实木家具制作工艺流程修订版
实木家具的工艺流程

实木家具的工艺流程实木家具是指家具的主要结构材料为实木的家具。
实木家具因其天然、环保、耐用等特点,受到越来越多消费者的青睐。
而实木家具的制作工艺也是非常复杂的,需要经过多道工序才能完成一件精美的实木家具。
下面将介绍实木家具的工艺流程。
一、原材料采购。
实木家具的制作首先需要准备好原材料,主要是各种不同种类的实木。
在原材料采购阶段,需要选择优质的实木材料,包括橡木、榉木、榆木、柚木等,这些木材都具有不同的特点和用途。
在采购原材料时,需要考虑木材的干燥度、密度、纹理等因素,以确保制作出的家具具有良好的质量和外观。
二、木材处理。
在原材料采购完成后,需要对木材进行处理。
首先是木材的干燥处理,以去除木材中的水分,防止家具在制作过程中出现变形、开裂等问题。
干燥处理一般分为空气干燥和窑炉干燥两种方式,需要根据不同的木材种类和厚度来选择合适的干燥方式。
然后是对木材进行切割、刨光等加工,将木材加工成各种需要的形状和尺寸。
三、家具设计。
在木材处理完成后,需要进行家具的设计。
家具设计需要考虑到家具的功能、结构、外观等方面,以确保设计出的家具符合人体工程学,同时具有美观的外观。
在设计过程中,需要使用CAD等设计软件进行绘制,并根据实际需要进行不断的修改和完善,直到满足要求为止。
四、家具制作。
家具制作是实木家具制作的关键环节。
制作过程中需要进行木工加工、拼接、打磨、上色等多道工序。
首先是木工加工,根据设计图纸将木材进行切割、雕刻等加工,制作出家具的各个部件。
然后是家具的拼接,将加工好的木材部件进行组装,使用胶水、螺丝等固定材料将各部件连接在一起。
接着是家具的打磨,对家具表面进行打磨处理,使家具表面光滑平整。
最后是上色,根据设计要求对家具进行上色处理,使其具有良好的外观效果。
五、家具装配。
家具制作完成后,需要进行家具的装配。
家具装配是将制作好的各个部件进行组装,使其成为一件完整的家具。
在装配过程中需要注意各部件的连接方式、角度、位置等,确保家具的结构牢固稳定。
实木家具生产工艺流程

实木家具生产工艺流程一:备料1.板材干燥,将木材的含水率控制在8%~10%,没有干燥过的木材一般含水率在50%以上,干燥过后的木材不容易出现爆裂变形等现象。
2.平衡,把干燥过的木头自然放置几天,让木材恢复平衡。
3.选料配料,木制品按其部位可分为外表用料、内部用料以及暗用料三种。
外表用料露在外面,如写字台的面、橱柜的可视部分等;内部用料指用在制品内部,如内档、底版等;暗用料指在正常使用情况下看不到的零部件,如抽屉导轨、包镶板、内衬条等.选材时注意节疤、内裂、蓝变、朽木、端裂.4.粗刨,给毛料板材定厚.5.风剪,毛料板材修整长度。
下料按所需长度加长20mm。
6.修边,截去毛料板材上不能用的毛边。
7.配板,木料配板选材分直纹、山纹,颜色搭配一致,配板宽度按所需宽度合理放余量。
选料时要把内裂、端裂、节疤、蓝变、朽木部分取下。
8.布胶,在木材之间均匀布胶,胶的配比:固化剂(10—15克)、拼板胶(100克)的比,每次调胶500克左右。
9.拼板,使用拼板机将木材进行拼装,拼板注意高低差、长短差、色差、节疤。
10.陈化,布胶完成的木材放置2小时左右,让胶水凝固。
11.砂刨,刨去木材之间多余的胶水,使木材板面无多余胶水。
12.锯切定宽,用单片锯给木材定宽.13.四面刨成型,根据需要的形状刨出木材。
14.养生,将木材自然放置24小时左右。
二:木工1.宽砂定厚,按要求砂止符合加工要求的尺寸,机加完成后进行抛光砂,,粗砂一次砂0。
2mm,抛光砂一次砂0.1mm.2.精切,给毛料定长,加工过程中做到无崩茬、发黑,长与宽加工误差不超过0。
2mm,1米以下对角线≤0。
5mm,1米以上板片对角线应≤1mm.3.成型,根据图纸将木材加工成型。
加工时不允许有崩茬、毛刺、跳刀和发黑现象,加工的部件表面应光滑、平整、线型流畅一致,加工前检查设备部件螺丝有无松动,模板是否安装规范,刀具是否装紧,加工过程中禁止顺刀进料,部件尺寸误差不超过0。
实木家具制作详细工艺流程完整版
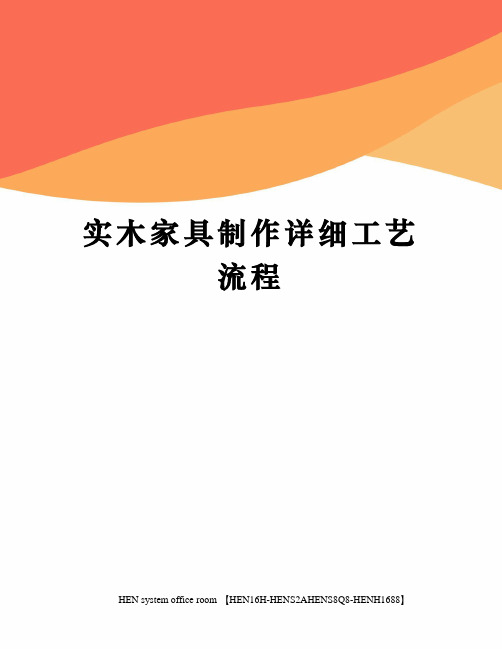
实木家具制作详细工艺流程HEN system office room 【HEN16H-HENS2AHENS8Q8-HENH1688】WORD文档,可下载修改?是指由天然木材制成的家具,家具表面一般都能看到木材真实的纹理它不仅仅包括人们印象家具的所有用材都是实木,包括桌面、柜子的门板、侧板等均用纯实木制成,不使用其他任何形式的人造实木家具工艺流程介绍?1、产品生产总步骤;备料生加工成型油漆总装备料:从原木变成板材等。
包括对木材的蒸煮杀菌等定型处理,再干燥到8%~12%左右的含水量水率后出炉即可使用。
生加工:形成产品木胚工件;包括:断料、开料、平刨、压刨等加工工序。
成型:加工制造成符合各种设计形状的部件。
2、实木家具生产流程:断料开料(直料、弯料)平刨压刨出齿、接齿机械加工安装二次烘干油漆包装入库机械加工:包含了锣机、出榫、打孔、机磨等加工工序。
3、板式家具生产流程介绍:开料冷压精锯封边排孔钉装试装油漆包装入库4、实木家具油漆工艺流程:A、田园雅筑(19系列)油漆工艺:白坯含平台喷第一次底油(待干2小时)打第一次油磨手工擦色(三次)喷第二次底油(待干3小时)打色油磨面油(待干小时)包装B、雅茗(16系列)油漆工艺:白坯含平台喷第一次底油(待干3小时)手工擦色打底色磨含平台喷第二次底油(待干3小时)打油磨修色(待干3小时)色油磨面油(待干小时)包装5、油漆涂饰:目前在家具上使用的油漆分为五大类:水溶性油漆、硝基漆(NC)、光敏油漆(UV)不饱和聚脂漆(PU)、饱和聚脂漆(PE)。
1、水溶性油漆:目前公认最环保的涂料,因为它使用“水”作为稀释剂,挥发物无毒无味,在欧洲广泛使用,但国内暂时得不到有效推广——价格过于昂贵(目前国内价格为150~180元/公斤)。
但这是家具界的发展方向。
加工方式可用喷涂或刷涂。
2、硝基漆(NC):是一种由天然原材料(生漆)加工制成,稀释剂是松节水。
中国人很早的时候已经开始使用这种涂料。
实木家具生产工艺流程
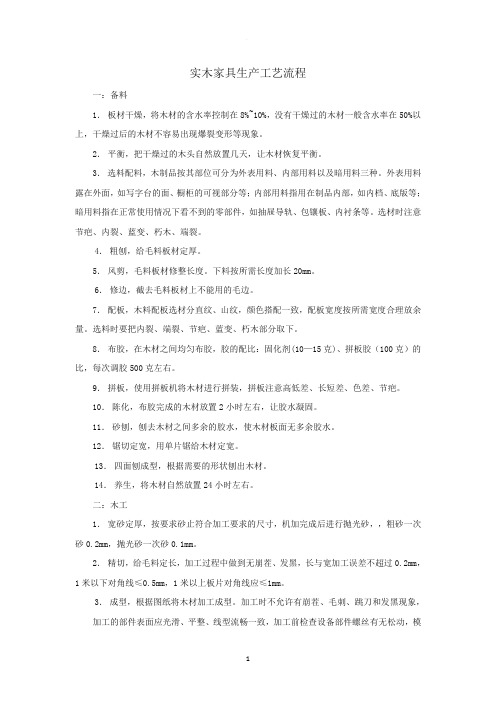
实木家具生产工艺流程一:备料1.板材干燥,将木材的含水率控制在8%~10%,没有干燥过的木材一般含水率在50%以上,干燥过后的木材不容易出现爆裂变形等现象。
2.平衡,把干燥过的木头自然放置几天,让木材恢复平衡。
3.选料配料,木制品按其部位可分为外表用料、内部用料以及暗用料三种。
外表用料露在外面,如写字台的面、橱柜的可视部分等;内部用料指用在制品内部,如内档、底版等;暗用料指在正常使用情况下看不到的零部件,如抽屉导轨、包镶板、内衬条等。
选材时注意节疤、内裂、蓝变、朽木、端裂。
4.粗刨,给毛料板材定厚。
5.风剪,毛料板材修整长度。
下料按所需长度加长20mm。
6.修边,截去毛料板材上不能用的毛边。
7.配板,木料配板选材分直纹、山纹,颜色搭配一致,配板宽度按所需宽度合理放余量。
选料时要把内裂、端裂、节疤、蓝变、朽木部分取下。
8.布胶,在木材之间均匀布胶,胶的配比:固化剂(10—15克)、拼板胶(100克)的比,每次调胶500克左右。
9.拼板,使用拼板机将木材进行拼装,拼板注意高低差、长短差、色差、节疤。
10.陈化,布胶完成的木材放置2小时左右,让胶水凝固。
11.砂刨,刨去木材之间多余的胶水,使木材板面无多余胶水。
12.锯切定宽,用单片锯给木材定宽。
13.四面刨成型,根据需要的形状刨出木材。
14.养生,将木材自然放置24小时左右。
二:木工1.宽砂定厚,按要求砂止符合加工要求的尺寸,机加完成后进行抛光砂,,粗砂一次砂0.2mm,抛光砂一次砂0.1mm。
2.精切,给毛料定长,加工过程中做到无崩茬、发黑,长与宽加工误差不超过0.2mm,1米以下对角线≤0.5mm,1米以上板片对角线应≤1mm。
3.成型,根据图纸将木材加工成型。
加工时不允许有崩茬、毛刺、跳刀和发黑现象,加工的部件表面应光滑、平整、线型流畅一致,加工前检查设备部件螺丝有无松动,模板是否安装规范,刀具是否装紧,加工过程中禁止顺刀进料,部件尺寸误差不超过0.2mm。
实木家具加工流程

实木家具加工工艺主要内容为实木零件的加工工艺。
实木零件的工艺过程是指通过各种加工设备改变原材料的形状、尺寸或物理性质,将原材料加工成符合技术要求的产品时,所进行的一系列工作的总和称为工艺过程。
它是由若干个工序组成的。
干燥-配料-毛料加工-胶合加工-弯曲加工-净料加工—部件装配-部件加工-总装配、涂饰(1)干燥:湿的板材、方材通过干燥窑干燥或自然干燥等方式,将材料的含水率控制在一定的范围内,即与使用该家具地区的木材年平衡含水率相适应。
用于家具制造的其他材料如集成材、层积材及各种人造板的含水率也要加以控制。
(2)配料:①合理选料:根据产品质量要求和特点来选择树种、纹理、颜色等。
高档家具所有零件都尽可能选用同一种树种来配料,如所选用树种为珍贵树种则家具的成本就会很高。
起支撑作用的家具零件要考虑其强度,普通家具也是如此。
②合理确定加工余量和含水率:含水率应内外均匀一致,无内应力,防止在加工和使用过程中产生翘曲、开裂等现象;根据设备情况及加工工序的多少合理地留出加工余量。
③合理选择配料方式:一般应该遵循倍数毛料原则,即毛料与净料的长度、宽度、厚度都可以是倍数关系。
最佳方案是毛料和净料的断面尺寸相当(应有一定的加工余量),长度则是被加工零件的倍数。
其目的是减少浪费和提高生产效率。
(3)毛料加工:将锯材加工成外形尺寸准确的零件,为净料加工提供准确的定位基准。
(4)胶合加工:主要指板方材胶合、空心板的制造、贴面等。
(5)弯曲加工:主要指实木弯曲、单板胶合弯曲、锯口弯曲等。
(6)净料加工:主要指开榫、钻孔、开槽、车形、仿形、镂铣、打榫眼、磨光等。
(7)部件装配:就是把零件通过榫卯结构、圆榫连接、胶粘剂、钉子、木螺丝钉及五金联接件组装起来成为部件。
(8)部件加工:主要是指装配好的部件的加工,如门的再修正、砂光。
(9)总装配和涂饰:将部件、零件通过一定方式连接起来,再油漆。
如:学生课画桌生产工艺包括以下个过程1、配料:配料一般需用到下列机器:切床、压刨、开料锯、平刨、铣床、拼板机、带锯、四面刨等。
实木家具制作详细工艺流程
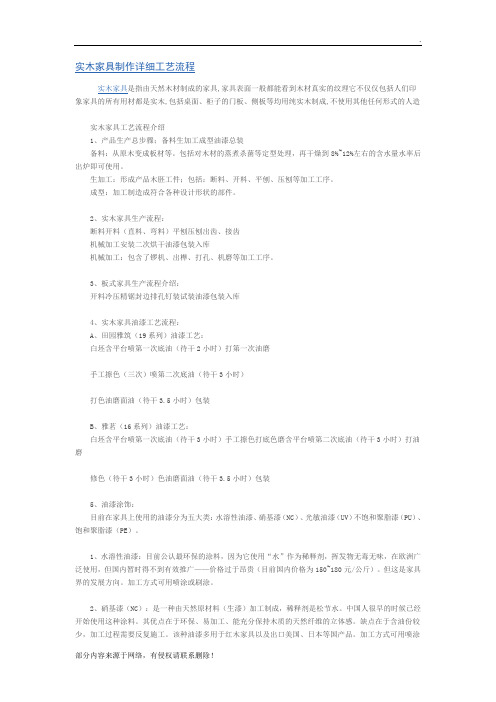
实木家具制作详细工艺流程实木家具是指由天然木材制成的家具,家具表面一般都能看到木材真实的纹理它不仅仅包括人们印象家具的所有用材都是实木,包括桌面、柜子的门板、侧板等均用纯实木制成,不使用其他任何形式的人造实木家具工艺流程介绍1、产品生产总步骤;备料生加工成型油漆总装备料:从原木变成板材等。
包括对木材的蒸煮杀菌等定型处理,再干燥到8%~12%左右的含水量水率后出炉即可使用。
生加工:形成产品木胚工件;包括:断料、开料、平刨、压刨等加工工序。
成型:加工制造成符合各种设计形状的部件。
2、实木家具生产流程:断料开料(直料、弯料)平刨压刨出齿、接齿机械加工安装二次烘干油漆包装入库机械加工:包含了锣机、出榫、打孔、机磨等加工工序。
3、板式家具生产流程介绍:开料冷压精锯封边排孔钉装试装油漆包装入库4、实木家具油漆工艺流程:A、田园雅筑(19系列)油漆工艺:白坯含平台喷第一次底油(待干2小时)打第一次油磨手工擦色(三次)喷第二次底油(待干3小时)打色油磨面油(待干3.5小时)包装B、雅茗(16系列)油漆工艺:白坯含平台喷第一次底油(待干3小时)手工擦色打底色磨含平台喷第二次底油(待干3小时)打油磨修色(待干3小时)色油磨面油(待干3.5小时)包装5、油漆涂饰:目前在家具上使用的油漆分为五大类:水溶性油漆、硝基漆(NC)、光敏油漆(UV)不饱和聚脂漆(PU)、饱和聚脂漆(PE)。
1、水溶性油漆:目前公认最环保的涂料,因为它使用“水”作为稀释剂,挥发物无毒无味,在欧洲广泛使用,但国内暂时得不到有效推广——价格过于昂贵(目前国内价格为150~180元/公斤)。
但这是家具界的发展方向。
加工方式可用喷涂或刷涂。
2、硝基漆(NC):是一种由天然原材料(生漆)加工制成,稀释剂是松节水。
中国人很早的时候已经开始使用这种涂料。
其优点在于环保、易加工、能充分保持木质的天然纤维的立体感。
缺点在于含油份较少,加工过程需要反复施工。
该种油漆多用于红木家具以及出口美国、日本等国产品。
实木家具生产工艺流程

一、实木生产工艺流程图(1)
实木烘干实木余料带断锯拼板纵平压刨定定定返锣雕刻铣
实木余料
指
拼板接烘
料
锯
长
宽
厚
机
钻裁线出榫开补一度一度手机砂上胶、装木榫上夹具、整装、清补、手清砂白坯成品检验、
形
孔
准
锯
槽
烂80120180240
、二度
、二度
补子
°
腻
=360
清
组装、
角磨清胶、
入
装
实木家具生产工艺流程(2)
木皮余料实木烘干压板拼板备料板式封木皮边机加工砂光组装涂装
板材开料
断贴木皮料裁纵平压刨实木封边定定装
拼
锯
准
花
锣
长宽
边排精Βιβλιοθήκη 钻开纵出铣钻裁槽锯孔榫准行
砂
砂
组
光
整装
磨打
油漆
包装
压备料拼花热压机加工砂光组装装涂
开料
定厚
砂光
板
冷压
裁
准
封实木边
拼
花
热
压
裁锣排
钻
准
边
封实木边
精
妙
组
合
整
装
油
漆
包.
装
实木家具的生产工艺流程
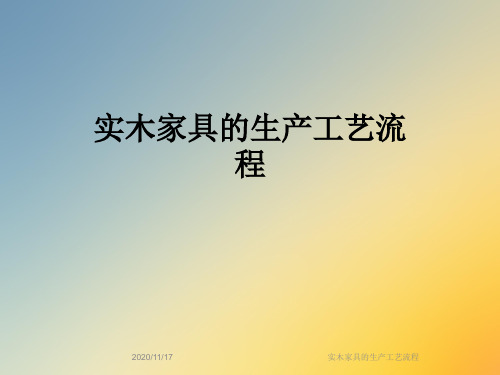
片无裂纹,锯齿有无松动与脱落,如有应更换锯片。锯切 中,如锯片变钝也应更换;批量加工前应先试车,检查子口 规格是否符合图纸要求。 2. 使用材料:不同规格尺寸的净 料。 3. 质量要求:
实木家具的生产工艺流程
子口要求符合图纸要求,误差范围+1MM,对于有选材标 准中允许小缺陷的工件。进锯时应尽量将小缺陷在开子口 时切除或将允许的缺陷留在背面。 实木门生产流程四、调 胶 1.基本工艺及操作要求
实木家具的生产工艺流程
程十四、开玻璃池 1.基本工艺和操作要求:开机前先检查 刀具是否夹紧,根据图纸确认玻璃位置,正反两面均用铁 锤击穿表板,便开螺机头刀。螺玻璃池内边时,螺机刀头 要垂直,端部导向滚要紧靠内
实木家具的生产工艺流程
框木方,待基本形状加工好后,玻璃池四角要用木斧修整 成直角。 2.质量要求:玻璃池周边木材应该无腐朽和凹凸 不平的缺陷,其四周要平直、光滑、上下一致。且四个角 均为90°。 实木门生产流
实木家具的生产工艺流 程
2020/11/17
实木家具的生产工艺流程
作要求:开机前,须将刀头按图纸调整到加工规定的位置。 然后先试车,试出的榫头尺寸符合要求后才批量生产。加 工时的进料速度V进均匀适当,不可猛拉硬撞,以免损坏 刀具,影响精度。 使用材料:
实木家具的生产工艺流程
具有准确规格尺寸的净材。 质量要求:榫肩要与工件长度 方向呈45°或90°角,或符合装配要求,榫头尺寸要符合 图纸规定或装配要求。 实木门生产流程一、钻榫眼 1.其本 工艺和操作要求:开
实木家具的生产工艺流程
时要均速进料,不可猛撞据片,半成品加工应轻放,以免 损坏产品。 2.使用材料 3.质量要求:门的长、宽尺寸要符 合图纸要求,公差范围+1MM,门的两相邻边成90°角, 锯边要光滑,不允许
制作实木家具工艺流程

制作实木家具工艺流程实木家具是指家具主要由天然实木材料制成的家具,因其具有天然、环保、耐用等特点,受到越来越多消费者的青睐。
制作实木家具需要经过多道工艺流程,下面就为大家介绍一下制作实木家具的工艺流程。
第一步:原木采购制作实木家具的第一步是原木采购。
选择高质量的原木是制作高品质实木家具的基础。
在采购原木时,需要注意木材的种类、水分含量、树龄等因素,以确保原木的质量符合制作家具的要求。
第二步:原木预处理在将原木用于制作家具之前,需要进行原木的预处理工作。
首先是对原木进行去皮、锯切等加工,将原木加工成符合家具制作需要的木料。
然后需要对木料进行干燥处理,以降低木材的含水率,提高木材的稳定性和耐久性。
第三步:设计制图在进行实木家具制作之前,需要根据客户的需求和设计师的设计图纸进行详细的制作工艺流程计划。
制作家具的工艺流程包括家具的尺寸、结构、拼接方式、零部件加工等内容,需要进行详细的设计和制图工作。
第四步:木料加工木料加工是制作实木家具的关键环节。
在木料加工过程中,需要根据设计图纸将木料进行切割、刨削、雕刻等加工工艺,将木料加工成家具所需的各种零部件,包括家具的框架、面板、托座等。
第五步:拼接组装在木料加工完成后,需要将各个零部件进行拼接组装。
拼接组装工艺需要经验丰富的技术工人进行操作,确保家具的结构稳固、连接牢固。
在拼接组装过程中,需要使用专业的胶水、螺丝等连接材料,确保家具的质量。
第六步:修整打磨拼接组装完成后,需要对家具进行修整打磨工艺。
修整打磨工艺是为了去除家具表面的毛刺、瑕疵,使家具表面光滑、平整。
在修整打磨过程中,需要使用不同粗细的砂纸进行打磨,最终达到家具表面光滑细腻的效果。
第七步:涂装装饰家具的涂装装饰是制作实木家具的最后一个工艺环节。
在涂装装饰过程中,需要对家具进行上色、喷漆、打蜡等工艺,使家具表面呈现出丰富的色彩和纹理,提高家具的美观度和保护性能。
第八步:质量检验在制作实木家具的工艺流程完成后,需要进行严格的质量检验。
实木家具制作工艺流程
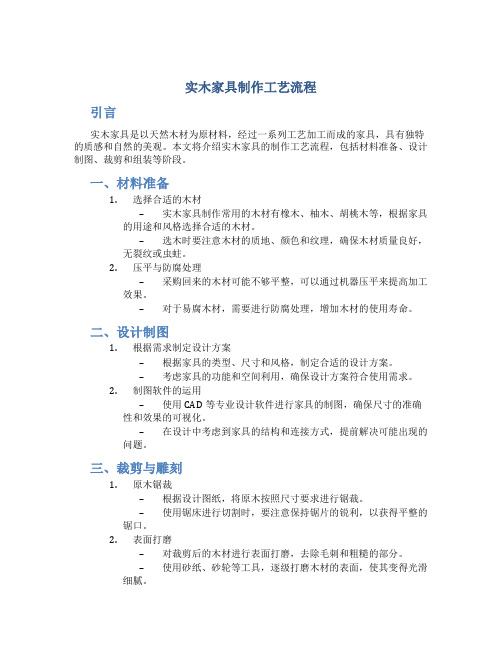
实木家具制作工艺流程引言实木家具是以天然木材为原材料,经过一系列工艺加工而成的家具,具有独特的质感和自然的美观。
本文将介绍实木家具的制作工艺流程,包括材料准备、设计制图、裁剪和组装等阶段。
一、材料准备1.选择合适的木材–实木家具制作常用的木材有橡木、柚木、胡桃木等,根据家具的用途和风格选择合适的木材。
–选木时要注意木材的质地、颜色和纹理,确保木材质量良好,无裂纹或虫蛀。
2.压平与防腐处理–采购回来的木材可能不够平整,可以通过机器压平来提高加工效果。
–对于易腐木材,需要进行防腐处理,增加木材的使用寿命。
二、设计制图1.根据需求制定设计方案–根据家具的类型、尺寸和风格,制定合适的设计方案。
–考虑家具的功能和空间利用,确保设计方案符合使用需求。
2.制图软件的运用–使用CAD等专业设计软件进行家具的制图,确保尺寸的准确性和效果的可视化。
–在设计中考虑到家具的结构和连接方式,提前解决可能出现的问题。
三、裁剪与雕刻1.原木锯裁–根据设计图纸,将原木按照尺寸要求进行锯裁。
–使用锯床进行切割时,要注意保持锯片的锐利,以获得平整的锯口。
2.表面打磨–对裁剪后的木材进行表面打磨,去除毛刺和粗糙的部分。
–使用砂纸、砂轮等工具,逐级打磨木材的表面,使其变得光滑细腻。
3.雕刻和装饰–根据设计要求和个人喜好,进行木材的雕刻和装饰。
–可以使用刻刀、雕刻机等工具进行细致的雕刻,营造出独特的艺术效果。
四、组装与涂装1.零件组装–根据设计图纸,将裁剪好的木材零件进行组装。
–使用合适的连接方式,如螺丝、胶水等,将家具的不同零件连接在一起。
2.结构加固–在组装过程中,需要注意家具的结构稳定性。
–可以通过加固木材连接处、添加托座或支撑物等方式增加家具的稳固性。
3.表面涂装–在家具组装完成后,进行表面的涂装处理,以增加外观亮丽度和防护效果。
–先进行底漆处理,然后进行上色和面漆施工,最后进行打磨和抛光,使家具表面平整光滑。
五、质量检验与包装1.质量检验–在家具制作完成后,进行质量检验,确保产品的质量符合要求。
实木家具生产工艺流程
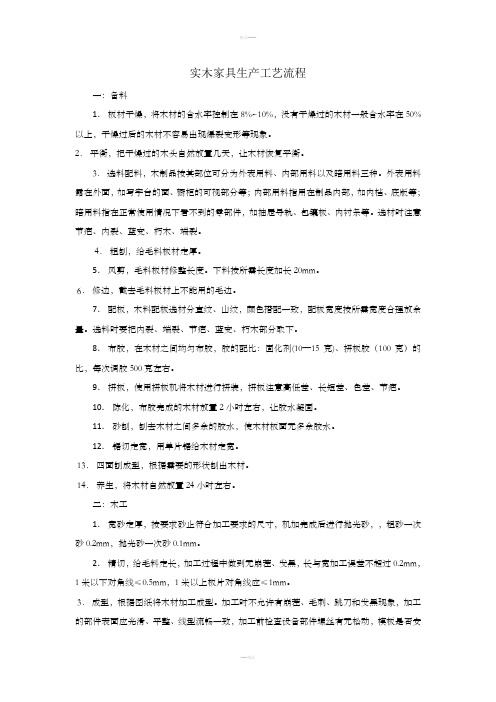
实木家具生产工艺流程一:备料1.板材干燥,将木材的含水率控制在8%~10%,没有干燥过的木材一般含水率在50%以上,干燥过后的木材不容易出现爆裂变形等现象。
2.平衡,把干燥过的木头自然放置几天,让木材恢复平衡。
3.选料配料,木制品按其部位可分为外表用料、内部用料以及暗用料三种。
外表用料露在外面,如写字台的面、橱柜的可视部分等;内部用料指用在制品内部,如内档、底版等;暗用料指在正常使用情况下看不到的零部件,如抽屉导轨、包镶板、内衬条等。
选材时注意节疤、内裂、蓝变、朽木、端裂。
4.粗刨,给毛料板材定厚。
5.风剪,毛料板材修整长度。
下料按所需长度加长20mm。
6.修边,截去毛料板材上不能用的毛边。
7.配板,木料配板选材分直纹、山纹,颜色搭配一致,配板宽度按所需宽度合理放余量。
选料时要把内裂、端裂、节疤、蓝变、朽木部分取下。
8.布胶,在木材之间均匀布胶,胶的配比:固化剂(10—15克)、拼板胶(100克)的比,每次调胶500克左右。
9.拼板,使用拼板机将木材进行拼装,拼板注意高低差、长短差、色差、节疤。
10.陈化,布胶完成的木材放置2小时左右,让胶水凝固。
11.砂刨,刨去木材之间多余的胶水,使木材板面无多余胶水。
12.锯切定宽,用单片锯给木材定宽。
13.四面刨成型,根据需要的形状刨出木材。
14.养生,将木材自然放置24小时左右。
二:木工1.宽砂定厚,按要求砂止符合加工要求的尺寸,机加完成后进行抛光砂,,粗砂一次砂0.2mm,抛光砂一次砂0.1mm。
2.精切,给毛料定长,加工过程中做到无崩茬、发黑,长与宽加工误差不超过0.2mm,1米以下对角线≤0.5mm,1米以上板片对角线应≤1mm。
3.成型,根据图纸将木材加工成型。
加工时不允许有崩茬、毛刺、跳刀和发黑现象,加工的部件表面应光滑、平整、线型流畅一致,加工前检查设备部件螺丝有无松动,模板是否安装规范,刀具是否装紧,加工过程中禁止顺刀进料,部件尺寸误差不超过0.2mm。
实木家具制作工艺流程
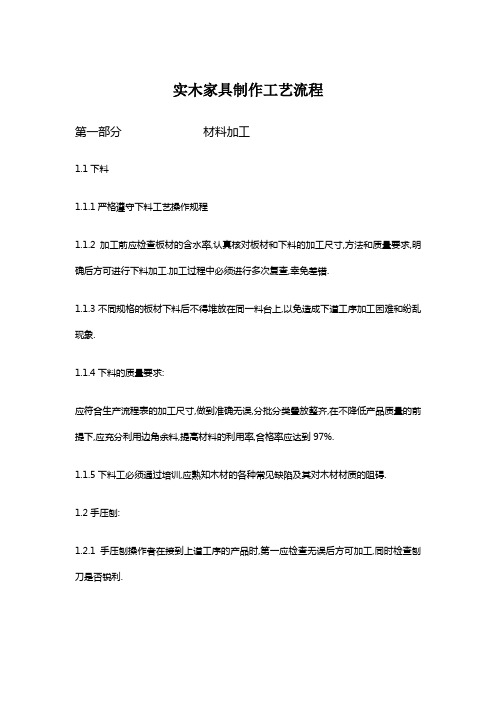
实木家具制作工艺流程第一部分材料加工1.1下料1.1.1严格遵守下料工艺操作规程1.1.2加工前应检查板材的含水率,认真核对板材和下料的加工尺寸,方法和质量要求,明确后方可进行下料加工.加工过程中必须进行多次复查,幸免差错.1.1.3不同规格的板材下料后不得堆放在同一料台上,以免造成下道工序加工困难和纷乱现象.1.1.4下料的质量要求:应符合生产流程表的加工尺寸,做到准确无误,分批分类叠放整齐,在不降低产品质量的前提下,应充分利用边角余料,提高材料的利用率,合格率应达到97%.1.1.5下料工必须通过培训,应熟知木材的各种常见缺陷及其对木材材质的阻碍.1.2手压刨:1.2.1手压刨操作者在接到上道工序的产品时,第一应检查无误后方可加工,同时检查刨刀是否锐利.1.1.2手压刨加工出的产品应笔直,平滑,规格标准一致,殘茬深度在0.3mm之内,交角必须保证90度,无戗茬.1.2.3加工好的部件按规格分类摆放,同时检查上道工序的产品质量对不合格件应及时选出.1.2.4手压刨加工的产品合格率应在98%以上.1.3冲锯:1.3.1锯边前要认真核对部件与生产流程表是否相符,准确无误后方可加工.1.3.2确保锯边质量,幸免差错,调机后加工第一件产品是,主副机手应分别检查,核对无误后方可进行加工,并在加工中多次检查,及时发觉问题,及时操纵质量事故.1.3.3锯边的质量要求符合工艺规定,准确直角,大小锯路一致,误差在0.2mm之内,锯面应平滑,无崩口,锯痕,同时检查上道工序的产品质量,对不合格产品应及时选出.1.4自动刨:1.4.1严格遵守工艺操作规程1.4.2质量要求直角,平滑,规格标准一致,薄厚正负误差在0.2mm之内,同时对不合格产品及时选出.1.4.3加工好的部件,应按流程表分批分类叠放整齐.1.4.4自动刨加工质量应在98%以上.1.5开齿指接机:1.5.1开齿机主机手在开齿过程中终须对上一道工序下来的料进行检查,发觉端部带有活节及较硬纹理时应给予挑出,幸免加工后显现崩齿.1.5.2指接前的料必须选择,原那么是按树种,薄厚宽窄,颜色及缺陷情形进行分类摆放.1.5.3指接料必须按照生产任务单所规定长度来进行定长指接,按需求生产.1.5.4关于选料过程中发觉的有死节,夹皮或钝棱等缺陷要挑出.送到下料锯或单片锯截除后再进行选料插接.1.5.5指接完的料不承诺再上下料锯加工.1.5.6指接后的料合格率为98%以上.1.6拼板:1.6.1原材料经两面刨选出厚度一致的板材,下料锯除去木材中的节子,腐朽等缺陷,开齿机将水线,腐朽等缺陷选出后进行指接,拼板.1.6.2拼板要注意色差,弦向,平均涂胶,涂胶量为250-300g/m2,胶与固化剂的配比为100:15,对板材施加10-15kg/m2的压力,时刻在40分钟左右.拼后放置2-4小时方可进行下一步加工.1.7四面刨:1.7.1严格遵守操作规程1.7.2四面刨主机手第一批阅生产任务单,按要求调整机器,调好后用废旧部件试机,主副机手应对试件进行检查,确保无误后方可加工.1.7.3针对不同的树种,材质调整适当的进料速度,幸免戗茬,在加工过程中应对上道工序下来的料进行检查,对薄厚不均,宽窄不一的料要选出,幸免损坏刀具.1.7.4四面刨两面吃刀量为3mm以内,加工误差要求正负0.2mm之内,要求加工面平坦,光滑,无戗茬.1.7.5合格率为98%以上.第二部分精加工2.1精截:2.1.1严格遵守工艺操作规程.2.1.2认真核对生产流程表和部件规格尺寸,明确后方可进行加工.2.1.3为确保精截的加工质量,符合工艺流程,幸免差错,第一检查锯截面是否方直,明确后方可进行加工,加工时合理选料,幸免不合格件流到下道工序.2.1.4精截的加工质量,锯截面应平滑,整齐,无崩口,锯痕等缺点,并在加工过程中多次检查,以防跑尺.及时发觉问题,并报质检人员进行处理.2.1.5加工好的部件,必须按生产流程表分批分类摆放,不得多批多类混放,合格率98%以上.2.2立铣:2.2.1立铣加工精度高,主机手终须通过严格选择,由具有识图能力和设备调试能力及有实际体会的职员充当.2.2.2认真核对图纸部件加工尺寸和要求,需要按型加工的部件必须按照图纸尺寸要求,由专人做好标准模具,加工前应用旧部件试机,准确无误后方可进行部件加工.并在加工中多次进行复查.2.2.3进料速度要适当.刃具要锐利,不可猛推猛拉,采纳送料器加工时,送料器的压力要适当.台面清洁,防止压出伤痕,划痕,造成质量事故.产品试加工时,工艺复杂的部件应请质检员,工段长等检查核实.2.2.4质量要求符合图纸和加工工艺规定,加工面准确,平滑,无崩口无毛刺,部件要合理摆放,合格率98%.2.3排钻:2.3.1严格遵守工艺操作规程.2.3.2认真检查核对部件生产流程表和图纸尺寸,材料同所加工的部件,材料,尺寸是否相符,明确后方可进行加工.2.3.3为保证加工质量,要求刀具必须锐利,压板或台面必须保持清洁,无木渣或铁钉及其它物,以防压坏部件,造成缺失.2.3.4主机手调机时应用旧部件进行调机,在加工第一块部件时,应认真检查核对,新产品或加工工艺复杂的部件应请质检员,工段长等检查核实,部件在加工到5件左右时应再一次检查,加工中应多次检查.2.3.5钻孔质量要求符合图纸加工尺寸和工艺要求,无误差,孔深孔位标准一致,部件摆放整齐,合格率99%2.4砂光:2.4.1主机手应所加工料的树种和部件表面质量要求选择适宜的砂带.2.4.2关于需要砂光的部件要顺纤维方向送料,幸免横向磨削,显现横向条痕.砂光的单位不能过大,否那么将留下沟纹.2.4.3加工前要认真选料,加工中要多次检查,加工面要求平坦,光滑,无刨痕,戗茬,锯痕等缺陷,如须立刨或二次砂光加工的个别种类部件,应留出足够的加工余量.第三部分组装3.1打磨3.1.1严格遵守工艺操作规程.部件要轻拿轻放.3.1.2打磨是整个家具外观质量的关键之一,必须认真对待此项工作,勤检查,如发觉问题应及时上报质检验员处理.3.1.3打磨要求表面光滑无硬棱,无刀痕,无砂痕,死角,沟痕,打磨时保持原有的部件弧度和曲度,将不合格部件及时选出,单独存放.3.1.4加工好的部件必须按照流程表分类摆放整齐,合格率99%3.2装配:3.2.1严格遵守工艺操作规程.3.2.2加工前应保持工作台面洁净,不得有钉头,沙粒,木屑等杂物,并做到加工中及时清扫以免刮花,刮伤部件,显现质量事故.3.2.3安装木塞时应选优质木塞,涂胶平均,以保证质量,安装螺丝时,必须用专用工具,主意将杂物擦净.3.2.4装配质量要求符合图纸工艺规定,牢固,平坦,严密,无伤痕,无锤印.3.2.5加工好的部件应合理摆放,以免压伤,合格率100%3.3组装3.3.1严格遵守工艺操作规程.3.3.2组装时,第一检查各个部件之间的产品代号,是否统一.加工质量是否合格.工作台要清洁,每个孔位必须涂好胶,部件颜色搭配安装,木塞不承诺有腐朽,死节等缺陷,以保证产品质量,整套部件安装后必须牢固.3.3.3加工好的部件必须配套摆放,合格率100%3.4试装3.4.1钻孔位检查:孔位,孔径,加工精度.3.4.2非钻孔部件:部件规格,材料品种,级别,加工精度.3.4.3立铣部件规格,加工面,崩口,曲面加工中的经线等.3.4.4按加工单顺序,检查合格后方可试装,检查组装质量,各间隙误差正负0.5mm结构牢固.3.4.5不合格品分析缘故,及时反映给质管人员处理.第四部分油漆4.1选料:4.1.1严格遵守工艺操作规程.4.1.2油漆前所有部件,经专职人员选择,发觉有加工质量问题的部件及时选出交修补人员处理.4.1.3选料时必须认真做好油漆前预备工作,对有压痕,划痕和戗茬的部件应打砂纸和补泥处理(按每批图纸质量要求为准)4.1.4选好的部件应分批分类整齐摆放,以免碰伤部件.阻碍产品质量.4.2喷漆:4.2.1严格遵守油漆工艺流程.4.2.2油漆是整个产品质量优劣的关键,也是直截了当决定整个家具外观质量的关键,必须认真抓好此项治理工作,严格把好质量关.4.2.3喷漆前一定要吹净灰尘,油漆质量要求漆面结实光滑,纹理清晰洁净,边角整齐,无流油,破油,气泡,粗纹,伤痕,发白等现象,走枪平均,不漏不流,底漆与面漆性质必须一致.4.2.4油漆着色时颜色要和封样要求一致,不得有花色,过深,过浅,着色不均等现象.涂料(油漆,色浆,稀料)应严格执行配比标准.4.2.5产品加工后应按步骤,分批分类摆放整齐,合格率98%4.3油漆打磨:4.3.1严格遵守工艺操作规程. 部件要轻拿轻放4.3.2打磨是整个油漆质量的关键之一.应认真做好油漆前的预备工作.保持台面清洁,防止划伤部件.4.3.3打砂纸时,要轻打细磨,打细,打全,砂纸的目数应按每遍油漆后的要求使用.不得擅自使用.以免阻碍油漆质量.对不合格的部件要及时选出,以免阻碍产品配套.4.3.4加工好的部件应分批分类摆放,做好喷漆前的预备工作,合格率100%4.4二试装:4.4.1检查项目:1)部件装配方向,质量,木塞孔是否施胶.2)组装部件应检查其精度,铁钉,木条装配情形,螺丝帽是否下沉3)喷漆是否有色差,光洁度等.4.5备料:4.5.1逐件检查是否漏打配件,铁钉,木螺丝有无下沉.4.5.2板面专门是门,台面,抽屉面有无损害,油漆情形.4.5.3备料时,数量要检查,发觉严峻损坏要找质检员处理.4.6包装:4.6.1包装前的所有部件必须通过备料质检员进行全面检查,同时进行产品的试装工作,准确后方可包装.4.6.2部件需用吹塑纸铺垫或包严,包装箱四角均用泡沫垫角挤实.4.6.3部件许多包,不多包,不错包.4.6.4每十块核对一下部件数量(包括配件包)发觉问题及时手拆包查找.4.6.5包装的产品应100%合格.同时进行拆包试装,完全无误后方可入库.榫卯结构的研究中国家具之榫卯结构讲解三碰肩,又名棕角榫,其做法通常是将要支撑的立柱顶端处开长短两个榫头,两侧为榫肩,靠里面为直角平肩,在需要支撑的面板上开出相应的卯眼,靠别处的卯眼上面挖出一块和梯形格角一样的缺口,两根木枨榫对卯眼一扣即可连接。
实木家具生产工艺流程 (2)

实木家具生产工艺流程一:备料1.板材干燥,将木材的含水率控制在8%~10%,没有干燥过的木材一般含水率在50%以上,干燥事后的木材不简单出现爆裂变形等现象。
2.均衡,把干燥过的木头自然搁置几日,让木材恢复均衡。
3.选料配料,木制品按其部位可分为表面用料、内部用料以及暗用料三种。
表面用料露在外面,如写字台的面、橱柜的可视部分等;内部用料指用在制品内部,如内档、底版等;暗用料指在正常使用状况下看不到的零零件,如抽屉导轨、包镶板、内衬条等。
选材时注意节疤、内裂、蓝变、朽木、端裂。
4.粗刨,给毛料板材定厚。
5.风剪,毛料板材修整长度。
下料按所需长度加长20mm。
6.修边,截去毛料板材上不可以用的毛边。
7.配板,木材配板选材分直纹、山纹,颜色搭配一致,配板宽度按所需宽度合理放余量。
选料时要把内裂、端裂、节疤、蓝变、朽木部分取下。
8.布胶,在木材之间平均布胶,胶的配比:固化剂(10 — 15 克 ) 、拼板胶( 100 克)的比,每次调胶500 克左右。
9.拼板,使用拼板机将木材进行拼装,拼板注意高低差、长短差、色差、节疤。
10.陈化,布胶达成的木材搁置 2 小时左右,让胶水凝结。
11.砂刨,刨去木材之间剩余的胶水,使木材板面无剩余胶水。
12.锯切定宽,用单片锯给木材定宽。
13.四周刨成型,依据需要的形状刨出木材。
14.养生,将木材自然搁置24 小时左右。
二:木匠1.宽砂定厚,按要求砂止切合加工要求的尺寸,机加达成后进行抛光砂,,粗砂一次砂,抛光砂一次砂。
2.精切,给毛料定长,加工过程中做到无崩茬、发黑,长与宽加工偏差不超出, 1 米以下对角线≤, 1 米以上板片对角线应≤1mm。
3.成型,依据图纸将木材加工成型。
加工时不同意有崩茬、毛刺、跳刀和发黑现象,加工的零件表面应圆滑、平坦、线型流利一致,加工前检查设施零件螺丝有无松动,模板能否安装规范,刀具能否装紧,加工过程中严禁顺刀进料,零件尺寸偏差不超出。
4.钻孔,按图纸的工艺要求钻孔,加工过程中做到无崩口、无刺现象,孔位加工偏差不得超出,产品要做到配套钻孔,常试装、勤检查,保证产品的质量。
- 1、下载文档前请自行甄别文档内容的完整性,平台不提供额外的编辑、内容补充、找答案等附加服务。
- 2、"仅部分预览"的文档,不可在线预览部分如存在完整性等问题,可反馈申请退款(可完整预览的文档不适用该条件!)。
- 3、如文档侵犯您的权益,请联系客服反馈,我们会尽快为您处理(人工客服工作时间:9:00-18:30)。
实木家具制作工艺流程修订版IBMT standardization office【IBMT5AB-IBMT08-IBMT2C-ZZT18】实木家具工艺质量要求与操作程序第一部分材料加工1.1下料1.1.1严格遵守下料工艺操作规程1.1.2加工前应检查板材的含水率,仔细核对板材和下料的加工尺寸,方法和质量要求,明确后方可进行下料加工.加工过程中必须进行多次复查,避免差错.1.1.3不同规格的板材下料后不得堆放在同一料台上,以免造成下道工序加工困难和混乱现象.1.1.4下料的质量要求:应符合生产流程表的加工尺寸,做到准确无误,分批分类叠放整齐,在不降低产品质量的前提下,应充分利用边角余料,提高材料的利用率,合格率应达到97%.1.1.5下料工必须经过培训,应熟知木材的各种常见缺陷及其对木材材质的影响.1.2手压刨:1.2.1手压刨操作者在接到上道工序的产品时,首先应检查无误后方可加工,同时检查刨刀是否锋利.1.1.2手压刨加工出的产品应笔直,平滑,规格标准一致,残茬深度在0.3mm之内,交角必须保证90度,无戗茬.1.2.3加工好的部件按规格分类摆放,同时检查上道工序的产品质量对不合格件应及时选出.1.2.4手压刨加工的产品合格率应在98%以上.1.3冲锯:1.3.1锯边前要仔细核对部件与生产流程表是否相符,准确无误后方可加工.1.3.2确保锯边质量,避免差错,调机后加工第一件产品是,主副机手应分别检查,核对无误后方可进行加工,并在加工中多次检查,及时发现问题,及时控制质量事故.1.3.3锯边的质量要求符合工艺规定,准确直角,大小锯路一致,误差在0.2mm之内,锯面应平滑,无崩口,锯痕,同时检查上道工序的产品质量,对不合格产品应及时选出.1.4自动刨:1.4.1严格遵守工艺操作规程1.4.2质量要求直角,平滑,规格标准一致,薄厚正负误差在0.2mm之内,同时对不合格产品及时选出.1.4.3加工好的部件,应按流程表分批分类叠放整齐.1.4.4自动刨加工质量应在98%以上.1.5开齿指接机:1.5.1开齿机主机手在开齿过程中终须对上一道工序下来的料进行检查,发现端部带有活节及较硬纹理时应给予挑出,避免加工后出现崩齿.1.5.2指接前的料必须挑选,原则是按树种,薄厚宽窄,颜色及缺陷情况进行分类摆放.1.5.3指接料必须按照生产任务单所规定长度来进行定长指接,按需求生产.1.5.4对于选料过程中发现的有死节,夹皮或钝棱等缺陷要挑出.送到下料锯或单片锯截除后再进行选料插接.1.5.5指接完的料不允许再上下料锯加工.1.5.6指接后的料合格率为98%以上.1.6拼板:1.6.1原材料经两面刨选出厚度一致的板材,下料锯除去木材中的节子,腐朽等缺陷,开齿机将水线,腐朽等缺陷选出后进行指接,拼板.1.6.2拼板要注意色差,弦向,均匀涂胶,涂胶量为250-300g/m2,胶与固化剂的配比为100:15,对板材施加10-15kg/m2的压力,时间在40分钟左右.拼后放置2-4小时方可进行下一步加工.1.7四面刨:1.7.1严格遵守操作规程1.7.2四面刨主机手首先审阅生产任务单,按要求调整机器,调好后用废旧部件试机,主副机手应对试件进行检查,确保无误后方可加工.1.7.3针对不同的树种,材质调整适当的进料速度,避免戗茬,在加工过程中应对上道工序下来的料进行检查,对薄厚不均,宽窄不一的料要选出,避免损坏刀具.1.7.4四面刨两面吃刀量为3mm以内,加工误差要求正负0.2mm之内,要求加工面平整,光滑,无戗茬.1.7.5合格率为98%以上.第二部分精加工2.1精截:2.1.1严格遵守工艺操作规程.2.1.2仔细核对生产流程表和部件规格尺寸,明确后方可进行加工.2.1.3为确保精截的加工质量,符合工艺流程,避免差错,首先检查锯截面是否方直,明确后方可进行加工,加工时合理选料,避免不合格件流到下道工序.2.1.4精截的加工质量,锯截面应平滑,整齐,无崩口,锯痕等缺点,并在加工过程中多次检查,以防跑尺.及时发现问题,并报质检人员进行处理.2.1.5加工好的部件,必须按生产流程表分批分类摆放,不得多批多类混放,合格率98%以上.2.2立铣:2.2.1立铣加工精度高,主机手终须经过严格挑选,由具有识图能力和设备调试能力及有实际经验的员工充当.2.2.2仔细核对图纸部件加工尺寸和要求,需要按型加工的部件必须按照图纸尺寸要求,由专人做好标准模具,加工前应用旧部件试机,准确无误后方可进行部件加工.并在加工中多次进行复查.2.2.3进料速度要适当.刃具要锋利,不可猛推猛拉,采用送料器加工时,送料器的压力要适当.台面清洁,防止压出伤痕,划痕,造成质量事故.产品试加工时,工艺复杂的部件应请质检员,工段长等检查核实.2.2.4质量要求符合图纸和加工工艺规定,加工面准确,平滑,无崩口无毛刺,部件要合理摆放,合格率98%.2.3排钻:2.3.1严格遵守工艺操作规程.2.3.2仔细检查核对部件生产流程表和图纸尺寸,材料同所加工的部件,材料,尺寸是否相符,明确后方可进行加工.2.3.3为保证加工质量,要求刀具必须锋利,压板或台面必须保持清洁,无木渣或铁钉及其它物,以防压坏部件,造成损失.2.3.4主机手调机时应用旧部件进行调机,在加工第一块部件时,应认真检查核对,新产品或加工工艺复杂的部件应请质检员,工段长等检查核实,部件在加工到5件左右时应再一次检查,加工中应多次检查.2.3.5钻孔质量要求符合图纸加工尺寸和工艺要求,无误差,孔深孔位标准一致,部件摆放整齐,合格率99%2.4砂光:2.4.1主机手应所加工料的树种和部件表面质量要求选择适宜的砂带.2.4.2对于需要砂光的部件要顺纤维方向送料,避免横向磨削,出现横向条痕.砂光的单位不能过大,否则将留下沟纹.2.4.3加工前要认真选料,加工中要多次检查,加工面要求平整,光滑,无刨痕,戗茬,锯痕等缺陷,如须立刨或二次砂光加工的个别种类部件,应留出足够的加工余量.第三部分组装3.1打磨3.1.1严格遵守工艺操作规程.部件要轻拿轻放.3.1.2打磨是整个家具外观质量的关键之一,必须认真对待此项工作,勤检查,如发现问题应及时上报质检验员处理.3.1.3打磨要求表面光滑无硬棱,无刀痕,无砂痕,死角,沟痕,打磨时保持原有的部件弧度和曲度,将不合格部件及时选出,单独存放.3.1.4加工好的部件必须按照流程表分类摆放整齐,合格率99%3.2装配:3.2.1严格遵守工艺操作规程.3.2.2加工前应保持工作台面干净,不得有钉头,沙粒,木屑等杂物,并做到加工中及时清扫以免刮花,刮伤部件,出现质量事故.3.2.3安装木塞时应选优质木塞,涂胶均匀,以保证质量,安装螺丝时,必须用专用工具,主意将杂物擦净.3.2.4装配质量要求符合图纸工艺规定,牢固,平整,严密,无伤痕,无锤印.3.2.5加工好的部件应合理摆放,以免压伤,合格率100%3.3组装3.3.1严格遵守工艺操作规程.3.3.2组装时,首先检查各个部件之间的产品代号,是否统一.加工质量是否合格.工作台要清洁,每个孔位必须涂好胶,部件颜色搭配安装,木塞不允许有腐朽,死节等缺陷,以保证产品质量,整套部件安装后必须牢固.3.3.3加工好的部件必须配套摆放,合格率100%3.4试装3.4.1钻孔位检查:孔位,孔径,加工精度.3.4.2非钻孔部件:部件规格,材料品种,级别,加工精度.3.4.3立铣部件规格,加工面,崩口,曲面加工中的经线等.3.4.4按加工单顺序,检查合格后方可试装,检查组装质量,各间隙误差正负0.5mm结构牢固.3.4.5不合格品分析原因,及时反映给质管人员处理.第四部分油漆4.1选料:4.1.1严格遵守工艺操作规程.4.1.2油漆前所有部件,经专职人员筛选,发现有加工质量问题的部件及时选出交修补人员处理.4.1.3选料时必须认真做好油漆前准备工作,对有压痕,划痕和戗茬的部件应打砂纸和补泥处理(按每批图纸质量要求为准)4.1.4选好的部件应分批分类整齐摆放,以免碰伤部件.影响产品质量.4.2喷漆:4.2.1严格遵守油漆工艺流程.4.2.2油漆是整个产品质量优劣的关键,也是直接决定整个家具外观质量的关键,必须认真抓好此项管理工作,严格把好质量关.4.2.3喷漆前一定要吹净灰尘,油漆质量要求漆面结实光滑,纹理清晰干净,边角整齐,无流油,破油,气泡,粗纹,伤痕,发白等现象,走枪均匀,不漏不流,底漆与面漆性质必须一致.4.2.4油漆着色时颜色要和封样要求一致,不得有花色,过深,过浅,着色不均等现象.涂料(油漆,色浆,稀料)应严格执行配比标准.4.2.5产品加工后应按步骤,分批分类摆放整齐,合格率98%4.3油漆打磨:4.3.1严格遵守工艺操作规程. 部件要轻拿轻放4.3.2打磨是整个油漆质量的关键之一.应认真做好油漆前的准备工作.保持台面清洁,防止划伤部件.4.3.3打砂纸时,要轻打细磨,打细,打全,砂纸的目数应按每遍油漆后的要求使用.不得擅自使用.以免影响油漆质量.对不合格的部件要及时选出,以免影响产品配套.4.3.4加工好的部件应分批分类摆放,做好喷漆前的准备工作,合格率100%4.4二试装:4.4.1检查项目:1)部件装配方向,质量,木塞孔是否施胶.2)组装部件应检查其精度,铁钉,木条装配情况,螺丝帽是否下沉3)喷漆是否有色差,光洁度等.4.5备料:4.5.1逐件检查是否漏打配件,铁钉,木螺丝有无下沉.4.5.2板面尤其是门,台面,抽屉面有无损伤,油漆情况.4.5.3备料时,数量要检查,发现严重损坏要找质检员处理.4.6包装:4.6.1包装前的所有部件必须经过备料质检员进行全面检查,同时进行产品的试装工作,准确后方可包装.4.6.2部件需用吹塑纸铺垫或包严,包装箱四角均用泡沫垫角挤实.4.6.3部件不少包,不多包,不错包.4.6.4每十块核对一下部件数量(包括配件包)发现问题及时手拆包查找.4.6.5包装的产品应100%合格.同时进行拆包试装,完全无误后方可入库.榫卯结构的研究中国家具之榫卯结构讲解三碰肩,又名棕角榫,其做法通常是将要支撑的立柱顶端处开长短两个榫头,两侧为榫肩,靠里面为直角平肩,在需要支撑的面板上开出相应的卯眼,靠外面的卯眼上面挖出一块和梯形格角一样的缺口,两根木枨榫对卯眼一扣即可连接。
在这样连接后,家具结构的两个看面上各有一个肩,而腿足或立柱部位留有一个肩,三个肩碰在一起故叫三碰肩。
凡是有盖或有底的家具部位都可使用这种结构连接。
三碰肩是一种比较科学的做法,它的榫头在中间,两边均有榫肩,可以辅助榫头承受部分压力不易扭动,加强了竖材的支撑能力,使得家具坚固耐用,同时也打破了结构处横竖线条平直过于呆板的气氛,锦上添花地烘托出家具流畅的线条美。