塑料注射模的设计程序及要点
注射模的设计步骤

注射模的设计步骤•一、设计前应明确的事项•二、模具结构设计的一般步骤一、设计前应明确的事项–以模具设计任务书(由塑料生产部门提出)为依据–包括以下内容:①经过审签的正规塑件图纸(塑料牌号、透明度等)Ø最好附上样品(更为形象和直观,还能提供有价值的信息,如所采用的浇口位置、顶出位置、分型面等);②塑料制件说明书及技术要求;③塑料制件的生产数量及所用注射机;④注射模基本结构、交货期限及价格等。
–应明确如下事项:①熟悉塑件几何形状、明确使用要求Ø对于形状复杂的塑件,除了看懂图纸、在头脑中建立清晰的三维形象外(初学者最好能根据产品图绘制出塑件的轴侧图),特别要充分了解塑件的用途,塑件的各部分在该用途下各起什么作用,进而明确塑件的成型收缩率、透明度、尺寸公差、表面粗糙度、允许的变形范围等问题;②检查塑件的成型工艺性Ø对塑件进行成型工艺的检查,以确认塑件的各个细节是否符合注射成型的工艺性条件。
优质的模具不仅仅取决于模具结构的正确性,还取决于塑件的结构能否满足成型工艺的要求;③明确注射机的型号和规格Ø在设计前要确定采用什么型号和规格的注射机,这样在模具设计中才能有的放矢,正确处理好注射模与注射机的关系。
④制定注射成型工艺卡,以指导模具设计工作和实际的注射成型加工。
一般应包括如下内容:Ø塑件概况:包括简图、质量、壁厚、投影面积、有无侧凹和嵌件等;Ø塑料概况:如品名、出产厂家、颜色、干燥情况等;Ø必要的注射机数据:如动模板和定模板尺寸、模具最大空间、螺杆类型、额定功率等;Ø注射压力与行程简图;Ø注射成型条件:包括加料筒各段温度、注射温度、模具温度、冷却介质温度、锁模力、螺杆背压、注射压力、注射速度、循环周期(注射、保压、冷却、开模时间)等。
二、模具结构设计的一般步骤1.确定型腔的数目Ø根据锁模力、最大注射量、制件的精度要求、经济性等,在设计时应根据实际情况决定采用哪一种;2.选定分型面Ø虽然在塑件设计阶段分型面已经考虑或者选定,在模具设计阶段仍应再次校核,从模具结构及成型工艺的角度判断分型面的选择是否最为合理;3.确定型腔的配置Ø实质上是模具结构总体方案的规划和确定。
塑料注射模具设计基本流程
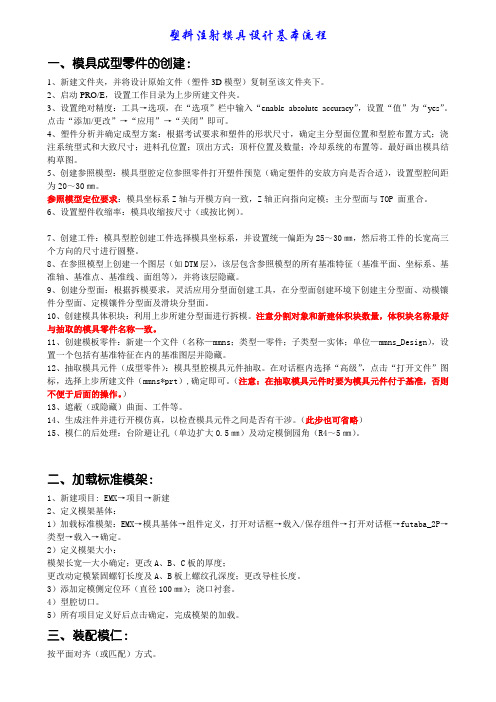
塑料注射模具设计基本流程一、模具成型零件的创建:1、新建文件夹,并将设计原始文件(塑件3D模型)复制至该文件夹下。
2、启动PRO/E,设置工作目录为上步所建文件夹。
3、设置绝对精度:工具→选项,在“选项”栏中输入“enable_absolute_accuracy”,设置“值”为“yes”。
点击“添加/更改”→“应用”→“关闭”即可。
4、塑件分析并确定成型方案:根据考试要求和塑件的形状尺寸,确定主分型面位置和型腔布置方式;浇注系统型式和大致尺寸;进料孔位置;顶出方式;顶杆位置及数量;冷却系统的布置等。
最好画出模具结构草图。
5、创建参照模型:模具型腔定位参照零件打开塑件预览(确定塑件的安放方向是否合适),设置型腔间距为20~30㎜。
参照模型定位要求:模具坐标系Z轴与开模方向一致,Z轴正向指向定模;主分型面与TOP 面重合。
6、设置塑件收缩率:模具收缩按尺寸(或按比例)。
7、创建工件:模具型腔创建工件选择模具坐标系,并设置统一偏距为25~30㎜,然后将工件的长宽高三个方向的尺寸进行圆整。
8、在参照模型上创建一个图层(如DTM层),该层包含参照模型的所有基准特征(基准平面、坐标系、基准轴、基准点、基准线、面组等),并将该层隐藏。
9、创建分型面:根据拆模要求,灵活应用分型面创建工具,在分型面创建环境下创建主分型面、动模镶件分型面、定模镶件分型面及滑块分型面。
10、创建模具体积块:利用上步所建分型面进行拆模。
注意分割对象和新建体积块数量,体积块名称最好与抽取的模具零件名称一致。
11、创建模板零件:新建一个文件(名称—mmns;类型—零件;子类型—实体;单位—mmns_Design),设置一个包括有基准特征在内的基准图层并隐藏。
12、抽取模具元件(成型零件):模具型腔模具元件抽取。
在对话框内选择“高级”,点击“打开文件”图标,选择上步所建文件(mmns*prt),确定即可。
(注意:在抽取模具元件时要为模具元件付于基准,否则不便于后面的操作。
第2章 塑料注射模设计要点

第2章塑料注射模设计要点塑料注射模是塑料模具中产量、产值最大,同时也是技术难度最大的一类模具。
因此,模具设计实训中应至少完成一副塑料注射模的设计(以下除非特别注明,本书中的塑料模一般指的就是塑料注射模);本章结合企业的工作实际,将塑料模相关的设计要点与规范做一简要的复习。
2.1 常用塑料及其成型特点常见塑料的中英文名称及与模具设计相关的参数,如表2- 1和错误!未找到引用源。
表2- 2所示。
表2- 1 常用的工程塑料及其成型特点表2- 2 常用的通用塑料及其成型特点2.2 塑料注射模的基本组成一般情况下,对于塑料模具而言,主要有二类,一类为二板模,俗称大水口模;另一类为三板模,俗称细水口模。
不管是二板模,还是三板模,塑料模具一般由以下几个部分组成。
1、模架:模架构成了塑料模具最基本的框架部分。
模架一般可从专业模架厂商处直接采购。
2、塑料模具的核心部分——型腔和型芯:主型腔和主型芯俗称模仁或内模,是模具里面最重要的组成部分。
设计工作的大部分时间的也花费在模仁的设计上。
不过,相对有些比较简单的模具,它没有模仁部分,产品直接在模板上面成形,特别是早期的塑料模具大都如此,这种结构已经逐步淘汰。
3、塑料模具附助零件:如定位环、浇口套、推杆(也称顶杆或顶针)、拉料杆(俗称抓料销)、支撑柱、顶出板导柱导套、支撑钉(俗称垃圾钉)等。
如果是三板模,往往还要设置专门的顺序开模控制机构。
4、塑料模具的附助系统:一般的塑料模具有以下三个系统:浇注系统、顶出系统、冷却系统。
有时,因为所运用的塑料材料需加热的温度很高,所以,有的模具还会存在一个加热系统。
5、当塑料制品侧向有孔或卡勾的时候,模具还必须设置一个或多个处理这些孔、卡脱模的机构,如滑块、斜推杆杆、油压缸等等。
这种处理的机构称之为侧向分型与抽芯机构。
2.3 标准模架为了在缩短模具的设计与制造时间,模具制造企业的往往将工作的重点放在模仁的设计与加工上,而作为基础构建的模架往往采用专业厂家的标准模架。
注射模设计步骤与实例
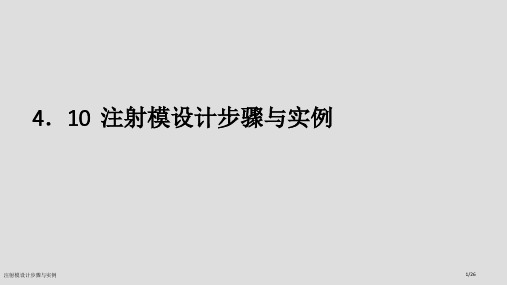
❖ 因为上模板座和上凸模固定板尺寸尚不确定,初定δ=
25mm,D=20mm,计算后,取L=55mm。假如以后δ,有
注射模设计步改骤与变实例,则再修正L长度。
12/26
❖ ④滑块与导槽设计 ❖ 滑块与侧型芯(孔)连接方式设计 本例中侧向抽芯机
构主要是用于成型零件侧向孔和侧向凸台,因为侧 向孔和侧向凸台尺寸较小,考虑到型芯强度和装配 问题,采取组合式结构。型芯与滑块连接采取镶嵌 方式,其结构如图4-149所表示。 ❖ 滑块导滑方式 本例中为使模具结构紧凑,降低模 具装配复杂程度,拟采取整体式滑块和整体导向槽 形式,其结构如图4-149所表示。为提升滑块导向 精度,装配时可对导向槽或滑块采取配磨、配研装 配方法。 ❖ 滑块导滑长度和定位装置设计 本例中因为侧芯距 较短,故导滑长度只要符合滑块在开模时定位要求 即可。滑块定位装置采取弹簧与台阶组合形式,如 图4-149所表示。
4.10 注射模设计步骤与实例
注射模设计步骤与实例
1/26
4.10.1 注射模设计基本程序
❖ 1.了解塑件技术要求 ❖ 2.依据塑件形状尺寸,估算塑件体积和重量 ❖ 3.分析塑件,确定成形方案 ❖ 4.绘制方案草图 ❖ 5.设计计算 ❖ 6.绘制模具设计总装图 ❖ 7.绘制零件工作图 ❖ 8,经过全方面审核后投产加工
❖ 另加3~5mm抽芯安全系数,可取抽芯距S轴=4.9mm。
❖ ②确定斜导柱倾角 斜导柱倾角是斜抽芯机构主要技术参数 之一,它与抽拔力以及抽芯距有直接关系,—般取α=15°~ 20°,本例中选取α=20°。
❖ ③确定斜导柱尺寸 斜导柱直径取决于抽拨力及其倾斜角度, 可按设计资料相关公式进行计算,本例采取经验估值,取斜 导柱直径d=14mm。斜导柱长度依据抽芯距、固定端模板厚 度、斜销直径及斜角大小确定(参见本章第六节斜导柱长度 计算公式)。
注射模设计指导

1 注射模设计的一般程序(1) 塑件分析①工艺性分析(分析产品的结构形状、尺寸大小、特点、特征、使用要求)仔细阅读塑件零件图,从塑件的塑料品种、塑件形状、尺寸精度、表面粗糙度等各方面考虑注射成型工艺的可行性和经济性,必要时,要与产品设计者探讨塑件的材料种类与结构修改的可能性。
具体地:◆根据使用要求进行产品的结构设计设计方法和要点参考“塑料件结构工艺性”部分◆针对已设计好的产品图样,分析塑料件结构的合理性分析问题的出发点,一是成型工艺性,二是模具结构的复杂性②确定塑件的生产类型小批量生产时,为降低成本,模具尽可能简单;在大批量生产时,应在保证塑件质量前提下,尽量采用一模多腔或高速自动化生产,以缩短生产周期,提高生产效率,即对模具的推出机构,塑件和流道凝料的自动脱模机构等应该提出更严格的要求。
③选择塑件的材料该项工作不是不需要做的工作。
选择时的主要依据是塑件的使用要求;在满足使用要求的前提下,其成型性能应与塑件结构、尺寸等相适应。
④查阅相关手册,记录塑料的相关参数如:收缩率、允许最小壁厚、脱模斜度、成型压力(或注射压力)、模腔的温度以及相关的成型工艺(参数)要求等⑤计算塑件的体积和质量计算塑件的体积和质量是为了选用注射机,提高设备利用率,确定模具型腔数。
(2) 预选注射机预选注射机的依据是注射量、塑化量、锁模力等。
这时根据注射模与注射机的关系,既可以根据设备参数确定模具参数,也可以根据模具要求选择注射机参数。
相关公式参考教材p74~80。
记录注射机与设计模具有关的技术参数记录注射机与设计模具有关的技术参数为模具设计作好准备。
主要参数有:注射机定位环的直径、喷嘴前端孔径及球面半径、注射机最大注射量、锁模力、注射压力、塑化量、固定模板和移动模板面积大小及安装螺孔位置、注射机拉杆的间距、闭合厚度、开模行程、顶出行程等。
最好是初选符合上述要求的几种规格的注射机已备挑选。
(3) 计算成型零件的工作尺寸相关公式参考教材p129~138。
注塑模具设计流程
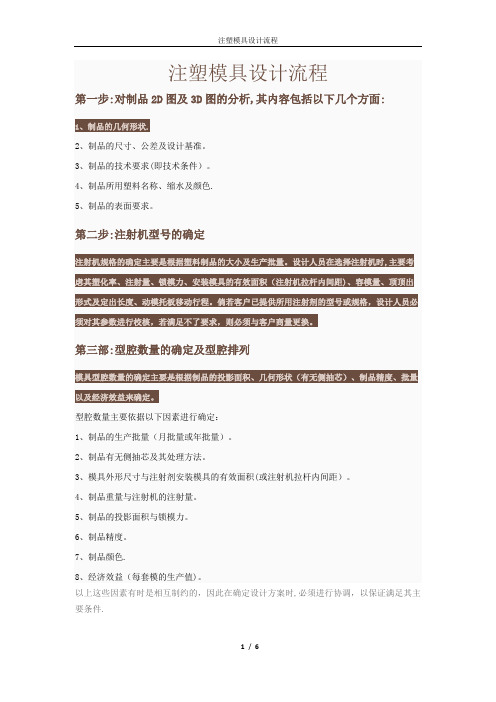
注塑模具设计流程第一步:对制品2D图及3D图的分析,其内容包括以下几个方面:1、制品的几何形状.2、制品的尺寸、公差及设计基准。
3、制品的技术要求(即技术条件)。
4、制品所用塑料名称、缩水及颜色.5、制品的表面要求。
第二步:注射机型号的确定注射机规格的确定主要是根据塑料制品的大小及生产批量。
设计人员在选择注射机时,主要考虑其塑化率、注射量、锁模力、安装模具的有效面积(注射机拉杆内间距)、容模量、顶顶出形式及定出长度、动模托板移动行程。
倘若客户已提供所用注射剂的型号或规格,设计人员必须对其参数进行校核,若满足不了要求,则必须与客户商量更换。
第三部:型腔数量的确定及型腔排列模具型腔数量的确定主要是根据制品的投影面积、几何形状(有无侧抽芯)、制品精度、批量以及经济效益来确定。
型腔数量主要依据以下因素进行确定:1、制品的生产批量(月批量或年批量)。
2、制品有无侧抽芯及其处理方法。
3、模具外形尺寸与注射剂安装模具的有效面积(或注射机拉杆内间距)。
4、制品重量与注射机的注射量。
5、制品的投影面积与锁模力。
6、制品精度。
7、制品颜色.8、经济效益(每套模的生产值)。
以上这些因素有时是相互制约的,因此在确定设计方案时,必须进行协调,以保证满足其主要条件.型腔数量确定之后,便进行型腔的排列,以及型腔位置的布局。
型腔的排列涉及模具尺寸、浇注系统的设计、浇注系统的平衡、抽芯(滑块)机构的设计、镶件型芯的设计以及热流道系统的设计。
以上这些问题由于分型面及浇口位置的选择有关,所以在具体设计过程中,要进行必要的调整,以达到最完美的设计。
第四步:分型面的确定分型面,在一些国外的制品图中已作具体规定,但在很多的模具设计中要由模具人员来确定,一般来讲,在平面上的分型面比较容易处理,有时碰到立体形式的分型面就应当特别注意.其分型面的选择应遵照以下原则:1、不影响制品的外观,尤其是对外观有明确要求的制品,更应注意分型面对外观的影响.2、利于保证制品的精度。
试述塑料注射模设计流程及主要内容

试述塑料注射模设计流程及主要内容下载提示:该文档是本店铺精心编制而成的,希望大家下载后,能够帮助大家解决实际问题。
文档下载后可定制修改,请根据实际需要进行调整和使用,谢谢!本店铺为大家提供各种类型的实用资料,如教育随笔、日记赏析、句子摘抄、古诗大全、经典美文、话题作文、工作总结、词语解析、文案摘录、其他资料等等,想了解不同资料格式和写法,敬请关注!Download tips: This document is carefully compiled by this editor. I hope that after you download it, it can help you solve practical problems. The document can be customized and modified after downloading, please adjust and use it according to actual needs, thank you! In addition, this shop provides you with various types of practical materials, such as educational essays, diary appreciation, sentence excerpts, ancient poems, classic articles, topic composition, work summary, word parsing, copy excerpts, other materials and so on, want to know different data formats and writing methods, please pay attention!塑料注射模设计流程及主要内容在塑料制品生产中,注射模设计是至关重要的一环。
第2章 塑料注射模设计

U形截面分流道的优缺点和梯形的基本相同,常用于小型制品,如图2-6(c) 所示;
半圆形截面和矩形截面分流道因为比表面积较大,一般不常用,如图2-6(d) 和图2-6(e)所示。
图2-6 分流道的截面形状
2.分流道设计
单腔注射模通常不用分流道,但多腔注射模必须开设分流道。
分流道开设在动、定模分型面的两侧或任意一侧,其截面形状如图 2-6所示。
— 24 —
圆形截面分流道的比表面积(流道表壁面积与容积的比值)最小,塑料熔体的 热量不易散发,所受流动阻力也小,但需要开设在分型面两侧,而且上、下两 部分必须互相吻合,加工难度较大,如图2-6(a)所示;
(2)分流道。
主流道与浇口之间的一段流道, 它是熔融塑料由主流道流入型腔的过渡 段,能使塑料的流向得到平稳的转换。
(3)浇口。 浇口是分流道与型腔之间的狭窄部分,也 是最短小的部分。 (4)冷料穴。 其作用是储存两次注射间隔中产生的冷料 头,以防止冷料头进入型腔造成塑件熔接 不牢,影响塑件质量,甚至发生冷料头堵 塞住浇口,而造成成形不满。
(4)侧浇口。 设置在模具的分型面处,从塑件的内或外侧进料,截面为矩形的浇口 称为侧浇口,如图2-12所示。
图2-12 侧浇口
5.浇口部位的选择 塑件上浇口开设部位的选择,应注意以下几点: (1)避免熔体破裂现象在塑件上产生缺陷。 (2)考虑分子取向方位对塑件性能的影响。 (3)浇口开在塑件壁最厚处。 (4)减少熔接痕和增加熔接牢度。 (5)防止料流将型芯或嵌件挤歪变形。 (6)保证型腔充满。
2.3.2 普通浇注系统设计
1.主流道设计 主流道的几何形状和尺寸如图2-5所示,其截面形状一般为圆形,设 计时应注意下列事项。 (1)主流道的尺寸。主流道的尺寸应当适宜,一般情况下,主流道 进口端的截面直径取为4~8mm,若熔体流动性好且制品较小时,直径可 设计得小一些;反之则要设计得大一些。
塑料注射模设计程序

塑料注射模设计程序引言塑料注射模是用于塑料制品生产的重要工具,其设计合理与否直接影响着产品质量和生产效率。
为了提高塑料注射模的设计效率和准确性,许多公司或个人开发了各种塑料注射模设计程序。
本文将介绍一种基于计算机辅助设计(CAD)的塑料注射模设计程序,并探讨其在实际应用中的优势和潜在问题。
程序功能该塑料注射模设计程序具有以下功能:1.塑料注射模图形建模:通过绘制平面图、剖面图和三维模型,准确描述了注射模的结构和形状。
2.零件装配:将注射模的各个零部件按照设计要求进行装配,确保整个注射模的功能完善。
3.参数调整:通过调整注射模的参数,如模具尺寸、冷却系统等,优化设计方案,实现最佳的注射模性能。
4.工程图纸生成:根据注射模的设计,自动生成详细的工程图纸,方便制造和装配。
程序优势相比传统的手工设计,基于CAD的塑料注射模设计程序具有以下优势:1.提高设计效率:使用CAD软件进行设计,可以快速绘制和修改注射模图形,大大缩短了设计周期。
2.提高设计准确性:CAD软件可以精确计算各个零部件的尺寸和装配间隙,避免了手工绘图中可能出现的误差。
3.优化设计方案:程序通过参数调整功能,可以自动模拟注射模在不同工况下的性能,以实现最佳设计方案。
4.方便协作与共享:CAD软件支持文件的导入和导出,方便设计师之间的协作和共享设计文件。
程序潜在问题尽管基于CAD的塑料注射模设计程序具有众多优势,但也存在一些潜在问题需要注意:1.学习成本较高:使用CAD软件需要一定的培训和学习成本,特别是对于没有相关经验的设计师来说。
2.软件兼容性:不同的CAD软件存在兼容性问题,可能会因为文件格式的差异导致协作和共享的困难。
3.依赖于计算机硬件:程序需要较高性能的计算机硬件支持,特别是处理大型注射模设计时。
结论基于计算机辅助设计(CAD)的塑料注射模设计程序在推动塑料注射模设计领域的发展中起到了重要作用。
它们提高了设计效率和准确性,优化了设计方案,并方便了设计师之间的协作与共享。
第2章 塑料注射模设计要点

第2章塑料注射模设计要点塑料注射模是塑料模具中产量、产值最大,同时也是技术难度最大的一类模具。
因此,模具设计实训中应至少完成一副塑料注射模的设计〔以下除非特殊注明,本书中的塑料模一般指应该实是根基塑料注射模〕;本章结合企业的工作实际,将塑料模相关的设计要点与标准做一简要的复习。
2.1 常用塑料及其成型特点常见塑料的中英文名称及与模具设计相关的参数,如表2-1和表2-2所示。
表2-常用的工程塑料及其成型特点表2-常用的通用塑料及其成型特点2.2 塑料注射模的全然组成一般情况下,关于塑料模具而言,要紧有二类,一类为二板模,俗称大水口模;另一类为三板模,俗称细水口模。
不管是二板模,依旧三板模,塑料模具一般由以下几个局部组成。
1、模架:模架构成了塑料模具最全然的框架局部。
模架一般可从专业模架厂商处直截了当采购。
2、塑料模具的核心局部——型腔和型芯:主型腔和主型芯俗称模仁或内模,是模具里面最重要的组成局部。
设计工作的大局部时刻的也花费在模仁的设计上。
只是,相对有些比立简单的模具,它没有模仁局部,产品直截了当在模板上面成形,特殊是早期的塑料模具大都如此,这种结构差不多逐步淘汰。
3、塑料模具附助零件:如定位环、浇口套、推杆〔也称顶杆或顶针〕、拉料杆〔俗称抓料销〕、支撑柱、顶出板导柱导套、支撑钉〔俗称垃圾钉〕等。
要是是三板模,往往还要设置专门的顺序开模操纵机构。
4、塑料模具的附助系统:一般的塑料模具有以下三个系统:浇注系统、顶出系统、冷却系统。
有时,因为所运用的塑料材料需加热的温度特殊高,因此,有的模具还会存在一个加热系统。
5、当塑料制品侧向有孔或卡勾的时候,模具还必须设置一个或多个处理这些孔、卡脱模的机构,如滑块、歪推杆杆、油压缸等等。
这种处理的机构称之为侧向分型与抽芯机构。
2.3 标准模架为了在缩短模具的设计与制造时刻,模具制造企业的往往将工作的重点放在模仁的设计与加工上,而作为根底构建的模架往往采纳专业厂家的标准模架。
第2章节 塑料注射模设计要点
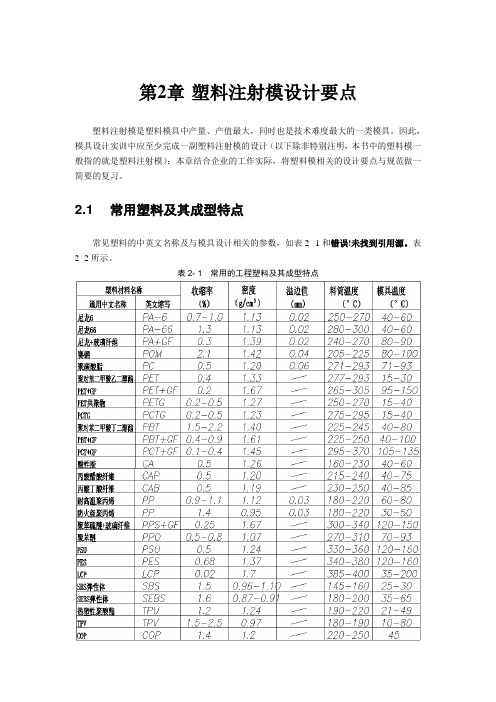
第2章塑料注射模设计要点塑料注射模是塑料模具中产量、产值最大,同时也是技术难度最大的一类模具。
因此,模具设计实训中应至少完成一副塑料注射模的设计(以下除非特别注明,本书中的塑料模一般指的就是塑料注射模);本章结合企业的工作实际,将塑料模相关的设计要点与规范做一简要的复习。
2.1 常用塑料及其成型特点常见塑料的中英文名称及与模具设计相关的参数,如表2- 1和错误!未找到引用源。
表2- 2所示。
表2- 1 常用的工程塑料及其成型特点表2- 2 常用的通用塑料及其成型特点2.2 塑料注射模的基本组成一般情况下,对于塑料模具而言,主要有二类,一类为二板模,俗称大水口模;另一类为三板模,俗称细水口模。
不管是二板模,还是三板模,塑料模具一般由以下几个部分组成。
1、模架:模架构成了塑料模具最基本的框架部分。
模架一般可从专业模架厂商处直接采购。
2、塑料模具的核心部分——型腔和型芯:主型腔和主型芯俗称模仁或内模,是模具里面最重要的组成部分。
设计工作的大部分时间的也花费在模仁的设计上。
不过,相对有些比较简单的模具,它没有模仁部分,产品直接在模板上面成形,特别是早期的塑料模具大都如此,这种结构已经逐步淘汰。
3、塑料模具附助零件:如定位环、浇口套、推杆(也称顶杆或顶针)、拉料杆(俗称抓料销)、支撑柱、顶出板导柱导套、支撑钉(俗称垃圾钉)等。
如果是三板模,往往还要设置专门的顺序开模控制机构。
4、塑料模具的附助系统:一般的塑料模具有以下三个系统:浇注系统、顶出系统、冷却系统。
有时,因为所运用的塑料材料需加热的温度很高,所以,有的模具还会存在一个加热系统。
5、当塑料制品侧向有孔或卡勾的时候,模具还必须设置一个或多个处理这些孔、卡脱模的机构,如滑块、斜推杆杆、油压缸等等。
这种处理的机构称之为侧向分型与抽芯机构。
2.3 标准模架为了在缩短模具的设计与制造时间,模具制造企业的往往将工作的重点放在模仁的设计与加工上,而作为基础构建的模架往往采用专业厂家的标准模架。
塑料注射成型模具设计程序
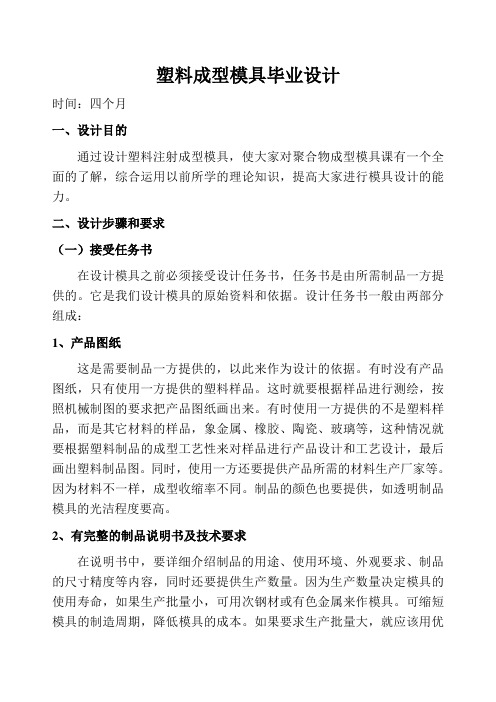
塑料成型模具毕业设计时间:四个月一、设计目的通过设计塑料注射成型模具,使大家对聚合物成型模具课有一个全面的了解,综合运用以前所学的理论知识,提高大家进行模具设计的能力。
二、设计步骤和要求(一)接受任务书在设计模具之前必须接受设计任务书,任务书是由所需制品一方提供的。
它是我们设计模具的原始资料和依据。
设计任务书一般由两部分组成:1、产品图纸这是需要制品一方提供的,以此来作为设计的依据。
有时没有产品图纸,只有使用一方提供的塑料样品。
这时就要根据样品进行测绘,按照机械制图的要求把产品图纸画出来。
有时使用一方提供的不是塑料样品,而是其它材料的样品,象金属、橡胶、陶瓷、玻璃等,这种情况就要根据塑料制品的成型工艺性来对样品进行产品设计和工艺设计,最后画出塑料制品图。
同时,使用一方还要提供产品所需的材料生产厂家等。
因为材料不一样,成型收缩率不同。
制品的颜色也要提供,如透明制品模具的光洁程度要高。
2、有完整的制品说明书及技术要求在说明书中,要详细介绍制品的用途、使用环境、外观要求、制品的尺寸精度等内容,同时还要提供生产数量。
因为生产数量决定模具的使用寿命,如果生产批量小,可用次钢材或有色金属来作模具。
可缩短模具的制造周期,降低模具的成本。
如果要求生产批量大,就应该用优质钢材来做模具,以提高模具的使用寿命。
我们这次设计任务就是给大家一个塑料制品,根据制品的形状、尺寸、技术要求等设计出一套完整的塑料注射成型模具。
当我们拿到这个制品时,首先要做的工作就是:1)绘制产品图产品图是我们设计注射模具的根据,因此要严格按照机械制图的要求,对制品进行测绘,画出图纸,并标明制品的材料,图纸比例及制品的一些特殊要求。
像制品的生产批量、体积、重量、特殊的使用条件,与其它零件的配合等。
2)标注出全部的尺寸自己测绘下来的产品图标注上全部的尺寸,塑料件的尺寸公差先在讲义P235上表3-2常用材料公差等级中选用一般精度来确定塑件的精度等级,对照P236上表3-3根据孔正轴负的原则来确定公差值。
注射模设计步骤及实例

选择排气的方法,排气槽位置、大小等。
整理ppt
11
模具设计中或初步设计完成后,一般还需 进行以下校核:
① 校核所选择的注射机注射压力和锁模力能否满 足塑件成型要求,校核模具外形尺寸可否方便 安装,行程是否满足模塑成型要求及取件要求。
② 对成型零件和主要受力零部件必须校核其强度 和刚度,尤其是刚度。
⑤ 有关试模及检查方面的要求。
整理ppt
17
4.14.10 总装图和零件图的绘制
整理ppt
18
6. 绘制全部零件图
由模具总装图拆画零件图的顺序应为:先内后外,先成型 零件后结构零件。
零件图的绘制和尺寸标注应符合机械制图国家标准的规定, 要注明全部尺寸、公差配合、表面粗糙度、材料、热处理要求 及其他技术要求,模具零件在图样上位置应该按该零件在装配 图中方位画出,不要随意旋转或颠倒,以防画错,影响装配。
循环周期等。
整理ppt
6
3. 模具结构设计
注射模具的结构设计一般需解决以下问题:
① 选定分型面 ② 确定型腔的数目和布置 ③ 浇注系统的设计 ④ 成型零部件的设计 ⑤ 脱模推出结构的设计 ⑥ 侧向分型抽芯机构的设计 ⑦ 温度调节系统的设计 ⑧ 排气系统的设计 ⑨ 模具外形结构及所有连接、定位、导向件位置的设计。
模具温度: 50~70°C ;
注射压力: 60~100MPa ;
成形时间: 注射时间2~5s,保压时间5~10s,
冷却时间5~15s整。理ppt
23
2. 模具的基本结构
(1)确定成型方法
塑件采用注射成型法生产。为保证塑件表面质量, 使用点浇口成形,因此模具应为双分型面注射模( 三板 式注射模)。
整理ppt
塑料注射模设计程序

2021年3月7日
7.2塑料模设计及制造实例
二、确定成型设备选择与模塑工艺规程编制
1.计算塑件的体积和重量
⑴计算塑件的体积:V=200172.30mm3(过程略) ⑵计算塑件的重量:根据有关手册查得ρ=1.2Kg·dm3 所以,塑件的重量为:W=ρV =200172.30×1.2×10-3 =240.20g
图a小端为分型面
图b大端为分型面
采用这种方案,侧面抽芯机构设在动模部分,模具结构也较 为简单。所以,选塑件大端底平面作为分型面较为合适。 18
7.2塑料模设计及制造实例
三、注射模的结构设计
2021年3月7日
2.型腔数目的确定及型腔的排列
由于该塑件采用的是一模一件成型,所以,型腔布 置在模具的中间。这样也有利于浇注系统的排列和模具 的平衡。
1.型芯和型腔工作尺寸的计算 2.侧壁厚度与底板厚度的计算 3.斜导柱等侧抽芯有关计算 4.冷却与加热系统有关计算
5
7.1塑料模设计程序
四、绘制模具结构草图
2021年3月7日
模具结构方案和有关尺寸确定后绘制模具结构草图
逐步完善和确定各零件的结构和尺寸
尽量选用标准组合结构和标准件
草图结束要对初选设备做全面校核
12
7.2塑料模设计及制造实例
一、塑件的工艺性分析
1.塑件的原材料分析
2021年3月7日
结论
1.熔融温度高且熔体粘度大,对于大于200g的塑件应用螺杆式 注射机成型,喷嘴宜用敞开式延伸喷嘴,并加热,严格控制模 具温度,一般在70~1200为宜,模具应用耐磨钢,并淬火; 2.水敏性强,加工前必须干燥处理,否则会出现银丝、气泡及 强度显著下降现象; 3.易产生应力集中,严格控制成型条件,塑件成型后需退火处 理,消除内应力;塑件壁不宜厚,避免有尖角、缺口和金属嵌 件造成应力集中,脱模斜度宜取20。
注射模设计程序及设计实例

注射模设计程序及设计实例一、注射模设计须考虑的问题在进行注射模设计之前,必须考虑好以下问题:1)仔细阅读“模具设计任务书”,明确塑件所用塑料的牌号与要求、塑件的技术要求、成型方法、生产批量以及塑件的使用功能。
2)针对“任务书”中的塑件零件图或提供的塑件进行产品结构工艺分析,确定成型方法的可行性,必要时还要与塑件工艺员或塑件结构设计人员进行技术交流。
3)了解模具制造单位的生产条件和生产习惯,并掌握模具使用单位的成型设备资料和注射工艺水平,准备着手进行注射模设计。
二、设计程序模具设计的程序不是一成不变的,其基本步骤如下:1.初步估算塑件(包括浇注系统凝料在内)的体积及质量。
塑件的体积及质量越大,浇注系统凝料所占的比例越小;反之,越大。
2.初选注射成型机的型号和规格。
3.确定模具基本结构(应对多种方案进行分析比较)。
4.进行模具结构方案设计。
(1)确定型腔数目及配置;(2)选择分型面;(3)确定浇注系统;(4)确定型腔、型芯的结构及固定方式;(5)确定脱模推出机构的结构类型,需要侧向抽芯的,要确定侧向抽芯机构的结构类型;(6)确定导向机构的具体结构;(7)确定排气机构;(8)确定模具加热、冷却方式;(9)绘制模具装配草图。
5.相关模具零件的强度、刚度校核,以及模具与注射成型机的相关参数的校核。
6.根据模具零件的强度、刚度校核,修改完善模具装配图。
7.拆画非标准模具零件图。
8.复核设计图样。
三、设计举例与分析图1所示为电脑编织机的专用调节旋钮,材料为ABS塑料,精度等级为一般精度(4 级精度),制品要求外观表面光泽、无杂色,无收缩痕迹,生产批量中等。
试设计注射成型模具。
图1 塑料旋钮零件图(一)产品工艺性分析1.材料性能ABS为热塑性材料,密度1.03~1.07g/cm3,抗拉强度30~5OMPa,抗弯强度41~76MPa,拉伸弹性模量1587~2277 MPa,弯曲弹性模量1380~2690 MPa,收缩率0.3%~0.8%, 常取0.5%。
注射模的设计步骤

确定型腔数目
绘制模具的结构草图
校核模具有关零 件的强度及刚度
选择分型面 确定型腔的配置 确定浇注系统
确定排气方式
确定凹模和型芯 的结构和固定方式
校核模具与注射 机的有关尺寸
绘制模具总装图和 非标准零件工作图
确定脱模方式
冷却系统和 推出机构的细化
复核设计图样
塑料成型工艺与模具设计
ቤተ መጻሕፍቲ ባይዱ
塑料成型工艺与模具设计
注射模的设计步骤
1.1 设计前的准备工作
1.
经过审签的正规制品图纸
明确设计任务
塑件说明书及技术要求
塑件的生产量及所用注射机 注射模具的基本
结构、交货期限及价格
2.
熟悉塑件结构 分析塑件工艺性
熟悉塑件几何形状 明确使用要求
检查塑件的成型工艺性
明确注射机的型号和规格
1.2 注射模结构设计的一般步骤
试述塑料注射模设计流程及主要内容

试述塑料注射模设计流程及主要内容【英文回答】。
Plastic Injection Mold Design Process and Key Considerations.The plastic injection mold design process plays a crucial role in the manufacturing of plastic products. It involves a series of steps that determine the quality and efficiency of the mold. Here's an overview of the process and its key aspects:1. Part Design Analysis:The process begins with analyzing the part design to understand its geometry, dimensions, and any special requirements. This analysis helps identify potential challenges and areas for optimization.2. Mold Concept Development:Based on the part design, the mold designer develops a concept that defines the mold's overall structure, layout, and components. It involves determining the number of cavities, gate location, and cooling channels.3. Mold Design Detailing:The next step involves detailing the mold design by specifying the dimensions, tolerances, and materials for each component. It includes designing the mold base, cavity inserts, core inserts, and ejector system.4. Mold Simulation and Analysis:The mold design is then simulated and analyzed using specialized software to predict the molding process and identify potential issues. This step helps optimize the design for efficient filling and cooling.5. Mold Manufacturing:Once the design is finalized, the mold is manufactured using precision machining and other techniques. This process requires high accuracy and attention to detail to ensure the mold meets the design specifications.6. Mold Testing and Optimization:After manufacturing, the mold undergoes testing to verify its performance and identify any necessary adjustments. This involves running trial shots to evaluate the product quality, cycle time, and any potential defects.Key Considerations for Plastic Injection Mold Design:Material selection: The mold material must be compatible with the plastic resin and withstand the molding process conditions.Gate design: The gate location and type influence the flow of plastic into the mold and ultimately the product quality.Cooling system: Efficient cooling channels ensure the plastic solidifies properly and reduces cycle time.Ejection system: The ejector system must effectively remove the finished products from the mold without causing damage.Surface finish: The mold's surface finish impacts the product's appearance and functionality.【中文回答】。
- 1、下载文档前请自行甄别文档内容的完整性,平台不提供额外的编辑、内容补充、找答案等附加服务。
- 2、"仅部分预览"的文档,不可在线预览部分如存在完整性等问题,可反馈申请退款(可完整预览的文档不适用该条件!)。
- 3、如文档侵犯您的权益,请联系客服反馈,我们会尽快为您处理(人工客服工作时间:9:00-18:30)。
在设计塑料注射模时,其设计程序和设计要点大致如下:
1. 研究分析产品零件图纸,掌握塑件的用途\使用和外观要求\装配精度及确定所允许的浇口及飞边位置,并要了解塑料品种及其成形的工艺性。
2. 选择注射机规格\型号。
3. 按塑件生产批量\注射机的规格和塑件大小,确定出一模可出几个塑件及位置布置方案。
4. 确定模具结构方案。
在确定时,可构思几种模具结构形式,进行分析比较,最后确定一种容易制造\便于操作\确保成型塑件质量的模具结构。
5. 核定以下几个注射工艺参数。
i. 根据塑件大小以及所确定的一模多件状况,核定注射机的容量是否合适。
ii. 计算型腔压力,核定注射机锁模力。
iii. 选择与注射机工作台面相适应的标准模架规格,核定模架是否能容纳所定的一模多腔的塑件数量,并考虑模架的安装及固定方法。
iv. 经上述计算和核定后,若不合适,应给以重新确定模具结构方案。
v. 选择推件机构,推出机构一定要设计得合理,不能使塑件变形,并要核对注射机的开模距能否取出塑件及推出方式。
vi. 在注射机上的定位方法,包括定位直径,喷嘴孔直径及喷嘴定位直径等。
6. 绘制模具总装配图。
i. 画出模具中心线及模具主视及侧视图外形线。
确定支模与定模的分型面,确保塑件留在动模一侧。
ii. 画出塑件位置及动模\定模型芯\流道和浇口位置。
iii. 在动模投影面上出塑像件位置\动模芯\流道\冷却水道\布置导向孔\复位杆孔\推杆孔及固定螺钉和销钉孔位置,并在主视图上表示各零件的零的装配关系,必要时要加剖面剖视图。
有抽芯机构时,要同时出。
iv. 填写标题栏及技术要求。
7. 对模具各部位进行必要的强度及刚度计算和核对,不例行时,应给以修订或加强。
8. 画出各零件图,如成型零件的成形尺寸要进行必要的计算,并标出公并非,表面质量及技术要求。
9. 校对\审核并进行必要的个性。
10. 完成设计\制图\校对或审核签字后,可进行描图复印。