第2章 液压机的本体结构及设计计算分解
液压机

主要焊接结构件的设计1、液压机的本体液压机的本体分为铸造结构、焊接结构以及铸焊混合结构。
近代由于焊接技术的进步,液压机本体采用焊接结构的已很普遍,焊接结构对单件小批量生产的企业非常合适。
焊接结构的优点是:制造工艺灵活、方便、结构重量轻、外形美观、制造成本低,铸造结构有其自身的特点,对某些使用工艺是很合适的,因此目前焊接结构还是不能完全代替铸造结构的。
液压机的主要焊接结构件是指上横梁(CROWN)、滑块(SLIDE)、底座(BED)、立柱(UPRIGHT)、移动工作台(MOVING BOLSTER)等。
这些焊接构件的结构设计不应是铸造结构模式的简单变化,不同用途,公称力大小不同,外形尺寸不同的液压机的焊接构件也不能简单地采用一种结构模式,整体焊接框架不能简单地按组合框架的模式简单的变形。
但任何一个具体的结构设计必须按实际的情况考虑问题,所以下面介绍的原则必须结合具体的设计创造性的灵活运用。
焊接结构设计的另一个重要问题是焊接接头的设计。
焊接构件中,甚么部位采用全焊透接头,甚么部位采用不焊透接头,甚么接头开坡口,甚么接头不开坡口,坡口应该是甚么型式和大小等。
因此研究液压机结构件的设计对提高设计水平、设计质量、降低成本是很有意义的。
本资料的目的是研究这些问题,提出一些设计原则或总结一些经验,用来指导设计。
2、关于焊接接头焊接接头必须保证连接部位的强度,接头的形式及大小必须适应当代焊接技术并满足施焊的要求。
现代工艺一般都采用气保焊,焊接接头与接头部位的受力状况,与板厚有关。
接头的设计应该是在满足受力的前提下尽量简单,尽量的小。
这样才能减少变形,降低成本。
理论上对T型接头的研究证明,三分之一钝边的坡口的焊接接头即和被焊板等强度,下面提出的C方式接头就是根据这个理论并参照日本小松株式会社压力机溶接基准制订的。
对接焊缝及要求受力处则要求采用下面提出的D方式接头。
一般联系筋板采用A方式接头的不开坡口的角焊缝。
焊接接头及其坡口型式见表一。
液压机设计

1 绪论1.1 液压机原理液压机是一种利用液体压力能来传递能量,以实现各种压力加工工艺的机器。
液压机是一种可用于加工金属、塑料、木材、皮革、、橡胶等各种材料的压力加工机械,能完成断崖、冲压、折边、冷挤、校直、弯曲、成形、打包等多种工艺,具有压力和速度可大范围无级调整、可在任意位置输出全部功率和保持所需压力等优点,因而用途十分广泛。
液压机根据帕斯卡原理制成,其工作原理如图1所示。
两个充满工作液体的具有柱寒或活塞的容腔由管道相连接,当小柱塞1上的作用力为F 1时,液体的压力为11F p A =,A 1为柱塞1的工作面积。
根据帕斯卡原理:在密闭的容器中,液体压力在各个方向上是相等的,则压力p 将传递到容腔的每一点,因此,在大柱塞2上特产生向上的作用力F 2,迫使工件3变形,且2211A F F A = 式中:A 2——大柱塞2的工作面积。
图1-1液压机工作原理 1--小柱塞 2--大柱塞 3--工件液压机的机构形式很多,其中以四柱立式液压机最为常见。
液压机一般由本体(主机)及液压系统两部分组成。
最常见的液压机本体结构简图如图2所示。
它由上横梁1、下横梁3、四个立柱2和十六个内外螺母组成一个封闭框架,框架承受全部工作裁荷。
工作缸9固定在上横梁1上,工作缸内接有工作柱塞8,它与活动横粱7相连接。
活动横梁以四鞘立柱为导向,在上、下横哭之间接复运动。
在活动横梁的下表面上,一般固定有上模(上砧),而下模(下砧)则固定于下横粱上的工作台上。
当高压液体进人工作缸后,在工作柱塞上产生很大的压力,并推动柱塞、活动横梁及上模向下运动,使工件5在上、下模之间产生塑性变形。
回程缸4固定在下横梁上,其中有回程柱塞6,它与活动横梁相连接。
回程时,工作缸通低压,高压液体进入回程缸,推动回程柱塞6向上运动,带动活动攒粱回到原始位置,完成一个工作循环。
图1-2液压缸本体图1—上横梁 2—立柱 3—下横梁 4—回程缸5—工件 6—回程柱塞 7活动横梁 8—工作柱塞 9—工作缸1.2液压机的特点液压机与其他锻压设备相比具有以下特点:(1)基于液压传动的原理,执行元件(缸及柱塞或活塞)结构简单,结构上易于实现很大的工作压力、较大的工作空间和较长的工作行程,因此适应性强,便于压制大型工件或较长较高的工件。
800MN多向模锻液压机本体结构设计及分析

beam up—beam,lower
and horizontal beam by the丘nitc element soRware
ANSYS.It analysed their rationality.
By the contact method,the dissertation analysed the prestressed unitized
1.2多向模锻工艺简述
模锻生产在提高锻件的精度,节约金属材料,减少机械加工等方面具 有重要的作用,随着我国工业飞跃的前进,模锻已在工业生产中得到广泛 的应用。模锻的成形实质是将金属毛坯加热到锻造温度使其具有良好的塑 性,然后置于锻模的模腔内,在模锻设备的压力作用下,使其产生不可逆 的塑性变形而充满模腔,于是获得所需形状锻件的一种压力加工方法。
With this understanding,the dissertation designed the unitized construction of up—beam,lower beam and horizontal beam.
The dissertation analysed the key part three-dimensioned mode of unitary
论文基于液压机设计理论,参考已有大型模锻液压机结构和设计经验, 通过可行性分析,确定了800MN多向模锻液压机的结构与技术参数,给出 了压机的本体结构设计方案,在此基础上,论文分别给出了压机关键部件 包括上、下横梁及水平梁的分块组合结构设计。
论文以大型有限元软件ANSYS作为分析工具,对800 MN多向模锻液 压机的关键部件包括上、下横粱及水平梁的整体结构进行了三维计算,对 其结构设计的合理性进行了分析。
大型模锻液压机主要用于生产大型铝、镁合金以及钛和钛合金的模锻 件。过去,飞机的大梁是用铆接方式组合,大梁的重量重,铆钉孔容易产 生应力集中。采用大型压机整体模锻大粱,可以减轻重量,减少了接头, 消除应力集中。另外,采用自由锻件和轧材为毛坯进行机械加工时,由于 金属纤维被切断,机械强度被严重削弱,而模锻件的纤维方向与零件的轮 廓形状相符合,因此零件的强度高,使用寿命长。同时,还可以节约贵重 的高强度合金,减少零件机械加工与装配的工作量,用自由锻件或轧材制 造零件时金属利用率非常低,而用模锻件时金属利用率最高可达90%。
液压机的压力计算方法及公式
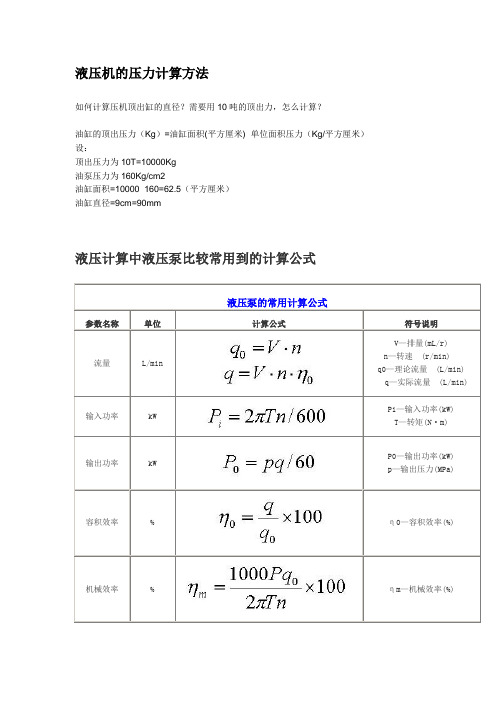
液压机的压力计算方法如何计算压机顶出缸的直径?需要用10吨的顶出力,怎么计算?油缸的顶出压力(Kg)=油缸面积(平方厘米)×单位面积压力(Kg/平方厘米)设:顶出压力为10T=10000Kg油泵压力为160Kg/cm2油缸面积=10000÷160=62.5(平方厘米)油缸直径=9cm=90mm液压计算中液压泵比较常用到的计算公式液压泵的常用计算公式参数名称单位计算公式符号说明流量L/minV—排量(mL/r) n—转速(r/min)q0—理论流量(L/min) q—实际流量(L/min)输入功率kW Pi—输入功率(kW) T—转矩(N·m)输出功率kW P0—输出功率(kW) p—输出压力(MPa)容积效率% η0—容积效率(%) 机械效率% ηm—机械效率(%)总效率% η—总效率(%)油缸压力计算公式油缸工作时候的压力是由负载决定的,物理学力的压力等于力除以作用面积(即P=F/S)如果要计算油缸的输出力,可按一下公式计算:设活塞(也就是缸筒)的半径为R (单位mm)活塞杆的半径为r (单位mm)工作时的压力位P (单位MPa)则油缸的推力F推=3.14*R*R*P (单位N) 油缸的拉力F拉=3.14*(R*R-r*r)*P (单位N)液压常用计算公式项目公式符号意义液壓缸面積(cm2) A =πD2/4 D:液壓缸有效活塞直徑 (cm)液壓缸速度 (m/min) V = Q / A Q:流量 (l / min)液壓缸需要的流量(l/min) Q=V×A/10=A×S/10t V:速度 (m/min)S:液壓缸行程 (m)t:時間(min)液壓缸出力(kgf) F = p × AF = (p × A)-(p×A)(有背壓存在時)p:壓力(kgf /cm2)泵或馬達流量(l/min) Q = q × n / 1000 q:泵或马达的幾何排量(cc/rev)n:转速(rpm)泵或馬達轉速(rpm) n = Q / q ×1000 Q:流量 (l / min)泵或馬達扭矩(N.m) T = q × p / 20π液壓泵所需功率 (kw) P = Q × p / 612管內流速(m/s) v = Q ×21.22 / d2 d:管內徑(mm)管內壓力降(kgf/cm2) △P=0.000698×USLQ/d4 U:油的黏度(cst)S:油的比重L:管的長度(m)Q:流量(l/min)d:管的內徑(cm)液压油缸行程所需时间计算公式⑴、当活塞杆伸出时,时间为(15×3.14×缸径的平方×油缸行程)÷流量当活塞杆缩回时,时间为[15×3.14×(缸径的平方-杆径的平方)×油缸行程]÷流量缸径单位为:m 杆径单位为:m 行程单位为:m 流量单位为:L/min⑵、活塞杆伸出:T=10^3*π*D^2/(4*Q) 活塞杆收回:T=10^3*π*(D^2-d^2)/(4*Q) 其中:T:所需时间π:3.14D:缸筒内径 d:杆劲Q:系统流量例题:油缸直径是220毫米,行程4300毫米,电动机功率22千瓦,液压泵用多大排量?油缸循环时间长短?(以下仅做参考)液压泵的选择:1)确定液压泵的最大工作压力pppp≥p1+∑△p (21)式中 p1——液压缸或液压马达最大工作压力;∑△p——从液压泵出口到液压缸或液压马达入口之间总的管路损失。
液压机油缸设计计算公式
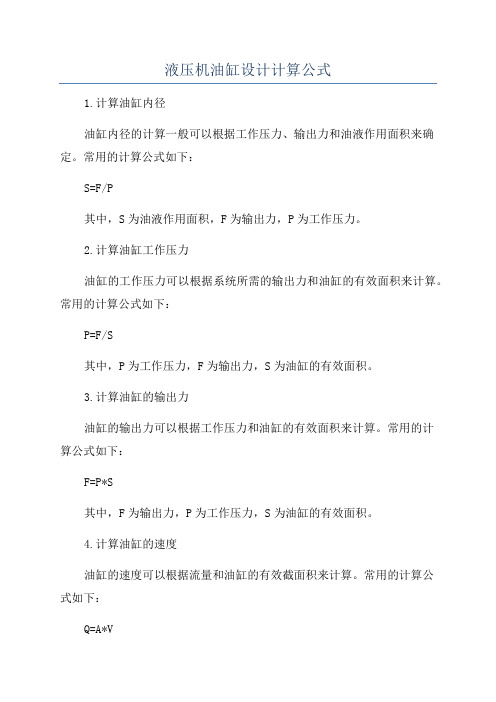
液压机油缸设计计算公式
1.计算油缸内径
油缸内径的计算一般可以根据工作压力、输出力和油液作用面积来确定。
常用的计算公式如下:
S=F/P
其中,S为油液作用面积,F为输出力,P为工作压力。
2.计算油缸工作压力
油缸的工作压力可以根据系统所需的输出力和油缸的有效面积来计算。
常用的计算公式如下:
P=F/S
其中,P为工作压力,F为输出力,S为油缸的有效面积。
3.计算油缸的输出力
油缸的输出力可以根据工作压力和油缸的有效面积来计算。
常用的计
算公式如下:
F=P*S
其中,F为输出力,P为工作压力,S为油缸的有效面积。
4.计算油缸的速度
油缸的速度可以根据流量和油缸的有效截面积来计算。
常用的计算公
式如下:
Q=A*V
其中,Q为流量,A为油缸的有效截面积,V为油缸的速度。
除了以上的计算公式外,液压机油缸的设计还需要考虑油缸的结构形式、工作环境、密封性能、轴向稳定性等因素,这些因素会直接影响油缸的性能和使用寿命。
因此,设计液压机油缸时需要综合考虑以上因素,并根据具体的应用要求进行合理的选择和优化。
综上所述,液压机油缸设计计算公式是制定液压机油缸尺寸和参数的重要依据,通过合理的计算和选择,可以确保液压机油缸的性能和使用寿命,从而实现液压系统的稳定运行和高效工作。
液压系统的设计与计算
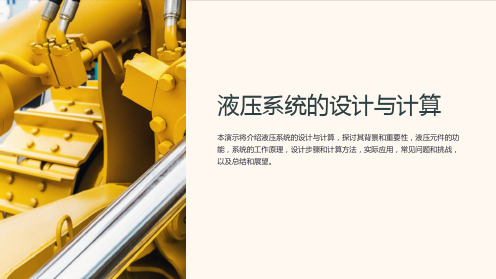
本演示将介绍液压系统的设计与计算,探讨其背景和重要性,液压元件的功 能,系统的工作原理,设计步骤和计算方法,实际应用,常见问题和挑战, 以及总结和展望。
背景和重要性
了解液压系统设计和计算的背景和重要性,探索在现代机械工程中的广泛应用和对工业自动化的 重要贡献。
1 工业领域
广泛应用于工厂设备、建筑机械等领域,提升工作效率和减少人力需求。
根据系统的流量需求和力的 要求计算液压泵和缸的流量 和压力。
元件配合和选取
根据系统要求和元件性能选 择合适的液压元件,确保系 统的可靠性和效率。
设计案例和实际应用
通过设计案例和实际应用探讨液压系统在不同领域中的广泛应用和创新。
土木工程
工业自动化
汽车维修
液压挖掘机在土木工程中的应用, 提高施工效率和减轻劳动强度。
液压系统在工厂自动化中的应用, 提高生产线的效率和自动化程度。
液压汽车升降机的应用,方便维 修和保养汽车,提高工作效率。
液压系统设计中的常见问题和挑战
描述液压系统设计过程中可能遇到的常见问题和挑战,以及如何解决和克服这些问题。
1 泄漏问题
泄漏是液压系统常见的问 题,需要通过合适的密封 和维护解决。
液压阀
控制液压系统中液压流体的流 动和压力。
液压系统的基本原理和工作过程
探讨液压系统的基本原理和工作过程,包括压力传递和转换,液体流动和控制的关键原则。
1
压力传递
通过液压系统,在系统中传递和增加压
液体流动
2
体的流动,从液压泵出发
到执行器,使得机械元件能够工作。
3
2 运输和航空
在飞机、汽车和船舶等交通工具中的重要作用,提供高效和可靠的动力传输。
液压机设计的计算资料
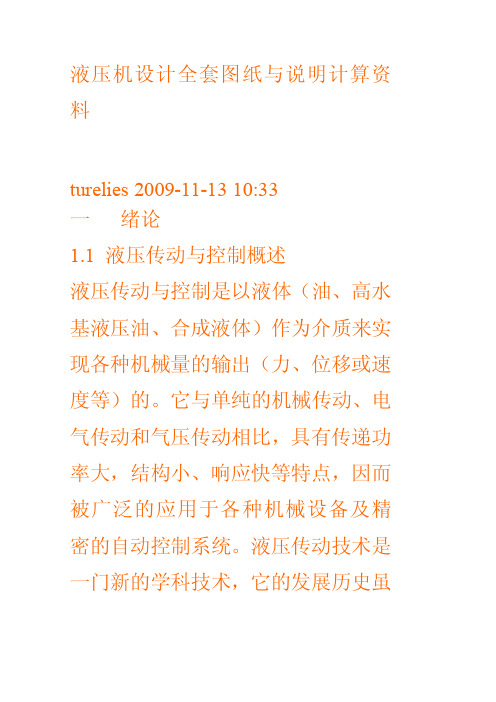
上液压缸工作循环 (1) 快速下行。按下起动按钮, 电磁铁 1YA 通电,这时的油路为:
液压缸上腔的供油的油路 变量泵 1—换向阀 6 右位—节流阀
8—压力继电器 11—液压缸 15 液压缸下腔的回油路 液压缸下腔 15—液控单向阀 7—换向 阀 6 右位—电磁阀 5—背压阀 4—油 箱 油路分析:变量泵 1 的液压油经过换 向阀 6 的右位,液压油分两条油路: 一条油路通过节流阀 7 流经继电器 11,另一条路直接流向液压缸的上腔 和压力表。使液压缸的上腔加压。液 压缸 15 下腔通过液控单向阀 7 经过 换向阀 6 的右位流经背压阀,再流到 油箱。因为这是背压阀产生的背压使 接副油箱旁边的液控单向阀 7 打开, 使副油箱 13 的液压油经过副油箱旁
在国防工业中:海、陆、空各种战备
武器均采用液压传动与控制。如飞 机、坦克、舰艇、雷达、火炮、导弹 及火箭等。 在民用工业中:有机床工业、冶金工 业、工程机械、农业方面,汽车工业、 轻纺工业、船舶工业。 另外,近几年又出现了太阳跟踪系 统、海浪模拟装置、飞机驾驶模拟、 船舶驾驶模拟器、地震再现、火箭助 飞发射装置、宇航环境模拟、高层建 筑防震系统及紧急刹车装置等,均采 用了液压技术。 总之,一切工程领域,凡是有机械设 备的场合,均可采用液压技术。它的 发展如此之快,应用如此之广,其原
液压机设计全套图纸与说明计算资 料
turelies 2009-11-13 10:33 一 绪论 1.1 液压传动与控制概述 液压传动与控制是以液体(油、高水 基液压油、合成液体)作为介质来实 现各种机械量的输出(力、位移或速 度等)的。它与单纯的机械传动、电 气传动和气压传动相比,具有传递功 率大,结构小、响应快等特点,因而 被广泛的应用于各种机械设备及精 密的自动控制系统。液压传动技术是 一门新的学科技术,它的发展历史虽
液压机主要焊接结构件的设计
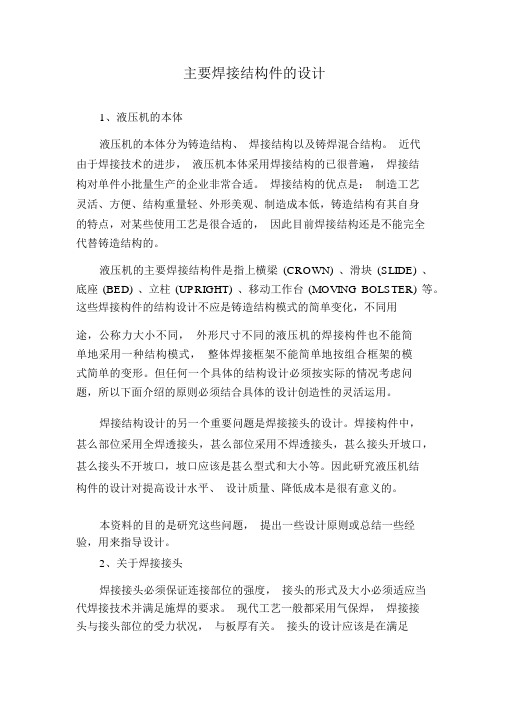
主要焊接结构件的设计1、液压机的本体液压机的本体分为铸造结构、焊接结构以及铸焊混合结构。
近代由于焊接技术的进步,液压机本体采用焊接结构的已很普遍,焊接结构对单件小批量生产的企业非常合适。
焊接结构的优点是:制造工艺灵活、方便、结构重量轻、外形美观、制造成本低,铸造结构有其自身的特点,对某些使用工艺是很合适的,因此目前焊接结构还是不能完全代替铸造结构的。
液压机的主要焊接结构件是指上横梁(CROWN) 、滑块(SLIDE) 、底座(BED) 、立柱(UPRIGHT) 、移动工作台(MOVING BOLSTER) 等。
这些焊接构件的结构设计不应是铸造结构模式的简单变化,不同用途,公称力大小不同,外形尺寸不同的液压机的焊接构件也不能简单地采用一种结构模式,整体焊接框架不能简单地按组合框架的模式简单的变形。
但任何一个具体的结构设计必须按实际的情况考虑问题,所以下面介绍的原则必须结合具体的设计创造性的灵活运用。
焊接结构设计的另一个重要问题是焊接接头的设计。
焊接构件中,甚么部位采用全焊透接头,甚么部位采用不焊透接头,甚么接头开坡口,甚么接头不开坡口,坡口应该是甚么型式和大小等。
因此研究液压机结构件的设计对提高设计水平、设计质量、降低成本是很有意义的。
本资料的目的是研究这些问题,提出一些设计原则或总结一些经验,用来指导设计。
2、关于焊接接头焊接接头必须保证连接部位的强度,接头的形式及大小必须适应当代焊接技术并满足施焊的要求。
现代工艺一般都采用气保焊,焊接接头与接头部位的受力状况,与板厚有关。
接头的设计应该是在满足受力的前提下尽量简单,尽量的小。
这样才能减少变形,降低成本。
理论上对 T 型接头的研究证明,三分之一钝边的坡口的焊接接头即和被焊板等强度,下面提出的 C 方式接头就是根据这个理论并参照日本小松株式会社压力机溶接基准制订的。
对接焊缝及要求受力处则要求采用下面提出的 D 方式接头。
一般联系筋板采用 A 方式接头的不开坡口的角焊缝。
液压机的设计与分析

液压机的设计与分析摘要:随着我国制造业的快速发展,大型精密液压机的需求也随之快速增长,这也对生产设备精度、自动化程度和生产效率提出更高的技术要求。
本文通过对液压机系统的工作原理、液压机运转的设计思路、液压机的整体控制方案设计三方面进行分析,阐述了液压控制系统的变频器的设计、液压机工程分析、应用程序开发过程中的关键技术。
关键词:液压机设计分析工程1液压系统的工作原理液压机的工作原理是由上、下滑块顶出机构的运动,上滑块机构由主液压缸也就是上缸来驱动,顶出机构由辅助液压缸也就是下缸驱动。
液压机上滑块通过四个导柱导向和主缸驱动,实现上滑块机构的驱动,详细驱动如下所示。
上缸的快速下行→上缸的慢速下行→上缸的慢速加压→上缸的预卸→上缸的慢速回程→上缸的快速回程→停止。
下缸一般布置在工作台的中间孔内,用来驱动下滑快的顶出机构,详细驱动XXX如下。
下缸的向上顶出→下缸的向下退回。
2液压机运转的设计思路使用液压机前必须要仔细阅读分析液压机的使用手册。
在滑块的运行过程中,绝对不允许身体的任何部位进入危险区内,尽可能地防止人身伤害事故的发生。
液压机使用的电器元件都是有使用寿命的,如果达到了使用寿命,就必须要更换元件,以此来确保作业的安全。
非技术人员绝对不允许打开控制箱,以防止发生危险事故。
不能随便将电气箱门打开。
在对电气箱箱门进行开启时,首先要把箱门上的电源开关关掉,并让手柄和延伸杆脱开,然后才可以打开门锁。
滑块的封闭高度彻底调整完成以后,必须要把滑块调整开关关掉,这时机床才可以正常地进行冲压。
液压机床操作完成后,必须要看管好操作的按钮开关。
3液压机的整体控制方案设计一般的液压机首要是用于小型机械零件冲压和定形的。
生产线把材料送入用液压机冲压成型,并颠末输料线输出。
本液压机为可编程控制器控制。
由凸轮控制器发出液压机运转所需角度。
液压机的结构和功能描述如下。
300t的液压机一般使用刚性转键式离合器,如许能够在使用和维修时比较方便。
工程液压机方案设计

工程液压机方案设计一、前言液压机作为一种广泛应用于工程领域的设备,其在各种领域都具有重要的作用。
液压机以其高效、稳定的特性,被广泛应用于金属加工、压制成形、塑料模塑、压铸、挤压等领域。
本文将从设计液压机的整体结构、工作原理、控制系统及其他重要部件进行详细阐述。
通过本文的阐述,读者可以对液压机的设计原理有更加深刻的认识。
二、液压机的整体结构1.液压机的基本结构液压机主要由上横梁、下工作台、活塞缸、导向柱、液压系统、电气控制系统等部分组成。
其中,上横梁和下工作台被用于夹紧和固定被压制的工件,活塞缸用于提供压力,并且通过活塞的上下运动来实现对工件的压制。
导向柱起到引导和固定活塞缸的作用。
液压系统则提供液压力,控制系统用于实现对液压机的各种操作。
2.结构设计要点液压机的结构设计应该保证其具有足够的刚性和稳定性。
在设计上,应该采用一体式或者桥式结构,以提高整机的稳定性。
此外,为了适应不同的工艺要求,一些液压机还应具有一定的可调节性,使其具有更广泛的适用性和多功能性。
三、液压机的工作原理1.液压传动的工作原理液压机的工作原理是利用液体在封闭容器中的传递压力来实现工件的压制。
液压系统一般由液压泵、控制阀、油缸、液压缸等部分组成。
当液压泵启动时,液体将被泵送至液压缸内,从而产生一定的压力。
然后,通过控制阀的调节和控制,液压缸内的压力可以被传递到被压制的工件上,从而实现对工件的加工。
2.液压机的工作过程液压机的工作过程一般包括充液、压制、返回三个阶段。
首先,液压泵启动,将液体泵入液压缸内,使之充满液体;其次,通过控制阀的操作,使活塞缸的活塞开始向下运动,形成一定的压力,对工件进行压制;最后,当需要停止压制时,操作控制系统,使液压缸内的液体回流到油箱,活塞缸返回原位,从而完成一次压制过程。
四、液压机的控制系统1.液压机的控制方案液压机的控制系统一般由电气控制系统和液压控制系统组成,其中液压控制系统用于控制液体的流动和压力的变化,电气控制系统则用于控制各种执行元件和控制器的动作。
煤矿用液压挖掘机结构组成及计算
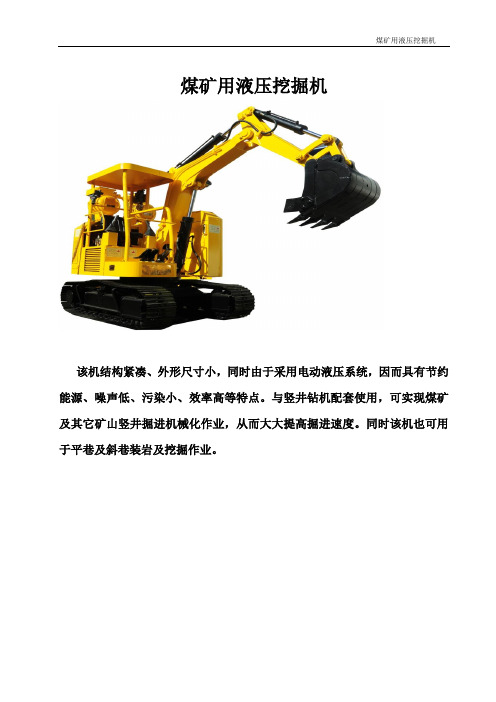
煤矿用液压挖掘机该机结构紧凑、外形尺寸小,同时由于采用电动液压系统,因而具有节约能源、噪声低、污染小、效率高等特点。
与竖井钻机配套使用,可实现煤矿及其它矿山竖井掘进机械化作业,从而大大提高掘进速度。
同时该机也可用于平巷及斜巷装岩及挖掘作业。
结构组成由1工作装置总成、2推土铲、3回转平台、4液压系统、5底盘总成、6机罩、7顶棚、8电气系统等组成。
性能特点:1、外形尺寸小,结构紧凑,效率高。
2、底盘为焊接结构、整体性好,刚性和强度大。
3、行走驱动装置有两条履带,用于履带链轮驱动的行走减速机是带内置液压马达极紧凑的传动部件,每条履带单独用液压马达作动力,通过减速机驱动使车辆行驶。
行走减速机采用国际流行的内藏式行走减速机,最高行走速度为2.4公里/小时,4、采用电动液压系统,具有噪声低、无尾气污染的特点,同时电气系统用防爆元件,更适用于井下(尤其是煤矿)使用。
1 总体参数计算1.1 功率计算1.1.1电动机原始参数电动机功率:37kW1.1.2液压泵参数液压主泵型号: PVK-2B-505-N-4191A主泵排量: 50ml /rev主泵最大流量: 110 l/min主泵起调压力: 12Mpa主泵输入功率: kW (W=110*12/(60*0.97)=22.7)主泵输入扭矩: N •m (Pq=159×12×50×0.001=95.4)伺服系统压力: 3.9 Mpa1.1.3功率储备系数、扭矩储备系数功率储备系数:K1= (29.4-22.7-2.5)/29.4 =14.3%扭矩储备系统:K2= (144-95.4)/144 = 50%通过以上计算功率储备系数、扭矩储备系统均大于10%,发动机能够稳定地工作。
1.2 回转速度、回转力矩计算1.2.1回转机构原始数据:回转马达型号: PCL-200-18B-1S2-8486A回转马达排量: 33.8ml/rev回转马达最大供油量: 39l/min回转减速机速比: i1 18.4输出轴齿数/模数: 14/7回转系统压力: 21Mpa回转齿圈齿数: 86终传动速比: i2 86/14=6.1431.2.2回转速度计算:回转马达转速(容积效率设定为0.96):n1= 39/33.8×1000×0.94= 1085rpm回转速度: n=211i i n =1085/(18.4×6.143) =9.6rpm1.2.3回转力矩计算:马达输出转矩(机械效率设定为0.85):Nm i p v M g 7.176714.3204.1885.02108.33201=⨯⨯⨯⨯=∆=πη 回转力矩Nm Mi M h 10859143.67.17672=⨯==1.3 行走性能计算1.3.1基本参数整机质量 G=4800kg履带内阻力 W=0.06G=2880N驱动轮节圆直径 Dk=0.4158m驱动轮齿数 Z=19轨链节距 t0=135mm履带轮距 L=1940mm履带轨距 A=1560mm履带高度(不包括凸缘) h=536mm履带板宽 B=400mm行走减速机速比 i =47.53行走马达减速机型号: PHV-4B-60BP-1S-8502A马达最大供油量: 50l/min行走马达排量(q max /q min ) 28.6/17.4 ml/rev1.3.2驱动力矩、行走牵引力计算液压系统压力 P=24.5MPa马达机构效率 ηm1=95%马达容积效率 ηv=98%行走机构机械效率ηm2=85%马达低速时输出扭矩 Mmmax=159⨯P ⨯qmax ⨯ηm1=159⨯24.5⨯28.6⨯0.001⨯95%=105.84N.m马达高速时输出扭矩 Mmmin=159⨯P ⨯qmin ⨯ηm2=159⨯24.5⨯17.4⨯0.001⨯95%=64.39N.m行走机构低速时输出扭矩 Mgmax= Mmmax ⨯i ⨯ηm2=105.84⨯47.53⨯85%=4276N.m行走机构高速时输出扭矩 Mgmin= Mmmin ⨯i ⨯ηm2=64.39⨯47.53⨯85%=2601.4N.m低速时行走牵引力 Tmax= 2⨯Mgmax/(Dk/2)=2⨯4276/(0.4158/2)=41135.2N实际低速时行走牵引力Tmaxa=Tmax - W=41135.2-2880N=38255.2N高速时行走牵引力Tmin= 2⨯Mgmin/(Dk/2)=2⨯2941/(0.4158/2)=25073.6N实际高速时行走牵引力Tmina=Tmin - W=25073.6-2880=22193.6N1.3.3爬坡能力计算设爬坡能力为:60%爬坡角度:α= arctan(60%) = 31°坡度阻力:W1 = Gsinα= 4800×9.8×sin(31°)= 24227.4N滚动阻力系数: f = 0.12滚动阻力W2= Gfcosα=4800×9.8×0.12×cos(31°)=4838.5N爬坡阻力W坡=W1+W2= 24227.4+4838.5=29065N因为最大牵引力Tmaxa=38255.2> W坡所以有60%的爬坡能力,由于受发动机油底壳的限制,本机爬坡能力为30°。
液压系统设计及计算

液压系统设计及计算液压系统设计及计算是指对液压系统进行整体设计和性能计算的过程。
液压系统设计包括液压系统的结构设计、元件选型、管道布置等方面,液压系统计算主要涉及液压系统的流量、压力、功率等参数的计算。
下面将分别介绍液压系统的设计和计算。
1.确定液压系统的功能要求,包括工作行程、工作压力、工作速度、工作负载等参数。
2.根据系统功能要求,选择适当的液压元件,如液压泵、液压马达、液压阀等。
3.根据系统的工作压力和流量要求,计算确定液压泵和液压马达的工作参数,包括流量、压力、速度、功率等参数。
4.根据系统的动力源情况,选择适当的液压泵和液压马达。
5.根据系统的工作压力和工作负载,计算确定液压阀的流量和压力损失。
6.设计液压系统的管道布置,包括管道的截面积、长度、弯头数目等参数。
7.设计液压系统的油箱、过滤器、冷却器等辅助元件。
液压系统计算的基本原理如下:1.流量计算:根据系统的工作行程和工作速度,计算液压系统的流量需求。
流量计算公式为Q=V/t,其中Q为体积流量,V为液压缸的有效工作体积,t为工作行程所需时间。
2.压力计算:根据系统的工作负载和元件的压力损失,计算液压系统的工作压力。
压力计算公式为P=F/A,其中P为压力,F为工作负载,A为液压缸的有效工作面积。
3.功率计算:根据系统的流量和压力,计算液压系统的功率需求。
功率计算公式为P=W/t,其中P为功率,W为工作所需的能量,t为工作所需时间。
4.效率计算:根据液压系统的损失和输出功率,计算液压系统的效率。
效率计算公式为η=(P输出/P输入)×100%,其中η为效率,P输出为输出功率,P输入为输入功率。
总之,液压系统设计和计算是液压技术中非常重要的一部分,通过合理的设计和准确的计算,可以保证液压系统的性能和可靠性。
对于液压系统的设计和计算,需要具备一定的液压原理和工程经验,并且不断学习和更新液压技术,提高设计和计算的水平。
四柱液压机设计说明书
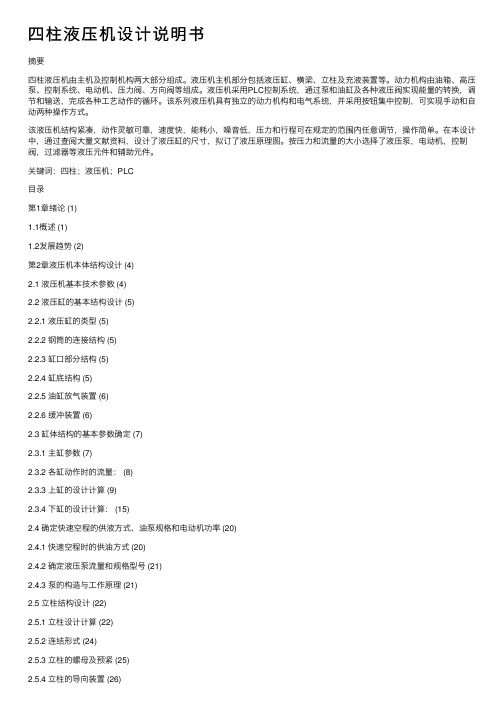
四柱液压机设计说明书摘要四柱液压机由主机及控制机构两⼤部分组成。
液压机主机部分包括液压缸、横梁、⽴柱及充液装置等。
动⼒机构由油箱、⾼压泵、控制系统、电动机、压⼒阀、⽅向阀等组成。
液压机采⽤PLC控制系统,通过泵和油缸及各种液压阀实现能量的转换,调节和输送,完成各种⼯艺动作的循环。
该系列液压机具有独⽴的动⼒机构和电⽓系统,并采⽤按钮集中控制,可实现⼿动和⾃动两种操作⽅式。
该液压机结构紧凑,动作灵敏可靠,速度快,能耗⼩,噪⾳低,压⼒和⾏程可在规定的范围内任意调节,操作简单。
在本设计中,通过查阅⼤量⽂献资料,设计了液压缸的尺⼨,拟订了液压原理图。
按压⼒和流量的⼤⼩选择了液压泵,电动机,控制阀,过滤器等液压元件和辅助元件。
关键词:四柱;液压机;PLC⽬录第1章绪论 (1)1.1概述 (1)1.2发展趋势 (2)第2章液压机本体结构设计 (4)2.1 液压机基本技术参数 (4)2.2 液压缸的基本结构设计 (5)2.2.1 液压缸的类型 (5)2.2.2 钢筒的连接结构 (5)2.2.3 缸⼝部分结构 (5)2.2.4 缸底结构 (5)2.2.5 油缸放⽓装置 (6)2.2.6 缓冲装置 (6)2.3 缸体结构的基本参数确定 (7)2.3.1 主缸参数 (7)2.3.2 各缸动作时的流量: (8)2.3.3 上缸的设计计算 (9)2.3.4 下缸的设计计算: (15)2.4 确定快速空程的供液⽅式、油泵规格和电动机功率 (20)2.4.1 快速空程时的供油⽅式 (20)2.4.2 确定液压泵流量和规格型号 (21)2.4.3 泵的构造与⼯作原理 (21)2.5 ⽴柱结构设计 (22)2.5.1 ⽴柱设计计算 (22)2.5.2 连结形式 (24)2.5.3 ⽴柱的螺母及预紧 (25)2.5.4 ⽴柱的导向装置 (26)2.5.5 限程套 (27)2.5.6 底座 (28)2.6 横梁参数的确定 (28)2.6.1 上横梁结构设计 (28)2.6.2 活动横梁结构设计 (29)2.6.3 下横梁结构设计 (29)2.6.4 各横梁参数的确定 (30)第3章液压系统及元件的设计 (31)3.1 液压系统原理 (31)3.1.1 ⼯作原理 (31)3.1.2 ⼯艺加⼯过程 (32)3.2 管道及管接头 (33)3.2.1 管道 (33)3.3 液压控制阀的选择 (35)3.3.1 先导式溢流阀 (35)3.3.2 节流阀 (35)3.3.3 单向阀 (35)3.3.4 电磁换向阀 (35)3.3.5 顺序阀 (35)3.3.6 背压阀 (36)第4章控制部分 (37)4.1 PLC概述 (37)4.2控制部分设计 (37)总结 (40)参考⽂献 (41)致谢 (42)附录1:英⽂及翻译 (43)附录2:程序梯形图 (51)第1章绪论1.1概述本次设计的题⽬由我实习的公司提供,主要是对铝合⾦材料等的加⼯。
液压机基础与本体结构

标称压力3150kN 一般用途四柱式液压机 第一种变型 液压机
三、 液压机的基本参数
以三梁四柱式液压机为例
标称压力(kN) 最大净空距H(mm) 最大行程h(mm) 立柱中心距L×B(mm×mm) 回程力(kN) 允许最大偏心距e(mm) 活动横梁的运动速度(mm/s) 移动工作台尺寸及行程(mm) 顶出力
1-上横梁,2-上砧,3-回程柱塞, 4立柱,5-移动工作台,6-回程缸 7-固 定梁,8-工作柱塞,9-下横梁 10-工
作缸 11-螺母
下拉式结构的优点:
(1)液压机重心低,稳定性好。 (2)工作缸位于地下,比较安全,且管道不易损坏。 (3)上横梁可设计的较窄,便于操作。 (4)立柱按对角线布置,操作工人有较宽的工作视野,
③ 最大行程h
➢ 活动横梁位于上限位置时,活 动横梁的立柱导套下平面到立 柱限程套上平面的距离,即,活动 横梁能够移动的最大距离. ➢应根据工件成型中所要求的最 大工作行程来确定.
④ 工作台尺寸(长×宽) ➢ 指工作台面上可利用的有效尺寸. ➢ 取决于模具(工具)的平面尺寸及工艺过程的安排.
⑤ 回程力 ➢ 考虑活动部分重量、回程工艺力(如拔模力等)、工作缸排 液阻力、各缸密封处摩擦力、活动横梁导向处摩擦力等. ⑥ 活动横梁运动速度 ➢工作行程速度、空程速度、回程速度 . ➢工作行程速度直接影响工件质量和对泵的功率要求. ⑦ 允许最大偏心距 ➢ 指工件变形阻力接近公称压力时,所能允许的最大偏心值. ⑧ 顶出器公称压力及行程. ➢ 由工艺要求确定.
立柱:是机架的重要支撑件和 主要受力件,又是活动横梁的 导向件,因此对立柱有较高的 强度、刚度和精度要求。
1-充液灌,2-工作缸,3-上横梁, 4-工作柱塞,5-立柱, 6-活动横梁, 7-下横梁
第二章 液压机本体结构设计

2.7本体结构与机架的选择液压机本体一般由机架、液压缸部件、运动部分及其导向装置及其他辅助装置组成。
辅助装置则是根据工艺需要而增设,如顶出装置、穿孔装置、移动工作台加热保温装置等。
工艺要求是影响液压机本体结构形式的最主要因素,由于在不同液压机上完成的工艺是多种多样的,因此液压机本体结构设计时应考虑以下三个基本原则:1尽可能好地满足工艺要求、便于操作。
2具有合理的强度与刚度,使用可靠,不易损坏。
3具有很好的经济性,重量轻,制造维修方便。
综合以上选择C形单柱式机架这种机架的主要特点是结构比较简单,工作区域宽敞,工作时可以从三面接近压机,特别适合于长度或宽度很大的中厚板的矫直、弯曲、成形、弯边等工序,操作方便,小型锻造液压机中也常用C形单柱式机架,单柱式机架的刚性比较差,一般做成空心箱型结构,以提高其抗弯刚度并减轻重量。
单柱机架可以是整体铸钢结构,也可以是钢板焊接结构。
图2.7 C形单柱液压机2.8 机架的力学分析与计算 2.8.1 初步确定上梁尺寸 液压机弯矩简图如图2.8.1 初步确定上梁截面尺寸如图2.8.2 立柱截面尺寸如图2.8.3 因此各截面参数如下:上梁:4z1m 0046.0=I ,21m 0752.0=Amm 3201=H ,mm 320h 1=,立柱:4z2m 0086.0=I ,22m 0906.0=A ,mm 3542=H ,mm 466h 2=,下梁和上梁截面关于立柱中线对称。
2.8.2强度校核 上弯曲应力a 83.430046.0320.063.010h 61z 1MP I M =⨯⨯=⋅=σ上梁剪切应力a 200752.0105.15.161MP A P =⨯==τ支柱弯曲应力()()a 89.360086.0354.0354.0275.0100906.0100.275662z 222MP I H H P A P =⨯+⨯+=⋅+⋅+=σ(受拉) ()()a 15.290086.0466.0466.0275.0100906.0100.275662z 222MP I H H P A P -=⨯+⨯-=⋅+⋅+=σ(受压)图2.8.3立柱截面图2.8.1 弯矩图图2.8.2上梁截面查GB/T 700-1988,得屈服极限为225MPa,安全系数取2,故许用应力[]a 5.112MP =σ,[]a 65MP =τ,上述应力都满足条件。
液压机.

一、典型结构形式概述
从机架形式看,有立式、与卧式。 从机架组成看,有立柱式、单臂式、框架式。 立柱式又可分为四柱、双柱、多柱等。 从工作缸的数量看,有单缸、双缸、多缸。
1、梁柱组合式
传统的结构形式, 最常见的是三梁四 柱式。
2、单臂式
结构简单,操 作方便,机架 刚性差
3、框架式
有整体式和组合式两种
• 四、简单的液压控制系统简介 液压机的工作循环一般包括: 空程向下(充液行程) 工作行程 保压 回程 停止 顶出缸顶出 顶出缸回程等。
回停 工 程止 作
顶停 回 出止 程
• 五、液压机的分类 • 液压机在锻压机械标准ZB—J62030—90中属于 第二类,类别代号为“Y”。液压机按其用途分为十 个组别: • (1)手动液压机(0组) 用于完成压力较小,可手工 操作的简单工作。 • (2)锻造液压机(1组) 用于自由锻造、钢锭开坯以 及有色与黑色金属模锻。 • (3)冲压液压机(2组) 用于各种薄板及厚板冲压, 其中有单动、双动及橡皮模冲压等。 • (4)一般用途液压机(3组) 包括各种万能式通用液 压机。 • (5)校正、压装用液压机(4组) 用于零件校形及装 配。
刚性好、导向精度高、 疲劳能力强、制造成本 高、操作不便
二、机架部件(梁柱组合式)
(一)立柱 1、立柱与横梁的连接形式: 双螺母式:加工、安装与维修方便,螺母易 松动需随时检修以免发生故障 锥台式:双锥台(加工困难、不易维修), 单锥台(不易维修,安装困难) 锥套式:可消除或减轻应力集中,多用于大 型压力机上
二、液压机的选用 选用或选购液压机时,应以该设备上进行的 主要工艺为依据,确保其主要技术参数均 满足工艺要求,结合实际情况来决定。
一般通用液压机具有如下特点: 1)工作台面较大,滑块行程较长,以满足多种工艺 的要求,主工作缸一般采用活塞式,实现压制及 回程。 2)设有浮动的顶出缸,供顶出工件、反向拉深、液 压压边和起液压垫的作用。 3)一般设有充液系统,可实现空程快速运动。 4)设有保压延时系统,具有保压、延时和自动回程 功能,并能进行定压成形和定程成形工作,有利 于金属和非金属粉末的压制。 5)具有点动、手动、半自动等工作方式,操作方便, 工作压力、压制速度及行程范围均可任意调节, 灵活性强。 6)结构简单,便于维修。
- 1、下载文档前请自行甄别文档内容的完整性,平台不提供额外的编辑、内容补充、找答案等附加服务。
- 2、"仅部分预览"的文档,不可在线预览部分如存在完整性等问题,可反馈申请退款(可完整预览的文档不适用该条件!)。
- 3、如文档侵犯您的权益,请联系客服反馈,我们会尽快为您处理(人工客服工作时间:9:00-18:30)。
3.液压机机架结构部件 3.2横梁 • 横梁强度计算。
第2章 液压机的本体结构及设计计算
3.液压机机架 结构部件
3.2横梁 • 横梁强度计
算。
第2章 液压机的本体结构及设计计算
3.液压机机架 结构部件
3.2横梁 • 横梁强度计
算。
第2章 液压机的本体结构及设计计算
第2章 液压机的本体结构及设计计算
3.液压机机架结构部件 • 立柱受偏心载荷强度
计算。
第2章 液压机的本体结构及设计计算
3.液压机机架结构部件 • 立柱导套。
第2章 液压机的本体结构及设计计算
3.液压机机架结构部件 • 立柱螺母。
第2章 液压机的本体结构及设计计算
3.液压机机 架结构部件 3.2横梁 • 横梁的结
确定液压缸的活塞和活塞杆直径,或柱塞杆直径。 由液体压力P和液压缸材料的许用应力计算出液压缸外径。 由液压缸的壁厚计算出液压缸体各参数。
第2章 液压机的本体结构及设计计算
3.液压机机架结构 部件 3.1立柱 • 立柱结构形式。
第2章 液压机的本体结构及设计计算
3.液压机机架结构部件 • 立柱形状尺寸要求。
3.液压机机架 结构部件
3.2横梁 • 横梁刚度
计算。
第2章 液压机的本体结构及设计计算
3.液压机机 架结构部件 3.3工作台 • 工作台
设计。
第2章 液压机的本体结构及设计计算
3.液压机机架结构部件 3.3工作台 • 工作台强度和刚度计
算。
第2章 液压机的本体结构及设计计算
3.液压机机架结构部件 3.5工作台计算。
第2章 液压机的本体结构及设计计算
3.液压机机 架结构部件 3.4滑块计算 • 滑块强度
和刚度计 算。
第2章 液压机的本体结构及设计计算
3.液压机机架 结构部件 • 滑块强度
计算。
第2章 液压机的本体结构及设计计算
3.液压机机架结构部件 • 滑块刚度计算。
第2章 液压机的本体结构及设计计算
3.液压机机架结构部件 3.5工作台垫板计算
总结
材料变形范围:上梁Q235焊接 0.20-0.22 滑块Q235焊接 ≤0.17 下梁Q235焊接 0.17-0.18
许用拉压应力:上梁Q235焊接 60MPa 滑块Q235焊接 60MPa 下梁Q235焊接 60MPa
许用剪切应力:上梁Q235焊接 45MPa 滑块Q235焊接 45MPa 下梁Q235焊接 45MPa
受力分为三部分,即缸底,法兰和中间厚壁圆筒。 油缸体各部分应力许用值: 油缸体中部许用应力为100 -120 MPa; 缸底许用应力为70 -100 MPa;· 油缸法兰处许用应力为70 -100 MPa; 油缸与上梁接触处的环形挤压应力为80-100 MPa(去除倒角)。 液压缸的有限元分析计算
第2章 液压机的本体结构及设计计算
第2章 液压机的本体结构及设计计算
2.液压缸部件 液压缸部件的结构:柱塞式液压缸
第2章 液压机的本体结构及设计计算
2.液压缸部件 • 液压缸部件的结构:活塞式液压缸
第2章 液压机的本体结构及设计计算
2.液压缸部件 液压缸部件的支撑形式: 法兰支撑;缸底支撑。 油缸柱塞与活动横梁的连接:刚性连接。 油缸柱塞与活动横梁的连接:球面连接。 导套及密封;导套标准JB2003-76;密封常用材料:聚
2.液压缸 部件 液压缸部 件的强度 计算:
中间厚壁 圆筒。
第2章 液压机的本体结构及设计计算
2.液压缸 部件 液压缸部 件的强度 计算:
法兰计算。
第2章 液压机的本体结构及设计计算
2.液压 缸部件液 压缸部件 的强度计 算:
缸底计算。
第2章 液压机的本体结构及设计计算
2.液压缸部件 液压缸设计步骤:
第2章 液压机的本体结构及设计计算
3.液压机机架结构部件 3.5工作台垫板计算 • 工作台强度和刚度计算。
第2章 液压机的本体结构及设计计算
3.液压机机架结构部件 3.5工作台垫板计算 • 工作台强度和刚度计算。
第2章 液压机的本体结构及设计计算
3.液压机机架结构部件 3.5工作台垫板计算 • 工作台强度和刚度计算。
第2章 液压机的本体结构及设计计算
• 本章内容
– 液压机的本体结构概述 – 液压缸部件 – 液压机机架结构部件
第2章 液压机的本体结构及设计计算
1.液压机的 本体结构概 述 • 单臂式
第2章 液压机的本体结构及设计计算
1.液压机的 本体结构概 述 • 四柱式
第2章 液压机的本体结构及设计计算
1.液压机的 本体结构概 述 分体框架式 整体框架式
工作台板ZG270-500 0.10-0.1260MPa
胺脂,耐油橡胶,夹布橡胶
第2章 液压机的本体结构及设计计算
2.液压缸部件 液压缸部件的强度计算:液压缸的损坏部位通常是 园筒筒壁;缸的法兰;缸底;气蚀。
第2章 液压机的本体结构及设计计算
2.液压缸部件 • 液压缸部件的强度计算 液压缸的损坏原因:
设计方面;加工制造方面;安装使用方面。 液压缸部件的强度计算: