汽车离合器主缸标准
汽车设计0206第二章 离合器设计 第六节 操纵机构
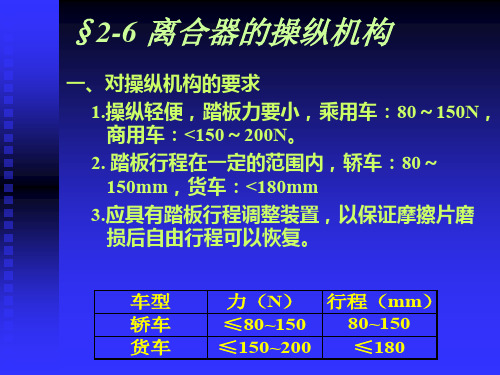
机械式和液压式操纵机构的助力器、气压式和自动 操纵机构等。
1.机械式:机械式操纵机构有杆系和绳索两种形 式。
普通杆系:结构简单、工作可靠,被广泛应用。 但其质量大,机械效率低,在远距离操纵时布置较 困难。
绳索式:传动机构可克服上述缺点,且可采用 吊挂式踏板结构。但其寿命较短,机械效率仍不高。 多用于轻型轿车中。
§2-6 离合器的操纵机构
一、对操纵机构的要求
4.应具有踏板行程限位器(限位螺钉),防止 操纵机构因受力过大而损坏。
5.具有足够刚度。 6. 传动效率要高。 7.发动机振动及车架和驾驶室的变形不会影响
其正常工作,操纵机构与车架、发动机无运 动干涉。 8.工作可靠、寿命长、维修保养方便。
§2-6 离合器的操纵机构
§2-6 离合器的操纵机构
液压式操纵机构主要由主缸、工作缸和 管路等部分组成,具有传动效率高、质量小、 布置方便、便于采用吊挂踏板、驾驶室容易 密封、驾驶室和车架变形不会影响其正常工 作、离合器接合较柔和等优点。广泛应用于 各种形式的汽车中。
§2-6 离合器的操纵机构
三、操纵机构的设计计算
踏板行程
S
S1 S2
(S0 f
ZS
c2 c1
)
a2b2d22 a1b1d12
§2-6 离合器的操纵机构
三、操纵机构的设计计算
踏板力(式2-43)
F
Ff i Fs
不考虑回位弹簧的作用,分离离合器所作功为:
WL
0.5
(F1
F )ZS
30J
§2-6 离合器的操纵机构
一、对操纵机构的要求 1.操纵轻便,踏板力要小,乘用车:80~150N, 商用车:<150~200N。 2. 踏板行程在一定的范围内,轿车:80~ 150mm,货车:<180mm 3.应具有踏板行程调整装置,以保证摩擦片磨 损后自由行程可以恢复。程(mm) ≤80~150 80~150 ≤150~200 ≤180
汽车干摩擦式离合器总成技术条件和台架试验方法

5.1.3.1.1 使载荷均匀作用于压盘表面,并与压盘工作表面垂直的试验台架。
5.1.3.1.2 试验夹具应能使盖总成模拟安装状态,如图 5 所示。
螺栓联接或压紧
加载 卸载
图 5 盖总成负荷特性试验示意图 5.1.3.2 试验步骤 5.1.3.2.1 将盖总成固定于试验夹具上,使压盘处于自由状态,如图 5 所示。 5.1.3.2.2 对压盘加载。螺旋弹簧离合器,加载使压盘超过工作点位置 2.5 mm 左右;膜片 弹簧离合器,加载使压盘超过负荷特性曲线谷值点位置 l mm 左右。然后卸载,直至卸掉全 部载荷,记录压盘上载荷随压盘位移变化的数值。
高度值即为分离指(杆)安装高度值。
5.1.1.3 分离指(杆)安装高度及分离指(杆)端面跳动量试验技术要求
在规定的条件下,盖总成的分离指(杆)安装高度偏差及端面跳动量应不大于表 1 中的
相应数值。
表 1 盖总成的分离指(杆)安装高度偏差及端面跳动量规定数值 mm
离合器规格 安装高度偏差
<200 ±1.0
4.2 对试验结果的评价 根据试验的性质、目的,将试验结果与产品图样技术要求或供需双方商定的技术要求等
进行比较,确定试件是否满足要求。 4.3 试验报告
试验完成后,编写试验报告,基本内容如下: a)试验名称; b)试验根据; c)试验目的; d)试验对象; e)试验方法和条件; f)试验结果与分析; g)试验结论。 5 试验方法和技术要求 5.1 盖总成功能特性试验 5.1.1 分离指(杆)安装高度及分离指(杆)端面跳动量试验 5.1.1.1 试验设备 5.1.1.1.1 能使载荷均匀作用于分离指(杆)端,并与压盘工作面垂直的测试台架。
浅谈汽车离合器主要参数的选择_赵鹏
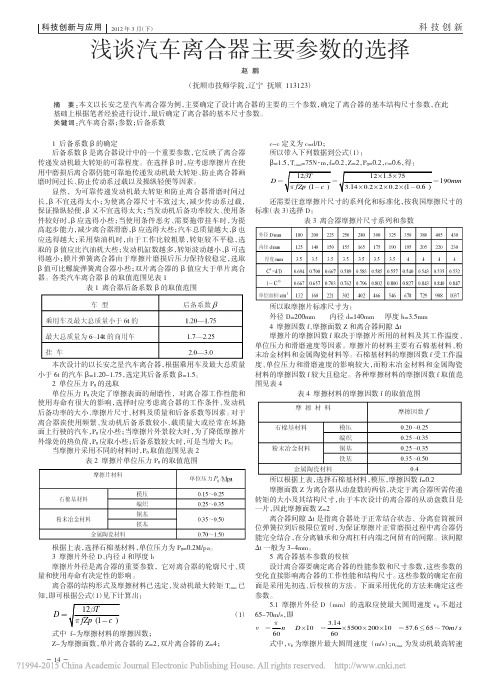
浅谈汽车离合器主要参数的选择赵鹏(抚顺市技师学院,辽宁抚顺113123)1后备系数β的确定后备系数β是离合器设计中的一个重要参数,它反映了离合器传递发动机最大转矩的可靠程度。
在选择β时,应考虑摩擦片在使用中磨损后离合器仍能可靠地传递发动机最大转矩、防止离合器画磨时间过长、防止传动系过载以及操纵轻便等因素。
显然,为可靠传递发动机最大转矩和防止离合器滑磨时间过长,β不宜选得太小;为使离合器尺寸不致过大,减少传动系过载,保证操纵轻便,β又不宜选得太大;当发动机后备功率较大、使用条件较好时,β应选得小些;当使用条件恶劣、需要拖带挂车时,为提高起步能力,减少离合器滑磨,β应选得大些;汽车总质量越大,β也应选得越大;采用柴油机时,由于工作比较粗暴,转矩较不平稳,选取的β值应比汽油机大些;发动机缸数越多,转矩波动越小,β可选得越小;膜片弹簧离合器由于摩擦片磨损后压力保持较稳定,选取β值可比螺旋弹簧离合器小些;双片离合器的β值应大于单片离合器。
各类汽车离合器β的取值范围见表1表1离合器后备系数β的取值范围本次设计的以长安之星汽车离合器,根据乘用车及最大总质量小于6t 的汽车β=1.20-1.75,选定其后备系数β=1.5。
2单位压力P 0的选取单位压力P 0决定了摩擦表面的耐磨性,对离合器工作性能和使用寿命有很大的影响,选择时应考虑离合器的工作条件、发动机后备功率的大小、摩擦片尺寸、材料及质量和后备系数等因素。
对于离合器诶使用频繁、发动机后备系数较小、载质量大或经常在坏路面上行驶的汽车,P 0应小些;当摩擦片外景较大时,为了降低摩擦片外缘处的热负荷,P 0应取小些;后备系数较大时,可是当增大P 0。
当摩擦片采用不同的材料时,P 0取值范围见表2表2摩擦片单位压力P 0的取值范围根据上表,选择石棉基材料,单位压力为P 0=0.2M/pa 。
3摩擦片外径D 、内径d 和厚度b 摩擦片外径是离合器的重要参数,它对离合器的轮廓尺寸、质量和使用寿命有决定性的影响。
重型汽车离合器参数选择设计

智能化参数选择技术的 发展历程
智能化参数选择技 术在重型汽车离合 器参数选择中的应
用
智能化参数选择技术的 优势和局限性
智能化参数选择技术的 发展趋势和前景
绿色环保材料 的定义和特点
绿色环保材料 在离合器参数 选择中的优势
绿色环保材料 在离合器参数 选择中的挑战
和问题
绿色环保材料 在离合器参数 选择中的应用 案例和效果分
离合器类型:干式单片离合器 扭矩需求:2000Nm 转速需求:2000rpm
工作环境:高温、高湿、高粉尘
材料选择:高强度钢、耐磨涂层
设计优化:优化摩擦片形状、优化 弹簧刚度、优化离合器间隙
品牌A离合器参数:扭矩、转速、尺寸等 品牌B离合器参数:扭矩、转速、尺寸等 品牌C离合器参数:扭矩、转速、尺寸等
析
智能化:离合 器参数选择将 更加智能化, 能够根据车辆 行驶状态和驾 驶员需求自动
调整
节能环保:离 合器参数选择 将更加注重节 能环保,降低
油耗和排放
舒适性:离合 器参数选择将 更加注重舒适 性,提高驾驶
体验
可靠性:离合 器参数选择将 更加注重可靠 性,提高离合 器的使用寿命
和稳定性
汇报人:
使用频率等因素
正确选择参数可以 提高离合器的耐用
性和可靠性
正确选择参数可以 降低维修成本和停
机时间
离合器参数选择不当可能 导致车辆起步困难、换挡
不平顺等问题
离合器参数选择不当可能 导致车辆在紧急情况下无 法及时响应,影响驾驶安
全
离合器参数选择不当可能 导致车辆在湿滑路面上打
滑,影响驾驶安全
离合器参数选择不当可能 导致车辆在长时间行驶后 出现磨损,影响驾驶安全
离合器设计手册
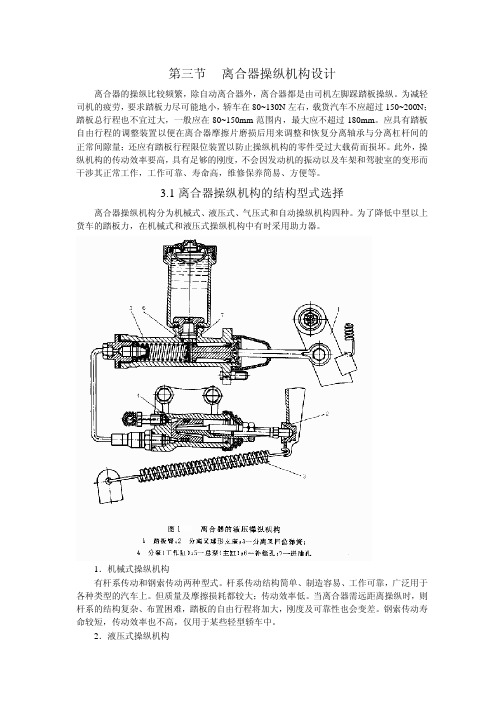
第三节离合器操纵机构设计离合器的操纵比较频繁,除自动离合器外,离合器都是由司机左脚踩踏板操纵。
为减轻司机的疲劳,要求踏板力尽可能地小,轿车在80~130N左右,载货汽车不应超过150~200N;踏板总行程也不宜过大,一般应在80~150mm范围内,最大应不超过180mm。
应具有踏板自由行程的调整装置以便在离合器摩擦片磨损后用来调整和恢复分离轴承与分离杠杆间的正常间隙量;还应有踏板行程限位装置以防止操纵机构的零件受过大载荷而损坏。
此外,操纵机构的传动效率要高,具有足够的刚度,不会因发动机的振动以及车架和驾驶室的变形而干涉其正常工作,工作可靠、寿命高,维修保养简易、方便等。
3.1 离合器操纵机构的结构型式选择离合器操纵机构分为机械式、液压式、气压式和自动操纵机构四种。
为了降低中型以上货车的踏板力,在机械式和液压式操纵机构中有时采用助力器。
1.机械式操纵机构有杆系传动和钢索传动两种型式。
杆系传动结构简单、制造容易、工作可靠,广泛用于各种类型的汽车上。
但质量及摩擦损耗都较大;传动效率低。
当离合器需远距离操纵时,则杆系的结构复杂、布置困难,踏板的自由行程将加大,刚度及可靠性也会变差。
钢索传动寿命较短,传动效率也不高,仅用于某些轻型轿车中。
2.液压式操纵机构如图1所示,液压式操纵机构由吊挂式离合器踏板、总泵(主缸)、分泵(工作缸)、管路系统、回位弹簧等组成。
具有摩擦阻力小,传动效率高,质量小,布置方便,接合柔和(有助于降低猛接离合器时传动系的动载荷),便于采用吊挂式踏板使该处地板易于密封,车架或车身的变形以及发动机的振动不会影响其工作,系统刚度好有助于减小踏板自由行程,也便于远距离操纵及采用可翻倾式驾驶室等优点。
它不仅最广泛地用于轿车及中、轻型客车及货车上,而且在大客车和重型货车上的应用也日益增多,但在中型以上的汽车上使用时应该加装助力器。
3.机械式和液压式操纵机构的助力器在中型以上的汽车上,为减轻离合器踏板力,在机械式和液压式操纵机构中常采用各种助力器。
离合器基本结构参数及尺寸的确定
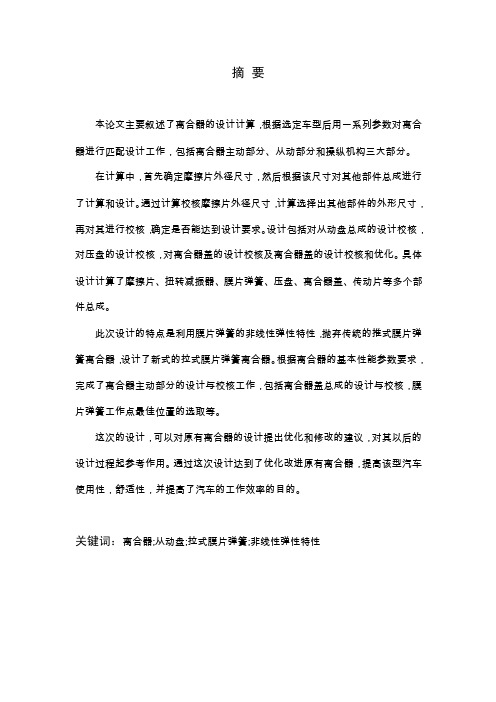
摘要本论文主要叙述了离合器的设计计算,根据选定车型后用一系列参数对离合器进行匹配设计工作,包括离合器主动部分、从动部分和操纵机构三大部分。
在计算中,首先确定摩擦片外径尺寸,然后根据该尺寸对其他部件总成进行了计算和设计。
通过计算校核摩擦片外径尺寸,计算选择出其他部件的外形尺寸,再对其进行校核,确定是否能达到设计要求。
设计包括对从动盘总成的设计校核,对压盘的设计校核,对离合器盖的设计校核及离合器盖的设计校核和优化。
具体设计计算了摩擦片、扭转减振器、膜片弹簧、压盘、离合器盖、传动片等多个部件总成。
此次设计的特点是利用膜片弹簧的非线性弹性特性,抛弃传统的推式膜片弹簧离合器,设计了新式的拉式膜片弹簧离合器。
根据离合器的基本性能参数要求,完成了离合器主动部分的设计与校核工作,包括离合器盖总成的设计与校核,膜片弹簧工作点最佳位置的选取等。
这次的设计,可以对原有离合器的设计提出优化和修改的建议,对其以后的设计过程起参考作用。
通过这次设计达到了优化改进原有离合器,提高该型汽车使用性,舒适性,并提高了汽车的工作效率的目的。
关键词:离合器;从动盘;拉式膜片弹簧;非线性弹性特性AbstractThis thesis mainly describes the clutch design and calculation, according to the selected models with a range of parameters matching the design of the clutch, including the active part of the clutch, the driven part and manipulate bodies of three parts.In the calculation, first determine the size diameter friction plate, and then according to the size of other parts assembly and design is calculated. Check by calculating the friction plate diameter size, calculated to select the size of other components, and then check them to see whether it can meet the design requirements. Design including the design of the driven disc assembly verification, the design of the pressure plate check on the clutch cover, clutch cover design verification and design verification and optimization. Calculation of the specific design of the friction plate, reversing the shock absorber, diaphragm spring, pressure plate, clutch cover, transmissioncomponents, such as chip assembly.The design is characterized by the use of the nonlinear elastic properties of the diaphragm spring, to abandon the traditional push-type diaphragm spring clutch, designed a new pull-type diaphragm spring clutch. According to the requirements of the basic performance parameters of the clutch, the clutch active part of the design and checking work, including the design of the clutch cover assembly and check the selection of the best position of the diaphragm spring operating point. The driven part with reversing the shock absorber separation of the driven plate .The design of the original design of the clutch to optimize and modify the proposal, its future role in the design process from the reference. Achieved through optimization of the design to improve the original clutch and improve the use of this type of vehicle, comfort, and enhance the work of automobile efficiency.Key words: Clutch; Follower plate; Pull the diaphragm spring; Nonlinear elastic characteristics1 绪论1.1离合器概述离合器是汽车传动系统的主要组成之一,也是传动系统中第一个总成。
离合器主要参数的选择

马
中、重货车
天
越、牵引车
飞
1.20~1.75 1.50~2.25 1.80~4.00
17
2、单位压力p0
汽
影响 p0 取值的因素
要求 p0
备注
车
工作条件
离合器使用频繁时 发动机后备功率小
设
衬片外径 D 大时
计
取小 取小 取小
如农村、市内 线速度提高、磨损增加
教
后备系数 β 较大
取大 滑磨功小、磨损速度下降
案
jB rB tB
60Si2MnA材料的许用应力为 1500~1700MPa。
马 天 飞
31
四. 主要参数的选择
汽
1. H/h 和 h
车
H/h决定了膜片弹簧弹性特性曲线的形状。
设
推荐 H/h =1.5~2.0, h =2~4mm
计
教
案
马 天 飞
32
2. R/r和R、r的选择
0.53≤c≤0.70
马
天 飞
3) β
1.2 4.0
22
汽
4) d
d>2R0+50
车
R0——减振弹簧位置半径
设
保证扭转减振器的安装
计
5) 单位面积传递的转矩
教 案
Tc0 Z
4Tc D2 d 2
Tc0
[Tc0 ]见表2 5
6) p0 0.10MPa p0 1.50MPa
长 复杂、拆装困
难
短 结构简单
①当离合器尺寸相同(D);Temax 一样;则F2=F2’
F1
F2 l 2 l1
离合器系统使用、保养、检修技术规范
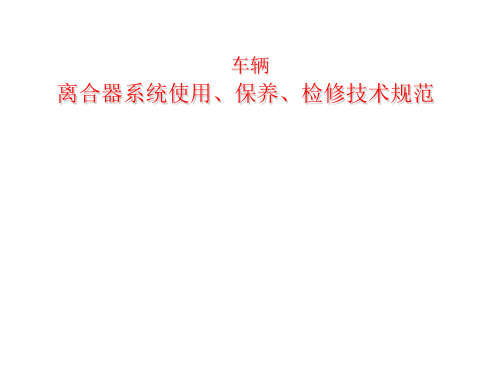
离合器接合状态示意图
目录 退出
前页
后页
离合器接合状态示意图
目录 退出
前页
后页
目录
三、汽车离合器及相关零部件的常见故障现象的 退出
诊断与维修
前页 后页
离合系统的功能是保证发动机与传动系统平稳
可靠地接合,并且能暂时而彻底地分离。接合是指
产生摩擦力矩,分离是指解除摩擦力矩。离合器工
作频繁,在汽车行驶时,由于滑动摩擦的作用各部
件容易磨损,变形或破裂等,摩擦力矩相应降低,
导致离合系统故障。为了尽可能地延长离合器的使
用寿命,因此,如何正确地对离合系统进行有效的
维护就显得相当重要。
离合器在使用过程中,经常出现的故障主要 有离合器踏板沉重、打滑、分离不彻底(挂档困难)、 发抖、发闯、异响等。
1、离合器踏板沉重的故障现象,原因,检验方法及维修
发生摩擦片烧蚀。
后页
如果不踩油门,二挡起步,有时发动机会熄火, 此时车体的振动不能说明离合器发抖。
离合器发抖,一般情况下摩擦片表面呈据齿状接触痕迹,有 时摩擦片表面局部粘油也会造成发抖,此时应确认油污 的来源并修复.
故障原因:
目录 退出
离合分泵无空行程
前页
刹车系统调整不当,过紧,行使后轮毂烫手
后页
第二步:在用打滑试车方法确认有离合器打滑的情况下,首先检 查离合器踏板有无自由行程,行程是否满足汽车厂家维修手 册的规定要求;检查离合器分离拨叉有无自由行程 (7~8mm).若不符合要求应调整至要求范围内,若仍不能排 除故障进行下一步.
第三步:检查调整刹车系统,若仍不能排除故障进行下一步.
第四步:拆下变速器,检查分离轴承,分离拔叉有无卡涉现象,若 有须更换.同时检查离合器有无粘油现象,若有须确认油污来 源,并修复。拆卸离合器,检查盘总成、盖总成、飞轮磨损是 否超标, 若磨损超标应更换.检查摩擦片是否有烧损现象,若 轻微烧损可用粗砂纸打磨后继续使用,若烧损严重则需更换。
汽车离合器技术标准

汽车离合器技术标准汽车离合器是汽车传动系统中的重要部件,它通过连接和断开发动机与变速器之间的动力传递,使车辆能够顺利换挡和停车。
离合器的性能直接影响着汽车的驾驶感受和燃油经济性,因此制定和遵守汽车离合器技术标准显得尤为重要。
首先,汽车离合器技术标准应包括离合器的材料要求。
离合器摩擦片和压盘的材料选择直接关系到离合器的寿命和性能。
常见的摩擦片材料有有机、金属和陶瓷,而压盘一般采用铸铁或铝合金。
这些材料的选择需要考虑到摩擦性能、耐磨性、散热性以及成本等因素,制定合理的技术标准可以确保离合器在各种工况下都能够稳定可靠地工作。
其次,技术标准还应包括离合器的结构设计要求。
离合器的结构设计直接关系到其传动效率和操作舒适性。
例如,离合器的弹簧和减震器的设计需要能够提供适当的压力和减震效果,以确保离合器在工作时能够平稳连接和断开。
此外,离合器的液压控制系统和调整装置也需要符合标准要求,以保证离合器的操作力和行程符合设计要求,从而确保换挡过程的平稳性和可靠性。
另外,技术标准还应考虑离合器的磨损和故障诊断要求。
离合器在长时间使用后会产生磨损,因此技术标准需要规定离合器磨损限度和检测方法,以便及时更换磨损严重的部件。
同时,标准还应包括离合器故障的诊断和排除方法,以确保在出现故障时能够迅速准确地找到问题并进行修复,减少因离合器故障而造成的安全隐患和经济损失。
最后,技术标准还应包括离合器的性能测试和评价方法。
通过对离合器的承载能力、传动效率、耐磨性等性能进行测试和评价,可以确保离合器的性能符合设计要求,并且能够在各种工况下稳定可靠地工作。
同时,还可以通过性能测试和评价来指导离合器的优化设计和制造工艺,提高离合器的质量和可靠性。
总之,制定和遵守汽车离合器技术标准对于提高离合器的性能和可靠性具有重要意义。
只有通过严格的材料要求、结构设计、磨损和故障诊断、性能测试和评价等方面的标准,才能够确保汽车离合器能够在各种工况下稳定可靠地工作,从而提高汽车的驾驶感受和安全性能,减少能源消耗和环境污染。
离合器液压操纵机构的组成

离合器液压操纵机构主要由离合器踏板、储液罐、高压和低压油管、离合器主缸、工作缸等组成。
离合器起始于离合器踏板,终于飞轮壳内的分离轴承。
离合器操纵机构是驾驶员借以使离合器分离,而后又使之柔和接合的一套机构,按照分离离合器所用传动装置的型式区分有机械式、液压式和助力器式。
离合器操纵机构的结构型式应根据对操纵机构的要求、车型、整车结构、生产条件等因素确定。
气压操纵机构的系统压力必须大于0.22MPa,气压助力液压操纵机构的储气筒内压缩空气的压力必须达到规定的标准(≥450kPa),否则踩踏离合器踏板时感到沉重。
此外,应确保液压工作缸、主缸和助力器各部的密封性,如有漏泄,离合器下踩也会感到沉重。
请注意,离合器液压操纵机构的组成可能因车型和制造商的不同而有所差异。
在进行任何维修或更换部件之前,建议查阅相关的车辆维修手册或咨询专业的汽车维修技师。
汽车离合器10

2.5.2 离合器主要零件的检修
(1)飞轮。 (2) 压盘和离合器盖。 (3) 从动盘 。 (4) 膜片弹簧。 (5) 螺旋弹簧。 (6) 分离杠杆、分离轴承和分离叉。
2.5.3离合器的装配与调整
1.离合器的装配 装配时应注意下列各点: (1) 弹簧长度和弹力应一致,如有部分弹簧长度稍短, 弹力稍弱,则应将弹力较弱的弹簧均匀对称的相间排放。 (2) 分离杠杆的各活动部位应涂少量润滑脂。 (3) 两从动盘的应短毂相对面向中间压盘,不许装错。 如果一片装反了,将使两从动盘之间的距离大于中间压盘的 厚度,工作中从动盘受压变形;如两片都装反了则离合器不 能装复。 (4) 中间压盘装复时,有弹簧座孔的一面向飞轮,其 锥形支撑弹簧大端装在座孔内。
18-分离轴承内套;19-锁止螺母;20-黄油嘴;21-离合器制动摩擦片; 22-变速器壳端面;23-变速器第-轴;24-分离轴承; 25-分离轴承套;26-分离轴承盖
2.3.5湿式离合器
图2-17湿式离合器 1-油勺;2-压盘;3-离合器底壳;4-润滑油;5-散热器;
6-集油器;7-从动盘钢片;8-孔系; 9-集油孔;1 0-油道
3)压紧机构 压紧弹簧
压盘
压紧机构主要由螺旋弹簧或膜片弹簧组成,与主 动部分一起旋转,它以离合器盖为依托,将压盘压向 飞轮,从而将处于飞轮和盘压间的从动盘压紧。
4)离合器操作机构
操纵机构是为驾驶员控制离合器分离与接合 程度的一套专设机构。它是由位于离合器壳内的 分离杠杆(在膜片弹簧离合器中,膜片弹簧兼起 分离杠杆的作用)、分离轴承、分离套筒、分离 叉、回位弹簧等机件组成的分离机构和位于离合 器壳外的离合器踏板及传动机构、助力机构等组 成。
汽车离合器基本参数的确定

217GLOBAL CITYGEOGRAPHY 汽车离合器基本参数的确定刘文庆(西华大学西华学院,四川 成都 610039)摘要:本文以轻型载重货车膜片弹簧离合器为例,其后备功率小。
主要根据已知的两个参数,进行初步的参数选择,然后根据约束条件判定初选参数是否符合要求,最后确定了离合器的基本尺寸参数。
关键词:膜片弹簧;离合器;基本尺寸参数一.已知参数设计车型:轻型载重货车 后备功率小 最大转矩:Temax/n1=294.0/2500rpm 发动机最高转速nmax=4700rpm二.基本参数及尺寸的确定1.摩擦片外径D、内径d 及厚度B 的确定(1)摩擦片外径是离合器的重要参数,它关系到离合器的轮廓结构,尺寸质量和使用寿命。
设计上一般首先确定摩擦片的外径D。
根据经验公式,利用经验公式进行初选:(1) 式中,KD表示直径系数表1 直径系数K D取值范围本次设计的是轻型货车,且初步设计单片,故初选:KD=16.5 根据已知的参数代入(1)公式算出:D=282.9 mm表 2 摩擦片尺寸系列根据表2中数据选择摩擦片外径D=280mm 内径d=165mm 从而确定摩擦片厚度为3.5mm2.离合器后备系数β的确定后备系数β是离合器设计中的一个重要参数,它反映了离合器传递发动机最大转矩的可靠程度。
后备系数β的选取还需要考虑很多因素。
为了可靠地传递转矩并且防止滑磨时间太长,β不应选的过小。
β不宜太大,若β取太大,离合器尺寸会相应变大,操纵机构变得复杂且不轻便,传动系会出现大的过载。
双片离合器的β值应大于单片离合器。
在开始设计离合器时,一般是参照统计资料,并根据汽车的使用条件,离合器结构形式的特点,初步选择后备系数。
根据标准,本次设计初步选择后备系数β=1.33.单位压力P 0的确定摩擦片上的单位压力P0值和离合器本身使用条件,后备系数的选取,摩擦片使用的材料、自身质量因素有很大的关联,当然摩擦片的直径也必须考虑。
汽车离合器主缸标准

汽车液压离合器主缸技术条件1.范围本标准规定了汽车液压离合器主缸总成的产品分类、技术要求、试验方法、检验规则及标志、包装、运输与贮存。
本标准适用于使用非石油基制动液的汽车液压离合器主缸总成(以下简称主缸)2.规范引用文件下列文件中的条款通过本标准的引用而成为本标准的条款。
凡是注日期的引用文件,其随后所有的修改单(不包括勘误的内容)或修订版均不适用于本标准,然而,鼓励根据本标准达成协议的各方研究是否可使用这些文件的最新版本。
凡是不注日期的引用文件,其最新版本适用于本标准。
GB/T1031-1995 表面粗糙度参数及其数值GB/T1801-1999 极限与配合公差带和配合的选择GB12981-2003 机动车辆制动液GB/T13384-1992 机电产品包装通用技术条件HG2865-1997 汽车液压制动橡胶皮碗3.产品分类3.1 按工作条件分为两类(见表1)主缸的最高工作液压为10MPa。
4.技术要求4.1基本要求4.1.1主缸应按规定程序批准的图样和文件制造,并应符合本标准的要求4.1.2主缸表面应清洁、无锈蚀、毛刺、裂纹和其它缺陷。
4.1.3 活塞皮碗应满足HG2865--1997的要求4.1.4制动液应符合GB12981-2003的要求4.2 总成性能要求4.2.1 常温性能:4.2.1.1 连通性能空气应从进液孔排出4.2.1.2 空行程活塞的行程应在0.5mm-1.8mm范围内4.2.1.3 输出功能活塞在推杆的反复作用下,动作灵活,制动液应从排液孔断续地流出.4.2.1.4 活塞回位时间活塞回位时间应不大于1.5S4.2.1.5 高压密封性能在主缸内建立起最高工作液压10MPa,保持30S液压降不大于0.3MPa。
4.2.1.6 耐压性能各部位无泄漏及异常现象4.2.1.7真空密封性在供液孔内产生真空度为0.026 MPa±0.004MPa.保压5S无泄漏。
4.2.1.8动态密封性在补偿孔关闭状态下,在出油口建立200KPa气压,稳压1S后,推动活塞至活塞最大行程减3mm处,再释放活塞回位到原处,一个往复行程压力降不大于2KPa.4.2.2工作耐久性能4.2.2.1高温耐久性能试验过程中各部位无明显泄漏,活塞动作灵活,无任何异常现象。
汽车离合器主缸补偿孔的尺寸链探讨
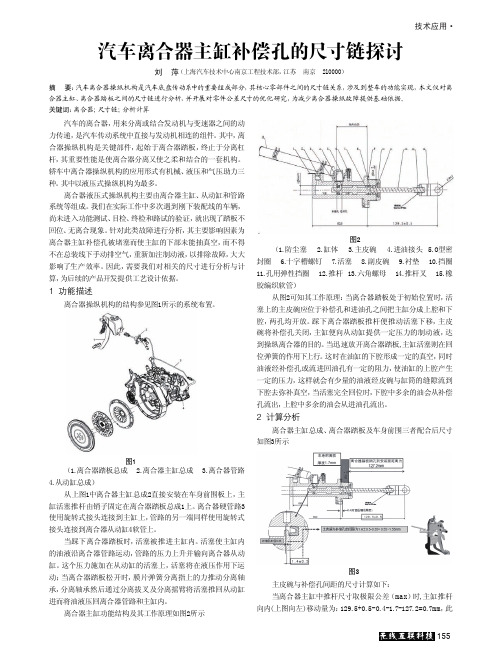
图4 主皮碗与补偿孔间距如图4所示 从以上尺寸计算及图4中可清晰看出此尺寸不会使主缸补 偿孔被堵塞。 4 结束语 综上分析可知: 使用离合器主缸推杆尺寸129.5±0.5公差带由1.0修改为 0.6较为合适;而在汽车行驶一定里程后,为实现系统工作可靠 及正常油压,当液压系统中因漏油或因温度变化引起油液的体 积变化时,则可借补偿孔适时使整个油路中油量得到增减,从 而保证正常油压和油液堵塞孔。 离合器主缸推杆的间距补偿还可以通过调整图2中推杆 (件号1)上六角螺母(件号13)来进行调节。
汽车的离合器,用来分离或结合发动机与变速器之间的动 力传递,是汽车传动系统中直接与发动机相连的组件。其中,离 合器操纵机构是关键部件,起始于离合器踏板,终止于分离杠 杆,其重要性能是使离合器分离又使之柔和结合的一套机构。 轿车中离合器操纵机构的应用形式有机械、液压和气压助力三 种。其中以液压式操纵机构为最多。
摘 要:目前我国人口老龄化程度越来越高,选择在老年公寓等养老机构生活的老年人越来越多。本文分析了我国老年公寓的现状与存在问 题,探索了老龄化背景下新型老年公寓的设计思路和方法,主要从当代老年公寓的服务、居住环境、交往、交通等方面进行分析和探讨,为老 年公寓设计走向人性化和合理话提供参考和建议。 关键词:老年公寓;规划设计;养老模式
2 计算分析
离合器主缸总成、离合器踏板及车身前围三者配合后尺寸 如图3所示
图1 (1.离合器踏板总成 2.离合器主缸总成 3.离合器管路 4.从动缸总成) 从上图1中离合器主缸总成2直接安装在车身前围板上,主 缸活塞推杆由销子固定在离合器踏板总成1上。离合器硬管路3 使用旋转式接头连接到主缸上,管路的另一端同样使用旋转式 接头连接到离合器从动缸4软管上。 当踩下离合器踏板时,活塞被推进主缸内。活塞使主缸内 的油液沿离合器管路运动,管路的压力上升并输向离合器从动 缸。这个压力施加在从动缸的活塞上,活塞将在液压作用下运 动;当离合器踏板松开时,膜片弹簧分离指上的力推动分离轴 承,分离轴承然后通过分离拔叉及分离摇臂将活塞推回从动缸 进而将油液压回离合器管路和主缸内。 离合器主缸功能结构及其工作原理如图2所示
【故障情报站】别克英朗更换离合器主缸的技术指导

【故障情报站】别克英朗更换离合器主缸的技术指导涉及车辆2015—2017年款别克全新英朗手动挡车型。
故障内容以上部分车辆由于零件受残留油脂影响,极端情况下离合器主缸可能工作异常,造成换挡困难,存在安全隐患。
针对这一问题,需更换离合器主缸以消除隐患,具体操作步骤如下。
1.断开离合器主缸软管并排空(1)断开总泵储液罐和离合器主缸储液罐之间的软管接口,使软管自然垂落,并使用合适的容器置于储液罐及软管接口下端,拧开总泵储液罐盖,让制动液从接口处流出,当无油液流出时,取下接油液的容器。
(2)从变速器上断开离合器执行器缸前管,使离合器执行器缸前管自然垂落,让管路内制动液流尽,同时踩20次制动踏板,以利于液体流出。
2.拆卸离合器总泵(1)拆下制动踏板导销及其卡夹,将离合器总泵从离合器踏板上断开。
(2)断开离合器执行器缸前管的固定螺栓及卡扣。
(3)从离合器总泵上断开执行器缸前管。
(4)拆下离合器总泵螺母。
3.安装新的离合器总泵(1)更换新的离合器总泵,并将螺母紧固至22N·m。
(2)安装离合器执行器缸前管,拧紧固定螺栓,装好卡扣。
(3)用干净的布擦拭油壶出油口,清理杂质,然后安装离合器总泵储液罐软管。
(4)将离合器总泵连接到离合器踏板,并安装制动踏板导销及卡夹。
4.清理离合器系统(1)清洁储液罐及周边的外侧表面。
先不要连接离合器执行器缸前管变速器端的接头,在总泵储液罐中持续缓缓加入新的DOT 4+制动液。
待制动液从离合器执行器缸前管接头流出大概200mL后,停止加注制动液,然后连接执行器缸前管至执行器缸。
(2)将DOT 4+制动液加注至正确油位。
添加完制动液后,将储液罐盖子以正确的方向旋入,拧紧后旋盖应处于下图所示的正确位置。
5.对液压离合器系统排气(1)液压离合器执行器仅可从放气阀放气,将一根透明的排气软管一端连接至排气阀,另一端连接至收集容器。
(2)在助手的帮助下,一人踩踏离合踏板5~10次(1次/秒),然后保持踏板压力;另一人同时拧松排气阀,待含有空气气泡的油液流出后,再拧紧排气阀。
- 1、下载文档前请自行甄别文档内容的完整性,平台不提供额外的编辑、内容补充、找答案等附加服务。
- 2、"仅部分预览"的文档,不可在线预览部分如存在完整性等问题,可反馈申请退款(可完整预览的文档不适用该条件!)。
- 3、如文档侵犯您的权益,请联系客服反馈,我们会尽快为您处理(人工客服工作时间:9:00-18:30)。
汽车液压离合器主缸技术条件
1.范围
本标准规定了汽车液压离合器主缸总成的产品分类、技术要求、试验方法、检验规则及标志、包装、运输与贮存。
本标准适用于使用非石油基制动液的汽车液压离合器主缸总成(以下简称主缸)
2.规范引用文件
下列文件中的条款通过本标准的引用而成为本标准的条款。
凡是注日期的引用文件,其随后所有的修改单(不包括勘误的内容)或修订版均不适用于本标准,然而,鼓励根据本标准达成协议的各方研究是否可使用这些文件的最新版本。
凡是不注日期的引用文件,其最新版本适用于本标准。
GB/T1031-1995 表面粗糙度参数及其数值
GB/T1801-1999 极限与配合公差带和配合的选择
GB12981-2003 机动车辆制动液
GB/T13384-1992 机电产品包装通用技术条件
HG2865-1997 汽车液压制动橡胶皮碗
3.产品分类
3.1 按工作条件分为两类(见表1)
主缸的最高工作液压为10MPa。
4.技术要求
4.1基本要求
4.1.1主缸应按规定程序批准的图样和文件制造,并应符合本标准的要求
4.1.2主缸表面应清洁、无锈蚀、毛刺、裂纹和其它缺陷。
4.1.3 活塞皮碗应满足HG2865--1997的要求
4.1.4制动液应符合GB12981-2003的要求
4.2 总成性能要求
4.2.1 常温性能:
4.2.1.1 连通性能
空气应从进液孔排出
4.2.1.2 空行程
活塞的行程应在0.5mm-1.8mm范围内
4.2.1.3 输出功能
活塞在推杆的反复作用下,动作灵活,制动液应从排液孔断续地流出.
4.2.1.4 活塞回位时间
活塞回位时间应不大于1.5S
4.2.1.5 高压密封性能
在主缸内建立起最高工作液压10MPa,保持30S液压降不大于0.3MPa。
4.2.1.6 耐压性能
各部位无泄漏及异常现象
4.2.1.7真空密封性
在供液孔内产生真空度为0.026 MPa±0.004MPa.保压5S无泄漏。
4.2.1.8动态密封性
在补偿孔关闭状态下,在出油口建立200KPa气压,稳压1S后,推动活塞至活塞最大行程减3mm处,再释放活塞回位到原处,一个往复行程压力降不大于2KPa.
4.2.2工作耐久性能
4.2.2.1高温耐久性能
试验过程中各部位无明显泄漏,活塞动作灵活,无任何异常现象。
4.2.2.2常温耐久性能
试验过程中各部位无明显泄漏,活塞动作灵活,无任何异常现象
4.2.3 清洁度
主缸清洁度限值不大于18mg
5. 试验方法
5.1 试验装置
图1 耐久性试验主缸装置
5.1.1 冲程装置
冲程装置可以为机械、气动或液压式三种,能够单次地与周期地推动主缸,单次地推动主缸时在液压系统中能建立起最高工作液压的130%,且可以保持活塞在不同冲程位置。
周期地推动主缸时,频率为1000次/h±100次/h。
5.1.2 工作缸装置
工作缸装置如图1所示,试验时将工作缸进液孔与主缸排液孔连接
5.2 试验要求
5.2.1试验样品应符合制造厂的技术要求,每次试验样品不少于3件,试验结束后才能解体总成,特殊情况除外。
5.2.2 试验用制动液为非石油基制动液,应满足GB12981-2003的要求,具体牌号可以由供需双方商定。
5.3 常温性能试验
5.3.1 试验条件
a)压力表精度不低于0.4级
b)环境温度 10-32℃
5.3.2 试验方法
5.3.2.1连通性能试验
向主缸排液孔通入不大于0.1MPa气压,观察进液孔是否有气体排出。
5.3.2.2 空行程试验
向主缸排液孔通入0.05MPa-0.15MPa气压,空气由进液孔排出后,缓慢地推动活塞,当气流停止从进液孔排出时,记录活塞最小位移量。
5.3.2.3输出功能试验
向主缸内注满制动液,排净系统中的空气,连续反复地推动活塞,观察制动液的排出状况及活塞动作的灵活性。
5.3.2.4活塞回位时间测量
向主缸内注满制动液,排净系统中的空气,将活塞推至最大行程后,关闭排液孔,迅速撤消推杆力,记录活塞完全返回原位的时间
5.3.2.5高压密封性能试验
向主缸注满制动液,排净系统中的空气,推动活塞在主缸内中建立起最高工作液压10MPa,稳压后保持推杆位置不变,30S后记录液压降。
5.3.2.6耐压性能试验
试验装置同上,缓慢地推动活塞,经过15S±5S在主缸内建立起最高工作液压的130%(13MPa)稳压后保持推杆位置不变,5S后记录液压降。
5.3.2.7真空密封性试验
将主缸供液孔与真空源连接,使主缸处于工作状态,在供液孔内产生真空度为0.026 MPa ±0.004MPa,检测付皮碗与供液腔的密封性, 5S后记录变化量。
5.3.8动态密封性
试验装置同上,缓慢地推动活塞,推动4mm主密封圈堵上补偿孔以后,在制动腔中建立起200KPa±5KPa气压,稳压1S后,缓慢地推动活塞至活塞最大行程减3mm处,再缓慢地释放活塞至原处后记录液压降。
5.4 工作耐久性能试验
5.4.1 试验条件
试验条件见表2
5.4.2 试验方法
向主缸内注满制动液排净系统中的空气,确认液压系统无任何泄漏后,把主缸试验装置安装在恒温箱中,在主缸下面放滤纸,开始试验。
试验过程中每2h观察有无泄漏情况。
20%或以下 90%或以上活塞行程(mm)
图2 活塞行程与液压关系曲线
5.5清洁度检验
试验方法按QGn29008.13的规定检验清洁度
6.检验规则
6.1 主缸须经制造厂检验部门检验合格后方可出厂,并附有产品质量合格文件。
6.2 出厂检验
6.2.1本标准4.2.1.7、4.2.1.8为出厂检验项目。
随机抽样3件,进行逐项检验。
6.2.2本标准中4.2.3 每月抽查一次
6.3型式试验
6.3.1有下列情况之一的,应进行型式检验:
a)新产品投产时;
b)材料和工艺有重大改进可能影响产品性能时;
c)正常生产每年进行一次;
d)国家质量监督检验机构抽检产品时。
6.3.2型式检验的样品从该检验合格的产品中随机抽样,数量3件。
6.3.3如有不合格项,应加倍抽样对不合格项进行复验,若复验结果仍不合格,则判定为不合格。
6.4 订货单位有权抽检产品。
抽检项目和抽样方案由供需双方商定。
6.5在正常使用和保养条件下,自出厂之日起一年内,且里程不超过25000公里,产品确因制造质量不良而引起的损坏,制造厂应免费给予更换或修理。
7.标志、包装、运输、贮存
7.1 每件产品在醒目的部位标注制造厂标记、标明商标、产品名称、产品型号、出厂年月7.2 产品包装应符合GB/T13384-1992的规定并附有合格证
7.3 产品包装应牢固,能保证产品在运输和贮存期的安全和清洁,包装箱面或标签上应注明:制造厂名称、产品名称、产品型号或标记、数量、制造日期。