罩壳注塑模设计
罩壳注塑模具设计

湖南大学衡阳分校毕业设计题目罩壳设计说明书专业班级学号学生姓名指导教师年月日共28 页第 1 页共28 页第1 页湖南大学衡阳分校课程设计共28 页第2 页湖南大学衡阳分校课程设计共28 页第3 页湖南大学衡阳分校课程设计共28 页第4 页湖南大学衡阳分校课程设计共28 页第5 页湖南大学衡阳分校课程设计图2 – 1塑件塑件的工作条件对精度要求较高,根据ABS的性能可选择其塑件的精度等级为4级共28 页第6 页湖南大学衡阳分校课程设计共28 页第7 页湖南大学衡阳分校课程设计共28 页第8 页湖南大学衡阳分校课程设计共28 页第9 页湖南大学衡阳分校课程设计共28 页第10 页湖南大学衡阳分校课程设计共28 页第11 页湖南大学衡阳分校课程设计共28 页第12 页湖南大学衡阳分校课程设计共28 页第13 页共28 页第14 页共28 页第15 页共28 页第16 页湖南大学衡阳分校课程设计1-动模 2-推件板 3-凹模板 4-推料板 5-定模座板共28 页第17 页湖南大学衡阳分校课程设计共28 页第18 页共28 页第19 页共28 页第20 页共28 页第21 页共28 页第22 页共28 页第23 页共28 页第24 页共28 页第25 页共28 页第26 页湖南大学衡阳分校课程设计共28 页第27 页共28 页第28 页共28 页第29 页。
方罩壳注塑模设计

方罩壳注塑模设计贺 斌 田福祥 熊 艳 (青岛建筑工程学院,青岛 266033) (济南三爱富氟化工有限责任公司,济南 250031) 摘要 分析方罩壳塑件的工艺特性,对比两种模具设计方案,论述优选后的模具结构和工作原理。
该模具利用斜导柱抽芯机构及定模推出机构解决了带侧向凸起的塑件的脱模问题,模具结构紧凑,推出可靠,安装操作方便,成型塑件质量好,生产效率高。
关键词 注塑模 定模推出机构 斜导柱 抽芯机构1 塑件特点图1所示为方罩壳塑料容器,材料为ABS [1]。
ABS 具有较高的力学性能,流动性好、易于成型;成型收缩率小,理论计算收缩率为0.5%;溢料值为0.04mm ;比热容较低,在模具中凝固较快,模塑周期短。
塑件尺寸稳定,表面光亮。
图1 方罩壳塑料容器该塑件为50mm ×30mm 的方形件,高30mm 。
底部外侧有外径12mm 、内径7mm 、高10mm 的凸起接水嘴,接水嘴的外侧边缘是横截面为梯形的凸环,高度1mm 。
塑件要求内外表面光滑,无顶出痕迹及明显的浇口痕迹。
2 方案分析根据塑件形状特点可知,塑件在模具内有两种摆放方式,一种底部向上放置,另一种底部向下放置。
对前一种摆放方式,动模部分存在塑件对型芯的包紧力,定模部分存在接水嘴梯形凸环滞留在定模型腔里的阻力,且大于型芯上的包紧力,因此启模时塑件不会留在动模型芯上,若强制其脱离定模,必然会损坏塑件。
所以若采用此种摆放方式应在定模内安装推出机构以解除梯形凸环滞留在定模型腔里的阻力。
对后一种摆放方式,塑件对型芯的包紧力存在于定模部分,接水嘴梯形凸环的阻力存在于动模部分,尽管凸环的阻力大于型芯的包紧力,但强制脱模仍然会使塑件凸环处受到损伤,这就需要在定模上安装推出机构以解除塑件对型芯的包紧力,动模上安装侧向抽芯机构以解除推出时塑件滞留在动模内的阻力。
对比两种方案,综合考虑模具结构和尺寸,采用后一种即底部向下放置的设计方案。
3 模具结构根据塑件在模具内底部向下的摆放方式,模具设计成三板式[2],一模两件,如图2所示。
聚苯乙烯罩注塑模具设计说明书(含全套CAD图纸)

定 ..................................... 72.4 初步选择注射机 ......................................................... 72.4.1 塑件的体积估算 ...................................................... 72.4.2 注射量的确 定 ........................................................ 72.4.3 锁模力的确 定 ........................................................ 82.4.4 注射压力的确 定 ...................................................... 83 模具设计过 程 .................................................93.1 浇注系统的设 计 ........................................................ 93.1.1 主流道的设 计 ........................................................ 93.2 浇口设 计 ............................................................. 103.3 分型面的选择设计原 则 ................................................. 113.4 成型零部件的设 计 ..................................................... 123.4.1 成型零件的结构设 计 ................................................. 123.4.2 成型零件的尺寸计 算 ................................................. 143.4.3 型腔侧壁厚度和底板厚度的确 定 ....................................... 163.4.3.1 型腔侧壁厚度的计 算 ............................................... 163.4.3.2 型腔底板厚度的计 算 ............................................... 173.5 侧抽机构设 计 ......................................................... 183.5.1 抽芯距的确定与抽拔力的计 算 ......................................... 183.5.2 斜导柱分型抽芯机构的设 计 ........................................... 183.6 模架的选择 ........................................................... 193.7 导向机构的设计 ....................................................... 203.7.1 导柱的设 计 ......................................................... 203.7.2 导套的设 计 ......................................................... 203.8 脱模机构的设 计 ....................................................... 213.8.1 推出机构的设 计 ..................................................... 213.8.2 脱模力的计 算 ....................................................... 213.9 模具温度调节系统设 计 .................................................. 223.9.1 热量的计 算 ......................................................... 223.9.2 冷却水量的计 算 ..................................................... 223.9.3 冷却水管直径的计 算 .....................10 模具加热系统的设 计 .................................................. 233.11 模具排气槽的设 计 .................................................... 234 模具材料的选 择 ..............................................245 模具的校核计 算 ..............................................245.1 注射机参数校 核 ....................................................... 245.1.1 模具安装尺寸的校 核 ................................................. 24总结..........................................................25谢 辞........................................................26参考文献......................................................27附 录........................................................28 桂林电子科技大学毕业设计(论文)报告用纸 第1页 共 29 页 1 选题背景 1.1 选题的目的及意义 随着塑料材料研究的不断深 入和塑料应用的日趋广泛,在现代工业和日用产品中所用到的越来越多地采用塑料
毕业设计(论文)剃须刀壳罩注塑模具设计(全套图纸三维)

本科毕业论文(设计)题目剃须刀壳罩注塑模设计作者机械工程学院学院专业料成型与控制工程学号指导教师二〇一五年三月二十一日摘要塑料成型制品是以塑料为主要结构材料经成型加工获得的制品,又叫做塑料制件,简称塑件。
塑料成型制品应用广泛,特别是在电子仪表、电器设备、通信工具等方面获得大量应用。
如各种受力不大的壳体、支架、结构件、装饰件等;作为塑料制品的主要生产基础工艺装备的塑料模具,在国民经济占有重要的地位,模具技术也已成为衡量一个国家产品制造水平的重要标志。
注射成型是塑料成型的一种重要方法,它主要适用于热塑性的成型可以一次成型形状复杂的精密塑件,本次设计就是将剃须刀壳罩作为设计模型,将注塑模具的相关知识作为依据,阐述塑料注塑模具的整体设计过程。
本文设计的内容就是剃须刀壳罩注塑模具,材料为PP,根据其结构形状特点以及通过对剃须刀壳罩成型工艺的正确分析,确定型腔的总体布局,选择分型面,确定脱模方式,设计浇注系统等;同时本文对注塑模具进行简要介绍,对注塑模具中的主要零件进行设计计算,在设计过程中着重考虑其生产实际中的经济性和合理性。
关键词:注塑模具;注射成型;分型面全套图纸,加153893706PPtractPlastic molding products are plastic as the main structural material. The pr ocessing of products.Referred to as the plastic parts.plastic molding products are widely used.Especially in the electronic instrument electrical equipment ,commu nication tools ,etc to obtain a large number of applications . such as all kinds of stress are shell stents structure decoration.Based process equipment as the ma in production of plastic products of plastic mold .occupies an important position in national economy mould technology has also become to measure a national product manufacture level of important symbol.Injection molding plastic molding is an important method .it is mainly suitable for thermoplastic molding .and ca n be a complicated shape of precision plastic forming parts is the adsl surface shell as a design model .This paper will be injection mold related knowledge a s the basis.the overall design process of plastic injection mould are expounded.Design the content of this article is shell of plastic injection mould ,materi als for PP .According to the shape of the structure characteristics and through t he analysis of the right across the shell molding process,determine the overall d istribution of cavity choose the parting surface determine the demoulding way . The design of gating system,etc.Keywords:Plastic mold;injection molding;the parting surface目录诚信申明 (I)摘要 (II)PPtract (III)第一章绪论 (2)1.1我国模具行业的发展方向和前景 (2)1.2 注塑模具设计与制造技术 (3)1.3 UG模具设计的基本流程 (7)1.4课题意义 (9)第二章注塑件的设计 (9)2.1 功能设计 (9)2.2 材料选择 (9)2.3 结构设计 (10)2.4 塑件的尺寸精度及表面质量 (11)第三章塑件3D建模及注射成型工艺分析 (12)3.1塑件的3D模型 (12)3.2塑件的注射成型工艺性分析 (12)3.3注塑机 (12)第四章模具结构设计 (14)4.1型腔数目的确定 (14)4.2分型面的确定 (14)4.3浇口的确定 (14)4.4模具材料的确定 (14)4.5浇注系统的设计 (15)4.6成型零件结构设计 (17)4.7 抽芯结构设计 (18)4.8模架的选用 (20)4.9导向机构的设计 (20)4.10顶出机构的设计 (21)4.11排气设计 (22)4.12温度调节系统设计 (22)第五章注射机的校核 (24)5.1最大注塑量的校核 (24)5.2锁模力的校核 (24)5.3模具外形尺寸校核 (24)5.4模具厚度校核 (24)5.5模具安装尺寸校核 (25)5.6开模行程校核 (25)第六章模具总装设计 (26)6.1模具装配及加工要求 (26)6.2模具工作原理 (28)结论................................................. 错误!未定义书签。
PA66罩壳注塑模具设计说明书
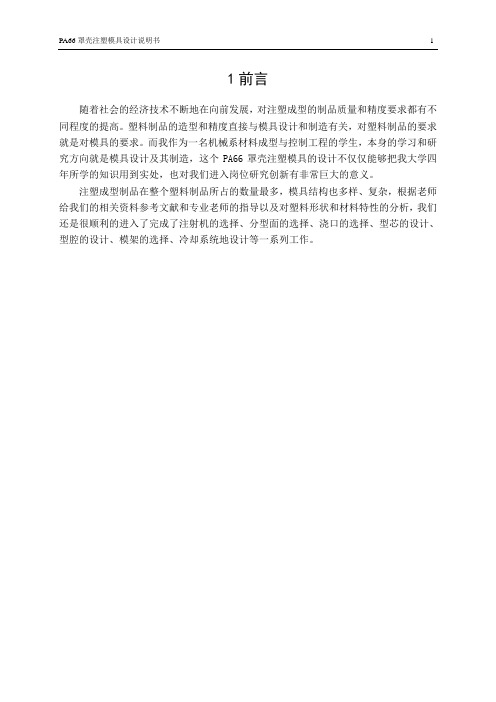
1前言随着社会的经济技术不断地在向前发展,对注塑成型的制品质量和精度要求都有不同程度的提高。
塑料制品的造型和精度直接与模具设计和制造有关,对塑料制品的要求就是对模具的要求。
而我作为一名机械系材料成型与控制工程的学生,本身的学习和研究方向就是模具设计及其制造,这个PA66罩壳注塑模具的设计不仅仅能够把我大学四年所学的知识用到实处,也对我们进入岗位研究创新有非常巨大的意义。
注塑成型制品在整个塑料制品所占的数量最多,模具结构也多样、复杂,根据老师给我们的相关资料参考文献和专业老师的指导以及对塑料形状和材料特性的分析,我们还是很顺利的进入了完成了注射机的选择、分型面的选择、浇口的选择、型芯的设计、型腔的设计、模架的选择、冷却系统地设计等一系列工作。
2塑件材料及工艺分析图2.1所示为塑料罩壳,材料为PA66,PA66坚韧、耐磨、耐油、耐水、抗霉菌,但吸水大,适用于一般机械零件、减摩耐磨零件、传动零件以及化工、电器、仪表等的外壳零件。
图2-1 塑料罩壳2.1 PA66成型特性分析PA66聚酰胺,在聚酰胺材料中有较高的熔点。
它是一种半晶体-晶体材料。
PA66在较高温度也能保持较强的强度和刚度。
PA66具有优秀的韧性,耐磨性,自润滑性,耐油性,耐化学性、气体透过性,耐水性和抗酶菌。
为了提高PA66的机械特征,常常加入各种各样的改性剂。
这个性质可以用来加工很薄的元件。
它的粘度对温度变化很敏感。
其成型特性如下:(1)PA66在成型后仍旧具有吸湿性,其程度重要取决于材料的组成、壁厚以及环境条件。
在产品设计时,一定要考虑吸湿性对几何稳定性的影响。
(2)为了提高PA66的机械特征,常常加入各种各样的改性剂。
玻璃就是最常见的添加剂,有时为了提高抗冲击性还加入合成橡胶,如epdm和sbr等。
(3)PA66的粘性较低,因此流动性很好(但不如PA6)。
这个性质可以用来加工很薄的元件。
它的粘度对温度变化很敏感。
(4)PA66的收缩率在1%~2%之间,加入玻璃纤维添加剂可以将收缩率降低到0.2%~1%。
圆罩壳注塑模具课程设计
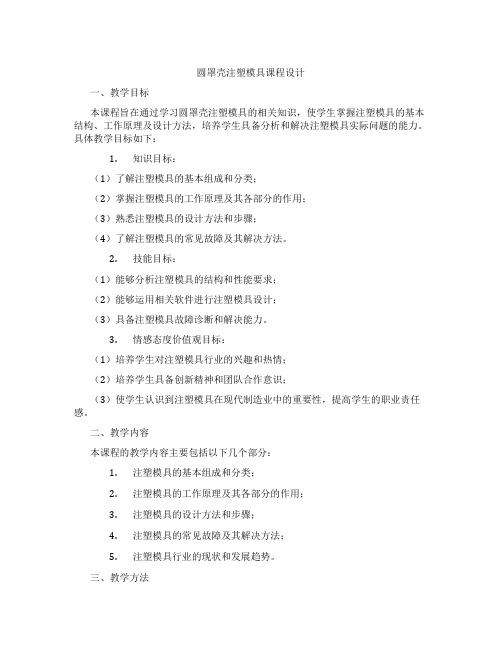
圆罩壳注塑模具课程设计一、教学目标本课程旨在通过学习圆罩壳注塑模具的相关知识,使学生掌握注塑模具的基本结构、工作原理及设计方法,培养学生具备分析和解决注塑模具实际问题的能力。
具体教学目标如下:1.知识目标:(1)了解注塑模具的基本组成和分类;(2)掌握注塑模具的工作原理及其各部分的作用;(3)熟悉注塑模具的设计方法和步骤;(4)了解注塑模具的常见故障及其解决方法。
2.技能目标:(1)能够分析注塑模具的结构和性能要求;(2)能够运用相关软件进行注塑模具设计;(3)具备注塑模具故障诊断和解决能力。
3.情感态度价值观目标:(1)培养学生对注塑模具行业的兴趣和热情;(2)培养学生具备创新精神和团队合作意识;(3)使学生认识到注塑模具在现代制造业中的重要性,提高学生的职业责任感。
二、教学内容本课程的教学内容主要包括以下几个部分:1.注塑模具的基本组成和分类;2.注塑模具的工作原理及其各部分的作用;3.注塑模具的设计方法和步骤;4.注塑模具的常见故障及其解决方法;5.注塑模具行业的现状和发展趋势。
三、教学方法为了提高教学效果,本课程将采用多种教学方法,包括:1.讲授法:通过讲解注塑模具的基本概念、原理和设计方法,使学生掌握相关知识;2.案例分析法:分析实际案例,使学生了解注塑模具在实际生产中的应用和解决实际问题的能力;3.实验法:学生进行注塑模具的实验操作,培养学生的动手能力和实际操作技能;4.讨论法:学生进行分组讨论,促进学生间的交流与合作,提高学生的思维能力和创新能力。
四、教学资源为了支持本课程的教学,我们将准备以下教学资源:1.教材:选用权威、实用的注塑模具教材,为学生提供系统的理论知识;2.参考书:提供相关的注塑模具设计手册、论文等参考资料,丰富学生的知识体系;3.多媒体资料:制作精美的课件、动画等多媒体资料,提高学生的学习兴趣;4.实验设备:准备注塑模具实验设备,为学生提供实践操作的机会。
五、教学评估本课程的教学评估将采用多元化评价方式,全面、客观地评价学生的学习成果。
外壳注塑模具设计

目录1工艺性能分析和结构方案的确定和所需设备的校核............................ 工艺性能分析和模具方案的确定..............................................工艺性能分析 ................................................确定模具结构方案 ............................................ 注射机型号的选定及校核....................................................注射量的计算 ................................................锁模力的计算 ................................................选择注射机.................................................. 2浇注系统的设计和排溢系统的设计.......................................... 主流道的设计..............................................................主流道的设计 ................................................浇口的设计..................................................分流道的设计 ................................................冷料穴的设计 ................................................排溢系统的设计 ..............................................3 成型零部件的设计........................................................ 凹模型腔的设计............................................................凹模直径....................................................凹模深度圆柱部分 ............................................凸模型芯的设计............................................................凸模径向尺寸 ................................................ 成型塑件侧面型芯的设计.................................................... 4侧抽和内抽机构的设计及校核.............................................. 浇注系统凝料的脱出........................................................ 推出方式的确定............................................................ 侧抽零件的设计............................................................抽芯距S的计算 ......................................斜销有效长度L的计算 ........................................斜销的直径d .................................................斜销长度的计算 ..............................................5 模架的设计.............................................................. 模架的设计和对其的校核....................................................模架的选择..................................................定模座板的设计 ..............................................侧抽芯滑块的设计 ............................................型芯固定板的设计 ............................................垫板的设计..................................................垫块的设计和校核 ............................................动模座板的设计 .............................................. 6推出机构和复位机构的设计................................................推出机构和复位机构的设计..................................................脱模力的计算 ................................................拉杆直径的确定 ..............................................推件机构导向的设计 ..........................................复位机构的设计 .............................................. 7冷却系统的设计和校核.................................................... 冷却水道的设计............................................................冷却水道的选择 ..............................................冷却水的体积流量 ............................................冷却管道直径的确定 ..........................................冷却水在管道中的流速 ........................................冷却管道孔壁与冷却水之间的传热模系数.........................冷却管道的总传热面积 ........................................模具上应开设的冷却水孔数..................................... 参考文献...............................................................1工艺性能分析和结构方案的确定和所需设备的校核工艺性能分析和模具方案的确定1.1.1工艺性能分析图零件图1形状:如图所示,该制件为塑料外壳,外形尺寸直径为Φ108mm,壁厚为3mm,高为16mm,形状为圆形壳体;2性能:所设计塑件材料为尼龙1010,聚酰胺类塑料在分子结构中含有亲水的聚酰基,是一种吸湿性材料,,化学稳定性较好,机械强度较好;吸水性较小,平均吸水率为%—%;为了顺利的成型,事先必须进行干燥,促使水分降至%以下,干燥是最好用真空干燥;表干燥参数真空度烘箱温度料层厚度干燥时间水分含量1333Pa 90—25mm以下8—12h %—%110℃1.1.2确定模具结构方案1 成型方式的确定由于聚酰胺为结晶性塑料,流动性好,成型收缩率较大,所以采用注射成型;(2)确定分型面考虑到外壳的形状、大小和PA的流动性,采用矩形侧浇口,其优点是截面形状简单、易于加工、便于试模后修正,并采用单分型面,瓣合内抽结构;图分型面示意图(3)确定型腔数目估算塑件的质量:取ρ=cm3, 那么mn =ρg78.111272.1045.1=⨯=νv:由三维造型软件确定塑件体积为112723mm 考虑到塑件的尺寸较小,在此采用一模两腔; 注射机型号的选定及校核1.2.1注射量的计算通过计算可知,塑件质量mn =,流道凝料的质量m2=,上述确定为一模两腔,所以注射量m=21+×mn=3×=;1.2.2锁模力的计算流道凝料包括浇口在分型面上的投影面积A2,根据分析,A2是塑件在分型面上的投影面积A1的倍—倍,因此可用;A=A1+A2=A1+0.35 A1=××π=3689mm2所以F=P腔A=30×3689=型腔压力P取30MPa1.2.3选择注射机根据每一周期的注射量和锁模力的计算值,可选用选用XS-ZY-125卧式注射机,因为螺杆在注射机中既可旋转又可前后移动,能够胜任塑料的塑化、混合和注射工作,这一点远胜于柱塞式注射机,在动力熔融作用下,强烈的搅拌与剪切作用不仅有利于熔体混合均匀,而且避免了波动的机筒温度对熔体温度的影响,因此能得到良好的塑化效果;表注射机的主要技术规格:理论注射量g/cm3125 锁模力KN 900螺杆直径mm 42 模板行程mm 300 注射压力Mpa 119 最大模具厚度mm300定位孔径mm 100 最小模具厚度mm200(1)注射有关参数的校核1)注射量的校核M=n mn +mj≤ mg2×1+×=<×250=200注射量符合要求2)注射压力的校核取PA的注射压力为P=90Mpa为保证足够的注射压力,取系数K=Pe≥K P0= =117MPa 而p e =130MPa 注射压力校核合格;3锁模力的校核取压力损耗系数K=,注射机的实际注射压力F=900×=630KN,所需的锁模力F= ,锁模力校核合格,其他安装时的校核要待模架选定,结构尺寸确定以后才可进行;2浇注系统的设计和排溢系统的设计主流道的设计2.1.1主流道的设计1 主流道通常设计成圆锥形,其锥角α=2°~4°,取为3°;内壁表面粗糙度一般为Ra=μm;(2)为防止主流到与喷嘴处溢料,主流道对接处制成半球形凹坑,其半径 R2=R1+1~2=13㎜,其小端直径d2=d1+~1=5 ㎜;凹坑深取h=4 ㎜;图浇口套示意图(3)为减小料流转向过渡时的阻力,主流道大端呈圆角过渡,其圆角半径取r=2 ㎜; (4)在保证塑料良好成型的前提下,主流道L应尽量短,否则将增多流道凝料,且增加压力损失,使塑料降温过多而影响注射成型;一般L≤60㎜,可初定L=50 mm; (5)由于主流道与塑料熔体及喷嘴反复接触和碰撞,因此常将主流道制成可拆卸的主流道衬套,便于用优质钢材加工和热处理;2.1.2浇口的设计1由于考虑到塑件的外观尺寸和塑件的形状,则选用矩形侧浇口如图图模型图(6)尺寸的确定根据经验公式:h=nt查表取n= h=nt=×=mm取h=mm浇口宽度式中A——为塑件外表面面积,mm浇口长度取L=mm2.1.3分流道的设计参考塑料成型加工与模具,知圆形和正方形流道效率最高,分型面为平面时常采用梯形浇口,因此本设计采用梯形截面流道;①分流道长度,取L=10mm②分流道尺寸,查参考文献6,取D=4mm③分流道表面的粗糙度分流道表面不要求太光洁,表面粗糙度通取Ra=μm④分流道与浇口的连接形式采用圆弧连接2.1.4冷料穴的设计由于取凝料不需要侧向移动,为实现自动化操作,将凝料与塑件一起推出动模,故采用钩形头冷料穴如图图冷料穴2.1.5排溢系统的设计成型型腔体积比较小,气体会沿着分型面和斜滑块与固定板之间的间隙向外排出;3侧抽和内抽机构的设计及校核浇注系统凝料的脱出按安装方式,型腔数目和结构特征以及所选用的矩形侧浇口确定注射模具选用瓣合单分型面;主流道设在定模一侧,分流道设在分型面上;开模后由于动模上拉料杆的拉料作用以及塑件因收缩包紧在型芯上,制品连同流道内的凝料一起留在动模一侧,动模上设置推出机构,用以推出制件和流道内的凝料;推出方式的确定由于制件需要内抽机构来完成最终的脱模及推出;所以,塑件成型后,穴内冷料与拉料杆的钩头搭接在一起,拉料杆固定在推杆固定板上;开模时,拉料杆通过钩头拉住穴内冷料,使主流道凝料脱出定模,然后随推出机构运动,同时顶杆推动内抽斜滑块,完成内抽,使凝料与塑件一起推出动模;这种机构便于实现自动化可提高生产效率;侧抽零件的设计抽芯距S 的计算22)2/()2/(d D S -= +2~3=22255.26-+2~3,取11mm斜销有效长度L 的计算斜销的倾角α=20°斜销的直径D采用瓣合结构,侧抽芯力的计算:制件为圆环×2形断面时,所需脱模力式中:1K ——无量纲系数,其值随λ与φ而异,λ=r/δ, 1K 从表中选取为 2K ——无量纲系数,其值随f 与φ而异,2K 从表中选取为E ——塑料的弹性模量,从附录中选取为1800MPaS ——塑料的平均成型收缩率,从相关材料中选取为%L ——制件对型芯的包容长度为0.5mmf ——制件与型芯之间的摩擦因数查为ϕ——模具型芯的脱模斜度为r ——型芯的平均长度为μ——塑料的泊松比查表的为0A ——盲孔制品型芯在垂直与脱模方向上的投影面积 计算得,之间所需的脱模力N F 449=最大弯曲力W F ,查表得KN F W 1=由KN F W 1=,︒=20α,mm H W 4.30=,查表的斜销的直径d=12mm 斜销长度的计算斜导柱长度可按下列公式计算式中 L ——斜导柱总长度;D ——斜导柱固定部分大端直径;S ——抽拔距;h ——斜导柱固定板厚度;d ——斜导柱直径;α——斜导柱倾斜角;)105(20sin 1120tan 122120cos 4520tan 1721~+︒+︒⨯+︒+︒⨯⨯=L ,取mm L 95= 4 模架的设计模架的设计和对其的校核模架的选择由于该制件的结构复杂,需要侧抽及内抽,没有标准的模架可以选用,就需要参考标准并通过计算来确定;定模座板的设计定模座板同时也是型腔板1.型腔板侧壁的厚度组合式: [][]⎪⎪⎭⎫ ⎝⎛--=12P r S σσ 式中 []σ——型腔材料的许用应力,MPa,一般中碳钢[]σ=180 MPa;2.圆形型腔底部厚度组合式:[]σ222.1pr t =式中 p —— 塑料熔体对型腔的压力,MPa;根据塑件大小、型腔数、脱模方式,取定模座板的尺寸B ×L ×H=315×250×45mm 侧抽芯滑块的设计侧抽芯滑块用来成型制件的侧表面,其厚度与与侧抽芯距有关,尺寸为如零件图所示;型芯固定板的设计该板用来固定型芯,取厚度为32mm垫板的设计参考标准模架,取垫板的尺寸为:250×250×40mm垫块的设计和校核C 为垫块尺寸,C=推出行程+推杆固定板厚度+5~10=12++16+5~10=~所以垫块厚度C 取80mm,宽度取50mm动模座板的设计取动模座板的尺寸的315×315×35mm从设计模架可知,模架外形尺寸:宽×长×高=315×315×模具高,200﹤﹤300故,合格;模具开模所需行程S=H 1+H 2+5~10mm式中 H 1——塑料脱模需要的顶出距离;H 2——塑件的厚度;S=58++5~10mm=~﹤300mm 注射机开模行程其他参数在前面校核均合格,所以本模具所选注射机完全合格,满足使用要求;6 推出机构和复位机构的设计推出机构和复位机构的设计6.1.1 脱模力的计算制件为圆环×7形断面时,所需脱模力为式中:1K ——无量纲系数,其值随λ与φ而异,λ=r/δ, 1K 从表中选取为 2K ——无量纲系数,其值随f 与φ而异,2K 从表中选取为E ——塑料的弹性模量,从附录中选取为1800MPaS ——塑料的平均成型收缩率,从相关材料中选取为%L ——制件对型芯的包容长度为7mmf ——制件与型芯之间的摩擦因数查为ϕ——模具型芯的脱模斜度为r ——型芯的平均长度为μ——塑料的泊松比查表的为0A ——盲孔制品型芯在垂直与脱模方向上的投影面积计算得,之间所需的脱模力N F 1010=6.1.2 拉杆直径的确定根据压杆稳定公式,推杆的直径式中 K ——安全系数,查表得K =L ——拉杆的长度,取L =F ——脱模力,上述求得N F 1010=n ——拉杆数目,n 为1根E ——钢材的弹性模量为210000MPa计算得mm d 6.4=,取mm 6对于拉杆直径进行强度校核所以拉杆直径校核合格6.1.3 推件机构导向的设计侧抽芯依靠斜导柱进行导向,由于该制件的结构特殊,不需要其它的导向结构;6.1.4 复位机构的设计其作用是使完成推出任务的推出零部件回复到初始位置,模具图中采用弹簧复位,将弹簧套在一定拉杆上,由于塑件质量轻、结构特殊、复位力要求小,并且结构简单、价格低廉,故可只采用弹簧复位;7 冷却系统的设计和校核冷却水道的设计7.1.1 冷却水道的选择塑料模具的温度直接影响到塑件的成型质量和生产效率,要得到优质产品,模具必须进行温控;但对于尼龙来说,模具温度在40~80℃,可利用熔融塑料传给模具的余热来解决;在模具上不需设置加热装置,但必须设置冷却装置,缩短成型冷却时间,提高生产效率;由于塑件的投影面积较大,故选用直流冷却回路;7.1.2 冷却水的体积流量式中 v q ——冷却介质的体积流量,mm m /3;W ——单位时间每min 内注入模具内的塑料质量kg /min按每分钟注射两次:4.90221.45=⨯;1Q ——单位质量的塑件在凝固时所放出的热量,查表得:kg kJ /6500;ρ——冷却水的密度3/100m kg ;1c ——冷却水的比热容:C kg kJ ︒⋅/187.4;1θ——冷却水的出口温度C ︒23;2θ——冷却水的入口温度C ︒20;7.1.3冷却管道直径的确定为了使冷却水处于湍流状态,有考虑到塑件尺寸以及推出系统的结构查表得:d=8mm,冷却水道所选位置如图图冷却管道7.1.4冷却水在管道中的流速所以冷却水为湍流状态,管道直径合格;7.1.5冷却管道孔壁与冷却水之间的传热模系数7.1.6冷却管道的总传热面积7.1.7模具上应开设的冷却水孔数为使模具冷却均匀,取冷却水孔数为2;参考文献1 邹继强主编. 塑料模具设计参考资料汇编. 北京:清华大学出版社,20012 刘昌祺主编. 塑料模具设计. 北京:机械工业出版社,20033 潘淑清主编.几何精度规范学 . 北京:北京理工大学出版社,19984 贾润礼,程志远主编. 实用注射模设计手册. 北京:中国轻工业出版社,20015 唐志玉等编.塑料模具师指南.北京:国防工业出版社,20056 黄虹主编.塑料成型加工与模具.北京:化学工业出版社,2003。
罩盖注射模具的设计

罩盖注射模具的设计一、塑件的工艺型分析1.塑件的的成型工艺型分析塑件如图1所示:名称:罩盖材料:ABS数量:大批量生产1.1塑件材料特性ABS塑料(丙烯腈-丁二烯-苯乙烯共聚物)是在聚苯乙烯分子中导入了丙烯腈、丁二烯等异种单体厚成为的改性共聚物,也可以成为改性聚苯乙烯,具有聚苯乙烯更好的使用性能和工艺性能。
ABS塑料是一种常用的具有良好的综合力学性能的工程塑料。
它具有良好的机械强度,提别是抗冲击强度;具有一定的耐磨性、耐水性、耐寒性、耐油性、化学稳定性等性能。
一般为无定型料,不透明,无毒,无味,成型塑件的表面有较好的光泽。
其缺点是耐热性不高,并且耐气候性较差,在紫外线的作用下易变硬发脆。
1.2塑件材料成型性能使用ABS注射成型塑件是,由于熔体粘度高,所需要的注射成型压力高,因此塑件对型芯的包紧力较大,故塑件鹰采用较大的脱模斜度;另外熔体粘度高,使ABS塑件易产生熔接痕,所以模具设计时应注意尽量减少浇注系统对流料的阻力。
ABS易吸水,成型加工前应进行干燥处理。
在正常成型条件下,ABS塑件的尺寸稳定性较好。
1.3塑件结构、尺寸精度和表面质量分析塑件结构分析:塑件外形简单,壁厚均匀,且符合最小壁厚要求;无需侧向分型与抽新机构,使模具结构设计简单,可以采用整体式型腔和型芯。
根据塑件的设计壁厚均匀的原则,塑件未注圆角设计为:外圆角R=1.5x t=1.5x 2=3mm;内圆角r =0.5x 2=1mm;塑件未注明脱模斜度,因塑件较高,模具设计时需将脱模斜度的设计考虑在内,型芯是以小端为基准,向扩大的方向去,型腔是以大端为基准向缩小的方向取。
开模脱出塑件时,希望塑件留在有脱模装置的动模一侧,要求塑件留在型芯上,该塑件内表面的脱模斜度应小于外表面的脱模斜度。
塑件尺寸精度分析:该塑件尺寸精度没有特殊要求,未注公差的尺寸为自由尺寸,可以按MT5查取,查《塑料注射模结构与设计》一书中表4-10知,该塑件主要尺寸公差标注为:外形尺寸:65,50,15,Ф20;内形尺寸:61,16074.0−064.0−038.0−044.0−5.00+2.00+表面质量分析:该塑件要求外形美观,表面无斑点、气泡、和熔接痕。
塑料模课程设计-壳罩塑件注塑模设计

塑料成型工艺及模具设计课程设计说明书壳罩塑件注塑模设计学生姓名:专业:材料成型及控制工程班级:1203班学号:指导教师:职称教授完成时间:2015年12月湖南工学院塑料课程设计课题任务书学院:机械工程学院专业:材料成型及控制工程专业摘要本课程设计为一壳罩塑件,如图1所示。
塑件结构比较简单,塑件质量要求是不允许有裂纹、变形缺陷,塑件壁厚均匀,脱模斜度30′~1°,材料可自选(选择pp材料),塑件公差按模具设计要求进行转换。
图1 壳罩塑件尺寸目录1.塑件材料及工艺分析 (4)1.1塑件材料………………………………………………………………………1.2 PP材料的工艺分析……………………………………………………………………… 1.3 注射工艺参数………………………………………………………………………2.拟定模具的结构形式和初选注射机 (5)2.1 分型面位置的确定………………………………………………………2.2 型腔数量和排位方式的确定………………………………………………………2.3 注射机型号的确定………………………………………………………3.浇注系统的设计 (9)3.1 主流道的设计………………………………………………………3.2 分流道的设计………………………………………………………3.3 浇口的设计………………………………………………………3.4 校核主流道的剪切速率………………………………………………………3.5 冷料穴的设计及计算………………………………………………………4.成型零件的机构设计及计算 (13)4.1 成型零件的结构设计………………………………………………………4.2 成型零件刚才的选用…………………………………………………………………4.3 成型零件工作尺寸的计算……………………………………………………………4.4 成型零件尺寸及动模垫板厚度的计算......................................................5.脱模推出机构的设计 (17)5.1 脱模力的计算………………………………………………………………………5.2 推出方式的确定.................................................................................6.模架的确定 (19)6.1各模板尺寸的确定………………………………………………………………………6.2模架各尺寸的校核………………………………………………………………………7.冷却系统的设计 (20)7.1 冷却介质………………………………………………………………………7.2 冷却系统的简单计算……………………………………………………………………8.排气槽的设计 (23)9.导向与定位结构的设计 (23)10.参考文献 (23)1.塑件材料及工艺分析1.1 塑件材料该塑件为塑料罩壳,壁厚为2.5mm,塑件外型尺寸不大,选用PP塑料,塑件精度要求为MT3级。
透明塑料罩壳注射模设计
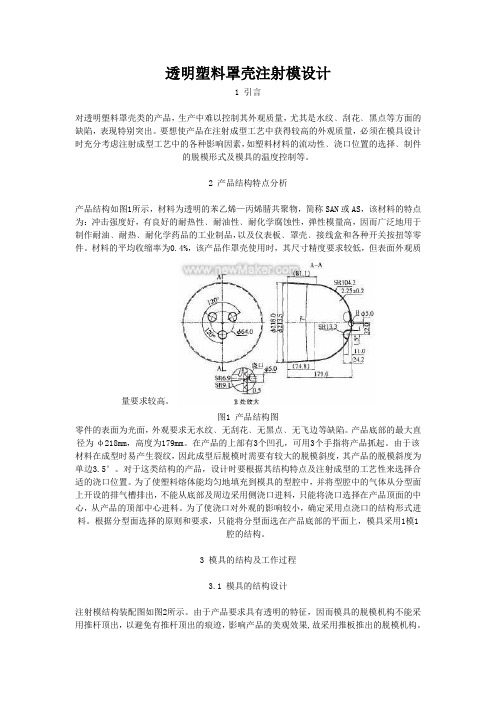
透明塑料罩壳注射模设计1 引言对透明塑料罩壳类的产品,生产中难以控制其外观质量,尤其是水纹﹑刮花﹑黑点等方面的缺陷,表现特别突出。
要想使产品在注射成型工艺中获得较高的外观质量,必须在模具设计时充分考虑注射成型工艺中的各种影响因素,如塑料材料的流动性﹑浇口位置的选择﹑制件的脱模形式及模具的温度控制等。
2 产品结构特点分析产品结构如图1所示,材料为透明的苯乙烯—丙烯腈共聚物,简称SAN或AS,该材料的特点为:冲击强度好,有良好的耐热性﹑耐油性﹑耐化学腐蚀性,弹性模量高,因而广泛地用于制作耐油﹑耐热﹑耐化学药品的工业制品,以及仪表板﹑罩壳﹑接线盒和各种开关按扭等零件。
材料的平均收缩率为0.4%,该产品作罩壳使用时,其尺寸精度要求较低,但表面外观质量要求较高。
图1 产品结构图零件的表面为光面,外观要求无水纹﹑无刮花﹑无黑点﹑无飞边等缺陷。
产品底部的最大直径为φ218mm,高度为179mm。
在产品的上部有3个凹孔,可用3个手指将产品抓起。
由于该材料在成型时易产生裂纹,因此成型后脱模时需要有较大的脱模斜度,其产品的脱模斜度为单边3.5°。
对于这类结构的产品,设计时要根据其结构特点及注射成型的工艺性来选择合适的浇口位置。
为了使塑料熔体能均匀地填充到模具的型腔中,并将型腔中的气体从分型面上开设的排气槽排出,不能从底部及周边采用侧浇口进料,只能将浇口选择在产品顶面的中心,从产品的顶部中心进料。
为了使浇口对外观的影响较小,确定采用点浇口的结构形式进料。
根据分型面选择的原则和要求,只能将分型面选在产品底部的平面上,模具采用1模1腔的结构。
3 模具的结构及工作过程3.1 模具的结构设计注射模结构装配图如图2所示。
由于产品要求具有透明的特征,因而模具的脱模机构不能采用推杆顶出,以避免有推杆顶出的痕迹,影响产品的美观效果,故采用推板推出的脱模机构。
顶板用内六角螺钉固定在复位杆上,并在复位杆上于动模板和推杆固定板之间增设压缩弹簧,以便开模后推板脱模机构能自动复位。
方罩壳注塑模设计
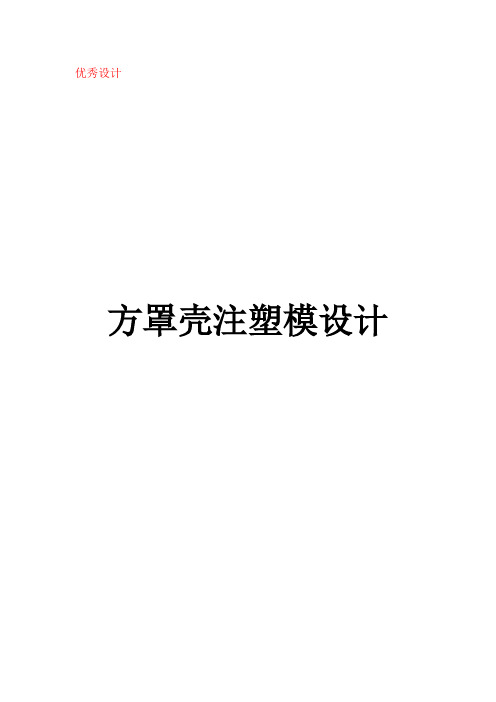
优秀设计方罩壳注塑模设计毕业设计课题申报表专业 20** 级目录一、塑件制品分析 (4)二、注塑机的选用 (11)三、模具设计的有关计算 (13)四、模具结构设计: (18)五、总体尺寸的确定,选购模架: (23)六、注塑机的参数校核: (23)七、模具的装配与检验: (25)八、参考文献: (27)附:工艺规程说明书 (28)附:毕业实习报告 (46)一、塑件制品分析1、用途:聚丙烯可用做各种机械零件,如:法兰、接头、泵叶轮、汽车零件和自行车零件;可作为水、蒸汽、各种酸碱等的输送管道,化工容器和其他设备的衬里、表面涂层;可制造盖和本体和一的箱壳,各种绝缘零件,并用与医药工业中。
2、品种:改制品的塑料品种为热塑性塑料中的PP(聚丙烯),聚丙烯无毒,无味,无色。
外观与聚乙烯较为相似,但更透明、更轻,其密度为:0.90~0.91g/cm3.它不吸水,光泽好且易着色,具有优良的介电性能,耐水性,化学稳定性,易于成型加工。
其屈服强度、抗拉强度、抗压强度、硬度及弹性均比一般塑料优良。
聚丙烯注射成形一体铰链有特别高的抗弯曲疲劳强度。
聚丙烯的熔点为:164℃~170℃,耐热性好,可在100℃以上温度下消毒灭菌,但在-35℃时会发生脆裂,且在氧、热、光的作用下极易解聚、老化,所以必须加入防化剂。
3、塑件形状:该制件形状为旋转体,上端有M10的螺纹,形状较为简单:(如图)制品材料:PP4、尺寸精度:由于改制件未标注公差,查(《塑料模具设计与制造》P39表1-11、1-12)取MT5,B类公差。
5、①表面粗糙度:该制品可按照成型方法不同可查表(《塑料模具设计与制造》P42表1-13取值),但一般取值为1.2~0.2um,本书参考0.2um 一值。
②塑件表面质量,热塑性塑料产生的常见性表观质量缺陷及产生原因如下表:6、生产批量:由于该制件几何形状较小故设计成一模多腔,则为大批量生产。
7、成型工艺分析:①收缩性:速件从模具中取出后冷料到温室,其尺寸体积全发生变化,这种性能称为收缩性。
矩形上壳罩注射模具的设计

毕业设计设计题目:矩形上壳罩注射模具的设计班级:姓名:指导教师:一、设计任务书1、塑料制品名称:矩形上壳罩2、塑料原料:ABS3、生产批量:10万件4、塑件图:如图1-1a所示为上壳罩的二维图样,如图1-1b为上壳罩的三维图样。
图1-1a上壳罩的二维图样图1-1b上壳罩的三维图样二、塑件的结构工艺性分析:1.塑件的成型特性:ABS是聚苯乙烯的改性产品,是不透明非结晶型聚合物,无毒、无味,密度为1.02-1.05g/cm2。
ABS具有突出的力学性能,坚固、坚韧、坚硬;具有一定的化学稳定性和良好的介电性能;具有较好的尺寸稳定性,易于成型和机械加工,成型塑件表面有较好的光泽,经过调色可配成任何颜色,表面可镀铬。
其缺点是耐热性差,连续工作温度为70℃左右,热变形温度为93℃左右,但热变形比聚苯乙烯、聚氯乙烯、尼龙等都高;耐候性差,在紫外线作用下易变硬发脆。
ABS可采用注射、挤出、可延、吹塑、真空成型、电镀、焊接及表面涂饰等多种成型加工方法。
ABS成型性能如下:(1)易吸水,成型加工前应进行干燥处理,表面光泽要求高的塑件应长时间预热干燥。
(2)流动性中等,溢边值为0.04mm左右。
(3)壁厚和熔料温度对收缩率影响极小,塑件尺寸精度高。
(4)比热容低,塑化效率高,凝固也快,固成型周期短。
(5)表面粘度对剪切速率的依赖性很强,因此模具设计中大都采用点浇口形式。
(6)顶出力过大或机械加工时塑件表面会留下白色痕迹,脱模斜度易取2°以上。
(7)易产生熔接痕,模具设计时应注意尽量减少浇注系统对料流的阻力。
(8)易采用高料温、高模温、高注射压力成型。
在要求塑件精度高时模具温度可控制在50-60℃;而在强调塑件光泽和耐热性时,模具温度应控制在60-80℃。
2.塑件的结构工艺性分析:(1)塑件的尺寸精度分析:该需标注公差的尺寸有ø18±0.1、2xø12+0.0180、30±0.14,属于一般精度要求,其他尺寸均为未标注公差的自由尺寸,可按MT5查取公差。
塑料外壳注塑模具设计

天津大学(高等教育自学考试)本科生毕业设计(论文)任务书机械工程学院办学点模具设计与制造专业10 班设计(论文)题目盒形带侧向抽芯塑件注射模具设计完成日期自2012年07月01日至2012年08月30日止指导教师李国华办学单位负责人黄东霞批准日期学生崔健接受任务日期前言这是我们第二次走进模具设计的课堂,第二次完成了自己的设计。
我们利用三个星期的时间完成了这次注塑模具设计的全部工·序,并整理成了文档。
第一次是大一时减速箱的设计,那是只能是初步的了解了模具设计,而这次是更深刻的。
三个星期的时间匆匆而过,我们即将告别大学的生活,它成了我大学生活中美好的回忆。
这次完成的成果是我们组所有人的功劳,我们六个人互相配合,分工合作,很快就把设计的大概完成了,在其他组中我们算是领先的。
我们各自都动脑动手,在作业中意识到自己缺乏什么需要什么,对以前的专业知识有了更深一步的理解。
在整个设计当中,也出现了不少问题,我们及时解决,不懂的就到书上找答案,并和指导老师相互探讨、交流、帮助,最终问题得到解决。
知识在不断更新,社会在不断前进,制造业中的模具设计与制造走在社会的前沿。
现作为大学生的我们即将毕业,对很快就要投身工作的我们来说,应熟练自己的专业软件,撑握模具制造与设计的理论知识,更重要的是理论与实践相结合。
本说明书主要介绍了这一模具题目的设计思想过程,从用铅笔作零件图到电脑上用CAD作图,到校核计算,到模具制造工艺等,从各方面叙述了我们所设计的模具制品的整个思想过程。
特别是里面的工艺分析和零件的工艺卡片上,花费了我们很大工夫,当然也是设计中最精细、做的做好的一部分。
里面的内容基本上都是我们自己完成的,利用CAD软件作产品图、模板、导柱、导套、装配图、零件图等。
通过这次的毕业设计,我们将二年所学的知识进行归纳总结,觉得自己的模具专业知识水平有了很大的提高,CAD软件作图有了更近一步的深华。
理论与实践找到了一个结合点。
防护罩注塑模设计课程设计
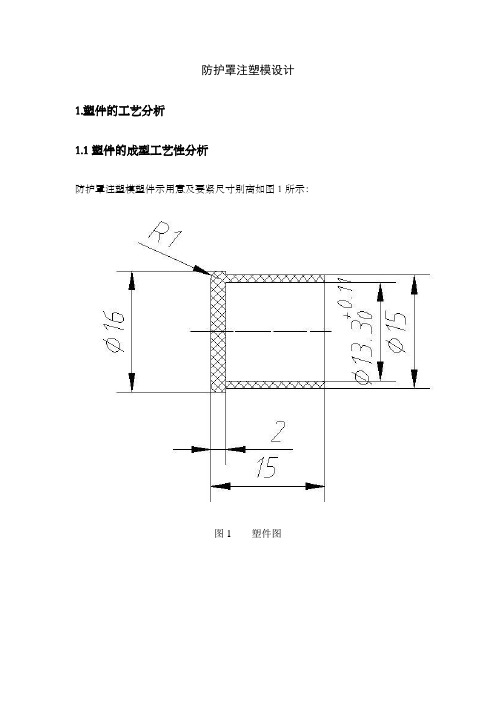
防护罩注塑模设计1.塑件的工艺分析1.1塑件的成型工艺性分析防护罩注塑模塑件示用意及要紧尺寸别离如图1所示:图1 塑件图塑件实体三维图如图2所示:图2名称:防护罩注塑模材料:LDPE(低密度聚乙烯)产品数量:大量量生产塑件尺寸:如图1所示技术要求:去浇口飞边,色泽本色。
1.2塑件材料LDPE的性能聚乙烯无毒、无味,呈乳白色,密度为0.91~0.96g/cm3,有必然的机械强度,但表面硬度差。
其绝缘性能优良,常温下不溶于任何一种已知的溶剂,有高度的耐水性,长期与水接触,其性能可维持不变。
聚乙烯能耐寒,在-60℃时仍有较好的力学性能,在-70℃时仍有必然的柔软性。
聚乙烯成型时流动性较好,在流动方向上与垂直方向上的收缩不同较大,注射方向的收缩率大于垂直方向的收缩率,易产生缩孔;冷却速度慢,必需充分冷却,且冷却速度要均匀;质软易脱模,塑件上有浅的侧凹时可强行脱模。
1.3LDPE塑料的成型工艺参数:低密度聚乙烯的弹性模量E=840~950MPa,泊松比µ=0.38,收缩率1.5~3.5%,注射温度150~170,模具温度30~45℃,注射压力60~100℃,保压力40~50℃,注射时刻0~5S,保压时刻15~60S,冷却时刻15~60S,成型时刻40~140S。
2模具的大体结构设计及设备、模架的选择2.1模具的大体结构2.1.1确信成型方式塑件采纳注射成型法生产。
为保证塑件表面质量,利用点浇口成形,因此模具应为双分型面注射模(三板式注射模)。
2.1.2型腔布置塑件形状较简单,质量较小,生产批量较大。
因此应利用多型腔注射模具。
模具采纳一模二腔、平稳布置。
如此,模具尺寸较小,制造加工方便,生产效率高,塑件本钱较低。
其布置如图3所示:图3 型腔布置2.1.3确信分型面塑件分型面的选择应保证塑件的质量要求,本实例中塑件的分型面有多种选择。
图a的分型面选择在轴线上,会使塑件表面留下分型面痕迹,影响塑件表面质量,同时这种分型面也使侧向抽芯困难;图b的分型面选择在下端面,塑件的外表面可以在整体凹模型腔内成型,塑件大部分外表面光滑,仅在侧向抽芯处留有分型面痕迹。
- 1、下载文档前请自行甄别文档内容的完整性,平台不提供额外的编辑、内容补充、找答案等附加服务。
- 2、"仅部分预览"的文档,不可在线预览部分如存在完整性等问题,可反馈申请退款(可完整预览的文档不适用该条件!)。
- 3、如文档侵犯您的权益,请联系客服反馈,我们会尽快为您处理(人工客服工作时间:9:00-18:30)。
X学院课程设计课程名称:注塑模课程设计题目名称:罩壳注塑模设计专业班级:学号:学生姓名:指导导师:目录设计题目⋯⋯⋯⋯⋯⋯⋯⋯⋯⋯⋯⋯⋯⋯⋯⋯⋯⋯⋯⋯⋯⋯⋯⋯⋯⋯⋯⋯2一: 塑件的工艺性分析⋯⋯⋯⋯⋯⋯⋯⋯⋯⋯⋯⋯⋯⋯⋯⋯⋯⋯⋯⋯⋯⋯⋯31、塑件的原材料分析⋯⋯⋯⋯⋯⋯⋯⋯⋯⋯⋯⋯⋯⋯⋯⋯⋯⋯⋯⋯⋯⋯⋯32、塑件的结构工艺性分析⋯⋯⋯⋯⋯⋯⋯⋯⋯⋯⋯⋯⋯⋯⋯⋯⋯⋯⋯⋯⋯43、塑件的尺寸精度分析⋯⋯⋯⋯⋯⋯⋯⋯⋯⋯⋯⋯⋯⋯⋯⋯⋯⋯⋯⋯⋯⋯44、塑件表面质量分析⋯⋯⋯⋯⋯⋯⋯⋯⋯⋯⋯⋯⋯⋯⋯⋯⋯⋯⋯⋯⋯⋯4 二: 成型设备选择与校核⋯⋯⋯⋯⋯⋯⋯⋯⋯⋯⋯⋯⋯⋯⋯⋯⋯⋯⋯⋯⋯41、注塑机的初选⋯⋯⋯⋯⋯⋯⋯⋯⋯⋯⋯⋯⋯⋯⋯⋯⋯⋯⋯⋯⋯⋯⋯⋯⋯42、注塑机的校核与终选⋯⋯⋯⋯⋯⋯⋯⋯⋯⋯⋯⋯⋯⋯⋯⋯⋯⋯⋯⋯⋯⋯53、塑件模塑成型工艺参数的确定⋯⋯⋯⋯⋯⋯⋯⋯⋯⋯⋯⋯⋯⋯⋯⋯⋯⋯6三: 注射模的结构设计⋯⋯⋯⋯⋯⋯⋯⋯⋯⋯⋯⋯⋯⋯⋯⋯⋯⋯⋯⋯⋯⋯61、分型面的选择⋯⋯⋯⋯⋯⋯⋯⋯⋯⋯⋯⋯⋯⋯⋯⋯⋯⋯⋯⋯⋯⋯⋯⋯⋯72、型腔数目的确定及型腔的排列⋯⋯⋯⋯⋯⋯⋯⋯⋯⋯⋯⋯⋯⋯⋯⋯⋯83、注系统的设计⋯⋯⋯⋯⋯⋯⋯⋯⋯⋯⋯⋯⋯⋯⋯⋯⋯⋯⋯⋯⋯⋯⋯⋯⋯84、型芯、型腔结构的确定⋯⋯⋯⋯⋯⋯⋯⋯⋯⋯⋯⋯⋯⋯⋯⋯⋯⋯⋯⋯⋯9 四: 成型零件尺寸计算⋯⋯⋯⋯⋯⋯⋯⋯⋯⋯⋯⋯⋯⋯⋯⋯⋯⋯⋯⋯⋯⋯10 五: 冷却系统的设计⋯⋯⋯⋯⋯⋯⋯⋯⋯⋯⋯⋯⋯⋯⋯⋯⋯⋯⋯⋯⋯⋯⋯10 1、冷却直径和位置⋯⋯⋯⋯⋯⋯⋯⋯⋯⋯⋯⋯⋯⋯⋯⋯⋯⋯⋯⋯⋯⋯⋯10 2、冷却介质⋯⋯⋯⋯⋯⋯⋯⋯⋯⋯⋯⋯⋯⋯⋯⋯⋯⋯⋯⋯⋯⋯⋯⋯⋯⋯1 1 六、模架的尺寸⋯⋯⋯⋯⋯⋯⋯⋯⋯⋯⋯⋯⋯⋯⋯⋯⋯⋯⋯⋯⋯⋯⋯⋯1 1 七.排气系统的设计⋯⋯⋯⋯⋯⋯⋯⋯⋯⋯⋯⋯⋯⋯⋯⋯⋯⋯⋯⋯⋯⋯⋯1 2 八:导向与定位结构的设计⋯⋯⋯⋯⋯⋯⋯⋯⋯⋯⋯⋯⋯⋯⋯⋯⋯⋯⋯⋯1 2 九:推件方式的选择⋯⋯⋯⋯⋯⋯⋯⋯⋯⋯⋯⋯⋯⋯⋯⋯⋯⋯⋯⋯⋯⋯⋯1 2 十:模具的工作原理及特点⋯⋯⋯⋯⋯⋯⋯⋯⋯⋯⋯⋯⋯⋯⋯⋯⋯⋯⋯⋯131、工作原理⋯⋯⋯⋯⋯⋯⋯⋯⋯⋯⋯⋯⋯⋯⋯⋯⋯⋯⋯⋯⋯⋯⋯⋯⋯⋯142、结构特点⋯⋯⋯⋯⋯⋯⋯⋯⋯⋯⋯⋯⋯⋯⋯⋯⋯⋯⋯⋯⋯⋯⋯⋯⋯⋯14设计小结⋯⋯⋯⋯⋯⋯⋯⋯⋯⋯⋯⋯⋯⋯⋯⋯⋯⋯⋯⋯⋯⋯⋯⋯⋯⋯⋯⋯15 参考文献⋯⋯⋯⋯⋯⋯⋯⋯⋯⋯⋯⋯⋯⋯⋯⋯⋯⋯⋯⋯⋯⋯⋯⋯⋯⋯⋯⋯15.塑件的工艺性分析塑件的工艺性分析包括: 塑件的原材料分析、塑件的尺寸精度分析、塑件表面质量和塑件的工艺性分析, 其具体分析如下:1、塑件的原材料分析塑件材料该塑件为塑料罩壳,壁厚为3mm,塑件外型尺寸不大,选用PP 塑料,塑件精度要求为MT5 级。
性能:密度小,强度、刚性、硬度、耐热性均优于HDPE,可在100℃左右使用。
具有优良的耐腐蚀性,良好的高频绝热性,不受温度影响,但低温变脆,不耐磨,易老化。
成型特性:1) 结晶型塑料,吸湿性小,可能发生熔体破裂,长期与热金属接触易发生分解;2) 流动性极好,溢边值0.03mm 左右;3) 冷却速度快,浇注系统及冷却系统的散热性适度;4) 成型收缩范围大,收缩率大,已发生缩孔,凹痕、变形,取向性强5) 注意控制成型温度,料温低时取向性明显,尤其低温高压时明显,模具温度低于50℃以下塑件无光泽,易产生熔接痕、流痕;90℃以上时已发生翘曲、变形;6) 塑件应壁厚均匀,避免缺口,尖角,以防止应力集中物理、热性能、力学性能、电气性能2、塑件的结构工艺性分析⑴ 从图纸上分析, 该塑件的外形为回转体, 壁厚均匀, 都为3.2mm,且符合最小壁厚要求.⑵ 塑件型腔较大, 有尺寸相等的孔, 它们均符合最小孔径要求.3、塑件的尺寸精度分析塑件的型腔尺寸:3、 塑件表面质量分析:4、 该塑件为工业用罩盖塑料 ,对其表面质量没有什么高的要求 , 粗糙度可取Ra3.2um ,塑件内部也不需要较高的表面粗糙度要求 , 所以内外表面的粗糙 度都 3取 Ra3.2um.二、 成型设备的选择及校核1、注塑机的初选1.1计算塑件的体积 根据制件的三维模型,利用三维软件直接求得塑件的体积为:V = 1032mm 3=10.32cm 3;1.2 计算塑件的质量查手册得密度为: = 0.9g/cm 3 塑件的质量为: M=V × =9.288g1.3 选用注射机根据总体积 V =1.288cm 3,初步选取螺杆式注塑成型机 XS —ZY —60 注塑成型机XS —ZY —60主要参数如下表所示2、注塑机的终选2.1 注射量的校核由公式:0.8W公≥W注W公——注塑机的公称注塑量( cm3);W注——每模的塑料体积量,是所有型腔的塑料加上浇注系统塑料的总和 (cm3);如前所述,塑件及浇注系统的总体积为1032mm3远小于注塑机的理论注250cm3,故满足要求。
2.2 模具闭合高度的校核公式:Hmin﹤H 闭﹤Hmax 如装配图可知模具的闭合高度H 闭=260mm,而注塑成型机的最大模具厚度Hmax=350mm, 最小模具厚度Hmin=250mm,满足Hmin﹤H 闭﹤Hmax 安装要求。
2.3 模具安装部分的校核模具的外形尺寸为300mm×250 mm,故能满足安装要求。
模具定位圈的直径?=注塑机定位孔的直径? 100,满足安装要求。
浇口套的球面半径为SR1=SR+(1-2)=2满0 足要求。
浇口套小端直径R1=R+9(1-2)=4+1=5满足要求。
2.4 模具开模行程的校核公式:H模= H1+ H2≤H注H模——模具的开模行程(mm ) H注——注塑成型机移模行程(mm ) H1——制件的推出距离( mm ) H2——包括流道凝料在内的制品的高度( mm) 代入数据得:H 模=≤H 注=350mm,满足要求。
2.5 锁模力的校核公式:F≥KAPmF ——注射机的额定压力(kN) ;A ——制件和流道在分型面上的投影面积之和(cm) Pm——型腔的平均压力(Mpa) ;这里取15MPa K——安全系数,通常取K=1.1~1.2 ;将数据代入公式得:KAPm=1.1×15X2826*2=93.258KNF=1800KN>93.258KN,满足要求。
2.6 注射压力的校核公式:Pmax ≥K′P0Pmax——注射机的额定注射压力(Mpa) ;P0——注射成形时的所需调用的注射压力(Mpa) ;K′——安全系数将数据代入公式得:K′P0=1.3× 80=104 MPa ≤Pmax=130Mpa 满足要求。
结论:选取螺杆式注塑成型机XS—ZY—250完全符合本模具的使用要求3、塑件模塑成型工艺参数的确定注射成型工艺参数见下表试模时可根据实际情况作适当调整三、注射模的结构设计注射模结构设计主要包括: 分型面的选择、模具型腔数目的确定及型腔的排列、浇注系统设计、型芯、型腔结构的确定、推件方式、侧抽芯机构的设计、模具结构零件设计等内容.1、分型面的选择该塑件为工业用圆盖塑料, 对其表面质量没有什么高的要求,只要求外径没有明显的斑点及熔接痕. 在选择分型面时, 根据分型面的选择原则, 考虑不影响塑件的外观以及成型后能够顺利取出制件,有以下方案:由分型面选择原则,2、型腔数目的确定及型腔的排列由于该塑件采用一模二件成型, 所以, 型腔布置在模具的中间. 这样也有利于浇注系统的排列和模具的平衡.3、浇注系统的设计(1) 主流道设计a、主流道尺寸主流道是指浇注系统中从注射机喷嘴与模具接触处开始到分流道为止的塑料熔体的流动通道,是熔体最先流经模具的部分,它的形状与尺寸对塑料熔体的流动速度和充模时间有较大的影响,因此,必须使熔体的温度降和压力损失最小。
根据手册查得XS-ZY-60 型注射机喷嘴的有关尺寸:喷嘴球半径:R0 =18mm 喷嘴孔直径:d 0 =Ф4mm 定位孔的直径:Ф 100mm 主流道通常设计在浇口套中,为了让主流道凝料能顺利从浇口套中拔出,主流道设计成圆锥形,其锥角为2~6.,内壁表面粗糙度Ra小于0.4um,小端直径d 注射机喷嘴直径大0.5~1mm,小端直径D 一般取3~6mm。
现取锥角a=4。
,小端直径比喷嘴直径大1mm 套一般采用碳素工具钢材料制造,热处理淬火硬度50~55HRC。
由于小端的前面是球面,其深度为3~5mm,这里取3mm,注射机喷嘴的球面在该位置与模具接触并且贴合,因此要求主流道球面半径比喷嘴球面半径大1~2mm。
浇口套与模板间配合采用H7/m6 。
主流道是一端与注射机喷嘴相接触,另一端与分流道相连的一段带有锥度的流动通道。
主流道小端尺寸为5mm。
主流道的长度由定模座板和定模板厚度确定,一般L 不超过60mm。
b、主流道衬套的形式主流道小端入口处与注射机喷嘴反复接触,属易损件,对材料要求较严,因而模具主流道部分常设计成可拆卸更换的主流道衬套形式,以便有效的选用优质钢材单独进行加工和热处理。
常用浇口套分为浇口套、定位圈整体式和浇口套与定位圈单独分开两种(下图为后者),由于注射机的喷嘴球半径为18mm,所以浇口套的为R22mm。
根据模具主流道与喷嘴的关系:R=R0+(1~2)mmD=d0+(0.5 ~1)mm取主流道的球面半径R=20mm 主流道的小端直径d=Ф 5mm 设计如图c、主流道衬套的固定因为采用的为分开式, 所以用定位圈配合固定在模具的面板上。
定位圈的外径为Φ125mm,内径Φ35.5mm。
具体固定形式如下图所示:(2) 分流道的设计分流道的形状及尺寸与塑件的体积、壁厚、形状的复杂程度、注射速率等因素有关.该塑件的体积比较大但形状并不复杂,且壁厚均匀,可以考虑采用多点进料的方式, 缩短分流道的长度, 有利于塑件的成型和外观质量的保证.从便于加工的方面考虑, 采用截面形状为半圆形的分流道. 查有关的手册, 选择R=2mm.由于分流道中与模具接触的外层塑料迅速冷却,只有中心部位的塑料熔体的流动状态较为理想,因面分流道的内表面粗糙度Ra并不要求很低,一般取1.6 μm左右既可,这样表面稍不光滑,有助于塑料熔体的外层冷却皮层固定,从而与中心部位的熔体之间产生一定的速度差,以保证熔体流动时具有适宜的剪切速率和剪切热。
(3) 浇口设计a. 浇口形式的选择由于该塑件外观质量要求不高, 浇口的位置和大小还是要不能太影响塑件的外观同时, 也应该尽量使模具结构简单.根据对塑件结构的分析及已确定的分型面的位置,选择侧浇口主要用于圆筒形制品或中间有孔的制品,它可使进料均匀, 在整个圆周上进料的流速大致相同, 空气容易顺序排出,同时避免了侧浇口的型芯对面的熔接痕, 但是浇口凝料去除困难, 需要切削加工或冲切法去除.b、浇口位置的选择模具设计时,浇口的位置及尺寸要求比较严格,初步试模后还需进一步修改浇口尺寸,无论采用何种浇口,其开设位置对塑件成型性能及质量影响很大,因此合理选择浇口的开设位置是提高质量的重要环节,同时浇口位置的不同还影响模具结构。