氮化铝粉末特性对氮化铝-氮化硼复合陶瓷结构和性能的影响
常用无机粉体填料优缺点分析

常用无机粉体填料优缺点分析1、氮化铝(AlN),优点:导热系数特别高。
缺点:价格昂贵,通常每公斤在千元以上;氮化铝吸潮后会与水反应会水解AlN+3H20=Al (OH)3+NH3,水解产生的Al(OH)3会使导热通路产生停止,进而影响声子的传递,因此做成制品后热导率偏低。
即使用硅烷偶联剂进行表面处理,也不能保证100%填料表面被包覆。
单纯使用氮化铝,虽然可以达到较高的热导率,但体系粘度极具上升,严重限制了产品的应用领域。
2、氮化硼(BN),优点:导热系数特别高,性质稳定。
缺点:价格很高,市场价从几百元到上千元(依据产品品质不同差别较大),虽然单纯使用氮化硼可以达到较高的热导率,但与氮化铝仿佛,大量填充后体系粘度极具上升,严重限制了产品的应用领域。
有国外厂商有生产球形BN,产品粒径大,比表面积小,填充率高,不易增粘,价格极高。
3、碳化硅(SiC)优点:导热系数较高。
缺点:合成过程中产生的碳及石墨难以去除,导致产品纯度较低,电导率高,不适合电子用胶。
密度大,在有机硅类胶中易沉淀分层,影响产品应用。
环氧胶中较为适用。
4、氧化镁(MgO)优点:价格便宜。
缺点:在空气中易吸潮,增粘性较强,不能大量填充;耐酸性差,一般情况下很简单被酸腐蚀,限制了其在酸性环境下的应用。
5、—氧化铝(针状)优点:价格便宜。
缺点:添加量低,在液体硅胶中,一般针状氧化铝的最大添加量一般为300份左右,所得产品导热率有限。
6、—氧化铝(球形)优点:填充量大,在液体硅胶中,球形氧化铝最大可添加到600~800份,所得制品导热率高。
缺点:价格较贵,但低于氮化硼和氮化铝。
7、氧化锌(ZnO)优点:粒径及均匀性很好,适合生产导热硅脂。
缺点:导热性偏低,不适合生产高导热产品;质轻,增粘性较强,不适合灌封。
8、二氧化硅(结晶型)优点:密度大,适合灌封;价格低,适合大量填充,降低成本。
缺点:导热性偏低,不适合生产高导热产品。
密度较高,可能产生分层。
氮化处理对陶瓷材料耐磨性能的提升研究

氮化处理对陶瓷材料耐磨性能的提升研究氮化处理是一种常见的陶瓷材料表面改性技术,可以显著提高陶瓷材料的耐磨性能。
本文将介绍氮化处理对陶瓷材料耐磨性能提升的研究。
氮化处理是通过在陶瓷材料表面形成一层氮化物薄膜来增强材料的硬度和耐磨性。
一种常见的氮化处理方法是离子注入氮化,即将陶瓷材料放入含氮离子的离子注入设备中,利用高能离子注入技术将氮离子注入材料表层,形成氮化物薄膜。
研究表明,氮化处理可以显著提高陶瓷材料的硬度和耐磨性。
氮气化合物膜能使陶瓷表面硬度提高5倍以上,耐磨性能提高10倍以上,大大延长了陶瓷材料的使用寿命。
氮化处理还能增加材料的抗腐蚀性能和耐高温性能,提高了陶瓷材料的综合性能。
氮化处理对陶瓷材料耐磨性能提升的机制主要有以下几个方面。
首先,氮化物薄膜的形成提高了材料表层的硬度,使其能够更好地抵抗磨损。
其次,氮化物薄膜的形成改善了材料表面的摩擦特性,减小了磨擦系数,减少了磨损。
此外,氮化处理还能提高材料的表面光洁度,减少表面粗糙度,进一步减小了磨损。
在氮化处理中,影响陶瓷材料耐磨性能提升的因素有很多。
首先是氮化时间和温度的选择,过长或过高的处理条件会导致氮化物层过厚,反而影响陶瓷材料的性能。
其次是离子注入能量的选择,能量过低会导致氮化物层的形成不完全,能量过高会导致陶瓷材料的晶体结构破坏。
此外,还要考虑氮化处理前的材料表面处理等因素。
总的来说,氮化处理是一种有效的提高陶瓷材料耐磨性能的方法。
通过形成氮化物薄膜,可以显著提高陶瓷材料的硬度和耐磨性,延长其使用寿命。
然而,氮化处理还存在一些问题,如处理温度和时间的选择、氮化物层的粘附性等,需要进一步研究和改进。
未来,可以进一步研究氮化处理对不同类型陶瓷材料的影响,探索更好的氮化处理方法,提高陶瓷材料的耐磨性能。
氮化处理是一种常见的陶瓷材料表面改性技术,可以显著提高陶瓷材料的耐磨性能。
本文将进一步介绍氮化处理对陶瓷材料耐磨性能提升的相关内容。
在陶瓷材料中,氮化物薄膜的形成是提高材料硬度和耐磨性的关键。
氮化处理对陶瓷材料导热性能的改善研究
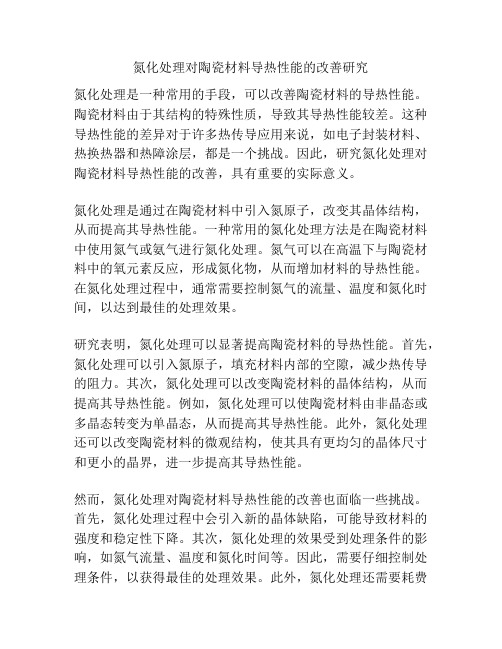
氮化处理对陶瓷材料导热性能的改善研究氮化处理是一种常用的手段,可以改善陶瓷材料的导热性能。
陶瓷材料由于其结构的特殊性质,导致其导热性能较差。
这种导热性能的差异对于许多热传导应用来说,如电子封装材料、热换热器和热障涂层,都是一个挑战。
因此,研究氮化处理对陶瓷材料导热性能的改善,具有重要的实际意义。
氮化处理是通过在陶瓷材料中引入氮原子,改变其晶体结构,从而提高其导热性能。
一种常用的氮化处理方法是在陶瓷材料中使用氮气或氨气进行氮化处理。
氮气可以在高温下与陶瓷材料中的氧元素反应,形成氮化物,从而增加材料的导热性能。
在氮化处理过程中,通常需要控制氮气的流量、温度和氮化时间,以达到最佳的处理效果。
研究表明,氮化处理可以显著提高陶瓷材料的导热性能。
首先,氮化处理可以引入氮原子,填充材料内部的空隙,减少热传导的阻力。
其次,氮化处理可以改变陶瓷材料的晶体结构,从而提高其导热性能。
例如,氮化处理可以使陶瓷材料由非晶态或多晶态转变为单晶态,从而提高其导热性能。
此外,氮化处理还可以改变陶瓷材料的微观结构,使其具有更均匀的晶体尺寸和更小的晶界,进一步提高其导热性能。
然而,氮化处理对陶瓷材料导热性能的改善也面临一些挑战。
首先,氮化处理过程中会引入新的晶体缺陷,可能导致材料的强度和稳定性下降。
其次,氮化处理的效果受到处理条件的影响,如氮气流量、温度和氮化时间等。
因此,需要仔细控制处理条件,以获得最佳的处理效果。
此外,氮化处理还需要耗费大量的能源和时间,增加了生产成本。
综上所述,氮化处理是一种有效的手段,可以改善陶瓷材料的导热性能。
通过引入氮原子和改变晶体结构等方式,可以显著提高材料的导热性能。
然而,氮化处理过程中还存在一些挑战,如晶体缺陷的引入和处理条件的控制等。
因此,未来的研究需要进一步探索氮化处理对陶瓷材料导热性能的影响,并寻找新的、更有效的处理方法。
只有这样,才能更好地提高陶瓷材料的导热性能,满足各种热传导应用的需求。
氮化铝综述
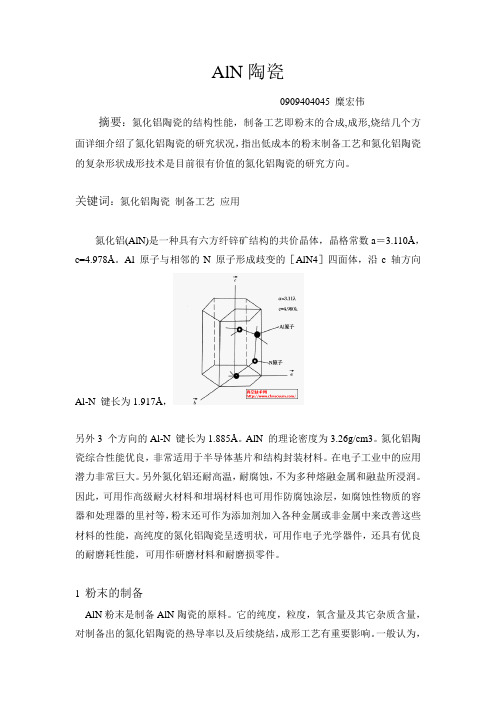
AlN陶瓷0909404045 糜宏伟摘要:氮化铝陶瓷的结构性能,制备工艺即粉末的合成,成形,烧结几个方面详细介绍了氮化铝陶瓷的研究状况,指出低成本的粉末制备工艺和氮化铝陶瓷的复杂形状成形技术是目前很有价值的氮化铝陶瓷的研究方向。
关键词:氮化铝陶瓷制备工艺应用氮化铝(AlN)是一种具有六方纤锌矿结构的共价晶体,晶格常数a=3.110Å,c=4.978Å。
Al 原子与相邻的N 原子形成歧变的[AlN4]四面体,沿c 轴方向Al-N 键长为1.917Å,另外3 个方向的Al-N 键长为1.885Å。
AlN 的理论密度为3.26g/cm3。
氮化铝陶瓷综合性能优良,非常适用于半导体基片和结构封装材料。
在电子工业中的应用潜力非常巨大。
另外氮化铝还耐高温,耐腐蚀,不为多种熔融金属和融盐所浸润。
因此,可用作高级耐火材料和坩埚材料也可用作防腐蚀涂层,如腐蚀性物质的容器和处理器的里衬等,粉末还可作为添加剂加入各种金属或非金属中来改善这些材料的性能,高纯度的氮化铝陶瓷呈透明状,可用作电子光学器件,还具有优良的耐磨耗性能,可用作研磨材料和耐磨损零件。
1 粉末的制备AlN粉末是制备AlN陶瓷的原料。
它的纯度,粒度,氧含量及其它杂质含量,对制备出的氮化铝陶瓷的热导率以及后续烧结,成形工艺有重要影响。
一般认为,要获得性能优良的AlN陶瓷材料,必须首先制备出高纯度,细粒度,窄粒度分布,性能稳定的AlN粉末。
目前,氮化铝粉末的合成方法主要有3种:铝粉直接氮化法,碳热还原法,自蔓延高温合成法。
其中,前2种方法已应用于工业化大规模生产,自蔓延高温合成法也开始在工业生产中应用。
1.1 铝粉直接氮化法直接氮化法就是在高温氮气氛围中,铝粉直接与氮气化合生成氮化铝粉末,反应温度一般在800~1200℃化学反应式为:铝粉直接氮化法优点是原料丰富,工艺简单,适宜大规模生产。
目前已经应用于工业生产。
但是该方法也存在明显不足,由于铝粉氮化反应为强放热反应,反应过程不易控制,放出的大量热量易使铝形成融块,阻碍氮气的扩散,造成反应不完全,反应产物往往需要粉碎处理,因此难以合成高纯度,细粒度的产品。
氮化硼与氮化铝的导热系数

氮化硼与氮化铝的导热系数氮化硼(BN)和氮化铝(AlN)是两种常用的导热材料,具有优异的导热性能,广泛应用于电子器件、导热材料和热管理领域。
本文将围绕氮化硼和氮化铝的导热系数展开讨论。
一、氮化硼的导热系数氮化硼是一种非常好的导热材料,具有较高的导热系数。
其导热系数通常在100-200 W/(m·K)之间,甚至可以高达300 W/(m·K)。
相比之下,许多金属的导热系数只有几十到几百W/(m·K)。
因此,氮化硼在高温和高功率应用中表现出色,能够有效地传递热量。
氮化硼的导热性能与其晶体结构有关。
氮化硼具有类似于石墨的层状结构,其中硼原子和氮原子交替排列形成类似于石墨的层。
这种层状结构使得氮化硼在热传导方面表现出色,热量可以沿着层状结构的平面方向快速传播。
氮化硼的导热系数还受到其晶体缺陷和杂质含量的影响。
晶体结构中的缺陷和杂质会散射热传导的载流子,从而降低导热系数。
因此,高纯度的氮化硼通常具有较高的导热系数。
二、氮化铝的导热系数与氮化硼相比,氮化铝的导热系数略低一些,通常在100-200 W/(m·K)之间。
不过,相对于许多其他常见的导热材料来说,氮化铝的导热性能仍然非常出色。
氮化铝具有六方晶体结构,其中铝原子和氮原子交替排列形成六角形的晶胞。
这种晶体结构使得氮化铝在热传导方面表现出色,热量可以沿着六方晶体的c轴方向快速传播。
类似于氮化硼,氮化铝的导热性能也受到晶体缺陷和杂质含量的影响。
晶体结构中的缺陷和杂质会散射热传导的载流子,从而降低导热系数。
因此,高纯度的氮化铝通常具有较高的导热系数。
三、氮化硼与氮化铝的比较虽然氮化硼和氮化铝的导热系数相差不大,但氮化硼在一些方面表现出更好的导热性能。
首先,由于氮化硼具有层状结构,其导热性能在平面方向上更好。
而氮化铝由于其六方晶体结构,其导热性能在c轴方向上更好。
其次,氮化硼相对于氮化铝来说更容易制备高纯度的材料,因此其导热系数可能更高。
氮化硼与氮化铝的导热系数
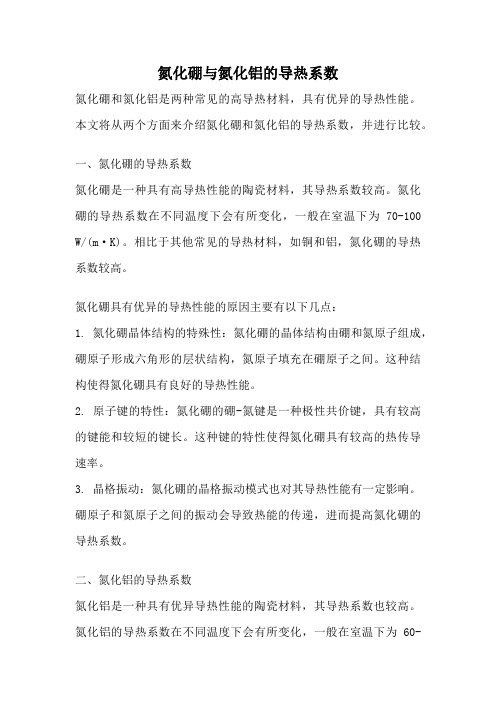
氮化硼与氮化铝的导热系数氮化硼和氮化铝是两种常见的高导热材料,具有优异的导热性能。
本文将从两个方面来介绍氮化硼和氮化铝的导热系数,并进行比较。
一、氮化硼的导热系数氮化硼是一种具有高导热性能的陶瓷材料,其导热系数较高。
氮化硼的导热系数在不同温度下会有所变化,一般在室温下为70-100 W/(m·K)。
相比于其他常见的导热材料,如铜和铝,氮化硼的导热系数较高。
氮化硼具有优异的导热性能的原因主要有以下几点:1. 氮化硼晶体结构的特殊性:氮化硼的晶体结构由硼和氮原子组成,硼原子形成六角形的层状结构,氮原子填充在硼原子之间。
这种结构使得氮化硼具有良好的导热性能。
2. 原子键的特性:氮化硼的硼-氮键是一种极性共价键,具有较高的键能和较短的键长。
这种键的特性使得氮化硼具有较高的热传导速率。
3. 晶格振动:氮化硼的晶格振动模式也对其导热性能有一定影响。
硼原子和氮原子之间的振动会导致热能的传递,进而提高氮化硼的导热系数。
二、氮化铝的导热系数氮化铝是一种具有优异导热性能的陶瓷材料,其导热系数也较高。
氮化铝的导热系数在不同温度下会有所变化,一般在室温下为60-200 W/(m·K)。
相比于氮化硼,氮化铝的导热系数更高一些。
氮化铝具有优异导热性能的原因主要有以下几点:1. 晶体结构的特殊性:氮化铝的晶体结构由铝和氮原子组成,形成六角形的层状结构。
这种结构使得氮化铝具有良好的导热性能。
2. 原子键的特性:氮化铝的铝-氮键是一种极性共价键,具有较高的键能和较短的键长。
这种键的特性使得氮化铝具有较高的热传导速率。
3. 晶格振动:氮化铝的晶格振动模式也对其导热性能有一定影响。
铝原子和氮原子之间的振动会导致热能的传递,进而提高氮化铝的导热系数。
三、氮化硼和氮化铝的比较氮化硼和氮化铝都是具有高导热性能的材料,但在导热系数方面略有差异。
一般情况下,氮化铝的导热系数要高于氮化硼。
在实际应用中,选择氮化硼还是氮化铝取决于具体的需求。
一文看氮化铝的性质用途
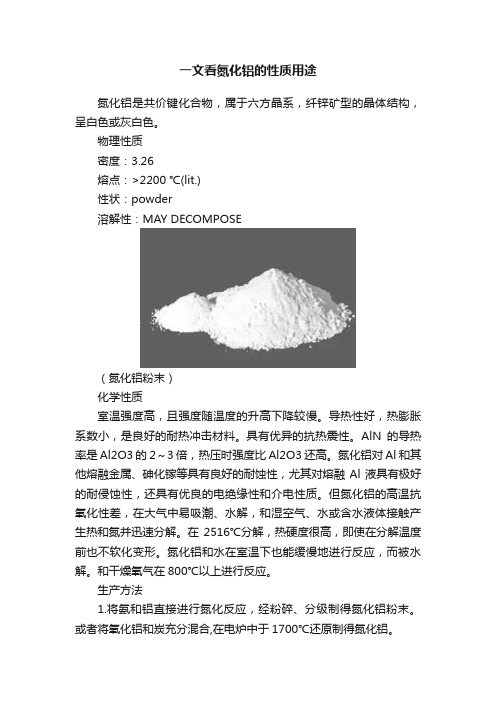
一文看氮化铝的性质用途氮化铝是共价键化合物,属于六方晶系,纤锌矿型的晶体结构,呈白色或灰白色。
物理性质密度:3.26熔点:>2200 ℃(lit.)性状:powder溶解性:MAY DECOMPOSE(氮化铝粉末)化学性质室温强度高,且强度随温度的升高下降较慢。
导热性好,热膨胀系数小,是良好的耐热冲击材料。
具有优异的抗热震性。
AlN的导热率是Al2O3的2~3倍,热压时强度比Al2O3还高。
氮化铝对Al和其他熔融金属、砷化镓等具有良好的耐蚀性,尤其对熔融Al液具有极好的耐侵蚀性,还具有优良的电绝缘性和介电性质。
但氮化铝的高温抗氧化性差,在大气中易吸潮、水解,和湿空气、水或含水液体接触产生热和氮并迅速分解。
在2516℃分解,热硬度很高,即使在分解温度前也不软化变形。
氮化铝和水在室温下也能缓慢地进行反应,而被水解。
和干燥氧气在800℃以上进行反应。
生产方法1.将氨和铝直接进行氮化反应,经粉碎、分级制得氮化铝粉末。
或者将氧化铝和炭充分混合,在电炉中于1700℃还原制得氮化铝。
2.将高纯度铝粉脱脂(用乙醚抽提或在氮气流中加热到150℃)后,放到镍盘中,将盘放在石英或瓷制反应管内,在提纯的氮气流中慢慢地进行加热。
氮化反应在820℃左右时发出白光迅速地进行。
此时,必须大量通氮以防止反应管内出现减压。
这个激烈的反应完毕后,在氮气流中冷却。
由于产物内包有金属铝,可将其粉碎,并在氮气流中于1100~1200℃温度下再加热1~2h,即得到灰白色氮化铝。
另外,将铝在1200~1400℃下蒸发气化,使其与氮气反应即得到氮化铝的须状物(金属晶须)。
此外,也有将AlCl3·NH3加成物进行热分解的制法。
3.直接氮化法将氮和铝直接进行氮化反应,经粉碎、分级制得。
氮化铝产品质量受反应炉温、原料的预混合以及循环氮化铝粉末所占的混合比例、氮化铝比表面积等条件的影响。
因此需严格控制工艺过程,得到稳定特性的氮化铝粉末(如比表面积、一次粒径、凝聚粒径、松密度和表面特性等)。
氮化铝陶瓷屈服强度
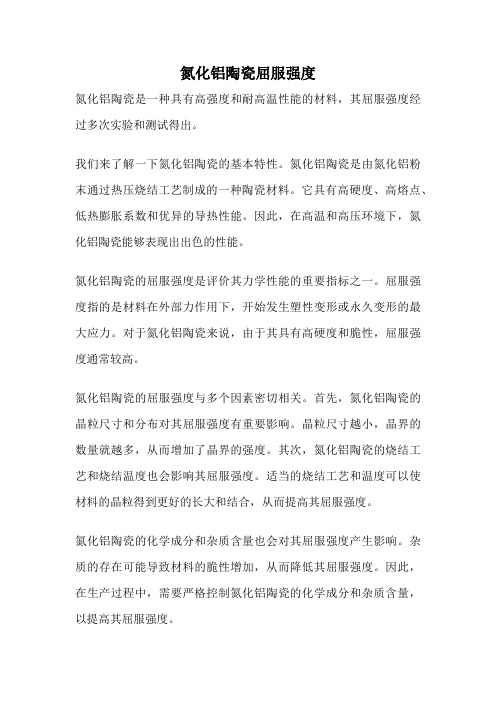
氮化铝陶瓷屈服强度
氮化铝陶瓷是一种具有高强度和耐高温性能的材料,其屈服强度经过多次实验和测试得出。
我们来了解一下氮化铝陶瓷的基本特性。
氮化铝陶瓷是由氮化铝粉末通过热压烧结工艺制成的一种陶瓷材料。
它具有高硬度、高熔点、低热膨胀系数和优异的导热性能。
因此,在高温和高压环境下,氮化铝陶瓷能够表现出出色的性能。
氮化铝陶瓷的屈服强度是评价其力学性能的重要指标之一。
屈服强度指的是材料在外部力作用下,开始发生塑性变形或永久变形的最大应力。
对于氮化铝陶瓷来说,由于其具有高硬度和脆性,屈服强度通常较高。
氮化铝陶瓷的屈服强度与多个因素密切相关。
首先,氮化铝陶瓷的晶粒尺寸和分布对其屈服强度有重要影响。
晶粒尺寸越小,晶界的数量就越多,从而增加了晶界的强度。
其次,氮化铝陶瓷的烧结工艺和烧结温度也会影响其屈服强度。
适当的烧结工艺和温度可以使材料的晶粒得到更好的长大和结合,从而提高其屈服强度。
氮化铝陶瓷的化学成分和杂质含量也会对其屈服强度产生影响。
杂质的存在可能导致材料的脆性增加,从而降低其屈服强度。
因此,在生产过程中,需要严格控制氮化铝陶瓷的化学成分和杂质含量,以提高其屈服强度。
总的来说,氮化铝陶瓷的屈服强度取决于多个因素,包括晶粒尺寸和分布、烧结工艺和温度、化学成分和杂质含量等。
通过合理的工艺和控制,可以提高氮化铝陶瓷的屈服强度,从而满足不同领域对高强度材料的需求。
浅谈氮化铝的性质、制备及应用

浅谈氮化铝的性质、制备及应用1氮化铝的性质氮化铝(AlN)是一种综合性能优异的先进陶瓷材料,是一种被国内外专家一致看好的新型封装材料,也是目前公认的最有发展前途的高热导陶瓷材料。
对其的研究开始于一个多世纪以前,但当时仅将其用作固氮剂化肥使用。
作为共价化合物的氮化铝,由于其具有较高的熔点和较低的自扩散系数,导致其难以烧结。
直到上世纪50年代,氮化铝陶瓷才被人们首次制得,并作为一种耐火材料使用,而后广泛应用于纯铁、铝以及铝合金的熔炼。
从上世纪70年代以来,随着研究的进一步深入,氮化铝的制备工艺逐渐走向成熟,其应用的领域和规模也不断扩大。
氮化铝是一种共价键化合物,具有六方纤锌矿型结构形态,晶格常数为a=3.11、c=4.98,如图1-1所示。
其理论密度为3.26g/cm3,莫氏硬度为7~8,分解温度为2200~2250℃。
[1]图1-1氮化铝的晶体结构氮化铝陶瓷具有较高的热导率,适应于高功率、高引线和大尺寸芯片;它的热膨胀系数与硅匹配,介电常数较低;其材质机械强度高,在严酷的条件下仍能照常工作。
因此,氮化铝可以制成很薄的衬底,以满足不同封装基片的应用要求。
氮化铝陶瓷作为高热导、高密封材料有很大的发展潜力,是陶瓷封装材料研究的重要发展领域。
人们预计,在基片和封装两大领域,氮化铝陶瓷最终将取代目前的氧化铝陶瓷和氧化铍陶瓷。
[2]氮化铝陶瓷的主要特点如下:1)热导率高,是氧化铝陶瓷的5~10倍,与剧毒氧化铍相当;2)热膨胀系数(4.3×10-6/℃)与半导体硅材料(3.5-4.0×10-6/℃)匹配;3)机械性能好,高于氧化铍陶瓷,接近氧化铝;4)电性能优良,具有极高的绝缘电阻和低的介质损耗;5)可以进行多层布线,实现封装的高密度和小型化;6)无毒,有利于环保。
[3]2氮化铝粉体的制备2.1直接氮化法氮化铝在自然界中不存在,现在是由金属铝粉末直接氮化合成或由Al2O3碳热还原后再直接氮化法制备,其化学反应式为:2Al(s)+N2(g)→2AlN(s)直接氮化法具有若干优点:1)成本低廉;2)原料丰富;3)反应体系简单,没有副反应;4)反应温度低于碳热还原;5)适合大规模生产。
【精品文章】氮化铝粉体的特性及应用
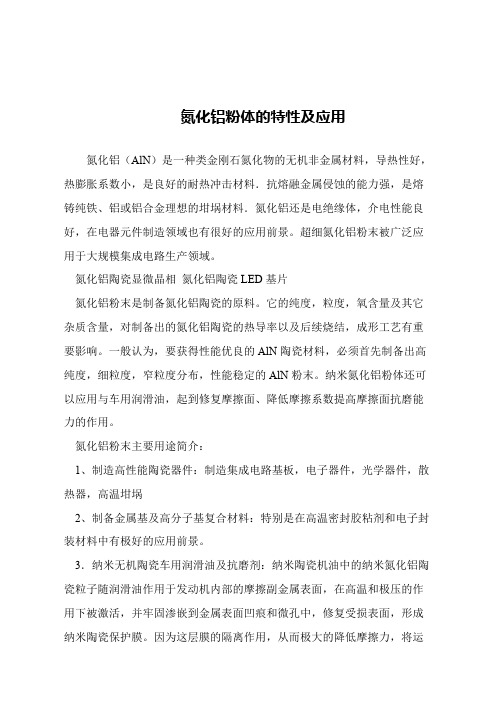
氮化铝粉体的特性及应用
氮化铝(AlN)是一种类金刚石氮化物的无机非金属材料,导热性好,热膨胀系数小,是良好的耐热冲击材料.抗熔融金属侵蚀的能力强,是熔铸纯铁、铝或铝合金理想的坩埚材料.氮化铝还是电绝缘体,介电性能良好,在电器元件制造领域也有很好的应用前景。
超细氮化铝粉末被广泛应用于大规模集成电路生产领域。
氮化铝陶瓷显微晶相氮化铝陶瓷LED基片
氮化铝粉末是制备氮化铝陶瓷的原料。
它的纯度,粒度,氧含量及其它杂质含量,对制备出的氮化铝陶瓷的热导率以及后续烧结,成形工艺有重要影响。
一般认为,要获得性能优良的AlN陶瓷材料,必须首先制备出高纯度,细粒度,窄粒度分布,性能稳定的AlN粉末。
纳米氮化铝粉体还可以应用与车用润滑油,起到修复摩擦面、降低摩擦系数提高摩擦面抗磨能力的作用。
氮化铝粉末主要用途简介:
1、制造高性能陶瓷器件:制造集成电路基板,电子器件,光学器件,散热器,高温坩埚
2、制备金属基及高分子基复合材料:特别是在高温密封胶粘剂和电子封装材料中有极好的应用前景。
3.纳米无机陶瓷车用润滑油及抗磨剂:纳米陶瓷机油中的纳米氮化铝陶瓷粒子随润滑油作用于发动机内部的摩擦副金属表面,在高温和极压的作用下被激活,并牢固渗嵌到金属表面凹痕和微孔中,修复受损表面,形成纳米陶瓷保护膜。
因为这层膜的隔离作用,从而极大的降低摩擦力,将运。
氧化铝陶瓷材料中氮化处理对性能的影响与优化
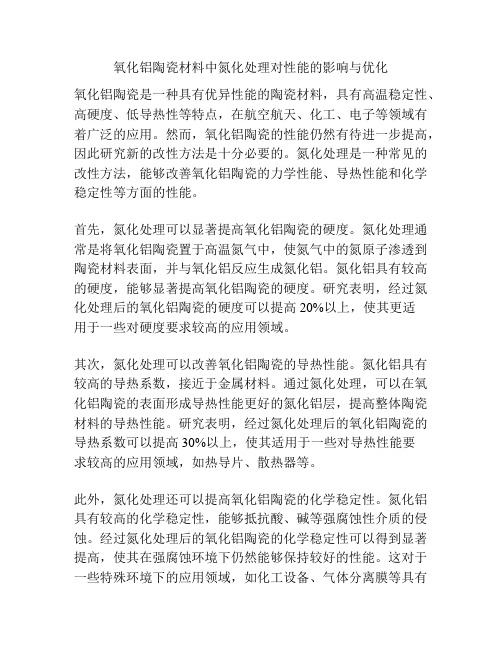
氧化铝陶瓷材料中氮化处理对性能的影响与优化氧化铝陶瓷是一种具有优异性能的陶瓷材料,具有高温稳定性、高硬度、低导热性等特点,在航空航天、化工、电子等领域有着广泛的应用。
然而,氧化铝陶瓷的性能仍然有待进一步提高,因此研究新的改性方法是十分必要的。
氮化处理是一种常见的改性方法,能够改善氧化铝陶瓷的力学性能、导热性能和化学稳定性等方面的性能。
首先,氮化处理可以显著提高氧化铝陶瓷的硬度。
氮化处理通常是将氧化铝陶瓷置于高温氮气中,使氮气中的氮原子渗透到陶瓷材料表面,并与氧化铝反应生成氮化铝。
氮化铝具有较高的硬度,能够显著提高氧化铝陶瓷的硬度。
研究表明,经过氮化处理后的氧化铝陶瓷的硬度可以提高20%以上,使其更适用于一些对硬度要求较高的应用领域。
其次,氮化处理可以改善氧化铝陶瓷的导热性能。
氮化铝具有较高的导热系数,接近于金属材料。
通过氮化处理,可以在氧化铝陶瓷的表面形成导热性能更好的氮化铝层,提高整体陶瓷材料的导热性能。
研究表明,经过氮化处理后的氧化铝陶瓷的导热系数可以提高30%以上,使其适用于一些对导热性能要求较高的应用领域,如热导片、散热器等。
此外,氮化处理还可以提高氧化铝陶瓷的化学稳定性。
氮化铝具有较高的化学稳定性,能够抵抗酸、碱等强腐蚀性介质的侵蚀。
经过氮化处理后的氧化铝陶瓷的化学稳定性可以得到显著提高,使其在强腐蚀环境下仍然能够保持较好的性能。
这对于一些特殊环境下的应用领域,如化工设备、气体分离膜等具有重要意义。
总的来说,氮化处理对氧化铝陶瓷材料的性能有着显著的影响,并且在提高硬度、导热性能和化学稳定性方面具有优势。
然而,氮化处理的最佳条件还需要进一步研究和优化。
例如,氮化处理的温度、时间以及氮气流量等影响氮化效果的参数需要进行系统的实验研究,以找到最佳的处理条件。
此外,还可以结合其他改性方法,如添加适量的陶瓷颗粒增强材料等,进一步提高氧化铝陶瓷的性能。
总之,氮化处理是一种有效的提高氧化铝陶瓷性能的方法,可以提高硬度、导热性能和化学稳定性等方面的性能。
陶瓷复合装甲材料研究和发展

新材料技术在军事上的用途也是十分广泛的,用于武器装备可使其升级换代,性能大大提高,目前在军事领域里新材料技术正向高功能化、复合轻量和智能化的方向发展。
陶瓷材料作为一种先进的高技术材料,它具有种高强度、高硬度、耐腐蚀、高耐磨性和重量轻的特点,它不仅应用在坦克的防护上,而且也应用在飞机、舰船、车辆、关键部位的防弹遮蔽层和单兵作战的防护上,它的应用范围越来越广泛。
实践表明,世界上许多先进坦克的防护装甲采用高性能陶瓷后,防护能力明显提高,陶瓷已经成为复合装甲不可缺少的材料之一。
但是,陶瓷材料的易脆性是阻碍它应用的主要原因。
目前,改进陶瓷脆性的研究已取得了较大进展。
主要的途径是通过复合,提高陶瓷的强度、韧性、抗弹性能降低价格,扩大应用领域,提高材料的使用可靠性。
装甲防护的发展史也可以看成是“甲”与“弹”的斗争史,这种“矛”与“盾”的发展是相互并行的。
人们在十分重视研制新的优质抗弹陶瓷的同时,也需要对陶瓷复合装甲的侵彻机理和抗弹机理进行研究;目前对于均质装甲的侵彻和损伤机理的研究在国内外已经发展成熟,而对于由陶瓷组成的复合装甲的侵彻和[1]陶瓷复合装甲材料研究和发展康永柴秀娟1、陕西金泰氯碱化工有限公司技术中心榆林7181002、1TheResearchCenterofShaanxiJintaiChlor-alkaliChemicalCo.,LTD.Yulin718100China;2ShaanxiJintaiChlor-alkaliChemicalCo.,LTD.Yulin718100China12KANGYongCHAIXiu-juan陕西金泰氯碱化工有限公司榆林718100、、;12THE RESEARCH &DEVELOPMENT OF CERAMICCOMPOSITE AMOUR MATERIALS【摘要】陶瓷复合装甲由于在防护领域的应用背景而引起人们的广泛关注。
本文综述了陶瓷复合装甲的研究和发展方向。
关于氮化铝的调研报告

关于氮化铝的调研报告摘要:本篇介绍了氮化铝的理化性质,功能作用、实际生活运用,制备方法,发展历史进程等一些知识。
近年来电子设备向高速,小型、高效率、高可靠性,半导体器件向高集成、大规模、多片状、高效率,电路配线向微细、短线、低电阻方向发展。
例如为了使计算机运行速度更快需要在集成电路基片上排布更多的线路。
集成电路技术朝高集成度、高运算速度、大功率方向发展,因此集成块单位体积内产生的热量大幅度的增加,每块的基片所需传送的功率也将大幅度的增加,假如这些热量不能通过集成块的基片迅速散发出去,集成块难以正常工作,情况严重时,可以导致集成块被烧坏。
常用的基片主要有树脂基片、金属基片、陶瓷基片三大类。
目前已用于实际和开发应用高导热基片有氧化铝、碳化硅、氧化铍、氮化铝、CVD-BN.碳化硅的热导率虽然高,但是电容大,电阻率低,绝缘性差。
氧化铍毒性大,不利于实际运用。
BN难以烧结致密,低密度的BN热导率、机械强度急剧恶化,无法做成绝缘材料。
而氮化铝陶瓷是一种高技术新型陶瓷。
氮化铝基板具有极高的热导率,无毒、耐腐蚀、耐高温,热化学稳定性好等特点。
所以作为当今学材料化学的大学生,我们有必要了解AIN的知识。
1862年氮化铝首次被合成以来,对其研究可以分为三个阶段:在20世纪初,仅用作固氮中间体,并有若干相关专利:50年代后期开始,随着非氧化物陶瓷受到重视,开始讲AIN作为一种新型材料来进行研究,侧重于将其作为结构材料运用:近10年来,AIN陶瓷的研究的热点是提高特传导性能,应用对象是电路基片封装材料,取得了显著地进展和成就. 然而由于AIN的制备工艺复杂,费财费力,所以氮化铝陶瓷基片到目前为止仍然不能进行大规模的生产和应用。
但是氮化铝陶瓷的优越的性能,吸引了各国的很多科学工作者对其的研究,开发和应用。
其中,日本从1984年开始推广应用,1985年几家主要著名的电子产品公司已经比较广泛,如东芝、日本电气。
日立等公司。
美国、英国、印度,德国、法国等国家也正加紧研究和开发它。
AlN-BN复相陶瓷的热等静压制备与性能研究

AlN-BN复相陶瓷的热等静压制备与性能研究彭旭;朱德贵;李杨绪;周加敏;吕振;郭鹏超【摘要】以氮化铝(AlN)和氮化硼(BN)为原料,无烧结助剂、热等静压烧结制备了AlN-BN复相陶瓷,研究了热等静压温度和压强对两种不同原料配比(摩尔比)烧结试样的微观结构和性能的影响.结果表明:增加BN的添加量对复相陶瓷的烧结致密化影响较小,但逐渐降低硬度和热导率、增大体积电阻率.相同原料配比下,复相陶瓷的密度越高,其热导率、体积电阻率、硬度越高.热导率和体积电阻率的实测值与两相复合模型方程λcom=λ2(λ1+F)(1-Φ)(λ2-λ1)/λ2-(1+F)(1-Φ)(λ2-λ1)较为符合.当nAlN∶nBN=75∶25时,在温度为1600℃、压强为90 MPa、保温3h的热等静压工艺下可以制备出相对密度达98.03%、热导率为77.29 W/(m·K)、体积电阻率为1.35× 1015Ω·cm的复相陶瓷.【期刊名称】《无机材料学报》【年(卷),期】2016(031)005【总页数】7页(P535-541)【关键词】AlN-BN复相陶瓷;热等静压;热导率;体积电阻率【作者】彭旭;朱德贵;李杨绪;周加敏;吕振;郭鹏超【作者单位】西南交通大学材料先进技术教育部重点实验室,成都 610031;西南交通大学材料先进技术教育部重点实验室,成都 610031;西南交通大学材料先进技术教育部重点实验室,成都 610031;西南交通大学材料先进技术教育部重点实验室,成都 610031;西南交通大学材料先进技术教育部重点实验室,成都 610031;西南交通大学材料先进技术教育部重点实验室,成都 610031【正文语种】中文【中图分类】TB332氮化铝(AlN)陶瓷具有高热导率、高绝缘性、耐高温、无毒、良好的力学性能等优良特性, 是大规模集成电路和大功率器件的理想散热和封装材料。
但AlN硬度高、脆性大、韧性低、加工难等缺点, 使传统加工方法难以制备出形状复杂的材料[1-2]。
氮化铝综述
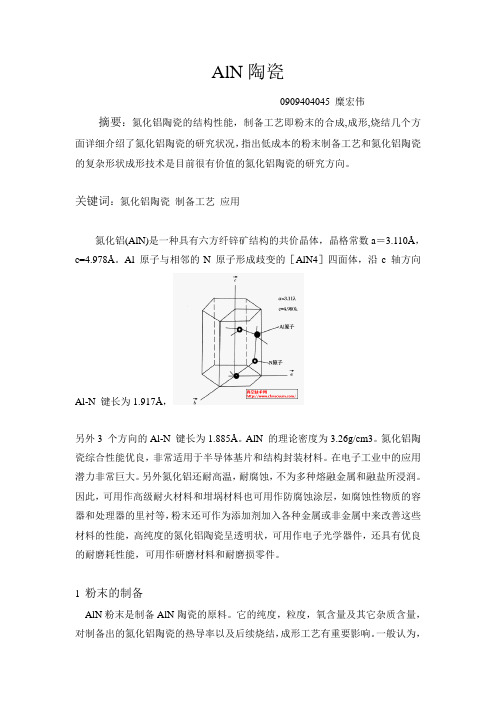
AlN陶瓷0909404045 糜宏伟摘要:氮化铝陶瓷的结构性能,制备工艺即粉末的合成,成形,烧结几个方面详细介绍了氮化铝陶瓷的研究状况,指出低成本的粉末制备工艺和氮化铝陶瓷的复杂形状成形技术是目前很有价值的氮化铝陶瓷的研究方向。
关键词:氮化铝陶瓷制备工艺应用氮化铝(AlN)是一种具有六方纤锌矿结构的共价晶体,晶格常数a=3.110Å,c=4.978Å。
Al 原子与相邻的N 原子形成歧变的[AlN4]四面体,沿c 轴方向Al-N 键长为1.917Å,另外3 个方向的Al-N 键长为1.885Å。
AlN 的理论密度为3.26g/cm3。
氮化铝陶瓷综合性能优良,非常适用于半导体基片和结构封装材料。
在电子工业中的应用潜力非常巨大。
另外氮化铝还耐高温,耐腐蚀,不为多种熔融金属和融盐所浸润。
因此,可用作高级耐火材料和坩埚材料也可用作防腐蚀涂层,如腐蚀性物质的容器和处理器的里衬等,粉末还可作为添加剂加入各种金属或非金属中来改善这些材料的性能,高纯度的氮化铝陶瓷呈透明状,可用作电子光学器件,还具有优良的耐磨耗性能,可用作研磨材料和耐磨损零件。
1 粉末的制备AlN粉末是制备AlN陶瓷的原料。
它的纯度,粒度,氧含量及其它杂质含量,对制备出的氮化铝陶瓷的热导率以及后续烧结,成形工艺有重要影响。
一般认为,要获得性能优良的AlN陶瓷材料,必须首先制备出高纯度,细粒度,窄粒度分布,性能稳定的AlN粉末。
目前,氮化铝粉末的合成方法主要有3种:铝粉直接氮化法,碳热还原法,自蔓延高温合成法。
其中,前2种方法已应用于工业化大规模生产,自蔓延高温合成法也开始在工业生产中应用。
1.1 铝粉直接氮化法直接氮化法就是在高温氮气氛围中,铝粉直接与氮气化合生成氮化铝粉末,反应温度一般在800~1200℃化学反应式为:铝粉直接氮化法优点是原料丰富,工艺简单,适宜大规模生产。
目前已经应用于工业生产。
但是该方法也存在明显不足,由于铝粉氮化反应为强放热反应,反应过程不易控制,放出的大量热量易使铝形成融块,阻碍氮气的扩散,造成反应不完全,反应产物往往需要粉碎处理,因此难以合成高纯度,细粒度的产品。
氮化铝粉末用途

氮化铝粉末用途以氮化铝粉末用途为题,我们将探讨氮化铝粉末的应用领域及其特性。
氮化铝粉末是一种具有优异性能的材料,被广泛应用于许多领域。
氮化铝粉末在电子行业中具有重要地位。
由于氮化铝具有良好的导热性和绝缘性能,它被广泛用作高功率电子器件的散热材料。
例如,氮化铝粉末可以用于制造LED封装材料,LED是一种高效节能的照明设备,而氮化铝粉末的应用可以提高LED的散热性能,延长其使用寿命。
此外,氮化铝粉末还可以用于制造功率模块、电子封装材料等。
氮化铝粉末在陶瓷行业中也有广泛的应用。
氮化铝具有优异的耐磨性、抗腐蚀性和高温稳定性,因此被广泛应用于制造陶瓷刀具、陶瓷瓷器等产品。
氮化铝粉末可以用于制备高硬度的陶瓷刀具,这些刀具具有优异的切削性能和耐磨性,适用于加工硬质材料。
同时,氮化铝粉末还可以用于制造高温陶瓷材料,用于制造耐火砖、耐火涂料等,具有良好的耐高温性能。
氮化铝粉末还在光电子行业中具有重要作用。
氮化铝具有优异的光学性能,可用于制造光学窗口、光学镜片和光学涂层等光学元件。
氮化铝粉末可以用于制备高透明度和高硬度的光学材料,这些材料可广泛应用于光学仪器、激光器、光纤通信等领域。
除了上述应用领域,氮化铝粉末还具有其他一些特殊的应用。
例如,氮化铝粉末可以用于制备陶瓷纳米复合材料,这些复合材料具有优异的力学性能和热性能,适用于航空航天、汽车工业等领域。
此外,氮化铝粉末还可以用于制备高导热材料,用于制造散热器、导热胶等产品。
氮化铝粉末是一种具有广泛应用的材料。
它在电子、陶瓷、光电子等行业中发挥着重要作用,可以用于制造散热材料、陶瓷刀具、光学元件等产品。
随着科技的不断发展,氮化铝粉末有望在更多领域得到应用,为各行各业带来更多的创新和发展机遇。
氮化铝与氮化硼相结合
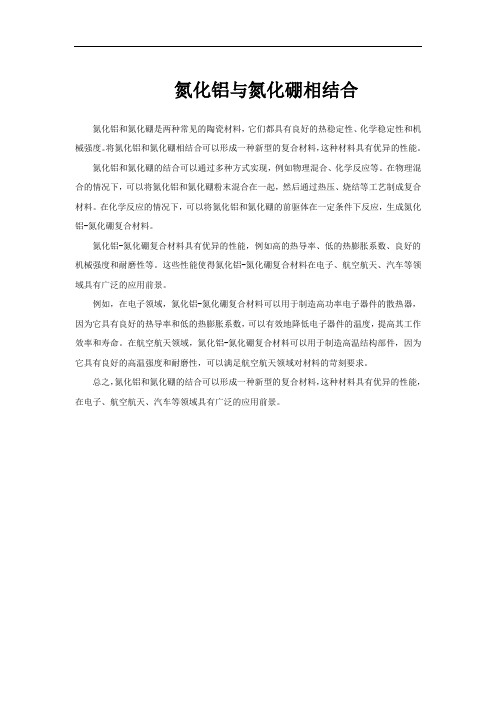
氮化铝与氮化硼相结合
氮化铝和氮化硼是两种常见的陶瓷材料,它们都具有良好的热稳定性、化学稳定性和机械强度。
将氮化铝和氮化硼相结合可以形成一种新型的复合材料,这种材料具有优异的性能。
氮化铝和氮化硼的结合可以通过多种方式实现,例如物理混合、化学反应等。
在物理混合的情况下,可以将氮化铝和氮化硼粉末混合在一起,然后通过热压、烧结等工艺制成复合材料。
在化学反应的情况下,可以将氮化铝和氮化硼的前驱体在一定条件下反应,生成氮化铝-氮化硼复合材料。
氮化铝-氮化硼复合材料具有优异的性能,例如高的热导率、低的热膨胀系数、良好的机械强度和耐磨性等。
这些性能使得氮化铝-氮化硼复合材料在电子、航空航天、汽车等领域具有广泛的应用前景。
例如,在电子领域,氮化铝-氮化硼复合材料可以用于制造高功率电子器件的散热器,因为它具有良好的热导率和低的热膨胀系数,可以有效地降低电子器件的温度,提高其工作效率和寿命。
在航空航天领域,氮化铝-氮化硼复合材料可以用于制造高温结构部件,因为它具有良好的高温强度和耐磨性,可以满足航空航天领域对材料的苛刻要求。
总之,氮化铝和氮化硼的结合可以形成一种新型的复合材料,这种材料具有优异的性能,在电子、航空航天、汽车等领域具有广泛的应用前景。
氮化铝—氮化硼复合陶瓷的制备和性能
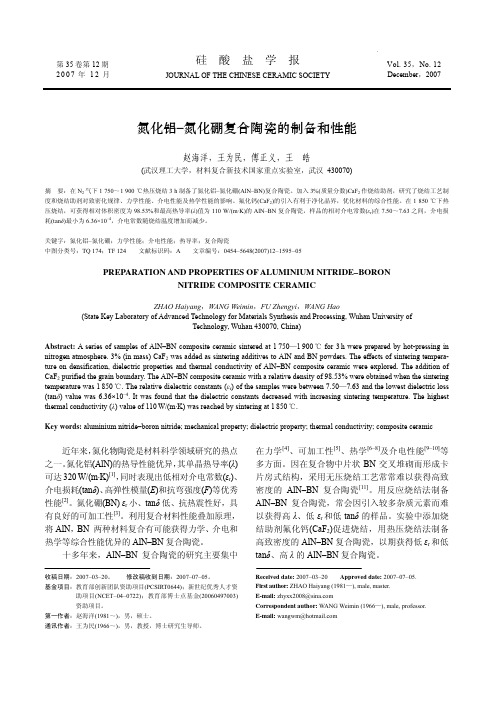
王海龙等:二硼化锆基超高温陶瓷的制备及性能· 1595 ·第35卷第12期氮化铝–氮化硼复合陶瓷的制备和性能赵海洋,王为民,傅正义,王皓(武汉理工大学,材料复合新技术国家重点实验室,武汉 430070)摘要:在N2气下1750~1900℃热压烧结3h制备了氮化铝–氮化硼(AlN–BN)复合陶瓷。
加入3%(质量分数)CaF2作烧结助剂,研究了烧结工艺制度和烧结助剂对致密化规律、力学性能、介电性能及热学性能的影响。
氟化钙(CaF2)的引入有利于净化晶界,优化材料的综合性能。
在1850℃下热压烧结,可获得相对体积密度为98.53%和最高热导率(λ)值为110W/(m·K)的AlN–BN复合陶瓷,样品的相对介电常数(εr)在7.50~7.63之间,介电损耗(tanδ)最小为6.36×10–4,介电常数随烧结温度增加而减少。
关键字:氮化铝–氮化硼;力学性能;介电性能;热导率;复合陶瓷中图分类号:TQ 174;TF 124 文献标识码:A 文章编号:0454–5648(2007)12–1595–05PREPARATION AND PROPERTIES OF ALUMINIUM NITRIDE–BORONNITRIDE COMPOSITE CERAMICZHAO Haiyang,WANG Weimin,FU Zhengyi,WANG Hao(State Key Laboratory of Advanced Technology for Materials Synthesis and Processing, Wuhan University ofTechnology, Wuhan 430070, China)Abstract: A series of samples of AlN–BN composite ceramic sintered at 1750—1900℃ for 3h were prepared by hot-pressing in nitrogen atmosphere. 3% (in mass) CaF2 was added as sintering additives to AlN and BN powders. The effects of sintering tempera-ture on densification, dielectric properties and thermal conductivity of AlN–BN composite ceramic were explored. The addition of CaF2 purified the grain boundary. The AlN–BN composite ceramic with a relative density of 98.53% were obtained when the sintering temperature was 1850℃. The relative dielectric constants (εr) of the samples were between 7.50—7.63 and the lowest dielectric loss (tanδ)value was 6.36×10–4. It was found that the dielectric constants decreased with increasing sintering temperature. The highest thermal conductivity (λ) value of 110W/(m·K) was reached by sintering at 1850.℃Key words: aluminium nitride–boron nitride; mechanical property; dielectric property; thermal conductivity; composite ceramic近年来,氮化物陶瓷是材料科学领域研究的热点之一。
- 1、下载文档前请自行甄别文档内容的完整性,平台不提供额外的编辑、内容补充、找答案等附加服务。
- 2、"仅部分预览"的文档,不可在线预览部分如存在完整性等问题,可反馈申请退款(可完整预览的文档不适用该条件!)。
- 3、如文档侵犯您的权益,请联系客服反馈,我们会尽快为您处理(人工客服工作时间:9:00-18:30)。
Key words:aluminum nitride—bomn ni廿ide composite ceramics;thennal conductiVity;densi匆ing;microstmcture
摘要:以比表面积为4.26m!/g、氧含量(质量分数,下同)为O.98%和比表面积为17.4m2/g、氧含量为1.69%的2种AlN粉末为原料,用无压烧结工 艺制备氮化铝氮化硼(AlN 15BN,BN为1 5%)复合陶瓷,研究了A1N粉末对复合陶瓷显微结构和性能的影响。结果表明:AlN粉末对复合陶瓷的致 密化过程以及陶瓷的性能有重要影响。由丁二高比表面积AlN粉末的烧结活性好,AlN一15BN复合陶瓷的烧结致密化温度主要集中在l 500~1 650℃之 间。在l 650℃烧结3 h后,A1N—15BN复合陶瓷的相对密度可达95.6%,热导率为108.4 w,(m·K),硬度日R。为72。继续升高烧结温度,AlN一15BN 复合陶瓷的致密度变化/{;大,热导率升高,硬度下降。在1 850℃烧结后,AlN-一15BN复合陶瓷的热导率为132.6 w“m·K),Rockwell硬度(^,R。)为64.2。 低比表面积的AlN粉末所制备的AlN—15BN复合陶瓷的致密化过程主要发生在1 650~1 800℃间。在1 850℃烧结3 h,制备出AlN一15BN复合陶瓷 的相对密度为86.4%,热导率为104.2W/(m·K),环.为56.2。
combustion precursor was at 1 500—1 650℃.The AlN一1 5BN ceramics with relative density 95.6%and Rockwell hardness日R.=72
were obtained aRer sintering at 1 650℃for 3 h.The density of this composite did not increase with the cominual increase of sintering
关键词:氮化铝一氮化硼复合陶瓷:热导率 致密化;显微结构 中图分类号:T0174 文献标识码:A 文章编号:045和5648(2007)03一0332一05
EFFECT oF ALUMINUM NITRIDE PoWDER CHARACTEIUSTICS oN MICRoSTRUCTURE AND PRoPERTIES oF ALUMINUM NITRIDE—BoRoN NITRIDE CoMPoSITE CERAMICS
12.8
w(N)/ %
33.20 32.56 42.61
w(O)/ % 0.98
w(Fo), %
0.001 3 0.00l 0 0.0100
w(Si)/ %
O.00l 1 0.OOO 8 O.0500
w(Ca)/ %
0.0180 O.001 2 O.0400
Ⅵ,(Ni)/ %
0.001 O O.000 5 O.0100
of Anq powder have a great innuence on the densification
temper籼e and Dr0Derties of A1N—l 5BN cer锄ics.The densification
of composite ceramics with AlN powders sVnthesized from the
!:≥刀v膨,理7,,D己,.砌P,f1._,s己刀、rwPfl,.L,.S而甜日f1,Q乙r.j氲口聆办“j1,3 (1.school of Materials Science and Engineering,univers崎of science and Technology Beijing,Beijing 100083;2.school of
末2的平均粒径为0.1哪。
。
AlN Dowder l AlN powder 2 BN
Tablel
表1原料粉末的性能 Properties of raw material powde邢
Meall panicle size/ Specmc surface arca/
um
(m二·f。)
0.4
4.26
17.4
AlN__BN复合陶瓷结构和性能的影响,至今尚未见 相关报道。实验中,用2种比表面积不同的AlN粉 末为原料,研究了无压烧结工艺下,AlN粉末特性 对AlN_BN复合陶瓷致密化行为以及显微结构和性 能的影响。
1实
验
用碳热还原法制备2种AlN粉末,其中:用沉 淀前驱物制备AlN粉末1:用低温燃烧合成前驱物 制备A1N粉末2,具体制备工艺如文献[9—1 0]所述。 h_BN粉末为市售粉末。表1列出了2种AlN粉末 和BN粉末的性能。由表l可以看出:2种AlN粉 末的比表面积和氧含量f质量分数,下同)差别较大, AlN粉末1的比表面积和氧含量分别为4.26 m2儋和 0.98%;A1N粉末2的比表面积和氧含量分别为17.4 m2/g和1.69%,均高于AlN粉末1的。图l为2种 AlN粉末的SEM照片。由图1可以看出:2种粉末 均为形状规则的近球形颗粒,分散性能良好,其中: AlN粉末1粒度较粗,平均粒径为0.4 um;AlN粉
h-BN陶瓷属于共价化合物,固相扩散系数低, 是一种很难烧结的材料。另外,由于h_BN为片状 晶体结构,高温下烧结时这种片状晶体结构的生长 不仅不能使陶瓷致密,反而会由于片状晶体的长大 形成卡片房式结构,起到支撑作用而阻碍材料的收 缩和致密【5剖。为了获得高致密度的BN复合陶瓷, Kanai等【7J研究了不同的烧结工艺,并通过添加CaC2, Y203,Cao和M90等烧结助剂,在热压条件下制 备出致密度大于96%的复合陶瓷。众所周知,除了 改善烧结方式外,提高粉末烧结活性是促进材料致 密化的另一条重要途径,Hagio等【8J用机械一化学活 化法提高了h_BN的活性,使其烧结性能得到明显 改善。然而,通过改变AlN粉末性能来制备AlN-_BN 复合陶瓷,研究无压烧结工艺中A1N粉末特性对
氮化铝(A1N)陶瓷具有高的热导率、可靠的电绝 缘性、耐高温、耐腐蚀、无毒、良好的力学性能以 及与硅相匹配的热膨胀系数等一系列优良性能,在
许多高技术领域的应用越来越广泛【1。2]。但是,AlN 陶瓷材料硬度高(Rockwell硬度%h=90左右)、脆性 大,难以机械加工。六方氮化硼(h_BN)陶瓷具有层
Received date:2006_09_07.
Approved date:2006_11_08.
First author:QrN Mingli(1975 )'male,doctoh associate research fellow.
E-mail:mlqin75@hotmail.com Correspondent author:DU Xueli(1972一),female,postgmduate student for
第35卷第3期 2007年3月
硅酸盐学报
JOURNAL 0F THE CHnqESE CERAMIC SOCIETY
V01.35,No.3 March,2007
氮化铝粉末特性对氮化铝一氮化硼复合陶瓷结构和性能的影响
秦明礼1,杜学丽1,一,孙伟1,李帅1,曲选辉1,3
(1.北京科技大学材料科学与工程学院,北京100083;2.天津理工大学材料科学与工程学院,天津300191; 3.北京科技大学,新金属材料国家重点实验室,北京100083)
Materials science and Engineering,Tianjin univers毋ofTechnology,Tianjin 300191;3.state Key Laboratory for Advanced Metals and Materials,Universi够of Science and Tecllnolog)r Beijing,Beijing 1 00083,China)
用mchimedes排水法测量AlN陶瓷烧结样品的 密度。用NETzSCH LFA 427激光热导仪测定烧结 样品的热扩散系数0[,然后计算所制备A1N陶瓷样 品的热导率∥11】。用日本3014_z2型X射线衍射 (X.ray di衢action,XRD,Cu K。)仪分析不同温度下 烧结样品的物相组成。用JSM一5600LU型扫描电镜 (scann 万ing方e数lec据tron microscope,SEM)观察陶瓷材料
¨,(c)/ %
O.0800 O.1700
一
以无水乙醇为介质,在塑料罐中将A1N粉末、 BN粉末和Y203粉末湿法混磨3~5h后,将浆料于 70℃烘干、粉碎、过筛。将所得混合粉末先后用单 向钢模压制和冷等静压成型,制得陶瓷素坯。将素 坯放入石墨坩埚中烧结,在氮气流速为1.0 L/min的 立式碳管炉加热烧结,升温速率为3℃/min,烧结 温度在1 400~1 850℃之间,在适当的温度保温3h, 制备出烧结样品。
cer锄ics.The of BN is 1 5%in mass)comDosite
effbct of AlN powder chamcteristics on the microstructure and properties of
ch撇cteristics AlN—l 5BN composites were studied.It was found that the
tempera_cI】re.However’me thennal conductivity was increased with the increasing ofsintering temperatlJre and could reach 132.6W/(m·K)
when simered at 1 850℃,but the hardness was reversed to日蠢.=64.2.For ArN—15BN cer锄ics prepared with powders synthesized fbm the precipitated precursor’the densification tempera_cllre was in the r肌ge of 1 650_一1 800℃.The AlN一1 5BN cer锄ics with relative den—