光化学蚀刻
在PCB碱性蚀刻中常见的问题的原因和故障解决方法

在PCB碱性蚀刻中常见的问题的原因和故障解决方法
PCB蚀刻技术通常所指蚀刻也称光化学蚀刻,指通过曝光制版、显影后,将要蚀刻区域的保护膜去除,在蚀刻时接触化学溶液,达到溶解腐蚀的作用,形成凹凸或者镂空成型的效果。
随着PCB工业的发展,各种导线之阻抗要求也越来越高,这必然要求导线的宽度控制更加严格。
在生活中的广泛运用,PCB的质量越来越好,越来越可靠,它是设计工艺也越来越多样化,也更加的完善。
蚀刻技术在PCB设计中的也越来越广泛。
1.问题:印制电路中蚀刻速率降低
原因:
由于工艺参数控制不当引起的
解决方法:
按工艺要求进行检查及调整温度、喷淋压力、溶液比重、PH值和氯化铵的含量等工艺参数到工艺规定值。
2.问题:印制电路中蚀刻液出现沉淀
原因:
(1)氨的含量过低
(2)水稀释过量
(3)溶液比重过大
解决方法:
(1)调整PH值到达工艺规定值或适当降低抽风量。
(2)调整时严格按工艺要求的规定或适当降低抽风量执行。
(3)按工艺要求排放出部分比重高的溶液经分析后补加氯化铵和氨的水溶液,使蚀刻液的比重调整到工艺充许的范围。
3.问题:印制电路中金属抗蚀镀层被浸蚀
原因:。
半导体 光刻蚀刻
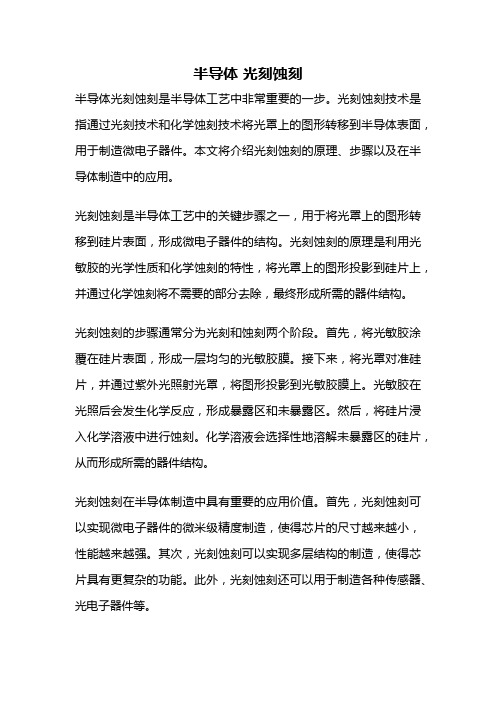
半导体光刻蚀刻半导体光刻蚀刻是半导体工艺中非常重要的一步。
光刻蚀刻技术是指通过光刻技术和化学蚀刻技术将光罩上的图形转移到半导体表面,用于制造微电子器件。
本文将介绍光刻蚀刻的原理、步骤以及在半导体制造中的应用。
光刻蚀刻是半导体工艺中的关键步骤之一,用于将光罩上的图形转移到硅片表面,形成微电子器件的结构。
光刻蚀刻的原理是利用光敏胶的光学性质和化学蚀刻的特性,将光罩上的图形投影到硅片上,并通过化学蚀刻将不需要的部分去除,最终形成所需的器件结构。
光刻蚀刻的步骤通常分为光刻和蚀刻两个阶段。
首先,将光敏胶涂覆在硅片表面,形成一层均匀的光敏胶膜。
接下来,将光罩对准硅片,并通过紫外光照射光罩,将图形投影到光敏胶膜上。
光敏胶在光照后会发生化学反应,形成暴露区和未暴露区。
然后,将硅片浸入化学溶液中进行蚀刻。
化学溶液会选择性地溶解未暴露区的硅片,从而形成所需的器件结构。
光刻蚀刻在半导体制造中具有重要的应用价值。
首先,光刻蚀刻可以实现微电子器件的微米级精度制造,使得芯片的尺寸越来越小,性能越来越强。
其次,光刻蚀刻可以实现多层结构的制造,使得芯片具有更复杂的功能。
此外,光刻蚀刻还可以用于制造各种传感器、光电子器件等。
然而,光刻蚀刻也面临一些挑战和限制。
首先,光刻蚀刻的精度受到光学系统和化学蚀刻溶液的限制,难以实现纳米级别的制造。
其次,光刻蚀刻的成本较高,需要昂贵的设备和材料。
此外,光刻蚀刻还存在一些工艺问题,如光刻胶的选择、光刻胶的曝光剂选择等。
为了克服这些问题,科研人员不断进行研究和改进。
他们开发了更先进的光刻蚀刻技术,如多重光刻、纳米光刻等,以提高制造精度。
同时,他们还研究新型的光刻胶和曝光剂,以改善光刻胶的性能。
此外,还研究了新型的蚀刻溶液和工艺条件,以提高蚀刻的选择性和均匀性。
半导体光刻蚀刻是半导体制造中至关重要的一步。
它通过光刻和蚀刻技术将光罩上的图形转移到硅片表面,用于制造微电子器件。
光刻蚀刻具有精度高、多层结构制造能力强等优点,但也面临着成本高、精度受限等挑战。
标牌蚀刻工艺

标牌蚀刻工艺是一种常见的金属表面处理技术,主要应用于标牌、标识、商标等产品的制作过程中。
其基本原理是利用化学或物理方法将金属表面的部分材料去除,从而形成所需的文字、图案或图形等。
常见的标牌蚀刻工艺包括:
1.化学蚀刻:使用化学蚀刻剂对金属表面进行处理,使其部分材料被去除。
化学蚀刻剂通常是一种酸性或碱性溶液,通过与金属表面的金属离子反应,去除部分金属材料,形成所需的文字、图案或图形等。
2.激光蚀刻:利用激光束对金属表面进行处理,使其部分材料被去除。
激光蚀刻具有高精度、高速度、高效率等优点,适用于复杂形状和细小文字的制作。
3.电化学蚀刻:通过在金属表面施加电压,使其部分材料发生氧化或还原反应,从而去除部分金属材料。
电化学蚀刻适用于金属材料表面的精细加工和高质量蚀刻。
标牌蚀刻工艺具有制作速度快、效果好、成本低等优点,被广泛应用于各种标牌、标识、商标等产品的制作中。
化学蚀刻技术课件

无误。
穿戴防护用品
02
操作人员必须穿戴防护眼镜、实验服、化学防护手套等防护用
品,防止化学试剂溅到身上。
保持通风
03
在操作过程中,要保持实验室通风良好,避免有害气体在室内
积聚。
废液处理与环保要求
废液分类处理
根据废液的性质和成分,将其进行分类存放和处理,避免混合后 产生有毒有害气体或发生危险。
废液回收利用
蚀刻处理
选择合适的蚀刻液
根据基材的特性和工艺要 求选择合适的蚀刻液,确 保其具有较高的蚀刻速率 和选择性。
控制蚀刻条件
控制蚀刻液的浓度、温度、 PH值等条件,以确保蚀刻 过程的稳定性和精度。
蚀刻方式
采用浸泡、喷淋、刷涂等 方式进行蚀刻处理,确保 基材表面被均匀蚀刻。
去胶与清洗
去胶
去除抗蚀剂掩膜,将其彻底清洗干净,以便后续处理。
化学蚀刻技术课件
• 化学蚀刻技术概述 • 化学蚀刻技术的基本原理 • 化学蚀刻技术的工艺流程 • 化学蚀刻技术的材料选择 • 化学蚀刻技术的质量控制 • 化学蚀刻技术的安全与环保
01
化学蚀刻技术概述
定义与特点
定义
化学蚀刻技术是一种利 用化学反应将材料进行 选择性溶解或去除的工
艺过程。
高精度
能够实现高精度的图形 转移,满足微细加工的
总结词:性能测试
详细描述:在化学蚀刻过程中,抗蚀 剂的性能至关重要。通过性能测试, 如耐酸性、耐碱性、耐温度性等,可 以评估抗蚀剂的适用性和稳定性。
抗蚀剂的性能检测与控制
总结词:成分分析
VS
详细描述:对抗蚀剂进行成分分析, 了解其化学成分和浓度,有助于优化 配方和工艺参数。同时,成分分析还 可以及时发现潜在的问题和失效模式。
半导体工艺光刻+蚀刻 ppt课件
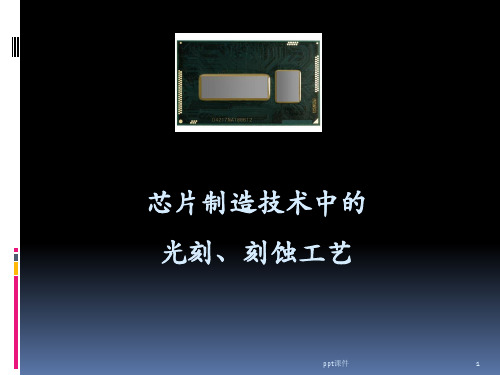
ppt课件
1
▪ 芯片制造工艺 ▪ 光刻工艺
▪ 刻蚀工艺
ppt课件
2
精品资料
ppt课件
4
光刻+蚀刻
最重要
决定着芯片的最小尺寸 制造时间的40-50% 制造成本的30%
ppt课件
5
玻璃模版 光刻胶膜
硅片
光刻 光化学反应
蚀刻
腐蚀
ppt课件
6
ppt课件
7
光刻原理
模版上的铬岛
紫外光
光刻胶的曝光区
光p刻ho胶tor层esist 氧化ox层ide
sil硅ico衬n 底substrate
使光衰弱的被曝光区
光刻胶上的阴影
岛
光刻胶层
窗口
氧化层 硅衬底
光刻胶显影后的最终图形
ppt课件
8
▪ 使用光敏材料(光刻胶)和可控制的曝 光在光刻胶膜层形成三维图形
▪ 在后续工艺(蚀刻)中,保护下面的材料
ppt课件
9
HMDS
清洗+喷涂粘附剂
光刻工艺步骤
紫外光
光刻胶
模版
旋转涂胶
软烘
对准和曝光
曝光后烘焙
显影
坚膜烘焙
显影检查
ppt课件
10
涂胶
模板 曝光
显影
ppt课件
11
Normal under
Incomplete
over
ppt课件
12
光刻工艺 —— 显影后
ppt课件
13
蚀刻工艺
▪ 光刻胶上的IC设计图形
晶圆表面
▪ 腐蚀作用,从Si片表面去除不需要的材料, 如Si、SiO2,金属、光刻胶等
包材工艺丨蚀刻工艺介绍及工艺分析

包材工艺丨蚀刻工艺介绍及工艺分析导LEAD语蚀刻是将材料使用化学反应或物理撞击作用而移除的技术。
蚀刻技术具有灵活性、准确性高、生产效率高等优点,同时又能够赋予包材精美的美观效果。
本文分享蚀刻工艺的相关知识,内容供优品包材系统的采供朋友们参考:一、定义蚀刻是将材料利用化学反应或物理撞击作用而去除的技术(也即利用合适的化学溶液腐蚀去除材质上未被光阻覆盖(感光膜)的部分,达到一定的雕刻深度)。
二、特点生产过程无外力冲击、不变形、平整度好;生产周期短、应变快、不需模具的设计、制造;产品无毛刺、无凸起、两面一样光、一样平;按图案加工平面凹凸型的金属材料制品,如:文字、数字及复杂图型、图案。
制造各种精密的,任意形状的通孔零件。
三、原理通常所指蚀刻也称光化学蚀刻,指通过曝光制版、显影后,将要蚀刻区域的保护膜区处,在蚀刻时接触化学溶液,达到溶解腐蚀的作用,形成凹凸或者镂空成型的效果。
四、蚀刻类型干性蚀刻干性蚀刻乃是利用化学品(通常是盐酸)与所欲蚀刻之薄膜起化学反应,产生气体或可溶性生成物,达到图案定义之目的。
在干蚀刻技术中,一般多采用电浆蚀刻与活性离子蚀刻。
而所谓干蚀刻,则是利用干蚀刻机台产生电浆,将所欲蚀刻之薄膜反应产生气体由PUMP抽走,达到图案定义之目的。
湿性蚀刻最早的蚀刻技术是利用特定的溶液与薄膜间所进行的化学反应来去除薄膜未被光阻覆盖的部分,而达到蚀刻的目的,这种蚀刻方式也就是所谓的湿式蚀刻。
因为湿式蚀刻是利用化学反应来进行薄膜的去除,而化学反应本身不具方向性,因此湿式蚀刻过程为等向性,一般而言此方式不足以定义3微米以下的线宽,但对于3微米以上的线宽定义湿式蚀刻仍然为一可选择采用的技术五、常用介质FeCl3三氯化铁因其工艺稳定,操作方便,价格便宜,因此为广大蚀刻加工企事业单位所采用;主要在印制电路、电子和金属精饰等工业中被广泛采用,一般用来蚀刻铜、铜合金、不锈钢、铁、锌及铝等。
三氯化铁蚀刻液适用于网印抗蚀印料、液体感光胶、干膜、镀金蚀层的印制板的蚀刻(不适用于镍、锡、锡铅合金等抗蚀层)NaOH是一种常见的重要强碱。
微细加工工艺技术

微细加工工艺技术微细加工工艺技术是一种应用于微电子、光学、纳米学等领域的高精度加工技术,该技术能够实现对微细结构的精密加工。
在微细加工工艺技术中,常常采用的加工方法有激光刻蚀、化学蚀刻、光刻以及微电子束等。
激光刻蚀是一种应用激光照射,通过激光束的高能量将材料表面局部蚀刻的加工方法。
与传统的机械刻蚀相比,激光刻蚀具有高精度、高效率的优点。
在激光刻蚀中,光束的聚焦度和光斑直径是影响加工精度的重要参数。
化学蚀刻是一种利用特定的化学反应,在材料表面选择性地产生化学蚀刻产物,并将其去除的加工方法。
化学蚀刻通常需要制备特定的蚀刻溶液,通过控制溶液的浓度和温度,来影响化学反应的速率和选择性。
化学蚀刻可以实现微细结构的高精度加工,并被广泛应用于光学元件和微流控芯片等领域。
光刻是一种基于光化学反应的加工方法,通过光阻的选择性暴露和去除,来形成所需的图案结构。
在光刻过程中,首先在材料表面涂敷一层光刻胶,然后利用光刻机的紫外光照射和显影等步骤,实现图案的转移。
光刻具有高精度、高分辨率和高重复性的优点,是微细加工中不可或缺的工艺之一。
微电子束也是一种实现微细结构加工的重要方法。
微电子束利用高能电子束在材料表面定向照射,经过准直、聚焦和偏转等步骤,将电子束的能量转化为对材料的加工作用。
通过控制电子束的参数,如能量、聚焦度和扫描速度等,可以实现对微细结构的精密加工。
微电子束在高精度加工领域具有很大的应用潜力,尤其在微电子器件、光电器件以及半导体器件等方面,具有广阔的发展前景。
总的来说,微细加工工艺技术是一种实现高精度加工的重要方法,包括激光刻蚀、化学蚀刻、光刻和微电子束等。
这些加工方法在微电子、光学、纳米学等领域发挥着重要作用,推动了相关技术的进步和应用的发展。
未来随着科学技术的不断进步,微细加工工艺技术将继续发展壮大,为人类社会带来更多的科技成果和应用产品。
光化学腐蚀加工介绍

光化学腐蚀加工介绍
光化学腐蚀加工是一种非传统的减材加工工艺,通过照相和化学技术对金属工件进行成形。
这种加工方式在工件上形成设计图像,并使用强化学溶液选择性地腐蚀并去除未受保护区域的多余材料,从而留下完美且清晰的图像或零件。
具体来说,光化学腐蚀加工分干蚀刻制程和湿蚀刻制程两种方式。
在蚀刻过程中,通过对不锈钢进行制版曝光、显影后,对不锈钢需要蚀刻的区域进行保护膜去除。
然后,通过化学药剂对不锈钢进行腐蚀,使用两个阳性图形通过从两面的化学研磨达到溶解腐蚀的作用,形成凹凸或者镂空成型的效果。
光化学腐蚀加工的工艺流程包括清洗、滚涂、曝光、显影、蚀刻、退膜、清洗和检测等步骤。
这种加工方式的优势在于,与传统加工方法相比,它提供了许多优势,例如更高的精度和更小的公差,而且被广泛应用于各个行业。
光化学腐蚀加工的具体应用会因行业和工件的要求而有所不同。
在某些领域中,这种加工方式可以用于制造具有复杂形状和精细细节的零件,例如精密仪器、医疗器械和航空航天部件等。
此外,由于其高精度和可控性,光化学腐蚀加工也可以用于制造微电子器件和集成电路等高技术产品。
总的来说,光化学腐蚀加工是一种先进的金属加工技术,能够提供高精度、高效率和小公差的加工效果,因此在许多行业中都有广泛的应用前景。
PCB电路板蚀刻工艺及过程控制 - 电子技术

PCB电路板蚀刻工艺及过程控制 - 电子技术印刷线路板从光板到显出线路图形的过程是一个比较复杂的物理和化学反应的过程,本文就对其最后的一步--蚀刻进行解析。
目前,印刷电路板(PCB)加工的典型工艺采用"图形电镀法"。
即先在板子外层需保留的铜箔部分上,也就是电路的图形部分上预镀一层铅锡抗蚀层,然后用化学方式将其余的铜箔腐蚀掉,称为蚀刻。
一.蚀刻的种类要注意的是,蚀刻时的板子上面有两层铜。
在外层蚀刻工艺中仅仅有一层铜是必须被全部蚀刻掉的,其余的将形成最终所需要的电路。
这种类型的图形电镀,其特点是镀铜层仅存在于铅锡抗蚀层的下面。
另外一种工艺方法是整个板子上都镀铜,感光膜以外的部分仅仅是锡或铅锡抗蚀层。
这种工艺称为“全板镀铜工艺“。
与图形电镀相比,全板镀铜的最大缺点是板面各处都要镀两次铜而且蚀刻时还必须都把它们腐蚀掉。
因此当导线线宽十分精细时将会产生一系列的问题。
同时,侧腐蚀会严重影响线条的均匀性。
在印制板外层电路的加工工艺中,还有另外一种方法,就是用感光膜代替金属镀层做抗蚀层。
这种方法非常近似于内层蚀刻工艺,可以参阅内层制作工艺中的蚀刻。
目前,锡或铅锡是最常用的抗蚀层,用在氨性蚀刻剂的蚀刻工艺中.氨性蚀刻剂是普遍使用的化工药液,与锡或铅锡不发生任何化学反应。
氨性蚀刻剂主要是指氨水/氯化氨蚀刻液。
此外,在市场上还可以买到氨水/硫酸氨蚀刻药液。
以硫酸盐为基的蚀刻药液,使用后,其中的铜可以用电解的方法分离出来,因此能够重复使用。
由于它的腐蚀速率较低,一般在实际生产中不多见,但有望用在无氯蚀刻中。
有人试验用硫酸-双氧水做蚀刻剂来腐蚀外层图形。
由于包括经济和废液处理方面等许多原因,这种工艺尚未在商用的意义上被大量采用.更进一步说,硫酸-双氧水,不能用于铅锡抗蚀层的蚀刻,而这种工艺不是PCB外层制作中的主要方法,故决大多数人很少问津。
二.蚀刻质量及先期存在的问题对蚀刻质量的基本要求就是能够将除抗蚀层下面以外的所有铜层完全去除干净,止此而已。
光化学蚀刻涂油墨工艺_概述及解释说明

光化学蚀刻涂油墨工艺概述及解释说明1. 引言1.1 概述光化学蚀刻涂油墨工艺是一项主要应用于制造业的先进技术,能够实现精细的图案和文字印刷。
该工艺通过光化学的原理,结合蚀刻和涂油墨的过程,实现对材料表面进行加工和定制。
这种工艺广泛应用于电子设备制造、半导体行业、纳米技术领域等领域。
它不仅提供了高精度、高效率的生产方式,还具有环保、节能等优势。
1.2 文章结构本文将首先介绍光化学蚀刻涂油墨工艺的基本原理和流程,并概述其在各个行业中的应用情况。
接着,将以解释说明的形式深入探讨该工艺在不同方面的重要性和独特之处。
最后,本文将总结主要观点和发现结果,并展望光化学蚀刻涂油墨工艺的未来发展前景。
1.3 目的本文旨在全面介绍光化学蚀刻涂油墨工艺,包括其基本原理、工艺流程以及应用领域。
通过对该工艺的解释说明,提供对读者的深入理解。
同时,本文将探讨该工艺的重要性和应用前景,为相关行业和研究机构提供参考和指导。
2. 光化学蚀刻涂油墨工艺2.1 光化学蚀刻技术简介:光化学蚀刻技术是一种基于光敏物质的可控制造过程,常常用于制作微米和纳米尺度结构。
通过光敏物质对特定波长的光照射后,产生化学反应从而实现对材料表面的溶解或改变。
这一技术在微电子、生物医药、传感器等领域有着广泛的应用。
2.2 涂油墨工艺概述:涂油墨是指将某种特定配方的颜料或色浆均匀地涂覆到基材表面上,以形成所需图案或提供特定功能。
涂油墨工艺在印刷、包装、电子显示等行业得到了广泛应用。
2.3 工艺原理和流程说明:光化学蚀刻涂油墨工艺结合了光化学蚀刻技术和涂油墨工艺,实现了精确控制和高质量的图案形成。
工艺原理:首先,通过在基材表面涂覆一层光敏性聚合物薄膜,使其能够对特定波长的光起反应。
然后,使用光刻技术将设计好的图案投影到光敏薄膜上,并通过光曝露来使其在受光区域发生化学反应。
接着,利用相应的溶剂或蚀刻液进行显影,溶解掉未曝露部分的聚合物。
最后,在剩余的聚合物表面上涂覆油墨并进行固化,形成所需图案。
PCB蚀刻技术及问题的分析

目录摘要 (1)1.引言 (5)2.PCB蚀刻技术 (5)2.1蚀刻方式 (6)2.2喷淋蚀刻的设备 (7)3.蚀刻反应的基本原理及故障和排除方法 (9)3.1酸性氯化铜蚀刻液 (9)3.2碱性氨类蚀刻液 (13)4.常见问题及改善和环境保护 (15)4.1设备的保养 (15)4.2生产过程中应注意的事项 (15)4.3生产安全与环境保护 (16)结语 (16)致谢 (17)参考文献 (17)1. 引言20世纪的40年代,英国人Paul Eisler博士及其助手,第一个采用了印制电路板(Printed Circuit Board,PCB)制造整机——收音机,并率先提出了印制电路板的概念。
经过多年的研究与生产实践,印制电路产业获得了很大的发展。
目前,PCB已广泛用于军事、通信、计算机、自动化等领域,成为绝大多数电子产品达到电路互连不可缺少的主要组成部件。
另外,随着集成电路的发明与应用,电子产品的小型化、高性能化,极大地推动了PCB向多层、深孔、微孔及微导电化的方向发展。
随着PCB工业的发展,各种导线之阻抗要求也越来越高,这必然要求导线的宽度控制更加严格. 在生活中的广泛运用,PCB的质量越来越好,越来越可靠,它是设计工艺也越来越多样化,也更加的完善。
蚀刻技术在PCB设计中的也越来越广泛。
蚀刻技术是利用化学感光材料的光敏特性, 在基体金属基片两面均匀涂敷感光材料采用光刻方法, 将胶膜板上栅网产显形状精确地复制到金属基片两面的感光层掩膜上通过显影去除未感光部分的掩膜, 将裸露的金属部分在后续的加工中与腐蚀液直接喷压接触而被蚀除, 最终获取所需的几何形状及高精度尺寸的产品技术蚀刻技术。
为了我们更好的学习了解PCB蚀刻工序的工艺技术及过程中易出现的问题。
但随着人类的进步和科技的发展,蚀刻技术面临着许多的新的课题,比如环境污染,工艺复杂、不简化,工艺材料对人体有害,部分资源循环利用性不强等。
本文就将结合上述问题对PCB蚀刻技术作些介绍,并对工艺改进途径方面做些探讨。
蚀刻

开料---素材清洗---上油墨(涂布)---烘烤---曝光 (固化)--显影---描油---烘烤---蚀刻---去膜清洗(脱膜)---贴 保护膜---检验---包装
微蚀(溶液为碱)---溢流水洗---市水洗---酸洗---溢流水洗2---溢流水洗3-市水洗---吸干---强风吹---热风烘干 先在产品上涂上感光油,放入隧道炉;1号炉94度烘烤(温范围65度120度)---2号炉120度烘烤(温范围95度-120度)---3号炉120度烘烤 (温范围95度-120度)---4号炉120度烘烤(温范围95度-120度)---5号 炉88度烘烤(温范围80度-120度)---产品出来过程总时间5分钟。 先将菲林片(印有所需图案)放在产品上贴合,有曝光人员放入曝光 机的玻璃板上用特有的工具压平,再把产品推入机内(曝光温度根据 产品厚度而定,温度在30度属正的,但产品0.8以上,则曝光温度150 度) 曝光时间10秒
将产品放在显影海绵轮上,传送到显影机内,产品间隔5CM。显影温度在2540度(溶液为工业碳酸钠和水浓度在0.8%-1.5%),产品在传送轮上向前传动, 此过程到显影药水区为60秒,最后检查并放在待蚀刻放置区。待蚀刻之前由修 改人员把产品漏白点处用油默或油漆笔填补好,放入铁架里待蚀刻。 产品放入蚀刻机内过程5分钟(蚀刻溶液为三氯化铁CL) 蚀刻过的产品放入纯硝酸槽里1分钟30秒,出来再放入硝酸10%槽里1分钟,再用 清水冲洗干净,最后把产品放进清洗机温度在70+/-10度,浸泡时间控制在5-6 分钟后OK. 最后检验成品有无变形,水痕和手痕,确定为良品后包装。 不锈钢,不锈 铁,铜和铝 铝材:酸和铝反应快,尺寸不好管控。不锈钢:尺寸好管控 蚀刻的良率为95%,铝材在95% 3D的蚀刻油墨损耗比2D大,差异在涂布油墨耗损3D比2D 2-2.5倍 蚀刻的温度一般在32-37度 一般蚀刻的精度可控制在+/-0.1
蚀刻
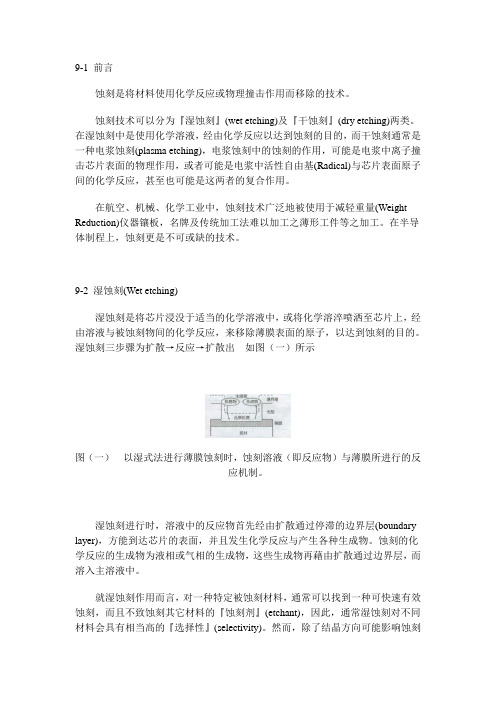
9-1 前言蚀刻是将材料使用化学反应或物理撞击作用而移除的技术。
蚀刻技术可以分为『湿蚀刻』(wet etching)及『干蚀刻』(dry etching)两类。
在湿蚀刻中是使用化学溶液,经由化学反应以达到蚀刻的目的,而干蚀刻通常是一种电浆蚀刻(plasma etching),电浆蚀刻中的蚀刻的作用,可能是电浆中离子撞击芯片表面的物理作用,或者可能是电浆中活性自由基(Radical)与芯片表面原子间的化学反应,甚至也可能是这两者的复合作用。
在航空、机械、化学工业中,蚀刻技术广泛地被使用于减轻重量(Weight Reduction)仪器镶板,名牌及传统加工法难以加工之薄形工件等之加工。
在半导体制程上,蚀刻更是不可或缺的技术。
9-2 湿蚀刻(Wet etching)湿蚀刻是将芯片浸没于适当的化学溶液中,或将化学溶淬喷洒至芯片上,经由溶液与被蚀刻物间的化学反应,来移除薄膜表面的原子,以达到蚀刻的目的。
湿蚀刻三步骤为扩散→反应→扩散出如图(一)所示图(一)以湿式法进行薄膜蚀刻时,蚀刻溶液(即反应物)与薄膜所进行的反应机制。
湿蚀刻进行时,溶液中的反应物首先经由扩散通过停滞的边界层(boundary layer),方能到达芯片的表面,并且发生化学反应与产生各种生成物。
蚀刻的化学反应的生成物为液相或气相的生成物,这些生成物再藉由扩散通过边界层,而溶入主溶液中。
就湿蚀刻作用而言,对一种特定被蚀刻材料,通常可以找到一种可快速有效蚀刻,而且不致蚀刻其它材料的『蚀刻剂』(etchant),因此,通常湿蚀刻对不同材料会具有相当高的『选择性』(selectivity)。
然而,除了结晶方向可能影响蚀刻速率外,由于化学反应并不会对特定方向有任何的偏好,因此湿蚀刻本质上乃是一种『等向性蚀刻』(isotropic etching)。
等向性蚀刻意味着,湿蚀刻不但会在纵向进行蚀刻,而且也会有横向的蚀刻效果。
横向蚀刻会导致所谓『底切』(undercut)的现象发生,使得图形无法精确转移至芯片,如图(二)所示。
金属蚀刻工艺

金属蚀刻也称光化学金属蚀刻指通过曝光制版、显影后,将要金属蚀刻区域的保护膜去除,在金属蚀刻时接触化学溶液,达到溶解腐蚀的作用,形成凹凸或者镂空成型的效果。
下面就让广德均瑞电子科技为您简单解析,希望可以帮助到您!
蚀刻是金属板模图纹装饰过程中的关键,要想得到条纹清晰、装饰性很强的图纹制品,必须注意控制好蚀刻工艺的条件。
金属的种类不同,其蚀刻的工艺流程也不同,但大致的工序如下:金属蚀刻板→除油→水洗→浸蚀→水洗→干燥→丝网印刷→千燥→水浸2~3min→蚀刻图案文字→水洗→除墨→水洗→酸洗→水洗→电解抛光→水洗→染色或电镀→水洗→热水洗→干燥→软布抛(擦光)光→喷涂透明漆→干燥→检验→成品包装。
广德均瑞电子科技有限公司注册资金500万人民币,拥有不锈钢五金蚀刻加工独立法人环评资质,厂房面积2000平方米,6条不锈钢生产线,公司销售生产管理人员均超十年不锈钢蚀刻生产加工经验。
公司主要生产集成电路导线架;接地端子; 表面贴装零件(SMT)模板;精密线材布线钢板;编码器光栅;手机按键、RDIF天线、基板及金属配件;(VFD)栅网、陈列、支架;电极针(放电针);各类金属过滤网片/喇叭网片;眼镜框架;精密元器件掩模板;LCD背光模仁、钢版;显像管荫罩;电脑硬盘骨架;金属蚀刻发热片工艺等。
广德均瑞电子科技是以补强钢片为主打产品的蚀刻厂,ISO9001认证工厂,具有独立法人和环评资质,持有排污许可证的企业。
拥有6蚀刻加工生产线,免费提供FPC补强板工艺解决方案以及蚀刻行业资讯。
金属化学蚀刻

金属化学蚀刻是之金属在干燥气体(如氧、氯、硫化氢等)和非电解质溶液(配置的蚀刻液)中进行化学反应的结果。
化学反应作用引起腐蚀,在腐蚀过程中不产生电流。
下面就让广德均瑞电子科技为您简单解析,希望可以帮助到您!
通常所指蚀刻也称光化学蚀刻(photochemical etching),指通过曝光制版、显影后,将要蚀刻区域的保护膜去除,在蚀刻时接触化学溶液,达到溶解腐蚀的作用,形成凹凸或者镂空成型的效果。
最早可用来制造铜版、锌版等印刷凹凸版,也广泛地被使用于减轻重量(Weight Reduction)仪器镶板,名牌及传统加工法难以加工之薄形工件等之加工;经过不断改良和工艺设备发展,亦可以用于航空、机械、化学工业中电子薄片零件精密蚀刻产品的加工,特别在半导体制程上,蚀刻更是不可或缺的技术。
比如Moto V3的键盘,文字和符号均为采用镂空蚀刻工艺成型。
广德均瑞电子科技有限公司注册资金500万人民币,拥有不锈钢五金蚀刻加工独立法人环评资质,厂房面积2000平方米,6条不锈钢生产线,公司销售生产管理人员均超十年不锈钢蚀刻生产加工经验。
公司主要生产集成电路导线架;接地端子; 表面贴装零件(SMT)模板;精密线材布线钢板;编码器光栅;手机按键、RDIF天线、基板及金属配件;(VFD)栅网、陈列、支架;电极针(放电针);各类金属过滤网片/喇叭网片;眼镜框架;精密元器件掩模板;LCD背光模仁、钢版;显像管荫罩;电脑硬盘骨架;金属蚀刻发热片工艺等。
广德均瑞电子科技是以补强钢片为主打产品的蚀刻厂,ISO9001认证工厂,具有独立法人和环评资质,持有排污许可证的企业。
拥有6蚀刻加工生产线,免费提供FPC补强板工艺解决方案以及蚀刻行业资讯。
蚀刻工艺原理

蚀刻工艺原理蚀刻工艺是一种常见的微纳加工技术,广泛应用于半导体、光学器件、传感器等领域。
蚀刻工艺的原理是利用化学溶液或等离子体对材料表面进行加工,从而实现微纳米级的结构加工。
本文将介绍蚀刻工艺的原理及其在微纳加工中的应用。
蚀刻工艺的原理主要包括化学蚀刻和物理蚀刻两种方式。
化学蚀刻是利用化学溶液对材料表面进行溶解,从而实现加工的目的。
而物理蚀刻则是利用等离子体或离子束对材料表面进行加工,通过物理碰撞或能量转移来改变材料表面的形貌。
两种蚀刻方式都能够实现微纳米级的加工精度,但其加工速度和加工适用材料有所不同。
化学蚀刻的原理是利用化学溶液中的特定成分对材料表面进行溶解。
在蚀刻过程中,化学溶液中的特定成分会与材料表面发生化学反应,从而使材料表面发生溶解或化学变化。
常见的化学蚀刻溶液包括酸性溶液、碱性溶液和氧化剂等。
不同的化学蚀刻溶液对不同材料具有特定的选择性,可以实现对特定材料的精确加工。
物理蚀刻的原理是利用等离子体或离子束对材料表面进行加工。
在物理蚀刻过程中,等离子体或离子束会对材料表面施加能量,从而使材料表面发生物理碰撞或能量转移。
通过控制等离子体或离子束的能量和方向,可以实现对材料表面的精确加工。
物理蚀刻通常用于对硬脆材料的加工,如硅、玻璃等。
蚀刻工艺在微纳加工中具有重要的应用价值。
通过蚀刻工艺,可以实现对微纳米结构的精确加工,包括微孔、微槽、微柱等结构的加工。
这些微纳结构在半导体器件、光学器件、传感器等领域具有重要的应用,如微型芯片、光栅结构、微流控芯片等。
蚀刻工艺还可以实现对材料表面的改性,如表面的疏水处理、光学薄膜的制备等。
总之,蚀刻工艺是一种重要的微纳加工技术,其原理包括化学蚀刻和物理蚀刻两种方式。
通过蚀刻工艺,可以实现对微纳米结构的精确加工,具有广泛的应用前景。
随着微纳加工技术的不断发展,蚀刻工艺将在更多领域发挥重要作用。
蚀刻

蚀刻蚀刻的定义:蚀刻是将材料使用化学反应或物理撞击作用而移除的技术。
蚀刻的分类:蚀刻技术可以分为湿蚀刻(wet etching)和干蚀刻(dry etching)两类。
蚀刻的原理:通常所指蚀刻也称光化学蚀刻(photochemical etching),指通过曝光制版、显影后,将要蚀刻区域的保护摸去处,在蚀刻时接触化学溶液,达到溶解腐蚀的作用,形成凹凸或者镂空成型的效果。
在湿蚀刻中是使用化学溶液,经由化学反应以达到蚀刻的目的,而干蚀刻通常是一种电浆蚀刻(plasma etching),电浆蚀刻中的蚀刻的作用,可能是电浆中离子撞击芯片表面的物理作用,或者可能是电浆中活性自由基(Radical)与芯片表面原子间的化学反应,甚至也可能是这两者的复合作用。
半导体制程中常见几种物质的湿式蚀刻:硅、二氧化硅、氮化硅。
硅的湿式蚀刻:在半导体制程中,单晶硅与复晶硅的蚀刻通常利用硝酸与氢氟酸的混合液来进行。
此反应是利用硝酸将硅表面氧化成二氧化硅,再利用氢氟酸将形成的二氧化硅溶解去除。
反应式:Si + HNO3 + 6HF à H2SiF6 + HNO2 + H2 + H2O上述的反应中可添加醋酸作为缓冲剂(Buffer Agent),以抑制硝酸的解离。
而蚀刻速率的调整可藉由改变硝酸与氢氟酸的比例,并配合醋酸添加与水的稀释加以控制。
在某些应用中,常利用蚀刻溶液对于不同硅晶面的不同蚀刻速率加以进行。
例如使用氢氧化钾与异丙醇的混合溶液进行硅的蚀刻。
这种溶液对硅的(100)面的蚀刻速率远较(111)面快了许多,因此在(100)平面方向的晶圆上,蚀刻后的轮廓将形成V型的沟渠。
而此种蚀刻方式常见于微机械组件的制作上。
二氧化硅的湿式蚀刻:在微电子组件制作应用中,二氧化硅的湿式蚀刻通常采用氢氟酸溶液加以进行。
而二氧化硅可与室温的氢氟酸溶液进行反应,但却不会蚀刻硅基材及复晶硅。
应式:SiO2 + 6HF à H2 + SiF6 + 2H2O由于氢氟酸对二氧化硅的蚀刻速率相当高,在制程上很难控制,因此在实际应用上都是使用稀释后的氢氟酸溶液,或是添加氟化铵作为缓冲剂的混合液,来进行二氧化硅的蚀刻。
金属光化学蚀刻工艺

金属光化学蚀刻工艺
金属光化学蚀刻工艺是一种利用光照与化学反应相结合来蚀刻金属表面的方法。
该工艺可用于制备具有微纳米结构的金属表面,以用于光学、电子、光电等领域的应用。
金属光化学蚀刻工艺的基本步骤包括:
1. 光敏剂涂覆:将光敏剂涂覆在金属表面上。
光敏剂是一种可以对光线敏感的物质,通常是光敏树脂。
2. 阳极处理:将光敏剂涂层暴露在光照下,通常使用紫外线照射。
光敏剂在光照下会发生化学反应,形成特定的反应物。
3. 化学反应:将经过光敏剂处理的金属样品浸入蚀刻液中。
蚀刻液中的化学物质与光敏剂反应生成的反应物发生反应,从而溶解金属表面上的一些部分。
4. 清洗和处理:将蚀刻后的样品进行清洗,去除蚀刻液等残留物,以及对蚀刻表面进行后续处理。
金属光化学蚀刻工艺可以实现对金属表面的高精度蚀刻,并能在纳米尺度上形成复杂的微纳米结构。
这些结构可以用于制造微纳米光学器件、传感器、纳米线阵列等,具有广泛的应用前景。
谈谈光学化学蚀刻技术的应用及其特点
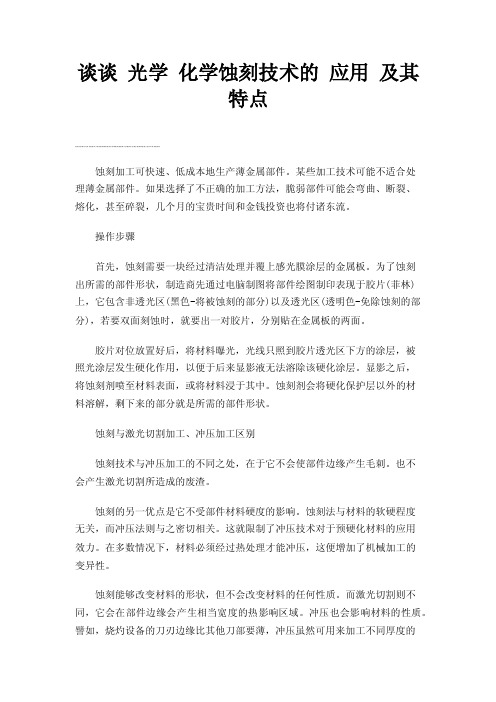
谈谈光学化学蚀刻技术的应用及其特点蚀刻加工可快速、低成本地生产薄金属部件。
某些加工技术可能不适合处理薄金属部件。
如果选择了不正确的加工方法,脆弱部件可能会弯曲、断裂、熔化,甚至碎裂,几个月的宝贵时间和金钱投资也将付诸东流。
操作步骤首先,蚀刻需要一块经过清洁处理并覆上感光膜涂层的金属板。
为了蚀刻出所需的部件形状,制造商先通过电脑制图将部件绘图制印表现于胶片(菲林)上,它包含非透光区(黑色-将被蚀刻的部分)以及透光区(透明色-免除蚀刻的部分),若要双面刻蚀时,就要出一对胶片,分别贴在金属板的两面。
胶片对位放置好后,将材料曝光,光线只照到胶片透光区下方的涂层,被照光涂层发生硬化作用,以便于后来显影液无法溶除该硬化涂层。
显影之后,将蚀刻剂喷至材料表面,或将材料浸于其中。
蚀刻剂会将硬化保护层以外的材料溶解,剩下来的部分就是所需的部件形状。
蚀刻与激光切割加工、冲压加工区别蚀刻技术与冲压加工的不同之处,在于它不会使部件边缘产生毛刺。
也不会产生激光切割所造成的废渣。
蚀刻的另一优点是它不受部件材料硬度的影响。
蚀刻法与材料的软硬程度无关,而冲压法则与之密切相关。
这就限制了冲压技术对于预硬化材料的应用效力。
在多数情况下,材料必须经过热处理才能冲压,这便增加了机械加工的变异性。
蚀刻能够改变材料的形状,但不会改变材料的任何性质。
而激光切割则不同,它会在部件边缘会产生相当宽度的热影响区域。
冲压也会影响材料的性质。
譬如,烧灼设备的刀刃边缘比其他刀部要薄,冲压虽然可用来加工不同厚度的部件,但需要高吨位的压力挤压金属才能形成较薄区域。
这会使金属的这些区域变得更硬,出现一种所谓的加工硬化效应。
因此,经此种方法加工的部件会在不同厚度的区域产生不同特质。
相比之下,蚀刻可以在不影响材料本身硬度的条件下加工不同厚度的部件。
蚀刻可以通过减少工具的制造周期来大幅缩短部件的生产过程。
当制造商决定修改设计时,也能及时方便地修改胶片。
而制造冲压工具根据其复杂程度需要4至12周且传统模具一旦制成则难以修改。
光蚀刻技术原理

光蚀刻技术原理
光蚀刻技术是一种利用光化学反应来制造微型结构的技术。
它是一种非接触式的加工方法,可以制造出高精度、高分辨率的微型结构,广泛应用于微电子、光电子、生物医学等领域。
光蚀刻技术的原理是利用光敏树脂的光化学反应来制造微型结构。
光敏树脂是一种特殊的聚合物材料,它可以在紫外线的照射下发生聚合反应,形成一层坚硬的保护层。
在光敏树脂上覆盖一层掩膜,然后用紫外线照射掩膜,掩膜上的图案就会被转移到光敏树脂上。
接着,将光敏树脂浸泡在蚀刻液中,蚀刻液会将未被保护的部分蚀刻掉,形成微型结构。
光蚀刻技术的优点是可以制造出高精度、高分辨率的微型结构。
由于光敏树脂的聚合反应是一种非接触式的加工方法,因此可以制造出非常细小的结构,甚至可以制造出纳米级别的结构。
此外,光蚀刻技术还可以制造出复杂的三维结构,具有很高的灵活性和可塑性。
光蚀刻技术的应用非常广泛。
在微电子领域,光蚀刻技术可以制造出微处理器、存储器、传感器等微型电子元件。
在光电子领域,光蚀刻技术可以制造出光纤、光波导、光栅等微型光学元件。
在生物医学领域,光蚀刻技术可以制造出微型生物芯片、微型药物传递系统等微型生物医学元件。
光蚀刻技术是一种非常重要的微型加工技术,具有广泛的应用前景。
随着科技的不断发展,光蚀刻技术将会越来越成熟,为人类带来更多的科技创新和发展。
- 1、下载文档前请自行甄别文档内容的完整性,平台不提供额外的编辑、内容补充、找答案等附加服务。
- 2、"仅部分预览"的文档,不可在线预览部分如存在完整性等问题,可反馈申请退款(可完整预览的文档不适用该条件!)。
- 3、如文档侵犯您的权益,请联系客服反馈,我们会尽快为您处理(人工客服工作时间:9:00-18:30)。
Supporting Online Materials for
Carbon-based Supercapacitors Produced by Activation of Graphene
Yanwu Zhu,1 Shanthi Murali,1 Meryl D. Stoller,1 K. J. Ganesh,1 Weiwei Cai,1 Paulo J. Ferreira,1 Adam Pirkle,2 Robert M. Wallace,2 Katie A. Cychosz,3 Matthias Thommes,3 Dong Su,4 Eric A. Stach,4 Rodney S. Ruoff1,*
/cgi/content/full/science.1200770/DC1
Supporting Online Material for
Carbon-Based Supercapacitors Produced by Activation of Graphene
Yanwu Zhu, Shanthi Murali, Meryl D. Stoller, K. J. Ganesh, Weiwei Cai, Paulo J. Ferreira, Adam Pirkle, Robert M. Wallace, Katie A. Cychosz, Matthias Thommes, Dong Su, Eric A. Stach, Rodney S. Ruoff*
*To whom correspondence should be addressed. E-mail: r.ruoff@
Published 12 May 2011 on Science Express DOI: 10.1126/science.1200770 This PDF file includes: SOM Text Figs. S1 to S12 References Other Supporting Online Material for this manuscript includes the following: (available at /cgi/content/full/science.1200770/DC1) Movie S1
2
2. Characterization methods The a-MEGO was analyzed by scanning electron microscopy (SEM, Hitachi S5500, 30 kV), transmission electron microscopy (TEM, JEOL 2010F, 200 kV at UT-Austin; TEM, spherical aberration corrected FEI Titan 80/300, 80 kV at BNL; the spherical and chromatic aberration corrected TEAM instrument at LBNL, see: /TEAM-
1
Department of Mechanical Engineering and Materials Science and Engineering Program, The University of Texas at Austin, One University Station C2200, Austin, TX 78712 Department of Materials Science and Engineering, The University of Texas at Dallas, 800 W. Campbell Rd, Richardson, TX 7s of a-MEGO and a-TEGO from MEGO and TEGO The synthesis of microwave exfoliated graphite oxide (MEGO) followed the method described in Ref (1). Briefly, graphite oxide (GO) powders made from the modified Hummers’ method were irradiated in a domestic microwave oven (GE, JES0736SM1SS) operated at 1100 W for 1 minute. During the irradiation, a large volume expansion of the GO powder occurred and the black, fluffy MEGO powder obtained was collected for activation. Typically, 400 mg MEGO powder was dispersed in 20 ml 7M aqueous KOH solution and stirred for 4 hours at a speed of 400 rpm, followed by another 20 hours of static soaking in ambient conditions. The extra KOH solution was removed by briefly filtering the mixture through a polycarbonate membrane (Whatman, 0.2 m); then the mixture was dried in the lab environment at 65 oC for 24 hours. A control MEGO sample, made with the same soaking-drying process but with no KOH was also prepared, and 85% of the mass remained after drying. A KOH to MEGO ratio was calculated by assuming the MEGO in the dry MEGO/KOH mixture gave the same mass yield, i.e., 85%. It was found that the KOH uptake (KOH/MEGO ratio) was linearly dependent on the molarity of the KOH solution, with other process parameters held constant (such as the amount of MEGO from the same batch of GO and the volume of KOH solution). For the MEGO soaked in 20 ml 7M KOH as described above, the KOH/MEGO ratio was 8.90.3. The dry MEGO/KOH mixture was heated at 800 oC for 1 hour in a horizontal tube furnace (50-mm diameter), with an argon flow of 150 sccm and working pressure of ~ 400 Torr. The temperature was ramped from room temperature to 800 oC at 5 oC/min. After cooling down in vacuum, the sample was repeatedly washed by de-ionized water until a pH value of 7 was reached. Then the sample was dried at 65 oC in ambient for 2 hours, followed by thermal annealing at 800 oC in vacuum (0.1 Torr) for 2 hours, to generate ‘activated MEGO’ (a-MEGO) powders. Thermally exfoliated graphite oxide (‘TEGO’), made by ‘thermal shocking’ of GO at 250 oC in ambient (2), was activated following the same process. The a-MEGO and a-TEGO so obtained were characterized in a variety of ways, and supercapacitor measurements were made, as described in the main text and below.
3 4
2
Quantachrome Instruments, 1900 Corporate Drive, Boynton Beach, FL 33426
*
Center for Functional Nanomaterials, Brookhaven National Laboratory, Upton, NY 11973 E-mail: r.ruoff@
Table of Contents
1. Synthesis of a-MEGO and a-TEGO from MEGO and TEGO 2. Characterization methods 3. Supercapacitor measurements 4. Fig. S1: dependence of a-MEGO SSA on ratio of KOH to MEGO 5. Fig. S2: SEM/STEM images of a-MEGO 6. Fig. S3: EPR measurements of a-MEGO 7. Fig. S4: XPS data for a-MEGO and analysis 8. Fig. S5: Raman and FTIR analysis of a-MEGO 9. Fig. S6: Comparison of N2 BET data for MEGO and a-MEGO 10. Fig. S7: QSDFT pore size distribution of a-MEGO 11. Fig. S8: Supercapacitor performance of a-MEGO with TEA BF4/AN electrolyte 12. Fig. S9: Stability testing of supercapacitor having a-MEGO with BMIM BF4 electrolyte 13. Fig. S10: Supercapacitor performance of a-MEGO with EMIM TFSI electrolyte 14. Fig. S11: N2 adsorption results for a-TEGO 15. Fig. S12: Supercapacitor performance of a-TEGO with BMIM BF4/AN electrolyte 16. Movies S1 17. References