弯管工艺方案
弯管制造典型工艺-1

目录弯管制造工艺流程示意图 (2)1.范围 (3)2.引用标准 (3)3.术语和定义 (3)4. 弯管制造工艺流程 (3)5. 弯管制造工艺要求 (3)6.通球表 (18)弯管制造工艺流程示意图注:1.D w≥133mm的钢管需做钢印移植;2.合金材料需做光谱检验。
1.范围本标准规定了锅炉平面弯管成形制造技术要求及验收要求。
本典型工艺适用于图1。
1~3个弯头的平面弯管,空间弯管可分解为几个平面弯管,分解后的平面弯管仍可参照本工艺。
图12.引用标准JB/T3375-2002《锅炉用材料入厂验收规则》JB/T1611-1993《锅炉管子制造技术条件》JB/T1612-1994《锅炉水压试验技术条件》JB/T1613-1993《锅炉受压元件焊接技术条件》JB/T1615-1991《锅炉油漆和包装技术条件》JB/T4308-1999《锅炉产品钢印及标记移植规定》JB/T4730.1~6-2005《承压设备无损检测》《蒸汽锅炉安全技术监察规程》19963.术语和定义H:停止点W:见证点4.弯管制造工艺流程见第2页《弯管制造工艺流程示意图》5.工艺要求5.1材料验收5.1.1 制造管子的材料应符合图纸设计要求,材料代用应按规定程序审批。
5.1.2制造管子用的钢材和焊接材料必须经过检验部门按JB/T3375-2002的规定进行入厂检验,未经检验或检验不合格者不准用于生产。
用于额定蒸汽压力不大于0.4MPa 的蒸汽锅炉和额定热功率不大于4.2MW 且额定出水温度小于120℃的热水锅炉的管子材料,如原始质量证明书齐全,且材料标记清晰、齐全时,可免于复检。
5.2 确定下料尺寸L5.2.1图1(c )中两端外倒角1×30°,且两端不需加长,下料长度L 按下列公式计算:公式一:()10232132211ααα++∆-⨯+++++++=l B L L L L L L L L b a中中 单位:mm 。
青浦区双层弯管加工工艺

青浦区双层弯管加工工艺一、工艺概述青浦区双层弯管加工工艺是一种将金属管材进行弯曲加工,使其呈现出双层结构的加工方法。
该工艺主要应用于汽车、机械制造等领域。
二、材料准备1.选材:根据客户要求和实际需要选择合适的金属管材,常用的有不锈钢、铜、铝等。
2.切割:将选好的金属管材按照所需长度进行切割,确保长度符合要求。
三、弯管加工1.弯曲:将切割好的金属管材放入弯曲机中进行弯曲加工。
在此过程中需要注意以下几点:(1)操作人员应按照图纸要求调整弯曲机的角度和半径,确保弯曲后的形状符合要求。
(2)在进行弯曲时,需要控制好力度和速度,避免过度变形或破损。
2.修整:在完成弯曲后,需要对双层结构部分进行修整。
具体操作如下:(1)使用手动或电动砂轮机对双层结构部分进行打磨和修整,使其表面光滑平整。
(2)对于不规则的双层结构部分,需要使用手动锉刀进行修整,保证其形状符合要求。
四、焊接处理1.清洗:在进行焊接处理前,需要对弯曲后的金属管材进行清洗,去除表面的油污和氧化物等杂质。
2.定位:将清洗好的金属管材放入定位器中进行定位。
在此过程中需要注意以下几点:(1)将金属管材和定位器按照图纸要求进行定位,确保双层结构部分对齐。
(2)使用夹具将金属管材固定在定位器上,避免移动或晃动。
3.焊接:在完成定位后,使用电弧焊或氩弧焊等方法对双层结构部分进行焊接。
在此过程中需要注意以下几点:(1)操作人员应按照图纸要求选择合适的焊接方法和参数,确保焊接质量符合要求。
(2)在进行焊接时需要控制好温度和速度,避免过度加热或冷却。
五、表面处理1.喷涂:在完成焊接处理后,需要对表面进行喷涂处理,以保护金属管材不受腐蚀和氧化。
具体操作如下:(1)使用砂纸或钢丝刷等工具对金属管材表面进行打磨和清洁。
(2)选择合适的喷涂设备和颜料,将颜料均匀地喷涂在金属管材表面上。
2.烘干:在完成喷涂后,需要对金属管材进行烘干处理,以加快颜料的干燥速度。
具体操作如下:(1)将喷涂好的金属管材放入烘箱中进行烘干处理。
冷弯管加工施工方案

冷弯管加工施工方案冷弯管加工是一种常见的金属加工技术,通过对金属管进行弯曲,可以得到不同弯度和形状的管材。
冷弯管在建筑、汽车、航空等领域广泛应用,具有重要的作用。
在进行冷弯管加工施工时,需要根据具体的需求和要求,制定合理的施工方案。
下面是一个1200字以上的冷弯管加工施工方案。
1.施工前的准备工作在进行冷弯管加工之前,需要进行一些准备工作,以确保施工的安全和顺利进行。
首先要对施工现场进行认真检查,确保没有安全隐患。
其次,要制定详细的施工计划,包括施工时间、工人配备、材料准备等。
最后,要对加工设备进行检查和维护,确保设备的正常运转。
2.材料准备在进行冷弯管加工时,需要准备一些必要的材料和工具。
首先要准备好需要加工的冷弯管,根据实际需求选择合适的材料。
其次,要准备好相应的刀具和夹具,以便进行加工。
此外,还需要准备一些辅助材料,如焊接材料和润滑剂等。
3.加工工艺冷弯管加工的具体工艺包括弯曲、切割、打孔等步骤。
在进行冷弯管弯曲时,要选择合适的弯曲半径和弯曲角度,以确保弯曲后的管材符合设计要求。
在进行切割和打孔时,要采用适当的刀具和工具,保证切割和打孔的质量和准确度。
4.安全措施在进行冷弯管加工时,要注意安全措施,确保工人的身体安全和设备的正常运行。
首先要针对冷弯管加工的特点和要求,提前做好安全培训和防护措施,如佩戴防护眼镜、手套和口罩等。
其次,要对加工设备和工作环境进行安全检查,发现问题及时解决。
最后,要加强施工现场的管理,做好施工记录和事故处理,确保施工的顺利进行。
5.质量控制在冷弯管加工过程中,要严格控制质量,确保加工件的准确度和表面质量。
首先要对加工前的管材进行检查,排除有缺陷的材料。
其次,在加工过程中要严格按照工艺要求进行操作,确保加工件的尺寸和形状的准确度。
最后,在加工完成后要进行材料检验和表面处理,确保加工件的质量和外观。
6.健全的服务体系为了提高冷弯管加工的效率和质量,建议建立健全的服务体系。
弯管制造典型工艺

目录弯管制造工艺流程示意图 (2)1.范围 (3)2.引用标准 (3)3.术语和定义 (3)4. 弯管制造工艺流程 (3)5. 弯管制造工艺要求 (3)6.通球表 (18)弯管制造工艺流程示意图1.范围可参照本工艺。
2.引用标准JB/T3375-2002JB/T1611-1993JB/T1612-1994JB/T1613-1993JB/T1615-1991JB/T4308-1999JB/T4730.1~3.术语和定义H:停止点4.5.工艺要求5.1材料验收5.1.1制造管子的材料应符合图纸设计要求,材料代用应按规定程序审批。
5.1.2 制造管子用的钢材和焊接材料必须经过检验部门按JB/T3375-2002的规定进行入厂检验,未经检验或检验不合格者不准用于生产。
用于额定蒸汽压力不大于0.4MPa 的蒸汽锅炉和额定热功率不大于4.2MW 且额定出水温度小于120℃的热水锅炉的管子材料,如原始质量证明书齐全,且材料标记清晰、齐全时,可免于复检。
5.2 确定下料尺寸L5.2.1图1(c )中两端外倒角1×30°,且两端不需加长,下料长度L 按下列公式计算:公式一:()10232132211ααα++∆-⨯+++++++=l B L L L L L L L L b a )))中中 单位:mm 。
式中:a L 、b L —管子两端直段长度,单位:mm 。
1中L 、2中L —管子中间直段长度,单位:mm 。
1α、2α、3α—分别为管子弯头的弯曲角度,单位为:度。
1L )、2L )、3L )—分别为管子弯头1α、2α、3α 对应中性层弧长,单位:mm 。
B —管子一端倒角需留的机械加工余量,其值按表1选取。
表1 单位:mm l∆—弯头每弯10°管子伸长量,其值可按下列公式二计算。
l ∆=︒180πα2r ⋅R r ⋅ 单位:公式二:mm 。
式中: r =2SD w - R —弯管半径,单位:mm 。
弯管制作工艺范文

弯管制作工艺范文1.材料准备:首先选择合适的管材作为原料,通常使用金属管材,如钢管、铝管、铜管等。
管材应具备良好的可弯曲性和韧性,以确保在加工过程中不会出现断裂或变形。
另外,还要根据弯曲的需求选择相应尺寸和材质的弯头和配件。
2.设计规划:根据需要制作弯管的要求,设计弯管的形状、角度和弯曲半径等参数。
在设计过程中需要考虑弯管的功能、安装环境、外观要求等因素。
3.弯管操作:将管材端部插入弯曲机械设备的弯头中,紧固好固定装置。
调整弯头的角度和位置,使其与设计要求一致。
启动弯曲机械设备,开始对管材进行弯曲加工。
通过调整弯曲机械设备的各个参数,如轴向力、旋转角度和速度等,使管材能够平稳、均匀地进行弯曲,避免局部过度压力导致管材变形或破损。
4.弯管检验:制作完成后,进行弯管的质量检验。
主要检查弯管的弯曲角度、形状和尺寸是否符合设计要求。
可以使用测量工具如坡度计、角尺、卷尺等进行测量。
同时,还需要检查弯管表面是否存在裂纹、凹陷或其他缺陷。
5.表面处理:根据需要对弯管的表面进行处理。
可采用砂光、抛光、喷涂等方法进行处理,以增加弯管的耐腐蚀性和美观度。
6.包装运输:根据弯管的尺寸和形状,选择合适的包装材料将其包装好。
在装箱过程中需要注意避免弯管的碰撞和磨损,以免影响其质量。
7.应用领域:弯管广泛应用于建筑、汽车、航空航天、石油化工等行业。
如建筑中的暖通空调管道、汽车中的排气管、航天器中的管路系统等。
总结:弯管制作工艺涉及到材料准备、设计规划、弯管操作、弯管检验、表面处理和包装运输等环节。
通过合理的设计和精湛的加工技术,可以制作出符合设计要求的高质量弯管。
sa210-a1弯管热处理工艺

sa210-a1弯管热处理工艺
SA210-A1是一种低碳钢,主要用于制造锅炉管和超级加热器管。
热处理工艺可以改善钢管的机械性能和耐腐蚀性。
SA210-A1的热处理工艺可以包括以下步骤:
1. 加热处理:将SA210-A1钢管加热到适当的温度,通常在800°C至900°C之间,保持一段时间,以使钢管内部组织发生
一定的相变。
这个过程被称为退火。
2. 空冷:将加热处理后的钢管从炉中取出,让其在空气中自然冷却到室温。
这个过程被称为空冷退火,可以使钢管的组织得到进一步调整,并提高其硬度和强度。
3. 淬火和回火:根据需要,钢管还可以进行淬火和回火处理,以进一步改善其机械性能。
淬火是将钢管迅速冷却至室温以下,通常使用水、油或盐溶液进行冷却。
回火是在淬火后将钢管加热到适当的温度,然后保持一段时间,最后进行空冷。
这个过程有助于减轻淬火过程中产生的内应力,并提高钢管的韧性。
4. 控制冷却:用于获得特定的组织和性能,可以通过调整冷却速率来实现。
例如,缓慢冷却可以产生细小的晶粒结构,提高钢管的韧性和耐腐蚀性。
总之,SA210-A1钢管的热处理工艺可以根据具体要求进行调整,以获得最佳的机械性能和耐腐蚀性能。
弯管制造典型工艺-1

目录弯管制造工艺流程示意图 (2)1.范围 (3)2.引用标准 (3)3.术语和定义 (3)4. 弯管制造工艺流程 (3)5. 弯管制造工艺要求 (3)6.通球表 (18)弯管制造工艺流程示意图注:1.D w≥133mm的钢管需做钢印移植;2.合金材料需做光谱检验。
1.范围本标准规定了锅炉平面弯管成形制造技术要求及验收要求。
本典型工艺适用于图1。
1~3个弯头的平面弯管,空间弯管可分解为几个平面弯管,分解后的平面弯管仍可参照本工艺。
图12.引用标准JB/T3375-2002《锅炉用材料入厂验收规则》JB/T1611-1993《锅炉管子制造技术条件》JB/T1612-1994《锅炉水压试验技术条件》JB/T1613-1993《锅炉受压元件焊接技术条件》JB/T1615-1991《锅炉油漆和包装技术条件》JB/T4308-1999《锅炉产品钢印及标记移植规定》JB/T4730.1~6-2005《承压设备无损检测》《蒸汽锅炉安全技术监察规程》19963.术语和定义H:停止点W:见证点4.弯管制造工艺流程见第2页《弯管制造工艺流程示意图》5.工艺要求5.1材料验收5.1.1 制造管子的材料应符合图纸设计要求,材料代用应按规定程序审批。
5.1.2制造管子用的钢材和焊接材料必须经过检验部门按JB/T3375-2002的规定进行入厂检验,未经检验或检验不合格者不准用于生产。
用于额定蒸汽压力不大于0.4MPa 的蒸汽锅炉和额定热功率不大于4.2MW 且额定出水温度小于120℃的热水锅炉的管子材料,如原始质量证明书齐全,且材料标记清晰、齐全时,可免于复检。
5.2 确定下料尺寸L5.2.1图1(c )中两端外倒角1×30°,且两端不需加长,下料长度L 按下列公式计算:公式一:()10232132211ααα++∆-⨯+++++++=l B L L L L L L L L b a中中 单位:mm 。
弯管制造典型工艺

目录弯管制造工艺流程示意图 (2)1.范围 (3)2.引用标准 (3)3.术语和定义 (3)4. 弯管制造工艺流程 (3)5. 弯管制造工艺要求 (3)6.通球表 (18)弯管制造工艺流程示意图1.范围本标准规定了锅炉平面弯管成形制造技术要求及验收要求。
本典型工艺适用于图1。
1~3个弯头的平面弯管,空间弯管可分解为几个平面弯管,分解后的平面弯管仍可参照本工艺。
图12.引用标准JB/T3375-2002《锅炉用材料入厂验收规则》JB/T1611-1993《锅炉管子制造技术条件》JB/T1612-1994《锅炉水压试验技术条件》JB/T1613-1993《锅炉受压元件焊接技术条件》JB/T1615-1991《锅炉油漆和包装技术条件》JB/T4308-1999《锅炉产品钢印及标记移植规定》JB/~6-2005《承压设备无损检测》《蒸汽锅炉安全技术监察规程》19963.术语和定义H:停止点 W:见证点4.弯管制造工艺流程见第2页《弯管制造工艺流程示意图》5.工艺要求5.1材料验收5.1.1制造管子的材料应符合图纸设计要求,材料代用应按规定程序审批。
5.1.2制造管子用的钢材和焊接材料必须经过检验部门按JB/T3375-2002的规定进行入厂检验,未经检验或检验不合格者不准用于生产。
用于额定蒸汽压力不大于的蒸汽锅炉和额定热功率不大于且额定出水温度小于120℃的热水锅炉的管子材料,如原始质量证明书齐全,且材料标记清晰、齐全时,可免于复检。
5.2 确定下料尺寸L5.2.1图1(c )中两端外倒角1×30°,且两端不需加长,下料长度L 按下列公式计算:公式一:()10232132211ααα++∆-⨯+++++++=l B L L L L L L L L b a中中 单位:mm 。
式中:a L 、b L —管子两端直段长度,单位:mm 。
1中L 、2中L —管子中间直段长度,单位:mm 。
弯管制作工艺范文

弯管制作工艺范文
要求能简要说明每一道工序和操作要求
一、制作工具
1.卷板机:用于弯管的加工,可以制作出各种不同的弯曲管,也可以
完成内外弯曲和任意角度的弯曲;
2.橡皮轮:用于调整弯曲管的位置,确保在施加力之前定位正确;
3.热收缩套管:用于保护弯管,使其不受外界影响;
4.弯曲测量器:用于测量弯管的角度,防止弯曲过度;
5.钻孔机:用于钻孔,制作管上的孔;
6.抛光机:用于抛光弯管表面,使其光滑无毛刺。
二、制作步骤
1.准备材料:根据选择的钢管材料,准备所需的管材及螺栓、垫圈等
必要的配件;
2.弯曲加工:把所需的钢管放入卷板机中,根据设计尺寸和要求进行
弯管加工,将弯管放入橡皮轮中,调节位置,施加力进行弯曲;
3.温度保护:当弯曲完成后,使用热收缩套管进行保护,防止弯管的
变形;
4.测量角度:使用弯曲测量器,测量好弯管的角度,确保角度在标准
要求范围之内;
5.钻孔:把弯管固定在钻孔机上,根据要求钻孔,保证孔位尺寸精确;
6.抛光:把弯管放入抛光机中,把弯管表面抛光,以保证表面光滑无毛刺;。
弯管加工工艺范文
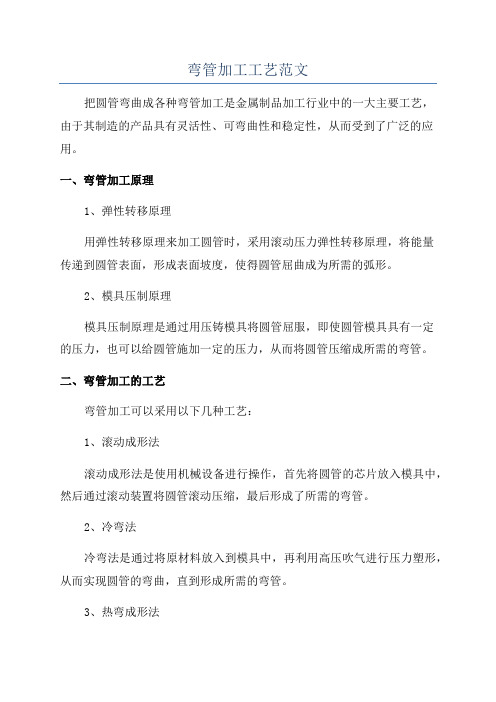
弯管加工工艺范文
把圆管弯曲成各种弯管加工是金属制品加工行业中的一大主要工艺,
由于其制造的产品具有灵活性、可弯曲性和稳定性,从而受到了广泛的应用。
一、弯管加工原理
1、弹性转移原理
用弹性转移原理来加工圆管时,采用滚动压力弹性转移原理,将能量
传递到圆管表面,形成表面坡度,使得圆管屈曲成为所需的弧形。
2、模具压制原理
模具压制原理是通过用压铸模具将圆管屈服,即使圆管模具具有一定
的压力,也可以给圆管施加一定的压力,从而将圆管压缩成所需的弯管。
二、弯管加工的工艺
弯管加工可以采用以下几种工艺:
1、滚动成形法
滚动成形法是使用机械设备进行操作,首先将圆管的芯片放入模具中,然后通过滚动装置将圆管滚动压缩,最后形成了所需的弯管。
2、冷弯法
冷弯法是通过将原材料放入到模具中,再利用高压吹气进行压力塑形,从而实现圆管的弯曲,直到形成所需的弯管。
3、热弯成形法
热弯成形法是通过将圆管热处理后,将其放入模具中,利用压力将其压塑成所需的形状,从而达到圆管弯曲的目的。
三、弯管加工的应用。
弯管制作工艺
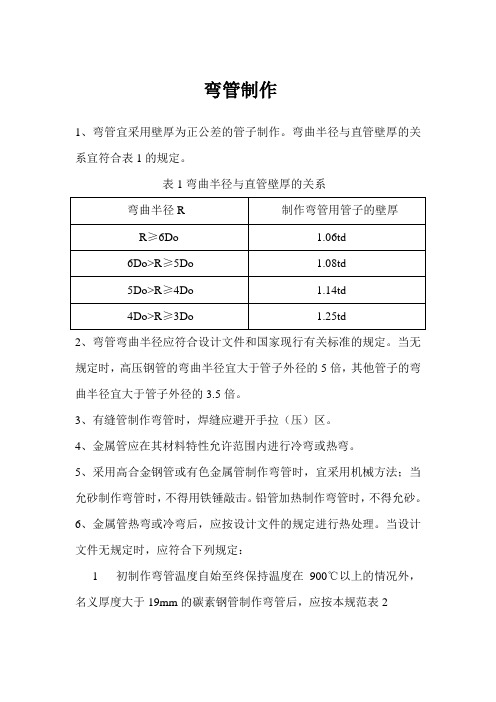
弯管制作1、弯管宜采用壁厚为正公差的管子制作。
弯曲半径与直管壁厚的关系宜符合表1的规定。
表1弯曲半径与直管壁厚的关系弯曲半径R 制作弯管用管子的壁厚R≥6Do 1.06td6Do>R≥5Do 1.08td5Do>R≥4Do 1.14td4Do>R≥3Do 1.25td2、弯管弯曲半径应符合设计文件和国家现行有关标准的规定。
当无规定时,高压钢管的弯曲半径宜大于管子外径的5倍,其他管子的弯曲半径宜大于管子外径的3.5倍。
3、有缝管制作弯管时,焊缝应避开手拉(压)区。
4、金属管应在其材料特性允许范围内进行冷弯或热弯。
5、采用高合金钢管或有色金属管制作弯管时,宜采用机械方法;当允砂制作弯管时,不得用铁锤敲击。
铅管加热制作弯管时,不得允砂。
6、金属管热弯或冷弯后,应按设计文件的规定进行热处理。
当设计文件无规定时,应符合下列规定:1 初制作弯管温度自始至终保持温度在900℃以上的情况外,名义厚度大于19mm的碳素钢管制作弯管后,应按本规范表2表2 管道热处理基本要求母材类别名义厚度t(mm)母材最小规定抗拉强度(Mpa)热处理温度(℃)恒温时间(mim/mm)最短恒温时间(h)碳钢(C)、≤19全部不要求——碳锰钢(C-Mn) >19 全部600~650 2.4 1 铬钼合金钢≤19≤490不要求——(C-Mo、Mn-Mo、Cr-Mo) >19 全部600~720 2.4 1 Cr≤0.5%全部>490 600~720 2.4 1 铬钼合金钢(C-Mo)≤13≤490不要求——0.5%<Cr≤2%>13 全部700~750 2.4 2全部>490 700~750 2.4 2 铬钼合金钢(Cr-Mo)≤13全部不要求——2.25%≤Cr≤3%>13 全部700~760 2.4 2 铬钼合金钢(Cr-Mo)3%<Cr≤10%全部全部700~760 2.4 2 马氏体不锈钢全部全部不要求——铁素体不锈钢全部全部不要求——奥氏体不锈钢全部全部不要求——低温镍钢≤19全部不要求——(Ni≤4%)>19 全部600~640 1.2 1 注:热处理的加热速率和冷却速率应符合下列规定:1 当加热温度升至400℃时,加热速率不应超过(205×25/t)℃/h,且不得大于205℃/h。
不锈钢弯管的制造工艺
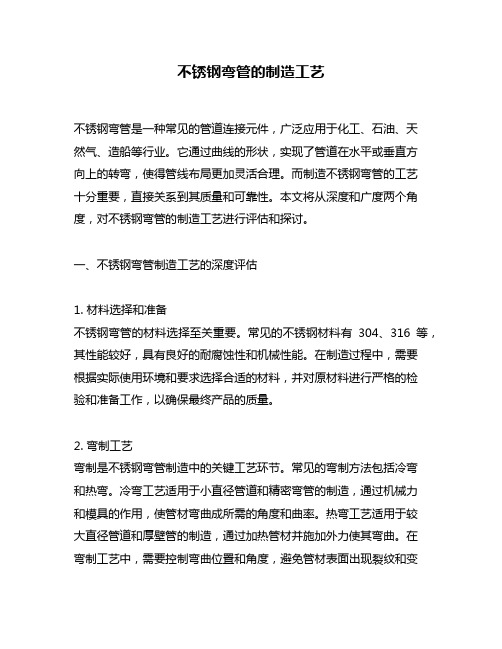
不锈钢弯管的制造工艺不锈钢弯管是一种常见的管道连接元件,广泛应用于化工、石油、天然气、造船等行业。
它通过曲线的形状,实现了管道在水平或垂直方向上的转弯,使得管线布局更加灵活合理。
而制造不锈钢弯管的工艺十分重要,直接关系到其质量和可靠性。
本文将从深度和广度两个角度,对不锈钢弯管的制造工艺进行评估和探讨。
一、不锈钢弯管制造工艺的深度评估1. 材料选择和准备不锈钢弯管的材料选择至关重要。
常见的不锈钢材料有304、316等,其性能较好,具有良好的耐腐蚀性和机械性能。
在制造过程中,需要根据实际使用环境和要求选择合适的材料,并对原材料进行严格的检验和准备工作,以确保最终产品的质量。
2. 弯制工艺弯制是不锈钢弯管制造中的关键工艺环节。
常见的弯制方法包括冷弯和热弯。
冷弯工艺适用于小直径管道和精密弯管的制造,通过机械力和模具的作用,使管材弯曲成所需的角度和曲率。
热弯工艺适用于较大直径管道和厚壁管的制造,通过加热管材并施加外力使其弯曲。
在弯制工艺中,需要控制弯曲位置和角度,避免管材表面出现裂纹和变形。
3. 焊接工艺不锈钢弯管在制造过程中可能需要焊接工艺。
焊接技术的选用对最终产品的质量和性能有着重要影响。
常见的焊接方法包括TIG焊和MIG/MAG焊。
TIG焊适用于对接焊缝和角焊缝的制造,具有焊缝美观、机械性能好等优点;MIG/MAG焊适用于对接焊缝的制造,具有焊接速度快、适用于大批量生产等优点。
在焊接过程中,需要控制焊接温度和速度,确保焊缝质量和强度。
4. 表面处理工艺不锈钢弯管的表面处理工艺主要包括酸洗、抛光和喷砂等。
酸洗工艺可以去除管材表面的氧化皮和污染物,提高管材的耐腐蚀性;抛光工艺可以改善管材表面的光洁度和美观度;喷砂工艺可以增加管材表面的粗糙度,提高涂层附着力。
表面处理工艺的选择应根据不锈钢弯管的使用环境和要求进行,并严格按照工艺规范进行操作。
二、不锈钢弯管制造工艺的广度评估1. 制造工艺优化制造工艺的优化是提高不锈钢弯管制造效率和质量的重要手段。
铜管u弯管工艺方法

铜管u弯管工艺方法铜管U弯管在很多地方都能用到呢,比如说家里的空调铜管有时候就需要做U弯管处理。
那这工艺方法都有啥呀?一、工具准备。
咱得先有合适的工具。
弯管器那是必不可少的啦。
就像厨师做菜得有锅铲一样,做铜管U弯管,弯管器就是咱的得力助手。
而且呀,这个弯管器得根据铜管的管径大小来选哦,不然就像小鞋穿大脚或者大脚穿小鞋,都不合适。
除了弯管器,可能还需要一些辅助的测量工具,像卷尺之类的,这样才能知道弯管的尺寸是不是准确。
二、铜管的前期处理。
铜管在弯管之前也得拾掇拾掇。
先把铜管检查一下,看看表面有没有坑坑洼洼或者裂缝啥的。
要是有这些小毛病,那弯管的时候可能就会出问题。
就好比一个人要是身体有点小毛病,去做剧烈运动就容易出岔子。
如果铜管上有脏东西,也得清理干净,不然脏东西可能就会影响弯管的质量。
三、弯管操作。
开始弯管啦。
把铜管放到弯管器里,要放稳当哦。
然后慢慢地用力开始弯。
这个时候就像在捏橡皮泥一样,不过铜管可不像橡皮泥那么软,得小心翼翼地来。
要是弯得太快或者用力不均匀,铜管可能就会变形得很难看,就不是咱们想要的漂亮的U形了。
而且在弯的过程中,要时刻看着弯管的角度,可不能弯过了头或者弯得不够。
这就需要咱的眼睛像小雷达一样,时刻盯着。
四、后期检查。
弯好之后呢,可不能就这么完事儿了。
要仔细检查一下弯管的质量。
看看U形是不是对称,铜管有没有出现褶皱或者瘪掉的地方。
如果有问题,那可能就得重新来一次。
这就像做完作业得检查一样,有错误就得改过来。
铜管U弯管工艺方法其实也不难,只要咱们细心一点,按照这些小步骤来,就能做出漂亮又合格的U弯管啦。
薄壁不锈钢管弯管工艺
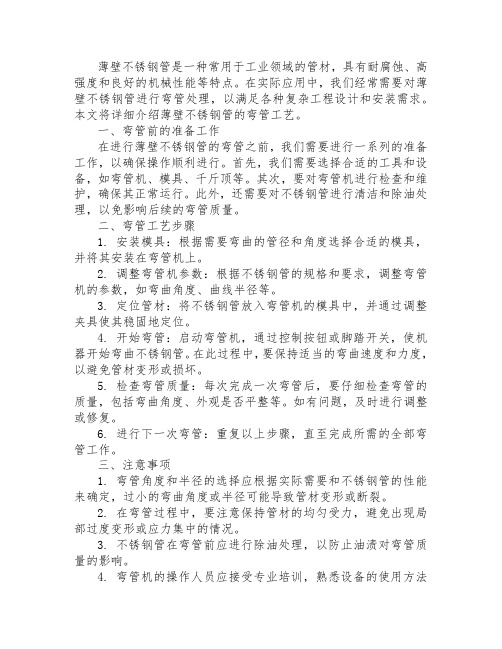
薄壁不锈钢管是一种常用于工业领域的管材,具有耐腐蚀、高强度和良好的机械性能等特点。
在实际应用中,我们经常需要对薄壁不锈钢管进行弯管处理,以满足各种复杂工程设计和安装需求。
本文将详细介绍薄壁不锈钢管的弯管工艺。
一、弯管前的准备工作在进行薄壁不锈钢管的弯管之前,我们需要进行一系列的准备工作,以确保操作顺利进行。
首先,我们需要选择合适的工具和设备,如弯管机、模具、千斤顶等。
其次,要对弯管机进行检查和维护,确保其正常运行。
此外,还需要对不锈钢管进行清洁和除油处理,以免影响后续的弯管质量。
二、弯管工艺步骤1. 安装模具:根据需要弯曲的管径和角度选择合适的模具,并将其安装在弯管机上。
2. 调整弯管机参数:根据不锈钢管的规格和要求,调整弯管机的参数,如弯曲角度、曲线半径等。
3. 定位管材:将不锈钢管放入弯管机的模具中,并通过调整夹具使其稳固地定位。
4. 开始弯管:启动弯管机,通过控制按钮或脚踏开关,使机器开始弯曲不锈钢管。
在此过程中,要保持适当的弯曲速度和力度,以避免管材变形或损坏。
5. 检查弯管质量:每次完成一次弯管后,要仔细检查弯管的质量,包括弯曲角度、外观是否平整等。
如有问题,及时进行调整或修复。
6. 进行下一次弯管:重复以上步骤,直至完成所需的全部弯管工作。
三、注意事项1. 弯管角度和半径的选择应根据实际需要和不锈钢管的性能来确定,过小的弯曲角度或半径可能导致管材变形或断裂。
2. 在弯管过程中,要注意保持管材的均匀受力,避免出现局部过度变形或应力集中的情况。
3. 不锈钢管在弯管前应进行除油处理,以防止油渍对弯管质量的影响。
4. 弯管机的操作人员应接受专业培训,熟悉设备的使用方法和安全操作规程,以确保人身安全和操作质量。
四、常见问题及解决办法1. 弯管过程中出现管材折断的情况:可能是由于不锈钢管的质量问题或者弯曲力度过大导致的,需要更换质量可靠的管材或调整弯曲参数。
2. 弯管后出现不平整或外观不良的情况:可能是由于模具损坏或者弯管机参数调整不当导致的,需要进行相应的维修或调整。
弯管制作工艺方案

弯管制作工艺方案1弯管加工制作工艺流程2弯管加工方式本工程结构呈花瓣形状,构件多为空间多向弯曲,深化设计过程中运用多段平面弯管进行拟合的思路,将空间多向弯曲构件转换为平面内单向弯曲构件,有效地解决了空间多向弯曲构件加工的难题,使得加工效率更高,精度更有保证。
弯管加工一般采用两种方式,分别为冷弯加工成形与热加工成形。
对于需进行弯管的构件,截面≥800mm的钢管采用中频弯圆,对截面<800mm的钢管采用机械冷弯。
先确定其弯曲半径、弯曲管件的起始点及终点,并做好标记,然后用JXW-700型弯管机或弯制模具进行管件的弯圆。
弯曲后,钢管表面不能出现折痕和凹凸不平的现象。
弯圆后切割端头,并在工装划出纵向直线,相隔 90°四条及节点圆周环线,并打样冲眼,以便于钢管的对接。
当钢管采用热加工成形时,一般采用中频或高频弯管机,加热温度应控制在900~1000℃;碳素结构钢管和低合金结构管在温度下降到400℃以下时应结束加工,低合金结构钢应自然冷却。
中高频弯圆的钢管避免多次加热。
多次加热会导致材质变脆,造成硬化。
同时,加工温度过低时,应避免强行弯曲。
JXW-700型弯管机制弯模具中频弯管机中频弯管机制作成品3弯管放样利用计算机数控模拟放样,使单根杆件两端在同一水平线内,确定弯管半径,放样时应留出足够的余量,如下图:4弯管厚度减薄补偿弯管在制作过程中,由于外径表面存在拉伸作用,厚度难以避免存在减薄的情况,按照相关规范,壁厚与设计壁厚的的差值不得大于±1mm及设计壁厚的10%中的较小值。
如果制作成品差值不满足要求时,需加大管壁以满足设计要求。
弯管制作厚度减薄率计算方式如下:式中φ——弯曲角度,radD——外直径,mmδ1——弯曲后外侧管壁壁厚,mmδ0——弯曲前外侧管壁壁厚,mm根据以上公式可知弯管壁厚减薄率的计算公式为:式中C——弯管壁厚减薄率由于理论计算与实际操作偏差,弯管批量制作前,应进行试弯试验,经检定合格后得出相应工艺参数后,才能进行批量制作。
冷弯管弯制工法

冷弯管弯制工法一、工法特点1、能够很好的控制冷弯管管口、弯曲段的椭圆度,平面度,直焊缝高度。
2、能够对母材管口,外防腐层和减阻涂层起到很好的保护。
二、适用围本工法适用于管径φ400mm-φ1066mm围,管壁厚7.1-26.2毫米之间,曲率半径≥40D,X50-X70材质的钢管。
三、工艺原理1、屈服原理:通过在钢管预定的地方(钢管的、外部)施加一定的作用力,使之发生塑性变形,达到一定的弯曲角度的施工原理。
2、曲率半径:冷弯管就是通过若干次微分塑性变形,达到圆弧状所形成的。
进给量为300毫米,曲率半径大于或等于40D。
四、工艺流程弯管工艺流程图五、工法要点(一)施工准备1、施工场地选择施工场地宽阔平整,有足够的工作面积,且要求布局合理。
在工作区不允许有高压线等不适合吊装作业的障碍物,作业地面要求平整、坚硬,适合运输设备的进入和装卸。
2、管堆的制作根据冷弯管的堆放规则,弯管应堆放在管堆上,管堆用不损害钢管材质和防腐层的材料堆砌而成。
不允许放置在石头、砖瓦等硬性物体上。
管堆的高度应保证弯管离开地面200mm以上,且弯管只能进行单层堆放。
3、设备的就位为严格执行施工规,弯管机必须水平放置,且具有可调性。
在设备下方垫一层碎石,既可以强化地基,还可以调整设备的平整度,然后组装、调试好设备,在弯管施工前应校平,前后左右误差不得大于0.1°。
4、其它制作晴雨棚,有利于保护好人、设备;制作安全标语、警示牌,做到现场文明施工,争创优质工程。
(二)弯管准备1、正式弯管前,应作好以下几项工作:①调整胎芯的主要参数(根据钢管壁厚调整胎芯的型号);②弯管机性能应能满足弯管工艺参数,具有良好的工作状态,准确的量值显示和安全性;③配合设备应能满足弯管要求,具有良好的工作状态;④应根据委托单位的委托单加工;⑤应对弯管机模具和待加工的钢管、外进行清理,防止杂物将外防腐层和减阻涂层划伤。
2、在弯管机前设两个导管架,目的是以便在防腐管进入设备前能够调整直焊缝的位置;且需要用软物体捆绑好,以免破坏防腐层和母材,且它们之间的最佳距离为7米,有利于施工。
弯管加工工艺流程

弯管加工工艺流程1.弯管夹具的分析考虑到装夹方便,我们设计了弯管夹具。
在花盘上安装一个弯管,以管端面和内孔定位,夹紧19 mm处。
此夹具设计简单,但定位误差太大。
首先,受工件尺寸公差的影响,无法保证加工部位的中心线与夹具的回转轴线同心要求;其次,工件所加工圆柱面的轴线相对于其另一圆柱轴线的旋转自由度无法限制。
所以,第一种方案还没有实施便宣告失败。
2.V形滑块夹具的分析在总结第一套方案经验的基础上,我们又设计了V形滑块夹具。
如图3,夹具有两对V形滑块4可在导板5中滑动,通过调节螺钉2的旋转来拖动V形滑块以起到定心并夹紧的作用。
夹具在夹紧19 mm处的同时,21.5mm凸起结构起到了轴向定位作用。
理论分析证明夹具符合设计原理,可以使用。
此夹具投入生产后,暴露出了一些缺陷。
首先,因19 mm处尺寸大小一致性差,经常导致必须同时调整两个V形滑块来找正的现象,极大地降低了生产效率,同时废品率居高不下。
其次,工件装夹费时,V形滑块要后退较大的距离,才能卸下工件。
实践证明,此夹具不能适应大批量的生产。
3.一槽一柱夹具的分析在充分总结和分析先前失败经验的基础上,我们又设计了一槽一柱的夹具。
如图4,此夹具主要由一个开有横向通槽的本体1和顶尖套2组成。
使用时,只需三爪自定心卡盘夹紧本体1,工件如图所示放入槽内,由顶尖套2(装在车床顶尖上)轻轻顶紧工件即可。
定位原理:靠19.5mm的槽卡住工件21.5mm凸起结构处来轴向定位,靠顶尖套的60 锥体和15.5 mm圆柱面完成径向定位,同时槽结构本身即起到拨杆作用,限制工件绕机床回转轴线转动。
夹具的制作与使用注意事项:本体1在加工19.5mm的通槽时,应保证槽通过圆柱的中心线;同时,考虑到循环管在弯曲时,局部存在尺寸变大而超过19 mm宽,可将槽底加宽一些(如图4宽22 mm的槽);顶尖套2的60 锥体起径向定位和顶紧的作用,锥体前部圆柱起辅助定位和支承作用,所以都必须与顶尖4有一定同轴度要求:因顶尖套与顶尖为紧密配合,所以顶尖套需留有排气孔,以利于其与顶尖的装配。
- 1、下载文档前请自行甄别文档内容的完整性,平台不提供额外的编辑、内容补充、找答案等附加服务。
- 2、"仅部分预览"的文档,不可在线预览部分如存在完整性等问题,可反馈申请退款(可完整预览的文档不适用该条件!)。
- 3、如文档侵犯您的权益,请联系客服反馈,我们会尽快为您处理(人工客服工作时间:9:00-18:30)。
冷弯管煨制工艺1)第一弯制点的确定。
弯管机弯制点到定位点的距离为2.45米,西气东输标准要求的直管段为大于或等于2米,每次弯制角度不能大于0.5度,冷弯管的曲率半径大于或等于40D。
举例:如需煨制一个9度的冷弯管,冷弯管的长度为11800毫米,每次以0.5度计算,需18次,每次的进给量为300毫米,弧线长:18×300=5400毫米直管段:11800-5400=6400毫米但根据设备的结构尺寸和厂家的要求,前端的最短距离为2450米,后端的最短距离为3200米,所以直管段为2450+3200=5650毫米,考虑到管材外管的均匀性,前端留出一部分,即求出管端伸出量为6400-5650=750毫米。
注意:实践证明该算法只在理论上能够实现,而且忽略了对管端的影响,然而,西气东输的标准关键就是在此,是重点也是难点,实际上,在第一次煨制点达到0.5度,对端口的椭圆度影响极大,不可能达到西气东输的标准(就意大利Goriziane公司生产的设备而言),而且,直防腐管的椭圆度就存在,所以端口的伸长量可采用以下经验值(或方法)a、如果以0.5度/次计算,那么曲率半径为:D Dn 84.3337.3425.0sin 15.02sin 15.0===Φ=米 b 、给每根管子留出2次余量,所以弧线长为20×300=6000毫米直管段为11800-6000=5800毫米伸长量为5800-5650=150毫米这样能够增大冷弯管的曲率半径,达到标准的要求。
c 、如果煨制较小度数的冷弯管,可以在端口段弯制较小度数,有利于减小管口的椭圆图。
2)弯管工艺a 、在弯管机前设有两个土台(软物体即可),以便在管材进入设备前能够调整直焊缝的位置(详见西气东输管道工程冷弯管弯制技术标准,以下简称标准)。
b 、用长度大于7-8米的钢卷尺划出防腐管的中心线,以便于用吊带(宽600毫米,载重量为32吨)能够平衡的吊起,可以水平的进入弯管机。
c 、防腐管进入设备的方向有两种可能,视具体情况而定,Ⅰ)当防腐管弯制不需要内胎芯时,可以从两端进入。
Ⅱ)当防腐管弯制需要内胎芯时,只能从前端进入。
Ⅲ)按照标准的要求和设备现有的能力,西气东输所有的冷弯管煨制都需要内胎芯。
3)吊车的选择,第26标段和第18标段的冷弯管工程采用的吊车为40吨履带吊(见下图1),它具有吨位大,爬杆长,能行走等优点,是一种较理想的吊装设备。
4)当用吊带把防腐管送入一半管材到设备后(见下图),把前边的楔块抬起到适当的位置,放松吊带,履带吊向前走,取下吊带,把管口扶正装置(即带有平板钩的吊钩)用吊车吊起(见图),然后履带吊车向后行走,把剩下的一半送入设备中,在防腐管进入设备的同时,操作手应该认真的配合,控制内胎芯在管中行走,保持重心在适当的位置,以利于防腐管的顺利进入,防腐管进入难的主要原因有:1)防腐管没有放在滚轮上;2)前部楔块抬得较高,高出滚轮,产生很大摩擦力;3)吊车的吊装行走方向与设备的前后方向不平行,使得防腐管与设备产生侧向摩擦力。
图1 图2 图35)防腐管进入设备后,把绞车(其作用是用于防腐管弯制时提供进给的动力源)伸出(如图),根据需弯制的角度确定伸长余量,利用绞车进行拉动防腐管到适当的位置,画好第一次煨制点,然后每隔900毫米(3次)再划一条线,该做法是用来确定进给量(如图)。
6)同时,用线锥在防腐管前端的上下管壁划好垂直线,以利于吊钩位置的确定,从而减小了冷弯管的平面度误差,该方法至关重要,在弯制的每一部的同时,都要注意它的变化,尽量控制它的偏差,提高冷弯管的质量。
7)内胎芯的位置确定,通过第26标段和第18标段冷弯管的弯制经验可以得出,不同的管材壁厚,如果内胎芯的位置保持不变的话,楔块对端口椭圆度的影响是不同的。
8)当一切准备工作做好后,就可以开始煨制了,注意:操作手必须一心一意的工作,认真地对待每一个细节,不可忽视,因为每根管材的造价昂贵,加上西气东输管道工程的标准非常严格,稍不小心,就会造成管材的报废。
a、涨内胎芯:直到内胎芯的压力达到最大值(81bar约8.1MPa),设备采用的是溢流阀,该压力具有可调性,其步骤详见弯管机操作说明书。
b、找平管材的方向,使防腐管在模具与底座和楔块中,实现该过程需要两个手柄(底座控制手柄,楔块控制手柄)。
9)当防腐管放好后,楔块压力达到210bar时,按下底座控制手柄,使主顶油缸上升,上升到一定高度时,松开手柄,停顿1-2秒,减少回弹性,此时可以用角度尺测量冷弯管的角度,测量方法见下图(冷弯管角度的确定,角度尺的用法),然后上抬底座控制手柄,释放油缸压力,上抬楔块控制手柄,释放楔块油缸压力,然后再测量弯管角度,可以发现前后角度的变化,由于钢材的弹性造成,但如何知道钢材的反弹率呢,一般情况下,弯制角度达1度时,实际的自然角度只有0.5度。
每一根冷弯管开始煨制时,前两次和后两次和中部一次需进行测量,可以减少各种因素造成的对弯管角度(材质)的影响。
注意:角度尺放置的方向需朝同一个方向,原因是减小角度误差。
10)按下绞车控制手柄,冷弯管向前进给300毫米,执行第9、10步,完成后,上抬内胎芯控制手柄,释放内胎芯压力,11)再次按下绞车控制手柄,使冷弯管进给300毫米,在工作人员的配合下,使内胎芯向后倒退300毫米,使得内胎芯回到第一次弯制的地点,这样保证了内胎芯永远在模具的下方,目的是为了保证弯制点(弯曲段)的椭圆度偏差。
然后重复第9、10、11、12步,进行每弯两次退一次内胎芯的循环过程。
12)当冷弯管达到了所需的要求后,需把冷弯管从设备中吊出,具体步骤如下:a、按下绞车控制手柄,使冷弯管向前行走,同时上抬内胎芯行走控制手柄,使得内胎芯行走控制液压管与地面保持静止,减小了液压管的磨损,同时降低了工人的劳动强度。
b、当冷弯管的末端达到模具的末端时,按下楔块控制手柄,使楔块抬起,把冷弯托起,摘下平口钓钩,换上吊带,在冷弯管中部起吊,步骤与进管时相反。
c、把冷弯管放到平台上后,换用吊管沟调到成品堆放区,以备待检。
14、冷弯管的质量检验和标志,a、冷弯管椭圆度的测量(包括两端、中部)见下图1、图2b、当管端要求有坡口时应符合下图3规定图1 图2 图3椭圆度:=图1值-图2值c、冷弯管检漏:该工程采用的是电火花检漏仪,检漏电压为25Kv。
检漏的冷弯管须接地良好,不然会造成静电伤人。
d、管材编号的要求和规定及工具附图B18-EH0038(9+410)-02-21.0-6°05´-015-SJ检验员监理各项指标检漏角度日期钱永志合格合格6°05´ 2002.6.18e、弯管标志及重要参数管材标示XQ-SM-005138 API5L0042.3 81 2001φ1016×21.0×11760材质X70炉批号11811126 CPPCE 中油管道镇江防腐厂甲29/10 3LPE-S成套标志应用模版喷刷法清楚而耐久的喷刷在每一根弯管端部的内表面上。
成套标志应包括下列事项:a)公称直径(D N)b)外径(D)c)壁厚(t)d)弯管钢级e)弯曲半径f)弯曲角度g)购方代表h)弯管编号I)制造商名称或商标重要参数-0.5°≤角度偏差≤0.5°弯管平面度应不大于25毫米弯管管端垂直度不大于2.5毫米15、冷弯管的吊装,在冷弯管运输过程中,一定要保护好防腐层不受伤害,需要在运输设备上放置管堆,且不许与硬物体接触,一般采用草袋子装软土后摆放好,装车时,应小心轻放。
无缝钢管标准无缝钢管是一种具有中空截面、周边没有接缝的长条钢材。
钢管具有中空截面,大量用作输送流体的管道,如输送石油、天然气、煤气、水及某些固体物料的管道等。
钢管与圆钢等实心钢材相比,在抗弯抗扭强度相同时,重量较轻,是一种经济截面钢材,广泛用于制造结构件和机械零件,如石油钻杆、汽车传动轴、自行车架以及建筑施工中用的钢脚手架等。
用钢管制造环形零件,可提高材料利用率,简化制造工序,节约材料和加工工时,如滚动轴承套圈、千斤顶套等,目前已广泛用钢管来制造。
钢管还是各种常规武器不可缺少的材料,枪管、炮筒等都要钢管来制造。
钢管按横截面积形状的不同可分为圆管和异型管。
由于在周长相等的条件下,圆面积最大,用圆形管可以输送更多的流体。
此外,圆环截面在承受内部或外部径向压力时,受力较均匀,因此,绝大多数钢管是圆管。
但是,圆管也有一定的局限性,如在受平面弯曲的条件下,圆管就不如方、矩形管抗弯强度大,一些农机具骨架、钢木家具等就常用方、矩形管。
根据不同用途还需有其他截面形状的异型钢管。
1.结构用无缝钢管(GB/T8162-1999)是用于一般结构和机械结构的无缝钢管。
2.流体输送用无缝钢管(GB/T8163-1999)是用于输送水、油、气等流体的一般无缝钢管。
3.低中压锅炉用无缝钢管(GB3087-1999)是用于制造各种结构低中压锅炉过热蒸汽管、沸水管及机车锅炉用过热蒸汽管、大烟管、小烟管和拱砖管用的优质碳素结构钢热轧和冷拔(轧)无缝钢管。
4.高压锅炉用无缝钢管(GB5310-1995)是用于制造高压及其以上压力的水管锅炉受热面用的优质碳素钢、合金钢和不锈耐热钢无缝钢管。
5.化肥设备用高压无缝钢管(GB6479-2000)是适用于工作温度为-40~400℃、工作压力为10~30Ma的化工设备和管道的优质碳素结构钢和合金钢无缝钢管。
6.石油裂化用无缝钢管(GB9948-88)是适用于石油精炼厂的炉管、热交换器和管道无缝钢管。
7.地质钻探用钢管(YB235-70)是供地质部门进行岩心钻探使用的钢管,按用途可分为钻杆、钻铤、岩心管、套管和沉淀管等。
8.金刚石岩芯钻探用无缝钢管(GB3423-82)是用于金刚石岩芯钻探的钻杆、岩心杆、套管的无缝钢管。
9.石油钻探管(YB528-65)是用于石油钻探两端内加厚或外加厚的无缝钢管。
钢管分车丝和不车丝两种,车丝管用接头联结,不车丝管用对焊的方法与工具接头联结。
10.船舶用碳钢无缝钢管(GB5213-85)是制造船舶I级耐压管系、Ⅱ级耐压管系、锅炉及过热器用的碳素钢无缝钢管。
碳素钢无缝钢管管壁工作温度不超过450℃,合金钢无缝钢管管壁工作温度超过450℃。
11.汽车半轴套管用无缝钢管(GB3088-82)是制造汽车半轴套管及驱动桥桥壳轴管用的优质碳素结构钢和合金结构钢热轧无缝钢管。
12.柴油机用高压油管(GB3093-2002)是制造柴油机喷射系统高压管用的冷拔无缝钢管。
13.液压和气动缸筒用精密内径无缝钢管(GB8713-88)是制造液压和气动缸筒用的具有精密内径尺寸的冷拔或冷轧精密无缝钢管。
14.冷拔或冷轧精密无缝钢管(GB3639-2000)是用于机械结构、液压设备的尺寸精度高和表面光洁度好的冷拔或冷轧精密无缝钢管。