300吨汽车吊支腿受力计算书
汽车吊受力计算范文

汽车吊受力计算范文汽车吊是用于吊装汽车或其他货物的设备,承受着吊装物体的重量和施加在吊装链条上的拉力。
在进行汽车吊受力计算时,需要考虑吊装物体的重力、摩擦力、加速度等因素,并根据实际情况选择合适的安全系数。
首先,我们来计算吊装物体的重力对吊装链条的拉力产生的影响。
假设吊装物体的重量为W,重力加速度为g,那么吊装链条的拉力F可以通过以下公式计算:F=W+Ff其中W是吊装物体的重量,Ff是由于摩擦力引起的链条和物体间的附加拉力。
摩擦力是通过吊装链条与物体接触面之间的摩擦产生的,通常情况下可以忽略不计。
但是如果链条与物体之间存在滑动的情况,摩擦力就不可忽略了。
当链条与物体之间存在滑动时,摩擦力Ff可以通过以下公式计算:Ff=μN其中μ是摩擦系数,N是吊装物体的重力对吊钩产生的垂直力。
垂直力N可以通过以下公式计算:N=W-T其中T是吊钩和吊装链条上任意连接点之间的摩擦力。
当吊钩和吊装链条之间存在摩擦时,摩擦力会受到吊钩和吊装链条所受力的影响。
可以根据实际情况估算T的大小。
除了重力和摩擦力,汽车吊还需要考虑加速度对吊装链条的影响。
当物体处于加速状态时,吊装链条上会产生额外的拉力。
根据牛顿第二定律,额外的拉力可以通过以下公式计算:Fa=m*a其中m是吊装物体的质量,a是物体的加速度。
Fa为吊装链条在加速状态下所承受的额外拉力。
最后,在进行受力计算时还要考虑安全系数。
安全系数是指实际所需的最小工作载荷与计算得到的吊装链条的极限工作载荷之间的比值。
通常情况下,安全系数的取值范围为4到5,但是在一些特殊应用场景中,安全系数的值可能需要进一步增加。
综上所述,汽车吊的受力计算主要包括重力、摩擦力、加速度的计算,并根据实际情况选择合适的安全系数。
在实际应用中,为了确保吊装链条的安全性,建议在计算得到的拉力基础上增加一定的裕量。
另外,还需要定期对吊装链条进行检查和维护,确保其正常工作和使用寿命。
汽车吊机支腿反力计算及梁板受力分析
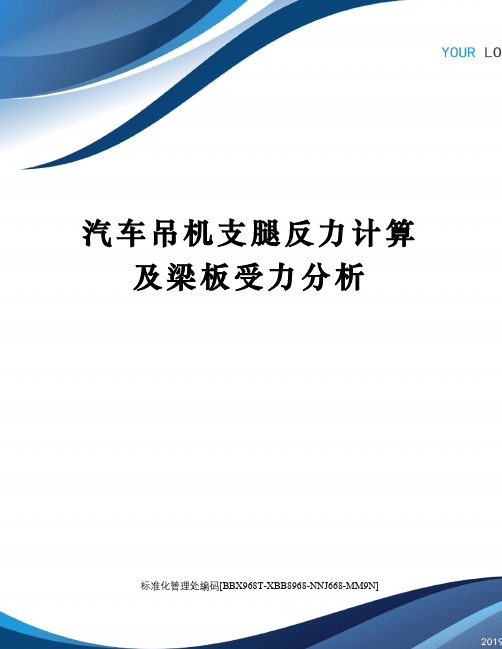
汽车吊机支腿反力计算及梁板受力分析标准化管理处编码[BBX968T-XBB8968-NNJ668-MM9N]附件三:汽车吊机支腿反力计算及梁板受力分析一、模型建立及臂架回转过程受力分析汽车吊机四点支承受力计算模型简图如图1所示,G0为下车重量;G1为上车和吊重的重量和,移到位于对称轴上的回转中心后产生力矩M;e0、e1为G、G1位置到四支腿中心的距离,按对称轴为直角坐标系定位。
R1、R2、R3、R4分别是四支腿的支反力,其中R3、R4为近吊装物处两支腿反力,徐工QY130K汽车起重机支腿间距如图1中,a=,b=。
为简化计算,假设4条支腿支撑在同一水平面内,它们的刚度相同且支撑地面的刚度相同。
1、支点反力计算公式由图1受力简图,分别计算臂架转化来的集中力矩M和吊重P,最后在支腿处迭加,根据受力平衡可得:图1 四支腿反力简图e 0、e1为G、G1位置到四支腿对称中心的距离。
2、计算底盘重心点位置当架吊机设边梁时,所需吊幅最大,为13m,臂长约为,根据额定起重表,幅度14m、臂长最大吊重为>22t,满足起吊要求。
徐工QY130K汽车起重机车长,宽3m,行驶状态车重55t,主要技术参数详见表1。
表1 徐工QY130K汽车起重机主要参数吊机支腿纵向距离,横向距离,支腿箱体位于2桥和3桥之间以及车架后端,工作时配重38000kg 。
根据车轴及转盘中心位置计算吊装下车重心点G 0,尺寸位置关系详见图2,由合力矩确定的平行力系中心即为吊车重心。
图2 车轴及转盘中心位置尺寸由轴重参数得:下车重量G 0=9100+9100+9100+12500+12700+9700=62200 kg上车配重重量=38000 kg上车未加配重时重心到车后边缘距离Rc 为:9700312700 4.412500 5.7591007.62910010.04910011.46622006.78Rc m ⨯+⨯+⨯+⨯+⨯+⨯== 则下车重心G 0到臂架回转中心G 1的纵向距离为工作臂架回转中心G 1到两后支腿的纵向距离为,上车配重及吊重支点G1到支腿对称轴中心O点距离e1=,下车重心G到支腿对称中心O的距离e=。
300吨汽车吊支腿受力计算书

300吨汽车吊支腿受力计算书
300吨汽车吊支腿下地基承载力计算
考虑到300吨吊车吊装时的实际工况,吊车吊装过程中,吊装空心板
梁、配重与吊车两个支脚成一条直线时为吊车最不利受力状态(如下图所示),故进行支腿承载力计算时,根据1-1吊车受力平面图进行计算,根据图示可知,空心板梁重吊车自重G i=69t,力臂L i=,吊重(空心梁+钢丝绳)
G2二、力臂L2=,吊车配重G3=100t、力臂L3=,根据受力状态图可列方程为:
G i x +G3 x =G2XX
将数据代入以上公式,可得:R i=604KN
混凝土支点自重:2m*3m*2m*25KN/m=300KN,则支点处受力和为:
604+300=904KN故支点处应力为:904/ (2*3)=151Kpa,根据设计资料,在站台面以下2m处地质为硬质粘土0=250Kpa> 151Kpa,故满足地基承载力要求。
L1- -
1 11
用转时旱否利受力状态半匡冬
2)汽车吊选用:
根据提供汽车吊工况参数表以及梁体、吊车自重可查表选择,取双机
抬吊折减系数;吊装示意图如下所示:
吊装空心板梁时:选用两台75t汽车吊,工作半径7m,臂长18m 时对应起吊能力为:32t;故一台吊车吊装能力:32*=>(+)/2=,满足吊装要求。
吊装300t汽车吊时:选用一台100t、一台200t汽车吊,其中100t汽车吊工作半径6m,臂长时对应起吊能力为:47t;200t汽车吊工作半径12m,臂长对应起吊能力为:,故100t吊车吊装能力:47*=>,满足吊装要求。
NK7O礎冃平板
孝感站内山道
3COT吊车。
300t桥式起重机设计计算书

300t桥式起重机设计计算书原始参数:跨度= 33.4起重量: 320起升高度: 221)。
截面确定,主要参数列表上翼缘板厚度δ1= 20下翼缘板厚度δ2= 20主腹板厚度δ3= 14副腹板厚度δ4= 12腹板高度H= 2650腹板内侧宽度B= 1800上翼缘板宽度B1= 2075下翼缘板宽度B2= 1920小车轨距b= 6, 小车基距= 4.385大车轴距= 6一,总体设计桥架尺寸的确定1.大车轴距B0=(1/4 ~1/6)L= 8.35~ 5.666667根据小车轨距和偏轨箱形梁宽度以及大车运行机构的设置,取BO= 6,端梁全长 6 2.主梁尺寸高度 h=(1/14~1-17)L= 2.571429~ 1.235294取腹板高 h0= 2650主梁总高度 H1= 2690主梁宽度 b=(0.4~0.5)H1= 1076~ 1345取b= 1800主梁端部变截面长d=L/8= 4.175取d= 4.173.端梁尺寸高度H2≈0.5*H1= 1345取H2= 1200考虑大车轮安装,端梁内宽b0= 540总宽B2= 900,上翼缘板厚δ1= 20,下翼缘板δ2= 20,腹板δ3= 16 二.主,端梁截面几何性质主梁: A= 148800A0= 4840710形心: x1= 852.3763x2= 1013.624y1= 1317.1875y2= 1372.8125Ix= 2968.75I1=Iy= 897.1606端梁 A= 74400Ix=I2=Iy= 5.398525E+09三.载荷1.固定载荷主梁自重载荷Fq'=k*ρ*A*g= 16042.41072填充系数k取k=1.4,考虑走台重量小车轨道重量 Fg=mg*g= 1111.6692栏杆等重量 Fl=ml*g= 981主梁的匀布载荷Fq=Fq'+Fg+Fl= 18135.079922.小车轮压.满载小车静轮压ΣP =Pj1+Pj2= 20950003.动力效应系数Ψ1=1.1Ψ2=1+0.7*Vq= 1.066667Ψ4=1.1+0.058*Vd*h^0.5= 1.162833(h=1mm)统一取较大值Ψ= 1.1628334.惯性载荷大,小车都是8个车轮,其中总轮数是主动轮的I= 4倍,按车轮打滑条件确定大,小车运行的惯性力一根主梁上的小车惯性力为Pxg=ΣP/(I*7)= 74821.86大车运行起,制动惯性力(一根主梁上)为PH=ΣP/(I*7)= 74821.86FH=Fq/(I*7)= 647.6814主梁跨端设备惯性力影响小,忽略不计5.偏斜运行侧向力一根主梁的重量为PG=Fq(L-0.4)= 598457.63736一根端梁单位长度的重量为:Fq1=k*ρ*A*g= 16042.41072一根端梁的重量为PGd=Fq1*B= 37814.25384一组大车运行机构的重量(两组对称配置)为PGj=mj*g= 7877.43司机室及设备的重量(按合力计)为PGs=ms*g= 19620333333(1),满载小车在主梁跨中央左侧端梁总静轮压计算PR1=0.5*(PQ+PGx)+0.5*(2*PG)+PGs*(1-d2/L)+PGj+PGd= 2886807.0457509由L/B0= 5.666667,查得λ=0 .1927778侧向力为Ps1=0.5*PR1*λ= 278256.5(2)满载小车在主梁左极限位置左侧端梁总静轮压为PR2 = (PQ + PGx) * (1 - 2 / L) + PG + PGs * (1 - 3 / L) + PGj + PGd= 3760641. 测向力为:PS2=0.5*PR2*λ= 362484.06.扭转载荷偏轨箱形梁由ΣPh和PH的偏心作用而产生移动扭矩,其他载荷PGj,PGs产生的扭矩较小且作用方向相反,故不计算44444偏轨箱形梁弯心在梁截面的对称形心X轴上(不考虑翼缘外伸部分),弯心至主腹板中线的距离为e1=δ2*(b-δ1/2-δ2/2)/(δ1+δ2)= 836.9231轨道高hg= 150h''=0.5*H1+hg= 1495移动扭矩为Tp=ΣP*e1= 1753031.N.MTH=PH*h''= 111858N.M四,主梁计算1.内力(1)垂直内力计算大车传动侧的主梁.在固定载荷与移动载荷的作用下,主梁按简支梁计算,55555固定载荷作用下主梁跨中的弯矩为Mq=Ψ * (Fq * L ^ 2 / 8 + PGj * 0.94 / 2 + PGs * 3 / 2)= 2979154.跨端剪切力为:Fqc=Ψ * (0.5 * Fq * L + PGj + PGs * (1 - 3 / L))= 382096.1移动载荷作用下主梁的内力1) 满载小车在跨中,跨中E点弯矩为Mp=Ψ * ΣP / (4 * L) * (L - b1) ^ 2轮压合力ΣP与左轮的距离为b1=P2*b/ΣP= 2.7则,Mp= .1124064跨中E点剪切力为Fp=0.5 * Ψ * ΣP * (1 - b1 / L)= 999253.1跨中内扭矩为Tn= 0.5 * (Ψ * TP + TH)= 10751712).满载小车在跨端极限位置(z=e1),小车左轮距梁端距离为C1 = e1-l1≈ 2-0.48 * b=0-.1048跨端剪切力为Fpc=Ψ * ΣP * (L - b1 - C1) / L 2246846.跨端内扭矩为Tn1=(Ψ * TP + TH) * (1 - e1 / L)= 2021578.主梁跨中总弯矩为Mx=Mq+Mp= .2403829主梁跨端总剪切力(支撑力)为FR=Fc=Fqc+Fpc= 2628943.09864868(2)水平载荷1)水平惯性载荷.在水平载荷PH及FH作用下,桥架按刚架计算.因偏轨箱形梁与端梁连接面较宽,应取两主梁轴线K'代替原小车轨距K构成新的水平刚架,这样比较符合实际,于是K'=K+2*x1= 7.010753b=K'/2= 3.505376a=0.5*(B0-K')=-.5053764水平刚架计算模型66666①.下车在跨中,刚架的计算系数为:r1 = 1 + 2 * a * b * 7 / (3 * (a + b) * L)= .4332559跨中水平弯矩(与单梁桥架公式相同)为:MH = PH / 4 * L * (1 - 1 / (2 * r1)) + FH / 8 * L ^ 2 * (1 - 2 / (3 * r1))= 275 221.5跨中水平剪切力为Fph≈0.5*PH= 37410.43跨中轴力为NH = (a - b) / (a * b * r1) * (FH * L ^ 2 / 12 + PH * L / 8)= 630239.003709905 ②小车在跨端.跨端水平剪切力为F'CH= FH * L * 0.5 + PH * (1 - 2 / L)= 81157.382)偏斜侧向力.在偏斜侧向力作用下,桥架也按水平刚架分析,这时,计算系数为rs=1+K'*I1/(3*L*I2)= 2.840749①小车在跨中,侧向力为PS1= 278256.5超前力为Pw1=PS1*B0/L= 49986.56端梁中点的轴力为Nd1=0.5*Pw1= 24993.08端梁中点的水平剪切力为Fd1=PS1 * (0.5 - a / K' / rs)= 153222.8主梁跨中的水平弯矩为Ms= PS1 * a + Fd1 * b - Nd1 * 0.5 * L=-64284.9主梁轴力为Ns1=PS1-Fd1= 125033.7主梁跨中总的水平弯矩为My=MH+Ms= 210936.6②小车在跨端.侧向力为PS2= 362484.0超前力为PW2= PS2 * B0 / L= 65116.71端梁中点的轴力为Nd2=0.5*PW2= 32558.35端梁中点的水平剪切力为Fd2=PS2 * (0.5 - a / k' / rs)= 199603.4主梁跨端的水平弯矩为Mcs=PS2 * a + Fd2 * b= 459982.3主梁跨端的水平剪切力为Fcs=Pw2-Nd2= 32558.35主梁跨端总的水平剪切力为FcH=F'cH+Fcs= 113715.8小车在跨端时,主梁跨中水平弯矩与惯性载荷下的水平弯矩组合值较小,不需计算2.强度需要计算主梁跨中截面的危险点①,②,③的强度(1)主腹板上边缘点①的应力主腹板边至轨顶距离为hy=hg+δ1= 170σm = Ψ * Pj1 / (2 * hy + 50) / δ3= 227.5192垂直弯矩产生的应力为σ01 = Mx *y / Ix= 29.86319水平弯矩产生的应力为σ02= My * X1 / Iy= 2.154519E-03惯性载荷与侧向力对主梁产生的轴向力较小且作用方向相反,应力很小,故不计算主梁上翼缘的静矩为Sy=δ1 * B1 * ( Y1 - 0.5 * δ1)= .25主腹板上边的切应力为τ = Fp * Sy / (Ix * (δ3 + δ4)) + Tn / (2 * A0 * δ3)= 2.491124点①的折算应力为σ0=σ01+σ02= 29.30334σ1 = (σ0 ^ 2 + σm ^ 2 - σ0 * σm + 3 * τ ^ 2) ^ 0.5= 214.9575(2) 点②的应力σ2 = (Mx * Y2 / Ix + My * (B1 - x1111) / Iy) = 154.4977(3) 点③的应力;σ3 = 1.15 * ((Mx * Y2 / Ix + My * (x2 - 20) / Iy)) = 177.1513(4)主梁跨端的切应力主梁跨端截面变小,为便与主,端梁联接,取腹板高度等于端梁高度hd= 1240mm,跨端只需计算切应力1) 主腹板,承受垂直剪力FC及扭矩Tn1,故主腹板中点切应力为τ = 1.5 * FC / hd / (δ3 + δ4) + Tn1 / 2 / δ3 / A0主梁跨端封闭截面面积为A0=(B+0.5*δ1+0.5*δ2)*(h0+δ0)= 4840710( δ0为端梁翼缘板厚度)代入上式τ = 1.5 * FC / hd / (δ3 + δ4) + Tn1 / 2 / δ3 / A0= 153.162副腹板中两切应力反向,可不计算2).翼缘板.承受水平剪应力Fch= 113715.8及扭矩Tn1= 2021578.τ = 1.5 * FcH / (δ1 * (2 * B1 + B2)) + Tn1 / (2 * δ1 * A0)= 24.5106主梁翼缘焊缝厚度取hf= 14mm,采用自动焊,不需计算3.主梁疲劳强度校核桥架工作级别为A 5,应按载荷组合I计算主梁跨中的最大弯矩截面(E)的疲劳强度由于水平惯性载荷产生的应力很小,为了计算简明而忽略惯性应力求截面E的最大弯矩核最小弯矩,满载小车位于跨中(轮压P1在E点上),则Mmax=Mx= .24038297空载小车位于右侧跨端时左端支反力为FR1 ≈ 17088.74532Mmin = Mq + Ψ * FR1 * (L - 1.5) * 0.5= 3296102.3626827(1)验算主腹板受拉翼缘焊缝④的疲劳强度888σmax=Mx * (Y2 - δ1) / Ix= 149.0652σmin=Mmin * (Y2 - δ1) / Ix = 24.66905应力循环特性r=σmin/σmax=0 .3623882根据工作级别A 5,应力集中等级K1及材料Q235,查的[σ_1]= 0MPa,σb=370MPa焊缝拉伸疲劳许用应力为[σr1]=1.67*[σ_1]/(1-r*(1-[σ_1]/0.45/σb))= 0σmax= 149.0652<[σr1]. (合格)(2) 验算横隔板下端焊缝与主腹板联接处⑤σmax = Mx * (Y2 - 50 - δ2) / Ix= 0σmin = Mmin * (Y2 - 50 - δ2) / Ix= 0r=σmin/σmax=0 0显然,相同工况下的应力循环特性是一致的根据A 5及Q235,横隔板采用双面连续贴角焊缝连接,板底与受拉翼缘间隙为50mm,应力集中等级为K3,查得[σ_1]= 0拉伸疲劳许用应力为[σr1]=1.67*[σ_1]/(1-r*(1-[σ_1]/0.45/σb))= 0σmax= 0<[σr1]. (合格)由于切应力很小,忽略不计4.主梁稳定性(1)整体稳定性主梁高宽比h/b= 1.45(2)局部稳定性翼缘板b0/δ0= 90需要设置一条纵向加强劲,不再验算翼缘最大外伸部分be/δ0= 8.75(稳定)主腹板 h0/δ3= 189.5714副腹板 h0/δ4= 220.3333需要设置横隔板及一条纵向加强劲,主,副腹板相同,不再验算隔板间距a= 2650mm,纵向加劲肋位置h= 662.5mm1)验算跨中主腹板上区格I得稳定性,区格两边正应力为σ1=σ01 + σ02= 29.30334σ2 = σ01 * (Y1 - h - δ1) / ( Y1 - δ1) + σ02= 13.71399ξ=σ2/σ1=0 .52601(属于不均匀压缩板)区格I得欧拉应力为σE = 18.6 * (100 * δ3 / b) ^ 2= 83.06(b=h= 662.5)区格分别受σ1,σm和τ作用时得临界压力为σ1cr=χ*Kσ*σE嵌固系数χ=1.2,α=a/b= 4,屈曲系数Kσ=8.4/(ξ+1.1)= 5.648665则σ'1cr=χ*Kσ*σE= 532.4247需修正,则σ1cr=235 * (1 - 235 / 5.3 / σ'1cr)= 215.6789腹板边局部压应力σm= 227.5192压力分布长c=2*hy+50= 390α=a/b= 4 >3,按a=3b计算α==3β=c/a=c/(3b)= .4166039区格I属双边局部压缩,板得屈曲系数为Km=0.8 * (2 + 0.7 / α ^ 2) * (1 + β) / β/ α= 3.377721σ'mcr= χ * Km * σE= 336.5089需修正,则σmcr = 235 * (1 - 235 / 5.3 / σ'mcr)= 204.0938区格平均切应力为τ = Fp / h0 / (δ3 + δ4) + Tn / (2 * A0 * δ3)= 22.4113由α=a/b= 4>1,板得屈曲系数为Kτ=5.34+4/α^2= 5.59τ'cr = χ * Kτ * σE= 557.99613^0.5*τ'cr= 965.05263^0.5*τcr=235 * (1 - 235 / 5.3 / (3^0.5τ'cr))= 224.0223τcr=3^0.5*τcr/3^0.5= 129.7572区格上边缘得复合应力为(σ1 ^ 2 + σm ^ 2 - σ1 * σm + 3 * τ ^ 2) ^ 0.5= 217.3781α=a/b= 4>2,区格的临界复合应力为σcr = (σ1 ^ 2 + σm ^ 2 - σ1 * σm + 3 * τ ^ 2) ^ 0.5 / ((1 + ξ) / 4 * (σ1 / σ1cr) + (((3 - ξ) / 4 * (σ1 / σ1cr)) ^ 2 + (σm / σmcr) ^ 2 + (τ / τcr)) ^ 0.5)= 175.1041[σcr]=σcr/n= 175.1041/3= 131.7249(σ1 ^ 2 + σm ^ 2 - σ1 * σm + 3 * τ ^ 2) ^ 0.5<[σcr]区格II的尺寸与I相同,而应力较小,故不需再计算,主腹板外测设置短加紧肋,与上翼缘板顶紧以支撑小车轨道,间距a1= 662.5mm2)验算跨中副腹板上区格I的稳定性.副腹板上区格I只受σ1及τ的作用.区格两边的正应力为σ1 = σ01 + σ02 * (x2 - ((B1 - B) / 2 - δ3 / 2)) / X1= 29.13297σ2 = σ01 * (Y1 - Hh - δ1) / ( Y1 - δ1) + σ02 * (x2 - ((B1 - B) / 2 - δ3 / 2)) / X1= 13.54362切应力为:τ = Fp / H / (δ3 + δ4) - Tn / (2 * A0 * δ4)= 5.09597(很小)区格I的欧拉应力为σE = 18.6 * (100 * δ4 / b) ^ 2= 61.0314ξ=σ2/σ1=0 .5000227(属于不均匀压缩)α=a/b= 4>1屈曲系数Kσ=8.4/(ξ+1.1)= 5.011532σ'1cr=χ*Kσ*σE= 391.0216σ'1cr>0.75σs需要修正,则σ1cr= 235 * (1 - 235 / 5.3 / σ'1cr)= 215.6789α=a/b= 4>1,Kτ=5.34+4/α^2= 5.59τ'cr = χ * Kτ * σE= 409.75223^0.5τ'cr= 709.055需修正,则3^0.5τcr= 235 * (1 - 235 / 5.3 / 3^0.5τ'cr)= 220.6415τcr = 3^0.5τcr / 3 ^ 0.5= 129.7572复合应力为(σ1 ^ 2 + 3 * τ ^ 2) ^ 0.5= 30.43619α=a/b= 4>2,区格I的临界复合应力为σcr = (σ1 ^ 2 + 3 * τ ^ 2) ^ 0.5 / (((1 + ξ) / 4 * (σ1 / σ1cr) + ((3 - ξ) / 4 * (σ1 / σ1cr)) ^ 2 + (τ / τcr)) ^ 0.5)= 98.00591(σ1 ^ 2 + 3 * τ ^ 2) ^ 0.5<σcr/n= 56.35229区格II和跨端应力较小,不再计算3) 加紧肋的确定,横隔板的厚度δ= 8mm,板中开孔尺寸为 2150X 1400mm五,主梁与端梁的连接主,端梁采用连接板贴角焊缝连接.主梁两侧各用一块连接板与主,端梁的腹板焊接,连接板厚度δ= 14mm,高度h1=0.95hd= 1178取h1= 1170mm,主梁腹板与端梁腹板之间留有20~50 mm的间隙,在组装桥架时用来调整跨度.主梁翼缘板伸出梁端套装在端梁翼缘板外侧,并用贴角缝(取hf= 20mm)周边焊住.必要时可在主梁端部内侧主,端梁的上,下翼缘处焊上三角板,以增强连接的水平刚度,承受水平内力,连接构造如下9主梁最大支撑力为FR= 2628943.09864868连接板需要的焊缝长度为lf=1.2 * FR / (2 * 0.7 * hf * 100) + 10= 2826.216实际h1>lf (足够)主,端梁的连接焊缝足够承受连接的水平弯矩和剪切力,故不再计算六. 刚度计算(1) 桥架的垂直静刚度满载小车位于主梁跨中产生的静挠度为Y = ΣP / (48 * 206000# * Ix) * (L ^ 3 - b ^ 2 * / 2 * (3 * L - b))= 42.6 885<[Y]=L/1000 33.4(2)桥架的水平惯性位移X = PH * L ^ 3 / (48 * 206000 * Iy) * (1 - 0.75 / r1) + 5 * FH * L ^ 4 / (384 * 206000 * Iy) * (1 - 0.8 / r1)= .134011<[X]=L/2000= 16.7(3)垂直动刚度起重机垂直动防毒以满载小车位于桥架跨中的垂直自振频率来表征,计算如下全桥架中点换算质量为m1=0.5*(2mG)+mx= 178599.6起升质量m2=mQ+m0= 338870起升载荷 PQ=m2*g= 3296000起升钢丝绳滑轮组的最大下放长度为lr=Hq= 22桥架跨中静位移为Y0 = PQ / (48 * 206000# * Ix * 2) * (L ^ 3 - b ^ 2 / 2 * (3 * L - b))= 33. 23372起升钢丝绳滑轮组的静伸长为λ0 = PQ * lr / (nr * 100000# * Ar)= 0结构质量影响系数为β = m1 / m2 * (y0 / (y0 + λ0)) ^ 2= .4166039桥式起重机的垂直自振频率为fv= 1 / (2*π) * (9810 / (y0 + λ0) / (1 + β)) ^ 0.5= 2.215037>[fv]=2Hz (合格)(4).水平动刚度起重机水平动刚度以物品高位悬挂,满载小车位于桥架跨中的水平自振频率来表征半桥架中点的换算质量为me=0.5*(mG+mx+mQ+m0)= 258734.3半刚架跨中在单位水平力作用下产生的水平位移为δe = L ^ 3 / (48 * 206000# * Iy) * (1 - 0.75 / r1)= 5.036852E-06桥式起重机的水平自振频率为fh = 1 /(2*π)* (1000 / (me * δe)) ^ 0.5= 4.864732fh>[fh]=1.5~2Hz (合格)七.桥架拱度桥架跨度中央的标准拱度值为f0=L/1000= 33.4考虑制造因素,实取y0=1.4*f0= 46.76跨度中央两边按抛物曲线y=y0X(1-4a^2/L^2)设置拱度,距跨中为a1=L/8的点 Y1 = 46.76 * (1 - 4 * (L / 8) ^ 2 / L ^ 2)= 43.8375距跨中为a2=L/4的点 Y2 = 46.76 * (1 - 4 * (L / 4) ^ 2 / L ^ 2)= 35.07距跨中为a3=3L/8的点 Y3 = 46.76 * (1 - 4 * (3*L / 8) ^ 2 / L ^ 2)= 20.4575 至此,桥架结构设计全部合格.仅供个人用于学习、研究;不得用于商业用途。
汽车吊吊装计算书

汽车吊吊装计算书汽车吊吊装计算书附件:附件1:汽车吊吊装计算书根据相关规范、技术规程规定要求,根据吊装重量计算确定吊车型号应考虑安全系数,同时结合本项目特点考虑采用双机抬吊方式吊装的折减系数,复核验算如下:一、预制小箱梁吊装汽车吊工况及验算本项目后张法预应力20m砼预制箱梁单片边梁梁长20m,高1.176米,中板顶宽2.4米,板底宽1.0米,重量为51.25t。
预制小箱梁计划采用汽车吊双机抬吊,吊装钢丝绳位置选择在距构件两端1.5m 的位置。
运输便道及吊装平台地面标高为20.3m,设计桥面标高为24.207m(北0#台)~24.427m(中1#墩)~24.644m(南2#台),桥面结构层厚度为0.2m,则设计小箱梁面标高为24.007m(北0#台)~24.227m(中1#墩)~24.444m(南2#台)。
1.汽车吊的选型及验算(1)0#-1#跨吊装:计划采用一台130T,一台300T汽车吊吊装小箱梁,吊装钢丝绳位置选择在距构件两端1.5m的位置,130T吊车停机在0#桥台,300T 吊车停机在施工平台,先吊装主梁7~主梁4四片箱梁,然后130T吊车站位不变,300T吊车收臂移车到施工便道,吊装主梁3~主梁1三片箱梁。
具体汽车吊站位详见附图。
(2)1#-2#跨吊装:同0#-1#跨吊装。
最不利工况:300t吊车站位0#-1#跨施工平台,吊装最左侧边梁(主梁7),边梁设计混凝土20.5方,重51.25吨。
(3)QY130T汽车吊选型验算1)QY130K汽车起重机起升性能表表1 主臂起重性能表(kg, m)2)130汽车吊起重重量计算G总= Q1+Q2=51.25+2=53.25t式中:Q1—为单片小箱梁的自重,在此取Q1 =51.25吨;Q2—吊车吊钩及索具的重量,Q2=2吨;双机抬吊按一台QY130T型汽车吊负荷平均分配,即单机实际承担的理论载荷为26.63t,考虑动载系数 1.2,安全吊装预制小箱梁的全重(单机承担的)=26.63×1.2=31.95t。
吨汽车吊支腿受力计算书

300吨汽车吊支腿下地基承载力计算
考虑到300吨吊车吊装时的实际工况,吊车吊装过程中,吊装空心板梁、配重与吊车两个支脚成一条直线时为吊车最不利受力状态(如下图所示),故进行支腿承载力计算时,根据1-1吊车受力平面图进行计算,根据图示可知,空心板梁重吊车自重G1=69t,力臂L1=,吊重(空心梁+钢丝绳)G2=、力臂L2=,吊车配重G3=100t、力臂L3=,根据受力状态图可列方程为:
G1×+G3×=G2××
将数据代入以上公式,可得:R1=604KN
混凝土支点自重:2m*3m*2m*25KN/m=300KN,则支点处受力和为:604+300=904KN,故支点处应力为:904/(2*3)=151Kpa,根据设计资料,在站台面以下2m处地质为硬质粘土,σ0=250Kpa>151Kpa,故满足地基承载力要求。
2)汽车吊选用:
根据提供汽车吊工况参数表以及梁体、吊车自重可查表选择,取双机抬吊折减系数;吊装示意图如下所示:
吊装空心板梁时:选用两台75t汽车吊,工作半径7m,臂长18m时对应起吊能力为:32t;故一台吊车吊装能力:32*=>(+)/2=,满足吊装要求。
吊装300t汽车吊时:选用一台100t、一台200t汽车吊,其中100t汽车吊工作半径6m,臂长时对应起吊能力为:47t;200t汽车吊工作半径12m,臂长对应起吊能力为:,故100t吊车吊装能力:47*=>,满足吊装要求。
吨汽车吊支腿受力计算书

吨汽车吊支腿受力计算
书
IMB standardization office【IMB 5AB- IMBK 08- IMB 2C】
300吨汽车吊支腿下地基承载力计算
考虑到300吨吊车吊装时的实际工况,吊车吊装过程中,吊装空心板梁、配重与吊车两个支脚成一条直线时为吊车最不利受力状态(如下图所示),故进行支腿承载力计算时,根据1-1吊车受力平面图进行计算,根据图示可知,空心板梁重吊车自重G1=69t,力臂L1=,吊重(空心梁+钢丝绳)G2=、力臂L2=,吊车配重G3=100t、力臂L3=,根据受力状态图可列方程为:
G1×+G3×=G2××
将数据代入以上公式,可得:R1=604KN
混凝土支点自重:2m*3m*2m*25KN/m=300KN,则支点处受力和为:604+300=904KN,故支点处应力为:904/(2*3)=151Kpa,根据设计资料,在站台面以下2m处地质为硬质粘土,σ0=250Kpa>151Kpa,故满足地基承载力要求。
2)汽车吊选用:
根据提供汽车吊工况参数表以及梁体、吊车自重可查表选择,取双机抬吊折减系数;吊装示意图如下所示:
吊装空心板梁时:选用两台75t汽车吊,工作半径7m,臂长18m时对应起吊能力为:32t;故一台吊车吊装能力:32*=>(+)/2=,满足吊装要求。
吊装300t汽车吊时:选用一台100t、一台200t汽车吊,其中100t汽车吊工作半径6m,臂长时对应起吊能力为:47t;200t汽车吊工作半径
12m,臂长对应起吊能力为:,故100t吊车吊装能力:47*=>,满足吊装要求。
300吨吊车计算公式表

300吨吊车计算公式表
摘要:
1.300 吨吊车的概述
2.300 吨吊车计算公式表的内容
3.300 吨吊车计算公式表的应用
4.结论
正文:
【300 吨吊车的概述】
300 吨吊车是一种大型的吊装设备,它的主要作用是在各种工程中进行吊装作业,例如桥梁建设、大型设备安装等。
300 吨吊车的吊装能力极强,可以满足各种大型工程的需求。
【300 吨吊车计算公式表的内容】
300 吨吊车计算公式表主要包括以下内容:
1.吊车荷载计算公式:用于计算吊车在吊装物品时所能承受的最大荷载。
2.吊车稳定性计算公式:用于计算吊车在吊装物品时的稳定性,以确保吊车不会因为不稳定而发生倾翻。
3.吊车起重力矩计算公式:用于计算吊车在吊装物品时的起重力矩,以确保吊车能够顺利完成吊装作业。
【300 吨吊车计算公式表的应用】
300 吨吊车计算公式表在实际工程中应用广泛,它可以帮助工程师在进行吊装作业前,对吊车的性能进行精确的计算和评估,从而保证吊装作业的安全
性和顺利性。
汽车吊机支腿反力计算及梁板受力分析
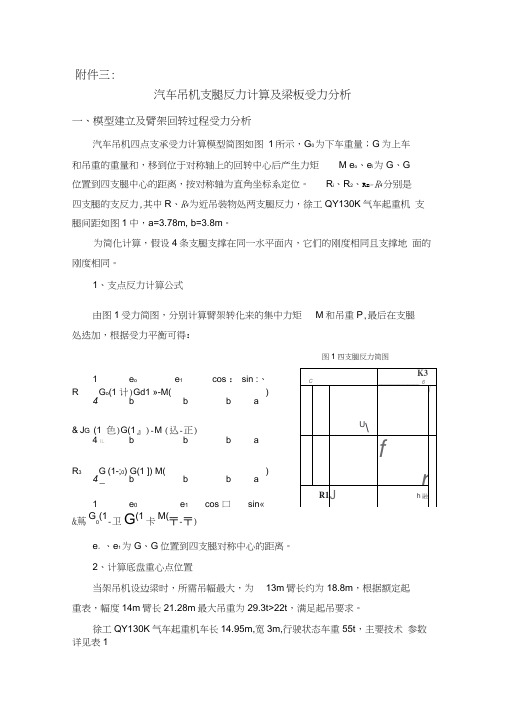
汽车吊机支腿反力计算及梁板受力分析一、模型建立及臂架回转过程受力分析汽车吊机四点支承受力计算模型简图如图 1所示,G 0为下车重量;G 为上车 和吊重的重量和,移到位于对称轴上的回转中心后产生力矩 M e o 、e i 为G 、G 位置到四支腿中心的距离,按对称轴为直角坐标系定位。
R i 、R 2、R B > R 4分别是四支腿的支反力,其中R 、R 4为近吊装物处两支腿反力,徐工QY130K 气车起重机 支腿间距如图1中,a=3.78m, b=3.8m 。
为简化计算,假设4条支腿支撑在同一水平面内,它们的刚度相同且支撑地 面的刚度相同。
1、支点反力计算公式由图1受力简图,分别计算臂架转化来的集中力矩 M 和吊重P ,最后在支腿 处迭加,根据受力平衡可得:1 e o e 1 cos : sin :、RG o (1 计)Gd1 »-M( )4 b bb a& J G °(1 色)G(1』)-M (込-正)4 IL b b b a R 3G °(1-;0) G(1 ]) M( )4 _ b b b a1e 0e 1cos 口sin «&蔦G 0(1-卫G (1卡M(〒-〒)e 。
、e 1为G 、G 位置到四支腿对称中心的距离。
2、计算底盘重心点位置当架吊机设边梁时,所需吊幅最大,为 13m 臂长约为18.8m ,根据额定起 重表,幅度14m 臂长21.28m 最大吊重为29.3t>22t ,满足起吊要求。
徐工QY130K 气车起重机车长14.95m,宽3m,行驶状态车重55t ,主要技术 参数详见表1附件三:图1四支腿反力简图表1 徐工QY130K 气车起重机主要参数类另U 项目单位参数尺寸参数整机全长mm 14950整机全宽mm 3000 整机全高mm 3950轴距第一、二mm 1420第二、三mm 2420第三、四mm 1875第四、五mm 1350第五、六mm 1400重量参数行驶状态整机自重kg 55000 一/二轴kg 9100/9100重量^参数乂三/四轴kg 9100/12500五/六轴kg 12700/9700 支腿距离纵向m 7.56横向m 7.6 转台尾部回转半径(平衡重)mm 4600吊机支腿纵向距离7.56m,横向距离7.6m,支腿箱体位于2桥和3桥之间以及车架后端,工作时配重38000kg。
吨汽车吊支腿受力计算书

吨汽车吊支腿受力计算书 Last updated on the afternoon of January 3, 2021
300吨汽车吊支腿下地基承载力计算
考虑到300吨吊车吊装时的实际工况,吊车吊装过程中,吊装空心板梁、配重与吊车两个支脚成一条直线时为吊车最不利受力状态(如下图所示),故进行支腿承载力计算时,根据1-1吊车受力平面图进行计算,根据图示可知,空心板梁重吊车自重G1=69t,力臂L1=,吊重(空心梁+钢丝绳)G2=、力臂L2=,吊车配重G3=100t、力臂L3=,根据受力状态图可列方程为:
G1×+G3×=G2××
将数据代入以上公式,可得:R1=604KN
混凝土支点自重:2m*3m*2m*25KN/m=300KN,则支点处受力和为:604+300=904KN,故支点处应力为:904/(2*3)=151Kpa,根据设计资料,在站台面以下2m处地质为硬质粘土,σ0=250Kpa>151Kpa,故满足地基承载力要求。
2)汽车吊选用:
根据提供汽车吊工况参数表以及梁体、吊车自重可查表选择,取双机抬吊折减系数;吊装示意图如下所示:
吊装空心板梁时:选用两台75t汽车吊,工作半径7m,臂长18m时对应起吊能力为:32t;故一台吊车吊装能力:32*=>(+)/2=,满足吊装要求。
吊装300t汽车吊时:选用一台100t、一台200t汽车吊,其中100t汽车吊工作半径6m,臂长时对应起吊能力为:47t;200t汽车吊工作半径
12m,臂长对应起吊能力为:,故100t吊车吊装能力:47*=>,满足吊装要求。
300t汽车吊支腿受力计算书

300吨汽车吊支腿下地基承载力计算
考虑到300吨吊车吊装时的实际工况,吊车吊装过程中,吊装管廊、配重与吊车两个支脚成一条直线时为吊车最不利受力状态(如下图所示),故进行支腿承载力计算时,根据1-1吊车受力平面图进行计算,根据图示可知,吊车自重G1=79.65t,力臂L1=1.367m,吊重(管廊+钢丝绳)G2=40t、力臂L2=20m,吊车配重G3=98.2t、力臂L3=4.181m,根据受力状态图可列方程为:
G1×1.367+G3×4.181=G2×18.549-R1×5.946
将数据代入以上公式,可得:R1=604KN
混凝土支点自重:2m*3m*2m*25KN/m=300KN,则支点处受力和为:604+300=904KN,故支点处应力为:904/(2*3)=151Kpa,根据设计资料,在站台面以下2m处地质为硬质粘土,σ0=250Kpa>151Kpa,故满足地基承载力要求。
2)汽车吊选用:
根据提供汽车吊工况参数表以及梁体、吊车自重可查表选择,取双机抬吊折减系数0.8;吊装示意图如下所示:
吊装空心板梁时:选用两台75t汽车吊,工作半径7m,臂长18m时对应起吊能力为:32t;故一台吊车吊装能力:32*0.8=25.6t>(46.8+0.38)/2=23.59t,满足吊装要求。
吊装300t汽车吊时:选用一台100t、一台200t汽车吊,其中100t汽车吊工作半径6m,臂长12.2m时对应起吊能力为:47t;200t汽车吊工作半径12m,臂长17.6m对应起吊能力为:49.5t,故100t吊车吊装能力:47*0.8=37.6t>34.69t,满足吊装要求。
汽车吊受力计算
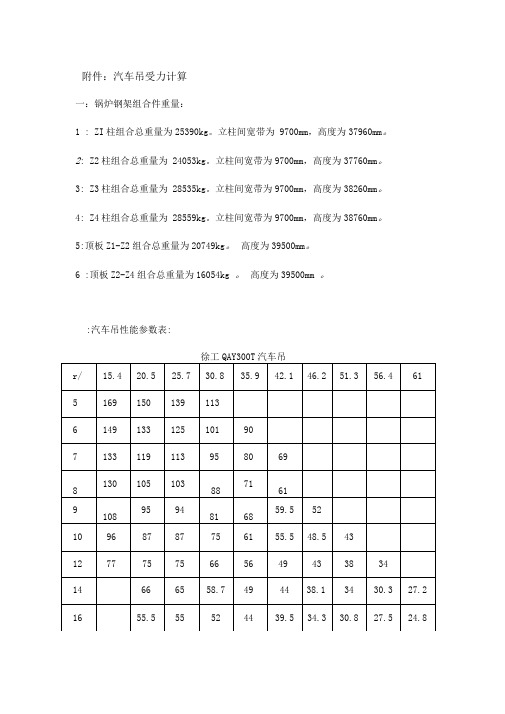
附件:汽车吊受力计算一:锅炉钢架组合件重量:1 : ZI柱组合总重量为25390kg。
立柱间宽带为 9700mm,高度为37960mm。
2: Z2柱组合总重量为 24053kg。
立柱间宽带为9700mm,高度为37760mm。
3: Z3柱组合总重量为 28535kg。
立柱间宽带为9700mm,高度为38260mm。
4: Z4柱组合总重量为 28559kg。
立柱间宽带为9700mm,高度为38760mm。
5:顶板Z1-Z2组合总重量为20749kg。
高度为39500mm。
6 :顶板Z2-Z4组合总重量为16054kg 。
高度为39500mm 。
:汽车吊性能参数表:徐工QAY300T汽车吊三:根据实际情况我公司研究决定在锅炉钢架吊装、安装过程中,使用一台300T 的汽车吊,一台100T的汽车吊来进行吊装工作,以300T汽车吊为主吊,以100T 汽车吊为副吊。
1:在Z1柱组合件的吊装时,汽车吊停在1#炉、2#炉中间,在吊装过程中汽车吊主臂高度为42米,最大吊装半径为16米。
查表得知吊车主臂最大受力为39.5T, 安全系数为0.8,39.5 X).8 = 31.6T,大于Z1柱组合重量25.39T。
2:在Z2柱组合件的吊装时,汽车吊停在1#炉、2#炉中间,在吊装过程中汽车吊主臂高度为42米,最大吊装半径为16米。
查表得知吊车主臂最大受力为39.5T, 安全系数为0.8,39.5 X).8 = 31.6T,大于Z2柱组合重量24.053T。
3:在Z3柱组合件的吊装时,汽车吊停在1#炉、2#炉中间,在吊装过程中汽车吊主臂高度为42米,最大吊装半径为16米。
查表得知吊车主臂最大受力为39.5T, 安全系数为0.8,39.5 X).8 = 31.6T,大于Z3柱组合重量28.535T。
4:在顶板梁Z1-Z2组合的吊装时,汽车吊停在1#炉、2#炉中间,在吊装过程中汽车吊主臂高度为48米,吊装半径为10米。
查表得知主臂最大受力为43T,安全系数为0.8,43 X).8 = 34.4T,大于大于顶板梁Z1-Z2组合重量20.749T。
300吨吊车参数

420/1800
发动机额定扭矩
N.m/(r/min)
2700/1080
行驶参数
最高行驶速度
km/h
75
最小转弯直径
m
24
最小离地间隙
mm
接近角
°
19
离去角
°
19
最大爬坡能力
%
40
百公里油耗
L
主要性能参数
最大额定总起重量
t
300
最小额定幅度
mm
转台尾部回转半径
m
最大起重力矩
kN.m
9526
300吨吊车参数
尺寸参数
Unit
QAY300
整体全长
mm
18210
整机全宽
mm
整机全高
mm
4000
重量参数
行驶状态整机质量
kg
79680
前轴轴荷(一、二、三轴)
kg11Βιβλιοθήκη 25后轴轴荷(四、五、六、七)
kg
11201
动力参数
发动机型号
TAD722VE
OM502LA.III/5
发动机额定功率
kW/(r/min)
基本臂
m
最长主臂
m
最长主臂+副臂
m
支腿纵向距离
m
8.7
支腿横向距离
m
9.2
工作速度参数
起重臂变幅时间
s
起重臂全伸时间
s
最大回转速度
r/min
主起升机构最大速度(单绳)(空载)
m/min
副起升机构最大速度(单绳)(空载)
m/min
汽车吊机支腿反力计算及梁板受力分析
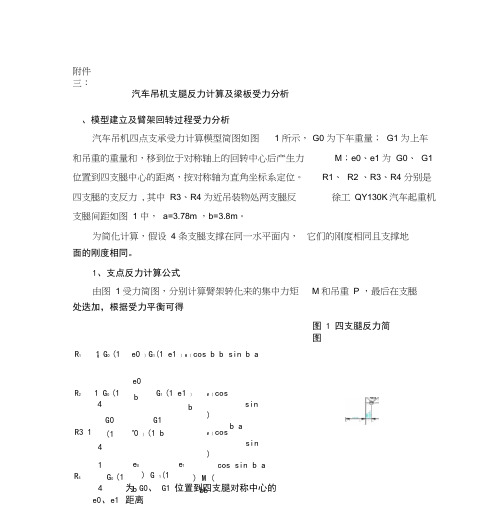
汽车吊机支腿反力计算及梁板受力分析、模型建立及臂架回转过程受力分析面的刚度相同。
1、支点反力计算公式处迭加,根据受力平衡可得附件三:R 11 4 G0 (1 e0 ) G 1(1 e1 ) M ( cos b b sin b a 图 1 四支腿反力简图R 21 G 0 (1 4 e0)bG 1 (1 e1 )bM (cossin)b aR3 1G0(14 G1e0 ) (1 bM (cossin)b a1 R 44G 0 (1e 0) G 1(1 b e 1) M ( bbcos sin 为 G0、 G1 位置到四支腿对称中心的汽车吊机四点支承受力计算模型简图如图1 所示, G0 为下车重量; G1 为上车和吊重的重量和,移到位于对称轴上的回转中心后产生力矩M ;e0、e1 为 G0、 G1 位置到四支腿中心的距离,按对称轴为直角坐标系定位。
R1、 R2 、R3、R4 分别是四支腿的支反力 , 其中 R3、R4 为近吊装物处两支腿反力,徐工 QY130K 汽车起重机支腿间距如图 1 中, a=3.78m ,b=3.8m 。
为简化计算,假设 4 条支腿支撑在同一水平面内, 它们的刚度相同且支撑地 由图 1 受力简图,分别计算臂架转化来的集中力矩 M 和吊重 P ,最后在支腿2、计算底盘重心点位置当架吊机设边梁时,所需吊幅最大,为13m,臂长约为18.8m ,根据额定起重表,幅度14m、臂长21.28m 最大吊重为29.3t>22t ,满足起吊要求。
徐工QY130K汽车起重机车长14.95m ,宽3m,行驶状态车重55t ,主要技术参数详见表 1 。
mmm2 重转台)尾部回转半径(平衡徐工 QY130K 汽车起重机主要参 表 1 数7.56m ,横向距离 7.6m ,支腿箱体位于 吊机支腿纵向距离4600桥和 3 桥之间及车架后端,工作时配重 38000kg 。
根据车轴及转盘中心位置计算吊装下车重心图 2 车轴及转盘中心位置尺寸由轴重参数得:下车重量 G0 =9100+9100+9100+12500+12700+9700=62200 kg 上车配重重量 =38000 kg 上车未加配重时重心到车后边缘距离 Rc 为:9700 3 12700 4.4 12500 5.75 9100 7.62 9100 10.04 9100 11.46 Rc622006.78m则下车重心 G0 到臂架回转中心 G1 的纵向距离为 6.78-4.9=1.88m工作臂架回转中心 G1 到两后支腿的纵向距离为 3.63m ,上车配重及吊重支点G1 到支腿对称轴中心 O 点距离 e1=0.15m ,下车重心 G0 到支腿对称中心 O 的距 离 e0=1.88-0.15=1.73m 。
汽车吊支腿负荷计算

汽车吊支腿负荷计算汽车吊支腿是一种用于汽车起重机、搅拌车和其他重型车辆的装置,用于增加车辆的稳定性和承载能力。
在使用汽车吊支腿时,需要进行负荷计算,以确保吊支腿可以承受所需的重量。
本文将介绍汽车吊支腿负荷计算的基本原理和方法。
1.静态稳定计算静态稳定计算的关键是计算吊支腿的最大承载能力,并确保其能够承受所需的重量。
静态稳定计算一般需要考虑以下几个参数:-吊支腿的长度和背离车体的角度:吊支腿的长度和与车体背离的角度将直接影响吊支腿的承载能力。
一般来说,吊支腿长度越长,背离角度越小,承载能力越大。
-车辆的重量和重心位置:计算吊支腿的承载能力时,需要考虑车辆的总重量和重心位置。
重心位置越高,对吊支腿的负荷也越大。
-地面的稳定性:地面的稳定性也会对吊支腿的负荷产生影响。
如果地面不稳定,吊支腿需要承受更大的负荷。
基于以上参数,可以使用以下公式计算吊支腿的最大承载能力:P = W / sinθ + H * R / (L * sinθ) + M * R / (L * sinθ)其中,P为吊支腿的最大承载能力,W为车辆的总重量,θ为吊支腿与水平面的夹角,H为吊支腿与车体背离的水平距离,R为吊支腿与地面的水平距离,L为吊支腿的长度,M为地面的摩擦系数。
2.动态稳定计算动态稳定计算主要考虑吊支腿在车辆行驶或吊装货物时的稳定性。
动态稳定计算需要考虑以下几个因素:-车辆的动态载荷:车辆行驶或吊装货物时,会产生动态载荷,对吊支腿的负荷产生影响。
动态载荷由车辆的行驶速度、行驶路况和吊装货物的重量等因素决定。
-吊支腿的承载能力:吊支腿需要根据动态载荷计算其承载能力。
一般来说,动态稳定计算中的吊支腿承载能力要比静态稳定计算中的要大。
动态稳定计算的具体方法可以参考相关的国家标准和规范,根据实际情况进行计算。
综上所述,汽车吊支腿的负荷计算需要考虑静态稳定和动态稳定两个方面。
在计算时,需要知道车辆的总重量、重心、吊支腿的长度和背离角度、地面的稳定性等参数,并使用相应的公式进行计算。
汽车吊受力计算
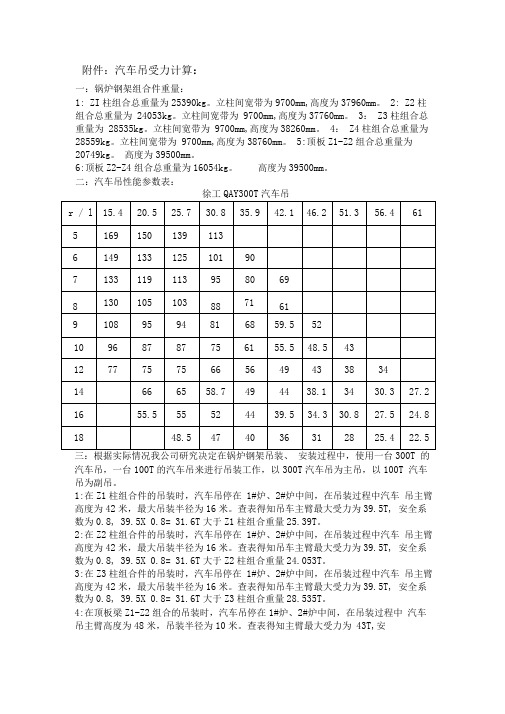
71
61
9
108
95
94
81
68
59.5
52
10
96
87
87
75
61
55.5
48.5
43
12
77
75
75
66
56
49
43
38
34
14
66
65
58.7
49
44
38.1
34
30.3
27.2165来自.5555244
39.5
34.3
30.8
27.5
24.8
18
48.5
47
40
36
31
28
25.4
22.5
三:根据实际情况我公司研究决定在锅炉钢架吊装、 安装过程中,使用一台300T的汽车吊,一台100T的汽车吊来进行吊装工作,以300T汽车吊为主吊,以100T汽车吊为副吊。
1:在Z1柱组合件的吊装时,汽车吊停在1#炉、2#炉中间,在吊装过程中汽车 吊主臂高度为42米,最大吊装半径为16米。查表得知吊车主臂最大受力为39.5T,安全系数为0.8,39.5X 0.8=31.6T大于Z1柱组合重量25.39T。
4:在顶板梁Z1-Z2组合的吊装时,汽车吊停在1#炉、2#炉中间,在吊装过程中 汽车吊主臂高度为48米,吊装半径为10米。查表得知主臂最大受力为43T,安
全系数为0.8,43X0.8=34.4T,大于大于顶板梁Z1-Z2组合重量20.749T。
3:在Z4柱组合件的吊装时,汽车吊停在炉后,在吊装过程中汽车吊主臂高度 为42米,吊装半径为16米。查表得知主臂最大受力为39.5T,安全系数为0.8, 39.5X 0.8=31.6T大于Z4柱组合重量28.559T。
汽车吊机支腿反力计算及梁板受力分析
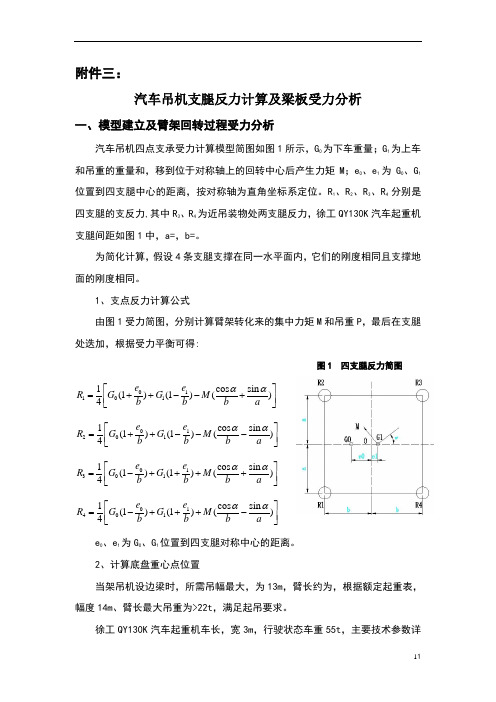
v1.0 可编辑可修改附件三:汽车吊机支腿反力计算及梁板受力分析一、模型建立及臂架回转过程受力分析汽车吊机四点支承受力计算模型简图如图1所示,G 0为下车重量;G 1为上车和吊重的重量和,移到位于对称轴上的回转中心后产生力矩M ;e 0、e 1为G 0、G 1位置到四支腿中心的距离,按对称轴为直角坐标系定位。
R 1、R 2、R 3、R 4分别是四支腿的支反力,其中R 3、R 4为近吊装物处两支腿反力,徐工QY130K 汽车起重机支腿间距如图1中,a=,b=。
为简化计算,假设4条支腿支撑在同一水平面内,它们的刚度相同且支撑地面的刚度相同。
1、支点反力计算公式由图1受力简图,分别计算臂架转化来的集中力矩M 和吊重P ,最后在支腿处迭加,根据受力平衡可得:图1 四支腿反力简图011011cos sin (1)(1)()4e e R G G M b b b a αα⎡⎤=++--+⎢⎥⎣⎦ 012011cos sin (1)(1)()4e e R G G M b b b a αα⎡⎤=++---⎢⎥⎣⎦ 013011cos sin (1)(1)()4e e R G G M b b b a αα⎡⎤=-++++⎢⎥⎣⎦ 014011cos sin (1)(1)()4e e R G G M b b b a αα⎡⎤=-+++-⎢⎥⎣⎦e 0、e 1为G 0、G 1位置到四支腿对称中心的距离。
2、计算底盘重心点位置当架吊机设边梁时,所需吊幅最大,为13m ,臂长约为,根据额定起重表,幅度14m 、臂长最大吊重为>22t ,满足起吊要求。
徐工QY130K 汽车起重机车长,宽3m ,行驶状态车重55t ,主要技术参数详见表1。
表1 徐工QY130K汽车起重机主要参数吊机支腿纵向距离,横向距离,支腿箱体位于2桥和3桥之间以及车架后端,工作时配重38000kg。
根据车轴及转盘中心位置计算吊装下车重心点G,尺寸位置关系详见图2,由合力矩确定的平行力系中心即为吊车重心。
- 1、下载文档前请自行甄别文档内容的完整性,平台不提供额外的编辑、内容补充、找答案等附加服务。
- 2、"仅部分预览"的文档,不可在线预览部分如存在完整性等问题,可反馈申请退款(可完整预览的文档不适用该条件!)。
- 3、如文档侵犯您的权益,请联系客服反馈,我们会尽快为您处理(人工客服工作时间:9:00-18:30)。
300吨汽车吊支腿受力
计算书
-CAL-FENGHAI.-(YICAI)-Company One1
300吨汽车吊支腿下地基承载力计算
考虑到300吨吊车吊装时的实际工况,吊车吊装过程中,吊装空心板梁、配重与吊车两个支脚成一条直线时为吊车最不利受力状态(如下图所示),故进行支腿承载力计算时,根据1-1吊车受力平面图进行计算,根据图示可知,空心板梁重吊车自重G1=69t,力臂L1=,吊重(空心梁+钢丝绳)G2=、力臂L2=,吊车配重G3=100t、力臂L3=,根据受力状态图可列方程为:
G1×+G3×=G2××
将数据代入以上公式,可得:R1=604KN
混凝土支点自重:2m*3m*2m*25KN/m=300KN,则支点处受力和为:604+300=904KN,故支点处应力为:904/(2*3)=151Kpa,根据设计资料,在站台面以下2m处地质为硬质粘土,σ0=250Kpa>151Kpa,故满足地基承载力要求。
2)汽车吊选用:
根据提供汽车吊工况参数表以及梁体、吊车自重可查表选择,取双机抬吊折减系数;吊装示意图如下所示:
吊装空心板梁时:选用两台75t汽车吊,工作半径7m,臂长18m时对应起吊能力为:32t;故一台吊车吊装能力:32*=>(+)/2=,满足吊装要求。
吊装300t汽车吊时:选用一台100t、一台200t汽车吊,其中100t汽车吊工作半径6m,臂长时对应起吊能力为:47t;200t汽车吊工作半径
12m,臂长对应起吊能力为:,故100t吊车吊装能力:47*=>,满足吊装要求。