微电铸工艺
电铸工艺文档
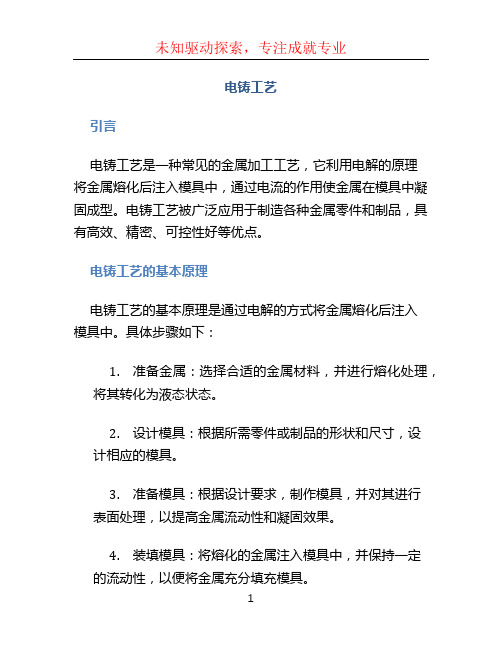
电铸工艺引言电铸工艺是一种常见的金属加工工艺,它利用电解的原理将金属熔化后注入模具中,通过电流的作用使金属在模具中凝固成型。
电铸工艺被广泛应用于制造各种金属零件和制品,具有高效、精密、可控性好等优点。
电铸工艺的基本原理电铸工艺的基本原理是通过电解的方式将金属熔化后注入模具中。
具体步骤如下:1.准备金属:选择合适的金属材料,并进行熔化处理,将其转化为液态状态。
2.设计模具:根据所需零件或制品的形状和尺寸,设计相应的模具。
3.准备模具:根据设计要求,制作模具,并对其进行表面处理,以提高金属流动性和凝固效果。
4.装填模具:将熔化的金属注入模具中,并保持一定的流动性,以便将金属充分填充模具。
5.通电加热:将模具连接到电源上,通电加热,使金属在模具中快速凝固。
6.拆卸模具:待金属完全凝固后,拆卸模具,取出成品。
电铸工艺的优势相比传统的铸造工艺,电铸工艺具有以下优势:1.高效:电铸工艺的加热速度快,凝固时间短,可以快速得到成品,提高生产效率。
2.精密:电铸工艺可以实现高精度的模具加热控制,保证成品尺寸精度和表面质量。
3.可控性好:电铸工艺可以通过调整加热功率、温度和时间等参数,灵活控制金属的凝固过程,适应不同的工艺需求。
4.适用范围广:电铸工艺适用于多种金属材料的加工,如铜、铝、锌等,可以满足不同行业的需求。
5.节约资源:电铸工艺可以减少原材料的浪费,提高材料利用率,并且不需要额外的熔炼设备,节约能源。
电铸工艺的应用领域电铸工艺广泛应用于以下领域:1.精密零件制造:电铸工艺可以实现高精度的零件制造,被广泛应用于航空航天、汽车、电子等领域。
2.铸造艺术品:电铸工艺可以制造各种精美的铸造艺术品,如雕塑、戒指等,具有高度的艺术价值。
3.电子元器件制造:电铸工艺可以制造高精度的电子元器件,如连接器、插座等,提供良好的电气性能。
4.精密仪器制造:电铸工艺可以制造各种精密仪器配件,如光学仪器、医疗设备等,提供稳定的性能表现。
电铸技术的工艺原理及应用

电铸技术的工艺原理及应用1. 电铸技术的简介电铸技术是一种重要的金属制造工艺,它通过在导电模具中施加电压和电流,使金属在模具表面析出形成薄壁金属制品。
电铸技术又被称为电解成形、电沉积、电火花加工等。
电铸技术具有高精度、高效率、低成本的优点,被广泛应用于制造业。
2. 电铸技术的基本原理电铸技术的基本原理是利用电化学的原理,在导电模具表面生成金属材料。
主要包括以下几个步骤:2.1 模具制备首先需要制作一个导电模具,通常使用金属或者制导性材料制作。
模具的表面需要经过特殊处理,以保证金属可以在上面均匀析出。
2.2 电解液准备准备一种电解液,其中含有金属离子,是金属析出的源头。
电解液的组成根据需要制造的金属制品而变化。
2.3 施加电压和电流将导电模具浸入电解液中,并施加适当的电压和电流。
通过电解反应,金属离子在模具表面析出,逐渐形成金属制品。
2.4 脱模和后处理金属制品形成后,需要从模具中取出,进行脱模处理。
脱模后,可能还需要进行后处理,例如去除表面氧化层、进行抛光等。
3. 电铸技术的应用领域电铸技术在制造业有着广泛的应用,以下是几个典型的应用领域:3.1 珠宝制造电铸技术可以用于珠宝制造,通过在导电模具中析出黄金、银等金属,制作出精美的珠宝首饰。
3.2 小型零件制造电铸技术可以制造小型零件,例如手机组件、手表零件等。
由于电铸技术具有高精度的特点,可以生产出复杂形状的小型零件。
3.3 硬质合金制造电铸技术可以制造硬质合金,例如切割工具、钻头等。
通过电铸技术,可以控制合金的成分和结构,改善硬质合金的性能。
3.4 特殊材料制造电铸技术可以制造一些特殊材料,例如形状记忆合金等。
通过控制电铸工艺参数,可以获得特殊材料的特殊性能。
3.5 快速成型制造电铸技术可以用于快速成型制造,例如快速铸造模具、快速制造金属零件等。
电铸技术具有高效率的特点,可以满足快速制造的需求。
4. 电铸技术的发展趋势随着科技的不断进步,电铸技术也在不断发展。
微电铸工艺现状和发展趋势
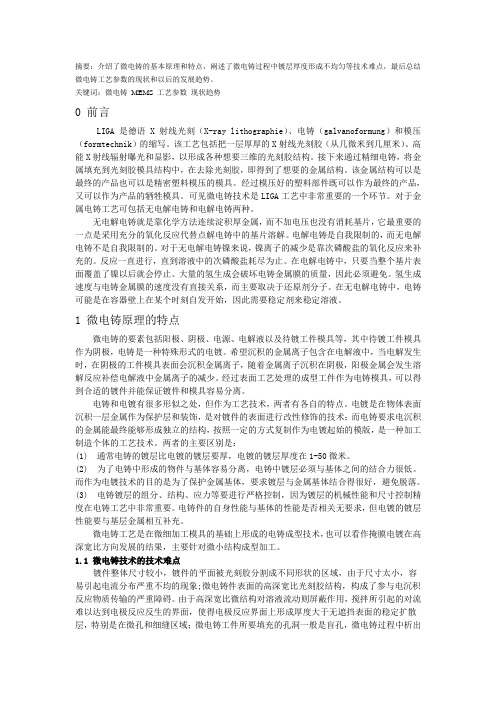
摘要:介绍了微电铸的基本原理和特点,阐述了微电铸过程中镀层厚度形成不均匀等技术难点,最后总结微电铸工艺参数的现状和以后的发展趋势。
关键词:微电铸MEMS 工艺参数现状趋势0 前言LIGA是德语X射线光刻(X-ray lithographie)、电铸(galvanoformung)和模压(formtechnik)的缩写。
该工艺包括把一层厚厚的X射线光刻胶(从几微米到几厘米)、高能X射线辐射曝光和显影,以形成各种想要三维的光刻胶结构。
接下来通过精细电铸,将金属填充到光刻胶模具结构中,在去除光刻胶,即得到了想要的金属结构。
该金属结构可以是最终的产品也可以是精密塑料模压的模具。
经过模压好的塑料部件既可以作为最终的产品,又可以作为产品的牺牲模具。
可见微电铸技术是LIGA工艺中非常重要的一个环节。
对于金属电铸工艺可包括无电解电铸和电解电铸两种。
无电解电铸就是靠化学方法连续淀积厚金属,而不加电压也没有消耗基片,它最重要的一点是采用充分的氧化反应代替点解电铸中的基片溶解。
电解电铸是自我限制的,而无电解电铸不是自我限制的。
对于无电解电铸镍来说,镍离子的减少是靠次磷酸盐的氧化反应来补充的。
反应一直进行,直到溶液中的次磷酸盐耗尽为止。
在电解电铸中,只要当整个基片表面覆盖了镍以后就会停止。
大量的氢生成会破坏电铸金属膜的质量,因此必须避免。
氢生成速度与电铸金属膜的速度没有直接关系,而主要取决于还原剂分子。
在无电解电铸中,电铸可能是在容器壁上在某个时刻自发开始,因此需要稳定剂来稳定溶液。
1 微电铸原理的特点微电铸的要素包括阳极、阴极、电源、电解液以及待镀工件模具等,其中待镀工件模具作为阴极,电铸是一种特殊形式的电镀。
希望沉积的金属离子包含在电解液中,当电解发生时,在阴极的工件模具表面会沉积金属离子,随着金属离子沉积在阴极,阳极金属会发生溶解反应补偿电解液中金属离子的减少。
经过表面工艺处理的成型工件作为电铸模具,可以得到合适的镀件并能保证镀件和模具容易分离。
电铸工艺流程介绍特点应用及注意事项

电铸工艺流程介绍特点应用及注意事项电铸工艺是一种先进的制造工艺,它通过将金属加热至液态,然后注入到模具中,使其凝固成型。
本文将介绍电铸工艺的流程、特点、应用和注意事项。
一、电铸工艺流程电铸工艺包括准备模具、准备金属材料、加热金属、注入模具、冷却凝固、取出成品等几个主要步骤。
1.准备模具:首先要根据产品的形状和尺寸,制作好对应的模具,模具的材质和设计都直接影响到产品的质量和成型效果。
2.准备金属材料:选择合适的金属材料,根据产品的设计要求进行配比,并在一定的温度和湿度下进行预处理。
3.加热金属:将金属加热至液态,通常采用电炉或其他加热设备进行加热,确保金属达到合适的温度和流动性。
4.注入模具:在金属达到合适的温度后,将其注入到模具中,这一步要求操作精准,确保金属填充模具的每一个细节。
5.冷却凝固:金属注入模具后,需要等待一定的时间让其冷却凝固,这个过程会影响产品的硬度和强度。
6.取出成品:待金属完全冷却后,取出成品,并进行后续的清理和处理,最终得到符合设计要求的成品。
二、电铸工艺特点1.精度高:电铸工艺可以制作出尺寸精准、表面光滑的产品,非常适合制造精密零部件。
2.材料利用率高:由于是将金属加热成液态后注入模具,因此可以减少材料的浪费,提高材料的利用率。
3.生产效率高:电铸工艺可以大规模生产出相同尺寸和形状的产品,生产效率高,成本低。
4.适用范围广:电铸工艺可以用于多种金属材料,包括铝合金、铜合金、锌合金等,适用范围广。
5.成本较低:与其他制造工艺相比,电铸工艺的成本较低,可以大幅降低产品的生产成本。
三、电铸工艺应用电铸工艺在汽车制造、电子产品制造、航空航天、建筑装饰等领域都有广泛的应用。
1.汽车制造:汽车的零部件中有许多都是通过电铸工艺制造的,例如引擎外壳、车轮轮毂等,这些产品需要具备一定的强度和耐磨性。
2.电子产品制造:电铸工艺可以制造出精密的电子产品外壳、散热器等部件,保证产品的质量和外观。
微电铸技术及其工艺优化进展研究

而, 微电铸工艺中存在的铸层厚度均匀性差、 制作周 期长、 残留内应力大、 铸层易出现缺陷及硬度低等不 足也严重制约着其应用与发展
[ G @ F]
( $ )在微电铸过程中, 由于电流的边缘效应, 电 力线容易在芯模的尖角、 边缘处集中, 电流密度也就 相应较大, 因此该处铸层厚度大于平均厚度。而中 部电力线相对稀疏, 电流密度较小, 铸层厚度小于平 均厚度。 ( " )对于具有高深宽比的复杂零件, 除了电流 的边缘效应外, 槽侧壁对槽底会起到一定的屏蔽作
2世纪32年代4516等人发现在以覆金陶瓷或喷漆玻璃作为衬底的同时降低电铸温度可有效改善复制微结构的表面质量以及铸层的延展性从而取代硅或云母等传统电铸衬底等人在传统直流电铸的基础上进行了脉冲电铸技术的实验研究得出了脉冲电铸可以显著改善铸层质量的结论等人总结了前人的研究成果发现在相同的平均电流密度下反脉冲电铸可以获得比脉冲电铸更光滑的表面然而这却是以降低电流效率为代价的等人提出采用旋转圆盘作阴极不但可以提高电铸均匀性增强铸层排氢能力而且还不会影响电铸层的表面质量j研究发现金属沉积表面会自然地呈现为凹面对整个沉积层而言边缘厚度约是中间厚度的两倍他们进一步提出了采用辅助阴极的办法降低电铸不均匀性实验证明效果显著等人通过改变脉冲电铸的波形来抑制晶粒生长提高形核率与常规的直流电铸方波脉冲电铸相比能够获得更好的表面均电铸速率的提高微电铸工艺中金属离子的沉积速率直接关系到微结构加工周期的长短从而也进一步决定了整个工艺的实际应用价值
[$ @ ; ] 等高新技术领域, 并受到日益广泛的关注 。然
量理论分析和理论建模, 并在改善铸层均匀性、 提高 电铸速率、 消除内应力以及优化沉积层性能等方面 做了很多有益的探索和尝试。
电铸工艺流程

电铸工艺流程电铸工艺流程指的是利用电解沉积技术将金属材料或合金材料沉积在金属模具上的一种工艺。
下面将详细介绍电铸工艺流程。
首先,准备金属模具。
金属模具是电铸工艺的基础,它需要具备一定的导电性和耐腐蚀性能。
常见的金属模具材料包括铝合金、铜合金等。
需要根据产品的形状和尺寸选择合适的模具。
其次,准备电解液。
电解液是电铸工艺中起到导电和输送金属离子的作用。
一般来说,电解液由金属盐和其他添加剂组成,可以根据需要选择不同的电解液。
在操作过程中,需要控制电解液的温度和PH值,以保证工艺的稳定性和产品的质量。
然后,进行前期处理。
前期处理包括清洗模具、调整电解液浓度和温度等。
首先,将模具进行清洗,去除表面的油污和杂质,以保证金属沉积的均匀性。
然后,根据需要调整电解液的浓度和温度,使其达到最佳工艺状态。
接着,开始电铸。
将准备好的金属模具放入电解槽中,并通过电源将正极和负极与模具和电解液相连。
当通电后,电源会产生一定的电流,通过电解液中的金属离子向模具表面沉积。
在沉积过程中,需要控制电流的大小和时间,以达到预期的沉积厚度和均匀性。
最后,进行后期处理。
后期处理主要包括产品的清洗、除锈和抛光等工序。
首先,将电铸好的产品从模具中取出,进行清洗,去除电解液和其他杂质。
然后,根据需要对产品进行除锈和抛光,以提高表面的光洁度和质量。
总的来说,电铸工艺流程分为准备模具、准备电解液、前期处理、电铸和后期处理五个步骤。
通过合理控制各个步骤中的参数,可以获得理想的电铸产品。
电铸工艺具有成本低、生产效率高、产品精度高、材料利用率高等优点,被广泛应用于各个领域,如航天、汽车、电子等。
电铸工艺技术

电铸工艺技术
电铸工艺技术是一种将液体金属通过电解沉积的方法制造金属制品的技术。
它是利用电解质的电解和金属的电化学特性,将金属溶解在电解质中,然后通过施加电流,使金属离子在电极上还原成金属,从而得到所需的金属制品。
以下将详细介绍电铸工艺技术的原理、优势和应用。
首先,电铸工艺技术的原理是基于电化学原理的。
当金属在电解质中溶解时,金属会释放出电子,这些电子会流动到电极上,然后通过施加电流,将电子重新引导回金属,使金属离子重新还原成金属,从而实现金属的沉积和制造。
其次,电铸工艺技术具有许多优势。
首先,电铸能够制造出形状复杂的金属制品,如零件、模具等,能够满足不同行业的需求。
其次,电铸工艺具有高度的自动化和数字化控制能力,能够实现高精度的制造。
此外,由于电铸工艺的特性,其制造的金属制品具有均匀的组织结构,密度高,性能优良,能够满足高要求的工程应用。
最后,电铸工艺技术有广泛的应用领域。
首先,它广泛应用于汽车、电子、航空航天等行业的零部件制造中。
例如,汽车发动机的活塞、缸套等部件就可以通过电铸工艺来制造,以提高零部件的性能和质量。
其次,电铸工艺也可以应用于珠宝制造中,可以制造出精美的银首饰、黄金项链等。
此外,电铸工艺还可以用于制造模具、工艺品等。
综上所述,电铸工艺技术是一种通过电解沉积金属制品的技术,
具有原理清晰、优势明显、应用广泛等特点。
随着科技的不断进步,电铸工艺技术也会不断发展和完善,为各行各业提供更好的金属制品解决方案。
电铸工艺流程

电铸工艺流程电铸工艺是一种利用电解作用将金属或合金沉积在导电基底上的方法,广泛应用于制造业中。
电铸工艺流程包括原料准备、模具制备、电解液配制、电铸操作等多个环节。
下面将详细介绍电铸工艺的流程。
首先,原料准备是电铸工艺的第一步。
在进行电铸之前,需要准备好所需的金属或合金原料,确保其纯度和质量符合要求。
同时,还需要准备好其他辅助材料,如模具、电解液等。
接下来是模具制备。
模具的制备对于电铸工艺至关重要,它直接影响到最终产品的质量。
在制备模具时,需要根据产品的形状和尺寸设计制作相应的模具,确保能够满足产品的要求。
第三步是电解液配制。
电解液是电铸过程中的重要介质,它能够提供必要的离子以及维持电流的稳定。
在配制电解液时,需要根据不同金属或合金的特性,选择合适的电解液配方,并严格按照配方比例进行配制。
然后是电铸操作。
在进行电铸操作时,需要将准备好的原料放置在电解槽中,通过施加电流,使金属或合金离子在导电基底上沉积,最终形成所需的产品。
在电铸过程中,需要控制好电流密度、温度、时间等参数,确保产品的质量和稳定性。
最后是产品处理。
经过电铸后,产品需要进行一定的处理,如去除残留的电解液、清洗、抛光等,最终得到成品。
产品处理的质量直接关系到最终产品的外观和性能,因此需要特别注意。
总的来说,电铸工艺流程包括原料准备、模具制备、电解液配制、电铸操作和产品处理等多个环节,每个环节都需要严格控制和操作,确保最终产品的质量和稳定性。
希望通过本文的介绍,能够对电铸工艺流程有一个更加全面和深入的了解。
电铸工艺流程介绍特点应用及注意事项

电铸工艺流程介绍特点应用及注意事项The process of electroforming is a widely used technique in various industries, which involves the deposition of metal onto a conductive surface through an electrochemical reaction. This method offers several advantages such ashigh dimensional accuracy, excellent surface finish, andthe ability to create complex shapes.电铸工艺是一种在各行业广泛应用的技术,通过电化学反应将金属沉积在导电表面上。
这种方法具有高精度、优异的表面光洁度和制造复杂形状的能力等多个优点。
The electroforming process consists of several steps. First, a pattern or mandrel is created using materials such as wax or plastic. This pattern is then coated with a conductive material, typically copper, to enhance its electrical conductivity. Next, the pattern is immersed in anelectrolyte solution containing metal ions that will be deposited onto the surface. An electrode is connected tothe pattern and current is applied, causing the metal ionsto migrate and deposit onto the pattern's surface. Thisdeposition continues until the desired thickness is achieved.电铸工艺包括几个步骤。
简述电铸成型的加工工艺流程

简述电铸成型的加工工艺流程够帮助大家解决实际的问题。
文档下载后可定制随意修改,请根据实际需要进行相应的调整和使用,谢谢!并且,本店铺为大家提供各种各样类型的实用资料,如教育随笔、日记赏析、句子摘抄、古诗大全、经典美文、话题作文、工作总结、词语解析、文案摘录、其他资料等等,如想了解不同资料格式和写法,敬请关注!Download tips: This document is carefully compiled by theeditor.I hope that after you download them,they can help yousolve practical problems. The document can be customized andmodified after downloading,please adjust and use it according toactual needs, thank you!In addition, our shop provides you with various types ofpractical materials,such as educational essays, diaryappreciation,sentence excerpts,ancient poems,classic articles,topic composition,work summary,word parsing,copy excerpts,other materials and so on,want to know different data formats andwriting methods,please pay attention!电铸成型,又称为电沉积成型或电镀成型,是一种利用电解原理在特定模具表面精确复制细微结构的加工技术,广泛应用于精密零件制造、模具制造、工艺品复制等领域。
电铸工艺流程电铸的特点、原理及应用

电铸工艺流程|电铸的特点、原理及应用什么是电铸?电铸是指在芯模上电沉积,然后分离以制造(或复制)金属制品的工艺。
它的基本原理和电镀相同。
但是,电镀时要求得到与基体结合牢固的金属镀层,以达到防护、装饰等目的,而电铸层要和芯模分离,其厚度也远大于电镀层。
电铸工艺流程:电铸的工艺流程可分四大部分:原模的选择与制作、电铸前处理、电铸和电铸后处理。
原模一般根据所选用的材料不同分为金属原模和非金属原模,根据用途不同又可分为一次性和反复使用原模。
对于金属原模电铸前处理主要包括表面净化(表面整理、除油和除锈等)和脱模处理。
表面净化是为获得均匀平整的电铸制品,脱模处理则是设置脱模剂或隔离层,便于电铸后脱模。
对于非金属原模电铸前表面净化(除油、敏化和活化等)是为导电化处理奠定基础,而导电化处理则是让非金属原模表面金属化。
电铸后处理包括衬背和脱模,衬背用于加固电铸制品,避免脱模或后续加工时损坏。
电铸的特点:电铸和一般机械加工工艺相比有很多优点:(1)能把机械加工较困难的零件内表面转化为芯模外表面,能把难成型的金属转化为易成型的芯模材料(如蜡、树脂等),因而能制造用其它方法不能(或很难)制造的特殊形状的零件。
(2)能准确地复制表面轮廓和微细纹路。
(3)改变溶液组成和工作条件,使用添加剂,能使电铸层的性能在宽广的范围内变化,以适应不同的需要。
(4)能够得到尺寸精度高、表面光洁度好的产品。
同一芯模生产的电铸件一致性好。
(5)能得到纯度很高的金属制品(电解金属)、多层结构的构件,并能把各种金属、非金属部件拼镀成一个整体。
由于有上述特点,电铸工艺被用来制造形状复杂、精度高的空心零件(如波导管等),注塑用的模具、薄壁零件(有时厚仅几十微米),复制精细的表面轮廓(如唱片模、艺术品)等,将成为广泛应用的工艺之一;但是,电铸也有一些缺点如生产周期长,成本比较高,厚度很难均匀,并且会把芯模上的伤痕带到产品上。
电铸的原理:电铸是利用金属离子阴极电沉积原理,在导电原模(芯模)上沉积金属、合金或复合材料,并将其与原模分离以制取制品的过程。
电铸工艺流程
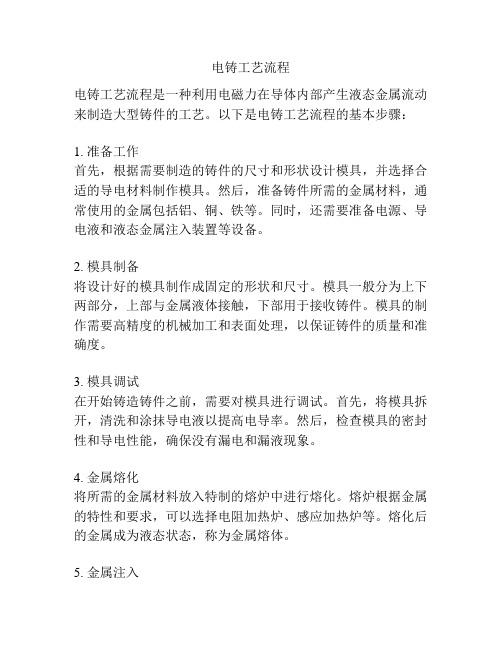
电铸工艺流程电铸工艺流程是一种利用电磁力在导体内部产生液态金属流动来制造大型铸件的工艺。
以下是电铸工艺流程的基本步骤:1. 准备工作首先,根据需要制造的铸件的尺寸和形状设计模具,并选择合适的导电材料制作模具。
然后,准备铸件所需的金属材料,通常使用的金属包括铝、铜、铁等。
同时,还需要准备电源、导电液和液态金属注入装置等设备。
2. 模具制备将设计好的模具制作成固定的形状和尺寸。
模具一般分为上下两部分,上部与金属液体接触,下部用于接收铸件。
模具的制作需要高精度的机械加工和表面处理,以保证铸件的质量和准确度。
3. 模具调试在开始铸造铸件之前,需要对模具进行调试。
首先,将模具拆开,清洗和涂抹导电液以提高电导率。
然后,检查模具的密封性和导电性能,确保没有漏电和漏液现象。
4. 金属熔化将所需的金属材料放入特制的熔炉中进行熔化。
熔炉根据金属的特性和要求,可以选择电阻加热炉、感应加热炉等。
熔化后的金属成为液态状态,称为金属熔体。
5. 金属注入将金属熔体通过注具注入模具中。
注入过程需要准确控制注入速度和压力,以及金属熔体的温度和流动性。
通常采用压力差和重力的作用,在模具底部设置冷却水进行凝固和固化。
6. 冷却和固化待金属熔体注入模具中后,利用模具的导热性将金属熔体迅速冷却,使其凝固成铸件的形状。
通过控制冷却速度和时间,可以获得不同的金属结构和性能。
7. 铸件脱模在金属熔体凝固成铸件后,需将模具拆开,将铸件从模具中取出。
脱模时需注意铸件的形状和尺寸,避免损坏铸件。
8. 表面处理将脱模的铸件进行表面处理,包括去除表面氧化层、修复毛刺和缺陷等。
这些处理措施可以提高铸件的表面光洁度和质量。
9. 后续加工根据铸件的要求和用途,可能需要进行一些后续加工,例如切割、钻孔、抛光和热处理等。
这些加工措施可以改善铸件的精度、强度和耐腐蚀性。
10. 检验和质量控制最后,对铸件进行检验和质量控制。
检验包括尺寸检查、力学性能测试和金属成分分析等。
电铸工艺_??????

电铸工艺
电铸工艺是一种利用电极的电流来控制熔融金属的液态流动,通过电化学作用在工作模具中沉积金属以制造零件或
制品的制造工艺。
它包括以下几个主要步骤:
1. 准备工作:准备金属材料、模具和电极等必要的工具和
设备。
同时,确保工作环境符合安全要求。
2. 设计模具:根据要制造的零件或制品的形状和尺寸,设
计相应的模具。
模具可以是单一的,也可以是多个组成的。
3. 铸模准备:将模具安装在适当的设备上,并确保其保持
水平和稳定。
在模具中涂抹适量的模具光油,以防止熔融
金属黏附在模具上。
4. 准备电解液:根据所使用的金属和工艺要求,配制适合
的电解液。
电解液是由金属盐和溶剂等组成的。
5. 运行设备:将模具安装在电铸设备中,并确保其与电源
和控制系统正确连接。
调整电流、温度和时间等参数,以
控制金属的沉积速度和薄度。
6. 电铸操作:开始电铸过程,将熔融金属注入模具中,并
使其流动和沉积。
通过控制电流的大小和时间的长短,调
节金属的沉积速度和厚度。
7. 确认质量:待金属完全冷却后,取出模具,检查制造的
零件或制品是否符合设计要求。
如有需要,对其进行后续
的热处理、表面处理或其它加工工序。
总的来说,电铸工艺具有高生产效率、产品成型精度高、
材料利用率高等优点。
它广泛应用于电子设备、汽车工业、航空航天等领域的零部件制造。
电铸工艺流程电铸的特点原理及应用

电铸工艺流程电铸的特点原理及应用
一、特点:
1.精度高:电铸工艺流程可以制造出形状复杂的零件,在精密领域有
广泛应用。
2.表面光滑:由于电解液的流动状态和离子的受电场作用,电铸零件
的表面很光滑,无需经过后续的抛光处理。
3.成本低:相对于传统的机械加工方法,电铸只需要少量的原材料和
设备,成本较低。
4.生产效率高:电铸可以实现批量生产,提高生产效率。
二、原理:
电铸是指在电场的作用下,由溶解在电解液中的金属离子通过还原反
应沉积在电极上的一种金属加工方法。
其基本原理主要包括以下几个方面:
2.电解液中电场的作用:当电流通过电解液时,形成电场,使电解液
中的金属离子发生迁移,向电极方向运动。
3.金属的沉积:金属离子到达电极上后,受电极的还原作用,将金属
离子还原为金属,沉积在电极表面形成金属层。
三、应用:
由于电铸工艺流程具有精度高、表面光滑、成本低、生产效率高等特点,广泛应用于各个领域,如下:
1.珠宝加工:电铸技术可以制造出精美、细致的珠宝首饰。
2.模具制造:电铸可以制造出具有复杂形状的模具,用于塑料注射、
压铸等行业。
3.制造复杂形状的零件:电铸可以制造出形状复杂、精度高的金属零件,如微型轴承、声学器件等。
4.表面处理:电铸可以用于金属的镀层加工,如镀金、镀银等。
5.光学元件制造:电铸可以制造出高精度的光学元件,如光学反射镜、光学棱镜等。
综上所述,电铸工艺流程在精度高、表面光滑、成本低、生产效率高
等方面具有优势,并广泛应用于珠宝加工、模具制造、制造复杂形状的零件、表面处理、光学元件制造等领域。
模具电铸件工艺流程
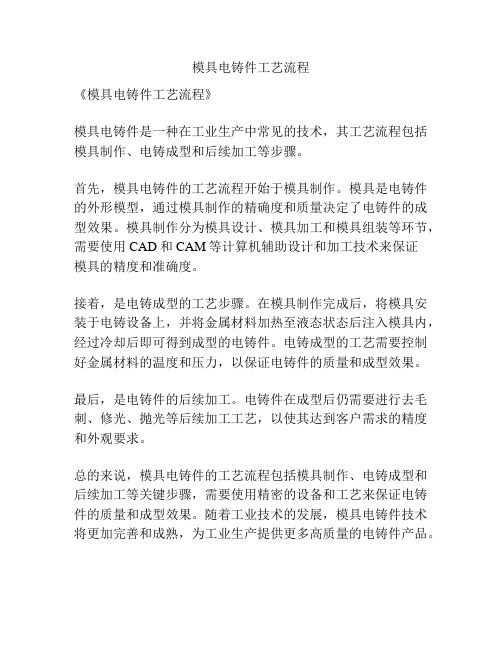
模具电铸件工艺流程
《模具电铸件工艺流程》
模具电铸件是一种在工业生产中常见的技术,其工艺流程包括模具制作、电铸成型和后续加工等步骤。
首先,模具电铸件的工艺流程开始于模具制作。
模具是电铸件的外形模型,通过模具制作的精确度和质量决定了电铸件的成型效果。
模具制作分为模具设计、模具加工和模具组装等环节,需要使用CAD和CAM等计算机辅助设计和加工技术来保证
模具的精度和准确度。
接着,是电铸成型的工艺步骤。
在模具制作完成后,将模具安装于电铸设备上,并将金属材料加热至液态状态后注入模具内,经过冷却后即可得到成型的电铸件。
电铸成型的工艺需要控制好金属材料的温度和压力,以保证电铸件的质量和成型效果。
最后,是电铸件的后续加工。
电铸件在成型后仍需要进行去毛刺、修光、抛光等后续加工工艺,以使其达到客户需求的精度和外观要求。
总的来说,模具电铸件的工艺流程包括模具制作、电铸成型和后续加工等关键步骤,需要使用精密的设备和工艺来保证电铸件的质量和成型效果。
随着工业技术的发展,模具电铸件技术将更加完善和成熟,为工业生产提供更多高质量的电铸件产品。
什么是电铸工艺

什么是电铸工艺?它有什么特点?电铸是在芯模表面电沉积金属,然后使两者分离来制取零件的工艺。
其基本原理与电镀相同,其区别在于电镀层要与基材牢固结合,而电铸层要与基材(芯模)分离;电镀层的厚度一般只有几微米到几十微米,而电铸层有零点几毫米到几毫米。
作为一种金属成型加工的工艺,电铸具有下述优点:1)能准确的复制出芯模的表面形貌。
如用电铸镍制造压制唱片或光盘的压膜。
2)可将难以甚至不能进行的内型面加工转变为容易进行的外型面加工,从而可大大提高加工零件的精度。
如电铸生产特殊型面的波导管、气切割嘴、塑料注射成型模具型腔。
3)容易得到由不同金属或金属与非金属组合的多层结构件。
如在芯模上电沉积薄的金、银、铜层后再缠绕碳纤维.环氧复合材料来制作轻型波导。
4)可电铸连接某些不能或不便于焊接的材料。
这是电铸加工的一种延伸。
如可电铸连接不锈钢一铝(或钛、铍)接头。
5)对电铸零件的尺寸原则上没有限制。
如可电铸长达5m、电铸层约lOmm的风洞喷管内壁,在不锈钢芯模上电铸出连续的、厚度约10μm的镍箔。
电铸的主要缺点是:1)在复杂型面的芯模表面难以得到厚度均匀的电铸层。
但可用对其表面进行机加工的方式予以补偿。
2)由于电铸层对芯模表面的复制性好,使其表面上的划伤等缺陷也会复制到电铸产品上。
3)生产周期长(薄壁件除外)。
一般沉积速度为:铜0.04~0.2mm/h、镍0.02~0.1mm/h、铁0.02~0.15mm/h。
原则上,凡能电沉积的金属或合金均可用于电铸,但从其性能、成本和工艺上考虑,尚有铜、镍、铁、镍钴合金等少数几种有实用价值。
目前在工业中广泛应用的只有铜和镍。
微电铸工艺—工艺参数

理工大学研究生试卷系别:机械工程学院课程名称微制造与微机械电子系统学号:姓名:考试时间:2013年1 月15 日微电铸工艺—工艺参数(理工大学机械工程学院116024)摘要:随着MEMS和LIGA两种技术的发展,微电铸工艺以其独特的优势,受到越来越多的关注。
本文介绍了微电铸的基本原理和特点及其一些研究现状和发展趋势。
文中着重强调了微电铸工艺的工艺参数,如电源波形,PH值,阴极电流密度,空气搅拌,电解液温度等。
以及研究人员为了得到更好的铸层效果,对其工艺参数进行优化所取得的成就,体现在气孔问题的解决,残余应力的消除,镀层不均的改善等。
关键词:微细加工微电铸工艺参数Micro-lectroforming Technology—Process Parameters (Dalian University of Technology,Department of Mechanical Engineering, DaLian 116024)Abstract:With the development of the technology of MEMS and LIGA, Micro-electroforming technology with its unique advantagesis inducing more and more attention.This Paper mainly introduced the fundamental and characteristics of micro-electroforming, and its some research and development trends. The article emphasized the process parameters of the micro -electroforming technology, including Power waveform,PH value,cathode current density, stirring,temperature of electrolyte and so on.As well as in order to get a better cast layer,researchers optimize the process parameters to obtain achievements,including the solution of the problem to hole,the elimination of residual internal stress,the improvement of poor evenness and so on.Key words: Micro-fabrication Micro—electroforming Process parameters0 前言微电铸工艺(Micro Electroforming Technology)是随着MEMS技术的快速发展,在继承传统电铸工艺特点的基础上,形成是一种非硅基微细结构加工的重要精密电铸技术,广泛用于MEMS技术领域[1]。
电铸工艺
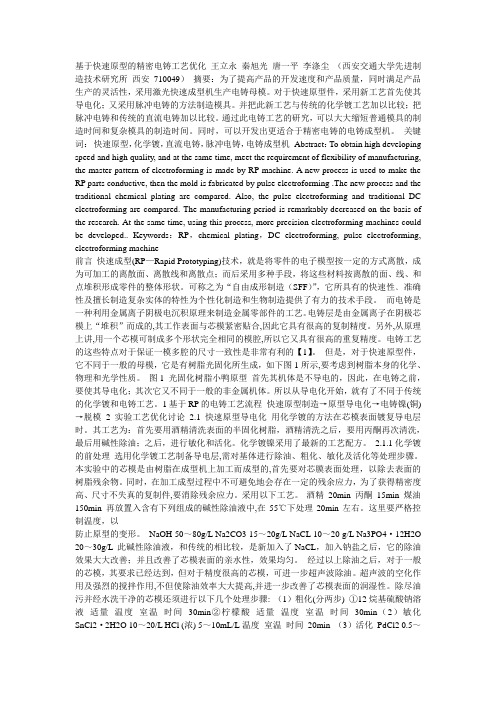
基于快速原型的精密电铸工艺优化王立永秦旭光唐一平李涤尘(西安交通大学先进制造技术研究所西安710049)摘要:为了提高产品的开发速度和产品质量,同时满足产品生产的灵活性,采用激光快速成型机生产电铸母模。
对于快速原型件,采用新工艺首先使其导电化;又采用脉冲电铸的方法制造模具。
并把此新工艺与传统的化学镀工艺加以比较;把脉冲电铸和传统的直流电铸加以比较。
通过此电铸工艺的研究,可以大大缩短普通模具的制造时间和复杂模具的制造时间。
同时,可以开发出更适合于精密电铸的电铸成型机。
关键词:快速原型,化学镀,直流电铸,脉冲电铸,电铸成型机Abstract:To obtain high developing speed and high quality, and at the same time, meet the requirement of flexibility of manufacturing, the master pattern of electroforming is made by RP machine. A new process is used to make the RP parts conductive, then the mold is fabricated by pulse electroforming .The new process and the traditional chemical plating are compared. Also, the pulse electroforming and traditional DC electroforming are compared. The manufacturing period is remarkably decreased on the basis of the research. At the same time, using this process, more precision electroforming machines could be developed.. Keywords:RP,chemical plating,DC electroforming, pulse electroforming, electroforming machine前言快速成型(RP—Rapid Prototyping)技术,就是将零件的电子模型按一定的方式离散,成为可加工的离散面、离散线和离散点;而后采用多种手段,将这些材料按离散的面、线、和点堆积形成零件的整体形状。
电铸工艺的原理和特点

电铸工艺的原理和特点
1. 嘿,你知道电铸工艺到底是个啥玩意儿吗?就好比用魔法把金属一点点“变”出来!比如说,想要个精致的小饰品,就可以通过电铸工艺把它给“变”出来哦!
2. 电铸工艺的原理啊,简单来说,就是让金属离子乖乖听话,一层一层地堆积起来呢!这不就像搭积木一样,一点点堆出想要的形状嘛!像一些复杂的模具就是这么制造出来的呀!
3. 哇塞,电铸工艺的特点那可厉害了!它能做出超精细的东西,精细到让人惊叹!这就跟微雕艺术似的,那么小却那么完美,比如那些超小的电子元件!
4. 你想想看,电铸工艺能让金属拥有那么神奇的变化,岂不是很妙?就像能赋予金属新的生命一样!一些高级的艺术品不就是电铸工艺的杰作嘛!
5. 电铸工艺厉害就厉害在它的稳定性啊!一直能保持那么好的效果,这多让人安心啊!就如同一个靠谱的朋友,永远不会掉链子,像那些高质量的工业零部件!
6. 哎呀,电铸工艺能精准地复制出各种形状,这多牛啊!简直就是复制粘贴的高手啊!像那些需要一模一样的零件不就靠它嘛!
7. 电铸工艺还有个特点,就是能做出很薄的金属层哦,薄得惊人!这就像一张纸那么薄,却有着大大的能量,比如那些超薄的金属箔!
8. 难道你不觉得电铸工艺特别神奇吗?能把普通的金属变得这么不普通!就好比灰姑娘摇身一变成了公主,那些华丽的装饰很多都是电铸工艺的成果呀!
9. 电铸工艺真的是超厉害的,它能创造出无数让人惊喜的东西,给我们的生活带来了很多的精彩和便利呀!。
- 1、下载文档前请自行甄别文档内容的完整性,平台不提供额外的编辑、内容补充、找答案等附加服务。
- 2、"仅部分预览"的文档,不可在线预览部分如存在完整性等问题,可反馈申请退款(可完整预览的文档不适用该条件!)。
- 3、如文档侵犯您的权益,请联系客服反馈,我们会尽快为您处理(人工客服工作时间:9:00-18:30)。
微电铸的工艺参数等探究0 前言微电铸工艺(microelect roforming technology) 是在传统电铸工艺的基础上建立起来的新概念,具有微小结构成型、复杂结构成型、高精度和批量生产等突出优点,它既可以看作是在微细加工模具基础上的传统电铸技术的延伸,也可以认为是掩膜电镀在高深宽比方向发展的结果,微电铸工艺是LIGA/准LIGA 技术的核心内容,其中LIGA是德文Lithographie、Galvanoformung和Abformung三个词的缩写,是X射线深层光刻、微电铸和微复制工艺的完美结合,在MEMS技术领域有广泛应用[1]。
从本质上分析,LIGA/准LIGA工艺微电铸可以分为性质不同的两个阶段:第一阶段是在掩模微结构的深层填充金属;第二阶段是在整个光刻胶和金属结构表面沉积厚度为6-10mm的厚金属膜,以便加工成压铸膜的基座。
1 微电铸工艺的研究进展与趋势对微电铸工艺的技术难点,研究人员在理论分析的基础上,从微电铸过程的数值模拟和工作参数试验优化等方面开展工作,探索微电铸的内在规律,取得了一系列进展,形成一些有重要参考价值的工作规范和指导意见,有力的促进了微电铸技术在MEMS领域的广泛应用[2]。
首先,基于高深宽比掩膜微结构是微电铸工艺关键影响因素的认识,建立了能够体现高深宽比微区传质特征的电极界面模型。
在微流体运动中引入高深宽比结构因素,建立了能够体现高深宽比微结构对界面稳定层增厚产生影响的电极界面物理模型。
其次,通过数值解析,系统分析一般镀液体系典型结构中电流密度再分布的规律。
如果待镀微区的开口尺寸较大,也就是掩膜微结构深宽比较小,则微电铸电流在沉积区域的再分布并不充分,靠近掩膜边缘的电流密度将显著高于中心部位,形成边缘高而中间低的马鞍型厚度分布这是掩膜电镀体系中常见的厚度分布样式。
如果待镀微区开口较小,也就是高深宽比微结构掩膜存在的情形,则在进入掩膜开口区域之后,电流密度将在传质阻力的作用下实现充分再分布,形成中间部分电流密度较大,整体镀层厚度比较均匀的理想结果。
微电铸工艺是LIGA/ UV-LIGA技术的核心内容,在MEMS技术和微/纳米制造领域中有着良好的应用前景[3]。
作为一种先进的制造技术,微电铸工艺主要用于制作各种精密、异型、复杂、微细等难以用传统加工方法制得的或加工成本很高的结构,适用于航空、航天、核工业、仪器仪表、微型机械等高新技术领域,并受到日益广泛的关注。
然而,微电铸工艺中存在的铸层厚度均匀性差、制作周期长、残留内应力大、铸层易出现缺陷及硬度低等不足也严重制约着其应用与发展,因此有必要对其进行深入的研究,解决其存在的问题,这对于提高微电铸的工艺水平、推动其发展具有非常重要的现实意义。
2 微电铸工艺介绍2.1 微电铸的基本过程图1为微电铸的简易装置示意图[4]。
主要由电极、电解液和电源组成。
电解液是电铸时金属离子的载体,是含有金属盐且易于导电的溶液。
通常包含有其他的添加剂以增强电铸的质量。
电极有阴极和阳极,阴极与电源的负极相连,一般是用于电铸微结构的样片,阳极与电源的正极相连,一般是与微电铸构件相同材料的金属物。
电铸的过程是一个电化学过程,它包括阳极过程、液相中传质过程(迁移,对流和扩散过程)以及阴极过程。
不同于表面电镀,微电铸是在深的微槽中填充金属,如何将电铸液快速均匀地传输到深的微槽中是微电铸的关键,必须因此对作为金属离子载体的电铸液成分的传输方式做详细的研究。
被沉积的离子主要以迁移扩散和对流三种方式传输电极。
图1 微电铸工作原理图2.2 微电铸的工艺特点与传统电铸工艺相比,微电铸工艺的特点主要体现在以下几个方面:1.作为待镀微型模具的光刻胶微结构不导电给深孔和细缝填充创造了可能。
传统电铸屏蔽作用,微细深孔难以密实填充,往往形成封闭空腔,但是,由各种深度光刻和刻蚀所形成的深槽、深孔,它们的侧壁一般不导电,对进入孔内电流并不产生屏蔽作用。
所以,合理调整电铸工作参数,可以通过微电铸填充微型缝隙和孔洞,制造高深宽比金属微结构。
2.镀件整体尺寸较小,起始面处于同一个平面上,但是被不导电的光刻胶分割成不同形状的区域。
这些微小区域或相互连通或相互隔绝。
但是由于处于同一个平面上,而且尺寸较小,即存在电流分布严重不均匀现象。
3.微电铸工件所要填充的孔洞都是盲孔,镀液的浸润和完全填充需要谨慎对待,微电铸过程中析出的氢气需要设法予以排除。
开口很小的微细盲孔很难为普通电解液所填充,表面张力是主要原因,添加表面活性剂以降低电镀液的表面张力是解决问题的常用方法,但是仍然必须辅以机械震动或超声搅拌等辅助措施才能够使存于盲孔内的气体离开,这些都要在工艺设计中加以考虑。
综合以上分析,微电铸不但兼有掩膜电镀和传统电铸两个方面的特征[5],而且还有其自身需要解决的独特技术问题, 因此需要开展深入系统的工艺技术研究。
3 微电铸的电铸液成分研究采用电化学测量技术,可以研究微电铸过程电极反应的典型电化学特征,提供镀液改良和工艺参数优化的电化学依据。
而采用电化学交流阻抗技术,可以对有高深宽比掩膜的微电铸电极进行电极反应动力学测量,从而明确观察到高深宽比掩膜所造成的传质阻力增加进而成为电沉积过程控制因素的电极现象。
在这样的条件下进行微电铸操作,按照传统电沉积理论是无法得到致密金属结构的针对性的电化学测量,借助有关电沉积过程电化学研究的长期技术积累,为电解液选择和关键工艺参数的快速优化提供了实证之外的便捷方法。
电铸镀液体系有氨基磺酸盐体系或硫酸盐体系,主盐浓度一般取该类电镀液的上限, 包含一定量的氯化物作为阳极活化剂。
按照各种组分在电铸过程中所起的作用,可将电解液看成是由主盐、导电盐、缓冲剂、阳极活化物、络合剂、添加剂等组成。
实践证明[6],一种较好的Watts 镍电解液的成分配比:硫酸镍(300g/L)、氯化镍(45g/L)、硼酸(35 g/L)、糖精(2g/L)、苯亚黄酸钠(0.2g/L)、十二烷基硫酸(O.2g/L)、光亮剂(2tool/L)、硫酸镁(20 g/L)、酒石酸钾钠(10g/L)、氯化钠(10g/L)。
由此电铸得到的镀层的晶粒不仅带有光泽,且增长稳定,厚度均匀,颗粒细小,无明显针孔现象。
为了实现深孔和微孔的电铸,首先要解决的关键技术一方面是使电镀液进入微孔,另一方面是改善电镀液的液相传质,使消耗的金属离子能得到及时的补充。
另外,影响深镀和镀层质量的因素还包括阴极极化、镀液电导率、阴极电流效率等[7]。
因此,有必要对电铸液中的各种主要成分作一简单的探讨。
1.氯化镍(F3GB)氯化镍(F3GB)是电镀液的主盐,也作为导电盐,含镍量高,可以提高极限电流密度限,而大量的氯离子可以有效地防止阳极钝化,提高电镀液的分散能力。
实验中加入硼酸(HIJ)是为了维持电铸液的PH值恒定,防止镍离子在阴极基体附近以碱性物质析出,造成电铸层疏松。
2.表面活性剂(十二烷基磺酸钠)电镀液表面张力的存在致使镀液不能进入微孔,另外,表面张力的存在也会影响阴极产生气泡的排除,使电流出现波动从而导致电铸质量下降,所以,表面张力的减小是微米电铸技术存在的最大难题。
加入少量的表面活性剂可以明显地减小电镀液表面张力,但是当表面活性剂的加入量大于一定量时,改变表面张力的效果不再十分明显,如果再加入过量或者加入其它的高分子物质会起到相反的效果。
所以,对于表面活性剂的添加,要控制量的加入。
3.极化度也是影响电镀层厚度的主要因素,极化度较大时,阴极表面上的镀层会更均匀。
①无添加剂时,极化现象随电流密度的增大而增加,极化度随电流密度的增大而降低。
电流密度低时, 电力线的边缘效应对镀层均匀性的影响较低。
此时, 阴极极化度很大, 在极化作用的影响下, 阴极面会产生二次电流分配, 使得微结构边缘处的电流密度高于中间处的电流密度, 从而得到呈帽形结构的镀层。
随着电流密度的升高, 极化度逐渐降低,对电力线分布的影响减弱, 而边缘效应的影响逐渐增强。
在这两种因素的共同作用下, 镀层表面趋于平整。
②有添加剂时通过与未加入添加剂的实验结果相比较,使用添加剂后得到的镀层均匀性的变化与未使用添加剂搅拌、搅拌速率、电解液使用时间、PH值等。
这些工艺参数对铸层均匀性的影响远不如电流密度等因素的影响那么明显。
在微电铸的过程中,搅拌增加了电解液中金属离子的扩散速率, 影响了电铸结构总体的均匀性。
而对于使用时间较长的电解液,尽管在电铸的过程中金属离子会从阳极得到补充,但电解液中金属离子的浓度还是会随着电铸的消耗而逐渐降低。
同时电解液中的析氢现象使得电解液的PH值逐渐升高,在一定程度上降低了铸层的沉积速率。
4 微电铸的工艺参数探究随着微机电系统(MEMS)和微影微电铸微模铸(LIGA)两种技术的发展,微电铸工艺正逐渐展现着其独特的魅力和发展潜力。
然而,现有工艺中存在的缺陷也严重阻碍了其进一步发展。
因此,对微电铸工艺进行深入研究,突破其工艺瓶颈,将对微加工工艺的应用和推广起着重要作用[8]。
微电铸是UV-LIGA的关键工艺,研究微电铸电极过程动力学特性,有助于弄清影响电极反应特别是阴极电沉积速度的各种因素,从而提出有效的工艺措施干预微电铸过程。
采用微加工制造的超微电极技术,可以在掩膜圈定的微区内测量其中的PH值和反应活性物质的空间分布,特别是稳定扩散层内的浓度梯度及其变化的信息直观地掌握微电铸反应过程中主要影响参数的微观分布及其变化规律,有助于建立更为切合实际的结构模型,指导工艺优化,也是进行微电铸技术研究的重要技术手段[9]。
更多的研究工作集中在实证方法方面, 对选定的镀液体系, 进行镀液组成、工作参数和微电铸结果的比较分析, 最终确定优化的工作条件,形成一些指导性的工艺规范,这对微电铸方法的使用者更具有实用价值,下面对一些已经形成共识的部分作一总结。
以电镀镍技术为例,对微电铸的工艺参数作简要的探究说明。
一、尽量少用添加剂控制目标镀层均匀性和内应力是最重要的控制目标。
出于控制内应力的目的, 微电铸镍一般不使用光亮添加剂,特别是第二类光亮剂。
但是作为消除应力的添加剂,在硫酸盐镀液体系中,常常使用糖精之类磺酸盐,而氨基磺酸类镀液则不需要添加,否则容易产生压应力,同样比较难以控制。
阳极含有氯化物的镀液可以采用一般纯镍阳极,适当的屏蔽或者仿形有助于改善电沉积的宏观均匀性, 必须使用阳极袋以减少颗粒杂质影响铸件性质的可能性[10]。
二、阴极电流密度低的电流密度容易满足良好深层微电铸的基本条件,避免因高深宽比微结构所造成的极限传质控制。
但是电流密度过低,阴极极化作用小,镀层的结晶晶粒较粗, 而且电流密度越小,镀速越慢,工作效率不高;电流密度过高, 虽然镀速很快,但是会使阴极附近严重缺乏金属离子,从而形成疏松的镀层应以深宽比最大的深孔或细缝为参考选择电流密度,深宽比越大,允许的电流密度越小。