工件定位与夹紧
4 工件定位与夹紧方案的确定

(4)扩大机床使用范围和改变机床用途
如:铣床加分度头,就可以加工有等分要求的工件。 利用镗模,可以用车床或摇臂钻床镗削箱体的孔系。
12
§4.1.2 机床夹具的分类
按夹具应用范围划分
➢(1)通用夹具 三爪、四爪卡盘、平口钳等,一般由专业 厂生产,常作为机床附件提供给用户。
防转菱形销限制: Z 方向转动自由度
63
4.3 任务3 选择夹具定位元件
➢工件定位时,首先要根据加 工要求,确定工件需要限制 的自由度,选择合适的表面 作为定位基准面。 ➢工件的定位基准面有多种形 式,如平面、外圆柱面、内 孔等。 ➢根据定位基准面的不同,采 用不同的夹具定位元件,使 定位元件的定位面和工件的 定位基准面相接触或配合, 从而实现工件的定位。
顶尖限制: Y、Z 方向转动自 由度
61
过定位问题分析 ➢ 图示工件要在端面加工螺孔时,如何进行定位?
62
➢使用长圆柱销时,X、Y方 向的转动自由度重复限制, 当夹紧时,连杆会产生变形。
短长圆柱销限制: X、 Y 方向的移动自由度 X、 Y 方向的转动自由度
大端面限制: Z 方向的移动自由度 X、 Y 的转动自由度
图4-1 轴套零件图
9
4.1 任务1 认识机床夹具
本节要点
机床夹具的功能 机床夹具在机械加工中的作用 夹具的分类 机床夹具的组成
10
§4.1.1 机床夹具的功能与作用
1.机床夹具的功能
机床夹具的主要功能: ➢定位——工件在夹具中相对于刀具和机床占有正确的加 工位置。 ➢夹紧——把工件压紧夹牢,并保持这个确定的位置在加 工过程中稳定不变。
2)夹紧元件及装置
3)对刀及导向 元件
工件定位与夹紧

互 为基 准的原则
当相关表面位置精度要求很高但精加工余量很小,加工时 要用这些表面互相作为定位基准。
精度高于6级的淬火齿轮,齿形 相对于轴线的位置精度要求很 高,加工需用磨齿工艺。因淬 火后齿轮孔和齿面均产生变形, 而孔和磨齿的加工余量都很小, 故先以齿面为定位基准磨孔; 再以孔为基准磨齿面。 齿面和齿轮孔互为基准。
2. 工艺基准
(3)测量基准
检验零件时,用以测量加工 表面的尺寸、形状、位置等误 差所依据的基准。
图2-47 零件的设计基准与工艺基准示例
2. 工艺基准
(4)装配基准
装配时用以确定零件、组件 和部件相对于其他零件、组件 和部件的位置所采用的基准。
传动轴
键 传动齿轮
图2-48 齿轮的装配基准
(二)精基准及其选择原则
1.机床夹具的组成
(1)定位装置 :是由定位元件及其组合构成的,用于确定 工件在夹具中的正确位置,常见的定位方式是以平面、圆孔、 外圆定位。圆柱销5、菱形销9、支承板4
(2)夹紧装置 : 保持工件在夹具中的确定位置,保证定位 可靠,使工件在切削力的作用下不产生移动。包括夹紧元件、 传动装置及动力装置等。螺杆8、螺母7、开口垫圈6
4) 工件以组合表面定位
图2-68 一面两销定位
一面两孔:在加工箱体类零件时经常采用一面两孔 组合(一个大平面及与该平面相垂直的两个圆孔组合) 定位、夹具上相应的定位元件是一面两销。为了避 免由于过定位而引起的工件安装时的干涉,两销中 一个应采用菱形销。菱形销的宽度可以通过简单的 几何关系导出。
3.常见定位方式及定位元件
9
一、零件的基准及其分类
什么是基准?
基准就是用来确定生产对象 上几何要素间的几何关系所依 据的点、线、面。
工件定位与夹紧

第3章工件定位与夹紧一.简答题:3-1.工件在夹具中定位、夹紧的任务是什么?定位:把工件装好,就是在机床上使工件相对于刀具及机床有正确的位上加工置。
工件只有在这个位置上接受加工,才能保证被加工表面达到所要求的各项技术教育要求。
夹紧:把工件夹牢,就是指定位好的工件,在加工过程中不会受切削力、离心力、冲击、振动等外力的影响而变动位置。
3-2.一批工件在夹具中定位的目的是什么?它与一个工件在加工时的定位有何不同?3-3.何谓重得定位与欠定位?重复定位在哪些情况下不允许出现?欠定位产生的后果是什么?欠定位:按照加工要求应该限制的自由度没有被限制的定位称为欠定位。
欠定位是不允许的。
因为欠定位保证不了加工要求。
重复定位:工件的一个或几个自由度被不同的定位元件重复限制的定位称为过定位。
当过定位导致工件或定位元件变形,影响加工精度时,应该严禁采用。
但当过定位并不影响加工精度,反而对提高加工精度有利时,也可以采用。
3-4.辅助支承起什么作用?使用应注意什么问题?生产中,由于工件形状以及夹紧力、切削力、工件重力等原因可能使工件在定位后还产生变形或定位不稳定。
常需要设置辅助支承。
辅助支承是用来提高工件的支承刚度和稳定性的,起辅助作用,决不允许破坏主要支承的主要定位作用。
各种辅助支承在每次卸下工件后,必须松开,装上工件后再调整和锁紧。
由于采用辅助支承会使夹具结构复杂,操作时间增加,因此当定位基准面精度较高,允许重复定位时,往往用增加固定支承的方法增加支承刚度3-5.选择定位基准时,应遵循哪些原则?定位时据以确定工件在夹具中位置的点、线、面称为定位基准。
定位基准有粗基准和精基准之分。
零件开始加工时,所有的面均未加工,只能以毛坯面作定位基准,这种以毛坯面为定位基准的,称为粗基准,以后的加工,必须以加工过的表面做定位基准,以加工过表面为定位基准的称精基准。
在加工中,首先使用的是粗基准,但在选样定位基准时,为了保证零件的加工精度,首先考虑的是选择精基准,精基准选定以后,再考虑合理地选择粗基准。
工件在数控机床上的定位与装夹
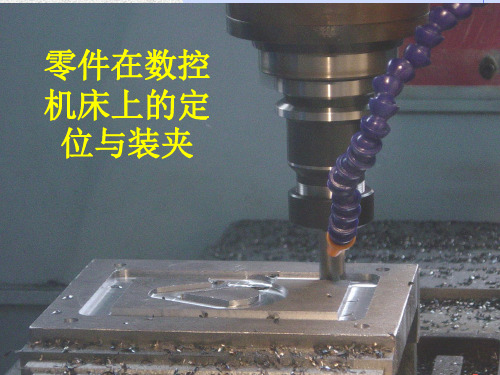
精基准的选择
Ø 在实际生产中,经常使用的统1基准形式有: 1 轴类零件常使用两顶尖孔作统1基准; 2 箱体类零件常使用1面两孔 1个较大的平面和两个距离较
远的销孔 作统1基准; 3 盘套类零件常使用止口面 1端面和1短圆孔 作统1基准; 4 套类零件用1长孔和1止推面作统1基准
Ø 采用统1基准原则好处: 1 有利于保证各加工表面之间的位置精度; 2 可以简化夹具设计,减少工件搬动和翻转次数
a)
b)
c)
图5-2 粗基准选择比较
粗基准的选择
工序1
工序1
工序2
工序2
图5-3 床身粗基准选择比较
重要表面原则
为保证重要表面的加工余量均匀,应选择重要加 工面为粗基准
精基准的选择原则
应保证加工精度和工件安装方便可靠
基准重合原则 基准统1原则 自为基准原则
选用设计基准作为定位基准,避免因基 准不重合带来的误差
课堂讨论
数控车床的装夹找正
Ø 打表找正 通过调整卡爪,使得工件坐标系 的Z轴与数控车床的主轴回转中心轴线重合
Ø 单件的偏心工件 Ø 使用3爪自动定心卡盘装夹较长的工件 Ø 3爪自动定心卡盘的精度不高
7、数控铣床的装夹
通用夹具的选用
平口钳分固定侧与活动侧,固定侧与底面 作为定位面,活动侧用于夹紧
选择平整、光洁、面积大、无飞边毛刺和浇 冒口的表面以便定位准确、夹紧可靠
作为粗基准的表面粗糙且不规则,多次使用 无法保证各加工表面的位置精度
粗基准的选择
◆保证相互位置要求原则——如果首先要求保证工件上加 工面与不加工面的相互位置要求,则应以不加工面作为粗基 准 ◆余量均匀分配原则——如果首先要求保证工件某重要表 面加工余量均匀时,应选择该表面的毛坯面作为粗基准
第三节 工件的定位与夹紧

3.使用四爪单动卡盘时的注意事项 3.使用四爪单动卡盘时的注意事项
• (1)夹持部分不宜过长,一般为 )夹持部分不宜过长,一般为10-15mm比较 比较 事宜。 事宜。 • (2)为防止夹伤工件,装夹已加工表面时应垫铜 )为防止夹伤工件, 皮。 • (3)找正时应在导轨上垫上木板,以防工件掉下 )找正时应在导轨上垫上木板, 来砸伤床面。 来砸伤床面。 • (4)找正时不能同时松开两个卡爪,以防工件掉 )找正时不能同时松开两个卡爪, 下。 • (5)找正时主轴应放在空挡位置,以使卡盘转动 )找正时主轴应放在空挡位置, 轻便。 轻便。 • (6)工件找正后,四个卡爪的夹紧力要基本一致, )工件找正后,四个卡爪的夹紧力要基本一致, 以防车削过程中工作位移。 以防车削过程中工作位移。 • (7)当装夹较大的工件时,切削用量不宜过大。 )当装夹较大的工件时,切削用量两顶尖装夹刚性较差,因此在车削轴类零件,尤其是较重的工件时, 常采用一夹一顶装夹。为了防止工件轴向位移,须在卡盘内装一限位支 撑,见书17页1-15a,或利用工件的台阶作限位,见1-15b。由于一夹一 顶装夹刚性好,轴向定位准确,且比较安全,能承受较大的轴向切削力, 因此应用广泛。
三、用两顶尖定位与夹紧工件
• 1.两顶尖定位的特点及 使用范围
• 两顶尖装夹工件方便,不 需找正,装夹精度高。对 于较长的、须经过多次装 夹的、或工序较多的工件, 为保证装夹精度,可用两 顶尖装夹。(如图) • 用两顶尖装夹工件,必须 先在端面上钻出中心孔。
2.中心孔的种类及适用场合 2.中心孔的种类及适用场合
二、用四爪单动卡盘定位与夹紧工件
• 1.四爪单动卡盘的工作 特点 • 特点:四个卡爪单独 特点: 调节, 调节,装夹工件需要 找正且比较费时。 找正且比较费时。定 位精度可达0.01mm。 位精度可达 。 适用安装圆形、 适用安装圆形、正方 长方形、 形、长方形、内外圆 偏心、 偏心、椭圆形及其它 不规则零件。 不规则零件。加紧力 加紧更可靠。 大,加紧更可靠。
工件的定位与夹紧
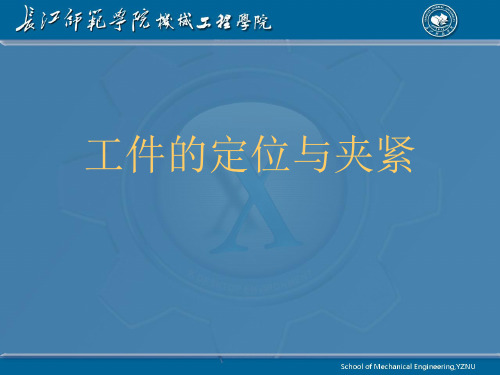
划线找正法示例Leabharlann 图2 划线找正装夹图3 套筒零件简图
1.快换钻套 2.导向套 3.钻模板 4.开口垫圈 5.螺母 6.定位销 7.夹具体
图 4 套筒钻夹具
二、工件的定位 工件的定位
◆六点定位原理
:任一刚体在空间都有六个自由度,为 使工件完全定位,必须有合理分布的 六个定位支承点分别限制其六个自由 度,使工件的位置唯一。
●基准
设计基准 工序基准 工序基准 定位基准( 定位基准(大平面、长圆柱面或轴线) ) 三者重合,提高位置精度
●定位元件 定位元件
◆定位元件的基本要求 ①足够的精度 ②足够的硬度和耐磨性 ③足够的强度和刚度 ④工艺性好
◆平面定位 ◇主要支承 —限制自由度 ①固定支承 —支承钉
支承板 非标支承板 ②可调支承 —一批工件调一次
(原则上不允许)
zz
o
x
y
注:若不限制 y 等 为欠定位,不符要求
图7
完全定位
z
z
y
X
o y
不完全定位
X
图8
x y
后果:
1.心轴 2.支承凸台 3.工件 4.压板
1)机床心轴弯曲 2)工件翘曲变形 图9 插齿时齿坯的定位(过定位) 插齿时齿坯的定位(过定位)
x y
图10 齿坯过定位的影响
改变定位结构避免过定位
Z
x、 y、 z
( y (
z
O
(
z
x 、 y 、z
x ( x
X
(
(
Y y
y
5 4
Z
6
O
y Y
3 2
1
X
图5 长方体定位时支承点的分布
工件在夹具中的定位与夹紧

(3)精基准的选择
主要应保证加工精度和装夹方便
选择精基准一般应遵循以下原则:
1)基准重合原则
设计(工序)与定位
2)基准统一原则
各工序的基准相同
3)互为基准原则
两表面位置精度高
4)自为基准原则
加工余量小而均匀
考虑定位方案时,先分析必须消除哪些自由度, 再以相应定位点去限制。
(3)欠定位与过定位
工件应限制的自由度未被限制的定位,为欠定位, 在实际生产中是绝对不允许的。
工件一个自由度被两个或以上支承点重复限制的 定位称为过定位或重复定位。一般来说也是不合 理的。
过定位造成的后果: (1)使工件或夹具元件变形,引起加工误差; (2)使部分工件不能安装,产生定位干涉(如一面两销)
六点定位原理。
实际中一个定位元件可体现一个或多个支承点, 视具体工作方式及其与工件接触范围大小而定
定位与夹紧的区别: 定位是使工件占有一个正 确的位置,夹紧是使工件保持这个正确位置。
(2)完全定位与不完全定位 工件的六个自由度被完全限制的定位称完全定位, 允许少于六点的定位称为不完全定位。 都是合理的定位方式。
(2)夹紧力作用点的确定 1)夹紧力应作用在刚度较好部位
2)夹紧力作用点应正对支承元件或位于支承元件
形成的支承面内
3)夹紧力作用点应尽可能靠近加工表面
(3)夹紧力大小的估算
夹紧力的大小根据切削力、工件重力的 大小、方向和相互位置关系具体计算,并 乘以安全系数K ,一般精加工K =1.5~2, 粗加工K = 2.5~3。
向上的变动量。由工件定位面和夹具定位元件的制造误差 以及两者之间的间隙所引起。
第一章 工件的定位

32
3、过定位与欠定位
1).分析:工件的定位支 承点少于应限制的自由度 数时,会造成什么后果? 结果:应限制了自由度来 被限制,导致加工时达不 到要求的加工精度。 ① 欠定位:加工中,工件定位点数少于应限制的自由度
数。会产生不良后果。 ② 过定位:工件的某个自由度被限制两次以上。
2).过定位是否允许?一般来说过定位将使工件定位不确定, 夹紧后会使工件或定位元件产生变形。
②过定位不一定就是完全定位? ③多于六个定位点的定位一定是过定位?
38
4、应用六点定位原则应注意的问题 1)方法问题:
①根据工序加工技术要求和工件形状的特点,确 定应限制 那些自由度,而用相应的定位点数目去消除。 ②分析时也可反过来分析哪几个自由度可不必限 制,剩下 的就是要限制的了。
(2)过定位有时是允许的,而欠定位决不允许,欠定位的 后果只导致加工时达不到加工精度。 过定位优点:使定位可能更为可靠,如冰箱有四个支 承点。 缺点:易使工件的定位精度受影响,使工件或夹具夹 39 紧后产生变形。
②优点:夹具结构简单,可避免因夹具本身的制造误差而产生
的定位误差,因此,定位精度高。 如:加工误差 < 0.01~0.005mm,采用夹具加工难以达到。 适用场合:单件小批生产中(如工具修理车间)。
(2)划线找正安装
对重、大、复杂工件的加工,往往是在待加工处划 线,然后
6 装上机床,工件在机床或夹具上位置按所 划的线进行找正定位。
10
11
三、机床夹具的分类 1、分类方法:
1)按夹具的应用范围:通用夹具、专用夹具、可调夹具、组合 夹具、随行夹具; 2)按加工类型:车床夹具、钻床夹具、镗床夹具、磨床夹具、 数控机床夹具等; 3)按夹紧力来源:手动夹具、气动夹具、液压夹具、电磁夹具、 真空夹具。 机床夹具通常按夹具的应用范围进行。
第3章工件的定位与夹紧
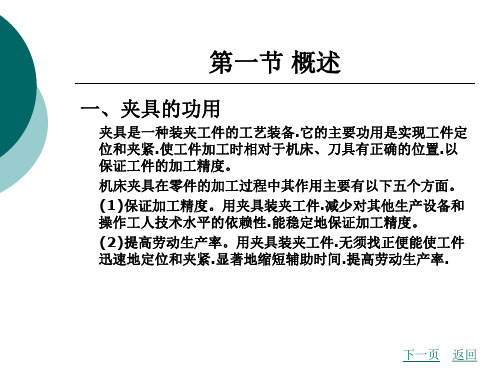
上一页 下一页 返回
第一节 概述
二、机床夹具的分类
机床夹具的种类繁多.可以从不同的角度对机床夹具进行分类。 常用的分类方法有以下几种。 1.按夹具的使用特点分类 (1)通用夹具已经标准化的.可加工一定范围内不同工件的夹 具.称为通用夹具. (2)专用夹具专为某一工件的某道工序设计制造的夹具.称为 专用夹具 (3)可调夹具。夹具的某些元件可调整或可更换.以适应多种 工件加工的夹具.称为可调夹具. (4)组合夹具。采用标准的组合夹具元件、部件.专为某一工 件的某道工序组装的夹具.称为组合夹具。 (5)拼装夹具。用专门的标准化、系列化的拼装夹具零部件 拼装而成的夹具.称为拼装夹具.
上一页 下一页 返回
第二节 工件定位原理
四、限制工件自由度与加工要求的关系
1.完全定位 工件在夹具体上六个自由度完全限制.称为完全定位。 2.不完全定位 这种根据加工要求.允许某些自由度不限制的定位称为“‘不 完全定位”。 3.欠定位 在满足加工要求的前提下.采用不完全定位是允许的。但是应 该限制的自由度.没有布置适当的支承点加以限制.这种定位 称为欠定位。 4.必须正确处理过定位 夹具上的定位元件重复限制工件的同一个或几个自由度.这种 重复限制工件自由度的定位称为过定位。
第一节 概述
一、夹具的功用
夹具是一种装夹工件的工艺装备.它的主要功用是实现工件定 位和夹紧.使工件加工时相对于机床、刀具有正确的位置.以 保证工件的加工精度。 机床夹具在零件的加工过程中其作用主要有以下五个方面。 (1)保证加工精度。用夹具装夹工件.减少对其他生产设备和 操作工人技术水平的依赖性.能稳定地保证加工精度。 (2)提高劳动生产率。用夹具装夹工件.无须找正便能使工件 迅速地定位和夹紧.显著地缩短辅助时间.提高劳动生产率.
项目3:机械加工的工件装夹
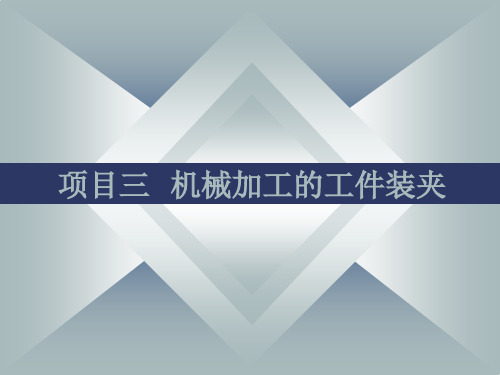
3.夹紧装置结构要简单,制造容易,体积小, 强度、 刚度要足够,能确保加工时工件定位的稳定、可靠 不发生振动。
4.夹紧装置操作应方便、安全、省力、夹紧动作迅速。
5.应有足够的夹紧行程和装卸工件的间隙。
1) 夹紧力的方向应有助于定位稳定,且主夹紧力朝向 主要定位基准面 (限制自由度最多或定位精度要求高 的定位面)。
1.完全定位 工件的六个自由度全部被限制的定位状态,称 为完全定位。当工件在三个坐标方向均有尺寸或位置精度要 求时,一般采用这种定位方式。
2.不完全定位 工件被限制的自由度数目少于六个,但能保 证加工要求时的定位状态。工件在夹具中定位时,广泛采用 不完全定位。
3.欠定位 工件实际定位所限制的自由度少于按其加工要求 所必须限制的自由度,这种定位状态称为欠定位。由于在欠 定位状态下对工件进行加工,无法保证其工序加工要求,因 此,在确定工件的定位方案时,不允许采用欠定位方式。
四、机床夹具的组成 1.定位装置 定位元件及其组合构成定位装置,其作用是确定工件在 夹具中的位置。 2.夹紧装置 夹紧装置的作用是保证工件在夹具中的准确位置不会因 外力作用而发生变化,使加工顺利进行。 3.连接元件 连接元件用以确定夹具本身在机床上的位置,如车床夹 具所使用的过渡盘,铣床夹具所使用的定位键等都是连接元件。 4.导向、对刀元件 确定刀具位置并引导刀具进行加工时需要使用导 向元件,如钻床夹具上的钻套、镗床夹具中的镗套;而铣床夹具中的 对刀块是典型的对刀元件,根据它来快速调整刀具相对于夹具的位置 。 5.其它装置或元件 为了满足加工要求及提高夹具的使用性能,有些 夹具上还设有分度装置、靠模装置、预定位装置、上下料装置、顶出 装置、平衡块、吊装元件等。 6.夹具体 夹具体是夹具的基础件,上述元件或装置在夹具体上安装 后组成一个有机整体,以实现夹具在机械加工过程中的作用。
第8章(1-2)机床夹具的基本概念和工件的定位与定位误差

2、由于加工精度要求,不必限制所有自由度
(三)欠定位:工件在夹具中定位时,若定位 支承点数目少于工序加工所要求的数目,工 件定位不足,称为欠定位。
(四)重复定位:工件在夹具中定位时,若几 个定位支承点重复限制一个或几个自由度, 称为重复定位(超定位)。
*当以形、位精度较低的毛坯面定位时,不允 许重复定位。 *为提高定位稳定性和刚度,以加工过的表面 定位时,可以出现重复定位。
=
d 1 (1 ) 2 sin 2
2)尺寸H2的定位误差 设计基准 为C,定位基准为A,其最大的位 置变动量为 C1C2 即定位误差:
H C1C2 AC2 AC1
2
( AO2 O2C2 ) ( AO1 O1C1 )
3)尺寸H3的定位误差 设计基准 = 为O,定位基准为A,其最大的 位置变动量为 O1O2 即定位误差:
计算得到,根据一批工件的定位由一种可能的极端 位置变为另一种极端位置时δ位置和δ不重的方向的异 同,以确定公式中的加减号。
(二)几种典型表面定位时的定位误差 1、平面定位时的定位误差 *毛坯表面定位: 由于实际表面相 对于其理想位置 有较大的变动范 围,存在基准位 置误差。
δ定位(H)= δ位置(M)
分析:机床保证 了小孔与销的轴线 之间的尺寸,但因 销孔之间存在间隙, 销、孔、外圆均存 在尺寸误差,均会 引起尺寸H的变化。 Hmax:当销最小、 孔最大、外圆最大, 销孔右边接触 Hmin:当销最小、 孔最大、外圆最小, 销孔左边接触
例:孔—销配合例子
基准位置误差δ位置(O):定位基准O相对于其 理想位置O’的最大变动量
(2)对定误差δ对定:与夹具相对于刀具及
切削成形运动有关的加工误差。 包括: 对刀误差δ对刀:夹具相对于刀具位置有关的
第三章工件的定位与夹紧
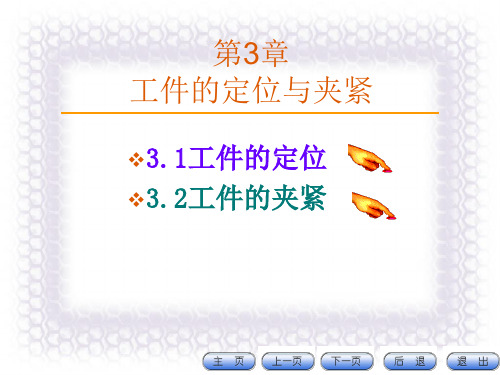
b)测量基准——工件在测量、检验时所 使用的基准。 c)工序基准——在工序简图上用来确定 本工序加工表面加工后的尺寸、形状、位 置的基准。 d)装配基准——装配时用来确定零件或 部件在产品中的相对位置所采用的基准。 零件上的基准通常就是零件表面上具体存 在的一些点、线、面,但也可以是一些假 定的点、线、面,如孔或轴的中心线、槽 的对称面等。这些假定的基准,必须由零 件上某些相应的具体表面来体现,这些表 面称为基准面。
图 直接找正法示例 a)磨内孔时工件的找正 b)刨槽时工件的找正
图 划线找正法示例
❖ 利用夹具定位法——将工件直接安装在夹 具的定位元件上的方法
❖ 特点: ①工件在夹具中的正确定位,是通 过工件上的定位基准面与夹具上的定位元 件相接触而实现的。因此,不再需要找正 便可将工件夹紧。 ②由于夹具预先在机床 上已调整好位置,因此,工件通过夹具相 对于机床也就占有了正确的位置 ③通过夹 具上的对刀装置,保证了工件加工表面相 对于刀具的正确位置。
(1)基准及其分类 用来确定生产对象上几何要素间的几何关系 所依据的那些点、线、面称为基准。基准分 为设计基准和工艺基准,工艺基准又分为定 位基准、测量基准、工序基准和装配基准。
1)设计基准——设计图样上所采用的基准。 它是标注设计尺寸的起点,或中心线、对称 线、圆心等。 2)工艺基准——在工艺过程中所采用的基准。 a)定位基准——在加工中用作定位的基准。 它的位置既表明了工件在机床或夹具上的位 置,用该基准可以使工件在机床或夹具上占 据确定的位置。工件在机床或夹具上定位时, 定位基准就是工件上直接与机床或夹具的定 位元件相接触的点、线、面。定位基准又分 为粗基准(没经过切削加工的毛坯面)和精 基准(经过切削加工的表面)。
c)可调支承:高度可以调节的支承,一个 可调支承限制工件一个自由度。 主要用于以制造精度不高的毛坯面定位的场 合。
第3章 工件的定位和夹紧

3.3 工件方式及定位元件
(a)平顶支承钉;(b)圆顶支承钉 ; (c)网纹顶支承钉; (d)带衬套支承钉 图3-8 几种常用支承钉
3.3 工件方式及定位元件
(a) 为平板式支承板;(b)斜槽式支承板 图3-9 两种常用的支承板
3.3 工件方式及定位元件
(2)可调支承。可调支承的顶端位置可以在一定的范围内调 整。如图3-10所示为几种常用的可调支承典型结构。
图3-6 常见的几种过定位实例
3.2 工件的定位
( 复限制而出现过定位。此时可采取如下措施解决。
No Image
No Image
如图3-6(b)所示为孔与端面联合定位。由于大端面可以限制3个自由度 受到重 、 、 ),而长销可以限制 4 个自由度( x 、 z 、 、 ),因此,、 z z z
此外,按使用机床类型可分为车床夹具、铣床夹具、钻床夹 具、镗床夹具、磨床夹具、齿轮机床夹具和其他机床夹具等。按 驱动夹具工作的动力源可分为气动夹具、液压夹具、气液夹具、 电动夹具、磁力夹具和真空夹具等。
3.1 机床夹具概述
四、机床夹具的组成
机床夹具通常由定位元件、夹紧装置、安装连接元件、导向 元件、对刀元件和夹具体等几个部分组成,如图3-1所示。
3.2 工件的定位
三、定位的类型
1.完全定位与不完全定位
(1)完全定位。工件的6个自由度完全被限制的定位情况, 如图3-4(c)所示。
(2)不完全定位。工件的6个自由度不需完全被限制的定位 情况,如图3-4(a)和图3-4(b)所示。
完全定位和不完全定位,这两种定位类型都是正确可行的, 生产中被广泛采用。
3.4 工件的夹紧
二、夹紧装置的组成
夹紧装置的组成,如图3-23所示,由以下3部分组成。
工件在夹具中的定位与夹紧讲稿课件

用,降低夹具制造过程中的能耗和资源消耗。
THANKS 感谢观看
课程目标
01
02
03
04
掌握工件在夹具中的定位原理 和方法
理解夹紧力的作用和计算方法
学习常见定位与夹紧机构的组 成和工作原理
了解定位与夹紧误差的分析和 补偿方法
02 工件定位原理
定位要素
01
02
03
基准点
工件上的确定位置,用作 确定工件在夹具中的位置 。
定位元件
夹具中用于限制工件自由 度的元件。
按孔定位
根据工件上的孔的形状和位置, 选择相应的定位元件进行定位。
按外轮廓定位
根据工件的外轮廓形状和位置, 选择相应的定位元件进行定位。
03 夹具设计基础
夹具的组成
01
02
03
04
定位元件
用于确定工件在夹具中的位置 ,通常由导轨、挡块、定位销
等组成。
夹紧机构
用于将工件固定在夹具中的装 置,通常由气动或液压系统驱
定位系统
由基准点和定位元件组成 的系统,用于确定工件在 夹具中的位置。
定位原理
完全定位
工件的六个自由度都被限 制,可以确定工件在夹具 中的精确位置。
不完全定位
工件的自由度没有被全部 限制,部分自由度没有被 限制。
欠定位
工件的自由度没有被全部 限制,部分自由度被限制 。
定位方法
按加工面定位
根据工件加工面的位置和形状, 选择相应的定位元件进行定位。
02
柔性化与模块化设计
为了适应多品种、小批量的生产需求,工件定位与夹紧技术正朝着柔性
化和模块化方向发展。通过采用可重构的夹具系统,实现快速更换和调
工件的装夹指的是工件的定位和夹紧
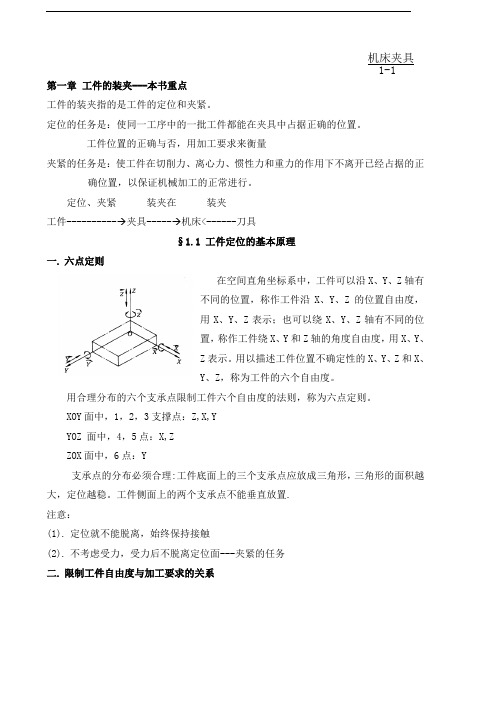
第一章工件的装夹---本书重点工件的装夹指的是工件的定位和夹紧。
定位的任务是:使同一工序中的一批工件都能在夹具中占据正确的位置。
工件位置的正确与否,用加工要求来衡量夹紧的任务是:使工件在切削力、离心力、惯性力和重力的作用下不离开已经占据的正确位置,以保证机械加工的正常进行。
定位、夹紧装夹在装夹工件----------→夹具-----→机床<------刀具§1.1 工件定位的基本原理一. 六点定则在空间直角坐标系中,工件可以沿X、Y、Z轴有不同的位置,称作工件沿X、Y、Z的位置自由度,用X、Y、Z表示;也可以绕X、Y、Z轴有不同的位置,称作工件绕X、Y和Z轴的角度自由度,用X、Y、Z表示。
用以描述工件位置不确定性的X、Y、Z和X、Y、Z,称为工件的六个自由度。
用合理分布的六个支承点限制工件六个自由度的法则,称为六点定则。
XOY面中,1,2,3支撑点:Z,X,YYOZ 面中,4,5点:X,ZZOX面中,6点:Y支承点的分布必须合理:工件底面上的三个支承点应放成三角形,三角形的面积越大,定位越稳。
工件侧面上的两个支承点不能垂直放置.注意:(1).定位就不能脱离,始终保持接触(2).不考虑受力,受力后不脱离定位面---夹紧的任务二. 限制工件自由度与加工要求的关系按照加工要求确定工件必须限制的自由度,在夹具设计中是首先要解决的问题。
加工要求-→工件需要限制的自由度<---→定位元件的选择表1-2 满足加工要求必须限制的自由度1.完全定位:工件的六个自由度都限制了的定位称为完全定位。
2.不完全定位:工件被限制的自由度少于六个,但能保证加工要求的定位。
在工件定位时,以下几种情况允许不完全定位:l)加工通孔或通槽时,沿贯通钢的位置自由度可不限制。
2)毛坯(本工序加工前)是轴对称时,绕对称轴的角度自由度可不限制。
3)加工贯通的平面时,除可不限制沿两个贯通轴的位置自由度外,还可不限制绕垂直加工面的轴的角度自由度。
机床夹具概述和工件的定位与夹紧教案课程

3、按驱动夹具工作的动力源分类可分为:手动夹具、液压夹具、气动夹具、电动夹具等。
3.1.3 机床夹具的组成夹具的组成(1)定位元件 (图)定位元件保证工件在夹具中处于正确的位置。
(2)夹紧装置 (图)夹紧装置的作用是将工件压紧夹牢,保证工件在加工过程中受到外力(切削力等)作用时不离开已经占据的正确位置。
(3) 对刀或导向装置对刀或导向装置用于确定刀具相对于定位元件的正确位置。
(4) 连接元件连接元件是确定夹具在机床上正确位置的元件。
(5) 夹具体夹具体是机床夹具的基础件,(6) 其它装置或元件它们是指夹具中因特殊需要而设置的装置或元件。
若需加工按一定规律分布的多个表面时,常设置分度装置;为了能方便、准确地定位,常设置预定位装置;对于大型夹具,常设置吊装元件等。
3.1.4 机床夹具的作用1、保证加工精度,稳定加工质量。
2、扩大机床的功能3、提高劳动生产率。
4、降低生产成本。
5、改善劳动条件,降低对工人的技术要求。
3.2.1工件的定位1、工件常用的定位方法:(1) 直接找正法概念:用划针、百分表等工具直接找正工件位置并加以夹紧的方法称直接找正法。
特点:生产率低,精度取决于工人的技术水平和测量工具的精度(2) 划线找正法概念:先用划针画出要加工表面的位置,再按划线用划针找正工件在机床上的位置并加以夹紧。
特点:费时,又需要技术高的划线工(3)在夹具上定位使用概念:使用通用或专用夹具,使工件在机床夹具中迅速有一确定的定位,不需要找正就能保证工件与机床、刀具间的正确位置。
特点:生产效率高,定位精度好,应用与成批以及单件小批量生产中。
2、工件定位的基本原理(1)六点定位原理工件的六个自由度长方体形工件的定位①、概念:用合理分布的六个支承点限制工件六个自由度的法则,称为六点定位原理。
②、“六点定位原理”应注意:1) 定位支承点限制工件自由度的作用,应理解为定位支承点与工件定位基准面始终保持紧贴接触。
2) 一个定位支承点仅限制一个自由度,一个工件仅有六个自由度,所设置的定位支承点数目,原则上不应超过六个。
- 1、下载文档前请自行甄别文档内容的完整性,平台不提供额外的编辑、内容补充、找答案等附加服务。
- 2、"仅部分预览"的文档,不可在线预览部分如存在完整性等问题,可反馈申请退款(可完整预览的文档不适用该条件!)。
- 3、如文档侵犯您的权益,请联系客服反馈,我们会尽快为您处理(人工客服工作时间:9:00-18:30)。
第3章工件定位与夹紧
一.简答题:
3-1.工件在夹具中定位、夹紧的任务是什么?
定位:把工件装好,就是在机床上使工件相对于刀具及机床有正确的位上加工置。
工件只有在这个位置上接受加工,才能保证被加工表面达到所要求的各项技术教育要求。
夹紧:把工件夹牢,就是指定位好的工件,在加工过程中不会受切削力、离心力、冲击、振动等外力的影响而变动位置。
3-2.一批工件在夹具中定位的目的是什么?它与一个工件在加工时的定位有何不同?
3-3.何谓重得定位与欠定位?重复定位在哪些情况下不允许出现?欠定位产生的后果是什么?
欠定位:按照加工要求应该限制的自由度没有被限制的定位称为欠定位。
欠定位是不允许的。
因为欠定位保证不了加工要求。
重复定位:工件的一个或几个自由度被不同的定位元件重复限制的定位称为过定位。
当过定位导致工件或定位元件变形,影响加工精度时,应该严禁采用。
但当过定位并不影响加工精度,反而对提高加工精度有利时,也可以采用。
3-4.辅助支承起什么作用?使用应注意什么问题?
生产中,由于工件形状以及夹紧力、切削力、工件重力等原因可能使工件在定位后还产生变形或定位不稳定。
常需要设置辅助支承。
辅助支承是用来提高工件的支承刚度和稳定性的,起辅助作用,决不允许破坏主要支承的主要定位作用。
各种辅助支承在每次卸下工件后,必须松开,装上工件后再调整和锁紧。
由于采用辅助支承会使夹具结构复杂,操作时间增加,因此当定位基准面精度较高,允许重复定位时,往往用增加固定支承的方法增加支承刚度
3-5.选择定位基准时,应遵循哪些原则?
定位时据以确定工件在夹具中位置的点、线、面称为定位基准。
定位基准有粗基准和精基准之分。
零件开始加工时,所有的面均未加工,只能以毛坯面作定位基准,这种以毛坯面为定位基准的,称为粗基准,以后的加工,必须以加工过的表面做定位基准,以加工过表面为定位基准的称精基准。
在加工中,首先使用的是粗基准,但在选样定位基准时,为了保证零件的加工精度,首先考虑的是选择精基准,精基准选定以后,再考虑合理地选择粗基准。
3-6.夹紧装置设计的基本要求是什么?确定夹紧力的方向和作用点的原则有哪些?
夹紧机构应满足下面要求:
1. 夹紧过程中,必须保证定位准确可靠,而不破坏原有的定位。
2. 夹紧力的大小要可靠、适应,既要保证工件在整个加工过程中位置稳定不变、振动小,又要使工件不产生过大的夹紧变形。
3. 夹紧装置的自动化和复杂程度应与生产类型相适应,在保证生产效率的前提下,其结构要力求简单,工艺性好,便于制造和维修。
4. 夹紧装置应具有良好的自锁性能,以保证在源动力波动或消失后,仍能保持夹紧状态。
5. 夹紧装置的操作应当方便、安全、省力。
1. 夹紧力方向的确定原则
夹紧力的作用方向不仅影响加工精度,而且还影响夹紧的实际效果。
具体应考虑如下几
点:
(1)夹紧力的作用方向应保证定位准确可靠,而不破坏工件的原有定位精度
工件在夹紧力作用下,应确保其定位基面贴在定位元件的工作表面上。
为此要求主夹紧力的方向应指向主要定位基准面,其余夹紧力方向应指向工件的定位支承。
(2)夹紧力的作用方向应使工件的夹紧变形尽量小
(3)夹紧力作用方向应使所需夹紧力尽可能小
2. 选择夹紧力作用点的原则
夹紧力作用点的位置、数目及布局同样应遵循保证工件夹紧稳定、可靠、不破坏工件原来的定位以及夹紧变形尽量小的原则,具体应考虑如下几点:
(1)夹紧力作用点应能保持工件定位稳固而不至引起工件发生位移或偏转。
(2) 夹紧力作用点应使夹紧变形尽量小
(3)夹紧力的作用点应保证定位稳定、夹紧可靠。
3-7.何谓联动夹紧机构?设计联运夹紧机构时应注意哪些问题?
联动夹紧是指操纵一个手柄或利用一个动力装置,就能对一个工件的同一方向或不同方向的多点进行均匀夹紧,或同时夹紧若干个工件。
3-8.夹具体的结构型式有几种?
二.定位分析题:
1.根据工件的加工要求,确定工件在夹具中定位时应限制的自由度。
3-9.如题3-69图所示,镗фD孔。
其余表面已加工。
、、、
3-10 如题3-70图所示,加工尺寸为41±0.1mm、角度450±10ˊ的斜面,其余尺寸均已加工。
图3-69 图3-70
、、、、、
3-11.如题3-71图所示,同时钻2-фd孔,A面、фD均已加工。
、、、、
3-12.如题3-72图所示,钻фd孔,A面、фD均已加工。
、、、、
图3-71 图3-72
3-13.如题3-73图所示,在一个夹具上钻、铰ф8H7及ф6H7孔,其余表面均已加工。
、、、、、
3-14.如题3-74图所示,加工ф8+00.05mm孔,其余表面均已加工。
图3-73 图3-74
、、、、
2.试确定各定位元件限制了工件哪几个自由度?分别属于哪种定位方式?
3-15.如题3-75图所示,钻孔фC。
图3-75
两个短v形块限制:、、、
支撑钉限制:
菱形销限制:
属于完全定位。
3-16.如图3-76所示,镗前面大孔。
图3-76
支撑板:、、
支撑钉:
菱形销:、
属于完全定位。
3-17.如题3-77——图3-78图所示。
图3-77 图3-78 图3-77 :
定位块:、、
两v形块:、、
属于完全定位。
图3-78:
底面:、、
圆柱销:、
浮动v形块:
属于完全定位。
三.夹紧分析题:
3-18.试分析图示各夹紧机构中夹紧力的方向和作用点是否合理?若不合理应如何改进?
图3-79
(a)Fw方向不合理,Fw应朝向主要定位基面。
(在上表面朝下夹紧)
(b)Fw作用点不合理,易使工件变形,改为上面两个端口处。
(c)Fw作用点不合理,易破坏定位,Fw指向大定位钉中心处。
(d)Fw作用点不合理,易变形,作用在刚性较好的部位。
(e)作用点不合理,右端螺杆作用点移到左端支撑的中心处。
(f)Fw方向不合理,应从右向左夹紧。
3-19.试分析图示的各夹紧机构是否合理?怎样改进?
(a)不合理,增加压块,参看图3-48(a)。
(b)不合理,左端螺杆部位离加工表面太远,应改为向上些,同时底部支撑的右边挡块加高。
(c)不合理,上不两个压块容易造成只有一个能夹紧,改为摆动压块。
(d)不合理,夹紧力作用在工件刚性较差部位,易变形,改为作用在工件圆周壁处。
图3-80。