不锈钢焊缝内部质量控制
不锈钢焊缝处理方法
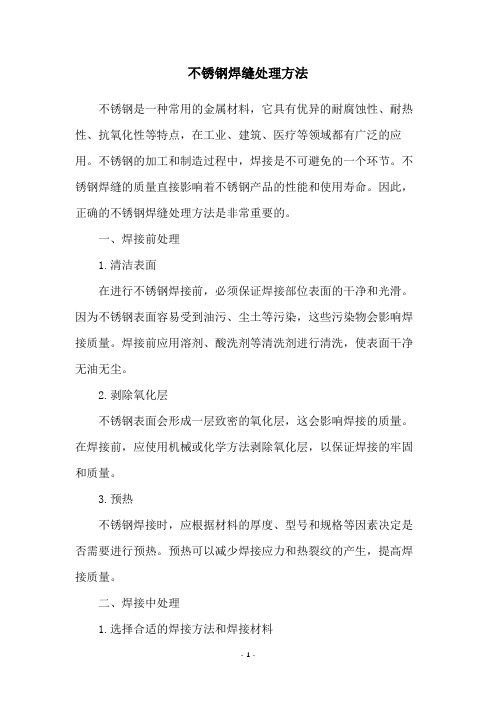
不锈钢焊缝处理方法不锈钢是一种常用的金属材料,它具有优异的耐腐蚀性、耐热性、抗氧化性等特点,在工业、建筑、医疗等领域都有广泛的应用。
不锈钢的加工和制造过程中,焊接是不可避免的一个环节。
不锈钢焊缝的质量直接影响着不锈钢产品的性能和使用寿命。
因此,正确的不锈钢焊缝处理方法是非常重要的。
一、焊接前处理1.清洁表面在进行不锈钢焊接前,必须保证焊接部位表面的干净和光滑。
因为不锈钢表面容易受到油污、尘土等污染,这些污染物会影响焊接质量。
焊接前应用溶剂、酸洗剂等清洗剂进行清洗,使表面干净无油无尘。
2.剥除氧化层不锈钢表面会形成一层致密的氧化层,这会影响焊接的质量。
在焊接前,应使用机械或化学方法剥除氧化层,以保证焊接的牢固和质量。
3.预热不锈钢焊接时,应根据材料的厚度、型号和规格等因素决定是否需要进行预热。
预热可以减少焊接应力和热裂纹的产生,提高焊接质量。
二、焊接中处理1.选择合适的焊接方法和焊接材料不锈钢焊接的方法有很多种,如TIG焊、MIG焊、手工电弧焊等。
不同的焊接方法适用于不同的材料和工况。
在选择焊接方法时,应根据实际情况进行选择。
同时,选择合适的焊接材料也非常重要,应根据不锈钢的材质、规格、用途等因素进行选择。
2.控制焊接参数焊接参数包括焊接电流、电压、焊接速度、焊接温度等因素。
这些参数的调整对焊接质量有很大影响。
在焊接过程中,应根据实际情况进行调整,以保证焊缝的质量。
3.保护焊缝不锈钢焊接时,焊缝易受到氧化、腐蚀等影响,因此需要进行保护。
常用的保护方法有惰性气体保护、氩弧焊保护等。
这些方法可以有效地保护焊缝,提高焊接质量。
三、焊接后处理1.去除焊渣焊接后,焊缝上会留下一些焊渣,这些焊渣会影响焊缝的质量。
因此,应及时去除焊缝上的焊渣,以保证焊缝的平整和光滑。
2.打磨和抛光为了使焊接后的焊缝表面更加光滑和美观,应进行打磨和抛光处理。
这可以消除焊接时产生的毛刺、划痕等缺陷,提高焊接质量。
3.消除焊接应力焊接后,焊接部位会产生应力。
不锈钢带极堆焊质量问题及控制措施【建筑工程类独家文档首发】
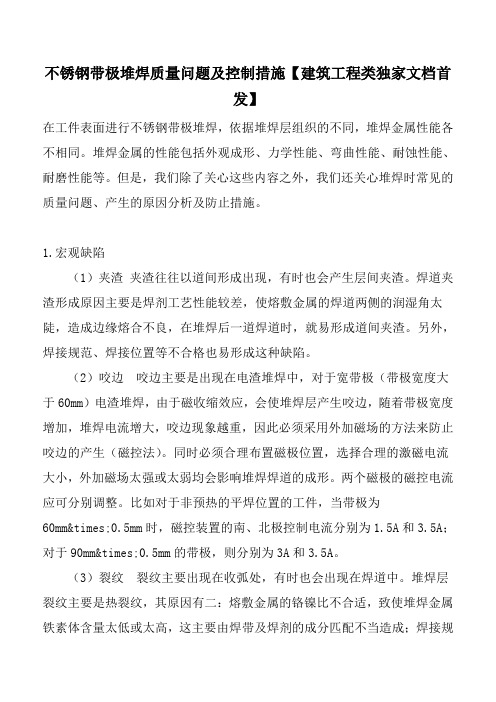
不锈钢带极堆焊质量问题及控制措施【建筑工程类独家文档首发】在工件表面进行不锈钢带极堆焊,依据堆焊层组织的不同,堆焊金属性能各不相同。
堆焊金属的性能包括外观成形、力学性能、弯曲性能、耐蚀性能、耐磨性能等。
但是,我们除了关心这些内容之外,我们还关心堆焊时常见的质量问题、产生的原因分析及防止措施。
1.宏观缺陷(1)夹渣夹渣往往以道间形成出现,有时也会产生层间夹渣。
焊道夹渣形成原因主要是焊剂工艺性能较差,使熔敷金属的焊道两侧的润湿角太陡,造成边缘熔合不良,在堆焊后一道焊道时,就易形成道间夹渣。
另外,焊接规范、焊接位置等不合格也易形成这种缺陷。
(2)咬边咬边主要是出现在电渣堆焊中,对于宽带极(带极宽度大于60mm)电渣堆焊,由于磁收缩效应,会使堆焊层产生咬边,随着带极宽度增加,堆焊电流增大,咬边现象越重,因此必须采用外加磁场的方法来防止咬边的产生(磁控法)。
同时必须合理布置磁极位置,选择合理的激磁电流大小,外加磁场太强或太弱均会影响堆焊焊道的成形。
两个磁极的磁控电流应可分别调整。
比如对于非预热的平焊位置的工件,当带极为60mm×0.5mm时,磁控装置的南、北极控制电流分别为1.5A和3.5A;对于90mm×0.5mm的带极,则分别为3A和3.5A。
(3)裂纹裂纹主要出现在收弧处,有时也会出现在焊道中。
堆焊层裂纹主要是热裂纹,其原因有二:熔敷金属的铬镍比不合适,致使堆焊金属铁素体含量太低或太高,这主要由焊带及焊剂的成分匹配不当造成;焊接规范不当,电流过大也易造成热裂纹。
(4)未熔合堆焊层与母材间结合面或层间易出现未熔合现象,由于烧结型焊剂比熔炼型焊剂堆焊重量轻,故熔深比较小。
一旦操作不当或焊接规范参数掌握不适,易出现结合面未熔合或层间未熔合缺陷。
上面介绍了常见宏观缺陷及防止措施,除此之外,在实际产品堆焊时,还应注意以下几点。
一是焊前严格对母材打磨,去除铁锈、油污等影响焊接的因素且必须预热。
不锈钢焊接工艺要点和注意事项

不锈钢焊接工艺要点和注意事项一、不锈钢焊接工艺要点:1.选择合适的焊接方法:不锈钢焊接常用的方法包括手工电弧焊、氩弧焊、TIG焊、MIG/MAG焊等,选择适合的焊接方法可以根据具体需求进行判断。
2.选择合适的焊接材料:不锈钢的焊接材料要和母材具有一致的化学成分、冶金性能和耐蚀性能,以保证焊接接头的质量。
3.确保焊接面干净:在焊接之前,要保证焊接面的干净度,通过刮除氧化层、油脂和其他杂质,可以使用酸性或碱性清洗剂进行清洗。
4.控制焊接参数:控制焊接电流、电压、焊接速度等参数,以保证焊接过程中的熔融状态和热输入量,避免产生过多的热应力。
5.合理选择焊接顺序:大型不锈钢构件的焊接顺序要循序渐进,避免热应力的集中和变形的发生。
6.控制焊接热输入:避免产生过多的热应力,可以采取预热、焊接层间温度控制、控制冷却速度等措施。
7.合理选用填充材料:对于一些不锈钢材料,需要选用添加元素的填充材料,以提高焊接接头的强度和耐蚀性。
8.保持密封性:焊接过程中要保持密封性,避免空气进入焊接接头,以避免氧化和腐蚀。
二、不锈钢焊接的注意事项:1.防止氧化:不锈钢焊接过程中需要避免氧化,可以使用保护性气体如氩气进行保护,避免氧气进入焊接接头。
2.注意预热和后热处理:尤其是对于厚板材料和高合金不锈钢,预热和后热处理非常重要,可以减少热应力和残余应力,提高焊接接头的强度和耐蚀性。
3.控制焊接变形:不锈钢焊接容易发生变形,可以通过控制焊接顺序和方法,以及使用临时支架等方法来减少变形。
4.注意焊接序列和方向:焊接接头的序列和方向应当遵循一定的原则,避免产生过多的焊缝和热应力集中。
5.合理选择气体保护:不锈钢焊接过程中,选择合适的气体保护有助于减少氧化和减少焊缝材料中的杂质。
6.细节处理:对于不锈钢焊接接头的边缘和焊缝部分,需要进行细致的处理,保证其质量和耐蚀性。
7.严格控制焊接质量:不锈钢焊接的质量直接影响其耐蚀性能,需要严格控制焊接质量,特别是焊接接头的表面质量和焊缝的性能。
氩弧焊焊接不锈钢质量问题报告

氩弧焊焊接不锈钢质量问题分析报告1. 引言1.1 报告目的和范围本报告旨在系统地分析和识别在采用氩弧焊技术焊接不锈钢过程中遭遇的质量问题。
通过对焊接过程的细致审查,本报告将揭示影响焊接质量的关键因素,并提供相应的解决策略。
研究范围涵盖了从材料选择、设备条件到操作技巧等多个方面,以确保全面覆盖可能导致质量问题的各个环节。
1.2 氩弧焊技术概述氩弧焊是一种广泛应用于不锈钢焊接的精密焊接技术。
它使用惰性气体氩作为保护气体,以防止焊接区域与大气中的氧气、氮气和其他有害气体反应,从而保持焊缝的纯净度和机械性能。
该技术适用于各种不锈钢材料,并且能够实现高质量的焊接效果,因此在制造业和维修业中占有重要地位。
1.3 不锈钢焊接的重要性不锈钢因其优异的耐腐蚀性、高温强度和良好的机械性能而被广泛用于多个行业,如化工、食品加工、医疗器械和建筑等。
在这些应用中,焊接作为连接不锈钢结构的主要手段,其质量直接关系到产品的安全、可靠性和寿命。
因此,确保焊接过程的质量至关重要,这不仅涉及到生产效率,更关乎最终产品的品质和用户的安全。
2. 材料与方法2.1 焊接材料的选择在本研究中,选用的不锈钢材料为AISI 304型号,这是一种广泛应用的奥氏体不锈钢,具有良好的综合性能,包括优秀的耐腐蚀性和成形性。
化学成分主要包括铬、镍等合金元素,这些成分共同赋予材料其特有的性能。
为了确保焊接质量,所有材料在使用前都经过了严格的质量检验,以排除材料缺陷对焊接质量的潜在影响。
2.2 氩弧焊设备及参数设置氩弧焊设备采用的是最新型号的自动焊机,该设备具备高精度的电流和电压控制系统,能够保证焊接过程中的稳定性。
焊机配备有先进的气体保护系统,确保焊缝区域在整个焊接过程中得到充分保护,避免氧化和污染。
参数设置方面,根据不锈钢材料的厚度和所需的焊缝性能,精心调整了电流强度、焊接速度和气体流量等关键参数,以达到最佳的焊接效果。
2.3 焊接过程描述焊接过程遵循了标准化的操作流程。
不锈钢焊接工艺及变形控制

管理及其他M anagement and other不锈钢焊接工艺及变形控制高艳华摘要:在当前工业生产过程中,不锈钢焊接工艺最常被采用,其焊接技术水平对于不锈钢产品的质量影响是直接的。
所以本文中首先讨论了不锈钢焊接工艺基本操作方法与相关焊接变形控制要点。
并结合某D工业生产企业分析了企业工厂内部的不锈钢焊接工艺技术要点,分析导致D工业生产企业中不锈钢焊接变形的重要原因,最后对企业不锈钢焊接技术及其变形控制的重要措施进行了全面剖析。
关键词:不锈钢焊接工艺;变形控制;原因;技术要点;误差不锈钢材料本身具有强耐腐蚀性,因此,它被广泛用于制造应用,例如家庭和工业应用。
不锈钢的焊接技术非常复杂,它确保不锈钢产品的应用范围进一步被扩大,因此,焊接技术已经非常频繁地用于生产过程中。
在焊接过程中,不锈钢部件在相对较短的时间内迅速产生大量热量。
如果散热不好,会造成不锈钢元件严重变形,长此以往不锈钢构件在生产过程中就会出现负面影响。
为此,必须要加强不锈钢的焊接工艺,主要对其变形控制问题进行科学合理分析。
1 不锈钢焊接工艺的具体操作方法根据现有技术,焊接不锈钢的方法有3种:第一种是手工电弧焊(SMAW),主要是利用手工操纵焊条进行焊接,也被称之为“手弧焊”。
手弧焊机方法主要将焊条与焊件作为两端电极,而被焊接金属则被称为焊件或母材。
在焊接过程中由于电弧温度高、吹力作用大、所以能够使得局部焊件被熔化,形成凹坑,这一凹坑被称之为“熔池”。
换言之,这就是在焊件表面到熔池底部的距离,熔池的深度被称为“熔透深度”。
手工电弧焊操作方法简单,它在特定的生产和应用过程中最为常见。
它主要在焊接操作中使用直流电,电极为非合金或合金金属电极和芯线。
一般电极是可以作为焊缝MIG展开焊接操作的,即第二种不锈钢焊接操作方法——熔化极气体保护焊MAG/MIG焊接,这种焊接方法是一种自动气体保护电弧焊方法。
具体工作过程还应采用平板式焊接电源,电压应调至弧长4~6mm左右。
浅谈不锈钢管道焊接施工的质量控制
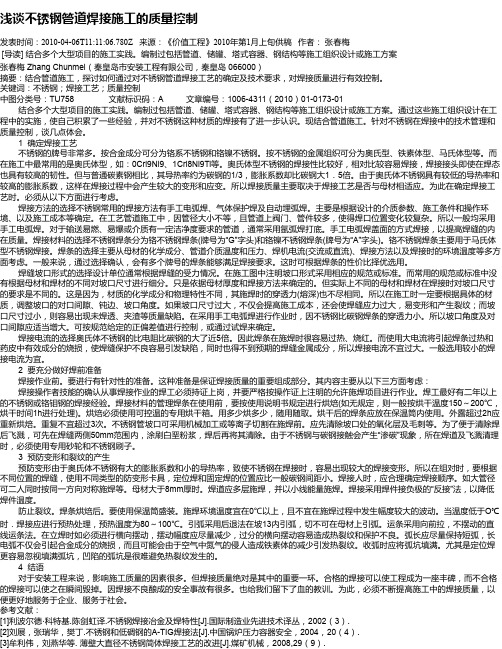
浅谈不锈钢管道焊接施工的质量控制发表时间:2010-04-06T11:11:06.780Z 来源:《价值工程》2010年第1月上旬供稿作者:张春梅[导读] 结合多个大型项目的施工实践。
编制过包括管道、储罐、塔式容器、钢结构等施工组织设计或施工方案张春梅 Zhang Chunmei(秦皇岛市安装工程有限公司,秦皇岛 066000)摘要:结合管道施工,探讨如何通过对不锈钢管道焊接工艺的确定及技术要求,对焊接质量进行有效控制。
关键词:不锈钢;焊接工艺;质量控制中图分类号:TU758 文献标识码:A 文章编号:1006-4311(2010)01-0173-01 结合多个大型项目的施工实践。
编制过包括管道、储罐、塔式容器、钢结构等施工组织设计或施工方案。
通过这些施工组织设计在工程中的实施,使自己积累了一些经验,并对不锈钢这种材质的焊接有了进一步认识。
现结合管道施工。
针对不锈钢在焊接中的技术管理和质量控制,谈几点体会。
1 确定焊接工艺不锈钢的牌号非常多。
按合金成分可分为铬系不锈钢和铬镍不锈钢。
按不锈钢的金属组织可分为奥氏型、铁素体型、马氏体型等。
而在施工中最常用的是奥氏体型,如:0Crl9Ni9、1Crl8Ni9Ti等。
奥氏体型不锈钢的焊接性比较好,相对比较容易焊接,焊接接头即使在焊态也具有较高的韧性。
但与普通碳素钢相比,其导热率约为碳钢的1/3,膨胀系数却比碳钢大1.5倍。
由于奥氏体不锈钢具有较低的导热率和较高的膨胀系数,这样在焊接过程中会产生较大的变形和应变。
所以焊接质量主要取决于焊接工艺是否与母材相适应。
为此在确定焊接工艺时。
必须从以下方面进行考虑。
焊接方法的选择不锈钢常用的焊接方法有手工电弧焊、气体保护焊及自动埋弧焊。
主要是根据设计的介质参数、施工条件和操作环境、以及施工成本等确定。
在工艺管道施工中,因管径大小不等,且管道上阀门、管件较多,使得焊口位置变化较复杂。
所以一般均采用手工电弧焊。
对于输送易燃、易爆或介质有一定洁净度要求的管道,通常采用氩弧焊打底。
不锈钢焊缝分级

不锈钢焊缝分级:根据外观质量,不锈钢焊缝分为一级、二级和三级。
一级焊缝要求对“每条焊缝长度的100%”进行超声波探伤;
二级焊缝要求对“每条焊缝长度的20%”进行抽检,且不小于200mm进行超声波探伤。
一级、二级焊缝均为全焊透的焊缝,并不允许存在如表面气孔、夹渣、弧坑裂纹、电弧檫伤等缺陷。
一级、二级焊缝的抗拉压、抗弯、抗剪强度均与母材相同三级质量检查只对全部焊缝进行外观缺陷及几何尺寸检查,其外观可见缺陷及几何尺寸偏差必须符合三级合格标准要求;二级质量检查除对外观进行检查并达到二级质量合格标准外,还需用超声波或射线探伤20%焊缝,达到B级检验Ⅲ级合格要求;一级质量检查除外观进行检查并符合一级合格标准外,还需用超声波或射线对焊缝100%探伤,达到B级检验Ⅱ级合格要求。
焊接质量改进措施

焊接质量改进措施1、电压表、电流表指示不正确,致使电压、电流过大,应即时更换电压表和电流表。
2、坡口生锈后应打磨,否则焊接容易产生气孔。
3、板间对口间隙应控制在1~2mm,否则焊接容易产生未焊透。
4、不锈钢焊接与碳钢相比,电压、电流应小10%。
5、焊缝余高应控制在15%δ。
6、引弧与收弧:应在引弧板或坡口引弧,禁止在非焊接部位引弧,焊缝应在收弧板上收弧,弧坑应填满。
7、防止打弧:应防止地线、电源线、焊钳与焊件打弧。
8、弧坑的打磨与补焊:电弧擦伤处的弧坑需经打磨,使其均匀过渡到母材厚度小于规定值时,则需补焊。
9、受压角焊缝:其根部应保证焊透,焊脚应符合要求:(1)δ≤12,自动焊焊脚:0~4mm;手动焊焊脚:0~1.5mm。
(2)12<δ≤25,自动焊焊脚:0~4mm;手动焊焊脚:0~1.5mm。
10、清根:双面焊要求清理焊根,显露出正面打底的焊缝金属,对于自动焊,若经试验确认能保证焊透,也可不作清根处理。
11、接弧处的要求:应保证焊透和熔合。
12、层间温度:施焊过程中应控制层间温度不超过规定的围,对焊件预热时,应控制层间温度不低于预热温度。
13、中断焊接时的要求:每条焊缝应尽一次焊完,当中断焊接时,对冷裂纹敏感的焊件应及时采取后热、缓冷等措施.重新焊接时,仍需按规定进行预热。
14、改善焊接质量的锤击:需采用锤击改善焊接质量时,第一层焊缝和盖面层焊缝不宜锤击。
15、引弧板、引出板及试板的去板:引弧板、引出板、产品焊接试板和焊接工艺纪律检查试板不应锤击打落。
16、焊接时应随时磕渣,否则焊接容易产生夹渣。
17、焊速不应过快,否则容易产生未焊透、夹渣等缺陷。
18、焊一道工序前应考虑下一道工序。
19、二保焊手法应从右向左,而手工焊应从左向右。
20、焊接薄板时,应采用二保焊点焊,不仅焊接不变形,而且焊缝很美观。
21、焊工应有爱岗敬业的精神。
不锈钢管道焊接要求规范

不锈钢管道焊接要求规范首先,对于不锈钢管道焊接,需要使用合适的焊接工艺和设备。
选择合适的焊接方法,如TIG焊、MIG/MAG焊等,并确保手持焊接工具的质量和状态良好,以避免出现焊接质量不良的情况。
其次,焊接前应对管道进行清洁和预处理。
先使用溶剂或酸性清洗剂对管道进行清洗,去除表面的油污、氧化层等,确保焊接区域的干净。
然后进行机械处理,如刮砂、研磨等,以提高接头的质量。
接着,需要选择合适的焊接材料。
在不锈钢管道的焊接中,一般采用相同或类似的不锈钢材料作为填充材料,以确保焊缝的强度和耐腐蚀性与基材一致。
同时,还需要注意材料的质量和充分的保质期。
在进行焊接前,需要进行焊前检查和准备。
焊接前应对焊缝进行检查,包括焊缝的几何尺寸、间隙、孔隙、裂纹等缺陷,确保焊接区域的质量。
同时要对管道进行固定,以避免在焊接过程中发生位移。
焊接过程中,需要注意控制焊接参数和采取适当的预热和后热处理。
控制焊接电流、电压、速度等参数,以保证焊缝的质量和强度。
对于不锈钢管道,一般需要进行适当的预热和后热处理,以减少焊接应力和提高焊缝的质量。
焊接完成后,需要进行焊后检查和清理。
对焊缝进行目测和无损检测,检查焊缝的外观和内部缺陷,以确保焊接质量。
同时,还需要清理焊后的残渣和焊接区域的杂物,防止对管道的使用产生不良影响。
最后,对焊接过程进行记录和档案管理。
记录焊接的参数、材料、检查结果等信息,以备将来的跟踪和追溯。
对于重要的管道焊接,还需要制定相关的焊接规程和手册,供操作人员参考和遵守。
综上所述,不锈钢管道焊接需要遵循一系列的规范和要求,包括选择合适的焊接工艺和设备、进行焊前准备和检查、控制焊接参数和进行预热后热处理、进行焊后检查和清理等。
只有遵守这些规范和要求,才能保证不锈钢管道焊接的质量和安全性。
不锈钢板材焊接要求
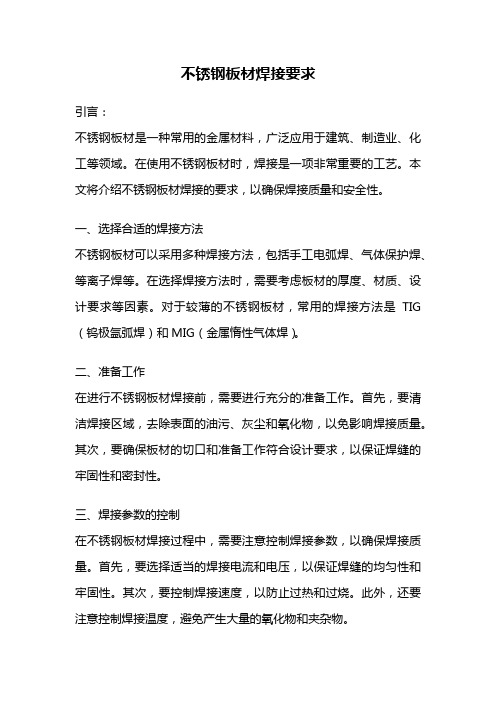
不锈钢板材焊接要求引言:不锈钢板材是一种常用的金属材料,广泛应用于建筑、制造业、化工等领域。
在使用不锈钢板材时,焊接是一项非常重要的工艺。
本文将介绍不锈钢板材焊接的要求,以确保焊接质量和安全性。
一、选择合适的焊接方法不锈钢板材可以采用多种焊接方法,包括手工电弧焊、气体保护焊、等离子焊等。
在选择焊接方法时,需要考虑板材的厚度、材质、设计要求等因素。
对于较薄的不锈钢板材,常用的焊接方法是TIG (钨极氩弧焊)和MIG(金属惰性气体焊)。
二、准备工作在进行不锈钢板材焊接前,需要进行充分的准备工作。
首先,要清洁焊接区域,去除表面的油污、灰尘和氧化物,以免影响焊接质量。
其次,要确保板材的切口和准备工作符合设计要求,以保证焊缝的牢固性和密封性。
三、焊接参数的控制在不锈钢板材焊接过程中,需要注意控制焊接参数,以确保焊接质量。
首先,要选择适当的焊接电流和电压,以保证焊缝的均匀性和牢固性。
其次,要控制焊接速度,以防止过热和过烧。
此外,还要注意控制焊接温度,避免产生大量的氧化物和夹杂物。
四、保护气体的选择在不锈钢板材焊接过程中,保护气体是非常重要的。
常用的保护气体有氩气、氩气和氢气混合物等。
保护气体可以防止焊接区域与空气接触,避免氧化和污染,提高焊缝的质量和密封性。
五、焊接后的处理焊接完成后,需要进行适当的后处理工作。
首先,要清理焊接区域,去除焊渣和氧化物。
其次,要对焊缝进行检测,以确保焊接质量。
最后,要进行表面处理,使焊接区域与周围的不锈钢板材表面达到一致,提高整体美观度。
六、注意安全事项在进行不锈钢板材焊接时,要注意安全事项。
首先,要佩戴适当的个人防护装备,包括焊接面具、手套、防护服等。
其次,要确保焊接区域通风良好,以防止有害气体积聚。
最后,要遵循焊接操作规程,避免发生意外事故。
结论:不锈钢板材焊接是一项重要的工艺,需要遵循一定的要求和步骤。
选择合适的焊接方法、进行充分的准备工作、控制焊接参数、选择适当的保护气体、进行焊后处理以及注意安全事项,都是确保不锈钢板材焊接质量和安全性的关键。
不锈钢焊接技术相关标准及要求
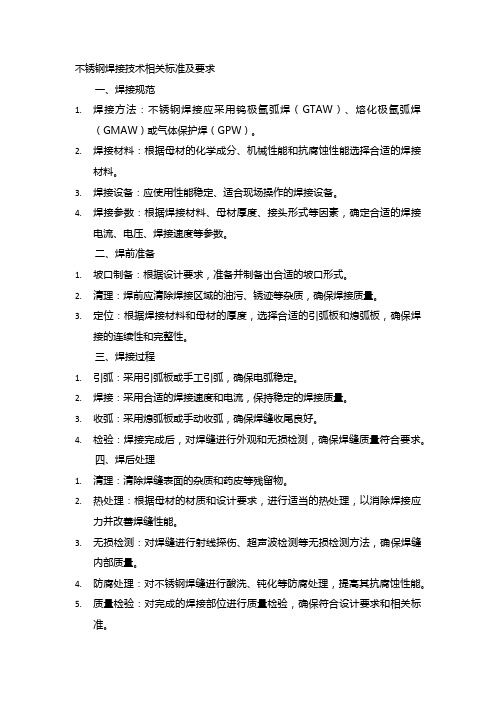
不锈钢焊接技术相关标准及要求
一、焊接规范
1.焊接方法:不锈钢焊接应采用钨极氩弧焊(GTAW)、熔化极氩弧焊
(GMAW)或气体保护焊(GPW)。
2.焊接材料:根据母材的化学成分、机械性能和抗腐蚀性能选择合适的焊接
材料。
3.焊接设备:应使用性能稳定、适合现场操作的焊接设备。
4.焊接参数:根据焊接材料、母材厚度、接头形式等因素,确定合适的焊接
电流、电压、焊接速度等参数。
二、焊前准备
1.坡口制备:根据设计要求,准备并制备出合适的坡口形式。
2.清理:焊前应清除焊接区域的油污、锈迹等杂质,确保焊接质量。
3.定位:根据焊接材料和母材的厚度,选择合适的引弧板和熄弧板,确保焊
接的连续性和完整性。
三、焊接过程
1.引弧:采用引弧板或手工引弧,确保电弧稳定。
2.焊接:采用合适的焊接速度和电流,保持稳定的焊接质量。
3.收弧:采用熄弧板或手动收弧,确保焊缝收尾良好。
4.检验:焊接完成后,对焊缝进行外观和无损检测,确保焊缝质量符合要求。
四、焊后处理
1.清理:清除焊缝表面的杂质和药皮等残留物。
2.热处理:根据母材的材质和设计要求,进行适当的热处理,以消除焊接应
力并改善焊缝性能。
3.无损检测:对焊缝进行射线探伤、超声波检测等无损检测方法,确保焊缝
内部质量。
4.防腐处理:对不锈钢焊缝进行酸洗、钝化等防腐处理,提高其抗腐蚀性能。
5.质量检验:对完成的焊接部位进行质量检验,确保符合设计要求和相关标
准。
双相不锈钢的焊接技巧和要点
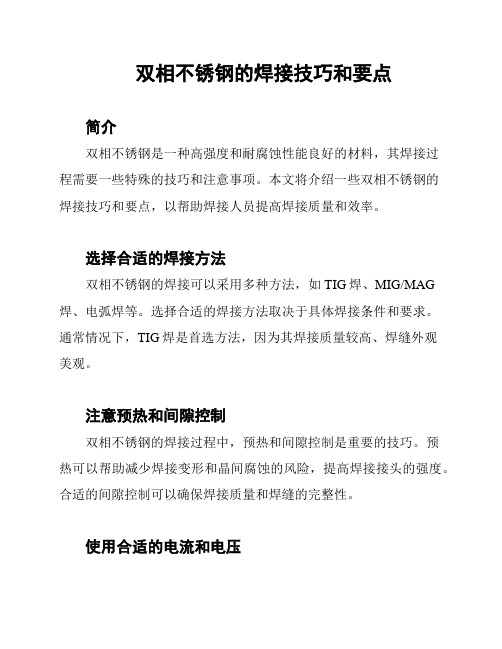
双相不锈钢的焊接技巧和要点简介双相不锈钢是一种高强度和耐腐蚀性能良好的材料,其焊接过程需要一些特殊的技巧和注意事项。
本文将介绍一些双相不锈钢的焊接技巧和要点,以帮助焊接人员提高焊接质量和效率。
选择合适的焊接方法双相不锈钢的焊接可以采用多种方法,如TIG焊、MIG/MAG 焊、电弧焊等。
选择合适的焊接方法取决于具体焊接条件和要求。
通常情况下,TIG焊是首选方法,因为其焊接质量较高、焊缝外观美观。
注意预热和间隙控制双相不锈钢的焊接过程中,预热和间隙控制是重要的技巧。
预热可以帮助减少焊接变形和晶间腐蚀的风险,提高焊接接头的强度。
合适的间隙控制可以确保焊接质量和焊缝的完整性。
使用合适的电流和电压选择合适的电流和电压是双相不锈钢焊接中的关键。
过高的电流和电压会导致焊接区域过热,产生气孔和裂纹。
而过低的电流和电压则可能导致焊接不充分,影响焊缝质量。
根据焊接规范和试验结果确定合适的电流和电压范围。
使用适合的焊接材料双相不锈钢的焊接通常需要使用相同或相似成分的焊接材料,以确保焊接接头的性能和腐蚀性能与基材一致。
同时,选择合适的焊接材料可以有效降低焊接变形和裂纹风险。
控制焊接速度和焊接参数在焊接双相不锈钢时,控制焊接速度和焊接参数是非常重要的。
过高的焊接速度可能导致焊缝质量不佳,而过低的焊接速度则可能引起过热和热影响区过大。
根据焊接试验和经验,控制合适的焊接速度和参数,以获得最佳的焊接质量。
注意焊后处理焊接完成后,及时进行焊后处理是确保焊接质量的重要环节。
焊后处理包括去除焊渣、清理焊缝、消除应力、进行表面处理等。
正确的焊后处理可以提高焊接接头的性能和耐腐蚀性。
结论双相不锈钢的焊接需要一些特殊的技巧和要点,我们应该选择合适的焊接方法,注意预热和间隙控制,使用适合的电流和电压,选择合适的焊接材料,控制焊接速度和焊接参数,以及进行正确的焊后处理。
通过遵循这些技巧和要点,我们可以提高双相不锈钢焊接的质量和效率。
以上为双相不锈钢的焊接技巧和要点,希望能对您有所帮助。
核电站大口径不锈钢薄壁管焊接质量控制

核电站大口径不锈钢薄壁管焊接质量控制摘要:现阶段,随着现代化建设的发展,我国的科学技术的发展也越来越完善。
大口径(6″及以上)不锈钢薄壁管道广泛用于核电站辅助系统,壁厚大多为3.05~4.78mm。
根据RCC-M2000+2002补遗S7436规范要求,打底焊至5mm前,背部需建立并维持良好的氩气室以保护焊缝背部,避免焊接时氧化、发渣。
在核电维修中,由于管道管径大且管道内有残水、风压等,导致氩气保护效果差,因管道的管壁较薄容易出现变形和错边、打底焊接易出现缺陷等原因,导致薄壁不锈钢在役维修焊接过程中常出现焊缝无损检测不合格,从而导致耽误大修关键路径的情况。
因此,针对大口径不锈钢薄壁管焊接的技术特点,制定有效的质量控制手段,确保焊接质量,保障核电机组的安全可靠运行。
关键词:核电站大口径;不锈钢薄壁管;焊接质量控制引言不锈钢薄壁管道广泛用于核电站辅助管道系统,是在役核电维修中的重要项目,其焊接质量直接影响核电的运行质量。
在役核电站维修中对于大口径不锈钢薄壁管道的焊接存在充氩困难、管道变形、根部氧化等问题。
重点论述了通过氩气室的选择和效果验证、使用合适的管道组对方法和采用合适的焊接方法和工艺参数,以及焊接过程中的关键点验证,能够确保大口径不锈钢薄壁管的焊接质量,并在中广核多个电站机组大修中得到应用,具有良好的适用性。
1大口径薄壁不锈钢管道在役焊接难点1.1充氩对于大口径薄壁不锈钢管道焊接,充氩效果的好坏直接影响焊接质量,而充氩效果受氩气室的布置、系统压力、充氩点、潮气等多种因素影响。
由于大口径薄壁不锈钢管道的氩气室的空间大,所需充氩时间长,而氩气内腔越大,充氩保护效果越不明显,尤其是在相连管线复杂的情况下,系统可能存在的负压/正压等情况均会导致氩气室难以建立并长期维持稳定;另外在核电维修过程中,受制于系统运行条件,运行后管道中可能存在残水,充氩及排气点的选择也是充氩效果的制约因素之一;充氩效果不佳时,焊接过程中易出现背部发渣、未熔合、未焊透等缺陷,从而直接影响焊接质量。
不锈钢管道焊接出现的常见问题
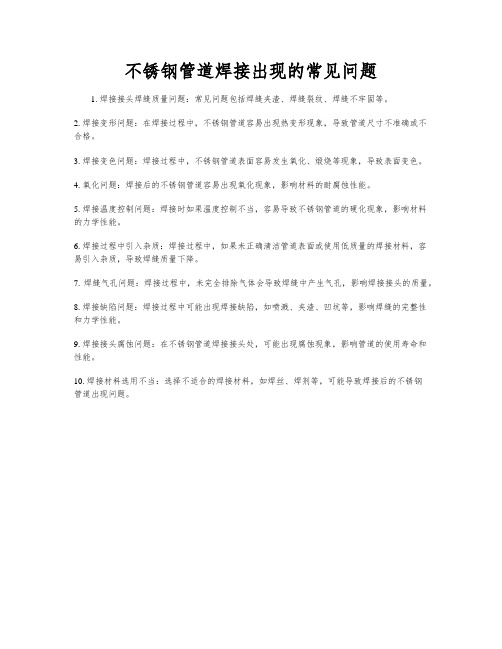
不锈钢管道焊接出现的常见问题
1. 焊接接头焊缝质量问题:常见问题包括焊缝夹渣、焊缝裂纹、焊缝不牢固等。
2. 焊接变形问题:在焊接过程中,不锈钢管道容易出现热变形现象,导致管道尺寸不准确或不
合格。
3. 焊接变色问题:焊接过程中,不锈钢管道表面容易发生氧化、煅烧等现象,导致表面变色。
4. 氧化问题:焊接后的不锈钢管道容易出现氧化现象,影响材料的耐腐蚀性能。
5. 焊接温度控制问题:焊接时如果温度控制不当,容易导致不锈钢管道的硬化现象,影响材料
的力学性能。
6. 焊接过程中引入杂质:焊接过程中,如果未正确清洁管道表面或使用低质量的焊接材料,容
易引入杂质,导致焊缝质量下降。
7. 焊缝气孔问题:焊接过程中,未完全排除气体会导致焊缝中产生气孔,影响焊接接头的质量。
8. 焊接缺陷问题:焊接过程中可能出现焊接缺陷,如喷溅、夹渣、凹坑等,影响焊缝的完整性
和力学性能。
9. 焊接接头腐蚀问题:在不锈钢管道焊接接头处,可能出现腐蚀现象,影响管道的使用寿命和
性能。
10. 焊接材料选用不当:选择不适合的焊接材料,如焊丝、焊剂等,可能导致焊接后的不锈钢
管道出现问题。
不锈钢结构焊接质量缺陷及处理方法

不锈钢结构焊接质量缺陷及处理方法
引言
不锈钢结构在工程领域中扮演着重要的角色,而焊接是不锈钢
结构加工中最常用的方法之一。
然而,焊接过程中可能会出现质量
缺陷,这些缺陷对结构的强度和耐久性产生不利影响。
因此,了解
焊接质量缺陷的种类和处理方法至关重要。
焊接质量缺陷分类
1. 气孔:焊接过程中由于气体未完全排出而形成的孔洞。
气孔
会降低焊缝的强度和密封性。
2. 夹渣:焊接过程中未将杂质和氧化物排除导致的夹在焊缝中
的残渣。
夹渣会导致焊缝表面不平整并减弱焊缝的强度。
3. 裂纹:焊接过程中因应力集中而导致的开裂。
裂纹可能出现
在焊缝或母材中,对结构造成严重损坏。
4. 错边:焊接过程中,焊缝没有完全覆盖母材边缘形成的瑕疵。
错边会降低焊缝的强度和密封性。
处理方法
1. 气孔:采取良好的焊接工艺并控制焊接参数,如合适的焊接速度和电流。
使用合适的气体或气体混合物来防止气孔的形成。
2. 夹渣:使用适当的焊接工艺,确保焊缝与母材之间的接触面干净,并避免杂质和氧化物的进入。
3. 裂纹:通过控制应力和预热焊接部位来减少应力集中。
选择合适的焊接材料和焊接方法,以减少裂纹的形成。
4. 错边:确保焊缝完全覆盖母材边缘,可采用合适的焊接工艺和角度,并进行适当的焊后处理。
结论
不锈钢结构焊接质量缺陷的处理方法多种多样,关键在于采取合适的焊接工艺和控制焊接参数。
通过了解质量缺陷的分类和处理方法,可以确保不锈钢结构焊接的质量和耐久性,从而有效提高工程项目的安全性和可靠性。
不锈钢管焊接工艺及检验

不锈钢管焊接工艺及检验一、引言不锈钢管是一种广泛应用于工业领域的管材,其焊接工艺及检验对于保证管道质量和安全具有重要意义。
本文将从焊接工艺和检验两个方面进行介绍和分析。
二、不锈钢管焊接工艺1. 焊接方法不锈钢管的焊接方法主要包括手工电弧焊、氩弧焊和等离子焊。
其中,手工电弧焊是常用的焊接方法,适用于小口径、低压力的管道焊接;氩弧焊适用于对焊缝质量要求较高的场合;等离子焊适用于大口径、厚壁不锈钢管的焊接。
2. 焊接参数在不锈钢管的焊接过程中,焊接参数的选择对于焊缝质量具有重要影响。
焊接参数包括焊接电压、电流、焊接速度等。
合理选择焊接参数可以保证焊接质量,避免焊接缺陷的产生。
3. 焊接材料不锈钢管的焊接材料通常是与管材相同或相似的不锈钢焊条。
选择合适的焊接材料可以保证焊缝的耐腐蚀性和力学性能与管材一致。
4. 焊接工艺控制在不锈钢管的焊接过程中,需要控制好工艺参数,避免焊接缺陷的产生。
例如,在焊接过程中要控制好焊接电流、焊接速度和焊接温度,避免过热或过冷引起的焊接缺陷。
三、不锈钢管焊接检验1. 可视检验可视检验是不锈钢管焊接工艺中常用的一种检验方法。
通过对焊缝外观的观察,可以判断焊缝是否存在裂纹、气孔、夹渣等缺陷。
2. 射线检测射线检测是一种常用的无损检测方法,可以用于检测不锈钢管焊缝内部的缺陷。
通过将射线通过焊缝,利用射线的吸收和散射情况来判断焊缝是否存在缺陷。
3. 超声波检测超声波检测是一种常用的无损检测方法,可以用于检测不锈钢管焊缝的内部和表面缺陷。
通过超声波的传播和反射情况来判断焊缝是否存在缺陷。
4. 磁粉检测磁粉检测是一种常用的表面缺陷检测方法,适用于检测不锈钢管焊缝表面的裂纹、夹渣等缺陷。
通过在焊缝表面涂上磁粉,利用磁粉的吸附和聚集情况来判断焊缝是否存在缺陷。
四、结论不锈钢管的焊接工艺及检验对于保证管道质量和安全具有重要意义。
合理选择焊接方法、控制焊接参数和选择合适的焊接材料可以保证焊接质量;可视检验、射线检测、超声波检测和磁粉检测是常用的焊接检验方法,可以有效地检测焊缝的质量和缺陷。
关于不锈钢焊缝开裂质量报告整改方案

关于不锈钢焊缝开裂质量报告整改方案一、引言不锈钢焊缝开裂是焊接过程中常见的质量问题之一,其可能导致焊接件的强度和密封性下降,进而影响整体工程质量。
本文针对不锈钢焊缝开裂质量问题,提出了一套整改方案,旨在解决该问题并提升焊接质量。
二、问题分析不锈钢焊缝开裂主要有以下几个原因:1. 焊接参数不合理:焊接过程中,焊接电流、电压、焊接速度等参数的不合理选择可能导致焊缝过热或过冷,从而引发开裂问题。
2. 焊接材料质量问题:不锈钢焊接材料的质量差异会对焊缝的开裂倾向产生影响,如硫含量过高、杂质过多等。
3. 焊接工艺不当:焊接工艺中的预热、间隙控制、焊接顺序等环节若处理不当,也可能导致焊缝开裂。
4. 焊接环境不良:焊接环境中存在的氧气、水分等会对焊接质量产生不良影响,如生成气孔、氧化等,从而增加焊缝开裂的风险。
三、整改方案为解决不锈钢焊缝开裂质量问题,我们提出以下整改方案:1. 优化焊接参数:根据不同焊接材料和工件厚度,合理选择焊接电流、电压和焊接速度,确保焊接过程中的热输入均匀分布,避免焊缝过热或过冷。
2. 选择高质量的焊接材料:选用低硫、低杂质的不锈钢焊接材料,确保焊缝的质量稳定性和可靠性。
3. 优化焊接工艺:合理控制焊接预热温度和间隙,采用适当的焊接顺序,确保焊接过程中的温度梯度适中,避免焊缝开裂的风险。
4. 提升焊接环境:优化焊接环境,减少氧气和水分的存在,采取防护措施,避免氧化和气孔等不良现象的发生。
四、实施步骤1. 设立焊接参数优化小组:由焊接工程师、质量工程师和工艺工程师组成,共同制定焊接参数优化方案。
2. 选用高质量焊接材料:与供应商保持密切合作,选择低硫、低杂质的不锈钢焊接材料,并进行质量监控。
3. 优化焊接工艺:根据焊接材料和工件的特性,制定焊接工艺文件,明确焊接顺序、预热温度和间隙要求,并进行工艺验证。
4. 完善焊接环境:改善焊接工作区域的通风设施,减少氧气和水分的存在,防止不良环境对焊接质量的影响。
不锈钢焊接层间温度控制

不锈钢焊接层间温度控制摘要:一、不锈钢焊接的重要性二、层间温度的控制方法1.控制层间温度的标准2.控制层间温度的实际操作方法三、层间温度控制的重要性1.对焊接质量的影响2.对焊接材料的影响四、如何有效控制层间温度1.选择合适的焊接方法2.控制焊接电流和电压3.焊接过程中的实时监测五、总结正文:不锈钢焊接是各种行业中常见的工艺过程,其质量直接影响到焊接件的使用寿命和性能。
在焊接过程中,层间温度的控制是一个至关重要的环节。
如果层间温度过高或过低,都可能影响到焊接质量。
因此,掌握合适的层间温度控制方法,对于提高焊接质量具有重要的意义。
一般来说,按照通常的不锈钢焊接规程,层间温度应控制在不超过60摄氏度。
这是因为,在不锈钢焊接过程中,层间温度过高会导致焊缝周围的材料发生晶粒长大,从而影响到焊接件的力学性能和耐腐蚀性。
反之,层间温度过低则会使得焊缝成型不良,容易出现夹渣、未熔合等焊接缺陷。
在实际操作中,控制层间温度的方式主要有以下几点:首先,选择合适的焊接方法。
不同的焊接方法对应的层间温度控制范围不同。
例如,TIG焊接和MIG焊接在不锈钢焊接中较为常见,其层间温度控制范围分别在60-100摄氏度和100-150摄氏度之间。
其次,控制焊接电流和电压。
焊接电流和电压的大小直接影响到焊接热量的大小,从而影响到层间温度。
一般来说,焊接电流和电压的增大,会使得焊接热量增加,层间温度升高。
因此,在焊接过程中,需要根据焊接材料和焊接厚度,合理选择焊接电流和电压,以达到合适的层间温度。
最后,焊接过程中的实时监测。
通过红外线测温仪等设备,实时监测焊接过程中的层间温度,并根据实际情况进行调整。
总的来说,层间温度的控制是不锈钢焊接过程中至关重要的一环。
只有通过合理的焊接方法、适当的焊接参数和实时的温度监测,才能确保焊接质量。
不锈钢焊缝处理要求
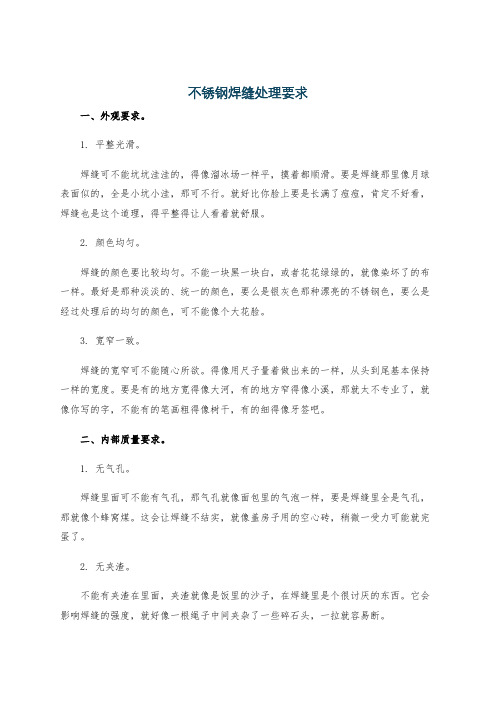
不锈钢焊缝处理要求一、外观要求。
1. 平整光滑。
焊缝可不能坑坑洼洼的,得像溜冰场一样平,摸着都顺滑。
要是焊缝那里像月球表面似的,全是小坑小洼,那可不行。
就好比你脸上要是长满了痘痘,肯定不好看,焊缝也是这个道理,得平整得让人看着就舒服。
2. 颜色均匀。
焊缝的颜色要比较均匀。
不能一块黑一块白,或者花花绿绿的,就像染坏了的布一样。
最好是那种淡淡的、统一的颜色,要么是银灰色那种漂亮的不锈钢色,要么是经过处理后的均匀的颜色,可不能像个大花脸。
3. 宽窄一致。
焊缝的宽窄可不能随心所欲。
得像用尺子量着做出来的一样,从头到尾基本保持一样的宽度。
要是有的地方宽得像大河,有的地方窄得像小溪,那就太不专业了,就像你写的字,不能有的笔画粗得像树干,有的细得像牙签吧。
二、内部质量要求。
1. 无气孔。
焊缝里面可不能有气孔,那气孔就像面包里的气泡一样,要是焊缝里全是气孔,那就像个蜂窝煤。
这会让焊缝不结实,就像盖房子用的空心砖,稍微一受力可能就完蛋了。
2. 无夹渣。
不能有夹渣在里面,夹渣就像是饭里的沙子,在焊缝里是个很讨厌的东西。
它会影响焊缝的强度,就好像一根绳子中间夹杂了一些碎石头,一拉就容易断。
3. 完全熔合。
焊接的地方得完全熔合在一起,就像两块巧克力融化后完美地融合成一块一样。
要是没有完全熔合,就好比两块拼图没拼好,中间有缝隙,那这个焊缝肯定不牢固,在使用过程中很容易出问题。
三、表面处理。
1. 清洁。
焊缝表面得干干净净的,不能有什么油污啊、铁锈啊之类的脏东西。
这就像你要洗脸一样,脸洗干净了才好看,焊缝也得把那些脏东西清理掉,这样它才能展现出不锈钢的那种光亮、干净的样子。
2. 必要时进行钝化处理。
如果需要的话,要做钝化处理。
这就像是给焊缝穿上一层保护膜,让它更耐腐蚀,就像给娇嫩的皮肤擦上防晒霜,防止被腐蚀这个“大太阳”给晒伤了。
- 1、下载文档前请自行甄别文档内容的完整性,平台不提供额外的编辑、内容补充、找答案等附加服务。
- 2、"仅部分预览"的文档,不可在线预览部分如存在完整性等问题,可反馈申请退款(可完整预览的文档不适用该条件!)。
- 3、如文档侵犯您的权益,请联系客服反馈,我们会尽快为您处理(人工客服工作时间:9:00-18:30)。
不锈钢焊缝内部质量控制
摘要:通过对不锈钢TP304/304焊接性分析,工艺措施、参数多次试验等,研究、制定合理的焊接工艺方法,控制焊缝内部成型质量,满足业主的特殊要求(内壁光滑、平齐),为
以后类似施工提供经验。
关键词:不锈钢304/304L 焊接工艺方法内部质量
1 前言
TP304/304L是美标的无缝或焊接不锈钢管,是近年新兴的一种奥氏体不锈钢材料,在生产304的同时,控制其中碳的含量,使其低于0.3%,所以在制造这种管材就标识为304/304L,表示这种材料既可以用作304使用也可以用作304L使用。
TP304/304L俗称双证钢,即耐腐蚀性满足304L 的要求,力学性能满足304的要求,取两种材料的优点,价格比304L 便宜较多,应用较广。
我单位承建的神华陕西甲醇下游加工项目聚丙烯装置,使用的不锈钢材质就是TP304/304L,其中有部分管道等级为3G2L-5X的不锈钢(设计压力2.77MPa,设计温度150℃,管径以4寸居多,介质为聚丙烯粉料),设计要求较高,要求100%RT且内壁必须平滑,业主对焊接质量控制较严,如何保证焊缝内部质量是施工的重点,我们经过多次焊接试验和培训,选取、制定了合适的焊接工艺,满足了施工要求。
现对工程不锈钢焊接施工进行总结,为以后的同类施工积累经验,提供参考。
2 焊接性分析
TP304/304L力学性能与国内材料0Cr18Ni9相近,但含碳量较低,比0Cr18Ni9具有来良好的耐晶间腐蚀能力,属于超低碳奥氏体不锈钢,其管材合格证上的化学成分及力学性能见下表:
化学成分
力学性能
奥氏体不锈钢具有良好的可焊性,在任何温度下都不会发生相变,对氢脆不敏感,在焊态下奥氏体不锈钢接头也有较好的塑性和韧性,焊接的主要问题是焊接热裂纹和晶间腐蚀,采用合理的焊接工艺可有效的避免焊接问题的产生。
焊接热裂纹产生主要因素有两个,一是液相线和固相线距离大,凝固过程中温度范围大,使低熔点杂质偏析严重,而且集中在晶界处。
二是不锈钢的物理性能与碳钢有很大区别,不锈钢的线膨胀系数比碳钢约大50%,热导率比碳钢低,约为其1/3左右,电阻率是碳钢的5倍,所以焊缝冷却收缩时应力也大。
晶间腐蚀主要是奥氏体不锈钢在450~850℃温度区范围内停留一定时间后,在晶界处会析出Cr23C6,使晶界处的晶粒增大形成贫铬区,接触到腐蚀介质后贫铬区极易腐蚀,受到晶间腐蚀的不锈钢在表面上没有任何变化,但在受力时会沿晶界断裂,几乎完全丧失强度。
3 焊缝内部缺陷及原因分析
工程施工重点是保证焊缝质量的前提下内壁平齐,打底焊的好坏是控制焊缝内部质量的关键,因氩气保护效果好,合金元素过渡系数高,焊缝成分易于控制,焊接热源较集中,又有氩气的冷却作用,其焊接热影响区较窄,晶粒长大倾向小,在施工过程中不会产生飞溅、焊缝成型美观,焊缝上不存在渣壳,无需清理,接头质量高,所以氩弧焊是焊接奥氏体较为理想的焊接方法。
使用氩弧焊打底,按照评定合格的焊接工艺评定制定的焊接工艺措施,正常施焊,焊缝内部成型较好,一般不会出现外观缺陷,偶尔出现内部缺陷较多的主要是成型不良、烧穿等,这与不遵守焊
这些缺陷可以通过适当的工艺措施来减少和避免,但在此工程中,我们要在保证焊缝内在质量的前提下,重点是控制内部余高,经过咨询专家及内部讨论,我们一致认为在保证焊透的前提下,组对间隙越小越好,为此我们以φ114X6的试管进行多次小间隙焊接试验,得出组对间隙在0.5-0.8mm之间时,采用合理的工艺参数,焊缝内部成型较为理想,但由于不锈钢膨胀系数大,在焊接中后期,组对间隙收缩,内部容易出现未熔和、未焊透及内部凹陷的缺陷,经讨论分析:我们认为内部凹陷主要是铁水融化后,焊工为控制内部余高,填充焊丝不足,未熔和、未焊透,主要是没有组对间隙、电流选择不合适、焊工对熔池情况掌控不够等。
针对这些缺陷,我们一方面培训焊工进行多练习,一方面通过加强组对质量(间隙、钝边、点固方式、坡口角度等)、调整焊接电流、送丝速度、送丝方式、焊接试件等,选取最合适焊接工艺参数及措施。
4 焊接过程控制
4.1 焊接方法选择
管道焊接全部采用氩弧焊打底,至少氩弧焊接2遍后才可手工电弧焊填充、盖面。
4.2 焊材的选择
根据焊接性分析,结合管道使用条件,通过焊接工艺评定验证后,焊丝选用ER308L,直径2.0mm,焊条选择A002,这是一种高铬高镍超低碳的焊材,在保证了焊缝力学性能及合金元素的稳定的同时又对防止晶间腐蚀有利,在焊接时要保证焊丝的干燥与清洁。
4.3 焊接坡口
坡口形式及尺寸一般按照保证焊接质量、填充金属少、熔合比小、便于操作等原则选用。
经
与业主沟通讨论,选取优秀焊工并通过多次焊接试验,最终制定的坡口角度60-70℃,间隙小于0.8mm(在焊透的情况下,为保证内部与母材平齐,间隙尽量小),钝边0-0.5mm。
4.4 焊接工艺要求:
保护气体:氩气,纯度≥99.99%
焊机:ZX7-400逆变式直流焊接
清理:对口前必须把坡口内外两侧20mm范围内的油污、毛刺、氧化物及其他对焊接有害物质清理干净,防止低熔点物质进入焊道,预防热裂纹产生。
加工:加工、切割、打磨、运输等使用专有的不锈钢工具,与碳钢隔离,尽量减少碳污染,使焊缝中含碳量减少,有利于防止晶间腐蚀的产生。
组对:内壁一定要平齐,不允许有任何错边,当有错边量时,标定好位置,使用砂轮机打磨平齐。
定位焊:采用搭桥式定位,焊接参数与正式焊一样,定位点2-3个,此定位焊不会影响焊缝内部成型质量且内部不用充气,清理方面。
焊接工艺参数:经过多次试验、记录,检查、检验的效果,氩弧打底焊我们得出一个较为合理的焊接工艺参数,(手工电弧焊按照正常工艺评定参数)
TP304/304L管道氩弧打底焊焊接工艺参数
4.5 质量控制技术措施
(1)氩弧焊风速不得大于2m/s,焊接时搭设防风棚,防止气孔产生。
(2)氩弧打底焊时,内部气体充气保护,开始时宜采用较大流量,确保管内空气完全排除后方可施焊,焊接时内部保护用的流量应适当降低。
(3)固定焊接时一般从6点位置起弧焊接到定位焊处,在焊接过程中焊丝端头保持不离熔池并不断填入和向前移动,这样可以提高焊丝熔化速度并让焊丝分担一部分热量,减少焊件热输入和焊丝端部氧化,降低在送丝过程中对气体保护的影响,在焊接底部要注意焊丝送丝速度,以免出现内凹现象。
在焊接顶部时,注意熔池情况,间断性送丝,焊丝前段应置于保护气体中,及时补充熔池内铁水量,但不能使铁水过多致使内部余高超标。
收弧时应减慢焊接速度,增加填充量,填满熔池以免出现弧坑、热裂纹和缩孔。
电弧熄灭后焊枪喷嘴仍然要对准熔池以延长氩气保护时间,防止氧化。
第二层以后可按照工艺评定参数正常焊接。
(4)施焊时尽量一次不间断焊完,减少接头数量及焊缝收缩。
(5)在工艺参数允许的范围内,尽量采用小线能量、小电流、短电弧、快速焊,层间温度控制在150℃以下,必要时可使用水强制冷却,减少不锈钢在腐蚀敏感温度的停留时间。
(6)焊件表面不得有电弧擦伤、不得在焊件表面引弧、收弧。
(7)焊接时应确保引弧与收弧处的质量,收弧时将弧坑填满,并用砂轮机修磨平整。
(8)地线使用铜钳或不锈钢夹具,要与母材接触良好。
5 难点及重点
我们挑选多名优秀焊工培训、练习,最后选出2名焊工正式焊接此类管线,每道焊缝组对,
都必须经业主检查合格后,才允许打底焊接。
对工艺措施、焊接参数,业主、项目部质检员进行实时监控,打底余高过高时必须割口重新组对焊接。
焊接的重点及难点是保证焊缝无损检测合格的基础,焊缝内部余高在0-0.5mm之间,一定不能低于母材。
在焊接试验过程中,焊缝内壁两侧熔合良好,稍微内凹(低于母材),业主检查后认为是合格的焊缝,但在无损检测底片上显示为内壁未熔或未焊透,虽然业主与检测单位沟通过,但在不能查看到内壁情况下,谁也不能保证内壁熔合良好,因此不允许焊缝内凹。
焊工在小间隙打底时,一定要集中精力观察熔池情况,注重焊接速度及送丝速度的配合,既要防止熔池铁水过多产生内部余高过高、也要防止熔池铁水过少产生内部凹陷,这需要焊工多练习。
6 效果及结论
通过对TP304/304L小间隙焊接试验,制定合理的焊接工艺并用于施工,在施工过程中加强施工管理、严格控制焊接工艺参数,保证了焊接质量、避免返工操作,达到事半功倍的目的。
焊缝内壁成型良好,余高基本与内壁平齐,焊缝纹路细密均匀,达到了业主的要求,焊接一次合格率达98%以上。
工程实践证明此工艺可以保证焊接质量,也为同类要求的不锈钢焊接提供了焊接工艺和数据参考。
参考文献:
(1)《焊接工程师手册》陈祝年北京机械工业出版社.2002年1月
(2)《焊工实用技术手册》朱玉义江苏科学技术出版社.2002年1月
(3)《现场设备、工业管道焊接工程施工规范》 GB50236-2011 中国计划出版社.2011年10月
(4)《金属管道焊接工艺便携手册》柳金海陈百城北京.机械工业出版社.2005年1月。