塑胶件设计指导宝典教程
产品结构设计04塑胶件设计指南

壁厚太大: 零件产生缩水、气孔和翘曲等质量问题; 零件冷却时间增加,成型周期加长,零件生产效率低; 零件用料增加,产品成本增加;
常用塑胶材料合适壁厚范围(单位mm):
PE PP Nylon PS AS PMM PVC PC ABS POM A
最小 0.9 0.6 0.6 1.0 1.0 1.5 1.5 1.5 1.5 1.5 最大 4.0 3.5 3.0 4.0 4.0 5.0 5.0 5.0 4.5 5.0
B.降低零件材料成本:
降低零件厚度; 通过添加加强肋而不是增加壁厚的方法提高零件强度;
零件较厚的部分去除材料;
C. 简化零件设计,降低模具成本:
KISS原则(Keep it simple, stupid),简单就是美! 零件中的每一个特征必须有存在的理由,否则,该特征是能够去除的。
D.避免零件严格的公差:
容易发生破裂而失效; 在承受冲击载荷时,保持零件剖面的完整性,避免在冲击载荷方向上
零件剖面出现缺口和应力集中。
36
8.提高塑胶件外观的设计
A.选择合适的塑胶材料; B. 避免零件外观表面缩水:
合适的零件壁厚; 通过设计掩盖缩水;
“U”形槽
“火山口”设计;
塑胶设计指南
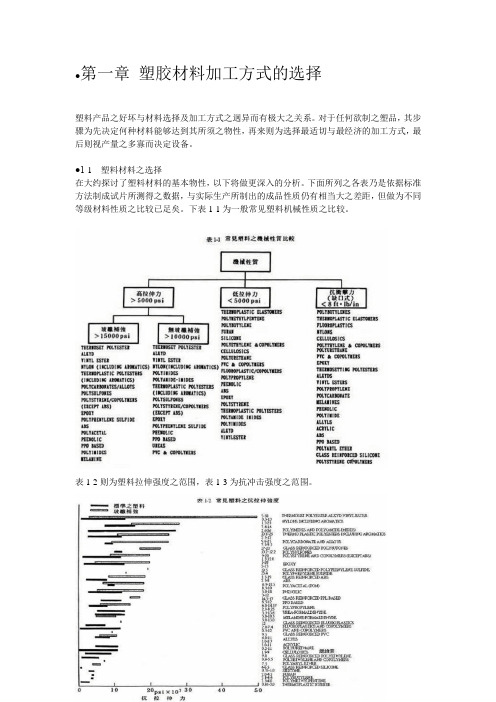
●第一章塑胶材料加工方式的选择塑料产品之好坏与材料选择及加工方式之迥异而有极大之关系。
对于任何欲制之塑品,其步骤为先决定何种材料能够达到其所须之物性,再来则为选择最适切与最经济的加工方式,最后则视产量之多寡而决定设备。
●1-1塑料材料之选择在大约探讨了塑料材料的基本物性,以下将做更深入的分析。
下面所列之各表乃是依据标准方法制成试片所测得之数据,与实际生产所制出的成品性质仍有相当大之差距,但做为不同等级材料性质之比较已足矣。
下表1-1为一般常见塑料机械性质之比较。
表1-2则为塑料拉伸强度之范围,表1-3为抗冲击强度之范围。
表1-4及表1-5,则为塑料之其它性质。
参考以上各表,即大约可知塑品用何种材料可达到其用途之所须性质要求。
一般而言加了玻纤后,可增加拉伸力、减少拉伸量、抗磨耗力降低、挠曲力增高、热变形温度增加、热膨胀降低及较不透明,而耐冲击力则不一定。
但是硬度(除非高填充)、电气性质、抗化学性及抗天候性则甚无影响。
表1-6则为一般材料之机械性质之定性趋势表。
若是依各种用途来分,所使用之塑料大概可列表如1-7所示。
●1-2塑料加工方式之选择塑料之加工方式五花八门,随着材料及成品而有极大之差异。
以下对一般常见的加工方式,作一番简介:1. 射出成形(injection molding)在所有之塑料加工成形方法上,射出成形最为被广泛使用。
其法为热塑性塑料或热固性塑料导入于射出成形机的加热筒中,俟其完全熔融后,藉由柱塞或螺杆之压力,产生热能及摩擦热能,将其注入于闭合模具之模穴中,固化后,再开启模具取出成品。
此种加工技术因材料、机械设计及制品要求而衍生出其它之方法,如预嵌入金属零件之插件成形、多色及混色的射出成形,结构发泡的射出成形、气体辅助射出成形(gas assisted injection molding)、共射出成形(coinjection)、射出中空成形及利用液态单体或液态预聚合物为原料之反应射出成形(RIM)等方法。
塑料模具设计教程-塑件

第三章塑件一﹑塑件的基本內容1.立體空間內容﹐几何結構﹐尺寸及精度。
2.塑件表面的內容﹑標記﹑符號﹑文字﹑表面圖案﹑圖形﹑粗糙度。
3.靜態﹑動態性能﹐機械﹑物理﹑化學等性能。
4.環境﹑人機工程。
5.塑料的選擇。
6.成本﹑價格。
7.成型模具及成型方法實現的可行性﹐經濟性等。
二﹑几何結構及尺寸精度1.結構包括內部結構和外部結構的設計。
1-1.形狀﹕塑件的形狀應盡可能保証有利于成型原則。
1-2.脫模斜度﹕由于塑件冷卻后產生收縮﹐會使塑件緊緊包住模具型芯和型腔中的击起部分(主要包模仁)﹐為了便于取出塑件﹐防止脫模時撞傷或擦傷塑件﹐設計塑件時﹐其內外表面沿脫模方向均應具有足夠的脫模斜度。
在設計時﹐應注意以下几個方面﹕a.壓縮成型較大的塑件時﹐要求內表面的脫模斜度大于外表面的脫模斜度。
b.常用脫模斜度值為1°~1.5°﹐也可小到0.5°。
c.對于高度不大的塑件﹐可不取脫模斜度。
1-3.壁厚﹕塑件的壁厚與使用要求及工藝要求有關。
a.在塑模成型上﹐壁厚過小﹐熔融塑膠在模具型腔中的流動陰力較大。
b.壁厚過大﹐會造成用料過多﹐增加成本﹐且會給成型工藝帶來困難。
在塑件上還會產生氣泡﹐縮孔﹑凹痕﹑翹曲等﹐影響產品外觀。
c.在成型工藝上還要求塑件各部位的壁厚盡可能均勻。
1-4.加強筋﹕它是塑件中經常會用到的增加塑件強度的辦法﹐其優點﹕a.使塑件壁厚均勻﹐即節約了材料﹐又提高了強度﹐還可避免塑件中外觀缺陷。
b.增加塑件的剛性。
c.沿料流方向的加強筋還能降低塑料的充模陰力。
加強筋的設計要求﹕a.為了增強塑件的強度及剛性﹐加強筋應設計得矮一些﹐多一些為好。
b.加強筋之間的中心距應大于兩倍的壁厚。
c.對于薄壁塑件﹐也可將其設計成球面或拱曲面形狀。
1-5.支承面﹕以塑件的整個底面作為支承面是不合理的。
通常利用的是邊框支承或底腳支承。
1-6.圓角﹕塑件上除了使用上要求必須采用尖角之外﹐其余所有轉角處均應采用圓弧過渡﹐因為尖角處易產生應力集中﹐影響塑件強度。
注塑模具实用教程第3章塑料制品设计
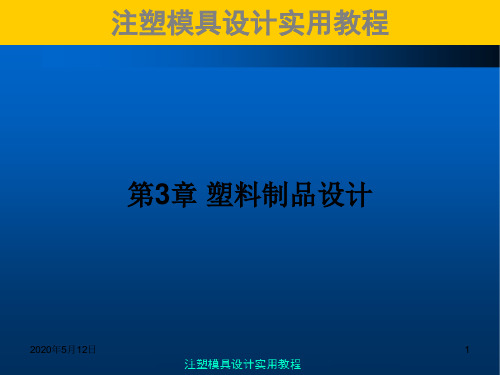
第3章 塑料制品设计
3.2塑件的尺寸与精度
3.2.1塑件的尺寸
1.塑件的尺寸首先受到塑料的流动性限制。 2.塑件尺寸还受成型设备的限制。
目前,世界上最大的注塑机在法国,该机可以注射出总质 量可达170kg的塑件;世界上最小的注塑机在徳国,该机的注射
量只有0.1g,用于生产0.05g的塑件。
2018年11月2日
36
第3章 塑料制品设计
实例
2018年11月2日
37
第3章 塑料制品设计
3-3-9 嵌件
塑料制品中镶入嵌件的目的是增强制品局部的强度、硬度、 耐磨性、导电性、导磁性等,或者是增加制品尺寸及形状的稳定 性,或者是降低塑料的消耗。嵌件的材料有金属、玻璃、木材和 已成型的塑料等,其中金属嵌件用得最为普遍。
2018年11月2日 32
第3章 塑料制品设计
(3)通孔的不同成型方法(重点):
2018年11月2日
33
第3章 塑料制品设计
(4)用拼合型芯成型孔:
2018年11月2日
34
第3章 塑料制品设计
3.3.7螺纹设计
塑件中的螺纹可用模塑方法成型出来,或切削方法获得;
经常拆装或受力大的螺纹,要采用金属螺纹嵌件来成型;
2018年11月2日
12
第3章 塑料制品设计
(3)塑胶件表面处理
1、喷油; 2、移印; 3、丝印; 4、印刷; 5、真空镀膜; 6、电镀; 7、蚀纹; 8、喷砂。
2018年11月18年11月2日
14
第3章 塑料制品设计
2018年11月2日
15
第3章 塑料制品设计
2018年11月2日 20
第3章 塑料制品设计
塑料模设计教程
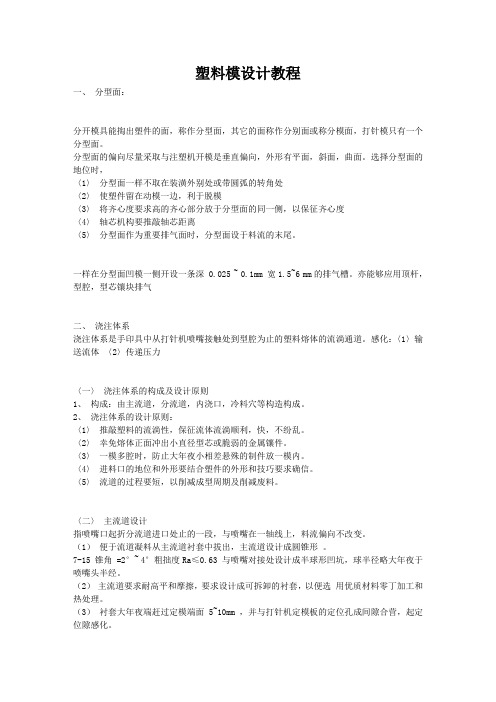
塑料模设计教程一、分型面:分开模具能掏出塑件的面,称作分型面,其它的面称作分别面或称分模面,打针模只有一个分型面。
分型面的偏向尽量采取与注塑机开模是垂直偏向,外形有平面,斜面,曲面。
选择分型面的地位时,〈1〉分型面一样不取在装潢外别处或带圆弧的转角处〈2〉使塑件留在动模一边,利于脱模〈3〉将齐心度要求高的齐心部分放于分型面的同一侧,以保征齐心度〈4〉轴芯机构要推敲轴芯距离〈5〉分型面作为重要排气面时,分型面设于料流的末尾。
一样在分型面凹模一侧开设一条深 0.025 ~ 0.1mm 宽1.5~6 mm的排气槽。
亦能够应用顶杆,型腔,型芯镶块排气二、浇注体系浇注体系是手印具中从打针机喷嘴接触处到型腔为止的塑料熔体的流淌通道。
感化:〈1〉输送流体〈2〉传递压力〈一〉浇注体系的构成及设计原则1、构成:由主流道,分流道,内浇口,冷料穴等构造构成。
2、浇注体系的设计原则:〈1〉推敲塑料的流淌性,保征流体流淌顺利,快,不纷乱。
〈2〉幸免熔体正面冲出小直径型芯或脆弱的金属镶件。
〈3〉一模多腔时,防止大年夜小相差悬殊的制件放一模内。
〈4〉进料口的地位和外形要结合塑件的外形和技巧要求确信。
〈5〉流道的过程要短,以削减成型周期及削减废料。
〈二〉主流道设计指喷嘴口起折分流道进口处止的一段,与喷嘴在一轴线上,料流偏向不改变。
(1)便于流道凝料从主流道衬套中拔出,主流道设计成圆锥形。
7-15 锥角 =2°~ 4°粗拙度Ra≤0.63 与喷嘴对接处设计成半球形凹坑,球半径略大年夜于喷嘴头半经。
(2)主流道要求耐高平和摩擦,要求设计成可拆卸的衬套,以便选用优质材料零丁加工和热处理。
(3)衬套大年夜端赶过定模端面 5~10mm ,并与打针机定模板的定位孔成间隙合营,起定位隙感化。
(4)主流道衬套与塑料接触面较大年夜时,因为腔体内反压力的感化使衬套易从模具中退出,可设计定住。
(5)直角式打针机中,主流道设计在分型面上,不需沿轴线上拔出凝料可设计成粗的圆柱形。
塑胶件结构设计手册(精华板)
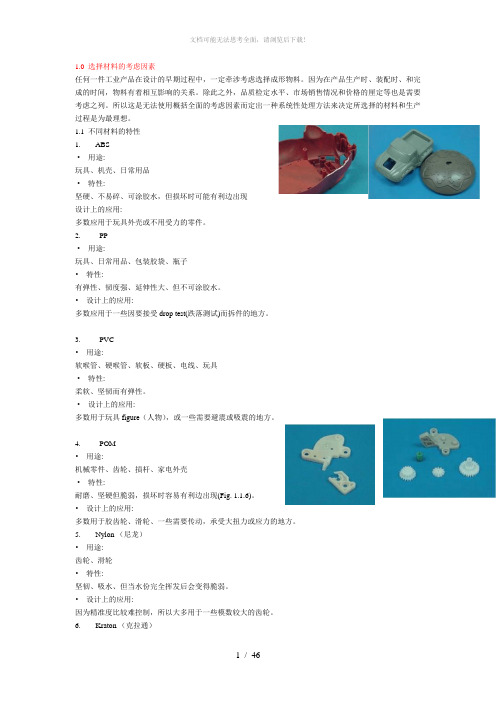
1.0 选择材料的考虑因素任何一件工业产品在设计的早期过程中,一定牵涉考虑选择成形物料。
因为在产品生产时、装配时、和完成的时间,物料有着相互影响的关系。
除此之外,品质检定水平、市场销售情况和价格的厘定等也是需要考虑之列。
所以这是无法使用概括全面的考虑因素而定出一种系统性处理方法来决定所选择的材料和生产过程是为最理想。
1.1 不同材料的特性1. ABS•用途:玩具、机壳、日常用品•特性:坚硬、不易碎、可涂胶水,但损坏时可能有利边出现设计上的应用:多数应用于玩具外壳或不用受力的零件。
2.PP•用途:玩具、日常用品、包装胶袋、瓶子•特性:有弹性、韧度强、延伸性大、但不可涂胶水。
•设计上的应用:多数应用于一些因要接受drop test(跌落测试)而拆件的地方。
3.PVC•用途:软喉管、硬喉管、软板、硬板、电线、玩具•特性:柔软、坚韧而有弹性。
•设计上的应用:多数用于玩具figure(人物),或一些需要避震或吸震的地方。
4.POM•用途:机械零件、齿轮、摃杆、家电外壳•特性:耐磨、坚硬但脆弱,损坏时容易有利边出现(Fig. 1.1.6)。
•设计上的应用:多数用于胶齿轮、滑轮、一些需要传动,承受大扭力或应力的地方。
5. Nylon (尼龙)•用途:齿轮、滑轮•特性:坚韧、吸水、但当水份完全挥发后会变得脆弱。
•设计上的应用:因为精准度比较难控制,所以大多用于一些模数较大的齿轮。
6. Kraton (克拉通)用途: 摩打垫特性: 柔软,有弹性,韧度高,延伸性强。
设计上的应用: 多数作为摩打垫,吸收摩打震动,减低噪音。
Table 1.1.1 一般胶料的特性与用途2.0 壁厚 [Wall Thickness]壁厚的大小取决于产品需要承受的外力、是否作为其它零件的支撑、承接柱位的数量、伸出部份的多少以及选用的塑料材料而定。
一般的热塑性塑料的壁厚设计应以4mm为限。
从经济角度来看,过厚的产品设计不但增加物料成本,延长生产周期(冷却时间),增加生产成本。
塑胶件结构设计手册(精华板)之欧阳道创编
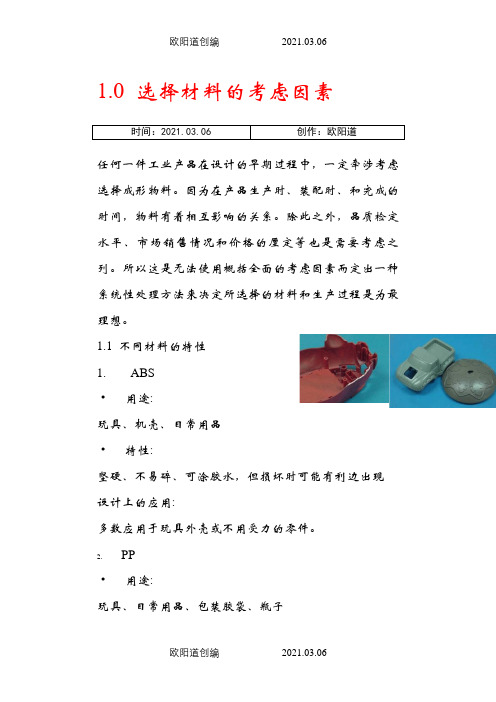
1.0 选择材料的考虑因素时间:2021.03.06 创作:欧阳道任何一件工业产品在设计的早期过程中,一定牵涉考虑选择成形物料。
因为在产品生产时、装配时、和完成的时间,物料有着相互影响的关系。
除此之外,品质检定水平、市场销售情况和价格的厘定等也是需要考虑之列。
所以这是无法使用概括全面的考虑因素而定出一种系统性处理方法来决定所选择的材料和生产过程是为最理想。
1.1 不同材料的特性1. ABS•用途:玩具、机壳、日常用品•特性:坚硬、不易碎、可涂胶水,但损坏时可能有利边出现设计上的应用:多数应用于玩具外壳或不用受力的零件。
2.PP•用途:玩具、日常用品、包装胶袋、瓶子•特性:有弹性、韧度强、延伸性大、但不可涂胶水。
•设计上的应用:多数应用于一些因要接受drop test(跌落测试)而拆件的地方。
3.PVC•用途:软喉管、硬喉管、软板、硬板、电线、玩具•特性:柔软、坚韧而有弹性。
•设计上的应用:多数用于玩具figure(人物),或一些需要避震或吸震的地方。
4.POM•用途:机械零件、齿轮、摃杆、家电外壳•特性:耐磨、坚硬但脆弱,损坏时容易有利边出现(Fig. 1.1.6)。
•设计上的应用:多数用于胶齿轮、滑轮、一些需要传动,承受大扭力或应力的地方。
5. Nylon (尼龙)•用途:齿轮、滑轮•特性:坚韧、吸水、但当水份完全挥发后会变得脆弱。
•设计上的应用:因为精准度比较难控制,所以大多用于一些模数较大的齿轮。
6. Kraton (克拉通)用途: 摩打垫特性: 柔软,有弹性,韧度高,延伸性强。
设计上的应用: 多数作为摩打垫,吸收摩打震动,减低噪音。
Table 1.1.1 一般胶料的特性与用途2.0 壁厚 [Wall Thickness]壁厚的大小取决于产品需要承受的外力、是否作为其它零件的支撑、承接柱位的数量、伸出部份的多少以及选用的塑料材料而定。
一般的热塑性塑料的壁厚设计应以4mm为限。
从经济角度来看,过厚的产品设计不但增加物料成本,延长生产周期(冷却时间),增加生产成本。
2019塑胶件机构设计详细版

进阶篇:3.1)塑胶件设计标签:塑胶件工艺结构2016年12月07日13:10:28 2626人阅读评论(0) 收藏举报分类:结构设计(80)作者同类文章X目录(?)[+]基础阅读塑胶简介1 定义与特性2 分类3 材料选择依据4 注塑成型机塑胶件设计指南1 零件壁厚11 零件壁厚必须适中12 尽量减少零件壁厚13 零件壁厚均匀14 软件壁厚分析功能2 避免尖角21 避免零件外部尖角22 避免在塑胶熔料流动方向上产生尖角23 避免在零件连接处产生尖角3 脱模斜度31 零件若无特殊需求脱模斜度一般取1232 收缩率较大的塑胶件脱模斜度较大33 尺寸精度要求较高的特征处取较小脱模斜度34 公模侧脱模斜度小于母模侧以利于脱模35 壁厚较厚时成型收缩大取较大脱模斜度36 咬花面与复杂面取较大脱模斜度37 玻纤增强塑料取较大脱模斜度38 零件某些平面因为功能需要可以不设置脱模斜度但模具则需设计侧抽芯结构模具结构复杂成本高39 在零件功能和外观等允许情况下零件脱模斜度尽可能取大310 脱模斜度的大小与方向不能影响零件的功能实现4 加强肋的设计41 加强筋的厚度不应该超过塑胶零件厚度的506042 加强筋的高度不能超过塑胶零件厚度的3倍43 加强筋根部圆角为塑胶零件厚度的02505倍44 加强筋的脱模斜度一般为051545 加强筋与加强筋之间的距离至少为塑胶零件厚度的2倍46 加强筋的设计需要遵守均匀壁厚原则47 加强筋的顶端增加斜角避免困气48 加强筋的方向与塑胶溶料的流向一致5 支柱的设计51 支柱的外径为内径的2倍52 支柱的厚度不超过零件厚度的06倍53 支柱的高度不超过零件厚度的5倍54 支柱的根部圆角为零件壁厚的02505倍55 支柱根部厚度为零件壁厚的07倍56 支柱的脱模斜度一般内径025外径0557 保证支柱与零件壁连接58 单独的支柱四周增加加强筋补强59 支柱的设计需要遵守均匀壁厚原则6 孔的设计61 孔的深度不能太深若太深采用阶梯孔成型62 避免盲孔不通孔底面太薄63 孔与孔的间距及孔与零件边缘尺寸避免太小64 零件上的孔尽量远离零件受载荷部位65 可以在孔的边缘增加凸缘增加孔的强度66 避免与零件脱模方向垂直的侧孔67 长孔的设计避免阻碍塑胶溶料的流动68 风孔的设计7雕刻文字符号及花纹71 塑胶部品种超过20g以上的部品必须追加材质标识72 雕刻区通常要求咬薄薄的花纹HT106目的避免在塑胶成型时出现流痕73 雕刻文字符号及花纹设计指南8 提高塑胶件强度的设计81 通过添加加强肋而不是增加壁厚来提高零件强度82 加强肋的方向要考虑载荷的方向83 多个加强肋的方向比单个较厚或较高的加强肋好84 设计零件增强剖面85 增加侧壁和优化侧壁剖面形状来提高零件强度86 避免零件应力集中87 合理设置浇口避免零件在熔接痕区域承受载荷88 其它方法9 提高塑胶件外观的设计91 选择合适的塑胶材料92 避免零件外观表面缩水921 合适的零件壁厚922 通过设计掩盖缩水923 合理的浇口位置93 预测零件变形设计减少变形94 外观零件之间设计美工沟95 避免外观零件表面出现熔接痕951 塑胶件表面咬花可以部分掩盖熔接痕但并不能完全掩盖熔接痕952 喷漆可以掩盖熔接痕953 合理设置浇口的位置和数量避免在零件重要外观表面产生熔接痕954 保证模具通风顺畅96 合理选择分模线避免零件重要外观面出现断差或者毛边97 顶针避免设计在零件重要外观面10 降低塑胶件成本的设计101 设计多功能的零件102 降低零件材料成本103 简化零件设计降低模具成本104 避免零件严格的公差105 零件设计避免倒扣1051 避免零件内部侧凹1052 避免零件外部侧凹1053 避免抽芯机构受阻106 降低模具修改成本106 1 零件的可注射性设计1062 减少产品设计修改次数1063 避免添加材料的模具修改107 使用卡勾代替螺丝等固定结构108 合理选择模具穴数和冷热流道系统109 零件外观装饰特征文字和符号宜向外凸出1010 设计零件和模具使得浇口能够自动切除或者把浇口隐藏在产品内部避免对浇口二次加工1011 把分型面隐藏在产品内部避免对分型面二次切除加工11 注塑模具可行性设计111 卡扣等结构应为斜销或滑块预留足够的退出空间112 避免模具出现薄铁以及强度太低的设计塑胶件的装配1 卡扣装配11 卡扣的尺寸12 卡扣根部增加圆角13 卡扣均匀分布14 使用定位柱辅助卡扣装配和提高装配精度15 卡扣设计避免增加模具复杂度16 考虑模具修改方便性2 机械紧固自攻螺钉21 装配次数22 支柱的内径和外径23 螺牙咬合长度不少于2倍螺钉公称直径24 支柱的深度至少比螺钉长度高05毫米25 支柱顶部增加斜角或沉孔26 支柱四周增加加强筋根部添加圆角27 合理的驱动扭矩3 超声波焊接将结构后注推书塑胶件DFMA表格1 塑胶件设计检查2 塑胶件装配方式设计检查塑胶件公差标准1 尺寸公差2 角度公差3 形位公差4 表面粗糙度本章目的:设计符合注射(塑胶)工艺的零件,不再犯简单错误,不必再为反复修改模具而烦恼。
塑胶产品设计方法及注意事项

第六章塑料件设计工艺塑胶件设计一般步骤塑料件是在工业造型的基础上进行的结构设计,首先看有无相似的产品借鉴,再对产品及零件进行详尽的功能分解,确定零件的折分、壁厚、脱模斜度、零件间的过渡处理、连接处理、零件的强度处理等主要工艺问题。
1)相似借鉴在设计前,首先应查找公司和同行类似的产品,原有的产品发生过那些问题,有那些不足,参考现有的成熟结构,避免有问题的结构形式。
2)确定零件折分、零件间的过渡、连接、间隙处理从造型图和效果图理解造型风格,配合产品的功能分解,确定零件折分的数目(不同的表面状态要么分为不同的零件,要么在不同的表面之间须有过度处理),确定零件表面间的过度处理,决定零件之间的连接方式,零件之间的配合间隙。
3)零件强度与连接强度的确定根据产品大小,确定零件主体壁厚。
零件本身的强度,由壁厚塑料件、结构形式(平板形状的的塑料件强度最差)、加强筋与加强骨共同决定。
在决定零件的单个强度的同时,须确定零件之间的连接强度,改变连接强度的方法有,加螺钉柱,加止口,加扣位,加上下顶住的加强骨。
4)脱模斜度的确定脱模斜度要根据材料(PP,PE硅胶,橡胶能强行脱模)、表面状态(饰纹的斜度要比光面的大,蚀纹面的斜度尽可能比样板要求的大0.5度,保证蚀纹表面不被损伤,提高产品的良品率)、透明与否决定零件应有的脱模斜度(透明的斜度要大)等因素综合确定。
公司不同的产品系列推荐的材料种类。
表6-1 不同塑料零件的推荐材料塑胶件的表面处理表6-2 塑料表面处理的选择塑胶件的工艺技术要求.塑胶件零件的壁厚选择塑胶件,对壁厚均匀性有要求,壁厚不均匀工件将有缩水痕迹,要求加强筋与主体壁厚的比值最好为0.4以下,最大比值不超过0.6.塑胶零件的脱模斜度在立体图的构建中,凡影响外观,影响装配的地方需要画出斜度,加强筋一般不画斜度。
塑胶零件的脱模斜度由材料,表面饰纹状态,零件透明与否决定。
硬质塑料比软质塑料的脱模斜度大,零件越高,孔越深,斜度越小。
Plastic Parts Design Guide(塑料零件设计指南)

Sinks
Sink
Improved Sinks 槽优化
36
Grained or
Stippled
Surface
Tooled Depression
Offset at Rib
Sinks
Ribs Design 筋设计
37
should be improved
Better
Best
Good Design, Strength
Flow Direction
Gate
Transverse Direction
Glass Fiber Resists Shrinkage in Direction of Alignment/Flow
Gate Location & Shrinkage
浇口位置和收缩率
8
Mineral Reinforced
Shrinkage & Warpage收缩和翘曲
13
Case on a ‘plate + rib’ profile
b
a
Gate L
h w
Gate
Flow angle Isochrones
Shrinkage & Warpage 收缩和翘曲 Glass reinforced materials
Deformation trend
45
Good Design, Example
好的设计,例如:
46
Steel
Plastic
Good Design, Example
好的设计,例如:
47
48
THANKS
22C
530
Flow Direction Knit Line
塑胶件设计指导
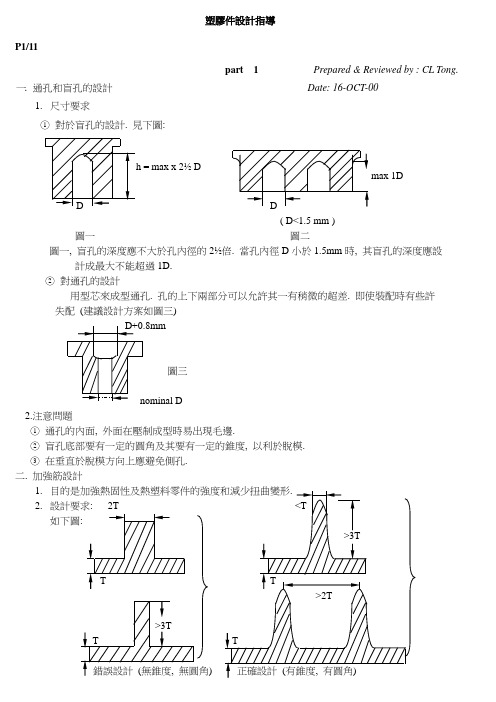
塑膠件設計指導P1/11part 1 Prepared & Reviewed by : CL Tong.一. 通孔和盲孔的設計 Date: 16-OCT-001. 尺寸要求○1 對於盲孔的設計. 見下圖:max 1D( D<1.5 mm ) 圖一圖二圖一, 盲孔的深度應不大於孔內徑的2½倍. 當孔內徑D 小於1.5mm 時, 其盲孔的深度應設計成最大不能超過1D.○2 對通孔的設計用型芯來成型通孔. 孔的上下兩部分可以允許其一有稍微的超差. 即使裝配時有些許 失配 (建議設計方案如圖三)圖三2.注意問題○1 通孔的內面, 外面在壓制成型時易出現毛邊. ○2 盲孔底部要有一定的圓角及其要有一定的錐度, 以利於脫模. ○3 在垂直於脫模方向上應避免側孔. 二. 加強筋設計1.2. 設計要求: 2T 如下圖)圖四P2/11 圖四中, 加強筋根部的厚度應不大於所要加強部分壁厚T, 筋高度應大於3T, 而筋與筋之間的距離(筋中心線與筋中心線之間) 應大於2T.3.注意問題○1多根加強筋設計其效果優於單根加強筋(即使你增大其厚度或高度)○2筋的根部要有一定的圓角, 要有一定的錐度, 以利於脫模.○3加強筋的方向應跟模壓, 成型, 熔料流動方向相一致.三.击台1.目的: 增強孔的穩固及強度或裝配附件之用.2.設計要求圖五圖六击台高度最大不超過击台根部尺寸D的二倍, 击台根部外徑與內徑之差的一半應為0.8T如圖五. 击台跟平面相裝配時, 击台須設計在成型件的四周. 且其高度如圖六所示應為0.4mm. 如果A外平面的平面度要求較高. 還需要打磨.3.注意問題○1击台根部要有一定的圓角和其要有一定的錐度, 以利於脫模.○2當击台高度過高時, 可在击台外部加加強筋, 不僅可以增大击台強度. 而且還有利於促進熔爐塑料的流動.四.錐度設計1.含義: 由於成型時零件內外表面收縮率不一致, 在設計時, 根據塑料對型蕊的粘附力要大於對型腔的粘附力, 設置內表面錐度大於外表面錐度.2.注意問題○1成型件設計要有一定錐度是有利於脫模.○2同樣有利於減少成型過程中瑕疵的形成.五.螺紋的設計(熱固性塑料)塑料螺紋包括螺紋孔和螺牙.1.如下圖○1螺牙要圓, 不宜尖.○2螺紋長度要短.2.如下圖P3/11, 螺紋的中心線位於分型面上.3.螺牙角選擇為32º4.採取成型後再加工螺紋方式去獲取塑料螺紋.5.當螺紋孔要多次裝配時, 建議使用內嵌件.六.嵌件1.要求:○1在塑膠件成型之後. 立即把嵌件壓制到膠件上. 讓包圍著嵌件的部分收縮而來緊嵌件.○2外部嵌件會因為合成物料的收縮而松軟, 內部嵌件會因它的收縮而破裂. 所以在設計嵌件時應考慮配套零件的壁厚,嵌件包圍部分壁厚設計參考表6.1-3.(略)2.注意問題○1用模具壓制嵌件時, 易出現嵌件由於圍壁出現收縮而松動又或者壁易出現斷裂現象.七.平面度由於在成型時易混入氣泡等使熱固性塑料出現收縮現象. 要獲得良好的平面度十分不易的. 通常要求表面留有0.3%的余量.八.零件圖:最終零件圖要指出, 哪一個地方不可以出現分型線. 不可以出現澆口痕, 哪一個地方需要印上模號和模具標記. 哪一個表面出現缺點不能接受等等. 使用SPI/SPE的配套完模工具作為指導.這樣做的目的是易於發現問題和解決問題.九.尺寸因素熱固性塑料成型件尺寸精度可以達到要求公差. 但是, 其精度難以跟加工金屬零件相提並論.造成這樣的原因是:1.塑膠料的收縮率(在成型中).2.成型後塑膠料的收縮率.3.時間, 溫度, 壓力(成型條件)4.模具類型.5.射出及預成型尺寸.6.熔料的流量變異.7.塑膠料種類.十.公差尺寸公差表參考表6.1.4(略)P4/11PART 2一. 注射成型過程○1粒狀塑膠料加入到料斗在180℃高溫下隔熔成液體狀. (熔化的溫度同塑膠料的種類和成型條件有關) 進入鋼模, 被水冷卻成固體狀(水在模外) 取零件.○2整個過程周期為45秒. 壓力為70,000Kpa, 大部分時間用於冷卻.二. 注射成型件的典型特徵及發展趨勢.注射成型適用於大批量複雜零件的生產. 雖然其仍然有極多局限性, 但由於一個注射成型產品可以代替裝配出來的產品, 所以, 其經濟性很好, 另外, 由於顏色, 形狀可以一次性成型做到, 免去二次加工.○1主要特徵:I. 廣泛應用於薄壁零件, 但也可以成型大塊及不同壁厚的零件.II. 強度低, 適用於外殼, 連接桿等受力較小的場合.○2發展超勢熱塑性材料強度會變得越來越大, 機械特性越來越好, 一些類似尼龍, 複合碳酸鹽等,其強度可以同鐵, 鋁, 甚至鋼相比美.PART 3 P5/11一. 收縮率的影響1.啤模時會產生許多不規則或拗曲的形狀, 常見的有夾水紋, 縮水等, 它們常發生在零件較厚的部位.(如圖七)圖七2.另一種經常產生的缺限就是“U”型楔面收縮(如圖八). 第三種情況就是在左右平面收縮變形. (如圖九) 方向易產生平面出現固收縮而引起的曲線.圖八圖九二. 經濟的生產數量注射模適用於量生產的, 一般不會用此方式, 除非有上萬或者更多零件要生產. 之所以有此限製是因為每種零件都需做一個自己獨有的模.只有大量生產開模的經費才能在批量生產中收回, 即便是很小的零件都要花幾千元的開模費. 那些較大較複雜的零件就更會花上萬乃甚至十萬元的經費.三. 合適的原料多種合適的熱熔膠可用於注射模生產. 常用的有聚乙烯﹑PVC﹑尼龍﹑ABS﹑等.注射模在熱塑模市場有很重要的地位, 因此工程人員必須設法使之更利於生產. 物理特性及價格常是選擇這些材料時比加工性能更為重要的因素.通常, 高性能的工程塑料往往比日常使用的塑料像PE料, PP料, PS料等之類更難開模, 特別是PVC雖具有價廉和高性能的優點, 但卻比一般塑膠更難注塑, 最主要的缺點是它的熔點到凝固溫度範圍太窄.表6-2-2列出了一些常用的注塑材料及其特性, 價格和使用範圍. (略)四. 設計指南1.水口及頂針位:設計者須考慮它們的方位, 因為它們會對表面成型產生影響. 如果注件有內外側的話, 水口常開在下側. 水口一般的方位見圖6-2-6(略) 圓形或圓柱型注件的中央水口或者近於中央水口(較大面積的注件)在注塑時是最理想的安全模塑頂料方式.2.注件厚度:表6-2-3 列出了注件厚度的正常值及下限(略), 表明了塑料在注塑完工以前它在模件中冷卻和固化的趨勢, 塑料流動愈緩慢, 則注件厚度要求愈窄, 當然注件的厚度要盡可能的一致. 即便是不得已要改動厚度, 最好變動要舒緩, 不突變.(如圖十)圖十P6/11錯誤設計 正確設計錯誤設計 稍好設計 最好設計3. 孔的設計● 注塑件開孔雖可行卻是開模最複雜的一個因素. 孔周圍易產生飛邊以及 “夾紋” 或是 “夾水weld line圖十一●兩孔間距或是孔到邊的距離至少要有一個孔徑. (如圖十二)錯誤設計 正確設計 圖十二●為避免外應力的影響,單孔必須開在距注件邊緣三個或以上孔徑的地方.(如圖十三)P7/11正確設計錯誤設計圖十三●通孔較盲孔好, 因為做孔所用到的頂針可以在兩頭加以固定, 這樣做出的孔位置尺寸很標準而且可以避免彎曲或折斷.●在注件底部開孔較在邊上開孔好, 因為後者須要可折卸頂針.●盲孔深度須小於兩孔徑之和, 若孔徑為1.5mm或更小, 那麼其深度最小應有一個孔徑. (如圖十四)大孔小孔圖十四●利用击台可以增加盲孔深度, 這須用到較硬的頂針(型蕊). (如圖十五)錯誤設計正確設計圖十五●切去通孔零件兩端的部分可縮短頂針(型蕊)的長度. (如圖十六)錯誤設計正確設計(此設計可降低心棒受損危險性)圖十六4.加強筋●加強筋必須比注件的厚度薄一些, 防止注件表面縮水. 比較好的方法是保證加強的寬度為注件厚度的一半或更少.P8/11●同樣為避免縮水, 加強筋高度須不大於壁厚的1.5倍.●如果有必要, 可以用兩個筋位去加強注件強度用以代替一個更高的筋位的作用.這些筋位須以兩個或以上壁厚的距離分散開來.●為使注件順利地從模中取出, 加強筋必須與注件方位垂直.●由加強筋引起的縮水可以通過在其對面增加凹槽的方法加以減輕和去除. (如圖十七)蝕紋錯誤正確正確正確圖十七●加強筋的設計規則如圖十八.錯誤設計正確設計5.击台: 主要用於塑件的表面突起.●它必須有較大的半徑和圓角.●在加強筋中說明過的原則同樣適用於击台一節. 圖十九表明了固體击台的最大高度和寬度.圖十九●如果可能, 將击台做至邊角處可有助於充模時塑料的流動, 若有必要, 在做可拆裝的击台時,加個聯接筋位將有助於塑膠充模.●如果可能, 盡力避免在罐上部做击台, 因為這將會產生更多氣泡.P9/11●在击台上採用5°錐度, 其設計與加強筋相同.●如果較大的击台要用到, 那必須是中空, 且與塑件厚保持一致.6.凹槽凹槽在注塑中同樣會用到, 只是他們要用到滑動型蕊和分模方式, 凹槽可開在注件的分型線或其延長線方向上, 以避免型心的拉力作用. 凹槽可以不依靠型蕊的拉力即可較容易的脫模. 如果凹槽被移除, 則另一半模必定會保持完好. 那麼頂針(型蕊)將被用於脫模. 凹槽的一般設計尺寸如圖二十.7.螺紋設計螺紋成型盡管很複雜, 但卻是可以辦到的可使用以下三個方法:●螺紋成型後使用旋轉型蕊. 可以使模件順利地從模中取出.●令螺絲軸線與分型面一致. 這樣可避免用到旋轉型蕊, 且可以在模型間得到更好的配合以減少螺紋上的流痕. 這種方案僅用於外部螺紋制作, 且成本昂貴, 除非螺紋可以遠離分型面,而通常這也是可行的. 如果這種方法不適用, 另一種可能的方式將被要求用來移除分型面在螺紋上產生的流痕.●減少螺紋齒數, 降低螺牙高度, 零件可以直接從模腔中脫出而不須從製品中擰下來. 螺牙未端不宜延長到與垂直底面相接處, 否則易使脆性塑料件發生斷裂, 螺紋的始端均不應突然開始和結束, 而應有過渡部分. 因為它方便取出而且避免了多余的飛邊, 以致模件很難配合,甚至生成流痕. 如果是剛性螺紋, 必須使用金屬模蕊.P10/11PART 4原始設計改善設計(增強強度)有時候為了確保產品具有足夠的強度有必要修改設計方案. 防止縮水方法之一是在部件易於受影響的表面加鋸齒狀的骨位.標準的外形為模具工業的發展所需要, 因為它便宜, 且易於採購. 如果有仍何可能我們寧可用標準件, 這對於大現模生產尤其顯得重要.※擠出材料熱熔物的選擇非常重要, 特別是對一種新技術, 新產品. 高強度的苯乙烯是一種最易擠出的塑膠, 纖維與丙烯居其次, 最難擠出的材料為尼龍. 軟塑料不如硬塑料易於擠出到一個細小公差, 快速冷卻會產生內應力並導致裂紋生成. 透明材料(如: PE; 尼龍; VC和PP)常在冷水中冷卻.通過不平衡壓模ABS和PS較PE, PP料易擠出成型. 後者比前者具有更低的熔解強度和更易改變的條件(測試條件易控制).如果採用“雙料擠塑”的材料不同, (除外)那它們之間的結合可能是不完整的. 完全不同的材料連接在一起要通過凹槽. 燕尾槽或機械連接. 當要對不同的塑料作雙料擠塑時一定要考慮材料間的相容性.例如: 增型擠塑乙烯基就與PS不相容.※材料的特點:1.ABS--- 硬性好, 易出模可調任何顏色. 可塑出任何複雜外形. 公差控制水平較高. 用於房屋, 門柱手柄等.2.CA--- 價廉, 通用硬性要求高或較高產品. 顏色可任何意調製. 耐氣候性差, 須涂上防護油, 汽油和大量清潔液體. 易清洗, 斷面較薄.3.CAB--- 與2 類同,但有更好的耐熱與氣候浸蝕性氣味難聞. 顏色可隨意配製, 用於標志倍存.4.CP--- 與3相似只是沒有怪味.5.EC--- 硬性彈性好, 易出模. 公差易控制. 低溫下穩定. 用於膠管刀刃及裝飾部件.6.EV A--- 柔性好, 可配製任何顏色. 外形單調. 用於低性能小五金. 印章, 墊圈等.7.尼龍--- 體輕, 很高的延伸性, 僅用於較單一的外形產品. 對公差要求不高. 凝固速度快. 很好的吸水性. 用於膠管, 路標, 摩擦溝道等.8.PC--- 最好的整體平衡性. 用於製造標準的外形. 公差控制容易. 較貴. 須特別處理, 但其吸水性,導熱性差. 用於燈罩, 消毒櫃等.9.PE--- (高密度)比低密度的PE更加堅硬, 公差難控制. 用於皮帶, 棍棒等.10.PE--- (低密度)較軟, 難以成型. 很好的非導電性,室溫下即能溶解. 用於膠管, 手柄, 緩沖器等.11.PP--- 很輕,標準公差控制. 不適用於複雜的外形. 可調多種顏色. 用於高性能絞鏈樞扭, 滑動導架等.12.PS--- 價廉, 適用於任何顏色, 易碎, 擠塑有限製. 用於燈罩等.13.PS--- 高彈性, 堅硬, 低價. 用於複雜外形. 標準公差控制. 顏色不限. 用於滑動門的導架等.14.PVC--- (柔軟) 通用於各種硬度. 標準的複雜外形. 標準的公差控制.用於各種顏色, 常用於進氣口, 密封圈.P11/1115.PVC--- (硬) 易出模, 可用於複雜外形, 優良的非導電性特性.公差控制容易. 有顏色限製. 常用於導電體的殼和蓋.16. PN--- 可用於各種硬性可調出, 用於各種顏色. 耐磨性好, 常用於傳送帶.17. VD--與15相似. 其非導電特性比PVC(硬)更加好. 複雜的外形, 優良的公差控制特性. 可擠塑出任何顏色. 用於製做熱水管, 高溫涂藥器等.PART 5一.影響尺寸的因素:盡管模塑零件能夠保證這種變異的緊配合公差, 但是對可獲得一定精度的金屬零件之尺寸卻不能保證原因有以下幾種:1.材料收縮力, 包括材料收縮過程中的均勻和不確定性.2.塑料有高的熱膨脹系數, 因此, 如果公差定得過大或過小, 設計者就應定出溫度並采取測量措施.3.盡管有對壓力, 溫度, 時間設定作自動調節的設備, 但這些因素在從一次注塑到另一次注塑間都會有一些變化, 這些變化的結果導致模塑零件輕微的尺寸變化.4.塑料零件通常較金屬零件有較大的柔軟性.由於柔軟因素的存在使得塑膠零件的緊配合無多大必要. 裝配時, 如果有必要去確保一個好配合常可通過零件輕微的變形達到. 如有必要, 明智的設計者可利用設計塑膠零件的击台和击緣去確保與相配零件表面的對稱.與其它過程相比, 緊配合會大大的增加注塑模零件的成本, 精密(公差)模具比粗製(公差) 模具的成本更高, 正如當零額外的緊配合時就會導致加工成本的增加, 例如, 須為壓力, 溫度和循環時間增加相關過程控制, 因而也許會增加循環時間或需要膠件出模後的熱套裝置, 廢品率也更高.不同的塑料材料有不同的公差特性, 低收縮率材料能以相應公差被恆定的注塑, 玻璃或礦物填充材料的注塑比非填充材料更精確. 更多模腔數的使用導致降低所注塑零件控制尺寸的精確. 根據以往經驗, 對每個模腔在第一次啤塑之後的尺寸允差都應增加5%, 例台, 一單模腔在某一尺寸具有±0.1mm的允差;在模腔長為10應有±0.15mm (0.006in) 的允差(公差增加10x5percent=50%).表 6.2.4(略)及6.2.5(略)為不同塑料材料的尺寸公差的建儀值, 這些表格數據, 是由塑膠工業行業提供數據所歸納出的. 代表了以往和現在塑膠模工業的發展成果, 個別模廠的合同形式和協議所規定的也許有變化.。
《专业齐全的塑胶卡扣设计指导》PPT课件

塑膠扣形狀的設計多樣性
塑膠扣的種類 在生活中常用的塑膠卡扣大致上可分為三大類
縣臂式卡勾
圓環形卡勾
球形卡勾
縣臂式塑膠卡勾又可分為兩大類,恆截面與變截面卡勾
以下是第一種恆截面的卡勾的示意圖,它的截面是無變化的規則矩形。
如果在此卡勾的材料物理特性知道的情況下,最大允許變形量 y 和被迫變形力Fb 可 以用以下公式計算出來的。
卡勾的設計對成品結構的影響
因為斜頂退位的原因,挨近角落的卡勾孔不可能都挨近拐角,但盡 可能把其中一處卡扣靠近拐角處,另一邊卡勾孔避開斜頂孔退位即 可,這樣才能避免組裝間隙和落摔不過等問題
斜頂的退位
斜頂的退位
卡勾的設計對成品結構的影響
卡槽避空的位置盡量不要做在兩個電池相 接的地方,這樣容易造成直邊凸起
专业齐全的塑胶卡扣设计指导
(Suitable for teaching courseware and reports)
塑膠卡扣應用的優點
◆ 無需其它材料,降低產品成本 ◆ 操作簡單 ◆ 有替代螺絲,螺母,華司等昂貴金屬件的功能 ◆ 適應如一般塑膠件的組裝 ◆ 沒有像焊接與點膠的復雜操作技術要求 ◆ 一些塑膠產品能重復撤裝利用
縣臂式不規則恆截面塑膠卡勾結構的基本原理 其它各式截面的臂
以下公式是適應於臂為不規則截面(但為不變化的)的懸臂式卡勾的計算方式
Es=相交系數 L=臂的長度 I=當前截面的慣性 e=中心到外形的距離 ε=是材料充許最大的變形度
縣臂式不規則恆截面塑膠卡勾結構的基本原理
縣臂式變截面塑膠卡勾結構的基本原理
卡勾的設計對成型的影響
此種卡扣是在上一種卡扣的基礎上演變而來,它的優點是強度很大,充型較上面容易 它的不足點是,厚度增厚,容易縮水導致外觀不良。
塑料产品设计指南
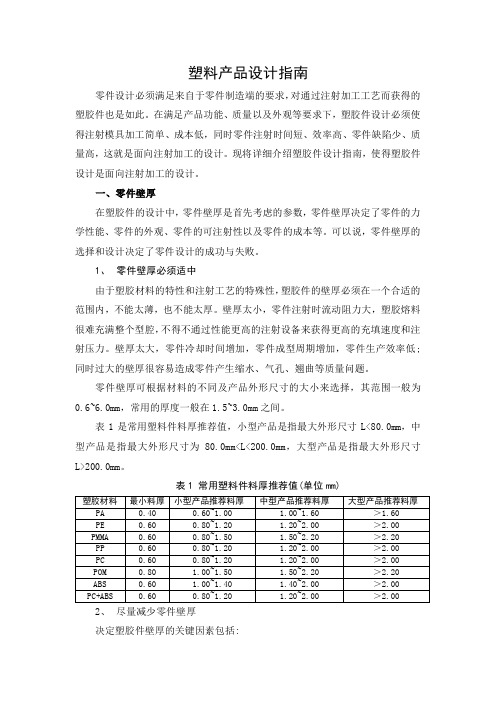
塑料产品设计指南零件设计必须满足来自于零件制造端的要求,对通过注射加工工艺而获得的塑胶件也是如此。
在满足产品功能、质量以及外观等要求下,塑胶件设计必须使得注射模具加工简单、成本低,同时零件注射时间短、效率高、零件缺陷少、质量高,这就是面向注射加工的设计。
现将详细介绍塑胶件设计指南,使得塑胶件设计是面向注射加工的设计。
一、零件壁厚在塑胶件的设计中,零件壁厚是首先考虑的参数,零件壁厚决定了零件的力学性能、零件的外观、零件的可注射性以及零件的成本等。
可以说,零件壁厚的选择和设计决定了零件设计的成功与失败。
1、零件壁厚必须适中由于塑胶材料的特性和注射工艺的特殊性,塑胶件的壁厚必须在一个合适的范围内,不能太薄,也不能太厚。
壁厚太小,零件注射时流动阻力大,塑胶熔料很难充满整个型腔,不得不通过性能更高的注射设备来获得更高的充填速度和注射压力。
壁厚太大,零件冷却时间增加,零件成型周期增加,零件生产效率低;同时过大的壁厚很容易造成零件产生缩水、气孔、翘曲等质量问题。
零件壁厚可根据材料的不同及产品外形尺寸的大小来选择,其范围一般为0.6~6.0mm,常用的厚度一般在1.5~3.0mm之间。
表1是常用塑料件料厚推荐值,小型产品是指最大外形尺寸L<80.0mm,中型产品是指最大外形尺寸为80.0mm<L<200.0mm,大型产品是指最大外形尺寸L>200.0mm。
表1 常用塑料件料厚推荐值(单位mm)2、尽量减少零件壁厚决定塑胶件壁厚的关键因素包括:1)零件的结构强度是否足够。
一般来说,壁厚越大,零件强度越好。
但零件壁厚超过一定范围时,由于缩水和气孔等质量问题的产生,增加零件壁厚反而会降低零件强度。
2)零件成型时能否抵抗脱模力。
零件太薄,容易因顶出而变形。
3)能否抵抗装配时的紧固力。
4)有金属埋入件时,埋入件周围强度是否足够。
一般金属埋入件与周围塑胶材料收缩不均匀,容易产生应力集中,强度低。
5)零件能否均匀分散所承受的冲击力。
塑胶件结构设计培训教材1

14/60
三、加强筋
塑料的强度并不依其壁厚之增大而增大。反 之,由于壁厚增大而际致收缩时产生内应力, 反而降低其强度。塑料制件的强度以刚度为主。 应采取薄壁的网格组合结构。在薄壁的基础上, 于相应的部位设置加强筋,以提其截面的惯性 矩,是较好的方法。 由于加强筋与本体作垂直相贯,其衔接处的 厚度增大,以致于该处收缩凹陷,影响强度及 外观。
29/60
表2-9 孔径与孔深的关系
孔的形式 成形方式 压 塑 横 孔 竖 孔 挤 塑 或 注 射 孔的深度 通 孔 2.5d 5d 10d 不 通 孔 <1.5d <2.5d 4~5d
注:1、d为孔的直径。 2、采用纤维状塑料时,表中数值乘 系数0.73 0 73。计的工艺要求
第一节 塑件几何形状
一、塑件的壁厚 塑件的壁厚首先决定于塑件的使用要求,即 强度、结构、重量、电气性能、尺寸稳定性 以及装配等各项要求。 另外还应尽量使其各部壁厚均匀,避免太薄, 会引起收缩不均匀使塑件变形或产生气泡、 凹陷等成形工艺问题。
4/60
塑件壁厚一般在1~6mm范围内。而通常 1 mm 取值为2~3mm。大型塑件的壁厚也有至 mm。 2 mm或更大的,这都随塑料类型及塑件 6mm 大小而定。表1-1列出热塑性塑料制品 的最小壁厚及常用壁厚推荐值。
良 不良 说 明 当相邻两孔 接近时,应 设计成长孔 如该孔为固 定用孔,孔 周应设凸台
31/60
良
不良
说 明 固定用螺帽 钉孔,如不 需要露出螺 帽钉头时, 应使用螺帽 钉、孔做成 沉头孔而不 用锥孔
32/60
良
不良
说 明 对穿孔应 注意设计 成能设置 型芯的结 构
33/60
表2-11 复杂孔的成形方法 与设计关系
- 1、下载文档前请自行甄别文档内容的完整性,平台不提供额外的编辑、内容补充、找答案等附加服务。
- 2、"仅部分预览"的文档,不可在线预览部分如存在完整性等问题,可反馈申请退款(可完整预览的文档不适用该条件!)。
- 3、如文档侵犯您的权益,请联系客服反馈,我们会尽快为您处理(人工客服工作时间:9:00-18:30)。
塑胶件设计指导宝典
一、塑胶件结构设计基本原则:
▶结构设计要合理:装配间隙合理,所有插入式的结构均应预留间隙;保证有足够的强度和刚度(安规测试),并适当设计合理的安全系数。
▶塑件的结构设计应综合考虑模具的可制造性,尽量简化模具的制造。
▶塑件的结构要考虑其可塑性,即零件注塑生产效率要高,尽量降低注塑的报废率。
▶考虑便于装配生产(尤其和装配不能冲突)。
▶塑件的结构尽可能采用标准、成熟的结构,所谓模块化设计。
▶能通用/公用的,尽量使用已有的零件,不新开模具。
▶兼顾成本
二、塑胶件基础结构设计指南
1.零件壁厚
①合适的壁厚
塑胶产品的胶厚(整体外壳)通常在0.80-3.00左右, 壁厚太小:强度低;流大,熔料难充满; 壁厚太大:零件产生加,成型周期加长,零件生产效率低;(请关注weixin:shujishi1818)
常用塑胶材料合适壁厚范围(单位mm):
②尽量减少零件壁厚,决定零件壁厚的因素如下:
▶零件的强度要求;
▶零件成型时能否抵抗脱模力;
▶零件能够抵抗装配时的紧固力;
▶有金属埋入件时,埋入件周围强度是否足够;
▶孔的强度是否足够;
▶错误的做法:为提高零件强度,片面的增加零件壁厚。
③零件壁厚均匀
尽可能采用多种方法使壁厚保持均匀:
当壁厚不均匀时:
2. 圆角设计
在塑件设计过程中,为了避免应力集中,提高塑件强度,改善塑件的流动情况及便于脱模,在塑件的各面或内部连接处,应采用圆弧过度。
另外,塑件上的圆角对于模具制造和机械加工及提高模具强度,也是不可少的。
在塑件结构上无特殊要求时,塑件的各转角处均应有半径不小于0.5~1mm的圆角。
允许的情况下,圆角应尽量大。
对于内外表面的拐角处,外圆角应为内圆角加壁厚,可减少内应力,并能保证壁厚均匀一致。
(请关注weixin:shujishi1818)
①避免零件外部尖角
②避免在塑胶熔料流动方向上产生尖角
③避免在零件连接处产生尖角
3. 脱模斜度
一般来说,对模塑产品的任何一个侧面,都需有一定量的脱模斜度,以便产品从模具中顺利脱出。
脱模斜度的大小一般以0.5度至1度间居多。
具体选择脱模斜度注意以下几点:
▶塑件表面是光面的,尺寸精度要求高的,收缩率小的,应选用较小的脱模斜度,如
0.5°。
▶较高、较大的尺寸,根据实际计算取较小的脱模斜度,比如双筒洗衣机大桶的筋板,计算后取0.15°~0.2°。
▶塑件的收缩率大的,应选用较大的斜度值。
▶塑件壁厚较厚时,会使成型收缩增大,脱模斜度应采用较大的数值。
▶透明件脱模斜度应加大,以免引起划伤。
一般情况下,PS料脱模斜度应不少于2.5°~3°,ABS及PC料脱模斜度应不小于1.5°~2°。
▶带皮纹、喷砂等外观处理的塑件侧壁应根据具体情况取2°~5°的脱模斜度,视具体的皮纹深度而定。
皮纹深度越深,脱模斜度应越大。
▶结构设计成对插时,插穿面斜度一般为1°-3°。
(请关注weixin:shujishi1818)
4. 脱模斜度的大小与方向不能影响零件的功能实现:
5. 加强筋的设计
塑胶产品大部分都有加强筋,因加强筋在不增加产品整体胶厚的情况下可以大大增加其整体强度,对大型和受力的产品尤其有用,同时还能防止产品变形。
加强筋的厚度通常取整体胶厚的0.5-0.7倍,如大于0.7倍则容易缩水。
加强筋的高度较大时则要做0.5-1.5的斜度(因其出模阻力大),高度较矮时可不做斜度。
6. 加强筋的设计原则:
①壁厚均匀:
②顶端增加斜角避免困气:
④筋的方向与塑胶熔料方向一致:
7. 孔的设计
从利于模具加工方面的角度考虑,孔最好做成形状规则简单的圆孔,尽可能不要做成复杂的异型孔,孔径不宜太小,孔深与孔径比不宜太大,因细而长的模具型芯容易断、变形。
①孔的深度尺寸:
②孔与孔的间距及孔与零件边缘尺寸:
③避免盲孔根部太薄:
③零件上的孔尽量远离受载荷部位:
④孔的边缘增加凸缘增加孔的强度:
⑤避免与零件脱模方向垂直的侧孔:
8. 支柱的设计
①壁厚均匀:
②保持与零件璧的连接:
③单独支柱四周增加加强肋:
三、提高塑胶件强度的结构设计指南
1.通过添加加强肋而不是增加壁厚来提高零件强度:
2.加强肋的方向要考虑载荷的方向:
3.多个加强肋的方向比单个较厚或较高的加强肋好:
4.设计零件增强剖面:
5.增加侧壁:
6.避免零件应力集中;
7.避免零件在熔接痕区域承受载荷;
8.其它方法:
▶玻纤增强塑料常用来代替普通塑胶材料来提高塑胶件强度,需要注意的是玻纤增强塑胶只在玻纤的方向上提高零件的强度;
▶塑胶件承受压缩载荷的能力比承受拉伸载荷的能力强;
▶避免零件承受圆周载荷。
零件承受圆周载荷时,例如金属镶件处,很容易发生破裂而失效;
▶在承受冲击载荷时,保持零件剖面的完整性,避免在冲击载荷方向上零件剖面出现缺口和应力集中。
四、提高塑胶件外观的结构设计
1.选择合适的塑胶材料;
2.避免零件外观表面缩水
▶通过设计掩盖缩水;
▶ “火山口”设计;
3、避免零件外观表面缩水:
▶合理的浇口位置;
4.避免零件变形:
5.设计美工沟:
6.避免外观零件表面出现熔接痕:
▶塑胶件表面咬花可以部分掩盖熔接痕,但并不能完全掩盖熔接痕;▶喷漆可以掩盖熔接痕;
▶合理设置浇口的位置和数量,避免在零件重要外观表面产生熔接痕;▶保证模具通风顺畅。
F.避免外观零件表面出现断差或毛边;
五、降低塑胶件成本的设计
1.设计多功能的零件:
2.降低零件材料成本:
▶通过添加加强肋而不是增加壁厚的方法提高零件强度;
▶零件较厚的部分去除材料;C.简化零件设计,降低模具成本:KISS原则(Keep it simple, stupid),简单就是美!零件中的每一个特征必须有存在的理由,否则,该特征是能够去除的。
D.避免零件严格的公差:公差越严格,零件制造成本就越高;
3.零件设计避免倒扣:
▶有些外侧倒扣可以通过重新设计分模线而避免:
▶重新设计零件特征避免倒扣:
4.降低模具修改成本:
▶零件的可注塑性设计;
▶减少产品设计修改次数;
▶避免添加材料的模具修改;G.使用卡扣代替螺钉等固定结构。
六、注塑模具可行性设计
1.卡扣等结构应为斜销(或滑块)预留足够的退出空间:
2.避免模具出现薄铁以及强度太低的设计:
七、塑胶件的装配设计
塑胶件的装配各种装配方式的优缺点
1.卡扣装配
2. 卡扣设计指南
①卡扣的尺寸:
▶卡扣厚度t = 0.5~0.6T
▶卡扣的根部圆角Rmin = 0.5t
▶卡扣的高度H = 5~10t
▶卡扣的装配导入角α= 25°~ 35°
▶卡扣的拆卸角度β:β≈35°用于不需外力的可拆卸的装配;β≈45°用于需较小外力的可拆卸的装配;β≈80°~90°用于需很大外力的不可拆卸的装配;
▶卡扣的顶端厚度Y ≤ t
②卡扣根部增加圆角:
③卡扣均匀分布
▶均匀的设置在零件的四周,以均匀承受载荷
▶靠近零件容易变形的地方;
⑤使用定位柱辅助卡扣装配和提高装配精度:
⑥卡扣根部增加圆角:
⑥考虑模具修改方便性
▶卡扣尺寸一般会经过多次修改,可先做小,以保证修模的方便性
3. 机械紧固:自攻螺钉
▶自攻螺钉的种类:
A. 装配次数
装配次数一般不超过3次
B. 支柱的内径和外径
C. 螺牙咬合长度不少于2倍螺钉公称直径
D. 支柱的深度至少比螺钉长度高0.5毫米
E.支柱顶部增加斜角或沉孔。
D.支柱四周增加加强筋、根部添加圆角
E.支柱最常见的失效方式是支柱破裂
4. 超声波焊接:导熔线设计
▶正确的导熔线设计
▶设计定位特征
▶增加塑胶件焊接面与焊接头的面积
▶把近程焊接作为第一选择。