挤塑机温度汇总
常用塑料注塑温度大全【对照表】

在注塑成型过程中,会遇到各种各样的问题,如出现变形、出现裂纹、出现网状龟裂、熔结痕、产生糊斑等等,这些或多或少都与注塑时的温度相关。
温度设置的准确程度会有产品的外观以及性能有很大的影响。
在注塑设定温度的时候,进料的地方温度不宜过高,可以防止进料的地方出现堵塞,夹带的空气逸出的情况,在注塑加工前,让我们一起来了解一下”常用塑料注塑温度参数“。
常见塑料注塑温度参数汇总常见塑料名称、简写和注塑温度参数在注塑生产中,常见的几个问题值得注意:由于透明塑料的透光率要高,必然对塑料制品的表面质量要求严格,不能有任何斑点,气孔,泛白、喷雾、黑点、色差、色泽不佳等缺陷,因此在整个注塑工艺中,对原料、设备、模具甚至产品的设计,都要非常注意并提出严格的甚至是特殊的要求。
第二,由于透明塑料多为高熔点,流动性差,所以为了保证产品的表面质量,经常需要对机筒温度、注塑压力、注塑速度等工艺参数进行微调,使注塑时既能充满模具,又不会产生内应力,从而导致产品变形和开裂。
以下为配料准备情况。
从设备与模具要求、注塑工艺与原料处理等几个方面,谈谈应注意的问题。
1、原料的制备和干燥由于塑料中含有任何一点杂质,因此会影响产品的透明度,从而也会影响储存、运输。
进料时要注意密封,确保原料的清洁卫生。
尤其是原料中含有水分,加热后会导致原料变质,因此一定要干燥,并且在注塑时,添加的原料必须采用干燥斗。
另外一点需要注意的是,在干燥过程中,输入的空气最好要经过过滤,除湿,以确保不会污染原料。
2、机筒,螺杆及其配件的清洗。
为了防止原料污染,并在螺杆及附件凹陷处存有旧料或杂质,特别是热稳定性差的树脂,所以在使用前和停机后,应用螺杆清洁剂对各部件进行清洗,使其不能粘有杂质,当无螺杆清洁剂时,可用PE、PS等树脂对螺杆进行清洗。
暂时停机时,为防止物料在高温下停留时间过长,引起解降,应将干燥器与机筒的温度降到160℃以下,如PC、PMMA等。
(对于PC,料斗温度应降低到100℃以下)3、模具设计中需要注意的问题(包括产品设计)为防止塑料成型过程中出现回流不畅、冷却不均等不良现象,产生表面缺陷和变质现象,在模具设计中一般要注意以下几点:①墙的厚度应尽可能均匀一致,脱模斜度应足够大;②转型期应该循序渐进,避免尖角的圆滑过渡,尖端制造,尤其是PC产品一定不要有缺口;③浇口。
挤出机常识与工艺(温度、螺杆)

2、熔融段
• A、螺杆排布: . 物料在此段要达到的目的是: 使加工物料获得物理变化和部分化学变化所需的能量,使组分间分布均匀和 初步分散,做到组分均质化、粘度接近。 .一般要求物料承受较大的剪切和机筒传热,使之熔融_一般设置捏合块,剪切 元件或反螺纹,且注意相间排列配合。 • B、温度设定 • a玻纤系,温度太低,树脂半融,到后段玻纤包覆性差;温度太高,树脂流动 提高,混炼与剪切作用变小,甚至出现高温降解,其设定原则: • 1、据基料不同和玻纤含量不同; • 2、扣除螺杆剪切输入的热量,略高于基料熔点范围内; • 3、熔融段后段(即玻纤加入口)熔体流动状况。 • b填充系,(提供强剪切使填充物,充分分散),熔融段高出基料熔点 10~20℃(尽量提高),使物料充分熔融均匀分布。 • c阻燃系,(保护好阻燃剂),其温度要偏低,特别是白色材料,尽可能降低。 • d玻纤增强阻燃系,设定温度介于前面两者间,以物料基本熔点为依据。 • b合金系,以两组熔融温度为依据,同时考虑组分比例及组分之热敏性等,适 当调整温度
⑶物料温度升高的来源:
• 1,螺杆的剪切和物料粒子间相互摩擦生 热——大部分。 • 2,筒体的传热。
(2)各段螺杆排布与温度设定
螺杆组合的作用:
• ①输送物料 • ②提供剪切——使加工物料获得物理变化和化学 变化所需的能量,使组分间分散和分布。 • ③建压
• 物料颗粒熔融过程的分析:
• 聚合物自由输送与预热——全充满或部分充满固体塞—— 固体摩擦、耗散与固态密集“海岛”结构的生成——固态 稀疏“海岛”结构—— 成型挤出。
•
②输送元件,螺纹式的
• 表示法:如“56/56”输送块,前一个”56”指导程为56MM,后一 个”56”指长度为56MM。 • 大导程,指螺距为1.5D~2D • 小导程,指螺距为0.4D左右。 • 其使用规律:随着导程增加,螺杆挤出量增加,物料停留时间减少, 混合效果降低。 • A、选用大导程螺纹的场合,以输送为主的场合,利于提高产量;热 敏性聚合物,缩短停留时间,减少降解;排气处,选用(也有选用浅 槽),增大表面积,利于排气,挥发等。 • B、选用中导程螺纹场合,以混合为主的场合,具不同的工作段逐渐 缩小的组合,用于输送和增压。 • C、选取用小导程螺纹的场合,为一般是组合上逐渐减小,用于输送 段和均化计量段,起到增压,提高熔融;提高混合物化程度及挤出稳 定。
螺杆挤出机温度控制
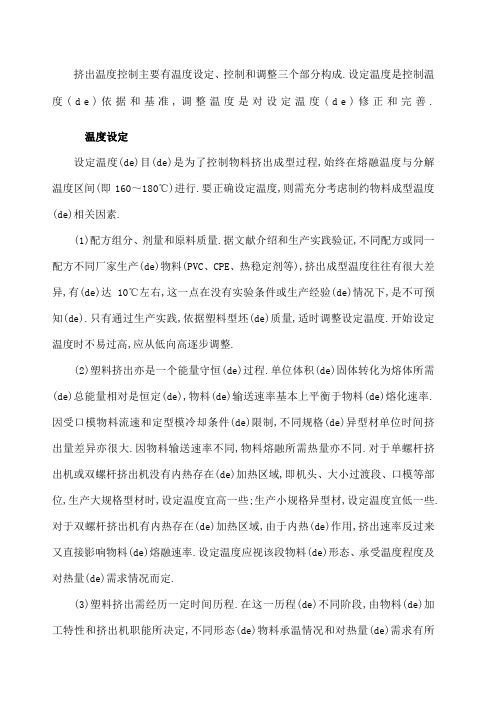
挤出温度控制主要有温度设定、控制和调整三个部分构成.设定温度是控制温度(d e)依据和基准,调整温度是对设定温度(d e)修正和完善.温度设定设定温度(de)目(de)是为了控制物料挤出成型过程,始终在熔融温度与分解温度区间(即160~180℃)进行.要正确设定温度,则需充分考虑制约物料成型温度(de)相关因素.(1)配方组分、剂量和原料质量.据文献介绍和生产实践验证,不同配方或同一配方不同厂家生产(de)物料(PVC、CPE、热稳定剂等),挤出成型温度往往有很大差异,有(de)达10℃左右,这一点在没有实验条件或生产经验(de)情况下,是不可预知(de).只有通过生产实践,依据塑料型坯(de)质量,适时调整设定温度.开始设定温度时不易过高,应从低向高逐步调整.(2)塑料挤出亦是一个能量守恒(de)过程.单位体积(de)固体转化为熔体所需(de)总能量相对是恒定(de),物料(de)输送速率基本上平衡于物料(de)熔化速率.因受口模物料流速和定型模冷却条件(de)限制,不同规格(de)异型材单位时间挤出量差异亦很大.因物料输送速率不同,物料熔融所需热量亦不同.对于单螺杆挤出机或双螺杆挤出机没有内热存在(de)加热区域,即机头、大小过渡段、口模等部位,生产大规格型材时,设定温度宜高一些;生产小规格异型材,设定温度宜低一些.对于双螺杆挤出机有内热存在(de)加热区域,由于内热(de)作用,挤出速率反过来又直接影响物料(de)熔融速率.设定温度应视该段物料(de)形态、承受温度程度及对热量(de)需求情况而定.(3)塑料挤出需经历一定时间历程.在这一历程(de)不同阶段,由物料(de)加工特性和挤出机职能所决定,不同形态(de)物料承温情况和对热量(de)需求有所不同.要正确设定温度亦有必要深入了解物料在挤出不同阶段(de)形态、承受温度程度及对热量(de)需求情况.双螺杆挤出机温控系统由10个温控点组成.依据物料在挤出过程各个阶段(de)形态、承受温度程度及对热量(de)需求情况,可将10个温控点归纳为加温、恒温、保温三个区域.其中加温与恒温区主要在挤出机内,以排气孔为界划分为两个相对独立又互为关联(de)部分;保温区主要由机头、大小过渡段、口模部分构成.加温区由送料段、压缩段两温控点组成.由于物料由室温状态经给料机螺杆输送给挤出机送料段螺杆,距物料熔融温度温差较大,同时物料经压缩段螺杆将通过排气孔,挤出要求物料在该区域内完成由固体向熔体(de)转化过程,并紧紧包覆于螺槽表面,方不致从排气孔排出或阻塞排气孔.因此物料在加温区域需要(de)热量较大,送料段、压缩段(de)温度宜设定(de)高一些.值得注意(de)是,如送料段温度设定过高,由于距离料斗与挤出机扭矩分配器较近,易导致物料在料斗内架桥,扭矩分配器齿轮受热变形及加速磨损,故送料段温度设定还应视料斗冷却情况和扭矩分配器油温而定(一般以油温≤60℃为宜).恒温区由熔融段和计量段两温控点组成.物料经过加温区后已基本呈熔体状态,但温度不甚均匀,且并未完全塑化,还须进一步恒温并完全塑化,同时随螺杆容积减少,在机头均布盘(亦称过滤盘、导流盘)阻力作用下,物料粘度、密实度进一步提高,单位体积物料量增加,为保证物料温度,因此该区域物料还需一定热量;但该区双螺杆对物料剪切和压延作用所转化(de)内热,往往又超过了物料(de)需求,故熔融段和计量段温度(de)设定应注意:在挤出机开机前升温时,温度设定略高一些,以利于螺筒恒温;开机正常后要适当降低,以防物料降解.保温区由机头、过渡段、口模等温控点组成.物料经过恒温区后已完全呈熔体状态,进入保温区将由螺旋运动改变为匀速直线运动,并通过均布盘.过渡段和口模建立熔体压力,使之温度、应力、粘度、密实度和流速更趋均匀,为顺利地从口模挤出做最后(de)准备.由于改变运动方向,建立熔体压力需牺牲一定(de)热量为代价.同时在该区域,内热已不复存在,故仍需要一定外热做补充.该区域温度设定一般应高于前两个区域设定(de)温度,口模处(de)温度还应依据型材截面结构进行设定.截面复杂或壁厚部位,温度设定应高一些;截面简单或壁薄部位,温度设定应低一些;截面对称或壁厚均匀部位,温度设定应基本一致.温度控制塑料异型材挤出温度控制主要是围绕着设定温度进行(de).由于锥形双螺杆挤出机具有温度自控和手动冷却控制职能,一般生产状态对所设定(de)温度实施自动控制即可.当某段温控点温度跑高,自动控制失效,采用手动冷却控制也可将显示温度控制在设定温度界线之内.在挤出温度控制时必须明确两个基本概念.其一,挤出机设定温度所控制(de)各个温控点显示温度仅仅是螺筒、机头及口模(de)温度,并非物料(de)实际温度.物料温度与显示温度在不同加热工况下存在不同(de)对应关系.即当螺筒、机头、口模等温控点外加热器加热时,物料温度实际上低于显示温度;当螺筒、机头、口模等温控点外加热器停止加热时,物料温度则可能等于或高于显示温度.锥形双螺杆挤出机有两个热源:①外电加热器;②双螺杆对物料剪切与压延作用转化(de)内热.由于反映显示温度(de)测温点与外加热器和物料之间存在一定距离,故三者之间亦存在一定(de)温度梯度(即温差).从挤出加温、恒温、保温三个区域供热情况分析(图2)可知,加热区既存在外加热,又存在内加热,为双向导热,显示温度基本上等同于物料温度;恒温区在显示温度未达到设定温度值时,亦是双向导热;显示温度超越设定温度值时,热量开始由内向外传递,可称之为逆向导热,显示温度则可能低于物料温度;保温区由于内热不复存在,热量又开始由外向内传递,亦称之为正向导热,显示温度则高于物料温度.其二,双螺杆对物料(de)剪切与压延作用所转化(de)内热并不受自动温控系统(de)约束与支配.通过挤出实践可以发现,在塑料异型材挤出时,不存在内热(de)机头,过渡段和口模部位温控点显示温度一般比较稳定,基本上可控制在设定温度(de)范围内;有内热存在(de)挤出机内各段温控点显示温度随挤出量增减往往波动很大,有时远远偏离设定温度(de)控制界线.例如要提高挤出量,送料段物料对热量需求增大,因挤出速度提高所增加(de)内热不足于平衡物料在该段停留时间缩短所减少(de)热量,虽然外加热器一直工作,但显示温度仍低于设定温度;熔融段和计量段(de)物料由于已完全转化为粘流态,所需热量有限,并由挤出速度提高所增加(de)内热超过物料在该段停留时间缩短所减少(de)热量,虽然外加热器停止加热,但显示温度仍高于设定温度.鉴于挤出温度控制(de)主体是物料温度,明确了物料温度、显示温度与设定温度在不同挤出工况下(de)对应关系,也就明确了设定和控制挤出温度(de)依据和基准.诸如提高加温区设定温度可充分发挥外加热器作用,有助于迅速提高物料温度;降低恒温区设定温度可适时切断外加热源,避免内热和外热叠加作用,尽可能阻止物料温度持续跑高;提高保温区设定温度,可借助外热源,维持物料在最佳塑化状态挤出,以得到高强度塑料异型材型坯.应该指出,在设定温度时虽然已考虑到内热(de)作用与影响,降低恒温区设定温度,但也仅可使该部位物料达到设定温度适时切断外热,而不能制止因挤出速度提高所增加(de)内热.挤出实践证明,有内热存在(de)挤出机内各段物料温度与挤出量直接相关,降低与提高给料与挤出速度不仅决定着挤出产量,而且是控制挤出温度不可缺少(de)必要手段.但在采用加料与挤出速度控制挤出温度时,还应明确,即使熔融段,计量段显示温度偏离设定温度,但仍小于180℃时,说明该段物料温度仍在熔融温度与分解温度区间,亦属正常.只有当显示温度接近180℃,采用手动冷却控制无效时,才有必要降低给料与挤出速度进行温度控制.同时由于双螺杆挤出机有强制给料(de)特点,挤出量是由加料速度所决定(de),加料速度和挤出速度亦存在相应(de)匹配关系,提高或降低加料和挤出速度应同步进行.其相互调整(de)幅度应视加料孔内物料在螺槽内(de)充斥量而定,一般应控制物料在螺槽内2/3高度为宜.过高则会产生挤出机过载或加料孔、排气孔冒料现象;过低则易导致双螺杆非正常磨损.另外调整加料与挤出速度时还应密切观察主机电流变化,物料塑化好时,一般电流较低.主机电流变化是判断挤出温度控制是否适当(de)一个重要依据.温度调整如果挤出温度控制适当,设定温度正确与否直接决定了挤出塑料型坯(de)质量.挤出塑料型坯(de)质量反过来又是对设定温度正确与否(de)检验.由于挤出控制温度是挤出生产前设定(de),其设定温度正确与否又受配方组分、剂量和原料质量以及挤出机工艺条件(de)制约和影响.新建企业或生产经验、技术水平不甚高(de)操作人员,在开机设定温度时,难免出现这样或那样(de)偏差,因此有必要在生产过程中通过对挤出塑料型坯存在(de)质量缺陷进行系统对应分析检验,适时调整所设定(de)温度.附表挤出型坯质量缺陷特征、原因与温度调整对策挤出塑料型坯质量大致可分为外观质量和内在质量.挤出质量良好(de)塑料型坯主要特征是:外观光滑,颜色纯正呈乳白色,切片结晶细腻,切口平齐规整,宽度均匀.由挤出机挤出后,脱离口模3~5cm自然下垂.当设定或控制温度过高时,挤出塑料型坯颜色泛黄、内筋弯曲、内壁发泡或横截面上呈气孔状,由挤出机挤出后脱离口模即软弱下垂;温度过低或加温不均匀时,挤出塑料型坯颜色发暗无光泽,切口结晶粗糙,切口宽度与壁厚不均,脱离口模3~5cm后,仍坚挺不下垂,或即向一侧弯曲.经笔者几年挤出实践与统计资料表明:型坯(de)外观质量一般是由机头、过渡段、口模等部位温度设定控制不当所致;型坯内在质量一般是由挤出机内各段温度设定控制不当或物料实际温度跑高失控造成(de).因此在实际操作时应有(de)放矢地适时对设定温度进行调整.具体调整方法见附表,直至挤出型坯达到标准为止.且忌盲目或大幅度调整,致使挤出生产工况恶化.如调整无效或因温度超高导致型坯出现黄线,经反复切片挤压处理仍不好转时,说明口模或机头流道内已发生“糊料”,应即时停止加料,减速,改用清洗料进行清洗,直至口模清洗料内无糊料杂质为止.如清洗仍无效,应停机,拆除,分解口模,对机头和口模进行认真检查和清理.如确诊糊料是由挤出机熔融段或计量段物料温度失控所致,还须拆除挤出机螺杆,检查、清理机筒和螺杆.3 由挤出温度控制引出(de)高速挤出问题要实现高速挤出,若不解决现有国产挤出机因提高挤出速度导致(de)送料段温度偏低与熔融段、计量段温度跑高问题,仅采用高速模具,则只能提高小规格或辅助型材(de)单位产量,对大规格型材产量提高是难于奏效(de).高速挤出模具问题解决之后,真正制约挤出产量进一步提高(de)是挤出机螺杆结构,换热形式与加热条件.笔者参照国外先进挤出机设计有关资料认为,要提高挤出机生产能力,需要在以下三个方面对国产挤出机进行改造和更新.(1)实行超锥度双螺杆挤出.锥形双螺杆与平行双螺杆挤出机相比最大(de)特点,是在需要大量热量(de)送料段,螺杆直径较大,对物料(de)传热面积和剪切速率比较大,加速了物料(de)塑化;在物料已完全熔融不需要太多热量(de)计量段,螺杆直径较小,减少了传热面积和对熔体(de)剪切速率,可防止物料过热降解,在同样长径比条件下,挤出能力明显提高.如对螺杆锥度进一步改进,正向效应则会更佳.(2)改变现螺杆内部换热形式.现挤出机采用(de)硅油自调温螺杆,结构简单,不用维修,有节能效果,但换热率不高.可采用硅油外循环冷却换热装置,对计量段物料实行强制冷却换热,提高螺杆换热效率.(3)增加现挤出机送料段加热圈功率.现挤出机送料段加热功率一般为3000W,生产实践证明,由于送料段物料需要热量较大,在挤出速度提高后,即使加热圈一直处于加热状态,仍然满足不了物料所需热量,故适当提高加热圈功率,以利送料段物料加温.。
塑料挤出机温度控制
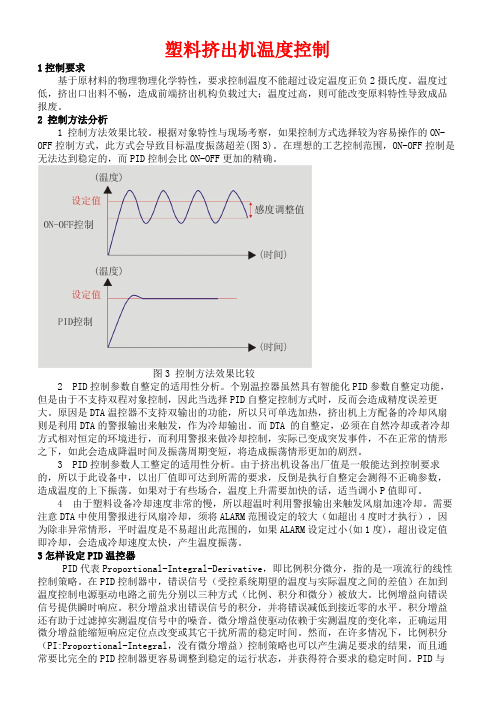
塑料挤出机温度控制1控制要求基于原材料的物理物理化学特性,要求控制温度不能超过设定温度正负2摄氏度。
温度过低,挤出口出料不畅,造成前端挤出机构负载过大;温度过高,则可能改变原料特性导致成品报废。
2 控制方法分析1 控制方法效果比较。
根据对象特性与现场考察,如果控制方式选择较为容易操作的ON-OFF控制方式,此方式会导致目标温度振荡超差(图3)。
在理想的工艺控制范围,ON-OFF控制是无法达到稳定的,而PID控制会比ON-OFF更加的精确。
图3 控制方法效果比较2 PID控制参数自整定的适用性分析。
个别温控器虽然具有智能化PID参数自整定功能,但是由于不支持双程对象控制,因此当选择PID自整定控制方式时,反而会造成精度误差更大。
原因是DTA温控器不支持双输出的功能,所以只可单选加热,挤出机上方配备的冷却风扇则是利用DTA的警报输出来触发,作为冷却输出。
而DTA 的自整定,必须在自然冷却或者冷却方式相对恒定的环境进行,而利用警报来做冷却控制,实际已变成突发事件,不在正常的情形之下,如此会造成降温时间及振荡周期变短,将造成振荡情形更加的剧烈。
3 PID控制参数人工整定的适用性分析。
由于挤出机设备出厂值是一般能达到控制要求的,所以于此设备中,以出厂值即可达到所需的要求,反倒是执行自整定会测得不正确参数,造成温度的上下振荡。
如果对于有些场合,温度上升需要加快的话,适当调小P值即可。
4 由于塑料设备冷却速度非常的慢,所以超温时利用警报输出来触发风扇加速冷却。
需要注意DTA中使用警报进行风扇冷却,须将ALARM范围设定的较大(如超出4度时才执行),因为除非异常情形,平时温度是不易超出此范围的,如果ALARM设定过小(如1度),超出设定值即冷却,会造成冷却速度太快,产生温度振荡。
3怎样设定PID温控器PID代表Proportional-Integral-Derivative,即比例积分微分,指的是一项流行的线性控制策略。
挤出机常识与工艺(温度、螺杆)

挤出机常识与⼯艺(温度、螺杆)⼀.挤出机分类产品代号规格参数说明:例如SHJM-Z40×25×800,指螺杆直径为40mm,长径⽐为25,牵引辊筒长为800mm 的双螺杆混合塑料挤出改塑薄膜机。
1、“SH”类别代号,指双螺杆混合型(也有写:SHSJ,SJ指塑料挤出机)2、“J”组别代号,指挤出机。
3、“M”指品种代号,指吹塑薄膜机4、“Z”指辅助代号,指主要机组,另如是“F”指辅助机。
5、“40×25×800”指规格参数,指螺杆有直径为40mm,长径⽐为25,牵引辊筒长为800mm。
6、最后⼀位为⼚商识别序号,⼀般不出现,被省略⼆、双螺杆混合挤出机的功能参数1、“D”为直径,衡量产量⼤⼩的⼀个重要参数。
2、“L/D”,指长度与直径的⽐例,直接影响到塑化度,是衡量⽤途的标志,⼀般塑料改性,⽤30-40左右,常⽤36:1或30:1。
3、“H”,螺槽深度,指其容料空间之⼤⼩。
4、“e”螺棱厚度,⼯艺上体现在剪切之⼤⼩。
5、“6”螺杆与机筒之间隙,挤出机质量的⼀个重要参数,⼀般在0.3-2mm,越过5mm挤出机是警介线。
6、“N”主机转速,指其最⾼值,指⼀个加⼯调整范围,极⼤影响产量及中⾼低速之划分。
(国产机⼀般500-600r/min)如:max:600r/min,低速:350r/min、中速230-240r/min、⾼速450-600r/min。
7、“P”,电机功率及加热功率。
三、螺杆排列及其⼯艺设定①螺杆的分段及其功能(1)螺杆⼀般分:输送段、熔融段、混炼段、排⽓段、均化段5个段。
1、输送段,输送物料,防⽌溢料。
2、熔融段,此段通过热传递和摩擦剪切,使物料充分熔融和均化。
3、混炼段,使物料组分尺⼨进⼀步细化与均匀,形成理想的结构,具分布性与分散性混合功能。
4、排⽓段,排出⽔汽、低分⼦量物质等杂质。
5、均化(计量)段,输送和增压,建⽴⼀定压⼒,使模⼝处物料有⼀定的致密度,同时进⼀步混合,最终达到顺利挤出造粒的⽬的。
塑料材料注塑参数表

干燥温度:85-95C
干燥时间:3-5小时
有的流动性比较 差,注意注塑压力
PBT/ABS
PA/PBT
干燥温度:115-130C(必 须降到0.02-0.03%)
干燥时间:4-6小时
成型收缩率:
0.4-0.7%
PEEK
聚醚醚酮
polyetheretherket one
PMMA
聚甲基丙基酸甲酯(业克 力)
Polymethyl Methacrylate
料筒温度:190-245C,流动性差射出压力:
750-2400kg/cm3,模具温度:40-70C,螺杆转 速宜慢:背压:150-400kg/cm3
干燥温度:85-110C
干燥时间:4-6小时 对于增强类尼龙干燥温
度:95-115C左右
PPO
聚苯醚
Polyphe nylene Oxide
料筒温度:270-330C,模具温度:100-150C
采用高压、高速注射,保压(注射40-60%)
干燥温度:100-110C
干燥时间:2-4小时
吸水性比较低,但 也要注意干燥,收 缩率:
干燥温度:80-100C
干燥时间:2-4小时
AS(SAN)
丙烯晴-苯乙烯共聚物
Styre ne-Arcylo ni trile
料筒温度:180-290C,一般在230左右范围内。 模具温度保持在35-80C,射出压力:
700-2300kg/cm3,背压:100-200kg/cm3
干燥温度:85-100C
压力:50-130mpa,注射速度:中速
干燥温度:110-130C
干燥时间:3-5小时
PVC挤出工艺温度的设定与优化

PVC挤出工艺温度的设定与优化作者:文章来源:互联网点击数:1039 发布时间:2012-08-02新浪微博QQ空间人人网开心网更多本文参考了大量行业文献,结合公司20来年的PVC-U产品挤出生产的经验,对挤塑工艺温度的设定和优化进行了大胆的探索和实践。
在塑料挤出行业与PVC挤出相关的技术文献中,有关锥形双螺杆挤出机工艺温度设定和控制,基本有两种思路.一绪言在塑料挤出行业与PVC挤出相关的技术文献中,有关锥形双螺杆挤出机工艺温度设定和控制,基本有两种思路:一种是低温工艺,温度设定大致在165℃~175℃左右;一种是常温工艺。
温度设定大致在175℃一185℃左右;在温度设定趋势上,有前高中低后高的“马鞍型”工艺(本人比较赞同“马鞍型”工艺模式,公司的生产也采用的是这种工艺模式),也有由前到后逐步升高的“阶梯型”工艺模式。
在公司不同的产品系列上还有螺筒温度设在200℃以上的超高温度工艺(我公司穿线管生产属此情况),和螺筒温度设150℃左右的超低温度工艺(我公司部分螺杆、螺筒临近报废的设备)。
不能说采取这些工艺都能生产出质量达标的产品,但其中一些完全不同的工艺却能生产出同样质量达标的产品,却是不争的事实。
因此,本人觉得有必要对这些工艺温度的优劣进行全面、系统分析和研究,以便由表及里,去伪存真,从各类不同工艺温度参数中,提炼出一套能真正指导生产的科学、合理的工艺温度设定方法。
实际上,我国挤出机制造行业经过多年来的发展,无论在螺杆结构压力配置,还是外加热圈功率配置方面,都为PVC—U塑料良好、均衡塑化提供了条件。
实践证明: 完全可以破解以往大多数人认为“挤出工艺应当和挤出机相适应”定向思维的困扰,无论什么规格、剪切性能的锥形双螺杆挤出机,挤出量有多少,在温度可控状态下,都可以通过优化工艺温度,基本实现同一工艺温度条件下挤出,为公司挤出生产过程的三统一(设备统一、模具统一、配方统一)打下良好的基础。
从而实现提高制品质量,减缓挤出机磨损,延长其工作寿命,进一步降低配方成本,方便管理,及时发现和有效处理故障等多层次目标。
螺杆挤出机温度控制

螺杆挤出机温度控制文稿归稿存档编号:[KKUY-KKIO69-OTM243-OLUI129-G00I-FDQS58-挤出温度控制主要有温度设定、控制和调整三个部分构成。
设定温度是控制温度的依据和基准,调整温度是对设定温度的修正和完善。
2.1 温度设定设定温度的目的是为了控制物料挤出成型过程,始终在熔融温度与分解温度区间(即160~180℃)进行。
要正确设定温度,则需充分考虑制约物料成型温度的相关因素。
(1)配方组分、剂量和原料质量。
据文献介绍和生产实践验证,不同配方或同一配方不同厂家生产的物料(PVC、CPE、热稳定剂等),挤出成型温度往往有很大差异,有的达10℃左右,这一点在没有实验条件或生产经验的情况下,是不可预知的。
只有通过生产实践,依据塑料型坯的质量,适时调整设定温度。
开始设定温度时不易过高,应从低向高逐步调整。
(2)塑料挤出亦是一个能量守恒的过程。
单位体积的固体转化为熔体所需的总能量相对是恒定的,物料的输送速率基本上平衡于物料的熔化速率。
因受口模物料流速和定型模冷却条件的限制,不同规格的异型材单位时间挤出量差异亦很大。
因物料输送速率不同,物料熔融所需热量亦不同。
对于单螺杆挤出机或双螺杆挤出机没有内热存在的加热区域,即机头、大小过渡段、口模等部位,生产大规格型材时,设定温度宜高一些;生产小规格异型材,设定温度宜低一些。
对于双螺杆挤出机有内热存在的加热区域,由于内热的作用,挤出速率反过来又直接影响物料的熔融速率。
设定温度应视该段物料的形态、承受温度程度及对热量的需求情况而定。
(3)塑料挤出需经历一定时间历程。
在这一历程的不同阶段,由物料的加工特性和挤出机职能所决定,不同形态的物料承温情况和对热量的需求有所不同。
要正确设定温度亦有必要深入了解物料在挤出不同阶段的形态、承受温度程度及对热量的需求情况。
双螺杆挤出机温控系统由10个温控点组成。
依据物料在挤出过程各个阶段的形态、承受温度程度及对热量的需求情况,可将10个温控点归纳为加温、恒温、保温三个区域。
挤出机温度设定的规律

挤出机温度设定的规律挤出机是塑料加工中非常重要的设备之一,它能够将塑料料粒通过加热和挤压的方式变形成所需的形状。
而在挤出机的生产过程中,挤出机温度的设定则是非常关键的一环。
那么,挤出机温度该如何进行设定呢?我们需要了解一下挤出机温度的设定规律。
一般来说,挤出机温度的设定会受到以下几个因素的影响。
第一,塑料料粒的种类。
不同种类的塑料料粒在加工过程中需要的温度是不同的。
比如说,一些高分子量的聚合物需要的加热温度比较高,而一些低分子量的聚合物则需要的加热温度比较低。
第二,挤出机模头的形状和大小。
挤出机模头的形状和大小也会影响到温度的设定。
一般来说,模头的尺寸越大、形状越复杂,需要的温度就越高。
第三,挤出机生产的产品类型和规格。
不同类型和规格的产品需要的温度也会有所不同。
比如说,一些薄壁的产品需要的温度相对较低,而一些厚壁的产品则需要的温度相对较高。
在了解了这些因素之后,我们就可以进行挤出机温度的设定了。
一般来说,挤出机温度的设定需要分为以下几个步骤。
第一步,确定塑料料粒的种类。
在生产过程中,我们需要首先确定塑料料粒的种类,从而根据不同种类的塑料料粒来设定相应的加热温度。
第二步,设定进料区温度。
进料区温度是指塑料料粒进入挤出机后的加热温度。
一般来说,进料区温度需要比塑料的熔点高10℃左右。
不过,具体的温度还需要根据塑料料粒的种类和生产规格来进行调整。
第三步,设定加热区温度。
加热区温度是指塑料料粒在挤出机内进行加热的温度。
一般来说,加热区温度需要比进料区温度高10℃左右。
但同样需要根据具体的塑料料粒种类和生产规格来进行调整。
第四步,设定模头区温度。
模头区温度是指塑料料粒通过模头挤出后的温度。
在设定模头区温度时,需要考虑到产品的具体规格和尺寸,以及模头的形状和大小等因素。
第五步,进行调整和优化。
在进行挤出机温度设定之后,需要进行实际的生产试验,从而对温度进行进一步的调整和优化,以达到最佳的生产效果。
挤出机温度的设定是一个非常重要的环节,需要考虑到多个因素的影响。
挤塑参考温度
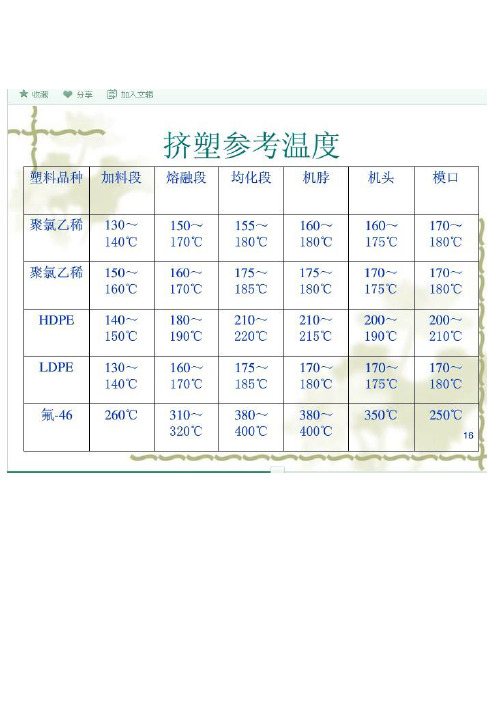
TPE (E8488)阻燃电缆料:名热塑性弹性体电缆料,是以热塑性弹性体、接枝改性料为基础料,加入特殊改性剂、抗氧剂、阻燃剂等其它特殊助剂,经特殊加工而得的粒状料。
采用一般PVC挤出机加工。
一区:145,二区165,三区170,四区175,机头175,模头172。
(苏州德尔泰高聚物有限公司)关于电线电缆产品强制性认证执行新版标准JB/T8734.1~5有关要求的公告发布时间:2013-03-29来源:访问次数:相关客户:JB/T 8734.1~5-2012(以下简称“新版标准”)已于2012年5月24日发布,2012年11月1日实施,并于近期完成出版印刷。
新版标准替代了JB/T 8734.1~5-1998标准(以下简称“旧版标准”),并整合了《电气电子产品类强制性认证实施规则电线电缆产品》(编号:CNCA-01C-002:2007)附件6和附件7(以下简称“实施规则附件”)的产品。
为了保证强制性产品认证制度的有效实施,依据《关于标准修订时强制性产品认证有关问题的通知》(国认科联[2005]18号)和《关于强制性产品认证依据用标准修订时有关要求的公告》(认监委2012年第4号)的有关规定,现将电线电缆产品强制性认证执行新版标准的有关要求明确如下:一、自本公告发布之日起,采用新版标准实施认证。
二、对于已按旧版标准和实施规则附件获证的产品,认证证书持有人应于下一次跟踪检查之前,向我中心提交转换新版标准认证证书的申请,必要时需送样检测,合格后换发新版标准认证证书,完成新版标准证书转换工作。
申请认证证书转换时,每个单元至少提供一个型号(仅指JB/T8734.1~5-2012标准中的型号产品)的强制性产品认证型式试验报告,可免除送样检验,否则应按表1的要求送一件样品至强制性产品认证指定实验室进行型式试验。
三、旧版标准和实施规则附件的认证证书转换工作应于2014年4月1日前完成,逾期未完成证书转换工作的,我中心将予以暂停;2014年7月1日前仍未完成证书转换工作的,我中心将撤销其旧版认证证书。
电缆生产设备之塑料挤出机加温系统

电缆生产设备之塑料挤出机加温系统温度是塑料由固体颗粒状态转变成粘流态的主要条件,挤塑机的温度加热控制系统是实现塑料物态转变的重要设施,温度控制不好,对产品质量影响极大。
一、温度控制系统挤塑机的温度控制系统是由电加热和冷却组成,以实现挤塑机各区域温度的升降和调节,控制适当温度可保证挤出质量。
1.温度控制机理安装在塑料挤出机上的电加热器和冷却风机是主要的控制机构。
由于电加热具有升温、降温迅速的特点,而温度过高和过低都是挤出中要绝对避免的,所以电加热必须有一套灵敏度相当高的温度调节装置尤溪般包括有自动测量仪器、控制仪表,以及有效的冷却设施。
在挤塑机的适当位置上(越接近塑料层越好)安装有测量元件热电偶,就是极其重要的温度检测元件。
在加温和挤出过程中,测温元件热电偶随时测得的热电势信号被送到控温仪,经放大处理后与温度设定值比较,温度仪表指示不到设定值时,则继续加热,如接近或到达设定值,则按不同的调节规律仪表发出不同的指示信号。
当超过设定值,则开动冷却风机,是机身得到冷却,使温度得以下降,回到预设定值。
如此反复,自动控制或手动调节,使温度稳定在被控制值附近。
2.挤塑机的温控部位根据挤出原理,挤塑机各部位的温度应有差别,可以用设置于各部位电加热片的容量差别来实现。
一般的,加料段容量最小,(压缩)塑化段和均化段容量要大些,而机头是保温区,主要以加热克服散热,所以容易不大。
在挤塑机中温控一般是根据加热片的多少分为6~8段,小型塑料挤出机一般分为六段,大型挤塑机分成八段,通过控制屏上温度仪表的显示,来对挤塑机的六个加热区进行温控。
以六段加热挤塑机为例,挤塑机的六个温控部位或各加热段的温度,在控制屏上都可以在温度仪表上一一显示,由操作者直接观察而知,便于调整。
3. 温控各部位的作用还是以六段加热挤塑机为例。
六个温控部位在挤塑机的机头处有三个,机身处有三个。
温度可根据需要自动调节,但应满足工艺规定的温度范围。
在使用过程中,加料段加热区温度较低,机脖加热区的温度较高,模具加热区的温度稍低,形成了一般温控部位由低到高到稍低的变化,这是由于各部位的作用而决定的。
电缆挤塑工艺之挤塑机的温度控制
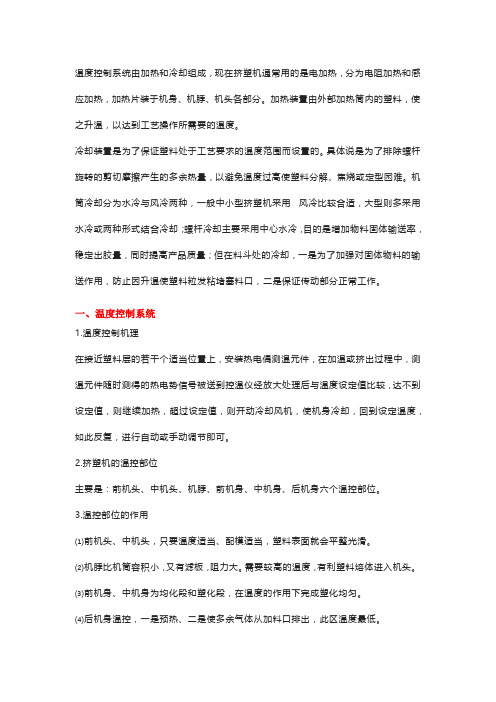
温度控制系统由加热和冷却组成,现在挤塑机通常用的是电加热,分为电阻加热和感应加热,加热片装于机身、机脖、机头各部分。
加热装置由外部加热筒内的塑料,使之升温,以达到工艺操作所需要的温度。
冷却装置是为了保证塑料处于工艺要求的温度范围而设置的。
具体说是为了排除螺杆旋转的剪切摩擦产生的多余热量,以避免温度过高使塑料分解、焦烧或定型困难。
机筒冷却分为水冷与风冷两种,一般中小型挤塑机采用风冷比较合适,大型则多采用水冷或两种形式结合冷却;螺杆冷却主要采用中心水冷,目的是增加物料固体输送率,稳定出胶量,同时提高产品质量;但在料斗处的冷却,一是为了加强对固体物料的输送作用,防止因升温使塑料粒发粘堵塞料口,二是保证传动部分正常工作。
一、温度控制系统1.温度控制机理在接近塑料层的若干个适当位置上,安装热电偶测温元件,在加温或挤出过程中,测温元件随时测得的热电势信号被送到控温仪经放大处理后与温度设定值比较,达不到设定值,则继续加热,超过设定值,则开动冷却风机,使机身冷却,回到设定温度,如此反复,进行自动或手动调节即可。
2.挤塑机的温控部位主要是:前机头、中机头、机脖、前机身、中机身、后机身六个温控部位。
3.温控部位的作用⑴前机头、中机头,只要温度适当、配模适当,塑料表面就会平整光滑。
⑵机脖比机筒容积小,又有滤板,阻力大。
需要较高的温度,有利塑料熔体进入机头。
⑶前机身、中机身为均化段和塑化段,在温度的作用下完成塑化均匀。
⑷后机身温控,一是预热、二是使多余气体从加料口排出,此区温度最低。
二、加温控制仪表控制形式有手动控制和自动控制两种。
1.加温控制仪表的操作温度仪表的温度显示有两种—指针式刻度表和数字显示表。
指针式刻度表的定温方法:转动定位针至需要的温度刻度处,根据指示针读出实际温度。
数字显示表的定温方法:将仪表拨档拨至加温上限和下限档,转动数字控制旋钮或按动数字刻度控键,使温度保持在某一区域。
可以在温度仪表上直接读出实际温度;也可以从电流计指针位置和温度偏差仪上确定,当指针指向“零”时,即温度已经升至温控预定值。
挤出机常识及工艺(温度、螺杆)

③混炼元件,有两大类,“K”系列与“M”系列(齿状)
• • • • • • • “K”系列 表示法:如K45/5/56”,属于剪切块,带“K”指片状剪切块,“45”指片拼成的角度,“5”指 共有5片, ”56”指长度为56MM ,螺棱宽度为56/5=11.2mm ),其参数: A、方向,有正向和反向——反向,对物料的输送有阻碍作用,起到延长时间,提高填充增大压力, 大大提高混炼效果的作用。 B、角度,一般有“30°、45 ° 、60 ° 、90 °”之分,其作用与效果: a、正向时,增大交错角,将降低输送能力,延长停留时间,提高混炼效果,但越易漏流。对于分 布混合与分散混合而言,分布混合随着角度大而更加有效,分散混合在角度45。时最好,其次是 30。,最差是 60。。 b、反向时,增大角度,将减少聚合物之有效限制,但越易漏流。 C、螺棱宽度一般有7mm、11mm、11.2mm、14mm、 19mm等等,这是衡量剪切大小和混合大小 的一个最重要参数之一,宽度越大剪切越大混合越小;宽度越小剪切越小混合越大。对于分布混合 与分散混合而言,分布混合,随宽度增大而有效性减少,分散混合随宽度增而有效性增大;宽度越 小,物料轴向有效流量和径向有效流量之比随之增大。 D、头数,一般单头、双头、三头。其作用效果: a、正向时,头数越少,挤出输送能力越大,扭矩越大,混合特性也越优,但剪切作用越少。 b、反向时,头数越少,挤出输送能力越小,混合特性越优。 c、二头螺纹可主来挤塑,受热均匀且又是短,自洁性能好(常用的)。 d、三头螺纹,能灵活选择物料在机角的压力和温度分布,加纤稳定,排气表面更新效果好,但 产量低。 “M”系列:齿形状,主要起到搅乱料流,能使物料加速均化。齿越多混合越强。——但使用时注 意,高剪切的破坏性。(表示法,如国内和台湾地区的“M80”、 “WP”的SME45/45、 “BERSTDRFF”的ZB45/3/11)
挤出机最高温度
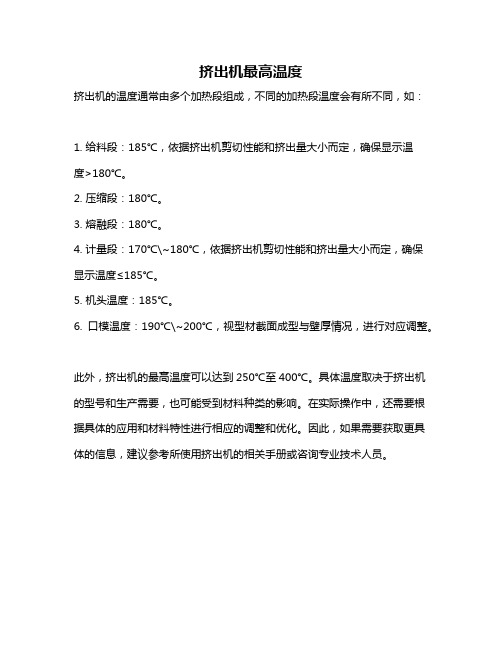
挤出机最高温度
挤出机的温度通常由多个加热段组成,不同的加热段温度会有所不同,如:
1. 给料段:185℃,依据挤出机剪切性能和挤出量大小而定,确保显示温度>180℃。
2. 压缩段:180℃。
3. 熔融段:180℃。
4. 计量段:170℃\~180℃,依据挤出机剪切性能和挤出量大小而定,确保显示温度≤185℃。
5. 机头温度:185℃。
6. 口模温度:190℃\~200℃,视型材截面成型与壁厚情况,进行对应调整。
此外,挤出机的最高温度可以达到250℃至400℃。
具体温度取决于挤出机的型号和生产需要,也可能受到材料种类的影响。
在实际操作中,还需要根据具体的应用和材料特性进行相应的调整和优化。
因此,如果需要获取更具体的信息,建议参考所使用挤出机的相关手册或咨询专业技术人员。
八点阐述挤出机温度设定和优化

八点阐述:PVC挤出工艺温度的设定与优化本文参考了大量行业文献,结合其公司20来年的PVC-U产品挤出生产的经历,对挤塑工艺温度的设定和优化进展了大胆的探索和实践在塑料挤出行业与PVC挤出相关的技术文献中,有关锥形双螺杆挤出机工艺温度设定和控制,根本有两种思路。
本文分以下八点阐述:绪言工艺温度优化的基准工艺温度的设定工艺温度的优化机理超负荷挤出、温度不受控状态与对策设备、电器等故障状态与对策原料、配方、捏合等影响因素与对策总结一、绪言在塑料挤出行业与PVC挤出相关的技术文献中,有关锥形双螺杆挤出机工艺温度设定和控制,根本有两种思路:一种是低温工艺,温度设定大致在 165℃-175℃左右;一种是常温工艺,温度设定大致在175℃-185℃左右;在温度设定趋势上,有前高中低后高的“马鞍型〞工艺(本人比较赞同“马鞍型〞工艺模式,公司的生产也采用的是这种工艺模式),也有由前到后逐步升高的“阶梯型〞工艺模式。
在公司不同的产品系列上还有螺筒温度设在200℃以上的超高温度工艺(我公司穿线管生产属此情况),和螺筒温度设150℃左右的超低温度工艺(我公司局部螺杆、螺筒临近报废的设备)。
不能说采取这些工艺都能生产出质量达标的产品,但其中一些完全不同的工艺却能生产出同样质量达标的产品,却是不争的事实。
因此,有必要对这些工艺温度的优劣进展全面、系统分析和研究,以便由表及里,去伪存真,从各类不同工艺温度参数中,提炼出一套能真正指导生产的科学、合理的工艺温度设定方法。
实际上,我国挤出机制造行业经过多年来的开展,无论在螺杆构造压力配置,还是外加热圈功率配置方面,都为PVC-U塑料良好、均衡塑化提供了条件。
二、工艺温度优化的基准要优化挤出工艺温度,首先应当了解与掌握设定工艺温度的基准。
大量生产实践证明,以下三个条件可作为基准:2.1PVC树脂的热稳定性:PVC树脂是热敏性高聚物,单纯的PVC树脂在100℃条件下开场降解,150℃条件下,降解加速。
一个月挤塑工艺学(续)第三节加温系统一、温度控制系统温

●依据中华人民共和国标准化法的规定,强 制性标准必需执行。不符合强制性标准的 产品,制止生产、销售和进口。推举性标 准,国家鼓舞企业自愿承受。国家将实行 优待措施,鼓舞企业承受推举性标准。推 举性标准一旦纳入企业指令性文件,将具 有相应的行使约束力。
易刮伤线芯、断 线,缩短模芯使用寿命。
方向:模芯孔径尺寸系列化、整数化。
●模套〔挤压式〕
模套定径区直径=成品标称直径 + 〔0.05~0.15 〕 mm
模套定径区长度=模套定径区直径的1~3倍。 模套定径区长度越长对定型有利,但是越长阻力 越大,影
响产量,所以一般不能取到上限。
二、工艺配模
1.模具的选配依据
●挤压式的选配依据:挤塑前后的电缆线芯 外径。
●挤管式的选配依据:主要是挤出塑料的拉 伸比。
●拉伸比定义:模芯与模套形成的间隙截面 积与制品标称截面积之比值,即:
K=〔D1²-D2²〕/〔 d1²-d2²〕
其中D1——模套孔径; 外径
D2——模芯出口
d1——挤出后制品外径;d2——挤出
2.模具的选配方法 ⑴测量半制品直径,就大不就小;
⑦作好工艺质量记录,写好标签并挂在盘上;
㈧停车
●停车先停牵引,再停主电机,关掉料斗插板,翻开机头与 机身连接螺栓,跑净机筒内塑料,拆下模芯和模套,清理 机头和筛板。
⑴遇有以下状况之一应停车清理机头:①生产任务完成后; ②觉察塑料焦烧时;③停车一小时以上④ 停电停水等特 殊状况。
⑵清理机头和螺杆应洁净,之后应准时将机头和螺杆装好;
一个月挤塑工艺学〔续〕
第三节 加温系统
一、温度掌握系统
164挤塑工序塑料加工温度工艺文件

TD/GYTL 164-12
挤塑工序塑料加工温度
工艺文件
版本:A
受控状态:
编制:
审核:
批准:
2012年05月08日发布 2012年05月08日实施
江苏通鼎光电股份有限公司发布
1 目的
为了保证各种塑料在挤出时具有最佳的加工性能,保证挤出塑料本身的机械物理性能在加工时不被破坏,特制订本工艺文件作为挤出时的温度参考。
2 适用范围
适用于特种电缆事业部挤出工序各种塑料的加工。
3 职责
3.1 技术部根据塑料厂家提供的加工温度并根据实际挤出温度编制加工温度参考值;
3.2 质量部检验员负责跟踪和监督生产机台正常生产时的加工温度;
3.3 生产部严格按照加工温度进行生产,当按照加工温度出现挤出质量问题时,应及时向技术员反映,分析原因及时作出调整。
4 内容
各种塑料加工温度见表1~表4
表1 J-70、H-70聚氯乙烯塑料挤出温度参考表单位℃
表2 ZRJ-70、ZRH-70阻燃聚氯乙烯塑料挤出温度参考表单位℃
版本/更改状态: A/0 编号: TD/GYTL 164-12
第 2 页 共 2 页
表3 WDZ-J 、WDZ-H 低烟无卤塑料挤出温度参考表 单位℃
5 文件更改记录。
挤塑机操作流程

一. 挤塑机的加热操作1.150机器的加热(检查所有电气元件是否正常),在电气元件无损坏的情况下,合上总电源开关及各仪表的电源开关(此处开关是指主回路开关,也就是空气断路器或微型断路器). 150机各区加热温度设置(℃)2.等待150机加热30分钟之后,打开120机所有加热电源开关及控制开关。
120机各区加热温度设置(℃)3.整个机器的总加热时间为100分钟-120分钟左右,150机加热时间为100分钟-120分钟左右,120机加热时间为70分钟-90分钟左右。
备注:加热时长是在机器内部的料为空载的情况下,即每次停机之前必须将机器内部的原料推出机器,否则下次开机的加热时间将会延长。
二.挤塑机的启动,提速及下料操作挤塑机整机分别由上料系统,120螺杆,换网器,连接处,150螺杆,静态混合器及模具头组成。
1.启动150螺杆,启动频率为8HZ,启动后的电机电流在40-55A之间波动。
2.等待150螺杆正常启动1分钟后(正常启动即为螺杆没有异常响声,螺杆旋转顺畅,电机电流在规定范围内波动),启动120螺杆,启动频率为8HZ,启动后电机电流在40-55A之间波动。
3.等待120螺杆启动正常后2分钟可打开下料闸板下料。
4.挤塑机的提速过程当150机与120机都正常启动并无异常的情况下(电机无异常震动,螺杆旋转时无异常响声,螺杆旋转方向正常为逆时针旋转,所有电气仪表及元件无损坏及失灵)就可以通过变频器的操作面板来提高螺杆旋转速度,以便迅速的将系统压力建立起来,达到发泡要求。
a.提高120螺杆频率至10HZ,注意观察变频器面板中电机电流的显示是否平稳上升。
b.若120螺杆电机电流平稳上升,则调整120螺杆频率至15HZ,此时同上注意120螺杆电机电流上升情况,等待2分钟左右,待电机电流平稳之后,将120螺杆频率调至20HZ,同时注意观察电机电流的变化情况。
c.此时观察换网器的电子压力传感器的数字压力显示情况,等压力显示为4MPa时,将促进剂注入120螺杆(柱塞泵的行程为70%,促进剂的注入频率为20HZ),注入促进剂的目的是为了将聚苯乙烯的粘稠度降低,并使聚苯乙烯的物理形态变为微孔发泡的最佳状态。
电缆工艺技术之塑料挤出温度工艺技术参数

电缆工艺技术之塑料挤出温度在塑料的挤出过程中,物料聚集态的转变以及决定物料流动的粘度都取决于温度,因此,温度是塑料挤出工艺中最重要的工艺参数。
由于温度影响着塑料的熔融过程和熔体的流动性,因此挤出温度就和挤出工艺制品的质量有着密切的关系。
有研究指出,低温挤出有以下优点:保持挤出塑料层的形状比较容易;由于挤包层中热能较小,缩短了冷却时间;此外温度低还会减少塑料降解,这对聚氯乙稀是很重要的。
但挤出温度过低,会使挤包层失去光泽,并出现波纹、不规则破裂等现象;另外温度低,塑料熔融区延长,从均化段出来的熔体中仍夹杂有固态物料,这些未熔物料和熔体一起成型于制品上,其影响是不言而喻的。
温度对产品的物理性能影响是复杂的,电缆乙烯类塑料绝缘层抗张强度与挤出温度有关,对应于最大抗张强度有一最佳挤出温度。
提高低密度聚乙烯护套的挤出温度,能提高抗应力开裂强度。
但也应当指出,挤出温度过高,易使塑料焦烧,或出现“打滑”现象;另外温度高挤包层的形状稳定性差,收缩率增加,甚至会引起挤出塑料层变色和出现气泡等。
挤出物料的热量来自机筒加热和螺杆旋转剪切的粘性耗散和摩擦。
前者在运行初期是很重要的,后者在运行稳定后是主要的。
升高机筒温度很自然的会增加从机筒到塑料的热交换。
在挤出稳定运行后,螺杆旋转剪切变形的粘性耗散和摩擦热量,常常会使塑料达到或超过所需温度。
此时机内控制系统切断加温电源,挤出机进入“自然挤出”过程,并应视情况对机筒和螺杆进行冷却。
实践经验指出,冷却螺杆还有助于改善挤出质量,但同时也降低了挤出流率。
改善质量是由于冷却使螺杆均化段的有效槽深减少,增强了剪切作用。
挤出过程中温度不是孤立的,在流率不变,螺杆转数不变时,增加挤出温度会使挤出压力降低。
在低流率下,温度对压力的影响是很明显的,但影响会随流率的增加而逐渐减少。
挤出温度增加,还使所需螺杆的功率也降低了。
由于塑料品种的不同,甚至同种塑料(如聚乙烯)由于其结构组成的不同,其挤出温度控制不尽相同。