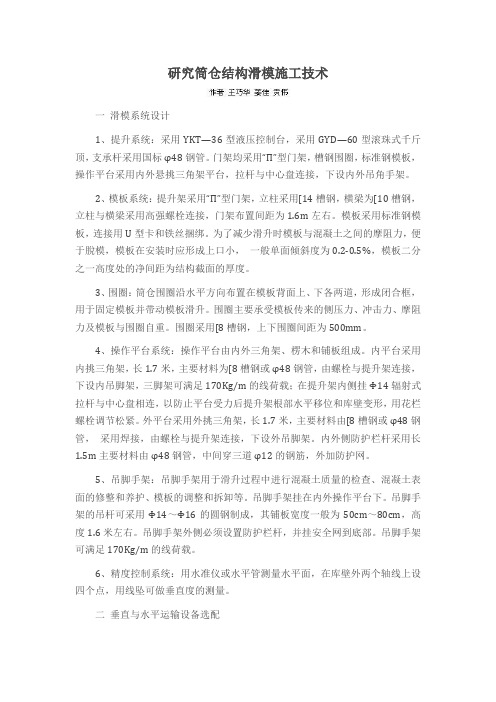
研究筒仓结构滑模施工技术一滑模系统设计1、提升系统:采用YKT—36型液压控制台,采用GYD—60型滚珠式千斤顶,支承杆采用国标φ48钢管。
门架均采用“Π”型门架,槽钢围圈,标准钢模板,操作平台采用内外悬挑三角架平台,拉杆与中心盘连接,下设内外吊角手架。
2、模板系统:提升架采用“П”型门架,立柱采用[14槽钢,横梁为[10槽钢,立柱与横梁采用高强螺栓连接,门架布置间距为1.6m左右。
模板采用标准钢模板,连接用U型卡和铁丝捆绑。
为了减少滑升时模板与混凝土之间的摩阻力,便于脫模,模板在安装时应形成上口小,一般单面倾斜度为0.2-0.5%,模板二分之一高度处的净间距为结构截面的厚度。
3、围圈:筒仓围圈沿水平方向布置在模板背面上、下各两道,形成闭合框,用于固定模板并带动模板滑升。
围圈主要承受模板传来的侧压力、冲击力、摩阻力及模板与围圈自重。
围圈采用[8槽钢,上下围圈间距为500mm。
4、操作平台系统:操作平台由内外三角架、楞木和铺板组成。
内平台采用内挑三角架,长1.7米,主要材料为[8槽钢或φ48钢管,由螺栓与提升架连接,下设内吊脚架,三脚架可满足170Kg/m的线荷载;在提升架内侧挂Φ14辐射式拉杆与中心盘相连,以防止平台受力后提升架根部水平移位和库壁变形,用花栏螺栓调节松紧。
外平台采用外挑三角架,长1.7米,主要材料由[8槽钢或φ48钢管,采用焊接,由螺栓与提升架连接,下设外吊脚架。
内外侧防护栏杆采用长1.5m主要材料由φ48钢管,中间穿三道φ12的钢筋,外加防护网。
5、吊脚手架:吊脚手架用于滑升过程中进行混凝土质量的检查、混凝土表面的修整和养护、模板的调整和拆卸等。
吊脚手架挂在内外操作平台下。
吊脚手架的吊杆可采用Φ14~Φ16的圆钢制成,其铺板宽度一般为50cm~80cm,高度1.6米左右。
吊脚手架外侧必须设置防护栏杆,并挂安全网到底部。
吊脚手架可满足170Kg/m的线荷载。
6、精度控制系统:用水准仪或水平管测量水平面,在库壁外两个轴线上设四个点,用线坠可做垂直度的测量。
浅谈筒仓滑膜施工技术及控制要点

浅谈筒仓滑膜施工技术及控制要点作者:万春利来源:《中国房地产业·上旬》2021年第12期【摘要】滑膜是利用一定动力使模板系统沿着混凝土表面滑动而成型的现浇混凝土结构的施工方法的总称。
根据提升动力不同分为电动升模和液压滑膜。
目前滑膜工艺主要应用在筒体结构施工中,同常规施工工艺方法相比,筒仓滑膜施工技术具有施工周期短、速度块、施工成本低、机械化程度高等特点。
本文结合工程实例,对筒仓滑膜施工技术及控制要点进行简单分析。
【关键词】筒仓滑膜;施工技术;控制要点【DOI】10.12334/j.issn.1002-8536.2021.34.0601、引言1.1 滑膜施工技术的应用滑膜施工技术始于本世纪初期,由于液压滑膜千斤顶和集中控制设备的研制成功,四十年代中期在国外得到了较大的发展。
我国在本世纪三十年代,开始试用手动滑膜施工,至七十年代,这项施工工艺开始在全国推广应用,并得到了较快发展。
滑膜施工技术主要应用于水泥行业、热电行业、煤炭行业、水利行业、粮食仓储等,是高层现浇混凝土剪力墙结构和筒体结构采用的主要工业化施工方法之一。
1.2 滑膜施工的优点滑膜施工工艺特点是模板一次组装成型,装拆工序少,模板系统、操作平台系统均使用液压提升系统进行提升,不用再支设模板和搭拆脚手架,可节省大量材料和人工,具有机械化程度高、占用场地少、劳动强度低、综合效益显著的特点,在施工过程中,能连续滑升作业,施工速度块,混凝土连续浇筑,可减少施工缝,工程质量和结构整体性能好,利于满足结构气密、防渗透性要求。
2、滑膜施工技术设计滑膜施工是一种现浇混凝土工程的连续成型施工工艺。
其施工方法是按照施工对象的平面形状,在地面上预先将滑膜装置安装就位,随着不断地绑扎钢筋和分层浇筑混凝土,利用液压提升设备将滑膜装置滑离地面并使其不断的向上滑升,直至达到设计高度为止。
本文以某麦芽厂筒仓工程为例(以下简称本工程):筒仓由3行5列共15个立仓、8个星仓连体组成,总高度为51.5米;立仓直径10米,壁厚为200mm,其中10个为大仓,5个为三分仓;三分仓墙壁厚为200mm;筒仓内设倒圆锥形漏斗,漏斗壁厚为变截面尺寸,厚度分别为400mm和250mm,与筒壁成45°夹角,漏斗在漏斗顶处设置一道环梁,截面尺寸为800x1600mm,顶标高为+8.1米;在+8.1米处,漏斗与筒壁以漏斗环梁连结,漏斗环梁下设有八个扶壁柱,截面尺寸500×800mm,均匀布置,扶壁柱顶标高为+8.1m。
- 1、下载文档前请自行甄别文档内容的完整性,平台不提供额外的编辑、内容补充、找答案等附加服务。
- 2、"仅部分预览"的文档,不可在线预览部分如存在完整性等问题,可反馈申请退款(可完整预览的文档不适用该条件!)。
- 3、如文档侵犯您的权益,请联系客服反馈,我们会尽快为您处理(人工客服工作时间:9:00-18:30)。
浅谈直形挡墙的筒仓滑模施工技术
作者:武清茹
来源:《商品与质量·学术观察》2013年第04期
摘要:带有直形挡墙的混凝土筒仓,是近年来水泥生产工业出现的一种设计优化类型,是将散料储存功能有机结合的一种结构形式,属大直径髙型筒仓。
该类筒仓仓底位置设计较高,筒仓直径较大,仓板以下设有直形挡墙与库壁共同承载仓体及储料荷载(见圆形筒仓剖面示意图)。
因为增加了直形挡墙给筒仓滑模施工带来了很大难度,延长了工期,增加了施工成本。
本技术采用库内直形挡墙先预留插筋滑升至库底板,再二次施工直形挡墙的工艺,较好地解决了该类工程施工工期、成本以及滑模体系造型的突出问题。
关键词:直形挡墙筒仓滑模
1.工艺原理
先用已打好孔的木模板将直形挡墙的水平筋在库壁设计位置固定好(见预留插筋节点详图),再组装滑模模板体系,待库底板以下部位滑完后,边组装环梁模板边施工直形挡墙,既能保证滑模的施工质量又不影响施工工期,库底板以上部位采用适合单仓施工的库壁滑动模板技术体系,在模板构造方面,实现两种模板构造的兼容和相互转换,配合合理的施工工艺和作业方法,完成筒仓库壁和仓体结构的施工。
2.施工工艺流程:
筒仓滑模设计→库壁与直形挡墙预留插筋绑扎→库底板以下部位库壁滑模施工→空滑作业→环梁及直形挡墙施工→库底板施工→库壁筒体滑模施工
3.筒仓滑模体系设计
滑升模板体系设计原则:是保证施工各个阶段模板体系的整体性、稳定性、滑升同步性,保证模板施工的可控可调和滑模体系与预留插筋模板体系的无缝对接。
3.1滑模体系选型
3.1.1库壁在滑升过程中,因千斤顶本身性能存在偏差,易造成滑模体系整体性钢度在一定程度上减小,因此必须对滑模体系进行加强,滑模系统除正常的模板、围檩、提升架、操作平台等组成外,另需加设水平辐射拉杆(见水平辐射拉杆布置平面图)。
3.1.2直形挡墙滑模构造选型:为了便于直形挡墙的二次施工,直形挡墙与库壁相交处的模板要经过特殊处理,在直形挡墙与库壁滑模连接处增加具有竖向开槽的定型模板,以确保滑模体系与预留插筋模板相交处不漏浆不变形。
3.2滑模体系主要构件形式及构造关系
滑模系统由模板、围檩、提升架、提升系统、操作平台等组成。
a.模板:采用3mm厚、高度1200mm 、宽度250mm的钢模板。
库壁与直形挡墙连接处模板采用定型模板。
b.围檩:上下围檩将提升架连成整体,其强度、刚度、截面尺寸应由根据计算确定。
本工程采用[8槽钢制作,上下围檩间距800mm,内外各两道,围檩与模板连接采用8#铅丝绑扎牢固,围檩与门字架连接采用焊接。
上围檩距模板上口距离不大于250mm。
c.提升架:根据筒仓墙壁厚度设计,采用[14槽钢制作,选用门字型。
提升架的布置与千斤顶、支承杆的位置、数量相适应,且满足千斤顶、支承杆允许承载力和模板及围檩的刚度要求。
d.提升系统:
①千斤顶:千斤顶的布置以使千斤顶受力均衡为原则,经计算选用GYD-60型千斤滚珠式液压千斤顶。
其实际布置数大于计算数量,沿筒壁、直形挡墙均匀间距布置。
②支承杆:采用Q235A级钢制作的φ48×3.5钢管,其质量符合《直缝电焊钢管》
GB/T13793和《低压流体输送用焊接钢管》GB/T3092中3号普通钢管规定。
首节支承杆长度为1.5m、3m、4.5m、6m四种交错布置,以使支承杆接头相互错开,其垂直度偏差应不大于1/1000,采用焊接方法接长。
③液压油路设置:
液压控制台:综合考虑千斤顶数量、油路长度、结合回油时间、公称流量等因素选定,本工程选用YHJ-56型液压控制柜。
千斤顶油路:千斤顶布置原则是使每个千斤顶到液压控制台的油路长度基本一致,油路长短相差不超过5%为宜,且每条油路供油的千斤顶数量基本相等。
本工程采用三级并联油路,用一台YZKT-56型液压控制台控制,主油路3路,其中2路到筒仓壁,1路到直形挡墙,由分油器、支分油器再到千斤顶。
主油管采用φ16高压胶管,支油路用φ8高压胶管。
e.操作平台
操作平台分内操作平台和外操作平台,内、外操作平台均采用挑三脚架式操作平台。
采用∟50×5角钢,满铺50mm厚的脚手板,其中内操作平台宽1200mm,外操作平台宽1500mm。
直形挡墙处操作平台宽均为1200mm,与库壁内操作平台连接成整体。
f.拉杆:拉杆采用Φ14圆钢,两端采用4吨花蓝螺杆连接。
g.直形挡墙与库壁交接处节点及整体性措施:
直形挡墙与库壁交接处采用定型模板连接,使直形挡墙与库壁内围圈相互连接成一整体,保证了滑模系统的整体性。
3.3滑模系统设计和计算
滑模系统设计与验算执行应符合《滑动模板工程技术规范》GB50113的规定,采用以下计算方法:
根据仓体结构形式和工程施工图纸,编制详细的《施工组织设计》,按照工艺原理,设计液压提升和控制系统。
通过荷载计算确定所需的千斤顶规格数量,根据千斤顶的数量选用合适的液压控制台,合理选择油路布置方案。
3.3.1仓体周圈墙壁,液压提升系统所需千斤顶和支承杆的最小数量确定:
nmin =N/P0
式中 N—总垂直荷载(kN),应取规范GB50113第5.1.3条中所有竖向荷载之和;
P0—千斤顶或支承杆的允许承载力(kN),支承杆的允许承载力应按GB50113附录B确定,千斤顶的允许承载力为千斤顶额定提升能力的1/2,两者中取其较小者。
3.3.2千斤顶间距计算
千斤顶的布置应使千斤顶受力均衡,布置方式应符合以下规定:①筒体结构沿筒壁均匀布置;②平台上设有固定的较大荷载时,应按实际荷载增加千斤顶数量。
4.库壁滑模体系组装
4.1滑模组装前做好各部件编号、操作平台标记,弹出组装线及各种控制线。
4.2安装提升架,提升架的横梁与立柱必须刚性连接,两者的轴线应在同一平面内,在使用荷载作用下立柱的侧向变形应不大于2mm,提升架横梁上皮至模板顶部的高差为530mm。
4.3安装内外围檩,调整其位置,使其满足模板截面尺寸要求,在每侧模板的背后,上下各设置一道闭合式围檩,其间距一般为800mm,围檩与门字架采用焊接方式连接。
模板与模板之间用U形卡子连接,每侧不少于2个M12紧固螺栓。
特别要注意直形挡墙与内模连接处的加固,保证其连接牢固。
4.4内操作平台通常由承重桁架与平台铺板、栏杆组成,承重桁架与提升架的立柱螺栓连接。
外操作平台由支撑于提升架外立柱的三角挑架与平台铺板,平台外侧置防护栏杆,并在操作平台底部满挂安全网。
安装完挑三角架后,在门式架上安装辐射状水平钢拉杆,钢拉杆与门式架用花篮螺杆连接,调整筒仓模板的椭圆变形。