数控车床铣床通过对刀设置加工坐标系
数控机床对刀

(7)将光标移动至欲设定的偏置号处。
(8)输入Zβ(或0)。
(9)按软键[MESURE]。
(10)在手动方式中用一把实际刀具切削外圆。
(11)仅仅在Z方向上退刀,不要移动X,停止主轴。
(12)测量被车削部分的直径D。
(13)按功能键OFFSET/SETING。
(14)按软键[OFFSET]。
实习总结:
用试切法确定起刀点的位置对刀的步骤:
(1)在MDI或手动方式下,用基准刀切削工件端面;
(2)用点动移动X轴使刀具试切该端面,然后刀具沿X轴方向退出,停主轴。
记录该Z轴坐标值并输入系统。
(3)用基准刀切量工件外径。
(4)用点动移动Z轴使刀具切该工件的外圆表面,然后刀具沿Z方向退出,停主轴。用游表卡尺测量工件的直径,记录该X坐标值并输入系统。
(3)对刀点与对刀:对刀点是用来确定刀具与工件的相对位置关系的点,是确定工件坐标系与机床坐标系的关系的点。
对刀就是将刀具的刀位点置于对刀点上,以便建立工件坐标系。
(4)对刀基准(点):对刀时为确定对刀点的位置所依据的基准,该基可以是点、线、面,它可以设在工件上或夹具上或机床上。
(5)对刀参考点:是用来代表刀架、刀台或刀盘在机床坐标系内的位置的参考点,也称刀架中心或刀具参考点。
(5)对第二把刀,让刀架退离工件足够的地方,选择刀具号,重复(1)—(4)步骤。
法拉克车床对刀:
基准刀的对法:
(1)在手动方式中用一把实际刀具切削端面。
(2)仅仅在X轴方向上退刀,不要移动Z轴,停止主轴。
(3)测量工件坐标系的零点至端面的距离β(或0)。
(4)按功能键OFFSET/SETING。
(5)按软键[OFFSET]。
数控铣床的坐标系

• 而在操作与控制机床时,机床不同的运动结构就导致其进给运动部件 的运动方向是不同的。弄清这一点,对手动控制机床又很重要的意义。 因为大多数机床手动移动按钮正负指的是运动方向。同样为立式铣床, 动工作台式立式铣床Z轴坐标正方向为向上,而工作台运动正方向为向 下,由Z`表示。动主轴式立式铣床Z轴坐标正方向与工作台运动正方向 一致。
对于静止工件的运动,其与机床结构无关。而机床进给运动部件的方向
为机床实际运动方向,是与机床结构直接相关的。
• 在编程时,只要属于同一类的机床,无论刀具运动还是工作台运动,采 用的坐标系的方向都是一致的,即都是假定刀具运动,其与机床结构无 关。这样的编程人员在不考虑机床上工件与工具具体运动的情况下,就 可以依据零件样图,确定机床的加工过程。
右手笛卡尔坐标系
• 笛卡尔坐标系只表明六个坐标之间的关系, 而对于数控机床坐标方向的判断则有如下规 定
• 原则一:刀具相对于静止的工件坐标而运动
• 由于进给运动方向规定为刀具相对于静 止的工件的方向,因此,在加工零件时,无 论刀具运动,还是工件运动,为了统一编程 规则,永远假定刀具相对于静止的坐标系而 运动。
– 方向原则:X坐标轴平行于工件的装夹平面
– 正方向原则:对于刀具旋转的机床(如铣床、钻床、 镗床),X坐标轴的正方向为由刀具向立体柱看,右 侧为正
• 3.Y坐标的方向判定
• 根据Z坐标轴和X坐标轴的正方向,利用右手定 则可以确定Y坐标轴的正方向。
• 4.机床为了统一描述而人为规定的,规定的原则为刀具相
• 原则二:坐标轴正方向的判断顺序为先Z后 X再Y。下面以铣床为例进行说明。
• 1.Z坐标的方向判定
– 方向原则:与主轴轴线平行的坐标轴为Z坐标轴。对
数控铣床操作与对刀

数控铣床面板操作与对刀知识点:1、数控铣床操作面板的功能与使用方法;2、数控铣床操作说明书;3、对刀的方法4、刀具补偿概念技能点:1、能按照操作规程启动和停止机床;2、正确使用操作面板上的常用功能键;3、通过各种途径输入加工程序;4.进行对刀并确定相关参数坐标;5.正确地设置刀具参数;一、任务引入数控铣床的操作面板是由系统操作面板(CRT/MDI操作面板)和机械操作面板(也称为用户操作面板)组成。
面板上的功能开关和按键都有特定的含义。
由于数控铣床配用的数控系统不同,其机床操作面板的形式也不相同,但其各种开关、按键的功能及操作方法大同小异。
结合本校实际情况,以JM-850M数控铣床/加工中心上的Fanuc-Oi MC系统为例介绍数控铣床的操作。
二、任务分析要掌握数控铣床的操作,机床的操作面板的操作是关键,熟悉数控铣床的控制面板是操作机床的的基础,掌握操作面板上的常用功能键的使用以及机床的加工控制,是后续任务的基础。
三、相关知识(一)、Fanuc-Oi MC数控系统简介图2-1 Fanuc-Oi MC数控系统CRT/MDI面板Fanuc Oi Mate-MC数控系统面板由系统操作面板和机床控制面板三部分组成。
1、系统操作面板系统操作面板包括CRT显示区、MDI编辑面板。
如图2-1。
(1)、CRT显示区:位于整个机床面板的左上方。
包括显示区和屏幕相对应的功能软键(图2-2)。
(2)、编辑操作面板(MDI面板):一般位于CRT显示区的右侧。
MDI面板上键的位置(如图:2-3)和各按键的名称及功能见表2-1和表2-2。
图2-2 Fanuc Oi Mate-MC数控系统CRT显示区1、功能软键2、扩展软键图2-3 MDI面板表2-1 Fanuc Oi MC系统MDI面板上主功能键与功能说明表2-2 Fanuc Oi MC系统MDI面板上其他按键与功能说明2、机床控制面板Fanuc Oi Mate-MC数控系统的控制面板通常在CRT显示区的下方(如图:2-3),各按键(旋钮)的名称及功能见表2-3。
数控车床对刀及建立工件坐标系的几种方法

数控车床对刀及建立工件坐标系的方法在数控车床上加工零件时,我们通常先开机回零,然后安装零件毛坯和刀具,接着要进行对刀和建立工件坐标系的操作,最后才是编制程序和自动加工。
对刀操作的正确与否,直接会影响后续的加工。
对刀有误的话,轻则影响零件的加工精度,重则会造成机床事故。
所以作为数控车床的操作者,首先要掌握对刀及工件坐标系的建立方法。
数控车床上的对刀方法有两种:试切法对刀和机外对刀仪对刀。
一般学校没有机外对刀仪这种设备,所以采用试切法对刀。
而根据实际需要,试切法对刀又可以采用三种形式,本文以华中数控HNC-21/T系统为例来阐述这三种形式的对刀及工件坐标系的建立方法。
一、T对刀T对刀的基本原理是:对于每一把刀,我们假设将刀尖移至工件右端面中心,记下此时的机床指令X、Z的位置,并将它们输入到刀偏表里该刀的X偏置和Z 偏置中。
以后数控系统在执行程序指令时,会将刀具的偏置值加到指令的X、Z 坐标中,从而保证所到达的位置正确。
其具体的操作如下:(1)开启机床,释放“急停”按钮,按“回零”,再按“+X”和“+Z”,执行回参考点操作。
(2)按“主轴正转”启动主轴,按“手动”,将刀具移动到合适的位置然后按“-Z”手动车削外圆,最后按“+Z”沿Z向退刀,如图1所示。
(3)按“主轴停止”停止主轴,然后测量试切部分的直径,测得直径为Φ69.934,按“F4(MDI)”,再按“F2(刀偏表)”,将光条移到1号刀的试切直径上,回车,输入69.934,再回车,1号刀的X偏置会自动计算出来,如图3所示。
图1 图2(4)移动刀具到合适的位置,按“主轴正转”启动主轴,按“手动”,然后按“-X”手动车削端面,最后按“+X”沿X向退刀,如图2所示。
(5)按“主轴停止”停止主轴,将光条移到1号刀的试切长度上,回车,输入0,再回车,1号刀的Z偏置会自动计算出来,如图3所示。
图32号刀的对刀过程与1号刀类似,只不过不能切端面。
具体如下:(1)按“刀位转换”将2号刀换到切削位置,按“主轴正转”启动主轴,按“手动”,将刀具移动到合适的位置然后按“-Z”手动车削外圆,最后按“+Z”沿Z向退刀,如图4所示。
数控车床加工之工件坐标系

数控车床加工之工件坐标系的研究摘要:数控机床加工时很少直接在机床坐标系中编程和加工,而是直接根据零件图进行编程。
为了简化工艺和编程选择合理的工件坐标系显得尤为重要。
本文以数控车床为例,谈一谈实际加工中工件坐标系的选择和建立。
关键词:数控机床加工合理工件坐标系试切对刀法数控机床加工时很少直接在机床坐标系中编程和加工,而是直接根据零件图进行编程。
因为编程人员在编程时,不知道工件在机床坐标系中装夹的确切位置,因而也就无法确定工件上各点在机床坐标系中的坐标,当然也就无法进行编程。
为了使编程人员不必考虑工件在机床上的实际位置而能够直接根据图纸进行编程,通常以工件上某一基准点为原点,设定一个与机床坐标系有一定关系的坐标系,这个坐标系即称为编程坐标系或工件坐标系,其原点即为编程原点或工件原点,工件坐标系各坐标轴都与机床坐标系各轴平行。
工件坐标系在数控机床上的位置与工件装夹位置有关,工件装夹位置不同,以工件上某一基准点为原点建立的工件坐标系在数控机床上的位置也不同,数控加工时需进行对刀操作确定工件坐标系在数控机床上的位置,同时把在机床坐标系下的加工转换为在工件坐标系下的加工,使编程与加工的坐标系统一起来。
一.工件坐标系原点的选择原则工件坐标系原点的选择非常重要。
工件坐标系原点应根据零件的形状和加王工艺选择,一般应遵循以下原则:(1)工件坐标系原点选择时应尽量与零件图样的设计基准或工艺基准重合。
(2)工件坐标系原点应尽量选在尺寸精度高、表面粗糙度值低的工件表面上。
(3)便于进行加工点坐标值的计算,并尽可能避免由此而产生的误差。
(4)在机床上容易确定工件坐标系在机床坐标系中的位置,并便于加工和测量检验。
根据上述原则,数控车床加工中一般将工件编程原点设定在零件右端面或左端面中心上,如图1-1所示。
二.工件坐标系的建立方法数控机床加工前通常要用对刀的方法建立工件坐标系,数控车床上常用的对刀方法有试切对刀法和对刀仪自动对刀法两种。
数控FANUC对刀方法及坐标系建立[1]
![数控FANUC对刀方法及坐标系建立[1]](https://img.taocdn.com/s3/m/7e8e647eaeaad1f346933fe8.png)
一、基本坐标关系一般来讲,通常使用的有两个坐标系:一个是机械坐标系;另外一个是工件坐标系,也叫做程序坐标系。
在机床的机械坐标系中设有一个固定的参考点(假设为(X,Z))。
这个参考点的作用主要是用来给机床本身一个定位。
因为每次开机后无论刀架停留在哪个位置,系统都把当前位置设定为(0,0),这样势必造成基准的不统一,所以每次开机的第一步操作为参考点回归(有的称为回零点),也就是通过确定(X,Z)来确定原点(0,0)。
为了计算和编程方便,我们通常将程序原点设定在工件右端面的回转中心上,尽量使编程基准与设计、装配基准重合。
机械坐标系是机床唯一的基准,所以必须要弄清楚程序原点在机械坐标系中的位置。
这通常在接下来的对刀过程中完成。
二、对刀方法1.试切法对刀试切法对刀是实际中应用的最多的一种对刀方法。
下面以采用MITSUBISHI 50L数控系统的RFCZ12车床为例,来介绍具体操作方法。
工件和刀具装夹完毕,驱动主轴旋转,移动刀架至工件试切一段外圆。
然后保持X坐标不变移动Z轴刀具离开工件,测量出该段外圆的直径。
将其输入到相应的刀具参数中的刀长中,系统会自动用刀具当前X坐标减去试切出的那段外圆直径,即得到工件坐标系X原点的位置。
再移动刀具试切工件一端端面,在相应刀具参数中的刀宽中输入Z0,系统会自动将此时刀具的Z坐标减去刚才输入的数值,即得工件坐标系Z原点的位置。
例如,2#刀刀架在X为150.0车出的外圆直径为25.0,那么使用该把刀具切削时的程序原点X值为150.0-25.0=125.0;刀架在Z为180.0时切的端面为0,那么使用该把刀具切削时的程序原点Z值为180.0-0=180.0。
分别将(125.0,180.0)存入到2#刀具参数刀长中的X与Z中,在程序中使用T02就可以成功建立出工件坐标系。
事实上,找工件原点在机械坐标系中的位置并不是求该点的实际位置,而是找刀尖点到达(0,0)时刀架的位置。
采用这种方法对刀一般不使用标准刀,在加工之前需要将所要用刀的刀具全部都对好。
数控编程与操作教案(机工版)——第二讲 数控编程基础
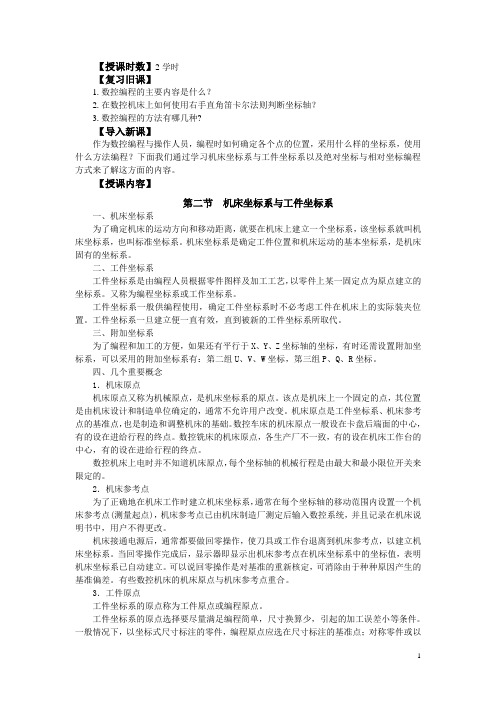
【授课时数】2学时【复习旧课】1.数控编程的主要内容是什么?2.在数控机床上如何使用右手直角笛卡尔法则判断坐标轴?3.数控编程的方法有哪几种?【导入新课】作为数控编程与操作人员,编程时如何确定各个点的位置,采用什么样的坐标系,使用什么方法编程?下面我们通过学习机床坐标系与工件坐标系以及绝对坐标与相对坐标编程方式来了解这方面的内容。
【授课内容】第二节机床坐标系与工件坐标系一、机床坐标系为了确定机床的运动方向和移动距离,就要在机床上建立一个坐标系,该坐标系就叫机床坐标系,也叫标准坐标系。
机床坐标系是确定工件位置和机床运动的基本坐标系,是机床固有的坐标系。
二、工件坐标系工件坐标系是由编程人员根据零件图样及加工工艺,以零件上某一固定点为原点建立的坐标系。
又称为编程坐标系或工作坐标系。
工件坐标系一般供编程使用,确定工件坐标系时不必考虑工件在机床上的实际装夹位置。
工件坐标系一旦建立便一直有效,直到被新的工件坐标系所取代。
三、附加坐标系为了编程和加工的方便,如果还有平行于X、Y、Z坐标轴的坐标,有时还需设置附加坐标系,可以采用的附加坐标系有:第二组U、V、W坐标,第三组P、Q、R坐标。
四、几个重要概念1.机床原点机床原点又称为机械原点,是机床坐标系的原点。
该点是机床上一个固定的点,其位置是由机床设计和制造单位确定的,通常不允许用户改变。
机床原点是工件坐标系、机床参考点的基准点,也是制造和调整机床的基础。
数控车床的机床原点一般设在卡盘后端面的中心,有的设在进给行程的终点。
数控铣床的机床原点,各生产厂不一致,有的设在机床工作台的中心,有的设在进给行程的终点。
数控机床上电时并不知道机床原点,每个坐标轴的机械行程是由最大和最小限位开关来限定的。
2.机床参考点为了正确地在机床工作时建立机床坐标系,通常在每个坐标轴的移动范围内设置一个机床参考点(测量起点),机床参考点已由机床制造厂测定后输入数控系统,并且记录在机床说明书中,用户不得更改。
详述数控铣床的对刀流程
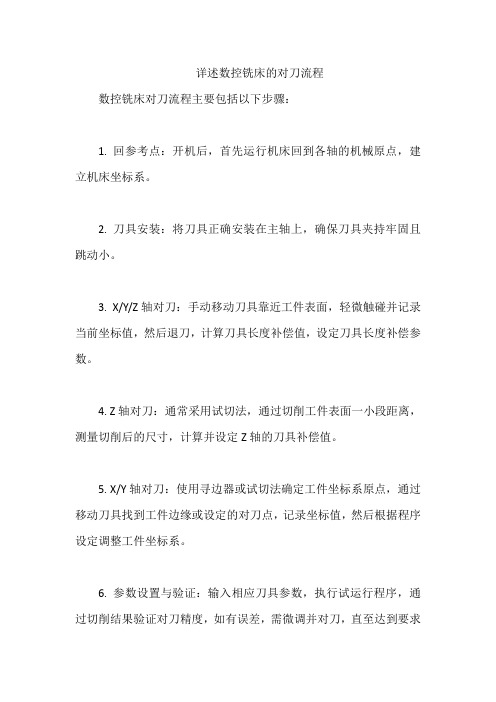
详述数控铣床的对刀流程
数控铣床对刀流程主要包括以下步骤:
1. 回参考点:开机后,首先运行机床回到各轴的机械原点,建立机床坐标系。
2. 刀具安装:将刀具正确安装在主轴上,确保刀具夹持牢固且跳动小。
3. X/Y/Z轴对刀:手动移动刀具靠近工件表面,轻微触碰并记录当前坐标值,然后退刀,计算刀具长度补偿值,设定刀具长度补偿参数。
4. Z轴对刀:通常采用试切法,通过切削工件表面一小段距离,测量切削后的尺寸,计算并设定Z轴的刀具补偿值。
5. X/Y轴对刀:使用寻边器或试切法确定工件坐标系原点,通过移动刀具找到工件边缘或设定的对刀点,记录坐标值,然后根据程序设定调整工件坐标系。
6. 参数设置与验证:输入相应刀具参数,执行试运行程序,通过切削结果验证对刀精度,如有误差,需微调并对刀,直至达到要求
精度。
机械制造与自动化专业《数控机床的坐标系和对刀》

数控机床的坐标系和对刀1.数控机床坐标系规定数控机床的坐标系及其运动方向,在国际标准中有统一规定。
标准的机床坐标系统一规定采用右手直角笛卡儿坐标系,如图5-9〔a〕所示。
图中大拇指的指向为X轴的正方向,食指指向为Y 轴的正方向,中指指向为Z轴的正方向。
围绕X、Y、Z轴旋转的圆周进给坐标轴分别用A、B、C表示,其正方向用右手螺旋法那么确定,以大拇指指向十X、十Y、十Z方向,那么食指、中指等的指向是圆周进给运动的+A、+B、+C,如图5-9〔c〕所示。
机床在加工过程中不管是刀具移动,还是被加工工件移动,都一律假定被加工工件相对静止不动,而刀具在移动,并规定刀具远离工件的运动方向为坐标轴的正方向。
图5-9 右手笛卡尔坐标系2.数控机床坐标系机床原点〔亦称为机床零点〕是机床上设置的一个固定的点,即机床坐标系的原点。
它在机床装配、调试时就已调整好,一般情况下不允许用户进行更改,因此它是一个固定点。
机床原点也是数控机床进行加工运动的基准参考点。
〔1〕数控车床的机床坐标系数控车床坐标系如图5-10所示,Z轴与车床导轨平行〔取卡盘中心线〕,正方向是远离车床卡盘的方向,X轴与Z轴垂直,平行于横向滑座,正方向是刀具远离主轴轴线的方向,坐标原点O 定在卡盘后端面与中心线交点处。
通常,当数控车床配置后置刀架时,其坐标系的表示形式如图5-11所示,机床原点为主轴轴线与主轴前端面的交点,如图5-11中的O点。
数控车床坐标系的原点也称机械原点。
从机床设计的角度来看,该点位置可任选,但从使用某一具体机床来看,这点却是机床上一个固定的点。
为了正确地建立机床坐标系,通常在每个坐标轴的移动范围内设置一个机床参考点作为测量起点,它是机床坐标系中一个固定不变的极限点,其固定位置由各轴向的机械挡块来确定。
一般数控机床开机后,通常要进行机动或手动回参考点以建立机床坐标系。
机床参考点可以与机床零点重合也可以不重合,通过参数指定机床参考点到机床零点的距离。
机床数控技术第3章数控加工程序的编制
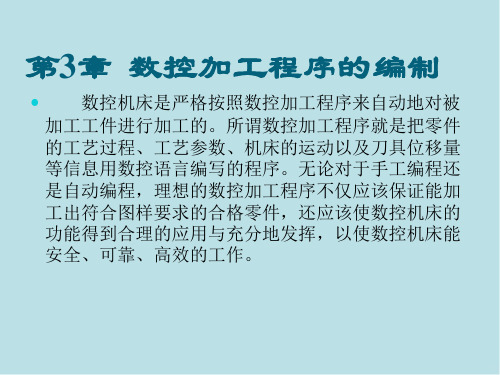
6. 程序校验和首件试切
程序送入数控系统后,通常需要经过试运行和首 件试切两步检查后,才能进行正式加工。通过试运行, 校对检查程序,也可利用数控机床的空运行功能进行 程序检验,检查机床的动作和运动轨迹的正确性。对 带有刀具轨迹动态模拟显示功能的数控机床可进行数 控模拟加工,以检查刀具轨迹是否正确;通过首件试 切可以检查其加工工艺及有关切削参数设定得是否合 理,加工精度能否满足零件图要求,加工工效如何, 以便进一步改进,直到加工出满意的零件为止。
1—脚踏开关 2—主轴卡盘 3—主轴箱 4—机床防护门 5—数控装置 6—对刀仪 7—刀具8—编程与操作面板 9—回转刀架 10—尾座 11—床身
3.2 数控车削加工程序编制
数控车床主要用来加工轴类零件的内外圆柱面、 圆锥面、螺纹表面、成形回转体表面等。对于盘类零 件可进行钻、扩、铰、镗孔等加工。数控车床还可以 完成车端面、切槽等加工。
3. 程序名
FANUC数控系统要求每个程序有一个程序名,
程序名由字母O开头和4位数字组成。如O0001、 O1000、O9999等
3.2.3 基本编程指令
1. 快速定位指令G00
格式:G00 X(U)_ Z(W)_;
说明:
(1) G00指令使刀具在点位控制方式下从当前点以快移速度 向目标点移动,G00可以简写成G0。绝对坐标X、Z和其增 量坐标U、W可以混编。不运动的坐标可以省略。
3.2.1 数控车床的编程特点
(1)在一个程序段中,可以用绝对坐标编程,也可用 增量坐标编程或二者混合编程。
(2)由于被加工零件的径向尺寸在图样上和在测量时 都以直径值表示,所以直径方向用绝对坐标(X)编程时 以直径值表示,用增量坐标(U)编程时以径向实际位移 量的2倍值表示,并附上方向符号。
数控机床操作指导
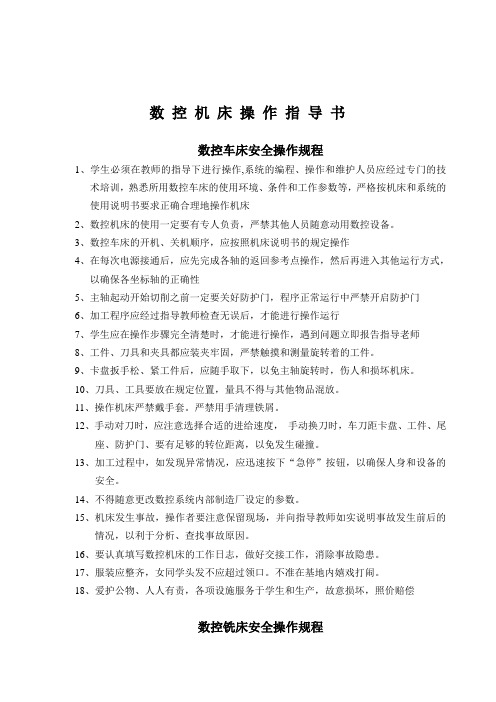
数控机床操作指导书数控车床安全操作规程1、学生必须在教师的指导下进行操作,系统的编程、操作和维护人员应经过专门的技术培训,熟悉所用数控车床的使用环境、条件和工作参数等,严格按机床和系统的使用说明书要求正确合理地操作机床2、数控机床的使用一定要有专人负责,严禁其他人员随意动用数控设备。
3、数控车床的开机、关机顺序,应按照机床说明书的规定操作4、在每次电源接通后,应先完成各轴的返回参考点操作,然后再进入其他运行方式,以确保各坐标轴的正确性5、主轴起动开始切削之前一定要关好防护门,程序正常运行中严禁开启防护门6、加工程序应经过指导教师检查无误后,才能进行操作运行7、学生应在操作步骤完全清楚时,才能进行操作,遇到问题立即报告指导老师8、工件、刀具和夹具都应装夹牢固,严禁触摸和测量旋转着的工件。
9、卡盘扳手松、紧工件后,应随手取下,以免主轴旋转时,伤人和损坏机床。
10、刀具、工具要放在规定位置,量具不得与其他物品混放。
11、操作机床严禁戴手套。
严禁用手清理铁屑。
12、手动对刀时,应注意选择合适的进给速度,手动换刀时,车刀距卡盘、工件、尾座、防护门、要有足够的转位距离,以免发生碰撞。
13、加工过程中,如发现异常情况,应迅速按下“急停”按钮,以确保人身和设备的安全。
14、不得随意更改数控系统内部制造厂设定的参数。
15、机床发生事故,操作者要注意保留现场,并向指导教师如实说明事故发生前后的情况,以利于分析、查找事故原因。
16、要认真填写数控机床的工作日志,做好交接工作,消除事故隐患。
17、服装应整齐,女同学头发不应超过领口。
不准在基地内嬉戏打闹。
18、爱护公物、人人有责,各项设施服务于学生和生产,故意损坏,照价赔偿数控铣床安全操作规程1、学生必须在教师指导下,按照操作步骤进行数控机床操作,熟悉所用数控铣床的使用环境、条件和工作参数等,严格按机床和系统的使用说明书要求正确合理地操作机床2、禁止多人同时操作,强调单人单机操作。
数控加工中工件坐标系的建立及其对刀技巧

图 4 工件坐标选择例图 Fig14 Graphic example of choosing workpiece cartesian
coordinates
5 结语 G92 指令和 G54~ G59 指令都能达到建立工件
坐标的目的 ,但使用方法有区别 : G92 指令对刀时 , G92 后面的坐标值一旦设定 ,
床坐标系 ,加工前必须通过对刀把它们统一起来 。通过 G92 和 G54~ G59 2 种指令 ,详细分析了建
பைடு நூலகம்
立工件坐标系的基本原理及对刀技巧 。
关键词 : 机床坐标系 ; 工件坐标系 ; G92 指令 ; G54~G59 指令
中图号 : TH161
文献标识码 : A
1 工件坐标系和机床坐标系 数控加工中必定会遇到 2 个坐标系 : (1) 编程时
3 G92 的编程格式及对刀方法 (1) 编程格式 G92 指令通过设定刀具起点 (对刀点) 相对于工
件坐标原点的相对位置建立工件坐标系 。此坐标系 一旦建立起来 ,后边的绝对值指令都是此工件坐标 系中的坐标值 ,如图 1 所示 。G92 的编程格式如下 :
G92 X - Y - Z - A - B - C - U - V - W 其中 X 、Y 、Z 、A 、B 、C 、U 、V 、W 为工件坐标原点到 刀具起点的有向距离[2] 。
XE = XW + 70 = - 50 - 30 + 70 = - 10
ZE = ZW + 30 = - 100. 5 + 30 = - 70. 5 计算好了起刀点 E 的机床坐标值后 ,就可以用 手动方式将刀尖精确地运动到起刀点上 。 4 G54~ G59 的编程格式和对刀方法[4] (1) 编程格式 G54~G59 同样是工件坐标系设定指令 ,也即是 把机床参考点坐标系与机床坐标系联系起来的指 令 。其编程格式如下 : G54 G55 G56 G57 G58 G59
数控铣床工件坐标系的建立及对刀操作

详细描述:在批量生产中,为了提高生产效率和降低成本,可以采用优化策略,如使用快速定位和高 效切削参数。同时,通过对刀操作优化,可以减少调整时间和提高加工精度,进一步增强生产效益。
感谢您的观看
THANKS
重要性
工件坐标系是加工过程中进行编程、 加工和检测的基础,正确的建立工件 坐标系是保证加工精度和质量的必要 条件。
坐标系的分类与选择
分类
绝对坐标系和相对坐标系。
选择
根据工件的特点和加工要求选择合适的坐标系,一般优先选择机床的固有坐标 系。
坐标系的原点与轴向
原点
工件坐标系的原点是用来确定工件几 何形状在机床上的位置的基准点。
如果发现工件坐标系存在误差, 需要进行修正操作,调整工件原 点的位置或坐标轴的方向。
将验证和修正结果记录在案,并 在需要时更新数控铣床控制系统 的数据。
03
对刀操作的基本步骤
确定对刀点
确定对刀点
在工件上选择一个固定的点作为 对刀点,通常选择工件的中心点 或某一角点。
对刀点的作用
对刀点是工件坐标系的原点,用 于建立工件坐标系,并确定工件 在机床坐标系中的位置。
轴向
工件坐标系的轴向是根据加工要求和 工件特点确定的,一般遵循右手笛卡 尔坐标系原则。
02
工件坐标系的建立方法
手动建立工件坐标系
01
02
03
确定工件原点
根据工件的设计或工艺要 求,选择一个基准点作为 工件原点。
输入坐标值
在数控铣床的控制系统上 输入工件原点的坐标值。
验证坐标系
通过试切或测量等方法验 证工件坐标系的准确性。
对刀误差的补偿方法
软件补偿
数控车床对刀与坐标系

反之 呢?
误差分析
读数偏小,则偏置 量绝对值变小,零 点向X正向移动, X向尺寸偏大
案例分析
车Φ28外圆,不考虑程序及 机床随即和系统误差,若测 得外圆Φ28.2,你会怎么调 整?
左端倒角及切断
编程作业
编程练习,注意粗精加工,毛坯Φ30, S≤700;F≤100MM/MIN
小结
三句话 两个图 你理解了吗?
程序零点(0,0)
机床坐标(-200,300)
(100,100) (35,5) (26,5)
(-100,-200) (-165,-295) (-174,-295)
若仿真时没有对刀:转换基准(0,0)——(0,0) 数控系统:机床原点就是程序零点, 导轨出现在机床原点(参考点)附近 实际加工时往往出现超程报警,你知道为什么吗? 工件位置与之前对刀不一致直接加工,会产生什 么情况?
数控车床坐标系与对刀
三句话 两个图
机床坐标系与编程坐标系
坐标系
原点
坐标轴
机床坐标系 坐标轴正 X,Z 向极限
建立
回零
作用
加工
编程坐标系 工件右端 X,Z 编程员设置 编程 面中心
数控加工时,系统需要知道编程坐标原点在机床坐标系 中的位置,通过对刀找到并设置在对应的刀偏表中
坐标系
1.P11理解
(1)机床坐标系是固定的,回零建立 机床原点、参考点的相对位置关系 (2)工件坐标系(编程坐标系) 编程人员在工件上确定的,便于计算和编程 (3)数控机床本质控制的是机床坐标,加工
关于对刀
1.试切外圆后,+Z方向退刀,测得试切直 径Φ28.5,当前机床坐标值为-220,请问刀 偏表中X向刀偏置为多少?
数控机床工件坐标系的设定与对刀方法

数控机床工件坐标系的设定与对刀方法2006年第2期第27卷总第456期职业技术教育(教学版)VOC棚0NALANDTECHN1CALEDUCATION(TeachingResearch)No.2,2006V01.27GeneralNo.456数控机床工件坐标系的设定与对刀方法刘兴良(西安航空技术高等专科学校,陕西西安710077)摘要:数控机床加工时,对刀及工件坐标系的设定是一项重要工作.本文基于数控机床的加工原理以及数控机床编程与操作实践经验,提出数控机床加工时工件坐标系的设定和与之对应的对刀方法.关键词:机床坐标系;工件坐标系;偏置补偿值;对刀;刀位点中图分类号:TG659文献标识码:A文章编号:1008—3219(2006)02—0066—02一,数控机床的加工原理数控机床进行加工时,刀具到达的位置的机械坐标值必须传递给CNC系统,然后由CNC系统发出信号并使刀具移动到这个位置.通常刀具到达的位置各坐标轴的机械坐标值,是工件坐标系原点在机床坐标系中各坐标轴上的机械坐标值+刀具在各坐标轴上的偏置补偿值+刀具在各坐标轴上磨损补偿值+程序指令的刀具在工件坐标系中的各坐标轴上的指令值.上述运算是由数控系统的内部源程序来实现的,但是加工前,操作人员必须把工件坐标系原点在机械坐标系中的位置坐标告诉数控系统,同时通过对刀确定各把刀具在各坐标轴上的偏置补偿值.二,数控车床工件坐标系设定与对刀方法第一种方法:程序中没有工件坐标系的设定指令.这种方法通过把刀架上的每把刀具的刀尖与工件坐标系的原点重合.如果实际上不能重合,可以通过计算确定他们重合时刀具在机械坐标系中各坐标轴上的机械坐标值,作为各把刀具在各坐标轴上的偏置补偿值.例如,工件坐标系的原点在卡盘前端面与工件轴线的交点上,对刀时,刀尖不能与工件坐标系的原点重合.此时,在手动或增量方式下,轻车工件前端外圆柱面长5ram,保持X向不动,沿+Z方向退刀,然后停止主轴旋转,测量轻车过的外圆柱面直径(一般采用直径编程方法).因为刀尖向工件中心移动时沿x的负方向移动,所以x机械坐标值减小.因此,用当前位置时的x向的机械坐标值减去测最到的工件直径值,结果就是这把刀x向的偏置补偿值. 对于z向的偏置补偿值的获得,用该把刀轻车工件端面,刀保持z向不动,沿+x方向退刀后,停止主轴旋转,测量轻车的端面至工件坐标系原点的轴向长度,然后用当前的z机械坐标值减去这个距离值,所得到的结果就是该把刀的z向的偏置补偿值.这种方法适用于华中世纪星数控系统与西门子802S/802D数控系统的车床.只要在一个合适的界面中输入试切直径和长度,由系统源程序自动完成计算,自动给x向和z向输入偏置值.对于FANUC系统,需要操作者计算完后,输入相应的刀具补偿号下,具体操作为:按压OFFSET(键)一补正(软键)一形状(软键),然后移动光标至该把刀具相应补偿号后.输入X向和z向偏置值.上述方法操作简单,可靠性好.通过刀具偏置值与机械坐标系紧密地联系在一起,代表了加工原理中工件坐标系原点在机械坐标系中的位置的机械坐标值+各把刀具的补偿值.只要不断电,不改变刀偏值,工件坐标系就会存在且不会改变.即使断电重新启动回参考点之后,工件坐标系还在原来位置.使用此方法,在程序开始时使用TO101就可以成功建立TO1号刀具的工件坐标系.各把刀确定各自工件坐标系原点,是靠调用刀具补偿号来实现的.编程时,在刀具运动之前,应有带有该把刀刀具补偿的换刀指令的执行.例如,T0101,开始加工前或中途换刀,应将刀架移到一个合适的位置,避免刀架转位时与其他零部件发生碰撞.第二种方法;程序开头用G50,zB(,B为收稿日期:2005—11-02作者简介:刘兴良(1969一),男,西安航空技术高等专科学校机械系讲师,研究方向:数控加工,数控原理.两个数值)设定工件坐标系(有的数控系统使用G92指令)x,zB的位置才能加工.对刀时先对基准刀,使基准刀的刀尖移到一个空间固定点,把此时刀具的所在位置设定为相对坐标系的零点. 然后,把其他刀具的刀尖移到该固定空间点.此时显示的相对坐标值就为该把刀相对于基准刀在x向z向的补偿值,把该值输入该把刀的补偿号中.例如,如果该空间固定点在卡盘前端面与工件轴线的交点,基准刀与其他刀具的刀尖不能移动到该固定空间点,则首先推算基准刀刀尖移动到空间固定点时刀具在机械坐标系中各坐标轴上的位置坐标,这个坐标值即为基准坐标值,然后推算其他刀具的刀尖运动到该固定空间点时,刀具在机械坐标系中各坐标轴上的坐标值,再用其他刀具运动到固定空间点时各坐标轴上的机械坐标值减去基准刀具运动到固定空间点时刀具在坐标轴上机械坐标值,结果即为该把刀相对于基准刀在各坐标轴方向上的补偿值.送入该把刀的补偿号下即可,而基准刀的补偿为零.采用这种方法,如果关机或断电后重新启动,建立的工件坐标系将丢失,重新开机后必须再对刀建立工件坐标系.在重复加工中,一个工件加工后,应让基准刀回到xB位置处,这样下一次加工时不需要对刀.第三种方法:CRT/MDI参数设定方式,运用G54一G59可以设定6个坐标系.这种工件坐标系的原点相对于机床参考点是不变的,与刀具无关.使用这种方法设置工件坐标系时,只是把基准刀的刀尖移动到与工件坐标系的原点重合时(如果不能重合,推算出理论重合时的刀具在各坐标轴的机械坐标值)刀具在各坐标轴上的机械坐标值记录下来,加工前送入G54一G59程序中使用的那个坐标系设定指令下的(x一,z一)寄存器中.对于基准刀,x,z向补偿值为O,其他刀相对于基准刀具的补偿值的获得原理与上面第二种方法中的相同.用这种方法设置的工件坐标系,对于加工前刀具所处的位置没有要求,对于加工完后刀具所处的位置也没有要求.机床断电重新开机.返回机床参考点后,原来建立的工件坐标系仍然有效.这种方法适用于批量生产,且工件在机床上有固定装夹位置的加工.三,数控铣床(加工中心)工件坐标系的设定与对刀方法第一种方法:在程序开头用G92XotY[3Z7来设定工件坐标系,(et.p.)为基准刀在设定的工件坐标系中的位置坐标.因此,加工开始前,必须把基准刀的刀位点(程序控制刀具运动的点)移到工件坐标系中(ot.p.)处,而基准刀的补偿值为O.加工前,要确定其他刀具相对予基准刀的长度补偿值.方法:把基准刀移动到与工件上表面接触.设置此位置为相对坐标系的原点,然后也把其他刀具移动到与工件上表面接触,看此时z的相对坐标值就是其他刀具相对于标准刀的长度补偿值, 把此值送到每把刀的长度补偿号中即可.对于半径补偿,对于具体刀具,具体加工,运用相应的补偿值即可.用G92设置的工件坐标系在断电后丢失,重新启动后,必须重新对刀.重复加工中,刀具的起始点与终结点应相同,避免下次加工乱刀.第二种方法:用CRT/MDI参数设定方式,运用G54一G59可以设置6个工件坐标系.使用这种方法时,必须通过人工计算,确定工件坐标系原点在机床机械坐标系中的位置坐标值,但数控机床的显示屏上显示的为刀具中心在机床机械坐标系中的坐标,推算时要考虑刀具刀位点移向工件坐标系原点时刀具沿机床各坐标轴的方向和距离.送入G54一G59程序中使用的,如G54下的x一,Y一,z一对于z后数值的确定,可以使用一把基准刀,让基准刀的刀尖移到工件坐标系z坐标轴的原点,一般在工件表面,并把此位置设置为相对坐标系原点,把此时Z机械坐标值送入G54下的z寄存器中,然后换装上其他刀具,也移动到工件座标系z轴的原点上,此时显示的相对坐标系中的z值,即为该把刀的长度补偿值,送入对应的补偿号中即可.OnInstallingofCoordinateSystemofWorkpiecesof NumericallyControlledMachineandToolsettingMethodsLiuXingliang(XianAerotechnicalCollege,XianShanxi710077,China)Abstract:Toolsettingandinstallingofcoordinatesystemofworkpiecesareimportanttasksw hilemachiningnu—mericallycontroHedmachines.AccordingtOtheprocessingprincipleofnumericallycontro lledmachinesandthe practicalexperienceoftheirprogrammeandoperation,theauthorputsforwardmethodsofins tallingcoordinate systemsofnumericallycontrolledmachinesworkpiecesandtoolaetting.Keywords:coordinatesystemofmachines;coordinatesystemofworkpieces;toolsetting 67。
数控铣床对刀的原理及方法步骤【附案例】
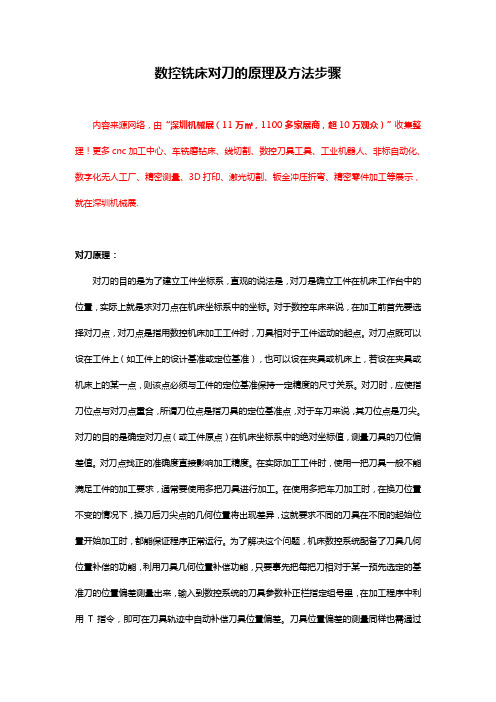
数控铣床对刀的原理及方法步骤内容来源网络,由“深圳机械展(11万㎡,1100多家展商,超10万观众)”收集整理!更多cnc加工中心、车铣磨钻床、线切割、数控刀具工具、工业机器人、非标自动化、数字化无人工厂、精密测量、3D打印、激光切割、钣金冲压折弯、精密零件加工等展示,就在深圳机械展.对刀原理:对刀的目的是为了建立工件坐标系,直观的说法是,对刀是确立工件在机床工作台中的位置,实际上就是求对刀点在机床坐标系中的坐标。
对于数控车床来说,在加工前首先要选择对刀点,对刀点是指用数控机床加工工件时,刀具相对于工件运动的起点。
对刀点既可以设在工件上(如工件上的设计基准或定位基准),也可以设在夹具或机床上,若设在夹具或机床上的某一点,则该点必须与工件的定位基准保持一定精度的尺寸关系。
对刀时,应使指刀位点与对刀点重合,所谓刀位点是指刀具的定位基准点,对于车刀来说,其刀位点是刀尖。
对刀的目的是确定对刀点(或工件原点)在机床坐标系中的绝对坐标值,测量刀具的刀位偏差值。
对刀点找正的准确度直接影响加工精度。
在实际加工工件时,使用一把刀具一般不能满足工件的加工要求,通常要使用多把刀具进行加工。
在使用多把车刀加工时,在换刀位置不变的情况下,换刀后刀尖点的几何位置将出现差异,这就要求不同的刀具在不同的起始位置开始加工时,都能保证程序正常运行。
为了解决这个问题,机床数控系统配备了刀具几何位置补偿的功能,利用刀具几何位置补偿功能,只要事先把每把刀相对于某一预先选定的基准刀的位置偏差测量出来,输入到数控系统的刀具参数补正栏指定组号里,在加工程序中利用T指令,即可在刀具轨迹中自动补偿刀具位置偏差。
刀具位置偏差的测量同样也需通过对刀操作来实现。
对刀方法:在数控加工中,对刀的基本方法有试切法、对刀仪对刀和自动对刀等。
本文以数控铣床为例,介绍几种常用的对刀方法。
1、试切对刀法:这种方法简单方便,但会在工件表面留下切削痕迹,且对刀精度较低。
6-数控铣削加工坐标系建立

• 5.机床加工坐标系设定的实例 • 下面以数控铣床(控制系统为FANUC 0M)加工坐标系
Hale Waihona Puke • 通常在数控铣床上机床原点和机床参考点是重合的;而 在数控车床上机床参考点是离机床原点最远的极限点。
• 2.编程原点
• 编程坐标系是编程人员根据零件图样及加工工艺等建立 的坐标系。编程坐标系一般供编程使用,确定编程坐标 系时,不必考虑工件毛坯在机床上的实际装夹位置。
• 为了编程方便,需要在图纸上选择一个适当的位置作为 编程原点,即程序原点或程序零点。对于简单零件,工 件零点一般就是编程原点,这时的编程坐标系就是工件 坐标系。而对于形状复杂的零件,需要编制几个程序或 子程序。为了编程方便和减少坐标值的计算,编程原点 就不一定设在工件零点上,而设在便于程序编制的位置。
• 这说明在设定了G54加工坐标系后,机床原点在加工坐 标系中的位置为:X=+392.626,Y=+246.460, Z=+32.033。这反过来也说明G54的设定值是正确的。
/*将程序原点定义在第二个零件上的工件原点
• ……
/*加工第二个零件
• N12 G00X0Y0
/*快速回程序原点
• 这里应注意比较G92与G54到G59指令之间的差别和不同的使用方法。G92指令须 后续坐标值指定当前工件坐标值,因此须单独一个程序段指定,尽管该程序段中有 位置指令值,但并不产生运动。另外,在使用G92指令前,必须保证机床处于加工 起始点,该点称为对刀点。
- 1、下载文档前请自行甄别文档内容的完整性,平台不提供额外的编辑、内容补充、找答案等附加服务。
- 2、"仅部分预览"的文档,不可在线预览部分如存在完整性等问题,可反馈申请退款(可完整预览的文档不适用该条件!)。
- 3、如文档侵犯您的权益,请联系客服反馈,我们会尽快为您处理(人工客服工作时间:9:00-18:30)。
• Y坐标设定值:Y= Y=Y1+Φ/2+δ+Y0 =-298.160+5+0.1+46.5= -246.46mm。
注:如图3所示,-298.160mm为坐标显示值;+5mm为测量 棒半径值;+0.1mm为塞尺厚度;+46.5为编程原点到工件 定位基准面在Y坐标方向的距离。
• 试切对刀步骤: 1.确定编程原点; 2.主轴正转; 3.移动刀具试切右端面;记录下当前位置的机床坐标值
Z-200; 4.试切外圆,记录下当前位置的机床坐标值X-70,沿Z向退
刀,主轴停,测量被试切的工件直径为60mm。
程序头用G54建立工件坐标系,如何设置?
• 进入G54界面,输入编程原点的机床坐标值: X-130, Z-200。
X= -(130-80)= -50,Z= -(200-100)= -100。
3.若加工前机床回零,程序用G50 X? Z?建立工件坐标系?
答:G50 X130 Z200;即参考点作为起刀点在(130,200)处。
数控车床上用G54设置工件坐标系
• 例如:在华中系统数控车床上用G54设置加工原点。
• 回参考点的操作(“回零”操作),也就是使刀具或工作台退回到机 床参考点。此时,机床显示器上将显示出机床参考点在机床坐标系中 的坐标值,就相当于在数控系统内部建立了一个以机床原点为坐标原 点中的,机用床户坐无标权系修。改如。上图所示,XR,ZR,该坐标值已存入数控系统
• 只有机床参考点被确认后,机床原点才被确认,刀具(或工作台)移 动才有基准。
• 将前面已测得的各项数据,按设定要求运算。 • X坐标设定值:X= X1+Φ/2+δ+X0
= - 437.726+5+0.1+40= -392.626mm。 注: - 437.726mm为X坐标显示值;
+5mm为测量棒半径值; +0.1mm为塞尺厚度; +40.0为编程原点到工件定位基准面在X坐标方向的距离。
• 练习:对刀过程如图所示:
1.计算出O1点的机床坐标? 答:X=-312.9-60=-372.9, Z=-130.123 2.若程序用G50 X80 Z100建立工件坐标系,如何操作? 答:MDI方式运动到机床坐标系X-292.9 Z-30.123处
3.若加工前机床回零,程序用G50 X? Z?建立工件坐标系? 答:G50 X372.9 Z130.123
• ②Y坐标设定值: Y=Y1+Φ/2+δ+Y0
注:如图3所示,Y1为坐标显示值,为负值; Φ/2为测量棒半径值; δ为塞尺厚度; Y0为编程原点到工件定位基准面在y坐标方向的距离,图2
中Y 0=46.5 mm。
• ③Z坐标设定值: Z=Z1—δ
注:Z1为坐标显示值,为负值; δ为塞尺厚度,如图4所示。
• 机床原点
机床原点,各个生产厂家不一致
机床原点(M)是指在机床上设置的一个固定点,即机床坐 标系的原点。它在机床装配、调试时就已确定下来,是数控机 床进行加工运动的基准参考点。
在数控车床上,机床 原点一般取在卡盘后端 面与主轴中心线的交点 处,同时,通过设置参 数的方法,也可将机床 原点设定在X、Z坐标的 正方向极限位置上。
X1 = - 437.726, Y1 = -298.160,如下图所示。 Z1 = -31.833,如图3、4所示。
• (4)计算设定值 按图3所示,将前面已测得的各项数据,按设定要求运算。 ①X坐标设定值: X=X1+Φ/2+δ+X0 注:X1为x坐标方向的显示值,为负值;
Φ/2为测量棒半径值; δ为塞尺厚度; X0为编程原点到工件定位基准面在x坐标方向的距离, 图2中X0=40 mm。
在数控车床上,机床原点一般取在卡盘后端面与主 轴中心线的交点处,同时,通过设置参数的方法,也可 将机床原点设定在X、Z坐标的正方向极限位置上。
一、数控车床通过试切对刀设置加工原点(工件坐标系原点)
• 数控机床开机时,必须先确定机床原点,而确定机床原点 的运动就是回参考点的操作(“回零”操作),此时,显ห้องสมุดไป่ตู้示屏上显示参考点在机床坐标系中的坐标为(0,0,0)。 这样通过确认参考点,就确定了机床原点。
• 数控铣床(如FANUC 0M)加工原点的设定步骤:
在选择了下图所示的被加工零件图样,并确定了编程原点位 置后,可按以下方法进行加工坐标系设定: (1)准备工作
机床回参考点,确认机床坐标系; (2)装夹工件毛坯
通过夹具使零件定位,并使工件定位基准面与机床运动方向一致;
(3)对刀测量 用简易对刀法测量,方法如下: • 用直径为φ10的标准测量棒、塞尺对刀,得到测量值为
• 在数控铣床上机床原点一般取在X、Y、Z坐标的正方向 极限位置上。
机床参考点
• 机床参考点:用于对机床运动进行检测和控制的固定位置 点。其位置是由机床制造厂家在每个进给轴上用限位开关 精确调整好的,坐标值已输入数控系统中,用户无权修改。 因此参考点对机床原点的坐标是一个已知数。
• 通常在数控车床上机床参考点(R)是离机床原点最远的 极限点。而数控铣床上机床原点和机床参考点是重合的。
4.程序头用G54建立工件坐标系,如何设置?
答:进入G54界面,输入编程原点的机床坐标值: X-372.9 Z-130.123。
二、数控铣床通过试切对刀设置加工原点(工件坐标系原点)
• 在数控铣床上机床原点一般取在X、Y、Z坐标的正方 向极限位置上。
• 通常数控铣床上机床原点和机床参考点是重合的。
数控车床试切对刀设置加工原点
• 试切对刀步骤: 1.确定编程原点; 2.主轴正转; 3.移动刀具试切右端面;记录下当前位置的机床坐标值 Z-200; 4.试切外圆,记录下当前位置的机床坐标值X-70,沿Z向 退刀,主轴停,测量试切直径为60mm。
1.计算出O1点的机床坐标(即O1相对于参考点),为: 答: X=-70-60=-130, Z=-200。
2.程序头用G50 X80 Z100建立工件坐标系即起刀点为(80,100),如 何操作?
这个起刀点是相 对于工件坐标系 的坐标值
答: MDI方式运动到机床坐标系X-50,Z-100处。试切后,工件坐标系 原点01相对于参考点的坐标已知道(-130,-200),要将起刀点的位 置折算为起刀点相对于参考点的位置,计算过程: