GBT 26492.3-2011 变形铝及铝合金铸锭及加工产品缺陷 第3部分:板、带缺陷
铝合金挤压工序中的主要缺陷分析及质量控制方法(DOC)
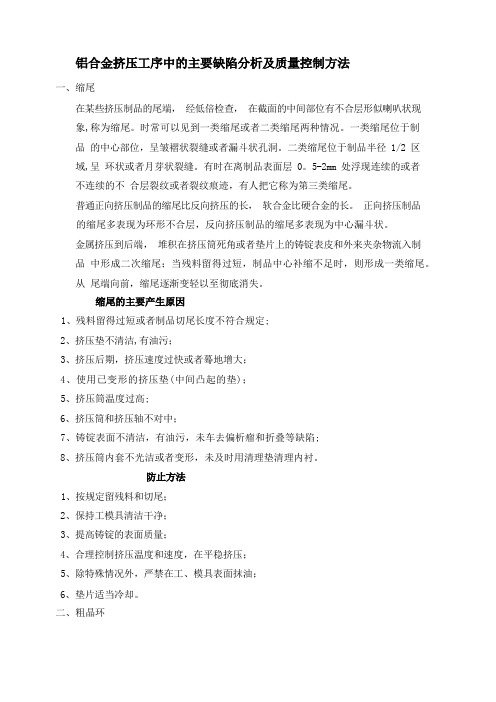
一、缩尾在某些挤压制品的尾端,经低倍检查,在截面的中间部位有不合层形似喇叭状现象,称为缩尾。
时常可以见到一类缩尾或者二类缩尾两种情况。
一类缩尾位于制品的中心部位,呈皱褶状裂缝或者漏斗状孔洞。
二类缩尾位于制品半径 1/2 区域,呈环状或者月芽状裂缝。
有时在离制品表面层 0。
5-2mm 处浮现连续的或者不连续的不合层裂纹或者裂纹痕迹,有人把它称为第三类缩尾。
普通正向挤压制品的缩尾比反向挤压的长,软合金比硬合金的长。
正向挤压制品的缩尾多表现为环形不合层,反向挤压制品的缩尾多表现为中心漏斗状。
金属挤压到后端,堆积在挤压筒死角或者垫片上的铸锭表皮和外来夹杂物流入制品中形成二次缩尾;当残料留得过短,制品中心补缩不足时,则形成一类缩尾。
从尾端向前,缩尾逐渐变轻以至彻底消失。
1、残料留得过短或者制品切尾长度不符合规定;2、挤压垫不清洁,有油污;3、挤压后期,挤压速度过快或者蓦地增大;4、使用已变形的挤压垫(中间凸起的垫);5、挤压筒温度过高;6、挤压筒和挤压轴不对中;7、铸锭表面不清洁,有油污,未车去偏析瘤和折叠等缺陷;8、挤压筒内套不光洁或者变形,未及时用清理垫清理内衬。
1、按规定留残料和切尾;2、保持工模具清洁干净;3、提高铸锭的表面质量;4、合理控制挤压温度和速度,在平稳挤压;5、除特殊情况外,严禁在工、模具表面抹油;6、垫片适当冷却。
二、粗晶环有些铝合金的挤压制品在固溶处理后的低倍试片上,沿制品周边形成粗大再结晶晶粒组织区,称为粗晶环.由于制品外形和加工方式不同,可形成环状、弧状及其他形式的粗晶环。
粗晶环的深度同尾端向前端逐渐减小以至彻底消失。
期形成机理是由热挤压后在制品表层形成的亚晶粒区,加热固溶处理后形成粗大的再结晶晶粒区。
1、挤压变形不均匀‘2、热处理温度过高,保温时间过长,使晶粒长大;3、便金化学成份不合理;4、普通的可热处理强化合金经热处理后都有粗晶环产生,特别是 6A02,2A50 等合金的型、棒材最为严重,不能消除,只能控制在一定范围内 ;5、挤压变形小或者变形不充分,或者处于临界变形范围,易产生粗晶环。
变形铝及铝合金铸锭及加工产品缺陷 第4部分:铝箔缺陷
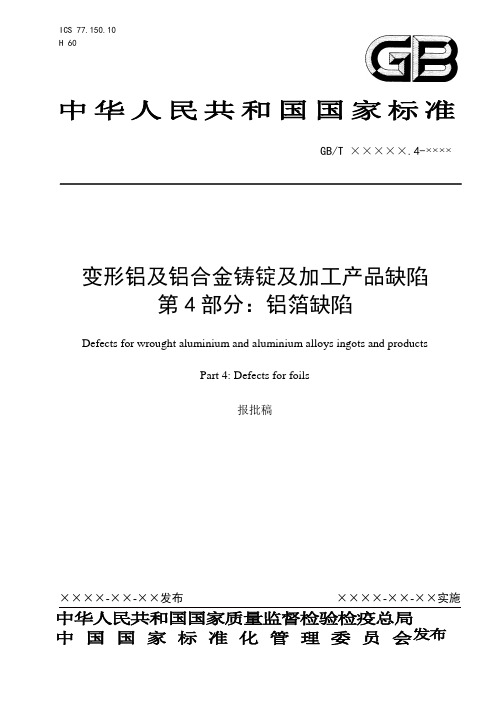
第4部分:铝箔缺陷
11
本部分规定了变形铝及铝合金箔材常见缺陷的定义、特征,并分析了其主要产生原因。
本部分适用于变形铝及铝合金箔材缺陷的分析与判定。
12
非金属压入
非金属夹杂压入箔材表面,表面呈明显的点状或长条状黄黑色缺陷(如图1)。
主要产生原因:
a)生产设备或环境不洁净;
我
1
GB/T XXXXX《变形铝及铝合金铸锭及加工产品缺陷》分为5个部分:
——第1部分 铸锭缺陷
——第2部分 铸轧带材缺陷
——第3部分 板、带缺陷
——第4部分 铝箔缺陷
——第5部分 管材、棒材、型材、线材缺陷
本部分为GB/T XXXXX的第4部分。
本部分由全国有色金属标准化技术委员会(SAC/TC243)归口。
b)轧辊表面粗糙度过高或轧辊表面有缺陷;
c)轧制油不够清洁;
d) 来料表面擦划伤;
e)轧制工艺参数不当;
e)生产环境不洁净。
图16针孔
开缝
铝箔经轧制后沿纵向自然开裂的现象。
主要产生原因:
a)轧制时后张力过小;
b)来料板型不良;
c)辊型控制不当;
d) 坯料存在气道;
f)入口侧打折或来料打折。
皱纹
铝箔表面呈现的细小的、纵向或斜向局部凸起的、一条或数条圆滑的沟槽(如图17)。
本部分负责起草单位:华北铝业有限公司。
本部分参加起草单位:厦门厦顺铝箔有限公司、云南新美铝铝箔有限公司、中国铝业西北铝加工分公司、中铝瑞闽铝板带有限公司、广东东阳光铝业股份有限公司、郑州铝业股份有限公司、东北轻合金有限责任公司、江苏常铝铝业股份有限公司。
本部分主要起草人:关世彤、卜长海、曹建峰、高珺、张丽华、段瑞芬、张深阳、郭义庆、林圣豪、佟颖、吴欣凤、金雯辉、马美珍、孔祥鹏。
铝合金压铸件所有缺陷及对策大全

铝合金压铸件所有缺陷及对策大全一、化学成份不合格主要合金元素或杂质含量与技术要求不符,在对试样作化学分析或光谱分析时发现。
1、配料计算不正确,元素烧损量考虑太少,配料计算有误等;2、原材料、回炉料的成分不准确或未作分析就投入使用;3、配料时称量不准;4、加料中出现问题,少加或多加及遗漏料等;5、材料保管混乱,产生混料;6、熔炼操作未按工艺操作,温度过高或熔炼时间过长,幸免于难烧损严重;7、化学分析不准确。
对策:1)、对氧化烧损严重的金属,在配料中应按技术标准的上限或经验烧损值上限配料计算;配料后并经过较核;2)、检查称重和化学分析、光谱分析是否正确;3)、定期校准衡器,不准确的禁用;4)、配料所需原料分开标注存放,按顺序排列使用;5)、加强原材料保管,标识清晰,存放有序;6)、合金液禁止过热或熔炼时间过长;7)、使用前经炉前分析,分析不合格应立即调整成分,补加炉料或冲淡;8)、熔炼沉渣及二级以上废料经重新精炼后掺加使用,比例不宜过高;9)、注意废料或使用过程中,有砂粒、石灰、油漆混入。
二、气孔铸件表面或内部出现的大或小的孔洞,形状比较规则;有分散的和比较集中的两类;在对铸件作X光透视或机械加工后可发现。
1、炉料带水气,使熔炉内水蒸气浓度增加;2、熔炉大、中修后未烘干或烘干不透;3、合金液过热,氧化吸气严重;4、熔炉、浇包工具氧等未烘干;5、脱模剂中喷涂过重或含发气量大;6、模具排气能力差;7、煤、煤气及油中的含水量超标。
对策:1)、严禁把带有水气的炉料装入炉中,装炉前要在炉边烘干;2)、炉子、坩埚及工具未烘干禁止使用;3)、注意铝液过热问题,停机时间要把炉调至保温状态;4)、精炼剂、除渣剂等未烘干禁止使用,使用时禁止对合金液激烈搅拌;5)、严格控制钙的含量;6)、选用挥发性气体量小的脱模剂,并注意配比和喷涂量要低;7)、未经干燥的氯气等气体和未经烘干的氯盐等固体不得使用。
三、涡流孔铸件内部的细小孔洞或合金液流汇处的大孔洞。
铸造铝合金热处理质量缺陷及其消除与预防
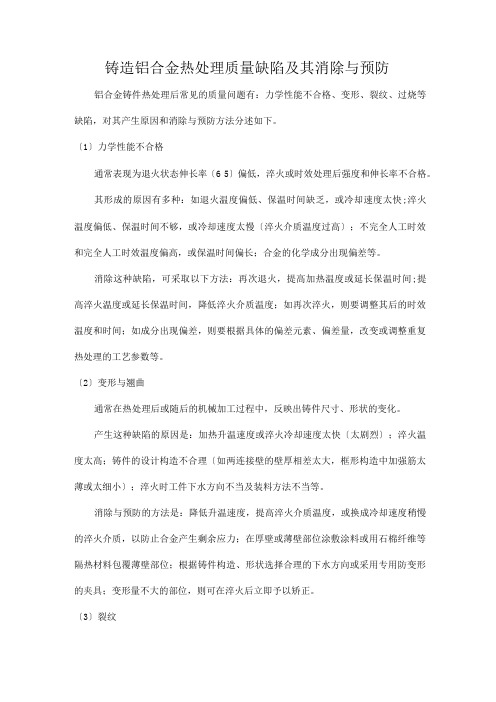
铸造铝合金热处理质量缺陷及其消除与预防铝合金铸件热处理后常见的质量问题有:力学性能不合格、变形、裂纹、过烧等缺陷,对其产生原因和消除与预防方法分述如下。
〔1〕力学性能不合格通常表现为退火状态伸长率〔6 5〕偏低,淬火或时效处理后强度和伸长率不合格。
其形成的原因有多种:如退火温度偏低、保温时间缺乏,或冷却速度太快;淬火温度偏低、保温时间不够,或冷却速度太慢〔淬火介质温度过高〕;不完全人工时效和完全人工时效温度偏高,或保温时间偏长;合金的化学成分出现偏差等。
消除这种缺陷,可采取以下方法:再次退火,提高加热温度或延长保温时间;提高淬火温度或延长保温时间,降低淬火介质温度;如再次淬火,则要调整其后的时效温度和时间;如成分出现偏差,则要根据具体的偏差元素、偏差量,改变或调整重复热处理的工艺参数等。
〔2〕变形与翘曲通常在热处理后或随后的机械加工过程中,反映出铸件尺寸、形状的变化。
产生这种缺陷的原因是:加热升温速度或淬火冷却速度太快〔太剧烈〕;淬火温度太高;铸件的设计构造不合理〔如两连接壁的壁厚相差太大,框形构造中加强筋太薄或太细小〕;淬火时工件下水方向不当及装料方法不当等。
消除与预防的方法是:降低升温速度,提高淬火介质温度,或换成冷却速度稍慢的淬火介质,以防止合金产生剩余应力;在厚壁或薄壁部位涂敷涂料或用石棉纤维等隔热材料包覆薄壁部位;根据铸件构造、形状选择合理的下水方向或采用专用防变形的夹具;变形量不大的部位,则可在淬火后立即予以矫正。
〔3〕裂纹表现为淬火后的铸件外表用肉眼可以看到明显的裂纹,或通过荧光检查肉眼看不见的微细裂纹。
裂纹多曲折不直并呈暗灰色。
产生裂纹的原因是:加热速度太快,淬火时冷却太快〔淬火温度过高或淬火介质温度过低,或淬火介质冷却速度太快〕;铸件构造设计不合理〔两连接壁壁厚差太大,框形件中间的加强筋太薄或太细小〕;装炉方法不当或下水方向不对;炉温不均匀,使铸件温度不均匀等。
消除与预防的方法是:减慢升温速度或采取等温淬火工艺;提高淬火介质温度或换成冷却速度慢的淬火介质;在壁厚或薄壁部位涂敷涂料或在薄壁部位包覆石棉等隔热材料;采用专用防开裂的淬火夹具,并选择正确的下水方向。
金属件缺陷检查规范标准

1.范围本规范规定了有关锐边、毛边、倒圆半径、V形裂痕、凹痕和外观清洁度的术语及可接受的标准。
本标准适用于康明斯(COMMINS)所有的成品金属零件和耐用组件。
2.适用文件下列适用文件可从列入CES 10054,标准化组织地址,的相关组织处获得。
a. CES 10054 ,标准化组织地址b. CES 10056 ,通用术语汇编3.定义在本标准中使用的术语以及在康明斯(COMMINS)技术标准中作为通用定义使用的术语均被定义在CES 10056 ,通用术语汇编中。
3.1锐边锐边是由二个面相交形成的边缘。
3.2毛边毛边是在表面的边缘上材料的突出部分,这是由于对材料的搬运、成形、下料和剪切等造成的。
3.3倒圆半径倒圆半径是一种画法引伸。
它规定了与孔或洞相交的进入棱必须采用砂纸、砂布片,砂轮或螺旋滚轮倒圆。
3.4 V形裂痕V形裂痕是表面上浅薄的V形凹痕或凹槽,其来自于非正常的加工或操作。
这种裂痕的边缘可能凸出相邻表面。
3.5凹痕凹痕是表面上深的V形凹痕或凹槽,其来自于非正常的加工或操作。
这种凹痕的边缘可能凸出相邻表面。
术语凹痕通常适用于应力集中器的缺陷。
3.6缺陷缺陷具有非正常的不规则性和不连续性,在表面上随机产生。
它包括毛边、V形裂痕、凹痕以及破裂、刮伤、气泡等。
除非另有规定,缺陷的影响不包括在平均粗糙度测量中。
▲3.7外观清洁度在合适光照下对非隐蔽表面进行肉眼检查的外观状态。
4.允限除非在图纸上另有规定,或对特殊类型的成品零件或耐用组件有其它检查标准,下列允限都是适用的。
4.1规定的锐边当在图纸上规定锐边时,允限应是在一条界线上无毛边,在另一条界线上最大倒棱,即为0.005。
(参考图A1:第4页的锐边)4.2规定的倒圆半径(参考图A2:第4页的倒圆半径)4.3毛边去除4.3.1功能表面除非另有规定,使用任何可产生0.005至于0.015英寸倒棱或倒圆的方法,在下列表面上,必须去除所有毛边以及必须倒纯所有锐边。
变形铝及铝合金板带材缺陷
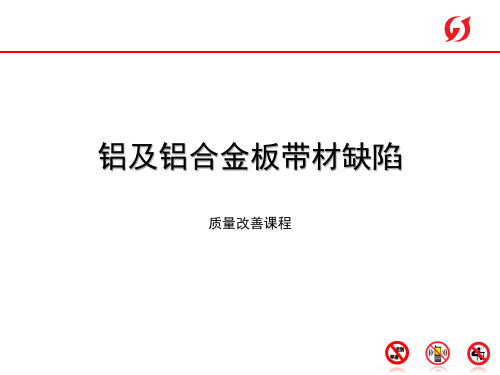
二、表面质量缺陷
横波【★★☆☆☆】
定义及特征
主要产生原因
影响
缺陷分级
涉及方面
主要影响产品
备注
垂直压延方向横贯板、带材表面的 波纹,波纹处厚度突变
a) 轧制过程中中间停机,或较快调整 压下量; 厚度公差超标 b) 精整时多辊矫直机在有较大压下量 无法使用 的情况下矫直时中间停车。
C
下道工序/顾 客反馈
涉及的方 面 缺陷分级
错装漏装 会引起难 一般外观 影响安全给使用者 必然会 会造成产 肯定造成 零部件, 肯定会造 致命缺陷 以纠正的 会影响寿 缺陷构不 影响关键 的所有缺 带来危险, 造成产 不涉及 品安装的 下道工序 装配不牢, 成顾客投 (A级) 非正常情 命 成致命缺 特性 陷 无法使用 品故障 困难 的混乱 在运输途 诉的 况 陷 中损坏 对下道工 某些性能 对产品外 错装漏装 可能会造 可能会 可能引起 序影响较 上严重偏 肯定会造 可能会影 观影响较 一般紧固 成顾客投 严重缺陷 引起易 易于纠正 可能影响 大或给下 影响重要 不涉及 离规定要 成装配困 响产品安 大或使产 件,用户 诉,一定 (B级) 于修复 的异常情 寿命 道工序造 特性 求,适用 难 装的顺利 品外观难 可自己解 会造成顾 的故障 况 成较大困 性下降 于接受 决 客抱怨 难 某些性能 可能影响 顾客可能 虽不符合 对产品外 不会成 装配的顺 对下道工 会抱怨或 一般缺陷 要求,但 不会影响 基本不影 观略有影 影响次要 不涉及 为故障 不影响 利进行, 序略有影 不涉及 有意见, (C级) 几乎不影 运行 响安装 响,但可 特性 的起因 但可以修 响 但不会提 响产品使 以接收 复 出的 用
备注
a) 热处理工艺不当; b) 热处理设备及仪表运转不正常。
变形铝及铝合金牌号_状态新国家标准简介
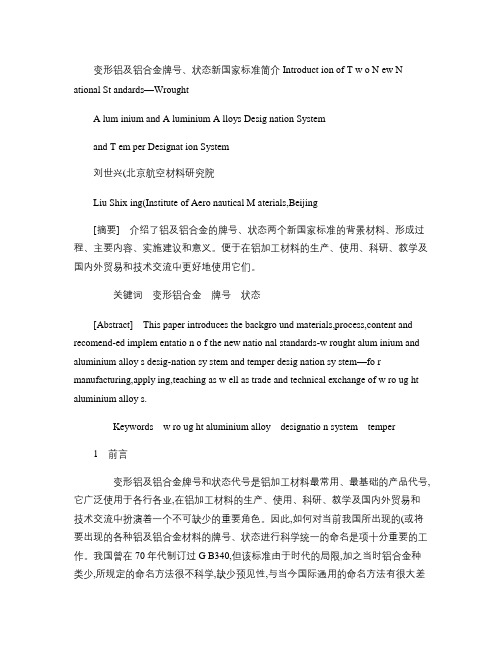
变形铝及铝合金牌号、状态新国家标准简介Introduct ion of T w o N ew N ational St andards—WroughtA lum inium and A luminium A lloys Desig nation Systemand T em per Designat ion System刘世兴(北京航空材料研究院Liu Shix ing(Institute of Aero nautical M aterials,Beijing[摘要]介绍了铝及铝合金的牌号、状态两个新国家标准的背景材料、形成过程、主要内容、实施建议和意义。
便于在铝加工材料的生产、使用、科研、教学及国内外贸易和技术交流中更好地使用它们。
关键词变形铝合金牌号状态[Abstract]This paper introduces the backgro und materials,process,content and recomend-ed implem entatio n o f the new natio nal standards-w rought alum inium and aluminium alloy s desig-nation sy stem and temper desig nation sy stem—fo r manufacturing,apply ing,teaching as w ell as trade and technical exchange of w ro ug ht aluminium alloy s.Keywords w ro ug ht aluminium alloy designatio n system temper 1前言变形铝及铝合金牌号和状态代号是铝加工材料最常用、最基础的产品代号,它广泛使用于各行各业,在铝加工材料的生产、使用、科研、教学及国内外贸易和技术交流中扮演着一个不可缺少的重要角色。
国家标准《变形铝及铝合金铸锭及其加工产品缺陷 第6部分:阳极氧化膜或有机聚涂层缺陷》编制说明(预审稿)
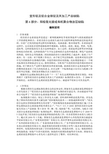
变形铝及铝合金铸锭及其加工产品缺陷第6部分:阳极氧化膜或有机聚合物涂层缺陷编制说明1任务来源铝及铝合金表面处理是通过一系列机械和化学表面预处理与表面成膜处理工序的搭配和组合,在铝及铝合金表面生成具有功能性和装饰性涂层的处理过程。
目前广泛使用的处理过程有阳极氧化、电泳涂漆、粉末喷涂等。
在表面处理过程中,会出现很多的性能缺陷和外观缺陷,如粉化、流痕、橘皮、黑斑、龟裂、疏松等。
这些缺陷的发生是合金材料成分、加工过程、表面处理过程等多种因素影响综合的结果。
这些缺陷的产生不仅会影响铝合金的外观质量,降低产品的使用性能,有时还会导致报废。
因而缺陷的存在大幅度降低了成品率,提高了生产成本。
另一方面,对于检测工作而言,由于缺乏判定的标准,也很难对现实过程中发生的缺陷作出准确的判断,并提供相应的应对措施。
而如果能够建立一个相关标准对各种缺陷进行定义,指明其特征,分析其产生的原因并提供相应的应对措施,对于解决生产过程中遇到的各种质量问题,提高铝及铝合金表面处理产品的整体质量就有了很大的现实意义。
并且这样一个标准的建立还可以为检测工作提供判定依据,同时添补国标在此方面的空白。
根据有色金属标准化委员会的“十一五”有色金属国家标准项目规划,本标准属于《变形铝及铝合金铸锭及其加工产品缺陷》标准的第6部分,于2008年开始制定,由国家有色金属质量监督检验中心、福建南平铝业公司负责起草。
2工作简况根据全国有色金属标准化委员会的总体安排,国家有色金属质量监督检验中心首先提出了“铝及铝合金表面处理缺陷”标准的项目建议书,并由福建南平铝业公司起草了“铝及铝合金表面处理缺陷”标准的草案稿。
标准批准立项后,制定工作首先从文献、资料调研和样品收集开始。
首先收集了国内外的相关参考文献包括“铝阳极氧化技术——缺陷成因和对策”、“铝及铝合金挤压型材缺陷事例及其对策”、“铝阳极氧化电泳涂装膜的缺陷汇编(日本轻金属制品协会表面处理技术委员会)”、“YS/T 417.5-2000|变形铝及铝合金铸锭及其加工产品缺陷第5部分管、棒、型、线缺陷”等。
变形铝及铝合金铸锭及加工产品缺陷 第4部分:铝箔缺陷
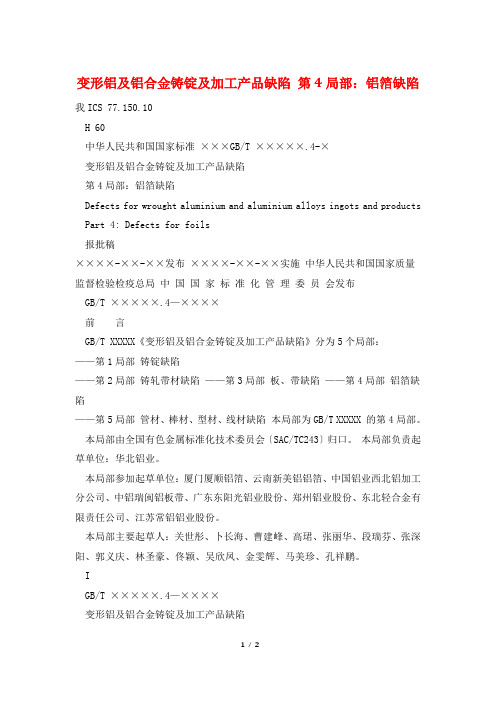
变形铝及铝合金铸锭及加工产品缺陷第4局部:铝箔缺陷我ICS 77.150.10H 60中华人民共和国国家标准×××GB/T ×××××.4-×变形铝及铝合金铸锭及加工产品缺陷第4局部:铝箔缺陷Defects for wrought aluminium and aluminium alloys ingots and products Part 4: Defects for foils报批稿××××-××-××发布××××-××-××实施中华人民共和国国家质量监督检验检疫总局中国国家标准化管理委员会发布GB/T ×××××.4—××××前言GB/T XXXXX《变形铝及铝合金铸锭及加工产品缺陷》分为5个局部:——第1局部铸锭缺陷——第2局部铸轧带材缺陷——第3局部板、带缺陷——第4局部铝箔缺陷——第5局部管材、棒材、型材、线材缺陷本局部为GB/T XXXXX 的第4局部。
本局部由全国有色金属标准化技术委员会〔SAC/TC243〕归口。
本局部负责起草单位:华北铝业。
本局部参加起草单位:厦门厦顺铝箔、云南新美铝铝箔、中国铝业西北铝加工分公司、中铝瑞闽铝板带、广东东阳光铝业股份、郑州铝业股份、东北轻合金有限责任公司、江苏常铝铝业股份。
本局部主要起草人:关世彤、卜长海、曹建峰、高珺、张丽华、段瑞芬、张深阳、郭义庆、林圣豪、佟颖、吴欣凤、金雯辉、马美珍、孔祥鹏。
IGB/T ×××××.4—××××变形铝及铝合金铸锭及加工产品缺陷第4局部:铝箔缺陷1 范围本局部规定了变形铝及铝合金箔材常见缺陷的定义、特征,并分析了其主要产生原因。
铝材检验标准

铝材检验标准 The document was finally revised on 2021广东唐氏集团铝型材检验标准第一章总则第一条为了规范公司铝型材检验标准,控制型材生产工艺以及成品出厂质量,规避市场风险,提升品牌形象,特制定本章。
第二条本标准规定了铝型材的技术标准、外观质量、检验方法。
本标准适用于建筑铝型材。
第三条本标准以GB5237-2008为基准拟定。
第四条公司旗下“永兴”、“亚阳”、“兴铝”三个品牌均以此标准为检验标准。
第五条涉及到商标方面的各项要求,应完全符合《商标法》、《广告法》、《反不正当竞争法》、《知识产权保护法》等法律、法规要求。
第二章基材第六条本部分规定了未经表面处理的铝合金建筑型材的要求、试验方法、检验规则、标识及合同(或订货单)内容。
第七条本部分适用于表面未经处理的建筑用铝合金热挤压型材(以下简称型材)。
第八条术语定义基材是指表面未经处理铝合金建筑型材。
装饰面是指型材经加工、制作并安装在建筑物上后,处于开启和关闭状态时,仍可看的见的表面。
外接圆是指能够将型材的横截面完全包围的最小的圆。
第九条基材(坯料)相关技术指标及外观要求,见下表:一) 长度要求定尺时,应在合同中注明,公称长度≤6m 时,允许偏差为﹢15mm;长度>6m时,允许偏差由双方协商决定。
(二) 以倍尺交货的型材,其总长度允许偏差为+20mm,需要加锯口余量时,应在合同中注明。
(三) 端头斜切度不应超过2°。
第十条力学性能取样部位的公称壁厚<时,不测定断后伸长率。
室温力学性能要求如下第十一条试验方法(一) 化学成分分析可采用化学分析法和仪器分析法等方法进行,化学成分仲裁分析按照GB/T 20975规定的方法进行。
(二) 力学性能拉伸试验按照GB/T 228-2002规定的方法进行,断后伸长率按照GB/T 228-2002中的条仲裁;维氏硬度试验按GB/T 规定的方法进行;韦氏硬度试验按YS/T 420规定的方法进行。
变形铝及铝合金热处理规范

变形铝及铝合金热处理规范ICS YS中华人民共和国有色金属行业标准YS/T ××××—×××× 变形铝及铝合金热处理规范 Wrought aluminium and aluminium alloys heat treatment (送审稿)××××—××—××发××××—××—××实全国有色标准化技术委员会发布YS/T ××××—×××× 目次前言 ..................................................................... .......... II1 范围 ..................................................................... ......... 12 规范性引用文件 ....................................................................13 定义 ................................................................. ............. 13.1 热处理.................................................................. ......... 13.2 热处理批次.................................................................. ..... 13.3 工作区.................................................................. ......... 13.4 固溶热处理造成的砂眼和气孔 ....................................................... 14 要求 ................................................................. ............. 24.1 建立工艺操作规程和工艺操作规程重新审定 ........................................... 24.2 定期工艺制度检查................................................................. 24.3 定期产品监测.................................................................. ... 24.4 热处理设备.................................................................. ..... 24.5 固溶热处理参数及工艺规程......................................................... 44.6 淬火参数和工艺规程............................................................... 84.7 装架和间距.................................................................. ..... 94.8 建议时效热处理.................................................................. 104.9 推荐的退火工艺.................................................................. 185 质量保证措施 ................................................................. .... 185.1 检查责任.................................................................. ...... 185.2 热处理设备的温度检??........................................................... 195.3 喷水淬火设备.................................................................. .. 195.4 产品定期监测.................................................................. .. 215.5 测试方法.................................................................. ...... 235.6 试验结果的判定.................................................................. 245.7 锻件的热处理批号................................................................ 25附录 A (资料性附录) 铝合金热处理常用知识 ......................................... 26A.1 盐浴槽的优点 ................................................................. .. 26A.2 气室炉的优点 ................................................................. .. 26A.3 固溶热处理 ................................................................. .... 26A.4 用于提高抗腐蚀能力的淬火 ....................................................... 27A.5 合金和状态代号 ................................................................. 27A.6 包铝板 ................................................................. ........ 27A.7 退火处理 ................................................................. ...... 27A.8 时效 ................................................................. .......... 27A.9 残余拉应力对腐蚀性能的影响 ..................................................... 28A.10 电导率、硬度和状态的关系 ......................................................28 IYS/T ××××—×××× 前言本标准首次制定。
铝合金压铸模的模具寿命

铝合金压铸模的模具寿命铝合金压铸模承受巨大交变工作应力,必须从模材,设计,加工,热处理及操作各方面加以注意才能得到长的模具寿命,以下是为使模具能达长寿命的22点要诀:1、高品质模材2、合理设计模壁厚及其它模具尺寸3、尽量采用镶件4、在可能条件下选用尽量大的转角R5、冷却水道与型面及转角的间距必须足够大6、粗加工后应去应力回火7、正确有热处理,淬火冷却须足够快8、彻底打磨去除EDM娈质层9、型面不可高度抛光10、模具型面应经氧化处理11、如选氮化,渗层不能太深12、以正确的方法预热模具至推荐的温度13、开始压铸5~10件应使用慢的锤头速度14、在得到合格产品的前提下尽量降低铝液温度15、不使用过高的铝液注射速度16、确保模具得到适当冷却,冷却水的温度应保持在40~50℃17、临时停机,应尽量合模并减小冷却水量,避免再开机时模具承受热冲击18、当模型面在最高温度时应关冷却液19、不过多的喷脱模剂20、在一定数量后的压铸后去应力回火压铸标准目录一、通用标准中国GB/T24001-1996 idt ISO 14001:1996 环境管理体系规范及使用指南GB/T19001-2000 idt ISO/FDIS9001:2000 质量管理体系––要求GB/T5611-1998铸造术语HB7578-1997铸件试制定型规范GB/T8063-94 铸造有色金属及其合金牌号表示方法GB/T13822-92 压铸有色合金试样GB5678-85 铸造合金光谱分析取样方法HB5343-94 铸造工艺质量控制GB/T6414-1999 铸件尺寸公差及机械加工余量GB/T15056-94 铸造表面粗糙度评定方法二、压铸机标准中国JB/T8083-1999 压铸机型式与基本参数JB/T8084.1-1999 冷室压铸机精度JB/T8084.2-1999 冷室压铸机技术条件JB/T6039.2-92 热室压铸机精度JB/T6039.3-92 热室压铸机技术条件三、压铸模标准中国GB8844-88 压铸模技术条件GB8847-88 压力铸造模具术语GB4678.1~15-84 压铸模零件GB4679-84 压铸模零件技术条件四、合金及工艺标准1. 铝合金中国GB/T1173-95 铸造铝合金GB/T8733-2000 铸造铝合金锭YS/T282-2000 铝中间合金锭JB/T7946.1-1999 铸造铝硅合金变质JB/T7946.2-1999 铸造铝硅合金过烧JB/T7946.3-1999 铸造铝合金针孔GB/T15115-94 压铸铝合金GB/T15114-94 铝合金压铸件HB5012-86 铝合金压铸件HB/Z220.2-92 铝合金金属型铸造HB/Z220.3-92 铝合金低压铸造HB/Z220.4-92 铝合金压力铸造HB/Z220.7-92 铝合金铸件浸渗GJB1695-93 铸造铝合金热处理规范国际标准 ISO3522-84 铸造铝合金ASTMB179-96 砂型铸件、永久型铸件及压铸件用铝合金锭ASTMB597-98 铝合金热处理JISH5302:2000 铝合金压铸件2. 镁合金中国GB1177-91 铸造镁合金GB/T13820-92 镁合金铸件国际标准IS O/DIS16220-1999 铸造镁合金ASTMB94-94 镁合金压铸件JISH5303-1991 镁合金压铸件3. 锌合金中国GB/T1175-1997 铸造锌合金GB/T13818-92 压铸锌合金GB/T13821-92 锌合金压铸件国际标准IS O301-1981 铸造用锌合金锭ASTMB240-98 压铸件用锌合金锭ASTMB327-98 压铸锌合金用铝中间合金JISH2021:1999 压铸用锌合金锭EN 12844:1998 锌和锌合金-铸件-规格五、铜合金中国GB1176-87 铸造铜合金技术条件GB/T15116-94 压铸铜合金GB/T15117-94 铜合金压铸件5. 铅锡合金中国GB/T8740-1988 铸造铅基轴承合金锭GB/T8740-1988 铸造锡基轴承合金锭JISH5601-1990 硬铅铸件JISH5401-1958 轴承合金DIN1741-1974 压铸用铅合金常見鋅合金成分鋅合金種類合金代號商業習用編號No.3 No.5 No.2 No.7ASTM AG40AAC41A-- --UNS Z33251 Z35530 -- Z33522SAE 903 925 921 --機械性質Die Cast Aged Die Cast Aged Die Cast Aged Die Cast Aged抗拉強度(Kg/mm2) 28.8 24.6 33.7 27.42 36.4 33.6 28.7 24.5降伏強度(Kg/mm2) -- -- -- -- -- -- -- --伸長率(%) 10 16 7 13 7 2 13 18剪切強率(Kg/mm2) 21.8 -- 26.7 -- 32.3 -- 21.8 --硬度(勃式) 82 72 91 80 100 98 80 67衝擊強度(J) 30.2 28.8 33.7 28.1 24.6 3.5 30.2 28.8疲勞強度(Kg/mm2,5%103 4.85 -- 5.76 -- 5.98 -- 4.78 --壓強度(Kg/mm2) 42 -- 60.9 42 -- 21.7 -- 65.1成份錠鑄件錠鑄件錠錠鑄件Al 3.9~4.3 3.5~4.3 3.9~4.3 3.5~4.3 3.9~4.3 3.9~4.3 3.5~4.3Mg .025~.50 .02~.05 .03~.06 .03~.08 .025~.50 .01~.02 .005~.020Cu .10max.25max075~1.25 .75~1.25 2.6~2.9 .10max.25maxFe .075 .10 .075 .10 .075 .075 .075Pb .004 .005 .004 .005 .004 .002 .003Cd .003 .004 .003 .004 .003 .002 .002Sn .002 .003 .002 .003 .002 .001 .001Ni -- -- -- -- -- .005~.002 .005~.002Zn 餘餘餘餘餘餘餘物性密度g/cm3 6.64 6.64 6.64 6.64熔解溫度˚C 382~387 381~386 379~390 381~387導電係數(%ACS) 27 26 25 27熱傳導係數(W/M˚K) 113 109 105 113熱膨脹係數(20~100˚C)(µm/m˚k) 27.36 27.36 27.72 27.36比熱kg˚C 0.419 0.419 0419 0.419收縮率6/1000 6/1000 6/1000 6/1000点击浏览该文件压铸模简介一、常用压铸合金成分和性能压铸合金成份有有色金属和黑色金属,广泛彩的有色金属合金分类如下:铅合金低熔点合金锡合金锌合金有色金属合金铝合金高熔点合金镁合金铜合金二、压铸件结构的工艺性1、壁厚〈1〉压铸件的最小壁厚与正常壁厚通常根据铸件面积而言。
铝及铝合金挤压型材尺寸偏差国家标准编制说明
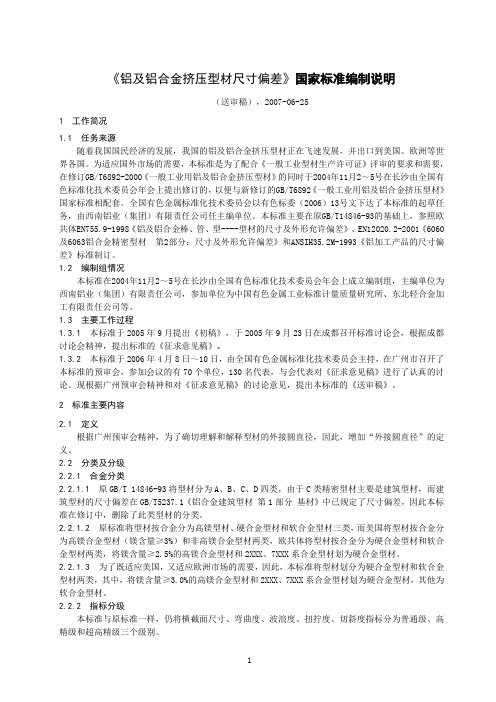
《铝及铝合金挤压型材尺寸偏差》国家标准编制说明(送审稿),2007-06-251 工作简况1.1 任务来源随着我国国民经济的发展,我国的铝及铝合金挤压型材正在飞速发展,并出口到美国、欧洲等世界各国。
为适应国外市场的需要,本标准是为了配合《一般工业型材生产许可证》评审的要求和需要,在修订GB/T6892-2000《一般工业用铝及铝合金挤压型材》的同时于2004年11月2~5号在长沙由全国有色标准化技术委员会年会上提出修订的,以便与新修订的GB/T6892《一般工业用铝及铝合金挤压型材》国家标准相配套。
全国有色金属标准化技术委员会以有色标委(2006)13号文下达了本标准的起草任务,由西南铝业(集团)有限责任公司任主编单位。
本标准主要在原GB/T14846-93的基础上,参照欧共体EN755.9-1998《铝及铝合金棒、管、型----型材的尺寸及外形允许偏差》、EN12020.2-2001《6060及6063铝合金精密型材第2部分:尺寸及外形允许偏差》和ANSIH35.2M-1993《铝加工产品的尺寸偏差》标准制订。
1.2 编制组情况本标准在2004年11月2~5号在长沙由全国有色标准化技术委员会年会上成立编制组,主编单位为西南铝业(集团)有限责任公司,参加单位为中国有色金属工业标准计量质量研究所、东北轻合金加工有限责任公司等。
1.3 主要工作过程1.3.1 本标准于2005年9月提出《初稿》,于2005年9月23日在成都召开标准讨论会,根据成都讨论会精神,提出标准的《征求意见稿》。
1.3.2 本标准于2006年4月8日~10日,由全国有色金属标准化技术委员会主持,在广州市召开了本标准的预审会,参加会议的有70个单位,130名代表,与会代表对《征求意见稿》进行了认真的讨论。
现根据广州预审会精神和对《征求意见稿》的讨论意见,提出本标准的《送审稿》。
2 标准主要内容2.1 定义根据广州预审会精神,为了确切理解和解释型材的外接圆直径,因此,增加“外接圆直径”的定义。
BS规范标准-精密铸钢和精密铸造合金规范标准

目录序号名称页码1.BS 3146 Part1-1992 精密铸钢和精密铸造合金 (2)2.BS 3146 Part21992耐蚀、耐热精密铸钢和NiCo基精密铸造合金的钢号与化学成分[再确认] (2)3.BS 3100 Part 4-1991耐蚀、耐热和高合金铸钢 (4)4.BS EN 102132-1995承压铸钢 (6)5.BS EN 102133-1995低温用承压铸钢 (6)6.BS EN 102134-1995奥氏体型和奥氏体铁素体型承压铸钢 (7)7.KS D4103-1995不锈、耐蚀铸钢韩国标准 (9)8.JB/T 6405-1992中国标准大型铸件用不锈铸钢 (10)9.GB/T 2100-1980不锈、耐蚀铸钢 (11)10.JIS G5122-1991耐热铸钢 (14)11.JIS G5131-1991高锰铸钢日本标准 (15)12.JIS G5121-1991不锈耐蚀铸钢 (15)13.ASTM A732/A732M-1998精密铸钢和精密铸造合金 (17)14.ASTM A732/A732M-1998钴基精密铸造合金 (18)15.ASTM A297/A297M-1998耐热铸钢和高温用铸钢 (19)16.ASTM A297/A297M-2000美国ASTM标准与UNS系统高温用奥氏体铸钢 (19)17.ASTM A216M-1998美国ASTM标准与UNS系统适合于熔焊的高温用碳素铸钢 (21)18.ASTM A447/A447M-1998美国ASTM标准高温用镍铬合金铸钢 (21)19.ASTM A560/A560M-1998美国ASTM标准抗高温腐蚀的镍铬铸造合金 (22)20.ASTM A27/A27M-2000工程与结构用铸钢 (22)21.ASTM A487/A487M-1998承压铸钢 (22)22.ASTM A128/A128M-1998高锰铸钢 (25)23.KS D4101-1995工程与结构用铸钢 (26)24.KS D4107-1991承压铸钢 (28)25.KS D4104-1995高锰铸钢 (29)26.KS D4105-1995耐热铸钢 (29)27.DIN SEW395-1998高锰铸钢和耐磨蚀铸钢 (30)28.DIN 17245-1987铁素体热强铸钢 (31)29.DIN 17465-1993耐热铸钢 (31)30.DIN 17445-1984不锈、耐蚀铸钢德国标准 (33)31.DIN 1681-1985工程与结构用铸钢 (36)32.JIS G5******* 工程与结构用铸钢 (38)33.JIS G5201-1991离心铸钢管 (41)34.GB/T 1503-1989轧辊用铸钢 (42)35.JB/T 6402-1992工程与结构用铸钢 (43)36.GB/T 11352-1989工程与结构用铸钢 (45)37.GB/T 7659-1987焊接结构用碳素铸钢 (46)38.GB/T 16253-1996承压铸钢 (47)39.GB/T 5680-1998高锰铸钢 (50)40.YB/T 036.4-1992高锰铸钢 (51)41.JB/T 6404--1992大型铸件用高锰铸钢 (51)42.GB/T 8492-1987耐热铸钢 (52)43.JB/T 6403-1992大型铸件用耐热铸钢 (53)BS 3146 Part1-1992 精密铸钢和精密铸造合金碳素精密铸钢和低合金精密铸钢的力学性能碳素精密铸钢和低合金精密铸钢的钢号与化学成分(质量分数)(%)BS 3146 Part21992耐蚀、耐热精密铸钢和NiCo基精密铸造合金的钢号与化学成分[再确认]BS 3100 Part 4-1991耐蚀、耐热和高合金铸钢耐蚀、耐热和高合金铸钢的热处理力学性能耐蚀、耐热和高合金铸钢的钢号与化学成分(质量分数)(%)BS EN 102132-1995承压铸钢室温和高温用承压铸钢的高温屈服强度①热处理代号:N-正火;Q-淬火,T-回火。
铸造件通用检验标准

铸造件通用检验标准前言铸造件的检验,以图纸为依据,如本标准与图纸不符,以图纸为检验标准。
为了使检验工作走向标准化,加强中间过程质量控制,特制定本检验标准。
1.范围本标准适用于本公司产品压铸件及机加工的检验、验收。
2.引用标准本标准引用了下列标准的条款.本标准发布时,这些引用标准均为有效版本.所有标准将进行修定,因此,鼓励依据本标准达成协议的各方尽可能采用下列标准的最新版本.GB4054—83 金属涂覆层外观分级GB/T 9286—88 色漆和清漆划痕试验GB/T 6739—96 涂膜硬度铅笔测定法GB/T 1733—93 漆膜耐水性测定法GB/T6742—93 漆膜弯曲试验(园柱轴)GB/T1732-93 漆膜耐冲击测定法GB/T1771—91 色漆和清漆耐中性盐污性能的测定GB 5267—85 螺纹紧固件电镀层GB 2792—81 压敏胶带180°剥离强度测定方法GB5935—86 轻工产品金属镀层的孔隙率测试方法GB6463—86 金属和其它无机覆盖层厚度测量方法评述GB10125-97 《人造气氛腐蚀试验盐雾试验》GB5270-86 金属覆盖层结合力及脆性测试GB/T1182-96 形状和位置公差GB4208-2008 外壳防护等级(IP代码)3.目的3.1确保压铸件判定的统一标准;3.2指引QC检验,将所有检验动作标准化。
4.定义磨花/磨痕:产品表面由于摩擦而造成的擦花痕刮伤/划伤:产品表面由于与尖硬物摩擦而造成的刮痕/划痕。
刀痕:因用锉刀或机加工时刀具所留下的痕迹砂带痕:因用砂带打磨所留下的痕迹拉模伤:顺着出模方向遗留在铸件表面上的拉伤痕迹。
凹陷:平滑表面上凹瘪的部分或者成型过程中填充不完整的部位压伤:切边模冲压或机加工时挤压所留下的痕迹碰伤:产品表面,边角受碰撞引起的变形痕迹顶针印:铸件表面由于模具顶针而形成凸出或凹下的痕迹行位印:铸件表面由于模具抽芯/镶块而形成凸出或凹下的痕迹冷隔:金属流对接未完全熔合形成的不规则下陷线性纹路,在外力作用下有发展趋势可能冷纹:肉眼可见与金属基体颜色不一样的纹络,无发展趋势印痕:铸件表面由于模具型腔磕碰挤压而形成凸出或凹下的痕迹流痕:表面上用手感觉得出的局部下陷的纹路,无发展趋势孔穴:气孔,缩孔和夹杂物等缺陷所形成的孔洞针孔:喷涂时表面产生的像针尖一样的小孔缺料/崩缺:外力敲击水口或切边模产生的缺损裂纹/裂痕:模具表面有呈直线状或波浪形的纹路,狭小而长,在外力的左右下有发展趋势龟裂纹:模具型腔表面龟裂形成的产品表面凸起或凹陷痕迹披锋:压铸件在分型面边缘出现的薄片毛边:边缘轮廓上因涂料堆积出现的边缘涂层不整齐现象斑点/麻点:产品表面形成的凸起颗粒或突出性杂物污点/脏点:颜色与正常表面不一致的色斑印迹气泡:涂层覆盖部分气体在烘烤时产生的泡状凸起缺陷桔皮/橘皮:涂层表面呈现出许多半圆状高低不平的桔子皮形状突起,易造成脱落起皮色差/异色:产品与色板的颜色差异露底/掉漆:局部无涂层或涂层缺失/覆盖不平露出底材积漆/溢漆:表面有较多漆团或漆点烧焦/发黄:喷涂烘烤不良造成表面留下的烧痕迹少漆/薄漆:喷涂不到位或涂层流动而造成的厚度不均匀补漆:因涂层损伤而用涂料所作的局部遮盖补救A 级面:指该表面位于工件或组装后经常看到的外表面,或客户日常操作能近距离视角接触,并直接正视关注的产品表面和商标文字和图案丝印表面B 级面:指该表面位于工件或组装背面,或不经常看到但在一定条件下能看到的面,或客户不明显关注的外观表面,或不易被客户直接视角接触正视的外部表面C 级面:指该表面位于工件或组装不可视面,或客户一般不易观察并关注到的内外部表面,或只有在装配过程中才能看到的面,或经其他工件覆盖需拆卸才能被客户直接视角接触正视的内外部表面5.内容5.1外观检验5.2性能检验5.3包装防护标识5.4机加工尺寸选用下表中等级-M级。
2012年实施标准化战略资金拟资助项目表
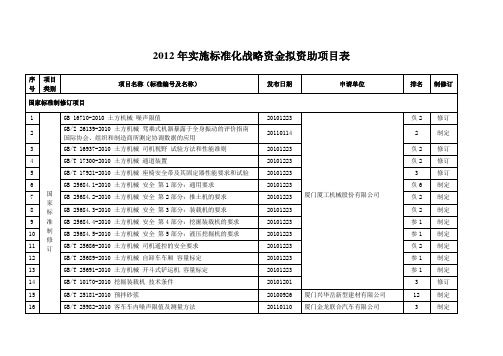
负6
制定
7
GB 25684.2-2010 土方机械 安全 第2部分:推土机的要求
20101223
负2
制定
8
GB 25684.3-2010 土方机械 安全 第3部分:装载机的要求
20101223
负2
制定
9
GB 25684.4-2010 土方机械 安全 第4部分:挖掘装载机的要求
20101223
20110114
2
制定
3
GB/T 16937-2010 土方机械 司机视野 试验方法和性能准则
20101223
负2
修订
4
GB/T 17300-2010 土方机械 通道装置
20101223
负2
修订
5
GB/T 17921-2010 土方机械 座椅安全带及其固定器性能要求和试验
20101223
3
修订
6
GB 25684.1-2010 土方机械 安全 第1部分:通用要求
制定
3
QB/T 4151-2010 工艺伞
20101229
太阳城(厦门)雨具有限公司
3
制定
4
SC/T 3119-2010 活鳗鲡
20101223
福建省水产研究所
1
制定
5
SC/T 3046-2010 冻烤鳗良好生产规范
20101223
福建省水产研究所
1
制定
6
QB/T 1692.4-2010 卫生香
20101122
参1
制定
10
GB 25684.5-2010 土方机械 安全 第5部分:液压挖掘机的要求
20101223
工程材料验收标准

玻璃砖、玻璃马赛克、
11
油漆
涂料
油漆
一般油漆
清漆、瓷漆、聚脂漆、
油脂漆、地板漆
耐腐蚀油漆
防锈漆、生漆、沥青漆
防火油漆
无极防火漆、
酚醛防火漆、
漆片
漆片(虫胶片)
涂料
一般涂料
106涂料、多彩内墙涂料
防瓷涂料
防瓷涂料
外墙喷涂
合成树脂乳液砂壁状
建筑涂料
耐腐蚀涂料
石蜡防腐涂料
防火涂料
防火涂料
防水涂料
聚胺脂防水涂料
复合硅酸盐水泥
32.5
32.5R
42.5
42.5R
52.5
52.5R
11.0
16.0
16.0
21.0
22.0
26.0
32.5
32.5
42.5
42.5
52.5
52.5
2.5
3.5
3.5
4.0
4.0
5.0
5.5
5.5
6.5
6.5
7.0
7.0
注:表中强度等级栏中R表示早强型,要求3d达到较高水平。
1.2各项技术要求应符合表1-2的规定。
渍后,其重量损失(%)
<5
<8
<12
强度
抗压强度
采用直径和高均为50㎜的圆柱体或长、宽、高均为50㎜的立方体岩石样品进行试验,在水饱和状态下,其抗压强度应不小于45MPa,其极限抗压强度与所浇注混凝土强度之比不应小于1.5倍。
压碎值(%)
不大于
碎石
10
20
30
卵石
12
16
16
表观密度(g/cm3)
铝及铝合金术语 第3部分:表面处理(标准状态:现行)

犌犅/犜 8005.3—2008
2.19 清洗 cleaning 2 2.20 水洗 rinsing 2 2.21 絮凝 flocculate 2 2.22 有效面 significantsurface 2 2.23 挂架 rack (jig) 2 2.24 阳极氧化膜 anodicoxidecoating 3 2.25 阳极氧化复合膜 combinedanodiccoating 3 2.26 有机聚合物喷涂膜 sprayingcoating 3 2.27 功能性氧化膜 functionalcoating 3 2.28 电镀 electroplating 3 2.29 化学镀 electrolessplating 3 2.30 颜色 colour 3 2.31 蓝卡 bluescale 3 2.32 灰卡 greyscale 3 3 表面预处理 3 3.1 表面预处理 surfacepretreatment 3 3.2 缎面处理 satinfinishing 3 3.3 亚光处理 mattefinishing 3 3.4 光亮浸渍 brightdipping 3 3.5 化学增光 chemicalbrightening 3 3.6 电解增光 electrobrightening 4 3.7 抛光 polishing 4
(ISO7583:1986,Anodizingofaluminiumanditsalloys —Vocabularytrilingualedition,MOD)
20080609发布
20081201实施
中华人民共和国国家质量监督检验检疫总局 中国国家标准化管理委员会
发布
犌犅/犜 8005.3—2008
Ⅱ
犌犅/犜 8005.3—2008
变形铝及铝合金铸锭的显微疏松检验
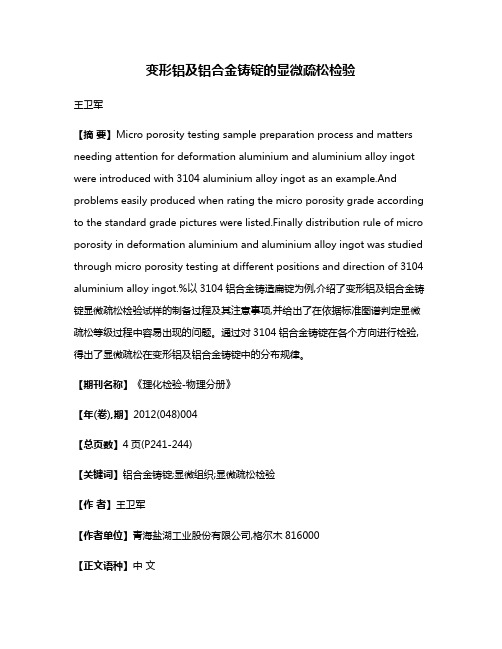
变形铝及铝合金铸锭的显微疏松检验王卫军【摘要】Micro porosity testing sample preparation process and matters needing attention for deformation aluminium and aluminium alloy ingot were introduced with 3104 aluminium alloy ingot as an example.And problems easily produced when rating the micro porosity grade according to the standard grade pictures were listed.Finally distribution rule of micro porosity in deformation aluminium and aluminium alloy ingot was studied through micro porosity testing at different positions and direction of 3104 aluminium alloy ingot.%以3104铝合金铸造扁锭为例,介绍了变形铝及铝合金铸锭显微疏松检验试样的制备过程及其注意事项,并给出了在依据标准图谱判定显微疏松等级过程中容易出现的问题。
通过对3104铝合金铸锭在各个方向进行检验,得出了显微疏松在变形铝及铝合金铸锭中的分布规律。
【期刊名称】《理化检验-物理分册》【年(卷),期】2012(048)004【总页数】4页(P241-244)【关键词】铝合金铸锭;显微组织;显微疏松检验【作者】王卫军【作者单位】青海盐湖工业股份有限公司,格尔木816000【正文语种】中文【中图分类】TG113.12疏松是液态铝合金在凝固过程中,体积收缩时得不到很好的补充,而在铝合金铸锭组织中出现的宏观或微观的分散性孔洞。
- 1、下载文档前请自行甄别文档内容的完整性,平台不提供额外的编辑、内容补充、找答案等附加服务。
- 2、"仅部分预览"的文档,不可在线预览部分如存在完整性等问题,可反馈申请退款(可完整预览的文档不适用该条件!)。
- 3、如文档侵犯您的权益,请联系客服反馈,我们会尽快为您处理(人工客服工作时间:9:00-18:30)。
变形铝及铝合金板、带缺陷1范围本标准规定了变形铝及铝合金板、带产品中常见的缺陷的定义、特征,分析了其产生的原因,并附有相应部分图片。
本标准适用于变形铝及铝合金板、带缺陷的分析与判定。
2缺陷定义、特征、产生原因典型事例2.1非金属压入2.1.1缺陷定义及特征非金属杂物压入板、带表面。
表面呈明显的点状或长条状黄黑色缺陷。
2.1.2产生原因a)轧制工序设备条件不清净;b)轧制工艺润滑剂不清静;c)工艺润滑剂喷射压力不足;d)板坯表面有擦划伤。
图1非金属压入2.2金属压入2.2.1缺陷定义及特征金属屑或金属碎片压入板、带表面。
压入物刮掉后呈大小不等的凹陷,破坏了压入板、带表面的连续性。
2.2.2产生原因a)热轧时辊边道次少,裂边的金属屑、条掉在板坯表面后压入;b)圆盘剪切边工序质量差,产生毛刺掉在带坯上经轧制后压入;c)轧辊粘铝后,其粘铝又被压在板坯上;d)热轧导尺夹得过紧,带下来的碎屑掉在板坯上后被压入。
图2金属压入2.3划伤2.3.1缺陷定义及特征因尖锐的物体(如板角、金属屑或设备上的尖锐物等)与板面接触,在相对滑动时所造成的呈单条状分布的伤痕。
2.3.2产生原因a)热轧机辊道、导板上粘铝使板、带划伤;b)冷轧机导板、压平辊等有突出的尖锐物;c)精整时板角划伤;d)涂油包装时油中有金属屑带到涂油辊或毛毡上而划伤板面。
图3划伤2.4擦伤2.4.1缺陷定义及特征由于物体间棱与面,或面与面接触后发生相对滑动或错动而在板、带表面造成的成束(或组)分布的伤痕。
2.4.2产生原因a)板、带在加工生产过程中与导路、设备接触时,产生相对摩擦而造成擦伤;b)冷轧卷端面不齐正,在立式炉退火翻转时产生错动、层与层之间产生擦伤;c)冷轧时张力不当,开卷时产生层间错动而产生擦伤;d)精整验收或包装操作不当产生板间滑动而造成擦伤。
图4擦伤2.5碰伤2.5.1缺陷定义及特征铝板、铝卷与其他物体碰撞后在板、带表面或端面产生的划痕,且大多数在凹陷边际有被挤出的金属存在。
2.5.2产生原因a)板、卷在搬运或存放过程中与其他物体碰撞产生;b)板、卷在退火料架或底盘上有其他突出物顶撞而产生。
图5碰伤(断面)2.6粘伤2.6.1缺陷定义及特征因板间或带材卷层间压力过大造成板、带表面呈点状、片状或条状的伤痕。
粘伤产生时往往上下板片(或卷层)呈对称性,有时呈周期性。
2.6.2产生原因a)热状态下板垛上压有重物;b)经退火的卷材,在较高温度下剪切;c)卷取时张力过大,或卷卡打得过紧。
图6粘伤2.7 印痕(辊印)2.7.1 缺陷定义及特征板、带表面存在的周期性凹陷。
凹陷处比较光滑。
2.7.2 产生原因a)轧辊及板、带表面粘有金属屑或脏物,当板、带通过生产机列后在板、带表面印下粘附物的痕迹;b)其他工艺设备(如:压光机、矫直机、给料辊、导辊)表面有缺陷或粘附脏物时,在板、带表面易产生印痕;c)包装涂油辊压得太紧,且油中有杂质时产生板材的印痕缺陷; d)套筒表面不清洁、不平整及存在光滑的凸起; d)卷取时,铝带粘附异物。
图7 印痕2.8 水痕2.8.1 缺陷定义及特征淬火板压光后表面上呈现的浅白色或浅黑色不规则的水线痕迹。
2.8.2 产生原因淬火后板材表面水分没有擦干净,经压光机压光后留下的痕迹。
图8 水痕2.9 表面污痕(花脸)2.9.1 缺陷定义及特征板、带表面发生光泽及颜色不均匀的污迹。
2.9.2 产生原因a)板、带表面不清洁;b)工艺润滑油质量差。
图9 花脸2.10 表面气泡2.10.1 缺陷定义及特征板、带表面不规则的圆形或条状空腔凸起。
凸起的边缘圆滑、板片上下不对称,分布无规律。
2.10.2 产生原因a)铸块表面凹凸不平、不清洁,表面偏析瘤深度较深;b)铣面量小,表面有缺陷或有印痕或刀痕较深;c)乳液进入包铝板与铸块间;d)铸块加热温度过高或时间过长;e)热处理时温度过高。
图6 表面气泡2.11 腐蚀2.11.1 缺陷定义及特征板、带表面与周围介质接触,发生化学或电化学反应后在板、带表面产生的缺陷。
腐蚀板、带失去金属光泽,严重时在表面产生灰白色的腐蚀产物。
2.11.2 产生原因a)淬火洗涤后,板材表面残留有酸、碱、硝盐;b)板、带放置保管不当,由于气候潮湿或水滴浸入表面引起腐蚀;c)生产过程中的工艺润滑剂中含有水分或呈碱性而腐蚀板、带;d)储运过程中,包装防腐层破坏,引起腐蚀。
图7 腐蚀2.12硝盐痕2.12.1缺陷定义及特征热处理硝盐介质残留在板材表面而产生的斑痕。
硝盐痕呈不规则的白色斑块,表面粗糙、无金属光泽。
2.12.2产生原因a)淬火后洗涤不彻底;b)压光前板面没有擦干净;c)板片表面残留有硝盐。
2.13油斑2.13.1缺陷定义及特征残留在板、带上的油污,经退火后形成的黄褐色程度不同的斑痕。
2.13.2产生原因a)冷轧用润滑油质量差;b)退火工艺不当;c)机械润滑油滴在板、带表面。
图13油斑2.14表面裂纹2.14.1缺陷定义及特征在板、带表面与压延方向成直角的裂口。
2.14.2产生原因a)铸锭加热温度过高;b)道次压下量过大;c)铸锭表面质量差。
图14裂纹(表面裂纹)2.15裂边2.15.1缺陷定义及特征板、带边部破裂,严重时呈锯齿状。
2.15.2产生原因a)热轧铸锭温度低、金属塑性差;b)辊型控制不当,使板、带边部出现拉应力;c)中间退火不充分,金属塑性差;d)剪切送料偏斜,一边没切掉;e)侧边包铝不完整;f)均火不充分;g)轧制率过大;h)浇口未切掉。
图15裂边2.16滑移线2.16.1缺陷定义及特征拉伸板表面,与拉伸方向约呈45°角的有规律的发暗条纹。
2.16.2产生原因拉伸量过大。
2.17侧边弯曲2.17.1缺陷定义及特征板、带的纵向侧边呈现向某一侧弯曲的非平直状态。
2.17.2产生原因a)轧机、压光机两端压下量不一样;b)轧机、压光机送料不正;c)板、带来料两侧厚度不一致,精整时产生侧弯;d)轧辊预热不良或乳液流量控制不当;e)工艺润滑剂浓度过高,打滑。
2.18波浪2.18.1缺陷定义及特征板、带由于不均匀变形而形成的各种不同的不平整现象的总称。
板、带边部产生的波浪称为边部波浪,中间产生的波浪称为中间波浪,既不在中间又不在两边的波浪称为二肋波浪。
2.18.2产生原因a)辊缝调整不平衡,辊型控制不合理;b)b)润滑冷却不均,使板、带变形不均;c)c)道次压下量分配不合理;d)来料质量不好,同板差超标;e)卷取张力使用不均。
图18波浪2.19包铝层错动2.19.1缺陷定义及特征热轧时包铝板偏移或横向摆动形成的板、带表面缺陷。
该缺陷沿板材边部为整齐的暗带、热处理后呈暗黄色条状痕迹。
2.19.2产生原因a)包铝板没有方正;b)焊合侧边包铝板时辊边量过大;c)热轧时铸块送料不正;d)切边时两边剪切宽度不均,一边切少;e)焊合压延时压下量小,没有焊合上。
2.20分层2.20.1缺陷定义及特征由于变形不均,在板材端部及边部中心产生的与板材表面平行的层裂。
2.20.2产生原因a)热轧道次压下量分配不当,压下量过大;b)铸锭加热不均匀或加热温度过高或过低。
图20分层2.21夹渣分层2.21.1缺陷定义及特征板材的横截面上产生与板材表面平行的条状裂纹,沿压延方向延伸,分布无规律。
2.21.2产生原因a)铸锭质量差,含有非金属夹杂;b)含气量高,疏松严重。
图21夹渣分层2.22粘铝2.22.1缺陷定义及特征轧辊与板、带表面由于润滑性能不好而引起板、带表面粗糙的粘伤。
2.22.2产生原因a)热轧时铸锭温度过高;b)轧制工艺不当,道次压下量大且轧速又快;c)工艺润滑剂性能差。
图22粘铝2.23过烧2.23.1缺陷定义及特征热处理时金属温度达到或超过低熔点共晶温度而产生特有组织的现象叫过烧。
过烧严重时表面呈现明显的氧化色(呈灰色或微黄色)、粗糙或密集小泡。
显微组织中出现晶界加粗或晶间复熔三角或晶内出现了复熔共晶球。
2.23.2产生原因a)未正确执行工艺制度;b)热处理设备及仪表运转不正常。
图23过烧2.24压折2.24.1缺陷定义及特征压过的皱折,皱折与轧制方向成一定角度。
压折处呈亮道花纹。
2.24.2产生原因a)压光机辊型不正确,板材不均匀变形而产生压折;b)压光前板材波浪过大,压下量又大,速度又快;c)压光时送料不正;d)冷轧时板带厚度不均匀,板形不良。
图24压折2.25乳液痕2.25.1缺陷定义及特征板、带表面残留的呈乳白色或灰黑色点状、条状痕迹。
2.25.2产生原因a)乳液温度高,冷轧最后一道乳液没有吹净,使乳液卷在卷筒里;b)乳液温度过高,乳液烧结在板面上。
图25乳液痕2.26压过划痕2.26.1缺陷定义及特征经轧辊压过了的擦、划伤、粘铝等表面损伤。
2.26.2产生原因导路、卷取、退火等工序产生擦、划伤、粘铝等损伤。
图26压过划痕2.27折伤2.27.1缺陷定义及特征板材弯折后产生的变形折痕。
2.27.2产生原因a)多辊矫直机上料时送料不正;b)薄板在翻片或搬运中受力不平衡;c)上垛片时受力不平衡。
图27折伤2.28油粘2.28.1缺陷定义及特征残留在带卷内的工艺润滑油及其他油污,在退火加热过程中氧化,聚合生成粘稠状沥青质,影响卷材的顺利展开。
2.28.2产生原因a)退火加热制度不当,油没有挥发完全;b)工艺润滑油技术指标不合理,或混入一定数量的设备润滑油。
2.29横波2.29.1缺陷定义及特征垂直压延方向横贯带板表面的波纹。
2.29.2产生原因a)轧制过程中工作辊颤动;b)轧制过程中中间停机,或较快调整压下量;c)精整时多辊矫直机在有较大压下量的情况下矫直时中间停车。
2.30明暗条纹2.30.1缺陷定义及特征组织不均匀,或有粗大晶粒存在而产生的与压延方向平行的明暗相间的光泽不同的条纹。
2.30.2产生原因a)铸锭表面质量差,热轧又没有铣面;b)板坯表面组织不均有粗大晶粒。
图30明暗条纹2.31铜扩散2.31.1缺陷定义及特征由于不适宜的加热制度使包铝板材基体金属中的铜原子扩散到包铝层的晶界上,形成须状晶界,扩散到板材表面时,在表面上形成黄褐色斑点。
2.31.2产生原因a)不正确的热处理制度,温度过高,或时间太长;b)b)淬火、退火等重复热处理次数太多;c)c)用错了包铝板。
图8铜扩散2.32贯穿气孔2.32.1缺陷定义及特征板材表面呈现出一种表面及边缘圆滑的圆形或长条形的贯穿板材整个厚度的空腔凸起,具有对称性。
这种凸起分布是无规则的。
2.32.2产生原因铸锭质量不好,含氢量过高,有集中气孔。
图22贯穿气孔2.33揉擦伤2.33.1缺陷定义及特征淬火时相邻板片间相互摩擦产生的伤痕。
擦伤条纹不规则,呈圆弧状,破坏了自然氧化膜和包覆层。
2.33.2产生原因a)淬火板材弯曲变形过大;b)淬火装料太多,板间间距小。