压铸生产工艺流程图
锌合金压铸生产工艺

锌合金压铸生产工艺
工艺流程图:原材料熔炼成份化验保温nook模具预热喷脱模剂合模压射检验去飞边检验表面处理成品入库取出铸件铸件顶出开模凝固保压1、生产操作流程:
4.1合金熔炼初始设定温度为435°c―440°c之间,待合金全部熔化后将温度调整为420℃―430℃的保温温度;
4.2合金全部熔融后展开清渣处置,并展开成份化验;4.3合金成分掌控为:元素含量4.31.10.060.020.0030.0030.001al3.8~cu0.7~mg0.035~fe<pb<cr<sn<余量
zn4.4调整压射比压:45~50kg/cm2;压射速度为:2.5m/s;充模时间为0.01s;涡轮时间为:1.5s;加热时间为:6s;4.5预演模具至150℃~200℃;
4.6均喷涂脱模剂和冲头油,原装脱剂与水的配比约为1:200;4.7退出顶出杆,并进行合模动作;
4.8上料后展开压射动作,将合金熔液压入模腔;
4.9铸件冷却后,按顶出铸件,并从模上中取出;
4.10检验铸件有没有热外木、气孔、缺料、腹满、花纹等瑕疵;4.11合格铸件除去管则、渣口、飞边等;4.12铸件表面展开甩砂处置,展开检验入库。
5、生产注意事项:
5.1保证合金铸锭存放于清洁、干燥的区域;5.2新料与回炉料的配比不超过50%;
5.3严格按照安全操作规程进行操作;5.4合格品与不合格品要标示清楚,严格区分;5.5生产操作过程中戴好劳保防护用品,保证安全生产;5.6生产结束作好机台设备的防护和清理工作。
压铸工艺流程图示资料

一、压铸(BODY)工艺流程图示1,压铸机调试2,压铸模安装4,模具预热、涂料7,合型(合模)10浇注压射11,保压12,开模、抽芯取件14,清理(整修)17,终检验3,压铸模设计与制造5,涂料配制6,模具清理8,合金熔炼保温9,嵌件准备13,表面质量检查15,时效处理16,铸件浸渗、喷丸处理二、压射压力P3 P4压力P2P1 P2P1T1 t2 t3 t4 保压时间升压充填增压注:t1 金属液在压室中未承受压力的时间;P1为一级(慢速)t2 金属液于压室中在压射冲头的作用下,通过内浇口充填型腔的时间;P2为二级(快速)t3 充填刚刚结束时的舜间;P3为三级(增压)t4 最终静压力;P4为补充压实铸件4P yP b=Лd2式中:P b 比压(Mpa); Py 机器的压射力(N);(压射力=压射缸直径×蓄压器压射时间最小压力)d 压室(冲头)直径(MM)选择比压考虑的的主要因素上海旭东压铸技术咨询培训资料压铸工艺参数比压因素选择条件高低壁厚薄壁厚壁压铸件结构形状复杂简单工艺性差些好些结晶温度范围大小压铸合金特性流动性差好密度大小比强度大小阻力大小浇注系统散热速度快慢公布合理不太合理排溢系统截面积大小内浇口速度快慢温度合金与压铸模具温度大小压铸各种合金常用比压表(Mpa)铸件壁厚≤3(mm) 铸件壁厚>3(mm)合金结构简单结构复杂结构简单结构复杂锌合金20-30 30-40 40-50 50-60 铝硅、铝铜合金25-35 35-45 45-60 60-70铝、镁合金30-40 40-50 50-65 65-75 镁合金30-40 40-50 50-65 65-80铜合金40-50 50-60 60-70 70-80 压力损失折算系数K直浇道导入口截面F1,K值与内浇铸口截面F2之比>1 =1 <1立式冷室压铸机0.66-0.70 0.72-0.74 0.76-0.78卧式冷室压铸机0.88压射速度浇注金属液量占压室容积百分数(%) 压射速度(cm/s)≤30 30-4030-60 20-30>60 10-20高压速度计算公式:VVh= ×[1+(n-1)×0.1]1/4Лd2T式中:Vh 高速压射速度(CM/S);V 型腔容积(CM3);N 型腔数;D 冲头直径(CM);T 适当的充填时间。
精密铸造过程工艺流程图

精密铸造过程工艺流程图本文由灵寿县洞里矿产加工厂整理制作, 转载请注明出处, 公司网址 公司专业生产铸造用石英砂、石英粉、铝矾土, 质优价廉, 真诚期待与您的合作具设计-----磨具制造----压蜡-----修蜡-----组树-------制壳(沾浆)-----脱蜡----型壳焙烧------化性分析---浇注----清理-----热处理-------机加工-----成品入库。
如过在详细点就是:压蜡(射蜡制蜡模)---修蜡----蜡检----组树(腊模组树)---制壳(先沾浆、淋沙、再沾浆、最后模壳风干)---脱蜡(蒸汽脱蜡)-------模壳焙烧--化性分析--浇注(在模壳内浇注钢水)----震动脱壳---铸件与浇棒切割分离----磨浇口---初检(毛胚检)---抛丸清理-----机加工-----抛光---成品检---入库铸造生产流程大体就是这样总的来说可以分为压蜡、制壳、浇注、后处理、检验压蜡包括(压蜡、修蜡、组树)压蜡---利用压蜡机进行制作腊模修蜡---对腊模进行修正组树---将腊模进行组树制壳包括(挂沙、挂浆、风干)后处理包括(修正、抛丸、喷砂、酸洗、)浇注包括(焙烧、化性分析也叫打光谱、浇注、震壳、切浇口、磨浇口)后处理包括(喷砂、抛丸、修正、酸洗)检验包括(蜡检、初检、中检、成品检)现代熔模精密铸造方法在工业生产中得到实际应用是在二十世纪四十年代。
当时航空喷气发动机的发展, 要求制造象叶片、叶轮、喷嘴等形状复杂, 尺寸精确以及表面光洁的耐热合金零件。
由于耐热合金材料难于机械加工, 零件形状复杂, 以致不能或难于用其它方法制造, 因此, 需要寻找一种新的精密的成型工艺, 于是借鉴古代流传下来的失蜡精密铸造, 经过对材料和工艺的改进, 现代精密铸造方法在古代工艺的基础上获得重要的发展。
所以, 航空工业的发展推动了精密铸造的应用, 而精密铸造的不断改进和完善, 也为航空工业进一步提高性能创造了有利的条件。
生产工艺流程图
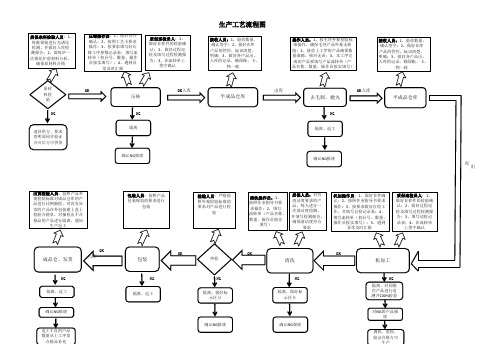
机加操作员:1、做好首件确 认;2、按照作业指导书要求 操作;3、按要求做好自检工 作,并填写自检记录表;4、 填写流转单(机台号、数量、 操作员按实填写);5、遇到 异常及时汇报
质保巡检员人:1、 做好首样件的检验确 认;2、做好过程巡 检及填写过程检测报 告;3、填写巡检记 录表;4、在流转单 上签字确认
原材 料检 验
OK 压铸
OK入库
出库
OK入库
半成品仓库
去毛刺、抛丸
NG
隔离、返工
半成品仓库
NG
NG
隔离
退回供方、要求 查明原因并验证 合可后方可供货
确认NG报废
确认NG报废
出 库
出货检验人员:按照产品外 观检验标准对成品仓库的产 品进行比例抽检,对没有异 常的产品在外包装箱上盖上 检验合格章,对抽检出不合 格品的产品进行隔离,通知 生产返工
生产工艺流程图
质保来料检验人员:1、 每批铝锭进行光谱仪 检测,并做好入库检 测报告;2、做每炉一 次熔化炉前材料分析, 确保原材料合格 压铸操作员:1、做好首件 确认;2、按照工艺卡要求 操作;3、按要求填写好压 铸工序参数记录表;填写流 转单(机台号、数量、操作 员按实填写);4、遇到异 常及时汇报 质保巡检员人:1、 做好首样件的检验确 认;2、做好过程巡 检及填写过程检测报 告;3、在流转单上 签字确认 接收人员:1、验收数量, 确认签字;2、做好在库 产品的管控,标识清楚、 明确;3、做好各产品出、 入库的记录,确保帐、卡、 物一致 操作人员:1、按毛坯外观检验标 准操作,确保毛坯产品外观无缺 陷;2、接收上工序的产品确保数 量准确、核对无误;3、本工序完 成的产品要填写产品流转单(产 品名称、数量、操作员按实填写) 接收人员:1、验收数量, 确认签字;2、做好在库 产品的管控,标识清楚、 明确;3、做好各产品出、 入库的记录,确保帐、卡、 物一致
压铸生产作业流程图
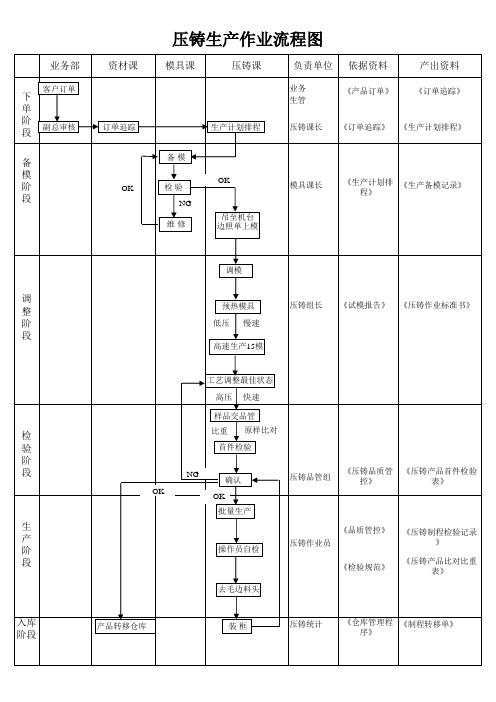
业务部 下 单 阶 段 备 模 阶 段
客户订单
资材课
模具课
压铸课
负责单位
业务 生管
依据资料
《产品订单》
产出资料
《订单追踪》
副总审核
订单追踪
生产计划排程
压铸课长
《订单追踪》
《生产计划排程》
备模 OK 模具课长 《生产计划排 《生产备模记录》 程》
OK
检验 NG 维修
吊至机台 边照单上模
《压铸制程检验记录 》 《压铸产品比对比重 表》
入库 阶段
产品转移仓库
装框
压铸统计
《仓库管理程序》 《制程转移单》
调模
调 整 阶 段
Байду номын сангаас
预热模具 低压 慢速
压铸组长
《试模报告》
《压铸作业标准书》
高速生产15模
工艺调整最佳状态 高压 快速
样品交品管
检 验 阶 段
OK
比重
原样比对
首件检验 NG 压铸品管组 《压铸品质管控》 《压铸产品首件检验 表》
确认 OK 批量生产
生 产 阶 段
《品质管控》 操作员自检 压铸作业员 《检验规范》 去毛边料头
压铸生产工艺

压铸生产工艺知识一.压铸生产的概念**压铸(DIE CASTING)就是将熔融合金在高压﹑高速条件下充满金属模并使其在高压下凝固冷却成型的精密铸造生产。
压铸制造出来的工件称为压铸件(DIE CASTINGS),压铸件主要特点尺寸公差很小(精密公差±0.08,一般公差±0.25),精密度高,表面不需经车削加工而只是经过整缘处理(如去批锋.抛光等)即可用于后工序如静电喷涂或装配生产。
二.压铸机(CASTING MACHINE)压铸机为热料室压铸机,基本结构如图所示:所用压铸机有两种型号:L.K。
DC—80(3台)﹑L。
K。
DC-160(4台),机器制造商:力劲机械厂有限公司(L.K。
MACHINERY CO.LTD)。
***机器的主要工作参数列表如下供参考:压铸机基本结构各部分作用;固定机板---—用以固定压铸模的静模(前模)部分;移动机构———-用以固定压铸模的动模(后模)部分;顶出机构-——-用以顶出压铸件;锁紧机构--——实现在压射过程中可靠地锁紧模具;配电及数显—电源供应﹑显示溶料温度﹑压铸程序及时间控制等;操纵台------控制压铸操作的系列动作;射料机构----将合金液推入模具型腔,进行充填成型;熔料室-——-—-将铸绽熔化为合金液并维持恒温。
***压铸机工序流程步骤:正常所采用的半自动生产操作,每个生产周期是靠开和关安全门来触发下一个局期,其流程可如图表达:关门--→(顶针退回)锁模—-→扣咀前—-→一速身料--→二速射料回錘喷(刷)说模剂←-—顶针顶出/钻取啤件←——开模←-—离咀三.压铸用的锌(Zinc)合金材料本公司所用皆为锌3#合金(EZDA 3PRESSURE KIECASTING ALLOY),其化学成份含量及作用如下表(见下页):1.锌合金主要性能特点如下:a)熔点较低;b)压铸成型效果好;c)铸件表面可镀金属,可以进行(静电)喷涂装饰;d)缺点:铸件易老化,抗腐蚀能力差.2.锌合金原料中掺入水口料对铸件的影响:在锌合金压铸生产中,适当地在材料中掺入水口料可降低铸件成本,但水口料掺入也会引致某些质量问题:a)水口料中往往含有杂质,使材料机械性能变差,使铸件不能满足使用要求:b)水口料中的化学成份巳发生变化,铝镁成份的减少会使材料理化性能变坏,从而会使铸件花纹和气泡等问题增多.如果通过化学鉴定及处理,在掺有水口料的锌合金(水口料一般不超过50%)中适当地加入铝和镁元素,并协同改善压铸模的排溢条件,选择适当的压铸参数,能够在一定程度上提高铸件质量,减少废品产生。
压铸工艺实操全过程
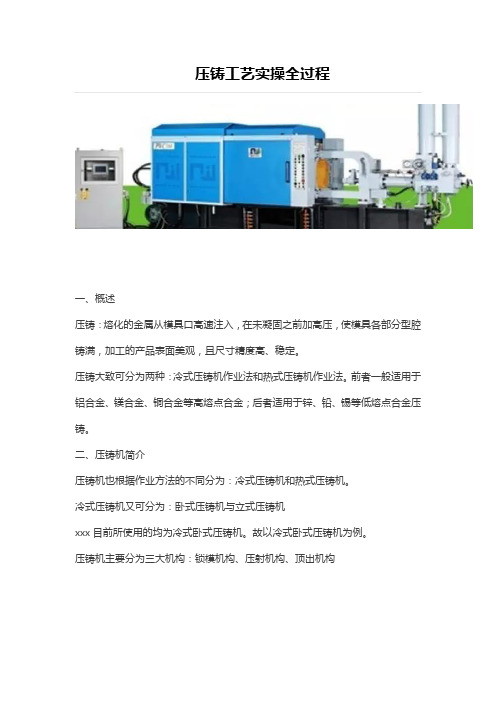
压铸工艺实操全过程一、概述压铸:熔化的金属从模具口高速注入,在未凝固之前加高压,使模具各部分型腔铸满,加工的产品表面美观,且尺寸精度高、稳定。
压铸大致可分为两种:冷式压铸机作业法和热式压铸机作业法。
前者一般适用于铝合金、镁合金、铜合金等高熔点合金;后者适用于锌、铅、锡等低熔点合金压铸。
二、压铸机简介压铸机也根据作业方法的不同分为:冷式压铸机和热式压铸机。
冷式压铸机又可分为:卧式压铸机与立式压铸机xxx目前所使用的均为冷式卧式压铸机。
故以冷式卧式压铸机为例。
压铸机主要分为三大机构:锁模机构、压射机构、顶出机构冷式压铸机本机各部名称:下面是冷式压铸机各装置的典型布局主要有压铸机本机、给汤机、喷涂机、取出机等组成。
三、压铸安全操作注意事项1、开机作业前,必须确认“安全门”、“非常停止按钮”、“操作电源开关”、的功能是否正常。
2、必须确认开合模、与取出机、喷雾机之间的安全互锁关系是否正常。
3、严禁两人或更多的人同时操作按钮。
当有帮手时(换模),必须在相互确认,高声呼喊,方可下一步动作。
4、压铸作业时,模具分型面前方严禁站人。
下面是铸造作业时发生灾害事故的分析:(数据来源日本)a 模具分型面最容易飞散铝液引起烫伤事故。
43%b 开模时候的料饼裂碎会引起烫伤事故。
7%c 被顶出板夹住引起事故。
6%d 被曲柄夹住引起事故。
2%e 其他的灾害事故42%5、取出机活动范围内严禁站人。
6、清理或修理模具时,必须关闭“操作电源开关”或按下“非常停止”按钮。
7、给汤机勺子作业前要预热、涂钛白粉、烘干,以免造成爆炸。
熔解炉中严禁注水。
8、压铸机、模具修理时,如有身体一部分要进入动作结构时,必须切断电源开关,以免机械误动造成人身伤害。
四、发生事故时的应急措施1、铝液爆炸时,操作工应尽快躲避,并高声通知。
2、发现火情,应立即关闭电源,随后用灭火器或砂子扑灭。
3、生产中,发现异常动作时,都应立即停止,报告领导,寻找原因。
4、如有人员受伤必须以最快速度送医院抢救。
生产工艺流程图和铸造工艺流程

生产工艺流程图铸造生产的工艺流程铸造生产是一个复杂的多工序组合的工艺过程,它包括以下主要工序:1〕生产工艺准备,根据要生产的零件图、生产批量和交货期限,制定生产工艺方案和工艺文件,绘制铸造工艺图;2〕生产准备,包括准备熔化用材料、造型制芯用材料和模样、芯盒、砂箱等工艺装备;3〕造型与制芯;4〕熔化与浇注;成形原理铸造生产是将金属加热熔化,使其具有流动性,然后浇入到具有一定形状的铸型型腔中,在重力或外力〔压力、离心力、电磁力等〕的作用下充满型腔,冷却并凝固成铸件〔或零件〕的一种金属成形方法.图1 铸造成形过程铸件一般作为毛坯经切削加工成为零件.但也有许多铸件无需切削加工就能满足零件的设计精度和表面粗糙度要求,直接作为零件使用.型砂的性能与组成1、型砂的性能型砂〔含芯砂〕的主要性能要求有强度、透气性、耐火度、退让性、流动性、紧实率和溃散性等.2、型砂的组成型砂由原砂、粘接剂和附加物组成.铸造用原砂要求含泥量少、颗粒均匀、形状为圆形和多角形的海砂、河砂或山砂等.铸造用粘接剂有粘土〔普通粘土和膨润土〕、水玻璃砂、树脂、合脂油和植物油等,分别称为粘土砂,水玻璃砂、树脂砂、合脂油砂和植物油砂等.为了进一步提高型〔芯〕砂的某些性能,往往要在型〔芯〕砂中加入一些附加物,如煤份、锯末、纸浆等.型砂结构,如图2所示.图2 型砂结构示意图工艺特点铸造是生产零件毛坯的主要方法之一,尤其对于有些脆性金属或合金材料〔如各种铸铁件、有色合金铸件等〕的零件毛坯,铸造几乎是唯一的加工方法.与其它加工方法相比,铸造工艺具有以下特点:1〕铸件可以不受金属材料、尺寸大小和重量的限制.铸件材料可以是各种铸铁、铸钢、铝合金、铜合金、镁合金、钛合金、锌合金和各种特殊合金材料;铸件可以小至几克,大到数百吨;铸件壁厚可以从0.5毫米到1米左右;铸件长度可以从几毫米到十几米.2〕铸造可以生产各种形状复杂的毛坯,特别适用于生产具有复杂内腔的零件毛坯,如各种箱体、缸体、叶片、叶轮等.3〕铸件的形状和大小可以与零件很接近,既节约金属材料,又省切削加工工时.4〕铸件一般使用的原材料来源广、铸件成本低.5〕铸造工艺灵活,生产率高,既可以手工生产,也可以机械化生产.铸件的手工造型手工造型的主要方法砂型铸造分为手工造型〔制芯〕和机器造型〔制芯〕.手工造型是指造型和制芯的主要工作均由手工完成;机器造型是指主要的造型工作,包括填砂、紧实、起模、合箱等由造型机完成.泊头铸造工量具友介绍手工造型的主要方法:手工造型因其操作灵活、适应性强,工艺装备简单,无需造型设备等特点,被广泛应用于单件小批量生产.但手工造型生产率低,劳动强度较大.手工造型的方法很多,常用的有以下几种:1.整模造型对于形状简单,端部为平面且又是最大截面的铸件应采用整模造型.整模造型操作简便,造型时整个模样全部置于一个砂箱内,不会出现错箱缺陷.整模造型适用于形状简单、最大截面在端部的铸件,如齿轮坯、轴承座、罩、壳等〔图2〕.图整模造型2.分模造型当铸件的最大截面不在铸件的端部时,为了便于造型和起模,模样要分成两半或几部分,这种造型称为分模造型.当铸件的最大截面在铸件的中间时,应采用两箱分模造型〔图3〕,模样从最大截面处分为两半部分〔用销钉定位〕.造型时模样分别置于上、下砂箱中,分模面〔模样与模样间的接合面〕与分型面〔砂型与砂型间的接合面〕位置相重合.两箱分模造型广泛用于形状比较复杂的铸件生产,如水管、轴套、阀体等有孔铸件.图3 套管的分模两箱造型过程铸件形状为两端截面大、中间截面小,如带轮、槽轮、车床四方刀架等,为保证顺利起模,应采用三箱分模造型〔图4〕.此时分模面应选在模样的最小截面处,而分型面仍选在铸件两端的最大截面处,由于三箱造型有两个分型面,降低了铸件高度方向的尺寸精度,增加了分型面处飞边毛刺的清整工作量,操作较复杂,生产率较低,不适用于机器造型,因此,三箱造型仅用于形状复杂、不能用两箱造型的铸件生产.图4 三箱分模造型举例3.活块模造型铸件上妨碍起模的部分〔如凸台、筋条等〕做成活块,用销子或燕尾结构使活块与模样主体形成可拆连接.起模时先取出模样主体,活块模仍留在铸型中,起模后再从侧面取出活块的造型方法称为活块模造型〔图5〕.活块模造型主要用于带有突出部分而妨碍起模的铸件、单件小批量、手工造型的场合.如果这类铸件批量大,需要机器造型时,可以用砂芯形成妨碍起模的那部分轮廓.图5 角铁的活块模造型工艺过程4.挖砂造型当铸件的外部轮廓为曲面〔如手轮等〕其最大截面不在端部,且模样又不宜分成两半时,应将模样做成整体,造型时挖掉妨碍取出模样的那部分型砂,这种造型方法称为挖砂造型.挖砂造型的分型面为曲面,造型时为了保证顺利起模,必须把砂挖到模样最大截面处〔图6〕.由于是手工挖砂,操作技术要求高,生产效率低,只适用于单件、小批量生产.图6 手轮的挖砂造型的工艺过程手工制芯型芯用来形成铸件内部空腔或局部外形.由于型芯的表面被高温金属液包围,长时间受到浮力作用和高温金属液的烘烤作用;铸件冷却凝固时,砂芯往往会阻碍铸件自由收缩;砂芯清理也比较困难.因此造芯用的芯砂要比型砂具有更高的强度、透气性、耐高温性、退让性和溃散性.手工制芯由于无需制芯设备,工艺装备简单,应用得很普遍.根据砂芯的大小和复杂程度,手工制芯用芯盒有整体式芯盒、对开式芯盒和可拆式芯盒,如图7所示.图7 芯盒制芯示意图零件、模样、芯盒与铸件的关系模样用来形成铸件的外部轮廓,芯盒用来制作砂芯,形成铸件的内部轮廓.造型时分别用模样和芯盒制作铸型和型芯.图1 分别表示零件、模样、芯盒和铸件的关系.制造模样和芯盒所选用的材料,与铸件大小、生产规模和造型方法有关.单件小批量生产、手工造型时常用木材制作模样和芯盒,大批量生产、机器造型时常用金属材料〔如铝合金、铸铁等〕或硬塑料制作模样和芯盒.图零件、模样、芯盒与铸件的关系铸造铸件常见缺陷分析铸造工艺过程复杂,影响铸件质量的因素很多,往往由于原材料控制不严,工艺方案不合理,生产操作不当,管理制度不完善等原因,会使铸件产生各种铸造缺陷.常见的铸件缺陷名称、特征和产生的原因,见表.常见铸件缺陷与产生原因缺陷名称特征产生的主要原因气孔在铸件内部或表面有大小不等的光滑孔洞①炉料不干或含氧化物、杂质多;②浇注工具或炉前添加剂未烘干;③型砂含水过多或起模和修型时刷水过多;④型芯烘干不充分或型芯通气孔被堵塞;⑤春砂过紧,型砂透气性差;⑥浇注温度过低或浇注速度太快等缩孔与缩松缩孔多分布在铸件厚断面处,形状不规则,孔内粗糙①铸件结构设计不合理,如壁厚相差过大,厚壁处未放冒口或冷铁;②浇注系统和冒口的位置不对;③浇注温度太高;④合金化学成分不合格,收缩率过大,冒口太小或太少砂眼在铸件内部或表面有型砂充塞的孔眼①型砂强度太低或砂型和型芯的紧实度不够,故型砂被金属液冲入型腔;②合箱时砂型局部损坏;③浇注系统不合理,内浇口方向不对,金属液冲坏了砂型;④合箱时型腔或浇口内散砂未清理干净粘砂铸件表面粗糙,粘有一层砂粒①原砂耐火度低或颗粒度太大;②型砂含泥量过高,耐火度下降;③浇注温度太高;④湿型铸造时型砂中煤粉含量太少;⑤干型铸造时铸型未刷涂斜或涂料太薄夹砂铸件表面产生的金属片状突起物,在金属片状突起物与铸件之间夹有一层型砂①型砂热湿拉强度低,型腔表面受热烘烤而膨胀开裂;②砂型局部紧实度过高,水分过多,水分烘干后型腔表面开裂;③浇注位置选择不当,型腔表面长时间受高温铁水烘烤而膨胀开裂;④浇注温度过高,浇注速度太慢错型铸件沿分型面有相对位置错移①模样的上半模和下半模未对准;②合箱时,上下砂箱错位;③上下砂箱未夹紧或上箱未加足够压铁,浇注时产生错箱冷隔铸件上有未完全融合的缝隙或洼坑,其交接处是圆滑的①浇注温度太低,合金流动性差;②浇注速度太慢或浇注中有断流;③浇注系统位置开设不当或内浇道横截面积太小;④铸件壁太薄;⑤直浇道〔含浇口杯〕高度不够;⑥浇注时金属量不够,型腔未充满浇不足铸件未被浇满裂纹铸件开裂,开裂处金属表面有氧化膜①铸件结构设计不合理,壁厚相差太大,冷却不均匀;②砂型和型芯的退让性差,或春砂过紧;③落砂过早;④浇口位置不当,致使铸件各部分收缩不均匀常见铸件缺陷与其预防措施序缺陷名称缺陷特征预防措施1气孔在铸件内部、表面或近于表面处,有大小不等的光滑孔眼,形状有圆的、长的与不规则的,有单个的,也有聚集成片的.颜色有白色的或带一层暗色,有时覆有一层氧化皮.降低熔炼时流言蜚语金属的吸气量.减少砂型在浇注过程中的发气量,改进铸件结构,提高砂型和型芯的透气性,使型内气体能顺利排出.2缩孔在铸件厚断面内部、两交界面的内部与厚断面和薄断面交接处的内部或表面,形状不规则,孔内粗糙不平,晶粒粗大.壁厚小且均匀的铸件要采用同时凝固,壁厚大且不均匀的铸件采用由薄向厚的顺序凝固,合理放置冒口的冷铁.3缩松在铸件内部微小而不连贯的缩孔,聚集在一处或多处,晶粒粗大,各晶粒间存在很小的孔眼,水压试验时渗水.壁间连接处尽量减小热节,尽量降低浇注温度和浇注速度.4渣气孔在铸件内部或表面形状不规则的孔眼.孔眼不光滑,里面全部或部分充塞着熔渣.提高铁液温度.降低熔渣粘性.提高浇注系统的挡渣能力.增大铸件内圆角.5砂眼在铸件内部或表面有充塞着型砂的孔眼.严格控制型砂性能和造型操作,合型前注意打扫型腔.6热裂在铸件上有穿透或不穿透的裂纹〔注要是弯曲形的〕,开裂处金属表皮氧化.严格控制铁液中的S、P含量.铸件壁厚尽量均匀.提高型砂和型芯的退让性.浇冒口不应阻碍铸件收缩.避免壁厚的突然改变.开型不能过早.不能激冷铸件.7冷裂在铸件上有穿透或不穿透的裂纹〔主要是直的〕,开裂处金属表皮氧化.8粘砂在铸件表面上,全部或部分覆盖着一层金属〔或金属氧化物〕与砂〔或涂料〕的混〔化〕合物或一层烧结构的型砂,致使铸件表面粗糙.减少砂粒间隙.适当降低金属的浇注温度.提高型砂、芯砂的耐火度.9夹砂在铸件表面上,有一层金属瘤状物或片状物,在金属瘤片和铸件之间夹有一层型砂.严格控制型砂、芯砂性能.改善浇注系统,使金属液流动平稳.大平面铸件要倾斜浇注.10冷隔在铸件上有一种未完全融合的缝隙或洼坑,其交界边缘是圆滑的.提高浇注温度和浇注速度.改善浇注系统.浇注时不断流.11浇不到由于金属液未完全充满型腔而产生的铸件缺肉.提高浇注温度和浇注速度.不要断流和防止跑火.铸造铸件金属液的浇注生产中,浇注时应遵循高温出炉,低温浇注的原则.因为提高金属液的出炉温度有利于夹杂物的彻底熔化、熔渣上浮,便于清渣和除气,减少铸件的夹渣和气孔缺陷;采用较低的浇注温度,则有利于降低金属液中的气体溶解度、液态收缩量和高温金属液对型腔表面的烘烤,避免产生气孔、粘砂和缩孔等缺陷.因此,在保证充满铸型型腔的前提下,尽量采用较低的浇注温度. 把金属液从浇包注入铸型的操作过程称为浇注.浇注操作不当会引起浇不足、冷隔、气孔、缩孔和夹渣等铸造缺陷,和造成人身伤害.为确保铸件质量、提高生产率以与做到安全生产,浇注时应严格遵守下列操作要领:〔1〕浇包、浇注工具、炉前处理用的孕育剂、球化剂等使用前必须充分烘干,烘干后才能使用.〔2〕浇注人员必须按要求穿好工作服,并配戴防护眼镜,工作场地应通畅无阻.浇包内的金属液不宜过满,以免在输送和浇注时溢出伤人.〔3〕正确选择浇注速度,即开始时应缓慢浇注,便于对准浇口,减少熔融金属对砂型的冲击和利于气体排出;随后快速浇注,以防止冷隔;快要浇满前又应缓慢浇注,即遵循慢、快、慢的原则.〔4〕对于液态收缩和凝固收缩比较大的铸件,如中、大型铸钢件,浇注后要与时从浇口或冒口补浇.〔5〕浇注时应与时将铸型中冒出的气体点燃顺气,以免由于铸型憋气而产生气孔,以与由于气体的不完全燃烧而损害人体健康和污染空气.铸造的坩埚炉熔化常用的铸造有色金属有铸造铝合金、铸造铜合金、铸造镁合金和铸造锌合金等.有色金属的熔点低,其常用的熔化用炉有坩埚炉和反射炉两类,用电、油、煤气或焦碳等作为燃料.中、小工厂普遍采用坩埚炉熔化,如电阻坩埚炉、焦碳坩埚炉等,生产大型铸件时一般使用反射炉熔化,如重油反射炉、煤气反射炉等.如图是坩埚炉的示意图.图坩埚炉的示意图熔模铸造熔模铸造又称失蜡铸造或精密铸造.它是用易熔材料〔如蜡料〕制成模样并组装成蜡模组,然后在模样表面上反复涂覆多层耐火涂料制成模壳,待模壳硬化和干燥后将蜡模熔去,模壳再经高温焙烧后浇注获得铸件的一种铸造方法.熔模铸造工艺过程.可用熔模铸造法生产的合金种类有碳素钢、合金钢、耐热合金、不锈钢、精密合金、永磁合金、轴承合金、铜合金、铝合金、钛合金和球墨铸铁等.熔模铸件的形状一般都比较复杂,铸件上可铸出孔的最小直径可达0.5mm,铸件的最小壁厚为0.3mm.在生产中可将一些原来由几个零件组合而成的部件,通过改变零件的结构,设计成为整体零件而直接由熔模铸造铸出,以节省加工工时和金属材料的消耗,使零件结构更为合理.熔模铸件的重量大多为零点几十牛〔即几十克到几公斤〕,太重的铸件用熔模铸造法生产较为麻烦,但目前生产大的熔模铸件的重量已达800牛左右.熔模铸造工艺过程较复杂,且不易控制,使用和消耗的材料较贵,故它适用于生产形状复杂、精度要求高、或很难进行其它加工的小型零件,如涡轮发动机的叶片等.金属型铸造,硬模铸造将液态金属浇入用金属材料制成的铸型而获得铸件的方法,称为金属型铸造.金属铸型可反复使用,又称为永久型铸造或硬模铸造.金属型一般用耐热铸铁或耐热钢做成.金属型铸造又称硬模铸造,它是将液体金属浇入金属铸型,以获得铸件的一种铸造方法.铸型是用金属制成,可以反复使用多次〔几百次到几千次〕.金属到铸造与砂型铸造比较:在技术上与经济上有许多优点.〔1〕金属型生产的铸件,其机械性能比砂型铸件高.同样合金,其抗拉强度平均可提高约25%,屈服强度平均提高约20%,其抗蚀性能和硬度亦显著提高;〔2〕铸件的精度和表面光洁度比砂型铸件高,而且质量和尺寸稳定;〔3〕铸件的工艺收得率高,液体金属耗量减少,一般可节约15~30%;〔4〕不用砂或者少用砂,一般可节约造型材料80~100%;此外,金属型铸造的生产效率高;使铸件产生缺陷的原因减少;工序简单,易实现机械化和自动化.金属型铸造虽有很多优点,但也有不足之处.如:<1> 金属型制造成本高;<2> 金属型不透气,而且无退让性,易造成铸件洗不足、开裂或铸铁件白日等缺陷;<3> 金属型铸造时,铸型的工作温度、合金的浇注温度和浇注速度,铸件在铸型中停留的时间,以与所用的涂料等,对铸件的质量的影响甚为敏感,需要严格控制.金属型铸造目前所能生产的铸件,在重量和形状方面还有一定的限制,如对黑色金属只能是形状简单的铸件;铸件的重量不可太大;壁厚也有限制,较小的铸件壁厚无法铸出.因此,在决定采用金属型铸造时,必须综合考虑下列各因素:铸件形状和重量大小必须合适;要有足够的批量;完成生产任务的期限许可.金属型铸件形成过程的特点金属型和砂型,在性能上有显著的区别,如砂型有透气性,而金属型则没有;砂型的导热性差,金属型的导热性很好,砂型有退让性,而金属型没有等.金属型的这些特点决定了它在铸件形成过程中有自己的规律.型腔内气体状态变化对铸件成型的影响:金属在充填时,型腔内的气体必须迅速排出,但金属又无透气性,只要对工艺稍加疏忽,就会给铸件的质量带来不良影响.铸件凝固过程中热交换的特点:金属液一旦进入型腔,就把热量传给金属型壁.液体金属通过型壁散失热量,进行凝固并产生收缩,而型壁在获得热量,升高温度的同时产生膨胀,结果在铸件与型壁之间形成了"间隙〞.在"铸件一间隙一金属型〞系统未到达同一温度之前,可以把铸件视为在"间隙〞中冷却,而金属型壁则通过"间隙〞被加热.金属型阻碍收缩对铸件的影响:金属型或金属型芯,在铸件凝固过磋甲无退让性,阻碍铸件收缩,这是它的又一特点.金属型铸造工艺1金属到的预热未预热的金属型不能进行浇注.这是因为金属型导热性好/液体金属冷却决,流动性剧烈降低,容易使铸件出现冷隔、浇不足夹杂、气孔等缺陷.未预热的金属型在浇注时,铸型,将受到强烈的热击,应力倍增,使其极易破坏.因此,金属型在开始工作前,应该先预热,适宜的预热温度〔即工作温度〕,随合金的种类、铸件结构和大小而定,一般通过试验确定.一般情况下,金属型的预热温度不低于1500C.金属型的预热方法有:〔1〕用喷灯或煤气火焰预热;〔2〕采用电阻加热器;〔3〕采用烘箱加热,其优点是温度均匀,但只适用于小件的金属型;〔4〕先将金属型放在炉上烘烤,然后浇注液体金属将金属型烫热.这种方法,只适用于小型铸型,因它要浪费一些金属液,也会降低铸型寿命.2金属型的浇注金属型的浇注温度,一般比砂型铸造时高.可根据合金种类、如化学成分、铸件大小和壁厚,通过试验确定.下表中数据可供参考.各种合金的浇注温度合金种类浇注温度℃合金种类浇注温度℃铝锡合金350~450 黄铜900~950锌合金450~480 锡青铜1100~1150铝合金680~740 铝青铜1150~1300镁合金715~740 铸铁1300~1370由于金属型的激冷和不透气,浇注速度应做到先慢,后快,再慢.在浇注过程中应尽量保证液流平稳.3铸件的出型和抽芯时间如果金属型芯在铸件中停留的时间愈长,由于铸件收缩产生的抱紧型芯的力就愈大,因此需要的抽芯力也愈大.金属型芯在镜件中最适宜的停留时间,是当铸件冷却到塑性变形温度X 围,并有足够的强度时,这时是抽芯最好的时机.铸件在金属型中停留的时间过长,型壁温度升高,需要更多的冷却时间,也会降低金属型的生产率.最合适的拔芯与铸件出型时间,一般用试验方法确定.4金属型工作温度的调节要保证金属型铸件的质量稳定,生产正常,首先要使金属型在生产过程中温度变化恒定.所以每浇一次,就需要将金属型打开,停放一段时间,待冷至规定温度时再浇.如靠自然冷却,需要时间较长,会降低生产率,因此常用强制冷却的方法.冷却的方式一般有以下几种:〔1〕风冷:即在金属型外围吹风冷却,强化对流散热.风冷方式的金属型,虽然结构简单,容易制造,成本低,但冷却效果不十分理想.〔2〕间接水冷:在金属型背面或某一局部,镶铸水套,其冷却效果比风冷好,适于浇注铜件或可锻铸铁件.但对浇注薄壁灰铁铸件或球铁铸件,激烈冷却,会增加铸件的缺陷.熔模铸造铸件的特点熔模铸造方法的另一优点是,它可以铸造各种合金的复杂的铸件,特别可以铸造高温合金铸件.如喷气式发动机的叶片,其流线型外廓与冷却用内腔,用机械加工工艺几乎无法形成.用熔模铸造工艺生产不仅可以做到批量生产,保证了铸件的一致性,而且避免了机械加工后残留刀纹的应力集中.熔模铸件尺寸精度较高,一般可达CT4-6〔砂型铸造为CT10~13,压铸为CT5~7〕,当然由于熔模铸造的工艺过程复杂,影响铸件尺寸精度的因素较多,例如模料的收缩、熔模的变形、型壳在加热和冷却过程中的线量变化、合金的收缩率以与在凝固过程中铸件的变形等,所以普通熔模铸件的尺寸精度虽然较高,但其一致性仍需提高〔采用中、高温蜡料的铸件尺寸一致性要提高很多〕.压制熔模时,采用型腔表面光洁度高的压型,因此,熔模的表面光洁度也比较高.此外,型壳由耐高温的特殊粘结剂和耐火材料配制成的耐火涂料涂挂在熔模上而制成,与熔融金属直接接触的型腔内表面光洁度高.所以,熔模铸件的表面光洁度比一般铸造件的高,一般可达Ra.1.6~3.2μm.熔模铸造最大的优点就是由于熔模铸件有着很高的尺寸精度和表面光洁度,所以可减少机械加工工作,只是在零件上要求较高的部位留少许加工余量即可,甚至某些铸件只留打磨、抛光余量,不必机械加工即可使用.由此可见,采用熔模铸造方法可大量节省机床设备和加工工时,大幅度节约金属原材料消耗.铸造生产的工艺流程铸造生产是一个复杂的多工序组合的工艺过程,它包括以下主要工序:1〕生产工艺准备,根据要生产的零件图、生产批量和交货期限,制定生产工艺方案和工艺文件,绘制铸造工艺图;2〕生产准备,包括准备熔化用材料、造型制芯用材料和模样、芯盒、砂箱等工艺装备;3〕造型与制芯;4〕熔化与浇注;成形原理铸造生产是将金属加热熔化,使其具有流动性,然后浇入到具有一定形状的铸型型腔中,在重力或外力〔压力、离心力、电磁力等〕的作用下充满型腔,冷却并凝固成铸件〔或零件〕的一种金属成形方法.图1 铸造成形过程铸件一般作为毛坯经切削加工成为零件.但也有许多铸件无需切削加工就能满足零件的设计精度和表面粗糙度要求,直接作为零件使用.型砂的性能与组成1、型砂的性能型砂〔含芯砂〕的主要性能要求有强度、透气性、耐火度、退让性、流动性、紧实率和溃散性等.2、型砂的组成型砂由原砂、粘接剂和附加物组成.铸造用原砂要求含泥量少、颗粒均匀、形状为圆形和多角形的海砂、河砂或山砂等.铸造用粘接剂有粘土〔普通粘土和膨润土〕、水玻璃砂、树脂、合脂油和植物油等,分别称为粘土砂,水玻璃砂、树脂砂、合脂油砂和植物油砂等.为了进一步提高型〔芯〕砂的某些性能,往往要在型〔芯〕砂中加入一些附加物,如煤份、锯末、纸浆等.。
过程流程图-铝压铸产品

机械加工工艺流程卡/Turning Process control card
3 尺寸¢8.74 用卡尺测量控制 /Dimension¢8.74 measure with M caliper
□
去油物 /Degreasing
喷砂处理/ Sand blasting
零件号 /Part No.
零件描 述 /Descr iption: 图样更 改等级
工序号 制造◇ /SN /MFG
3800100300
MOTOR COVER
A
搬运○ /Transit
储存△ /Store
检验□ /Inspect
过程描述 /Process Description
过程流程图
Process Flow Chart
文件编号: 创建日期:
BL 20101202 20101202
修改日期:
责任人:
特殊特 性/S.C
过程特性控制/Process Control Point
产品特性控制 /Production CC
控制方法/Control Plan
10
□ 进货检验/IQC
供应商提供材质证明/Supplier support material certificate
表面粗糙度25μ-45 μ/Anchor profile 25μ-45μ
用粗糙计测量控制/mearsure with roughmeter
铬酸盐处理指导书/ Chromating Process Guide Card
物料储存、搬运收发管理流程 /Store flow chart
检验作业指导书/Inspection WI
压铸机工作的循环程序图

压铸模具抽芯器上的行程开关及油管的接法一、抽芯器在安装后,必须先在电脑上进行选择。
选择方法:打开电脑“菜单”,找到“抽芯”选择,在要使用的抽芯序号上选择“选择”1、动模上的抽芯器一般应选择“锁模前”2、定模上的抽芯器一般应选择“锁模后”注意:定模抽芯器在1250吨上应选择“抽芯4”,1600吨应选择“抽芯7”。
3、抽芯器选择后,应选择抽芯压力,特别是用定模抽芯时应选择“140bar”。
“锁模前”的程序是:如程序循环图的“抽芯1”,压铸机先关门,再插芯,插芯到底,插芯(入限)信号得到后,才合模,开模后先抽芯,抽芯到底,抽芯(出限)信号得到后,才顶出。
“入限”和“出限”的信号可以在电脑“输入显示”上找到。
“锁模后”的程序是:如程序循环图的“抽芯2”,压铸机合模后,再插芯,插芯到底,插芯(入限)信号得到后,合模指示灯才能亮,才能压射。
铸件冷却时间到,先抽芯,抽芯到底,抽芯(出限)信号得到后,才能开模。
二、抽芯信号的连接1、抽芯信号的连接必须与选择的抽芯器及电磁阀相对应。
2、在接好线路后必须进行确认,抽芯器在抽出的位置时,电脑“输入显示”中对应的抽芯“出限”必须显示“1”“入限”显示“0”。
当抽芯器在插入的位置时“出限”显示“0”“入限”显示“1”。
3、如果几个抽芯器共用一个抽芯电磁阀,液压油管采用“并联”,行程开关采用“串联”连接,串联和并联按图示。
三、抽芯器的调试1、抽芯器安装后应打到“手动”位置,进行调整,确认动作正常,电脑“输入显示”中“入限”和“出限”信号正确。
2、定模抽芯器或需要选择“锁模后”的抽芯器,应先选择“锁模前”进行手动调整,确认动作正常,“出限”和“入限”信号正常后。
选回“锁模后”。
只有在上述连接、调整全部完成并得以确认后,才能进行生产。
上述方法要求压铸工必须认真学习、领会,如有不懂的地方应及时请教,如果一个月内还不会连接或调整抽芯器,将不得从事压铸工作。
2006-1-12 附图:压铸机工作循环程序图。
压铸基本工艺流程图

压铸工艺流程图
压铸简介:压铸的实质是将熔化好的合金铝水或锌水通过压铸机的压射冲头高速,高压运动而迅速充满模具型腔内,采用模具运水进行循环冷却而快速获得铸件。由于采用金属模具,生产出来的铸件具有光滑的表面,能保持铸件的尺寸精度及能生产各类形状结构复杂的零件。因而被世界各地广泛采用于生产制造汽车,摩托车配件,航天航空通讯器材,医疗器材,电子产品及建材装鉓类等ห้องสมุดไป่ตู้属加工工艺。
铝合金压铸工艺
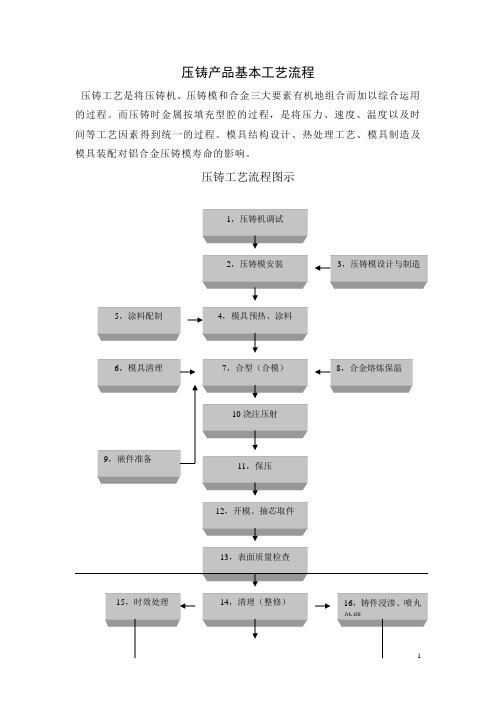
压铸产品基本工艺流程压铸工艺是将压铸机、压铸模和合金三大要素有机地组合而加以综合运用的过程。
而压铸时金属按填充型腔的过程,是将压力、速度、温度以及时间等工艺因素得到统一的过程。
模具结构设计、热处理工艺、模具制造及模具装配对铝合金压铸模寿命的影响。
压铸工艺流程图示1.11压铸工艺原理压铸工艺原理是利用高压将金属液高速压入一精密金属模具型腔内,金属液在压力作用下冷却凝固而形成铸件。
冷、热室压铸是压铸工艺的两种基本方式,其原理如图1-1所示。
冷室压铸中金属液由手工或自动浇注装置浇入压室内,然后压射冲头前进,将金属液压入型腔。
在热室压铸工艺中,压室垂直于坩埚内,金属液通过压室上的进料口自动流入压室。
压射冲头向下运动,推动金属液通过鹅颈管进入型腔。
金属液凝固后,压铸模具打开,取出铸件,完成一个压铸循环。
1.12压铸工艺的特点优点(1)可以制造形状复杂、轮廓清晰、薄壁深腔的金属零件。
压铸件的尺寸精度较高,表面粗糙度达Ra0.8—3.2um,互换性好。
(2)材料利用率高。
由于压铸件的精度较高,只需经过少量机械加工即可装配使用,有的压铸件可直接装配使用。
生产效率高。
由于高速充型,充型时间短,金属业凝固迅速,压铸作业循环速度快。
方便使用镶嵌件。
(3)缺点(1)由于高速填充,快速冷却,型腔中气体来不及排出,致使压铸件常有气孔及氧化夹杂物存在,从而降低了压铸件质量。
不能进行热处理。
(2)压铸机和压铸模费用昂贵,不适合小批量生产。
(3)压铸件尺寸受到限制。
压铸合金种类受到限制。
主要用来压铸锌合金、铝合金、镁合金及铜合金。
1.13压铸工艺的应用范围压铸生产效率高,能压铸形状复杂、尺寸精确、轮廓清晰、表面质量及强度、硬度都较高的压铸件,故应用较广,发展较快。
目前,铝合金压铸件产量较多,其次为锌合金压铸件。
第二章压铸合金2.1 压铸合金压铸合金是压铸生产的要素之一,要生产优良的压铸件,除了要有合理的零件构造、设计完善的压铸模和工艺性能优越的压铸机外,还需要有性能良好的合金。
锌合金压铸生产工艺

1
钢丝绳压铸设备操作流程
一、 生产操作流程:
设备安装调式完毕(注意液压泵转向方向和冷却泵旋转方向)和日常使用过程中,必须遵循;
1.1、接通控制箱边上的断路器,设备处于待操作状态;
2.1、打开【电源开关】,稍等 30 秒左右,等待触摸屏打开后,旋转【预约 加温】旋钮至【加温】位置,触摸屏会自动跳转至温控界面, 此时坩埚开始加温,炉嘴暂时不加温,等到坩埚温度到达 350℃ 后,炉
嘴
会自动加温,(注3.1
、待温度上升至所需温度并锅内的锌合金已经融化,将【手动自动】旋钮旋至【手动】界面,点击触摸屏上面的,【手动上升】,将
模具上升
到4.1、将模具安装好,冷却管插在模具上,不要有漏水现象,注意: 此时将【射料允许】调至【灯灭】状态,在按【手动合模】开关, 和模后不要有缝隙现象,在循环几次,确认模具安装无误!
5.1最后将射料【允许开关】打开,就可以自动工作了,
注意:下班之前将锅内的锌合金料尧至低于活塞缸套平面到一公分位置最佳;(这样对干锅的寿命延长很多倍)开机时请将泄压阀(电机接线盒旁边的旋钮)拧紧!维修时一定要打开泄压阀,将压力完全泄掉!
二、保养和维护:
2.1、定期检查冷却管路有无漏水和堵塞;
2.2、定期检查螺钉是否松动,并应拧紧;
2.3、定期检查加热圈、加热管是否正常工作;
2.4、每天必需给模具、导套、铜套加油润滑;
2.5、每年给油箱更换液压油,请使用46#抗磨液压
油;
2.6、设备关节处每班加油2 次以上,防止卡死;
2.7、每班检查油缸密封圈是否有漏油现象,并及时
修复;
2.8、定期检查继电器、接触器触点工作是否正常;
2。
压铸工艺流程图

镭雕
镭雕
镭雕反面、包
热整形
LCD框平面度≤0.2mm,TP平面度≤0.2mm
热整形SOP
12
整包
全检
牙孔、外观、结构、平面度
全检SOP
13 符号
整包
包装
用2号卡盒包装,一个卡盒装120 变更内容 变更人
包装SOP 变更时间
核准:
审核:
制表:
周国敏 FM-MP-05-01-13B
5
冲压
全检
裂纹、冷料、压伤、崩缺
冲压全检SOP
6
CNC/机加 CNC/机加钻孔攻牙
15-M1.4×0.3mm通牙
CNC/机加钻孔攻牙SOP
7
披锋
修披锋
用平锉刀,尖三角刀,软铝丝刷子
修披锋SOP
8
外发
钝化处理
钝化本色,盐雾测试需过24H以上OK,表面不能有脏污等不良
9
品保
抽检
表面要求无油污,手指印
10
工艺流程图 客户/图号 序号 1 责任部门
压铸
表单编号:B-FC-1605001
品名: 流程图
压铸
J508X
版本/版次
A/0
日期:
2017/5/6 指导性资料
压铸SOP
工艺简述
1出2
2
冲压
粗冲
油压冲床,1模出2
粗冲SOP
3
冲压
精冲1
自动冲床,1出1
精冲1SOP
4
冲压
精冲2
自动冲床,1出1
精冲2SOP