金属大型锻件热处理论文
金属材料与热处理论文关于金属材料的论文
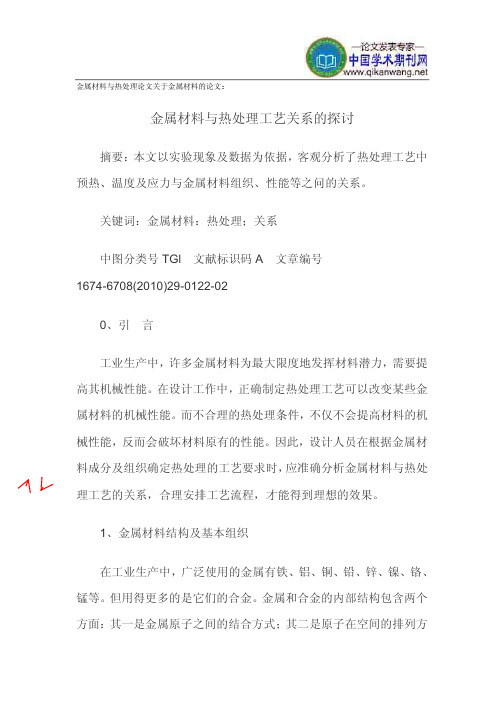
。的目的裂淬制抑终最和值力应小减 到达而从 �度速缩收的属金位部心中面截和差温面截小减量尽于在而
形变的来原替代来粒晶轴等的新生产域区的烈剧最形变在会 �后以度 温的高够足到热加属金形变冷当 。得获晶结再后理处热过通要主则化 细的织组属金而 。性韧强料材高提而从移滑错位碍阻而高增例比占所 界晶使粒晶化细过通是理原其 �法方要重种一的错位中体晶属金少减 是化强晶细。度强属金高提而从�降下度密错位的中料材属金使�错 位中体晶属金少减要是键关的性韧裂断属金高提。能性的展扩纹裂 抗抵下用作力外在料材的纹裂有含为解理以可际实性韧裂断 。纹裂的 寸尺同不、量数同不有含都际实料材何任�是点发出的学力裂断 系关的度温理处热与性韧裂断的料材属金 3.2
余残由是力应的裂开蚀腐力应起引分部大 。裂开蚀腐力应为称坏破裂 断性脆的生发下用作同共境环蚀腐定特和力应伸拉在料材属金 系关的力应理处热与裂开蚀腐力应抗料材属金 4.2
。性韧裂断的料材属金高提 以可�度温的理处热制控出得以可就们我�么那。行进能才程过晶结 再�时移迁行进能其使�子原活激以足�上之度温定一到热加属金形 变将须必此因�散扩的子原要需都大长与成形的核晶晶结再。段阶的 烈剧为最化变能性观宏的钢是�度温右左℃009�此因。大长始开粒 晶 �上以℃009 在 。级 2lBY 到达度粒晶 �粒晶轴等为部全乎几 �小细得 变然突粒晶�始开形变℃009 在。主为粒晶的长拉形变以然仍但�现 出量少有经已粒晶轴等中粒晶的形变℃008。化变状形的粒晶轴等 向渐逐始开粒晶的平扁�时℃007 在�为象现验实。貌形粒晶示显质 物学化用后光抛磨研�开剖割切线向轴沿样试的后缩压将再�理处火 退的)冷空(CAh6×℃086 行进再�温室至冷中气空在后然��05 形变 缩压 s03 温保率速形变的 1-01×5 以上机验试拟模热型 0051-elbeelC 在℃0011 和℃0001、℃009�℃008�℃007 在择选�后工 加机�柱圆小的当适割切线上料坯钢 YS 在�明证验实下以过通以可 。系关的显明有坏好果效晶结再的属金对度温同不 �此因 。晶结再态动 生发致导 �别级度密错位部局的高够足到累积会才中程过形变在料材 �下件条的度温形变和力应的定一在有只 。晶结再为称程过个这 �粒晶
锻件热处理技术
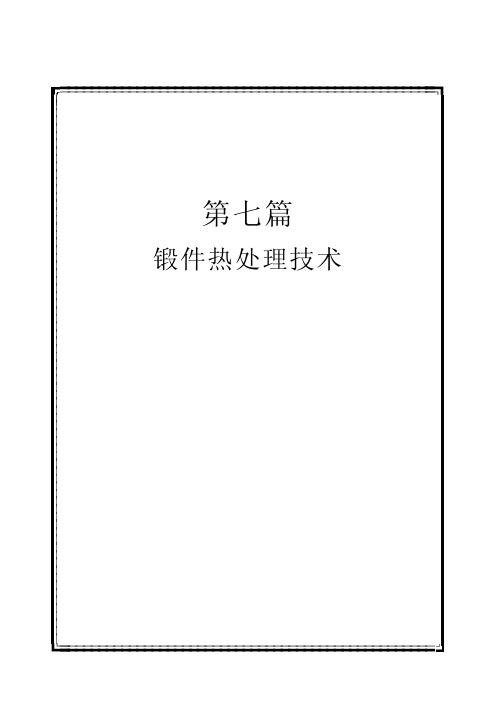
一、加热的目的和要求
(ÿ)加热的目的 提高金属的塑性,降低金属变形抗力,使之 易 于 成形,并 获 得良 好 的 锻后 组 织 和 力 学
差,以致造成过大的热应力,再叠加其它内应力,引起材料破裂。 ü准确实施给定的加热规 范,如 加 热 温 度、速 度、时 间 和 保 温 等 加 热 条 件,以 防 产 生
过热、过烧等缺陷。
二、加热方法
在锻压生产中,按采用热源不同,加热方法可分为燃料火焰加热和电加热两大类。 · ÿþüý ·
第七篇 锻件热处理技术
中小件
单件、成批
自由锻、 模锻
无炉门、多 采用 上排烟
中小件及 局部加热
成批
胎模锻、 模锻
炉 底 可 进 出 运 大、中型坯 动,便于装出料 料及钢锭
单件、中 小批量
自由锻、 钢锭开坯
利用燃料不完全 燃烧形成保护气 氛
中小件
成批
精密模锻
推杆式炉 连 续 式 加 热
转壁炉
转底炉
液、气
液、气 液、气
用推 料 机 推 料,
ÿÿÿÿÿÿÿÿÿÿÿÿÿÿÿÿÿÿÿÿÿÿÿÿÿÿÿÿÿÿÿÿÿÿÿÿÿÿÿÿÿÿÿÿÿÿÿÿÿþ
第七篇
锻件热处理技术
ÿÿÿÿÿÿÿÿÿÿÿÿÿÿÿÿÿÿÿÿÿÿÿÿÿÿÿÿÿÿÿÿÿÿÿÿÿÿÿÿÿÿÿÿÿÿÿÿÿþ
第一章 金属的锻造温度与加热规范
第一章 金属的锻造温度与加热规范
第一节 加热目的和加热方法
ÿþ 燃料火焰加热法 燃料火焰加热法(简称火焰加热法)是利用固体(煤、焦炭等)、液体(重油、柴油等)或 气体(煤气、天然气等)燃料燃烧所发生的热能加热坯料的方法,是在加热炉内进行。 火焰加热炉通用性强,投资少,建造比较容 易;燃 料 来 源广 泛,费 用比 较 低,所 以 广 为 采用。但是,火焰加热炉炉温和气氛较难控制,加温工劳动条件差。 火焰加热和常用加热炉的特点及应用范围见表 ý ü ÿ ü ÿ。
大型锻件锻后热处理的研究及注意事项

河北汇 工机械设备有 限公 司 ( 巨鹿 0 5 5 2 5 0 ) 杨钟胜
大 型 锻 件 的 白点 和氢 脆 缺 陷 的危 害性 很 大 ,所
以 大 型锻 件 锻 后 热 处 理 要 求 防 止 白点 和 氢 脆 ,同
瞬 间 形成 ,而 是 逐 渐 形成 的 。从 停 锻到 出现 白 点 , 需 要 经 历一 段时 间 ,这 段时 间称 之 为 白 点形 成 的孕 育 期 或潜 伏 期 。孕 育 期 的长 短取 决 于钢 的含 氢量 , 同时 也取 决 于锻 件 的厚 度 。
力 ,重结 晶细 化 晶粒 ,同时 去 氢 。
1 . 有关钢 中白点 的基本概念
( 1 )白点的危害性 白点是过 高 时 ,钢 显著 变
脆 ,从 本 质来 看 , 白点也 属 于脆 性 破 坏 。 白点 的存 在 使 钢 的 力学 性 能 特 别 是 横 向 塑 性 和 韧 性 急 剧 降 低 ,成 为最 危 险 的断 裂源 ,严 重影 响 零件 的 使 用性 能 和 寿 命 。 因此 ,锻 件 中一 旦 发现 白点 ,则 该 锻件 必须 报 废 。 ( 2 ) 白点 的 形 貌 在 锻 件 的 纵 向断 裂 面 上 呈
中含有足够数量的氢是形成白点的必要条件,内应
力 的存 在具 有 促进 白点形 成 的作 用 。 ( 5 )白 点 的 三大 特 点 ① 白点 从 来 不 在 锻 件 的 表面 形 成 。根 据 有 关资 料表 明 ,其形 成 总是 在 锻 件 内部 ,含有 白点 的 区域 离锻 件 表 面有 相 当一 段 距 离 ,约 5 0 mm。② 白点是 在 锻 后 ,当 锻件 冷 却 到 比
即进 行 锻后 去 氢 退火 。
金属材料热处理学期论文
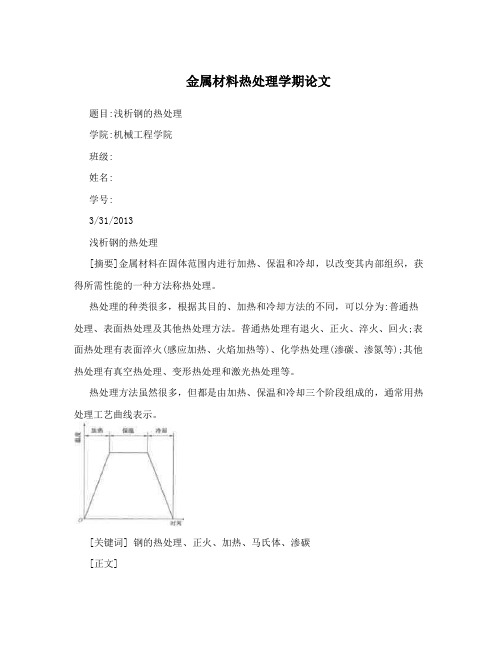
金属材料热处理学期论文题目:浅析钢的热处理学院:机械工程学院班级:姓名:学号:3/31/2013浅析钢的热处理[摘要]金属材料在固体范围内进行加热、保温和冷却,以改变其内部组织,获得所需性能的一种方法称热处理。
热处理的种类很多,根据其目的、加热和冷却方法的不同,可以分为:普通热处理、表面热处理及其他热处理方法。
普通热处理有退火、正火、淬火、回火;表面热处理有表面淬火(感应加热、火焰加热等)、化学热处理(渗碳、渗氮等);其他热处理有真空热处理、变形热处理和激光热处理等。
热处理方法虽然很多,但都是由加热、保温和冷却三个阶段组成的,通常用热处理工艺曲线表示。
[关键词] 钢的热处理、正火、加热、马氏体、渗碳[正文]一、钢的普通热处理根据加热及冷却的方法不同,获得金属材料的组织及性能也不同。
普通热处理可分为退火、正火、淬火和回火四种。
普通热处理是钢制零件制造过程中非常重要的工序。
退火1(退火工艺及其目的退火是将工件加热到适当温度,保温一定时间,然后缓慢冷却的热处理工艺,实际生产中常采取随炉冷却的方式。
退火的主要目的:?降低硬度,改善钢的成形和切削加工性能;?均匀钢的化学成分和组织;?消除内应力。
2(常用退火工艺方法根据处理的目的和要求的不同,钢的退火可分为完全退火、球化退火和去应力退火等。
下表为主要退火工艺方法及其应用。
名称工艺目的应用将钢加热至Ac以上330,50?,保温一定时间,主要用于亚共细化晶粒,消除过热完全退炉冷至室温析钢的铸、锻组织,降低硬度和改善火 (或炉冷至600?以下,件,有时也用于切削加工性能出炉空冷) 焊接结构使钢中的渗碳体球状将钢加热至Ac以上化,以降低钢的硬度,120,40?,保温一定时改善切削加工性,并为间,炉冷至室温,或快以后的热处理做好组织球化退主要用于共析速冷至略低于Ar温度,准备。
若钢的原始组织1火钢和过共析钢保温后出炉空冷,使钢中有严重的渗碳体网,中碳化物球状化的退火则在球化退火前应进行工艺正火消除,以保证球化退火效果使钢的化学成分和组均匀化退将钢加热到略低于固相织均匀化主要用于质量火(扩散线温度(Ac或Ac以上要求高的合金3cm退火) 150~300?),长时间保温铸锭、铸件或锻(10~15h),随炉冷却。
金属材料热处理工艺论文
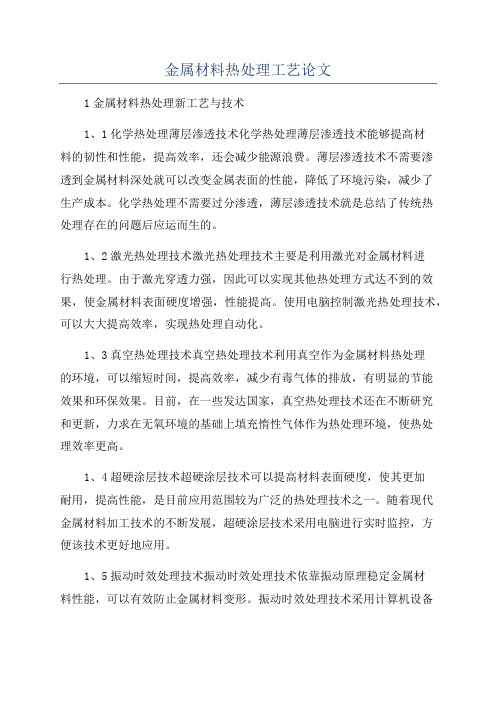
金属材料热处理工艺论文1金属材料热处理新工艺与技术1、1化学热处理薄层渗透技术化学热处理薄层渗透技术能够提高材料的韧性和性能,提高效率,还会减少能源浪费。
薄层渗透技术不需要渗透到金属材料深处就可以改变金属表面的性能,降低了环境污染,减少了生产成本。
化学热处理不需要过分渗透,薄层渗透技术就是总结了传统热处理存在的问题后应运而生的。
1、2激光热处理技术激光热处理技术主要是利用激光对金属材料进行热处理。
由于激光穿透力强,因此可以实现其他热处理方式达不到的效果,使金属材料表面硬度增强,性能提高。
使用电脑控制激光热处理技术,可以大大提高效率,实现热处理自动化。
1、3真空热处理技术真空热处理技术利用真空作为金属材料热处理的环境,可以缩短时间,提高效率,减少有毒气体的排放,有明显的节能效果和环保效果。
目前,在一些发达国家,真空热处理技术还在不断研究和更新,力求在无氧环境的基础上填充惰性气体作为热处理环境,使热处理效率更高。
1、4超硬涂层技术超硬涂层技术可以提高材料表面硬度,使其更加耐用,提高性能,是目前应用范围较为广泛的热处理技术之一。
随着现代金属材料加工技术的不断发展,超硬涂层技术采用电脑进行实时监控,方便该技术更好地应用。
1、5振动时效处理技术振动时效处理技术依靠振动原理稳定金属材料性能,可以有效防止金属材料变形。
振动时效处理技术采用计算机设备进行监控,既可以减少生产时间,提高效率,还能够降低成本,节能减耗,克服了传统热处理技术的不足。
2金属材料热处理工艺与技术展望随着金属材料热处理工艺与技术的不断发展,诞生了许多热处理技术。
其中,可控气氛热处理就是较为成熟的热处理技术之一。
可控气氛,顾名思义,就是一种可以控制和保护的气氛,是一种保护金属材料的气体介质。
可控气氛可以有效保护金属材料的表面性能,使热处理过程更为完善。
对于钢制工件而言,可控气氛热处理极为适合,可以给钢材料提供更为妥善的保护。
这是因为钢在热处理高温中很容易被氧化,表面破坏较为严重,但可控气氛热处理却能够避免钢被氧化。
钢的热处理原理与方法论文
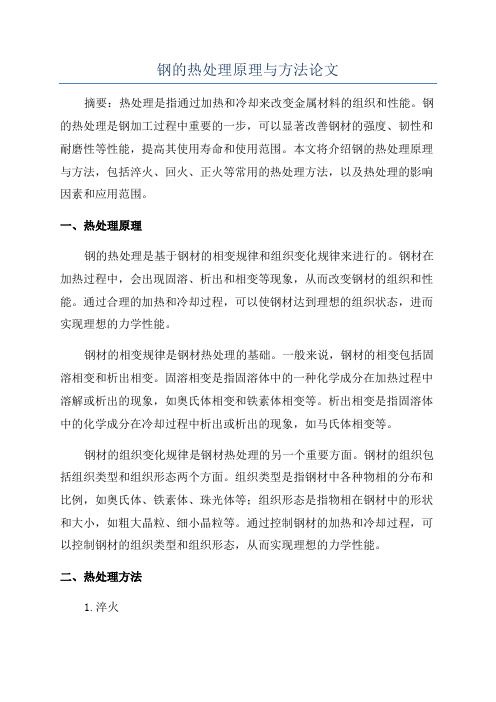
钢的热处理原理与方法论文摘要:热处理是指通过加热和冷却来改变金属材料的组织和性能。
钢的热处理是钢加工过程中重要的一步,可以显著改善钢材的强度、韧性和耐磨性等性能,提高其使用寿命和使用范围。
本文将介绍钢的热处理原理与方法,包括淬火、回火、正火等常用的热处理方法,以及热处理的影响因素和应用范围。
一、热处理原理钢的热处理是基于钢材的相变规律和组织变化规律来进行的。
钢材在加热过程中,会出现固溶、析出和相变等现象,从而改变钢材的组织和性能。
通过合理的加热和冷却过程,可以使钢材达到理想的组织状态,进而实现理想的力学性能。
钢材的相变规律是钢材热处理的基础。
一般来说,钢材的相变包括固溶相变和析出相变。
固溶相变是指固溶体中的一种化学成分在加热过程中溶解或析出的现象,如奥氏体相变和铁素体相变等。
析出相变是指固溶体中的化学成分在冷却过程中析出或析出的现象,如马氏体相变等。
钢材的组织变化规律是钢材热处理的另一个重要方面。
钢材的组织包括组织类型和组织形态两个方面。
组织类型是指钢材中各种物相的分布和比例,如奥氏体、铁素体、珠光体等;组织形态是指物相在钢材中的形状和大小,如粗大晶粒、细小晶粒等。
通过控制钢材的加热和冷却过程,可以控制钢材的组织类型和组织形态,从而实现理想的力学性能。
二、热处理方法1.淬火淬火是指将高温钢材迅速冷却到室温以下,使其产生马氏体相变。
马氏体具有高硬度和脆性的特点,可以显著提高钢材的硬度和强度,但降低了韧性。
因此,淬火一般需要进行回火处理来改善钢材的韧性。
2.回火回火是指将淬火后的钢材加热到较低温度并保温一段时间,然后冷却到室温。
回火可以消除淬火时产生的内应力和组织不均匀性,通过分解马氏体改善钢材的韧性,同时适当降低硬度和强度。
3.正火正火是指将低碳钢材加热到临界温度以上,保温一段时间,然后冷却至室温。
正火可以使铁素体相变为奥氏体,改善钢材的塑性和韧性,适用于需要保持一定塑性和耐久性的工件。
三、热处理的影响因素钢材的热处理效果和性能会受到多种因素的影响。
金属材料与热处理论文关于金属材料的论文
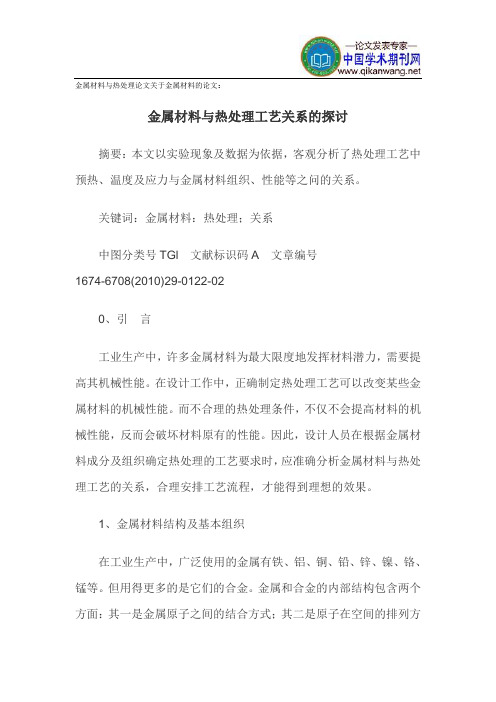
金属材料与热处理论文关于金属材料的论文:金属材料与热处理工艺关系的探讨摘要:本文以实验现象及数据为依据,客观分析了热处理工艺中预热、温度及应力与金属材料组织、性能等之问的关系。
关键词:金属材料:热处理;关系中图分类号TGl文献标识码A文章编号1674-6708(2010)29-0122-020、引言工业生产中,许多金属材料为最大限度地发挥材料潜力,需要提高其机械性能。
在设计工作中,正确制定热处理工艺可以改变某些金属材料的机械性能。
而不合理的热处理条件,不仅不会提高材料的机械性能,反而会破坏材料原有的性能。
因此,设计人员在根据金属材料成分及组织确定热处理的工艺要求时,应准确分析金属材料与热处理工艺的关系,合理安排工艺流程,才能得到理想的效果。
1、金属材料结构及基本组织在工业生产中,广泛使用的金属有铁、铝、铜、铅、锌、镍、铬、锰等。
但用得更多的是它们的合金。
金属和合金的内部结构包含两个方面:其一是金属原子之间的结合方式;其二是原子在空间的排列方式。
金属的性能和原子在空间的排列配置情况有密切的关系,原子排列方式不同,金属的性能就出现差异。
金属材料热处理过程是将金属工件放在一定的介质中加热到适宜的温度,并在此温度中保持一定时间后,又以不同速度在不同的介质中冷却,通过改变金属材料表面或内部的显微组织结构来改变其性能的一种工艺。
因此,对某些金属或合金来说,可以用热处理工艺来改变它的原子排列,进而改变其组织结构,控制其机械性能,以满足工程技术的需要。
不同的热处理条件会产生不同的材料性能改变效果,下面就金属的材料的某些性能来分析其与热处理工艺的关系,以便更好的提高材料的机械性能。
2、金属材料与热处理工艺的关系2.1金属材料的切削性能与热处理预热的关系金属材料加工的整个工艺流程中,如果切削加7-7-艺与热处理工艺之间能相互沟通,密切配合,对提高产品质量将有很大好处。
在金属切削过程中,由于被加工材料、切削刀具和切削条件的不同,金属的变形程度也不同,从而产生不同程度的光洁度。
大型锻件热处理过程的数值模拟研究
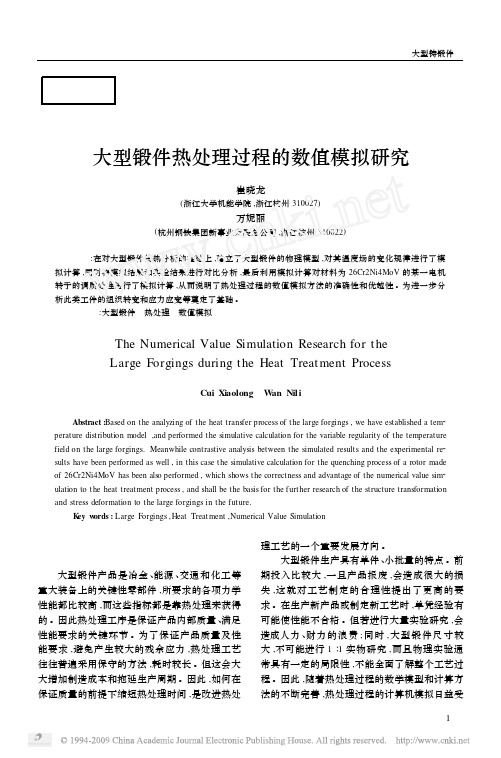
时间 (
8
10
12
14
16
18
20
无风
模拟值 实验值 绝对差值
724. 7 723. 3
1. 4
679. 1 682. 3
3. 2
646. 3 649. 8
3. 5
619. 5 617. 2
2. 3
595. 5 594. 0
1. 5
572. 7 574. 2
2
图 2 工件断面的几何形状
大型铸锻件
2. 2 建立差分方程
为了具体说明数值模拟在热处理过程中的
优越性 ,我们以图 2 所示的 L 形工件为例 ,用数
值模拟方法求解热处理时工件内温度场的变化
情况 ,然后和实验数据进行对比 。从而说明数值
模拟方法的准确性和优越性 。
用有限差分法求解 ,对内节点采用中心差
1. 5
550. 6 553. 4
2. 8
528. 7 525. 8
2. 9
507. 2 508. 8
1. 6
486. 1 487. 4
1. 3
A 向风
模拟值 实验值 绝对差值
648. 2 644. 8
3. 4
566. 1 567. 2
1. 1
512. 2 514. 5
2. 3
471. 7 473. 8
表 2 N 点温度变化过程( ℃)
6
8
10
12
765. 4 765. 8
0. 4
736. 0 733. 0
热微分方程[5 ] :
ρc
5T 5τ
=
λ(
52 T 5 x2
金属材料热处理毕业论文范文

金属材料热处理毕业论文范文一、论文说明本团队专注于毕业论文写作与辅导服务,擅长案例分析、编程仿真、图表绘制、理论分析等,论文写作300起,具体价格信息联系二、论文范文参考如下建筑金属材料与热处理工艺关系的探讨思路:在我国的建筑领域中,为了更好地提高建筑金属材料的利用效率,充分合理利用金属资源,在建筑金属材料的使用过程中,需要加强热处理工艺在金属材料中的应用,规范金属材料的加工处理工艺,努力做到物尽其用,节约资源。
如果建筑金属材料不能够使用合理正确的热处理工艺进行处理的话,不仅会对材料的机械性能造成不良影响,严重时还会破坏材料的原。
题目:金属材料热处理节能新技术分析思路:本文对金属材料热处理节能技术在我国机械工业中所起的作用,进行了深入的研究和分析。
近几年来随着科学技术的不断更新与发展,和随着我国经济实力的不断雄厚,发现我国在金属材料热处理中存在很多各式各样的问题。
对于机械工业和金属材料制造业来说,如何运用新的金属材料热处理节能技术,来减少在金属材料热处理环节中,对能源的高损耗和对环境。
题目:金属材料热处理节能新技术探析思路:随着现代社会科学技术与经济的不断飞速发展,机械工业以及制造业也迅速发展起来,对于工业制造中重要的金属材料来说,热处理技术是金属材料性能的保障。
在制造业中,热处理的数量很多,而且耗电量十分大,此外,热处理又是通过炉窑加热来使金属材料变化的,所以一定程度上对环境有所污染,所以,迫切要求热处理节能新技术的实际应用。
就金属材料。
题目:基于金属材料热处理节能新技术运用探究思路:本文通过对金属材料热处理新技术的研究,即节能新技术,来分析讨论我国目前金属材料热处理的发展,从而从中获取经验,来促进我国金属材料热处理节能技术的发展。
技术材料热处理的节能技术主要运用在真空热处理、热处理的震动实效处理、热处理CAD等方面。
题目:探讨金属材料与热处理工艺的关系思路:在现代工业生产中,机械性能的提高能使金属材料发挥最大限度的潜力。
金属材料热处理论文

金属材料热处理论文The final revision was on November 23, 2020金属材料热处理论文题目:热处理变形的影响因素专业:材料成型与控制热处理变形的影响因素摘要:工业发展日新月异,对机械精度和性能的要求也越来越高。
在工业零件生产中,热处理是必不可少的一部分,它对材料性能的影响非常大,金属热处理在改善材料各种性能的同时,热处理变形是不可避免的,并且会直接影响到工件的精度、强度、噪声和寿命,因此对于精度要求较高的零件要尽可能减小其变形量,着重分析温度是控制变形的关键因素的同时罗列几点次要因素。
关键词:热处理变形金属热处理变形因素温度一、引言什么是金属材料的热处理热处理有什么弊端(变形等)金属材料的热处理是将固态金属或合金,采用适当的方式进行加热、保温和冷却,有时并兼之以化学作用和机械作用,使金属合金内部的组织和结构发生改变,从而获得改善材料性能的工艺。
热处理工艺是使各种金属材料获得优良性能的重要手段。
很多实际应用中合理选用材料和各种成形工艺并不能满足金属工件所需要的力学性能、物理性能和化学性能,这时热处理工艺是必不可少的。
但是热处理工艺除了具有积极的作用之外,在处理过程中也不可避免地会产生或多或少的变形,而这又是机械加工中必须避免的,两者之间是共存而又需要避免的关系,只能采用相应的方法尽量把变形量控制在尽量小的范用内。
而要减小热处理的变形,我们就需要了解影响热处理变形的因素。
二、温度是变形的关键因素工业生产中实际应用的热处理工艺形式非常多,如退火,正火,回火,淬火等,但是它们的基本过程都是热作用过程,都是由加热、保温和冷却三个阶段组成的。
整个工艺过程都可以用加热速度、加热温度、保温时间、冷却速度以及热处理周期等几个参数来描述。
在热处理工艺中,要用到齐种加热炉,金属热处理便在这些加热炉中进行(如基本热处理中的退火、淬火、回火、化学热处理的渗碳、渗氨、渗铝、渗珞或去氢、去氧等等)。
热处理毕业论文:金属热处理(精编版)
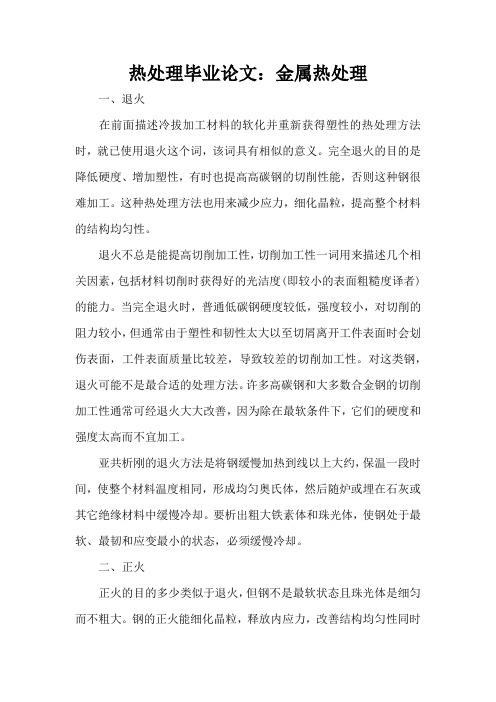
热处理毕业论文:金属热处理一、退火在前面描述冷拔加工材料的软化并重新获得塑性的热处理方法时,就已使用退火这个词,该词具有相似的意义。
完全退火的目的是降低硬度、增加塑性,有时也提高高碳钢的切削性能,否则这种钢很难加工。
这种热处理方法也用来减少应力,细化晶粒,提高整个材料的结构均匀性。
退火不总是能提高切削加工性,切削加工性一词用来描述几个相关因素,包括材料切削时获得好的光洁度(即较小的表面粗糙度译者)的能力。
当完全退火时,普通低碳钢硬度较低,强度较小,对切削的阻力较小,但通常由于塑性和韧性太大以至切屑离开工件表面时会划伤表面,工件表面质量比较差,导致较差的切削加工性。
对这类钢,退火可能不是最合适的处理方法。
许多高碳钢和大多数合金钢的切削加工性通常可经退火大大改善,因为除在最软条件下,它们的硬度和强度太高而不宜加工。
亚共析刚的退火方法是将钢缓慢加热到线以上大约,保温一段时间,使整个材料温度相同,形成均匀奥氏体,然后随炉或埋在石灰或其它绝缘材料中缓慢冷却。
要析出粗大铁素体和珠光体,使钢处于最软、最韧和应变最小的状态,必须缓慢冷却。
二、正火正火的目的多少类似于退火,但钢不是最软状态且珠光体是细匀而不粗大。
钢的正火能细化晶粒,释放内应力,改善结构均匀性同时恢复一些塑性,得到高的韧性。
这种方法经常用来改进切削加工性,减少应力,减少因部分切削加工或时效产生的变形。
正火方法是将亚析钢或过共析钢分别缓慢加热到ac3线或accm 线上约,保温一段时间以便形成奥氏体,并在静止空气中缓冷。
要注意,含碳量超过共析成分的钢要加热到accm线以上,而不是退火时的ac1线以上。
正火的目的是在奥氏体化过程中试图溶解所有渗碳体,从而尽可能减少晶界上的硬脆铁碳化合物,而得到小晶粒的细珠光体、最小自由铁素体和自由渗碳体。
三、球化退火通过球化退火可使钢得到最小的硬度和最大的塑性,它可使铁碳化合物以小球状分布在铁素体基体上。
为了使小颗粒球化更容易,通常对正火钢进行球化退火。
关于热处理的论文热处理工艺论文
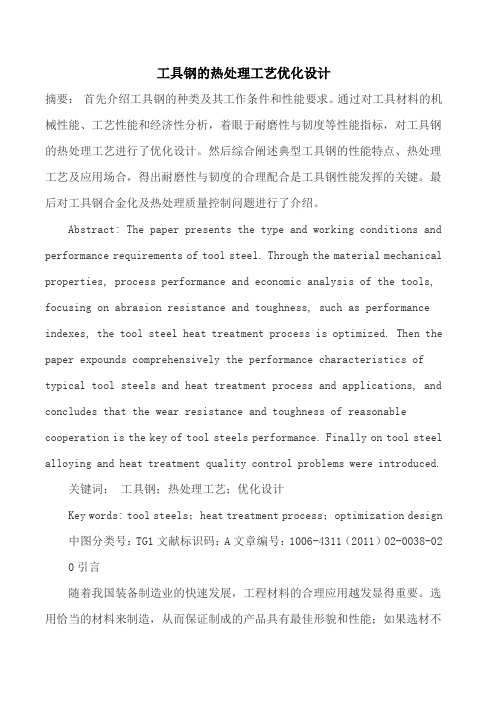
工具钢的热处理工艺优化设计摘要:首先介绍工具钢的种类及其工作条件和性能要求。
通过对工具材料的机械性能、工艺性能和经济性分析,着眼于耐磨性与韧度等性能指标,对工具钢的热处理工艺进行了优化设计。
然后综合阐述典型工具钢的性能特点、热处理工艺及应用场合,得出耐磨性与韧度的合理配合是工具钢性能发挥的关键。
最后对工具钢合金化及热处理质量控制问题进行了介绍。
Abstract: The paper presents the type and working conditions and performance requirements of tool steel. Through the material mechanical properties, process performance and economic analysis of the tools, focusing on abrasion resistance and toughness, such as performance indexes, the tool steel heat treatment process is optimized. Then the paper expounds comprehensively the performance characteristics of typical tool steels and heat treatment process and applications, and concludes that the wear resistance and toughness of reasonable cooperation is the key of tool steels performance. Finally on tool steel alloying and heat treatment quality control problems were introduced.关键词:工具钢;热处理工艺;优化设计Key words: tool steels;heat treatment process;optimization design 中图分类号:TG1文献标识码:A文章编号:1006-4311(2011)02-0038-02 0引言随着我国装备制造业的快速发展,工程材料的合理应用越发显得重要。
《2024年锻态7050铝合金热处理工艺研究》范文

《锻态7050铝合金热处理工艺研究》篇一一、引言锻态7050铝合金因其优良的机械性能、耐腐蚀性以及良好的加工性能,被广泛应用于航空、航天及高速列车等高端领域。
其热处理工艺对于提升合金的力学性能、改善微观结构具有至关重要的作用。
本文旨在研究锻态7050铝合金的热处理工艺,探索其最佳的热处理参数,为实际生产提供理论依据。
二、材料与方法1. 材料准备本实验选用锻态7050铝合金为研究对象,通过不同的热处理工艺对其进行处理。
2. 实验方法(1)热处理工艺制定:根据前人研究及实际生产经验,制定不同的热处理工艺,包括固溶温度、固溶时间、淬火介质及时效温度、时效时间等参数。
(2)样品制备:将锻态7050铝合金加工成标准试样,进行不同热处理工艺的处理。
(3)性能测试:对处理后的试样进行硬度、拉伸、冲击等性能测试,分析其力学性能。
(4)微观结构分析:利用金相显微镜、扫描电镜及透射电镜等手段,观察合金的微观结构变化。
三、实验结果与分析1. 硬度测试结果不同热处理工艺下,锻态7050铝合金的硬度变化如图1所示。
从图中可以看出,经过固溶淬火及时效处理后,合金的硬度得到显著提高。
其中,固溶温度为XXX℃、固溶时间为X小时、淬火介质为XXX、时效温度为XXX℃、时效时间为X小时的工艺参数下,合金的硬度达到最大值。
2. 拉伸性能测试结果不同热处理工艺对锻态7050铝合金的拉伸性能影响如图2所示。
经过优化后的热处理工艺,合金的抗拉强度、屈服强度及延伸率均得到提高。
其中,优化后的热处理工艺参数与硬度测试中得到的最佳参数一致。
3. 微观结构分析通过金相显微镜、扫描电镜及透射电镜观察,发现经过优化后的热处理工艺,锻态7050铝合金的晶粒得到细化,第二相分布更加均匀,有利于提高合金的力学性能。
四、讨论通过对比不同热处理工艺下的硬度、拉伸性能及微观结构,我们发现优化后的热处理工艺能够显著提高锻态7050铝合金的力学性能及微观结构。
这主要是因为合理的固溶温度和时间能使合金中的元素充分溶解,淬火介质的选择能够有效地保留固溶元素,而适时适量的时效处理则能使合金中的第二相充分析出,从而获得更好的力学性能。
30cr2ni2mo钢大型环类锻件的热处理工艺研究
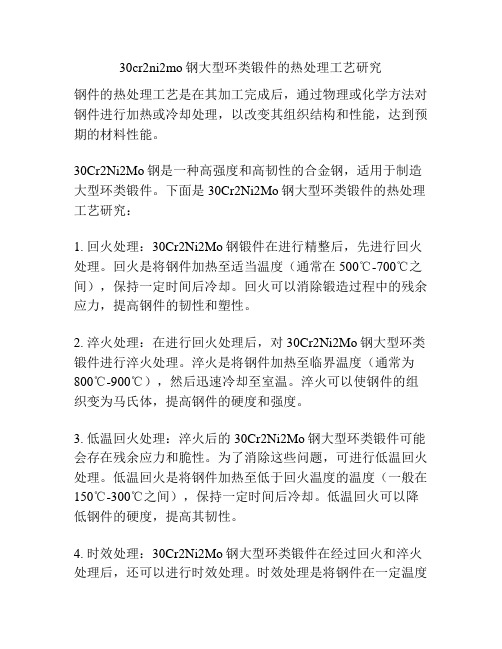
30cr2ni2mo钢大型环类锻件的热处理工艺研究钢件的热处理工艺是在其加工完成后,通过物理或化学方法对钢件进行加热或冷却处理,以改变其组织结构和性能,达到预期的材料性能。
30Cr2Ni2Mo钢是一种高强度和高韧性的合金钢,适用于制造大型环类锻件。
下面是30Cr2Ni2Mo钢大型环类锻件的热处理工艺研究:1. 回火处理:30Cr2Ni2Mo钢锻件在进行精整后,先进行回火处理。
回火是将钢件加热至适当温度(通常在500℃-700℃之间),保持一定时间后冷却。
回火可以消除锻造过程中的残余应力,提高钢件的韧性和塑性。
2. 淬火处理:在进行回火处理后,对30Cr2Ni2Mo钢大型环类锻件进行淬火处理。
淬火是将钢件加热至临界温度(通常为800℃-900℃),然后迅速冷却至室温。
淬火可以使钢件的组织变为马氏体,提高钢件的硬度和强度。
3. 低温回火处理:淬火后的30Cr2Ni2Mo钢大型环类锻件可能会存在残余应力和脆性。
为了消除这些问题,可进行低温回火处理。
低温回火是将钢件加热至低于回火温度的温度(一般在150℃-300℃之间),保持一定时间后冷却。
低温回火可以降低钢件的硬度,提高其韧性。
4. 时效处理:30Cr2Ni2Mo钢大型环类锻件在经过回火和淬火处理后,还可以进行时效处理。
时效处理是将钢件在一定温度下保持一段时间,以调整其组织结构和性能。
时效处理可以进一步提高钢件的强度和耐久性。
根据具体的工艺需求和钢件设计要求,以上热处理工艺可以进行适当的组合和调整,以达到最佳的性能和效果。
在进行热处理时,应注意加热温度、保温时间和冷却方式的控制,以确保钢件的质量和性能。
同时,热处理后的钢件还应进行适当的检测和试验,以验证其性能和质量。
合金钢自由锻件的热处理温度对性能的微观机制研究

合金钢自由锻件的热处理温度对性能的微观机制研究合金钢自由锻件是一种常用于制造高强度零件的重要材料。
热处理是提高合金钢自由锻件性能的关键步骤之一,其中温度是热处理过程中最重要的参数之一。
本文将针对合金钢自由锻件的热处理温度对性能的微观机制进行研究。
热处理温度对合金钢自由锻件的性能有着显著影响。
首先,适当的热处理温度能够有效调控合金钢自由锻件的组织结构。
在高温下,合金钢的晶界迁移速度增加,晶界扩散作用得到增强,有利于减少合金钢自由锻件的晶界位错数量,提高晶界的整体性能。
而低温下则可以减少晶界迁移速度,降低合金钢自由锻件的晶界位错密度,增加晶界的稳定性。
因此,通过控制热处理温度,可以优化合金钢自由锻件的晶界结构,提高其综合性能。
其次,热处理温度对合金钢自由锻件的相变行为产生重大影响。
在合金钢自由锻件的热处理过程中,晶格结构会发生相变,原子排列方式发生改变,从而导致合金钢自由锻件的力学性能发生变化。
研究发现,在一定温度范围内,合金钢自由锻件经历固溶、亚稳相析出、稳定相析出等相变过程。
固溶处理是指将合金钢自由锻件加热至高温区域,固溶不稳定相发生溶解。
亚稳相析出是指在快速冷却过程中,溶液中的亚稳固溶体过饱和,并开始析出亚稳相。
稳定相析出是指在温度降低的过程中,亚稳相进一步转变为稳定相。
因此,通过控制热处理温度,可以刺激相变行为,调控合金钢自由锻件的力学性能。
此外,热处理温度还会对合金钢自由锻件的晶体缺陷产生影响。
晶体缺陷是指晶体中的点缺陷、线缺陷和面缺陷,对材料的力学性能和潜在应力具有重要影响。
研究发现,合金钢自由锻件在高温下,晶体缺陷有利于扩散作用的发生,从而使合金钢自由锻件的塑性变形能力增强。
而在低温下,晶体缺陷对位错运动和塑性变形产生抑制作用,使合金钢自由锻件的强度增加。
因此,通过调控热处理温度,可以控制晶体缺陷的产生和分布,从而改善合金钢自由锻件的力学性能。
此外,热处理温度还会对合金钢自由锻件的晶界活动产生影响。
大型锻件的调质热处理探讨
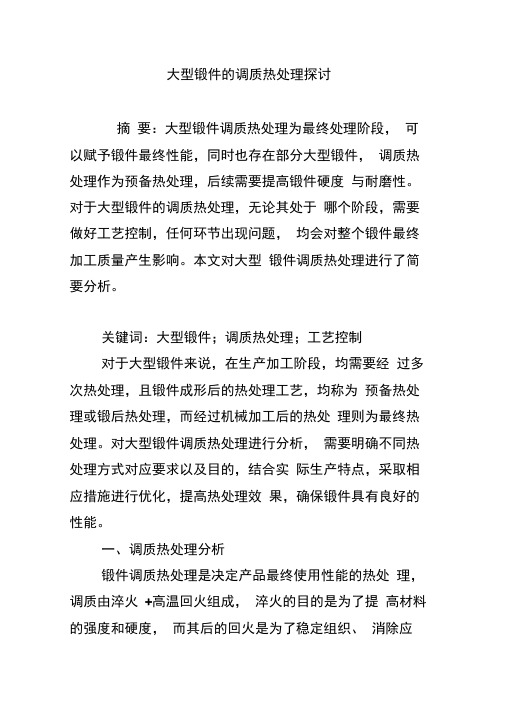
大型锻件的调质热处理探讨摘要:大型锻件调质热处理为最终处理阶段,可以赋予锻件最终性能,同时也存在部分大型锻件,调质热处理作为预备热处理,后续需要提高锻件硬度与耐磨性。
对于大型锻件的调质热处理,无论其处于哪个阶段,需要做好工艺控制,任何环节出现问题,均会对整个锻件最终加工质量产生影响。
本文对大型锻件调质热处理进行了简要分析。
关键词:大型锻件;调质热处理;工艺控制对于大型锻件来说,在生产加工阶段,均需要经过多次热处理,且锻件成形后的热处理工艺,均称为预备热处理或锻后热处理,而经过机械加工后的热处理则为最终热处理。
对大型锻件调质热处理进行分析,需要明确不同热处理方式对应要求以及目的,结合实际生产特点,采取相应措施进行优化,提高热处理效果,确保锻件具有良好的性能。
一、调质热处理分析锻件调质热处理是决定产品最终使用性能的热处理,调质由淬火+高温回火组成,淬火的目的是为了提高材料的强度和硬度,而其后的回火是为了稳定组织、消除应力、调整性能、减少脆性和提高可加工性。
通过对锻件进行调质热处理后,可以对其性能与材质进行最终调整,确保其具有良好的强度、韧性与塑性,具有较高的综合力学性能。
一般调质热处理多被用于中碳结构钢锻件中,对力学性能要求比较高的结构零部件均需要进行调质热处理。
调质热处理是金属材料热处理工艺之一,生产中对锻件加工完成后,也可以对粗坯调质热处理后在进行机械加工处理,来提高锻件性能。
二、大型锻件调质热处理分析1.锻件淬火加热第一,加热温度。
与小型锻件相比,大型锻件热处理过程中好更容易出现问题,其内部存在较多的冶金缺陷。
这样在对其进行热处理时,应取理论加热温度的上限,以保证保证偏析区也能达到相应的正火或淬火温度,使工件充分奥氏体化;或者是依据锻件成分或加热设备条件确定,保证所选加热温度可以满足生产要求。
第二,加热方式。
在对大型锻件进行加热处理时,对其有效截面进行分析,控制好装炉温度与加热速度,避免出现过大热应力。
金属的热处理论文范文

现代科技概论与知识产权课题名称金属的热处理专业专业方向班级学号学生姓名上海应用技术学院机械工程学院2012年11月8日金属的热处理摘要在人类的整个发展历程中,金属几乎是和社会息息相关的。
现在我们日常生活所用的各种设备大部分都是金属,想要符合社会的发展,就必须对材料进行热处理。
通过不同的工艺处理得到我们所需的性能不同的金属材料,对我们整个世界都产生了深远的影响,小到我们缝衣服用的针、掏耳勺,大到飞机、火箭都离不开金属。
因此热处理对材料的重要性不言而喻,我们虽然是世界上最早对金属进行冶炼的国家,但现在由于种种原因,我们在金属制造方面还是与欧美等发达国家存在较大的差距。
我们大学生时祖国的未来,希望我们可以奋发图强,将来做祖国的栋梁之才。
关键字金属的性能,热处理金属的热处理 (1)摘要 (1)关键字 (1)1.背景简介 (2)2.文献综述 (3)2.1金属材料的性能 (3)2.2金属的结晶和合金的构造 (4)2.2.1金属的结晶过程和同素异晶转变 (4)2.2.2合金的相结构 (4)2.3金属材料强化的机理及基本途径 (4)2.3.1金属围观强化机构的分类 (4)2.3.2工艺方法 (5)3.技术路线 (5)3.1退火 (5)3.1.1完全退火 (5)3.1.2低温退火 (5)3.2正火 (6)3.2.1普通正火 (6)3.2.2等温正火 (6)3.2.3水冷正火 (6)3.3淬火 (6)3.3.1完全淬火 (7)3.3.2不完全退火 (7)3.4回火 (7)3.4.1低温回火 (7)3.4.2中温回火 (8)3.4.3高温回火 (8)4.结论 (8)参考文献 (9)1.背景简介自二十世纪以来,金属物理的发展和其他新技术的移植应用,使金属热处理工艺得到很大发展。
其中比较有代表性的是1901~1925年,在工业生产中应用转筒炉进行气体渗碳;30年代出现露点电位差计,使炉内气氛的碳势达到可控,以后又研究出用二氧化碳红外仪、氧探头等进一步控制炉内气氛碳势的方法;60年代,热处理技术运用了等离子场的作用,发展了离子渗氮、渗碳工艺;激光、电子束技术的应用,又使金属获得了新的表面热处理和化学热处理方法。
钢的热处理研究论文
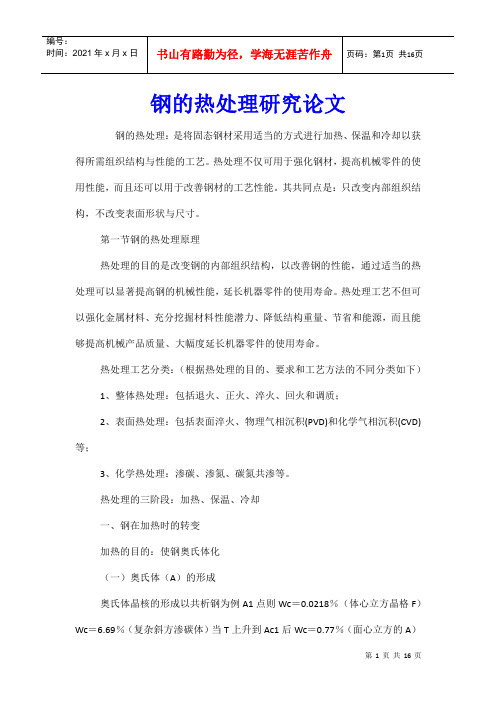
钢的热处理研究论文钢的热处理:是将固态钢材采用适当的方式进行加热、保温和冷却以获得所需组织结构与性能的工艺。
热处理不仅可用于强化钢材,提高机械零件的使用性能,而且还可以用于改善钢材的工艺性能。
其共同点是:只改变内部组织结构,不改变表面形状与尺寸。
第一节钢的热处理原理热处理的目的是改变钢的内部组织结构,以改善钢的性能,通过适当的热处理可以显著提高钢的机械性能,延长机器零件的使用寿命。
热处理工艺不但可以强化金属材料、充分挖掘材料性能潜力、降低结构重量、节省和能源,而且能够提高机械产品质量、大幅度延长机器零件的使用寿命。
热处理工艺分类:(根据热处理的目的、要求和工艺方法的不同分类如下)1、整体热处理:包括退火、正火、淬火、回火和调质;2、表面热处理:包括表面淬火、物理气相沉积(PVD)和化学气相沉积(CVD)等;3、化学热处理:渗碳、渗氮、碳氮共渗等。
热处理的三阶段:加热、保温、冷却一、钢在加热时的转变加热的目的:使钢奥氏体化(一)奥氏体(A)的形成奥氏体晶核的形成以共析钢为例A1点则Wc=0.0218%(体心立方晶格F)Wc=6.69%(复杂斜方渗碳体)当T上升到Ac1后Wc=0.77%(面心立方的A)由此可见转变过程中必须经过C和Fe原子的扩散,必须进行铁原子的晶格改组,即发生相变,A在铁素体和渗碳体的相界面上形成。
有两个有利条件①此相界面上成分介于铁素体和渗碳体之间②原子排列不规则,空位和位错密度高。
珠光体向奥氏体转变示意图a)形核b)长大c)剩余渗碳体溶解d)奥氏体均匀化(二)奥氏体晶粒的长大奥氏体大小用奥氏体晶粒度来表示。
分为00,0,1,2…10等十二个等级,其中常用的1~10级,4级以下为粗晶粒,5-8级为细晶粒,8级以上为超细晶粒。
影响A晶粒粗大因素1、加热温度越高,保温时间愈长,奥氏体晶粒越粗大。
因此,合理选择加热和保温时间。
以保证获得细小均匀的奥氏体组织。
(930~950℃以下加热,晶粒长大的倾向小,便于热处理)2、A中C含量上升则晶粒长大的倾向大。
钢铁材料热处理及组织性能论文
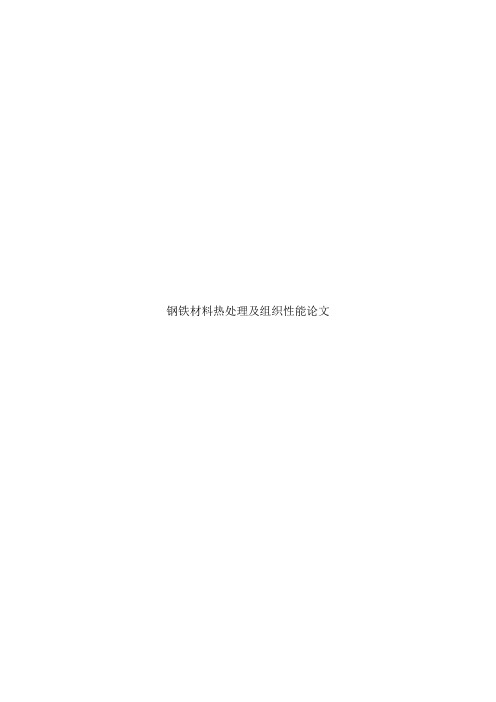
钢铁材料热处理及组织性能论文摘要:钢铁材料的热处理是钢铁材料在固态下,通过适当的方式进行加热、保温和冷却,改变钢材内部组织结构,改善钢的性能,改善毛坯在后续工序中的工艺性能,使工件获得优良的使用性能,从而充分发挥钢材的潜力,扩大其应用范围。
关键词:热处理,热处理时钢的组织,钢的热处理工艺背景简介:热处理是机械零件及工具制造过程中的重要工艺,它负担着改善钢铁材料组织和性能,充分发挥钢铁材料的潜力,提高和改善零件的使用性能和使用寿命的重要任务。
二十世纪以来,金属物理的发展和其他新技术的移植应用,使金属热处理工艺得到更大发展。
一个显著的进展是1901~1925年,在工业生产中应用转筒炉进行气体渗碳;30年代出现露点电位差计,使炉内气氛的碳势达到可控,以后又研究出用二氧化碳红外仪、氧探头等进一步控制炉内气氛碳势的方法;60年代,热处理技术运用了等离子场的作用,发展了离子渗氮、渗碳工艺;激光、电子束技术的应用,又使金属获得了新的表面热处理和化学热处理方法。
中国是能源消耗大户,机械制造行业是其中很重要的一个组成部分。
随着零部件、机械制造等重工业的不断发展,热处理对中国机械制造业的振兴和发展具有重要的支撑作用,而机械制造业的发展也必将带动中国热处理行业的快速发展,为中国热处理行业的发展提供广阔的发展空间,行业的发展前景广阔。
一、热处理1、钢在加热时的组织转变对钢铁材料而言,大多数热处理工艺首先都要将工件加热到钢的临界点以上,使原始组织部分或全部转变为奥氏体,然后再以适当的冷却速度冷却,使奥氏体转变为一定的组织并获得所需要的性能。
钢在加热过程中,由加热前的组织转变为奥氏体的过程称为钢的加热转变,即奥氏体化。
加热时形成的奥氏体的质量(成分均匀性及晶粒大小等),对冷却转变过程及组织、性能有极大影响。
钢在加热时奥氏体晶粒大小直接影响到热处理后钢的性能,晶粒小,冷却后组织也细小,反之,组织则粗大。
钢材晶粒细化,既能有效的提高强度,又能明显提高塑性和韧性,因此,获得细的奥氏体晶粒,对工件使用性能和质量都具有重要意义。
- 1、下载文档前请自行甄别文档内容的完整性,平台不提供额外的编辑、内容补充、找答案等附加服务。
- 2、"仅部分预览"的文档,不可在线预览部分如存在完整性等问题,可反馈申请退款(可完整预览的文档不适用该条件!)。
- 3、如文档侵犯您的权益,请联系客服反馈,我们会尽快为您处理(人工客服工作时间:9:00-18:30)。
小论大型锻件热处理
大型锻件是指用1000t或更大吨位水压机生产的锻件。
随着大型锻件的尺寸和重量的增加,热处理时有效厚度也随之发生变化。
由于截面的增大,不可避免地存在成分偏析、非金属夹杂、显微空隙等冶金缺陷,再加上相变潜热的影响,在加热和冷却过程中产生的应力较大,极易引工件的畸变和开裂,本文对大型锻件的热处理工艺参数进行了优化,并取得了显著经济效果。
一、大型锻件热处理可以解决的缺陷通常有以下几种
1.大晶粒
大晶粒通常是由于始锻温度过高和变形程度不足、或终锻温度过高、或变形程度落人临界变形区引起的。
铝合金变形程度过大,形成织构;高温合金变形温度过低,形成混合变形组织时也可能引起粗大晶粒,晶粒粗大将使锻件的塑性和韧性降低,疲劳性能明显下降。
2.晶粒不均匀
晶粒不均匀是指锻件某些部位的晶粒特别粗大,某些部位却较小。
产生晶粒不均匀的主要原因是坯料各处的变形不均匀使晶粒破碎程度不一,或局部区域的变形程度落人临界变形区,或高温合金局部加工硬化,或淬火加热时局部晶粒粗大。
耐热钢及高温合金对晶粒不均匀特别敏感。
晶粒不均匀将使锻件的持久性能、疲劳性能明显下降。
3.冷硬现象
变形时由于温度偏低或变形速度太快,以及锻后冷却过快,均可能使再结晶引起的软化跟不上变形引起的强化(硬化),从而使热锻后锻件内部仍部分保留冷变形组织。
这种组织的存在提高了锻件的强度和硬度,但降低了塑性和韧性。
严重的冷硬现象可能引起锻裂。
4.裂纹
裂纹通常是锻造时存在较大的拉应力、切应力或附加拉应力引起的。
裂纹发生的部位通常是在坯料应力最大、厚度最薄的部位。
如果坯料表面和内部有微裂纹、或坯料内存在组织缺陷,或热加工温度不当使材料塑性降低,或变形速度过快、变形程度过大,超过材料允许的塑性指针等,则在撤粗、拔长、冲孔、扩孔、弯曲和挤压等工序中都可能产生裂纹。
5.龟裂
龟裂是在锻件表面呈现较浅的龟状裂纹。
在锻件成形中受拉应力的表面(例如,未充满的凸出部分或受弯曲的部分)最容易产生这种缺陷。
引起龟裂的内因可能是多方面的:①原材料合cu、sn等易熔元素过多。
②高温长时间加热时,钢料表面有铜析出、表面晶粒粗大、脱碳、或经过多次加热的表面。
③燃料含硫量过高,有硫渗人钢料表面。
6.飞边裂纹
飞边裂纹是模锻及切边时在分模面处产生的裂纹。
飞边裂纹产生的原因可能是:①在模锻操作中由于重击使金属强烈流动产生穿筋现象。
②镁合金模锻件切边温度过低;铜合金模锻件切边温度过高。
7.铸造组织残留
铸造组织残留主要出现在用铸锭作坯料的锻件中。
铸态组织主要残留在锻件的困难变形区。
锻造比不够和锻造方法不当是铸造组织残留产生的主要原因,
铸造组织残留会使锻件的性能下降,尤其是冲击韧度和疲劳性能等。
8.碳化物偏析级别不符要求
碳化物偏析级别不符要求主要出现于莱氏体工模具钢中。
主要是锻件中的碳化物分布不均匀,呈大块状集中分布或呈网状分布。
造成这种缺陷的主要原因是原材料碳化物偏析级别差,加之改锻时锻比不够或锻造方法不当。
具有这种缺陷的锻件,热处理淬火时容易局部过热和淬裂。
制成的刃具和模具使用时易崩刃等。
13.带状组织
带状组织是铁素体和珠光体、铁素体和奥氏体、铁素体和贝氏体以及铁素体和马氏体在锻件中呈带状分布的一种组织,它们多出现在亚共折钢、奥氏体钢和半马氏体钢中。
这种组织,是在两相共存的情况下锻造变形时产生的带状组织能降低材料的横向塑性指针,特别是冲击韧性。
在锻造或零件工作时常易沿铁素体带或两相的交界处开裂。
14.局部充填不足
局部充填不足主要发生在筋肋、凸角、转角、圆角部位,尺寸不符合图样要求。
产生的原因可能是:①锻造温度低,金属流动性差;②设备吨位不够或锤击力不足;③制坯模设计不合理,坯料体积或截面尺寸不合格;④模膛中堆积氧化皮或焊合变形金属。
二、大型锻件热处理工艺
1.1 正火和淬火的加热
大型锻件特别是合金钢锻件,在加热方式上应采用阶梯升温方式加热。
有关资料表明l2 J大型锻件在350℃~500℃以及600℃~800℃时工件表面与心部存在最大温差,差值在300℃~400℃左右。
因此采用在450℃与650℃保温一段时间,然后再升温的加热方法是比较合适的。
大型锻件正火和淬火加热温度的选择,理论上与小型锻件是一致的,应取理论加热温度的上限,以保证偏析区也能达到相应的正火或淬火温度,使工件充分奥氏体化。
装炉温度≤400℃,并在450℃保持一定时间,以进一步减小锻件在蓝脆温度范围(250℃~350℃)内的温差。
在450℃保温之前由于锻件温度低,仍处于线弹性状态,如果表面与心部温差引起的热应力过大,可致锻件在加热过程中早期开裂。
因此,保温前加热速度一般控制在30℃/h-70℃/h;450℃保温后可适当加快升温速度但不能超过100℃/h~15012/h。
锻件经过650℃保温后,心部与表面还可能存在温差,但由于锻件处于塑性状态,尤其是当锻件加热到临界点温度以上时,相变超塑性伴随产生,因而导致开裂的可能性极小,此时可按设备功率升温。
均温时间凭经验目测决定,锻件表面温度均匀一致并和炉墙颜色相同时为止,工艺不做要求。
均温结束即开始保温,保温时间可根据公式(1)计算:
t=a·K·D (1)
式中t为加热时间(min);a为加热系数(rain/ram),碳素结构钢与低合金结构钢取0.40~0.50,中、高合金钢取0.50-0.60;K 是装炉系数;D是工件有效加热厚度。
1.2 回火加热
锻件在回火装炉的初始阶段,表面温度回升,心部温度进一步降低,以完成心部过冷奥氏体完全转变。
入炉温度应<400℃,并且在400℃左右保温一段时间。
为保证锻件表面与心部温差较小且无较大的应力,升温速度不应超过30℃/h~100℃/h。
回火工艺过程的温度较淬火的温度低(<650℃),所以均温时间难以用目测确定,因此回火工艺规程中没有规定均温时间,而是适当延长保温时间。
回
火保温时间也可按公式(1)计算,其中碳素钢、低合金钢a为1.0~1.5,高、中合金钢为1.2~1.7;工件有效厚度每100ram 回火保温时间不能少于4h。
1.3 正火和淬火冷却工艺
大型锻件正火冷却通常采用空冷、不同部位采用强力风冷或先进行短时间喷雾冷却后再采用强力风冷的冷却方式。
针对大型锻件的材料及要求,淬火冷却分别采用油冷、水冷、水一油双介质等冷却方法。
①油冷:3号锭子油,该介质的技术参数是运动粘度(50℃)为:17X 10 m2/s~23 X 10一m2/s,闪点为170℃,凝点为一15℃,淬火温度范围为一15℃~170℃。
为了缓解运动粘度大的缺点,可以安装冷却循环装置和加热装置。
冷却时间按公式(2)计算:
r=a·D (2)
式中r为冷却时间(S),D为工件有效厚度(mm),a为系数(s/mm),对45CrMo、3Cr13钢a一般为9~13。
②水冷:针对大型锻件水冷淬火后工件存在硬度不足的问题,采用15%的CaC12水溶液取代以前使用的自来水,并且安装冷却循环装置。
两种冷却介质的性能指标可知15%的CaC12水溶液与水相比,具有使用温度区间宽,最大冷速大,特性温度高,100"C~300~2的平均冷速小和适用范围广的优点。
冷却时间按公式(2)计算,其中a为1.5~2。
③水一油双介质冷却:对于40Cr、35CrMo、42CrMo等淬透性差和淬透性中等的低合金结构钢大型锻件,由于单纯的油冷淬火已不满足设计要求,而采用水冷工件开裂的倾向较大,在没有专用淬火液的条件下,采用水一油双介质淬火冷却工艺,冷却时间按公式(2)计算,其中水冷a为1~2,油冷a 为7~10。
在具体操作时应注意以下几点:水冷淬火之前要有较短时间的预冷,以减小热应力,使工件畸变和开裂倾向减小,而且还可以增加大型锻件的淬硬层,提高零件的综合力学性能;严格控制水油转换时的空冷时间,不宜超过20s。
1 .4 回火冷却工艺
一般在400℃以上的冷却速度应控制在50℃/h~高温回火(≥450℃)后必须采用水冷或油冷等冷却较5℃/h,对于40Cr、3Cr13等钢具有明显可逆回火脆性的材料,该种方法将使该材料的冲击韧性显著降低。
回火冷却时应考虑以下两点:①对无高温回火脆性材料,如45、35CrMo、42CrMo、45CrMo钢等,采用随炉冷却或空冷的缓慢冷却方式。
②对具有高温回火脆性的材料,如40Cr、3Cr13、Crl2钢等,在低温回火快的方式进行冷却,以避免出现回火脆性,为了进一步消除由于回火冷却带来的应力,然后补充进行一次400C左右的去除内应力退火。
热处理工艺对于去除大型锻件的缺陷有着越来越重要的作用,对提高锻件质量已经是不可缺少的工艺过程,进一步研究有效的热处理工艺变得至关重要。
参考文献:
1.机械工业职业技能鉴定指导中心.热处理工技术[M].北京:机械工业出版社
2.刘胜.浅谈连续式渗碳炉予处理炉的作用[j] 机械工人
3.孙宝兴.SrL连续式渗碳自动线的特点及应用[J].金属热处理
4.内滕武志.渗碳淬火实用技术[M].北京:机械工业出版社。