铝合金零件加工为什么会变形
铝合金零件的加工变形与工件表面变黑的原因
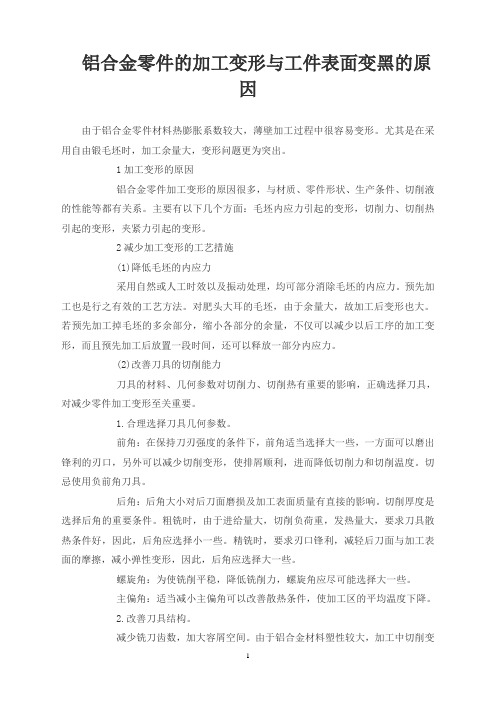
铝合金零件的加工变形与工件表面变黑的原因由于铝合金零件材料热膨胀系数较大,薄壁加工过程中很容易变形。
尤其是在采用自由锻毛坯时,加工余量大,变形问题更为突出。
1加工变形的原因铝合金零件加工变形的原因很多,与材质、零件形状、生产条件、切削液的性能等都有关系。
主要有以下几个方面:毛坯内应力引起的变形,切削力、切削热引起的变形,夹紧力引起的变形。
2减少加工变形的工艺措施(1)降低毛坯的内应力采用自然或人工时效以及振动处理,均可部分消除毛坯的内应力。
预先加工也是行之有效的工艺方法。
对肥头大耳的毛坯,由于余量大,故加工后变形也大。
若预先加工掉毛坯的多余部分,缩小各部分的余量,不仅可以减少以后工序的加工变形,而且预先加工后放置一段时间,还可以释放一部分内应力。
(2)改善刀具的切削能力刀具的材料、几何参数对切削力、切削热有重要的影响,正确选择刀具,对减少零件加工变形至关重要。
1.合理选择刀具几何参数。
前角:在保持刀刃强度的条件下,前角适当选择大一些,一方面可以磨出锋利的刃口,另外可以减少切削变形,使排屑顺利,进而降低切削力和切削温度。
切忌使用负前角刀具。
后角:后角大小对后刀面磨损及加工表面质量有直接的影响。
切削厚度是选择后角的重要条件。
粗铣时,由于进给量大,切削负荷重,发热量大,要求刀具散热条件好,因此,后角应选择小一些。
精铣时,要求刃口锋利,减轻后刀面与加工表面的摩擦,减小弹性变形,因此,后角应选择大一些。
螺旋角:为使铣削平稳,降低铣削力,螺旋角应尽可能选择大一些。
主偏角:适当减小主偏角可以改善散热条件,使加工区的平均温度下降。
2.改善刀具结构。
减少铣刀齿数,加大容屑空间。
由于铝合金材料塑性较大,加工中切削变形较大,需要较大的容屑空间,因此容屑槽底半径应该较大、铣刀齿数较少为好。
例如,φ20mm以下的铣刀采用两个刀齿;φ30-φ60mm的铣刀采用三个刀齿较好,以避免因切屑堵塞而引起薄壁铝合金零件的变形。
精磨刀齿:刀齿切削刃部的粗糙度值要小于Ra=0.4um。
铝合金零件加工变形原因分析及工艺控制对策探讨
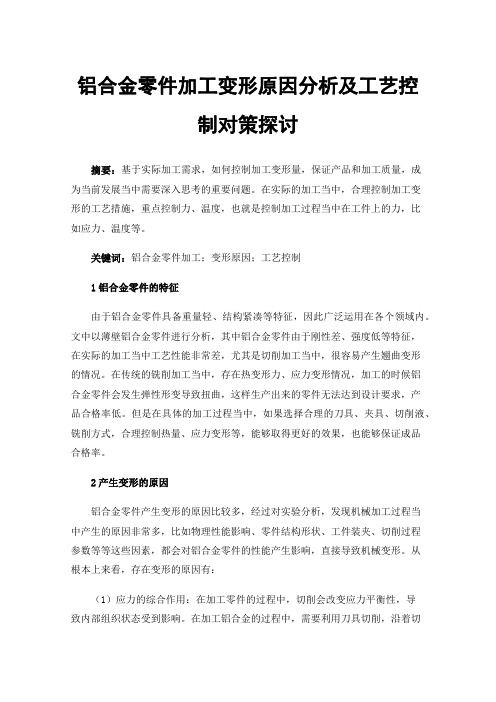
铝合金零件加工变形原因分析及工艺控制对策探讨摘要:基于实际加工需求,如何控制加工变形量,保证产品和加工质量,成为当前发展当中需要深入思考的重要问题。
在实际的加工当中,合理控制加工变形的工艺措施,重点控制力、温度,也就是控制加工过程当中在工件上的力,比如应力、温度等。
关键词:铝合金零件加工;变形原因;工艺控制1铝合金零件的特征由于铝合金零件具备重量轻、结构紧凑等特征,因此广泛运用在各个领域内。
文中以薄壁铝合金零件进行分析,其中铝合金零件由于刚性差、强度低等特征,在实际的加工当中工艺性能非常差,尤其是切削加工当中,很容易产生翘曲变形的情况。
在传统的铣削加工当中,存在热变形力、应力变形情况,加工的时候铝合金零件会发生弹性形变导致扭曲,这样生产出来的零件无法达到设计要求,产品合格率低。
但是在具体的加工过程当中,如果选择合理的刀具、夹具、切削液、铣削方式,合理控制热量、应力变形等,能够取得更好的效果,也能够保证成品合格率。
2产生变形的原因铝合金零件产生变形的原因比较多,经过对实验分析,发现机械加工过程当中产生的原因非常多,比如物理性能影响、零件结构形状、工件装夹、切削过程参数等等这些因素,都会对铝合金零件的性能产生影响,直接导致机械变形。
从根本上来看,存在变形的原因有:(1)应力的综合作用:在加工零件的过程中,切削会改变应力平衡性,导致内部组织状态受到影响。
在加工铝合金的过程中,需要利用刀具切削,沿着切削方向铝合金材料会产生变形问题,同时也会牵制相邻里层,在铝合金材料表面产生残余拉应力,在里层会产能参与压应力,在综合作用的影响下,铝合金零件因此出现变形问题。
(2)残余拉应力:在切削工作中,因为摩擦阻力的影响,引发塑性变形问题,在铝合金表面产生较多的热量,导致材料因此膨胀,如果里层温度比较低,表层发生膨胀问题之后,会阻挡里层材料,导致表层金属产生热应力。
如果热应力超过了铝合金材料屈服极限,将会引发压缩塑性变形问题。
铸铝为变形原因
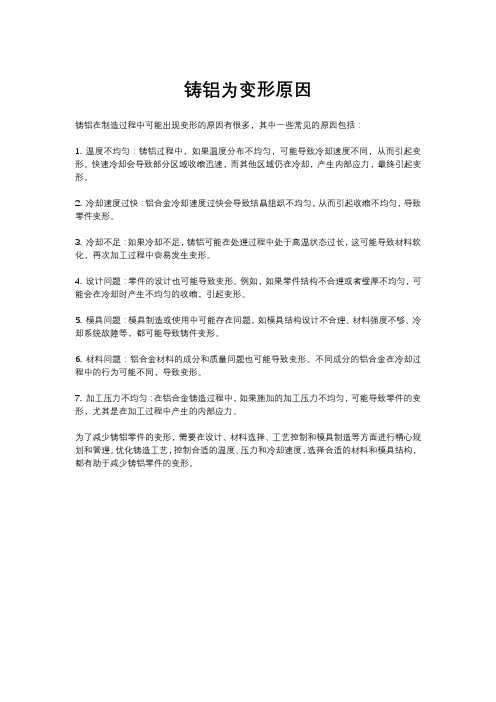
铸铝为变形原因
铸铝在制造过程中可能出现变形的原因有很多,其中一些常见的原因包括:
1. 温度不均匀:铸铝过程中,如果温度分布不均匀,可能导致冷却速度不同,从而引起变形。
快速冷却会导致部分区域收缩迅速,而其他区域仍在冷却,产生内部应力,最终引起变形。
2. 冷却速度过快:铝合金冷却速度过快会导致结晶组织不均匀,从而引起收缩不均匀,导致零件变形。
3. 冷却不足:如果冷却不足,铸铝可能在处理过程中处于高温状态过长,这可能导致材料软化,再次加工过程中容易发生变形。
4. 设计问题:零件的设计也可能导致变形。
例如,如果零件结构不合理或者壁厚不均匀,可能会在冷却时产生不均匀的收缩,引起变形。
5. 模具问题:模具制造或使用中可能存在问题,如模具结构设计不合理、材料强度不够、冷却系统故障等,都可能导致铸件变形。
6. 材料问题:铝合金材料的成分和质量问题也可能导致变形。
不同成分的铝合金在冷却过程中的行为可能不同,导致变形。
7. 加工压力不均匀:在铝合金铸造过程中,如果施加的加工压力不均匀,可能导致零件的变形,尤其是在加工过程中产生的内部应力。
为了减少铸铝零件的变形,需要在设计、材料选择、工艺控制和模具制造等方面进行精心规划和管理。
优化铸造工艺,控制合适的温度、压力和冷却速度,选择合适的材料和模具结构,都有助于减少铸铝零件的变形。
铝合金零件加工为什么会变形

铝合金零件加工为什么会变形
因为铝合金零件加工的加工过程,该类零件一般由铝合金板整体加工而成,该类零件金属去除量大、刚性低,在加工过程中会因残余应力、装夹力、切削运动三方面因素引起变形。
1 残余应力
金属材料在形成过程中,金属晶体的排列不是理想状态的整齐排列,晶体的大小和形状不尽相同,存在原始的残余应力,随着时间缓慢释放,产生一定的形变。
另外,在精密零件加工过程中,金属切削的塑性变形和刀具与工件间的摩擦热,使已加工的表面和里层温差较大,产生较大的热应力,形成热应力塑性变形。
金属切削过程中产生的变形并不是单一的原因造成的,往往是几种原因组合作用的结构,而且这种组合作用在加工过程中不是一成不变的,随着加工进行的不断变化,究竟哪一种原因对变形的影响最大,很难进行判断,只能从引起变形的原因入手,采取相应的工艺方法,尽量减小加工变形。
2 装夹力
由于铝合金薄壁腔体零件的壁比较薄,无论采用台虎钳装夹还是卡盘装夹,都会产生横向或径向的装夹力,不可避免会产生装夹变形。
装夹变形程度跟装夹力的大小有关,装夹力如果很大,就会形成不可恢复的塑性变形;如果较小,就会形成弹性变形,弹性变形会在零件卸载后恢复,但切削加工是在弹性变形没有恢复的时候进行的,单一弹性变形的恢复会为加工后的零件带来新的变形。
3 切削运动
切削过程是刀具和工件相互作用的过程,该过程使刀具从工件上去除部分材料。
切削运动使材料的晶体颗粒间产生挤压、拉伸、拉断等现象,这些现象会使晶体的原子间产生位移,形成不可恢复的塑性变形。
铝合金零件加工变形的解决方法
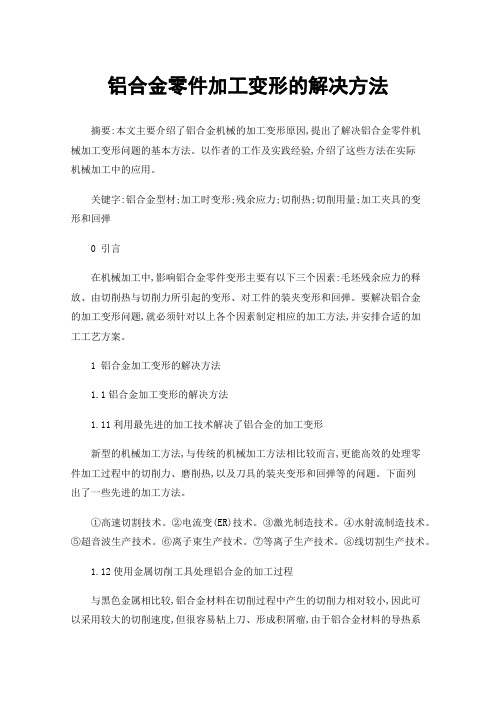
铝合金零件加工变形的解决方法摘要:本文主要介绍了铝合金机械的加工变形原因,提出了解决铝合金零件机械加工变形问题的基本方法。
以作者的工作及实践经验,介绍了这些方法在实际机械加工中的应用。
关键字:铝合金型材;加工时变形;残余应力;切削热;切削用量;加工夹具的变形和回弹0 引言在机械加工中,影响铝合金零件变形主要有以下三个因素:毛坯残余应力的释放、由切削热与切削力所引起的变形、对工件的装夹变形和回弹。
要解决铝合金的加工变形问题,就必须针对以上各个因素制定相应的加工方法,并安排合适的加工工艺方案。
1 铝合金加工变形的解决方法1.1铝合金加工变形的解决方法1.11利用最先进的加工技术解决了铝合金的加工变形新型的机械加工方法,与传统的机械加工方法相比较而言,更能高效的处理零件加工过程中的切削力、磨削热,以及刀具的装夹变形和回弹等的问题。
下面列出了一些先进的加工方法。
①高速切割技术。
②电流变(ER)技术。
③激光制造技术。
④水射流制造技术。
⑤超音波生产技术。
⑥离子束生产技术。
⑦等离子生产技术。
⑧线切割生产技术。
1.12使用金属切削工具处理铝合金的加工过程与黑色金属相比较,铝合金材料在切削过程中产生的切削力相对较小,因此可以采用较大的切削速度,但很容易粘上刀、形成积屑瘤,由于铝合金材料的导热系数较高,在切削时由切屑和零件导出的热量都较多,且切削区温度也较低,所以虽然刀具耐用度较高,但由于零件本身的温升也相对较快,很容易引起变形的产生。
因此,通过选用合适的刀具材料,在原刀具材料的基础上选用合适的刀具角度,并提高刀具表面的粗糙度的要求,对降低切削力和切削热十分有效。
1.13利用热处理解决相合金的加工变形解决铝合金型材加工应力问题的热处理方式,一般为去内部应力退火、再结品退火、均匀性退火及时效。
1.14利用冷处理解决铝合金的加工变形解决铝合金加热变形问题的冷处理技术,只要有振动时效和人工冷校形。
由于冷处理工艺节能、制造周期复、制造代价小,所以在制造流程中使用最广泛。
铝合金构件的变形矫正方法大全

铝合金构件的变形矫正方法大全,附有实例目前铝合金在产品加工制造行业被广泛应用。
铝合金产品在加工制造过程中由于受到外力或焊接应力的影响,通常会产生一定程度的变形,这些变形通常都要进行矫正,而使其符合产品质量要求。
实践证明,多数变形的构件是可以矫正的。
矫正的原理都是设法造成新的变形来达到抵消已经发生的变形。
在生产实际过程中普遍应用的矫正方法,主要有机械矫正、手工矫正和火焰矫正,因此要针对产品不同的结构和变形程度合理选择最佳的矫正方法,以获得最佳的矫正效果。
铝合金构件变形的原因(1)原材料在加工过程中产生的变形由于原材料在挤压生产过程中产生的残余应力而引起的变形。
如:挤压过程中冷却速度不一致、挤压设备调试失常等。
(2)在产品制造过程中产生的变形主要原因是外力影响。
如剪切过程中产生的剪切挤压应力、热切割过程中热胀冷缩产生的收缩应力等。
(3)焊接过程中产生的变形主要原因是焊缝周围产生的横向和纵向收缩应力,通常称为焊接应力引起的变形。
(4)构件变形的实质不论构件发生何种变形,其主要原因都是由于其内部存在不同程度和不同形式的残余应力,使其结构组织中一部分纤维变长受到周围的压应力,另一部分纤维变短受到周围的拉应力,从而造成了金属材料的变形。
矫正原理及常用方法矫正的原理就是通过外力或局部加热,使得较长的纤维缩短,较短的纤维伸长,最后使得各层的纤维长度趋于一致,或达到我们要求的纤维长度,从而消除变形或使变形减少到规定的范围之内。
各种矫正方法在现场使用过程中要根据其构件结构特点、变形形式、工件大小等不同情况做相应的选择,必要时还需采取多种矫正形式相结合的综合矫正法。
其中火焰矫正是应用最为广泛的一种方法,其对于大型构件和自身强度较大构件的变形矫正效果最好,但火焰矫正也是一门较难掌握的矫正方法,如加热位置、温度控制、冷却方式不当还会造成构件新的更大变形,甚至导致产品的报废。
因此,火焰矫正作业人员除要有丰富的实践经验外,还需掌握铝合金的热处理性能。
铝合金薄壁件加工变形控制
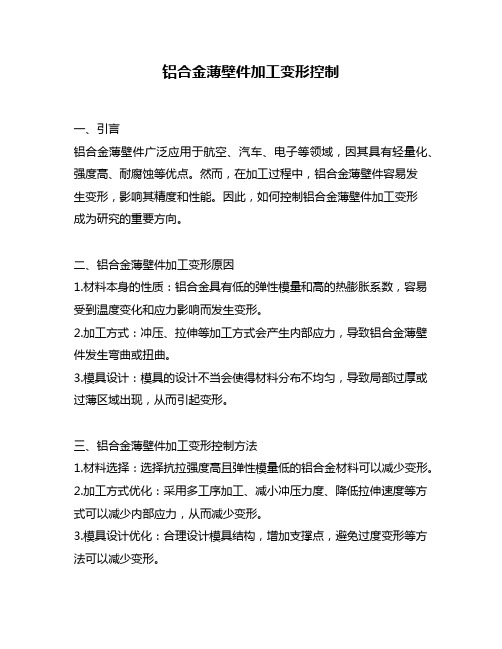
铝合金薄壁件加工变形控制一、引言铝合金薄壁件广泛应用于航空、汽车、电子等领域,因其具有轻量化、强度高、耐腐蚀等优点。
然而,在加工过程中,铝合金薄壁件容易发生变形,影响其精度和性能。
因此,如何控制铝合金薄壁件加工变形成为研究的重要方向。
二、铝合金薄壁件加工变形原因1.材料本身的性质:铝合金具有低的弹性模量和高的热膨胀系数,容易受到温度变化和应力影响而发生变形。
2.加工方式:冲压、拉伸等加工方式会产生内部应力,导致铝合金薄壁件发生弯曲或扭曲。
3.模具设计:模具的设计不当会使得材料分布不均匀,导致局部过厚或过薄区域出现,从而引起变形。
三、铝合金薄壁件加工变形控制方法1.材料选择:选择抗拉强度高且弹性模量低的铝合金材料可以减少变形。
2.加工方式优化:采用多工序加工、减小冲压力度、降低拉伸速度等方式可以减少内部应力,从而减少变形。
3.模具设计优化:合理设计模具结构,增加支撑点,避免过度变形等方法可以减少变形。
四、铝合金薄壁件加工变形控制实践1.材料选择:选择抗拉强度高的6061-T6铝合金材料进行试验。
结果表明,该材料相较于普通铝合金材料能够有效降低变形。
2.加工方式优化:采用多工序加工、缩短冲压时间、降低拉伸速度等方式进行试验。
结果表明,这些方法能够有效减少内部应力和变形。
3.模具设计优化:采用增加支撑点、增加模具刚度等方式进行试验。
结果表明,这些方法能够有效避免过度变形。
五、结论通过以上实践和研究,我们可以得出以下结论:1.选择抗拉强度高且弹性模量低的铝合金材料可以减少变形。
2.采用多工序加工、缩短冲压时间、降低拉伸速度等方式可以减少内部应力和变形。
3.合理设计模具结构,增加支撑点,避免过度变形等方法可以减少变形。
六、展望随着科技的不断进步,铝合金薄壁件加工变形控制的研究将会更加深入。
我们可以通过模拟分析、人工智能等方式来预测和控制铝合金薄壁件的变形,从而进一步提高其精度和性能。
试论铝合金材料加工变形控制措施

试论铝合金材料加工变形控制措施铝合金材料在工业生产中是应用比较广泛的加工材料,其具有重量轻、耐腐蚀性强、导热性好等优点,在工业制造中起到了非常重要作用。
在进行铝合金材料的加工中,会受到多种因素的影响而导致零件变形,这与使用的零件加工技术、加工设备、自然环境等因素有着直接的关系。
要想提高铝合金材料的加工质量,避免变形现象的发生,就需要掌握导致材料加工变形的原因,并采取针对性的措施去处理,才能提高加工效果,保证加工质量。
标签:铝合金材料;加工变形;控制措施一、铝合金加工变形因素导致铝合金材料在加工的过程中出现变形情况的因素有很多,其中主要有机床、夹具、切削参数、刀具以及切割技术等外界因素,还有温度、通风等自然因素,此外,来有一部分因素是来自于铝合金材料自身,铝合金材料的自身质量不合格也是导致其在加工时出现变形情况的主要原因导致其出现变形的原因主要有定位精度以及刚度,其中定位与精度给铝合金材料带来的影响要远远高于刚度;夹具因素给铝合金材料带来的影响主要有夹具的尺寸不合理、夹紧力过高等,这两种情况都会导致铝合金材料出现变形的现象;刀具因素导致铝合金材料出现变形情况的原因有很多,其中主要原因有刀具的各种形状参数、刀具的材质、刚性以及平衡性等等;切削参数是导致铝合金材料在加工过程中出现变形情况最为严重的一种因素。
以上这些都是导致铝合金材料在加工的过程中出现变形情况的主要原因,要想使铝合金材料在加工过程中出现变形情况的几率大幅下降,就必须要加强对以上因素的重视,尽可能的避免其给铝合金材料的加工带来影响。
二、挤压铝合金在机械加工过程中产生变形的主要原因和特点1、铝合金在机械加工过程中产生变形的主要原因在过去科学技术还不如现在发达的时候,那个时候的技术人员使用传统的加工方法对铝合金材料进行加工处理,冷热变形是导致零件变形的重要原因,在实践操作中我们得知,在进行切削加工的过程当中,切削时温度过高和切削时用力太大是导致零件变形的主要原因,对零件的机械加工都包含有,车,铣,饱,磨,膛等,在机械技工过程中直接导致铝合金变形的主要原因有,在进行按压操作时,导致零件的温度过高,在进行挤压的操作中挤压的速度过慢,材料在挤压机的出口温度达不到凝固状态,凝固状态,导致零件达不到凝固强化的基本效果,还有就是材料位置处的通风不佳导致风量不够用,引起零件在加工的过程当中,零件的冷却速度过慢,从而导致铝合金挤压产生变形,或者是工艺在时期内的效用不恰当,热风循环的不流畅,造成牵引机发生故障,使材料表面被压弯,最后一种是没有运用正确的方式方法进行模具的设计,造成模式在使用时设计上的不合理,在挤压下发生抖动造成材料出现波纹。
关于铝合金加工变形控制分析
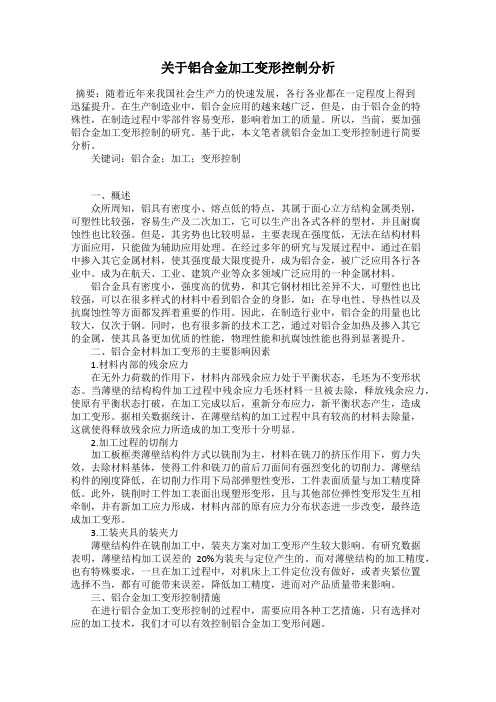
关于铝合金加工变形控制分析摘要:随着近年来我国社会生产力的快速发展,各行各业都在一定程度上得到迅猛提升。
在生产制造业中,铝合金应用的越来越广泛,但是,由于铝合金的特殊性,在制造过程中零部件容易变形,影响着加工的质量。
所以,当前,要加强铝合金加工变形控制的研究。
基于此,本文笔者就铝合金加工变形控制进行简要分析。
关键词:铝合金;加工;变形控制一、概述众所周知,铝具有密度小、熔点低的特点,其属于面心立方结构金属类别,可塑性比较强,容易生产及二次加工,它可以生产出各式各样的型材,并且耐腐蚀性也比较强。
但是,其劣势也比较明显,主要表现在强度低,无法在结构材料方面应用,只能做为辅助应用处理。
在经过多年的研究与发展过程中,通过在铝中掺入其它金属材料,使其强度最大限度提升,成为铝合金,被广泛应用各行各业中。
成为在航天、工业、建筑产业等众多领域广泛应用的一种金属材料。
铝合金具有密度小,强度高的优势,和其它钢材相比差异不大,可塑性也比较强,可以在很多样式的材料中看到铝合金的身影,如:在导电性、导热性以及抗腐蚀性等方面都发挥着重要的作用。
因此,在制造行业中,铝合金的用量也比较大,仅次于钢。
同时,也有很多新的技术工艺,通过对铝合金加热及掺入其它的金属,使其具备更加优质的性能,物理性能和抗腐蚀性能也得到显著提升。
二、铝合金材料加工变形的主要影响因素1.材料内部的残余应力在无外力荷载的作用下,材料内部残余应力处于平衡状态,毛坯为不变形状态。
当薄壁的结构构件加工过程中残余应力毛坯材料一旦被去除,释放残余应力,使原有平衡状态打破,在加工完成以后,重新分布应力,新平衡状态产生,造成加工变形。
据相关数据统计,在薄壁结构的加工过程中具有较高的材料去除量,这就使得释放残余应力所造成的加工变形十分明显。
2.加工过程的切削力加工板框类薄壁结构件方式以铣削为主,材料在铣刀的挤压作用下,剪力失效,去除材料基体,使得工件和铣刀的前后刀面间有强烈变化的切削力。
铝合金构件的变形矫正方法大全

铝合金构件的变形矫正方法大全,附有实例目前铝合金在产品加工制造行业被广泛应用。
铝合金产品在加工制造过程中由于受到外力或焊接应力的影响,通常会产生一定程度的变形,这些变形通常都要进行矫正,而使其符合产品质量要求。
实践证明,多数变形的构件是可以矫正的。
矫正的原理都是设法造成新的变形来达到抵消已经发生的变形。
在生产实际过程中普遍应用的矫正方法,主要有机械矫正、手工矫正和火焰矫正,因此要针对产品不同的结构和变形程度合理选择最佳的矫正方法,以获得最佳的矫正效果。
铝合金构件变形的原因(1)原材料在加工过程中产生的变形由于原材料在挤压生产过程中产生的残余应力而引起的变形。
如:挤压过程中冷却速度不一致、挤压设备调试失常等。
(2)在产品制造过程中产生的变形主要原因是外力影响。
如剪切过程中产生的剪切挤压应力、热切割过程中热胀冷缩产生的收缩应力等。
(3)焊接过程中产生的变形主要原因是焊缝周围产生的横向和纵向收缩应力,通常称为焊接应力引起的变形。
(4)构件变形的实质不论构件发生何种变形,其主要原因都是由于其内部存在不同程度和不同形式的残余应力,使其结构组织中一部分纤维变长受到周围的压应力,另一部分纤维变短受到周围的拉应力,从而造成了金属材料的变形。
矫正原理及常用方法矫正的原理就是通过外力或局部加热,使得较长的纤维缩短,较短的纤维伸长,最后使得各层的纤维长度趋于一致,或达到我们要求的纤维长度,从而消除变形或使变形减少到规定的范围之内。
各种矫正方法在现场使用过程中要根据其构件结构特点、变形形式、工件大小等不同情况做相应的选择,必要时还需采取多种矫正形式相结合的综合矫正法。
其中火焰矫正是应用最为广泛的一种方法,其对于大型构件和自身强度较大构件的变形矫正效果最好,但火焰矫正也是一门较难掌握的矫正方法,如加热位置、温度控制、冷却方式不当还会造成构件新的更大变形,甚至导致产品的报废。
因此,火焰矫正作业人员除要有丰富的实践经验外,还需掌握铝合金的热处理性能。
铝合金薄壁零件的加工工艺及变形控制探讨
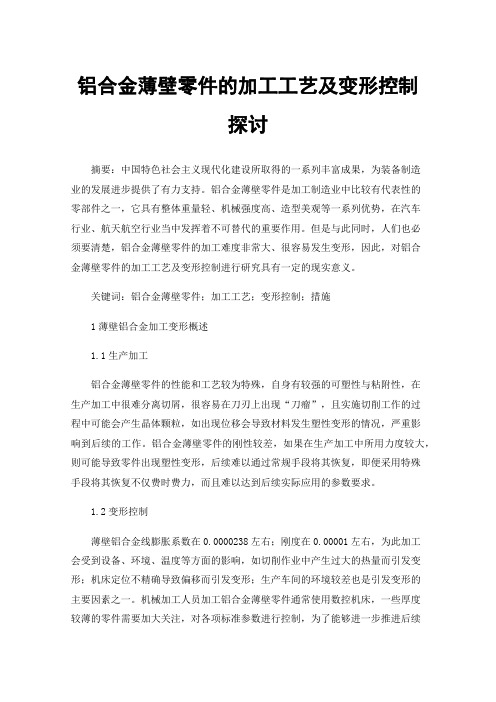
铝合金薄壁零件的加工工艺及变形控制探讨摘要:中国特色社会主义现代化建设所取得的一系列丰富成果,为装备制造业的发展进步提供了有力支持。
铝合金薄壁零件是加工制造业中比较有代表性的零部件之一,它具有整体重量轻、机械强度高、造型美观等一系列优势,在汽车行业、航天航空行业当中发挥着不可替代的重要作用。
但是与此同时,人们也必须要清楚,铝合金薄壁零件的加工难度非常大、很容易发生变形,因此,对铝合金薄壁零件的加工工艺及变形控制进行研究具有一定的现实意义。
关键词:铝合金薄壁零件;加工工艺;变形控制;措施1薄壁铝合金加工变形概述1.1生产加工铝合金薄壁零件的性能和工艺较为特殊,自身有较强的可塑性与粘附性,在生产加工中很难分离切屑,很容易在刀刃上出现“刀瘤”,且实施切削工作的过程中可能会产生晶体颗粒,如出现位移会导致材料发生塑性变形的情况,严重影响到后续的工作。
铝合金薄壁零件的刚性较差,如果在生产加工中所用力度较大,则可能导致零件出现塑性变形,后续难以通过常规手段将其恢复,即便采用特殊手段将其恢复不仅费时费力,而且难以达到后续实际应用的参数要求。
1.2变形控制薄壁铝合金线膨胀系数在0.0000238左右;刚度在0.00001左右,为此加工会受到设备、环境、温度等方面的影响,如切削作业中产生过大的热量而引发变形;机床定位不精确导致偏移而引发变形;生产车间的环境较差也是引发变形的主要因素之一。
机械加工人员加工铝合金薄壁零件通常使用数控机床,一些厚度较薄的零件需要加大关注,对各项标准参数进行控制,为了能够进一步推进后续行业的持续健康发展,需要着重考虑到设备、环境、温度等与金属材料的差异化特点,保证参数精确度符合预期的生产要求,从而有效解决加工伴有的质量问题。
2铝合金薄壁零件的加工工艺随着科技发展,中国的零部件加工技术越来越成熟,对于薄壁零部件的加工能力也在不断提升,铝合金薄壁零件是其中比较有代表性的零部件之一。
铝合金材质决定了该零部件具有比重指数小、比强度指数大的特点,而薄壁结构则导致该零部件的刚性不佳、容易变形,这给铝合金薄壁零件加工带来了一定挑战。
铝合金加工变形原因内应力

铝合金加工变形原因内应力内应力是指材料内部的各个部分之间存在的相互作用力。
在铝合金加工过程中,这些内应力往往会导致材料产生变形,影响材料的性能和使用寿命。
下面我们将从几个方面来解析铝合金加工变形的原因内应力。
铝合金的内应力主要来源于热处理过程中的冷却过程。
在热处理过程中,铝合金会经历加热和冷却的过程,而冷却过程中会产生内应力。
这是因为冷却速度不均匀,导致材料内部不同部分的温度变化不一致,从而产生内应力。
这种内应力在加工过程中会逐渐释放,导致材料产生变形。
铝合金在加工过程中还会受到外力的作用,从而产生内应力。
例如,铝合金在锻造、压力加工和拉伸等过程中,会受到外力的拉伸、压缩或剪切。
这些外力会引起材料内部各个部分之间的相互作用,从而产生内应力。
这种内应力会导致材料产生塑性变形或裂纹,影响材料的性能。
铝合金的内应力还与材料的组织结构有关。
铝合金是由铝和其他合金元素组成的,合金元素的添加会改变材料的晶体结构和组织形态。
不同的组织结构会导致材料内部存在不同的内应力分布。
例如,过大的晶粒会导致内部应力集中,从而增加材料的变形风险。
因此,在铝合金加工过程中,合理控制材料的组织结构是减少内应力的重要手段。
材料的加工温度和速度也会影响铝合金的内应力。
在加工过程中,材料的温度和速度会影响材料的变形行为和内应力的分布。
例如,高温下材料的塑性较好,容易产生较大的内应力。
而快速的冷却速度会导致材料内部产生较大的内应力。
因此,在铝合金加工过程中,合理控制加工温度和速度,可以有效减少内应力的产生。
铝合金加工变形的原因内应力主要包括热处理过程中的冷却过程、外力的作用、材料的组织结构以及加工温度和速度等因素。
了解这些因素对铝合金内应力的影响,可以有效地控制材料的变形,提高材料的性能和使用寿命。
在实际应用中,需要根据具体情况采取相应的措施,减少内应力的产生,确保铝合金的加工质量。
铝合金薄壁件加工中变形的因素分析与控制方法

铝合金薄壁件加工中变形的因素分析与控制方法一般认为,在壳体件、套筒件、环形件、盘形件、轴类件中,当零件壁厚与内径曲率半径(或轮廓尺寸)相比小于1:20时,称作为薄壁零件。
这一类零件的共同特点是受力形式复杂,刚度低,加工时极易引起误差变形或工件颤振,从而降低工件的加工精度。
薄壁零件因其制造难度极大,而成为国际上公认的复杂制造工艺问题。
一、薄壁件加工变形因素分析薄壁件由于刚度低,去除材料率大,在加工过程中容易产生变形,对装夹工艺要求高,使加工质量难以保证。
薄壁类零件在加工中引起变形的因素有很多,归纳总结有以下几个方面:1、工件材料的影响铝合金作为薄壁件最理想的结构材料,与其他金属材料相比,具有切削加工性好的特点。
但由于铝合金导热系数高、弹性模量小、屈强比大、极易产生回弹现象,大型薄壁件尤为显著。
因此,在相同载荷情况下,铝合金工件产生的变形要比钢铁材料的变形大,同时铝合金材料具有硬度小、塑性大和化学反应性高等性质,在其加工中极易产积屑瘤,从而影响工件的表面质量和尺寸精度。
2、毛坯初始残余应力的影响薄壁件加工中的变形与毛坯内部的初始残余应力有直接的关系,同时由于切削热和切削力的影响,使工件和刀具相接触处的材料产生不能回弹的塑性变形。
这种永久性的变形一旦受到力的作用就会产生残余应力,而在加工过程中,一旦破坏了毛坯的残余应力,工件内部为达到新的平衡状态而使应力重新分布,从而造成了工件的变形。
3、装夹方式的影响在加工中夹具对工件的夹、压而引起的变形直接影响着工件的表面精度,同时如果由于夹紧力的作用点选择不当而产生的附加应力,也将影响工件的加工精度。
其次,由于夹紧力与切削力产生的耦合效应,也将引起工件残余应力的重新分布,造成工件变形。
4、切削力和切削热的影响切削力是影响薄壁件变形的一个重要因素。
切削力会导致工件的回弹变形,产生不平度,当切削力达到工件材料的弹性极限会导致工件的挤压变形。
在切削加工过程中,刀具与工件之间的摩擦所作的功,材料在克服弹性、塑性变形过程中所做的功绝大部分转化为加工中的切削热,从而导致工件的各部分的温度差,使工件产生变形。
铝合金部件焊接变形的产生及控制

铝合金部件焊接变形的产生及控制发布时间:2021-11-07T09:50:04.187Z 来源:《中国科技信息》2021年10月下30期作者:赵一凡曹军营[导读] 为何使用基于铝合金在全部金属焊接工艺完成了以后会容易可能产生金属焊接典型变形,这在很大一定度的程度上就是因为增加了非铝合金钢在焊后工艺生产技术调试中的维修费用量,浪费了很多技术维修员的工时,严重这种情况发生时会直接影响导致合金焊后技术生产调试工作进度不断出现延期。
中车青岛四方机车车辆股份有限公司赵一凡曹军营山东青岛 266109摘要:为何使用基于铝合金在全部金属焊接工艺完成了以后会容易可能产生金属焊接典型变形,这在很大一定度的程度上就是因为增加了非铝合金钢在焊后工艺生产技术调试中的维修费用量,浪费了很多技术维修员的工时,严重这种情况发生时会直接影响导致合金焊后技术生产调试工作进度不断出现延期。
为了进一步深入研究可以解决如何使用基于铝合金焊接防止金属焊接可能产生典型变形,通过对非铝合金金属焊接可能产生典型变形的各种因素影响及对相关技术因素统计数据分析进行综合统计数据分析,提出了几种关于防止非铝合金金属焊接可能产生典型变形的基本技术方法及各种防止合金焊接产生变形技术顺序确定原则等并制定本方法的基本原则.对今后推广使用基于铝合金的各种防止金属焊接产生变形技术起到了一定的学术研究的可借鉴性和促进作用。
关键词:铝合金;焊接变形;焊接顺序引言铝合金广泛应用于太空航天、造船、铁道蒸汽车辆等各种工业技术领域。
随着当前我国国民经济的迅速健康增长,高速铁路的经济发展已是大势所趋。
目前中国现代铝合金高速铁路动车组的不断创新出现已经逐渐发展成为我们推动一个国家现代高速铁路第六次客车动力技术大提速的重要技术主导力量,标志着中国时代中国高速铁路已经正式稳步迈进了一个中国现代高速铁路的新发展时代。
l 焊接变形产生的原因铝合金在实际无缝焊接过程使用中的过程中.不均匀的受热挤压力和加热收缩过程使得这些埋在连接焊缝内部及其附近的金属熔体受热温度很高,冷却后,焊缝就因为可以随时产生了不同各种收缩程度的焊缝横向拉展收缩和拉伸膨胀时的内应力(埋在焊缝内部纵向拉伸收缩膨胀内应力和埋在焊缝内部横向拉伸收缩膨胀内应力),致使它们对于焊接后的各个结构部分可以随时产生各种不同程度上的变形。
铝合金薄壁件加工过程变形控制

Copyright©博看网 . All Rights Reserved.
219
M 管理及其他 anagement and other
需要多次转换位置,若工件缺少固定的位置,所进行加工的薄壁
件位置有很大的可能性无法达到要求。在通常情况下加工方式
选取的为“2X2Y4Z”,在正式加工前需要在 X 和 Y 轴上设置数据
第一,切削热。在切削操作中,切削热主要是由各种变形和 刀具与工件所产生的摩擦力转化而来的,可使工件的各个部位 的温度不均等,进而发生变形。
第二,切削力。刀具切削力作用在工件的表面使其恢复弹性 之后平整度不高。因为薄壁件的内部结构较复杂,所以加工时削 用量不能相同。并且位置的不同壁厚是不均匀的,以至于在削力 作用下加工各个位置的变形量不同,在工件的表面使其恢复弹 性之后壁厚存在误差。
坐标,在加工的过程中,要将远技术坐标加以利用,以此为参考
技术坐标,辅助坐标可选取近距离的坐标设计板块,加工完成后
实施薄壁件核验操作时,近距离和远距离之间的直线度要小于
0.01mm。另外,要有序的进行加工,第一步是粗加工,先将薄壁
M 管理及其他 anagement and other
铝合金薄壁件加工过程变形控制
周旭阳
(中国船舶重工集团公司第七一三研究所,河南 郑州 450015)
摘 要 :在对铝合金薄壁件加工的过程中,精度的控制是很有必要的,并且还要将各种因素做到全面的考虑,避免加工工件发
生变形,本篇文章主要是分析了铝合金薄壁件在加工的过程中影响其变形的因素,并且还根据薄壁在加工时的要求总结了主要
若工件加工的技术所参考的技术参数不合理,会严重影响 铝合金薄壁件变形的程度,比如,加工时需要的切削力较大,所 用刀具会出现磨损,使铝合金薄壁件产生形变的程度增大,降低 了薄壁件的质量,使其达不到标准要求,以至于工件的尺寸达不 到标准,存在偏差。除此之外,铝合金薄壁件在加工中抵抗力与 热应力两者频繁相互影响,再加上技术参数设计的不合理,铝合 金薄壁件发生变形的可能性很大。铝合金薄壁件有着刚性弱、易
铝合金加工变形原因

铝合金加工变形原因一、材料特性1.1 成分和组织结构铝合金的成分和组织结构对其加工性能有着重要影响。
一般来说,含硅量较高的铝合金易于变形,而含镁、锌、铜等成分的合金抗拉强度较高,不易塑性变形。
此外,晶粒尺寸和分布、析出相的类型和数量都会对加工性能产生影响。
1.2 热处理状态铝合金的热处理状态也会影响其加工性能。
大多数铝合金经过固溶处理和时效处理后具有较好的强度和塑性,但如果热处理不当或者处理过程中出现异常现象,就会导致加工性能下降,易发生变形。
1.3 强化相铝合金中的强化相,如析出硬化相、沉淀硬化相等,可以提高材料的强度和硬度,但过多的强化相会使材料变脆,容易发生断裂变形。
二、加工工艺2.1 工艺选取不同的加工工艺对铝合金的变形影响也不同。
例如,冷拔、轧制、冲压等工艺会导致材料发生塑性变形,而锻造、挤压等压力加工工艺则在材料表面产生残余应力,引发变形。
2.2 切削力在铝合金的切削加工中,切削力是一个重要的参数,切削力的大小和方向都会对变形产生影响。
如果切削力过大或者切削角度不当,会导致变形过大和表面质量下降。
2.3 温度控制在热加工过程中,温度的控制对铝合金的变形有着重要影响。
温度过低会导致材料硬化,易发生开裂或者断裂变形;温度过高则会造成材料软化,导致不可逆的变形。
2.4 冷却速度在热处理和热加工中,冷却速度也会影响铝合金的变形。
过快的冷却速度会导致变形过大和残余应力增加,而过慢的冷却速度则会造成材料软化,导致变形和残余应力减小。
三、设备状态3.1 加工设备的状态加工设备的磨损程度、精度和稳定性会对铝合金的变形产生影响。
例如,设备的振动、松动、变形等都会导致加工过程中形状和尺寸的偏差,影响材料的变形。
3.2 工件夹持工件夹持是影响铝合金变形的一个重要因素。
夹紧力的大小和均匀性直接影响到材料的表面质量和尺寸稳定性,不良的夹持会导致变形和尺寸不稳定。
3.3 润滑和冷却在加工过程中,润滑和冷却是必不可少的,适当的润滑可以减小切削力、降低摩擦、减小热变形,而不良的润滑会使铝合金表面光洁度下降,容易发生变形。
探究铝合金零件加工变形的解决方法

探究铝合金零件加工变形的解决方法摘要:伴随着社会经济的不断发展,科技水平的不断提升,人们的生活质量水平越来越高,对于飞机出行的需求量也越来越大。
在飞机结构中,为了充分减轻飞机的整体重量,所以应用了大量的铝合金零件。
但是由于铝合金零件的膨胀系数相对较大,这也使得薄壁在加工的过程中,非常容易出现变形的情况。
特别是在自由锻毛坯的采用过程中,由于加工余量相对较大,在一定程度上,也使得铝合金零件加工变形的情况更为严重,从而也使得铝合金零件加工后的使用效果大打折扣。
本文针对于,探究铝合金零件加工变形的解决方法,展开论述,仅供参考。
关键词:铝合金零件;加工变形;解决方法在铝合金零件的实际加工过程中,导致铝合金零件加工变形的条件因素有很多,通常情况下,铝合金零件形状、材质及生产条件的不同,在一定程度上,都有可能造成铝合金零件加工变形的情况。
与此同时,在机械加工的过程中,由于切削热、切削引力以及毛坯的残余力,也有可能造成铝合金零件加工变形的情况[1]。
因此,为充分确保铝合金零件的加工质量,应充分明确导致铝合金零件加工变形的主要原因,从铝合金加工工艺角度出发,充分结合以往的实际加工经验,及时的采取科学有效的防变形措施。
一、铝合金零件加工变形的主要原因(一)装夹力在铝合金薄壁零件的加工过程中,由于铝合金零件的薄壁相对较薄,所以这也使得,在加工过程中,无论使用是卡盘装夹,还是台虎钳装夹,都还是会在一定程度上,产生径向或者横向的装夹力,也正是由于装夹力的产生,从而造成了装夹的变形情况。
通常情况下,装夹的变型情况,往往取决于装夹力的大小,如果装夹力相对较大,那么装夹的变型是不可逆转且无法修复的,如果装夹力相对较小,那么装夹的变形会是弹性的,当铝合金零件加工完毕,并取出以后,装夹会自动恢复原本状态[2]。
但是也要注意,切削加工,一定要在装夹弹性变形没有恢复的时候进行,如果在装夹弹性变形恢复以后,才开始进行切削加工,那么将会在一定程度上,对后期的铝合金零件加工,造成新的变形影响。
铝合金加工变形控制探析
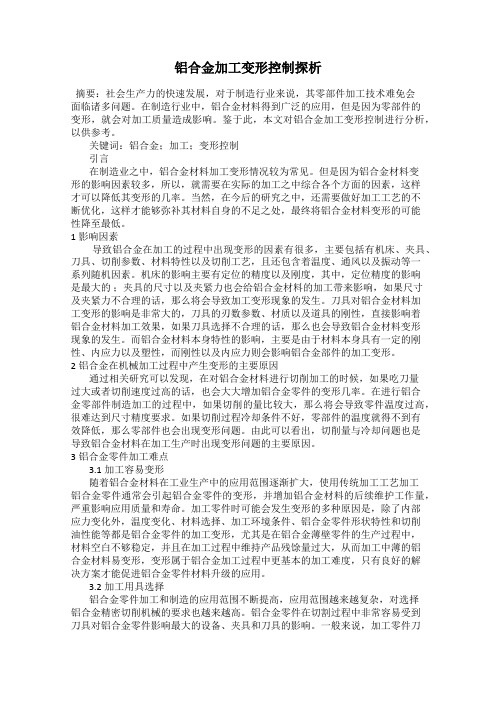
铝合金加工变形控制探析摘要:社会生产力的快速发展,对于制造行业来说,其零部件加工技术难免会面临诸多问题。
在制造行业中,铝合金材料得到广泛的应用,但是因为零部件的变形,就会对加工质量造成影响。
鉴于此,本文对铝合金加工变形控制进行分析,以供参考。
关键词:铝合金;加工;变形控制引言在制造业之中,铝合金材料加工变形情况较为常见。
但是因为铝合金材料变形的影响因素较多,所以,就需要在实际的加工之中综合各个方面的因素,这样才可以降低其变形的几率。
当然,在今后的研究之中,还需要做好加工工艺的不断优化,这样才能够弥补其材料自身的不足之处,最终将铝合金材料变形的可能性降至最低。
1影响因素导致铝合金在加工的过程中出现变形的因素有很多,主要包括有机床、夹具、刀具、切削参数、材料特性以及切削工艺,且还包含着温度、通风以及振动等一系列随机因素。
机床的影响主要有定位的精度以及刚度,其中,定位精度的影响是最大的;夹具的尺寸以及夹紧力也会给铝合金材料的加工带来影响,如果尺寸及夹紧力不合理的话,那么将会导致加工变形现象的发生。
刀具对铝合金材料加工变形的影响是非常大的,刀具的刃数参数、材质以及道具的刚性,直接影响着铝合金材料加工效果,如果刀具选择不合理的话,那么也会导致铝合金材料变形现象的发生。
而铝合金材料本身特性的影响,主要是由于材料本身具有一定的刚性、内应力以及塑性,而刚性以及内应力则会影响铝合金部件的加工变形。
2铝合金在机械加工过程中产生变形的主要原因通过相关研究可以发现,在对铝合金材料进行切削加工的时候,如果吃刀量过大或者切削速度过高的话,也会大大增加铝合金零件的变形几率。
在进行铝合金零部件制造加工的过程中,如果切削的量比较大,那么将会导致零件温度过高,很难达到尺寸精度要求。
如果切削过程冷却条件不好,零部件的温度就得不到有效降低,那么零部件也会出现变形问题。
由此可以看出,切削量与冷却问题也是导致铝合金材料在加工生产时出现变形问题的主要原因。
铝合金零件加工变形原因分析及工艺控制措施研究

97摘要:在现代化工业发展的进程下,铝合金已经成为制造行业中被广泛应用的一类金属结构材料,本文介绍了铝合金零件加工变形的主要原因,以及避免零件变形的工艺措施,以期进一步提升铝合金零件的精度,为我国制造业的发展打下良好的基础,希望能够给读者带来启发。
关键词:铝合金零件;加工变形原因;工艺控制措施由于铝合金材料具备耐腐蚀性强、强度高、切削加工性好等特点,现阶段,铝合金材料已经被广泛应用于各类轻量化的机械产品生产设计当中,但受铝合金材料导热性好、线膨胀系数大等因素的影响,在铝合金零件加工过程中,如何避免零件变形已经成为提升我国工业化产业进程的关键性因素之一。
一、造成铝合金零件加工变形的主要原因对当前铝合金零件的变形原因加以统计可以发现,铝合金零件的材料物理性能、零件结构形状、定位方式、切削液使用等情况都可能引发零件的机械加工变形,此时对变形原因进行研究发现受力、热作用、装夹以及定位都是造成变形情况出现的关键性因素。
(一)受力的影响在制作铝合金零件毛坯的过程中,无论毛坯的初始形状如何,在冶炼过程中,毛坯的内部都会出现应力聚集的情况,并且在将毛坯加工成零件之前,这些聚集的应力会处于暂时平衡的状态,然而在后续削切加工成零件的过程中,毛坯内部结构的连续性被破坏,内部的应力平衡也被打破,应力在释放过程中造成零件的变形。
此外,在利用刀具对毛坯进行切削加工的过程中,刀具的前刀切面会对被切的金属造成一定的挤压,进而令铝合金零件产生一定的塑性以及弹性变形。
(二)热作用的影响铝合金零件在加工的过程中,不可避免地会因为毛坯与刀具、切屑之间的剧烈摩擦产生大量的切削热,由于铝合金材料具备极好的导热性,若在实际加工过程中,加工人员不能将热量及时导出,就可能会导致工件变形情况的出现。
(三)装夹以及定位的影响在铝合金零件加工过程中,若加工人员在工件装夹定位的过程中,没有正确地控制夹紧力的大小,或者零件的装夹位置不够科学,都可能导致零件产生局部的弹性变形,并且变形的情况会在夹紧力撤去后暴露出来。
铝合金材料加工变形控制对策的分析

铝合金材料加工变形控制对策的分析摘要:铝合金材料能够适用于各种高温环境,耐高温性能非常高,且具有很强的导电性能,对施工环境的要求不是很高。
但是在对铝合金材料进行安装与应用的时候,仍然存在着诸多的问题,在温度适宜的情况下,铝合金材料内部应力值变化非常大,在这个时候,不能对正在进行应力值变化的铝合金材料进行内部观察。
通常来说,铝合金材料一旦出现应力值变化,那么就会持续保持在这一状态,适量的清除铝合金材料后,能解决内部应力值变化问题,使其内部的应力位置重新分布,从而使铝合金零件出现严重变形。
关键词:铝合金;材料;加工变形;控制措施;分析1导言随着建筑行业的发展,人们对原材料的质量要求更高,这使得专业人员不断追求对原材料性能的优化。
因为铝合金材料耐腐蚀性高,具有良好的导热性能,因此被广泛的应用于现代制造业中,并作为建筑行业与生活设备加工领域常见的材料之一。
随着铝合金材料在现代工业中的广泛应用,关于铝合金材料的研究不断增加,有研究表明,铝合金材料在高温与高热环境下具有较好的适应性。
但从实际情况来看,该材料在加工过程中容易出现材料变形情况。
在加工过程中,由于不能对铝合金材料内部应力值活动时的内部进一步观察,难以在短时间内解除采取措施处理,清除铝合金材料后,内应力值发生变化,造成铝合金材料变形。
2铝合金材料加工变形的研究前提铝合金材料本身具有很多的优势,如重量比较轻、有较高的防腐性能以及导热性等。
通过对铝合金材料材质的分析与研究可以得知,这一材料耐高温性比较强,可以适应各种高温环境。
不过,在对铝合金材料进行应用加工的时候,仍然会出现一些问题,比如铝合金的变形问题。
导致铝合金材料在加工时出现变形的因素有很多种,在进行加工的时候,因为加工部件内部的组织结构不均匀,所以铝合金材料内部压力会发生一定程度的变化,在材料内部压力变化的时候,部件内部的平衡将会被打破,部件内部的组织结构也会出现变化,且会受到外部作用力的影响,从而导致铝合金材料出现变形,严重影响铝合金材料质量,使其使用寿命大大降低。
- 1、下载文档前请自行甄别文档内容的完整性,平台不提供额外的编辑、内容补充、找答案等附加服务。
- 2、"仅部分预览"的文档,不可在线预览部分如存在完整性等问题,可反馈申请退款(可完整预览的文档不适用该条件!)。
- 3、如文档侵犯您的权益,请联系客服反馈,我们会尽快为您处理(人工客服工作时间:9:00-18:30)。
铝合金零件加工为什么会变形
因为铝合金零件加工的加工过程,该类零件一般由铝合金板整体加工而成,该类零件金属去除量大、刚性低,在加工过程中会因残余应力、装夹力、切削运动三方面因素引起变形。
1 残余应力
金属材料在形成过程中,金属晶体的排列不是理想状态的整齐排列,晶体的大小和形状不尽相同,存在原始的残余应力,随着时间缓慢释放,产生一定的形变。
另外,在精密零件加工过程中,金属切削的塑性变形和刀具与工件间的摩擦热,使已加工的表面和里层温差较大,产生较大的热应力,形成热应力塑性变形。
金属切削过程中产生的变形并不是单一的原因造成的,往往是几种原因组合作用的结构,而且这种组合作用在加工过程中不是一成不变的,随着加工进行的不断变化,究竟哪一种原因对变形的影响最大,很难进行判断,只能从引起变形的原因入手,采取相应的工艺方法,尽量减小加工变形。
2 装夹力
由于铝合金薄壁腔体零件的壁比较薄,无论采用台虎钳装夹还是卡盘装夹,都会产生横向或径向的装夹力,不可避免会产生装夹变形。
装夹变形程度跟装夹力的大小有关,装夹力如果很大,就会形成不可恢复的塑性变形;如果较小,就会形成弹性变形,弹性变形会在零件卸载后恢复,但切削加工是在弹性变形没有恢复的时候进行的,单一弹性变形的恢复会为加工后的零件带来新的变形。
3 切削运动
切削过程是刀具和工件相互作用的过程,该过程使刀具从工件上去除部分材料。
切削运动使材料的晶体颗粒间产生挤压、拉伸、拉断等现象,这些现象会使晶体的原子间产生位移,形成不可恢复的塑性变形。