铝合金薄壁件加工中变形的因素分析与控制方法
铝合金薄壁件加工变形控制工艺方法研究

铝合金薄壁件加工变形控制工艺方法研究发布时间:2021-12-29T01:21:12.823Z 来源:《中国科技人才》2021年第22期作者:刘世超[导读] 本文探讨铝合金薄壁件在铣削加工过程中产生加工变形的原因,并提出相应的解决办法来控制变形,为技术人员提供一些参考。
中航西安飞机工业集团股份有限公司制造工程部西安 710089[摘要] 随着现代航空制造工业的迅速发展,铝合金薄壁件在航空飞机上的使用日趋广泛,但铝合金薄壁件在加工时极易因为受到的切削力、热、夹紧力等因素的影响而产生变形,变形的影响因素是复杂的,这在机械加工行业是一个比较棘手的问题,因此减小薄壁件的加工变形一直是国内外学者研究的热点。
本文探讨铝合金薄壁件在铣削加工过程中产生加工变形的原因,并提出相应的解决办法来控制变形,为技术人员提供一些参考。
[关键词] 薄壁件残余应力工艺参数装夹方式变形控制1 薄壁件加工产生变形的原因分析航空铝合金薄壁件的加工变形问题,涉及力学、材料成形加工、切削加工和机械制造多个学科领域,是航空产品加工工艺中的瓶颈之一。
航空薄壁件的加工变形产生的原因很多,与毛坯的材料、零件的几何形状及刚度、以及加工工艺方法和加工设备等均有关系。
经研究分析,引起薄壁件加工变形的主要因素有以下几个方面:零件材料力学特性与结构特点的影响:航空铝合金的弹性模量约为 70 一 73MPa,约为钢的 1/3 左右。
由于其弹性模量小,屈强比大,在切削过程中极易产生回弹,特别是大型薄壁结构件,“让刀”和回弹现象更为严重;另外,航空薄壁件的结构也非常复杂,通常几何结构不对称,薄壁部位多,自身刚度差等,也是产生较大变形的内在因素。
切削过程中刀具与零件间力-热耦合作用的影响:零件加工过程中材料的去除过程伴随着切削力、热的产生;一方面零件与刀具的接触部分发生弹塑性变形,材料不断被刀具切除;另一方面工件产生回弹效应,发生“让刀”现象,特别是对于薄壁部分,“让刀”对加工精度的影响不容忽视。
铝合金零件加工变形原因分析及工艺控制对策探讨
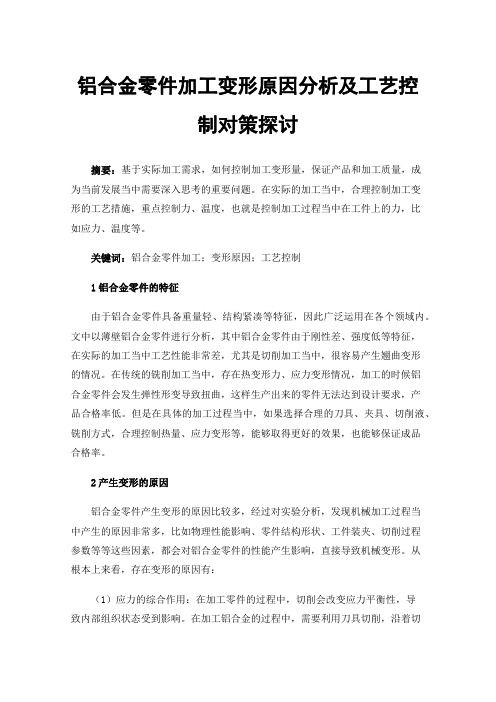
铝合金零件加工变形原因分析及工艺控制对策探讨摘要:基于实际加工需求,如何控制加工变形量,保证产品和加工质量,成为当前发展当中需要深入思考的重要问题。
在实际的加工当中,合理控制加工变形的工艺措施,重点控制力、温度,也就是控制加工过程当中在工件上的力,比如应力、温度等。
关键词:铝合金零件加工;变形原因;工艺控制1铝合金零件的特征由于铝合金零件具备重量轻、结构紧凑等特征,因此广泛运用在各个领域内。
文中以薄壁铝合金零件进行分析,其中铝合金零件由于刚性差、强度低等特征,在实际的加工当中工艺性能非常差,尤其是切削加工当中,很容易产生翘曲变形的情况。
在传统的铣削加工当中,存在热变形力、应力变形情况,加工的时候铝合金零件会发生弹性形变导致扭曲,这样生产出来的零件无法达到设计要求,产品合格率低。
但是在具体的加工过程当中,如果选择合理的刀具、夹具、切削液、铣削方式,合理控制热量、应力变形等,能够取得更好的效果,也能够保证成品合格率。
2产生变形的原因铝合金零件产生变形的原因比较多,经过对实验分析,发现机械加工过程当中产生的原因非常多,比如物理性能影响、零件结构形状、工件装夹、切削过程参数等等这些因素,都会对铝合金零件的性能产生影响,直接导致机械变形。
从根本上来看,存在变形的原因有:(1)应力的综合作用:在加工零件的过程中,切削会改变应力平衡性,导致内部组织状态受到影响。
在加工铝合金的过程中,需要利用刀具切削,沿着切削方向铝合金材料会产生变形问题,同时也会牵制相邻里层,在铝合金材料表面产生残余拉应力,在里层会产能参与压应力,在综合作用的影响下,铝合金零件因此出现变形问题。
(2)残余拉应力:在切削工作中,因为摩擦阻力的影响,引发塑性变形问题,在铝合金表面产生较多的热量,导致材料因此膨胀,如果里层温度比较低,表层发生膨胀问题之后,会阻挡里层材料,导致表层金属产生热应力。
如果热应力超过了铝合金材料屈服极限,将会引发压缩塑性变形问题。
铝件加工变形怎么办

铝件加工变形怎么办?工艺措施和操作技巧详解铝件零件加工变形的原因很多,与材质、零件形状、生产条件等都有关系。
主要有以下几个方面:毛坯内应力引起的变形,切削力、切削热引起的变形,夹紧力引起的变形。
一、减少加工变形的工艺措施1降低毛坯内应力采用自然或人工时效以及振动处理,均可部分消除毛坯的内应力。
预先加工也是行之有效的工艺方法。
对肥头大耳的毛坯,由于余量大,故加工后变形也大。
若预先加工掉毛坯的多余部分,缩小各部分的余量,不仅可以减少以后工序的加工变形,而且预先加工后放置一段时间,还可以释放一部分内应力。
2改善刀具的切削能力刀具的材料、几何参数对切削力、切削热有重要的影响,正确选择刀具,对减少零件加工变形至关重要。
(1)合理选择刀具几何参数。
①前角:在保持刀刃强度的条件下,前角适当选择大一些,一方面可以磨出锋利的刃口,另外可以减少切削变形,使排屑顺利,进而降低切削力和切削温度。
切忌使用负前角刀具。
②后角:后角大小对后刀面磨损及加工表面质量有直接的影响。
切削厚度是选择后角的重要条件。
粗铣时,由于进给量大,切削负荷重,发热量大,要求刀具散热条件好,因此,后角应选择小一些。
精铣时,要求刃口锋利,减轻后刀面与加工表面的摩擦,减小弹性变形,因此,后角应选择大一些。
③螺旋角:为使铣削平稳,降低铣削力,螺旋角应尽可能选择大一些。
④主偏角:适当减小主偏角可以改善散热条件,使加工区的平均温度下降。
(2)改善刀具结构。
①减少铣刀齿数,加大容屑空间。
由于铝件材料塑性较大,加工中切削变形较大,需要较大的容屑空间,因此容屑槽底半径应该较大、铣刀齿数较少为好。
②精磨刀齿。
刀齿切削刃部的粗糙度值要小于Ra=0.4um。
在使用新刀之前,应该用细油石在刀齿前、后面轻轻磨几下,以消除刃磨刀齿时残留的毛刺及轻微的锯齿纹。
这样,不但可以降低切削热而且切削变形也比较小。
③严格控制刀具的磨损标准。
刀具磨损后,工件表面粗糙度值增加,切削温度上升,工件变形随之增加。
铝合金薄壁件加工变形控制技术浅析

铝合金薄壁件加工变形控制技术浅析摘要:随着工业制造业的不断发展,在工业制造之中逐渐开始使用铝合金材料,并且其使用范围越来越广泛,但是其加工技术还需要进一步的控制。
在进行铝合金材料加工的过程中,应该注意对于其加工变形的控制。
基于此,本文在分析铝合金材料加工变形影响因素与特点的基础上,通过先进的加工技术、冷处理技术、热处理技术、合理的装夹方式、合理利用切削刀具,从而对于铝合金硬铝板料变形的处理对于其加工变形控制进行深入的探讨,以便在后续的工序操作中,能够轻松的应对,满足整体的质量要求。
关键词:铝合金薄壁;加工变形;控制;技术引言铝合金在实际加工过程中存在易变型的问题,特别是加工余量大,可装夹面较小的情况下,通过对中单位用量较大的铝合金零件进行分析,详细介绍零件加工工艺流程的制定,包括零件的加工方法,加工中遇到的问题及如何解决问题,最后成功制定出合理工艺流程,保证质量的同时也提高了生产效率。
1.铝合金材料加工变形的主要影响因素与特点1.1影响因素针对铝合金材料的加工变形,主要包含机床、刀具、夹具等,也包含了通风条件、温度等因素。
其中,钢度会受到机床定位精度的影响。
在进行工件装夹中,如果夹紧点选择错误,就会影响夹紧力的作用;如果夹具和工件接触面相对较小,也会对其度带来影响,如果其本身的钢度无法满足要求,在实施装夹力的时候就会引发变形。
另外,刀具对于铝合金的加工变形带来的影响主要是针对材料、钢性以及耐用度等方面。
不过在所有因素之中,最为明显的还是切削参数的影响。
在实施高速切削时,会带走大部分的切削热。
当进一步减少工件热变形,并且切削参数不够合理的时候,就很容易出现加工零件震动的问题,进而降低加工精度,引发加工变形。
在进行铝合金材料加工变形因素分析中,其主要包含:第一,温度以及挤压速度不够合理。
在相对较长时间内,铝合金材料加工都是选择的传统加工模式,这样会影响对于加工温度的实际把握;第二,在加工过程中,对于材料位置的选择不够合理。
薄壁零件加工变形分析及控制方案
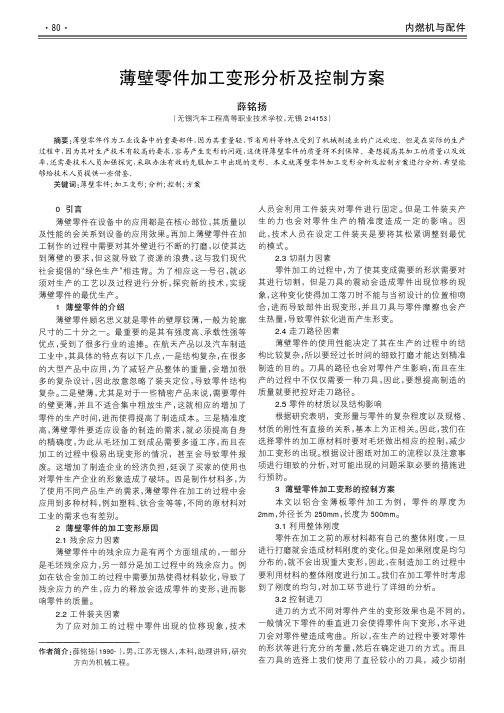
0引言薄壁零件在设备中的应用都是在核心部位,其质量以及性能的会关系到设备的应用效果。
再加上薄壁零件在加工制作的过程中需要对其外壁进行不断的打磨,以使其达到薄壁的要求,但这就导致了资源的浪费,这与我们现代社会提倡的“绿色生产”相违背。
为了相应这一号召,就必须对生产的工艺以及过程进行分析,探究新的技术,实现薄壁零件的最优生产。
1薄壁零件的介绍薄壁零件顾名思义就是零件的壁厚较薄,一般为轮廓尺寸的二十分之一。
最重要的是其有强度高、承载性强等优点,受到了很多行业的追捧。
在航天产品以及汽车制造工业中,其具体的特点有以下几点,一是结构复杂,在很多的大型产品中应用,为了减轻产品整体的重量,会增加很多的复杂设计,因此故意忽略了装夹定位,导致零件结构复杂。
二是壁薄,尤其是对于一些精密产品来说,需要零件的壁更薄,并且不适合集中粗放生产,这就相应的增加了零件的生产时间,进而使得提高了制造成本。
三是精准度高,薄壁零件要适应设备的制造的需求,就必须提高自身的精确度,为此从毛坯加工到成品需要多道工序,而且在加工的过程中极易出现变形的情况,甚至会导致零件报废。
这增加了制造企业的经济负担,延误了买家的使用也对零件生产企业的形象造成了破坏。
四是制作材料多,为了使用不同产品生产的需求,薄壁零件在加工的过程中会应用到多种材料,例如塑料、钛合金等等,不同的原材料对工业的需求也有差别。
2薄壁零件的加工变形原因2.1残余应力因素薄壁零件中的残余应力是有两个方面组成的,一部分是毛坯残余应力,另一部分是加工过程中的残余应力。
例如在钛合金加工的过程中需要加热使得材料软化,导致了残余应力的产生,应力的释放会造成零件的变形,进而影响零件的质量。
2.2工件装夹因素为了应对加工的过程中零件出现的位移现象,技术人员会利用工件装夹对零件进行固定。
但是工件装夹产生的力也会对零件生产的精准度造成一定的影响。
因此,技术人员在设定工件装夹是要将其松紧调整到最优的模式。
减少薄壁零件产生变形的主要措施

减少薄壁零件产生变形的主要措施薄壁零件在现代制造中可是常客,但说到它们的变形问题,那可真是让人头疼得像一颗老鼠在心里跑。
今天就聊聊,怎么才能有效减少这些变形,让咱的薄壁零件在工厂里乖乖待着,不再像个调皮的小孩。
1. 材料选择很重要1.1 材料性质说到材料,真是不能掉以轻心。
薄壁零件的材料就像是打比赛的运动员,得选对了,才能发挥出最佳状态。
通常,咱们得选那些强度高、韧性好的材料,比如某些铝合金或者高强度钢。
这样一来,就能减少在加工和使用过程中出现的变形情况。
毕竟,强者自有强者的道理嘛。
1.2 材料处理除了选择好材料,后续的处理工艺也不能马虎。
热处理、冷加工这些小细节,都是决定材料最终性能的大功臣。
比如,适当的热处理可以让材料内部的晶体结构更加稳定,变形的几率自然就降低了。
就像咱们吃饭一样,讲究的不是光有好菜,还得看怎么烹饪,才能把味道调到最佳。
2. 设计阶段得用心2.1 设计优化设计环节可是重中之重,咱们可不能草草了事。
薄壁零件的结构设计得合理,才能避免后续的变形问题。
要尽量让受力均匀,避免局部应力集中。
要是设计得不够合理,变形就跟过年一样,年年有余,没完没了。
2.2 加工余量加工余量也得考虑清楚,太少了会让零件受力不均,太多了又浪费材料。
就像做菜,要有点盐,但不能放太多,否则味道就变了。
我们可以在设计时就合理规划一下加工余量,这样才能做到既经济又实用。
3. 加工过程的细节把控3.1 加工工艺咱们进入加工环节,得注意工艺参数的设置。
比如,刀具的选择、切削速度、进给率等,这些都是影响零件加工质量的重要因素。
选择合适的切削工具,不仅可以提高加工效率,还能有效减少变形。
就像选对了鞋子,走路也能轻松许多。
3.2 夹具的使用夹具的使用更是不能忽视!好的夹具能牢牢把住零件,让它在加工过程中不乱跑。
就像是给小孩系好安全带,才能确保他乖乖待在座位上。
如果夹具设计得不合理,零件就容易在加工中发生变形,最后吃亏的可是咱自己。
铝合金薄壁件加工变形控制技术研究

铝合金薄壁件加工 变形控制技术发展 趋势和展望
铝合金薄壁件加工变形控制技术需要高精度和高稳定性的设备,导致制造成本较高。
铝合金薄壁件加工变形控制技术需要精确的工艺参数和操作技巧,对工人的技能水平要求较高。
铝合金薄壁件加工变形控制技术需要长时间的加工过程,导致生产效率较低。
铝合金薄壁件加工变形控制技术需要严格的质量检测和控制,对检测设备的精度和可靠性要求 较高。
技术方案和实施过程应用案例:介绍铝合金薄壁件加工变形控制技术在具体产品中的应用案例,如航空航天、汽 车、电子等领域,说明该技术的应用价值和广泛性。
提高了铝合金薄壁 件加工精度和表面 质量
减少了加工过程中 的材料浪费和废品 率
提高了生产效率和 加工周期,降低了 生产成本
为企业带来了显著 的经济效益和社会 效益
铝合金薄壁件加工 变形控制技术
进给量:优化进给量可以提 高加工精度和减小变形
切削速度:选择合适的切削 速度以减小加工变形
切削深度:合理选择切削深度, 避免过大的切削力导致工件变 形
刀具薄壁件装 夹方式对加工变 形的影响
优化装夹方式的 方法和原理
铝合金薄壁件加工 变形控制实验研究
铝合金薄壁件:材料为5A06铝合金,壁厚为1mm
实验设备:数控加工中心、切削液、夹具等
实验环境:温度20±5℃,湿度50±10%
实验步骤:加工前对铝合金薄壁件进行热处理和表面处理,采用合适的切削参数进行加工, 观察并记录加工变形情况
实验材料:铝 合金薄壁件
实验设备:加 工机床、测量
加大研发投入,持 续探索更有效的加 工变形控制技术。
加强产学研合作, 推动铝合金薄壁件 加工变形控制技术 的创新发展。
建立完善的加工变 形控制技术标准体 系,提升行业整体 水平。
铝合金零件加工变形的解决方法
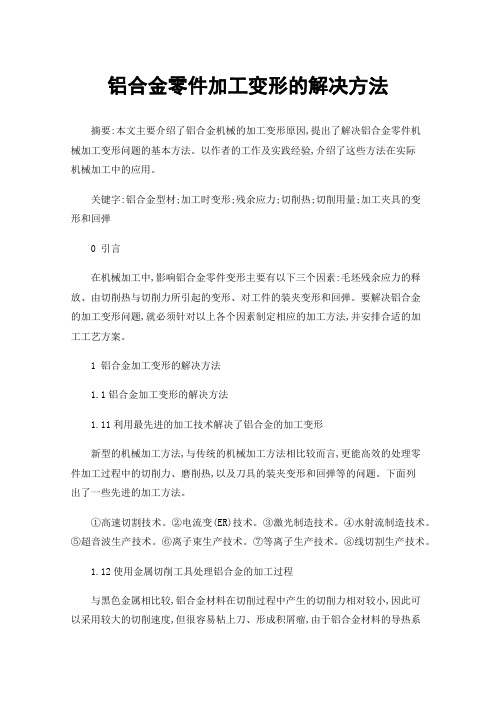
铝合金零件加工变形的解决方法摘要:本文主要介绍了铝合金机械的加工变形原因,提出了解决铝合金零件机械加工变形问题的基本方法。
以作者的工作及实践经验,介绍了这些方法在实际机械加工中的应用。
关键字:铝合金型材;加工时变形;残余应力;切削热;切削用量;加工夹具的变形和回弹0 引言在机械加工中,影响铝合金零件变形主要有以下三个因素:毛坯残余应力的释放、由切削热与切削力所引起的变形、对工件的装夹变形和回弹。
要解决铝合金的加工变形问题,就必须针对以上各个因素制定相应的加工方法,并安排合适的加工工艺方案。
1 铝合金加工变形的解决方法1.1铝合金加工变形的解决方法1.11利用最先进的加工技术解决了铝合金的加工变形新型的机械加工方法,与传统的机械加工方法相比较而言,更能高效的处理零件加工过程中的切削力、磨削热,以及刀具的装夹变形和回弹等的问题。
下面列出了一些先进的加工方法。
①高速切割技术。
②电流变(ER)技术。
③激光制造技术。
④水射流制造技术。
⑤超音波生产技术。
⑥离子束生产技术。
⑦等离子生产技术。
⑧线切割生产技术。
1.12使用金属切削工具处理铝合金的加工过程与黑色金属相比较,铝合金材料在切削过程中产生的切削力相对较小,因此可以采用较大的切削速度,但很容易粘上刀、形成积屑瘤,由于铝合金材料的导热系数较高,在切削时由切屑和零件导出的热量都较多,且切削区温度也较低,所以虽然刀具耐用度较高,但由于零件本身的温升也相对较快,很容易引起变形的产生。
因此,通过选用合适的刀具材料,在原刀具材料的基础上选用合适的刀具角度,并提高刀具表面的粗糙度的要求,对降低切削力和切削热十分有效。
1.13利用热处理解决相合金的加工变形解决铝合金型材加工应力问题的热处理方式,一般为去内部应力退火、再结品退火、均匀性退火及时效。
1.14利用冷处理解决铝合金的加工变形解决铝合金加热变形问题的冷处理技术,只要有振动时效和人工冷校形。
由于冷处理工艺节能、制造周期复、制造代价小,所以在制造流程中使用最广泛。
薄壁零件加工中存在的问题

薄壁零件加工中存在的问题在薄壁零件加工中,可能会面临一些常见的问题。
解决这些问题需要仔细分析每个步骤,并采取相应的措施。
以下是一些可能存在的问题和解决建议:1.变形问题:原因:薄壁零件在加工中容易发生变形,主要是由于切削力引起的材料内应力释放。
解决方案:选择合适的切削参数,采用适当的刀具,减小切削力。
可以考虑采用工艺补偿或者后续的校正工序。
2.毛刺和切屑:原因:薄壁零件的切屑很容易残留在切削区域,形成毛刺。
解决方案:采用适当的切削速度和进给速度,选择合适的切削刃具。
可以考虑添加冷却液以减少热影响,避免切削区域积聚切屑。
3.表面质量问题:原因:薄壁零件的加工可能导致表面粗糙度增加或表面平整度降低。
解决方案:使用高精度的加工设备和刀具。
确保刀具磨损良好,避免振动和共振问题。
定期检查和维护设备。
4.工艺稳定性问题:原因:薄壁零件的加工可能受到环境温度、湿度等因素的影响,导致工艺不稳定。
解决方案:控制加工环境的温湿度,采用合适的工艺参数。
在加工之前,对材料和设备进行预热,确保加工过程中的稳定性。
5.材料选择问题:原因:不同的材料对于薄壁零件加工的难度不同。
解决方案:在设计阶段选择适合加工的材料,考虑材料的强度、塑性等特性。
必要时,进行材料热处理以提高加工性能。
6.加工成本问题:原因:薄壁零件的加工可能涉及到高难度的工艺,导致加工成本增加。
解决方案:寻找合适的工艺和设备,优化刀具选择和切削参数,以降低加工成本。
考虑批量生产以提高效益。
通过综合考虑材料、工艺、设备和人员等因素,可以有效解决薄壁零件加工中可能出现的问题,提高加工质量和效率。
铝合金薄壁件加工变形控制
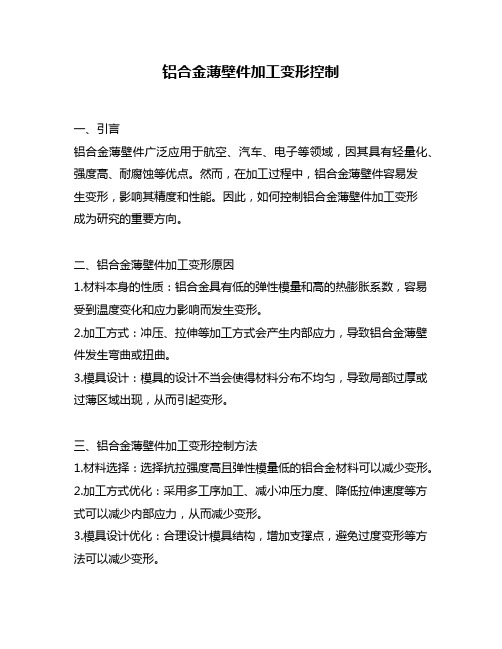
铝合金薄壁件加工变形控制一、引言铝合金薄壁件广泛应用于航空、汽车、电子等领域,因其具有轻量化、强度高、耐腐蚀等优点。
然而,在加工过程中,铝合金薄壁件容易发生变形,影响其精度和性能。
因此,如何控制铝合金薄壁件加工变形成为研究的重要方向。
二、铝合金薄壁件加工变形原因1.材料本身的性质:铝合金具有低的弹性模量和高的热膨胀系数,容易受到温度变化和应力影响而发生变形。
2.加工方式:冲压、拉伸等加工方式会产生内部应力,导致铝合金薄壁件发生弯曲或扭曲。
3.模具设计:模具的设计不当会使得材料分布不均匀,导致局部过厚或过薄区域出现,从而引起变形。
三、铝合金薄壁件加工变形控制方法1.材料选择:选择抗拉强度高且弹性模量低的铝合金材料可以减少变形。
2.加工方式优化:采用多工序加工、减小冲压力度、降低拉伸速度等方式可以减少内部应力,从而减少变形。
3.模具设计优化:合理设计模具结构,增加支撑点,避免过度变形等方法可以减少变形。
四、铝合金薄壁件加工变形控制实践1.材料选择:选择抗拉强度高的6061-T6铝合金材料进行试验。
结果表明,该材料相较于普通铝合金材料能够有效降低变形。
2.加工方式优化:采用多工序加工、缩短冲压时间、降低拉伸速度等方式进行试验。
结果表明,这些方法能够有效减少内部应力和变形。
3.模具设计优化:采用增加支撑点、增加模具刚度等方式进行试验。
结果表明,这些方法能够有效避免过度变形。
五、结论通过以上实践和研究,我们可以得出以下结论:1.选择抗拉强度高且弹性模量低的铝合金材料可以减少变形。
2.采用多工序加工、缩短冲压时间、降低拉伸速度等方式可以减少内部应力和变形。
3.合理设计模具结构,增加支撑点,避免过度变形等方法可以减少变形。
六、展望随着科技的不断进步,铝合金薄壁件加工变形控制的研究将会更加深入。
我们可以通过模拟分析、人工智能等方式来预测和控制铝合金薄壁件的变形,从而进一步提高其精度和性能。
试论铝合金材料加工变形控制措施

试论铝合金材料加工变形控制措施铝合金材料在工业生产中是应用比较广泛的加工材料,其具有重量轻、耐腐蚀性强、导热性好等优点,在工业制造中起到了非常重要作用。
在进行铝合金材料的加工中,会受到多种因素的影响而导致零件变形,这与使用的零件加工技术、加工设备、自然环境等因素有着直接的关系。
要想提高铝合金材料的加工质量,避免变形现象的发生,就需要掌握导致材料加工变形的原因,并采取针对性的措施去处理,才能提高加工效果,保证加工质量。
标签:铝合金材料;加工变形;控制措施一、铝合金加工变形因素导致铝合金材料在加工的过程中出现变形情况的因素有很多,其中主要有机床、夹具、切削参数、刀具以及切割技术等外界因素,还有温度、通风等自然因素,此外,来有一部分因素是来自于铝合金材料自身,铝合金材料的自身质量不合格也是导致其在加工时出现变形情况的主要原因导致其出现变形的原因主要有定位精度以及刚度,其中定位与精度给铝合金材料带来的影响要远远高于刚度;夹具因素给铝合金材料带来的影响主要有夹具的尺寸不合理、夹紧力过高等,这两种情况都会导致铝合金材料出现变形的现象;刀具因素导致铝合金材料出现变形情况的原因有很多,其中主要原因有刀具的各种形状参数、刀具的材质、刚性以及平衡性等等;切削参数是导致铝合金材料在加工过程中出现变形情况最为严重的一种因素。
以上这些都是导致铝合金材料在加工的过程中出现变形情况的主要原因,要想使铝合金材料在加工过程中出现变形情况的几率大幅下降,就必须要加强对以上因素的重视,尽可能的避免其给铝合金材料的加工带来影响。
二、挤压铝合金在机械加工过程中产生变形的主要原因和特点1、铝合金在机械加工过程中产生变形的主要原因在过去科学技术还不如现在发达的时候,那个时候的技术人员使用传统的加工方法对铝合金材料进行加工处理,冷热变形是导致零件变形的重要原因,在实践操作中我们得知,在进行切削加工的过程当中,切削时温度过高和切削时用力太大是导致零件变形的主要原因,对零件的机械加工都包含有,车,铣,饱,磨,膛等,在机械技工过程中直接导致铝合金变形的主要原因有,在进行按压操作时,导致零件的温度过高,在进行挤压的操作中挤压的速度过慢,材料在挤压机的出口温度达不到凝固状态,凝固状态,导致零件达不到凝固强化的基本效果,还有就是材料位置处的通风不佳导致风量不够用,引起零件在加工的过程当中,零件的冷却速度过慢,从而导致铝合金挤压产生变形,或者是工艺在时期内的效用不恰当,热风循环的不流畅,造成牵引机发生故障,使材料表面被压弯,最后一种是没有运用正确的方式方法进行模具的设计,造成模式在使用时设计上的不合理,在挤压下发生抖动造成材料出现波纹。
铝合金薄壁零件的加工工艺及变形控制探讨
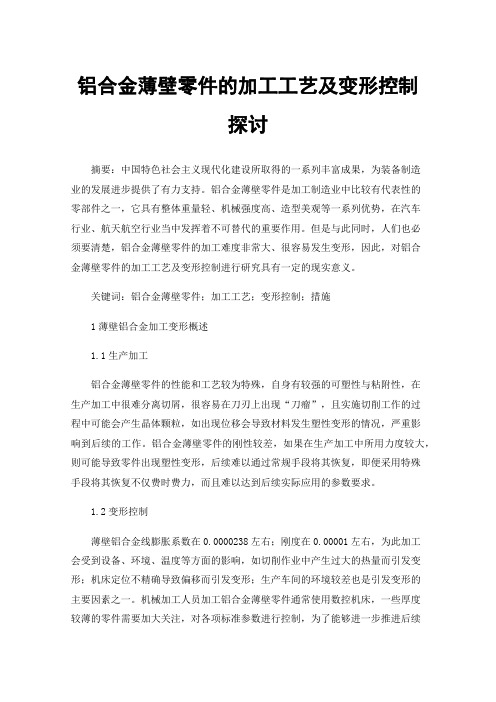
铝合金薄壁零件的加工工艺及变形控制探讨摘要:中国特色社会主义现代化建设所取得的一系列丰富成果,为装备制造业的发展进步提供了有力支持。
铝合金薄壁零件是加工制造业中比较有代表性的零部件之一,它具有整体重量轻、机械强度高、造型美观等一系列优势,在汽车行业、航天航空行业当中发挥着不可替代的重要作用。
但是与此同时,人们也必须要清楚,铝合金薄壁零件的加工难度非常大、很容易发生变形,因此,对铝合金薄壁零件的加工工艺及变形控制进行研究具有一定的现实意义。
关键词:铝合金薄壁零件;加工工艺;变形控制;措施1薄壁铝合金加工变形概述1.1生产加工铝合金薄壁零件的性能和工艺较为特殊,自身有较强的可塑性与粘附性,在生产加工中很难分离切屑,很容易在刀刃上出现“刀瘤”,且实施切削工作的过程中可能会产生晶体颗粒,如出现位移会导致材料发生塑性变形的情况,严重影响到后续的工作。
铝合金薄壁零件的刚性较差,如果在生产加工中所用力度较大,则可能导致零件出现塑性变形,后续难以通过常规手段将其恢复,即便采用特殊手段将其恢复不仅费时费力,而且难以达到后续实际应用的参数要求。
1.2变形控制薄壁铝合金线膨胀系数在0.0000238左右;刚度在0.00001左右,为此加工会受到设备、环境、温度等方面的影响,如切削作业中产生过大的热量而引发变形;机床定位不精确导致偏移而引发变形;生产车间的环境较差也是引发变形的主要因素之一。
机械加工人员加工铝合金薄壁零件通常使用数控机床,一些厚度较薄的零件需要加大关注,对各项标准参数进行控制,为了能够进一步推进后续行业的持续健康发展,需要着重考虑到设备、环境、温度等与金属材料的差异化特点,保证参数精确度符合预期的生产要求,从而有效解决加工伴有的质量问题。
2铝合金薄壁零件的加工工艺随着科技发展,中国的零部件加工技术越来越成熟,对于薄壁零部件的加工能力也在不断提升,铝合金薄壁零件是其中比较有代表性的零部件之一。
铝合金材质决定了该零部件具有比重指数小、比强度指数大的特点,而薄壁结构则导致该零部件的刚性不佳、容易变形,这给铝合金薄壁零件加工带来了一定挑战。
薄壁零件的变形

薄壁零件的变形引言:薄壁零件是工程设计中常见的一类零件,它们通常具有较大的长度和宽度,但相对较小的厚度。
由于其特殊的结构,薄壁零件容易发生变形。
本文将探讨薄壁零件变形的原因、影响以及相应的解决方法。
一、薄壁零件变形的原因1.材料特性:薄壁零件通常采用金属材料制造,而金属材料在受力时容易发生塑性变形。
由于薄壁零件的厚度较小,其受力时的应力集中效应较为明显,进而导致材料发生变形。
2.制造工艺:薄壁零件在加工过程中,如切割、折弯、焊接等,容易受到应力的集中,从而引起变形。
此外,制造工艺中的温度变化、冷却过程等也会对薄壁零件的形状产生影响。
3.外部环境:薄壁零件在使用过程中,受到外部力的作用,如振动、冲击、压力等,这些外部环境的变化也会导致零件的变形。
二、薄壁零件变形的影响1.几何形状:薄壁零件变形会导致其几何形状发生改变,不符合设计要求,从而影响零件的功能和装配。
2.尺寸精度:薄壁零件的变形会使其尺寸精度下降,无法满足设计要求,导致装配困难或无法正常工作。
3.强度和刚度:薄壁零件变形后,其强度和刚度可能会下降,从而影响零件的承载能力和稳定性。
三、薄壁零件变形的解决方法1.材料选择:选择具有较高强度和刚度的材料,以减小薄壁零件受力时的塑性变形。
同时,可以考虑使用复合材料等新型材料来提高薄壁零件的性能。
2.结构优化:通过优化薄壁零件的结构,减小应力集中,提高其受力均匀性。
可以采用增加加强筋、加大壁厚等方式来改善零件的结构。
3.制造工艺:合理选择制造工艺,控制加工过程中的变形。
采用适当的预应力、热处理等工艺措施,可以减小薄壁零件的变形。
4.应力分析:通过应力分析,确定薄壁零件的受力情况,找出应力集中的部位,并进行合理的加强设计,以提高零件的抗变形能力。
5.温度控制:在制造和使用薄壁零件时,注意控制温度的变化,避免温度差异引起的热应力导致变形。
结论:薄壁零件的变形是工程设计中常见的问题,其原因主要包括材料特性、制造工艺和外部环境等因素。
铝合金材料加工中的变形机理与控制

铝合金材料加工中的变形机理与控制在当今的工业生产中,铝合金材料的加工已成为不可或缺的一部分。
由于铝合金材料具有轻质、高强度、耐腐蚀等优点,并且价格相对便宜,因此在汽车、飞机、电子、建筑等领域都有着广泛的应用。
然而,在铝合金材料加工过程中常常会出现变形的问题,这不仅影响了产品的质量,还会增加生产成本。
因此,研究铝合金材料加工中的变形机理与控制是提高生产效率和降低生产成本的重要手段。
一、铝合金材料的变形机理铝合金材料在加工过程中经历了许多形变。
其主要的形变方式有拉伸、压缩、弯曲、剪切等。
不同的形变方式会产生不同的变形机理。
下面主要介绍拉伸和压缩这两种最常见的形变方式。
1. 拉伸变形在铝合金材料的拉伸过程中,材料受到的拉伸力会使材料逐渐拉长,并且横截面积逐渐缩小。
这时候,材料会产生应变,即形变量与原长的比值。
应变又可分为线性应变和非线性应变两种。
线性应变是指拉伸应变与应力成比例,而非线性应变则是指应变随应力呈现出曲线关系。
材料的弹性模量是材料的线性应变和应力的比值,它是用来描述材料抵抗外力变形的能力。
2. 压缩变形与拉伸变形相比,材料在压缩变形过程中受到相反的作用力。
当材料受到压缩力时,横向的体积会缩小,而材料的长度会变短,从而产生应变。
与拉伸变形不同的是,材料在压缩过程中易发生屈曲和剪切,因此压缩变形所产生的应力比拉伸变形更加复杂。
二、铝合金材料变形的控制方法由于变形会对铝合金材料的结构和性质产生影响,因此必须采取一些控制措施来减少或避免变形。
下面介绍一些常见的控制方法。
1. 降低加工温度铝合金的塑性随着温度的升高而增加,因此在加工过程中降低材料的温度可以减少变形。
降低温度的方法有两种:一是通过在加工前对材料进行冷处理,使其温度降至室温以下,然后再进行加工,这种方法适用于小尺寸零件的生产;二是采用低温加工方法,在加工过程中持续降温,控制加工温度在一定范围内,从而减少变形。
2. 选择适当的加工方式在铝合金材料加工过程中,不同的加工方式对材料的变形具有不同的影响。
薄壁铝合金零件热处理变形控制工艺研究
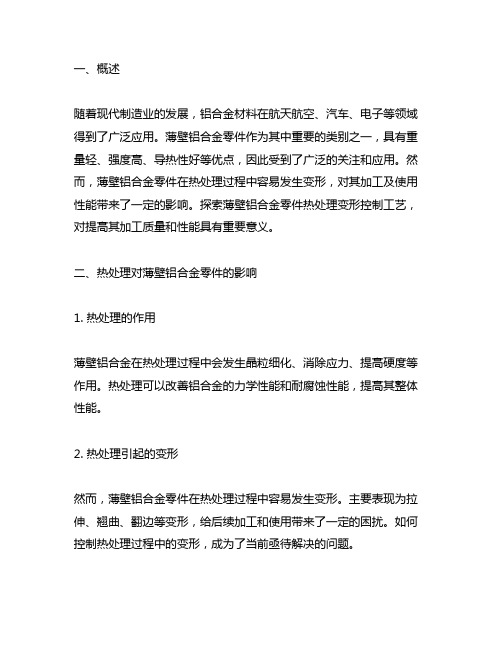
一、概述随着现代制造业的发展,铝合金材料在航天航空、汽车、电子等领域得到了广泛应用。
薄壁铝合金零件作为其中重要的类别之一,具有重量轻、强度高、导热性好等优点,因此受到了广泛的关注和应用。
然而,薄壁铝合金零件在热处理过程中容易发生变形,对其加工及使用性能带来了一定的影响。
探索薄壁铝合金零件热处理变形控制工艺,对提高其加工质量和性能具有重要意义。
二、热处理对薄壁铝合金零件的影响1. 热处理的作用薄壁铝合金在热处理过程中会发生晶粒细化、消除应力、提高硬度等作用。
热处理可以改善铝合金的力学性能和耐腐蚀性能,提高其整体性能。
2. 热处理引起的变形然而,薄壁铝合金零件在热处理过程中容易发生变形。
主要表现为拉伸、翘曲、翻边等变形,给后续加工和使用带来了一定的困扰。
如何控制热处理过程中的变形,成为了当前亟待解决的问题。
目前,针对薄壁铝合金零件热处理变形控制工艺的研究主要集中在以下几个方面:1. 工艺优化通过对热处理工艺参数的优化调整,如回火温度、保温时间、冷却速度等,来控制薄壁铝合金零件的变形,取得了一定的成果。
2. 材料选择选择合适的铝合金材料,具有良好的热处理性能和变形抗性,可以减少热处理过程中的变形。
3. 模具设计合理设计热处理模具,对薄壁铝合金零件进行支撑和定位,可以有效减少变形。
然而,目前对于薄壁铝合金零件的热处理变形控制工艺研究还存在许多不足之处,尚未形成系统和完善的工艺方案。
1. 完善工艺方案进一步深入研究和实验,总结和形成一套完善的薄壁铝合金零件热处理变形控制工艺方案,为实际生产提供可靠的技术支持。
2. 开展多学科交叉研究尝试将材料学、机械工程、热处理工艺等多学科知识相结合,寻找更全面、更有效的热处理变形控制方案。
3. 推动产学研深度合作加强与企业的合作,充分借鉴和应用实际生产中的经验与需求,推动科研成果转化和工艺优化。
通过以上努力,相信在不久的将来,薄壁铝合金零件热处理变形控制工艺将迎来一次重要的突破和进步,为相关领域的发展做出更大的贡献。
铝型材加工中心外壳变形的原因是什么

铝型材加工中心外壳变形的原因是什么铝合金外壳的加工变形,特别是薄壁外壳,是一个常见的技术问题。
因此,我们的铝型材加工中心工厂须分析变形的原因,然后实行相应的对策来防止变形。
1.铝壳的材料等级和结构多而杂性会影响外壳的变形CNC加工铝壳的变形和外形的多而杂性.纵横比与壁厚有关,直接关系到材料的刚度和稳定性。
所以,在设计产品的铝壳时,应尽量削减这些因素对工件变形的影响。
特别是在大型零件外壳加工定制中,结构应合理。
加工前应严格把握铝合金坯料的硬度和孔隙率,以保证坯料的质量,削减由此产生的工件变形。
2.加工中心加工夹具引起的铝壳变形铝壳加工和材料坯料夹紧时,应先选择正确的夹紧面,然后依据夹紧面的位置选择合适的夹紧力。
因此,夹紧表面和应力表面应尽可能全都,以便夹紧力作用于工件。
当多个方向的夹紧力作用于工件时,应考虑夹紧力的挨次。
应先施加夹紧力,使工件与支架接触,不易过大。
紧要用于平衡切削力的夹紧力应在后续工序中使用。
3.铝壳加工参数引起的变形在加工中心机床的切割过程中,外壳受到切割力的影响,在力的方向上产生相应的弹性变形,即加工行业。
应实行相应的措施来处理加工参数和刀具选择。
精加工需要锋利的刀具。
一方面可以削减刀具与工件摩擦形成的阻力,另一方面可以提高刀具切割工件时的散热效果。
从而削减工件上残留的内应力。
单刃铣削法通常用于铣削薄壁套管零件的大表面。
刀具参数接受较大的主偏角和较大的前角,以降低切削阻力。
由于这个工具很轻.在生产中快,削减了薄壁零件的变形,广泛应用于生产。
在薄壁铝壳的定制加工过程中,加工过程中切削力尺寸的合理刀具角度.加工过程中产生的热变形和工件表面的微观质量是特别紧要的。
刀具前角的大小计划了刀具的切割变形和前角的锐度。
大前角削减了切割变形和摩擦,但假如前角过大,刀具楔形角度减小,刀具强度减弱,刀具散热差,磨损加速度加快。
因此,在加工铝合金薄壁腔时,一般接受高速工具和硬质合金工具。
正确选择工具是处理铝壳工件变形的关键。
铝合金零件加工变形原因分析及工艺控制措施研究

97摘要:在现代化工业发展的进程下,铝合金已经成为制造行业中被广泛应用的一类金属结构材料,本文介绍了铝合金零件加工变形的主要原因,以及避免零件变形的工艺措施,以期进一步提升铝合金零件的精度,为我国制造业的发展打下良好的基础,希望能够给读者带来启发。
关键词:铝合金零件;加工变形原因;工艺控制措施由于铝合金材料具备耐腐蚀性强、强度高、切削加工性好等特点,现阶段,铝合金材料已经被广泛应用于各类轻量化的机械产品生产设计当中,但受铝合金材料导热性好、线膨胀系数大等因素的影响,在铝合金零件加工过程中,如何避免零件变形已经成为提升我国工业化产业进程的关键性因素之一。
一、造成铝合金零件加工变形的主要原因对当前铝合金零件的变形原因加以统计可以发现,铝合金零件的材料物理性能、零件结构形状、定位方式、切削液使用等情况都可能引发零件的机械加工变形,此时对变形原因进行研究发现受力、热作用、装夹以及定位都是造成变形情况出现的关键性因素。
(一)受力的影响在制作铝合金零件毛坯的过程中,无论毛坯的初始形状如何,在冶炼过程中,毛坯的内部都会出现应力聚集的情况,并且在将毛坯加工成零件之前,这些聚集的应力会处于暂时平衡的状态,然而在后续削切加工成零件的过程中,毛坯内部结构的连续性被破坏,内部的应力平衡也被打破,应力在释放过程中造成零件的变形。
此外,在利用刀具对毛坯进行切削加工的过程中,刀具的前刀切面会对被切的金属造成一定的挤压,进而令铝合金零件产生一定的塑性以及弹性变形。
(二)热作用的影响铝合金零件在加工的过程中,不可避免地会因为毛坯与刀具、切屑之间的剧烈摩擦产生大量的切削热,由于铝合金材料具备极好的导热性,若在实际加工过程中,加工人员不能将热量及时导出,就可能会导致工件变形情况的出现。
(三)装夹以及定位的影响在铝合金零件加工过程中,若加工人员在工件装夹定位的过程中,没有正确地控制夹紧力的大小,或者零件的装夹位置不够科学,都可能导致零件产生局部的弹性变形,并且变形的情况会在夹紧力撤去后暴露出来。
铝合金材料加工变形控制对策的分析

铝合金材料加工变形控制对策的分析摘要:铝合金材料能够适用于各种高温环境,耐高温性能非常高,且具有很强的导电性能,对施工环境的要求不是很高。
但是在对铝合金材料进行安装与应用的时候,仍然存在着诸多的问题,在温度适宜的情况下,铝合金材料内部应力值变化非常大,在这个时候,不能对正在进行应力值变化的铝合金材料进行内部观察。
通常来说,铝合金材料一旦出现应力值变化,那么就会持续保持在这一状态,适量的清除铝合金材料后,能解决内部应力值变化问题,使其内部的应力位置重新分布,从而使铝合金零件出现严重变形。
关键词:铝合金;材料;加工变形;控制措施;分析1导言随着建筑行业的发展,人们对原材料的质量要求更高,这使得专业人员不断追求对原材料性能的优化。
因为铝合金材料耐腐蚀性高,具有良好的导热性能,因此被广泛的应用于现代制造业中,并作为建筑行业与生活设备加工领域常见的材料之一。
随着铝合金材料在现代工业中的广泛应用,关于铝合金材料的研究不断增加,有研究表明,铝合金材料在高温与高热环境下具有较好的适应性。
但从实际情况来看,该材料在加工过程中容易出现材料变形情况。
在加工过程中,由于不能对铝合金材料内部应力值活动时的内部进一步观察,难以在短时间内解除采取措施处理,清除铝合金材料后,内应力值发生变化,造成铝合金材料变形。
2铝合金材料加工变形的研究前提铝合金材料本身具有很多的优势,如重量比较轻、有较高的防腐性能以及导热性等。
通过对铝合金材料材质的分析与研究可以得知,这一材料耐高温性比较强,可以适应各种高温环境。
不过,在对铝合金材料进行应用加工的时候,仍然会出现一些问题,比如铝合金的变形问题。
导致铝合金材料在加工时出现变形的因素有很多种,在进行加工的时候,因为加工部件内部的组织结构不均匀,所以铝合金材料内部压力会发生一定程度的变化,在材料内部压力变化的时候,部件内部的平衡将会被打破,部件内部的组织结构也会出现变化,且会受到外部作用力的影响,从而导致铝合金材料出现变形,严重影响铝合金材料质量,使其使用寿命大大降低。
控制薄壁壳体铝合金材料变形车削工艺
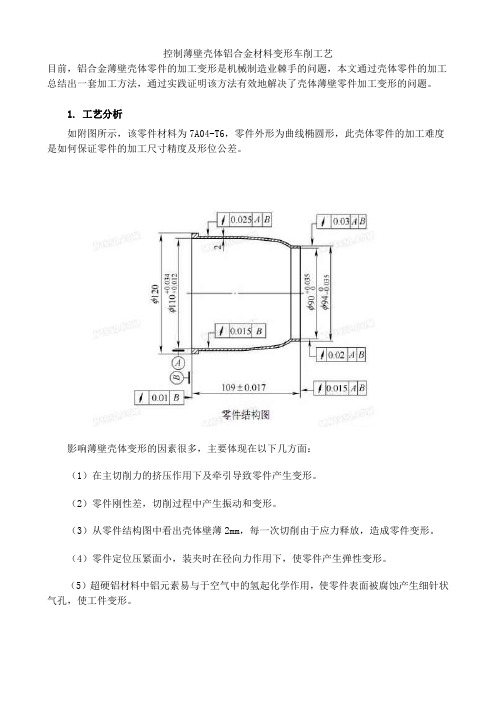
控制薄壁壳体铝合金材料变形车削工艺目前,铝合金薄壁壳体零件的加工变形是机械制造业棘手的问题,本文通过壳体零件的加工总结出一套加工方法,通过实践证明该方法有效地解决了壳体薄壁零件加工变形的问题。
1. 工艺分析如附图所示,该零件材料为7A04-T6,零件外形为曲线椭圆形,此壳体零件的加工难度是如何保证零件的加工尺寸精度及形位公差。
影响薄壁壳体变形的因素很多,主要体现在以下几方面:(1)在主切削力的挤压作用下及牵引导致零件产生变形。
(2)零件刚性差,切削过程中产生振动和变形。
(3)从零件结构图中看出壳体壁薄2mm,每一次切削由于应力释放,造成零件变形。
(4)零件定位压紧面小,装夹时在径向力作用下,使零件产生弹性变形。
(5)超硬铝材料中铝元素易与于空气中的氢起化学作用,使零件表面被腐蚀产生细针状气孔,使工件变形。
2. 解决方案通过以上分析,造成薄壁壳体零件加工变形的主要因素是切削振动、切削力、加工应力及夹紧力,因此通过以下方法有效地减小变形。
(1)合理的选择加工刀具控制变形。
刀钝会使零件主切削抗力加大,零件轴向压力加大,造成零件变形。
刀具切削刃太锋利,虽说有利于切削,但易加速刀具磨损,将零件拉向切削力的反方向,同样使零件变形。
经实践粗加工时:刀具选用R形断屑槽,前角γo=20°~25°,后角αo=6°~10°;主偏角κr=91°~93°;负偏角κ'r=6°~8°;主要是减小刀具摩擦及振动。
精加工时:前角γo=25°~30°,后角ao=10°~12°;主偏角κr=45°~90°,负偏角κ'r=10°~15°;主要是减小径向切削力,避免振动,并且加宽了主切削刃,从而减小了单位长度上的负荷,刀尖角大,散热快。
刃倾角λs=5°~10°,粗加工取小值,精加工取大值,用来弥补法向前角大而引起刀刃强度差的缺陷。
- 1、下载文档前请自行甄别文档内容的完整性,平台不提供额外的编辑、内容补充、找答案等附加服务。
- 2、"仅部分预览"的文档,不可在线预览部分如存在完整性等问题,可反馈申请退款(可完整预览的文档不适用该条件!)。
- 3、如文档侵犯您的权益,请联系客服反馈,我们会尽快为您处理(人工客服工作时间:9:00-18:30)。
铝合金薄壁件加工中变形的因素分析与控制方法
一般认为,在壳体件、套筒件、环形件、盘形件、轴类件中,当零件壁厚与内径曲率半径(或轮廓尺寸)相比小于1:20时,称作为薄壁零件。
这一类零件的共同特点是受力形式复杂,刚度低,加工时极易引起误差变形或工件颤振,从而降低工件的加工精度。
薄壁零件因其制造难度极大,而成为国际上公认的复杂制造工艺问题。
一、薄壁件加工变形因素分析
薄壁件由于刚度低,去除材料率大,在加工过程中容易产生变形,对装夹工艺要求高,使加工质量难以保证。
薄壁类零件在加工中引起变形的因素有很多,归纳总结有以下几个方面:
1、工件材料的影响
铝合金作为薄壁件最理想的结构材料,与其他金属材料相比,具有切削加工性好的特点。
但由于铝合金导热系数高、弹性模量小、屈强比大、极易产生回弹现象,大型薄壁件尤为显著。
因此,在相同载荷情况下,铝合金工件产生的变形要比钢铁材料的变形大,同时铝合金材料具有硬度小、塑性大和化学反应性高等性质,在其加工中极易产积屑瘤,从而影响工件的表面质量和尺寸精度。
2、毛坯初始残余应力的影响
薄壁件加工中的变形与毛坯内部的初始残余应力有直接的关系,同时由于切削热和切削力的影响,使工件和刀具相接触处的材料产生不能回弹的塑性变形。
这种永久性的变形一旦受到力的作用就会产生残余应力,而在加工过程中,一旦破坏了毛坯的残余应力,工件内部为达到新的平衡状态而使应力重新分布,从而造成了工件的变形。
3、装夹方式的影响
在加工中夹具对工件的夹、压而引起的变形直接影响着工件的表面精度,同时如果由于夹紧力的作用点选择不当而产生的附加应力,也将影响工件的加工精度。
其次,由于夹紧力与切削力产生的耦合效应,也将引起工件残余应力的重新分布,造成工件变形。
4、切削力和切削热的影响
切削力是影响薄壁件变形的一个重要因素。
切削力会导致工件的回弹变形,产生不平度,当切削力达到工件材料的弹性极限会导致工件的挤压变形。
在切削加工过程中,刀具与工件之间的摩擦所作的功,材料在克服弹性、塑性变形过程中所做的功绝大部分转化为加工中的切削热,从而导致工件的各部分的温度差,
使工件产生变形。
5、加工路线的因素
金属材料在加工过程中由于受到机械力和切削热等因素产生的永久性变形一旦受到邻近部分金属材料的阻挡就势必产生残余应力,因此残余应力对工件变形的影响很大程度上取决于加工路线的选取。
路径不同,产生的新的残余应力与原有残余应力的耦合顺序和祸合效果不同,将引起工件变形的不同。
二、铝合金薄壁件加工变形的控制途径
1、消除和均匀内化残余应力
薄壁件在加工中随着金属材料被切除,一方面会带来原有残余应力的释放,另一方面会在已加工表面产生新的残余应力,进而会影响工件的加工质量和精度。
生产中,如能做到把毛坯残余应力降低或均匀化,则可极大程度降低工件的加工变形。
目前,在生产实践中,為达到此目的,采用在原材料制作中采取化学成分控制、熔炼浇铸和挤压成型、固溶淬火和时效处理等方法。
2、优化刀具路径
薄壁件加工中,走刀路径的不同,残余应力将产生不同的作用效果。
如果走刀路径选取的不合理,在高速加工中会出现由于切削载荷突变,给机床、工件和刀具带来冲击,严重时会损坏。
在实际加工中,刀具路径的选取可遵循以下优化规则:
(1)采用螺旋或圆弧进刀方法,使刀具渐入零件,保证加工中不产生突变的切削力,减小刀具磨损,延长使用寿命。
(2)尽量采用顺铣,以便保证加工过程平稳、工件表面质量好、刀具磨损小、不产生过切现象等。
(3)要保证切削的连续平稳性,切削速度要连续,不要有大幅度的突变。
(4)选取小的轴向切深量,以减小切削力,降低切削热,保障排屑的通畅。
(5)保证切削方向的改变时平稳逐渐的,刀具轨迹应避免尖角,课采用圆弧或其它曲线来代替。
3、改进装夹方式
夹具是在加工中对工件起定位和夹紧作用的装置,而在影响薄壁件加工变形的诸多因素中,装夹应力引起的变形约占20%-60%。
因此,铝合金薄壁件高速加工中,夹具除了应满足夹紧和定位的基本要求外,还应考虑其刚性差、易变形
等因素。
目前,在国外发达国家,整在使用电控永磁吸盘装夹,它在高速加工中具有相当重要的作用。
4、选择合理的切削参数
高速加工中的切削三要素(切削速度、背吃刀量、每齿进给量)对被加工工件的质量和精度有着直接的影响。
在高速切削加工中,随着切削速度的增大,切削力减小,切削温度升高,摩擦系数减小,但当切削速度Vc>1500m/min时,将会增加切削力,增大机床功率消耗。
在薄壁件数控加工中,为解决易变形问题提出了基于四步(确定边界点、确定关键区域、修改切削参数、修改刀位文件)的进给量局部优化法。
在切削参数选择时,应该尽量选取小的每齿进给量和切削深度,可以通过提高切削速度的方式提高进给速度。
每齿进给量越小,工件表面残留高度越低,表面粗糙度值越低。
所以在高速切削中,提高零件表面质量的一个有效途径是减小进给量,但也不宜过小,进给量过小,会增加刀具刃口圆弧半径对工件加工表面的挤压,增加冷硬程度和残余应力。