汽车纵梁加工工艺及设备的选择.doc
卡车纵梁自动化生产工艺分析

。
l 79
滚压 成形 后对 纵梁进 行检 测 ,根据滚 压 工序卡 对不 同型 号 纵 梁 主 要 进 行长 度 、翼 面高 度 、翼 面 角度 的检 测 ,每 批 卷 料 只 需 检测 前 四 件 后 两件 , 中间 部分 抽 检
1 门。 即 可 。检 测 合 格 的纵 梁 ,利 用地 面 机 械 化传 输 系 统运 送 至 通 过 式打 标 机 进 行打 标 ,形 成 永 久 性标 识 。
浪形 ( 见 图4) ,影 响加工精度 。纵 梁一般在端部 进行切
割 ,不 同型号 纵梁切割方式也 不尽相 同。
( a) 抛丸处理前
( b) 抛丸处理后
图5 抛 丸前 后 板 材 表 面 情 况 对 比
砸
抛 丸后板 材经 起重 机运 至折 弯机进 行 折弯 ,折 弯机 为国产设备 ,如 图6 所 示 根据 型号将板材 折弯成相 应角 度 与腹 面落 差后 运至板 材缓 存 区 ,对折 弯后板 材进 行折 弯角度 与腹 面落差检 测以保证折 弯质 量
至; 中孔机 上 料 线 ,经红 外 识 别 纵 梁标 号 后 反 馈至 主控 制 系 统 ,由主 控 制 系统 给 出冲 孔机 打 孔 位 置 并进 行; 中 孔 ,; 中孔 后 由人 工 对卷 料 成 形 首 末纵 梁 ; 中孔 数量 进行
检 测
图3 等离子切割机
图4 切 割 面
( 3) 抛丸 、折弯与压合
卡车纵梁 自动化生产工艺分析
机械 第 儿设 汁研究院 仃限 公 - d
纵 梁生产工 艺水平是 影响卡 车产 品质量 的重要 因素 对 国内某卡 车纵 梁滚 压车 间 自动化 生产情 况进 行 了详细 介绍 ,阐述 了卡 车纵 梁 自动化 生产 工艺及滚 压 、冲孔 、等 离子切 割 、抛 丸 、折 弯 、压合 等工 序戍形 方法与精度控 制 ,对 国 内相关行 业提 高纵 梁生产效率 ,提升 纵梁产品 质量水平起到 了一定的指 导作 用
浅谈汽车车架纵梁加工设备的选择

浅谈汽车车架纵梁加工设备的选择着汽车工业的日益发展,汽车纵梁的数量和品种也不断增加,纵梁加工设备也不断创新完善,从而合理地选择纵梁加工设备是汽车纵梁制造企业保持强劲的竞争力的关键。
一般纵梁由主梁和加强梁组成,梁的形状为U型。
加强梁装在主梁内,用铆钉连接。
根据车型不同,纵梁分直梁式和曲梁式;又分等截面梁和变截面梁。
一、纵梁的加工工序一般加工工序分两类,即先加工孔后成形或先成形后加工孔。
1、落料——加工孔——成形——(弯曲)2、落料——成形——加工孔——(弯曲)二、加工设备的选用1、落料(1)剪切型:用纵剪机和剪板机来完成。
(2)落料型:用大型压力机来完成。
2、成形(1)单面折弯型:用大型折弯机来完成。
(2)双面折弯型:用大型压力机来完成。
比较3、孔加工(1)平板上的孔加工a、钻孔型:全部孔由数台摇臂钻床来完成,或由大型数控钻床来完成(可以几块板叠放一起钻)。
b、冲孔+钻孔型:主梁上的全部孔和加强梁的腹板孔由数控冲孔压力机来完成;成形后以主梁的翼板孔为准钻出加强梁的翼板孔(主梁和加强梁上孔的重合位置精度较高)。
c、冲孔型:全部孔由数控冲孔压力机来完成。
(2)U形梁上的孔加工a、钻孔型:全部孔由三面数控钻孔生产线或工件回转式单面数控钻孔生产线来完成。
b、冲孔+钻孔型:腹板孔由冲孔数控生产线来完成,翼板孔由双面钻孔数控生产线来完成(翼板孔很少)。
c、冲孔型:全部孔由几台冲孔压力机组成的数控生产线来完成。
比较4、弯曲a、普通型:由大型压力机来完成。
b、专用型:由专用数控弯曲机来完成,即一台固定压力机与一台可回转压力机铰接,并分别压紧腹板,通过油缸拉或推可回转压力机来完成折弯。
在两台压力机上设有三对油缸对翼板进行夹紧,防止起皱。
三、平板冲孔生产线一般由上料、坯料对中、进料辊道、送料机械手、冲孔压力机、出料辊道、下料等部分组成。
1、平板冲孔压力机的形式(1)回转模库和回转下模式模具为环形排列。
上模放在回转模库上,下模装在回转模架上。
重型汽车车架纵梁加工工艺

重型汽车车架纵梁加工工艺
重型汽车车架纵梁加工工艺是汽车制造过程中一个重要环节,它是汽车车体结构及外
观整体曲面工艺的关键。
因此,汽车车架纵梁的高度准确加工工艺具有重要意义。
汽车车架纵梁的加工工艺主要由切割、焊接、压模三大环节组成,可以分为以下几个
步骤:
第一步,将汽车车架纵梁外观整体曲面加工切割
首先在汽车车架纵梁上标绘出切割轮廓,然后将汽车车架纵梁放置在数控车床上,利
用CNC加工中心进行数控切削精度高,加工精度达到了±0.2毫米,将模具的轮廓精确切
割完成,使汽车车架纵梁的外形准确的加工。
第二步,将汽车车架纵梁进行焊接
焊接汽车车架纵梁主要是采用钢管和铝合金等材料,使用熔焊焊接可以达到很好的效果,焊接完成后,将产品整体包裹熔剂,使汽车车架纵梁的外形更加美观光滑。
第三步,汽车车架纵梁的压模
压模的精度较高,比如汽车车架纵梁,因为要求高度一致和曲率准确,只能用机械压铸,一般通过采用多种加热模具和机械压模工艺实现汽车车架纵梁的加工,最终使汽车车
架纵梁的外观和尺寸完全符合要求。
总之,汽车车架纵梁加工工艺是一个耗时、高精度的工艺,因此要求设备的精度和效
能要求都比较高。
其加工完毕的汽车车架纵梁,其质量也与此对应的质量也更加的高质量。
浅议中型客车纵梁制造工艺方案(精)
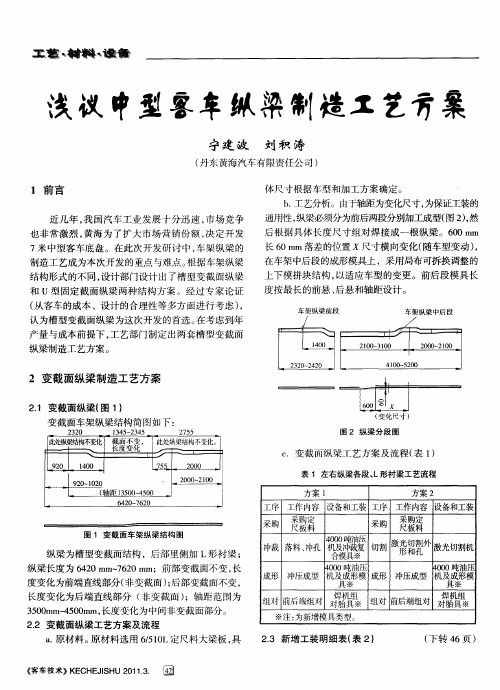
工序 工作内容 设备和工装 工序 工作 内容 设备和工装
图 1 变截 面 车 架 纵 梁结 构 图
纵梁 为槽 型变 截 面结 构 ,后 部里 侧加 L形 衬梁 ;
纵梁 长度为 6 4 2 0 m m~ 7 6 2 0 m m;前 部变截 面不变 , 长 度变化为前端 直线部分 ( 非 变截 面) ; 后部变截 面不变 , 长度变 化为后 端直线 部分 ( 非 变截 面 ) ;轴 距范 围为 3 5 0 0 mm - 4 5 0 0 m m, 长度变化为 中间非变截 面部 分。 2 . 2 变截面 纵梁工 艺方案 及流程 a . 原材料 。 原 材料选 用 6 / 5 I O L定尺料 大梁板 , 具
4 0 0 0 吨油压 激光切割外 激光切 冲裁 落料 、 冲孔 机及冲 裁复 切割 形和孔 割机 合模具※
4 0 0 0吨油压 4 0 0 0 吨油压 成形 冲压成 型 机及成形模 成形 冲压成型 机及成形模
具※ 具※
组对 前后端组对 焊机组 焊机组 对胎具 ※ 组对 前后端组对 对胎具※
认 为槽 型变截 面纵 梁 为这次开 发 的首 选 。 在考 虑到年
度 按最长 的前悬 、 后悬 和轴距设 计 。
车架 纵 梁前段 车架纵 梁 中后 段
产量 与成本 前提下 , 工艺 部 门制定 出两套槽 型变 截 面 纵梁 制造工 艺方案 。
2 变截 面纵梁制造工艺方案
2 . 1 变截面 纵梁 ( 图1 ) 变截 面车架 纵梁结构 简 图如下 :
※注: 为新增模具类型。
2 . 3 新增 工装明 细表( 表 2)
( 下转 4 6页 )
《 客车技 术》 K E C H E J I S H U 2 0 1 1 . 3 . 固
汽车纵梁加工工艺及设备的选择
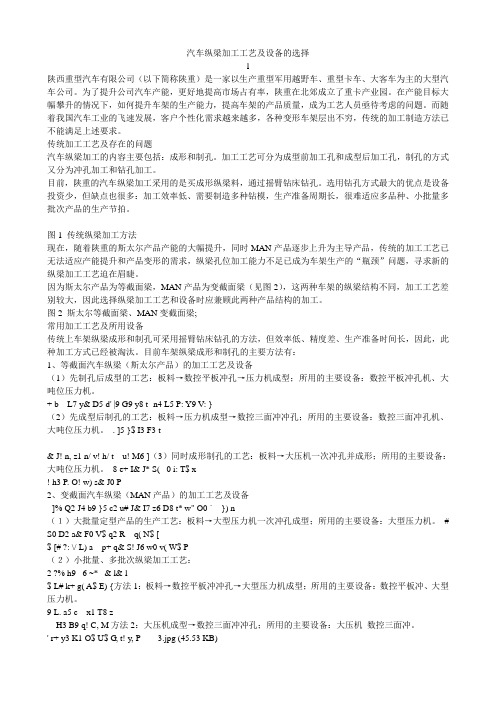
汽车纵梁加工工艺及设备的选择l陕西重型汽车有限公司(以下简称陕重)是一家以生产重型军用越野车、重型卡车、大客车为主的大型汽车公司。
为了提升公司汽车产能,更好地提高市场占有率,陕重在北郊成立了重卡产业园。
在产能目标大幅攀升的情况下,如何提升车架的生产能力,提高车架的产品质量,成为工艺人员亟待考虑的问题。
而随着我国汽车工业的飞速发展,客户个性化需求越来越多,各种变形车架层出不穷,传统的加工制造方法已不能满足上述要求。
传统加工工艺及存在的问题汽车纵梁加工的内容主要包括:成形和制孔。
加工工艺可分为成型前加工孔和成型后加工孔,制孔的方式又分为冲孔加工和钻孔加工。
目前,陕重的汽车纵梁加工采用的是买成形纵梁料,通过摇臂钻床钻孔。
选用钻孔方式最大的优点是设备投资少,但缺点也很多:加工效率低、需要制造多种钻模,生产准备周期长,很难适应多品种、小批量多批次产品的生产节拍。
图1 传统纵梁加工方法现在,随着陕重的斯太尔产品产能的大幅提升,同时MAN产品逐步上升为主导产品,传统的加工工艺已无法适应产能提升和产品变形的需求,纵梁孔位加工能力不足已成为车架生产的“瓶颈”问题,寻求新的纵梁加工工艺迫在眉睫。
因为斯太尔产品为等截面梁,MAN产品为变截面梁(见图2),这两种车架的纵梁结构不同,加工工艺差别较大,因此选择纵梁加工工艺和设备时应兼顾此两种产品结构的加工。
图2 斯太尔等截面梁、MAN变截面梁;常用加工工艺及所用设备传统上车架纵梁成形和制孔可采用摇臂钻床钻孔的方法,但效率低、精度差、生产准备时间长,因此,此种加工方式已经被淘汰。
目前车架纵梁成形和制孔的主要方法有:1、等截面汽车纵梁(斯太尔产品)的加工工艺及设备(1)先制孔后成型的工艺:板料→数控平板冲孔→压力机成型;所用的主要设备:数控平板冲孔机、大吨位压力机。
+ b L7 y& D5 d' |9 G9 y8 t- n4 L5 P: Y9 V: }(2)先成型后制孔的工艺:板料→压力机成型→数控三面冲冲孔;所用的主要设备:数控三面冲孔机、大吨位压力机。
重型汽车车架纵梁加工

第 2 期 8
收稿 日期 :0 1 0 一 O 2 1 — 8 l
重型汽 车车架纵梁加 工
乔 战 林
( 太原长安重 型汽 车有 限公 司 , 山西太原 ,3 0 2 00 3 )
摘
要: 从重型 汽车车架纵 梁生产线 的组成及加 工范围入手 , 概述 了重型汽 车车 架纵
梁加工工艺流程 , 细介绍 了重 型汽 车车架纵 梁的加 工过程 。 详
关键词 : 重型 汽车 ; 车架纵梁 ; 生产线 ; 工艺流程
中图 分 类 号 : 4 U6 文献 标 识 码 : A 22 主 梁 三 面 冲 孔 工 位 .
重型汽车车架纵梁 加工 生产线 以国内经济适用 的 “ 精益生 产 ” 式为设 计 的指 导思想 , 分贯彻成 熟技术 、 济 、 方 充 经 方便 、 安 全 的设 计原则 , 使该生产线具有一定 的柔性生产能力 。本生产线 属于多 品种 、 小成批 生产 , 设备 的选 型充 分考 虑柔 性化生 产 , 坚
() 3本焊接工位所产生 的焊烟通过专用排 烟装置进行处理 。
() 4 夹具形状为 “ ” , 紧方式为手工螺栓拧 紧。 c型 夹
25 主副梁配钻腹面孔工位 .
钻孔工序 由 1 2台摇臂钻分 3个工位组 成 , 据不 同规格纵 根
梁的孔数及其孔位 分布 , 梁腹面孔分 3 工位配钻 , 将纵 个 各工位
科 技情报开发与经济
文章编号 : 0 — 0 3 2 1 )8 0 2 — 2 1 5 6 3 (0 12 — 2 10 0
S IT C F R A IND V L P E T&E O O Y C- E HI O M TO E E O M N N CN M
21 年 0 1
汽车纵梁压机技术说明

性能特点:本机器适用于汽车纵梁拉伸工艺,也可以从事其它金属薄板压制成型以及校正等工艺。
本机器具有独立的动力机构和电气系统,采用PLC控制技术、闭环同步控制系统按钮集中控制,可实现点动、手动、半自动三种操作方式,并根据用户不同长度产品的工艺要求采取不同的程序控制,降低功耗。
本机器的工作压力、压制速度、行程范围均可根据工艺要求进行调整。
本机器采用三梁多柱结构形式,三梁采用焊接梁进行时效处理,机器具有足够的刚度和强度,操作空间宽敞.便于四面观察和安装调整模具,整机结构简单,外形美观。
液压系统采用集成插装系统和比例控制阀相结合,可实现流量大、同步精度高抗偏载能力大的要求,且结构简单、紧凑,动作灵敏可靠,便于故障的诊断和排除。
本机器动力系统上置,减少机器的占地面积。
上梁四周设有安全护栏,并备有爬梯,便于安装及维修。
三、结构概述:本机器由主机及控制机构两个部分组成。
通过管路及电气系统装置联系起来构成完整一体。
主机部分分为机身、主缸、顶缸及充液装置等部分,控制机构包括动力机构、限程装置、管路及电气控制箱等部分。
现将各分机构和作用分述如下:(一)机身机身为整体框架结构由滑块、工作台、液压垫、导向机构等组成,依靠四角八面导轨定位导向,机器精度高、抗偏载能力强。
滑块与主缸活塞由连接法兰相联接,滑块及工作台表面均有T形槽,以便于安装模具,T形槽尺寸见附图1及2。
(二) 主缸主缸结构,缸体靠缸口台肩及大锁母紧固于上横梁内。
活塞下端用法兰与滑块相联接。
活塞头部材料为铸铁,作导向用。
活塞头外圆装有方向相反的密封环,内圆装有O形环,将缸内形成上下两个油腔,缸口部分也装有密封环及O形环,由缸口锁母来锁紧,以保证下腔密封。
(三)顶缸顶缸装于工作台中心孔内,用锁紧螺母加以固定,结构与主缸相同。
(四)动力机构动力机构由油箱、油泵电机组、插装阀控制系统及各种压力阀、方向阀等组成。
它是产生和分配工作液压,使主机实现各种动作的机构,安装在机身右侧。
做汽车的都该了解下,汽车纵梁的制造工艺及装备

做汽车的都该了解下,汽车纵梁的制造工艺及装备载货汽车纵梁是各种轻型、中型及重型载货汽车车架的主要构件,载货汽车车架一般由左右两根纵梁和几根横梁组成,车架作为整个汽车的基体,是组装发动机、传动系统、悬架、转向系统等各部件的骨架,承受来自车身内外的各种载荷作用。
同时,由于载货车车架的结构尺寸较大,各部件之间的装配工艺比较严格,其结构形式及加工工艺直接影响到重型载货汽车的品质。
在车架的主要构成部件中,左右纵梁是整个车架的主体,是汽车其他部件的装配基础,同时也是汽车的关键承载部件。
车型的多样化和发动机等核心部件的改型等因素造成车架纵梁的形状、尺寸和孔的大小及数量、分布等都有不同程度的差别,同时由于载货汽车的承重要求造成其纵梁材料一般较厚、尺寸较长(几乎与整车相当),所以载货汽车纵梁的制造工艺极为复杂,其制造成本相对也比较高。
随着汽车工业的飞速发展及科技的不断进步,纵梁的制造工艺及相应工装设备也不断改进和优化。
随之涌现出各种柔性化的纵梁制造技术及工艺,汽车纵梁的生产方式逐渐由“单一品种、大批量、小批次”向“多品种、小批量、多批次”转变,本文主要对现代载货汽车纵梁的制造工艺及相应的加工设备做简要论述。
制造工艺及装备随着汽车工业的日益发展,载货汽车纵梁的数量和品种也不断增加,纵梁的制造工艺和加工设备也不断创新和完善。
总体来说,载货汽车纵梁的制造工艺主要分为3个工序内容:落料、孔加工和成形加工。
其整体制造工艺流程则为上述三种工序内容的部分或全部组合。
1. 各工序内容及相应加工设备(1)落料一般汽车厂直接采购的原材料钢板都是大块板料(见图1),需要根据不同的产品将板料加工出所需的形状和尺寸,此工序即为落料。
根据加工设备的不同,落料工序主要分为剪切落料、模具落料和切割落料三种形式。
剪切落料的设备是剪板机(见图2),根据其加工板料长度的不同,有3m、6m、8m和12m等不同规格;剪板机无需开发模具,在设备规格允许范围内可获得不同厚度、长度和宽度规格的料片;但剪板机只能下矩形料片,只适用于等截面U形梁的生产,对于变截面梁则不适用。
工艺商用车车架纵梁加工工艺方法比较

⼯艺商⽤车车架纵梁加⼯⼯艺⽅法⽐较欢迎阅读本篇⽂章,⽂末有福利哦!商⽤车车架纵梁产品结构特点纵梁与其他冲压件对⽐,其特点有以下⼏⽅⾯:(1)外形长、板料厚。
根据车型功能不同,纵梁长度范围⼤概为5~12m,厚度范围为4~10mm。
例如,牵引车车架纵梁长度⼀般在6~8m,载货⾃卸车架纵梁长度⼀般在8~12m。
(2)孔数多。
商⽤车80%以上的重要总成和部件在车架纵梁上进⾏装配。
例如,发动机、变速箱、车桥、驾驶室及外挂件等,纵梁孔数⼀般为200~400个。
(3)结构不复杂但精度要求⾼。
以U形结构为主,由于纵梁的孔和型⾯⼤部分都是装配孔、装配⾯,所以尺⼨精度要求⾼。
(4)材料强度⾼。
钢板屈服强度δs为500~700MPa。
商⽤车车架纵梁与内加强板⼀般有单层板、双层板、三层板三种主要结构形式,⼀般内加强板厚度都不⼤于纵梁厚度。
根据不同车型承载需要,配置不同层次和不同板厚的加强板。
按截⾯分类有等截⾯和变截⾯两种,按腹⾯分类有等直和弯曲两种,具体如图1所⽰。
图1 加强板形状分类商⽤车纵梁加⼯⼯艺⽅法传统冲压⼯艺⼤型压床结合模具进⾏冷冲压加⼯是国内主要卡车制造商初期⽣产纵梁采⽤的⽣产⼯艺,这种⽣产模式适⽤于品种少批量⼤的⽣产。
在60到90年代,卡车产品种类少,⽣产批量⼤,模具冲压⽣产的效率⾼、稳定性好,解放公司卡车⼚在2004年前⼀直采⽤此⼯艺⽣产纵梁。
加⼯⼯艺流程为:倍尺钢板→酸洗→模具落料冲孔→模具压弯。
其优点是:(1)单⼀品种⼤批量⽣产效率⾼。
(2)⽣产⾯积⼩,物流环节少。
(3)落料冲孔,外形尺⼨孔位精度⾼,⼀致性好。
(4)产品适应性较强,直槽纵梁和变截⾯纵梁都能⽣产。
缺点是:(1)模具投资⼤,制造周期长。
⼀套商⽤车纵梁落料冲孔模具和压弯模具共计约需要500万左右,模具的制造周期为8~12个⽉,在新产品准备时,⽆法满⾜快速投产的需要。
(2)倍尺料封闭落料材料利⽤率低。
在封闭落料冲孔时,双侧侧搭边值为30mm,对⽐净尺料每件重15kg左右,按⽉产1万辆计算,每⽉多产⽣废料近300t。
简析汽车车架纵梁试制工艺
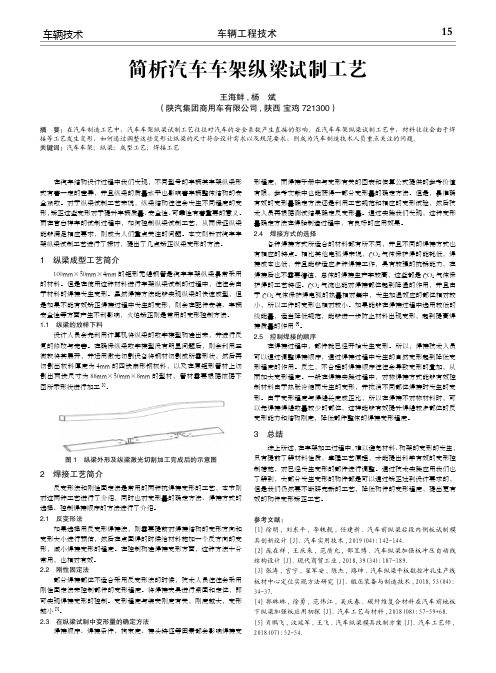
车辆工程技术15车辆技术 在汽车结构设计过程中我们发现,不同型号的车辆其车架纵梁形式有着一定的差异,并且纵梁的质量水平也影响着车辆整体结构的安全系数。
对于纵梁试制工艺来说,纵梁结构往往会发生不同程度的变形,矫正这些变形对于提升车辆质量、安全性、可靠性有着重要的意义。
而在首台样车的试制过程中,如何控制纵梁试制工艺,从而保证纵梁能够满足相应要求,则成为人们重点关注的问题。
本文则针对汽车车架纵梁试制工艺进行了探讨,提出了几点矫正纵梁变形的方法。
1 纵梁成型工艺简介 100mm×50mm×4mm 的矩形无缝钢管是汽车车架纵梁最常采用的材料。
但是在使用这种材料进行车架纵梁试制的过程中,往往会由于材料的焊接发生变形。
虽然焊接方法能够实现纵梁的快速成型,但是如果不能有效矫正焊接过程中发生的变形,则会在配件安装、车辆安全性等方面产生不利影响,火焰矫正则是常用的变形控制方法。
1.1 纵梁的放样下料 设计人员会先利用计算机将纵梁的数字模型构建出来,并进行反复的修改与完善。
在确保纵梁数字模型没有明显问题后,则会利用三微软将其展开,并运用激光切割设备将钢材切割成所需形状,然后再切割出板料厚度为4mm 的四块扇形钢板料,以及在原矩形管材上切割出两块尺寸为88mm×50mm×8mm 的型材,管材需要根据依据下图所示形状进行加工[1]。
简析汽车车架纵梁试制工艺王海鲜,杨 斌(陕汽集团商用车有限公司,陕西 宝鸡 721300)摘 要:在汽车制造工艺中,汽车车架纵梁试制工艺往往对汽车的安全系数产生直接的影响。
在汽车车架纵梁试制工艺中,材料往往会由于焊接等工艺发生变形,如何通过调整这些变形让纵梁的尺寸符合设计需求以及规范要求,则成为汽车制造技术人员重点关注的问题。
关键词:汽车车架;纵梁;成型工艺;焊接工艺2 焊接工艺简介 反变形法和刚性固定法是常用的两种抗焊接变形的工艺,本节则对这两种工艺进行了介绍,同时也对变形量的确定方法、焊接方式的选择、控制焊接顺序的方法进行了介绍。
汽车纵梁加工工艺及设备的选择

汽车纵梁加工工艺及设备的选择
苏向玲
【期刊名称】《汽车制造业》
【年(卷),期】2007(000)013
【摘要】汽车车架是汽车最重要的承载部件,而车架纵梁又是其中最关键的零件之一。
随着汽车工业的日益发展,汽车纵梁的数量和品种也在不断增加。
纵梁加工工艺、加工设备也在不断创新完善,合理地选择纵梁加工工艺及设备是汽车纵梁制造企业保持强劲竞争力的关键。
【总页数】3页(P67-68,74)
【作者】苏向玲
【作者单位】陕西重型汽车有限公司
【正文语种】中文
【中图分类】U463.326
【相关文献】
1.汽车V形扭梁的节能加工方法研究 [J], 董文彬;张雅晶;黄敏;张华;张新伟
2.汽车变速箱齿轮加工工艺及设备 [J], 陈鹏;舒义明
3.汽车桥壳机加工工艺及设备分析 [J], 丁叶;史俊领
4.汽车车架纵梁加工设备的选择 [J], 路永军
5.S14汽车纵梁数控钻铣床在纵梁加工工艺中的应用 [J], 付丽婕
因版权原因,仅展示原文概要,查看原文内容请购买。
- 1、下载文档前请自行甄别文档内容的完整性,平台不提供额外的编辑、内容补充、找答案等附加服务。
- 2、"仅部分预览"的文档,不可在线预览部分如存在完整性等问题,可反馈申请退款(可完整预览的文档不适用该条件!)。
- 3、如文档侵犯您的权益,请联系客服反馈,我们会尽快为您处理(人工客服工作时间:9:00-18:30)。
汽车纵梁加工工艺及设备的选择
陕西重型汽车有限公司(以下简称陕重)是一家以生产重型军用越野车、重型卡车、大客车为主的大型汽车公司。
为了提升公司汽车产能,更好地提高市场占有率,陕重在北郊成立了重卡产业园。
在产能目标大幅攀升的情况下,如何提升车架的生产能力,提高车架的产品质量,成为工艺人员亟待考虑的问题。
而随着我国汽车工业的飞速发展,客户个性化需求越来越多,各种变形车架层出不穷,传统的加工制造方法已不能满足上述要求。
传统加工工艺及存在的问题
汽车纵梁加工的内容主要包括:成形和制孔。
加工工艺可分为成型前加工孔和成型后加工孔,制孔的方式又分为冲孔加工和钻孔加工。
目前,陕重的汽车纵梁加工采用的是买成形纵梁料,通过摇臂钻床钻孔。
选用钻孔方式最大的优点是设备投资少,但缺点也很多:加工效率低、需要制造多种钻模,生产准备周期长,很难适应多品种、小批量多批次产品的生产节拍。
图1 传统纵梁加工方法
现在,随着陕重的斯太尔产品产能的大幅提升,同时MAN产品逐步上升为主导产品,传统的加工工艺已无法适应产能提升和产品变形的需求,纵梁孔位加工能力不足已成为车架生产的“瓶颈”问题,寻求新的纵梁加工工艺迫在眉睫。
因为斯太尔产品为等截面梁,MAN产品为变截面梁(见图2),这两种车架的纵梁结构不同,加工工艺差别较大,因此选择纵梁加工工艺和设备时应兼顾此两种产品结构的加工。
图2 斯太尔等截面梁、MAN变截面梁
常用加工工艺及所用设备
传统上车架纵梁成形和制孔可采用摇臂钻床钻孔的方法,但效率低、精度差、生产准备时间长,因此,此种加工方式已经被淘汰。
目前车架纵梁成形和制孔的主要方法有:
1、等截面汽车纵梁(斯太尔产品)的加工工艺及设备
(1)先制孔后成型的工艺:板料→数控平板冲孔→压力机成型;所用的主要设备:数控平板冲孔机、大吨位压力机。
(2)先成型后制孔的工艺:板料→压力机成型→数控三面冲冲孔;所用的主要设备:数控三面冲孔机、大吨位压力机。
(3)同时成形制孔的工艺:板料→大压机一次冲孔并成形;所用的主要设备:大吨位压力机。
2、变截面汽车纵梁(MAN产品)的加工工艺及设备
(1)大批量定型产品的生产工艺:板料→大型压力机一次冲孔成型;所用的主要设备:大型压力机。
(2)小批量、多批次纵梁加工工艺:
方法1:板料→数控平板冲冲孔→大型压力机成型;所用的主要设备:数控平板冲、大型压力机。
方法2:大压机成型→数控三面冲冲孔;所用的主要设备:大压机数控三面冲。
图3 陕重汽汽车大梁种类
加工工艺及所用设备的特点
目前,汽车纵梁加工工艺普遍采用了数控冲孔,汽车纵梁数控冲孔生产线的研制,改变了以往的加工工艺,提高了特殊梁的加工效率,具有较大的柔性,特别适合多品种、小批量的制造模式,可提高汽车制造厂的快速反应能力,增加了市场的竞争力,可产生较高的经济效益。
其特点如下:
1、生产效率高,劳动强度小
新产品生产准备时间短,对于纵梁孔的变化,生产准备仅为编程时间,输入CAD图形,可以自动生成加工程序,可以充分快速地满足市场和每个用户的要求,解决了现有摇臂钻床孔效率差、生产准备时间长、劳动强度低的问题。
采用原有方法,冲一个孔,带上下料最慢需要1.2s,钻一个孔最快需要10s。
当加工5595 mm长、200余孔的S35车纵梁时,5人需要14min,而采用数控冲只需4min。
加工1105 0mm长、350余孔O40车纵梁,5人需要28min,而采用数控冲加工350个孔只需8min。
2、产品质量高
数控冲加工解决了摇臂钻床钻孔时,漏孔和孔距尺寸超差而影响铆接和总装配进度及质量的问题,并且数控冲加工的孔没有毛刺,精度高于钻孔。
3、柔性化程度高
数控冲解决了传统钻孔方式所导致的孔加工能力不足的问题,而且对于不同车型纵梁孔的变化,生产准备时间仅仅是编程时间,缩短了新产品的开发周期,实现了产品由“单品种、大批量、少批次”向“多品种、小批量、多批次”转变,使精益生产得到推进和深化,为公司占领市场赢得了时间。
图4 大型压力机纵梁加工生产线
新工艺的选择和比较
基于冲孔加工的优点和特点,笔者认为,陕重的纵梁制孔工艺应该由钻孔加工改为冲孔加工,而纵梁加工工艺可使用3面数控冲、平板数控冲、大型压力机等设备。
现将3种冲孔加工方案分析如下:
1、采用平板数控冲
先制孔后成型,即平板数控冲+大型压力机的加工方法。
不用钻模及冲孔模,斯太尔等截面梁和MAN变截面梁都可以加工,无论从适用范围、加工的柔性等都是最佳的,而且,平板数控冲国内技术较成熟,完全可以满足加工工艺的需要。
2、采用三面数控冲
目前三面数控冲大致有两种形式:
(1)用于等截面加工的3面冲。
采用该方法可一次装卡完成纵梁上下翼面及腹面全部孔位的加工。
基本型为3个主机,由于汽车纵梁腹面上的孔径规格和数量占95%以上,翼面上的孔数极少,为了提高效率可做成4个主机,迅速提高车架生产能力。
其缺点是:MAN变截面梁不能加工,斯太尔产品(等截面)退出市场后限制使用。
(2)适用于等截面和变截面槽形梁的3面数控冲。
从加工范围看,选择1台5个主机的多功能3面冲,既可解决目前斯太尔等截面直梁制孔中产能、质量问题,也能兼顾将来MAN 变截面梁孔位加工的问题。
其缺点是:
□ 设备结构复杂,可靠性相对差,控制难度和价格相应增加;
□ 由于孔到纵梁翼面的距离小,数控冲冲模模座宽,倾斜翼面部分三角区内的个别孔不能冲,还需增加一步补孔工序,仍然没有解决一次加工完成所有纵梁孔的问题;
□ 冲位于倾斜翼面附近处的孔循环时间约增加2.5s,增加了冲一根纵梁的时间,影响生产节拍;
□ 从工艺流程分析,相比平板冲制孔加压力机成型的工艺,采用MAN产品变截面梁的先“成型”后“制孔”是将制孔由“易”便“难”。
3、采用大型压力机
将板料利用大型压力机直接进行冲孔并压形。
采用大型压力机,压形冲孔效率高,对于大批量的产品适用,但对于小批量、多批次的产品,由于大型压力机柔性不足,需要制造冲孔模,生产准备时间长,模具费用大,模具更换频繁,换模时间长,因此并不适合。
而陕重的产品多为小批量、多批次,所以,完全依靠大型压力机加工纵梁不适宜陕重的产品特点。
结论
通过以上对汽车纵梁加工工艺及设备的分析和对比,结合陕重汽车车架的年生产纲领和产品结构,本着投资合理的原则,笔者认为,对于陕重今后车架纵梁的成形和制孔,可按照以下方式进行:
1、板料——大型压力机成形冲孔(适用于大批量成熟车型)
2、板料——平板冲冲孔——大型压力机成型(适用于多品种、小批量、多批次车型)
此种加工方法,柔性高、效率高,既可生产等截面直大梁(斯太尔车型)又可生产变截面大梁(MAN车型),可满足年生产纲领。
适用于此加工工艺的设备有:平板数控冲、大型压力机。
车架是汽车最重要的承载部件,而车架纵梁又是其中的关键零件之一。
传统的加工车架纵梁的设备和生产工艺存在工艺性能不够好、产量低、尺寸精度差、长度调整不灵活以及容易冲裂板材和产品转型慢等缺点,陕重结合自身实际,寻找到了适合自己的加工工艺和相关设备,并将在今后的生产实践中不断更新和完善。