锻件的热处理
锻件热处理

锻件热处理锻件是一种金属成形加工方法,在完成锻造后需要经过热处理。
锻件热处理是指将锻件加热到一定的温度,使之发生一系列物理或化学变化,达到改变其组织结构和性能的目的。
本文将针对锻件热处理的流程、方法和机理进行阐述。
锻件热处理的流程锻件热处理流程通常包括三个步骤:加热、保温和冷却。
其中,加热和冷却的过程都非常关键,因为这两个步骤会直接影响到锻件的微观组织和力学性能。
1.加热加热是指将锻件加热到一定的温度,使之发生晶粒长大、变形、晶格缺陷消失、相变等变化,从而获得一定的机械性能。
加热温度和时间是通过锻件的成分、形状和尺寸等因素来决定的。
一般来说,锻件加热到一定温度后,其冷却速度直接影响到锻件的性能。
常见的加热方式包括电阻加热、燃气加热、电弧加热、激光加热等。
2.保温保温是指将已经加热到一定温度的锻件保持在一个固定的温度下一定时间,以使锻件内部保持均匀温度,从而达到热处理的效果。
保温时间和温度取决于锻件的材质和尺寸。
优化中间温度和时间会对晶粒尺寸和锻件性能有着直接的影响。
相较于加热和冷却,保温过程是一个相对简单的步骤。
3.冷却冷却是指将经过加热和保温过程的锻件缓慢冷却至室温,使之形成相应的组织结构和力学性能。
冷却方式和速度对锻件的性能有着直接的影响。
常用的冷却方式包括空气冷却、水冷却等。
锻件热处理的方法和机理1.灭火热处理灭火热处理是指将经过加热处理的锻件,迅速放入冷却介质中,使其迅速冷却达到强化锻件的目的。
灭火热处理可以分为水淬火、油淬火、高温淬火和空气冷却等多种方式,其中以水淬火的强度最大,油淬火次之,在高温淬火和空气冷却中最低。
灭火热处理的机理是利用快速冷却的方式,使锻件内部的物理性能和化学性能发生变化,形成更加细小的晶粒和组织结构。
从而达到提高锻件材质的强度和硬度的目的。
2.回火热处理回火热处理是指在灭火热处理完成后,对锻件进行再次加热并显著降低冷却速度,从而提高锻件的韧性和塑性。
对于某些硬度较高的锻件,为了兼顾强度与韧性的要求,通常需要进行回火处理。
锻造工艺过程及模具设计第3章锻造的加热

3.6.2 锻件的冷却规范
1.空冷 :在空气中冷却,速度较快 。
2.坑(箱)冷:锻件锻后放到地坑 或铁箱中封闭冷却,或埋入坑中砂 子、石灰或炉渣内冷却。
3.炉冷:锻件锻后直接装入炉中按 一定的冷却规范缓慢冷却。
3.7 中小钢锻件的热处理
3.7.1 退火 退火是将钢加热到一定的温度,保温
1)反应是可逆反应,向右:氧化反应,向左:
还原反应。 2)加热时,与空气消耗系数有关。
空气消耗系数:又称空气过剩系数,是燃料燃 烧实际供给的空气量与理论计算空气量之比。 3)空气充足时,炉气呈氧化性,空气不足时, 炉 气呈还原性。 4)控制反应前后的生成物与反应物的浓度比。
炉气和被加热钢材的平衡图如下:
• 电热体材料:铁铬铝合金 镍铬合金 碳化硅元件 二硅化钼
图3.1 电阻炉原理图 1-电热体 2-坯料 3-变压器
●盐浴炉加热原理: 电流通过炉内电极产生
的热量把导电介质——盐熔 融,通过高温介质的对流与 传导将埋入介质中的金属加 热。 ●盐浴炉的分类:按照热源的 位置分外热式和内热式。 ●盐浴炉加热的优点:
、
辐射加热坯料。
燃料来源方便、加热炉修造容易、
加热费低、适应性强。
缺点::劳动条件差,加热速度慢, 质量低、热效率低。
应用范围:大、中、小型坯料。
2 电加热 利用电能转换热能来加热坯料。
1)电阻加热 电阻加热与火焰加热原理相同,根据
发热元件的不同分为: 电阻炉加热、 盐浴炉加热、接触电
加热
• 电阻炉加热原理:利用电 流通过炉内的电热体产生 的能量,加热炉内的金属 坯料。原理如图3.1。
升温快、加热均匀,可 以实现 金属坯料整体或局 部的无氧化加热。 ●盐浴炉加热的缺点:
锻件热处理规范
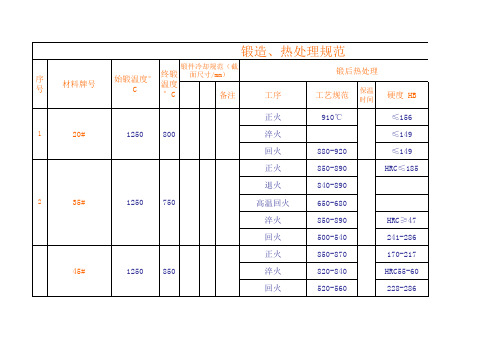
保温后缓冷到 705 等温2小时后 空冷
420
油冷或水冷 油冷、水冷或 空冷 炉冷至600空 冷 油或空冷 空冷 坑冷 固溶(空冷) 固溶
420
砂冷 水冷或空冷 空冷 固溶+时效 固溶+时效 砂冷
321 304 302
炉冷 炉冷
4140
炉冷 炉冷 空冷 空冷或风冷 空冷
52100
52100
油冷 空冷 砂冷
HB330-380 ≤207 156-207
HRC52-60 269-302
≤229
正火 38CrMoAl 1180 850 高温回火 淬火 退火 正火 40CrNiMo 1180 850 高温回火 淬火 回火 17Cr2Ni2Mo 1180 900 正火 25CrNiMo 1150 850 等温退火 20CrNiMo 20CrMnMo 1220 850 正火 回火
≤149 HRC≤185
2
35#
1250
750
高温回火 淬火 回火 正火
HRC≥47 241-286 170-217 HRC55-60 228-286
45#
1250
850
淬火 回火
55# 20CrMo 25CrMo
1250 1200
800 800
正火+回火 淬火 回火 调质 退火 正火 890-910 860-890 850-870 600-640 HRC50-55 207-241 HB<217 167 880 500 HRC32-33
≤229 ≤269
65Mn
1150
800
高温回火 淬火 回火 退火
HRC52-60 415-444 ≤187
20Mn2
锻造及锻后热处理工艺规范

目录1.钢质自由锻件加热工艺规范2.钢锭(坯)加热规范若干概念3.加热操作守则4.锻造操作守则5.锻件锻后冷却规范6.锻件锻后炉冷工艺曲线7.锻件锻后热装炉工艺曲线8.冷锻件校直前加热、校直后(补焊后)回火工艺曲线9.锻件各钢种正火(或退火)及高温回火温度表10.锻件有效截面计算方法钢质自由锻件加热工艺规范一.范围:本规范规定了钢质自由锻件的通用加热技术条件。
本规范适用于碳素钢、合金钢、高合金钢、高温合金钢(铁基、镍基)的冷、热、半热钢锭(坯)的锻造前加热二.常用钢号分组和始、终锻加热温度范围:注1:始锻温度为锻前加热允许最高炉温,由于钢锭的铸态初生晶粒加热时过热倾向比同钢号钢坯小,故两者的锻前加热温度相差20℃~30℃;注2:根据产品的特性、锻件技术条件、变形量等因素,始锻温度可以适当调整;注3:本规范未列入的钢种,可按化学成分相近的钢号确定;注4:重要的、关键产品的、特殊材质的钢号,其加热工艺曲线由技术部编制;注5:几种不同的钢种,不同尺寸的钢锭(或坯料),在同一加热炉加热时,要以合金成分高的,尺寸大的钢锭(或坯料)为依据编制加热工艺曲线。
三.冷钢坯。
钢锭加热规范:钢锭(坯)加热规范若干概念1.钢锭(坯)入炉前的表面温度≥550℃的称为热钢锭,400~550℃的称为半热钢锭(坯),≤400℃的称为冷钢锭。
2.锻件半成品坯料的加热平均直径计算原则:δ -壁厚H- 高度或长度D- 外径1)实心圆类:当D>H时,按H计算;当D<H时,按D计算。
2)筒类锻坯:H>D 当H>δ时,按1.3δ计算。
3)空心盘(环)类:H<D当H>δ时,按δ计算;当H<δ时,按H计算。
3.为了避免锻件粗晶组织,最后一火的始锻温度可按其剩余锻造比(Y)确定:Y=1.3~1.6 最高加热温度1050℃Y<1.3 最高加热温度950℃4.不同钢种不同规格的坯料同炉加热时,装炉温度和升温速度均按较低的选用,保温时间按较长的选用。
304法兰锻造热处理工艺流程

304不锈钢法兰的锻造和热处理工艺流程包括以下步骤:
1. 材料准备:选择合适的304不锈钢材料,并进行表面清洁和预处理。
2. 加热:将304不锈钢材料加热至适当的温度。
通常情况下,加热温度在1000°C到1200°C之间,具体温度取决于材料的精确要求和锻造工艺。
3. 锻造:将加热后的304不锈钢材料放入锻造设备中,通过锤击或压力形成需要的形状。
锻造一般分为自由锻造、模锻和冷锻等不同形式,根据实际需要进行选择。
4. 冷却和退火:锻件完成后,将其冷却至室温。
随后,可以对锻件进行退火处理以消除内部应力,并提高材料的机械性能和耐腐蚀性。
5. 修整和加工:对锻造后的304不锈钢法兰进行修整和加工,包括切割、磨削、钻孔等工序,以达到最终的尺寸和质量要求。
6. 清洁和检查:对锻造和加工后的304不锈钢法兰进行清洁,确保其表面没有污垢和缺陷。
随后,进行质量检查,包括外观检查、尺寸测量和材料性能测试等。
7. 表面处理:根据具体要求,可以对304不锈钢法兰进行表面处理,例如抛光、电镀或喷涂等,以增加其美观性和耐腐蚀性。
8. 包装和出厂:最后,将304不锈钢法兰进行适当的包装,确保其在运输和储存过程中不受损坏。
随后,发货给客户或仓库。
这是一般的304不锈钢法兰锻造和热处理工艺流程,具体的工艺流程可能因制造商和产品要求而有所不同。
在实际生产中,应根据具体情况进行调整和优化。
锻件工艺流程

锻件工艺流程锻件是一种通过将金属材料加热至一定温度后进行机械加工的工艺,常用于制造各种金属零件。
下面将介绍一下锻件的工艺流程。
首先,锻件的准备工作很重要。
选择合适的金属材料,如碳钢、合金钢等,并根据零件的要求进行切割、去除杂质等预处理工作。
还需要准备好相应的模具和锻压设备。
接下来是对金属材料进行加热处理。
将金属材料放入加热炉中加热,使其达到适合锻造的温度。
不同的金属材料需要不同的加热温度和时间,以确保锻件的质量。
加热后,金属材料进入锻造机进行锻造。
锻造分为冷锻和热锻两种方式。
冷锻是将金属材料加热至室温以下进行锻造,适用于一些脆性材料。
热锻是将金属材料加热至高温进行锻造,适用于大多数金属材料。
锻造时,使用锻道将金属材料置于模具中,然后用锻压设备施加压力,使金属材料变形并填充模具。
锻造完成后,锻件需要进行热处理。
热处理是通过加热和冷却的方式改变锻件的组织结构和性能。
常见的热处理方式包括退火、淬火和回火。
退火可以消除锻造过程中的应力和变形,提高锻件的塑性和韧性。
淬火可以使锻件的硬度增加,但也使其脆性增加。
回火可以降低锻件的硬度和脆性,提高其韧性。
最后,对锻件进行机械加工。
机械加工是为了使锻件达到最终的尺寸和形状要求。
常见的机械加工方式包括车削、铣削、钻孔等。
通过这些加工方式,可以去除锻件表面的氧化皮和毛刺,并使锻件的尺寸和形状精确到达到设计要求。
锻造工艺流程是一个复杂的过程,需要各个环节的密切配合和精确操作。
只有在合适的温度和压力条件下进行锻造,才能得到质量好的锻件。
通过热处理和机械加工,可以进一步提高锻件的性能和外观。
总结起来,锻件的工艺流程包括准备工作、材料加热、锻造、热处理和机械加工。
锻件工艺的正确操作和控制对于获得高质量的锻件非常重要,也对提高产品质量和使用寿命有着至关重要的影响。
坯料加热、锻件冷却及热处理

1.坯料加热、锻件冷却及热处理
Heating 、Cooling and Heat-Treatment of Forging work-piece
2.特种锻压与轧制
Special Forging and Rolling
一.坯料加热、锻件冷却及热处理
Heating 、Cooling and Teat Treatment of Forging work-piece
应用:用于各种材料、形状复杂件, 如铝合金炮弹引,高压阀体等。
5)粉末锻造
原理:将粉末冶金和精密模锻结合一起。
分类:粉末锻造-----直接加热锻造 烧结锻造-----烧结后加热锻造
粉末冷锻----用粉末成坯,烧结后冷锻。 特点:尺寸精度高,表面光洁;
性能、生产效率优于粉末冶金产品。 应用:汽车上火花塞壳;汽车齿轮和连杆。
3)等温锻造和超塑性锻造
原理:模具和坯料保持相同温度。 特点及应用: 用于锻造温度范围狭窄金属,如钛合金、铝合金等,
尤其航天工业薄壁零件。
4)液态锻造
原理:将液态金属直接注入模膛,施以静压力,使熔融 或半熔融态金属在压力下结晶凝固,并产生少量 塑性变形。
特点: 与铸造比:无须浇注系统,节约金属; 组织比压铸件细密。 与锻造比:成形压力小及能耗少2/3~~3/4; 组织比一般模锻件差。
节约原材料 产品强度和精度高、Ra低,产 品高 劳动条件好 生产率高
缺点: 变形抗力大,要求设备有较大能量、刚度
应用:成批小件生产
2)温挤压
原理:加热到比热锻温度低的温度挤压。 特点:降低冷、热锻缺点:
---比冷挤压变形抗力小,可加大变形量; ---比热挤压减轻氧化、脱碳,提高加工精度
应用:用于不易冷锻材料如:不锈钢、高温合金
大型锻件的调质热处理实践
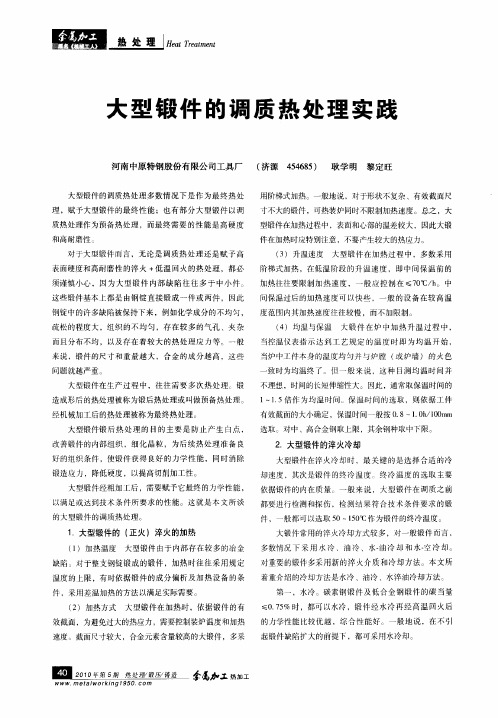
致 时为均温终了。但一般 来说 ,这 种 目测均温时 间并
大型锻件在生产 过程 中,往往需 要多次热处理 。锻
不理想 ,时间的长短伸缩性大 。因此 ,通常取保温时间的 l . ~15倍作 为均温时间。保 温时间的选取 ,则 依据 工件
造成形后 的热处理被称为锻后热处理或叫做预备热处理。
这些锻件基本上都 是由钢锭直接锻成 一件或两件 ,因此 钢锭 中的许多缺陷被保持下来 ,例如化学成分的不均匀 ,
疏松 的程度大 ,组 织的不均匀 ,存在 较多 的气孔 、夹 杂 而且分布不均 ,以及存在着较大 的热 处理应 力等。一般
问保 温过后的加热 速度可以快些 ,一般 的设 备在较高温
温度的 L限 ,有时依据锻件 的成 分偏 析及加热设 备的条
件 ,采用差温加热 的方法以满足实际需要 。
对重要的锻件 多采用新 的淬火介质和 冷却方法。本文所
着重介绍的冷却方法是水冷 、油冷 、水淬油冷却方法 。
第一 ,水冷。碳素钢锻件 及低合金钢 锻件的碳 当量 ≤O 7 %时 ,都可 以水冷,锻 件经水 冷再经高 温 回火后 .5
选取。对中 、高合金钢取上限,其余钢种取 中下限。
2 大型锻件的淬火冷却 .
大型锻件在淬火冷却时 ,最关键 的是选择 合适 的冷 却速度 ,其次是锻件 的终冷温 度。终 冷温度 的选取主要 依据锻件的内在质量 。一般来说 ,大型锻件在 调质之前 都要进行检测和探伤 ,检测结果符 合技术条件 要求 的锻 件,一般都可 以选取 5 0~l0 5 ℃作为锻件的终冷温度。 大锻件常用的淬火冷却方式较多 ,对一般锻件 而言 , 多数情况 下采 用 水 冷 、油 冷 、水一 冷却 和 水一 冷 却。 油 空
锻件的热处理
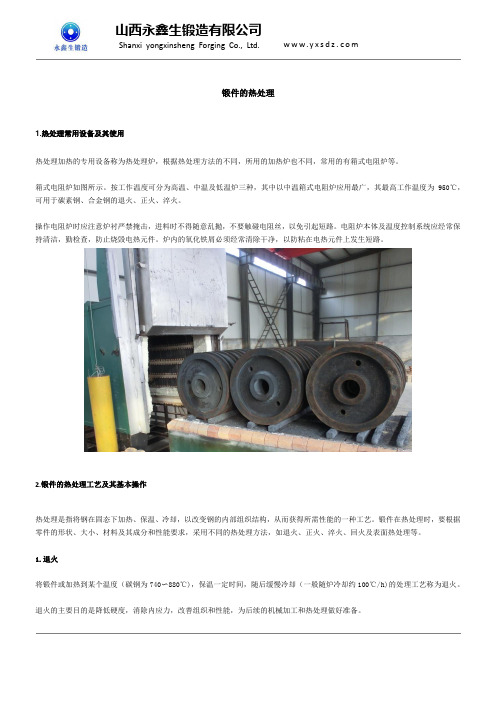
锻件的热处理1.热处理常用设备及其使用热处理加热的专用设备称为热处理炉,根据热处理方法的不同,所用的加热炉也不同,常用的有箱式电阻炉等。
箱式电阻炉如图所示。
按工作温度可分为高温、中温及低温炉三种,其中以中温箱式电阻炉应用最广,其最高工作温度为950℃,可用于碳素钢、合金钢的退火、正火、淬火。
操作电阻炉时应注意炉衬严禁掩击,进料时不得随意乱抛,不要触碰电阻丝,以免引起短路。
电阻炉本体及温度控制系统应经常保持清洁,勤检查,防止烧毁电热元件。
炉内的氧化铁屑必须经常清除干净,以防粘在电热元件上发生短路。
Array 2.锻件的热处理工艺及其基本操作热处理是指将钢在固态下加热、保温、冷却,以改变钢的内部组织结构,从而获得所需性能的一种工艺。
锻件在热处理时,要根据零件的形状、大小、材料及其成分和性能要求,采用不同的热处理方法,如退火、正火、淬火、回火及表面热处理等。
1.退火将锻件或加热到某个温度(碳钢为740〜880℃),保温一定时间,随后缓慢冷却(一般随炉冷却约100℃/h)的处理工艺称为退火。
退火的主要目的是降低硬度,消除内应力,改善组织和性能,为后续的机械加工和热处理做好准备。
2.正火将钢加热到某个温度,(碳钢为760〜920℃),保温一定时间,随后从炉中取出,在静止空气中冷却的处理工艺称为正火。
锻件正火的目的与退火基本相似,但正火的冷却速度比退火稍快,故能得到较细密的组织,机械性能较退火好。
正火后的钢硬度比退火高,对于低碳钢的工件更具存良好的切削加工性能(实践表明,硬度在HB170〜HB230范围内的钢锻件,切削加工性能较好,硬度过高或过低,切削加工性能均会下降)。
而对于中碳合金钢和高碳钢的工件,则因正火后硬度偏高,切削加工性能较差,以采用退火为宜。
正火难以消除内应力,为防止工件的裂纹和变形,对大件和形状复杂件仍多采用退火处理。
从经济方面考虑,正火比退火的生产周期缩短,设备利用率提高,节约能源,降低成本,操作简便,所以在可能条件下,应尽量以正火代替退火。
锻造及锻后热处理工艺规范DOC.doc
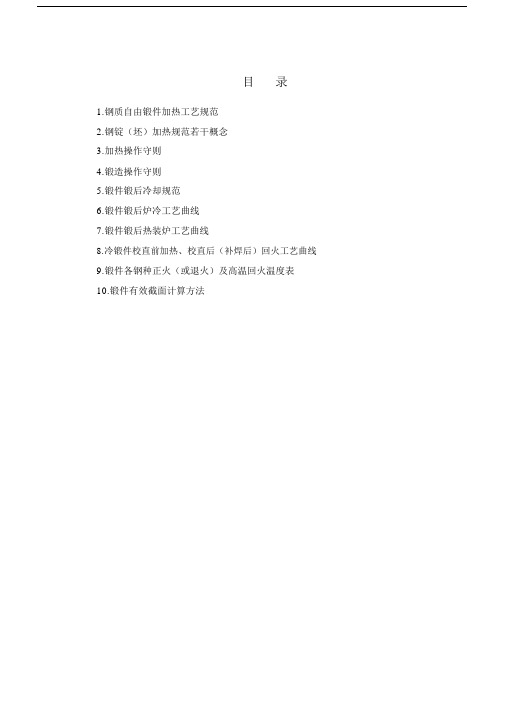
目录1.钢质自由锻件加热工艺规范2.钢锭(坯)加热规范若干概念3.加热操作守则4.锻造操作守则5.锻件锻后冷却规范6.锻件锻后炉冷工艺曲线7.锻件锻后热装炉工艺曲线8.冷锻件校直前加热、校直后(补焊后)回火工艺曲线9.锻件各钢种正火(或退火)及高温回火温度表10.锻件有效截面计算方法钢质自由锻件加热工艺规范一.范围:本规范规定了钢质自由锻件的通用加热技术条件。
本规范适用于碳素钢、合金钢、高合金钢、高温合金钢(铁基、镍基)的冷、热、半热钢锭(坯)的锻造前加热二.常用钢号分组和始、终锻加热温度范围:组号钢别Q195~Q255, 10~30Ⅰ35~45,15Mn~35Mn ,15Cr~35Cr50,55,40Mn~50Mn ,35Mn2-50Mn2 ,40Cr~55Cr ,20SiMn~35SiMn ,12CrMo~50CrMo ,34CrMo1A ,30CrMnSi , 20CrMnTi ,20MnMo ,Ⅱ12CrMoV~35CrMoV , 20MnMoNb , 14MnMoV~42MnMoV,38CrMoAlA ,38CrMnMo34CrNiMo~34CrNi3Mo,PCrNi1Mo~PCrNi3Mo,30Cr1Mo1V,25Cr2Ni4MoV ,22Cr2Ni4MoV ,5CrNiMo ,5CrMnMo ,37SiMn2MoV 30Cr2MoV ,40CrNiMo ,18CrNiW ,50Si2~60Si2 ,65Mn ,50CrNiW ,50CrMnMo ,60CrMnMo ,60CrMnVT7~T10 , 9Cr,9Cr2, 9Cr2Mo , 9Cr2V ,9CrSi ,70Cr3Mo ,Ⅲ1Cr13~4Cr13 ,86Cr2MoV ,Cr5Mo , 17-4PH0Cr18Ni9~2Cr18Ni9 ,0Cr18Ni9Ti , Cr17Ni2 , F316LN50Mn18Cr4 , 50Mn18Cr4N , 50Mn18Cr4WN , 18Cr18Mn18NGCr15,GCr15SiMn , 3Cr2W8V ,CrWMo , 4CrW2Si~6CrW2SiCr12MoV1 , 4Cr5MoVSi(H11) , W18Cr4VGH80, GH901, GH904 ,GH4145 ,WR26 ,ⅣNiCr20TiAl , incone1600, incone1800始锻温度终锻温度℃℃钢锭钢坯终锻精整12501220750700 1220120075070012201200800750 12001180850800 120011808508001200 1180 850 800 1180 1160 950 900 1130 1100 930 930注 1:始锻温度为锻前加热允许最高炉温,由于钢锭的铸态初生晶粒加热时过热倾向比同钢号钢坯小,故两者的锻前加热温度相差 20℃~30℃;注 2:根据产品的特性、锻件技术条件、变形量等因素,始锻温度可以适当调整;注 3:本规范未列入的钢种,可按化学成分相近的钢号确定;注 4:重要的、关键产品的、特殊材质的钢号,其加热工艺曲线由技术部编制;注 5:几种不同的钢种,不同尺寸的钢锭(或坯料),在同一加热炉加热时,要以合金成分高的,尺寸大的钢锭(或坯料)为依据编制加热工艺曲线。
锻造及锻后热处理工艺规范
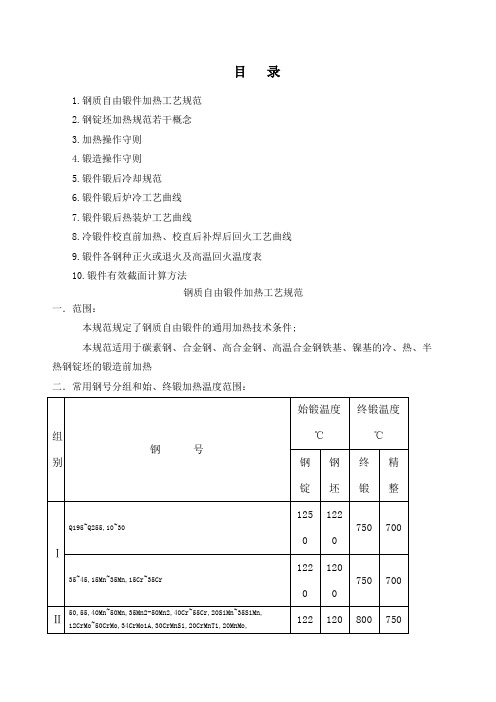
目录1.钢质自由锻件加热工艺规范2.钢锭坯加热规范若干概念3.加热操作守则4.锻造操作守则5.锻件锻后冷却规范6.锻件锻后炉冷工艺曲线7.锻件锻后热装炉工艺曲线8.冷锻件校直前加热、校直后补焊后回火工艺曲线9.锻件各钢种正火或退火及高温回火温度表10.锻件有效截面计算方法钢质自由锻件加热工艺规范一.范围:本规范规定了钢质自由锻件的通用加热技术条件;本规范适用于碳素钢、合金钢、高合金钢、高温合金钢铁基、镍基的冷、热、半热钢锭坯的锻造前加热二.常用钢号分组和始、终锻加热温度范围:注1:始锻温度为锻前加热允许最高炉温,由于钢锭的铸态初生晶粒加热时过热倾向比同钢号钢坯小,故两者的锻前加热温度相差20℃~30℃;注2:根据产品的特性、锻件技术条件、变形量等因素,始锻温度可以适当调整;注3:本规范未列入的钢种,可按化学成分相近的钢号确定;注4:重要的、关键产品的、特殊材质的钢号,其加热工艺曲线由技术部编制;注5:几种不同的钢种,不同尺寸的钢锭或坯料,在同一加热炉加热时,要以合金成分高的,尺寸大的钢锭或坯料为依据编制加热工艺曲线;三.冷钢坯;钢锭加热规范:钢锭坯加热规范若干概念1.钢锭坯入炉前的表面温度≥550℃的称为热钢锭,400~550℃的称为半热钢锭坯,≤400℃的称为冷钢锭;2.锻件半成品坯料的加热平均直径计算原则:δ -壁厚 H- 高度或长度 D- 外径1)实心圆类:当D>H时,按H计算;当D<H时,按D计算;2)筒类锻坯:H>D 当H>δ时,按δ计算;3)空心盘环类:H<D当H>δ时,按δ计算;当H<δ时,按H计算;3.为了避免锻件粗晶组织,最后一火的始锻温度可按其剩余锻造比Y确定:Y=~ 最高加热温度1050℃Y< 最高加热温度950℃4.不同钢种不同规格的坯料同炉加热时,装炉温度和升温速度均按较低的选用,保温时间按较长的选用;对要求加热温度低或保温时间短的坯料,可先出炉锻造;注:Y--锻造比加热操作守则1.钢锭坯装炉前,加热工应校对其冶炼炉号及锭件号,钢锭坯重量,尺寸以及钢锭坯的状态,并检查其表面质量,清除表面缺陷,不合格严禁装炉;2.重要的、关键产品的特殊材质的钢号,在进炉前由技术部向操作工进行技术交底;3.根据装炉实际情况,画好装炉图,记录装炉位置,做好实际操作记录,钢锭坯出炉顺序,及返回炉内锻坯位置要记录正确;4.钢锭坯加热过程中必须精心操作,严格控制装炉温度、升温或冷却速度,炉气应保持微正压,炉床上的氧化皮应定期清理;5.钢锭坯完成了加热保温时间之后因故不能出炉锻造时,可将炉温降至900~1050℃保温,若等到可出炉锻造时,则需将钢锭坯再加热至锻造温度下保温一段时间后方可出炉锻造;6.钢锭坯经炉内长时间保温之后因故不需再加热时,必须随炉以≤80℃/h 的降温速度将钢锭冷至250℃以下方可出炉;7.加热炉喷嘴要避免火焰直接喷射在钢锭坯的表面上,经常检查热电偶、热工仪表,使其正常运行,并维护和保养加热炉设备;锻造操作守则1.锻造前应熟悉锻造工艺卡的内容,重要、关键锻件,技术部门需要进行技术交底;2.锻造生产是集体操作,一定要开好班前会,了解加热情况,做好设备、工具准备工作,做到分工明确,指挥者应对生产的质量和安全负责;3.在生产中应做到“三勤”:勤量、勤卡、勤查;“四准”:标尺要定准、样棒要划准、卡钳要量准、尺寸要记准;4.生产时必须按照工艺卡进行锻造,不得任意改动,如工艺卡不合理或因特殊情况不能按照工艺卡执行,应及时向技术部反映,及时解决;5.锻造指挥者必须认真执行确保锻造工艺卡上各项工艺参数到位、锻造尺寸到位,确保锻件的锻造比镦粗比、拔长比,重要关键锻件做好生产过程的记录;6.严格控制终锻温度,特别是关键、重要锻件、高合金钢、高温合金钢;7.锻件完工后,锻件必须在相当于钢锭的底部端打上钢印钢号、冶炼炉号和锻件号,钢印必须正确、清楚;8.料头应用油漆写明分类标记,以便回收回炉;9.对于关键、重要锻件,或试制新产品钢种的锻件,有关技术人员必须跟班在现场,及时处理可能遇到的问题;锻件锻后冷却规范1.锻件锻后冷却必须按规范执行;若有特殊情况不能按规范执行须由技术部同意,并有书面意见;2.沙冷锻件,必须将沙子全部覆盖在锻件上,而不是将锻件置于沙坑中;3.锻件炉冷要根据不同钢种炉冷曲线工艺规范执行;4.锻件热装炉是按锻件锻后热处理曲线工艺规范执行锻件锻后正火、回火或退火;5.钢锭或钢坯冶炼工艺是采用EF+LF+VD或VODC方法;锻件锻后冷却规范按截面尺寸向下调低一档;锻件锻后炉冷工艺曲线一.一般锻件锻后炉冷工艺曲线Ⅰ:按锻件锻后冷却规范的炉冷钢号确定保温时间Ⅰ:1.Ⅱ类钢号炉冷保温时间按有效截面尺寸计算:~2h/100mm;2.Ⅲ类钢号炉冷保温时间按有效截面尺寸计算:~3h/100mm;3.Ⅳ类钢号炉冷保温时间按有效截面尺寸计算:4~5h/100mm; 二.重要锻件、有特殊要求的锻件锻后炉冷工艺曲线Ⅱ:一.一般锻件锻后热装炉——正火+回火热处理工艺曲线:2.640~660℃保温时间Ⅰ按2-3h保温时间计算;3.正火温度保温时间Ⅱ按有效截面尺寸计算:1~100mm;4.350~400℃过冷保温时间Ⅲ按有效截面尺寸计算:~1h/100mm;5.高温回火保温时间Ⅳ按有效截面尺寸:Ⅱ类钢号高温回火保温时间~2h/100mm,Ⅲ类钢号高温回火保温时间~100mm,Ⅳ类钢号高温回火保温时间4~5h/100mm;二.滚珠轴承钢、冷轧辊钢锻后热装炉球化退火工艺曲线:~650℃保温时间Ⅰ按3-4h保温时间计算;~800℃保温时间Ⅱ按有效截面尺寸计算:mm;~720℃650~670℃保温时间Ⅲ按有效截面尺寸计算:2h/mm;冷锻件校直前加热、校直补焊后回火工艺曲线。
常用锻件热处理工艺

820~840
≤241
T7、T8、T10、T12
790~820
≤69
退
火
T7、T8、T10、T12
750~780
炉冷到600~650℃,保温1~2h,再炉冷到600℃,出炉空冷
170~207
9CrSi、CrWMn、CrMn、9CrWMn、CrW5、GCr9、GCr5
770~780
炉冷到680~720℃,保温3~5h,再炉冷到600℃,出炉空冷
207~255
5CrMnMo、5CrWMn、5CrNiMo
760~790
炉冷到600℃以下空冷
锻件的热处理种类及应用
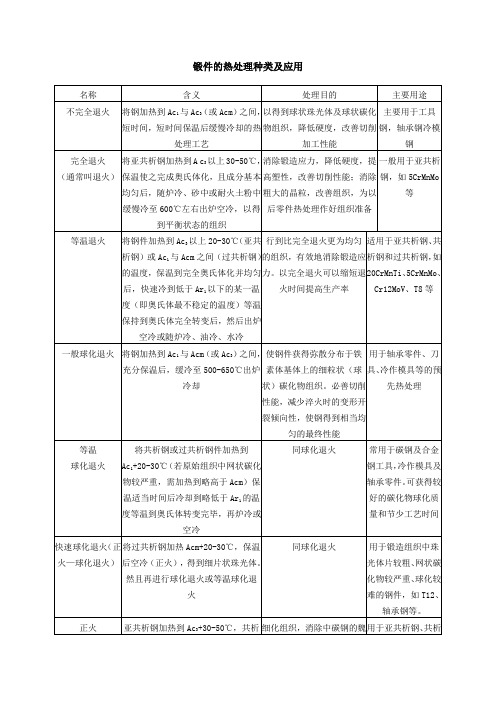
“蛤蟆皮” 铝合金、铜合金的坯料,在镦粗时表
由于坯料过热,晶粒粗大而引起
表面 面形成“蛤蟆皮”,或者出现类似秸 有粗晶环的铝合金毛坏,在镦粗时也会出现这种现象
皮的粗糙表面,严重时还要开裂
魏氏 α 相或 (α+β)钛合金坏料过热后,其显微由于加热温度超过了(α+β)钛合金的 β 转变温度而
(普通正火) 钢和过共析钢加热到 Acm+30-50℃, 氏组织或过共析钢的网状 钢和过共析钢的热
保温一定时间后空冷,得到珠光体型碳化物,减小应力,改善切
处理
组织的热处理
削加工性能
二段正火 按普通正火加热保温后,先把工件快 减少变形和消除非正常组 用于形状复杂或断
冷到 Ar1 以下 550℃左右,然后再放入
白点在合金结构钢中常见,在普通碳
钢中也有发现
缩孔残余 在锻件低倍检查时,出现不规则的皱 由于钢锭冒口部分产生的集中缩孔未切除干净,开坯
折状缝隙,形似裂纹,呈现深褐色或
和轧制时残留在钢坯内部而产生的
灰白色;高倍检查缩孔残余附近有大
量非金属夹杂物,质脆易剥落
铝合金挤压 经热处理后供应的铝合金挤压棒材, 主要是由于铝合金中 Mn、Cr 等元素以及挤压时金属
热处理工艺
将时效强化合金或不锈钢、耐热钢加 改善锻态时的强化相不均匀分 用于不锈钢、耐
热到一定高温(不锈钢、耐热钢为 布,降低硬度、提高塑性、抗 热钢和时效强化
1000-1150℃)使强化相全部或大部 蚀性及导电性或为以后的时效
合金
分溶入固溶体,并调整晶粒尺寸,然
处理进行准备
后以较快速度(水、空气等)冷却
棒材上的粗 在其横断面外层环形内出现粗大晶 与挤压筒壁之间的摩擦,使棒材表面层变形剧烈所致
各种热处理目的

HG 20603-1977之3.0.3有规定,锻件.......暂符合JB 4726~4728的相应要求。
JB4726-2000之5.5有规定,锻件应按表3中规定的热处理状态交货。
那么,请看5.5和表3吧,表比较大。
锻件按照标准来说全部应该是要热处理的,但是我们国家的实际情况是,一般的锻件分为一级锻件,二级锻件,三级锻件一级锻件一般情况下如果用户不要求是不热处理的二级锻件必须要热处理三级锻件除热处理外,还需要100%探伤.金属热处理是将金属材料(其中包括黑色金属材料和有色金属材料及其加工后的工件)在固态范围内,通过一定的加热,保温和冷却,使金属或合金的内部组织发生变化,从而获得预期的性能(如力学性能、加工性能、物理和化学性能)、组织和结构的工艺过程的总称。
一、退火(一)、概念:把钢加热到适当温度(一般Ac1以上),保温一定的时间,然后缓慢冷却,以获得接近平衡状态的组织的热处理方法。
(二)、目的:1、降低硬度,以利于切削加工;2、提高钢的塑性和韧性,以便于冷变形加工;3、改善或消除钢在铸造、轧制、锻造和焊接等过程中所造成的各种组织缺陷;4、细化晶粒,改善钢中碳化物的形态及分布,为最终热处理做好组织准备;5、消除内应力,以减少变形和防止开裂。
二、淬火(一)、概念:将钢加热到临界温度(Ac3或Ac1)以上,保温一定时间使之奥氏体化后,以大于临界冷却速度的冷速进行冷却,以得到高硬度的马氏体或下贝氏体的热处理工艺方法。
(二)、目的:1、提高工件的硬度和耐磨性;2、提高工件的综合力学性能或使工件获得较高的弹性;3、获得特殊的物理化学性能(磁性、耐蚀性、耐热性等)。
三、回火(一)、概念:将工件加热到钢的A1以下某一温度,保温一段时间,然后进行冷却(一般冷至室温)的热处理工艺。
(二)、目的:1、使工件获得所要求的力学性能;2、减少或消除残余应力;3、稳定工件的组织和尺寸。
(三)、分类:1、低温回火(150~250℃),如渗碳和碳氮共渗件,低合金超高强度钢等;2、中温回火(300~450℃),如各种弹簧钢等;3、高温回火(500~650℃),如螺栓、轴等。
16MnⅢ级锻件热处理工艺
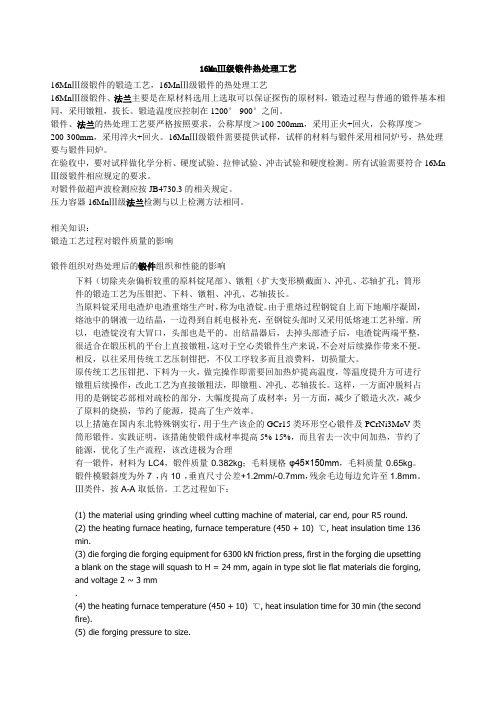
16MnⅢ级锻件热处理工艺16MnⅢ级锻件的锻造工艺,16MnⅢ级锻件的热处理工艺16MnⅢ级锻件、法兰主要是在原材料选用上选取可以保证探伤的原材料,锻造过程与普通的锻件基本相同,采用镦粗,拔长。
锻造温度应控制在1200°-900°之间。
锻件、法兰的热处理工艺要严格按照要求,公称厚度>100-200mm,采用正火+回火,公称厚度>200-300mm,采用淬火+回火。
16MnⅢ级锻件需要提供试样,试样的材料与锻件采用相同炉号,热处理要与锻件同炉。
在验收中,要对试样做化学分析、硬度试验、拉伸试验、冲击试验和硬度检测。
所有试验需要符合16Mn Ⅲ级锻件相应规定的要求。
对锻件做超声波检测应按JB4730.3的相关规定。
压力容器16MnⅢ级法兰检测与以上检测方法相同。
相关知识:锻造工艺过程对锻件质量的影响锻件组织对热处理后的锻件组织和性能的影响下料(切除夹杂偏析较重的原料锭尾部)、镦粗(扩大变形横截面)、冲孔、芯轴扩孔;筒形件的锻造工艺为压钳把、下料、镦粗、冲孔、芯轴拔长。
当原料锭采用电渣炉电渣重熔生产时,称为电渣锭。
由于重熔过程钢锭自上而下地顺序凝固,熔池中的钢液一边结晶,一边得到自耗电极补充,至钢锭头部时又采用低熔速工艺补缩。
所以,电渣锭没有大冒口,头部也是平的。
出结晶器后,去掉头部渣子后,电渣锭两端平整,很适合在锻压机的平台上直接镦粗,这对于空心类锻件生产来说,不会对后续操作带来不便。
相反,以往采用传统工艺压制钳把,不仅工序较多而且浪费料,切损量大。
原传统工艺压钳把、下料为一火,做完操作即需要回加热炉提高温度,等温度提升方可进行镦粗后续操作,改此工艺为直接镦粗法,即镦粗、冲孔、芯轴拔长。
这样,一方面冲脱料占用的是钢锭芯部相对疏松的部分,大幅度提高了成材率;另一方面,减少了锻造火次,减少了原料的烧损,节约了能源,提高了生产效率。
以上措施在国内东北特殊钢实行,用于生产该企的GCr15类环形空心锻件及PCrNi3MoV类筒形锻件。
锻造及锻后热处理工艺规范
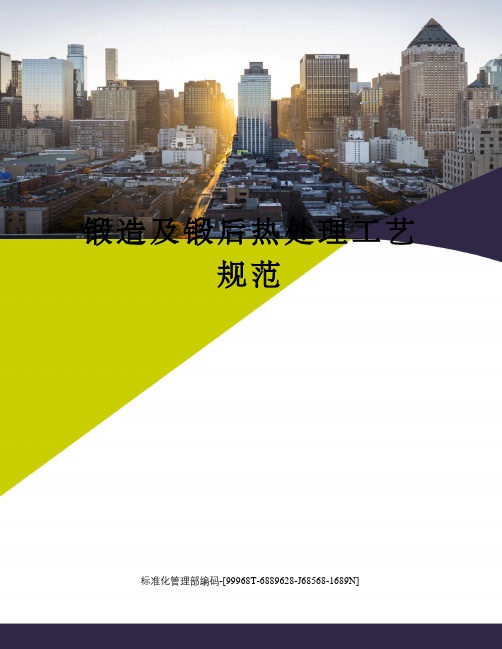
锻造及锻后热处理工艺规范标准化管理部编码-[99968T-6889628-J68568-1689N]目录1.钢质自由锻件加热工艺规范2.钢锭(坯)加热规范若干概念3.加热操作守则4.锻造操作守则5.锻件锻后冷却规范6.锻件锻后炉冷工艺曲线7.锻件锻后热装炉工艺曲线8.冷锻件校直前加热、校直后(补焊后)回火工艺曲线9.锻件各钢种正火(或退火)及高温回火温度表10.锻件有效截面计算方法钢质自由锻件加热工艺规范一.范围:本规范规定了钢质自由锻件的通用加热技术条件。
本规范适用于碳素钢、合金钢、高合金钢、高温合金钢(铁基、镍基)的冷、热、半热钢锭(坯)的锻造前加热二.常用钢号分组和始、终锻加热温度范围:注1:始锻温度为锻前加热允许最高炉温,由于钢锭的铸态初生晶粒加热时过热倾向比同钢号钢坯小,故两者的锻前加热温度相差20℃~30℃;注2:根据产品的特性、锻件技术条件、变形量等因素,始锻温度可以适当调整;注3:本规范未列入的钢种,可按化学成分相近的钢号确定;注4:重要的、关键产品的、特殊材质的钢号,其加热工艺曲线由技术部编制;注5:几种不同的钢种,不同尺寸的钢锭(或坯料),在同一加热炉加热时,要以合金成分高的,尺寸大的钢锭(或坯料)为依据编制加热工艺曲线。
三.冷钢坯。
钢锭加热规范:钢锭(坯)加热规范若干概念1.钢锭(坯)入炉前的表面温度≥550℃的称为热钢锭,400~550℃的称为半热钢锭(坯),≤400℃的称为冷钢锭。
2.锻件半成品坯料的加热平均直径计算原则:δ -壁厚 H- 高度或长度 D- 外径1)实心圆类:当D>H时,按H计算;当D<H时,按D计算。
2)筒类锻坯:H>D 当H>δ时,按δ计算。
3)空心盘(环)类:H<D当H>δ时,按δ计算;当H<δ时,按H计算。
3.为了避免锻件粗晶组织,最后一火的始锻温度可按其剩余锻造比(Y)确定:Y=~ 最高加热温度1050℃Y< 最高加热温度950℃4.不同钢种不同规格的坯料同炉加热时,装炉温度和升温速度均按较低的选用,保温时间按较长的选用。
锻件热处理标准

锻件热处理标准《锻件热处理标准:铸就卓越的关键密码》嘿,你知道吗?在工业的奇幻世界里,锻件就像是英勇的战士,而热处理标准就是它们的无敌秘籍!要是不了解这个标准,那制造出来的锻件可就像没头苍蝇一样,到处乱撞还不知道为啥不行呢!今天,就让我们一起揭开这神秘的锻件热处理标准的面纱,看看它到底有多重要!一、“火候大师:温度的精确掌控”在热处理的舞台上,温度那可是绝对的主角呀!“温度就像是锻件的魔法调料,多一度太老,少一度太嫩。
”温度的精确掌控简直太重要啦!就好比厨师做菜,火候不到位,菜就不好吃。
如果温度过高,锻件可能会变形甚至报废;温度过低,又达不到预期的性能效果。
比如在对钢铁锻件进行热处理时,不同的温度区间会导致不同的组织结构变化,从而影响其硬度、韧性等关键性能。
所以呀,一定要像大师级厨师一样,精准把握温度这个“魔法调料”的用量!二、“时间魔法师:时长的巧妙拿捏”时间在热处理中也是一位厉害的魔法师哟!“时间就像一场和锻件的浪漫约会,太短没感觉,太长会厌倦。
”可不是嘛,时间太短,热处理效果不充分;时间太长,不仅浪费能源,还可能对锻件造成不良影响。
就像烤面包一样,时间太短里面还是生的,时间太长就烤焦啦!比如铝合金锻件的固溶处理,需要在特定温度下保持一定的时间,才能使合金元素充分溶解和均匀分布,达到最佳性能。
这就需要我们巧妙地拿捏时间这个“浪漫约会”的时长啦!三、“冷却大侠:冷却方式的智慧选择”冷却这一环节可是个厉害的大侠呢!“冷却方式就像是锻件的乘凉秘籍,选对了就舒爽,选错了就难受。
”不同的冷却方式会给锻件带来截然不同的效果。
快速冷却可以获得较高的硬度和强度,但可能会导致较大的内应力;缓慢冷却则可以减少内应力,但可能会降低硬度。
这就好比夏天选择乘凉方式,吹空调太猛会感冒,扇扇子太慢又不解热。
所以呀,要根据锻件的材料和性能要求,智慧地选择冷却方式这个“乘凉秘籍”!四、“介质精灵:介质的神奇魔力”介质在热处理中就像一群可爱的精灵,有着神奇的魔力哟!“介质就像是锻件的魔法伙伴,找对了一起变强,找错了一起遭殃。
- 1、下载文档前请自行甄别文档内容的完整性,平台不提供额外的编辑、内容补充、找答案等附加服务。
- 2、"仅部分预览"的文档,不可在线预览部分如存在完整性等问题,可反馈申请退款(可完整预览的文档不适用该条件!)。
- 3、如文档侵犯您的权益,请联系客服反馈,我们会尽快为您处理(人工客服工作时间:9:00-18:30)。
(一)钢的普通热处理
• • “四把火”(退火、正火、淬火、回火)的工艺过程; “四把火”对零件加工和使用的影响和作用。
1、退火 • 退火是将钢加热至临界点Ac1以上或以下温度,保温 以后随炉缓慢冷却以获得近于平衡状态组织的热处理工艺。 其主要目的是均匀钢的化学成分及组织,细化晶粒,调整 硬度,消除内应力和加工硬化,改善钢的成形及切削加工 性能,并为淬火做好组织准备。 • 根据加热温度可分为临界温度(Ac1或Ac3)以上或 以下的退火。 • 前者又称相变重结晶退火,包括完全退火、扩散退火、不 完全退火和球化退火。后者包括再结晶退火及去应力退火。 • 按照冷却方式可分为等温退火和连续冷却退火。
(6)去应力退火 • 去应力退火:为消除铸造、锻造、焊接和机加工、冷变形等冷热 加工在工件中造成的残留内应力而进行的低温退火,称为去应力退火。 去应力退火是将钢件加热至低于Ac1的某一温度(一般为500 ℃~650 ℃),保温后随炉冷却, 这种处理可以消除约50%~80%的内应力, 不 引起组织变化。
(3)淬火的方法 • 选择适当的淬火方法同选用淬火介质一样,可以保证在获得所要求 的淬火组织和性能条件下,尽量减小淬火应力,减小工件变形和开裂 倾向。 • ①单介质淬火法 • 它是将奥氏体状态的工件放入一种淬火介质中一直冷却到室温的 淬火方法。 • ②双介质淬火法 • 它是先将奥氏体状态的工件在冷却能力强的淬火介质中冷却至 接近Ms点温度时,再立即转入冷却能力较弱的淬火介质中冷却,直 至完成马氏体转变。一般用水作为快冷淬火介质,用油作为慢冷淬火 介质。有时也可以采用水淬、空冷的方法。
•
从热处理工艺性能考虑,对于形状复杂要求变形很小的工件,如 果钢的淬透性较高,例如合金钢工件,可以在较缓慢的冷却介质中淬 火,如有些淬透性很高的钢,甚至可以在空气中冷却淬火,因此淬火 变形更小。 • 但是并非所有工件均要求很高的淬透性,例如承受弯曲或扭转的 轴类零件,其外缘承受最大应力,轴心部分应力较小,因此保证一定 淬透层深度就可以了。一些汽车、拖拉机的重负荷齿轮通过表面淬火 或化学热处理,获得一定深度的均匀淬硬层,即可达到表硬心韧的性 能要求,甚至可以采用淬透性低的低淬透性钢制造。焊接用钢采用淬 透性低的低碳钢制造,目的是避免焊缝及热影响区在焊后冷却过程中 得到马氏体组织,从而可以防止焊接构件的变形和开裂。
5、钢的回火 (1)回火的概念、目的 • 回火是将淬火钢加热到Ac1以下的某一温度保温后进行冷却的热 处理工艺。 • 回火的目的是减少或消除淬火应力,保证相应的组织转变,提高 钢的韧性和塑性,获得硬度、强度、塑性和韧性的适当配合,以满足 各种用途工件的性能要求。
(2)回火的分类 • 根据国家的组织和性能的要求,回火有低温回火、中温回火和高 温回火等几种。 • ①低温回火 • 低温回火温度约为150-250℃,回火组织为回火马氏体,和淬火马 氏体相比,回火马氏体保持了钢的高硬度、高强度和良好耐磨性。 • ②中温回火 • 中温回火温度一般在350-500℃之间,回火的组织为回火屈氏体。 钢具有高的弹性极限,较高的强度和硬度,良好的塑性和韧性。故中 温回火主要用于各种弹簧零件及热锻模具。
四、锻件的热处理
锻件热处理
•
锻件热处理按其热处理的目的不同可分为两组。 • 第一组,锻件热处理的目的既为金属切削加工提供最佳切削性能, 也为第二热处理作好组织准备。属于这一组的锻件常用渗碳钢、轴承 钢、工具钢等制造。 • 第二组,锻件热处理的目的是为了得到适当的组织,达到产品的 技术要求。而且在保证零件技术要求的前提下,应有适中的硬度和小 的硬度偏差以便在金属切削机床上获得经济的加工性能。锻件机械加 工后不再进行最终热处理。该组锻件一般由中碳钢和中碳合金钢制成。 锻件热处理最常见的工艺是退火(包括完全退火、等温退火、球化退 火等各种类型的退火)、正火(包括正火加高温回火)、调质(淬火 加高温回火)等。
(3)淬透性的意义 • 钢的淬透性是钢的热处理工艺性能,在生产中有重要的实际意义, 工件在整体淬火条件下,从表面至中心是否淬透,对其力学性能有重 要影响。一些在拉、压、弯曲或剪切载荷下工作的零件,例如各类齿 轮、轴类零件,希望整个截面都能被淬透,从而保证这些零件在整个 截面上得到均匀的力学性能。选择淬透性较高的钢才能满足这一性能 要求。而淬透性较低的钢,工件心部不能淬透,其力学性能低,特别 是冲击韧性低,不能充分发挥材料的性能潜力。 • 钢的淬透性越高,能淬透的工件截面尺寸越大。对于大截面的重 要工件,为了增加有效淬硬深度,必须选用过冷奥氏体很稳定的合金 钢。工件越大,要求的淬硬层越深钢的合金化程度应越高,所以淬透 性是机器零件选材的重要参考数据。
4、钢的淬透性 (1)淬透性的概念 • 钢的淬透性是指奥氏体化后的钢在淬火时获得马氏体的能力,其 大小用钢在一定条件下淬火获得的淬透层深度表示。 • 一定尺寸的工件在某介质中淬火,其淬透层的深度与工件截面各 点的冷却速度有关。 • 淬透性表示钢淬火时获得马氏体的能力,它反映钢的过冷奥氏体 稳定性,即与钢的临界冷却速度有关。过冷奥氏体稳定,临界淬火速 度越小,钢在一定条件下有效淬硬深度越深,则钢的淬透性越好。 (2) 淬透性的测定方法 • 我国国家标准规定:测定淬透性的方法有临界淬火直径法和末端 淬火试样法。钢的淬透性值可用J(HRC/d)表示,其中J表示末端淬 透性,d表示至水冷端的距离, HRC为该处测得的硬度值。
3、 淬火 • 钢的淬火与回火是热处理工艺中最重要、也是用途最广的工序。 • 淬火可以显著提高钢的强度和硬度。为了消除淬火钢的残余内应力, 得到不同强度、硬度和韧性配合的性能,需要配以不同的回火。所以 淬火和回火又是不可分割的、紧密衔接在一起的两种热处理工艺。 • 淬火、回火作为各种机器零件及工、模具的最终热处理是赋予钢 件最终性能的关键性工序,也是钢件热处理强化的重要手段之一。 (1) 淬火的定义和目的 • 淬火的定义: 把钢加热到临界点Ac1或Ac3以上,保温并随之以大 于临界冷却速度(Vk)冷却,以得到介稳状态的马氏体或下贝氏体组 织的热处理工艺方法称为淬火。
(1)均匀化退火 • 均匀化退火又称扩散退火 把钢加热到略低于固相线的温度下长时 间保温,然后以缓慢的冷却速度冷却,以获得均匀的组织和成分的热 处理工艺。 • 钢件均匀化退火的加热温度通常选择在Ac3或Accm以上 150~300℃。视钢种和偏析程度而异。碳钢一般为1100~1200℃,合 金钢一般为1200~1300℃。均匀化退火时间一般为10~15h。 • 均匀化退火的目的在于消除或减少金属铸锭、铸件或锻坯化学成 份偏析及显微组织(枝晶)的不均匀性,以达到均匀化目的。
③ 分级淬火法 • 它是将奥氏体化的工件首先淬入略高于 钢的Ms点的盐浴或碱浴炉中保温,当工件 内外温度均匀后,再从浴炉中取出空冷至 室温,完成马氏体转变。 • ④ 等温淬火 • 它是将奥氏体化后的工件淬入Ms点以上 某温度盐浴中等温保持足够长时间,使之 转变为下贝氏体组织,而后于空气中冷却 的淬火方法。
(2)完全退火 • 完全退火又称重结晶退火 是把钢加热至Ac3以上20 ℃~30 ℃, 保 温一定时间后缓慢冷却(随炉冷却或埋入石灰和砂中冷却), 以获得接近 平衡组织的热处理工艺。完全退火一般用于亚共析钢。 • 完全退火的目的在于,通过完全重结晶,使热加工造成的粗大、 不均匀的组织均匀化和细化,以提高性能;或使中碳以上的碳钢和合 金钢得到接近平衡状态的组织,以降低硬度,改善切削加工性能。由 于冷却速度缓慢,还可消除内应力。
(3)等温退火 • 等温退火 将钢件加热到高于Ac3 (或Ac1 ) 的温度, 保温适当时间 后, 较快地冷却到珠光体区的某一温度, 并等温保持, 使奥氏体等温转 变,然后缓慢冷却的热处理工艺。 • 等温退火的目的与完全退火相同, 能获得均匀的预期组织; 对于 奥氏体较稳定的合金钢, 可大大缩短退火时间。 • 完全退火全过程所需时间比较长,特别是对于某些奥氏体比较稳 定的合金钢,往往需要数十小时,甚至数天的时间。如果在对应于钢 的TTT曲线上的珠光体形成温度进行过冷奥氏体的等温转变处理,就 有可能在等温处理的后期稍快的进行冷却,以便大大缩短整个退、渗碳工件和其他高强度耐磨机器零件等的强度、硬 度和耐磨性; • ②结构钢通过淬火和回火之后获得良好的综合力学性能。 • ③此外,还有很少数的一部分工件是为了改善钢的物理和化学性能。 如提高磁钢的磁性,不锈钢淬火以消除第二相,从而改善其耐蚀性。 (2)淬火的介质 • 淬火时,最常用的淬火介质是水、盐水和油。
• ③高温回火 • 高温回火温度约为500-650℃,回火组织为回火索氏体。淬火和随 后的高温回火叫做调质处理。高温回火主要适用于中碳结构钢或低合 金结构钢,用来制作曲轴、连杆、连杆螺栓、汽车半轴、机床主轴及 齿轮等重要的机器零件。
(4) 不完全退火 • 不完全退火 将钢件加热至Ac1和Ac3之 间,经保温并缓慢冷却,以获得接近平衡 组织的热处理工艺称为不完全退火。 (5)球化退火 • 球化退火 为使钢中碳化物球状化的热 处理工艺。目的是使二次渗碳体及珠光体 中的渗碳体球状化(退火前正火将网状渗 碳体破碎),以降低硬度,改善切削加工 性能;并为以后的淬火作组织准备。球化 退火主要用于共析钢和过共析钢。
2、正火 • 钢材或钢件加热到Ac3和Accm以上30 ℃~50 ℃, 保温适当时间 后, 在自由流动的空气中均匀冷却的热处理称为正火。 • 正火可以作为预备热处理,为机械加工提供适宜的硬度,又能细 化晶粒、消除应力、消除魏氏组织和带状组织,为最终热处理提供合 适的组织状态。正火还可以作为最终热处理,为某些受力较小、性能 要求不高的碳素钢结构零件提供合适的机械性能,正火还能消除过共 析钢的网状碳化物,为球化退火做好组织准备。