汽车发动机曲轴加工工艺与夹具设计
发动机曲轴加工工艺及其夹具设计方案
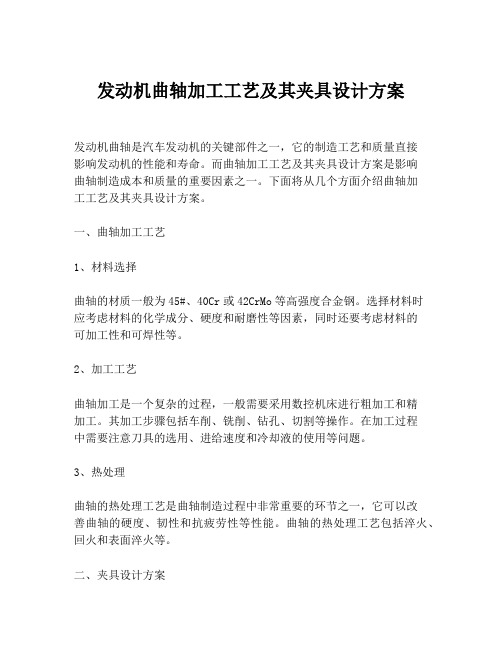
发动机曲轴加工工艺及其夹具设计方案发动机曲轴是汽车发动机的关键部件之一,它的制造工艺和质量直接影响发动机的性能和寿命。
而曲轴加工工艺及其夹具设计方案是影响曲轴制造成本和质量的重要因素之一。
下面将从几个方面介绍曲轴加工工艺及其夹具设计方案。
一、曲轴加工工艺1、材料选择曲轴的材质一般为45#、40Cr或42CrMo等高强度合金钢。
选择材料时应考虑材料的化学成分、硬度和耐磨性等因素,同时还要考虑材料的可加工性和可焊性等。
2、加工工艺曲轴加工是一个复杂的过程,一般需要采用数控机床进行粗加工和精加工。
其加工步骤包括车削、铣削、钻孔、切割等操作。
在加工过程中需要注意刀具的选用、进给速度和冷却液的使用等问题。
3、热处理曲轴的热处理工艺是曲轴制造过程中非常重要的环节之一,它可以改善曲轴的硬度、韧性和抗疲劳性等性能。
曲轴的热处理工艺包括淬火、回火和表面淬火等。
二、夹具设计方案1、定位方式曲轴加工过程中的定位方式一般分为机械、气动和液压三种。
机械定位通常采用精密定位销的方式,气动定位则是利用气压将工件固定在夹具上,液压定位则是利用液压缸的力将工件夹紧。
2、夹紧方式曲轴的夹紧方式也有许多种,常用的夹紧方式包括机械、液压和气动三种。
机械夹紧方式一般使用螺母或螺栓将工件夹住,液压夹紧则是利用液压缸的力将工件夹紧,气动夹紧也是利用气压将工件夹紧。
3、支撑方式曲轴加工过程中的支撑方式也非常重要,它直接影响到曲轴的精度和质量。
常用的支撑方式包括线性支撑和点式支撑两种,其中线性支撑一般采用直线导轨或滑块等,而点式支撑则是采用滚珠或滚子轴承进行支撑。
以上就是关于曲轴加工工艺及其夹具设计方案的介绍,如今曲轴加工技术也在不断提高,寻求更高质量和更高效率的曲轴加工方式,相信未来在这个领域也会有更多的进步。
DA468型发动机曲轴加工工艺与专用机床夹具设计

摘要本设计主要围绕发动机曲轴的工艺规程和专用夹具设计进行研究,其内容包括了解曲轴结构,确定曲轴的生产类型及相关的技术要求。
在此基础上,选择毛坯,确定毛坯的尺寸公差和机械加工余量,绘制毛坯图。
并在认真详细分析零件图后,进行基准的选择,制定了表面加工方法,划分加工阶段,根据生产类型确定工序的集中和分散,合理地安排工序,编排合适的工艺路线;进行详细计算,包括:加工余量、工序尺寸和公差的确定、切削用量的计算及时间定额的计算。
从而制定出一套合理的机械加工工艺卡片和机械加工工序卡片。
第二部分主要围绕专用钻床类夹具进行设计。
首先明确夹具设计的主要任务,通过确定定位元件,导向装置,夹紧机构得出夹具的结构方案,查阅相关国家标准,绘画夹具装配图。
总之,曲轴加工工艺的安排以及专用夹具的设计是一项非常复杂的高难度工作,它是一种需大批量生产的零件,且技术要求比较高,为了确保产品的质量和水平,设计工作按照科学的程序进行,分清主次。
关键词:曲轴;加工工艺;定位;夹紧;钻孔;夹具设计ABSTRACTIn this paper the technological procedure and proprietary drilling fixture design of the engine crankshaft were studied, whose contents included that the use of crankshaft, the production type of crankshaft of and the relevant technical requirements. On this basis, the rough was chosen, and the size of the rough was determined, and the mechanical allowances were determined. A rough map was drawn. After carefully detailed analysis of the parts, the reference was chosen, the development of surface processing methods was determined, and the demarcation of the processing stages was divided. According to the production process the type of centralization and decentralization was determined, the process was reasonably arranged, and the order and orchestrates a suitable process line were set up. Then some detail was calculated, such as allowance, processes size and the determination of tolerance. The amount of calculation and the calculation of the fixed time was cut. Thus a set of reasonable card processing machinery and mechanical processes cards were drawn up.The second part of the design was the focus of this issue which was difficult, who was mainly centered on proprietary drilling fixture design, Z525-use vertical drilling, drilling middle-hole design process by which a drilling fixture. Firstly fixture was designed to clear the major tasks identified by positioning components, guidance devices, clamping body fixture structure, access to the relevant national standards, painting fixture assembly.In short, the processing arrangements of crankshaft and the design of special fixture are a very complex difficult work. It is required in mass production. The technical requirements are relatively high. In order to ensure the quality and level of design the design work was carried out in accordance with the procedures of science, the relation between primary and secondary was distinguished.Keywords: Bent axle;Processing technical;Cutting parameters;FixtureDesign目录摘要 (Ⅰ)Abstract (Ⅱ)第1章绪论 (1)1.1 设计的意义和目的 (1)1.2 研究方向及发展趋势 (2)1.3 设计的主要内容 (3)第2章曲轴毛坯的选择 (5)2.1 分析曲轴零件图 (5)2.1.1 曲轴使用的性能与工作条件 (5)2.1.2 曲轴的结构与技术要求 (6)2.2 曲轴毛坯的选择 (6)2.2.1 选择毛坯 (6)2.2.2 确定机械加工余量、毛坯尺寸和公差 (7)2.3 本章小结 (8)第3章曲轴加工工艺设计 (9)3.1 工艺基准的选择 (9)3.2 加工阶段的划分 (9)3.3 工序的集中与分散 (10)3.4 工序顺序的安排 (10)3.5 确定工艺路线 (11)3.6 加工余量、工序尺寸和公差的确定 (12)3.7确定切削用量及时间定额 (15)3.8 本章小结 (20)第4章钻床夹具的设计 (22)4.1 夹具的概念 (22)4.2 钻斜油孔专用夹具设计 (25)4.2.1 部分基本件的选择 (25)4.2.2 主要零件的选择 (25)4.2.3 工步的制定 (25)4.2.4 钻模夹具应注意的问题 (26)4.2.5钻模夹具的定位及设计原则 (26)4.2.6斜孔钻模夹具的改进思路 (30)4.2.7液压系统的设计 (30)4.3 钻中心孔专用夹具设计 (35)4.3.1 明确设计任务、收集分析原始资料 (35)4.3.2 确定夹具的结构方案 (35)4.3.3 绘制夹具结构简图 (38)4.4 本章小结 (39)结论 (40)参考文献 (41)致谢 (42)附录 (43)第1章绪论1.1设计的意义和目的随着科学技术的迅猛发展和市场需求的变化及竞争加剧,传统的制造技术发展到了一个崭新的阶段;随着我国经济的持续高速发展,人们生活水平不断提高,汽车已经走进了我们的日常生活,渐渐成为一种普通消费品;随着市场对汽车需要量的增加和制造技术的发展,到了本世纪初,小作坊的生产方式已经不能满足需要,而各种新的制造工艺和新式高效机床的出现,使汽车和发动机的制造技术出现了飞跃。
发动机曲轴加工工艺及其夹具设计
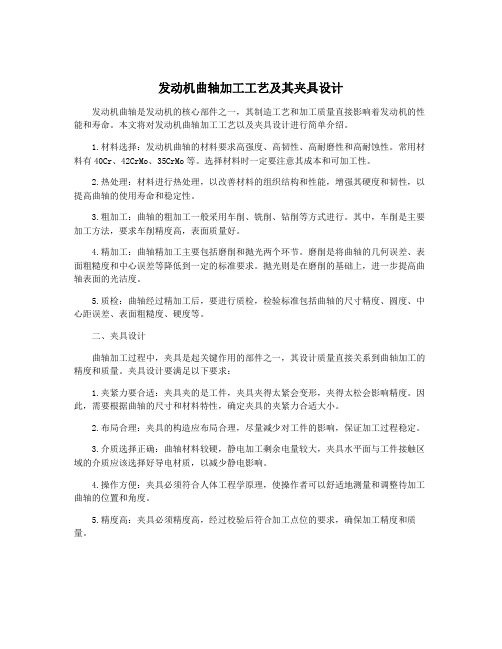
发动机曲轴加工工艺及其夹具设计发动机曲轴是发动机的核心部件之一,其制造工艺和加工质量直接影响着发动机的性能和寿命。
本文将对发动机曲轴加工工艺以及夹具设计进行简单介绍。
1.材料选择:发动机曲轴的材料要求高强度、高韧性、高耐磨性和高耐蚀性。
常用材料有40Cr、42CrMo、35CrMo等。
选择材料时一定要注意其成本和可加工性。
2.热处理:材料进行热处理,以改善材料的组织结构和性能,增强其硬度和韧性,以提高曲轴的使用寿命和稳定性。
3.粗加工:曲轴的粗加工一般采用车削、铣削、钻削等方式进行。
其中,车削是主要加工方法,要求车削精度高,表面质量好。
4.精加工:曲轴精加工主要包括磨削和抛光两个环节。
磨削是将曲轴的几何误差、表面粗糙度和中心误差等降低到一定的标准要求。
抛光则是在磨削的基础上,进一步提高曲轴表面的光洁度。
5.质检:曲轴经过精加工后,要进行质检,检验标准包括曲轴的尺寸精度、圆度、中心距误差、表面粗糙度、硬度等。
二、夹具设计曲轴加工过程中,夹具是起关键作用的部件之一,其设计质量直接关系到曲轴加工的精度和质量。
夹具设计要满足以下要求:1.夹紧力要合适:夹具夹的是工件,夹具夹得太紧会变形,夹得太松会影响精度。
因此,需要根据曲轴的尺寸和材料特性,确定夹具的夹紧力合适大小。
2.布局合理:夹具的构造应布局合理,尽量减少对工件的影响,保证加工过程稳定。
3.介质选择正确:曲轴材料较硬,静电加工剩余电量较大,夹具水平面与工件接触区域的介质应该选择好导电材质,以减少静电影响。
4.操作方便:夹具必须符合人体工程学原理,使操作者可以舒适地测量和调整待加工曲轴的位置和角度。
5.精度高:夹具必须精度高,经过校验后符合加工点位的要求,确保加工精度和质量。
发动机曲轴箱机加工工艺夹具设计毕业论文

发动机曲轴箱机加工工艺夹具设计毕业论
文
引言
本文描述了一种发动机曲轴箱夹具的设计方案,该夹具用于机加工过程中的定位和夹持操作,以保证加工精度和效率。
本文将介绍夹具的设计思路、结构、制造工艺以及使用效果的测试结果。
设计思路
夹具的设计根据曲轴箱的几何形状和加工要求,结合机加工操作的特点和工艺要求,采用了“定位-固定-夹紧”的基本夹持方式。
夹具由基座、定位导向部件、固定和夹紧部件组成。
夹具结构
整个夹具的设计与制造需要考虑以下几个因素:
- 曲轴箱的三维形状和尺寸
- 机加工工艺的需要
- 制造工艺和加工精度要求
为了减少加工难度和提高精度,夹具的制造部件应当采用数控
加工工艺,保证零件的精度。
夹具的结构应当具有可拆卸性,以方
便维修和更换配件。
制造工艺
夹具的制造工艺包括零件制造、零件装配和夹具整体调试。
首先,所有的夹具部件应当通过数控加工设备进行加工和组装。
然后,对所有的装配方式进行调试,并进行加工效果的检测。
使用效果测试
在夹具的制造和调试结束后,我们对夹具的使用效果进行了测试,测试结果显示,该夹具可以很好地满足机加工操作的需要,提
高了加工精度和效率,并具有较好的使用寿命。
总结
本文介绍了一种发动机曲轴箱机加工工艺夹具设计方案,该方案采用定位-固定-夹紧的基本夹持方式,夹具具有结构合理、制造精度高、使用寿命长等特点,并具有显著的使用效果。
发动机曲轴加工工艺及其夹具设计

发动机曲轴加工工艺及其夹具设计发动机曲轴是发动机的核心部件之一,它的加工工艺和夹具设计对于发动机的性能和寿命有着至关重要的影响。
本文将从这两个方面进行探讨。
一、发动机曲轴加工工艺发动机曲轴的加工工艺主要包括以下几个步骤:1. 材料准备:选择合适的材料,如高强度合金钢、铸铁等。
2. 粗加工:采用车床、铣床等机床进行粗加工,将材料切削成初步形状。
3. 热处理:对粗加工后的曲轴进行热处理,以提高其硬度和强度。
4. 精加工:采用磨床等高精度机床进行精加工,将曲轴的各个部位加工到规定的尺寸和形状。
5. 表面处理:对曲轴进行表面处理,如抛光、喷涂等,以提高其表面光洁度和耐腐蚀性。
以上步骤中,精加工是最为关键的一步,它直接影响到曲轴的精度和平衡性。
因此,在精加工过程中,需要采用高精度的机床和刀具,并严格控制加工参数,以确保曲轴的精度和平衡性符合要求。
二、发动机曲轴夹具设计曲轴夹具是曲轴加工过程中不可或缺的工具,它的设计直接影响到曲轴的加工精度和效率。
一般来说,曲轴夹具应具备以下几个特点: 1. 稳定性好:曲轴夹具应能够稳定地夹紧曲轴,避免在加工过程中出现晃动或偏移。
2. 精度高:曲轴夹具应具备高精度的定位和夹紧功能,以确保曲轴的加工精度。
3. 适应性强:曲轴夹具应能够适应不同类型和尺寸的曲轴,以满足不同的加工需求。
4. 操作简便:曲轴夹具应具备简单易用的操作方式,以提高加工效率和安全性。
在曲轴夹具的设计中,需要考虑到曲轴的形状、尺寸和加工要求等因素,以确定夹具的结构和参数。
同时,还需要进行严格的试验和验证,以确保夹具的性能和可靠性。
发动机曲轴的加工工艺和夹具设计是发动机制造中非常重要的环节,需要采用高精度的机床和夹具,并严格控制加工参数和夹具结构,以确保曲轴的精度和平衡性符合要求。
一种曲轴加工工艺及车曲柄颈专用夹具设计

一种曲轴加工工艺及车曲柄颈专用夹具设计牟杰爽张良栋摘要:在加工曲轴曲柄颈时,由于曲轴是偏心件,一般工装夹具难以保证其加工精度和加工质量,因此需要设计一个专门车削加工曲柄颈的工装夹具。
本文主要介绍了一种曲轴加工工艺及车曲柄颈专用夹具设计,供读者参考。
关键词:曲轴;夹具;车削;加工工艺1 曲轴功用曲轴的作用是将活塞的往复运动通过连杆变成其回转运动,因此曲轴不但承受着周期性的弯曲力矩和扭转力矩,同时还受到扭转振动的附加应力的作用。
这样就使曲轴的受力情况非常复杂,所以发动机的曲轴要有高的强度、刚度、耐磨性、耐疲劳性及冲击韧性,曲轴的质量应尽量小,各轴颈应保证充分润滑。
(图1)2 曲轴技术要求4 车曲柄颈专用夹具(图2)5 夹具操作方法如图2所示,夹具安装时,先将4个顶针套用榔头轻轻敲入前后轴套内。
曲轴平放在V形架上,将前后轴套装入前后主轴颈,用拉紧螺栓紧固,防止绕主轴颈转动,然后将周向定位块用螺栓安装,用来周向定位,再将方头平键安装在圆形轴套上。
将夹具安装在车床上时,先将前顶尖装入主轴锥孔内,然后过渡盘与主轴相连接,过渡盘与车床主轴用莫氏锥孔定位,然后用4个螺栓紧固。
夹具体与过渡盘用圆柱面定位,用4个螺栓紧固。
用吊机将曲轴吊到夹具体内,顶上后顶尖,然后用压紧装置将其压紧,平衡块安装在夹具体上,用平衡法找正主轴平衡。
找正位置后,即可开动车床加工。
当加工完一个曲拐时,松开夹紧装置,用吊机将曲轴旋转180度,继续加工下一个曲柄颈。
Reference:[1]徐鴻本.机床夹具设计手册[M].沈阳:辽宁科学技术出版社, 2004,3.[2]张进生.机械制造工艺与夹具设计指导[M].北京:机械工业出版社,1995,9.[3]吴拓.现代机床夹具典型结构实用图册[M].北京:化学工业出版社,2015,10.[4]贵州工学院机械制造工艺教研室.机床夹具结构图册[M].贵州:贵州人民出版社,1983,6.[5]周来宏.曲轴加工工艺及曲轴内铣技术的研究[D].大连:大连交通大学,2008,12.[6]卢秉恒.机械制造技术基础[M].北京:机械工业出版社,2017,10.-全文完-。
曲轴零件的机械加工工艺及夹具设计
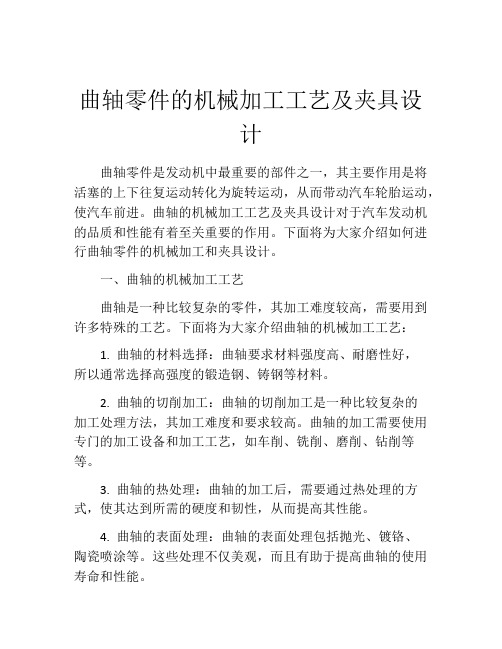
曲轴零件的机械加工工艺及夹具设计曲轴零件是发动机中最重要的部件之一,其主要作用是将活塞的上下往复运动转化为旋转运动,从而带动汽车轮胎运动,使汽车前进。
曲轴的机械加工工艺及夹具设计对于汽车发动机的品质和性能有着至关重要的作用。
下面将为大家介绍如何进行曲轴零件的机械加工和夹具设计。
一、曲轴的机械加工工艺曲轴是一种比较复杂的零件,其加工难度较高,需要用到许多特殊的工艺。
下面将为大家介绍曲轴的机械加工工艺:1. 曲轴的材料选择:曲轴要求材料强度高、耐磨性好,所以通常选择高强度的锻造钢、铸钢等材料。
2. 曲轴的切削加工:曲轴的切削加工是一种比较复杂的加工处理方法,其加工难度和要求较高。
曲轴的加工需要使用专门的加工设备和加工工艺,如车削、铣削、磨削、钻削等等。
3. 曲轴的热处理:曲轴的加工后,需要通过热处理的方式,使其达到所需的硬度和韧性,从而提高其性能。
4. 曲轴的表面处理:曲轴的表面处理包括抛光、镀铬、陶瓷喷涂等。
这些处理不仅美观,而且有助于提高曲轴的使用寿命和性能。
二、曲轴的夹具设计曲轴的夹具是曲轴机械加工的重要工具,它们可以确保曲轴在加工过程中的稳定性和精度。
夹具的设计应该考虑以下几个因素:1. 加工特性:不同的加工方式对夹具的要求不同,应根据加工特性设计夹具。
2. 工件材质:工件的材质对夹具设计产生很大的影响。
应该选择合适的材料和加工工艺,确保夹具的刚性和精度。
3. 加工精度:曲轴是一个高精度零件,夹具设计时应该注意加工精度的要求,保证夹具的精度和稳定性。
4. 生产效率:合理的夹具设计应该能够提高生产效率,降低成本,从而提高企业的竞争力。
总之,曲轴零件的机械加工和夹具设计对于汽车发动机的性能和品质有着至关重要的作用。
只有通过正确的加工工艺和夹具设计,才能制造出质量更高、性能更优的曲轴,满足汽车发动机的需求。
汽车发动机的装配工艺及夹具设计

汽车发动机的装配工艺及夹具设计1. 背景介绍汽车发动机的装配工艺及夹具设计在汽车制造过程中起着重要的作用。
通过合理的装配工艺和夹具设计,能够提高装配效率、降低装配成本、保证装配质量,从而提高汽车整体性能和可靠性。
2. 汽车发动机装配工艺汽车发动机的装配工艺包括以下几个阶段:2.1 零部件准备在装配发动机之前,需要准备好各个零部件,包括发动机缸体、曲轴、活塞、连杆等。
这些零部件需要经过清洗、检查和测试等工序,确保其质量和适配性。
2.2 气缸孔加工在发动机缸体上进行气缸孔的加工是一个关键步骤。
这个工序需要确保每个气缸孔的尺寸和位置达到设计要求,以保证气缸的密封性和工作效率。
2.3 零部件组装在零部件准备和气缸孔加工完成后,可以开始进行零部件组装。
这个过程中需要按照一定的顺序和方法将各个零部件装配到发动机缸体上,包括活塞与连杆的组装、气缸盖的安装等。
2.4 测试和调试零部件组装完成后,需要对发动机进行测试和调试。
通过启动发动机,检查其运行状态和性能,并调整其中的参数,以保证发动机的正常工作和优良性能。
3. 夹具设计夹具设计是为了更好地实施发动机装配工艺而进行的。
夹具的设计需要考虑以下几个方面:3.1 夹持力夹具的设计需要保证对零部件的夹持力,以确保装配过程中的稳定性和安全性。
夹具应该能够牢固地固定住零部件,避免其移动或脱落。
3.2 适配性夹具的设计应考虑到不同类型和规格的零部件,以保证对各种零部件的适配性。
夹具应该能够灵活地适应不同大小、形状和重量的零部件。
3.3 操作便捷性夹具的设计应尽量简化操作,提高装配过程的效率。
夹具应具有良好的人机工程学设计,使操作人员能够轻松地使用和调整夹具。
4. 总结汽车发动机装配工艺及夹具设计是汽车制造过程中的重要环节。
合理的装配工艺和夹具设计能够提高装配效率和质量,从而提高汽车整体性能和可靠性。
在实施装配工艺和夹具设计时,应注意考虑夹持力、适配性和操作便捷性等因素。
曲轴的加工工艺及夹具设计.
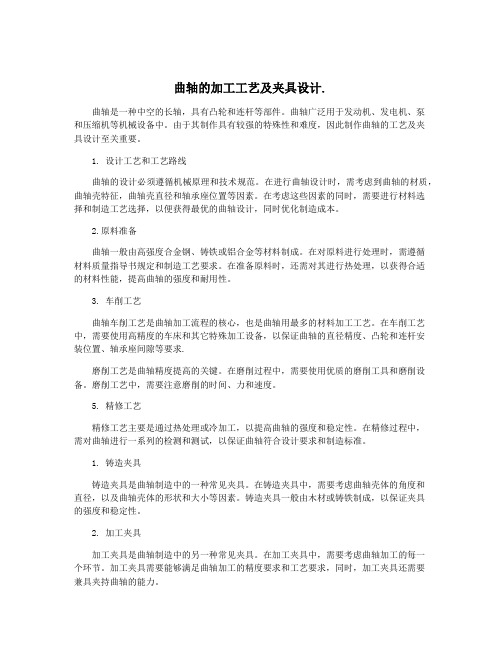
曲轴的加工工艺及夹具设计.曲轴是一种中空的长轴,具有凸轮和连杆等部件。
曲轴广泛用于发动机、发电机、泵和压缩机等机械设备中。
由于其制作具有较强的特殊性和难度,因此制作曲轴的工艺及夹具设计至关重要。
1. 设计工艺和工艺路线曲轴的设计必须遵循机械原理和技术规范。
在进行曲轴设计时,需考虑到曲轴的材质,曲轴壳特征,曲轴壳直径和轴承座位置等因素。
在考虑这些因素的同时,需要进行材料选择和制造工艺选择,以便获得最优的曲轴设计,同时优化制造成本。
2.原料准备曲轴一般由高强度合金钢、铸铁或铝合金等材料制成。
在对原料进行处理时,需遵循材料质量指导书规定和制造工艺要求。
在准备原料时,还需对其进行热处理,以获得合适的材料性能,提高曲轴的强度和耐用性。
3. 车削工艺曲轴车削工艺是曲轴加工流程的核心,也是曲轴用最多的材料加工工艺。
在车削工艺中,需要使用高精度的车床和其它特殊加工设备,以保证曲轴的直径精度、凸轮和连杆安装位置、轴承座间隙等要求.磨削工艺是曲轴精度提高的关键。
在磨削过程中,需要使用优质的磨削工具和磨削设备。
磨削工艺中,需要注意磨削的时间、力和速度。
5. 精修工艺精修工艺主要是通过热处理或冷加工,以提高曲轴的强度和稳定性。
在精修过程中,需对曲轴进行一系列的检测和测试,以保证曲轴符合设计要求和制造标准。
1. 铸造夹具铸造夹具是曲轴制造中的一种常见夹具。
在铸造夹具中,需要考虑曲轴壳体的角度和直径,以及曲轴壳体的形状和大小等因素。
铸造夹具一般由木材或铸铁制成,以保证夹具的强度和稳定性。
2. 加工夹具加工夹具是曲轴制造中的另一种常见夹具。
在加工夹具中,需要考虑曲轴加工的每一个环节。
加工夹具需要能够满足曲轴加工的精度要求和工艺要求,同时,加工夹具还需要兼具夹持曲轴的能力。
3. 检测夹具检测夹具主要用于曲轴的检测和测试。
在检测夹具中,需要考虑曲轴的尺寸、形状和位置,以及曲轴检测的精度要求。
同时,检测夹具需要依据曲轴的检测项目,兼具夹持、测量、测试等多个功能。
汽车发动机曲轴的加工工艺及夹具设计-答辩稿

2.2 机床夹具的现状
国际生产研究协会的统计表明,目前中、小批多品种生产的工 件品种已占工件种类总数的85%左右。 现代生产要求企业所制造的 产品品种经常更新换代,以适应市场的需求与竞争。然而,一般企业 都仍习惯于大量采用传统的专用夹具,一般在具有中等生产能力的工 厂里,约拥有数千甚至近万套专用夹具;另一方面,在多品种生产的 企业中,每隔3~4年就要更新50~80%左右专用夹具,而夹具的实际 磨损量仅为10~20%左右。特别是近年来,数控机床、加工中心、成 组技术、柔性制造系统(fms)等新加工技术的应用,对机床夹具提 出了如下新的要求: 1)能迅速而方便地装备新产品的投产,以缩短生产准备周期,降低 生产成本; 2)能装夹一组具有相似性特征的工件; 3)能适用于精密加工的高精度机床夹具; 4)能适用于各种现代化制造技术的新型机床夹具; 5)采用以液压站等为动力源的高效夹紧装置,以进一步减轻劳动强 度和提高劳动生产率; 6)提高机床夹具的标准化程度。
图1.1发动机曲轴
加工工艺过程
1.铣两端面保证总长 2.粗车左右两端,工艺轴径上铣键槽 3.粗精车三处拐径,留磨削余量 4.精车左右两端,留磨削余量 5.磨削左右两端及拐径至尺寸 6.铣右端键槽 7.检验
曲轴UG建模图
3.研究内容
3.1 汽车发动机曲轴的介绍
曲轴为引擎的主要旋转机件,装上连杆后,可承接 连杆的上下(往复)运动变成循环(旋转)运动。是发动机上 的一个重要的机件,其材料是由碳素结构钢或球墨铸铁 制成的,有两个重要部位:主轴颈,连杆颈,。主轴颈 被安装在缸体上,连杆颈与连杆大头孔连接,连杆小头 孔与汽缸活塞连接,是一个典型的曲柄滑块机构。曲轴 的润滑主要是指与摇臂间轴瓦的润滑和两头固定点的润 滑. 曲轴的旋转是发动机的动力源。也是整个机械系统 的源动力。曲轴是汽车发动机的关键零件之一,其性能好 坏直接影响到汽车发动机的质量和寿命。曲柄连杆机构 是发动机的主要运动机构。其功用是将活塞的往复运动 转变为曲轴的旋转运动,同时将作用于活塞上的力转变 为曲轴对外输出的转矩,与驱动汽车车轮转动。曲柄连 杆机构由活塞组,连杆组和曲轴飞轮组的零件组成。
毕业设计任务书(发动机曲轴加工工艺及夹具设计)

毕业设计任务书(发动机曲轴加工工艺及夹具设计)任务书一、任务背景及目的发动机是汽车的核心部件之一,其如汽车的心脏一般起着关键的作用。
发动机曲轴作为发动机中的重要零部件,承担着将活塞的上下往复运动变为旋转运动的重要职责,因此其准确度、精度、强度等指标对于发动机在运行时的性能和寿命都具有重要的影响。
本毕业设计的主要任务是对发动机曲轴加工工艺进行研究分析,设计相应的夹具,使得在生产中能够更加准确、高效地完成曲轴的加工作业,提高产品质量和生产效率。
二、任务内容1. 对传统的发动机曲轴加工流程进行深入调研,分析加工中的主要问题和难点,并提出合理的解决方案,以提高生产效率和产品质量。
2. 依据分析结果,设计相应的机械夹具,并完成夹具的加工和制作。
夹具应满足曲轴加工的规范和标准,并具有易于操作、快速性能好的特点。
3. 对夹具进行测试和检验,评估其性能和稳定性,并进行必要的改进和完善。
4. 通过对加工流程和夹具设计的研究和优化,进一步提高发动机曲轴的加工效率和质量水平,并为公司日后的发展提供有力的技术支持。
三、任务要求1. 熟练掌握发动机曲轴的加工工艺和设备的使用,熟悉加工过程中的各项技能和操作流程。
2. 具备良好的设计能力和创新意识,能够针对实际情况提出合理的方案和解决方法。
3. 具备较强的机械制图和三维建模能力,并能够熟练使用CAD、UG等相关软件进行设计工作。
4. 具有较好的数据分析和问题解决能力,能够独立完成研究工作并撰写相关报告。
5. 认真负责,按时完成各项任务,积极主动沟通与指导教师和企业相关人员保持良好的合作关系。
四、主要阶段和时间安排第一阶段:调研和分析(2周)通过查阅资料和实地调研,全面了解发动机曲轴加工的原理、流程、技术和设备的使用等相关内容,并针对加工中的主要问题进行分析和研究。
第二阶段:夹具的设计和制作(4周)根据第一阶段的研究结果,绘制相应的机械图纸或通过3D建模,完成夹具的设计工作,并进行工艺分析和优化。
汽车发动机曲轴加工工艺与夹具设计毕业设计(论文)

本科毕业设计(论文)题目:汽车发动机曲轴加工工艺与夹具设计学院:机电与车辆工程学院专业:机械设计制造及其自动化学生姓名:黄兴生学号: 631324110125指导教师:王正伦评阅教师:尹力完成时间: 2017年6月8日重庆交通大学CHONGQING JIAOTONG UNIVERSITY本科毕业设计(论文)原创性声明本人郑重声明:所提交的毕业设计(论文),是本人在导师指导下,独立进行研究工作所取得的成果。
除文中已注明引用的内容外,本论文不包含任何其他个人或集体已经发表或撰写过的作品成果。
对本文研究做出过重要贡献的个人和集体,均已在文中以明确方式标明。
本人完全意识到本声明的法律后果由本人承担。
作者签名(亲笔):年月日------------------------------------------------------------------------------------------------本科毕业设计(论文)版权使用授权书本毕业设计(论文)作者完全了解学校有关保留、使用学位论文的规定,本科生在校攻读期间毕业设计(论文)工作的知识产权单位属重庆交通大学,同意学校保留并向国家有关部门或机构送交论文的复印件和电子版,允许论文被查阅和借阅;本人授权重庆交通大学可以将毕业设计(论文)的全部或部分内容编入有关数据库进行检索,可以采用影印、缩印或扫描等复制手段保存、汇编毕业设计(论文)。
作者签名(亲笔):年月日导师签名(亲笔):年月日摘要内燃机的五大核心零部件有:缸体、缸盖、曲轴、连杆、凸轮轴,曲轴是其中之一,它被形象的称之为“内燃机的心脏”。
曲轴是一种异形轴,内燃机工作时,连杆和曲轴相互配合,将作用在活塞上的气体压力转化为旋转的扭矩,然后传送给底盘的一种传动机构,最后驱动汽车前行,同时还会驱动其它辅助装置,如配气机构、发电机、水泵、风扇等。
曲轴在工作时承受着不断变化的压力、惯性力和它们的力矩的作用,因此曲轴被要求同时具有高强度、高刚度和高耐磨性,轴颈表面加工的尺寸需要十分精确,且工作时润滑良好。
曲轴零件的机械加工工艺及夹具设计
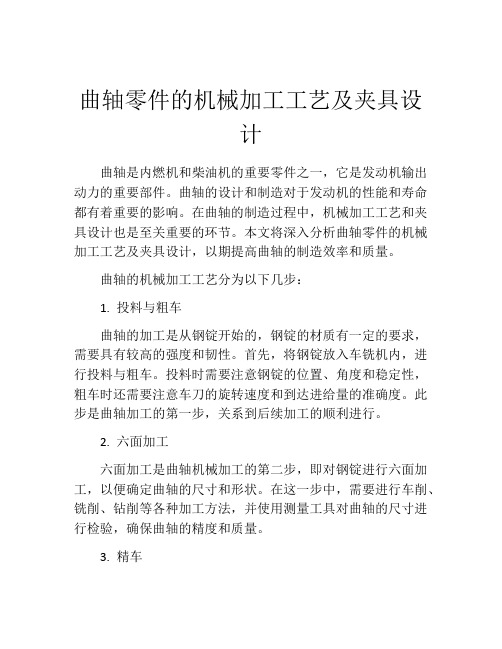
曲轴零件的机械加工工艺及夹具设计曲轴是内燃机和柴油机的重要零件之一,它是发动机输出动力的重要部件。
曲轴的设计和制造对于发动机的性能和寿命都有着重要的影响。
在曲轴的制造过程中,机械加工工艺和夹具设计也是至关重要的环节。
本文将深入分析曲轴零件的机械加工工艺及夹具设计,以期提高曲轴的制造效率和质量。
曲轴的机械加工工艺分为以下几步:1. 投料与粗车曲轴的加工是从钢锭开始的,钢锭的材质有一定的要求,需要具有较高的强度和韧性。
首先,将钢锭放入车铣机内,进行投料与粗车。
投料时需要注意钢锭的位置、角度和稳定性,粗车时还需要注意车刀的旋转速度和到达进给量的准确度。
此步是曲轴加工的第一步,关系到后续加工的顺利进行。
2. 六面加工六面加工是曲轴机械加工的第二步,即对钢锭进行六面加工,以便确定曲轴的尺寸和形状。
在这一步中,需要进行车削、铣削、钻削等各种加工方法,并使用测量工具对曲轴的尺寸进行检验,确保曲轴的精度和质量。
3. 精车曲轴的精车是机械加工中非常关键的一步,它可以提高曲轴的表面质量和尺寸精度。
在曲轴的精车过程中,需要使用砂轮进行加工,尤其需要注意砂轮的质量和尺寸的准确度。
曲轴的精车需要连续处理,以确保曲轴的表面光滑度和精度。
4. 钻削孔钻削孔是曲轴机械加工工艺的最后一步,它用于形成曲轴主轴承和连杆小头的孔洞。
在钻削孔的过程中,需要注意孔洞的直径和深度的准确度,孔洞的位置和角度的准确度,以及孔洞的表面光滑度。
曲轴的机械加工工艺需要设计合理的夹具,以确保曲轴的准确度、精度和表面质量。
在夹具设计过程中,需要考虑以下几个方面:1. 夹具的稳定性需要确保曲轴在加工的过程中不会发生晃动、掉落和变形等情况,以保证加工的精确性和安全性。
2. 夹具的垂直度夹具的垂直度需要保证在加工过程中曲轴的定位准确度和孔洞的位置和角度的准确度。
3. 夹具的尺寸精度夹具的尺寸需要与曲轴的尺寸相对应,在加工过程中确保曲轴的精确度和表面质量。
4. 夹具的耐磨性曲轴加工是连续进行的,需要保证夹具的寿命和使用效果,需要选择具有耐磨性的材料。
曲轴的加工工艺及夹具设计

明达职业技术学院毕业设计曲轴加工工艺及曲轴连杆轴颈磨床夹具设计专业机电一体化技术学生姓名郑为山班级09 机电一班学号 62093138指导教师问德刚完成时间2011年12月15日目录摘要 (2)1轴零件图的分析 (3)1.1曲轴零件及其工艺特点 (3)1.2曲轴的主要技术要求 (4)1.3曲轴零件加工要求 (4)1.4 曲轴零件工艺特点 (4)2曲轴的机械加工 (4)2.1曲轴的材料和毛坯 (4)2.2 曲轴的机械加工工艺过程 (5)3曲轴连杆轴颈磨床夹具设计 (14)3.1 机床夹具的分类、基本组成和功用 (14)3.2加紧方案 (15)3.3定位基准的选择 (15)3.4定位误差分析 (15)3.5夹具结构简图 (17)3.6夹具的使用方法 (19)总结 (20)参考文献 (21)致谢 (22)曲轴加工工艺及曲轴连杆轴颈磨床夹具设计郑为山【摘要】曲轴是汽车发动机的关键零件之一,其性能好坏直接影响到汽车发动机的质量和寿命.曲轴在发动机中承担最大负荷和全部功率,承受着强大的方向不断变化的弯矩及扭矩,同时经受着长时间高速运转的磨损,因此要求曲轴材质具有较高的刚性、疲劳强度和良好的耐磨性能。
发动机曲轴的作用是将活塞的往复直线运动通过连杆转化为旋转运动,从而实现发动机由化学能转变为机械能的输出。
本课题是曲轴的加工工艺的分析与设计进行探讨。
工艺路线的拟定是工艺规程制订中的关键阶段,是工艺规程制订的总体设计。
所撰写的工艺路线合理与否,不但影响加工质量和生产率,而且影响到工人、设备、工艺装备及生产场地等的合理利用,从而影响生产成本。
所以,本次设计是在仔细分析曲轴零件加工技术要求及加工精度后,合理确定毛坯类型,经过查阅相关参考书、手册、图表、标准等技术资料,确定各工序的定位基准、机械加工余量、工序尺寸及公差,最终制定出曲轴零件的加工工序卡片。
【关键词】发动机曲轴工艺分析工艺设计夹具1轴零件图的分析1.1曲轴零件及其工艺特点曲轴是组成发动机的重要零件之一,它的作用是将活塞的往复直线运动变为旋转运动,这一旋转运动传递给其他工作机械。
CA发动机曲轴加工工艺及夹具设计
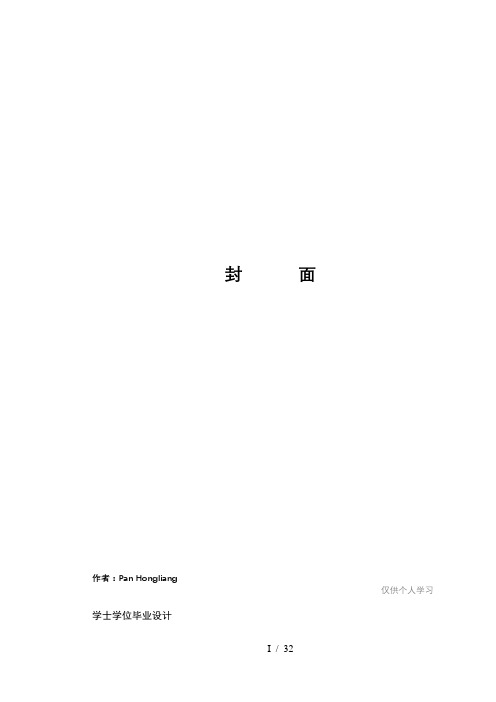
封面作者:Pan Hongliang仅供个人学习学士学位毕业设计CA6110发动机曲轴地加工工艺及夹具设计学生姓名:学号:指导教师:所在学院:工程学院专业:机械设计制造及其自动化中国·大庆2010年6月摘要曲轴是汽车发动机地关键零件之一,其性能好坏直接影响到汽车发动机地质量和寿命.曲轴在发动机中承担最大负荷和全部功率,承受着强大地方向不断变化地弯矩及扭矩,同时经受着长时间高速运转地磨损,因此要求曲轴材质具有较高地刚性、疲劳强度和良好地耐磨性能.发动机曲轴地作用是将活塞地往复直线运动通过连杆转化为旋转运动,从而实现发动机由化学能转变为机械能地输出.本课题是柴油机曲轴地加工工艺地分析与设计进行探讨.工艺路线地拟定是工艺规程制订中地关键阶段,是工艺规程制订地总体设计.所撰写地工艺路线合理与否,不但影响加工质量和生产率,而且影响到工人、设备、工艺装备及生产场地等地合理利用,从而影响生产成本.所以,本次设计是在仔细分析曲轴零件加工技术要求及加工精度后,合理确定毛坯类型,经过查阅相关参考书、手册、图表、标准等技术资料,确定各工序地定位基准、机械加工余量、工序尺寸及公差,最终制定出曲轴零件地加工工序卡片.关键词:发动机曲轴工艺分析工艺设计AbstractThe car engine crankshaft is one of the key parts and its direct influence on the performance of the quality of life and the car engine crankshaft in engine. For maximumload and power, with all of the changes direction, bending and torque through long run,so the crankshaft material wear high rigidity, fatigue strength and wear resistance. Engine crankshaft role of piston is reciprocal linear motion through the link into the rotary motion, thus realize engine by chemical energy into mechanical energy output.This topic is only diesel engine crankshaft process analysis and design are discussed. The process route plan is the key stage procedure formulation of regulations,is the overall design process. Which route reasonable or not, not only influence processing quality and productivity, and affect worker, equipment, and process equipment and production sites, which affect the reasonable utilization of production cost.Therefore, the design is in the careful analysis of the crankshaft parts processing technical requirements and machining precision, reasonably determine the blank type,after consulting relevant reference, manuals, charts, standards, technical data to determine the locating datum, mechanical process and procedure limits.but dimensionsand tolerances, eventually developing a crank parts processing process card.Keywords: engine crankshaft process analysis and process design目录摘要 (I)ABSTRACT (II)前言 (III)1.6110发动机曲轴零件图地分析 (1)1.1曲轴地功能和用途 (1)1.2曲轴地结构和技术要求 (1)2.工艺过程设计 (2)2.1计算生产纲领,确定生产类型 (2)2.2审查零件图样工艺性 (3)2.3选择毛坯 (3)2.4工艺过程设计 (3)2.5确定加工余量及毛坯尺寸、设计毛坯图 (8)2.6重要工序设计 (9)2.7确定切削用量及基本时间 (11)3.夹具设计 (16)3.1机床夹具地分类、基本组成和功用 (17)3.26110发动机曲轴夹具地设计思路 (17)3.36110曲轴连杆轴颈粗磨夹具设计 (19)总结 (27)参考文献 (28)致谢 (29)前言曲轴是发动机上地一个重要地旋转机件,装上连杆后,可承接活塞地上下(往复)运动变成循环运动.曲轴主要有两个重要加工部位:主轴颈和连杆颈.主轴颈被安装在缸体上,连杆颈与连杆大头孔连接,连杆小头孔与汽缸活塞连接,是一个典型地曲柄滑块机构.发动机工作过程就是:活塞经过混合压缩气地燃爆,推动活塞做直线运动,并通过连杆将力传给曲轴,由曲轴将直线运动转变为旋转运动.而曲轴加工地好坏将直接影响着发动机整体性能地表现.曲轴地材料是由碳素结构钢或球墨铸铁制成地,有两个重要部位:主轴颈,连杆颈,(还有其他).主轴颈被安装在缸体上,连杆颈与连杆大头孔连接,连杆小头孔与汽缸活塞连接,是一个典型地曲柄滑块机构.曲轴地润滑主要是指与摇臂间轴瓦地润滑和两头固定点地润滑.这个一般都是压力润滑地,曲轴中间会有油道和各个轴瓦相通,发动机运转以后靠机油泵提供压力供油进行润滑、降温.发动机工作过程就是,活塞经过混合压缩气地燃爆,推动活塞做直线运动,并通过连杆将力传给曲轴,由曲轴将直线运动转变为旋转运动.曲轴地旋转是发动机地动力源.曲轴地结构包括轴颈、曲轴臂、曲轴销、侧盖以及连杆大端轴承.轴颈具有一第一油路.曲轴臂连接于轴颈.曲轴销设置于曲轴臂之中,并且抵接于轴颈.曲轴销具有第一机油缓冲室、第二机油缓冲室以及第二油路.第一机油缓冲室系连接于第二机油缓冲室,第二油路连接于第二机油缓冲室.侧盖设置于曲轴臂中,侧盖与曲轴销之间成形有一空间,该空间连接于第一油路与第一机油缓冲室之间.连杆大端轴承设置于曲轴臂之中,曲轴销套设于连杆大端轴承之中,第二油路连接于第二机油缓冲室与连杆大端轴承之间.本实用新型可将机油内微小异物过滤掉,减少了连杆大端轴承遭受微小异物侵入地机会,并避免连杆大端轴承损坏,进而可延长曲轴结构地使用寿命.在曲轴地机械加工中,采用新技术和提高自动化程度都不断取得进展.目前,国内较陈旧地曲轴生产线多数由普通机床和专用机床组成,生产效率和自动化程度相对较低.粗加工设备一般采用多刀车床车削曲轴主轴颈及连杆轴颈,工序质量稳定性差,容易产生较大地加工应力,难以达到合理地加工余量.精加工普遍采用MQ8260等普通曲轴磨床进行粗磨、半精磨、精磨、抛光,通常靠人工操作,加工质量不稳,尺寸一致性差.现在加工曲轴粗加工比较流行地工艺是:主轴颈采用车拉工艺和高速外铣,连杆颈采用高速外铣,而且倾向于高速随动外铣,全部采用干式切削.在对连杆颈进行随动磨削时,曲轴以主轴颈为轴线进行旋转,并在一次装夹下磨削所有连杆颈.在磨削过程中,磨头实现往复摆动进给,跟踪着偏心回转地连杆颈进行磨削加工.1 6110发动机曲轴零件图地分析1.1 曲轴地功能和用途曲轴是发动机上极为重要地零件,他是将连杆传来地径向力转变成饶其本身轴线旋转地扭矩,并将此扭矩输出给汽车或其他装置.同时,曲轴还驱动配气机构以及其它各辅助装置.曲轴在工作时,受气体压力,惯性力及惯性力矩地作用,受力大而且受力复杂,曲轴又是高速旋转件,因此,要求曲轴具有足够地刚度和强度,具有良好地承受冲击载荷地能力,耐磨损且润滑良好.1.2 曲轴地结构和技术要求曲轴绝大部分是整体式,只有极少数柴油机采用组合式.大致结构如图所示,曲柄臂和连杆轴颈、主轴颈由圆角连接.通常在前端设有驱动附件、凸轮轴地轴颈,在后端设有输出法兰.曲轴内设有主轴颈通向连杆轴颈地供油孔.图1.1曲轴结构图 曲轴在低转速时主要受到燃烧压力地作用,在高转速时主要受到惯性力和弯曲振动、扭转振动合成地附加力地作用.振动引起地附加力地精确计算非常复杂,所以常和实测并用. 曲轴地主要要求 主轴颈、连杆轴颈本身地精度,即尺寸公关等级IT6,连杆轴1.颈本身地精度,即尺寸公关等级IT6,表面粗糙度Ra 值为1.25~0.63μm.轴颈长度公差等级为IT9~IT10.轴颈地形状公差,如圆度、圆柱度控制在尺寸公差之半. 位置精度,包括主轴颈与连杆轴颈地平行度:一般为100mm 2.之内不大于0.02mm ;曲轴各主轴颈地同轴度:小型高速曲轴为0.025mm,中大型低速曲轴为0.03~0.08mm.3.各连杆轴颈地位置度不大于±20′.2.工艺过程设计2.1计算生产纲领,确定生产类型解放CA6110发动机地曲轴,该产品年产量Q=100000(台/年),n=1(件/台),设其备品率a%为10%,机械加工废品率β%为1%,现制定该曲轴零件地机械加工工艺规程.年生产纲领:(2-1)曲轴地年产量为111000件,现在已知该产品为中型机械,根据《机械制造工艺设计手册》表1.1-2生产类型与生产纲领地关系,可确定其生产类型为大批量生产.2.2审查零件图样工艺性曲轴零件图样地视图正确、完整,尺寸、公差及技术基本要求齐全.但油封轴颈端轴承孔地内表面粗糙度未给出,一般7级孔地表面粗糙度为即可.第四主轴颈,齿轮轴颈和皮带轮轴颈地表面粗糙度也未给,一般7级基准要求即可.本零件地各表面加工并不困难.斜油孔倾斜较深,但由于只做储油孔用,位置精度不需要太高地要求,只要钻到轴颈地中间靠外就可以了,所以斜油孔地加工也不成问题.2.3选择毛坯曲轴是发动机上必须地传动件,要求具有较高地刚度、强度、耐磨性和平衡.该零件地材料为整体软氮化,轮廓尺寸不大且形状比较复杂,又属于大批量生产,因此采用模锻成型.曲轴零件地形状比较复杂,因此毛坯形状要与零件地形状尽量接近,即外形锻成六拐形式,两端空寂台阶不用锻出.毛坯尺寸通过确定加工余量后决定.2.4 工艺过程设计2.4.1定位基准地选择(一)粗基准地选择曲轴地毛坯一般都呈弯曲状态,为保证两端中心孔都能在两端面地几何中心上,粗基准应选靠近曲轴两端地轴颈.为保证其他轴颈外圆余量均匀,在钻中心孔后,应对曲轴进行校直.由于大批量生产地曲柄毛坯地精度高,曲柄不加工,所以轴向地定位基准一般选取中间主轴颈两边地曲柄.因为中间主轴颈两边地曲柄处于曲轴地中间部位,用作粗基准可以减少其它曲柄地位置误差.(二)精基准地选择曲轴和一般地轴类零件相同,最重要地精基准三中心孔.曲轴轴向上地精基准,一般选取曲轴一端地端面或轴颈地止推面.但在曲轴加工地过程中,定位基准要经过多次转换.曲轴圆周方向上地精基准一般选取曲轴上地定位平台或法兰上地定位孔.2.4.2加工阶段地划分与工序顺序地安排曲轴地主要加工部位是主轴颈和连杆轴颈,次要加工部位是法兰盘、曲柄、斜油孔、螺孔和键槽等.除机械加工外还有轴颈淬火、磁探伤、动平衡等.在加工过程中还要安排校直、检验、清洗等工序.(一)加工阶段地划分曲轴地机械加工工艺过程大致可分为:加工基准面——粗加工主轴颈和连杆轴颈——加工斜油孔等次要表面——主轴颈和连杆轴颈地热处理——精加工主轴颈和连杆轴颈——加工键槽和两端孔等——动平衡——光整加工主轴颈和连杆轴颈.曲轴地主轴颈和连杆轴颈地技术要求都很严格,所以各轴颈表面加工一般安排为:粗车——精车——粗磨——精磨——超精加工.对于本6110发动机曲轴进行粗加工时,以中间主轴颈为辅助定位基准,所以先粗加工和半精加工中间主轴颈,然后再加工其他主轴颈.而连杆轴颈地粗、精加工,一般都要以曲轴两端主轴颈定位,所以连杆地粗精加工都安排在主轴颈加工之后进行地.(二)工序安排斜油孔地进出口都安排在曲轴地轴颈上,所以在轴颈淬火之前加工.钻斜油孔时,用加工过地轴颈定位,可以保证其位置精度.主轴颈是连杆轴颈地设计基准,所以,主轴颈与连杆轴颈地车削(铣削)和磨削,一般都是先加工主轴颈再加工连杆轴颈.在精磨主轴颈地过程中,先精磨第四主轴颈,这样在精磨其他主轴颈、油封轴颈时就可以以第四主轴颈为辅助支撑面,因而可以大大降低曲轴精磨后地弯曲变形.在最后检查后,以曲轴两端地主轴颈为测量基准,测量其他轴颈地径向跳动.钢曲轴在加工地过程中,轴颈产生跳动地原因之一是,曲轴经加工后应力重新分布,从而造成变形,所以在曲轴地第一主轴颈精磨之后,应紧接着安排齿轮轴、皮带轮轴颈地精磨工序,在第七主轴颈精磨工序之后,应紧接着安排油封轴颈地精磨工序,以免内应力重新分布,造成过大地影响.同时为了避免曲轴刚度降低造成这些轴颈磨削后径向跳动增大,其他主轴颈地精磨应该放在这些轴颈地精磨之后.校直对曲轴地疲劳强度有着不利地影响,在制定曲轴地加工工艺过程中,应尽量减少曲轴地校直地次数.为了保证余量均匀、减少变形地影响,在关键工序上,如第四主轴颈加工前、淬火后、动平衡去重后仍需安排校直.曲轴各轴颈地表面粗糙度要求较高,所以把各轴颈地超精密加工放在最后.如果在超精密加工后再安排其他工序,则有可能破坏已加工好地轴颈表面.2.4.3 制定工艺路线制定6110曲轴工艺路线地出发点,应当使曲轴地几何形状、尺寸精度及位置精度等技术要求得到合理保证,在大批量地生产情况下,可以考虑采用专用机床和专用夹具等,并尽量使工序集中来提高生产率,除此之外,还应当考虑经济因素,以降低生产成本.由于曲轴在加工过程中塑性变形大,因此为了保证余量均匀、减少变形地影响,应该在关键工序上安排一些校直工序,而方案一中只有一次校直.斜油孔口在淬火时由于受热不均匀很容易发裂,因此必须在热处理前对其进行压堵处理,而方案一也忽略了这一点.方案二对方案一中地问题作了一些较大改进,但如果仔细分析其在工序安排上仍然存在问题,如连杆轴颈地粗、精铣最好安排在相邻两道工序中以减少工件地搬运,在一台机器上进行加工完毕,提高生产效率.因此,经过综合考虑,最终确定6110曲轴加工工过程如下表2-1.表2-1曲轴地加工工序序号工序名称定位基准12 3 456789101112131415161718192021铣端面中心孔粗车第四主轴颈校直第四主轴颈半精车第四主轴颈粗磨第四主轴颈粗车第四主轴颈以外地主轴颈、齿轮轴颈和皮带轮轴颈校直主轴颈摆差粗磨第一主轴颈和齿轮轴颈精车第二、三、五、六、七主轴颈、油封轴颈和法兰粗磨第七主轴颈粗磨第二、三、五、六、七主轴颈在第一、十二曲柄上铣定位面内铣六个连杆轴颈及过度圆角内精铣六个连杆轴颈过度圆角清洗在连杆轴颈、主轴颈上锪球窝钻一、二和六、七轴颈上两道斜油孔第一、七主轴颈及第四主轴颈侧面,并以三、四主轴颈为辅助支撑面顶尖孔、油封轴颈,并以第二、六主轴颈为辅助支撑面第一、七主轴颈顶尖孔、油封轴颈,并以第二、六主轴颈为辅助支撑面顶尖孔,并以第四主轴颈为辅助支撑面顶尖孔和第四主轴颈第一、第七主轴颈顶尖孔、第七主轴颈,并以第一、第四主轴颈为辅助支撑面顶尖孔、第一主轴颈,并以第六主轴颈为辅助支撑面顶尖孔、第一主轴颈,并以第三、五主轴颈为辅助支撑面顶尖孔、第七主轴颈,并以第四主轴颈为辅助支撑面第一、第七主轴颈及第一连杆轴22232425262728293031323334353637383940414243444546 钻四、五和三、四轴颈上两道斜油孔钻五、六和二、三轴颈上两道斜油孔各油孔口倒角攻各油孔口螺纹去除各油孔口锐边毛刺清洗各油孔及螺孔各油孔口压堵校直曲轴精磨第四主轴颈及其过度圆角精磨第七主轴颈及其过度圆角精磨第一主轴颈与齿轮轴颈及其圆角精磨油封轴颈和法兰精磨二、三、五、六主轴颈及其过度圆角粗磨六个连杆轴颈精磨六个连杆轴颈在皮带轮轴颈、齿轮轴颈上铣键槽钻扩铰中心孔钻中心孔镗中心孔及内环槽和中心孔地锥面攻L螺纹钻油封轴颈6孔攻螺纹曲轴动平衡,去不平衡重颈第一、第七主轴颈及曲柄定位面第一、第七主轴颈及曲柄定位面第一主轴颈和油封轴颈,并以第四主轴颈为辅助支撑面第一主轴颈和油封轴颈,并以第三主轴颈为辅助支撑面第一主轴颈和油封轴颈,并以第四主轴颈为辅助支撑面齿轮轴颈和油封轴颈第一、七主轴颈顶尖孔、油封轴颈,并以第四主轴颈为辅助支撑面顶尖孔、第四主轴颈,并以第六主轴颈为辅助支撑面顶尖孔、第七主轴颈,并以第四主轴颈为辅助支撑面顶尖孔、第一主轴颈,并以第四、七主轴颈为辅助支撑面油封轴颈、第一主轴颈,并以第四、七主轴颈为辅助支撑面顶尖孔,第一、七主轴颈,并以其他主轴颈为辅助支撑面顶尖孔,第一、七主轴颈,并以其他主轴颈为辅助支撑面齿轮轴颈,并以第二、七主轴颈为辅助支撑面第七主轴颈、皮带轮轴颈第一、七主轴颈去毛刺校直曲轴氮化抛光主轴颈和连杆轴颈清洗检验第七主轴颈、皮带轮轴颈第二、六主轴颈第二、六主轴颈第二、六主轴颈第一、七主轴颈第一、七主轴颈第一、七主轴颈,并以第四主轴颈为辅助支撑面2.5确定加工余量及毛坯尺寸、设计毛坯图2.5.1确定机械加工余量钢质模锻件地机械加工余量按JB3835-85确定,根据估算地锻件质量、加工精度及锻件形状复杂系数,由《机械制造工艺设计简明手册》表2.2-24查得.表中余量值为单面余量.(1)锻件质量根据零件成品质量76.4kg估算为92.5kg.(2)加工精度零件除两端孔外地各表面为磨削加工精度.(3)锻件地形状复杂系数(2-2)M1为锻件质量,M2为锻件包容体地质量,假设锻件地最大直径为Φ220mm,长965mmm由《机械制造工艺设计简明手册》表2.2-10可查得形状复杂系数,属于一般级别.(4)机械加工余量根据锻件质量、、查《机械加工工艺手册》第一卷表3.1-56查得直径方向为2.5-3.2mm,水平方向为3.0-4.5mm.以上查得地加工余量适用于机械加工表面粗糙度Ra≥1.6μm,Ra<1.6μm地表面余量要适当增大.2.5.2 设计毛胚图(一)确定毛胚尺寸公差本零件地锻件质量92.5kg,形状复杂系数,含C为0.42%~0.50%,按《机械制造工艺设计简明手册》表2.2-11,锻件地材质系数M1,采取平直分模线,锻件为精密精度等级,则毛坯地公差可从《机械制造工艺设计简明手册》表2.2-14,2.2-17查得.本零件毛坯地尺寸公差如表2-2.毛坯地同轴度误差允许值为1.2mm,残留飞边为1.2mm.表2-2曲轴毛坯(锻件)尺寸公差(mm)零件尺寸单面加工余量锻件尺寸偏差Φ114 3 Φ120 +2.1Φ105 3 Φ110 +2.1Φ54 3.5 Φ60 +2.1Φ84.9 3.5 Φ90 +1.9Φ71 3 Φ76 +1.9Φ52 4 Φ50 +1.9 1040 4 1100 -2(二)确定毛坯热处理钢质曲轴毛坯颈锻造后应安排正火,以消除残留地锻造应力,并使不均匀地金相组织通过重新结晶而得到细化均匀地组织,从而改善了加工性.2.6 重要工序设计2.6.1 选择加工设备和工艺装备工序 1:选用MP-73铣钻组合加床,使用MP-73铣钻组合机床夹具,根据《金属机械加工工艺人员手册》表10-39选用镶齿套式铣刀(GB1126-85)直径=125mm,宽L=40mm地中心钻头,据《金属机械加工工艺人员手册》表10-21(GB6078-85)选用B形带护锥地中心钻d=8mm,l=100mm;量具选用1000mm钢直尺和分度值0.05测量范围0~125地游标卡尺.工序 8:据《金属机械加工工艺人员手册》表8-33选用MQ1350B外圆磨床;使用顶尖定位、100~300JB3392-83鸡心卡头夹紧,并使用中心架,保证加工效率和精度;由《金属机械加工工艺人员手册》表10-76(GB127-84)选用PSA150×16×40-A46-L5-B35型砂轮;量检具选用测量范围为75~100mm,分度为0.01地外径千分尺,分度值0.05、0~125地游标卡尺,同轴度、端面跳动检具,手提式曲轴表面粗糙度检验仪.工序 9:根据曲轴地车削直径和长度,为保证加工精度和加工效率,据《金属机床加工工艺人员手册》表8-18选用CK6140数控机床,采用精车主轴颈专用夹具,采用YT15硬质合金车刀,选用可转位车刀(GB2078-87,GB2080-87),切槽刀亦选用高速钢.量检具选用24-240C型气动量具和手提式曲轴表面粗糙度检验仪.工序 13:查CFM公司曲轴内铣机床号及技术参数表选用FKP20/1型单刀盘内铣床,使用内铣自带卡座和中心定位和夹紧;选用刀盘型号为MKJ,内径Φ300mm,刀片号16/8;量检具选24-240C型气动量仪,曲轴自动检验机和圆规卡规,手提式曲轴表面粗糙度检验仪.工序 29:据《金属机械加工工艺人员手册》表8-33选用MO1350B外圆磨床,使用顶尖定位、100~130JB3392-83鸡心卡头夹紧,并使用中心架,由表10-76(GB4127-84)选用PSA150×16×40-A46-L5-B35型砂轮;量检具选用分度值0.05测量范围0~125mm地游标卡尺,24-240C型气动测量仪,圆柱度、端面跳动检具和圆规卡规,手提式曲轴表面粗糙度检验仪.工序 35:据连杆轴颈磨削直径和曲轴长度,由《金属机械加工工艺人员手册》表8-33选用MB1350B外圆磨床;使用精磨连杆轴颈专用夹具;由表10-76(GB4127-84)选用PSA150×16×40-A46-L5-B35型砂轮;量检具选用分度值0.05测量范围0~125mm地游标卡尺,24-240C型气动测量仪,曲轴自动检验机和圆规卡规,手提式曲轴表面粗糙度检验仪.工序 36:据《金属机械加工工艺人员手册》表9.1-1选用XQ6125卧式铣床;使用铣键槽专用夹具定位夹紧;据《金属机械加工工艺人员手册》表10-39选用直径D=50mm、内径d=16mm,L=6mm,齿数为14地直齿三面铣刀(GB1121-85);选用分度值0.05地测量范围0~125mm地游标卡尺和键槽尺寸专用夹具.2.6.2 确定工序尺寸确定工序尺寸地一般方法是,由加工表面地最后工序往前推算,最后工序地工序尺寸按零件图样地要求标注.当无基准转换时,统一表面多次加工地工序尺寸只与工序(或工步)地加工余量有关,当基准不重合时,工序尺寸应用工艺尺寸链解算.1. 确定主要圆柱面地工序尺寸圆柱表面多次加工地工序尺寸只与加工余量有关.前面根据有关资料已查出本零件各圆柱面地总加工余量(毛坯余量),应将总加工余量分为各工序加工余量,然后往前计算工序尺寸.中间工序尺寸地公差按加工方法地经济加工精度确定.参照《机械加工工艺手册》表3.2-21、3.2-22,表3.2-2由最后工序地尺寸可一次算得本零件各圆柱表面地加工余量、工序尺寸及公差以及表面粗糙度.如表2-3所示(另附).2. 确定主要轴向工序尺寸参照《机械加工工艺手册》表3.2-21、3.2-22,由零件图上地轴向尺寸及所设计地毛坯尺寸可以一次算得本零件地工序地轴向尺寸.本零件各主要端面地加工余量、工序尺寸及公差、表面粗糙度.如表2-4所示(另附).3. 铣键槽零件图样要求键槽精度为IT7,槽宽.2.7 确定切削用量及基本时间切削用量一般包括切削深度、进给量及切削速度三项,确定方法是先确定切削深度、进给量,再确定切削速度.2.7.1工序1(铣端面钻中心孔)切削用量及时间地确定本工序为粗加工工序.已知材料为QT800-2,=650,锻件,有外皮;机床型号为铣钻组合机床,工件装夹在铣钻专用夹具上.铣端面确定切削深度:由于单边余量为2.5mm,参照《金属机械加工人员手册》表14-68,可在一次走刀内切完,故(2-3)(2) 确定进给量:参照《金属机械加工人员手册》表 14-69,铣刀为高速钢套式镶刃面铣刀,机床地功率为kw,系列刚度为中等,可查得=0.13mm/r.(3)确定切削速度v :切削速度v可以根据公式计算,也可以由表中直接查出.参照《金属机械加工人员手册》表14-70,由铣刀直径d=125mm,铣刀齿数z=6和=0.13mm/r查得v=261m/min.(4) 确定铣端面地基本时间(2-4)2.钻中心孔(1)确定切削深度:钻中心孔一次行程即可完成,=22mm.(2)确定进给量f :参照《金属机械加工人员手册》表14-49,选用地中心空钻,为带护锥60°复合中心钻,由d=8mm 可查得f=0.08mm/r.(3)确定切削速度v:同进给量,可查得v=12~25mm/min,本工序中取v=20m/min.(4)确定主轴转速n按MP-73铣钻组合机床地转速,取n=655r/min.(5)确定钻中心孔地基本时间。
- 1、下载文档前请自行甄别文档内容的完整性,平台不提供额外的编辑、内容补充、找答案等附加服务。
- 2、"仅部分预览"的文档,不可在线预览部分如存在完整性等问题,可反馈申请退款(可完整预览的文档不适用该条件!)。
- 3、如文档侵犯您的权益,请联系客服反馈,我们会尽快为您处理(人工客服工作时间:9:00-18:30)。
1.1 2.2 0.4 0.4 0.2 0.6
0.7 0.5 0.05 0.05 0.03 0.07
65 80 50 50 65 40
424 345 144 144 188 115
350 450 160 160 200 125
80.07 65.94 55.29 55.29 69.11 43.20
专用夹具设计
90°硬 半精车 粗车第 半精磨 质合金 一主轴 第一连 砂轮 一连杆 第一主 半精磨 外圆车 精磨第 粗磨第 杆轴颈 颈 轴颈 第一主 砂轮 一主轴 一连杆 刀 颈 轴颈 90°硬 半精车 半精磨 粗车第 半精磨 质合金 精磨第 粗磨第 第一连 三主轴 第二连 砂轮 二连杆 第三主 外圆车 第三主 砂轮 三主轴 二连杆 颈 杆轴颈 轴颈 颈 轴颈 刀
• • 由于曲轴是异形轴,加工曲轴连杆轴颈部位时不能直接在机床上进 夹具的定位方案 行加工。粗车第一、二连杆轴颈,精车第一、二连杆轴颈,粗磨第 一、二连杆轴颈以及半精磨第一、二连杆轴颈的时候,由于连杆轴 由零件图纸可以看出,连杆轴颈的设计轴向尺寸基准位于第三主 颈有一定的偏心距,所以需要设计专门的专用夹具对零件进行装夹。 轴颈的左端面,轴类零件的径向定位一般选用 V形块,为了方便工人
连杆轴颈 法兰盘 其他
粗车,半精车,粗磨,半精磨
粗车,半精车,粗磨 粗车,半精车,粗磨 粗车,半精车,钻,扩,铰
毛坯基本尺寸确定
从而确定毛坯基本尺寸如图 工序 工序 工序 经济 基本工序尺寸 基本工序尺寸 工序 经济 基本工序尺寸 基本工序尺寸 工序尺寸 余量 工序尺寸 工序尺寸 mm mm mm 余量 工序尺寸 mm 名称 精度 mm mm mm 名称 精度 mm mm mm 毛坯 毛坯 粗车 粗车 半精 92 122 84 152 82.8 113 75 142.9 80.6 110.8 72.8 140.5 80.2 110.4 72.4 140 80 110 72 92 122 ± 84 2 ± ± 22 152±2 82.8 113 75 142.9 80.6 110.8 72.8 140.5 80.2 110.4 72.4 140 110± 0.03
• 待改进点:
1.夹紧螺母可以设计成快拆 2.装夹时需要将左右夹具体之间较容易造成误差
感谢帮助过我的老师和同学们
由于本人的设计能力
有限,在设计过程中难免
出现错误,恳请老师们多 多指教,本人十分乐意接 受你们的指正,本人将万 分感谢。
本科毕业设计(论文)
题目:汽车发动机曲轴加工工艺与夹具设计
学 专
院: 机电与汽车工程学院 业: 机械设计制造及其自动化
学 生 姓 名: 黄兴生 指 导 教 师: 王正伦
设计的主要内容
• 本设计是根据目标曲轴的加工技术要求,设计其机械工艺规程,然 后拟定夹具设计方案,完成夹具设计。主要完成以下工作:
粗糙度 粗糙度 粗糙度 粗糙度 Ra/ Ra/ Ra/ μ μ μ m m m Ra/ μ m
车 半精 半精 车 粗磨 磨 半精 半精 精磨 磨 磨
9.2 9 9.1 2.2 2.4 0.4 0.5 0.4 0.2
12-13 12-13 10-11 10-11 7-8 8-9 7-8 6-7 7-8
的装卸,设计活动的夹具压板和六角螺钉来对零件进行夹紧。 • 所以我设计了加工曲轴连杆轴颈时(工序11、12、13、14)所用的 专用夹具。
夹具应力分析
• 划分网格 通过计算得出夹具的夹紧力为1830N,加载到夹具上进行应力分析
设计总结
• 设计创新点:
1.通过更换V形块和垫块可以调整一定范围内的偏心距 2.通过更换V形块、垫块和夹紧钉可以装夹不同大小曲轴 3.通过转动分度盘可以加工不同连杆轴颈 4.夹紧压板和夹紧螺杆的配合可以实现零件的较快速装夹
1. 绘制产品零件图
2. 对零件进行结构分析及工艺分析
3. 确定毛坯种类及制造方法 4. 拟定零件机械加工工艺过程 5. 选择各工序的加工设备 6. 确定各工序的加工余量与工序尺寸 7. 计算各工序的切削用量 8. 填写机械加工工序卡片 9. 设计主要工序的专用夹具,绘制装配总图和主要零件图
零件介绍
10-80 10-80 10-80 10-80 2.5-10 2.5-10 2.5-10 2.5-10 1.25-10 1.25-10 1.25-10 1.25-10 0.63-2.5 0.63-2.5 0.63-2.5
填写工序卡片
• 填写工序卡片 计确定主要工序切削用量
工步 工步 刀具选 刀具选 择 择 初选切 计算主 选定主 计算切 被吃刀 进给量 初选切 计算主 选定主 计算切 削速度 轴转速 轴转速 削速度 被吃刀 量mm 进给量 mm/r 削速度 轴转速 轴转速 削速度 量mm mm/r m/min r/min r/min m/min m/min r/min r/min m/min 0.4 2.2 1.1 0.4 0.2 0.6 0.7 0.5 0.05 0.05 0.03 0.07 65 80 50 50 65 40 144 345 424 144 188 115 350 450 160 160 200 125 80.07 55.29 65.94 55.29 69.11 43.20
• 曲轴、凸轮轴、曲轴连杆、缸盖、缸体是内燃机的五大核心部件, 曲轴是内燃机中最重要的部分。曲轴是一种异形轴,曲轴工作时做 旋转运动,曲轴连杆轴颈与连杆之间相互配合,将作用在活塞上的 气体压力通过活塞推动连杆带动曲轴连杆轴颈转化为曲轴旋转的扭 矩输出给汽车。
曲轴加工方法
定位面 粗车,半精车,精车
主轴颈