密闭电石炉原料质量影响分析
密闭电石炉安全生产重点防控措施
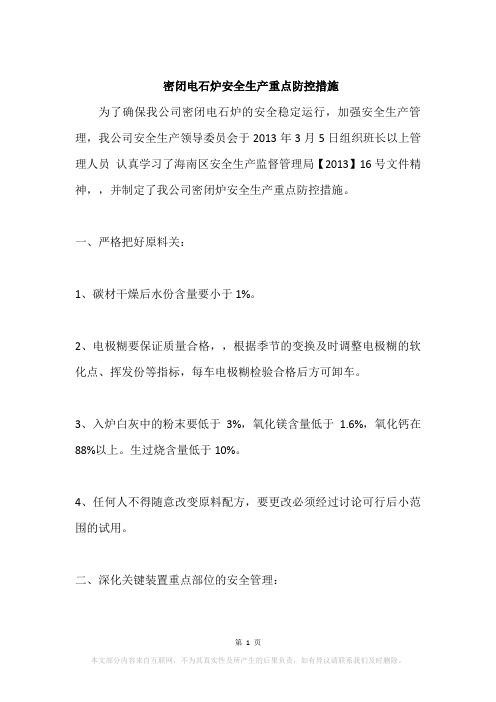
密闭电石炉安全生产重点防控措施为了确保我公司密闭电石炉的安全稳定运行,加强安全生产管理,我公司安全生产领导委员会于2013年3月5日组织班长以上管理人员认真学习了海南区安全生产监督管理局【2013】16号文件精神,,并制定了我公司密闭炉安全生产重点防控措施。
一、严格把好原料关:1、碳材干燥后水份含量要小于1%。
2、电极糊要保证质量合格,,根据季节的变换及时调整电极糊的软化点、挥发份等指标,每车电极糊检验合格后方可卸车。
3、入炉白灰中的粉末要低于3%,氧化镁含量低于1.6%,氧化钙在88%以上。
生过烧含量低于10%。
4、任何人不得随意改变原料配方,要更改必须经过讨论可行后小范围的试用。
二、深化关键装置重点部位的安全管理:5、由于密闭电石炉容量大,须采用有调压开关,在操作时尽可能的少调整电压,以增加调压开关的寿命。
6、依据公司设备检查制度和岗位检查制度,维修工和巡检工要检查水冷系统中的每个环节是否漏水和烧损情况,中控工要时刻注意各水路温度显示是否正常,班长要定时测定电极长度和入炉深度,检查绝缘好坏,如发现有隐患要及时处理,必要时要停炉停电检修。
7、维修工和巡检工要定期、不定期检查油压系统,要保证无渗漏,发现隐患要及时处理。
8、班长和巡检工要定时检查环型给料器的运行情况,对所有料仓要保证料位达到下锥体以上,避免炉气从料管进入料仓,造成巡检工作业空间一氧化碳气超标而造成危险。
9、要定期检查料柱使用情况,烧损到不能用时要及时更换,防止料面上升影响电极插入深度和电极绝缘造成炉盖和其它设备损坏。
10、中控工要控制好炉压,保持炉压在正负10Pa以内。
三、加强应急安全管理:11、设置炉气中氢气、氧气、一氧化碳分析的在线监测仪,电石炉DCS监控系统设置氢气、氧气高报、超高报声光报警信号,实现联锁停车,定期进行检测校验保证数据准确。
电石炉正常运行时氢气含量在12%以下,氧气在1%以下,当氢气含量突然增加同时炉内压力也增加时,要立即停电检查炉内是否漏水,严禁升降电极和开炉门,及时把人员撤离炉面。
密闭电石炉原料质量影响分析

原料分析石灰石的工艺指标生石灰的工艺指标焦炭的工艺指标灰分每增加1%电耗增加50~60度/吨;水分每增加1%电耗增加12度/吨;挥发分每增加1%电耗增加2.3~3.5度/吨;生烧率每增加1%电耗增加10度/吨。
1.理论配比:电石生成反应式CaO+3C==CaC2+CO56 36 64X=36÷64×100×B÷C+F/56÷64×100×B÷A+D+E式中:A――石灰中所含的氧化钙(CaO%);B――电石成分(CaC2%);C――碳素原料中所含的固定碳(C%);D――电石中游离氧化钙的含量;E――投炉石灰损失量(kg);F――投炉碳素原料的损失量(kg)。
X――炉料干基配比炉料湿基配比为:X(湿)=X/(1-水份)根据理论配比,计算出碳材固定碳每降低1%,每吨电石大约多消耗10公斤碳素。
2.生产中,在进行电石生成反应的同时,进行着如下副反应:CaC2=Ca+2C-60.7kJCaCO3=CaO+CO2-178kJCO2+C=2CO-164kJH2O+C=CO+H2-166kJCa(OH)2=CaO+H2O-109kJCa2SiO4=2CaO+SiO2-121kJSiO2+2C=Si+2CO-574kJFe2O3+3C=2Fe+3CO-452kJAl2O3+3C=2Al+3CO-1218kJMgO+C=Mg+CO-486kJ上述反应大部分是原料中带进的杂质所引起的。
发生这些副反应时,不但要消耗碳材和电能,而且有碍电石生成的反应过程,对生产是十分有害的。
3. 原料中杂质的影响原料中的杂质主要包括氧化镁、氧化硅、氧化铁、氧化铝等。
当炉料在电炉内反应生成碳化钙的同时,各种杂质也进行反应:SiO 2+2C=Si+2CO-574kJFe 2O 3+3C=2Fe+3CO-452kJAl 2O 3+3C=2Al+3CO-1218kJMgO +C =Mg +CO-486kJ上述反应不仅消耗电能和碳材,而且影响操作,破坏炉底,特别是氧化镁在熔融区迅速还原成金属镁,而使熔融区成为一个强烈的高温还原区,镁蒸气从这个炽热的区域大量逸出时,其中一部分镁与一氧化碳立即起反应,生成氧化镁:Mg +CO =MgO +C +489kJ此时,由于反应放出强热形成高温,局部硬壳遭到破坏,使带有杂质(Si 、Fe 、Al 、Mg )的液态电石侵蚀了炉底。
电石炉炉况不稳原因分析
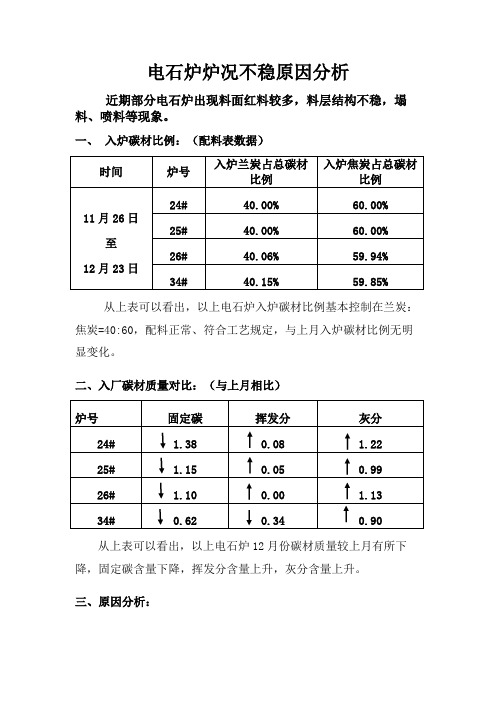
电石炉炉况不稳原因分析近期部分电石炉出现料面红料较多,料层结构不稳,塌料、喷料等现象。
一、入炉碳材比例:(配料表数据)从上表可以看出,以上电石炉入炉碳材比例基本控制在兰炭:焦炭=40:60,配料正常、符合工艺规定,与上月入炉碳材比例无明显变化。
二、入厂碳材质量对比:(与上月相比)从上表可以看出,以上电石炉12月份碳材质量较上月有所下降,固定碳含量下降,挥发分含量上升,灰分含量上升。
三、原因分析:1、入炉碳材固定碳含量下降,导致电石炉炉料配比降低,电石质量也随之降低。
而碳材中挥发分容易在反应区形成半融粘结状,使反应区物料下落困难,容易引起喷料现象发生,使热损失增加。
碳材中灰分的增加不但消耗碳素,而且导致电石质量下降。
2、电石炉停电频繁且停电时间比较长,长时间停电导致电石炉炉温较低,而送电后负荷提升较快导致电极上升,料面温度随之上升,液态电石翻腾厉害,塌料、喷料等随之出现。
3、电石炉漏水频繁,加之原料对入炉碳材水分控制不稳,导致炉内水分较高,石灰粉化产生粉末较多(且根据原料车间反应,近期进厂石灰粒度较小),电石炉塌料频繁,料面温度随之上升,支路电流增大,电极位置升高,而炉底温度反而降低,所以导致料面红料多,电石翻腾厉害。
4、电极工作长度较短且不稳定,从而导致电石炉料层不稳,塌料频繁,电极电流无法控制,长此以往导致电极上抬严重,炉底温度下降,电石翻腾厉害。
5、炉料配比调整频繁,导致电石质量波动较大,从而引起电极无法深入炉内或入炉太深。
6、料面处理还是不够彻底,捣、抅、扒做的都不够到位,且料面积灰清理不干净。
四、处理方法:1、首先,各电石炉加强设备的检修及巡检工作,减少非计划停车,尤其杜绝电石炉长时间停电。
2、各车间加强工艺操作,控制好电极电流,电极电流超标只会引起支路电流增加,料面温度升高、电极上抬,不利于生产正常运行。
3、电石炉长时间停电后负荷提升不宜太快,应按照负荷提升表进行负荷提升。
4、各车间应稳定炉料配比,尽量不要频繁调整配比,以免引起电石质量及炉况大幅度波动。
电石炉炉况不稳原因分析
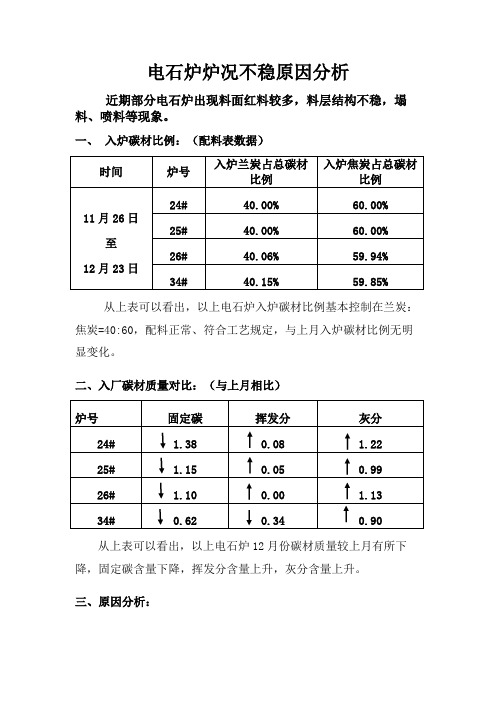
电石炉炉况不稳原因分析近期部分电石炉出现料面红料较多,料层结构不稳,塌料、喷料等现象。
一、入炉碳材比例:(配料表数据)从上表可以看出,以上电石炉入炉碳材比例基本控制在兰炭:焦炭=40:60,配料正常、符合工艺规定,与上月入炉碳材比例无明显变化。
二、入厂碳材质量对比:(与上月相比)从上表可以看出,以上电石炉12月份碳材质量较上月有所下降,固定碳含量下降,挥发分含量上升,灰分含量上升。
三、原因分析:1、入炉碳材固定碳含量下降,导致电石炉炉料配比降低,电石质量也随之降低。
而碳材中挥发分容易在反应区形成半融粘结状,使反应区物料下落困难,容易引起喷料现象发生,使热损失增加。
碳材中灰分的增加不但消耗碳素,而且导致电石质量下降。
2、电石炉停电频繁且停电时间比较长,长时间停电导致电石炉炉温较低,而送电后负荷提升较快导致电极上升,料面温度随之上升,液态电石翻腾厉害,塌料、喷料等随之出现。
3、电石炉漏水频繁,加之原料对入炉碳材水分控制不稳,导致炉内水分较高,石灰粉化产生粉末较多(且根据原料车间反应,近期进厂石灰粒度较小),电石炉塌料频繁,料面温度随之上升,支路电流增大,电极位置升高,而炉底温度反而降低,所以导致料面红料多,电石翻腾厉害。
4、电极工作长度较短且不稳定,从而导致电石炉料层不稳,塌料频繁,电极电流无法控制,长此以往导致电极上抬严重,炉底温度下降,电石翻腾厉害。
5、炉料配比调整频繁,导致电石质量波动较大,从而引起电极无法深入炉内或入炉太深。
6、料面处理还是不够彻底,捣、抅、扒做的都不够到位,且料面积灰清理不干净。
四、处理方法:1、首先,各电石炉加强设备的检修及巡检工作,减少非计划停车,尤其杜绝电石炉长时间停电。
2、各车间加强工艺操作,控制好电极电流,电极电流超标只会引起支路电流增加,料面温度升高、电极上抬,不利于生产正常运行。
3、电石炉长时间停电后负荷提升不宜太快,应按照负荷提升表进行负荷提升。
4、各车间应稳定炉料配比,尽量不要频繁调整配比,以免引起电石质量及炉况大幅度波动。
密闭电石炉生产精细化管理探讨
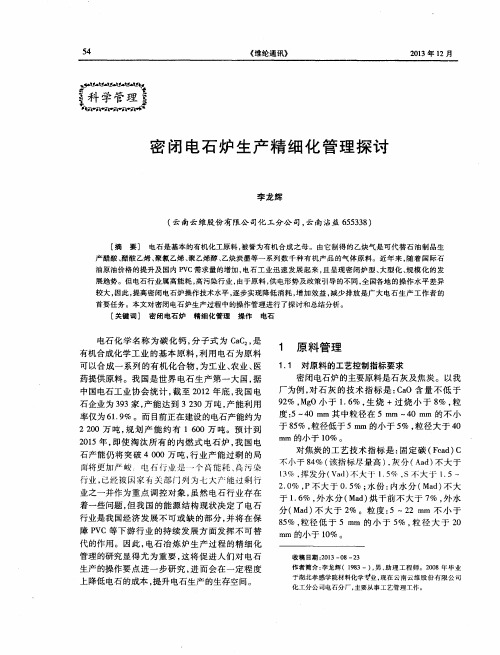
1 原 料 管 理
1 . 1 对原 料 的工艺 控制指 标要 求
可以合成一系列 的有机化合 物 , 为工业、 农业、 医 药提供原料。我 国是世界 电石生产第一大 国, 据 中 国电石工 业 协 会 统 计 , 截至 2 0 1 2年底 , 我 国 电
石企业 为 3 9 3家 , 产能达到 3 2 3 0万 吨 , 产 能利 用 率仅 为 6 1 . 9 % 。而 目前正 在 建设 的 电石 产能 约为
2 . O %, P不 大 于 0 . 5 %; 水份: 内水 分 ( Ma d ) 不 大
2 0 1 5 年, 即使 淘汰所有 的内燃式 电石 炉, 我 国电
石产 能 仍 将 突 破 4 0 0 0万 吨 , 行 业 产 能 过 剩 的局
而将更 加 严 峻 电 仃业 是 一 一个商能 耗 、 岛 污染 行业 , 已经 被 因 家 有 关 部 门 列 为 七 大 产 能 过剩 行
业之 一并作 为 重 点 调 控 对 象 , 虽 然 电石 行 业存 在 着 一 些问题 , 但 我 国 的 能 源 结 构 现 状 决定 了 电石 行 业是 我 国经 济 发 展 不 可 或 缺 的部 分 , 并 将 在 保 障P V C等 下 游 行 业 的持 续 发 展方 面发 挥 不 可替 代 的作 用 。因 此 , 电石 冶 炼 炉 生 产 过 程 的 精 细化 管 理 的研究 显 得 尤 为 重 要 , 这 将 促 进人 们 对 电石 生 产 的操作 要 点 进 一 步 研 究 , 进 而 会 在一 定 程 度 上降低 电石 的成 本 , 提升 电石 生 产 的生存 空间 。
5 5
1 . 2 对原 料 的 工艺 指标 管理 1 . 2 . 1 石 灰 的 管理
论原料杂质对电石炉的影响

论原料杂质对电石炉的影响电石生产影响因素很多,原料是电石生产的基础,没有好的原料是很难达到高产量,高产量,低单耗的行业标准,针对公司的生产工艺,电炉运行情况,原料品质等方面进行分析,总结,找出更加符合公司的生产操作,工艺调配规律,以便更加科学的指导生产,电石生产的三要素“原料,设备,操作”。
在原料设备得到保证的前提下,在操作上把握两个关键,一是配比的选择,二是能否把握更加合理的操作工艺,原料是核心,原料的好坏其最主要的是影响配比的准确性及影响电石的质量高低。
石灰过烧对配比的影响。
过烧含量过多则石灰活性度越差,反应速度越慢,这样就造成实际配比高,电石质量过高,造成出炉困难,由于出炉困难可能造成炉内电石没有出尽,容易引起翻电石,踏料现象。
还由于接触面积减少,会引起炉料电阻下降,电极容易上抬,对电炉稳定操作不利。
所以,我们应该认真的把握原料的入厂关,严格质量指标的控制,增大负荷提高炉温,控制石灰过烧含量过多对配比的影响,在适当降低配比。
石灰生烧含量对耗电量的影响,石灰生烧含量过高,则会增加消耗的电量,生烧率过高,及影响炉料的配比,又会影响电石炉的正常生产秩序,因此,生烧率不易超过5%。
石灰氧化镁含量对生产的影响,氧化镁对电石生产危害较大,氧化镁能在熔融区被迅速还原成金属镁,使熔融区成为一个强烈的高温还原区,镁蒸气从这个强烈的高温区大量溢出时,其中一部分与一氧化碳立即起反应,生产氧化镁,此反应放出大量的热,产生的高温区使局部硬壳被破坏,可能是液态电石继之外流,与耐火砖衬接触,侵蚀了砖衬;而另一部分镁蒸汽上升到炉料表面与一氧化碳或空气中的氧气反应,当镁与氧反应时,放出大量的热,使料面结壳,阻碍炉气排出,这就给操作带来了困难,更严重的是这一部分热量对炉体也会产生不良影响,反应热能使熔池破坏,会把电石堵在流出口内,甚至完全堵死流出口,因此电石炉内的氧化镁含量应尽量降低。
影响电石质量的因素分析
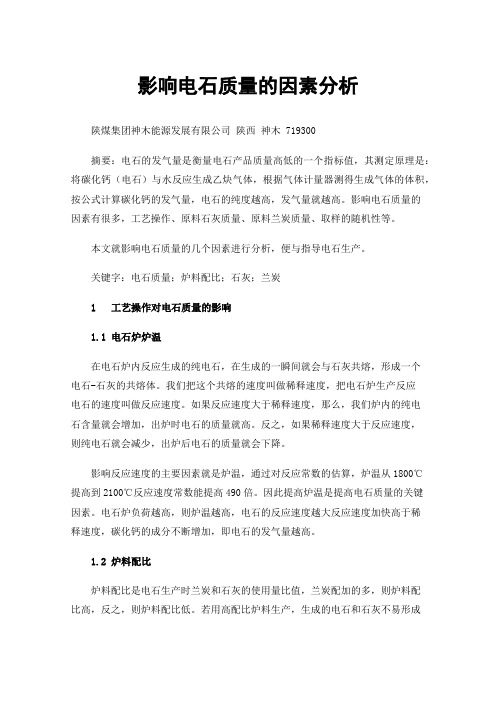
影响电石质量的因素分析陕煤集团神木能源发展有限公司陕西神木 719300摘要:电石的发气量是衡量电石产品质量高低的一个指标值,其测定原理是:将碳化钙(电石)与水反应生成乙炔气体,根据气体计量器测得生成气体的体积,按公式计算碳化钙的发气量,电石的纯度越高,发气量就越高。
影响电石质量的因素有很多,工艺操作、原料石灰质量、原料兰炭质量、取样的随机性等。
本文就影响电石质量的几个因素进行分析,便与指导电石生产。
关键字:电石质量;炉料配比;石灰;兰炭1 工艺操作对电石质量的影响1.1 电石炉炉温在电石炉内反应生成的纯电石,在生成的一瞬间就会与石灰共熔,形成一个电石-石灰的共熔体。
我们把这个共熔的速度叫做稀释速度,把电石炉生产反应电石的速度叫做反应速度。
如果反应速度大于稀释速度,那么,我们炉内的纯电石含量就会增加,出炉时电石的质量就高。
反之,如果稀释速度大于反应速度,则纯电石就会减少,出炉后电石的质量就会下降。
影响反应速度的主要因素就是炉温,通过对反应常数的估算,炉温从1800℃提高到2100℃反应速度常数能提高490倍。
因此提高炉温是提高电石质量的关键因素。
电石炉负荷越高,则炉温越高,电石的反应速度越大反应速度加快高于稀释速度,碳化钙的成分不断增加,即电石的发气量越高。
1.2 炉料配比炉料配比是电石生产时兰炭和石灰的使用量比值,兰炭配加的多,则炉料配比高,反之,则炉料配比低。
若用高配比炉料生产,生成的电石和石灰不易形成共熔体,可得到质量高的电石;若用低配比炉料,在反应过程中有过量的石灰存在,给电石和石灰形成共熔体提供了更有利的条件,可得到质量低的电石。
因此炉料配比的高低是影响电石质量的关键因素,但同时也要考虑实际的操作和装置运行的稳定性。
2 原料质量对电石质量的影响2.1 石灰石、石灰质量对电石质量的影响石灰是由石灰石经高温煅烧而成,石灰中的杂质和生过烧对电石质量也有一定的影响。
2.1.1二氧化硅的影响(1)石灰中的二氧化硅在炉内发生化学反应生成碳化硅沉积于炉底,造成炉底抬高。
密闭电石炉生产的系统优化探讨
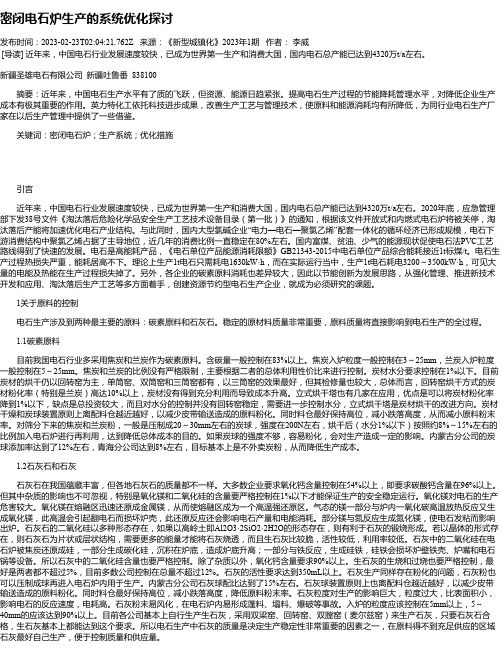
密闭电石炉生产的系统优化探讨发布时间:2023-02-23T02:04:21.762Z 来源:《新型城镇化》2023年1期作者:李威[导读] 近年来,中国电石行业发展速度较快,已成为世界第一生产和消费大国,国内电石总产能已达到4320万t/a左右。
新疆圣雄电石有限公司新疆吐鲁番 838100摘要:近年来,中国电石生产水平有了质的飞跃,但资源、能源日趋紧张。
提高电石生产过程的节能降耗管理水平,对降低企业生产成本有极其重要的作用。
英力特化工依托科技进步成果,改善生产工艺与管理技术,使原料和能源消耗均有所降低,为同行业电石生产厂家在以后生产管理中提供了一些借鉴。
关键词:密闭电石炉;生产系统;优化措施引言近年来,中国电石行业发展速度较快,已成为世界第一生产和消费大国,国内电石总产能已达到4320万t/a左右。
2020年底,应急管理部下发38号文件《淘汰落后危险化学品安全生产工艺技术设备目录(第一批)》的通知,根据该文件开放式和内燃式电石炉将被关停,淘汰落后产能将加速优化电石产业结构。
与此同时,国内大型氯碱企业“电力—电石—聚氯乙烯”配套一体化的循环经济已形成规模,电石下游消费结构中聚氯乙烯占据了主导地位,近几年的消费比例一直稳定在80%左右。
国内富煤、贫油、少气的能源现状促使电石法PVC工艺路线得到了快速的发展。
电石是高能耗产品,《电石单位产品能源消耗限额》GB21343-2015中电石单位产品综合能耗接近1t标煤/t。
电石生产过程热损失严重,能耗居高不下。
理论上生产1t电石只需耗电1630kW·h,而在实际运行当中,生产1t电石耗电3200~3500kW·h,可见大量的电能及热能在生产过程损失掉了。
另外,各企业的碳素原料消耗也差异较大,因此以节能创新为发展思路,从强化管理、推进新技术开发和应用、淘汰落后生产工艺等多方面着手,创建资源节约型电石生产企业,就成为必须研究的课题。
1关于原料的控制电石生产涉及到两种最主要的原料:碳素原料和石灰石。
影响密闭电石生产因素分析
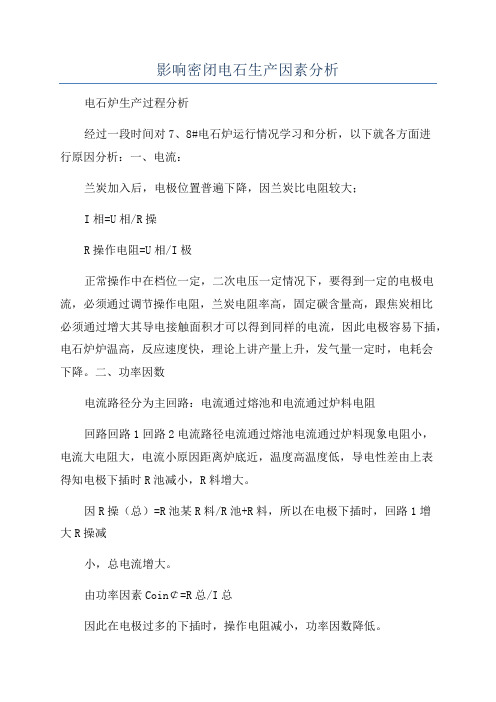
影响密闭电石生产因素分析电石炉生产过程分析经过一段时间对7、8#电石炉运行情况学习和分析,以下就各方面进行原因分析:一、电流:兰炭加入后,电极位置普遍下降,因兰炭比电阻较大;I相=U相/R操R操作电阻=U相/I极正常操作中在档位一定,二次电压一定情况下,要得到一定的电极电流,必须通过调节操作电阻,兰炭电阻率高,固定碳含量高,跟焦炭相比必须通过增大其导电接触面积才可以得到同样的电流,因此电极容易下插,电石炉炉温高,反应速度快,理论上讲产量上升,发气量一定时,电耗会下降。
二、功率因数电流路径分为主回路:电流通过熔池和电流通过炉料电阻回路回路1回路2电流路径电流通过熔池电流通过炉料现象电阻小,电流大电阻大,电流小原因距离炉底近,温度高温度低,导电性差由上表得知电极下插时R池减小,R料增大。
因R操(总)=R池某R料/R池+R料,所以在电极下插时,回路1增大R操减小,总电流增大。
由功率因素Coin¢=R总/I总因此在电极过多的下插时,操作电阻减小,功率因数降低。
三、电极位置有以上电流调节可以得知,要得到稳定的电流就必须通过调节操作电阻,电极位置相应变化,因此可以说在炉况稳定情况下,三相畅通,排除其他电器原因较短电极相插入料面浅,电阻大电流小,因此在三相反应配比相同时,电极位置降低相电极较短,按照3、2、1的互感关系,较短电极所带相电流小。
电极位置和埋入炉料内的深浅,不仅可引起熔池大小及其位置之波动,而且对料层结构影响很大,尤其对上层炉料电阻影响更为显著,所以电极升降对电流影响较大,在一定程度上也能够反应炉内电阻情况;但是也不能排除因出炉不及时造成炉内熔融电石累计,温度过高,发气量大造成的电极位置上抬。
当炉内炭比过大,炭过剩,炉料电阻减小,电流增大,必须通过调节电流导电面积来调节电流,造成电极位置波动。
四、炉料电阻电石炉内物料电阻包含电石和炉料两部分,电石质量越高,电阻越低。
同一质量电石其电阻随温度升高而降低。
密闭电石炉电极糊消耗偏高的原因分析及对应措施
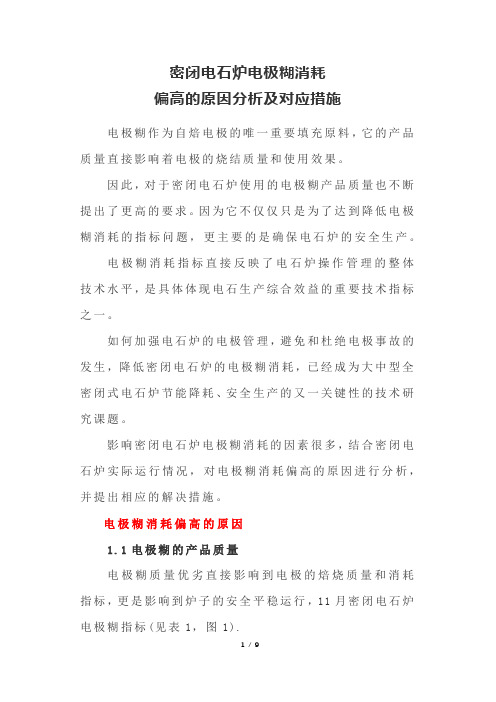
密闭电石炉电极糊消耗偏高的原因分析及对应措施电极糊作为自焙电极的唯一重要填充原料,它的产品质量直接影响着电极的烧结质量和使用效果。
因此,对于密闭电石炉使用的电极糊产品质量也不断提出了更高的要求。
因为它不仅仅只是为了达到降低电极糊消耗的指标问题,更主要的是确保电石炉的安全生产。
电极糊消耗指标直接反映了电石炉操作管理的整体技术水平,是具体体现电石生产综合效益的重要技术指标之一。
如何加强电石炉的电极管理,避免和杜绝电极事故的发生,降低密闭电石炉的电极糊消耗,已经成为大中型全密闭式电石炉节能降耗、安全生产的又一关键性的技术研究课题。
影响密闭电石炉电极糊消耗的因素很多,结合密闭电石炉实际运行情况,对电极糊消耗偏高的原因进行分析,并提出相应的解决措施。
电极糊消耗偏高的原因1.1电极糊的产品质量电极糊质量优劣直接影响到电极的焙烧质量和消耗指标,更是影响到炉子的安全平稳运行,11月密闭电石炉电极糊指标(见表1,图1).表1 11月密闭电石炉电极糊指标图1 11月电极糊灰分曲线灰分含量是一个严格控制的质量指标,因为它对电极的焙烧速度、导电性能、抗氧化性能、烧结密度、消耗速度等都有直接的影响,严格控制电极糊的灰分质量指标尤为关键,同时避免灰分越低越好的误区,并不是灰分越低越好,灰分太低,电极的焙烧强度不够,灰分太高容易造成电极的硬断,都会增加电极糊的消耗。
合理控制电极糊的产品质量,确保电石炉长期稳定运行。
1.2电极事故电石炉操作管理中发生电极软、硬断事故主要原因在于电极管理工作中对于某些操作细节尚未引起足够的重视,对于密闭电石炉电极实际入料深度测定不够准确,所以电极的入料深度经常出现大范围的波动,由于在调整电极时操作不当,在焙烧电极阶段极易发生电极事故,破坏电极焙烧的热平衡,重新建立起正常的焙烧秩序相当困难。
并且在大电流条件下强制性焙烧的电极质量气孔率较高、机械强度也差,其消耗速度将会加快。
由于处理电极事故造成热停炉频繁,电石产量减少,电极糊消耗受到极大影响,电极事故是影响电极糊消耗偏高的一个主要因素。
密闭电石炉原料质量的影响

原料质量影响1.碳材中灰份的影响焦炭中灰份含量的升高对电石电耗及焦炭消耗耗具有综合的影响。
灰份高即会造成固定碳含量降低,在电石生产时必然会影响炉料的配比,进而影响到炉料的电阻,造成电极上抬、热损失增大。
所以在实际生产中,因焦炭份分升高而造成电石电耗、焦耗的上升值会远远高于以上的计算。
据有关生产试验显示,焦炭中灰分每增加1%,电石电耗实际会上升达50~60kWh/t。
2、碳材中粉末的影响粉末多了以后,炉料透气性不好,电石生成过程中产生的一氧化碳气体不能顺利排出,减慢了电石生成反应的速度。
炉料透气性不好,使炉压增大,容易发生喷料和塌料现象。
结果使大量生料下落到熔池,使电极周围和熔池区域料层结构发生变化,炉料不是有序地连续发生变化,逐步沉降下去,而是突然有大量生料漏入熔池,造成电极上升,对炉温和电石炉内的反应的连续性产生很坏的影响,产品质量易降低。
同时易造成人身伤害。
粉末多的时候,许多粉末被炉气带走,炉料的配比就不准了。
粉末在料层中容易结成硬壳,电极附近产生支路电流,造成电极上升。
3.碳材中水分的影响假设焦炭投炉时为25℃,则每公斤水份由25℃上升到100℃需耗热314kJ,而水由100℃化为蒸汽需耗热2256.8kJ。
假设有50%的水蒸汽直接由100℃加热到550℃逸出,则需耗热:0.5×0.482×(550-100)×4.187=454.1kJ另外50%水蒸汽与碳作用:H2O + C =CO +H2-7300kJ/kgH2O18 12 28 20.5 0.33 0.77 0.055需耗热0.5×7300=3650kJCO+H2带出热为(0.77×0.259+0.055×0.26)×(550-100)×4.187=402.7kJ这样每公斤水份影响电耗合计为:314+2256.8+454.1+3650+402.7=7077.6kJ折合电能:7077.6/3600=1.97kWh假如每吨电石的焦耗为600kg,则焦炭中水份每1%,即影响电耗增加:600×1%×1.97=11.8kWh同时如果焦炭平均含碳量为84%,则碳素与每公斤水分反应增加的焦耗为0.33/0.84=0.39kg,则焦炭中水份每1%,即影响电石焦耗增加:600×1%×0.39=2.3kg4、碳材固定碳含量的影响在假定碳材中其他杂质含量不变的情况下,碳材固定碳含量越低,则碳材中灰份越高,其影响见“1、碳材中灰份的影响”。
电石生产危害因素辨识与分析

二 、火灾 、爆 炸危 害分 析
( )原 料 焦 炭 贮 存 与干 燥 时 ,由装 载机 、带 式输 送 机 及 斗 1 式 提 升 机 送 到 破 碎 筛 入 楼 筛 分 ,可 产 生 粒 径 微 小 的 煤 尘 ,若
、
工艺 过 程危 险 、有害 因素 辨识 分. 丰 斤
没 设除 尘 装 置 ,当 飞 扬 的 煤 粉 尘 与 空 气 混 合 达 到 爆 炸 极 限 后 , 如 遇 火 源 ,可 引 起煤 粉 尘 爆 炸 。振 动 筛 也 可 造 成 煤 粉 尘 飞 扬 , 若 没设 除 尘 装 置 , 当 飞 扬 的 煤 粉 尘 与 空 气 混 合 达 到 爆 炸 极 限 后 ,如 遇 火 源 ,也 可 引 起 煤 粉 尘 爆 炸 。 在 焦 炭 干 燥 时 ,干 燥
业 需 要 提 供 了 方 便 ,成 为 检 查 、 测 量 及 其 他 作 业 时 经 常 通 行 或 滞 留 的地 方 。但 是 同 时 因 位 于 高 处 ,也 就 存 在 着 一 定 的 危
错误 或 防 爆 电气 设 备 损 坏 , 导 致 发 生 电 气 打 火 引 发 火 灾 或 爆
破碎 、 焦炭 干 燥 、 电石生 产 、 固态 电石 冷却 、 碎 、 破 储存 以及 电极 壳 制 造、 炉气 净化 回收和 石 灰烧 制等 几 个 部 分 , 可 分大 体 划 分 为 原料 并 处理、 配料 、 电石 炉 反应 制 电石和 尾气 处理 4 个单 元 。 工程 及 辅 助 设 施 进 行 分 析 。 石灰 烧 制 的 石 灰 窑 , 电 石 炉 气 为 能 源 , 制 石 灰 , 产 过 以 烧 生 程 中涉 及 到 高 温 、 明火 和 有 毒 、 燃 的 C 气 体 , 需 要 对 其 进 易 O 也 行 危 险 、 害 因素 分 析 。 有
密闭电石炉安全
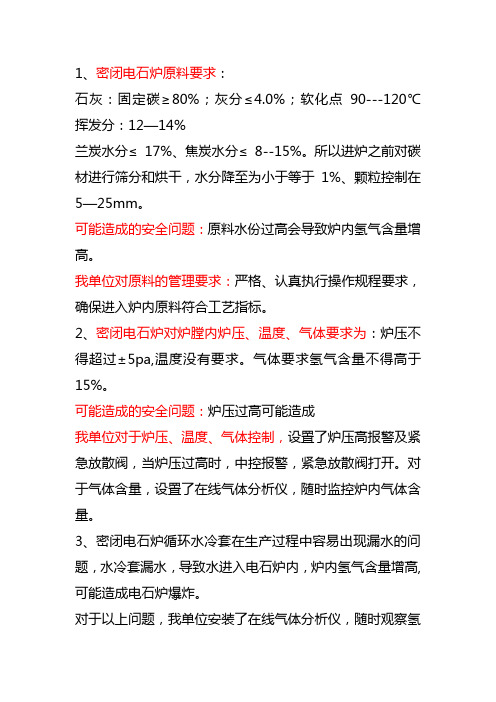
1、密闭电石炉原料要求:石灰:固定碳≥80%;灰分≤4.0%;软化点90---120℃挥发分:12—14%兰炭水分≤ 17%、焦炭水分≤ 8--15%。
所以进炉之前对碳材进行筛分和烘干,水分降至为小于等于1%、颗粒控制在5—25mm。
可能造成的安全问题:原料水份过高会导致炉内氢气含量增高。
我单位对原料的管理要求:严格、认真执行操作规程要求,确保进入炉内原料符合工艺指标。
2、密闭电石炉对炉膛内炉压、温度、气体要求为:炉压不得超过±5pa,温度没有要求。
气体要求氢气含量不得高于15%。
可能造成的安全问题:炉压过高可能造成我单位对于炉压、温度、气体控制,设臵了炉压高报警及紧急放散阀,当炉压过高时,中控报警,紧急放散阀打开。
对于气体含量,设臵了在线气体分析仪,随时监控炉内气体含量。
3、密闭电石炉循环水冷套在生产过程中容易出现漏水的问题,水冷套漏水,导致水进入电石炉内,炉内氢气含量增高,可能造成电石炉爆炸。
对于以上问题,我单位安装了在线气体分析仪,随时观察氢气含量,并设立巡检工不定时的检查。
4、电石炉的油压系统,正好布臵在电石炉二层顶上面,在炉压高和焊接电极筒时常常有火焰、火星进入到压放升降台中,故所有的液压系统应无渗漏,防止火灾发生。
我单位有专人巡检,液压系统处放臵灭火设施,防止火灾的发生。
5、环形料仓的料位信号应准确,在许多厂家由于环型料位信号失真,经常造成从料仓至下料管料放空,使炉气从料管进入空料仓,直接与空气接触发生爆炸。
我单位中控有监控设施,可直接明了的观察料位仓的料位,防止下料管料放空,避免爆炸的发生。
6、进出料时下料嘴正常时应有一定的长度,控制料面高度,当其损坏到一定程度,应及时更换,以防由于料嘴短料面上升,影响电极深入和电极自身绝缘,损坏炉盖和其它设备。
7、密闭电石炉在日常或遇到紧急情况开启炉门时容易出现喷料的事故,造成人员伤亡,我公司针对上述问题,在每次打开炉门前将炉内压力降至最低,打开紧急放散阀,保证炉内处于负压状态。
密闭电石炉(矿热炉)冶炼生产工艺过程、反应过程、料层结构分析
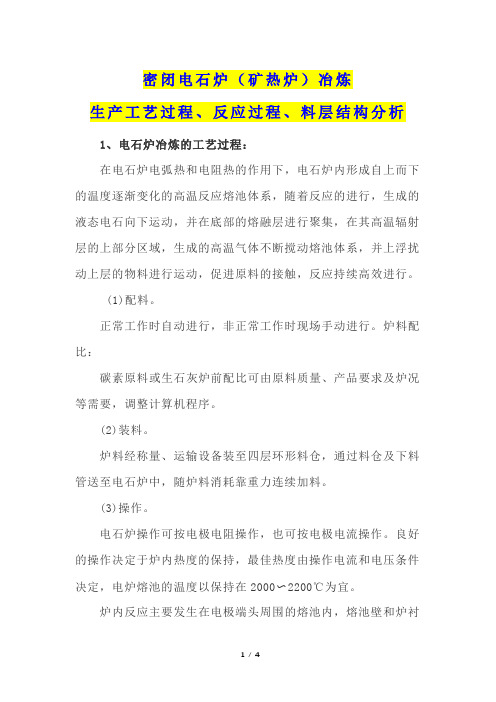
密闭电石炉(矿热炉)冶炼生产工艺过程、反应过程、料层结构分析1、电石炉冶炼的工艺过程:在电石炉电弧热和电阻热的作用下,电石炉内形成自上而下的温度逐渐变化的高温反应熔池体系,随着反应的进行,生成的液态电石向下运动,并在底部的熔融层进行聚集,在其高温辐射层的上部分区域,生成的高温气体不断搅动熔池体系,并上浮扰动上层的物料进行运动,促进原料的接触,反应持续高效进行。
(1)配料。
正常工作时自动进行,非正常工作时现场手动进行。
炉料配比:碳素原料或生石灰炉前配比可由原料质量、产品要求及炉况等需要,调整计算机程序。
(2)装料。
炉料经称量、运输设备装至四层环形料仓,通过料仓及下料管送至电石炉中,随炉料消耗靠重力连续加料。
(3)操作。
电石炉操作可按电极电阻操作,也可按电极电流操作。
良好的操作决定于炉内热度的保持,最佳热度由操作电流和电压条件决定,电炉熔池的温度以保持在2000〜2200℃为宜。
炉内反应主要发生在电极端头周围的熔池内,熔池壁和炉衬间的炉料起主要耐温绝热作用。
对入炉原料的成分、粒度、湿度和配比按有关规定,定期检查,必要时增加频次,以免造成炉料波动造成的电极电流或电阻波动,影响电石炉稳定运行、电极消耗过快和电石质量不稳定。
电极端头至炉底距离的期望值为1.3〜1.5m,其最佳距离要根据自身工艺条件,由经验确定。
(4)电极调节。
电极调节由升降油缸移动电极而实现。
电极调节应与变压器的电压级选择相结合,以获得理想的电极头位置和电石炉负荷。
电石炉采用自焙电极。
电极柱由充满电极糊的电极壳组成,新开炉电极端头焊有启动电机壳。
电极壳可传输大部分电极电流。
电极调节方式为:以电极电流或操作电阻为标准,由操作电脑点动及操作柜旋钮手动操作。
(5)炉气的主要成分及性质。
密闭的电石炉在其运行过程当中所产生化学反应工艺气体不会泄露到大气当中,同时密闭电石炉外部大气中的气体也不会进入到炉内。
密闭电石炉内部经过化学反应之后所产生的都是有害气体,这些有害气体主要是:CO、CO2、H2、CH4等。
密闭炉电石炉安全生产重点防范措施.docx

密闭炉电石炉安全生产重点防范措施为预防电石企业在生产过程中发生喷炉、爆炸等生产安全事故,我车间组织有关专家根据电石炉生产工艺,设备、原材料、辅助材料、产品的危险性及生产操作岗位的特点,特制定《电石炉生产技术防范措施30 条》,请各生产主任、班长、各工段负责人严格遵照执行。
严格控制原料的各项指标;把好原料关对预防喷炉事故至关重要,各企业从源头上控制好原料的各项指标,做到认真检查和化验,对不符合以下指标的原料坚决不入炉。
1、碳素材料中的水分含量半密闭炉电石炉采用自动上料系统的,碳素材料中的水份含量5%,采用人工上料的,碳素材料中水份含量8%,密闭电石炉碳素材料中的水份含量2%。
2、电极糊的选用电石生产企业使用电极糊要确保质量合格, 在使用前应查看电极糊的化验单 , 合格后方可使用 . 应选择具备一定规模的电极糊企业生产的产品 . 电极糊粒度 100 ㎜, 严禁将整块电极糊直接加入电极筒内 . 在换季阶段 , 应及时调整电极糊的软化点、挥发份等指标。
3、白灰中氧化镁的含量应尽量控制白灰中氧化镁的含量,尤其密闭炉应在 1.6%以下。
4、白灰中粉沫的含量要严格控制白灰中粉沫的含量,对粉沫含量高的白灰,必须经过筛分后方可进行投料,白灰中粉沫的含量,必须控制在3%以下。
加强设备安全管理在生产过程中,设备设施的功能失效、设计安装的不合理、操作不当都是导致事故发生的直接原因。
5、循环水系统进水槽阀门应安装在作业人员便于操作的安全区域,且高度不宜超过 1.5M。
6、电极筒上部应加装有防尘盖,并开设透气孔,以防止杂物进入电极筒,影响电极焙烧质量。
7、淘汰使用卷扬机拉运电石锅,尽可能使用自动行走牵引车拉运电石锅,牵引车要装有防倾倒设施,前后应设配重车。
8、电极压放系统,淘汰弹簧式抱紧系统,必须采用液压或气囊上、下抱紧装置,并加装限位装置,实现自动带电压放。
9、电石炉大修完毕送电前,应编制《开炉方案》,进行炉体、液压机压放系统、绝缘系统、冷却水循环系统、短网导电系统、出炉系统的验收,并且填写《验收确认表》备查;日常检修必须确保质量;把持器电极的检修必须注意导电接触原件的安装,必须确保与筋板自由平行,碟形弹簧预紧力符合要求。
密闭电石炉发生电极硬断事故的原因分析
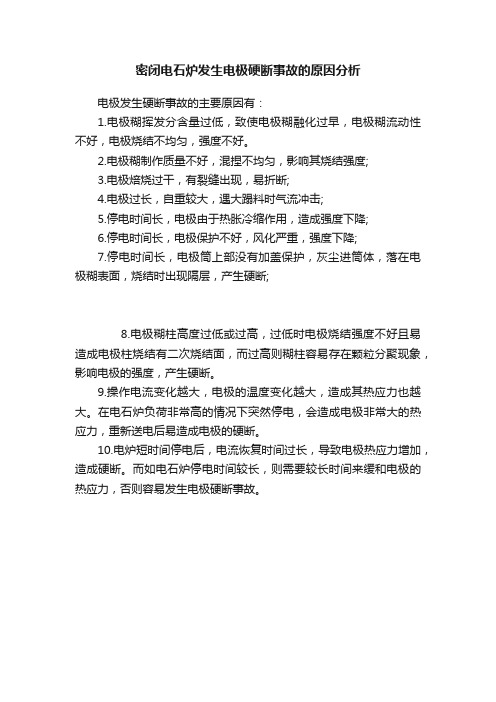
密闭电石炉发生电极硬断事故的原因分析
电极发生硬断事故的主要原因有:
1.电极糊挥发分含量过低,致使电极糊融化过早,电极糊流动性不好,电极烧结不均匀,强度不好。
2.电极糊制作质量不好,混捏不均匀,影响其烧结强度;
3.电极焙烧过干,有裂缝出现,易折断;
4.电极过长,自重较大,遇大蹋料时气流冲击;
5.停电时间长,电极由于热胀冷缩作用,造成强度下降;
6.停电时间长,电极保护不好,风化严重,强度下降;
7.停电时间长,电极筒上部没有加盖保护,灰尘进筒体,落在电极糊表面,烧结时出现隔层,产生硬断;
8.电极糊柱高度过低或过高,过低时电极烧结强度不好且易造成电极柱烧结有二次烧结面,而过高则糊柱容易存在颗粒分聚现象,影响电极的强度,产生硬断。
9.操作电流变化越大,电极的温度变化越大,造成其热应力也越大。
在电石炉负荷非常高的情况下突然停电,会造成电极非常大的热应力,重新送电后易造成电极的硬断。
10.电炉短时间停电后,电流恢复时间过长,导致电极热应力增加,造成硬断。
而如电石炉停电时间较长,则需要较长时间来缓和电极的热应力,否则容易发生电极硬断事故。
密闭电石炉生产难题解析

1、组合把持器烧筋片原因及预防措施a、电极壳允许承受电流(焙烧电极初期)(按14组、435mm长接触原件计算)弧形外壳有效面积:S1=π×1350×2=8478 mm2外筋板有效面积:S2=30×7×14=2940 mm2内筋板有效面积:S3=225×3×14=9450 mm2圆钢导电面积:S4=π/4×202×14=4398 mm2电极壳总面积:S= S1+S2+S3+S4=25266 mm2电极壳允许承受电流:钢材允许电流密度2。
2~2。
4A/ mm2I1=25266×(2。
2~2。
4)=55582~60638 A则:电极焙烧初期电流应控制在55000A以内。
外筋板允许电流:接触元件加紧面有效长435mm,外筋板宽度30 mm,外筋板厚度7mm,有效面积:S=435×7×14=42630mm2允许电流密度2。
2~2.4A/ mm2电极允许电流I2=42630×(2。
2~2.4)=93786~102312A外筋板钢板软化温度450~550℃,假定电流102312 A前电极壳保持常温,而电极壳从常温上升到550 ℃时热量为:Q=mc(t2-t1)=43.5×3×0.7×7。
8×10—3×4。
6×102×(550—20)=173714.8 J电极可壳筋板电阻率ρ=0。
0928 Ω·m,接触元件加紧有效长435 mm,外筋板宽30 mm,厚7 mm,外筋板电阻:R=ρl/s=0。
0978×30×10-3÷(435×10—3×7×10—3)=0.964 Ω如果外筋板由常温上升到550℃,热量全部由电流提供:Q=1。
005RtI2,忽略通电时间有:I=434A电极壳共14片外筋板 434×14=6076A故可输入最大电流为I=(93786~102312)+6076=99862~108388 A因此,电极电流应控制在110000 A以内.b、电极过焙烧,造成电极壳分离;c、内三角电流密度大;d、电极壳制作不好,焊接面不平整;e、底环缺口制作,安装误差;f、电极壳与吊挂架相连刺火,融化过快;底环气封垫板密封不严,造成蹿火,温度升高,加速筋板熔化。
密闭炉电石炉安全生产重点防范措施

编号:AQ-JS-01592( 安全技术)单位:_____________________审批:_____________________日期:_____________________WORD文档/ A4打印/ 可编辑密闭炉电石炉安全生产重点防范措施Key preventive measures for safe production of calcium carbide furnace with closed furnace密闭炉电石炉安全生产重点防范措施使用备注:技术安全主要是通过对技术和安全本质性的再认识以提高对技术和安全的理解,进而形成更加科学的技术安全观,并在新技术安全观指引下改进安全技术和安全措施,最终达到提高安全性的目的。
为预防电石企业在生产过程中发生喷炉、爆炸等生产安全事故,我车间组织有关专家根据电石炉生产工艺,设备、原材料、辅助材料、产品的危险性及生产操作岗位的特点,特制定《电石炉生产技术防范措施30条》,请各生产主任、班长、各工段负责人严格遵照执行。
严格控制原料的各项指标;把好原料关对预防喷炉事故至关重要,各企业从源头上控制好原料的各项指标,做到认真检查和化验,对不符合以下指标的原料坚决不入炉。
1、碳素材料中的水分含量半密闭炉电石炉采用自动上料系统的,碳素材料中的水份含量≤5%,采用人工上料的,碳素材料中水份含量≤8%,密闭电石炉碳素材料中的水份含量≤2%。
2、电极糊的选用电石生产企业使用电极糊要确保质量合格,在使用前应查看电极糊的化验单,合格后方可使用.应选择具备一定规模的电极糊企业生产的产品.电极糊粒度≤100㎜,严禁将整块电极糊直接加入电极筒内.在换季阶段,应及时调整电极糊的软化点、挥发份等指标。
3、白灰中氧化镁的含量应尽量控制白灰中氧化镁的含量,尤其密闭炉应在1.6%以下。
4、白灰中粉沫的含量要严格控制白灰中粉沫的含量,对粉沫含量高的白灰,必须经过筛分后方可进行投料,白灰中粉沫的含量,必须控制在3%以下。
密闭电石炉电极糊消耗偏高的原因分析及对应措施
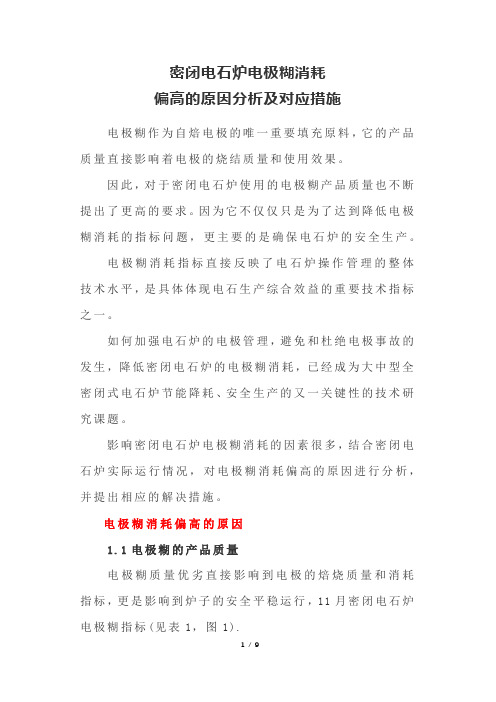
密闭电石炉电极糊消耗偏高的原因分析及对应措施电极糊作为自焙电极的唯一重要填充原料,它的产品质量直接影响着电极的烧结质量和使用效果。
因此,对于密闭电石炉使用的电极糊产品质量也不断提出了更高的要求。
因为它不仅仅只是为了达到降低电极糊消耗的指标问题,更主要的是确保电石炉的安全生产。
电极糊消耗指标直接反映了电石炉操作管理的整体技术水平,是具体体现电石生产综合效益的重要技术指标之一。
如何加强电石炉的电极管理,避免和杜绝电极事故的发生,降低密闭电石炉的电极糊消耗,已经成为大中型全密闭式电石炉节能降耗、安全生产的又一关键性的技术研究课题。
影响密闭电石炉电极糊消耗的因素很多,结合密闭电石炉实际运行情况,对电极糊消耗偏高的原因进行分析,并提出相应的解决措施。
电极糊消耗偏高的原因1.1电极糊的产品质量电极糊质量优劣直接影响到电极的焙烧质量和消耗指标,更是影响到炉子的安全平稳运行,11月密闭电石炉电极糊指标(见表1,图1).表1 11月密闭电石炉电极糊指标图1 11月电极糊灰分曲线灰分含量是一个严格控制的质量指标,因为它对电极的焙烧速度、导电性能、抗氧化性能、烧结密度、消耗速度等都有直接的影响,严格控制电极糊的灰分质量指标尤为关键,同时避免灰分越低越好的误区,并不是灰分越低越好,灰分太低,电极的焙烧强度不够,灰分太高容易造成电极的硬断,都会增加电极糊的消耗。
合理控制电极糊的产品质量,确保电石炉长期稳定运行。
1.2电极事故电石炉操作管理中发生电极软、硬断事故主要原因在于电极管理工作中对于某些操作细节尚未引起足够的重视,对于密闭电石炉电极实际入料深度测定不够准确,所以电极的入料深度经常出现大范围的波动,由于在调整电极时操作不当,在焙烧电极阶段极易发生电极事故,破坏电极焙烧的热平衡,重新建立起正常的焙烧秩序相当困难。
并且在大电流条件下强制性焙烧的电极质量气孔率较高、机械强度也差,其消耗速度将会加快。
由于处理电极事故造成热停炉频繁,电石产量减少,电极糊消耗受到极大影响,电极事故是影响电极糊消耗偏高的一个主要因素。
- 1、下载文档前请自行甄别文档内容的完整性,平台不提供额外的编辑、内容补充、找答案等附加服务。
- 2、"仅部分预览"的文档,不可在线预览部分如存在完整性等问题,可反馈申请退款(可完整预览的文档不适用该条件!)。
- 3、如文档侵犯您的权益,请联系客服反馈,我们会尽快为您处理(人工客服工作时间:9:00-18:30)。
原料分析石灰石的工艺指标生石灰的工艺指标焦炭的工艺指标灰分每增加1%电耗增加50~60度/吨;水分每增加1%电耗增加12度/吨;挥发分每增加1%电耗增加2.3~3.5度/吨;生烧率每增加1%电耗增加10度/吨。
1.理论配比:电石生成反应式CaO+3C==CaC2+CO56 36 64X=36÷64×100×B÷C+F/56÷64×100×B÷A+D+E式中:A――石灰中所含的氧化钙(CaO%);B――电石成分(CaC2%);C――碳素原料中所含的固定碳(C%);D――电石中游离氧化钙的含量;E――投炉石灰损失量(kg);F――投炉碳素原料的损失量(kg)。
X――炉料干基配比炉料湿基配比为:X(湿)=X/(1-水份)根据理论配比,计算出碳材固定碳每降低1%,每吨电石大约多消耗10公斤碳素。
2.生产中,在进行电石生成反应的同时,进行着如下副反应:CaC2=Ca+2C-60.7kJCaCO3=CaO+CO2-178kJCO2+C=2CO-164kJH2O+C=CO+H2-166kJCa(OH)2=CaO+H2O-109kJCa2SiO4=2CaO+SiO2-121kJSiO2+2C=Si+2CO-574kJFe2O3+3C=2Fe+3CO-452kJAl2O3+3C=2Al+3CO-1218kJMgO+C=Mg+CO-486kJ上述反应大部分是原料中带进的杂质所引起的。
发生这些副反应时,不但要消耗碳材和电能,而且有碍电石生成的反应过程,对生产是十分有害的。
3. 原料中杂质的影响原料中的杂质主要包括氧化镁、氧化硅、氧化铁、氧化铝等。
当炉料在电炉内反应生成碳化钙的同时,各种杂质也进行反应:SiO 2+2C=Si+2CO-574kJFe 2O 3+3C=2Fe+3CO-452kJAl 2O 3+3C=2Al+3CO-1218kJMgO +C =Mg +CO-486kJ上述反应不仅消耗电能和碳材,而且影响操作,破坏炉底,特别是氧化镁在熔融区迅速还原成金属镁,而使熔融区成为一个强烈的高温还原区,镁蒸气从这个炽热的区域大量逸出时,其中一部分镁与一氧化碳立即起反应,生成氧化镁:Mg +CO =MgO +C +489kJ此时,由于反应放出强热形成高温,局部硬壳遭到破坏,使带有杂质(Si 、Fe 、Al 、Mg )的液态电石侵蚀了炉底。
另一部镁上升到炉料表面,与一氧化碳或空气中的氧反应:Mg +21O 2=MgO +614kJ当镁与氧反应时,放出大量的热,使料面结块,阻碍炉气排出,并产生支路电流。
还破坏局部炉壳,甚至使熔灺遭到破坏,堵塞电石流出口。
实践证明,石灰中氧化镁含量每增加1%,则功率发气量将下降10~15L/kW ·h 。
还有部分氧化镁在熔融区与氮反应,生成的氮化镁(Mg 3N 2),使电石发粘,造成出炉困难。
影响正常生产。
二氧化硅在电石炉中被焦炭还原成硅,一部分在炉内生成碳化硅,沉积于炉底,造成炉底升高。
一部分与铁作用生成硅铁,硅铁会损坏炉壁铁壳,出炉时会损坏嘴和电石锅等。
氧化铝在电石炉内不能全部还原成铝,一部分混在电石里,降低了电石的质量,而大部分成为粘度很大的炉渣,沉积于炉底,使炉底升高,严重时,炉眼位置上移,造成电炉操作条件恶化。
氧化铁在电炉内与硅熔融成硅铁。
磷和硫在炉内分别与石灰中的氧化钙反应生成磷化钙和硫化钙混在电石中。
磷化钙在制造乙炔气时混在乙炔中有引起自燃和爆炸的危险,硫化钙在乙炔气燃烧时,变成二氧化硫气体,对金属设备有腐蚀作用。
依据氧化物的反应热量平衡计算,平均每公斤氧化物还原需要耗热折电2.5kWh、耗焦0.32kg。
如果炭材中灰分增加1%,按焦耗600kg/t计算,则影响电石电耗约600×1%×2.5=15kWh/t;影响电石焦耗约600×1%×0.32=1.92kg/t。
平均每公斤氧化镁及氧化硅还原需要耗热折电为3kWh、耗焦为0.35kg。
如果石灰中氧化镁及氧化硅含量增加1%,按电石石灰耗900kg/t计算,则影响电石电耗约900×1%×3=27kWh/t,影响焦耗约900×1%×0.35=3.15kg/t。
4.碳材中灰份的影响焦炭中灰分含量的升高对电石电耗及焦耗具有综合的影响。
灰分高即会造成固定碳含量降低,在电石生产时必然会影响炉料的配比,进而影响到炉料的电阻,造成电极上抬、热损失增大。
所以在实际生产中,因焦炭灰分升高而造成电石电耗、焦耗的上升值会远远高于以上的计算。
据有关生产试验显示,焦炭中灰分每增加1%,电石电耗实际会上升达50~60kWh/t。
5.碳材中水分的影响假设焦炭投炉时为25℃,则每公斤水份由25℃上升到100℃需耗热314kJ,而水由100℃化为蒸汽需耗热2256.8kJ。
假设有50%的水蒸汽直接由100℃加热到550℃逸出,则需耗热:0.5×0.482×(550-100)×4.187=454.1kJ另外50%水蒸汽与碳作用:H2O + C =CO +H2-7300kJ/kgH2O18 12 28 20.5 0.33 0.77 0.055需耗热0.5×7300=3650kJCO+H2带出热为(0.77×0.259+0.055×0.26)×(550-100)×4.187=402.7kJ这样每公斤水份影响电耗合计为:314+2256.8+454.1+3650+402.7=7077.6kJ折合电能:7077.6/3600=1.97kWh假如每吨电石的焦耗为600kg,则焦炭中水份每1%,即影响电耗增加:600×1%×1.97=11.8kWh同时如果焦炭平均含碳量为84%,则碳素与每公斤水分反应增加的焦耗为0.33/0.84=0.39kg,则焦炭中水份每1%,即影响电石焦耗增加:600×1%×0.39=2.3kg6.炭材中挥发份对电石电耗的影响炭素材料中挥发份对电石生产的危害也是不容忽视的,实践证明,挥发份在炉内有10~15%被分解和碳化,使碳素材料的效率降低。
若炭素原料中的挥发份增加1%,则生产每吨电石多耗电3~5kWh/t。
另外,挥发份靠近反应区,形成半融粘结状,使反应区物料下落困难,容易引起喷料现象,使热量损失增加。
对于开放炉,使炉面火焰增长,操作环境恶化。
7.石灰生过烧的影响大块石灰石中心部位来不及分解就被卸出窑来,这个夹心实际是碳酸钙。
在电石炉内这部分碳酸钙要进一步分解成石灰,然后与碳反应生成电石,分解碳酸钙需要热量,这个热量要由电能来提供,这就增加了电耗。
此外,还要影响炉料配比,打乱了电炉的正常生产秩序。
按碳酸钙分解反应式:CaCO3=CaO+CO2-1779.5kJ/kg CaCO3计算,每公斤碳酸钙分解后,生成0.44公斤CO2,这些生成的CO2中约有75%左右还会跟碳作用生成CO:CO2+C=2CO-3919kJ/kg CO2,需要耗热为3919×0.75×0.44=1293.3kJ,根据热量衡算,最终生成的CO2和CO随炉气逸出时带走热量为210kJ。
则每公斤碳酸钙在电石炉内分解所耗热折电为约0.91kWh,耗焦为0.11kg。
如果按电石石灰耗900kg/t计算,石灰中生烧增加1%,则影响电石电耗900×1%×0.91=8.19 kWh/t,影响焦耗约900×1%×0.11=0.99kg/t。
过烧石灰坚硬致密,比重大,反应接触面减小,活性差,影响产品质量和产量。
8.原料粒度的影响石灰粒度过大,接触面积小,反应速度慢;粒度过小,炉料透气性不好,影响炉气的排出,不仅影响操作,而且有碍于反应往生成电石的方向进行。
碳材粒度的不同,其电阻相差很大。
一般是粒度越小,电阻越大,在电炉上操作时,电极易深入炉内,对电炉操作有利。
但粒度过小,则透气性差,容易使炉料结块,电炉操作反而不利。
)p c (b 本结r a =ρρ-+接本结ρ=ρρ+根据层堆粒状焦炭电阻测试实验结果,粒状焦炭的名义结构电阻为粒状焦炭的本征电阻与接触电阻之和,可以近似地用下列公式表示:式中:r -焦粒的当量直径,cm ;p -层堆粒状焦炭所承受的负荷,MPa ;a 、b 、c -与焦粒几何形状有关的经验常数。
这样,影响粒状焦炭结构电阻的诸多因素就可以分别由焦炭的本征电阻和接触电阻所表现出来。
焦炭的本征电阻与温度的变化密切相关,温度越高,其本征电阻越小。
而粒径的大小、几何形状、粒度分布和焦层上压力的变化,则会改变堆层粒状焦炭的接触电阻。
如果认为焦炭几何形状、粒度分布及焦层上压力固定不变,仅考察焦炭粒度变化对接触电阻的影响,则焦炭粒径越大,其接触电阻越小。
对于不等径焦炭的粒度分布的影响,通常焦炭的密堆程度越大,则其接触电阻越小。
碳素原料粒度与电阻的关系见表:8.1.碳素原料粉末的影响碳素原料粉末对电石生产有很大影响;粉末多了以后,炉料透气性不好,电石生成过程中产生的一氧化碳气体不能顺利排出,减慢了电石生成反应的速度。
炉料透气性不好,使炉压增大,容易发生喷料和塌料现象。
结果使大量生料下落到熔池,使电极周围和熔池区域料层结构发生变化,炉料不是有序地连续发生变化,逐步沉降下去,而是突然有大量生料漏入熔池,造成电极上升,对炉温和电石炉内的反应的连续性产生很坏的影响,产品质量易降低。
同时易造成人身伤害。
粉末多的时候,许多粉末被炉气带走,炉料的配比就不准了。
粉末在料层中容易结成硬壳,电极附近产生支路电流,造成电极上升。
8.2.粉化石灰的影响石灰在生产和贮存的过程中,吸入空气和碳材中的水份而产生一部分氢氧化钙,氢氧化钙在电炉内发生如下反应:Ca(OH)2=CaO+H2O-109kJH2O+C=CO+H2-166kJ在电石生产过程中,粉化石灰不但要多消耗电能和炭素原料,而且还要影响电石操作。
炉料中的粉末含量较多时,容易使电极附近料层结成硬壳,产生棚料现象。
棚料有两种害处:一是降低炉料自由下落的速度,减少投料量,使电石炉减产;二是阻碍炉气自由排出,增大炉内压力,最后发生喷料和塌料等现象,影响电石炉正常操作。
按照氢氧化钙在炉内反应式进行衡算,每公斤石灰风化后投炉反应,将需要消耗热量4911.5kJ,折电为1.36kWh,需耗焦炭0.21kg。
如按电石石灰耗900kg/t计算,石灰风化1%,则影响电石电耗900×1%×1.36=12.24 kWh/t,影响焦耗约900×1%×0.21=1.89kg/t。