数控机床的机械结构概述
数控机床的典型机械结构
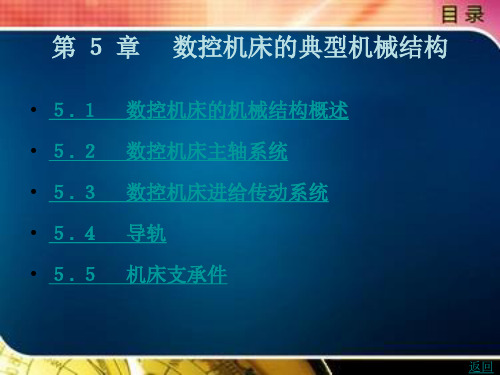
高传动件的制造精度与刚度。 • 3. 具有良好的抗振性和热稳定性 • 数控机床一般既要进行粗加工, 又要进行精加工。
上一页 下一页 返回
5. 2 数控机床主轴系统
• 加工时由于断续切削、加工余量不均匀、运动部件不平衡以及切削过 程中的自激振动等原因引起的冲击力或交变力的干扰, 使主轴产生振 动, 影响加工精度和表面粗糙度, 严重时甚至会破坏刀具或工件, 使加 工无法进行。 主轴系统的发热可能导致所有零部件产生热变形, 降低 传动效率, 破坏零部件之间的相对位置精度和运动精度而造成加工误 差。 因此, 要求主轴组件要有较高的固有频率、较好的动平衡、保持 合适的配合间隙并进行循环润滑等。
• 数控机床的机械结构仍然继承了普通机床的构成模式, 其零部件的设 计方法也同样类似于普通机床。
下一页 返回
5. 1 数控机床的机械结构概述
• 但近年来, 随着进给驱动、主轴驱动和CNC 的发展, 为适应高生产 效率的需要, 现今的数控机床有着独特的机械结构, 除机床基础件外, 主要由以下各部分组成。
上一页 下一页 返回
第6章 数组
• 6.1 一维数组 • 6.2 二维数组 • 6.3 字符数组 • 6.4 数组程序举例
6.1 一维数组
• 6.1.1一维数组的定义方式 • 一维数组的定义方式为: • 类型说明符数组名[常量表达式]; • 其中: • 类型说明符可以是任何一种基本数据类型或构造数据类型。 • 数组名是用户定义的数组标识符。 • 方括号中的常量表达式须为整型,其值表小数组元素的个数,也称为
来表示。 • (5)允许在同一个类型说明中说明多个数组和多个变量。
数控机床的机械结构概述ppt(52张)

数控机床的机械结构概述(ppt52页)
数控机床结构与装调工艺
具有适应无人化、柔性化加工的特殊部件
数控机床结构与装调工艺
广泛采用高效、无间隙传动装置和新技术、新产品
数控机床进行的是高速、高精度加工,再简化机械结构 的同时,对于机械传动装置和元件也提出了更高的要求。高 效、无间隙传动装置和元件在数控机床上去得了广泛的应用。 如:滚珠丝杠副、塑料滑动导轨、静压导轨、直线滚动导轨 等高效执行部件,不仅可以减少进给系统的摩擦阻力,提高 传动效率;而且还可以使运动平稳和获得较高的定位精度。
数控机床的机械结构概述(ppt52页)
数控机床的机械结构概述(ppt52页)
数控机床结构与装调工艺
对机械结构、零部件的要求高
高速、高效、高精度的加工要求,无人化管理以及工艺复 合化、功能集成化,一方面可以大大的提高生产率,同时,也 必然会使机床的开机时间,工作负载随之增加,机床必须在高 负荷下,长时间可靠工作。因此,对组成机床的各种零部件和 控制系统的可靠性要求很高。
数控机床的机械结构概述(ppt52页)
数控机床的机械结构概述(ppt52页)
数控机床结构与装调工艺
三、数控机床对机械结构的基本要求
具有较高的静、动刚度和良好抗震性
机床的刚度反映了机床机构抵抗变形的能力。机床 变形产生的误差,通常很难通过调整和补偿的方法予以 彻底的解决。为了满足数控机床高效、高精度、高可靠 性以及自动化的要求,与普通机床相比,数控机床应具 有更高的静刚度。此外,为了充分发挥机床的效率,加 大切削用量,还必须提高机床的抗震性,避免切削时产 生的共振和颤振。而提高机构的动刚度是提高机床抗震 性的基本途径。
数控机床的机械结构与传动

第二节 数控机床的典型机械结构
第二章 数控机床的机械结构与传动
2.1 滚珠丝杠螺母结构
滚珠丝杠螺母副的选用
滚珠丝杠螺母副的选择包括其精度、尺寸规格、支 撑方式等几个方面。
根据机床精度选用丝杠副的精度,根据机床载荷来 选定丝杠直径,对细长而又承受轴向压缩载荷的滚珠丝 杠,需核算压杆稳定性;对转速高,支撑距离大的滚珠 丝杠副需校核临界转速;对精度要求高的滚珠丝杠需校 核刚度。 1)精度等级的选择; 2)结构尺寸的选择; 3)验算。
主传动在中、高速 段为恒功率传动, 在低速段为恒转矩 传动。
第三节 数控机床的主传动系统
第二章 数控机床的机械结构与传动
3.2 主轴部件的结构
主轴部件的支撑与润滑
机床主轴带动刀具或夹具在支撑中做回转运动,应能传递切削转矩、受 切削抗力,并保证必要的旋转精度。
常用卡盘结构
数控车床工件夹紧装置可采用三爪自定心卡盘、四爪单动卡盘或弹簧夹 头等。
第四节 数控机床的进给传动系统
第二章 数控机床的机械结构与传动
4.2 数控机床进给传动系统的基本形式
实现直线进给运动主要有三种形式: 1)通过丝杠螺母副,将伺服电动机的旋 转运动变成直线运动。 2)通过齿轮、齿条副,将伺服电动机的 旋转运动变成直线运动。 3)直接采用直线电动机进行驱动。
减少传动件。 4)在加工中心上,还必须具有安装刀具和刀具交换所需的自动夹
紧装置,以及主轴定向准停装置,以保证刀具和主轴、刀库、 机械手的正确位置。 5)有C轴功能要求时,主轴还需要安装位置检测装置,以便实现对 主轴位置的控制。
第三节 数控机床的主传动系统
第二章 数控机床的机械结构与传动
3.1 主传动的基本要求和变速方式
第6章 数控机床的机械结构

1.滚珠丝杠的结构组成
滚珠丝杠由丝杠、螺母、滚珠和滚珠返回装置四 部分组成。按照滚珠的循环方式,滚珠丝杠螺母副分 内循环方式和外循环方式两大类。 内循环方式指在循环过程中滚珠始终保持和丝杠 接触,如图6.16所示。
图6.16 滚珠丝杠内循环方式 1-丝杠;2-反向器;3-滚珠;4-螺母
2)减少各运动零件的惯量
传动件的惯量对进给系统的启动和制动特性都有 影响,尤其是高速运转的零件,其惯量的影响更大。 3)减少运动件的摩擦阻力 机械传动结构的摩擦阻力,主要来自丝杠螺母副 和导轨。 4)响应速度快 快速响应是伺服系统的动态性能,反映了系统的 跟踪精度。它是工件在加工过程中,工作台在规定的 速度范围内灵敏而精确地跟踪指令,且不出现丢步现 象。
1-主轴 2-同步齿形带 3-主轴电机 4-永久磁铁 5-磁传感器 图6.11 加工中心主轴准停装置
4.主轴部件的结构
(1)数控车床主轴部件的结构 数控车床的主传动系
统一般采用交流无级调速电动机,通过皮带传动,带 动主轴旋转。 图 6.12为数控车床主轴外观图。图 6.13 为数控车床主轴部件的典型结构图。主轴电动机通过 带轮15把运动传给主轴7。
1. 齿轮变速的主传动方式
如图6.6(a)所示,主轴电机经过二级齿轮变速, 使主轴获得低速和高速两种转速系列,这种分段无级 变速,确保低速时的大扭矩,满足机床对扭矩特性的 要求,是大中型数控机床采用较多的一种配置方式。
2. 带传动主传动方式
如图6.6(b)所示,主轴电机经带传动传递给主轴, 带传动主要采用 V型带或齿形带传动,可以避免齿轮 传动时引起的振动与噪声,且其结构简单、安装调试 方便,应用广泛。
1.主轴部件的支承与润滑 根据主轴部件的工作精度、刚度、温升和结构的
数控机床机械结构设计和制造技术的创新研究
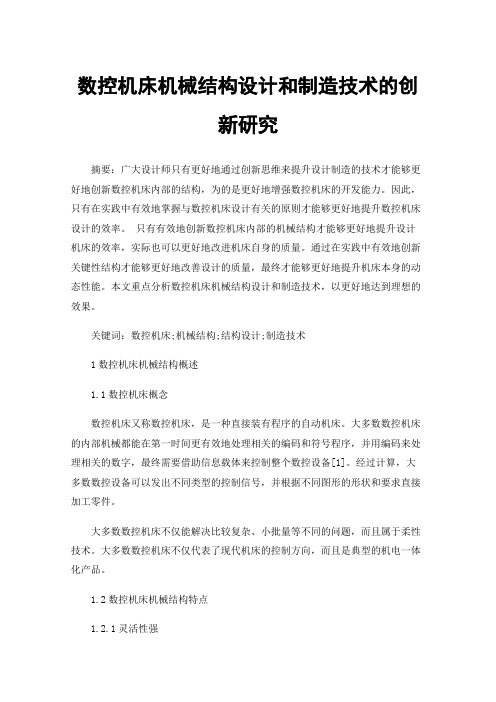
数控机床机械结构设计和制造技术的创新研究摘要:广大设计师只有更好地通过创新思维来提升设计制造的技术才能够更好地创新数控机床内部的结构,为的是更好地增强数控机床的开发能力。
因此,只有在实践中有效地掌握与数控机床设计有关的原则才能够更好地提升数控机床设计的效率。
只有有效地创新数控机床内部的机械结构才能够更好地提升设计机床的效率,实际也可以更好地改进机床自身的质量。
通过在实践中有效地创新关键性结构才能够更好地改善设计的质量,最终才能够更好地提升机床本身的动态性能。
本文重点分析数控机床机械结构设计和制造技术,以更好地达到理想的效果。
关键词:数控机床;机械结构;结构设计;制造技术1数控机床机械结构概述1.1数控机床概念数控机床又称数控机床,是一种直接装有程序的自动机床。
大多数数控机床的内部机械都能在第一时间更有效地处理相关的编码和符号程序,并用编码来处理相关的数字,最终需要借助信息载体来控制整个数控设备[1]。
经过计算,大多数数控设备可以发出不同类型的控制信号,并根据不同图形的形状和要求直接加工零件。
大多数数控机床不仅能解决比较复杂、小批量等不同的问题,而且属于柔性技术。
大多数数控机床不仅代表了现代机床的控制方向,而且是典型的机电一体化产品。
1.2数控机床机械结构特点1.2.1灵活性强数控机床在加工零件方面与普通机床有着直接的区别,即使是整个机床也可以在没有更多程序的帮助下得到更好的调整。
因此,更多的数控机床可用于加工不同类型的零件,并可用于产品开发过程中。
在实际应用中,不仅可以直接缩短生产周期,而且可以直接降低生产成本。
1.2.2高加工精度大多数数控机床的实际精度可达0.05-0.1mm。
在实际应用中,利用不同的数字信号形式可以直接输出不同的脉冲信号。
数控机床中的大多数数控装置都可以用来控制传动链之间的间隙和螺杆之间的平均误差。
因此,从实践来看,数控机床的实际加工精度更高。
1.2.3实际质量稳定可靠如果能用合适的数控机床直接加工零件,所涉及的刀具、程序和刀具是相同的,数控机床生产的零件质量是相对稳定的。
数控机床的机械结构

8.1 概 述
1-主轴电动机;2,3-伺服电动机
图8.1 HM-077数控车床传动系 统
7
主轴电动机1主要采 用变频电动机,主轴电 动机的动力通过带传动 传递至主轴 。
机床的Z向和X向进给 由两套伺服系统分别驱动, 伺服电动机3和2分别通过 同步齿形带传动滚珠丝杠 螺母副,实现床鞍和滑板 作纵向和横向运动。
27
8.2 数控机床的主传动系统
2.主轴轴承配置 ❖ 合理配置轴承可以提高主轴精度,降低温升,简化支承结 构。在数控机床上配置轴承时,前后轴承都应能承受径向 载荷,支承间距离要选择合理,并根据机床的实际情况配 置承受轴向力的轴承。 ❖ 滚动轴承的精度有E级(高级)、D级(精密级)、C级(特精 级)、B级(超精级)四种等级。
❖ 这就要求换刀时主轴必须准确停在某个径向位置上,保证 每次换刀时刀柄上的键槽对准主轴的端面键,为了满足主 轴准停这一功能要求而设置的装置称为主轴准停装置。
36
8.2 数控机床的主传动系统
1-主轴;2-同步带;3-主轴电动机;4-永久磁铁;5-磁传感器
图8.16 电气控制式主轴准停装置
37
8.2 数控机床的主传动系统
25
8.2 数控机床的主传动系统
❖ 要求主轴部件的精度要高,包括运动精度和安装刀具或夹 持工件的夹具的定位精度,要求主轴部件结构刚度要好, 要有较好的抗振性及热稳定性,因此数控机床主轴部件在 结构上要解决好主轴的支承、主轴内刀具自动装夹、主轴 的定向停止等问题。
26
8.2 数控机床的主传动系统
1.主轴轴承
13
8.2 数控机床的主传动系统
8.2.2 主传动类型
★ 数控机床主传动可以分为无级变速、分段无级变速两种 传动方式。 ★ 分段无级变速传动方式通常采用在无级变速电动机之后 串联机械有级变速,以满足数控机床要求的宽调速范围和转 矩特性,如图8.4(a)所示。 ★ 无级变速传动方式电动机本身的调速就能够满足要求, 不用齿轮变速,如图8.4(b)、(c)、(d)所示。
数控技术数控机床的机械结构

《数控技术—》—机械制造及自动化
这是大、中型数 控机床采用较多 的一种方式。
这主要应用在小 型数控机床上。
这种主传动方式大大简 化了主轴箱体结构,提 高了主轴部件的刚度。
8.2.2 主轴组件结构
一、主轴轴承的配置方式 1、前后支撑采用不同轴承
此配置形式使主轴的综合刚度大幅度提高,可以满足强 力切屑的要求,因此普遍应用于各类数控机床。 2、前轴承采用高精度双列向心推力球轴承
《数控技术—》—机械制造及自动化
2.抗震性好 机床工作时可能产生两种形态的振动:强迫振 动和自激振动。 数控机床在高速重切削情况下应无振动,以保 证加工工件的高精度和高的表面质量,特别要 注意的是避免切削时的自激振动,因此对数控 机床的动态特性提出更高的要求。
《数控技术—》—机械制造及自动化
3.热稳定性好 数控机床的热变形是影响加工精度的重要因素 。引起热变形的热源主要是机床的内部热源, 如电动机发热、摩擦热及切削热等。机床的热 膨胀不均是影响刀具与工件正确位置的一个主 要因素。机床的热稳定性好包括机床的温升小 ,产生温升后使温升对机床的变形影响小,机 床产生热变形时对精度的影响较小
《数控技术—》—机械制造及自动化
4.灵敏度高
数控机床要求在相当大的进给速度范围内能 达到较高的精度,因而运动部件应具有较高的 灵敏度。
导轨通常用滚动导轨,塑料导轨,静压导轨等 以减小摩擦力,使其无低速爬行现象。工作台 、刀架等部件的移动由伺服电机驱动,经过滚 珠丝杠传动,减少了进给系统所需的驱动扭矩 ,提高定位精度和运动平稳性。
15、我就像一个厨师,喜欢品尝食物。如果不好吃,我就不要它。2021年8月下午11时4分21.8.1623:04August 16, 2021
数控机床的机械结构

两级齿轮变速 液压拔叉实现齿轮滑移
22
CNC
4.3 数控机床的主传动系统
4.3.2 主轴的联接型式
➢ 定传动比的联结型式 主电动机和主轴一般采用定传动比的联结型
式,或是主电动机和主轴直接联结的型式,在使 用定传动比传动时,通常采用三角皮带或同步皮 带传动
电动机和主轴直接联结的型式,可以大大简 化主轴传动系统的结构,有效地提高主轴刚度和 可靠性。
4.4.2 数控机床进给传动系统的基本型式
➢ 数控机床的进给运动有两大类
– 直线进给运动:机床的基本坐标轴(X、Y、Z轴)以及和基本坐标轴平行的坐标轴(U 、V、W等)的运动
– 圆周进给运动:指绕基本坐标轴X、Y、Z回转的坐标轴运动。
➢ 实现直线进给运动主要有三种型式
▪ 通过丝杠(通常为滚珠丝杠或静压丝杠)螺母副,将伺服电动机的旋转运动变成直 线运动。
4.4.1数控机床对进给传动系统的要求
主要内容
(4)摩擦阻力要小
在进给系统中要尽量减少传动件之间的摩擦阻力, 尤其是减少丝杠传动和工作台运动导轨之间的摩擦, 以消除低速进给爬行现象,从而提高整个伺服进给系 统的稳定性。广泛采用滚珠丝杠和滚动导轨以及塑料 导轨和静压导轨。
42
CNC
4.4 数控机床的进给传动系统
19
CNC
4.3 数控机床的主传动系统
4.3.2 主轴的联接型式
➢ 用辅助机械变速机构联接 在使用无级变速传动的基础上,再增加两级或
三级辅助机械变速机构作为补充。通过分段变速方 式,确保低速时的大扭矩,扩大恒功率调速范围, 满足机床重切削时对扭矩的要求
辅助机械变速机构 :通过电磁离合器、液压 或气动带动滑移齿轮等方式实现
4.3.1主传动的基本要求和变速方式
数控机床的机械结构

数控机床的机械结构在数控机床进展的最初阶段,其机械结构与通用机床相比没有多大的变化,只是在自动变速、刀架与工作台自动转位与手柄操作等方面作些改变。
随着数控技术的进展,考虑到它的操纵方式与使用特点,才对机床的生产率、加工精度与寿命提出了更高的要求。
数控机床的主体机构有下列特点:1)由于使用了高性能的无级变速主轴及伺服传动系统,数控机床的极限传动结构大为简化,传动链也大大缩短;2)为习惯连续的自动化加工与提高加工生产率,数控机床机械结构具有较高的静、动态刚度与阻尼精度,与较高的耐磨性,而且热变形小;3)为减小摩擦、消除传动间隙与获得更高的加工精度,更多地使用了高效传动部件,如滚珠丝杠副与滚动导轨、消隙齿轮传动副等;4)为了改善劳动条件、减少辅助时间、改善操作性、提高劳动生产率,使用了刀具自动夹紧装置、刀库与自动换刀装置及自动排屑装置等辅助装置。
根据数控机床的适用场合与机构特点,对数控机床结构因提出下列要求:一、较高的机床静、动刚度数控机床是按照数控编程或者手动输入数据方式提供的指令自动进行加工的。
由于机械结构(如机床床身、导轨、工作台、刀架与主轴箱等)的几何精度与变形产生的定位误差在加工过程中不能人为地调整与补偿,因此,务必把各处机械结构部件产生的弹性变形操纵在最小限度内,以保证所要求的加工精度与表面质量。
为了提高数控机床主轴的刚度,不但经常使用三支撑结构,而且选用钢性很好的双列短圆柱滚子轴承与角接触向心推力轴承铰接出相信忒力轴承,以减小主轴的径向与轴向变形。
为了提高机床大件的刚度,使用封闭界面的床身,并使用液力平衡减少移动部件因位置变动造成的机床变形。
为了提高机床各部件的接触刚度,增加机床的承载能力,使用刮研的方法增加单位面积上的接触点,并在结合面之间施加足够大的预加载荷,以增加接触面积。
这些措施都能有效地提高接触刚度。
为了充分发挥数控机床的高效加工能力,并能进行稳固切削,在保证静态刚度的前提下,还务必提高动态刚度。
数控机床的结构概述

4.3.2主传动机械结构
数控机床机械结构要求:高抗振性 1)强迫振动 使机床产生强迫振动的内部振源有高速转动零部件的动态不平衡力、 往复运动件的换向冲击力、周期变化的切削力等。 2)自激振动 这里是指切削自激振动,也称颤振。如图所示。 3)提高机床抗振性的措施 (1) 减少机床的内部振源 (2) 提高静刚度 (3) 增加构件或结构的阻尼
4.3.2主传动机械结构
主轴部件结构: 数控机床的主轴部件,既要满足精加工时精度较高的要求, 又要具备粗加工时高效切削的能力,因此应有更高的动、静刚度 和抵抗变形的能力。主轴部件主要包括主轴、轴承、传动件和密 封件,对于具有自动换刀能力的数控机床,主轴部件还应有刀具 自动装卸装置、主轴准停装置和吹屑装置等。
当换刀时,在主轴上端油缸的上腔A通入压力 油,活塞12的端部推动拉杆7向下移动,同时压 缩蝶形弹簧11,当拉杆7下移到使双瓣卡爪5的下 端移出套筒14时,在弹簧6的作用下,卡爪张开, 喷气头13将刀柄顶松,刀具即可由机械手拔除。
待机械手将新刀装入后,油缸10的下腔通入 压力油,活塞12向上移,蝶形弹簧伸长将拉杆7 和双瓣卡爪5拉着向上,双瓣卡爪5重新进入套筒 14,将刀柄拉紧。
4.3.2主传动机械结构
数控机床机械结构要求:热变形对加工精度的影响小 数控机床的热变形,是影响加工精度的重要因素。引起机床热变形的 热源主要是机床的内部热源,如主电动机、进给电动机发热,摩擦热以及切 削热等。 减少机床热变形及其影响的措施是: 1)减少机床内部热源和发热量; 2)改善散热和隔热条件; 3)均热; 4)合理设计机床的结构布局,减小热变形对精度的影响; 5)采取热变形补偿措施。
4.2 数控机床的整体布局形式
(1)
图具有可编程尾架座双刀架数控车床。
数控机床的四大组成部分

数控机床的四大组成部分
数控机床的四大组成部分数控机床主要由主机部分、控制部分、驱动装置和辅助装置四部分组成。
(1)主机部分它是数控机床的主体,是数控机床的机械部件。
它包括床身、主轴箱、刀架、尾座、进给机构等组成。
(2)控制部分控制部分又称CNC装置,它是控制机床的核心,一般是一台机床专用控制计算机(包括机床印制板电路、屏幕显示器、键盘、纸带、磁带、驱动电路等)。
输入到控制部分的程序指令记录在信息载体上由程序读入装置接收,或由控制部分的键盘直接手动输入。
(3)驱动装置驱动装置是数控机床的执行机构的驱动部件,包括主轴电机、进给伺服电机等。
(4)辅助装置辅助装置是指数控机床的一些配套部件,包括液压、气动装置及冷却系统和排泄装置、防护设备等。
数控机床应用数控机床是一种装有程序控制系统的自动化机床,能够根据已编好的程序,使机床动作并加工零件。
它综合了机械、自动化、计算机、测量、微电子等最新技术,使用了多种传感器,在数控机床上应用的传感器主要有光电编码器、直线光栅、接近开关、温度传感器、霍尔传感器、电流传感器、电压传感器、压力传感器、液位传感器、旋转变压器、感应同步器、速度传感器等,主要用来检测位置、直线位移和角位移、速度、压力、温度等。
1、数控机床对传感器的要求1)可靠性高和抗干扰性强;
2)满足精度和速度的要求;
3)使用维护方便,适合机床运行环境;
4)成本低。
不同种类数控机床对传感器的要求也不尽相同,一般来说,大型机床要求速度响应高,中。
数控机床主轴部件结构介绍ppt(36张)

机电设备安装与调试
第二章 数控机床机械结构的装配与调试
数控机床主轴部件结构介绍(PPT36页)
情景三 数控机床主轴部件结构
三、主轴零、部件
1、主轴零件 要求:尺寸参数、端部结构、
材料、轴颈精度
机电设备安装与调试 数控机床主轴部件结构介绍(PPT36页)
电主轴
第二章 数控机床机械结构的装配与调试
电数控主车轴床液压卡盘
第二章 数控机床机械结构的装配与调试
数控机床主轴部件结构介绍(PPT36页)
情景三 数控机床主轴部件结构
三、主轴零、部件
5、主轴其它结构——主轴准
机电设备安装与调试 数控机床主轴部件结构介绍(PPT36页)
电加主工轴中心准停
第二章 数控机床机械结构的装配与调试
数控机床主轴部件结构介绍(PPT36页)
②、电动机经同步齿形带传动主轴
主轴电动机
机电设备安装与调试
第二章 数控机床机械结构的装配与调试
情景三 数控机床主轴部件结构
二、主传动系统的配置
③、电动机经齿轮变速传动主轴
主轴电动 机
机电设备安装与调试
第二章 数控机床机械结构的装配与调试
情景三 数控机床主轴部件结构
① 主轴电动机直接驱动(一体化主轴,电主轴)
情景三 数控机床主轴部件结构
阅读分析数控机床主轴箱装配图
机电设备安装与调试
第二章 数控机床机械结构的装配与调试
情景三 数控机床主轴部件结构
阅读分析数控机床主轴箱装配图
机电设备安装与调试
第二章 数控机床机械结构的装配与调试
情景三 数控机床主轴部件结构
一、对数控机床主传动系统的要求
①具有更大的调速范围并实现无级调速。 ②具有较高的精度与刚度,传递平稳,噪声低。 ③良好的抗振性和热稳定性 ④在车削中心上,要求主轴具有C轴控制功能。 ⑤在加工中心上,要求主轴具有高精度的准停功能。 ⑥具有恒线速度切削控制功能。
数控机床的机械结构

2、广泛采用高效、无间隙传动装置和新技术、新产品 3、具有适应无人化、柔性化加工的特殊部件
4、对机械结构、零部件的要求高
1.3 数控机床对机械结构的基本要求
1、提高机床结构的静刚度
刚度:结构在特定的激扰下抵抗变形的能力。 静载荷下抵抗变形的能力称为静刚度,动载荷下抵抗变形的能力称为动刚度, 即引起单位振幅所需要的动态力。 静刚度一般用结构的在静载荷作用下的变形多少来衡量,动刚度则是用结构的 固有频率来衡量;
间并联机构为基础,利用
计算机数字控制的方法, 以软件取代部分硬件,以 电气装置和电子器件取代 部分机械传动。
井冈山大学机电工程学院
23
数控机床的机械结构
3 数控机床的导轨
3.1 数控机床对导轨的基本要求 机床上的直线运动部件都是沿着它的床身、立柱、横梁等上 的导轨进行运动的,导轨的作用概括地说是对运动部件起导向和 支承作用,导轨的制造精度及精度保持性对机床加工精度有着重 要作用的影响。基本要求主要有: 导向精度高; 精度保持性好; 足够的刚度; 良好的摩擦特性; 此外,导轨结构工艺性要好,便于制造和装配,便于检验、 调整和维修,而且有合理的 导轨防护和润滑措施等。
井冈山大学机电工程学院
数控机床的机械结构
3.2数控机床导轨的种类与特点
滑动导轨
井冈山大学机电工程学院
数控机床的机械结构
3.2数控机床导轨的种类与特点
滚动导轨 滚动导轨是在导轨面之间放置滚珠、滚柱、滚针等滚动体,
使导轨面之间的滑动摩擦变成为滚动摩擦。滚动导轨与滑动导
轨相比的优点是: ①灵敏度高,且其动摩擦与静摩擦系数相差甚微,因而运动 平稳,低速移动时,不易出现爬行现象。 ②定位精度高,重复定位精度可达0.2μm。
数控机床的机械传动结构
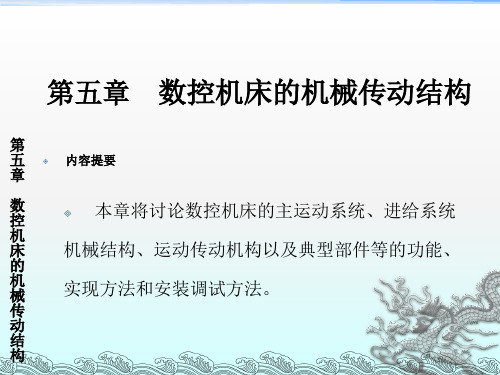
的
机
械 传
验算:扭转刚度、压曲刚度、临界转速与工作寿命
动
结
构
精度等级选择
第
二
滚珠丝杠的精度对数控机床的定位精度有直接影响。
节
进
主要精度指标:螺距(导程)误差、累积误差/300mm。
给
系
普通数控机床选用D级,精密数控机床选用C级;。
统
的
滚珠丝杠的热变形对数控机床定位精度的影响也不容忽视;
机
功用:将旋转运动变换成直线运动
第
分类:
二
节
➢ 滑动丝杠螺母副(旧机床数控化改造、经济型)
进
给
➢ 滚珠丝杠螺母副(广泛采用、普及型、高档型)
系
统 的
➢ 静压丝杠螺母副(用于高精度数控机床)
机
械
传
动
结
构
1、滚珠丝杠螺母副概述
➢ 工作原理:丝杆(螺母)旋转,滚珠在封闭滚道内沿滚道滚动、迫使
第
螺母(丝杆)轴向移动
第 六 1、进给系统的功用 章
数
协助完成加工表面的成形运动,传递所需的运动及动力。
控 机
2、进给系统机械部分的组成
床 的
传动机构+运动变换机构+导向机构+执行件(工作台)
机 械
传动机构: 齿轮传动、同步带传动
传 运动变换:丝杠螺母副、蜗杆齿条副、齿轮齿条副等 动
结 导向机构:导轨(滑动导轨、滚动导轨、静压导轨)
对主轴支承的基本要求是:
第 一 节
A.前后支承都应有承受径向载荷的轴承。 支承方式:两支承、三支承等。
B.要有承受双向轴向载荷式的推动轴承。
数
控
机
- 1、下载文档前请自行甄别文档内容的完整性,平台不提供额外的编辑、内容补充、找答案等附加服务。
- 2、"仅部分预览"的文档,不可在线预览部分如存在完整性等问题,可反馈申请退款(可完整预览的文档不适用该条件!)。
- 3、如文档侵犯您的权益,请联系客服反馈,我们会尽快为您处理(人工客服工作时间:9:00-18:30)。
第七章数控机床的机械结构第一节概述数控机床机械部分如图7-1,数控机床是高精度和高生产率的自动化机床,其加工过程中的动作顺序、运动部件的坐标位置与辅助功能,都是通过数字信息自动控制的,操作者在加工过程中无法干预,不能像在普通机床上加工零件那样,对机床本身的结构和装配的薄弱环节进行人为补偿,所以数控机床几乎在任何方面均要求比普通机床设计得更为完善,制造得更为精密。
为满足高精度、高效率、高自动化程度的要求,数控机床的结构设计已形成自己的独立体系,在这一结构的完善过程中,数控机床出现了不少完全新颖的结构与元件。
与普通机床相比,数控机床机械结构有许多要求:●性能要求高●电机过载能力强。
要求有较长时间(1-30min)和较大倍数的过载能力●在断续负载下,电机转速波动要小。
●速度响应要快,升降速时间要短。
●电机温升低,振动和噪音小。
●可靠性高,寿命长,维护容易。
●体积小,重量轻,与机床联接容易。
第二节 数控机床机械结构特点 一.主轴传动系统特点主轴传动链大大缩短,变速X 围大大扩大。
1. 普通电机—机械变速系统—主轴部件结构如图7-2能够满足各种切削运动转矩输出的要求,但变速X 围不大,由于是有级变速使切削速度的选择受到限制,而且该配置的结构较复杂,所以现在仅有少数经济型数控机床采用该配置,其它已很少采用。
2.变频器—交流电机—1-2机械变速—主轴部件如图7-3图7-2 传统机床主轴箱结构图7-1 数控机床机械结构部分这种配置的结构简单、安装调试方便,且在传动上能满足转速与转矩的输出要求,但其调速X 围与特性相对于交、直流主轴电机系统而言要差一些。
主要用于经济型或中低档数控机床上。
3. 交、直主轴电机 — 主轴部件如图7-4这种配置形式同上面一样,但电机是性能更好交直流主轴电机,数控系统控制加在电机上的电压,实现变速,测速发电机实现自动升降速,该电机变速X 围宽,最高转速可达8000 r/min ,且控制功能丰富,可满足中高档数控机床的控制要求。
测速发电机交直流电机图7-4 交流直流主轴电机结构变频器图7-3 B 变频调速示意图 图7-3 A 变频器加机械变速主轴箱结构4. 电主轴如图7-5电主轴又称内装式主轴电机,是最近几年在数控机床领域出现的将机床主轴与主轴电机融为一体的新技术,它与直线电机技术、高速刀具技术一起,将会把高速加工推向一个新时代。
电主轴是一套组件,它包括电主轴本身与其附件:电主轴、高频变频装置、油雾润滑器、冷却装置、内置编码器、换刀装置,即主轴与电机转子合为一体,其优点是主轴部件结构紧凑、重量轻、惯量小,可提高启动、停止的响应特性,利于控制振动和噪声。
转速高,目前最高可达200000 r/min。
其缺点是电机运转产生的振动和热量将直接影响到主轴。
图7-5电主轴示意图5. 主轴轴承寿命大大提高滚动轴承,滑动轴承,陶瓷轴承,磁悬浮轴承,寿命大大提高,转速从3000 rpm上升到10000 rpm,30000 rpm,到200000 rpm。
二.对数控机床进给系统要求为确保数控机床进给系统的传动精度和工作平稳性等,在设计机械传动装置时,提出如下要求。
1.高的传动精度与定位精度数控机床进给传动装置的传动精度和定位精度对零件的加工精度起着关键性的作用,对采用步进电动机驱动的开环控制系统尤其如此。
无论对点位、直线控制系统,还是轮廓控制系统,传动精度和定位精度都是表征数控机床性能的主要指标。
2.宽的进给调速X围伺服进给系统在承担全部工作负载的条件下,应具有很宽的调速X围,以适应各种工件材料、尺寸和刀具等变化的需要,工作进给速度X围可达3000-6000mm/min。
为了完成精密定位,伺服系统的低速趋近速度达0.1mm/min;为了缩短辅助时间,提高加工效率,快速移动速度应高达15m/min。
在多坐标联动的数控机床上,合成速度维持常数,是保证表面粗糙度要求的重要条件;为保证较高的轮廓精度,各坐标方向的运动速度也要配合适当;这是对数控系统和伺服进给系统提出的共同要求。
3.响应速度要快所谓快速响应特性是指进给系统对指令输入信号的响应速度与瞬态过程结束的迅速程度,即跟踪指令信号的响应要快;定位速度和轮廓切削进给速度要满足要求;工作台应能在规定的速度X围内灵敏而精确地跟踪指令,进行单步或连续移动,在运行时不出现丢步或多步现象。
进给系统响应速度的大小不仅影响机床的加工效率,而且影响加工精度。
设计中应使机床工作台与其传动机构的刚度、间隙、摩擦以与转动惯量尽可能达到最佳值,以提高进给系统的快速响应特性。
3.无间隙传动进给系统的传动间隙一般指反向间隙,即反向死区误差,它存在于整个传动链的各传动副中,直接影响数控机床的加工精度;因此,应尽量消除传动间隙,减小反向死区误差。
设计中可采用消除间隙的联轴节与有消除间隙措施的传动副等方法。
4.稳定性好、寿命长稳定性是伺服进给系统能够正常工作的最基本的条件,特别是在低速进给情况下不产生爬行,并能适应外加负载的变化而不发生共振。
稳定性与系统的惯性、刚性、阻尼与增益等都有关系,适当选择各项参数,并能达到最佳的工作性能,是伺服系统设计的目标。
所谓进给系统的寿命,主要指其保持数控机床传动精度和定位精度的时间长短,与各传动部件保持其原来制造精度的能力。
设计中各传动部件应选择合适的材料与合理的加工工艺与热处理方法,对于滚珠丝杠和传动齿轮,必须具有一定的耐磨性和适宜的润滑方式,以延长其寿命。
6.使用维护方便数控机床属高精度自动控制机床,主要用于单件、中小批量、高精度与复杂件的生产加工,机床的开机率相应就高,因此,进给系统的结构设计应便于维护和保养,最大限度地减小维修工作量,以提高机床的利用率。
三.对数控机床进给系统的特点(一)主轴脉冲编码器代替了螺纹传动链,传动链大大缩短,如图7-6(二)采用特殊导轨,摩擦力大大降低尽量采用低摩擦导轨。
导轨按摩擦性质分为:1.滑动导轨这种导轨副之间的摩擦为滑动摩擦的导轨,按摩擦状态又分为静压导轨和动压导轨。
静压是区别于动压的,动压是部件在运动时产生的承载油膜,而静压则不同,是利用外界油压的作用来承载的,需要将高压油用泵打入到工作部位,才能起承载作用。
利用外界的油压作用在导轨与摩擦副之间产生静压油膜,使活动部件浮起,即导轨与摩擦副之间不产生直接的接触。
因此摩擦和磨损都很小。
这里注意滚动轴承,滑动轴承原理。
2.滚动导轨这种导轨副之间的摩擦为滚动摩擦的导轨,以减小摩擦力,如图7-7。
电机 A 闭环伺服系统B 滚柱导轨3.贴塑导轨B 滚珠导轨图7-7 数控机床导轨1 234在滑动导轨面处采用贴塑导轨板,它是用耐磨氟氢软带做成的,使进给系统的刚度,摩擦阻尼系数静、动态特性处于最佳状态,有效减少导轨面磨损,廷长机床使用寿命。
(三)T型丝杠图3-2-67 把混合好的导轨胶涂在大拖板底面的平导轨和V型导轨表面上并贴贴塑导轨图3-2-68 将粘贴着贴塑导轨的大拖板按放在床身导轨上,中间垫薄纸薄纸贴塑导轨(四) 采用滚珠丝杠特点滚珠丝杠副是一种把旋转运动转化为直线运动的传动机构,在螺旋槽的丝杠螺母间装有滚珠作为中间传动件,以减少摩擦,如图7-14所示。
图中丝杠和螺母上都磨有圆弧形的螺旋槽,丝杠与螺母之间基本上为滚动摩擦。
为了防止滚珠从螺母中滚出来,在螺母的螺旋槽两端设有反向器使滚珠排成封闭状态,使滚珠能循环流动。
根据反向器结构不同,滚珠丝杠分为内循环和外循环两种结构。
滚珠丝杠副的特点是:1. 传动效率高,摩擦损失小。
滚珠丝杠副的传动效率η=0.92~0.96,比T 型丝杠提高3~4倍。
2.给予适当预紧,可消除丝杠和螺母的螺纹间隙,反向时就可以消除空行程死区,定位精度高,刚度好。
3.运动平稳,无爬行现象,传动精度高。
4.运动具有可逆性,可以从旋转运动转换为直线运动,也可以从直线运动转换为旋转运动,即丝杠和螺母都可以作为主动件。
5.磨损小,使用寿命长。
6.制造工艺复杂。
滚珠丝杠和螺母等元件的加工精度要求高,表面粗糙度也要求高,故制造成本高。
7.不容易自锁,特别是对于垂直丝杠,由于重力的作用,需加制动力自锁。
(四)内循环、外循环滚珠丝杠结构安装如图7-8 1.内循环、外循环滚珠丝杠结构如图7-8图6-1-17 原CA6140车床X 坐标T 型丝杠结构组件1-T 型丝杠座,固定在大拖板上 2-T 型丝杠 3、5-T 型丝母 4-消隙斜铁 6、7-M8内六角螺栓 8-中拖板与丝母联接座与其专用螺栓126782.内循环、外循环滚珠丝杠结构安装与反向间隙调整图7-8 A外循环滚珠丝杠结构示意图图7-8 B 内循环滚珠丝杠结构示意图图7-9 A 双螺母调整反向间隙法: 1、2为丝母,3为平键,4为调整反向间隙螺母图7-9 B在两个螺母的凸缘上各制有圆柱齿轮,两者齿数相差一个齿,并装入内齿圈中,内齿圈用螺钉或定位销固定在套筒上。
调整时,先取下两端的内齿圈,当两个滚珠螺母相对于套筒同方向转动一样齿数时,一个滚珠螺母对另一个滚珠螺母产生相对角位移,两个丝母轴向产生相对位移,达到消除间隙并施加预紧力的目的。
设丝杠螺距P ,1、2丝母齿数Z1、Z2,则两个丝母均转过一个齿时轴向位移之差为:P Z Z S ⎪⎭⎫ ⎝⎛-=∆2111(7-1)当Z1=99,Z2=100,P=6毫米时,6.0=∆S 微米,精度很高。
3.滚珠丝杠的拆装、清洗、维修(五)采用特殊齿轮结构,消除齿轮反向间隙如图7-101.采用双片齿轮错齿法,消除齿轮反向间隙,如图7-10 A图7-9 C 双螺母差齿调整反向间隙法:1、2为丝母,3,4为内齿轮图7-9 D 两螺母中间加垫片调整反向间隙法图7-10 A1、2为双片齿轮,3为拉簧,4为销子,5,6为螺栓螺母动画演示:2.采用轴向垫片错齿消除斜齿轮反向间隙,如图7-10 B图7-10 B 加工齿轮时将两个齿轮中间垫厚为t的垫片一起加工,装配时垫片测量反向间隙δ,垫片厚度增大为δ+δcosβ。
1、2为两个斜齿轮,3为垫片厚度t,4为螺旋角β3.采用轴向压簧错齿消除斜齿轮反向间隙,如图7-10 C图7-10 F 齿轮4和2是同轴齿轮,齿轮3和5是同轴齿轮,齿轮4和5与齿条啮合,施力器7使齿轮1与齿轮2和3同时啮合,产生左右推力,使齿轮4和齿轮5与齿条两个方向啮合紧密,消除反向间隙。
这样齿轮4或5就可以是电机轴上的齿轮。
(六)采用偏心套,以减小齿轮中心距消除齿轮反向间隙如图7-11图7-11 A 采用偏心套减小齿轮中心距消除齿轮反向间隙动画演示:============以上第19次课图7-11 B 采用偏心套减小齿轮中心距消除齿轮反向间隙(七)数控机床反向间隙1.反向间隙的概念图7-12 反向间隙的概念电机轴上键间隙,齿轮反向间隙,丝杠丝母反向间隙,工作台装配机械间隙对工作台的综合影响。