改善八大步骤
品质改善的步骤

4.作業方法(Method)
品質改善步驟
2.材料(Material) 活動的重點(細部的主要原因): 1>.材料的哪一部份會影響到特性(原料品質的不良,性能不足等). 2>.被搬入的材料質量有差錯(不小心而造成的錯誤、交貨期). 3>.作業中有異常材料混入(不小心而造成的錯誤、環境). 4>.材料的處理(品質不良、異常品各種的混入). 3.作業人員(Man) 活動的重點(細部的主要原因): 1>.作業人員中哪一因素影響到特性(經驗、技術、教育). 2>.作業是否與作業人員的特性一致(重新配置工作與教育訓練). 3>.作業人員的健康狀態(休養、飲食、睡眠). 4>.作業人員的品質意識(士氣、教育). ◎ 作業人員是否按照指示圖作業 ◎ 作業人員是否在熟讀指導書以后才開始作業.
5>.為甚麼(WHY> 6>.如何做(HOW TO DO) 7>.做多少(HOW MUCH)
品質改善步驟
3. 產生改善構想的方法
3.1 集益思廣
3.2 缺點列舉法
3.5 關聯圖法
3.6 系統圖法
3.3 奧斯本式自問法 3.7 其他
3.4 KJ法
3>.減少初期的不良產品
4>.減少品質的異常
5>.減少賠價請求.
6>.提高品質
7>.提高品質能力
活動的結果: 1>.使工程處於安定狀態
2>.防止抱怨的再度發生
3>.確實的遵守作業指導書
4>.使管理點明確
5>.依照管理圖進行管理工程 6>.標準化 7>.提高信賴性 8>.使管理制度化
2.成本(Cost)
生产七大浪费及改善八大步骤
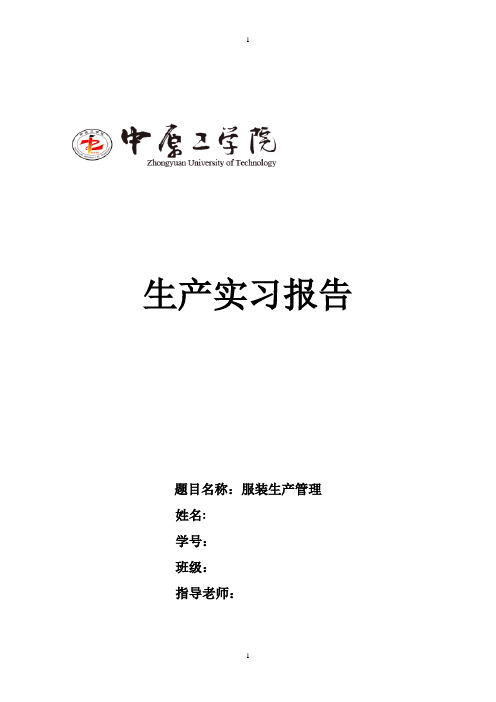
生产实习报告题目名称:服装生产管理姓名:学号:班级:指导老师:企业中普遍存在的八大浪费涉及过量生产、等待时间、运输、库存、过程(工序)、动作、产品缺陷以及忽视员工创造力,在生活中的现象和改善方法具体如下:1.、等待的浪费:即等着下一动作的来临。
造成原因常例如生产线的品种切换、作业不平衡、上下工序延误,下游无事可做、时常缺料设备闲置、品质不良、修机,制造通知或设计图未送到等。
改善:不要监视机器、不要巡逻救生、不要袖手旁观2.、搬运的无驮:搬运的动作分解开来,包含放置、堆积、移动、整理等动作,是传统的机能别水平式的布置造成的。
若使用输送带、无人搬运车不是搬运的合理化。
增加搬运批量、以及减少搬运频率、也不是合理化的搬运。
改善:不要乱流、不要粗流、不要停留3.、不良的浪费:任何的不良品产生,皆造成材料、机器、人工等的浪费。
造成原因为制程能力不足的技术层有问题及生产现物管理方式或管理观念错误所造成。
改善:不接受不良品、不制造不良品、不流出不良品。
减少不良的二十字真言:保持新鲜、迅速确实、三线一体、不要碰触、要一致性。
4.、动作的浪费:是指作业过程中不佳的浪费。
常见的浪费动作有:转向、反转、距离、寻找、堆叠、移动。
将产品重复从箱子里拿出来加工、加工后再放回箱子排列整齐、这是取放动作堆叠、移动的无驮。
改善:不插秧、不摇头、不弯腰。
5.、加工的浪费:指在生产过程中有些加工程序是可以省略、替代、重组或合并的。
如“压缩空气”“切削空气”冲床机器在整个加工过程中“碰碰”声音间接短效率高、较少发生“压缩空气”的现象。
否则相反。
改善:不做切削空气、不做木偶动作、不做立正动作。
6.、库存的浪费(为万恶之源):是因传统以来的许多错误生产观念所造成的。
分三种:1)材料库存:大量采购成本低。
2)在制品库存:不良重修机器故障。
3)成品库存:预测生产与实际需求量不同。
库存所带来的弊端:1)产生不必要的搬运、堆积、放置、防护处理找寻等浪费;2)使先进先出作业困难;3)损失利息及管理费用;4)物品贬值的风险以及占用空间而引起的投资浪费等。
现场改善8大步骤(非常实用)
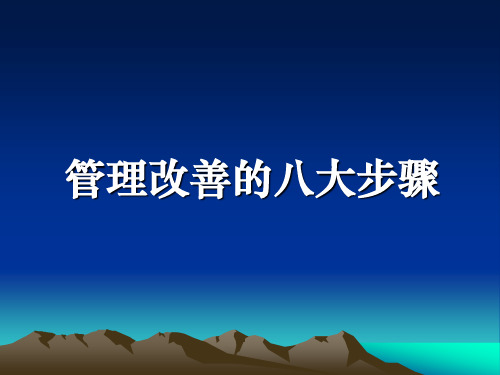
371 0%
廢 品 數 量 整 腳 不 合 格 其 它 (外 觀 ) 焊 錫 不 良 剝 漆 不 良 L值 過 高 磁 心 不 良 L值 過 低 點 膠 不 合 格 异 物 附 著 長 短 不 一 套 模 不 合 格 套 管 不 合 格 導 線 受 傷 繞 線 過 松 特 性 不 良
六、对策分析(挑骨头)
目的:对所有改善对策进行分析,将一 些无价值和无法操作的改善对策进 行排出。
改 善 对 策 表
序号 改善项目 改 善 对 策 执行部门 责任人
8D改善报告
见附表
七、明确改善执行计划(甘特图)
目的:对改善的推行项目制订执行计划, 做好工作执行的日程安排。
甘特图
序号
1 2 3
推行项目
管理改善的八大步骤
一、找问题
(柏拉图)
目的:依据各项KPI数据分析报表,找出问题的重
点。
1200000% 96% 98% 99% 99% 100% 100% 100% 100% 90%
不良数量
900000 800000 700000 600000 500000 400000 300000 200000 100000
不良数量累 计比例
0
二、找原因(鱼骨图)
目的:找出问题的原因, 对异常的原因进行 全面的分析。
鱼骨图
三、找主要原因(挑鱼刺)
目的:对异常的原因进行重点明确,明确出产 生异常的主要原因。 注意事项: A.找出的问题是最有影响的部分;
(也就是产生影响的80%部分)
B.在现状是有可操作性的;
四、找问题解决的主次(象限分析)
67% 56% 43% 242775 191738 24% 123427
专案改善八大步骤
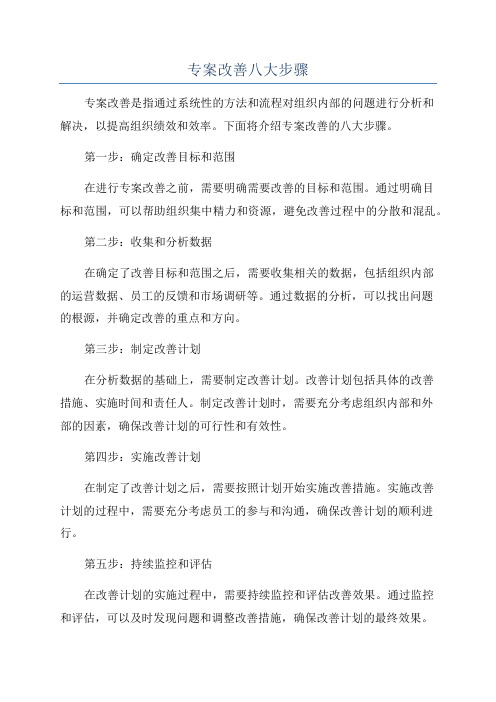
专案改善八大步骤专案改善是指通过系统性的方法和流程对组织内部的问题进行分析和解决,以提高组织绩效和效率。
下面将介绍专案改善的八大步骤。
第一步:确定改善目标和范围在进行专案改善之前,需要明确需要改善的目标和范围。
通过明确目标和范围,可以帮助组织集中精力和资源,避免改善过程中的分散和混乱。
第二步:收集和分析数据在确定了改善目标和范围之后,需要收集相关的数据,包括组织内部的运营数据、员工的反馈和市场调研等。
通过数据的分析,可以找出问题的根源,并确定改善的重点和方向。
第三步:制定改善计划在分析数据的基础上,需要制定改善计划。
改善计划包括具体的改善措施、实施时间和责任人。
制定改善计划时,需要充分考虑组织内部和外部的因素,确保改善计划的可行性和有效性。
第四步:实施改善计划在制定了改善计划之后,需要按照计划开始实施改善措施。
实施改善计划的过程中,需要充分考虑员工的参与和沟通,确保改善计划的顺利进行。
第五步:持续监控和评估在改善计划的实施过程中,需要持续监控和评估改善效果。
通过监控和评估,可以及时发现问题和调整改善措施,确保改善计划的最终效果。
第六步:培训和发展在实施改善计划的过程中,需要重视员工的培训和发展。
通过培训和发展,可以提高员工的能力和素质,增强组织的竞争力和创新能力。
第七步:建立改善文化在长期的改善过程中,需要建立改善文化。
改善文化包括组织内部的价值观、信念和行为准则,它能够鼓励员工提出问题和改善的建议,促进组织的学习和进步。
第八步:持续改善和创新改善是一个持续的过程,需要不断进行改进和创新。
通过持续改善和创新,组织可以不断提高绩效和效率,保持竞争优势。
总结起来,专案改善的八大步骤包括确定改善目标和范围、收集和分析数据、制定改善计划、实施改善计划、持续监控和评估、培训和发展、建立改善文化以及持续改善和创新。
通过按照这些步骤进行改善,可以帮助组织提高绩效和效率,保持竞争优势。
七大浪费及改善八大步骤
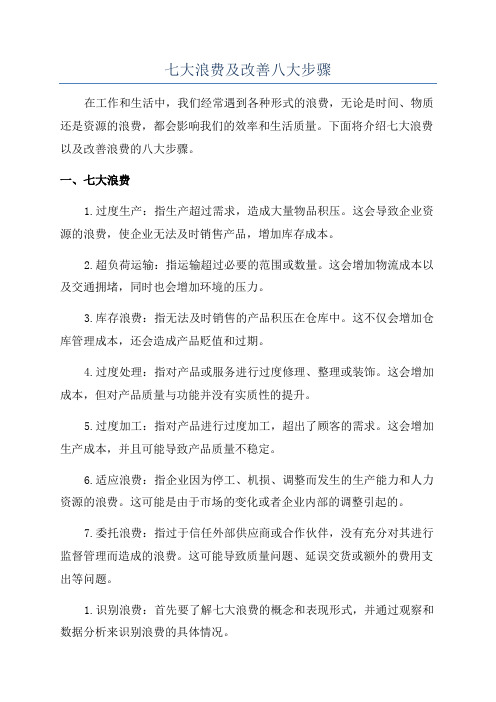
七大浪费及改善八大步骤在工作和生活中,我们经常遇到各种形式的浪费,无论是时间、物质还是资源的浪费,都会影响我们的效率和生活质量。
下面将介绍七大浪费以及改善浪费的八大步骤。
一、七大浪费1.过度生产:指生产超过需求,造成大量物品积压。
这会导致企业资源的浪费,使企业无法及时销售产品,增加库存成本。
2.超负荷运输:指运输超过必要的范围或数量。
这会增加物流成本以及交通拥堵,同时也会增加环境的压力。
3.库存浪费:指无法及时销售的产品积压在仓库中。
这不仅会增加仓库管理成本,还会造成产品贬值和过期。
4.过度处理:指对产品或服务进行过度修理、整理或装饰。
这会增加成本,但对产品质量与功能并没有实质性的提升。
5.过度加工:指对产品进行过度加工,超出了顾客的需求。
这会增加生产成本,并且可能导致产品质量不稳定。
6.适应浪费:指企业因为停工、机损、调整而发生的生产能力和人力资源的浪费。
这可能是由于市场的变化或者企业内部的调整引起的。
7.委托浪费:指过于信任外部供应商或合作伙伴,没有充分对其进行监督管理而造成的浪费。
这可能导致质量问题、延误交货或额外的费用支出等问题。
1.识别浪费:首先要了解七大浪费的概念和表现形式,并通过观察和数据分析来识别浪费的具体情况。
2.制定改善目标:根据识别出的浪费情况,制定明确的改善目标,包括减少过剩生产、降低物流成本、控制库存等方面。
3.分析原因:深入分析每个浪费现象背后的原因,找出造成浪费的根本问题。
4.寻找解决方案:根据分析结果,寻找符合实际情况的解决方案。
可以进行团队讨论和跨部门合作,以找到最佳的解决方案。
5.实施改善措施:在制定改善方案的基础上,通过有效的实施措施来减少浪费。
这涉及到管理的改进、流程的调整、员工的培训等多个方面。
6.持续改进:改善工作不是一次性的,而是需要持续不断的努力。
建立一个持续改进的机制,定期评估改善效果并进行调整。
7.培训与教育:通过培训和教育,提高员工对浪费的认识和改善意识。
IE七大浪费及改善八大步骤(精)

从成本主义、售价主义到利润主义说起」成本主久训价工成松■利润(独山性商庇尖方M 场)」售价主义:利润Tf价•成木(利河取决『沛场俾价的岛沁JI」利润主文:成木二桝价•利润(以利润为II标粟设址[| 目标成本的患想方式〉■我们嘤达到11标利润就必硕努力达到11标成札*成本的主菱但成*材料、人工、设备与管理.而M 料山市场调W决定•因此燹降低成本.必顼消除人工、设备及管理的浪费.何谓ANPS 中的浪费?J 凡足不会赚钱的动作东ANPS 的观念屮点 是浪费•例如工作中的寻找、搬运、翻转、取 放尊动m~M 然作业庚帘常累紂满头 大汗.但其动作并不是必须耍做的• 动与人字旁动的区别。
经此认知,看看我们金业内能见的浪费会§5 有哪些呢?一一请看下文:ANPS 中常见的七种浪费一、等待的浪费’即等着下一动作的耒审・追成 原因常有’作业不平衡、安井作业不当、待料、 品质不良、修机……等・等待的三不原则: 不要袖手旁) 二、it 运的无矢 ■、堆积.移动. 水平式的布■造成的.若使用输送带、无人it 运 车不是授运的合理化•増加撮运批量、以及减少 授运频率、也不是合理化的it 运. N 搬运三不原则:不要乱流、不要粗流、不要停留不要监视豔黯畑職r ▼三、不良的浪ih任何的不良品产生.皆造成材料、机器、人工等的浪费.追成廉因为制程能力不足的技术层有问题及生产现物管理方式或管理双念错误所造成.不良的三不原则:不接受不良品、不制造不良品・不流出不良品.减少不良的二十字真言:保持新鲜、迅速礎实. 三线一体.不要碰触、要一致性。
四、动作的浪费’是指作业过程中不佳的浪费.常見的浪费动作有,转向、反转、距离、寻找、堆移动•将产品重复从箱子里拿出来加工、加工后再放回箱子排列SE齐、这是取放动作堆叠、移动的无駅・动作三不原则:不插秧.不摇头、不弯腰。
w五、加工的浪费:指在生产过程中有些加工程序是可以省路、替代、重组或合并的・如鶯压缩空r❶•切削空气"冲床机器在務个加工过程中勢礒sr声音间接短效率高、较少发生•压缩空气*的现掠• 否则相反.加工三不原则:不做切削空气、不做木偶动作、不做立正动作。
改善八大步骤和统计手法 v1.0
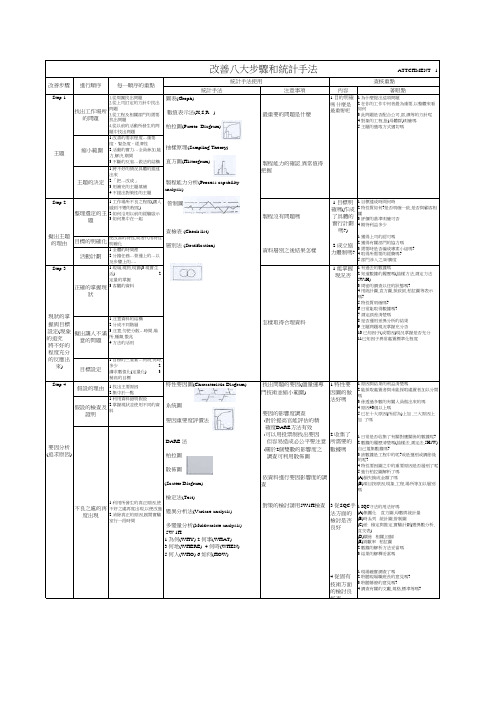
內容整理選定的主題目標的明確化活動計劃正確的掌握現狀擬出讓人不滿意的問題目標設定假設的理由假設的檢查及證明著眼點.特性要因圖(Characteristic Diagram).系統圖.要因重要度評價法.DARE 法.柏拉圖.散佈圖(Scatter Diagram).檢定法(Test).變異分析法(Variace analysis).多變量分析(Multivariate analysis).5W 1H1.為何(WHY)2.何事(WHAT)3.何地(WHERE)4.何時(WHEN)5.何人(WHO)6.如何(HOW).找出問題的要因(儘量運專門技術並縮小範圍).要因的影響度調查:對於提高官能評估的精 確度DARE 方法有效 :可以用投票制找出要因 但容易造成必公平要注意 :關於2個雙數的影響度之 調查可利用散佈圖..依資料進行要因影響度的調查.對策的檢討請用5W1H 檢查1.特性要因圖的做法好嗎2.收集了所需要的數據嗎3.從SQC 手法方面的檢討是否良好4.從固有技術方面的檢討良好否1.原因與結果的利益清楚嗎2.能採取處置者與未能採取處置者加以分開嗎3.係透過多數的有關人員做出來的嗎4.原因40個以上嗎5.已在十大原因(所認為)上加 ,三大原因上加了嗎1.日常是否收集了有關對應關係的數據呢?2.數據的履歷清楚嗎(抽樣法,測定法,5H1W)自己蒐集數據嗎?3.該數據是工程中的呢?或是選別或調節後的呢?4.特性要因圖之中的重要原因是否層別了呢5.進行柏拉圖解析了嗎(A)損失換成金額了嗎(B)項目按原因,現象,工程,場所等加以層別嗎1.SQC 守法的用法好嗎(A)集團化....直方圖,母數與統計量(B)時系列...統計圖,管制圖(C)差...檢定與推定,實驗計劃(變異數分析,直交表)(D)關係...相關,回歸(E)貢獻率...柏拉圖2.數據的解析方法妥當嗎3.結果的解釋妥當嗎1.現場確實調查了嗎2.聆聽現場職班長的意見嗎?3.聆聽幕僚的意見嗎?4.調查有關的文獻,規格,標準等嗎?.最重要的問題是什麼1.目的明確嗎 什麼是最重要呢1.為什麼提出這項問題2.在你的工作中何者最為重要,以整體來看如何3.此問題是否配合公司,部,課等的方針呢4.對象的工程,批(母體群)明確嗎5.主題的選取方式適切嗎改善八大步驟和統計手法 ATTCHMENT 11.目標明確嗎(作成了具體的實行計劃嗎?)2.成立協力體制嗎? 1.目標達成時間何時2.特性質如何?是否明確一致,是否與顧客相關3.評價的基準明確可否4.期待利益多少1.獲得上司的認可嗎2.獲得有關部門的協力嗎3.需要時是否編成專案小組嗎?4.取得所需要的經費嗎?5.部門涉入之深/廣度使改善的特性,或者代用特性明確化Step 2擬出主題的理由1.工作場所不良之程度(讓人感到不變的程度)2.如何沿用以前的經驗啟示3.如何集中在一起查核重點1.利用資料證明假設2.掌握現狀並使用不同的資料不良之處的再度出現1.利用所發生的真正原因,使不好之處再度出現,以便改進2.消除真正的原因,展開實驗室行一段時間1.能掌握現況否1.有過去的數據嗎2.知道數據的履歷嗎(抽樣方法,測定方法5W1H)3.周密的調查以往的狀態嗎?4.用統計圖,直方圖,採致詞,柏拉圖等表示嗎?5.特性質明確嗎?6.日常能取得數據嗎?7.測定誤差清楚嗎8.是否運用差異分析的結果9.主題問題現況掌握充分否10.已知因子(或要因)現況掌握是否充分11已知因子異常處置標準化程度.圖表(Groph). 數值表示法(X,S,R...).柏拉圖(Pareto Diagram).抽樣原理(Sampling Theory).直方圖(Historgram).製程能力分析(Process capability analysis) .管制圖(Crntrol chart).查檢表 (Check list).層別法 (Stratification).怎樣取得合理資料.製程能力的確認,異常值得把握.製程沒有問題嗎.資料層別之後結果怎樣統計手法使用統計手法注意事項1.全體的時間裡2.分擔任務…營運上的…以及步驟上的….1.找出主要原因2.集中於一點Step 3現狀的掌握與目標設定(現象的追究-----將不好的程度充分的反應出來)1.現場,現物,現實(3 現實生活)2.定量的掌握3.客觀的資料1.注意資料的結構2.分成不同階層3.注意,勿使分散…時間,場所,種類,徵兆4.方法的活用1.目標的三要素…何物,何時,多少2.講求數值化(定量化)3.稍高的目標Step 4要因分析(追求原因)Step 1主題改善步驟進行順序1.從周圍找出問題2.從上司訂定的方針中找出問題3.從工程及相關部門的需要找出問題4.從以前的活動所發生的問題中找出問題1.改善的要求程度…重要度,緊急度,經濟性2.活動的實力…全員參加,能力,解決,期間3.不斷的反省…做法的結構1.將不好的情況具體的描述出來2.「把…改成」3.用補充的主題填補4.不提出對策性的主題 縮小範圍每一順序的重點找出工作場所的問題主題的決定對策的提出1.對策的內容明確與否對策的實施2.作成了對策的實行計劃書嗎有形成果的掌握無形成果的掌握活動的反省今後的計劃將缺失檢討應用於下一次的活動1.標準化實施了嗎1.效果確認程度1.效果的掌握2.目標達成率3.其它無形效果為何柏拉圖.無因數方法.直方圖.管制圖.檢定法.抽樣檢驗法.反省的要點是實績/計劃(數據,方法)的對比.暫時處理和永久對策改善的檢討.所選的主題是否減少了不適合性.製程能力達到1.33以上了嗎?.對異常值原因很了解了嗎?是否有對異常原因的判明及採取防止再發生的方法.對策效果是否吻合.採去的方法是否適切.從步驟1開始.經由審核結果和目標的比較來確認被留下來的問題點.作業標準.檢驗標準.更新相關文件QAPS.SOP.OCAP.管理改善的步驟正確嗎?.固有技術的運用.IE改善手法.定案之後要依對策實施.將對策的詳細內容知各實施部門.有關連的部門的協力是很重要的.實施上沒有問題嗎.計劃實施.不能實行變更計劃1.對策的內容與解析結果是否良好2.是在發防止對策或只是修理處理呢?其區別明確嗎?3.用多少個對策案加以比對檢討呢?4.對策是否具體,愚巧5.對策執行的困難度1.此對策的實行負責人決定了嗎2.對策案何時詴行3.效果(經詴行)與預測吻合否4.與有關單位進行調整嗎5.實施評價的基準(效果及時期)明確嗎6.正式實施的時期何時Step8殘留問題與將來計劃(改變做法的探索)標準化徹底的瞭解實施完全的確認1.5W1H2.與相關部門的合作3.實施期間的明確化1.把缺失檢討用於今後的活動…QC式理念(QG的基本)2.期望該冷寓的成長….該領域活動的PDCA1.確實的實施1.重視必要的手續(新設計,修訂廢止的手續)2.更換日期的連絡要確實(避免混亂)3.有關人員的教育,訓練1.確立實施狀況的檢查體制2.實施日常的管理體制…..管制圖,管理圖表1.計劃與實施的差距2.解決問題活動的檢討3.營運方面的檢討1.如何把活動的檢討沿用於今後之活動2.明確地處理剩下的問題3.把獲得之效果,往水平方向擴展1.對策事項的內容反省了嗎?2.殘留問題檢討3.考慮下次的問題了1.有效對策是否納入標準化2.管理點及管理特性明確嗎3.管理特性用管制圖管制嗎?4.進行標準類(作業標準等)的制訂或改訂嗎?5.標準類的作成及改訂貫徹至作業員嗎?6.與有關部門進行標準類的調整嗎?1.沒有對策 ,察明其原因,有再度調查解析的意願嗎?2.再度進行解析對策嗎?3.反省僅止於記錄嗎?1.是否殘留問題點,其與要因分析結果之相關差異為何1.下次的主題為何2.回到 1.項(主題的選定)Step5對策及實施Step6效果確認(活動的結果)1.真正的原因與對策連接一起2.創意工夫…全員參與,集思廣益3.應急對策與恆久對策的明確化應急對策…消除某種現象恆久對策...消除某種原因4.計劃的擬訂1.先靠自己的力量2.上司,各成員的支援3.百折不撓的幹4. 對策與效果的結合…一次對策, 二次對策,實驗,試行5.教育,訓練1.效果的掌握 ,展示法…..現況掌握2.與目標進行比較3.每一對策的效果都要掌握4.二次性的效果也要掌握5.如果毫無效果的話….再從分析開始1.個人或者各種領域的水準2.工作場所的水準3.公司的水準----GC活動的目的4. 地域的水準Step7標準化(訂定對策,以免重蹈覆轍)因與結果的利益清楚嗎因40個以上嗎在十大原因(所認為)上加據的履歷清楚嗎(抽樣法,蒐集數據嗎?數據是工程中的呢?行柏拉圖解析了嗎失換成金額了嗎目按原因,現象,工程,C守法的用法好嗎團化....直方圖,系列...統計圖,管制圖..檢定與推定,實驗計劃係...相關,回歸獻率...柏拉圖據的解析方法妥當嗎果的解釋妥當嗎場確實調查了嗎聽現場職班長的意見嗎?聽幕僚的意見嗎?查有關的文獻,規格,什麼提出這項問題問題是否配合公司,部,象的工程,批(母體群)題的選取方式適切嗎標達成時間何時性質如何?是否明確一致,價的基準明確可否待利益多少得上司的認可嗎得有關部門的協力嗎得所需要的經費嗎?門涉入之深/廣度過去的數據嗎道數據的履歷嗎()密的調查以往的狀態嗎?統計圖,直方圖,採致詞,性質明確嗎?常能取得數據嗎?定誤差清楚嗎否運用差異分析的結果題問題現況掌握充分否知因子(或要因)果的掌握標達成率它無形效果為何在發防止對策或只是確嗎?策是否具體,愚巧策執行的困難度策案何時詴行果(經詴行)與預測吻合否有關單位進行調整嗎施評價的基準(式實施的時期何時效對策是否納入標準化理點及管理特性明確嗎理特性用管制圖管制嗎?行標準類(作業標準等)有對策 ,察明其原因,嗎?度進行解析對策嗎?省僅止於記錄嗎?否殘留問題點,為何次的主題為何到 1.項(主題的選定)。
精益生产八大步骤:生产效率提升与合理化改善
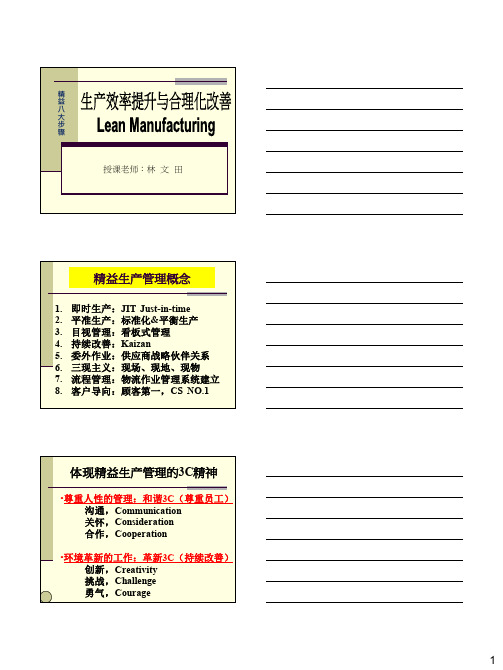
授课老师:林 文 田精益八大步骤1.即时生产:JIT Just-in-time2.平准生产:标准化&平衡生产3.目视管理:看板式管理4.持续改善:Kaizan5.委外作业:供应商战略伙伴关系6.三现主义:现场、现地、现物7.流程管理:物流作业管理系统建立 8.客户导向:顾客第一,CS NO.1精益生产管理概念体现精益生产管理的3C 精神•尊重人性的管理:和谐3C (尊重员工) 沟通,Communication 关怀,Consideration 合作,Cooperation•环境革新的工作:革新3C (持续改善) 创新,Creativity 挑战,Challenge 勇气,CourageWhat is Lean Manufacturing 什么是精益生产制造-五个原则LeanManufacturing精益生产Value 价值站在客户 的立场上Value Stream 价值流 从接单到发货 过程的一切活动Flow 流动象开发的河流 一样通畅流动Demand Pull需求拉动 BTR-按需求生产Perfect 完美没有任何事物 是完美的 不断改进降低成本, 改善质量, 缩短生产周期生产管理的新思维:Lean manufacturing1.精益生产管理的思维:PQCDMS2.精益生产管理的新4Ps3.生产管理工作者的六大职能4.准时化生产方式的思维:ECRSC 杜绝浪费精益生产管理的三大思维 &PQCDMSQ 改善品质D 加速流程P 流程计划M 团队士气S 工作安全TQM 人、机、料、法、测、环、信PI+SQ CD产能士气安全 S C 团队 C.D.IE生计5SMRPCRM 投入产出创造价值依据顾客需求建立价值创新的工作流程程序1. Phiosophy :长期理念:长期效益与价值选择。
2. Process :正确流程:重视流程管理(5M 管理)3. People + Partners :优秀员工+事业伙伴:重视人性、自主化4. Problems :解决问题:没有最好的,只有更好的!实践精益Lean Production 的4Ps实践精LP 的四大原则4Ps第一原则:长期经营的理念以长期为指标,既使牺牲短期利益。
改善八大步骤

4.調查有關的文獻,規格,標準等嗎
1.利用資料證明假設
2.掌握現況並使用不同資料
1.利用所發現的真正原因,使不好之處再度出現,以便改進.
2.消除真正原因,展開實驗試行一段時間.
改善8大驟和統計手法
改善步驟
推行順序
每一順序的重點
統計手法的使用
查核點
統計手法
注意事項
內容
著眼點
Step 5
4.二次對策的效果也要掌握
5.如果毫無效果的話…再從分析開始
柏拉圖
無母數方法
直方圖
管制圖
檢定法(Test)
抽樣檢驗法
反省的要點是實績/計劃(數據,方法)的對比
蜇時處理和永久對策改善的檢討
所選主題是否減少了不適合性
制程能力是否到達1.33以上
對異常值的原因很瞭解了嗎
是否有對異常原因的判明及採取防止再發生的方法
2.活動的實力…全員參與,能力解決,期間
3.不斷的反省…做法的結構
1.將不好的情況具體描述出來
2.把…改成……
3.用補充的課題填補
4.不提出對策性的主題
1.目的明確嗎
(作成具體的
實行計劃嗎)
2.成立協力體制嗎
1.目標達成時間何時
2.特性值如何?是否明確一致?是否與客戶相關?
3.期待利益多少
1.獲得上司的認可嗎
4.用統計圖,直方圖,管制圖,析拉等表示嗎
5.特性值明確嗎
6.日常能取得數據嗎
7.測定誤差清楚嗎
8.是否運用差異分析的結果
9.主要問題現況掌握充分否
10已知因子(或要因)現況掌握是否充分
11已知因子異常處理標準化程度
1.使改善的特性或代用特性明確化
DF1-11 专项改善八步骤法
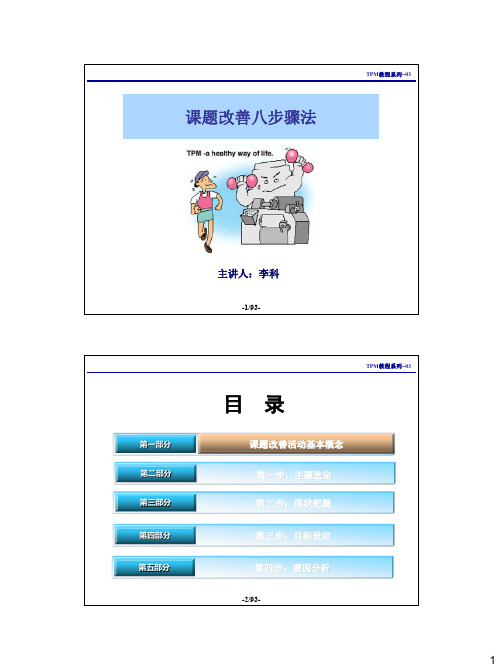
Act
-4/93-
2
TPM教程系列--03
课题改善小组的组建
1、自下而上的组建程序 此情况适用于由同一班组内的几个人自主组成的小组, 多数是先有课题后组建小组,在企业推行课题改善初期, 可能有先组建小组后选择课题的情况。
小组成立 小组起名 组长选举 申请注册
主管部门 审核
活动开始
注册登记
小组成立后发生人员变动时也应到主管部门登记备案。如:小组选定课题 后根据课题需要,邀请 相关部门人员参加而发生的人员变动。
-9/93-
TPM教程系列--03
三部课题
例1
正极涂敷量改善
制作: 韦华林 07-07-02
-10/93-
5
TPM教程系列--03
小组概况
课题名称 改善正极涂敷量 小组名 超差不良 啄木鸟
2007年04月
课题登记时 间 2007年04月 课题活动时 至2007年07 间 月
活动口号
无坚不摧、勇往直前!
目的性
八大特点
激励性
民主性 经济性
灵活性
-3/93-
TPM教程系列--03
课题改善活动开展的八步法
组 建 团 队
1 主 题 选 定
2 现 状 把 握
3 目 标 设 定
4 要 因 分 析
5 制 订 对 策
6 实 施 对 策
7 效 果 确 认
8 标 准 化 及 向 后 计 划
成 果 发 表
Plan
Do
Check
2.推算各步骤所需时间 (1)数据收集所需时间。 (2)对问题的现象、原因的了解程度。 (3)预期对策可能牵涉到的其他单位及其可能的配合度。
(4)在活动期间正常业务的变化。
精益课题改善八大步骤

精益课题改善八大步骤精益课题改善可不是一件能随便糊弄的事儿呀!这八大步骤,那可是相当重要呢!第一步,发现问题。
这就好像在茫茫人海中找到那个特别的人一样,得有双敏锐的眼睛。
生活中、工作里,到处都可能藏着问题,就看你能不能发现啦。
比如机器总是出故障,流程总是不顺畅,这些不就是等待我们去挖掘的宝藏问题嘛!第二步,分析问题。
哎呀呀,找到了问题可不能急着下手,得像侦探一样好好分析分析。
到底是什么原因导致的呀?是人的因素?还是设备的原因?或者是流程设计不合理?把这些都搞清楚,才能对症下药呀!第三步,设定目标。
咱不能漫无目的地干呀,得有个明确的方向。
就像跑步比赛,总得知道终点在哪儿吧。
把目标定好了,大家就有了努力的动力,朝着那个方向使劲儿。
第四步,制定方案。
这就好比做菜,有了食材还得有菜谱呀。
根据分析的结果,想出各种办法来解决问题,哪种方法最可行,就选哪种。
可别小瞧了这一步,这可是关键呢!第五步,实施计划。
光说不练假把式,计划制定好了就得行动起来。
大家齐心协力,按照方案一步一步来,遇到困难也别退缩,办法总比困难多嘛!第六步,检查效果。
看看我们的努力有没有成效呀,问题是不是得到了解决呀。
就像考试后看成绩一样,心里总是有点小期待呢。
第七步,标准化。
如果效果好,那可不能让这成果就这么溜走呀,得把好的方法固定下来,变成标准流程。
这样以后就照着做,免得又回到老样子。
第八步,持续改进。
世界在变,问题也在变呀,可不能躺在功劳簿上睡大觉。
要不断地寻找新的问题,不断地改进,这样才能一直进步呀!你想想,如果每个步骤都能认真做好,那会带来多大的变化呀!就像给机器加了润滑油,让一切都变得顺畅起来。
所以呀,可别小看了这八大步骤,它们可是能让我们的工作、生活变得更美好的法宝呢!大家都行动起来吧,让我们一起把问题都解决掉,让一切都变得越来越好!难道不是吗?。
专案改善八大步骤
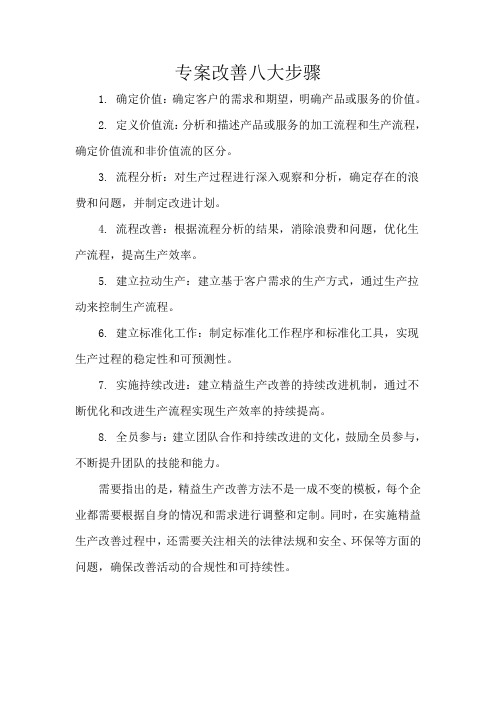
专案改善八大步骤
1. 确定价值:确定客户的需求和期望,明确产品或服务的价值。
2. 定义价值流:分析和描述产品或服务的加工流程和生产流程,确定价值流和非价值流的区分。
3. 流程分析:对生产过程进行深入观察和分析,确定存在的浪费和问题,并制定改进计划。
4. 流程改善:根据流程分析的结果,消除浪费和问题,优化生产流程,提高生产效率。
5. 建立拉动生产:建立基于客户需求的生产方式,通过生产拉动来控制生产流程。
6. 建立标准化工作:制定标准化工作程序和标准化工具,实现生产过程的稳定性和可预测性。
7. 实施持续改进:建立精益生产改善的持续改进机制,通过不断优化和改进生产流程实现生产效率的持续提高。
8. 全员参与:建立团队合作和持续改进的文化,鼓励全员参与,不断提升团队的技能和能力。
需要指出的是,精益生产改善方法不是一成不变的模板,每个企业都需要根据自身的情况和需求进行调整和定制。
同时,在实施精益生产改善过程中,还需要关注相关的法律法规和安全、环保等方面的问题,确保改善活动的合规性和可持续性。
改善八大步骤.
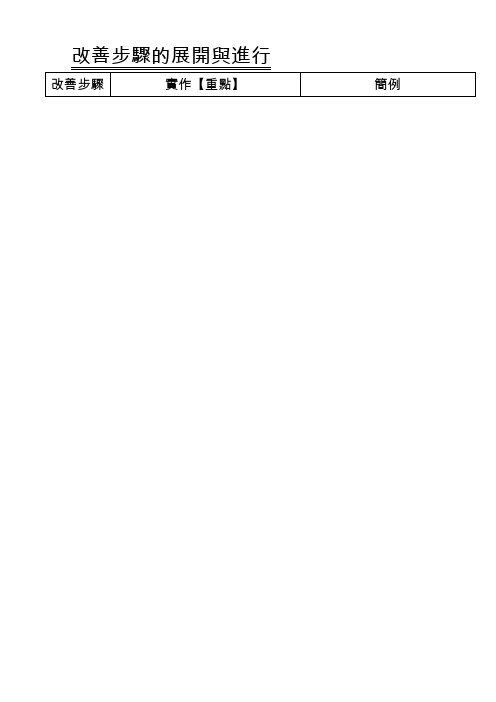
2.2 改善型: 提 企業水準 升 創新型問題突破 目標 Target 水 差距→攻擊點 準 2.3 創新型: 現有水準
3.改善型問題評價 D 型:現況真因及對策均明 A 型:現況真因明對策缺 X 型:現況真因仍不明 4.確定欲改善之問題 ※方針、參與、能力、顧客喜悅 5.將問題轉成改善題目 (動詞+受詞+評價特性) 3.1:活動主題篩選表 :主題篩選流程(範例) 5.1 縮短折條站接班時間
<3> 要因推移圖 3.2 總效果推移圖(範例)
4.1:標準化建議書(如附件) 4.標準化步驟: 4.1 有效對策之標準化程序及要 件。 4.2 更新標準作業書及相關圖面 4.3 相關文件之文號,及現場作業 執行記錄。 4.2:S.O.P 修訂之範例(如附件) 4.3:人員訓練
改善步驟的展開與進行
改善步驟的展開與進行
五 、 對 策 立 案 與 執 行
2.對策評核: 2.1 每一真因項目之多個可行方 案,評估優缺點擇出較佳方 案。 1.對策立案: 1.1 選定真因,初擬消除該真因的 方法並觀察結果。 1.2 依真因證實所得之初擬對策之 方法,逐一提出具體可行之作 法。 1.3 配合之相關措施與資源。
3.對策執行: 3.1 計劃 3.2 實施(有數據佐證)
改善步驟的展開與進行
六 、 效 果 確 認 與 標 準 化
3.對策之效果確認方法。 3.1:對 策 效果確認方法 層別推移圖 檢定法 <2>△ △ △ △ △ <4>※※※※※ 2.分段實施之對策,數據統計分析 2.對策逐一效果確認(與對策之 及證實。 PDCA 相結合) 1.對策執行之數據收集 ※期間 ※查檢表 1.對 策:<1>#### 實施者:許文林 確認者:王立人
減少錯誤的方向 ※對策型原因分析
《改善八大步骤》课件

THANKS
感谢观看
《改善八大步骤》ppt课件
目录
• 引言 • 明确问题 • 设定目标 • 制定对策 • 实施对策 • 检查效果 • 标准化 • 总结和未来计划
01
引言
改善的定义
01
改善是指通过不断优化和改进生 产、管理、服务等方面的工作, 提高工作效率、降低成本、提升 品质的过程。
02
改善是一种持续不断的过程,需 要不断发现和解决问题,不断寻 求改进和创新。
定期对员工进行考核,确保他们能够 按照新标准进行操作,并及时纠正不 规范的行为。
通过实践操作、模拟演练等方式,让 员工熟悉并掌握新标准操作流程。
08
总结和未来计划
对改善过程进行总结和反思
总结
回顾整个改善过程,包括改善的 背景、目标、实施步骤和效果, 分析其中的成功和不足之处。
反思
深入思考改善过程中的经验和教 训,找出可以改进的地方,为今 后的改善活动提供借鉴。
对未来计划进行规划和展望
规划
根据总结和反思的结果,制定未来改善的计划和目标,明确 具体的实施步骤和方法。
展望
对未来的改善趋势和方向进行预测,为企业的持续改进提供 战略指导。
确定下一步的改善重点和目标
重点
根据总结和反思的结果,确定下一步 改善的重点领域和关键问题,集中资 源和力量进行解决。
目标
设定具体的、可衡量的改善目标,明 确实现目标的时间节点和责任人,确 保改善活动的有效推进。
02
检查改善措施是否具有长期可持续性,是否能够在未来继续产
生良好的效果。
衡量改善的经济效益
03
评估改善措施对企业的经济效益的影响,包括成本降低、生产
效率提高等方面。
课题改善八大步骤

课题改善八大步骤
课题改善的八大步骤如下:
1. 确定改善主题:明确改善的目标和主题,可以从工作场所的问题、上司的方针、工程和相关部门的需求以及过去活动的经验中寻找。
2. 现状分析:收集与主题相关的数据和信息,进行现状分析,了解问题的真因,并明确改善的期望和目的。
3. 确定改善方案:基于现状分析,制定改善方案,包括改善动因、期望和目的。
4. 实施改善:根据改善方案,进行具体的实施工作,包括人员、记录、判读、方法等细节的安排。
5. 数据分析:对实施改善后的数据进行收集、整理和统计分析,了解改善的效果和重點。
6. 差异分析:通过对比改善前后的数据,进行差异分析,明确改善的效果和影响。
7. 要因分析和真因验证:采用适当的方法,如鱼骨图分析、系统图分析等,进行要因分析和真因验证,找出问题的根源和根本原因。
8. 成果比较和交流:将改善成果与改善前的状态进行比较,进行成果评价和交流,分享经验和教训,促进持续改进和提高。
以上是课题改善的八大步骤,每一步都有其特定的目标和要求,需要认真执行,以确保改善的有效性和持续性。
1。
改善八大步骤28页PPT

1、不要轻言放弃,否则对不起自己。
2、要冒一次险!整个生命就是一场冒险。走得最远的人,常是愿意 去做,并愿意去冒险的人。“稳妥”之船,从未能从岸边走远。-戴尔.卡耐基。
3、人生就像一杯没有加糖的咖啡,喝起来是苦涩的,回味起来却有 久久不会退去的余香。
4、守业的最好办法就是不断的发展。
5、当爱不能完美,我宁愿选择无悔,不管来生多么美丽,我不愿失 去今生对你的记忆,我不求天长地久的美景,我只要生生世世的轮 回里有你。
谢谢
11、越是没有本领的就越加自命不凡。——邓拓 12、越是无能的人,越喜欢挑剔别人的错儿。——爱尔兰 13、知人者智,自知者明。胜人者有力,自胜者强。——老子 14、意志坚强的人能把世界放在手中像泥块一样任意揉捏。——歌德 15、最具挑战性的挑战莫过于提升自我。——迈克尔·F·斯特利
- 1、下载文档前请自行甄别文档内容的完整性,平台不提供额外的编辑、内容补充、找答案等附加服务。
- 2、"仅部分预览"的文档,不可在线预览部分如存在完整性等问题,可反馈申请退款(可完整预览的文档不适用该条件!)。
- 3、如文档侵犯您的权益,请联系客服反馈,我们会尽快为您处理(人工客服工作时间:9:00-18:30)。
6.
7.
8.
未來計劃 Future Plan
自主研 Jishuken NPS 台新企管
改 善 基 本 技 巧
Kaizen Basic Rules . 掌握 NPS 新生產技術三原則 Follow 3 Articles of NPS (1) 一個流程 One Piece Fiow (2) 依據產距時間生產 Work To TT (3) 後拉式生產 Pull production . 三無思想 3-Mu Philosophy (1) 無馱Muda (2) 無理 Muri (3) 無穩 Mura . 改善動作之步驟 Steps of Kaizen (1) 要決定 TT Determine TT (2) 先做作業合理化,消除無馱 Rationalize opration to eliminate Muda (3) 將每一作業員的工作時間安排等於 TT,消除無理 Assign wworks of TT to each operator to eliminate Muri (4) 建立穩定的作業環境,消除無穩 Stablize operation to eliminate Mura
自主研 Jishuken NPS 台新企管 步驟 Step 名 稱 Dbscription
改 善 八 大 步 驟 Kaizen 8 Steps
參 考 文 件 /要 點 . Reference / * key Points
1.
主題選定 . NPS自主研究會登記表 Theme Selected . NPS Kaizen Registration Sheet
自主研 Jishuken NPS 台新企管
縮 短 交 期 技 巧 Shorten Throughput Time Rules
(1) 基本要領:實施一個流流線生產方式 Basic Rule : To implement One-Piece-Flow Line. (2) 實施平準化生產,減少換模批量,縮短換模時間 Introduce Leveling production,reduce changeover batch size and reduce changeover time. (3) 消除離島作業,朝同步化生產努力 Eliminate isolated work station,try to synchronize production. (4) 設定“最大-最小”在制量管理系統,剔除多餘在製品 Set the “Max-Min” WIP Control System,to eliminate extra WIP. (5) 建立“順序號碼”達成“先進先出” Design “ Sequence Code ” to control “ First In First O備或連續式設備 Prefer to using samll.continue machine i.s.o. big machine. (7) 掌握“品質三不原則”,提升良品率 Keep production line in the way of “ Fresh ”,“ Fast ”, and “ United ” to increase yield. (8) 改善瓶頸工程,提升全線生產速度 Kaizen bottleneck process to increase line output speed. (9) 嘗詴一個流生產,縮短加工時間 Try to introduce one-piece-flow,to reduce Process Time. (10) 實施全員生產保全,設備保有預防保養時間 Implement TPM,to let M / C have time to be preventive maintenance.
自主研 Jishuken NPS 台新企管
減 少 不 良 技 巧 Defect Reduction Rules
(1) 掌握“五現主義” Follow 5-Gen Principles 1. 走入“現場” Go to Gemba ( Shopfloor ) 2. 觀察“現物” OBSERVE Gembutsu ( Objects ) 3. 了解“現實” Realize Genjitsu ( Facts ) 4. 立即“現作” Immediate gentsuku ( Actions ) 5. 成果“現查” Results Gensa ( Confirmation ) (2) 運用“要因分析七手法” Make use of “ cause Analysis 7 tools ” 1. 做出柏拉圖,先從佔70% ~ 80% A類不良項目下手改善 Analyze by Pareto Chart,Start with A Category ( 70% ~ 80% of Defects ) to do Kaizen. 2. 掌握行成不良之因果關係圖 ( 魚骨圖 ),考慮 5 MIE ( 人員、機器、物料、方法、量測及環境 ) 之原因 Work out the cause-effect (Fishbone)diagram. Consider the factors of Man,Machine,Materials,Method, Measurement and Environment. 3. 運用五五法要問五次為什麼,找出不良之真因(確實造成不良之特定要因) Ask why five times 5WIH to find out root cause of defection. 4. 運用比較法,比較最好與最差之狀況,協助找出真因 Compare the best with the worst to find out root cause. 5. 運用放大法,放大不良品來觀察 Enlarge the defect to observe the fact. 6. 不良品解剖法,了解不良品之內涵 Dissect the defect,to realize the defective factors. 7. 利用潛水法,直到找到問題真因為止 Dive until find out the root cause. (3) 遵照十二字真言:“保持新鮮、迅速確實、三國統一” Keep production operation in the way of :“Fresh,Fast and United”. (4) 徹底以“防錯”技巧,根絕不良之來源 Use foolproof method to eliminate defects. (5) 重要觀念:自主全數檢查,自己做的產品自己檢查、自己修理。要做情報檢查,不要做判別檢查 Implement Self-100% inspection. Operator is in charge of production,inspection and rework the product. Do information inspection i.s.o. screen inspection. (6) 要做出不增加工時的自主全數檢查之技巧。例如自動檢查、塊規(Gauge)檢查、可/不可(Go/No Go)檢查等 Develop no man-hours added Self-100% inspection system by such as : Automatic inspection,gauge inspection,Go / No Go inspection etc...
目標設定 Target Setting . NPS自主研究會登記表 . NPS Kaizen Registration Sheet
* 產距時間 * Take Time
* 數量化 * Quantify
2.
3.
現況調查 . 流程圖 Process Flow Chart . 作業配分表 Process Time Chart Current Situation . 標準作業票 Standard Work Sheet . 標準作業組合票 Standard Work Combination Sheet . 製程別加工能力表 Process Capability sheet . 時間觀測表 Time Measurement Sheet . 改善成果表 kaizen Result Record * 五現主義“ 5 gen Principles ” : 現場 Gemba , 現物 Genbutsu , 現實 Genjitsu , 現作 Gentsuku , 現查 Gensa 要因分析 Cause Analysis . 改善快報 Kaizen News * 三無思想 “ 3-Mu phiosophy ” : 無馱Muda , 無理 Muns , 無穩 Mura * 五現主義 5 Gen Principles * 要因分析七手法 Cause Analysis 7tools : - 柏拉圖 Pareto Chart - 五五法 5x5WIH - 魚骨圖 Fishbone Chart - 比較法 Comparison - 放大法 Enlargement - 解剖法 Dissection - 潛水法 Dive
自主研 Jishuken NPS 台新企管
作 業 合 理 化 原 則 Principles of Operation Rationalization
(1) 作業員在同一邊工作,逆時針順序排列,盡量靠攏,一般為80公分 Operators work at the same side by counterclockwise process sequence,and work as closer as possible. Normal station pitch is 80 cm. (2) 不要搖頭,不要彎腰 No turn head,No bend body (A) 物料、工具要放在作業者正前方,且在正常工作範圍 Tool and parts should be located in front of operator and in the normal working area. * 料盒要設計成 Part container should be : 1 正面窄、縱深長 Narrow front side and longer length. 2 雙盒式置料 One part with twin containers 3 少量多回供應 Supply parts by less quantity but more frequent. (B) 物料、工具要定位且預放。工具要能懸掛起來 Tools and parts should be pre-positioned in a definite location,and hang up the tools. (3) 不要插秧,利用夾具使雙手能同時對稱反向動作 Utilize fixtures to let two hands no idle or hold time (4) 利用重力滑道及道具 Utilizze gravity chute and special designed tools (5) 作業區域保持乾淨,在製品不要堆積,保持一個流 Keep good housekeeping in work statio,follow one piece flow and no stack wip. (6) 水蜘蛛要能從另一側定時定量供料給作業員 Water spider should periodically provide fixed quantity of parts to operator from the opposite side of opposite. (7) 盡可能將前後工程連線起來 Connect processes as more as possible to flow line. 考詳細資料:工作改善(IE)七大手法:許文治著 Detailed reference:IE 7 Tools (Chinese version),by Arthur Hsu.