塑胶设计指南
产品结构设计04塑胶件设计指南

壁厚太大: 零件产生缩水、气孔和翘曲等质量问题; 零件冷却时间增加,成型周期加长,零件生产效率低; 零件用料增加,产品成本增加;
常用塑胶材料合适壁厚范围(单位mm):
PE PP Nylon PS AS PMM PVC PC ABS POM A
最小 0.9 0.6 0.6 1.0 1.0 1.5 1.5 1.5 1.5 1.5 最大 4.0 3.5 3.0 4.0 4.0 5.0 5.0 5.0 4.5 5.0
B.降低零件材料成本:
降低零件厚度; 通过添加加强肋而不是增加壁厚的方法提高零件强度;
零件较厚的部分去除材料;
C. 简化零件设计,降低模具成本:
KISS原则(Keep it simple, stupid),简单就是美! 零件中的每一个特征必须有存在的理由,否则,该特征是能够去除的。
D.避免零件严格的公差:
容易发生破裂而失效; 在承受冲击载荷时,保持零件剖面的完整性,避免在冲击载荷方向上
零件剖面出现缺口和应力集中。
36
8.提高塑胶件外观的设计
A.选择合适的塑胶材料; B. 避免零件外观表面缩水:
合适的零件壁厚; 通过设计掩盖缩水;
“U”形槽
“火山口”设计;
塑料件卡扣设计
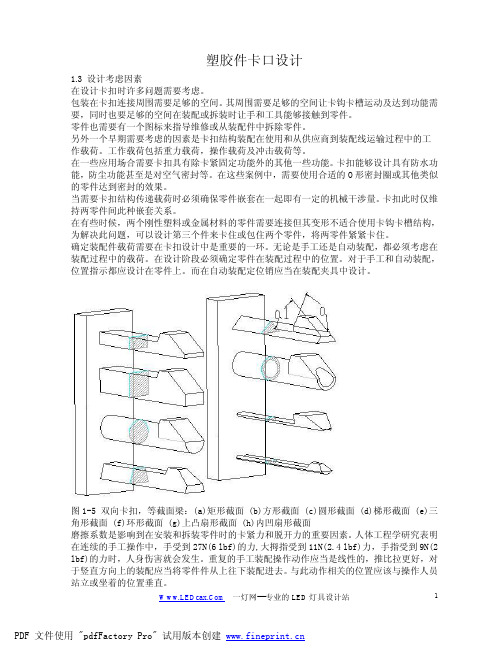
塑胶件卡口设计1.3 设计考虑因素在设计卡扣时许多问题需要考虑。
包装在卡扣连接周围需要足够的空间。
其周围需要足够的空间让卡钩卡槽运动及达到功能需要,同时也要足够的空间在装配或拆装时让手和工具能够接触到零件。
零件也需要有一个图标来指导维修或从装配件中拆除零件。
另外一个早期需要考虑的因素是卡扣结构装配在使用和从供应商到装配线运输过程中的工作载荷。
工作载荷包括重力载荷,操作载荷及冲击载荷等。
在一些应用场合需要卡扣具有除卡紧固定功能外的其他一些功能。
卡扣能够设计具有防水功能,防尘功能甚至是对空气密封等。
在这些案例中,需要使用合适的O形密封圈或其他类似的零件达到密封的效果。
当需要卡扣结构传递载荷时必须确保零件嵌套在一起即有一定的机械干涉量。
卡扣此时仅维持两零件间此种嵌套关系。
在有些时候,两个刚性塑料或金属材料的零件需要连接但其变形不适合使用卡钩卡槽结构,为解决此问题,可以设计第三个件来卡住或包住两个零件,将两零件紧紧卡住。
确定装配件载荷需要在卡扣设计中是重要的一环。
无论是手工还是自动装配,都必须考虑在装配过程中的载荷。
在设计阶段必须确定零件在装配过程中的位置。
对于手工和自动装配,位置指示都应设计在零件上。
而在自动装配定位销应当在装配夹具中设计。
图1-5 双向卡扣,等截面梁:(a)矩形截面 (b)方形截面 (c)圆形截面 (d)梯形截面 (e)三角形截面 (f)环形截面 (g)上凸扇形截面 (h)内凹扇形截面磨擦系数是影响到在安装和拆装零件时的卡紧力和脱开力的重要因素。
人体工程学研究表明在连续的手工操作中,手受到27N(6 lbf)的力,大拇指受到11N(2.4 lbf)力,手指受到9N(2 lbf)的力时,人身伤害就会发生。
重复的手工装配操作动作应当是线性的,推比拉更好,对于竖直方向上的装配应当将零件件从上往下装配进去。
与此动作相关的位置应该与操作人员站立或坐着的位置垂直。
理论上,两种材料之间的磨擦系数在0到1之间,并达不到0或1的情况。
塑胶结构设计规范
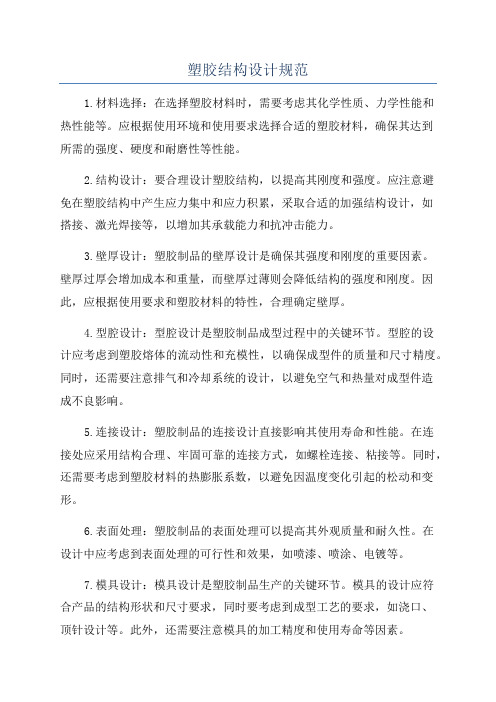
塑胶结构设计规范1.材料选择:在选择塑胶材料时,需要考虑其化学性质、力学性能和热性能等。
应根据使用环境和使用要求选择合适的塑胶材料,确保其达到所需的强度、硬度和耐磨性等性能。
2.结构设计:要合理设计塑胶结构,以提高其刚度和强度。
应注意避免在塑胶结构中产生应力集中和应力积累,采取合适的加强结构设计,如搭接、激光焊接等,以增加其承载能力和抗冲击能力。
3.壁厚设计:塑胶制品的壁厚设计是确保其强度和刚度的重要因素。
壁厚过厚会增加成本和重量,而壁厚过薄则会降低结构的强度和刚度。
因此,应根据使用要求和塑胶材料的特性,合理确定壁厚。
4.型腔设计:型腔设计是塑胶制品成型过程中的关键环节。
型腔的设计应考虑到塑胶熔体的流动性和充模性,以确保成型件的质量和尺寸精度。
同时,还需要注意排气和冷却系统的设计,以避免空气和热量对成型件造成不良影响。
5.连接设计:塑胶制品的连接设计直接影响其使用寿命和性能。
在连接处应采用结构合理、牢固可靠的连接方式,如螺栓连接、粘接等。
同时,还需要考虑到塑胶材料的热膨胀系数,以避免因温度变化引起的松动和变形。
6.表面处理:塑胶制品的表面处理可以提高其外观质量和耐久性。
在设计中应考虑到表面处理的可行性和效果,如喷漆、喷涂、电镀等。
7.模具设计:模具设计是塑胶制品生产的关键环节。
模具的设计应符合产品的结构形状和尺寸要求,同时要考虑到成型工艺的要求,如浇口、顶针设计等。
此外,还需要注意模具的加工精度和使用寿命等因素。
总之,塑胶结构设计规范是保证塑胶制品质量和性能的重要保证。
通过合理的材料选择、结构设计、壁厚设计等,可以提高塑胶结构的强度、刚度和耐久性,从而满足不同的使用需求。
塑胶跑道做法及技术要求

塑胶跑道做法及技术要求一、工程做法描述400米环形塑胶跑道运动场。
运动场内突沿半径为36米,共8条跑道,环形跑道内设置100mX65m天然草足球场,南北半圆内设置铅球区、跳远区、标枪区、铁饼链球区、三级跳远区、跳高区、泵房、水池等配套设施。
具体做法如下:1.跑道做法:挖土方、平整夯实一300mm厚碎石垫层一150mm厚,6%水泥石粉稳定层一50mm厚,粗粒沥青砼层一40mm厚,细粒沥青砼层一30mm厚,13mm厚混合型塑胶跑道;2.足球场:挖土方、平整夯实一盲沟、喷淋一250mm厚,碎石垫层一50mm厚,将原土挖出过筛后铺150mm种植兰引三号天然草;3.器械区:挖土方、平整夯实一200mm厚碎石垫层一100mm水泥砼层一20mm水泥砂浆抹面一25mm厚塑胶安全地垫。
4•篮球场铺地胶,做法:原水泥基础处理,铺10mm厚6%水泥石粉稳定层,沥青油喷洒。
40mm厚粗沥青混凝土层,20mm厚细沥青混凝土层。
5mm厚纯PU塑胶面层•安装篮球场灯光。
二、技术要求一)、塑胶面层技术指标1.耐久性塑胶面层必须在相当一段时间内保持它们的特性,在需要大修前至少维持8〜10年,当然,面层的寿命与使用的程度和使用的水平有关。
2.有效性要使在该面层上运动时的运动员感到舒适与安全,最基本的要求,要符合《国际田径协会联合会田径场地设施标准手册》中的相关规定。
3.测试:田径场在正式运作前必须经过实验室的实验测试,其目的是确信各种原材料相互兼容性组合;确信这种装置在大部分正常气候条件下能成功地安装;确信表面具有满意的耐久性;确信表面的特性能使田径运动员满意;确信原材料的成分、组合、安装方法、长期使用不对环境造成污染。
4.表面平坦在任何位置和方向上,每4米丈量距离不能超过6毫米的起伏,每1米丈量距离不能超过3毫米的起伏,而在不规则的一步丈量距离内不能超过1毫米的起伏。
5.表面厚度5.1塑胶面层的表面,由于磨损和风化会变薄,所以在跑道竣工时,表面平均厚度应该至少达到12mm,绝对不允许出现薄于10mm的地方,厚度在10mm和10.5mm之间的表面不能超过整个表面的5%,需要特别加厚区(撑竿跳高,标枪,三级跳远和跳高)不在上述范围之内,大型比赛时,表面的任何一处厚度都不得低于10mm。
钣金件-压铸件-挤压件-塑胶件结构工艺设计指南
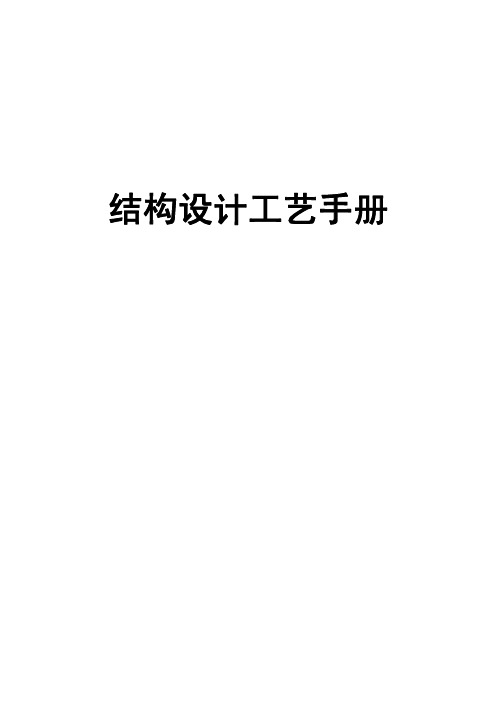
结构设计工艺手册前言公司现有零件中,不仅在打样过程中经常会有一些加工工艺性的问题,也有很多归档转产的零件存在加工困难的情况,不仅影响生产进度和交货,也影响结构件的质量。
如钣金零件的折弯,经常会发生折弯碰刀的情况;落料的外圆角、半圆凸台、异型孔的规格太多,以及一些不合理的形状设计,导致加工厂要多开很多不必要的落料模,大大增加模具的加工和管理成本;插箱的钣金导轨、拉伸凸台等设计,品种越来越多,需要统一、规范;喷漆和丝印,也经常出现喷涂选择不合理导致废品率较高、无法丝印等问题;有些钣金零件的点焊完全可以适当增加定位,不增加成本也不影响美观,实际上大部分设计是靠生产的工装定位,不仅麻烦、效率低,精度也不好;很多可以避免焊接的钣金零件,往往设计成角焊的结构形式,焊接和打磨都非常麻烦,不仅效率较低,而且外观质量也经常得不到保证,等等。
长期以来,这些相同的问题不断地重复发生,无论对产品质量还是产品的生产和进度,都会产生不良的影响。
编写这本《结构设计工艺手册》目的,就是为了方便工程师在结构设计时查阅一些常用的、关键的数据,更好地保证工程师设计出的零件有较好的加工工艺性,统一结构要素,减少不必要的开模,加快加工进度,降低加工成本,提高产品质量。
编写这本手册的同时,对《钣金模具手册》标准进行了彻底的改编,对一些典型的结构形状进行了优化和系列化,减少了品种,并在intralink库里对相关的模具建模,不仅方便设计人员进行结构设计,对模具的统一,也会起到较好的效果。
手册中一些典型的数据主要来源于参考资料,一些工艺上的极限尺寸,主要来源于加工厂家提供的数据,是我们应尽可能遵照的。
有些正在生产的零件,一些尺寸超出了手册中给出的极限尺寸,但并不能就能说明这些设计是有良好的工艺性,原则上是在满足产品性能的条件下,尽可能达到最好的加工工艺性。
由于时间和实际经验有限,手册中错误在所难免,恳请大家批评指正,希望经过一定时间的实践检验,经过将来补充、修订、完善之后,能够成为一部非常实用的参考书,对我们的设计工作起到很好的指导作用。
第三章:塑胶件设计指南
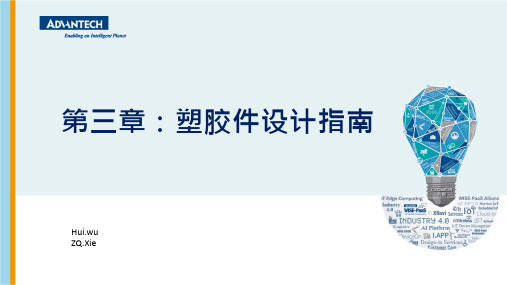
比重 1.25 1.39 1.58
比重 1.65 1.43 1.63 1.54
吸水率
标准:ASTM D570 ISO62
样品规格:1.圆片:直径50mm,厚度4mm
2.方片:60mm× 60mm× 1mm 3.条形:76.2mm× 25.4mm× 3.2mm
方法:
1. 把样品放到干燥箱干燥(条件50度/24小时), 移至干燥器中冷却 到室温,取出后测试每个样品的重量M1;
压缩模塑 压缩模塑又称模压,是模塑料在闭合模腔内借助加压的成型方法。通常,压缩模塑适用于热固性塑料,压缩模塑用的主 要设备是压机和塑模。压缩模塑的主要优点是可模压较大平面的制品和能大量生产。
溢出式
半溢出式
不溢出式
吹塑成型 借气体压力使闭合在模具中的热型坯吹胀成为中空制品,或管型坯无模吹胀成管膜的一种方法。该方法主要用于各种包 装容器和管式膜的制造。凡是熔流率为0.04 ~ 1.12的都是比较优良的中空吹塑材料,如聚乙烯、聚氯乙烯、聚丙烯、聚 苯乙烯、热塑性聚酯、聚碳酸酯、聚酰胺、醋酸纤维素和聚缩醛树脂等,其中以聚乙烯应用得最多。
常见塑料的比重
树脂 PA66 PA6 PC
PP PBT POM ABS PA46 LCP
比重 1.14 1.14 1.20
0.91 1.3 1.40 1.03 1.18 1.37
尼龙增强类 PA66+15%GF PA66+33%GF PA66+50%GF
卤素与无卤产品 FR285 NY NP216 BF509G6 NP516
注射成型(最常用) 注射成型(注塑)是使热塑性或热固性模塑料先在加热料筒中均匀塑化,而后由柱塞或移动螺杆推挤到闭合模具的模腔中 成型的一种方法。注射成型几乎适用于所有的热塑性塑料。近年来,注射成型也成功地用于成型某些热固性塑料。注射 成型的成型周期短(几秒到几分钟),成型制品质量可由几克到几十千克,能一次成型外形复杂、尺寸精确、带有金属或 非金属嵌件的模塑品。
钣金件-压铸件-挤压件-塑胶件结构工艺设计指南

由于时间和实际经验有限,手册中错误在所难免,恳请大家批评指正,希望经过一定时 间的实践检验,经过将来补充、修订、完善之后,能够成为一部非常实用的参考书,对我们 的设计工作起到很好的指导作用。考虑手册的篇幅和实用性,以及我们的设计主要是钣金零 件设计,因此,本手册主要以钣金件为主。
《工艺结构设计手册》(数冲、激光、数折、非标螺母)
《钣金冲压工艺手册》国防工业出版社
《冷冲压及塑料成型工艺与模具设计》机械工业出版社
《机械零件设计手册》 冶金出版社
《五金手册》 机械工业出版社
目录
1 第一章 钣金零件设计工艺................................................. 1 1.1 钣金材料的选材........................................................... 1 1.1.1 钣金材料的选材原则.................................................... 1 1.1.2 几种常用的板材........................................................ 1 1.1.3 材料对钣金加工工艺的影响.............................................. 3
1.2 冲孔和落料:........................................................... 5
结构设计:产品设计指南

结构设计:产品设计指南
产品的结构设计是有规律可循的,结构设计指南是由多代机械工程师通过真实的产品开发经验和教训总结而得,具有非常高的结构设计指导价值。
牛顿说过:如果说我比别人看得更远些,那是因为我站在了巨人的肩上。
一个成功的产品结构设计离不开对设计指南的遵循,机械工程师掌握了结构设计指南,就相当于牛顿站在了巨人的肩上。
常见的结构设计指南包括:面向装配的设计指南、塑胶件设计指南、钣金件设计指南和压铸件设计指南等,具体的指南可参考机械工业出版社出版的《面向制造和装配的产品设计指南》一书,掌握了这些指南,产品开发才有可能以更低的开发成本、更短的开发周期和更高的产品质量进行。
例如,面向装配的设计指南的主要内容有:减少零件数量、简化产品结构、零件标准化、产品模块化、设计稳定的基座、设计导向特征、零件先定位后固定、防错的设计、人机工程学的设计等等。
产品结构设计通过遵循面向装配的设计指南,提高产品的可装配性,从而提高产品装配效率、减少产品装配错误和装配时间、提高产品装配质量等。
上海磨石建筑培训。
塑胶模具之设计制作与管理
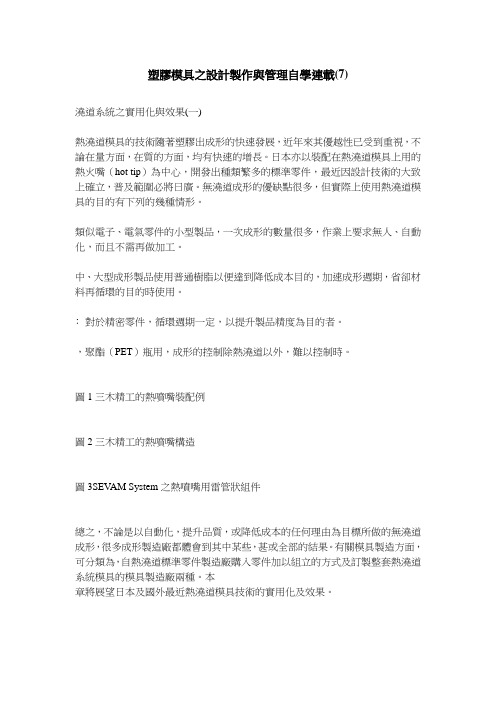
塑膠模具之設計製作與管理自學連載(7)澆道系統之實用化與效果(一)熱澆道模具的技術隨著塑膠出成形的快速發展,近年來其優越性已受到重視,不論在量方面,在質的方面,均有快速的增長。
日本亦以裝配在熱澆道模具上用的熱火嘴(hot tip)為中心,開發出種類繁多的標準零件,最近因設計技術的大致上確立,普及範圍必將日廣。
無澆道成形的優缺點很多,但實際上使用熱澆道模具的目的有下列的幾種情形。
類似電子、電氣零件的小型製品,一次成形的數量很多,作業上要求無人、自動化,而且不需再做加工。
中、大型成形製品使用普通樹脂以便達到降低成本目的,加速成形週期,省卻材料再循環的目的時使用。
﹕對於精密零件,循環週期一定,以提升製品精度為目的者。
,聚酯(PET)瓶用,成形的控制除熱澆道以外,難以控制時。
圖1三木精工的熱噴嘴裝配例圖2三木精工的熱噴嘴構造圖3SEVAM System之熱噴嘴用雷管狀組件總之,不論是以自動化,提升品質,或降低成本的任何理由為目標所做的無澆道成形,很多成形製造廠都體會到其中某些,甚或全部的結果。
有關模具製造方面,可分類為,自熱澆道標準零件製造廠購入零件加以組立的方式及訂製整套熱澆道系統模具的模具製造廠兩種。
本章將展望日本及國外最近熱澆道模具技術的實用化及效果。
圖4直接澆口(direct gate)模具組立例(SEVAM System)加熱噴嘴無澆道成形模具的其中一種方法,自古以來即有使用延長噴嘴,或使用關斷噴嘴(shut off nozzle)(有關無澆道成形的分類及歷史請參照其化文章)1)2)。
熱澆道用的澆口直接裝上加熱噴嘴亦可。
最近雖有一些標準零件開始銷售,但亦有只用做射出成形機先端用的細長噴嘴者。
不過本文所要介紹銷售中的標準零件,還是以熱澆道模具上所使用者為考慮對象。
三木精工的熱噴嘴(hot nozzle)此項熱噴嘴可直接用做延長噴嘴,或做副澆道澆口(subrunner gate)使用,如圖1所示。
塑胶折弯结构设计

塑胶折弯结构设计指南一、材料选择在进行塑胶折弯结构设计时,材料选择是至关重要的。
根据设计需求,包括强度要求、耐候性、防火性等因素,选择适合的材料。
常用塑胶材料包括ABS、PC、PVC、PET等,每种材料都有其独特的特性和适用范围。
二、折弯半径设计折弯半径是指在进行塑胶折弯时,材料内弯曲部分的半径。
折弯半径的大小直接影响折弯部分的美观度和强度。
一般来说,折弯半径应不小于板材厚度的1.5倍。
对于一些高强度材料,如PC等,折弯半径可能需要更大。
三、折弯角度设计折弯角度是指塑胶件折弯后形成的角度。
折弯角度的设计直接影响到产品的外观和使用效果。
在设计中,应根据实际需求来确定折弯角度,同时要考虑材料性能和折弯半径的影响。
四、折弯壁厚设计壁厚是影响塑胶折弯件强度和刚度的重要因素。
在壁厚设计中,需要考虑材料的性能、折弯半径和折弯角度等因素。
一般来说,壁厚不应小于板材厚度的1.5倍。
对于一些高强度材料,如PC等,壁厚可能需要更大。
五、结构设计优化在满足使用要求的前提下,应尽量简化结构,减少模具制造的难度和成本。
同时,要注意避免设计过于复杂,导致生产困难和成本增加。
六、材料性能考虑在设计中,需要考虑材料的力学性能、化学性能、热性能等因素。
这些因素将直接影响产品的使用性能和寿命。
因此,在选择材料时,应根据实际需求来选择具有合适性能的材料。
七、模具设计及制造模具是实现塑胶折弯的关键工具,模具的设计和制造直接影响到产品的质量和生产效率。
在进行模具设计时,需要考虑产品的形状、尺寸、材料等因素,同时要考虑到制造的可行性和成本。
在制造模具时,需要选择合适的制造方法和工艺,保证模具的精度和寿命。
八、生产工艺控制生产工艺控制是保证产品质量和生产效率的关键环节。
在生产过程中,需要控制好温度、压力、时间等工艺参数,确保产品的形状、尺寸和性能达到设计要求。
同时,需要对生产过程进行监控和记录,及时发现并解决问题。
九、品质及可靠性评估在完成产品设计后,需要对产品进行品质和可靠性评估。
塑料产品设计规范
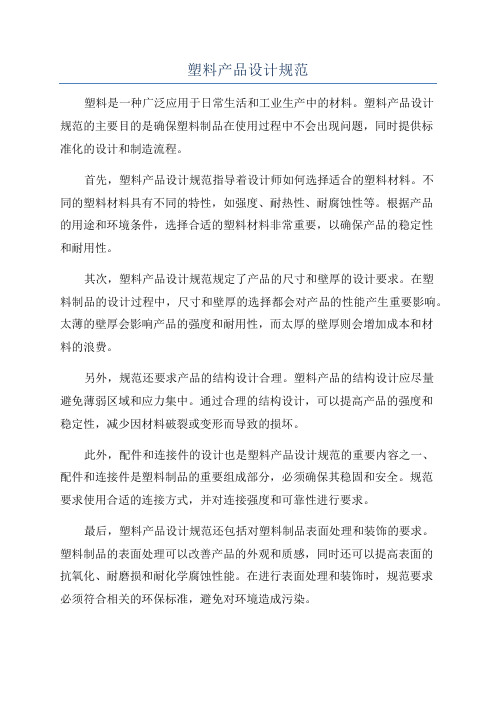
塑料产品设计规范塑料是一种广泛应用于日常生活和工业生产中的材料。
塑料产品设计规范的主要目的是确保塑料制品在使用过程中不会出现问题,同时提供标准化的设计和制造流程。
首先,塑料产品设计规范指导着设计师如何选择适合的塑料材料。
不同的塑料材料具有不同的特性,如强度、耐热性、耐腐蚀性等。
根据产品的用途和环境条件,选择合适的塑料材料非常重要,以确保产品的稳定性和耐用性。
其次,塑料产品设计规范规定了产品的尺寸和壁厚的设计要求。
在塑料制品的设计过程中,尺寸和壁厚的选择都会对产品的性能产生重要影响。
太薄的壁厚会影响产品的强度和耐用性,而太厚的壁厚则会增加成本和材料的浪费。
另外,规范还要求产品的结构设计合理。
塑料产品的结构设计应尽量避免薄弱区域和应力集中。
通过合理的结构设计,可以提高产品的强度和稳定性,减少因材料破裂或变形而导致的损坏。
此外,配件和连接件的设计也是塑料产品设计规范的重要内容之一、配件和连接件是塑料制品的重要组成部分,必须确保其稳固和安全。
规范要求使用合适的连接方式,并对连接强度和可靠性进行要求。
最后,塑料产品设计规范还包括对塑料制品表面处理和装饰的要求。
塑料制品的表面处理可以改善产品的外观和质感,同时还可以提高表面的抗氧化、耐磨损和耐化学腐蚀性能。
在进行表面处理和装饰时,规范要求必须符合相关的环保标准,避免对环境造成污染。
总之,塑料产品设计规范对确保塑料制品的质量和使用安全非常重要。
遵守规范可以帮助设计师选择适合的塑料材料、优化产品的尺寸和结构设计以及保证配件和连接件的质量。
只有遵守规范并进行有效的质量控制,才能生产出具有高质量和可靠性的塑料产品。
塑料产品设计指南
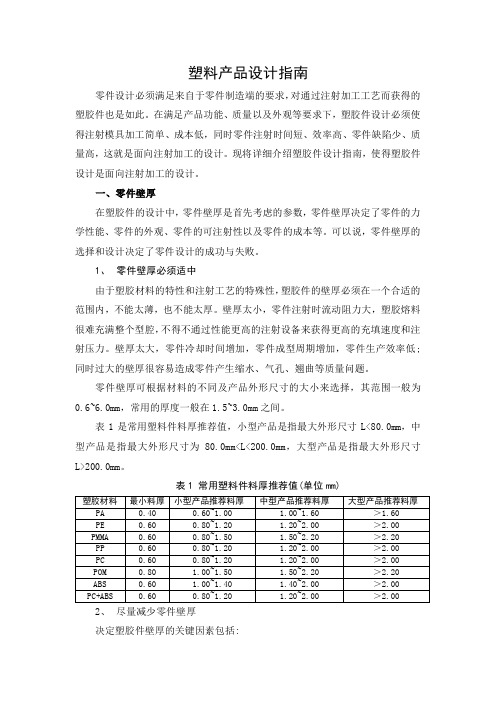
塑料产品设计指南零件设计必须满足来自于零件制造端的要求,对通过注射加工工艺而获得的塑胶件也是如此。
在满足产品功能、质量以及外观等要求下,塑胶件设计必须使得注射模具加工简单、成本低,同时零件注射时间短、效率高、零件缺陷少、质量高,这就是面向注射加工的设计。
现将详细介绍塑胶件设计指南,使得塑胶件设计是面向注射加工的设计。
一、零件壁厚在塑胶件的设计中,零件壁厚是首先考虑的参数,零件壁厚决定了零件的力学性能、零件的外观、零件的可注射性以及零件的成本等。
可以说,零件壁厚的选择和设计决定了零件设计的成功与失败。
1、零件壁厚必须适中由于塑胶材料的特性和注射工艺的特殊性,塑胶件的壁厚必须在一个合适的范围内,不能太薄,也不能太厚。
壁厚太小,零件注射时流动阻力大,塑胶熔料很难充满整个型腔,不得不通过性能更高的注射设备来获得更高的充填速度和注射压力。
壁厚太大,零件冷却时间增加,零件成型周期增加,零件生产效率低;同时过大的壁厚很容易造成零件产生缩水、气孔、翘曲等质量问题。
零件壁厚可根据材料的不同及产品外形尺寸的大小来选择,其范围一般为0.6~6.0mm,常用的厚度一般在1.5~3.0mm之间。
表1是常用塑料件料厚推荐值,小型产品是指最大外形尺寸L<80.0mm,中型产品是指最大外形尺寸为80.0mm<L<200.0mm,大型产品是指最大外形尺寸L>200.0mm。
表1 常用塑料件料厚推荐值(单位mm)2、尽量减少零件壁厚决定塑胶件壁厚的关键因素包括:1)零件的结构强度是否足够。
一般来说,壁厚越大,零件强度越好。
但零件壁厚超过一定范围时,由于缩水和气孔等质量问题的产生,增加零件壁厚反而会降低零件强度。
2)零件成型时能否抵抗脱模力。
零件太薄,容易因顶出而变形。
3)能否抵抗装配时的紧固力。
4)有金属埋入件时,埋入件周围强度是否足够。
一般金属埋入件与周围塑胶材料收缩不均匀,容易产生应力集中,强度低。
5)零件能否均匀分散所承受的冲击力。
模具设计指南
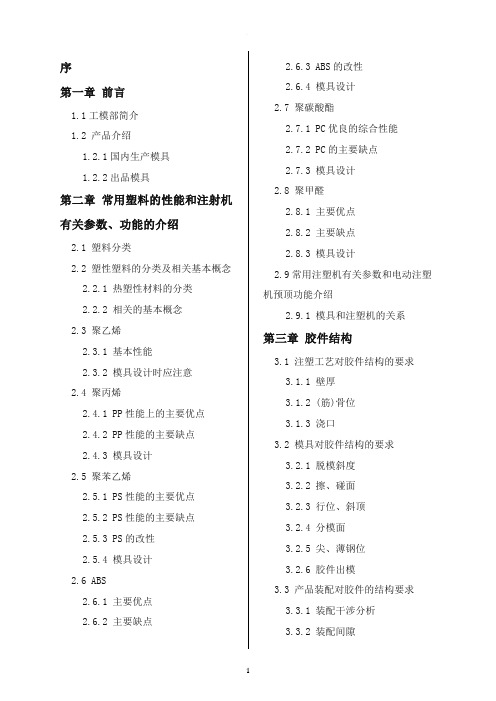
序第一章前言1.1工模部简介1.2 产品介绍1.2.1国内生产模具1.2.2出品模具第二章常用塑料的性能和注射机有关参数、功能的介绍2.1 塑料分类2.2 塑性塑料的分类及相关基本概念2.2.1 热塑性材料的分类2.2.2 相关的基本概念2.3 聚乙烯2.3.1 基本性能2.3.2 模具设计时应注意2.4 聚丙烯2.4.1 PP性能上的主要优点2.4.2 PP性能的主要缺点2.4.3 模具设计2.5 聚苯乙烯2.5.1 PS性能的主要优点2.5.2 PS性能的主要缺点2.5.3 PS的改性2.5.4 模具设计2.6 ABS2.6.1 主要优点2.6.2 主要缺点2.6.3 ABS的改性2.6.4 模具设计2.7 聚碳酸酯2.7.1 PC优良的综合性能2.7.2 PC的主要缺点2.7.3 模具设计2.8 聚甲醛2.8.1 主要优点2.8.2 主要缺点2.8.3 模具设计2.9常用注塑机有关参数和电动注塑机预顶功能介绍2.9.1 模具和注塑机的关系第三章胶件结构3.1 注塑工艺对胶件结构的要求3.1.1 壁厚3.1.2 (筋)骨位3.1.3 浇口3.2 模具对胶件结构的要求3.2.1 脱模斜度3.2.2 擦、碰面3.2.3 行位、斜顶3.2.4 分模面3.2.5 尖、薄钢位3.2.6 胶件出模3.3 产品装配对胶件的结构要求3.3.1 装配干涉分析3.3.2 装配间隙。
3.3.3 柱位、扣位连接3.4 表面要求3.4.1 文字、图案和浮雕3.4.2 胶件外形3.4.3 表面纹理附录1 客户资料的转换与处理1.1 资料处理1.2 文件转换1.3 IGS文件的处理第四章模具报价4.1 模具类型4.1.1 二板模(大水口模)4.1.2 三板模(细水口模)4.2 报价图的绘制及订料4.2.1 绘制报价图4.2.2 订料4.2.3 模具材料选用第五章模具结构设计胶件排位5.2 分模面的确定5.2.1 分模面选择原则5.2.2 分模面注意事项及要求5.3 模具强度5.3.1 强度校核5.3.2 提高整体强度5.3.3 加强组件强度5.4 成型零件设计5.4.1 胶料的成形收缩率5.4.2 脱模斜度5.4.3 成形零件的工艺性5.5 常用结构件设计5.5.1 定位圈5.5.2 唧咀5.5.3 紧固螺钉5.5.4 顶针5.5.5 司筒5.5.6 密封圈5.5.7 拉料杆5.5.8 垃圾钉5.5.9 弹簧5.5.10 定距拉板5.6模具图纸规范5.6.1 视图格式5.6.2 图纸编号5.6.3 基准角标识5.6.4 图纸输出要求第六章物料清单“BOM”及文件管理6.1 物料清单“BOM”的编制6.1.1 物料清单“BOM”的基本格式6.1.2 物料清单“BOM”的要求6.1.3 物料清单“BOM”的流程6.2 文件管理第七章行位设计。
设计指南-加强肋的设计
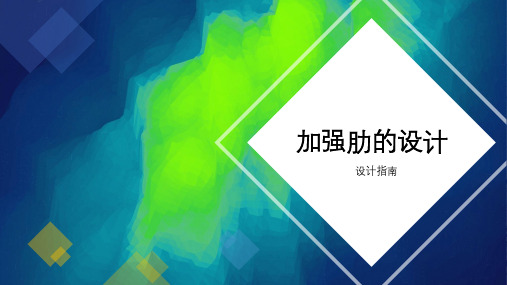
5. 加强肋与加强肋之间的间距至少 为塑胶件壁厚的2倍
6. 加强肋设计需要遵守均匀壁厚原则
7. 加强肋项端增加斜 角避免困气加强肋顶 端应避免直角的设计。
8ቤተ መጻሕፍቲ ባይዱ 加强肋方向与塑 胶熔料流向一致
加强肋的设计
设计指南
加强肋的设计参数
• 加强肋的厚度 • 高度 • 脱模斜度 • 根部圆角 • 加强肋与加强肋之间的间距等
1. 加强肋的厚度不应该超过 塑胶件壁厚的 50% ~ 60%
2. 加强肋的高度不能超过塑胶件壁厚的3 倍
3. 加强肋根部圆角为塑胶件壁厚的 0.25 ~ 0.5倍
4. 加强肋的脱模斜度 一般为0.5°~1.5°
- 1、下载文档前请自行甄别文档内容的完整性,平台不提供额外的编辑、内容补充、找答案等附加服务。
- 2、"仅部分预览"的文档,不可在线预览部分如存在完整性等问题,可反馈申请退款(可完整预览的文档不适用该条件!)。
- 3、如文档侵犯您的权益,请联系客服反馈,我们会尽快为您处理(人工客服工作时间:9:00-18:30)。
●第一章塑胶材料加工方式的选择塑料产品之好坏与材料选择及加工方式之迥异而有极大之关系。
对于任何欲制之塑品,其步骤为先决定何种材料能够达到其所须之物性,再来则为选择最适切与最经济的加工方式,最后则视产量之多寡而决定设备。
●1-1塑料材料之选择在大约探讨了塑料材料的基本物性,以下将做更深入的分析。
下面所列之各表乃是依据标准方法制成试片所测得之数据,与实际生产所制出的成品性质仍有相当大之差距,但做为不同等级材料性质之比较已足矣。
下表1-1为一般常见塑料机械性质之比较。
表1-2则为塑料拉伸强度之范围,表1-3为抗冲击强度之范围。
表1-4及表1-5,则为塑料之其它性质。
参考以上各表,即大约可知塑品用何种材料可达到其用途之所须性质要求。
一般而言加了玻纤后,可增加拉伸力、减少拉伸量、抗磨耗力降低、挠曲力增高、热变形温度增加、热膨胀降低及较不透明,而耐冲击力则不一定。
但是硬度(除非高填充)、电气性质、抗化学性及抗天候性则甚无影响。
表1-6则为一般材料之机械性质之定性趋势表。
若是依各种用途来分,所使用之塑料大概可列表如1-7所示。
●1-2塑料加工方式之选择塑料之加工方式五花八门,随着材料及成品而有极大之差异。
以下对一般常见的加工方式,作一番简介:1. 射出成形(injection molding)在所有之塑料加工成形方法上,射出成形最为被广泛使用。
其法为热塑性塑料或热固性塑料导入于射出成形机的加热筒中,俟其完全熔融后,藉由柱塞或螺杆之压力,产生热能及摩擦热能,将其注入于闭合模具之模穴中,固化后,再开启模具取出成品。
此种加工技术因材料、机械设计及制品要求而衍生出其它之方法,如预嵌入金属零件之插件成形、多色及混色的射出成形,结构发泡的射出成形、气体辅助射出成形(gas assisted injection molding)、共射出成形(coinjection)、射出中空成形及利用液态单体或液态预聚合物为原料之反应射出成形(RIM)等方法。
2. 押出加工(extrusion)将热塑性材料于押出机中加热、加压,再用螺杆予以押出,押出品之断面形状依模头而定,可为棒状、管状、平版状、异形状等等。
其它如吹膜押出、押出中空成形、压延加工,押出涂装及混炼切粒等皆在前半段应用押出机,现今流行的趋势是共押出加工(coextrusion),制成多层高功能的制品。
3. 压缩成形(compression molding)此为热固性塑料成形法之一种,先将热固性树脂预热后,置于开放的模穴内,闭模后施以热及压力,直至材料硬化为止。
酚醛树脂,美耐皿树脂及尿素甲醛等树脂常用此法成形,所制之成品为:家电制品外壳、零件、齿轮、家具餐具等。
4. 中空成形(blow molding)其法为先将热塑性塑料由押出机之模头押出,使成为薄管,此称为型胚(parison),再闭合模具,吹气而后成形。
此法之应用已愈来愈广泛,如汽车业,所用之材料也由传统之PE、PP、PVC、PET等,走向高性能的工程塑料。
其优点为制造大形品方便及一次成形,缺点则为塑品之各部份肉厚不易控制。
5. 回转成形(rotational molding)将常温粉状或液状之成形材料注入于回转模具中,利用加热及离心力使树脂均匀布满于模壁面,冷却后即可得中空之成形品。
此法最适当做大型物品之成形,缺点则为肉厚较难控制。
6. 吹膜押出(blown film estursion)一般制造薄膜之方式有二:(a)T模法(T-die method)。
(b)环模法(ring-die method)。
(a) T模法为平膜押出,制成之薄膜厚度较环模法制造的来的均匀。
由于引取方向之拉力较大,使得纵向强度较横向强度大的多,故很多已用双轴延伸的方法来制膜。
(b) 吹膜押出是采用环模法的操作方式,押出之熔胶经环形模,用空气吹成管膜,再予冷却即成胶膜。
聚烯烃类之塑料常以此法制造各种垃圾袋,收缩膜及食品包装膜等。
现在之高级包装膜则为利用共押出之方法来制造多层膜。
7. 热成形(thermoforming)此法为将热塑性塑料板加热软化后,用真空、空气或套合之金属予以加压成形。
其强度与塑板之厚度有关,产生之制品须经裁剪,多余的边料再予以回收。
8. 押出涂装与积层(extrusion coating & lamination)其法为用押出机将热塑性塑料熔化押出,经过T形模头后形成淋幕,然后涂布于连续移动的板状或膜状基材上,常用于日用品及食品之包装。
9. 转移成形(transfer molding)为用于热固性塑料的成形法,塑料料先于加热室(转移室)内加热软化,然后藉由转移冲柱之高压,迫使熔融材料穿过流道及浇口进入模穴中进行硬化反应。
此法非常适合于有金属插件时之情形且成形品精密度比压缩成形高者,但模具设计则较复杂且成品之机械强度较低。
10. 铸塑成形(casting)此法为将液状树脂配合硬化剂后,注入至开口之模具中,使其流至模具表面,在常压下使其干燥完成聚合反应的成形法;或者是将液状树脂涂布于移动之皮带上,或是在化学溶液中沉淀之,以获得塑料薄膜的方法。
11. 轮辗涂装(calender coating)利用滚轮表面之热,使熔融塑料涂布于布、皮或纸上的加工方法,PVC皮布是最常被轮辗加工之产品。
12. 粉末涂装(powder coating)此法是在被涂物上放置粉末,然后加热使粉末熔融的连续涂布法,可分为下列三种方式:(a) 焰喷法:将塑料粉末以丙烷或乙炔燃料气之火焰喷射,再熔化附着于受质体表面。
(b) 静电涂装:为利用静电将塑料粉末附着于受质体表面,再加热使之熔解。
(c) 流动浸渍涂装:将塑料粉末在流动床中浮动,再浸入加热过的金属物体,使熔着一层塑料覆膜。
一般我们常用之塑料粉末为PE、PP、PVC、Nylon及Epoxy等。
13. 发泡加工(foaming)发泡材料为含有气泡之材料,其假比重较实质密度为低。
依发泡法之分类有:常压加热法、加压发泡法、押出发泡法、射出发泡法、二液混合法及二段发泡法等。
一般押出发泡法所用之模头可分为T形模及环形模,后者常被用于聚苯乙烯发泡板,但如果是厚度大于5mm,则须使用T形模头来发泡。
常见之发泡材有PE、PP、PS、PVC、CPE、ABS及PC等。
结构发泡之设计,在本书第六章会另做详细说明。
14. 拉挤成形(pultrusion)此加工方式是玻纤补强产品产生的一种,藉由加热模头,连续式的拉出经过补强及硬化的树脂,而后成形。
其实一个最佳的塑料加工方式之选择,主要之决定在于材料之种类、产品之外形,产量之多寡及最重要的成本效益。
而往往一个同样之产品,可经由各种不同之加工方式而产生,如表1-8所示。
至于常用的塑料加工方法与所选择的热固性及热塑性材料则可藉表1-9,做个比较参考。
若产品之形状较为复杂及须要做内部之加工,则加工方式之选择可参考表1-10。
至于各加工方式、成本及产率之关系,可参考表1-11。
●第二章射出成型/产品设计●2-1 通论产品设计是利用材料,经设计成为新创的外形或结构,以制成指定作用或目的的产品。
其所须具备之条件为:1. 在功能上:要能符合使用者的需求。
2. 在使用操作上:要能符合使用者的习惯与身份。
3. 在外型上:要能合乎简单的制造原则并满足使用者的喜好。
4. 材料应用与加工方法上:要合乎经济与合理的原则,并能求得最适化而降低成本。
即任何一新产品,从构思到生产,对一公司而言,其考量前题为以下所列各项:‧将来性:公司未来发展领域的配合,成长性。
‧ 技术性:与该公司现有技术之关系,原料设备获得之难易及技术上成功的可能性。
‧ 领先性:是否可申请或抵触专利及制品是否具独特性。
‧ 销售可能性:产品的展望,推出市场之难易,销售网的建立及有无商品特征等可能性。
‧ 经济性:研究经费人员的多寡,开发期间的长短,设备投资额之获得及获利率的大小。
其它如材料之选择、加工方式、模具的设计、二次加工方式及安全规范、法令等,皆须详加考虑。
通常塑料新制品产生的方式可分为三种:1. 再设计(redesign):就是将现有产品的部分,做一些改变或修饰,使成为更具价值与流行的新产品。
现今市场上约莫80%,属于此类。
2. 组合(combination):结合两种以上不同功能,发展而成之新制品。
例如PC制成的潜水镜再贴上防雾膜,而成为价值更高的新产品。
此类新产品约占10%。
3. 创新(innovation):剩下的10%即为发明前所未有之新制品,此类产品由于须花费较长的时间在宣传及消费者的接受性上,所以通常这方面之设计比例较低。
塑料产品设计者与其它设计者最大的不同是,前者必须详加考虑塑料之各种物性,尤其是环境变化对物性之影响及在长时间负载下对产品之影响。
通常,塑料之物性数据是在实验室的环境下,依照美国标准测试方法(ASTM)而测得。
而所设计的塑料产品并不会正如测试样品在同样条件下成形或被加应力。
其它如:‧肉厚及形状。
‧所加负载之速率及时间长短。
‧玻纤之排列方向。
‧缝合线。
‧表面缺陷。
‧成形参数。
以上这些;都会影响到塑料产品之强度及韧性。
设计者亦须考虑到温度,湿度,阳光(紫外线),化学药剂等之影响。
所以了解其产品的最终目的而探讨相关的物性是非常重要的。
下表2-1为一标准的设计检查表(design check list)。
●2-2原型之设计为了能将实物从设计的阶段到真正的商品化,我们通常是建一原型而加以测试并修正。
最好的方法是尽可能的将原型与将商品化制造的加工方式相近。
大部份的工程塑料产品是由射出成型所制出,所以原模必须为一单模穴原型模具所制得。
以下将讨论各种制造原型之方法及其优缺点。
●2-2-1机械加工圆杆或平板、块法(machining from rod or slab stock)此法是当所允许的设计时间非常短及只须少量的原型和物体的形状非常简单的时候,我们可将其经机械加工而得。
这样不仅能帮助发展至固定的设计,亦能做为有限度的测试结果条件;但千万不能将其做为最后商品化的标准,其原因如下:‧其物性如强度,韧性及伸长量可能会小于真正的成形品,因为机械加工会在原模上留下痕迹。
‧强度及韧性可能会高于成形品,因为圆杆或平板块具较高的结晶度。
‧若是加了玻纤的产品,则玻纤的方向性影响会误导了结果。
‧成形品的特性如顶出针痕,浇口痕及不定形的表面结构将不会出现在原型上。
‧无法探讨缝合线及接合线之影响。