焊接件检验标准(更新)
ISO 焊接相关标准2022更新

ISO 焊接相关标准目录(2022年出版)
本目录可以用于了解最新焊接相关标准状态,作为追踪标准状态目录文件。
本目录为2022年更新。
ISO焊接相关标准目录,包括ISO标准分类组别25.160—焊接,硬钎焊和软钎焊,包括气焊,电弧焊,等离子焊,电子束焊,等离子切割等。
1.2 ISO 25.160.10 焊接工艺方法相关标准,包括热切割和堆焊标准
1.3 ISO 25.160.20 焊接填充材料相关标准,包括电极、填充金属和气体等相关标准
1.4 ISO 25.160.30 焊接设备相关标准,包括热切割设备
1.4 ISO 25.160.40 焊缝和焊接接头相关标准,包括焊接位置和焊接接头的破坏性和非破坏性试验
1.5 ISO 25.160.50 软钎焊和硬钎焊相关标准,包括硬钎焊和软钎焊合金和设备。
焊接件质量目视检验规范

焊接件质量目视检验规范IMB standardization office【IMB 5AB- IMBK 08- IMB 2C】湖南耐普泵业有限公司焊接件外观质量检验规范1.目的通过制定焊接件质量的外观检验规范,指导操作者和检验员在焊接、检验过程中的行为,使生产和检验有章可循,确保产品焊接件质量2.范围本规范适用于公司所有焊接件外观检测(含自制及外协)。
焊缝内部检测按国家标准及技术要求执行。
本规范适用于手工、机械(半自动)和自动类型的熔化极焊接方法,如手工电弧焊、氩弧焊、气体保护焊、埋弧焊等。
3.引用文件GB/T 324 《焊缝符号表示法》GB/T 3375 《焊接术语》GB/T 《金属熔化焊接头缺欠分类及说明》GB/T 19418 《钢的弧焊接头缺陷质量分级指南》GB/T19804 《焊接结构的一般尺寸公差和形位公差》JB/T10584《钢结构焊缝外形尺寸》GB/T12476 1~4 《焊接质量保证金属材料的熔化焊》GB50205 《钢结构工程施工质量验收规范》附条文说明ISO5807 《焊接质量等级》4.外形尺寸检验依据产品制造施工设计图图纸规定了产品精加工制造后必须达到的材质特性、几何特性(如形状、尺寸等)以及加工精度(如公差等)的要求。
技术标准包括国家的、行业的或企业的有关标准和技术法规。
在这些标准或法规中规定了产品的质量要求和质量评定的方法。
产品制造的工艺文件如焊接工艺规程、时效处理、热处理工艺规程等,在这些文件中根据工艺特点提出必须满足的工艺要求。
订货合同在订货合同中对产品提出的附加要求,作为技术文件的补充规定,同样是制造和验收的依据。
5.焊缝外观检验焊缝基本符号a :角焊缝厚度;b :焊缝余高的宽度;d :气孔的直径;h :缺陷尺寸(高度或宽度);s :对接焊缝公称厚度;t :壁厚或板厚;K :角焊缝的焊脚尺寸;C :焊缝宽度;Z: 角焊的焊角长度;焊缝分类及质量等级5.2.1 焊缝分类根据公司结构件的受力受压情况以及局部焊接部位的重要性,把焊缝分为A、B、C、D 等四类。
焊接 目视检查验收标准

焊接目视检查验收标准<<民用核安全设备焊工焊接操作工资格管理规定>>-- HAF603 附件2中对考试试件的检验要求a)板材、管材或接管角焊缝凸度或凹度应不大于1.5mm;焊角尺寸K=T+(0-3)mm ( T为设计焊角尺寸)不带衬垫的板材、管材、接管以及外径不小于76mm的管材试件背面焊缝的余高应不大于3mm.b)焊缝外形尺寸要求:c)堆焊两相邻焊道之间的凹下量不得大于1.5mm;焊道高度差应小于或等于1.5mm。
d)手工焊焊缝表面的咬边和背面凹坑不得超过下表规定:当对ASME B31.1管道焊缝进行检测时:序号检测项目Inspected items可接受的标准Inspected items andacceptance criteria1尺寸检查Dimensioncheck焊缝余高尺寸ExcessWeld Metal不低于母材且不大于3mmNot less than the basemetal and not exceed3mm角焊缝焊角尺寸fillet weld size 法兰:焊角尺寸≥1.4Tn 或衬套壁厚两者中的较小者。
Tn=管道的公称壁厚除法兰以外的承插焊,焊角尺寸≥1.09Tn或插座壁厚两者中的较小者。
Tn=管道的公称壁厚2 表面咬边SurfaceUnder深度不大于1/32”(1mm)undercut on surfacewhich is greater than1⁄32in. (1.0 mm) deep3 表面焊接气孔Surfacewelding应无None4 焊接裂纹No WeldingCrack应无None5 未焊透(仅适用于易于看到的内表面)IncompletePenetration(appliesonly when inside应无Nonesurface is readily accessible);6 表面未熔合surfacelack of fusion应无None7 线性缺陷lineardefect不大于3/16”(5mm)8 圆形缺陷circulardefect尺寸不大于3/16”(5mm),指示表面缩孔或者等于或多于四个分散的指示,其边缘间隔间距在任何方向等于或小于1/16”(2mm)surface porosity withrounded indicationshaving dimensionslesser than 3⁄16 in.(5.0 mm) or four ormore roundedindicationsseparated by 1⁄16 in.(2.0mm) or less edgeto edge in anydirection.当采用《钢结构焊接规范--碳钢》(AWS D1.1)进行检测时序号检测项目及可接受的标准静荷载非管材连接周期荷载非管材连接管材连接(所有荷载)1 禁止裂纹任何裂纹都不合格,无论尺寸及部位x x x2 焊缝/母材的熔合焊缝的相邻焊层之间及焊缝金属与母材之间必须完全熔合x x x3 弧坑横截面除了超出断续角焊缝有效长度的断续角焊缝的端部外,所有弧坑必须填焊至规定的焊缝尺寸x x x4 焊缝轮廓形状必须符合AWS D1.1中5.24节的要求x x x5 检验的时间所有钢焊缝的目检可以在完工焊缝冷却到环境温度时进行。
焊接检验标准:规范钣金结构件的检验标准
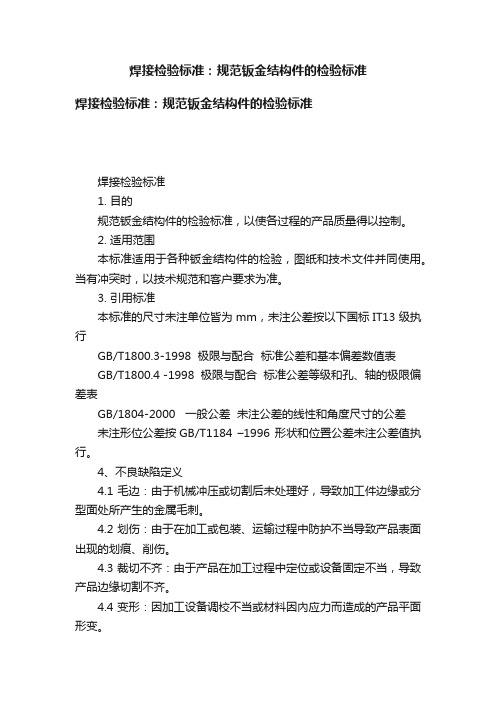
焊接检验标准:规范钣金结构件的检验标准焊接检验标准:规范钣金结构件的检验标准焊接检验标准1. 目的规范钣金结构件的检验标准,以使各过程的产品质量得以控制。
2. 适用范围本标准适用于各种钣金结构件的检验,图纸和技术文件并同使用。
当有冲突时,以技术规范和客户要求为准。
3. 引用标准本标准的尺寸未注单位皆为mm,未注公差按以下国标IT13级执行GB/T1800.3-1998 极限与配合标准公差和基本偏差数值表GB/T1800.4 -1998 极限与配合标准公差等级和孔、轴的极限偏差表GB/1804-2000 一般公差未注公差的线性和角度尺寸的公差未注形位公差按GB/T1184 –1996 形状和位置公差未注公差值执行。
4、不良缺陷定义4.1 毛边:由于机械冲压或切割后未处理好,导致加工件边缘或分型面处所产生的金属毛刺。
4.2 划伤:由于在加工或包装、运输过程中防护不当导致产品表面出现的划痕、削伤。
4.3 裁切不齐:由于产品在加工过程中定位或设备固定不当,导致产品边缘切割不齐。
4.4 变形:因加工设备调校不当或材料因內应力而造成的产品平面形变。
4.5 氧化生锈:因产品加工后未进行相应防锈处理或处理措施不当,而导致产品表面出现锈斑。
4.6 尺寸偏差:因加工设备的精度不够,导致产品尺寸偏差超过设计允许水平。
4.7“R角”过大/小:产品因折弯或冲压设备精度不够,导致折弯处弧度过大/小。
4.8 表面凹痕:由于材料热处理不好或材料生锈,其内部杂质导致金属表面形成的凹痕。
4.9 倒圆角不够:产品裁切边缘因切割或冲压原因产生的锐边未处理成圆弧状,易导致割手。
4.10 硬划痕:由于硬物磨擦而造成产品表面有明显深度的划痕(用指甲刮有明显感觉)。
4.11虚焊:因焊接操作不当造成的焊接不牢固。
4.12裂纹:焊后焊口处出现的裂痕。
5、焊接检验标准5.1焊缝应牢固、均匀,不得有虚焊、裂纹、未焊透、焊穿、豁口、咬边等缺陷。
焊缝长度、高度不均不允许超过长度、高度要求的10%。
焊钉(栓钉)焊接工程质量标准及检验方法

焊钉和钢材焊接的焊接工艺评定
应符合设计要求和国家现行有关标准的规定;瓷环应进行烘焙
检查焊接工艺评定报告和烘焙记录
4ቤተ መጻሕፍቲ ባይዱ
焊后弯曲试验
应符合现行有关标准的规定,其焊缝和热影响区不应有肉眼可见的裂纹
焊钉弯曲30°后用角尺检查和观察检查
般项Il
1
焊钉及焊接瓷环的规格、尺寸及偏差
应符合现行有关标准的规定
钢尺和游标卡尺量测
2
焊缝
应均匀,不应有局部未熔合或不足360°的焊脚
观察检查
2质量标准和检验方法:
焊钉(栓钉)焊接工程质量标准和检验方法
类别
序号
检验项目
质量标准
单位
检验方法及器具
主控项目
1
焊接材料的品种、规格、性能等
应符合现行国家产品标准和设计要求
检查质量合格证明文件,中文标志及检验报告等
2
重要钢结构采用的焊接材料
应进行抽样复验,复验结果应符合现行国家产品标准和设计
要求
检查复验报告
焊钉(栓钉)焊接工程质量标准及检验方法
1检查数量:
主控项目
1)第1项、第2项、第3项:应全数检查。
2)第4项:每批同类构件抽查10%,且不应少于10件;被抽查构件中,每件检查焊钉数量的1%,但不应少于1个。
一般项目
3)第1项:按量抽查1%,且不应少于10套。
4)第2项:按总焊钉数量抽查1%,且不应少于10个。
焊接检验标准

好孩子推车制造事业部昆山分部金工厂焊接产品质量控制手册(试用版)编制:审核:会签:批准:年月日焊接质量控制要求一、铝焊焊缝外观要求:铝焊合格品样件焊道宽度一般为6-9毫米, 鱼鳞片均匀,每英寸7-11片.(B类不合格)。
备注:焊缝质量基本可以代表焊接的整体质量以及焊接工人操作水平的高低.焊道中的各种缺陷会削弱零件的强度和承载能力.特别是裂纹,会不断的扩展,严重影响零件的使用寿命.铝焊接:鱼鳞片9±2片/英寸,宽度6-9mm,无焊渣、气孔、电击、裂纹(包括管内)、漏焊、焊破,接点圆滑无凸凹、针孔现象;焊接质量控制要求咬边造成裂纹:A类不合格收尾弧坑气孔:B类不合格焊缝不均匀,无鱼鳞片:A类不合格在原焊缝上直接补焊的虚焊:A类不合格正确做法:将焊缝锉掉一部份,然后先将焊缝融化后再加焊丝。
电灼伤:阳极氧化零件B类不合格喷粉零件C类不合格焊接质量控制要求一、铁焊焊缝要求:氩气保护铁焊接:无焊渣、气孔、灼伤、电击、咬边蚀肉、漏焊、焊破、虚焊,接点圆滑无、针孔、熔池现象。
宽度不小于5mm(B类不合格)。
焊缝接头:接点平整圆滑,无焊渣气孔、针孔、错位等不良缺陷。
收尾弧坑B类不合格飞溅造成的尖角B类不合格焊丝熔断B类不合格品焊穿,影响装配B类不合格第7页共21 页焊破A类不合格飞溅造成的焊珠焊接质量控制要求CO2焊接:焊道平整,无焊渣、气孔、灼伤、咬边蚀肉、漏焊、焊破、偏向现象,接点圆滑平整。
CO2点焊:焊点圆滑平整,无气孔、焊渣、针孔、裂纹、焊丝头粘付现象,焊点与基材融合良好焊点最小处尺寸须大于7mm (B类不合格)。
普通电弧焊焊接:焊道圆滑,无焊瘤、焊疤、夹渣现象,药皮层去除干净。
点焊直径大于7毫米(B类不合格)。
三、外观通用要求:管件表面不得有碰伤、划伤、模具擦伤,电击等不良。
C类不合格管件表面碰伤:判定方法,以圆珠笔倾斜于45度角垂直划伤面推动,有阻力NG,无阻力OK。
电镀、阳极氧化:B类不合格,喷涂C类不合格。
(完整版)激光焊接焊缝检测标准

(完整版)激光焊接焊缝检测标准-CAL-FENGHAI-(2020YEAR-YICAI)_JINGBIAN1 目的确立本公司激光焊接焊缝控制的标准。
2 范围本标准适用于本公司喷嘴环激光焊接及其他需要激光焊接件的所有图纸要求符合的焊缝,除在焊接图上有不同的焊接标准说明,其余(包括氩弧焊)均以本标准为依据执行。
3 职责质保部负责对本标准的实施及控制。
4标准内容4.1 焊缝焊接要求:2断,扭力值≥1.2N。
4.2焊缝外观质量要求:4.2.1焊缝质量外观检查规定操作工100﹪目视检查,检验员进行首末检查和过程抽检,目视怀疑尺寸超差的须送检验员进行复检确认。
4.2.2 焊缝表面缺陷检查:缺陷名称传递力的焊缝连接作用的焊缝图示裂纹不允许烧穿不允许焊偏不允许断弧不允许焊瘤不允许凹陷深度≤0.3mm 深度≤0.35表面气孔不允许小直径密集型气孔,单个气孔直径≥0.25mm气孔比例不大于整个焊缝的3﹪不允许小直径密集型气孔,单个气孔直径≥0.3mm气孔比例不大于整个焊缝的5﹪3咬边咬边深度≤母材厚度的4﹪咬边深度≤母材厚度的8﹪弧坑不包含在焊缝长度内允许长度不得超过熔宽的2倍,且不能烧穿。
焊接间隙不得大于0.2mm焊缝增高不大于0.2倍板的总厚度,不超过总厚度0.4mm表面夹渣夹渣与气孔同样判断4.3试验标准序号类型试验项目试验方法判定标准1尺寸直线度GB/T11336-2004 母材断面直线度<0.15mm2 翘曲度刀口尺+塞尺L<10 翘曲度≤0.210<L<12.5 翘曲度≤0.3 12.5<L<16 翘曲度≤0.53 间隙公差塞尺装夹母材时焊接间隙为0.05mm-0.10mm44.4焊接缺陷名称解释:4.4.1裂纹:缺陷多数存在于焊缝及焊缝热影响区域的微小裂缝。
此缺陷直接影响产品的机械性能4.4.2气孔:缺陷存在于焊缝内部及表面的孔洞。
此缺陷影响焊接强度。
4.4.3咬边:缺陷存在于焊缝与母材的交界熔合线部位,正常焊缝该处应为圆滑过渡。
焊缝外观检验标准
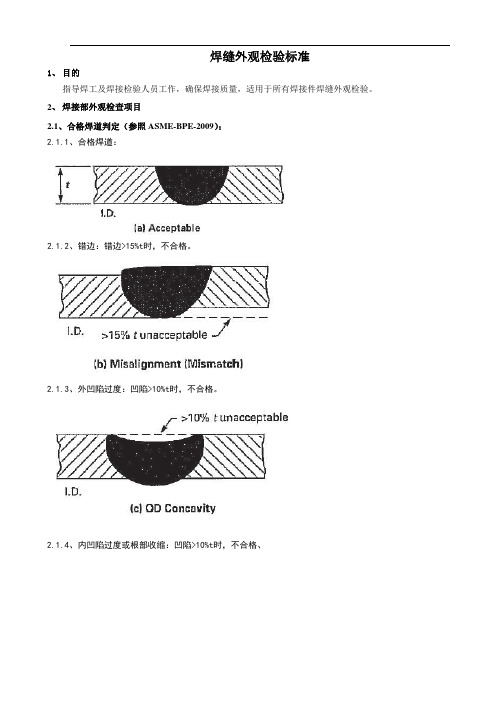
焊缝外观检验标准1、目的指导焊工及焊接检验人员工作,确保焊接质量,适用于所有焊接件焊缝外观检验。
2、焊接部外观检查项目2.1、合格焊道判定(参照ASME-BPE-2009):2.1.1、合格焊道:2.1.2、错边:错边>15%t时,不合格。
2.1.3、外凹陷过度:凹陷>10%t时,不合格。
2.1.4、内凹陷过度或根部收缩:凹陷>10%t时,不合格、2.1.5、未渗透,不合格。
2.1.6、凸出,凸出>0.015in(0.38mm)时,不合格。
2.1.7、整条焊缝,合格。
2.1.8、焊缝宽度偏差要求,焊缝最窄位置大于或等于最宽焊缝的50%,可以接受,反之不可以。
2.1.9、焊缝弯曲偏差要求,偏离焊缝<25%(或>75%)时,不可以接受。
2.2、焊道外观缺陷2.3、焊缝形状缺陷:2.3.1、错边:对接焊缝时两母材不在一平面上。
(管道对接时外径错边高度大于壁厚的15%时不合格)2.3.2、焊缝成形差:熔焊时,液态焊缝金属冷凝后形成的焊缝外形叫焊缝成形,焊缝成形差是指焊缝外观上,焊缝高低、宽窄不一,焊缝波纹不整齐甚至没有等。
2.3.3、焊脚尺寸:在角焊缝横截面中画出最大等腰三角形中,直角边的长度。
缺陷表现在焊脚尺寸小于设计要求和焊脚尺寸不等(单边)等。
、2.3.4、余高超差:余高高于要求或低于母材。
2.3.5、漏焊:要求焊接的焊缝未焊接。
表现在整条焊缝未焊接、整条焊缝部分未焊接、未填满弧坑、焊缝未填满未焊完等。
2.3.6、漏装:结构件中某一个或一个以上的零件未组焊上去。
2.3.7、飞溅;电弧擦伤;复合缺陷等其他缺陷。
3、检验方法。
3.1本标准只作为焊接部位外观检查的标准,对焊缝内部质量进行评定时,不适用本标准,焊缝内部质量要跟据相应的其它检查方法评定。
检验方法包括一下三种:3.1.1 肉眼观察。
3.1.2可使用放大镜检验,放大倍数应以五倍为限。
3.1.3采用渗透探伤。
渗透探伤是指采用荧光染料(荧光法)或红色染料(着色法)的渗透剂的渗透作用,显示缺陷痕迹的无损检验法。
焊接质量、试验与检验标准(doc 13页)
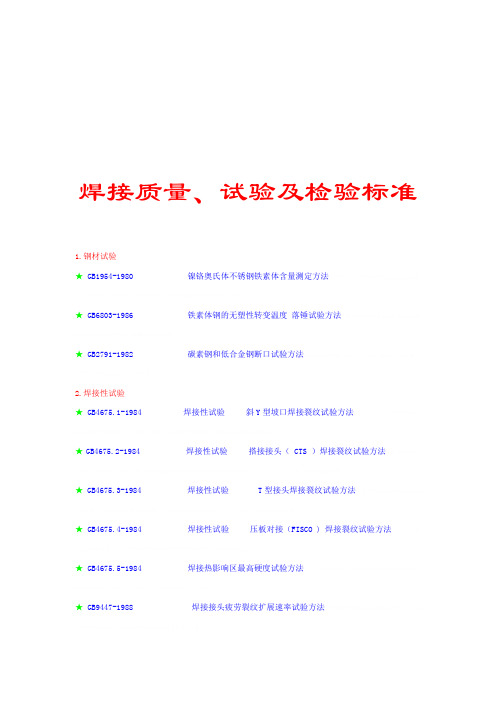
焊接质量、试验及检验标准1.钢材试验★ GB1954-1980 镍铬奥氏体不锈钢铁素体含量测定方法★ GB6803-1986 铁素体钢的无塑性转变温度落锤试验方法★ GB2791-1982 碳素钢和低合金钢断口试验方法2.焊接性试验★ GB4675.1-1984 焊接性试验斜Y型坡口焊接裂纹试验方法★GB4675.2-1984 焊接性试验搭接接头( CTS )焊接裂纹试验方法★ GB4675.3-1984 焊接性试验 T型接头焊接裂纹试验方法★ GB4675.4-1984 焊接性试验压板对接(FISCO ) 焊接裂纹试验方法★ GB4675.5-1984 焊接热影响区最高硬度试验方法★ GB9447-1988 焊接接头疲劳裂纹扩展速率试验方法★ GB2358-1980 裂纹张开位移(COD)试验方法★ GB7032-1986 T 型角焊接头弯曲试验方法★ GB9446-1988 焊接用插销冷裂纹试验方法★ GB4909.12-1985 裸电线试验方法镀层可焊性试验焊球法★ GB2424.17-1982 电工电子产品基本环境试验规程锡焊导则★ GB4074.26-1983 漆包线试验方法焊锡试验★ JB/ZQ3690 钢板可焊性试验方法★ SJ1798-1981 印制板可焊性测试方法3.力学性能试验方法★ GB2649-1989 焊接接头力学性能试验取样方法★GB2650-1989 焊接接头冲击试验方法★ GB2651-1989 焊接接头拉伸试验方法★ GB2652-1989 焊缝及熔敷金属拉伸试验方法★ GB2653-1989 焊接接头弯曲及压扁试验方法★GB2654-1989 焊接接头及堆焊金属硬度试验方法★GB2655-1989 焊接接头应变时效敏感性试验方法★ GB2656-1981 焊接接头和焊缝金属的疲劳试验方法★ GB11363-1989 釺焊接头强度试验方法★ GB8619-1989 釺缝强度试验方法4. 焊机材料试验★ GB3731-1983 涂料焊条效率、金属回收率和熔敷系数的测定★GB3965-1983 电焊条熔敷金属中扩散氢测定方法★ GB8454-1987 焊条用还原钛铁矿粉中亚铁量的测定★ GB5292.1-1985 熔炼焊剂化学分析方法重量法测定二氧化硅量★ GB5292.2-1985 熔炼焊剂化学分析方法电位滴定法测定氧化锰量★ GB292.3-1985 熔炼焊剂化学分析方法高锰酸盐光度法测定氧化锰量★ GB5292.4-1985 熔炼焊剂化学分析方法 EDTA容量法测定氧化铝量★ GB5292.5-1985 熔炼焊剂化学分析方法磺基水杨酸光度法测定氧化铁量★ GB5292.6-1985 熔炼焊剂化学分析方法热解法测定氧化钙量★GB5292.7-1985 熔炼焊剂及化学分析法氟氯化铅-EDTA容量法测定氟化钙量★ GB5292.8-1985 熔炼焊剂及化学分析法钼蓝光度法测定磷量★ GB5292.9-1985 熔炼焊剂及化学分析方法火焰光度法测定氧化钠、氧化钾量★ GB5292.10-1985 熔炼焊剂及化学分析法燃烧-库伦法测定碳量★ GB5292.11-1985 熔炼焊剂及化学分析法燃烧-碘量法测定流量★GB5292.12-1985 熔炼焊剂及化学分析法 EDTA容量法测定氧化钙、氧化镁量★ GB11364-1989 钎焊材料铺展性及填缝性试验方法★ GB4907.1-1985 电子器件用金、银及其合金釺焊料试验方法清洁性检验方法★ GB4907.2-1985 电子器件用金、银及其合金釺焊料试验方法溅散性试验方法★ JB3169-1982 喷焊合金粉末硬度力度检测★ JB3170-1982 喷焊合金粉末化学成分分析方法5.焊接检验★ GB/T12604.1-2005 无损检测术语超声检测★ GB/T12604.2-2005 无损检测术语射线检测★ GB/T12604.3-2005 无损检测术语渗透检测★ GB/T12604.4-2005 无损检测术语声发射检测★GB/T12604.5-2005 无损检测术语磁粉检测★ GB/T12604.6-2005 无损检测术语涡流检测★ GB5618-1985 线性象质计★ GB3323-1987 钢熔化对接接头射线照相和质量分级★ GB/T12605-1990 钢管环缝熔化焊对接接头射线透照工艺和质量分级★ GB11343-1989 接触式超声斜射探伤方法★ GB11344-1989 接触式超声波脉冲回波法测厚★ GB11345-1989 钢焊缝手工超声波探伤方法和探伤结果的分级★ GB2970-1982 中厚钢板超声波探伤方法★ JB1152-1981 锅炉和钢制压力容器对接焊缝超声波探伤★CB827-1980 船体焊缝超声波探伤★ GB10866-1989 锅炉受压元件焊接接头金相和断口检验方法★ GB11809-1989 核燃料棒焊缝金相检验★ZBJ04005-1987 渗透探伤方法★ ZBJ04003-1987 控制渗透探伤材料质量的方法★ JB3965-1985 钢制压力容器磁粉探伤★EJ187-1980 磁粉探伤标准★EJ186-1980 着色探伤标准★ JB/ZQ3692 焊接熔透量的钻孔检验方法★ JB/ZQ3693 钢焊缝内部缺陷的破断试验方法★GB11373-1989 热喷涂涂层厚度的无损检测方法★ EJ188-1980 焊缝真空盒检漏操作规程★JB1612-1982 锅炉水压试验技术条件★ GB9251-1988 气瓶水压试验方法★ GB9252-1988 气瓶疲劳试验方法★GB12135-1989 气瓶定期检查站技术条件★ GB12137-1989 气瓶密封性试验方法★ GB11639-1989 溶解乙炔气瓶多孔填料技术指标测定方法★ GB7446-1987 氢气检验方法★ GB4843-1984 氩气检验方法★ GB4845-1984 氮气检验方法6.焊接质量★ GB6416-1986 影响钢熔化焊接头质量的技术因素★ GB6417-1986 金属熔化焊焊缝缺陷分类及说明★ TJ12.1-1981 建筑机械焊接质量规定★ JB/ZQ3679 焊接部位的质量★ JB/ZQ3680 焊缝外观质量★ JB/TQ330-1983 通风机焊接质量检验★ CB999-1982 船体焊缝表面质量检验方法★JB3223-1983 焊条质量管理规程7.其他★ GB8923-1983 涂装前钢材表面锈蚀等级和除锈等级★ GB1223-1975 不锈耐酸钢晶间腐蚀倾向试验方法★GB4334.1-1984 不锈钢10%草酸浸蚀试验方法★ GB4334.2-1984 不锈钢硫酸-硫酸铁腐蚀试验方法★ GB4334.3-1984 不锈钢65%硝酸腐蚀试验方法★GB4334.4-1984 不锈钢硝酸-氢氟酸腐蚀试验方法★GB4334.5-1984 不锈钢硫酸-硫酸铜腐蚀试验方法★ GB4334.6-1984 不锈钢5%硫酸腐蚀试验方法★ GB4334.7-1984 不锈钢三氯化铁腐蚀方法★GB4334.8-1984 不锈钢42%氯化镁腐蚀试验方法★ GB4334.9-1984 不锈钢点蚀电位测定法焊接技术条件、质量检验、工艺评定标准集本篇是《焊接材料资料汇编》第五篇。
管道焊接检验标准

管道焊接对焊接方式和焊接质量,应按设计规定套用相应定额。
如设计无规定时,可参考以下规定套用相应定额项目。
1.Ⅰ、Ⅱ级焊缝以及管内壁清洁度要求严格,且焊后不易清理的管道(如透平机入口管、锅炉给水管、机组的循环油、控制油、密封油管道等)单面焊缝、宜采用氩电联焊。
合金钢管焊缝采用氩弧焊打底时,焊缝内侧宜充氩气保护。
2.奥氏体不锈钢管单面焊的焊缝,宜采用手工钨极氩弧焊打底,手工电弧焊填充盖面(氩电联焊)。
公称直径在50毫米以下的采用氩弧焊。
3.Ⅲ级以下焊缝碳钢管,公称直径在50毫米以下的(壁厚在3.5毫米以下)采用氧炔焊。
4.管道分类见表1注:⑴剧毒介质的管道按Ⅰ类管道。
⑵有毒介质,甲、乙类火灾危险物质的管道均升一类。
⑶“工作压力”项内任意为不分压力均为一级管道。
5.管口焊前预热和焊后热处理要求见表2。
注:⑴当焊接环境温度低于零度时,除规定壁厚必须作预热要求的金属外,其余金属壁厚也均应作适当的预热,使被焊接母材有手温感。
规定必须作预热要求的金属,定额项目内的预热消耗已考虑了温度变化因素,故不再增加预热。
⑵有应力腐蚀的碳素钢、合金钢,不论其壁厚条件,均应进行焊后热处理。
6.管口焊缝无损探伤计算规定数据:(1)管口焊接含量取定见表3。
表3(2)每个管口焊缝X光拍片张数,如无规定者可按表4计算。
表4注:⑴公称直径80毫米以下的管道焊缝X光透视检查拍片,一个焊口要求至少拍两张片。
定额中采用的胶片为85×300毫米的,实际上可用85×150毫米的胶片,执行定额时,人工和机械使用费壁变,材料费乘0.5系数。
⑵片子有效长度按片长减去搭接每边25毫米计算。
⑶管道焊口透视拍片的张数=管道等级规定的探伤百分比×焊口数量×张数(见表4)(3)管道各级焊缝射线探伤数量,应按设计规定计算。
如设计无规定时,按表5规定计算。
注:每条管线上最低探伤不得少于一个焊口。
SMT焊接质量检验 标准(最新版本)

焊接质量检验标准焊接在电子产品装配过程中是一项很重要的技术,也是制造电子产品的重要环节之一。
它在电子产品实验、调试、生产中应用非常广泛,而且工作量相当大,焊接质量的好坏,将直接影响到产品的质量。
电子产品的故障除元器件的原因外,大多数是由于焊接质量不佳而造成的。
(一)焊点的质量要求:对焊点的质量要求,应该包括它包括良好的电气接触、足够的机械强度和光洁整齐的外观三个方面,保证焊点质量最关键的一点,就是必须避免虚焊。
(1) 插件元件焊接可接受性要求:1.引脚凸出:单面板引脚伸出焊盘最大不超过2.3mm;最小不低于0.5 mm。
对于厚度超过2.3mm的通孔板(双面板),引脚长度已确定的元件(如IC、插座),引脚凸出是允许不可辨识的。
2.通孔的垂直填充:焊锡的垂直填充须达孔深度的75%,即板厚的3/4;焊接面引脚和孔壁润湿至少270°。
3.焊锡对通孔和非支撑孔焊盘的覆盖面积须≥75%。
4.插件元件焊点的特点是:①外形以焊接导线为中心,匀称、成裙形拉开。
②焊料的连接呈半弓形凹面,焊料与焊件交界处平滑,接触角尽可能小。
③表面有光泽且平滑,无裂纹、针孔、夹渣。
(2) 贴片(矩形或方形)元件焊接可接受性要求:1.贴片元件位置的歪斜或偏移的允收标准是:不超过其元件或焊盘宽度(其中较小者)的1/2,且不可违反最小电气间隙。
2.末端焊点宽度最小为元件可焊端宽度的50%或焊盘宽度的50%,其中较小者。
3.最小焊点高度为焊锡厚度加可焊端高度的25%或0.5 mm,其中较小者。
(3) 扁平焊片引脚焊接可接受性要求:1.扁平焊片引脚偏移的允收标准是:不超过其元件或焊盘宽度(其中较小者)的25%,且不违反最小电气间隙。
2.末端焊点宽度最小为元件引脚可焊端宽度的75%。
3.最小焊点高度为正常润湿。
(二)焊接质量的检验方法:⑴目视检查目视检查就是从外观上检查焊接质量是否合格,也就是从外观上评价焊点有什么缺陷。
目视检查的主要内容有:①是否有漏焊,即应该焊接的焊点没有焊上;②焊点的光泽好不好;③焊点的焊料足不足;④焊点的周围是否有残留的焊剂;⑤有没有连焊、焊盘有滑脱落;图2正确焊点剖面图(a)(b)凹形曲线主焊体焊接薄的边缘⑥焊点有没有裂纹;⑦焊点是不是凹凸不平;焊点是否有拉尖现象。
焊接检验标准规范
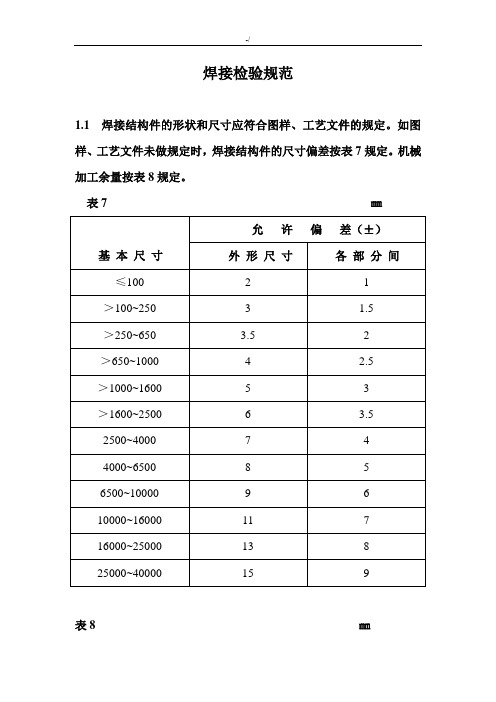
焊接检验规范1.1 焊接结构件的形状和尺寸应符合图样、工艺文件的规定。
如图样、工艺文件未做规定时,焊接结构件的尺寸偏差按表7规定。
机械加工余量按表8规定。
表7 ㎜表8 ㎜1.2 焊接结构零件在装配前必须经检查合格。
装配焊接结构零件时,必须保持图样上所注明的尺寸。
对于不合格的零件,禁止强力组装。
1.3 装配焊接结构时,两个焊件(或焊边)相互位置的偏差应符合下列规定:1.3.1 装配对接接头时,允许偏差按表9规定。
表9 ㎜1.3.2 装配搭接接头时,搭接宽度的偏差范围应为-2~+1.0㎜。
(图2)b △ba图21.3.3 装配截面复杂的结构时(图3),允许偏差按表10规定。
1.3.4 装配各式管路时,管壁间错移量(图4)允许在管壁厚度的10﹪以内,但不得超过1.5㎜。
图41.4 组装时的定位焊,应是以后焊缝的一部分,须按技术标准和图样的规定施焊,并应符合下列条件:1.4.1 定位焊与正式焊采用同一牌号焊条,其直径规格要小一级。
1.4.2 定位焊焊缝尺寸按表11选用。
主要部位可适当增加定位焊缝的尺寸和数量,但焊缝高度不得超过正式焊缝的高度。
1.4.3 对于主要的焊接结构件,在可能的条件下,应在背面定位焊,当正面焊好后,将背面的定位焊缝铲除后再焊背面。
1.4.4在焊缝交叉处和急剧变化的部位,不得进行定位焊。
1.4.5定位焊缝有裂纹时,必须铲除重焊,弧坑要填满。
1.5 超过规定偏差限度的焊接结构边缘上的裂纹和其它缺陷,应由技术检验部门检验同意后,用优良的焊条补焊。
1.6 装配完毕的焊接结构件经检验合格后方可焊接。
1.7 焊接前,应先清除焊接坡口区及距焊缝边缘20㎜以内的污物,如铁锈、氧化皮、油污、毛刺、熔渣、油漆等。
1.8 在露天焊接时,凡遇下雨、下雪、大风、或大雾的情况,应采取保护措施,否则不得进行焊接。
1.9 在0℃以下焊接时,应遵照下列条件:a.保证在焊接过程中,焊缝能自由收缩;b.不准用重锤打击所焊结构;c.焊前进行预热。
焊接质量检测标准
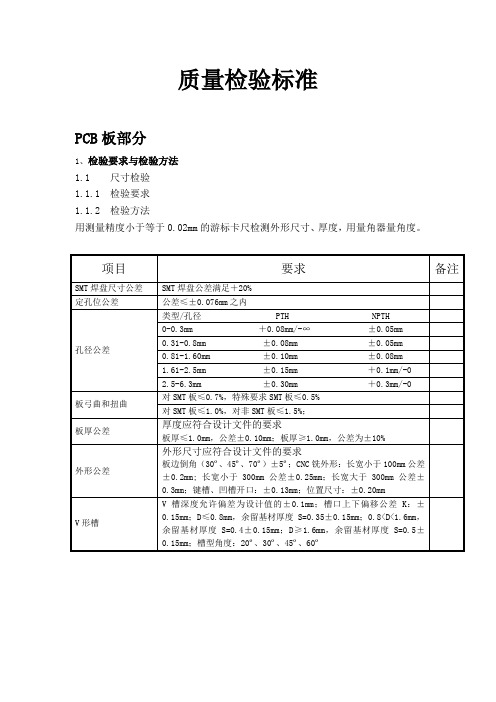
质量检验标准PCB板部分1、检验要求与检验方法1.1 尺寸检验1.1.1 检验要求1.1.2 检验方法用测量精度小于等于0.02mm的游标卡尺检测外形尺寸、厚度,用量角器量角度。
项目要求备注SMT焊盘尺寸公差SMT焊盘公差满足+20%定孔位公差公差≤±0.076mm之内孔径公差类型/孔径 PTH NPTH0-0.3mm +0.08mm/-∞±0.05mm 0.31-0.8mm ±0.08mm ±0.05mm0.81-1.60mm ±0.10mm ±0.08mm1.61-2.5mm ±0.15mm +0.1mm/-02.5-6.3mm ±0.30mm +0.3mm/-0板弓曲和扭曲对SMT板≤0.7%,特殊要求SMT板≤0.5% 对SMT板≤1.0%,对非SMT板≤1.5%;板厚公差厚度应符合设计文件的要求板厚≤1.0mm,公差±0.10mm;板厚≥1.0mm,公差为±10%外形公差外形尺寸应符合设计文件的要求板边倒角(30º、45º、70º)±5º;CNC铣外形:长宽小于100mm公差±0.2mm; 长宽小于300mm公差±0.25mm;长宽大于300mm公差±0.3mm;键槽、凹槽开口:±0.13mm;位置尺寸:±0.20mmV形槽V槽深度允许偏差为设计值的±0.1mm;槽口上下偏移公差K:±0.15mm;D≤0.8mm,余留基材厚度S=0.35±0.15mm;0.8<D<1.6mm,余留基材厚度S=0.4±0.15mm;D≥1.6mm,余留基材厚度S=0.5±0.15mm;槽型角度:20º、30º、45º、60º1.2 外观检验1.2.1 检验要求项目要求备注成品板边板边不出现缺口或者缺口/白边向内深入≤板边间距的50%,且任何地方的渗入≤2.54mm;UL板边不应露铜;板角/板边损伤板边、板角损伤未出现分层露织纹织纹隐现,玻璃纤维被树脂完全覆盖凹点和压痕直径小于0.076mm,且凹点面积不超过板子每面面积的5%;凹坑没有桥接导体;表面划伤划伤未使导体露铜、划伤未露出基材纤维;铜面划伤每面划伤≤5处,每条长度≤15mm镀金插头插头根部与导线及阻焊交界处露铜小于0.13mm,凹痕/压痕/针孔/缺口≤0.15mm且不超过3处,总面积不超过所有金手指的30%,不准许上铅锡;电镀孔内空穴(铜层)破洞不超过1个,破孔数未超过孔总数5%,横向≤90º,纵向≤板厚度的5%。
焊接件检验规范标准
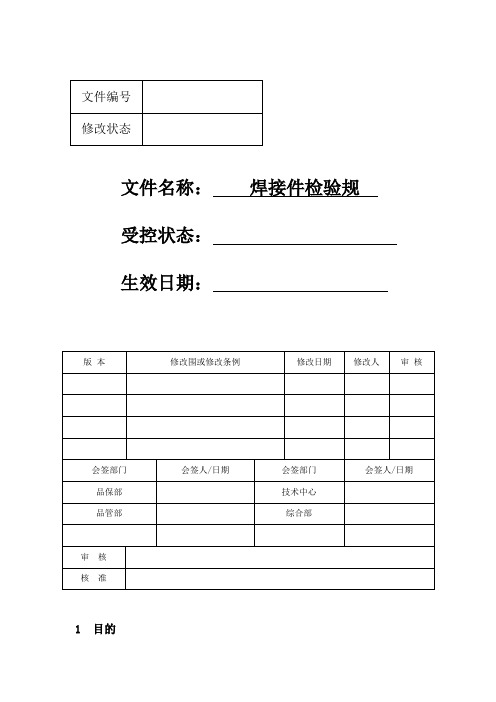
文件名称:焊接件检验规受控状态:生效日期:1 目的为规公司产品的焊接检验标准,确保检验的产品符合设计要求,从而达到保证被检测材料和部件的可靠性的目的,特制定本规。
2 定义本规所指产品包括承受动载或受力较大的箱体吊梁、悬挂件等有质量等级要求的焊接件,以及质量要求一般、受力较小、承受静载的焊接件。
3 围本标准适用于所有类型的钢、镍、钛、铝及其合金的熔焊接头(不包括电子束焊接),厚度大于0.5mm以上的材料焊接。
4 焊接术语质量等级:基于给定的缺欠类型,对焊接的质量进行分级描述。
短缺欠:焊接部分任意100mm长度,一个或多个缺欠总长度不大于25mm,或者焊接部分短于100mm长度,缺欠总长度不超过该长度的25%。
系统缺欠:待查焊接部分总长度以,按照特定距离均匀分布的缺欠,单个缺欠的尺寸在允许围以。
焊接裂纹:在焊接应力及其他因素共同作用下,焊接接头中局部位置的金属原子结合力遭到破坏而形成的新界面所产生的缝隙。
余高:焊缝表面两焊趾连线上的那部分金属高度。
角焊缝:沿两直交或近直交零件的交线所焊接的焊缝。
表面气孔:气孔是指焊接时,熔池中的气体未在金属凝固前逸出,残存于焊缝之中所形成的空穴。
当气体刚溢出表面而产生的孔洞未被填满金属液体凝固所形成的凹坑。
未焊透:焊缝金属没有进入接头根部的现象。
未熔合:焊缝金属与母材金属,或焊缝金属之间未熔化结合在一起的缺欠。
咬边:由于焊接参数选择不当,或操作方法不正确,沿焊趾的母材部位产生的沟槽或凹陷。
焊瘤:由于金属物在焊接过程中,通过电流造成金属焊点局部高温熔化,液体金属凝固时,在重力作用下金属流淌形成的微小疙瘩。
飞溅:熔化金属飞向熔池之外。
5 焊接符号本规中使用了以下符号:a:角焊标称焊缝厚度。
d:孔径。
h:缺欠的高度或宽度。
z:角焊的焊角尺寸。
t:壁厚或板厚。
b:焊缝宽度。
s:标称对接焊缝厚度(焊缝的有效厚度)。
6 要求本规必须经由培训合格的检验人员执行,为了方便检测产品的焊接品质,所有的待检产品应无表面涂层处理工序(如喷漆、喷塑等)。
焊接件检验规范以及注意事项

焊接检验规范1.目的和适用范围1.1本标准仅限铆焊制作的产品,即焊接结构件,机加工产品并不适合。
1.2明确焊接结构件的尺寸检验顺序、各类尺寸重要级别以及各级别尺寸允许误差。
(注意:未标注级别的尺寸并非意味着不需要检验,而是指按照最低级别标准检验)1.3作为评审不合格报告单签署让步、返工、报废的尺寸依据。
2.测量的精确性如果所要求的尺寸精度不合格,那么工程人员应考虑下列问题:——图纸所要求的产品尺寸精度确实是该产品使用时所必须的?——如果不是,什么样的公差可以为该产品使用所接受?——按本标准所要求的公差尺寸确实需要吗?——如果不是,何类公差可为该产品的使用所接受?2.1 各等级公差具体数据本标准要求的尺寸公差为一般焊接结构件的通用公差,数据来自GBT 19804-2005。
若工程师有其他特殊要求,必须在图纸上注明。
长度尺寸公差角度尺寸公差应采用角度的短边作为基准边,其长度可以延长至某特定的基准点。
在这种情况下,基准点应标准在图样上。
下图为角度公差两种表示方法直线度、平面度、平行度公差t直线度、平面度、平行度的测量方法:以标准的直线或平面与待测的直线或平面靠紧,两者之间的最大距离即直线度、平面度、平行度公差。
直线度测量图示(t 即为所要测量的直线度公差)2.2 公差等级的确定在未特别指出的情况下,请按下表确定各尺寸公差等级。
如表中未列出,则按作最低标准即D 级。
注:若工程师需要更高精度尺寸等级,请提前给工艺和检验人员发邮件通知,并给出具体理由。
A级:与其他重要产品刚性连接的定位尺寸且不可更改的。
如泵支座、发动机支座、罐支座与泵、发动机、罐相连的螺栓孔、罐支脚间距尺寸。
B级:与其他产品刚性连接的定位尺寸但可以更改的。
如橇座、拖车座上的各类支架位置尺寸,以钢管连接的罐、泵油箱各类孔距。
C级:关系到产品外形的尺寸——如罐、防碰架的长宽高;与其他产品柔性连接或有各种方法消除误差的定位尺寸——如以腰形孔定位的支架、以软管连接的各类孔距,使用卡箍的各种管汇法兰的尺寸。
焊接工艺评定试件和试样的试验与检验标准

焊接工艺评定试件和试样的试验与检验标准1.5.1试件的外观检验应符合下列规定:1对接、角接及T形等接头,应符合下列规定:1)用不小于5倍放大镜检查试件表面,不得有裂纹、未焊满、未熔合、焊瘤、气孔、夹渣等缺陷;2)焊缝咬边总长度不得超过焊缝两侧长度之和的15%,咬边深度不得大于0.5mm;3)焊缝外观尺寸应符合本标准8.2.2条中一级焊缝的要求(需疲劳验算结构的焊缝外观尺寸应符合本标准8.3.2条的要求)。
2栓钉焊接头外观检验应符合表1.5.1-1的要求。
当采用电弧焊方法进行栓钉焊接时,其焊缝最小焊脚尺寸应符合表1.5.1-2的要求。
表1.5.1-1栓钉焊接接头外观检验合格标准表1.5.1-2采用电弧焊方法的栓钉焊接接头最小焊脚尺寸1.5.2试件的无损检测应在外观检验合格后进行,无损检测方法根据设计要求确定。
射线检测应符合现行国家标准《金属熔化焊焊接接头射线照相》GB/T 3323的有关规定,焊缝质量不低于BⅠ级;超声波检测应符合本标准第8章的相关规定,焊缝质量不低于对接焊缝一级的质量要求。
1.5.3试样的力学性能、硬度及宏观酸蚀试验方法应符合下列规定:1拉伸试验方法应符合下列规定:1)对接接头拉伸试验应符合现行国家标准《焊接接头拉伸试验方法》GB/T 2651的有关规定;2)栓钉焊接头拉伸试验应符合图1.5.3-1的要求。
2 弯曲试验方法应符合下列规定:1)对接接头弯曲试验应符合现行国家标准《焊接接头弯曲试验方法》GB/T 2653的有关规定,弯心直径为4δ(δ为弯曲试样厚度),弯曲角度为180°。
面弯、背弯时试样厚度应为试件全厚度(δ<14mm );侧弯时试样厚度δ=10mm ,试件厚度小于等于40mm 时,试样宽度应为试件的全厚度,试件厚度超过40mm 时,可按20mm ~40mm 分层取样;2)栓钉焊接头弯曲试验应符合图1.5.3-2的要求。
弯曲垫片30°3 冲击试验应符合现行国家标准《焊接接头冲击试验方法》GB/T 2650的有关规定;4 宏观酸蚀试验应符合现行国家标准《钢的低倍组织及缺陷酸蚀检验法》GB 226的有关规定;5 硬度试验应符合现行国家标准《焊接接头硬度试验方法》GB/T 2654的有关规定。
焊接质量检验规范

目录:
一、前言 • 1、适用范围 • 2、引用标准 • 3、名词解释
二、焊缝质量接收标准 • 1、焊缝质量 • 1.1、焊缝外形尺寸 • 1.2、外部缺陷 • 1.3、焊道探伤等级及频次 • 2、焊道等级 • 2.1、C类焊道 • 2.2、B类焊道 • 2.3、A类焊道 2
3
1、适用范围
本规范适用于结构件的焊接质量检验。
13
2、焊道等级
2.3、A级焊缝
No 结构件名称
A类焊道描述
踏步焊缝
1
标准节
连接套焊缝
吊点板焊缝
2
平衡臂
接头焊缝
连接支板焊缝
3
塔帽
拉板架焊缝
上弦接头(双)焊缝
上弦接头(单)焊缝
4
起重臂 下弦接头(单)焊缝
下弦接头(双)焊缝
吊点板焊缝
部件数量
焊道数量
踏步:4个/节
2条/踏步
连接套:8个/节(12个/基节\强节) 2条/连接套
不允许 不允许
不允许
允许有稍微的凹陷e ≤1mm
不允许 不允许
个别电弧擦伤允许存在
不易清理处允许有少量的小 飞溅
10
1、焊缝质量
1.2.1、飞溅 所有焊缝的焊道上(右图Ⅰ区)不允许存在飞溅。 焊道两侧5cm以外区域(右图Ⅲ区)不允许存在
飞溅。焊道两侧5cm以内区域(右图Ⅱ区)飞溅标准: (1)、 A面飞溅标准:
在Ⅰ、Ⅱ区域内,每100mm长度内(上图蓝色箭头标识)允许存在3个焊瘤, 焊瘤最大直径≤0.5mm。 (2)、 B面飞溅标准:
在Ⅰ、Ⅱ区域内,每100mm长度内(上图蓝色 箭头标识)允许存在5个焊瘤,焊瘤最大直径≤2mm。 (3)、A/B定义: A面:能够直观看到的面,如上下支座的外表面、其他结构 件的表面, B面:不能够直观看到的面,如上下支座的内表面、标准节主弦封板。
焊接件检验标准

焊接件检验标准
焊接是一种常见的金属连接方式,广泛应用于汽车、航空航天、建筑等领域。
焊接件的质量直接影响着整个产品的安全性和可靠性,因此对焊接件的检验标准至关重要。
首先,焊接件的外观检验是非常重要的一环。
外观检验主要包
括焊缝的形状、尺寸、表面质量等方面。
焊缝应呈现出均匀、光滑、无裂纹、气孔和夹渣等缺陷,焊接件的外观质量直接关系到其机械
性能和耐腐蚀性能。
其次,焊接件的尺寸检验也是必不可少的一项内容。
尺寸检验
包括焊接件的长度、宽度、厚度等尺寸参数的测量,确保焊接件符
合设计要求,能够正确安装和使用。
此外,焊接件的材料成分检验也是非常重要的。
焊接件的材料
成分直接关系到其力学性能和耐腐蚀性能,因此需要对焊接材料进
行化学成分分析,确保其符合相关标准要求。
另外,焊接件的力学性能检验也是焊接件检验标准中的关键环节。
力学性能检验包括拉伸试验、冲击试验、硬度测试等,通过这
些测试可以评估焊接件的强度、韧性、硬度等力学性能指标,确保焊接件能够承受设计工况下的载荷。
最后,焊接件的非破坏检验也是必不可少的一项内容。
非破坏检验包括超声波检测、射线检测、磁粉检测等,通过这些方法可以发现焊接件内部的缺陷和隐患,确保焊接件的质量符合要求。
总的来说,焊接件的检验标准是非常严格和细致的,需要从外观、尺寸、材料成分、力学性能和非破坏检验等多个方面进行全面检验。
只有确保焊接件的质量符合标准要求,才能保证产品的安全可靠性。
焊接件的检验标准对于提高产品质量、确保使用安全具有重要意义。
- 1、下载文档前请自行甄别文档内容的完整性,平台不提供额外的编辑、内容补充、找答案等附加服务。
- 2、"仅部分预览"的文档,不可在线预览部分如存在完整性等问题,可反馈申请退款(可完整预览的文档不适用该条件!)。
- 3、如文档侵犯您的权益,请联系客服反馈,我们会尽快为您处理(人工客服工作时间:9:00-18:30)。
1.0目的
规范焊接件的检验标准,以使产品的工艺要求和一致性得到有效控制。
2.0范围
本标准适用于公司各种焊接件的检验,图纸和技术文件并同使用。
当有冲突时,以图纸要求为准。
3.0引用标准
GB/19804-2005 焊接结构的一般尺寸公差和形位公差
4.0检验标准
4.1标识
4.1.1 零部件必须分类摆放,不得混料;
4.1.2 来料每种零件必须在外包装上或顶面第一件贴标识,标识内容包括:订单号,零件名称、零件图号、规格型号、数量、日期等,如标识不清或无标识,零件混放,一律不予验收。
4.2 外观质量
4.2.1外观质量一般采用目测;
4.2.2零部件表面无油污、明显灰尘、锈蚀现象;
4.2.3零部件表面无敲击、磕碰痕迹,若有,须修磨平整;
4.2.4所有锐角必须倒钝(除非有特殊要求)、飞边毛刺必须打磨(不能割手)。
4.3焊缝质量
4.3.1 咬边:装机后外露的焊缝,不允许咬边,其他焊缝咬边深度h≤0.2+0.03t (较薄板厚度),且最深不得超过0.5mm,长度不超过焊缝全长的10%;
4.3.2表面气孔:装机后外露的或要求密封的焊缝,不允许有气孔,其他焊缝50mm 内允许有单个气孔,气孔直径Φ≤0.25t(较薄板厚度),最大不得超过1mm;
4.3.3表面夹渣:装机后外露的或要求密封的焊缝,不允许有夹渣,其他焊缝50mm 内允许有单个夹渣,夹渣直径Φ≤0.25t(较薄板厚度),最大不得超过2mm;
4.3.4焊缝裂纹:表面或内部都不允许有裂纹;
4.3.5错位:对接焊缝错位量h≤0.3t(较薄板厚度),最大不得超过0.5mm;4.3.6焊穿:不得有焊穿,焊穿部位必须补焊好;熔熬深度不得低于焊接母材的1/5。
焊接电流的选择Ø2.5≧70-95A, Ø3.2≧100-175A,Ø4≧200-300A......。
还有根据材质的厚薄和平焊,立焊,仰焊的实际情况需要灵活调节焊接电流。
不锈钢焊,铸铁焊,铝焊,二氧化碳保护焊,氩弧焊,埋弧焊,等。
根据实际
要求来调节电流大小,气压大小,运条速度,运条方式等等,灵活操作!
4.3.7虚焊、假焊、脱焊:不允许有;
4.3.8凹陷:装机后外露的焊缝不得有凹陷,其他焊缝凹陷量h≤0.2+0.03t,最大不得超过0.5mm,且不得超过焊缝全长的10%;
4.3.9飞溅:焊接飞溅物必须清除干净;
4.3.10弧坑:弧坑必须补焊填满;
4.3.11焊缝应均匀,呈鳞纹状,无明显凹凸。
向内方向最好使用工艺焊无需打磨。
4.4尺寸
4.4.1焊缝的尺寸及排列应符合图纸要求;对于机架要求:焊1000MM≦ 1.0MM。
2000-2500MM≦1-2MM。
检验对角线和垂直,平行度(×,⊥,∥)。
4.4.2对接焊缝有效厚度大于或等于较薄板厚;
4.4.3角接焊缝焊脚尺寸大于或等于较薄板厚;
4.4.4焊接件形位尺寸未注公差按GB/19804-2005中A级执行。
编制:WYH 审核:日期:20170503。