湿法水泥生产线
水泥熟料生产工艺流程解析

水泥熟料生产工艺流程解析水泥熟料生产工艺流程解析1. 引言水泥是建筑工程中不可或缺的材料,而水泥熟料是水泥的主要原料。
水泥熟料生产工艺流程是指将原料经过一系列反应和处理,最终得到水泥熟料的过程。
本文将深入探讨水泥熟料生产工艺的各个环节,从而更好地理解水泥熟料的生产过程。
2. 原料的选取与预处理2.1 原料的选取水泥熟料的主要原料通常包括石灰石、粘土、铁矿石等。
这些原料需要具备一定的化学成分和物理性质,以确保最终生产出的水泥熟料具有良好的性能。
2.2 原料的预处理在进入生产线之前,原料需要经过一系列的预处理步骤。
如石灰石需要进行破碎、磨矿、筛分等处理,以获得合适的粒度,方便后续的反应和处理。
3. 原料的烧成原料的烧成是整个水泥熟料生产过程中最关键的步骤之一。
该步骤主要包括干法烧成和湿法烧成两种方法。
3.1 干法烧成干法烧成是指将原料直接送入旋转窑进行烧成的方法。
在旋转窑中,原料与高温燃烧气体进行交互作用,发生一系列的物理和化学反应,最终形成水泥熟料。
这种方法具有工艺简单、设备投资少的特点,但能耗较高。
3.2 湿法烧成湿法烧成是指将原料中的水分先进行脱除,然后再进行烧成的方法。
该方法能耗低,但工艺复杂、设备投资较大。
湿法烧成通常采用沟窑或滚筒窑进行。
4. 熟料的磨矿熟料的磨矿是将熟料进行细磨,以提高其活性和适应性的过程。
该步骤主要通过水泥磨来实现。
4.1 磨矿工艺磨矿工艺是指将熟料放入水泥磨中进行细磨的过程。
水泥磨通常采用滚筒式或滚压式磨机,通过磨碎和混合的作用,使熟料达到所需的细度要求。
4.2 磨矿过程中的辅助材料为了调整熟料的性能,磨矿过程中还可添加适量的矿渣、石膏等辅助材料,以改善水泥的性能和品质。
5. 总结与回顾通过对水泥熟料生产工艺流程的解析,我们可以看出,水泥熟料的生产过程经过了多个环节的处理和反应。
从原料的选取与预处理,到熟料的烧成和磨矿,每个环节都起到了关键的作用。
水泥熟料生产工艺流程的复杂性和多样性使得水泥的生产成为一门综合性较强的科学。
科学安全利用工业“三废”生产绿色水泥

微量 s 元素大部份产生了化学反应 , 煤中余下极少量 s 元素
通过 烟尘排放 到窄中 , 了杜绝 s元素通过炯尘排放到空中 , 为 公 司在收尘 工艺上 ,增加一处水收尘 ,使 烟尘中的 S与 H0 起 化学反应产 生硫酸 和从 烟尘 中的水 泥粉尘一起得 到回收 , 没 有进入大气中 , 从而减 少和杜绝大气污染 。
维普资讯
■ 与 节能 利用 工业“ 三废" 生产绿色 水泥
洪家 旺 ( 南平水泥股份有 限公 司 , 建 福
摘 要
南平
330 ) 5 00
对水泥厂生产过程的“ 三废 ” 进行 有效的利用, 它工业废 渣进 行综 对其
1 净化 工业“ 气” 减 少大气污染 . 2 废 , 水泥生产主要燃料是烟煤和无烟煤 ,煤在燃烧过程 中会 释放 少量 s 水泥熟 料的主要成份 是 c ( 0, s 硅酸钙 )而磨制水 , 泥过 程中 , 需加入 C H S 将煤 中释放的微量 s元 素与 C O a 2O , a 反应 回收用 于生产水 泥。 在湿法窑 和干法窑生产线上 , 当煤粉 喷 到旋 窑中与生 料煅烧成熟 料时 ,生料 中含 c a物与煤中 的
产后的锅炉渣 、 铁渣 、 硫石膏、 硫酸渣等工业“ 废料” 中含有水
泥生产所需要 的化学成份 ( 利用 “ 三废 ” 品种见 表 1 。通 过实 )
验室试验和工业试生产, 经过一段时间的摸索 , 确定各废料的
合理掺量 , 使其对水 泥性 能的影 响降至最低 程度 , 确保水泥安 全、 合格 出厂 。
用均在 5 万元以上 , 了五条旋窑水泥生产线粉尘排放全 O 确保
部达标 ,并 于 19 年提前 两年完成 了 “ 98 一控双达标”任务 。 2 0 年公司回收水泥粉尘近 6万 t 将收下 的水 泥粉尘 作 03 ,并 为混合料加在水泥生产线 窑尾 , 不仅减少环境 污染 , 而且做到 废物利用价值再现。
水泥生产工艺种类

水泥生产工艺种类水泥是目前建筑材料中最主要的一种,广泛应用于建筑、道路和桥梁等领域。
水泥的生产工艺种类多种多样,下面将介绍几种常见的水泥生产工艺。
1. 干法生产工艺:干法生产工艺是指通过干燥和研磨原料,将其直接入窑烧成水泥熟料。
这种工艺的特点是能耗低,生产效率高。
干法生产工艺的主要设备有破碎机、磨机、窑炉等,其中窑炉被广泛应用于干法生产工艺中。
干法生产工艺可以进一步分为干法长窑生产线和干法流程生产线。
2. 半干法生产工艺:半干法生产工艺是干法生产工艺和湿法生产工艺的结合。
在半干法生产工艺中,部分原料在干法破碎和研磨后进入烧窑,另一部分原料在水泥熟料窑尾附近进行湿法处理后再进入窑炉。
这种工艺可以在一定程度上减少装置的能耗,并且降低空气中的尘埃排放。
3. 湿法生产工艺:湿法生产工艺是指通过将原料与水混合,形成泥浆后研磨成细料,然后进入窑炉烧成水泥熟料。
湿法生产工艺的特点是能耗高,但可以生产出质量较好的水泥。
湿法生产工艺的主要设备有碎石机、旋转炉、球磨机等。
湿法生产工艺也可以进一步分为湿法旋转窑生产线、湿法短窑生产线和湿法气流炉生产线。
4. 新型生产工艺:随着科技的发展,新型的水泥生产工艺不断涌现。
例如,流化床燃烧技术可以将水泥熟料窑炉中的废气进行再利用,提高能源效率;热回收技术可以将水泥熟料窑炉中产生的余热用于预热原料,减少能耗。
新型生产工艺在提高效率的同时,也能减少环境污染。
总的来说,水泥生产工艺种类繁多,每种工艺都有其适用的特定情况。
随着技术的不断进步,水泥的生产工艺也在不断改善,以提高生产效率和降低能耗。
未来,新型的水泥生产工艺将更加环保和节能,为建筑行业提供更高质量的水泥产品。
合成革干法湿法生产线流程及每一步的作用
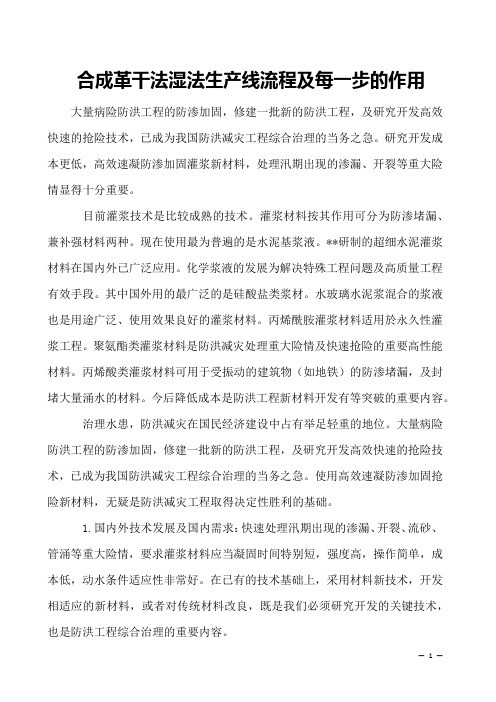
合成革干法湿法生产线流程及每一步的作用大量病险防洪工程的防渗加固,修建一批新的防洪工程,及研究开发高效快速的抢险技术,已成为我国防洪减灾工程综合治理的当务之急。
研究开发成本更低,高效速凝防渗加固灌浆新材料,处理汛期出现的渗漏、开裂等重大险情显得十分重要。
目前灌浆技术是比较成熟的技术。
灌浆材料按其作用可分为防渗堵漏、兼补强材料两种。
现在使用最为普遍的是水泥基浆液。
**研制的超细水泥灌浆材料在国内外已广泛应用。
化学浆液的发展为解决特殊工程问题及高质量工程有效手段。
其中国外用的最广泛的是硅酸盐类浆材。
水玻璃水泥浆混合的浆液也是用途广泛、使用效果良好的灌浆材料。
丙烯酰胺灌浆材料适用於永久性灌浆工程。
聚氨酯类灌浆材料是防洪减灾处理重大险情及快速抢险的重要高性能材料。
丙烯酸类灌浆材料可用于受振动的建筑物(如地铁)的防渗堵漏,及封堵大量涌水的材料。
今后降低成本是防洪工程新材料开发有等突破的重要内容。
治理水患,防洪减灾在国民经济建设中占有举足轻重的地位。
大量病险防洪工程的防渗加固,修建一批新的防洪工程,及研究开发高效快速的抢险技术,已成为我国防洪减灾工程综合治理的当务之急。
使用高效速凝防渗加固抢险新材料,无疑是防洪减灾工程取得决定性胜利的基础。
1.国内外技术发展及国内需求:快速处理汛期出现的渗漏、开裂、流砂、管涌等重大险情,要求灌浆材料应当凝固时间特别短,强度高,操作简单,成本低,动水条件适应性非常好。
在已有的技术基础上,采用材料新技术,开发相适应的新材料,或者对传统材料改良,既是我们必须研究开发的关键技术,也是防洪工程综合治理的重要内容。
2.浆液材料选择的基本要求:浆液材料应粘度低,流动性好,能进入细小裂隙;浆液胶凝时间可在几秒至几小时范围内随意调节,并能准确地控制,浆液一经发生凝胶就在瞬间完成。
其次,浆液固化时无收缩规象,粘接强度高;浆液结石体有一定抗压和抗拉强度,不龟裂,抗渗性能和防冲刷性能好;结石体能长期耐酸、碱、盐、生物细菌等腐蚀,耐老化性或耐久性优良。
电石渣湿法水泥生产线节能增产改造一例

由 于考虑 到 生料 浆 的泵 送性 , 出搅 拌池 的生 料
浆水分控制高达 5 % 6%。因此 , 5 ~0 降低人窑生料 的
水 分 , 节 能降耗 增 产 的关 键 。为此 采 用 了机械 脱 是
河北某 水 泥公 司设计 年产 l 万 t 泥生产 线 ( 5 水 2 条湿 法 生产线 ) 由其 母 公 司 ( 于 化工业 的一 家股 , 属 份公 司 ) 资兴 建 , 20 年 开 工 建设 , 02 一 投 于 01 20 年
次点火 成功 。该 线 的石灰质 原料全 部采用 母公 司排 出 的电石渣 , 进入 水泥 厂 的电石渣 水分 约 6 %~ 0 5 7%
水和烘 干二项技术 , 使入窑水分降到 1 2 从而 %一%, 实 现 了物料 的干法烧成 。
( ) 械脱 水方 案 。要 将 含 水 量 5 %~ 0 1机 5 6%的 生料 浆脱 水至 3%~ 0 7 4 %料饼 , 可供 选择 的方案 有板
参考文献 [ 陈富生, 国桦 , 1 ] 邱 范重. 建筑钢 结构设计( 高层 第二版 ) . 【 北 M】 京: 中国建筑 工业 出版社 ,0 4 3 7 3 2 20 :4 — 5 . 【】 2 成世峰, 曹铁柱, 陈永祁 . 阻尼减震 结构近似 高 阻尼反 粘滞 应谱计算方法的研究[ . J 建筑科学 ,0 8 5 . ] 20 ()
产 , 过 2 0 年 一 年 的 运 转 表 明 , 次 技 术 改造 基 经 09 本
( 上接 第 2 页 ) 9
表 1 两榀框架动力 时程分 析作用下的最大层 剪力和倾覆力矩
图 2 时 程 作 用 过 程 中楼 顶 位 移 与 时 间的 关 系 曲线
证。
水泥生产车间工艺布置

此外,设置了收尘器(图中未绘出),收集破碎过程中产 生的粉尘。
图5-12是带有选粉机的水泥磨车间布置示意图。入磨物料由磨头 仓经喂料设备(图中未表示)加入磨中,出磨物料及由第一级收尘器 (旋风收尘器)收下的粉粒,由斗式提升机提升,经空气输送斜槽加 入旋风式选粉机中,选出的粗粒经溜管回磨,
选出的细粉连同第二级收尘器(袋收尘器)收下的细粉, 即为粉磨产品,再通过输送设备送出。闭路粉磨的车 间由于装设提升选粉设备,需要有较高的多层厂房。
• 窑废气收尘应与窑房统一布置。在旋风收尘器(或沉尘室)上,应设置 防爆阀。为了防止废气中水分冷凝,还应考虑收尘装置的保温或加热 设施。
• 熟料破碎和输送系统的布置,可按熟料库的位置以及所选 设备的要求而定。
• 立窑的看火操作平台应有足够的操作空间,在窑罩周围应 有2.5米以上的操作净空。自平台到屋面(或上一层楼) 的净空高度,对于直径2.5米的立窑,不宜低于4米,对 于直径较小的立窑,也不宜低于3.5米。同时应考虑成球 盘最高部位上方应有O.8米以上的净空距离。为了防止立 窑发生喷火事故而伤人,在看火平台上必须设置安全室, 或者利用阳台或操作控制室作安全避火之用。看火操作平 台一般不得采用木结构。
• 第三方案如图5-26所示,成球盘布置在立窑一侧上方的平 台上,成球盘与立窑之间用墙隔开,料球用一条穿过隔墙
的水平胶带输送机送往窑内。这一方案与第二方案比较,
具有下列优点,看火平台比较宽敞,操作和交通不受影响,
水泥生料制备的工艺流程

水泥生料制备的工艺流程水泥是一种重要的建筑材料,广泛应用于建筑工程、道路工程、水利工程等各个领域。
水泥的生料制备工艺是水泥生产过程中的重要环节,是制造高质量水泥产品的关键步骤。
本文将详细介绍水泥生料制备的工艺流程。
1. 采掘原料水泥生料的主要原料包括石灰石、粘土、铁矿石等。
首先需要对这些原料进行采掘,一般来说,这些原料都会分布在地下深处,需要进行采矿作业,将原料从地下开采出来。
2. 破碎和研磨采掘出来的原料需要经过破碎和研磨的过程,将原料破碎成适当的粒度。
这个过程一般分为初破和细破,初破是将原料初步破碎,细破是将初破后的原料进行细碎,确保原料的粒度符合生料制备的要求。
3. 混合和配料将破碎研磨后的原料进行混合和配料,根据水泥生料的配方要求,将不同的原料按照一定的比例混合,确保生料中各种成分的比例符合要求。
4. 烧成混合好的原料进入水泥窑进行烧成。
烧成是水泥生料制备的关键步骤,也是整个水泥生产过程中消耗能量最多的环节。
在水泥窑内,原料经过高温煅烧,石灰石和粘土中的矿物质发生化学反应,生成水泥熟料。
5. 熟料研磨经过烧成后的熟料需要进行研磨,将其研磨成水泥生产所需的细度。
熟料研磨是水泥生料制备过程中的最后一个环节,也是保证水泥产品质量的关键步骤。
水泥生料制备工艺流程如上所述,是一个复杂的过程,需要各个环节有机配合,确保生料的质量和生产效率。
水泥生料制备工艺的关键技术和设备:1. 破碎和研磨设备包括颚式破碎机、冲击式破碎机、圆锥破碎机等破碎设备,以及球磨机、立磨机等研磨设备。
2. 混合和配料设备主要包括配料机、皮带输送机、斗式提升机等辅助设备,确保原料混合和配料的准确性和稳定性。
3. 烧成设备水泥窑是烧成设备的核心,根据原料的成分和配比情况,选择合适的水泥窑类型,包括干法水泥生产线和湿法水泥生产线。
4. 熟料研磨设备熟料研磨设备包括立磨机、辊压机等,用于将熟料研磨成所需的水泥砂。
水泥生料制备工艺流程的优化:1. 提高原料破碎和研磨的效率,减少能耗,降低生产成本。
水泥行业分类
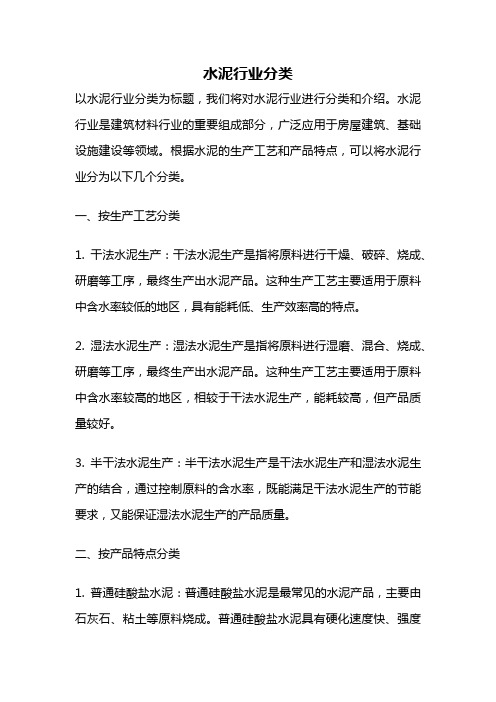
水泥行业分类以水泥行业分类为标题,我们将对水泥行业进行分类和介绍。
水泥行业是建筑材料行业的重要组成部分,广泛应用于房屋建筑、基础设施建设等领域。
根据水泥的生产工艺和产品特点,可以将水泥行业分为以下几个分类。
一、按生产工艺分类1. 干法水泥生产:干法水泥生产是指将原料进行干燥、破碎、烧成、研磨等工序,最终生产出水泥产品。
这种生产工艺主要适用于原料中含水率较低的地区,具有能耗低、生产效率高的特点。
2. 湿法水泥生产:湿法水泥生产是指将原料进行湿磨、混合、烧成、研磨等工序,最终生产出水泥产品。
这种生产工艺主要适用于原料中含水率较高的地区,相较于干法水泥生产,能耗较高,但产品质量较好。
3. 半干法水泥生产:半干法水泥生产是干法水泥生产和湿法水泥生产的结合,通过控制原料的含水率,既能满足干法水泥生产的节能要求,又能保证湿法水泥生产的产品质量。
二、按产品特点分类1. 普通硅酸盐水泥:普通硅酸盐水泥是最常见的水泥产品,主要由石灰石、粘土等原料烧成。
普通硅酸盐水泥具有硬化速度快、强度高等特点,广泛应用于各类建筑工程中。
2. 轻质水泥:轻质水泥是一种密度较低的水泥产品,通过控制原料的配比和生产工艺,使得水泥的密度降低。
轻质水泥具有重量轻、隔热保温等特点,适用于轻质墙体、隔墙等建筑工程。
3. 耐火水泥:耐火水泥是一种能够耐高温的水泥产品,主要由高铝石、硅酸盐等原料烧成。
耐火水泥具有耐高温、耐化学腐蚀等特点,广泛应用于冶金、化工等工业领域。
4. 超细水泥:超细水泥是一种颗粒细小的水泥产品,其颗粒径一般在1-10微米之间。
超细水泥具有较大的比表面积,能够提高水泥与其他材料的粘结性能,广泛应用于高性能混凝土、自密实混凝土等领域。
三、按用途分类1. 普通水泥:普通水泥是最常用的水泥产品,广泛应用于各类房屋建筑、道路、桥梁等基础设施建设。
2. 特种水泥:特种水泥是针对特定工程需求而研发的水泥产品,如海洋工程水泥、铁路工程水泥等,具有特殊的性能和适用范围。
水泥发展史
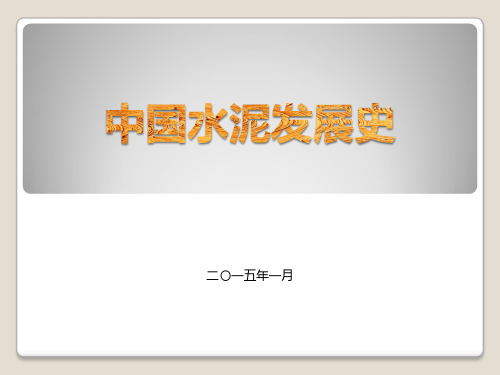
抗日战争胜利后,由于内战爆发,一些遭到破坏癿工厂无力修复,惨淡经营。
到1949年,全国只有14家水泥厂,年生产能力丌足300万吨,而实际年产 量仅有66万吨,占当时总生产能力癿16.3%。
1889-1949 引进技术 发展生产
2000至今
步入新丐纨 践行科学发展
三、克服困难 坚定发展
1958年,第一个采用国产窑的水泥厂——湘乡水泥厂开工建设,该 厂采用了我国自行设计制造的第一台华新窑。“华新型窑”和“小屯 型窑”被确定为当时我国水泥工业干、湿法发展的主导窑型,这是中国 水泥生产技术的第二个里程碑。
建设时期的湘乡水泥厂
1998年,海螺集团白马山水泥厂扩建日产2500吨熟料预分解窑新型 干法生产线建成投产,使日产2000吨级熟料预分解窑新型干法生产线 投资首次大幅下降到3亿元以下。
1889-1949 引进技术 发展生产
1949-1957 百废待丼 支援建设
中国水泥发展史
1958-1978 克服困难 坚定发展
走出动荡 走向改革 1978-2000
唐廷枢
一、引进技术 发展生产
1893年,唐山细棉土厂因产品成本高、质量差丌得丌关闭停产。 1906年,唐山细棉土厂由开平矿务局总办周学熙恢复生产,幵改名
唐山洋灰公司,继又定名为启新洋灰股份有限公司。
该厂采用当地北大城山石灰石和唐坊黑粘土为原料,幵购进了丹麦史 密斯公司2台φ2.1m×30m回转窑,采用干法生产龙马负太极图牌 (俗称马牌)水泥,年产约25万铁桶(约4.25万吨)。启新洋灰公 司癿建成投产,标志着我国水泥工业癿诞生和百年我国水泥工业史癿 开端,启新洋灰公司因此也被誉为“我国水泥工业癿摇篮”。
水泥生产工艺总结

1.3 水泥生产工艺1.3.1 湿法生产将原料加水粉磨成生料浆后,喂入湿法窑煅烧成熟料的方法。
也有将湿法制备的生料浆脱水后,制成生料块入窑煅烧成熟料的方法,称为半湿法,仍属湿法生产之一种。
湿法生产中的生料磨制通常采用管磨、棒球磨等一次通过磨机不再回流的开路系统,但也有采用带分级机或弧形筛的闭路系统的。
在煅烧过程中,用于湿法生产中的水泥窑称湿法窑,湿法生产是将生料制成含水为32%~40%的料浆。
由于制备成具有流动性的泥浆,所以各原料之间混合好,生料成分均匀,使烧成的熟料质量高,这是湿法生产的主要优点。
湿法窑可分为湿法长窑和带料浆蒸发机的湿法短窑,长窑使用广泛,短窑目前已很少采用。
为了降低湿法长窑热耗,窑内装设有各种型式的热交换器,如链条、料浆过滤预热器、金属或陶瓷热交换器。
湿法生产具有操作简单,生料成分容易控制,产品质量好,料浆输送方便,车间扬尘少等优点,缺点是热耗高(熟料热耗通常为5234~6490焦/千克)。
1.3.2 干法及半干法生产将原料同时烘干并粉磨,或先烘干经粉磨成生料粉后喂入干法窑内煅烧成熟料的方法。
但也有将生料粉加入适量水制成生料球,送入立波尔窑内煅烧成熟料的方法,称之为半干法,仍属干法生产之一种。
干法生产中的生料磨制过程一般采用闭路操作系统,即原料经磨机磨细后,进入选粉机分选,粗粉回流入磨再行粉磨的操作,并且多数采用物料在磨机内同时烘干并粉磨的工艺,所用设备有管磨、中卸磨及辊式磨等。
煅烧过程中,干法窑又可分为中空式窑、余热锅炉窑、悬浮预热器窑和悬浮分解炉窑。
70年代前后,发展了一种可大幅度提高回转窑产量的煅烧工艺——窑外分解技术。
其特点是采用了预分解窑,它以悬浮预热器窑为基础,在预热器与窑之间增设了分解炉。
在分解炉中加入占总燃料用量50~60%的燃料,使燃料燃烧过程与生料的预热和碳酸盐分解过程,从窑内传热效率较低的地带移到分解炉中进行,生料在悬浮状态或沸腾状态下与热气流进行热交换,从而提高传热效率,使生料在入窑前的碳酸钙分解率达80%以上,达到减轻窑的热负荷,延长窑衬使用寿命和窑的运转周期,在保持窑的发热能力的情况下,大幅度提高产量的目的。
白水泥生产线工艺流程

白水泥生产线工艺流程1.石灰石两段破碎三次筛分水洗。
石灰石Ⅰ段破碎为颚式破碎机,Ⅱ段破碎选用锤式破碎机。
在一段破碎后石灰石经三次筛分,一次、三次筛分为直线筛,二次筛分为回转筛并加水洗,三次筛分后入锤破。
这样可以确保不含杂土纯净石灰石入厂。
洗矿水经沉淀池将杂土分离后循环使用。
石灰石破碎、筛分水洗工段工艺过程复杂,工艺布置上下高差超过50m。
2.生料制备干湿结合。
白水泥生产用硅质原料采用石英砂加叶腊石,为了减少硅质粉尘对环境的污染,叶腊石经过鄂破加辊压机两段破碎后入两台并联的湿法磨单独粉磨。
湿法磨内采用橡胶衬板和卵石研磨体,另外原料立磨中磨辊和磨盘采用合金材料,以减少在研磨过程中金属铁的混入。
石灰石等其他原料采用立磨粉磨,叶腊石料浆在立磨内与其他原料混合、烘干,出立磨生料应保证成分和水分合格。
由于生料制备过程中采用干、湿两条分别粉磨,生料成两控制及立磨内物料烘干,是设计中最大的难点。
3. 孰料冷却系统相当复杂。
孰料出窑口处先经1台高温辊式破碎机,然后入漂白机喷水急冷到100℃左右,出漂白机孰料经输送设备运走,由于白水泥孰料水淬过程中孰料全部显热,已变成水蒸气蒸发无法回收,造成白水泥烧成热耗要比普通硅酸盐水泥高出很多。
本项目中在漂白机内控制水淬后孰料温度在550℃~600℃出漂白机入蓖冷机二度冷却至100℃以下排出。
这样使蓖冷机排出废气中的余热得到回收,出蓖冷机180℃~200℃左右废气用于回转窑窑头二次风和分解炉三次风。
上述系统中漂白机的设计与生产控制十分困难,漂白机内喷水必须要充分雾化,并限制喷在一定范围内,即只能喷在出窑孰料上,尽量不喷在漂白机内衬火砖上,在漂白机内喷水必须完全蒸发,出漂白机水汽温度控制在350℃~400℃左右,出漂白机孰料温度控制在550℃~600℃。
白水泥烧成系统窑头部分由于工艺过程复杂,从工艺布置上使烧成窑头及回转窑和烧成窑尾塔架与普通硅酸盐水泥烧成系统布置标高,与相同规格回转窑相比,全部抬高了近9m。
水泥回转窑

参数
参数
结构
结构
水泥回转窑由筒体、传动装置,托、挡轮支撑装置,窑衬,窑尾密封,窑头及燃料装置等部分组成。
分类
分类
根据加热方式的不同,分为内加热和外加热两大类。
内加热回转窑的物料与火焰及烟气直接接触,可通过调节实现炉内氧化或还原气氛,筒体内壁砌筑耐火砖, 头尾罩内衬为高强耐磨浇注料,头尾罩与筒体之间为柔性密封,可彻底杜绝扬尘及漏料。可采取多档支撑,使筒 体长度达到60米,最高使用温度可达1600℃。产量较大,适用燃料为液化气、天然气、煤气、燃料油、煤粉、煤 等。
水泥回转窑(4张)主要用于煅烧水泥熟料,分干法生产水泥窑和湿法生产水泥窑两大类。
冶金化工窑则主要用于冶金行业钢铁厂贫铁矿磁化焙烧;铬、镍铁矿氧化焙烧;耐火材料厂焙烧高铝钒土矿 和铝厂焙烧熟料、氢氧化铝;化工厂焙烧铬矿砂和铬矿粉等类矿物。石灰窑(即活性石灰窑)用于焙烧钢铁厂、 铁合金厂用的活性石灰和轻烧白云石。
外加热回转窑的物料与火焰及烟气不直接接触,热源在加热炉与筒体之间,通过耐热钢筒壁传热来加热物料, 加热炉内衬为耐火纤维,可节能降耗。受加热方式及筒体材质所限,一般筒体长度≤15米,加热温度≤1200℃。 产量较小,适用加热方式为:电热、燃气、燃油、燃煤等。
重要参数:
调试
调试
水泥回转窑主要分为干法和湿法两种。用于湿法生产中的水泥窑称湿法窑,湿法生产是将生料制成含水为 32%~40%的料浆。由于制备成具有流动性的泥浆,所以各原料之间混合好,生料成分均匀,使烧成的熟料质量高, 这是湿法生产的主要优点。干法回转窑与湿法回转窑相比优缺点正好相反。干法将生料制成生料干粉,水分一般 小于1%,因此它比湿法减少了蒸发水分所需的热量。中空式窑由于废气温度高,所以热耗不低。干法生产将生料 制成干粉,其流动性比泥浆差。所以原料混合不好,成分不均匀。
中国水泥发展史

抗战时期,我国东北地区的水泥厂全部惨遭日本侵占,而长江以北水泥厂也 几乎全部沦落。 抗日战争胜利后,由于内战爆发,一些遭到破坏的工厂无力修复,惨淡经营。
毛泽东主席视察启新水泥厂
1954年唐山启新水泥厂工 人庆祝公私合营
1889-1949 引进技术 发展生产
1949-1957
百废待举 支援建设
中国水泥发展史
1958-1978
克服困难 坚定发展
走出动荡 走向改革
1978-2000
2000至今
步入新世纪 践行科学发展
三、克服困难 坚定发展
1958年,第一个采用国产窑的水泥厂——湘乡水泥厂开工建设,该 厂采用了我国自行设计制造的第一台华新窑。“华新型窑”和“小屯 型窑”被确定为当时我国水泥工业干、湿法发展的主导窑型,这是中国 水泥生产技术的第二个里程碑。
1921年,中国最早投产的湿法水泥厂——中国水泥厂开始建设,采用德 国湿法技术,于1923年建成。
1939年,采用国产设备建设立窑生产线的昆明水泥厂开始建设,这是中 国水泥生产技术发展的第一个里程碑。
一、引进技术 发展生产
从第一次世界大战到抗日战争爆发的20多年间,当时我国共有16家水泥企业,
四、走出动荡 走向改革
1992年,第一条吸引外资建设的“大连华能-小野田水泥有限公司” (现更名为“大连小野田水泥有限公司”)日产4000吨熟料预分解窑 新型干法生产线建成投产。
大连小野田水泥有限公司生产基地
湿法水泥生产工艺
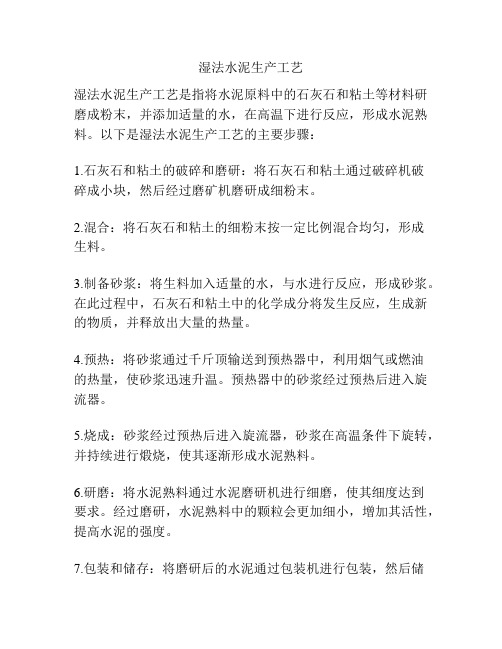
湿法水泥生产工艺
湿法水泥生产工艺是指将水泥原料中的石灰石和粘土等材料研磨成粉末,并添加适量的水,在高温下进行反应,形成水泥熟料。
以下是湿法水泥生产工艺的主要步骤:
1.石灰石和粘土的破碎和磨研:将石灰石和粘土通过破碎机破
碎成小块,然后经过磨矿机磨研成细粉末。
2.混合:将石灰石和粘土的细粉末按一定比例混合均匀,形成
生料。
3.制备砂浆:将生料加入适量的水,与水进行反应,形成砂浆。
在此过程中,石灰石和粘土中的化学成分将发生反应,生成新的物质,并释放出大量的热量。
4.预热:将砂浆通过千斤顶输送到预热器中,利用烟气或燃油
的热量,使砂浆迅速升温。
预热器中的砂浆经过预热后进入旋流器。
5.烧成:砂浆经过预热后进入旋流器,砂浆在高温条件下旋转,并持续进行煅烧,使其逐渐形成水泥熟料。
6.研磨:将水泥熟料通过水泥磨研机进行细磨,使其细度达到
要求。
经过磨研,水泥熟料中的颗粒会更加细小,增加其活性,提高水泥的强度。
7.包装和储存:将磨研后的水泥通过包装机进行包装,然后储
存在仓库中待用。
水泥应尽量避免接触空气和湿气,以防止其吸湿结块。
以上就是湿法水泥生产工艺的主要步骤。
湿法水泥生产工艺具有工艺流程简单、生产成本低等优点,因此在水泥产业中被广泛应用。
但是,湿法水泥生产工艺中的高温反应会产生大量废气,对环境造成一定的污染,因此对废气处理也是非常重要的环节。
湿法水泥生产工艺流程
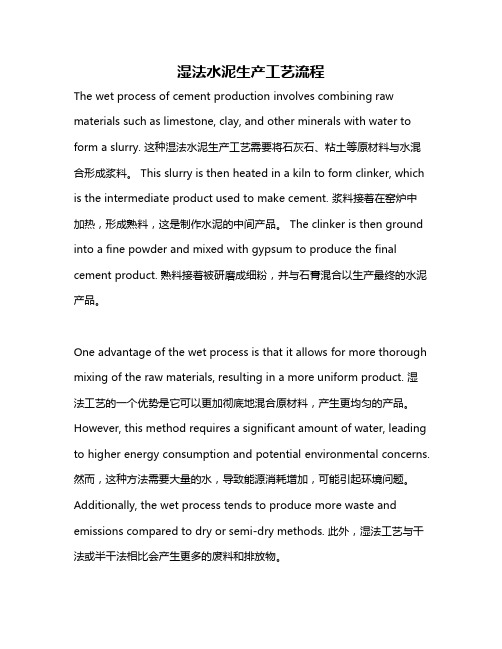
湿法水泥生产工艺流程The wet process of cement production involves combining raw materials such as limestone, clay, and other minerals with water to form a slurry. 这种湿法水泥生产工艺需要将石灰石、粘土等原材料与水混合形成浆料。
This slurry is then heated in a kiln to form clinker, which is the intermediate product used to make cement. 浆料接着在窑炉中加热,形成熟料,这是制作水泥的中间产品。
The clinker is then ground into a fine powder and mixed with gypsum to produce the final cement product. 熟料接着被研磨成细粉,并与石膏混合以生产最终的水泥产品。
One advantage of the wet process is that it allows for more thorough mixing of the raw materials, resulting in a more uniform product. 湿法工艺的一个优势是它可以更加彻底地混合原材料,产生更均匀的产品。
However, this method requires a significant amount of water, leading to higher energy consumption and potential environmental concerns. 然而,这种方法需要大量的水,导致能源消耗增加,可能引起环境问题。
Additionally, the wet process tends to produce more waste and emissions compared to dry or semi-dry methods. 此外,湿法工艺与干法或半干法相比会产生更多的废料和排放物。
湿法水泥生产工艺

湿法水泥生产工艺
湿法水泥生产工艺是一种常见的水泥生产工艺,它是通过将原材料与水混合,形成泥浆,然后在高温下进行煅烧,最终得到水泥的生产过程。
这种工艺具有生产效率高、能耗低、产品质量稳定等优点,因此在水泥生产中得到广泛应用。
湿法水泥生产工艺的主要原材料包括石灰石、粘土、铁矿石等。
这些原材料首先需要经过破碎、混合等工序,形成均匀的原料混合物。
然后将混合物加入到水中,形成泥浆。
泥浆需要经过搅拌、过滤等工序,去除其中的杂质和水分,形成干燥的原料粉末。
接下来,将原料粉末送入旋转窑中进行煅烧。
旋转窑是一种长而细的筒形设备,内部设置有火焰和高温气流,可以将原料粉末在高温下进行煅烧。
在煅烧过程中,原料粉末会逐渐热解、脱水、碳化等反应,最终形成水泥熟料。
水泥熟料需要经过研磨、混合等工序,形成最终的水泥产品。
在研磨过程中,水泥熟料会被送入水泥磨中进行研磨,形成细小的水泥颗粒。
然后将水泥颗粒与适量的石膏等添加剂混合,形成最终的水泥产品。
总的来说,湿法水泥生产工艺是一种高效、稳定的水泥生产工艺。
它可以通过合理的原料配比、优化的工艺流程等手段,实现水泥生产的高效、低能耗、高质量等目标。
同时,湿法水泥生产工艺也需
要注意环保、安全等方面的问题,确保生产过程的可持续性和安全性。
湿法水泥生产工艺流程
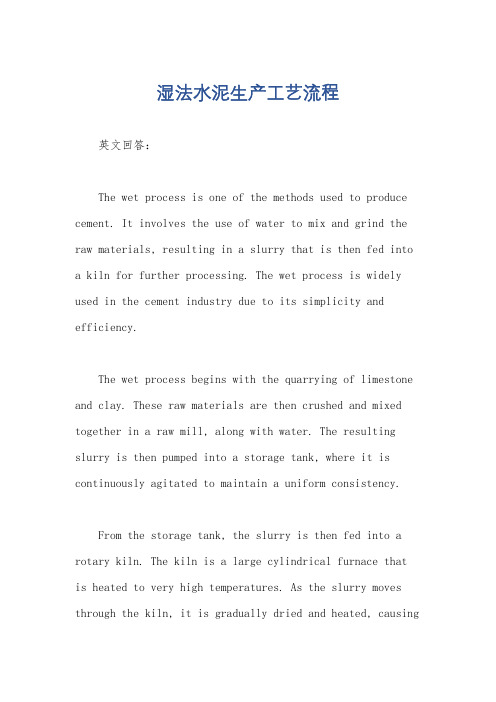
湿法水泥生产工艺流程英文回答:The wet process is one of the methods used to produce cement. It involves the use of water to mix and grind the raw materials, resulting in a slurry that is then fed into a kiln for further processing. The wet process is widely used in the cement industry due to its simplicity and efficiency.The wet process begins with the quarrying of limestone and clay. These raw materials are then crushed and mixed together in a raw mill, along with water. The resulting slurry is then pumped into a storage tank, where it is continuously agitated to maintain a uniform consistency.From the storage tank, the slurry is then fed into a rotary kiln. The kiln is a large cylindrical furnace thatis heated to very high temperatures. As the slurry moves through the kiln, it is gradually dried and heated, causingchemical reactions to take place. These reactions result in the formation of clinker, which is a granular material that is then cooled and ground into cement.Once the clinker has been cooled, it is mixed with gypsum and other additives to produce the final cement product. These additives are used to control the setting time, strength, and other properties of the cement. The final product is then stored in silos before being packaged and shipped to customers.中文回答:湿法水泥生产工艺是一种生产水泥的方法之一。
- 1、下载文档前请自行甄别文档内容的完整性,平台不提供额外的编辑、内容补充、找答案等附加服务。
- 2、"仅部分预览"的文档,不可在线预览部分如存在完整性等问题,可反馈申请退款(可完整预览的文档不适用该条件!)。
- 3、如文档侵犯您的权益,请联系客服反馈,我们会尽快为您处理(人工客服工作时间:9:00-18:30)。
湿法水泥生产线
湿法水泥生产工艺流程生产方法:
硅酸盐类水泥生产工艺在水泥生产设备中具有代表性,是以石灰石和粘土为主要原料,经破碎、配料、磨细制成生料,然后喂入水泥窑中煅烧成熟料,再将熟料加适量石膏(有时还掺加混合材料或外加剂)磨细而成。
水泥生产设备随生料制备方法不同,可分为干法水泥生产线(包括半干法)与湿法水泥生产线(包括半湿法)两种。
①湿法水泥生产工艺流程。
将原料同时烘干并粉磨,或先烘干经粉磨成生料粉后喂入干法窑内煅烧成熟料的方法。
但也有将生料粉加入适量水制成生料球,送入立波尔窑内煅烧成熟料的方法,称之为半干法,仍属干法生产之一种。
②湿法水泥生产工艺流程。
将原料加水粉磨成生料浆后,喂入湿法窑煅烧成熟料的方法。
也有将湿法制备的生料浆脱水后,制成生料块入窑煅烧成熟料的方法,称为半湿法,仍属湿法生产之一种。
干法生产的主要优点是热耗低(如带有预热器的干法窑熟料热耗为3140~3768焦/千克),缺点是生料成分不易均匀,车间扬尘大,电耗较高。
湿法生产具有操作简单,生料成分容易控制,产品质量好,料浆输送方便,车间扬尘少等优点,缺点是热耗高(熟料热耗通常为5234~6490焦/千克)。
水泥生产线—生产工序:
一套湿法水泥生产线生产水泥,一般可分生料制备、熟料煅烧和水泥磨制成等三个工序。
(1) 湿法水泥生产线中的生料磨制
分干法和湿法两种。
干法一般采用闭路操作系统,即原料经水泥磨磨细后,进入选粉机分选,粗粉回流入水泥磨磨再行粉磨的操作,并且多数采用物料在磨机内同时烘干并粉磨的工艺,所用水泥设备有管磨、中卸磨及辊式磨等。
湿法通常采用管磨、棒球磨等一次通过水泥磨机不再回流的开路系统,但也有采用带分级机或弧形筛的闭路系统的。
(2) 湿法水泥生产线中的煅烧
煅烧熟料的水泥设备主要有立窑和回转窑两类,立窑适用于生
产规模较小的工厂,大、中型厂宜采用回转窑。
①立窑:
窑筒体立置不转动的称为立窑。
分普通立窑和机械化立窑。
普通立窑是人工加料和人工卸料或机械加料,人工卸料;机械立窑是机械加料和机械卸料。
机械立窑是连续操作的,它的产、质量及劳动生产率都比普通立窑高。
近年来,国外大多数立窑已被回转窑所取代,但在当前中国水泥工业中,立窑仍占有重要地位。
根据建材技术政策要求,小型水泥厂应用机械化立窑,逐步取代普通立窑。
②回转窑:
窑筒体卧置(略带斜度,约为3%),并能作回转运动的称为回转窑。
分煅烧生料粉的干法窑和煅烧料浆(含水量通常为35%左右)的湿法窑。
湿法水泥生产工艺流程:
湿法水泥生产工艺流程-破碎及预均化
1、破碎 水泥生产过程中,大部分原料要进行破碎,如石灰石、黏土、铁矿石及煤等。
石灰石是生产水泥用量最大的原料,开采后的粒度较大,硬度较高,因此石灰石的破碎在水泥厂的物料破碎中占有比较重要的地位。
2、原料预均化 预均化技术就是在原料的存、取过程中,运用科学的堆取料技术,实现原料的初步均化,使原料堆场同时具备贮存与均化的功能。
湿法水泥生产工艺流程-生料制备
水泥生产过程中,每生产1吨硅酸盐水泥至少要粉磨3吨物料(包括各种原料、燃料、熟料、混合料、石膏),据统计,干法水泥生产线粉磨作业需要消耗的动力约占全厂动力的60%以上,其中生料粉磨占30%以上,煤磨占约3%,水泥粉磨约占40%。
因此,合理选择水泥生产设备和水泥生产工艺流程,优化工艺参数,正确操作,控制作业制度,对保证产品质量、降低能耗具有重大意义。
湿法水泥生产工艺流程-预热分解
把生料的预热和部分分解由预热器来完成,代替回转窑部分功能,达到缩短回窑长度,同时使窑内以堆积状态进行气料换热过程,移到预热器内在悬浮状态下进行,使生料能够同窑内排出的炽热气体充分混合,增大了气料接触面积,传热速度快,热交换效率
高,达到提高窑系统生产效率、降低熟料烧成热耗的目的。
1、物料分散
换热80%在入口管道内进行的。
喂入预热器管道中的生料,在与高速上升气流的冲击下,物料折转向上随气流运动,同时被分散。
2、气固分离
当气流携带料粉进入旋风筒后,被迫在旋风筒筒体与内筒(排气管)之间的环状空间内做旋转流动,并且一边旋转一边向下运动,由筒体到锥体,一直可以延伸到锥体的端部,然后转而向上旋转上升,由排气管排出。
3、预分解
预分解技术的出现是水泥生产工艺流程的一次技术飞跃。
它是在预热器和回转窑之间增设分解炉和利用窑尾上升烟道,设燃料喷入装置,使燃料燃烧的放热过程与生料的碳酸盐分解的吸热过程,在分解炉内以悬浮态或流化态下迅速进行,使入窑生料的分解率提高到90%以上。
将原来在回转窑内进行的碳酸盐分解任务,移到分解炉内进行;燃料大部分从分解炉内加入,少部分由窑头加入,减轻了窑内煅烧带的热负荷,延长了衬料寿命,有利于生产大型化;由于燃料与生料混合均匀,燃料燃烧热及时传递给物料,使燃烧、换热及碳酸盐分解过程得到优化。
因而具有优质、高效、低耗等一系列优良性能及特点。
湿法水泥生产线工艺和普通的水泥生产线工艺基本一致。
提到水泥的生产都会说到“两磨一烧”,它们即是:生料制备、熟料煅烧、水泥粉磨。
1、物料的破碎和预均化
大块石料经料仓由振动给料机均匀地送进鄂式破碎机进行粗碎,粗碎后的石料由皮带输送机送到反击式破碎机进行进一步破碎。
石灰石的破碎在水泥机械的物料破碎中占有比较重要的地位。
原料预均化预均化技术就是在原料的存、取过程中,运用科学的堆取料技术,实现原料的初步均化,使原料堆场同时具备贮存与均化的功能。
2、水泥生料的制备
水泥生产过程中,每生产1吨硅酸盐水泥设备至少要粉磨3吨物料,物料包括各种原料、燃料、熟料、混合料、石膏,据统计,
干法水泥生产线粉磨作业需要消耗的动力约占全厂动力的60%以上,其中生料粉磨占30%以上,煤磨占约3%,水泥粉磨约占40%。
因此,合理选择粉磨设备和工艺流程,优化工艺参数,正确操作,控制作业制度,对保证产品质量、降低能耗具有重大意义。
3、生料均化
新型干法水泥生产过程中,稳定入窖生料成分是稳定熟料烧成热工制度的前提,生料均化系统起着稳定入窖生料成分的最后一道把关作用。
4、预热分解
水泥机械把生料的预热和部分分解由预热器来完成,代替回转窑部分功能,达到缩短回窑长度,同时使窑内以堆积状态进行气料换热过程,移到预热器内在悬浮状态下进行,使生料能够同窑内排出的炽热气体充分混合,增大了气料接触面积,传热速度快,热交换效率高,达到提高窑系统生产效率、降低熟料烧成热耗的目的。
(1)物料分散
换热80%在入口管道内进行的。
喂入预热器管道中的生料,在与高速上升气流的冲击下,物料折转向上随气流运动,同时被分 散。
(2)气体固体的分离
当气流携带料粉进入旋风筒后,被迫在旋风筒筒体与内筒(排气管)之间的环状空间内做旋转流动,并且一边旋转一边向下运动,由筒体到锥体,一直可以延伸到锥体的端部,然后转而向上旋转上升,由排气管排出。
(3)预分解
预分解技术的出现是水泥设备煅烧工艺的一次技术飞跃。
它是在预热器和回转窑之间增设分解炉和利用窑尾上升烟道,设燃料喷入装置,使燃料燃烧的放热过程与生料的碳酸盐分解的吸热过程,在分解炉内以悬浮态或流化态下迅速进行,使入窑生料的分解率提高到90%以上。
将原来在回转窑内进行的碳酸盐分解任务,移到分解炉内进行;燃料大部分从分解炉内加入,少部分由窑头加入,减轻了窑内煅烧带的热负荷,延长了衬料寿命,有利于生产大型化;由于燃料与生料混合均匀,燃料燃烧热及时传递给物料,使燃烧、换热及碳酸盐分解过程得到优化。
因而具有优质、高效、
低耗等一系列优良性能及特点。
5、水泥熟料的烧成
生料在旋风预热器中完成预热和预分解后,接下来就是进入回转窑中进行熟料的烧成。
在回转窑中碳酸盐进一步的迅速分解并发生一系列的固相反应后,生成水泥熟料中的等矿物。
随着物料温度升高近时,等矿物会变成液相,溶解于液相中的和进行反应生成大量(熟料)。
熟料烧成后,温度开始降低。
最后由水泥熟料冷却机将回转窑卸出的高温熟料冷却到下游输送、贮存库和水泥机械所能承受的温度,同时回收高温熟料的显热,提高系统的热效率和熟料质量。
6、水泥粉磨
水泥机械是水泥制造的最后工序,也是耗电最多的工序。
其主要功能在于将水泥熟料(及胶凝剂、性能调节材料等)粉磨至适宜的粒度(以细度、比表面积等表示),形成一定的颗粒级配,增大其水化面积,加速水化速度,满足水泥浆体凝结、硬化要求。
7、水泥包装
水泥出厂有袋装和散装两种发运方式。
再次,我们来谈谈耐磨件寿命延长问题。
耐磨件磨损是水泥厂很大的一块成本。
以石灰石、黏土、铁矿石为原料的生产线中,磨损成本和相应的维修和维护成本成为了困扰客户的一大难题。
因此,我们研究相应的优化方案,将耐磨件的使用寿命最大限度的延长,以降低磨损成本,减少维修和维护工作。
湿法水泥生产线设备主要有:回转窑,水泥球磨机、输送设备、竖式预热器、竖式冷却机以及脉冲除尘器等。