塑料件的设计指南
塑胶件设计指南之简洁优美版

塑胶件设计指南之简洁优美版关注上方公众号“降本设计”,获取更多原创产品设计知识!均匀壁厚均匀壁厚,这是塑胶件设计最重要的原则。
避免壁厚急剧变化,保证平滑过渡。
局部过厚处掏空并使用加强筋补强局部过厚的区域会导致塑胶件发生缩水和翘曲等缺陷,需要进行掏空的设计,并使用加强筋补强。
避免尖角塑胶件的任意部位(分模线处除外)都需要避免尖角。
加强筋的设计加强筋常用于提高塑胶件的强度,其厚度一般在壁厚的0.5~0.7倍,加强筋厚度过厚会造成缩水,高度一般在壁厚的3倍以下。
脱模斜度在可能的情况下,设计至少2度的脱模斜度,特征高度越高,脱模斜度越大。
支柱当塑胶件需要使用螺纹连接时,推荐使用自攻螺丝,并在塑胶件上设计支柱。
不推荐螺牙注塑成型,这是因为直接成型的螺牙会在脱模时造成倒扣;也不推荐在塑胶件上直接攻牙,因为二次加工成本高。
螺纹嵌件当需要反复的拆卸时,可以使用螺纹嵌件。
螺纹嵌件可以通过热熔、超声波和模内注塑等方式加工。
卡扣紧固卡扣是最简单、最经济以及最快速的塑胶件紧固工艺。
干涉筋干涉筋是指塑胶件上的局部凸起特征,当其它零件例如轴承等装配到塑胶件之中时,干涉筋因为受力变形而把轴承卡紧。
干涉筋是轴、轴承类零件进行紧配合时常用的一种方法。
干涉量为0.25mm,干涉筋不必添加脱模斜度。
活铰链活铰链是塑胶件上较薄较有弹性的一部分,把一个塑胶件的两部分较硬实体连接为一个整体,并允许两部分实体绕着活动铰链旋转一定角度甚至180度以上。
倒扣尽量避免倒扣,倒扣会增加模具复杂度和模具成本。
强脱当塑料具有足够的弹性时,可以使用强脱。
强脱常用于加工杯盖中的螺纹。
避免对玻纤增强塑料使用强脱。
一般来说,PP、HDPE和PA可以承受直径大小5%的强脱。
滑块当塑胶件中存在倒扣时,由于美观或技术的原因,必须使用侧向的抽芯机构即滑块。
在塑胶件设计时,需要为滑块的运动提供预留空间;另外,滑块的运动方向应当与开模方向垂直,非垂直方向会使得模具复杂。
一些降本建议o避免倒扣。
塑料件的设计规范
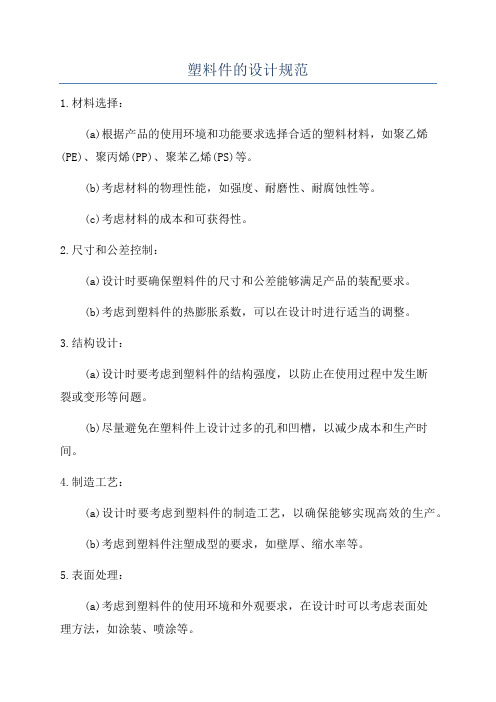
塑料件的设计规范1.材料选择:(a)根据产品的使用环境和功能要求选择合适的塑料材料,如聚乙烯(PE)、聚丙烯(PP)、聚苯乙烯(PS)等。
(b)考虑材料的物理性能,如强度、耐磨性、耐腐蚀性等。
(c)考虑材料的成本和可获得性。
2.尺寸和公差控制:(a)设计时要确保塑料件的尺寸和公差能够满足产品的装配要求。
(b)考虑到塑料件的热膨胀系数,可以在设计时进行适当的调整。
3.结构设计:(a)设计时要考虑到塑料件的结构强度,以防止在使用过程中发生断裂或变形等问题。
(b)尽量避免在塑料件上设计过多的孔和凹槽,以减少成本和生产时间。
4.制造工艺:(a)设计时要考虑到塑料件的制造工艺,以确保能够实现高效的生产。
(b)考虑到塑料件注塑成型的要求,如壁厚、缩水率等。
5.表面处理:(a)考虑到塑料件的使用环境和外观要求,在设计时可以考虑表面处理方法,如涂装、喷涂等。
(b)考虑到塑料件的耐候性,可以选择添加防紫外线(UV)剂。
6.排气和冷却:(a)设计时要确保塑料件的排气和冷却能够满足注塑成型的要求,以避免缺陷的产生。
(b)考虑到塑料件的形状和厚度变化,可以适当设计出气道和冷却系统。
7.注塑模具设计:(a)考虑到塑料件的形状、尺寸和结构,设计合适的注塑模具,以确保能够生产出符合要求的塑料件。
(b)考虑到模具的制造成本和使用寿命,可以合理选择模具材料和加工工艺。
总而言之,塑料件的设计规范是为了确保产品质量和生产效率,在材料选择、尺寸和公差控制、结构设计、制造工艺、表面处理、排气和冷却、注塑模具设计等方面提供了一些指导和标准。
通过遵守这些规范,设计师可以设计出高质量的塑料件,从而满足客户的需求。
塑胶设计指南
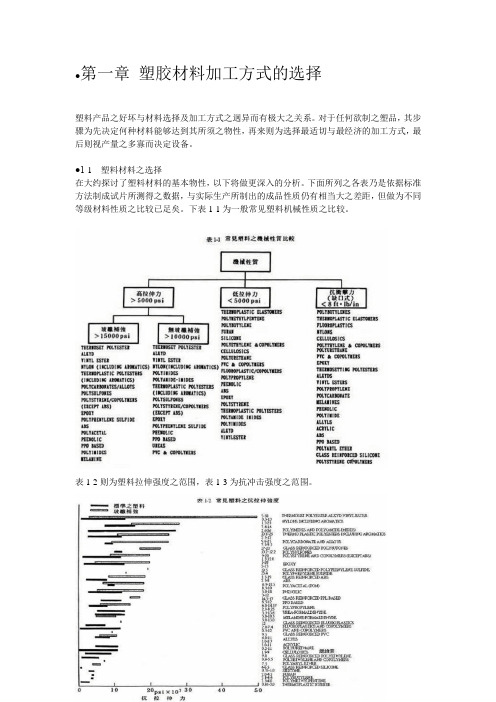
●第一章塑胶材料加工方式的选择塑料产品之好坏与材料选择及加工方式之迥异而有极大之关系。
对于任何欲制之塑品,其步骤为先决定何种材料能够达到其所须之物性,再来则为选择最适切与最经济的加工方式,最后则视产量之多寡而决定设备。
●1-1塑料材料之选择在大约探讨了塑料材料的基本物性,以下将做更深入的分析。
下面所列之各表乃是依据标准方法制成试片所测得之数据,与实际生产所制出的成品性质仍有相当大之差距,但做为不同等级材料性质之比较已足矣。
下表1-1为一般常见塑料机械性质之比较。
表1-2则为塑料拉伸强度之范围,表1-3为抗冲击强度之范围。
表1-4及表1-5,则为塑料之其它性质。
参考以上各表,即大约可知塑品用何种材料可达到其用途之所须性质要求。
一般而言加了玻纤后,可增加拉伸力、减少拉伸量、抗磨耗力降低、挠曲力增高、热变形温度增加、热膨胀降低及较不透明,而耐冲击力则不一定。
但是硬度(除非高填充)、电气性质、抗化学性及抗天候性则甚无影响。
表1-6则为一般材料之机械性质之定性趋势表。
若是依各种用途来分,所使用之塑料大概可列表如1-7所示。
●1-2塑料加工方式之选择塑料之加工方式五花八门,随着材料及成品而有极大之差异。
以下对一般常见的加工方式,作一番简介:1. 射出成形(injection molding)在所有之塑料加工成形方法上,射出成形最为被广泛使用。
其法为热塑性塑料或热固性塑料导入于射出成形机的加热筒中,俟其完全熔融后,藉由柱塞或螺杆之压力,产生热能及摩擦热能,将其注入于闭合模具之模穴中,固化后,再开启模具取出成品。
此种加工技术因材料、机械设计及制品要求而衍生出其它之方法,如预嵌入金属零件之插件成形、多色及混色的射出成形,结构发泡的射出成形、气体辅助射出成形(gas assisted injection molding)、共射出成形(coinjection)、射出中空成形及利用液态单体或液态预聚合物为原料之反应射出成形(RIM)等方法。
塑胶件设计准则较全
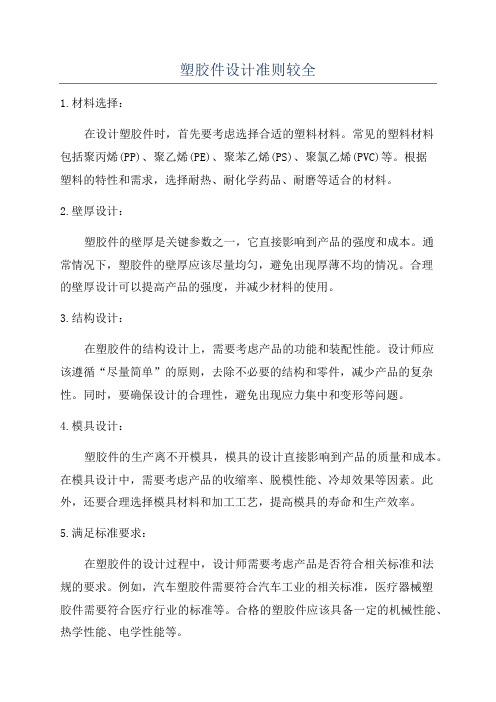
塑胶件设计准则较全1.材料选择:在设计塑胶件时,首先要考虑选择合适的塑料材料。
常见的塑料材料包括聚丙烯(PP)、聚乙烯(PE)、聚苯乙烯(PS)、聚氯乙烯(PVC)等。
根据塑料的特性和需求,选择耐热、耐化学药品、耐磨等适合的材料。
2.壁厚设计:塑胶件的壁厚是关键参数之一,它直接影响到产品的强度和成本。
通常情况下,塑胶件的壁厚应该尽量均匀,避免出现厚薄不均的情况。
合理的壁厚设计可以提高产品的强度,并减少材料的使用。
3.结构设计:在塑胶件的结构设计上,需要考虑产品的功能和装配性能。
设计师应该遵循“尽量简单”的原则,去除不必要的结构和零件,减少产品的复杂性。
同时,要确保设计的合理性,避免出现应力集中和变形等问题。
4.模具设计:塑胶件的生产离不开模具,模具的设计直接影响到产品的质量和成本。
在模具设计中,需要考虑产品的收缩率、脱模性能、冷却效果等因素。
此外,还要合理选择模具材料和加工工艺,提高模具的寿命和生产效率。
5.满足标准要求:在塑胶件的设计过程中,设计师需要考虑产品是否符合相关标准和法规的要求。
例如,汽车塑胶件需要符合汽车工业的相关标准,医疗器械塑胶件需要符合医疗行业的标准等。
合格的塑胶件应该具备一定的机械性能、热学性能、电学性能等。
6.通气设计:塑胶件在注塑过程中需要排除气体,否则会产生气泡和内部缺陷。
因此,在塑胶件的设计中,需要考虑通气的问题。
设计师可以在塑胶件的壁厚较大的地方设置气脱模系统,提高产品的质量。
7.可回收性设计:在现代社会,环保意识日益增强,可回收性成为塑胶件设计的一个重要考虑因素。
设计师应该尽量选择可回收的塑料材料,并设计可分解、可回收利用的产品。
总结起来,塑胶件设计准则涉及到材料选择、壁厚设计、结构设计、模具设计、标准要求、通气设计和可回收性设计等方面。
设计师在进行塑胶件设计时,应根据具体的产品需求和行业要求,合理应用这些准则,确保塑胶件的质量和性能,提高产品的竞争力。
塑胶件设计指导宝典教程
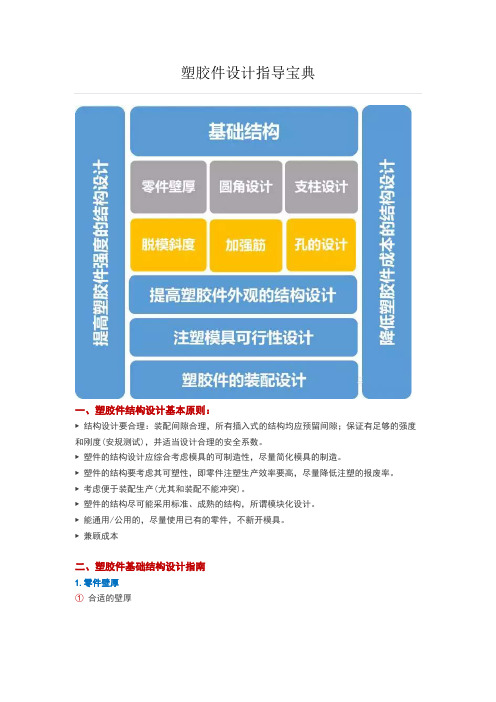
塑胶件设计指导宝典一、塑胶件结构设计基本原则:▶结构设计要合理:装配间隙合理,所有插入式的结构均应预留间隙;保证有足够的强度和刚度(安规测试),并适当设计合理的安全系数。
▶塑件的结构设计应综合考虑模具的可制造性,尽量简化模具的制造。
▶塑件的结构要考虑其可塑性,即零件注塑生产效率要高,尽量降低注塑的报废率。
▶考虑便于装配生产(尤其和装配不能冲突)。
▶塑件的结构尽可能采用标准、成熟的结构,所谓模块化设计。
▶能通用/公用的,尽量使用已有的零件,不新开模具。
▶兼顾成本二、塑胶件基础结构设计指南1.零件壁厚①合适的壁厚塑胶产品的胶厚(整体外壳)通常在0.80-3.00左右, 壁厚太小:强度低;流大,熔料难充满; 壁厚太大:零件产生加,成型周期加长,零件生产效率低;(请关注weixin:shujishi1818)常用塑胶材料合适壁厚范围(单位mm):②尽量减少零件壁厚,决定零件壁厚的因素如下:▶零件的强度要求;▶零件成型时能否抵抗脱模力;▶零件能够抵抗装配时的紧固力;▶有金属埋入件时,埋入件周围强度是否足够;▶孔的强度是否足够;▶错误的做法:为提高零件强度,片面的增加零件壁厚。
③零件壁厚均匀尽可能采用多种方法使壁厚保持均匀:当壁厚不均匀时:2. 圆角设计在塑件设计过程中,为了避免应力集中,提高塑件强度,改善塑件的流动情况及便于脱模,在塑件的各面或内部连接处,应采用圆弧过度。
另外,塑件上的圆角对于模具制造和机械加工及提高模具强度,也是不可少的。
在塑件结构上无特殊要求时,塑件的各转角处均应有半径不小于0.5~1mm的圆角。
允许的情况下,圆角应尽量大。
对于内外表面的拐角处,外圆角应为内圆角加壁厚,可减少内应力,并能保证壁厚均匀一致。
(请关注weixin:shujishi1818)①避免零件外部尖角②避免在塑胶熔料流动方向上产生尖角③避免在零件连接处产生尖角3. 脱模斜度一般来说,对模塑产品的任何一个侧面,都需有一定量的脱模斜度,以便产品从模具中顺利脱出。
塑料件卡扣连接设计指南
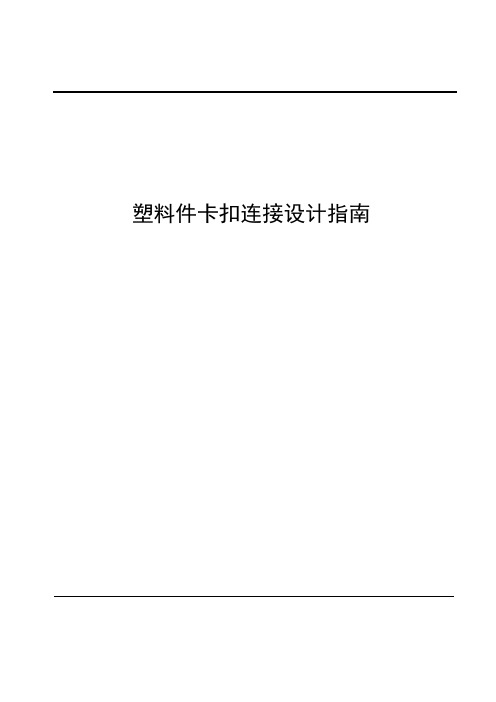
塑料件卡扣连接设计指南目次1.范围 (1)2.规范性引用文件 (1)3.定义 (1)4.塑料件卡扣连接概述 (2)4.1卡扣连接的关键要求 (2)4.2卡扣连接的要素 (4)5.约束概述 (12)5.1约束原理 (12)5.2约束原则 (16)5.3约束布置 (16)6.定位功能件设计 (21)6.1定位功能件类型 (21)6.2定位副的组合及其适配性 (29)6.3定位副与装配 (30)6.4定位副与保持 (33)7.锁紧功能件设计 (36)7.1锁紧功能件类型 (36)7.2锁紧功能件的结构设计与计算 (52)7.3对锁紧功能件装配与保持行为的分离 (76)前言为指导本公司塑料件卡扣连接的开发,特制定了本设计指南。
集成在产品上的卡扣连接与散件紧固或焊、粘接相比功能产品单一,无需配套;不要求焊接、点胶等复杂的操作;锁紧功能件由模具成型,一致性好,互换性强,尤其适合汽车行业的大批量生产;装配及拆卸往往不需要工具,便利性强;省去或减少了螺钉、螺母等散件的使用数量,降低了生产成本;可用于对外观有要求而不能使用散件紧固的产品。
且由于塑料产品的材料和工艺特性特别有利于集成式卡扣的开发,所以卡扣连接是一种普遍应用于汽车塑料产品的连接形式。
然而塑料件卡扣连接的可靠性特别依赖设计,本指南旨在对卡扣设计进行介绍,使读者了解相关知识并能应用在本公司塑料产品的设计开发中。
本指南由公司产品管理部提出并归口。
本指南起草单位:车身工程研究院。
本指南主要起草人:黄闿鸣本指南由车身工程研究院负责解释。
塑料件卡扣连接设计指南1.范围本指南主要从约束布置、定位功能件及锁紧功能件设计等方面对集成在塑料件上的卡扣连接进行介绍,也可为其他未集成在塑料件上的卡扣连接形式提供设计参考。
本指南用于指导本公司汽车塑料件卡扣连接的设计开发。
2.规范性引用文件下列文件中的条款通过本标准的引用而成为本标准的条款。
凡是注明日期的引用文件,其随后所有的修改单(不包括勘误的内容)或修订版均不适用于本标准,然而,鼓励根据本标准达成协议的各方研究是否可使用这些文件的最新版本。
塑胶件设计指南

塑胶件设计指南(jinyongcai)一、塑胶1、塑胶的定义塑胶:主要由碳、氧、氢和氮及其他有机或无机元素所构成,成品为固体,在制造过程中是熔融状的液体,因此可以籍加热使其熔化、加压力使其流动、冷却使其固化,而形成各种形状,此庞大而变化多端的材料族群称为塑胶。
2、塑胶的特征1)低强度与低韧性2)原料丰富,价格低廉3)成型容易,易加工成复杂形状,可大批量生产4)重量轻,低密度(塑胶比重0.9~2,铝2.7,铁7.8)5)受外力作用时容易产生连续变形6)色彩鲜明,着色容易,适当加入着色剂,可改变其色泽7)良好的绝缘性8)耐腐蚀性佳,耐水、耐油、耐酸、耐化学药品,而且不生锈9)耐热性差,大部份的塑料耐热温度约在150 ℃以下10)不导电性、不导热性11)可以具有其他特殊性质,例如透明性、弹性等3、注射成型(Injection Molding)一个典型的注射成型机主要包括:模具系统、射出系统、油压系统、控制系统、锁门系统等5个单元。
二、塑胶材料的选择1、塑胶材料的分类1.1、通用塑料通用塑料:指综合力学性能较低、不能作为结构件,但成型性能好、价格便宜、用途广、产量大的塑料。
如:PE、PP、EEA、PVC用处:薄膜、管材、鞋材、盆子、桶、包装材料等。
1.2、普通工程塑料普通综合塑料:指综合力学性能中等、在工程方面用作非承载荷的材料。
如:PS、HIPS、ABS、AAS、ACS、MBS、AS、PMMA用处:各种产品外壳和壳体类。
1.3、结构工程塑料结构工程塑料:指综合力学性能较高、在工程方面用做产品结构件、可以承受较高载荷的材料。
如:PA、POM、NORYL、PC、PBT、PET用处:各种产品外壳1.4、耐高温工程塑料耐高温工程塑料:指在高温条件下仍能保持较高力学性能的塑料,耐高温和高刚性。
如:PI、PPO、PPS、PSF、PAS、PAR用处:汽车发动机部件、油泵和气泵盖、电子电器仪表用高温插座等。
1.5、塑料合金塑料合金:指利用物理共混或化学接枝的方法而获得的高性能、功能化、专用化的一类新材料。
塑料件设计要点
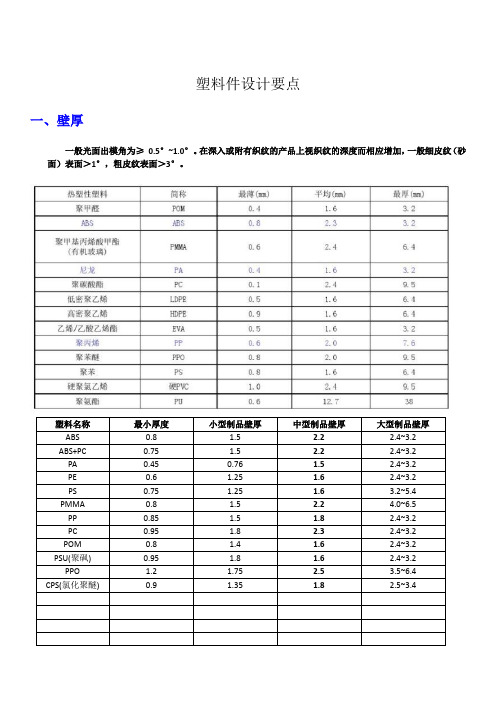
塑料件设计要点一、壁厚一般光面出模角为≥0.5°~1.0°。
在深入或附有织纹的产品上视织纹的深度而相应增加,一般细皮纹(砂面)表面>1°,粗皮纹表面>3°。
塑料名称最小厚度小型制品壁厚中型制品壁厚大型制品壁厚PP平均厚度取2~2.5,最溥处不小于0.7,最厚处不大于4.5(否则缩水严重)二、圆角筋骨与主体交接处:倒圆角与壁厚的比例为0.2至0.6之间,理想数值是在0.5左右(即圆角半径小于壁厚的一半)特别受力的柱子根部做圆角,约R0.5。
主体转角处尽量倒圆角,内侧圆角半径最小值为壁厚的20%(一般取50%=R/T=0.5),外侧圆角半径最小为壁厚值任意位置圆角最小R大于0.3三、筋骨ABS/PMMA:a=2.0~3.5,b=0.4a,r=0.3~0.6a,f=0.5度,c≦3a,d>3aPBT:a<3.2时,b<0.6a,r>0.5a,f=0.5~度,c≦3b,d>3aPBT:a>3.2时,b<0.4a,r>0.5a,f=0.5度,c≦3b,d>3aPC/PS/PPO: a<3.2时,b<0.4a,r=0.25~1a,f=0.5度,c≦3a,d>2.5aPC/PS/PPO: a>3.2时,b<0.6a,r=0.25~1a,f=0.5度,c≦3a,d>2.5aPA/PE: b<0.6a,r=0.25~1a,f=0.5度,c≦3a,d>2.5aPP:a=2~2.5,b=0.3a,r=0.25a,f=0.5度,c=2.5~3a,d>3a要求表面质量好的话c=1.5a(2mm厚的手柄盖c取3mm)四、支柱当 BOSS不是很高而在模具上又是用司筒顶出时,其可不用做斜度。
当BOSS很高时,通常在其外侧加做十字肋(筋),该十字肋通常要做1-2度的斜度,BOSS看情况也要做斜度。
塑胶件设计要点_1006

2 、作为铰链的薄膜尺寸应小于0.5mm,且保持均匀, 3 、注塑一体铰链时,浇口只能设计在铰链的某一侧。 九、 嵌件 1 、在注塑产品中镶入嵌件可增加局部强度、硬度、尺寸精度和设置小螺纹孔(轴),满足各种特殊需求。同时会 增加产品成本。 2 、嵌件一般为铜,也可以是其它金属或塑料件。 3 、嵌件在嵌入塑料中的部分应设计止转和防拔出结构。如:滚花、孔、折弯、压扁、轴肩等。 4 、嵌件周围塑料应适当加厚,以防止塑件应力开裂。 5 、设计嵌件时,应充分考虑其在模具中的定位方式(孔、销、磁性) 十、 标识 产品标识一般设置在产品内表面较平坦处,并采用凸起形式,选择法向与开模方向尺可能一致的面处设置标识,可 以避免拉伤。 十一、 注塑件精度 由于注塑时收缩率的不均匀性和不确定性,注塑件精度明显低于金属件,不能简单地套用机械零件的尺寸公差应按 标准选择适当的公差要求.我国也于1993年发布了GB/T14486-93 《工程塑料模塑塑料件尺寸公差》,设计者可根 据所用的塑料原料和制件使用要求,根据标准中的规定确定制件的尺寸公差。 十二、 注塑件的变形 提高注塑产品结构的刚性,减少变形。尽量避免平板结构,合理设置翻边,凹凸结构。设置合理的加强筋。 十三、扣位 1、将扣位装置设计成多个扣位同时共用,使整体的装置不会因为个别扣位的损坏而不能运作,从而增加其使用寿 命,再是多考滤加圆角,增加强度。 2、是扣位相关尺寸的公差要求十分严谨,倒扣位置过多容易形成扣位损坏;相反,倒扣位置过少则装配位置难於 控制或组合部份出现过松的现象。解决办法是要预留改模容易加胶的方式来实现。
四、 加强筋 1、 加强筋的合理应用,可增加产品刚性,减少变形。 2、 加强筋的厚度必须≤ (0.5~0.7)T产品壁厚,否则引起表面缩水。 3、 加强筋的单面斜度应大于1.5°,以避免顶伤。 五、圆角 1、 圆角太小可能引起产品应力集中,导致产品开裂。 2、圆角太小可能引起模具型腔应力集中,导致型腔开裂。 3、 设置合理的圆角,还可以改善模具的加工工艺,如型腔可直接用R刀铣加工,而避免低效率的电加工。 4 、不同的圆角可能会引起分型线的移动,应结合实际情况选择不同的圆角或清角。 六、 孔 1 、孔的形状应尽量简单,一般取圆形。 2 、孔的轴向和开模方向一致,可以避免抽芯。 3 、当孔的长径比大于2时,应设置脱模斜度。此时孔的直径应按小径尺寸(最大实体尺寸) 4 、盲孔的长径比一般不超过4,防孔针冲弯 5 、孔与产品边缘的距离一般大于孔径尺寸。 七、 注塑模的抽芯、滑块机构及避免 1、 当塑件按开模方向不能顺利脱模时,应设计抽芯滑块机构。抽芯机构滑块能成型复杂产品结构,但易引起产品 拼缝线、缩水等缺陷,并增加模具成本缩短模具寿命。 2、设计注塑产品时,如无特殊要求,尽量避免抽芯结构。如孔轴向和筋的方向改为开模方向,利用型腔型芯碰穿 等方法。 八、 一体铰链 1 、利用PP料的韧性,可将铰链设计成和产品一体。
Plastic Parts Design Guide(塑料零件设计指南)

Sinks
Sink
Improved Sinks 槽优化
36
Grained or
Stippled
Surface
Tooled Depression
Offset at Rib
Sinks
Ribs Design 筋设计
37
should be improved
Better
Best
Good Design, Strength
Flow Direction
Gate
Transverse Direction
Glass Fiber Resists Shrinkage in Direction of Alignment/Flow
Gate Location & Shrinkage
浇口位置和收缩率
8
Mineral Reinforced
Shrinkage & Warpage收缩和翘曲
13
Case on a ‘plate + rib’ profile
b
a
Gate L
h w
Gate
Flow angle Isochrones
Shrinkage & Warpage 收缩和翘曲 Glass reinforced materials
Deformation trend
45
Good Design, Example
好的设计,例如:
46
Steel
Plastic
Good Design, Example
好的设计,例如:
47
48
THANKS
22C
530
Flow Direction Knit Line
塑胶设计指南4
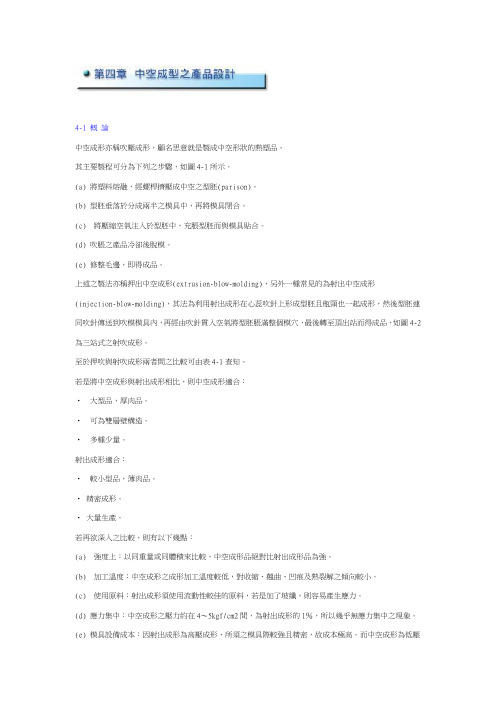
4-1 概論中空成形亦稱吹壓成形,顧名思意就是製成中空形狀的熱塑品。
其主要製程可分為下列之步驟,如圖4-1所示。
(a) 將塑料熔融,經螺桿擠壓成中空之型胚(parison)。
(b) 型胚垂落於分成兩半之模具中,再將模具閉合。
(c) 將壓縮空氣注入於型胚中,充脹型胚而與模具貼合。
(d) 吹脹之產品冷卻後脫模。
(e) 修整毛邊,即得成品。
上述之製法亦稱押出中空成形(extrusion-blow-molding),另外一種常見的為射出中空成形(injection-blow-molding),其法為利用射出成形在心蕊吹針上形成型胚且瓶頸也一起成形,然後型胚連同吹針傳送到吹模模具內,再經由吹針貫入空氣將型胚脹滿整個模穴,最後轉至頂出站而得成品,如圖4-2為三站式之射吹成形。
至於押吹與射吹成形兩者間之比較可由表4-1查知。
若是將中空成形與射出成形相比,則中空成形適合:‧大型品,厚肉品。
‧可為雙層壁構造。
‧多種少量。
射出成形適合:‧較小型品,薄肉品。
‧精密成形。
‧大量生產。
若再欲深入之比較,則有以下幾點:(a) 強度上:以同重量或同體積來比較,中空成形品絕對比射出成形品為強。
(b) 加工溫度:中空成形之成形加工溫度較低,對收縮、翹曲、凹痕及熱裂解之傾向較小。
(c) 使用原料:射出成形須使用流動性較佳的原料,若是加了玻纖,則容易產生應力。
(d) 應力集中:中空成形之壓力約在4~5kgf/cm2間,為射出成形的1%,所以幾乎無應力集中之現象。
(e) 模具設備成本:因射出成形為高壓成形,所須之模具際較強且精密,故成本極高。
而中空成形為低壓成形,所用模具可為鋁、鋅、或鋁合金。
中空成形之成形周期極短,以製造一個175毫升(6-OZ)之容器而言,其成形周期可在12秒內。
若有8個模穴的話,則每一小時可製出2400個產品,且可加裝自動切離邊料設備以省卻人工處理成本。
4-2 模具設計4-2-1 製造材料1. 鐵與鋼材:屬機械功能的,如安裝、導引、滑動、夾斷、切割、打孔等部位所須之組配件以鋼材為主。
塑件设计指南

目录第一章塑件设计的一般程序和原则 (1)1.1 塑件设计的一般程序 (1)1.2 塑件设计的一般原则 (1)第二章塑件的收缩 (1)第三章拔模斜度 (4)3.1拔模斜度确定要点 (4)3.2 制品拔模斜度设计 (5)第四章制品壁厚 (7)4.1制品壁厚的作用 (7)4.2 制品壁厚的设计 (7)第五章加强筋(含凸台、角撑) (12)5.1 加强筋的作用 (12)5.2 加强筋的形状及尺寸 (12)第六章支承面 (17)第七章圆角 (18)第八章孔 (19)8.1 制品孔的形式及成型方法 (19)8.2 孔的模塑成型 (20)8.3 孔的设计要点 (23)第九章侧面凸凹和侧孔 (26)9.1 制品的侧凸凹 (26)9.2 侧凸凹的设计与成型方法 (27)第十章螺纹 (31)10.1 塑件螺纹的类型与选用(图2—54) (31)10.2塑件螺纹的模塑成型方法 (32)10.3 塑件螺纹设计要点 (32)第十一章塑件中的嵌件 (35)11.1 嵌件的结构形式 (36)11.2 嵌件在塑件中的固定 (38)11.3 嵌件在模具中的安放与定位 (40)11.4 嵌件周围塑料的裂纹和联接强度 (42)11.5 装配式嵌件(制品模塑后再装入嵌件) (43)11.6 塑料嵌件(嵌件的外插注射模塑) (44)第十二章塑件的凸凹纹(滚花) (45)第十三章标记、符号 (47)第十四章制品的尺寸精度 (47)14.1 尺寸精度的组成及影响因素 (47)14.2 塑件尺寸公差 (49)附录一:塑料的基本概念及其常用工程塑料的性能特点 (52)附录二:塑料的成型工艺 (55)塑件设计指南塑件的结构设计又称塑件的功能特性设计或塑件的工艺性。
第一章 塑件设计的一般程序和原则1.1 塑件设计的一般程序1. 详细了解塑件的功能、环境条件和载荷条件2. 选定塑件品种3. 制定初步设计方案,绘制制品草图(形状、尺寸、壁厚、加强筋、孔的位置等)4. 样品制造、进行模拟试验或实际使用条件的试验5. 制品设计、绘制正规制品图纸6. 编制文件,包括塑件设计说明书和技术条件等。
塑料件的设计指南

1. 工程塑料的性能简介:有些固态物质具有分子排布有序,致密堆积的特性,如食用盐,糖,石英,矿物质和金属。
其它表现为固态物质,并不形成有规则的晶体排列方式。
它们只是冷却成为无序的或随机的分子团,称为无定型聚合物。
非晶体物质不是真正的固体,最普通的例子就是玻璃,它们只是过冷的,极端粘稠的液体。
塑料树脂可以分为结晶型和无定型的。
结晶型是相对的概念,由于聚合物的分子链大而复杂,所以不能够向无机化合物那样有完美的晶体排列次序。
不同的聚合物有不同的结晶表现,如高密度的聚乙烯有点结晶性,尼龙的会更强一些,聚甲醛(POM)的更强。
结晶型与无定型塑料的区别熔解/凝固结晶型会有一个熔点,熔解是需要熔解热,成型时会稳定性和硬度会迅速提高,所以结晶型塑料的成型周期比较短。
无定型物质的温度随着所加入的热量而增加,而且越来越呈现为液态。
成型的周期也比较长。
收缩结晶型塑料的收缩率会比较大,无定型的比较小结晶型塑料收缩率聚甲醛(POM)尼龙66聚丙烯~无定型塑料收缩率聚碳酸脂(PC)ABSPMMA聚苯乙烯由于收缩率小,无定型塑料有更好的尺寸稳定性,想我们通用的PC、ABS和PC+ABS 的最小公差可以规定为+/%塑料的其他性能不同的塑料聚合物以及添加一些助剂之后塑料会有不同的性能。
如添加玻纤(一般20%~40%)之后能够显著增加制成品的强度;GE的LEXAN PC和CYCOLOY PC+ABS的HF是高流动级,对于手机这类薄壳设计的注塑加工的难度有显著的改善;添加阻燃剂之后能够达到UL94 5V/V0级阻燃要求。
塑料选择手机里面比较通用的塑料选择是:手机外壳:GE PC EXL1414,SAMSUNG PC HF-1023IM,GE ABS+PC CYCOLOY 1200HF,GE ABS+PC CYCOLOY 2950、2950HF,其中GE PC EXL1414价格较贵大概是GE ABS+PC CYCOLOY 1200HF的两倍,GE ABS+PC CYCOLOY 2950、2950HF是阻燃级别电池壳:GE PC EXL1414,SAMSUNG PC HF-1023IM,GE 1200HF, GE CX7240(超薄电池底壳0.2mm)电镀件:奇美 PA-727,少数使用奇美PA-757、GE CYCOLAC EPBM电池卡扣或者运动件:POM2. 手机塑料件的平均肉厚为1.0mm~1.2mm。
塑料件设计_基础
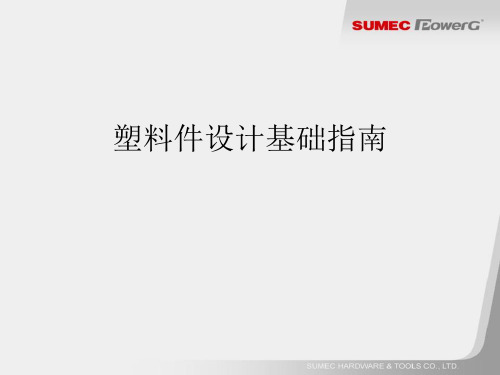
筋的厚度设计要求:50%~75%基体壁厚
壁厚(Wall Thickness)
不均匀壁厚产生的收缩
内部缩孔
缩痕
壁厚(Wall Thickness)
不合理的设计 改进的设计
壁厚(Wall Thickness)
不容易被抛光从而影响出模
壁厚(Wall Thickness)
塑料件的壁厚的设计有两个基本原则: • 在保证性能和用户体验的前提下尽可能薄的壁厚。 • 尽量均匀的壁厚。
均匀壁厚的好处是:注塑流动性好,减少外观缩痕,消除内部气孔,减少注塑后 应力,减少不同收缩比例带来的变形。 如果实际设计时很难做到壁厚一致,那么壁厚的变化不应超过公称壁厚的50%。
圆角处太薄
圆角处太厚
正确的设计
螺柱(Bosses)
螺柱设计的一般原则:
1. 螺柱尽可能不要独立布置,尽量与壳体用筋相连(图1)或用三角筋加强(图2) 2. 考虑是否会引起过多的壁厚而导致缩痕
一般尺寸要求
2-2.5D D
不正确设计
1.5mm
最大0.3t t
0.6t
正确设计
螺柱(Bosses)
设计流程(Design Flow)
根据公司的产品开发管理制度,塑料件的开发流程一般为:
概念
ID
CAD
CAE
模具
概念:根据立项要求,提出设计概念
ID:工业造型进行外形表皮设计 CAD:开发部根据表皮及设计需求进行实体设计 CAE:对设计的零件进行分析评估 模具:与模具制造厂家确定模具技术要求,并确认模具图纸
不正确
正确
正确
塑料产品设计指南
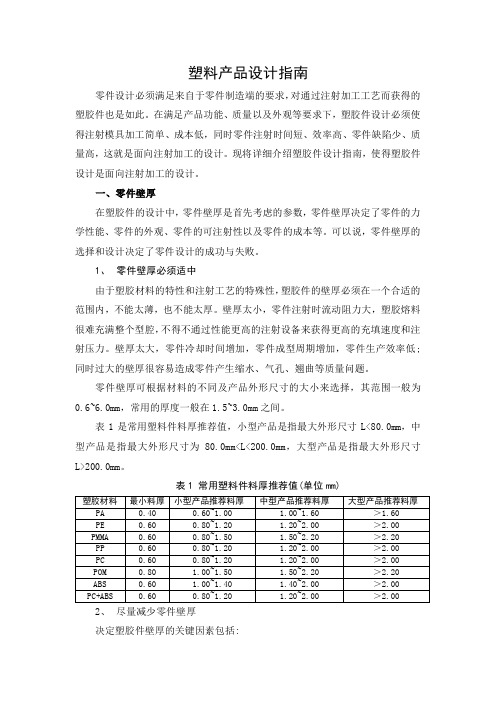
塑料产品设计指南零件设计必须满足来自于零件制造端的要求,对通过注射加工工艺而获得的塑胶件也是如此。
在满足产品功能、质量以及外观等要求下,塑胶件设计必须使得注射模具加工简单、成本低,同时零件注射时间短、效率高、零件缺陷少、质量高,这就是面向注射加工的设计。
现将详细介绍塑胶件设计指南,使得塑胶件设计是面向注射加工的设计。
一、零件壁厚在塑胶件的设计中,零件壁厚是首先考虑的参数,零件壁厚决定了零件的力学性能、零件的外观、零件的可注射性以及零件的成本等。
可以说,零件壁厚的选择和设计决定了零件设计的成功与失败。
1、零件壁厚必须适中由于塑胶材料的特性和注射工艺的特殊性,塑胶件的壁厚必须在一个合适的范围内,不能太薄,也不能太厚。
壁厚太小,零件注射时流动阻力大,塑胶熔料很难充满整个型腔,不得不通过性能更高的注射设备来获得更高的充填速度和注射压力。
壁厚太大,零件冷却时间增加,零件成型周期增加,零件生产效率低;同时过大的壁厚很容易造成零件产生缩水、气孔、翘曲等质量问题。
零件壁厚可根据材料的不同及产品外形尺寸的大小来选择,其范围一般为0.6~6.0mm,常用的厚度一般在1.5~3.0mm之间。
表1是常用塑料件料厚推荐值,小型产品是指最大外形尺寸L<80.0mm,中型产品是指最大外形尺寸为80.0mm<L<200.0mm,大型产品是指最大外形尺寸L>200.0mm。
表1 常用塑料件料厚推荐值(单位mm)2、尽量减少零件壁厚决定塑胶件壁厚的关键因素包括:1)零件的结构强度是否足够。
一般来说,壁厚越大,零件强度越好。
但零件壁厚超过一定范围时,由于缩水和气孔等质量问题的产生,增加零件壁厚反而会降低零件强度。
2)零件成型时能否抵抗脱模力。
零件太薄,容易因顶出而变形。
3)能否抵抗装配时的紧固力。
4)有金属埋入件时,埋入件周围强度是否足够。
一般金属埋入件与周围塑胶材料收缩不均匀,容易产生应力集中,强度低。
5)零件能否均匀分散所承受的冲击力。
塑胶设计指南5
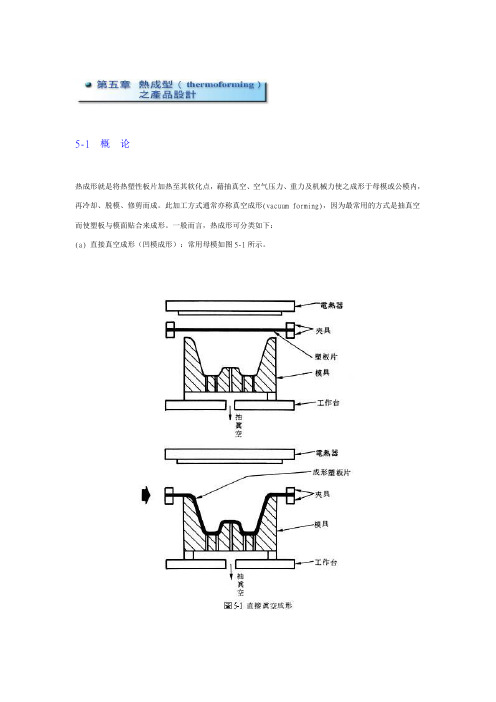
5-1概论热成形就是将热塑性板片加热至其软化点,藉抽真空、空气压力、重力及机械力使之成形于母模或公模内,再冷却、脱模、修剪而成。
此加工方式通常亦称真空成形(vacuum forming),因为最常用的方式是抽真空而使塑板与模面贴合来成形。
一般而言,热成形可分类如下:(a) 直接真空成形(凹模成形):常用母模如图5-1所示。
(b) 包模真空成形(drape vacuum forming):将热塑性板片夹于活动之框架上预热后,框架下降使板片覆盖于阳模四周,然后于阳模侧真空吸引成形。
(c) 模塞助压成形(plug assist forming):模穴部份固定不动,以公模塞下压使之预成形,再抽真空吸引成形的方法(图5-2)。
(d) 模塞助压反拉伸成形(plug assist reverse draw forming):模塞于下压前充气使受热板片些微膨胀,至定位时再抽真空吸引成形(图5-3)。
此法可避免成形品产生擦痕,极适用于成形宽且深的塑品。
(e) 真空迫回成形(vacuum snap-back forming):先下抽真空使塑板片成凹状,再强力的往上抽真空,使板片与公模紧紧的贴合。
此法可使肉厚之分布较均匀及使冷痕缺陷减到最少。
(f) 滑动环成形(slip-ring forming):用一可松动的夹具使成形时有容许的塑料慢慢往内滑行,以取代直接的拉引。
此法可使肉厚较匀称。
(g) 对模热成形(matched-mold forming):将热塑性板片加热软化后,再以上下两模对合加压而成形(图5-4)。
此法可得较精确的成品尺寸及光滑表面。
模具通常须用金属,成本较高。
(h)其它之热成形:如利用空气压力,通常为反方向的预成形,再正方向的成形,可制得均匀肉厚且深度较深的产品。
热成形最适宜制造薄肉厚且浅深度的塑品,最常见的是用于消费性的包装品。
其它如公交车、飞机内部的嵌板,电冰箱的衬套、广告板、小舟、事务机之外壳、搬运箱、轮廓地图、电视机后嵌板、门板及家具镶板等。
塑胶件设计

§ 塑件设计
3、塑件结构设计 满足使用要求 好的结构工艺性:是指塑件在满足使用要
求的前提下,其结构应尽可能符合成形工 艺要求,从而简化模具结构,降低生产成 本。
§ 塑件设计
1)塑件结构工艺性设计应遵循的原则:
在保证塑件的使用性能、物理、化学、介电性能与力学 性能等的前提下,尽量选用价格低廉和成形性能较好的 塑料,并力求结构简单、壁厚均匀、成形方便。
在设计塑件时应考虑其模具的总体结构,使模具型腔易 于设计制造,模具抽芯和推出机构简单。
在设计塑件时,应考虑原料的成形工艺性,如流动性、 收缩性等,塑件形状有利于模具分型、排气、补缩和冷 却。
§塑件设计
设计原则: ❖ 应考虑原材料的成型工艺性; ❖ 应考虑模具的总体结构,使模具型腔易于制
造,模具抽芯和推出机构简单; ❖ 在保证塑件使用性能、物理性能与力学性能、
电性能等的前提下,力求结构简单,壁厚均 匀,使用方便。
§ 塑件设计
1、塑件尺寸及其精度 1)塑件尺寸 设计原则:
❖ 受到塑料的流动性制约,流动性好的塑料可以成形较大 尺寸的塑件,反之能成形的塑件尺寸就较小。
§ 塑件设计
❖圆角(不小于0.5~1mm,一般外圆角R=1.5 内圆角R1=0.5 。)
作用: 避免应力集中,提高塑件强度 改善熔体流动情
况、便于脱模模具型腔不易因应力集中而开裂。
§ 塑件设计
❖ 孔的设计(包括通孔、盲孔、异形孔、螺 纹孔) 设计原则: ① 保证足够强度,以满足使用要求; ② 尽量避免侧孔。
§ 塑件设计
❖ 标记符号及表面彩饰
注意事项
①标记符号应放在分型面的平 行方向上,并有适当的斜 度(>10°)以便于脱模。
- 1、下载文档前请自行甄别文档内容的完整性,平台不提供额外的编辑、内容补充、找答案等附加服务。
- 2、"仅部分预览"的文档,不可在线预览部分如存在完整性等问题,可反馈申请退款(可完整预览的文档不适用该条件!)。
- 3、如文档侵犯您的权益,请联系客服反馈,我们会尽快为您处理(人工客服工作时间:9:00-18:30)。
1. 工程塑料的性能简介:
1.1有些固态物质具有分子排布有序,致密堆积的特性,如食用盐,糖,石英,
矿物质和金属。
其它表现为固态物质,并不形成有规则的晶体排列方式。
它们只是冷却成为无序的或随机的分子团,称为无定型聚合物。
非晶体物质不是真正的
固体,最普通的例子就是玻璃,它们只是过冷的,极端粘稠的液体。
塑料树脂可以分为结晶型和无定型的。
结晶型是相对的概念,由于聚合物的分子
链大而复杂,所以不能够向无机化合物那样有完美的晶体排列次序。
不同的聚合
物有不同的结晶表现,如高密度的聚乙烯有点结晶性,尼龙的会更强一些,聚甲醛(POM)的更强。
1.2 结晶型与无定型塑料的区别
熔解/凝固
结晶型会有一个熔点,熔解是需要熔解热,成型时会稳定性和硬度会迅速提高,
所以结晶型塑料的成型周期比较短。
无定型物质的温度随着所加入的热量而增加,而且越来越呈现为液态。
成型的周
期也比较长。
收缩
结晶型塑料的收缩率会比较大,无定型的比较小
结晶型塑料收缩率
聚甲醛(POM) 2.0
尼龙66 1.5
聚丙烯 1.0~2.5
无定型塑料收缩率
聚碳酸脂(PC) 0.6-0.8
ABS 0.4-0.7
PMMA 0.7
聚苯乙烯 0.4
由于收缩率小,无定型塑料有更好的尺寸稳定性,想我们通用的PC、ABS和PC+ABS 的最小公差可以规定为+/_0.002%
1.3 塑料的其他性能
不同的塑料聚合物以及添加一些助剂之后塑料会有不同的性能。
如添加玻纤(一般20%~40%)之后能够显著增加制成品的强度;GE的LEXAN PC和
CYCOLOY PC+ABS的HF是高流动级,对于手机这类薄壳设计的注塑加工的难度
有显著的改善;添加阻燃剂之后能够达到UL94 5V/V0级阻燃要求。
1.4 塑料选择
手机里面比较通用的塑料选择是:
PC H F-1023IM,GE A BS+PC CYCOLOY 1200HF,手机外壳:GE P C E XL1414,SAMSUNG
GE ABS+PC CYCOLOY
2950、2950HF,其中GE P C E XL1414价格较贵大概是GE A BS+PC
、2950HF是阻燃级别CYCOLOY 1200HF的两倍,GE ABS+PC CYCOLOY 2950
,GE 1200HF, GE CX7240(超电池壳:GE PC EXL1414,SAMSUNG PC HF-1023IM
薄电池底壳0.2mm)
电镀件:奇美 PA-727,少数使用奇美PA-757、GE CYCOLAC EPBM
电池卡扣或者运动件:POM
2. 手机塑料件的平均肉厚为 1.0mm~1.2mm。
较大面(如主副屏贴LENS处可以做
到0.5mm),局部可以做到0.35mm。
不同材料的最小肉厚不同,其中结晶性的塑料如铁弗龙、POM、尼龙可以做的比较小,PMMA、ABS次之,PC由于流动性比较差需要的最小肉厚比较大。
3. 壁厚尽量均一,如果是不可避免的变化可以通过转换区来避免肉厚的急剧变
化:
4. 产品转角处不要设计成锐角,尤其是非结晶性塑料如我们常用的ABS、PC对锐角造成的应力非常敏感,容易造成应力集中,影响制成品的强度。
同时圆滑过渡的也可以降低模腔压力,改善流动性。
4.1 由于锐角处刻痕会产生应力集中,下面是悬臂梁结构下r/t>0.6的情况下能够有效降低应力集中因子:
4.2 同样的所有的塑胶件的转角处都需要加上R角,内R角大于0.5t,最好是0.6~0.75t:
5. Rib的设计:
时,Rib的厚度最好不大于壳子本体厚度的
5.1 使用GE的CYCOLOY ABS+PC
0.6倍。
5.2 高度不要超过本体厚度的3~5倍。
5.3 拔模角度为0.5~1.0度。
5.4 在Rib的根部导Rib厚度的40%~60%的圆角。
5.5 两根Rib之间的间距最好在壁厚的3倍以上。
6. 卡勾的设计:
6.1 卡勾的卡入尺寸一般在0.5mm~0.8mm。
6.2 钩子从分模面下沉0.2mm,有利于模具制造。
6.3 钩子和卡槽的咬合面留0.05mm的间隙,以便日后修模。
6.4 卡槽顶端于钩子底部预留0.3mm的间隙,作为卡勾变形的回弹空间。
6.5 卡槽最好做成封闭式的(在壁厚保证不缩水的情况下),封闭面的肉厚
0.3~0.5mm。
6.6 其余配合面留0.1~0.2mm的间隙。
6.7 钩子的斜顶需留6~8mm的行程。
6.8 钩子的尖端导0.1mm的圆角,以便拆卸。
6.9 卡勾配合面处可以自主导2度的拔模,作为拆卸角。
6.10 卡槽底部导R角增加强度,所以肉厚不一的地方导斜角做转换区。
7. 模具铁料的厚度需要大于0.5mm。
8. 母模面拔模角最好大于3度。
每增加千分之一英寸的咬花深度需增加一度的
拔模角。
9. Boss的设计
Boss的目的是用来连接螺钉、导销等紧固件或者是做定位、热熔柱,设计Boss 的最重要原则就是避免没有支撑物,尽量让其与外壁或者肋相连增加强度。
9.1 一般Boss通用设计规则:
9.2 埋螺母的Boss设计:
螺母
螺母有钻石花和斜花纹两种,钻石花不适合热熔但在超声波工艺中表现良好;斜花纹埋植时有自我导向功能,扭拉力综合性能良好。
最好选滚花之间有沟
槽的螺母,沟槽可以容纳塑料,提高拉力。
在我们使用的对尖角敏感的无定型塑料(PC、ABS)不要使用花纹太尖的螺母。
螺母材质主要有三种: 1.标准黄铜C3604;2.低铅铜,符合欧盟ROHS环保标准;3.不锈钢。
一般情况下螺母不需要做表面处理,特殊的情况下可以电镀。
Boss的设计
螺母的Boss设计需要注意两点:
(一) Boss内径与螺母外径之间的关系,M1.2~M1.7的螺母,Boss内径=螺母外径+0.2~0.3mm;M2.0~M3.0的螺母,Boss内径=螺母外径+0.5~0.6mm。
(二) Boss孔深度的设计需要考虑溢胶空间,一般情况下为0.5~1.5mm。
通常螺母长度小于 2.5mm需要0.5mm~1.0mm,2.5mm~4.0mm的需要1.0mm~1.5mm。
螺母的埋入方式
螺母有三种埋入方式:模内成型、热熔埋植和超声波埋植,它们各有优缺点。
注意要点 1.模具顶针公差和螺母公差需要严格控制,参照旧版ISO螺纹孔规标准;
2.注意进胶点的设计,不能靠近螺母位置,以免料流冲击造成螺母位移埋植温度应低于塑料熔点10~20度
理想埋植温度为T+/_2度超声波瞬间释放能量,对螺母冲击大,容易破坏螺母
特别是螺纹结构
M1.6以下的螺母不适合超声波埋植
其他主要要点
一把螺母都有导向端,塑料孔不用特别设计斜角
设计塑料孔径时孔径尺寸大于螺母导向端直径0.03mm以上
热固性塑料不时候热熔和超声波埋植,可以选择精密而尖锐的滚花螺母直接压入
塑料孔位置尽量避开结合线处,避免因为应力存在埋植螺母时导致塑料孔破裂
螺母埋植后的端面高度高于塑料孔端面0.05mm
10. 孔的设计
10.1 全穿孔和半穿孔
全穿孔比半穿孔容易加工,因为全穿孔的穿孔销两端都有支撑,而半穿孔只有一端获得支撑,易于熔融的料流进入模穴造成尺寸偏差,所以半穿孔的深度最好不要超过半穿孔直径的两倍,如果要加深深度可以做成层次孔。
半穿孔底部的壁厚至少须为其孔径的1/6,否则成型后此处薄壁会膨胀变形。
10.2 多孔结构孔间距离
多孔结构中,孔与孔间,孔与侧壁间的距离须大于孔径,孔与边缘距离须大于两倍孔径。