齿轮变位系数
变位系数
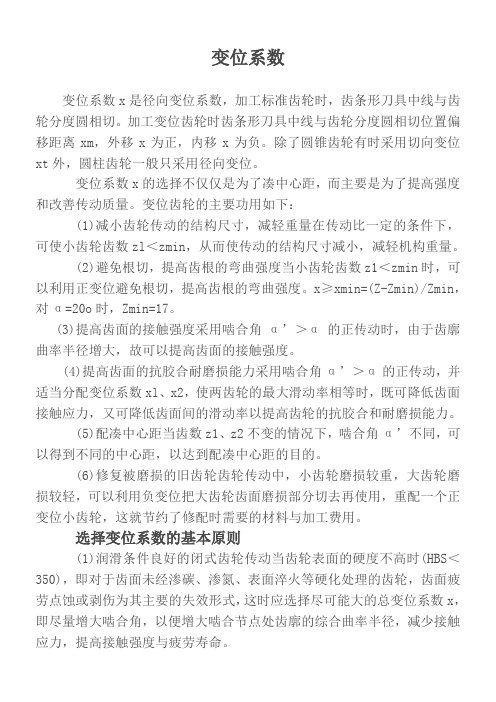
变位系数变位系数x是径向变位系数,加工标准齿轮时,齿条形刀具中线与齿轮分度圆相切。
加工变位齿轮时齿条形刀具中线与齿轮分度圆相切位置偏移距离xm,外移x为正,内移x为负。
除了圆锥齿轮有时采用切向变位xt外,圆柱齿轮一般只采用径向变位。
变位系数x的选择不仅仅是为了凑中心距,而主要是为了提高强度和改善传动质量。
变位齿轮的主要功用如下:(1)减小齿轮传动的结构尺寸,减轻重量在传动比一定的条件下,可使小齿轮齿数zl<zmin,从而使传动的结构尺寸减小,减轻机构重量。
(2)避免根切,提高齿根的弯曲强度当小齿轮齿数z1<zmin时,可以利用正变位避免根切,提高齿根的弯曲强度。
x≥xmin=(Z-Zmin)/Zmin,对α=20o时,Zmin=17。
(3)提高齿面的接触强度采用啮合角α’>α的正传动时,由于齿廓曲率半径增大,故可以提高齿面的接触强度。
(4)提高齿面的抗胶合耐磨损能力采用啮合角α’>α的正传动,并适当分配变位系数xl、x2,使两齿轮的最大滑动率相等时,既可降低齿面接触应力,又可降低齿面间的滑动率以提高齿轮的抗胶合和耐磨损能力。
(5)配凑中心距当齿数z1、z2不变的情况下,啮合角α’不同,可以得到不同的中心距,以达到配凑中心距的目的。
(6)修复被磨损的旧齿轮齿轮传动中,小齿轮磨损较重,大齿轮磨损较轻,可以利用负变位把大齿轮齿面磨损部分切去再使用,重配一个正变位小齿轮,这就节约了修配时需要的材料与加工费用。
选择变位系数的基本原则(1)润滑条件良好的闭式齿轮传动当齿轮表面的硬度不高时(HBS<350),即对于齿面未经渗碳、渗氮、表面淬火等硬化处理的齿轮,齿面疲劳点蚀或剥伤为其主要的失效形式,这时应选择尽可能大的总变位系数x,即尽量增大啮合角,以便增大啮合节点处齿廓的综合曲率半径,减少接触应力,提高接触强度与疲劳寿命。
当轮齿表面硬度较高时(HBS>350),常因齿根疲劳裂纹的扩展造成轮齿折断而使传动失效,这时,选择变位系数应使齿轮的齿根弯曲强度尽量增大,并尽量使相啮合的两齿轮具有相近的弯曲强度。
变位齿轮的计算方法

变位齿轮的计算方法1 变位齿轮的功用及变位系数变位齿轮具有以下功用:(1)避免根切;(2)提高齿面的接触强度和弯曲强度;(3)提高齿面的抗胶合和耐磨损能力;(4)修复旧齿轮;(5)配凑中心距。
对于齿数z=8~20的直齿圆柱齿轮,当顶圆直径d a=mz+2m+2xm时,不产生根切的最小变位系数x min,以及齿顶厚S a=0.4m和S a=0时的变位系数x sa=0.4m和x sa=0如表1所列。
2 变位齿轮的简易计算将变位齿轮无侧隙啮合方程式作如下变换:总变位系数中心距变动系数齿顶高变动系数表 1 齿数z=8~20圆柱齿轮的变位系数z x min x sa=0.4m x sa=08 910111213141516171819 200.53 0.47 0.42 0.36 0.30 0.24 0.18 0.12 0.06 0-0.05 -0.11 -0.170.180.220.270.310.350.390.430.460.500.530.560.590.620.560.630.700.760.820.880.930.981.031.081.131.181.23或Δy=xΣ-y式中:α——压力角,α=20°;α′——啮合角;z2、z1——大、小齿轮的齿数。
将上述三式分别除以,则得:由上述公式可以看出,当齿形角α一定时,x z、y z和Δy z均只为啮合角α′的函数。
在设计计算时,只要已知x z、y z、Δy z和α′四个参数中的任一参数,即可由变位齿轮的x z、y z、Δy z和啮合角α′的数值表(表2)中,查出其他三个参数,再进行下列计算。
一般齿轮手册上均列有此数值表。
式中正号用于外啮合,负号用于内啮合。
3 计算实例例1:已知一对外啮合变位直齿轮,齿数z1=18,z2=32,压力角α=20°,啮合角α′=22°18′,试确定总变位系数xΣ、中心距变动系数y及齿顶高变动系数Δy。
齿轮对基本参数

齿轮对基本参数****************************法面模数:3齿数:小齿轮=16;大齿轮=69压力角:0.3491螺旋角:0.2619变位系数:小齿轮=0.1;大齿轮=-0.1齿宽:小齿轮=50;大齿轮=36端面分度圆压力角:0.3604端面节圆压力角(即啮合角):0.3604基圆螺旋角:0.2457齿顶圆直径:小齿轮=56.2942;大齿轮=219.7061基圆直径:小齿轮=46.5023;大齿轮=200.5410中心矩:132.000113960836齿数比:4.3125当量齿数:小齿轮=17.6067;大齿轮=75.9289****************************设计参数****************************机构工作级别:M5机构类型:起升机构或非平衡变幅机构机构载荷状态:L2-中(机构经常承受中等载荷,较少承受最大载荷)齿轮啮合类型:外啮合齿轮精度等级:6级允许齿厚的磨损量占原齿厚的百分比:10%试验齿轮齿面接触疲劳极限应力:小齿轮=1350N/mm2;大齿轮=895N/mm2 试验齿轮齿根弯曲疲劳极限应力:小齿轮=325N/mm2;大齿轮=330N/mm2 ****************************计算载荷****************************电动机额定力矩传到计算零件的力矩:303.8980N.m小齿轮转速:155转/min----------------------------小齿轮疲劳计算基本载荷:347.0515N.m小齿轮工作最大扭矩:390.2050N.m----------------------------分度圆上基本切向力:13967.4969N----------------------------循环次数系数:小齿轮=1.0000;大齿轮=0.8208载荷系数:小齿轮=0.8100;大齿轮=0.8100等效切向力:小齿轮=11313.6725N;大齿轮=9286.7739N----------------------------齿轮的动载系数:1.0021齿向载荷分布系数:小齿轮=1.3555;大齿轮=1.4322齿面接触强度用的齿间载荷分配系数:1.0500对于齿面接触疲劳强度计算的计算切向力:小齿轮=16135.7975;大齿轮=13995.1343N----------------------------轮齿弯曲强度用的齿间载荷分配系数:1.0500对于轮齿弯曲疲劳强度计算的计算切向力:小齿轮=16135.7975;大齿轮=13995.1343N ----------------------------分度圆上最大切向力:15704.2609N对于齿面接触静强度计算的最大计算切向力:小齿轮=22351.1439;大齿轮=23617.0211N对于轮齿弯曲静强度计算的最大计算切向力:小齿轮=22351.1439;大齿轮=23617.0211N ****************************齿面接触强度计算参数****************************节点区域系数:2.4246弹性系数:189.8000重合度系数:0.8035螺旋角系数:0.9828节圆处的计算接触应力:小齿轮=1211.2739N/mm2;大齿轮=1128.0691N/mm2----------------------------工作硬化系数:1.0000许用接触耐久性应力:小齿轮=1350.0000N/mm2;大齿轮=895.0000N/mm2齿面接触耐久性安全系数:小齿轮=1.1145;大齿轮=0.7934----------------------------节圆处的最大计算接触应力:小齿轮=1425.5978N/mm2;大齿轮=1465.4119N/mm2齿面接触静强度安全系数:小齿轮=1.5152;大齿轮=0.9772****************************齿根弯曲强度计算参数****************************齿形系数:小齿轮=2.8251;大齿轮=2.2819应力修正系数:小齿轮=1.5634;大齿轮=1.7126重合度系数:0.7327螺旋角系数:0.8764磨损系数:1.2500计算的齿根弯曲应力:小齿轮=529.6723N/mm2;大齿轮=406.4848N/mm2----------------------------试验齿轮的应力修正系数:2.0000尺寸系数:小齿轮=1.0000;大齿轮=1.0000许用弯曲疲劳应力:小齿轮=650.0000N/mm2;大齿轮=660.0000N/mm2轮齿弯曲疲劳强度的安全系数:小齿轮=1.2272;大齿轮=1.6237----------------------------齿根弯曲最大计算应力:小齿轮=733.6968N/mm2;大齿轮=685.9498N/mm2轮齿弯曲静强度的安全系数:小齿轮=2.2148;大齿轮=2.4054********************************************************************************总体评价********************************************************************************-------齿面接触计算(疲劳强度安全系数应该大于等于1.0~1.25,静强度安全系数应该大于等于1。
齿轮变位系数计算公式
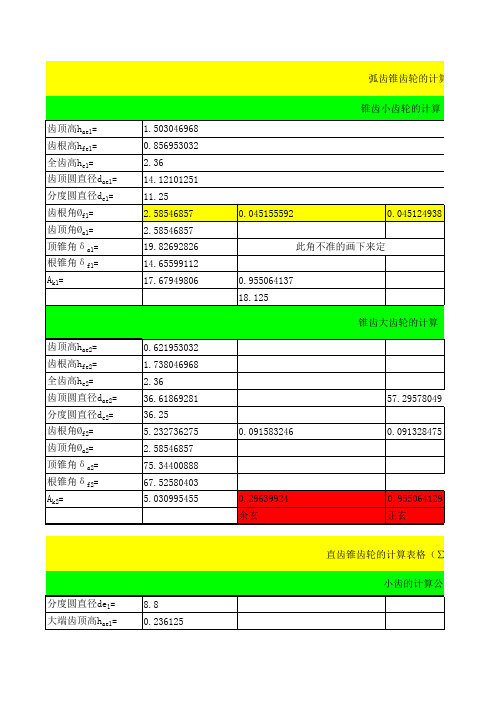
0.76
齿顶圆直径da=
6.129768836
齿根圆直径df=
3.28
基圆直径db=
4.51052458
齿距p=
基圆齿距pb=
齿厚s=
1.431342774
基圆齿厚sb=
1.412247101
齿顶圆压力角αa= 42.62181966
顶圆齿厚sa=
端面重合度εa=
0 14.4
根据传动要求和齿数和由图2-1a
分度圆直径de1= 大端齿顶高hae1=
8.8 0.236125
弧齿锥齿轮的计算表格 锥齿小齿轮的计算(弧齿)
0.045155592
0.045124938
此角不准的画下来定
0.955064137 18.125
锥齿大齿轮的计算(弧齿)
0.091583246
57.29578049 0.091328475
齿顶高hae2= 齿根高hfe2= 全齿高he2= 齿顶圆直径dae2= 分度圆直径de2= 齿根角Øf2= 齿顶角Øa2= 顶锥角δa2= 根锥角δf2= Ak2=
0.621953032 1.738046968 2.36 36.61869281 36.25 5.232736275 2.58546857 75.34400888 67.52580403 5.030995455
0.34906585 弧
变位系数X=
0.3
分度圆直径d=
4.8
标准中心距a=
9.6
总变位系数x∑=
0.35
啮合角α’=
18.36
名义中心距a'=
9.504884418
中心距的变动系数y= -0.118894478
齿顶高变动系数Δy= 0.468894478
(完整版)变位齿轮的计算方法
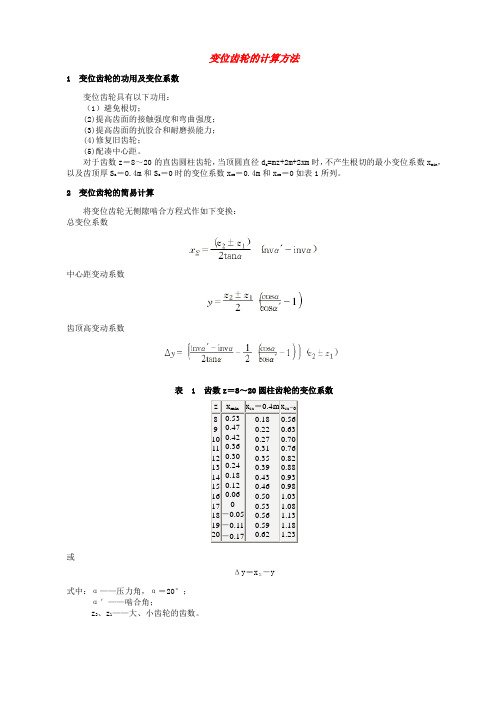
Wk=Wk*m+0.684xm
式中:Wk*——某齿数齿轮跨测k齿时,模数m=1的公法线长度。
表 2 变位齿轮的yz、xz、Δyz和啮合角α′(α=2ห้องสมุดไป่ตู้°)
α′
(分)
19°
20°
21°
yz
xz
Δyz
yz
xz
Δyz
yz
xz
Δyz
0
1
2
3
4
5
6
7
8
9
-0.00616
606
596
0.00107
118
129
139
150
161
172
183
194
205
0.00001
001
001
001
001
001
001
001
002
002
0.00768
779
790
802
813
825
836
847
859
870
0.00789
801
814
825
837
850
862
874
886
898
0.00022
023
023
024
236
246
257
268
279
290
301
312
0.00216
227
238
249
260
271
282
293
304
315
0.00002
002
002
003
003
齿轮变位系数

变位系数名称由来标准齿轮传动存在着一些局限性:(1)受根切限制,齿数不得少于Zmin,使传动结构不够紧凑;(2)不适合于安装中心距a'不等于标准中心距a的场合。
当a'<a时无法安装,当a'>a时,虽然可以安装,但会产生过大的侧隙而引起冲击振动,影响传动的平稳性;(3)一对标准齿轮传动时,小齿轮的齿根厚度小而啮合次数又较多,故小齿轮的强度较低,齿根部分磨损也较严重,因此小齿轮容易损坏,同时也限制了大齿轮的承载能力。
齿轮传动示意图为了改善齿轮传动的性能,出现了变位齿轮。
如图所示,当齿条插刀齿顶线超过极限啮合点N1,切出来的齿轮发生根切。
若将齿条插刀远离轮心O1一段距离(xm),齿顶线不再超过极限点N1,则切出来的齿轮不会发生根切,但此时齿条的分度线与齿轮的分度圆不再相切。
这种改变刀具与齿坯相对位置后切制出来的齿轮称为变位齿轮,刀具移动的距离xm称为变位量,x称为变位系数。
刀具远离轮心的变位称为正变位,此时x>0;刀具移近轮心的变位称为负变位,此时x<0。
标准齿轮就是变位系数x=0的齿轮。
概念齿轮的变位系数变位系数 x 是径向变位系数,加工标准齿轮时,齿条形刀具中线与齿轮分度圆相切。
加工变位齿轮时齿条形刀具中线与齿轮分度圆相切位置偏移距离 xm,外移 x 为正,内移 x 为负。
除了圆锥齿轮有时采用切向变位 xt 外,圆柱齿轮一般只采用径向变位。
变位系数 x 的选择不仅仅是为了凑中心距,而主要是为了提高强度和改善传动质量。
主要功用(1)减小齿轮传动的结构尺寸,减轻重量在传动比一定的条件下,可使小齿轮齿数 zl< zmin,从而使传动的结构尺寸减小,减轻机构重量。
(2)避免根切,提高齿根的弯曲强度当小齿轮齿数 z1<zmin 时,可以利用正变位避免根切,提高齿根的弯曲强度。
x≥xmin=(Z-Zmin)/Zmin,对α=20°时,Zmin=17。
齿轮变位系数公式

齿轮变位系数公式
齿轮是机械传动中常用的元件,齿轮传动的稳定性和可靠性是机械传动的关键之一。
在齿轮传动中,齿轮的变位系数是一个重要的参数,它可以反映齿轮传动的稳定性和可靠性等性能指标。
齿轮变位系数是指齿轮轴线之间的垂直距离与模数的比值,通常用符号ε表示。
齿轮变位系数的计算公式如下:
ε = (y1 + y2) / (2m)
其中,y1和y2分别表示相邻两个齿轮齿数之差的绝对值,m为模数。
该公式适用于所有齿轮传动类型,包括直齿轮、斜齿轮、圆弧齿轮等。
齿轮变位系数的计算可以通过手算和计算机辅助设计软件进行。
在手算时,需要准确测量齿轮的齿数和模数,并应用齿轮变位系数公式进行计算。
在计算机辅助设计软件中,可以直接输入齿轮参数,软件会自动计算齿轮变位系数。
齿轮变位系数的大小对齿轮传动的稳定性和可靠性有着重要的影响。
当齿轮变位系数太大时,齿轮传动会出现过载、振动等问题,影响传动系统的性能;当齿轮变位系数太小时,齿轮传动会出现接触不良、噪声等问题,同样会影响传动系统的性能。
因此,在齿轮设计
和选择时,需要合理地选取齿轮变位系数,以保证传动系统的稳定性和可靠性。
齿轮变位系数是齿轮传动中一个重要的性能指标,它的大小对传动系统的稳定性和可靠性有着重要的影响。
齿轮变位系数的计算公式简单易用,可以帮助工程师准确地计算齿轮的变位系数,从而保证传动系统的性能。
齿轮的变位系数

齿轮的变位系数变位系数x是径向变位系数,加工标准齿轮时,齿条形刀具中线与齿轮分度圆相切。
加工变位齿轮时齿条形刀具中线与齿轮分度圆相切位置偏移距离xm,外移x为正,内移x为负。
除了圆锥齿轮有时采用切向变位xt外,圆柱齿轮一般只采用径向变位。
变位系数x的选择不仅仅是为了凑中心距,而主要是为了提高强度和改善传动质量。
变位齿轮的主要功用如下:(1)减小齿轮传动的结构尺寸,减轻重量 在传动比一定的条件下,可使小齿轮齿数zl<zmin,从而使传动的结构尺寸减小,减轻机构重量。
(2)避免根切,提高齿根的弯曲强度 当小齿轮齿数z1<zmin时,可以利用正变位避免根切,提高齿根的弯曲强度。
x≥xmin=(Z-Zmin)/Zmin,对α=20o时,Zmin=17。
(3)提高齿面的接触强度 采用啮合角α’>α的正传动时,由于齿廓曲率半径增大,故可以提高齿面的接触强度。
(4)提高齿面的抗胶合耐磨损能力 采用啮合角α’>α的正传动,并适当分配变位系数xl、x2,使两齿轮的最大滑动率相等时,既可降低齿面接触应力,又可降低齿面间的滑动率以提高齿轮的抗胶合和耐磨损能力。
(5)配凑中心距 当齿数z1、z2不变的情况下,啮合角α’不同,可以得到不同的中心距,以达到配凑中心距的目的。
(6)修复被磨损的旧齿轮 齿轮传动中,小齿轮磨损较重,大齿轮磨损较轻,可以利用负变位把大齿轮齿面磨损部分切去再使用,重配一个正变位小齿轮,这就节约了修配时需要的材料与加工费用。
选择变位系数的基本原则(1)润滑条件良好的闭式齿轮传动 当齿轮表面的硬度不高时(HBS<350),即对于齿面未经渗碳、渗氮、表面淬火等硬化处理的齿轮,齿面疲劳点蚀或剥伤为其主要的失效形式,这时应选择尽可能大的总变位系数x,即尽量增大啮合角,以便增大啮合节点处齿廓的综合曲率半径,减少接触应力,提高接触强度与疲劳寿命。
当轮齿表面硬度较高时(HBS>350),常因齿根疲劳裂纹的扩展造成轮齿折断而使传动失效,这时,选择变位系数应使齿轮的齿根弯曲强度尽量增大,并尽量使相啮合的两齿轮具有相近的弯曲强度。
齿轮变位系数计算公式
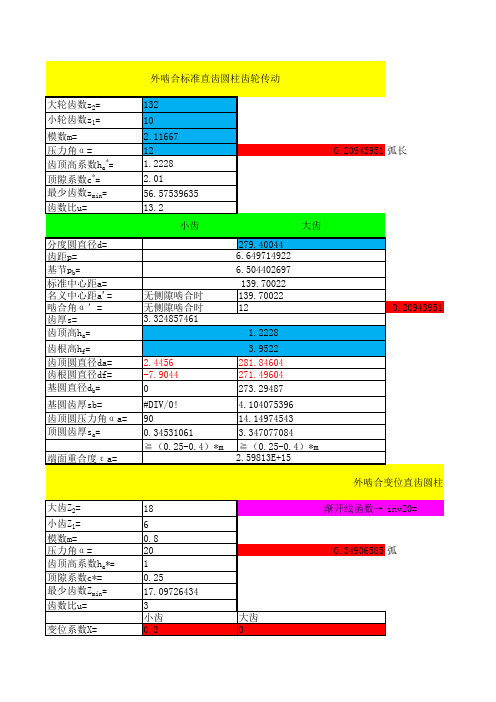
5.440588203
57.29578049 0.94200004 0.808736084
径向变位系数 x2=
0.4096875
分锥角δ2= 36.02737246
0.6288
弧
总
注:是弧度
变位系数X=
18
6 0.8 20 1 0.25 17.09726434 3 小齿 0.3
大齿 0
渐开线函数→ inv20= 0.34906585 弧
分度圆直径d=
4.8
标准中心距a=
9.6
总变位系数x∑=
0.35
啮合角α’=
18.36
名义中心距a'=
9.504884418
中心距的变动系数y= -0.118894478 齿顶高变动系数Δy= 0.468894478
10
0
0
啮合角α’= 名义中心距a'=
插齿刀的参数
切齿啮合角α0'= 切齿标准中心距ao= 切齿名义中心距ao'=
齿根圆直径df=
齿顶圆直径da= 基圆直径db= 齿距p= 基圆齿距pb= 齿厚s= 基圆齿厚sb= 齿顶圆压力角αa= 顶圆齿厚sa= 端面重合度εa=
19.32
齿数zo= 变位系数xo= 顶圆直径dao= 16.53 35 34.45290091 6.405801828 7.5000000 8.495894626 9.396926208
1.503046968 0.856953032 2.36 14.12101251 11.25 2.58546857 2.58546857 19.82692826 14.65599112 17.67949806
齿顶高hae2= 齿根高hfe2= 全齿高he2= 齿顶圆直径dae2= 分度圆直径de2= 齿根角Øf2= 齿顶角Øa2= 顶锥角δa2= 根锥角δf2= Ak2=
变位系数

变位系数变位系数,是用于减小齿轮传动的结构尺寸。
限制条件保证加工时不根切等选择原则润滑条件良好的闭式齿轮传动等主要功用减小齿轮传动的结构尺寸等目录1. 1 名称由来2. 2 概念3. 3 主要功用4. 4 选择原则5. 5 限制条件变位系数名称由来标准齿轮传动存在着一些局限性:(1)受根切限制,齿数不得少于Zmin,使传动结构不够紧凑;(2)不适合于安装中心距a'不等于标准中心距a的场合。
当a'<a时无法安装,当a'>a时,虽然可以安装,但会产生过大的侧隙而引起冲击振动,影响传动的平稳性;(3)一对标准齿轮传动时,小齿轮的齿根厚度小而啮合次数又较多,故小齿轮的强度较低,齿根部分磨损也较严重,因此小齿轮容易损坏,同时也限制了大齿轮的承载能力。
齿轮传动示意图为了改善齿轮传动的性能,出现了变位齿轮。
如图所示,当齿条插刀齿顶线超过极限啮合点N1,切出来的齿轮发生根切。
若将齿条插刀远离轮心O1一段距离(xm),齿顶线不再超过极限点N1,则切出来的齿轮不会发生根切,但此时齿条的分度线与齿轮的分度圆不再相切。
这种改变刀具与齿坯相对位置后切制出来的齿轮称为变位齿轮,刀具移动的距离xm称为变位量,x称为变位系数。
刀具远离轮心的变位称为正变位,此时x>0;刀具移近轮心的变位称为负变位,此时x<0。
标准齿轮就是变位系数x=0的齿轮。
变位系数概念齿轮的变位系数变位系数x 是径向变位系数,加工标准齿轮时,齿条形刀具中线与齿轮分度圆相切。
加工变位齿轮时齿条形刀具中线与齿轮分度圆相切位置偏移距离xm,外移x 为正,内移x 为负。
除了圆锥齿轮有时采用切向变位xt 外,圆柱齿轮一般只采用径向变位。
变位系数x 的选择不仅仅是为了凑中心距,而主要是为了提高强度和改善传动质量。
变位系数主要功用(1)减小齿轮传动的结构尺寸,减轻重量在传动比一定的条件下,可使小齿轮齿数zl< zmin,从而使传动的结构尺寸减小,减轻机构重量。
齿轮变位系数计算公式
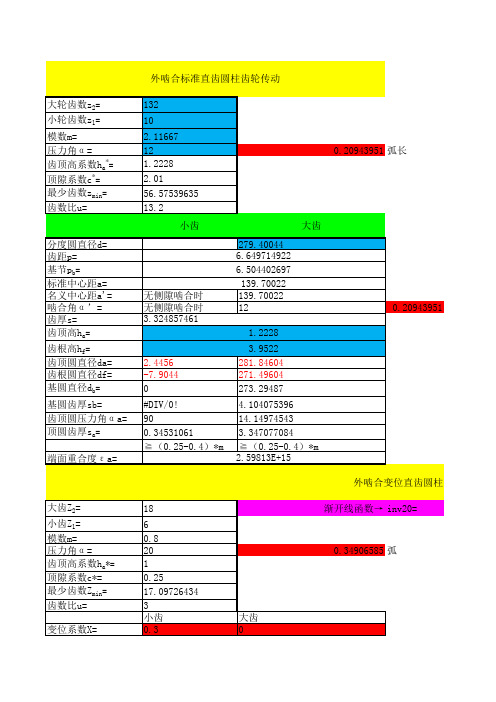
1.743355127
1.622393438
27.87834641
0.295868875
直齿外齿轮
公法线长度
公法线长度的计算 Wk=
标准齿轮 9.70116265
直齿外齿轮 斜齿外齿轮
跨测齿数 公法线长度 跨测齿厚
k= Wkn= k=
5.055555556
直齿外齿轮
公法线长度 跨测齿数
齿顶高hae1= 齿根高hfe1= 全齿高he1= 齿顶圆直径dae1= 分度圆直径de1= 齿根角Øf1= 齿顶角Øa1= 顶锥角δa1= 根锥角δf1= Ak1=
14.212488
齿根圆直径df=
11.14560191
基圆直径db=
12.5630209
法向齿距pn=
端面齿距pt=
5.199545947
法向基圆齿距pbn=
端面基圆齿距pbt=
基圆螺旋角βb=
21.46902352
法向齿厚sn=
2.35619449
端面齿厚st=
2.599772973
端面基圆齿厚sbt= 2.474242055
0.003117051
0.019 要查出,我没查,用时一定要
0.01
查
弧长
αa1
αa2
1.570796327 0.246959646
位直齿圆柱齿轮传动 0.014904
给定x∑求a' 0.320442451
αa1 0.743891086
αa2 0.479274389
inv20= invαa1= invαa2=
变位系数X=
18
6 0.8 20 1 0.25 17.09726434 3 小齿 0.3
变位系数

变位系数变位系数x是径向变位系数,加工标准齿轮时,齿条形刀具中线与齿轮分度圆相切。
加工变位齿轮时齿条形刀具中线与齿轮分度圆相切位置偏移距离xm,外移x为正,内移x为负。
除了圆锥齿轮有时采用切向变位xt外,圆柱齿轮一般只采用径向变位。
变位系数x的选择不仅仅是为了凑中心距,而主要是为了提高强度和改善传动质量。
变位齿轮的主要功用如下:(1)减小齿轮传动的结构尺寸,减轻重量在传动比一定的条件下,可使小齿轮齿数zl<zmin,从而使传动的结构尺寸减小,减轻机构重量。
(2)避免根切,提高齿根的弯曲强度当小齿轮齿数z1<zmin时,可以利用正变位避免根切,提高齿根的弯曲强度。
x≥xmin=(Z-Zmin)/Zmin,对α=20o时,Zmin=17。
(3)提高齿面的接触强度采用啮合角α’>α的正传动时,由于齿廓曲率半径增大,故可以提高齿面的接触强度。
(4)提高齿面的抗胶合耐磨损能力采用啮合角α’>α的正传动,并适当分配变位系数xl、x2,使两齿轮的最大滑动率相等时,既可降低齿面接触应力,又可降低齿面间的滑动率以提高齿轮的抗胶合和耐磨损能力。
(5)配凑中心距当齿数z1、z2不变的情况下,啮合角α’不同,可以得到不同的中心距,以达到配凑中心距的目的。
(6)修复被磨损的旧齿轮齿轮传动中,小齿轮磨损较重,大齿轮磨损较轻,可以利用负变位把大齿轮齿面磨损部分切去再使用,重配一个正变位小齿轮,这就节约了修配时需要的材料与加工费用。
选择变位系数的基本原则(1)润滑条件良好的闭式齿轮传动当齿轮表面的硬度不高时(HBS<350),即对于齿面未经渗碳、渗氮、表面淬火等硬化处理的齿轮,齿面疲劳点蚀或剥伤为其主要的失效形式,这时应选择尽可能大的总变位系数x,即尽量增大啮合角,以便增大啮合节点处齿廓的综合曲率半径,减少接触应力,提高接触强度与疲劳寿命。
当轮齿表面硬度较高时(HBS>350),常因齿根疲劳裂纹的扩展造成轮齿折断而使传动失效,这时,选择变位系数应使齿轮的齿根弯曲强度尽量增大,并尽量使相啮合的两齿轮具有相近的弯曲强度。
齿轮变位系数选择

变位系数x是径向变位系数,加工标准齿轮时,齿条形刀具中线与齿轮分度圆相切。
加工变位齿轮时齿条形刀具中线与齿轮分度圆相切位置偏移距离xm,外移x为正,内移x为负。
除了圆锥齿轮有时采用切向变位xt外,圆柱齿轮一般只采用径向变位。
变位系数x的选择不仅仅是为了凑中心距,而主要是为了提高强度和改善传动质量。
变位齿轮的主要功用如下:(1)减小齿轮传动的结构尺寸,减轻重量在传动比一定的条件下,可使小齿轮齿数zl<zmin,从而使传动的结构尺寸减小,减轻机构重量。
(2)避免根切,提高齿根的弯曲强度当小齿轮齿数z1<zmin时,可以利用正变位避免根切,提高齿根的弯曲强度。
x≥xmin=(Z-Zmin)/Zmin,对α=20o时,Zmin=17。
(3)提高齿面的接触强度采用啮合角α’>α的正传动时,由于齿廓曲率半径增大,故可以提高齿面的接触强度。
(4)提高齿面的抗胶合耐磨损能力采用啮合角α’>α的正传动,并适当分配变位系数xl、x2,使两齿轮的最大滑动率相等时,既可降低齿面接触应力,又可降低齿面间的滑动率以提高齿轮的抗胶合和耐磨损能力。
(5)配凑中心距当齿数z1、z2不变的情况下,啮合角α’不同,可以得到不同的中心距,以达到配凑中心距的目的。
(6)修复被磨损的旧齿轮齿轮传动中,小齿轮磨损较重,大齿轮磨损较轻,可以利用负变位把大齿轮齿面磨损部分切去再使用,重配一个正变位小齿轮,这就节约了修配时需要的材料与加工费用。
选择变位系数的基本原则(1)润滑条件良好的闭式齿轮传动当齿轮表面的硬度不高时(HBS <350),即对于齿面未经渗碳、渗氮、表面淬火等硬化处理的齿轮,齿面疲劳点蚀或剥伤为其主要的失效形式,这时应选择尽可能大的总变位系数x,即尽量增大啮合角,以便增大啮合节点处齿廓的综合曲率半径,减少接触应力,提高接触强度与疲劳寿命。
当轮齿表面硬度较高时(HBS>350),常因齿根疲劳裂纹的扩展造成轮齿折断而使传动失效,这时,选择变位系数应使齿轮的齿根弯曲强度尽量增大,并尽量使相啮合的两齿轮具有相近的弯曲强度。
直齿锥齿轮变位系数
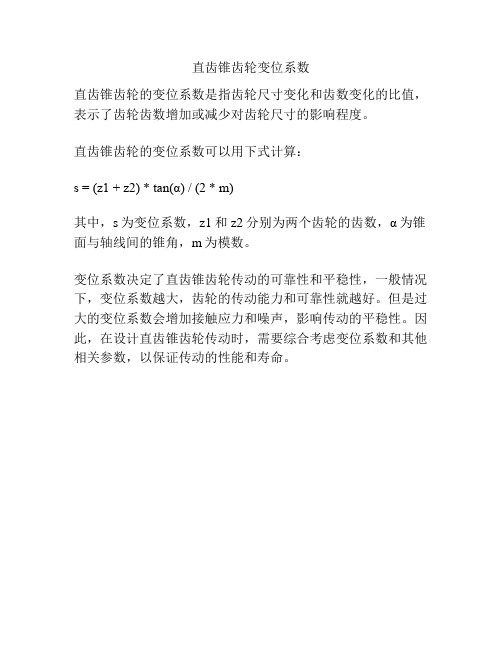
直齿锥齿轮变位系数
直齿锥齿轮的变位系数是指齿轮尺寸变化和齿数变化的比值,表示了齿轮齿数增加或减少对齿轮尺寸的影响程度。
直齿锥齿轮的变位系数可以用下式计算:
s = (z1 + z2) * tan(α) / (2 * m)
其中,s为变位系数,z1和z2分别为两个齿轮的齿数,α为锥面与轴线间的锥角,m为模数。
变位系数决定了直齿锥齿轮传动的可靠性和平稳性,一般情况下,变位系数越大,齿轮的传动能力和可靠性就越好。
但是过大的变位系数会增加接触应力和噪声,影响传动的平稳性。
因此,在设计直齿锥齿轮传动时,需要综合考虑变位系数和其他相关参数,以保证传动的性能和寿命。
变位齿轮的计算方法

变位齿轮的计算方法1 变位齿轮的功用及变位系数变位齿轮具有以下功用:(1)避免根切;(2)提高齿面的接触强度和弯曲强度;(3)提高齿面的抗胶合和耐磨损能力;(4)修复旧齿轮;(5)配凑中心距。
对于齿数z=8~20的直齿圆柱齿轮,当顶圆直径d a=mz+2m+2xm时,不产生根切的最小变位系数x min,以及齿顶厚S a=0。
4m和S a=0时的变位系数x sa=0.4m和x sa=0如表1所列。
2 变位齿轮的简易计算将变位齿轮无侧隙啮合方程式作如下变换:总变位系数中心距变动系数齿顶高变动系数表 1 齿数z=8~20圆柱齿轮的变位系数z x min x sa=0.4m x sa=08 910111213141516171819 200。
53 0.47 0。
42 0.36 0。
30 0.24 0.18 0。
12 0.06 0-0。
05 -0.11 -0。
170.180.220。
270.310.350。
390。
430.460.500。
530.560.590。
620.560.630。
700。
760.820。
880。
930.981。
031。
081.131。
181.23或Δy=xΣ-y式中:α-—压力角,α=20°;α′--啮合角;z2、z1——大、小齿轮的齿数。
将上述三式分别除以,则得:由上述公式可以看出,当齿形角α一定时,x z、y z和Δy z均只为啮合角α′的函数。
在设计计算时,只要已知x z、y z、Δy z和α′四个参数中的任一参数,即可由变位齿轮的x z、y z、Δy z和啮合角α′的数值表(表2)中,查出其他三个参数,再进行下列计算。
一般齿轮手册上均列有此数值表。
式中正号用于外啮合,负号用于内啮合。
3 计算实例例1:已知一对外啮合变位直齿轮,齿数z1=18,z2=32,压力角α=20°,啮合角α′=22°18′,试确定总变位系数xΣ、中心距变动系数y及齿顶高变动系数Δy。
齿轮变位系数

齿轮变位系数、侧隙选择
z1=10z2=60m=0.35
安装中心距12.3
材料为pa66
那么变位系数选择
侧隙的控制方法
侧隙根据经验选取
如果中心距为12.3
那么需要0.145的总变位系数
建议你小齿轮采用0.2变位
大齿轮采用-0.055变位
此时小齿轮齿顶稍有变尖
但可以满足0.1齿顶园角(线切割单变偏置)
1>按照常规,总变位0.145027。
按DIN 3992合理分配小齿x1≈0.28 x2 = 0.145027-x1= -0.134473 .
选择较大侧隙,例如GB2363-90 的 d , 也可以按照材料特性自己定义。
2>不需要拉大中心距。
3>小齿轮虽然存在一些根切,对啮合没有太大影响。
进啮点处0.0059 没有渐开线。
齿厚按照-0.03 考虑,用0.15 线丝切割模具型腔,还可以走丝不干涉。
4>PA66 按照 1.35% 考虑收缩,也可以按实际修改。
【本文来源】皇家小铺(/)【原文地址】/post/20090412434.html。
- 1、下载文档前请自行甄别文档内容的完整性,平台不提供额外的编辑、内容补充、找答案等附加服务。
- 2、"仅部分预览"的文档,不可在线预览部分如存在完整性等问题,可反馈申请退款(可完整预览的文档不适用该条件!)。
- 3、如文档侵犯您的权益,请联系客服反馈,我们会尽快为您处理(人工客服工作时间:9:00-18:30)。
齿轮变位系数
标准齿轮传动存在着一些局限性:(1)受根切限制,齿数不得少于Zmin,使传动结构不够紧凑;(2)不适合于安装中心距a'不等于标准中心距a的场合。
当a' <A时无法安装,当
A'>a时,虽然可以安装,但会产生过大的侧隙而引起冲击振动,影响传动的平稳性;(3)一对标准齿轮传动时,小齿轮的齿根厚度小而啮合次数又较多,故小齿轮的强度较低,齿
根部分磨损也较严重,因此小齿轮容易损坏,同时也限制了大齿轮的承载能力。
为了改善齿轮传动的性能,出现了变位齿轮。
如图所示,当齿条插刀齿顶线超过极限啮合点N1,切出来的齿轮发生根切。
若将齿条插刀远离轮心O1一段距离(xm),齿顶线不再超过极限点N1,则切出来的齿轮不会发生根切,但此时齿条的分度线与齿轮的分度圆不
再相切。
这种改变刀具与齿坯相对位置后切制出来的齿轮称为变位齿轮,刀具移动的距离xm称为变位量,x称为变位系数。
刀具远离轮心的变位称为正变位,此时x>0;刀具移近
轮心的变位称为负变位,此时x<0。
标准齿轮就是变位系数x=0的齿轮。
齿轮的变位系数变位系数x 是径向变位系数,加工标准齿轮时,齿条形刀具中线与齿轮
分度圆相切。
加工变位齿轮时齿条形刀具中线与齿轮分度圆相切位置偏移距离xm,外移
x 为正,内移x 为负。
除了圆锥齿轮有时采用切向变位xt 外,圆柱齿轮一般只采用径
向变位。
变位系数x 的选择不仅仅是为了凑中心距,而主要是为了提高强度和改善传动
质量。
(1)减小齿轮传动的结构尺寸,减轻重量在传动比一定的条件下,可使小齿轮齿数zl< zmin,从而使传动的结构尺寸减小,减轻机构重量。
(2)避免根切,提高齿根的弯曲强度当小齿轮齿数z1 (3)提高齿面的接触强度采用啮合
角α’>α的正传动时,由于齿廓曲率半径增大,故可以提高齿面的接触强度。
(4)
提高齿面的抗胶合耐磨损能力采用啮合角α’>α的正传动,并适当分配变位系数xl、x2,使两齿轮的最大滑动率相等时,既可降低齿面接触应力,又可降低齿面间的滑动率以提高齿轮的抗胶合和耐磨损能力。
(5)配凑中心距当齿数z1、z2 不变的情况下,啮合角α’不同,可以得到不同的中心
距,以达到配凑中心距的目的。
(6)修复被磨损的旧齿轮齿轮传动中,小齿轮磨损较重,大齿轮磨损较轻,可以利用负变
位把大齿轮齿面磨损部分切去再使用,重配一个正变位小齿轮,这就节约了修配时需要
的材料与加工费用。
(1)润滑条件良好的闭式齿轮传动当齿轮表面的硬度不高时(HBS350),常因齿根疲劳裂纹
的扩展造成轮齿折断而使传动失效,这时,选择变位系数应使齿轮的齿根弯曲强度尽量增大,并尽量使相啮合的两齿轮具有相近的弯曲强度。
(2)开式齿轮传动齿面研磨磨损或轮齿折断为其主要的失效形式。
故应选择总变位系数x
∑尽可能大的正变位齿轮,并适当分配变位系数,使两轮齿根处的最大滑动率相等,这样不仅可以减小最大滑动率,提高其耐磨损能力,同时还可以增大齿根厚度,提高轮齿的弯
曲强度。
(3)重载齿轮传动重载齿轮传动的齿面易产生胶合破坏,除了要选择合适的润滑油粘度,
或采用含有添加剂的活性润滑油等措施外,应用变位齿轮时,应尽量增大传动的啮合角(即
增大总变位系数x∑),并适当分配变位系数xl 和x2,以使最大滑动率接近相等,这样
不仅可以增大齿面的综合曲率半径,减小齿面接触应力,还可以减小最大滑动率以提高齿轮的抗胶合能力。
(4)高精度齿轮传动对于精度高于7 级的重载齿轮传动,为了减小节点处齿面上的压力,可以适当选择变位系数,使节点位于两对齿啮合区,以减少每一对啮合轮齿上的载荷,提
高承载能力。
(5)斜齿圆柱齿轮传动斜齿圆柱齿轮传动可以采用高度变位或角度变位,而实际上多采用
标准齿轮传动。
利用角度变位,可以增加齿面的综合曲率半径,有利于提高斜齿轮的接触
强度,但变位系数较大时,又会使啮合轮齿的接触线过分地缩短,反而降低其承载能力。
故采用角度变位,对提高斜齿圆柱齿轮的承载能力的效果并不大。
有时,为了配凑中心距的需要,采用变位齿轮时,可以按其当量齿数zv(=z/cos3β),仍用直齿圆圆柱齿轮选择
变位系数的方法确定其变位系数。
1保证加工时不根切;
2 保证加工时不顶切;
3 保证必要的齿顶厚;
4 保证必要的重合度
5 保证啮合时不干涉;通常采用角度变位,大、小齿轮都用正变位,按等滑动比的原则选取。