中天7号高炉冷却壁八年零破损
高炉冷却壁

高炉冷却壁发布: 2016-01-05 15:43 来源: 网络专业资料。
高炉冷却壁高炉冷却壁摘要:冷却壁是高炉重要的冷却设备,直接影响高炉炉体的使用寿命。
本文综述了国内外冷却壁的制备技术...高炉冷却壁摘要:冷却壁是高炉重要的冷却设备,直接影响高炉炉体的使用寿命。
本文综述了国内外冷却壁的制备技术、应用及其发展概况,分析了铸铁冷却壁、钢冷却壁和铜冷却壁的特点,并探讨了高炉冷却壁的未来发展趋势。
1. 前言高炉冷却壁是高炉内衬的重要水冷件,安装在高炉的炉身、炉腰、炉腹、炉缸等部位,不但承受高温,还承受炉料的磨损、熔渣的侵蚀和煤气流的冲刷,必须具备良好的热强度、耐热冲击、抗急冷急热性等综合性能。
冷却壁能有效地防止炉壳受热和烧红,高炉内衬砖被烧蚀后主要靠渣皮保护冷却壁本身,并维持高炉的安全生产。
因此,冷却壁的材质及性能好坏决定其工作寿命乃至高炉炉身的寿命。
国内外钢铁企业的生产情况证明,高炉长寿的关键之一是实现冷却壁的长寿[1,2]。
因而提高冷却壁的质量和使用寿命是高炉长寿的1个重要研究课题。
从20世纪70年代开始,西方一些发达国家对高炉冷却壁进行了大量的研究及材质的更新。
目前国外先进高炉的寿命可达15年以上,有的达20年以上,最近大修的部分高炉已将长寿目标定为30年[3]。
我国对冷却壁的制造、应用技术研究始于20世纪80年代中期,20多年来我国高炉冷却壁技术取得了长足的进展,但高炉冷却壁的设计研究和制作工艺与高炉长寿的目标还有一定的差距。
目前我国很多高炉一代炉役无中修寿命低于10年,仅少数高炉可实现10~15年。
高炉寿命的总体水平与国外先进水平相差较大[4]。
本文旨在总结国内外高炉冷却壁的制备技术和应用现状,分析各类冷却壁的特点,探讨未来高炉冷却壁今后的发展趋势。
2. 高炉冷却壁的种类、特点及其制备技术冷却壁是高炉的关键部件,在高温状态下工作,工作条件恶劣。
其破坏形式是在高温交变热应力作用下引起开裂漏水,使高炉被迫停炉大中修。
高炉冷却设备破损分析

炉冷 却设 备破 损 的主要 原 因如下 。
1 1 高温烧 蚀 . 冷 却壁 热 面的最 高工 作 温度应 低 于 7 9C, 0  ̄ 失
去 砖衬 保 护后 , 却 设 备 在 10 冷 00~10  ̄ 高温 30C的 条 件下 工作 , 当热 负荷 超 过 一 定值 时 , 烧 坏 铸铁 会 冷 却壁 。特 别 是 原 燃 料 条 件 较 差 的 高 炉 , 缘 气 边
在炉身下部至炉腹部位高温 区冷却设备破损数量
达到 2 % 以上 时 , 量 降 低 约 1% 、 比升 高 1 0 产 0 焦 0
~
1k/ 左 右 。 5gt
炉腹 至 炉 身 下 部 是 破 坏 作 用 最 强 的部 位 , 因 此 砖衬 的侵 蚀 速 度 最 快 , 般 只 能 保 持 4~5个 一
械磨损 、 和化 学 侵 蚀 等 综 合 的破 坏 作 用 。根 据 宝
钢技术 中心 和北 京 钢 铁 研 究 总 院 的研 究 结 果 , 高
炉况造成大 的影响。如果冷 却设 备破 损数 量较
多, 破损后 又 不能及 时 查 出并 关 水 , 造成 炉况 太 将 凉甚 至导 致 炉 缸 冻 结 。与 此 同时 , 却 板 破 损 后 冷 不 能起 托 砖作用 , 衬脱 落 , 合 理 的操 作 炉 型 受 砖 使
目前 , 国 高 炉 炉体 的 长 寿 问 题 仍 然 没 有 完 我 全 解决 , 一般 在开 炉一 年 以后 冷 却 板便 开 始 破 损 。
高炉冷却壁的破损机理及减少破损的措施

高炉冷却壁的破损机理及减少破损的措施摘要:高炉设计炉容为1580m3,于2011年2月开炉。
自2017年以来,发现炉基上涨速度加快,由2017年10月的31mm升高至2019年3月的86mm,高炉六至八段冷却壁破损严重,致使高炉被迫大修。
通过对高炉冷却壁的破损调查研究,得到如下结论:(1)球墨铸铁冷却壁破损的形式有开裂、烧损、熔化,并发现有水管的裸露和破损,其中8层冷却壁的受损数量最多。
冷却壁上出现最多的是纵向裂纹,对冷却壁的机械强度和力学性能有不利影响。
(2)对球墨铸铁冷却壁表面样进行元素及化合物分析,11-13层和15-17层的锌含量和碱金属含量较高。
锌和碱金属对冷却壁有化学侵蚀的危害,其生成的低熔点化合物对高炉顺行不利。
应当严格控制燃料和铁矿石的锌含量和碱金属含量,从源头上减少对冷却壁的化学侵蚀。
(3)由铸铁冷却壁试样的拉伸实验结果可知,冷却壁试样的抗拉强度(与没有经历生产的球墨铸铁相比)明显变小,且距离热面越近的试样,抗拉强度越小。
炉内的高温削弱了冷却壁的力学性能。
关键词:高炉;铸铁冷却壁;破损调查;破损机理分析1我国铜冷却壁的应用我国钢铁厂在2000年之前多采用铸铁冷却壁。
2002年,攀钢首次在高炉中安装了两段铜冷却壁[18]。
由于并无铜冷却壁的生产经验,攀钢只能自己摸索出合理的操作炉型和操作方法以维持炉况稳定。
经过十几年的研究、发展、改进,目前我国自主制造的部分铜冷却壁在各种技术数据上已达到甚至超过了国外产品的水准,但有些铜冷却壁仍然不能独立自主生产,依赖国外进口。
铜冷却壁在实际生产中的广泛应用为我国高炉冷却壁寿命的大幅延长做出了巨大贡献。
1.1铜冷却壁的优点及优势(1)导热性能好。
铸铁的导热系数仅有40×1.163W/(m∙℃)。
而铜的导热系数高达400W/(m∙℃)。
由此可见,铜的导热性能为铸铁的10倍左右。
所以,铜冷却壁热面与水管表面的温差很低,在实际生产中可控制在20℃以内。
高炉铜冷却壁破损的原因分析与防治

高炉铜冷却壁破损的原因分析与防治高炉是冶炼铁和炼钢的重要设备,而高炉铜冷却壁作为高炉内部的重要零部件,承担着冷却炉料和空气的作用,有着至关重要的作用。
在高炉正常运行过程中,铜冷却壁破损问题一直存在。
本文将从原因分析和防治措施两个方面进行阐述。
一、原因分析(一)原材料的选用高炉铜冷却壁一般采用无氧铜作为主要原料。
如果使用的无氧铜含有过高的杂质,或者成分不合格,就会影响到冷却壁的使用寿命。
如果原材料的熔炼温度不够高,会导致铜冷却壁的晶粒粗大,降低了材料的韧性和强度,使得冷却壁容易出现开裂和脱落。
(二)冷却壁的设计和制造工艺高炉铜冷却壁的设计和制造工艺直接影响到其使用寿命。
如果设计不合理或者制造工艺不到位,就会导致冷却壁存在裂纹、气孔、夹渣等缺陷,从而影响到冷却壁的整体性能。
(三)高炉操作参数的管理高炉的操作参数直接影响到冷却壁的使用寿命,主要包括高炉操作温度、气体流量、炉料质量等。
如果操作参数设置不合理,可能会导致冷却壁过热、气体侵蚀、炉料侵蚀等问题,从而加速冷却壁的破损。
(四)工作环境的影响高炉内部的工作环境也会对冷却壁的破损产生影响。
高炉内部存在有害气体、金属水蒸气等,会加速冷却壁的氧化腐蚀,从而缩短其使用寿命。
二、防治措施为了提高高炉铜冷却壁的使用寿命,应当选用优质的无氧铜作为原材料,并对原材料进行严格的质量把关,确保铜冷却壁的主要成分和杂质含量符合要求。
在冷却壁的设计和制造工艺中,应当采用先进的工艺技术和设备,确保其表面光洁度和内部质量达到标准要求。
对冷却壁进行严格的质量检验,确保没有裂纹、气孔、夹渣等缺陷。
对高炉的操作参数进行合理设置和调控,避免过高的温度、过大的气体流量等因素对冷却壁造成损害。
适时对冷却壁进行冷却和清理,防止炉料残渣的侵蚀。
高炉铜冷却壁破损问题是高炉运行中不可避免的。
但是通过对原因进行分析,并采取相应的防治措施,可以有效地延长铜冷却壁的使用寿命,减少破损对高炉运行的影响。
高炉冷却壁破损原因分析

好 些 ( 图 3 示 ) 1~4段 冷却 壁完好 无损 。 如 所 。 01
主要 是 高 炉 所用 焦 炭 品种 改 变 ,高 炉 顺行 较 差 ,
收 稿 日期 :0 0 0 — 8 2 1— 8 2 文 章 编 号 :0 0 15 2 1— 2 作 者 简介 : 波 ( 9 5 )男 , 门从 事 高 炉 设 备 点 检段 、、 81 ~ O段
光面球墨铸铁冷却壁
轧 制 四通 道 铜 冷 却 壁 双 层 水 冷 镶 砖 球 墨 铸 铁 冷 却 壁 特 种 喷 涂 料 S3 4 SC砖 iN 一 i
1 、2 1 1 段
1 、4段 3l
单层水冷镶砖球墨铸 铁冷却壁
倒 扣 球 墨 铸 铁 冷 却 壁
好 , 分 5段铜 冷 却 壁下 部 燕尾 槽磨 损 严 重 , 7 部 5段 l、
12 下部 工艺 孔漏 水 , 图 2所示 。 4 如 炉 身 8 9两段 球 墨 铸铁 镶 砖 冷 却 壁 破损 最 严 重 , 、 勾 头全 部 损坏 , 砖基 本 不 存 在 , 镶 几乎 全 部 露 出水 管 ,
炉底 至炉 喉共设 置 1 冷却壁 。 照炉 内纵 向各 区域 4段 按 不 同的工作 条件 和热 负荷 大小 ,采 用不 同结 构形 式 和 不 同材 质 的冷 却 壁见 表 1 。
表 I 全 冷 却 壁 ( 铁 + ) 案 主 要 特 征 铸 铜 方
部 位 1 3段  ̄ 冷 却 壁 结 构 光 面低 铬 铸 铁 冷 却 壁 砖 衬 材 质
E p r n e x h n e经 验 交 流 x ei c sE c a g e
高炉冷却壁破损原 因分析
魏 波 ,童 静 ,陈 先利 ( 阳钢铁集 团 有 限公 司炼 铁 厂 , 南安 阳市 4 5 0 安 河 5 0 4)
高炉中的冷却壁技术和维护
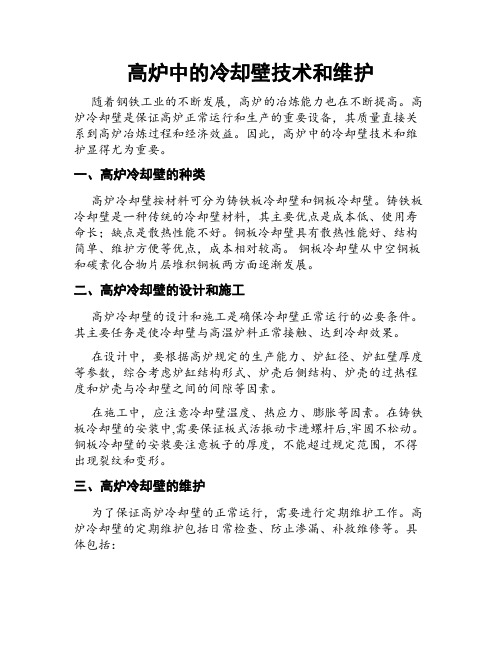
高炉中的冷却壁技术和维护随着钢铁工业的不断发展,高炉的冶炼能力也在不断提高。
高炉冷却壁是保证高炉正常运行和生产的重要设备,其质量直接关系到高炉冶炼过程和经济效益。
因此,高炉中的冷却壁技术和维护显得尤为重要。
一、高炉冷却壁的种类高炉冷却壁按材料可分为铸铁板冷却壁和铜板冷却壁。
铸铁板冷却壁是一种传统的冷却壁材料,其主要优点是成本低、使用寿命长;缺点是散热性能不好。
铜板冷却壁具有散热性能好、结构简单、维护方便等优点,成本相对较高。
铜板冷却壁从中空铜板和碳素化合物片层堆积铜板两方面逐渐发展。
二、高炉冷却壁的设计和施工高炉冷却壁的设计和施工是确保冷却壁正常运行的必要条件。
其主要任务是使冷却壁与高温炉料正常接触、达到冷却效果。
在设计中,要根据高炉规定的生产能力、炉缸径、炉缸壁厚度等参数,综合考虑炉缸结构形式、炉壳后侧结构、炉壳的过热程度和炉壳与冷却壁之间的间隙等因素。
在施工中,应注意冷却壁温度、热应力、膨胀等因素。
在铸铁板冷却壁的安装中,需要保证板式活振动卡进螺杆后,牢固不松动。
铜板冷却壁的安装要注意板子的厚度,不能超过规定范围,不得出现裂纹和变形。
三、高炉冷却壁的维护为了保证高炉冷却壁的正常运行,需要进行定期维护工作。
高炉冷却壁的定期维护包括日常检查、防止渗漏、补救维修等。
具体包括:1.日常检查:对高炉冷却壁内的冷却水、冷却水量和温度进行检查,以发现问题解决问题。
2.防止渗漏:定期检查铜板冷却壁的密封性,及时发现并修复问题;设计时应注意冷却水管的接头,保证不渗漏。
3.补救维修:冷却壁表面的耐火材料受到侵蚀或者受到冲击等动力作用会引起表面破损,导致外渗,此时需要用耐火材料堵漏,尽快修复,避免影响正常生产。
四、高炉冷却壁技术的发展高炉冷却壁技术的发展主要集中在两个方面:增强冷却壁散热能力和提高其使用寿命。
目前已有多种技术被应用于高炉中,如内部/外部增强冷却、强制通液、二级冷却、高温陶瓷材料等,并形成一定的规模。
高炉风口破损影响因素及处理方案研究

高炉风口破损影响因素及处理方案研究风口是高炉送风的关键部件,通过高炉风口吹入的高温热风和炉底焦炭氧化燃烧生成CO,CO在高温上升中还原出原来以氧化物形态存在的铁。
高炉风口的特点是传导性好、冷却均匀、冷却效率高、组织致密、耐磨性好等。
通常安装于腹炉与炉底之间的炉壁中。
高炉风口一般应用于钢铁、冶金、化工等行业,是金属冶炼业中重要的器具,本文主要针对高炉风口的破损的影响进行分析,并探讨有关的处理方案,做好相关的高炉风口养护工作。
标签:高炉风口;破损;影响因素;处理方案高炉的生产技术水平直接影响着整个企业的冶炼水平,而高炉的生产水平则直接受到风口的运作情况的影响。
在高炉风口破損后,高炉的生产也情况随之而受到影响,需要对高炉风口进行频繁的维修和更换,将会投入大量的维护成本,高炉的生产效益则降低了许多。
在维修保养的同时还要根据不同的高炉工况和使用及经济要求,选择正确适宜的方法。
高炉风口的结构有空腔水冷风口、双腔旋流风口、贯流式风口、双进双出风口、偏心式风口等几种,在进行探究有关高炉风口的破损因素及应对的同时,还要考虑高炉风口的材质和结构,做好全面的应对策略。
1 关于高炉风口的概况高炉风口常处在于十分恶劣的环境中,一般温度都会达到1500度以上,并且在使用过程中会有高温的铁流等物质的冲刷和磨损。
目前的高炉风口材质主要为高纯紫铜,在制造时,要从风口的轻度、刚度、抗龟裂性能等方面俩进行考虑,并且高炉风口的状态也有锻制、铜版卷制、铸造等不同的状态,工业上大多选择的是风口重量低、制造成本也较低的铜版卷制状态的高炉风口。
纯度越是高的高炉风口,其强度和刚度也越高,受损程度也随之降低。
2 高炉风口近几年的损坏情况由于高炉风口的使用环境恶劣,且会经受工业上的冶金产品、炉料、炉渣等的冲刷腐蚀,日积月累会形成严重的受损,甚至会导致高炉风口无法再继续进行使用,有关近年来高炉风口的破损情况如下表1。
从表1中可以看出,近年来高炉风口的破损情况均较为严重,受到损坏的高炉风口比例一直高居不下,这与使用者对高炉风口的保养及维修有很大关系,要及时对高炉风口的破损原因进行针对性的排查和应对,做好有效的高炉风口维护工作,才能在提高成产技术的同时,减少成本增长经济效益。
高炉冷却壁漏水情况分析及处理方法

高炉冷却壁漏水情况分析及处理方法摘要:冷却壁作为高炉本体冷却设备中最重要的一个组成部分,其起着隔绝炉内高温保护炉壳、合理的挂渣保持正确的操作炉型等关键性作用。
高炉冷却壁在高炉生产中由于使用年限等诸多原因,不可避免的会出现磨损、烧损等情况,导致冷却壁内冷却水管(水道)破损,发生冷却水漏入炉内的情况,进而引起局部炉缸不活、堆积、炉凉甚至炉缸结死,对高炉的安全生产、稳定顺行产生极为不利的影响,因此如何快速有效的处理冷却壁漏水在高炉生产过程中意义重大。
关键词:冷却壁;破损;漏水;有效处理1、高炉冷却壁的分类按照材质分类,目前高炉使用的冷却壁大致可分为:铸钢冷却壁、铸铁冷却壁、铜冷却壁,铸钢、铸铁冷却壁多使用埋管铸造的方式,即冷却水管弯曲成型后铸造在冷却壁内部,而铜冷却壁由于制造工艺的不同(多采用轧制的方式成型),其壁体内一般不进行埋管而是采用钻孔形成冷却水水道的方式。
2、冷却壁漏水情况分析2.1磨损冷却壁磨损表现为冷却壁整体厚度减薄直至冷却水管、水道穿漏,高炉内部由于炉料的不断下行冲刷、高温气流的上行冲刷,特别是冷却壁热面渣皮形成不稳的情况下,加上冷却壁使用年限不断增加就容易造成冷却壁磨损的情况发生。
冷却壁磨损往往都是整段或者呈区域出现,单根漏水量大,且漏水情况一旦出现则预示着大面积漏水的可能性存在,后续处理起来十分困难。
2.2烧损冷却壁烧损表现为冷却壁局部或者局部几块冷却壁因为路况失常、炉缸堆积、渣铁流动性差、冷却强度不足等因素影响导致冷却壁局部烧损烧穿冷却水管或水道,烧损情况一般不会导致大面积漏水的可能。
烧损导致的漏水量视烧损面积以及烧损的部位大小不确定。
2.3冷却水管拉裂冷却壁水管拉裂是因为冷却壁安装固定在炉壳上,冷却水管管头伸出炉外进行外部配管,随着高炉生产进行,炉壳受热发生形变,炉壳与冷却壁管头产生垂直或径向位移导致冷却壁水管拉裂。
拉裂的情况不可避免,但一般不会大面积出现。
拉裂导致的漏水量一般不会太大。
高炉铜冷却壁破损的原因分析与防治

高炉铜冷却壁破损的原因分析与防治高炉铜冷却壁是高炉的重要组件之一,其主要作用是冷却高炉内的铁水和渣,并维护高炉内的温度。
然而,在高炉冶炼生产中,铜冷却壁常常会出现破损的情况,这不仅会影响高炉的冶炼效率,还会给生产带来较大的安全隐患。
本文将针对高炉铜冷却壁破损的原因进行分析,并提出预防措施。
1、原材料含硫高铜冷却壁在工作时不可避免地与含有大量的硫的铁水接触,如果铁水中的硫含量过高,就会对铜冷却壁造成腐蚀作用,导致冷却壁破损。
2、冷却水温度过高冷却水的温度过高会导致铜冷却壁的热胀冷缩程度过大,使铜冷却壁出现破裂。
3、冷却水质量差如果冷却水中含有较多的杂质和氧化铁,这些物质会对铜冷却壁造成腐蚀和侵蚀,导致冷却壁出现破损。
此外,如果冷却水的pH值过低或过高,也会加速铜冷却壁的腐蚀速度。
4、炉壳开裂如果高炉炉壳出现开裂,铜冷却壁就会失去支撑,而且在铜冷却壁中流淌的铁水和渣会在壁面上挤压形成冷却堵塞,最终导致铜冷却壁破裂。
5、高炉操作失误高炉操作失误也是导致铜冷却壁破损的因素之一。
例如,如果高炉进料速度过快,铜冷却壁就会承受更大的热负荷,从而加速破损;又如,如果高炉倒铁流程不当,可能会使铁水喷到铜冷却壁上,造成局部过热,从而导致破损。
1、优化原料配比优化原料配比,降低铁水中的硫含量,可以有效地减轻铜冷却壁的腐蚀程度,延长其使用寿命。
严格控制冷却水的温度,避免铜冷却壁出现热胀冷缩现象,进而减少破损的风险。
改进冷却水的配制方法和合理选用防腐材料,可以有效地减少冷却水中的杂质和氧化铁,降低冷却水的pH值,减缓铜冷却壁的腐蚀速度。
4、定期检查高炉定期检查高炉内部情况,及时发现高炉炉壳的开裂情况,并采取相应措施加以修复,以减少破损的风险。
5、加强生产管理加强高炉生产管理,避免操作失误,定期对高炉运行情况进行监测和分析,发现异常情况及时处理,防止铜冷却壁破损。
三、结论高炉铜冷却壁是高炉冶炼生产中的重要组件之一,其破损会给高炉带来严重影响,因此需要我们采取一系列防治措施,从而延长铜冷却壁的使用寿命,保证高炉的运行稳定和生产效率。
高炉冷却壁破损原因及采取的措施
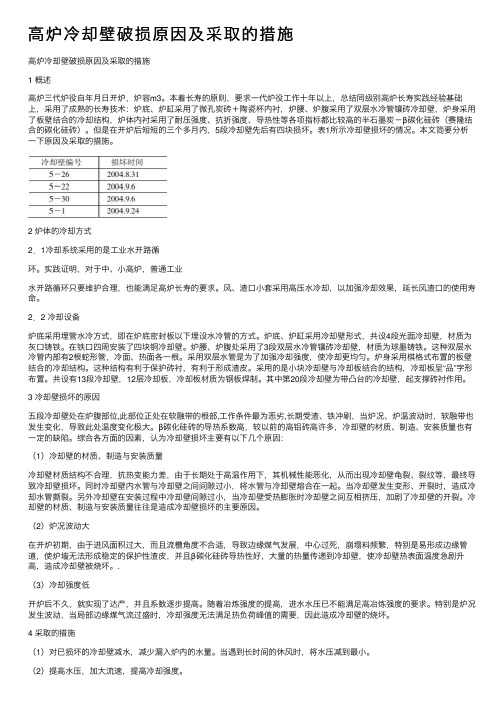
⾼炉冷却壁破损原因及采取的措施⾼炉冷却壁破损原因及采取的措施1 概述⾼炉三代炉役⾃年⽉⽇开炉,炉容m3。
本着长寿的原则,要求⼀代炉役⼯作⼗年以上,总结同级别⾼炉长寿实践经验基础上,采⽤了成熟的长寿技术:炉底、炉缸采⽤了微孔炭砖+陶瓷杯内衬,炉腰、炉腹采⽤了双层⽔冷管镶砖冷却壁,炉⾝采⽤了板壁结合的冷却结构,炉体内衬采⽤了耐压强度、抗折强度、导热性等各项指标都⽐较⾼的半⽯墨炭-β碳化硅砖(赛隆结合的碳化硅砖)。
但是在开炉后短短的三个多⽉内,5段冷却壁先后有四块损坏。
表1所⽰冷却壁损坏的情况。
本⽂简要分析⼀下原因及采取的措施。
2 炉体的冷却⽅式2.1冷却系统采⽤的是⼯业⽔开路循环。
实践证明,对于中、⼩⾼炉,普通⼯业⽔开路循环只要维护合理,也能满⾜⾼炉长寿的要求。
风、渣⼝⼩套采⽤⾼压⽔冷却,以加强冷却效果,延长风渣⼝的使⽤寿命。
2.2 冷却设备炉底采⽤埋管⽔冷⽅式,即在炉底密封板以下埋设⽔冷管的⽅式。
炉底、炉缸采⽤冷却壁形式,共设4段光⾯冷却壁,材质为灰⼝铸铁。
在铁⼝四周安装了四块铜冷却壁。
炉腰、炉腹处采⽤了3段双层⽔冷管镶砖冷却壁,材质为球墨铸铁。
这种双层⽔冷管内部有2根蛇形管,冷⾯、热⾯各⼀根。
采⽤双层⽔管是为了加强冷却强度,使冷却更均匀。
炉⾝采⽤棋格式布置的板壁结合的冷却结构。
这种结构有利于保护砖衬,有利于形成渣⽪。
采⽤的是⼩块冷却壁与冷却板结合的结构,冷却板呈“品”字形布置。
共设有13段冷却壁,12层冷却板,冷却板材质为钢板焊制。
其中第20段冷却壁为带凸台的冷却壁,起⽀撑砖衬作⽤。
3 冷却壁损坏的原因五段冷却壁处在炉腹部位,此部位正处在软融带的根部,⼯作条件最为恶劣,长期受渣、铁冲刷,当炉况、炉温波动时,软融带也发⽣变化,导致此处温度变化极⼤。
β碳化硅砖的导热系数⾼,较以前的⾼铝砖⾼许多,冷却壁的材质、制造、安装质量也有⼀定的缺陷。
综合各⽅⾯的因素,认为冷却壁损坏主要有以下⼏个原因:(1)冷却壁的材质、制造与安装质量冷却壁材质结构不合理,抗热变能⼒差,由于长期处于⾼温作⽤下,其机械性能恶化,从⽽出现冷却壁龟裂、裂纹等,最终导致冷却壁损坏。
邯钢8号高炉风口带冷却壁破损原因及对策

收 稿 日期 :0 2— 1 0 21 0 — 5
作者简介 : 郭先粜( 9 9一) 男,0 8年毕 业于北京科技大学 冶金 工程 专业 , 17 , 20 助理 工程 师.
38
南 方 金 属 S U HE N M T L 0 T R E AS
21 02年第 5期
L型铜冷 却壁 加 喷 涂料 结 构 , 依 炉 腹 角 大 小 确 定 可 推 向炉 内的深度 , 现 与 风 口带 冷 却设 施 的较 好 衔 实
Ke r s l s f r a e u e e b e ;c o i g w l a g y wo d :b u t u n c ;t y r lt o l a ;d ma e;p e a so s n l r c 集 团邯郸 钢 铁 集 团有 限责 任 公 司 ( 以 下 简称 “ 钢 ” 8号高 炉 有 效容 积 为 30 采用 邯 ) 20i , n 全冷 却 壁炉 体结 构 . 底 炉 缸 采 取 5段 光 面低 铬 铸 炉 铁冷 却 壁 , 炉腹 、 腰 、 身 下 采 用 4段 铜 冷却 壁 薄 炉 炉 壁 内衬 , 冷却 壁 热 面 喷涂 料 喷涂 , 底 、 缸采 用 铜 炉 炉 碳砖 、 陶瓷杯 与 风 口组 合 砖 综合 结构 , 设计 炉 型接 近
在使 用铜 冷 却壁 的高 炉 , 于炉 腹 的铜 冷 却 壁 由 和炉 缸铸 铁 冷却 壁厚 度 相 差 太 多 , 处 的 过 渡 一 直 此 是高 炉 设计 的一 个难 题 , 高 炉 创 新地 在 炉 腹 使用 本
解 和此设计 类 似 的安钢 、 钢与 武 钢 高炉 , 口带 冷 济 风
G O Xa — e , A GZ a-a,L h-e U i s n Y N h nhi I ii nh S j ( n a r n te C .Ld , a dn0 6 1 ,H bi HadnI nadSel o t. H na 50 5 ee) o
高炉铜冷却壁破损的原因分析与防治
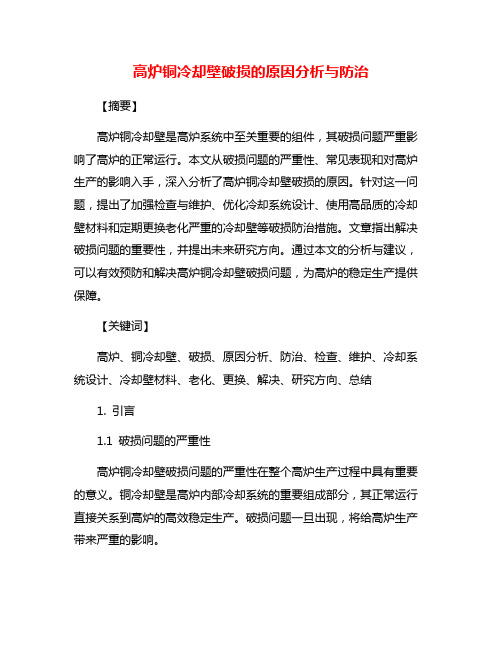
高炉铜冷却壁破损的原因分析与防治【摘要】高炉铜冷却壁是高炉系统中至关重要的组件,其破损问题严重影响了高炉的正常运行。
本文从破损问题的严重性、常见表现和对高炉生产的影响入手,深入分析了高炉铜冷却壁破损的原因。
针对这一问题,提出了加强检查与维护、优化冷却系统设计、使用高品质的冷却壁材料和定期更换老化严重的冷却壁等破损防治措施。
文章指出解决破损问题的重要性,并提出未来研究方向。
通过本文的分析与建议,可以有效预防和解决高炉铜冷却壁破损问题,为高炉的稳定生产提供保障。
【关键词】高炉、铜冷却壁、破损、原因分析、防治、检查、维护、冷却系统设计、冷却壁材料、老化、更换、解决、研究方向、总结1. 引言1.1 破损问题的严重性高炉铜冷却壁破损问题的严重性在整个高炉生产过程中具有重要的意义。
铜冷却壁是高炉内部冷却系统的重要组成部分,其正常运行直接关系到高炉的高效稳定生产。
破损问题一旦出现,将给高炉生产带来严重的影响。
铜冷却壁的破损会导致冷却效果下降,影响高炉内部温度的控制。
高炉内部温度过高会影响炉料的熔化和还原反应的进行,从而降低高炉的生产效率。
破损的铜冷却壁会导致高炉内部的冷却水泄漏,增加了维修和换装的成本,同时也会增加高炉停机的次数,影响生产的连续性和稳定性。
高炉铜冷却壁破损问题的严重性不仅表现在生产效率和成本上的影响,更属性于对整个高炉生产过程的稳定性和安全性的影响。
及时有效地对破损问题进行分析和防治显得尤为重要。
1.2 破损现象的常见表现高炉铜冷却壁破损的常见表现主要包括以下几点:首先是表面腐蚀和磨损,这是由于高炉操作过程中铜冷却壁受到高温、腐蚀性气体和熔融铁水的长期作用所导致的。
其次是冷却壁出现裂缝和断裂,这可能是由于冷却壁材料内部的应力超过承受能力造成的,也有可能是因为设计不合理或者使用寿命已过导致的。
另外还有冷却壁变形和变色的情况,这可能是由于冷却系统设计不当或者冷却水质量问题所引起的。
破损导致的冷却效果下降也是常见表现之一,这会影响高炉的正常运行和生产效率。
延长7号高炉冷却壁使用寿命生产实践

延 长 7号 高炉 冷 却 壁 使 用寿 命 生产 实践
莫云 星 , 陈建 华 , 曾庆 球 , 孙武 全
( 新余钢铁集 团有 限公 司 , 江西 新余 3 3 8 0 0 1 )
摘
要: 根据新钢 7 号高炉炉型设计采用的砖壁合一薄壁炉衬设计特点和不足, 结合新钢高炉生产实际, 在各层
出水包加装 了旋 塞阀 , 实现 了冷却强度 的灵 活控制 。同时 , 通 过采取 优化 高炉操 作 , 维护 好合理 的操 作炉 型和在 线砂 洗等措 施, 7号高 炉冷却 壁寿命 明显延 长。
关 键 词 : 高炉冷却; 薄壁炉衬; 砂洗 ; 高炉操作
中 图分 类 号 : T F 3 2 1 . 4
1 前 言
新 钢 7号 高 炉 于 2 0 0 4年 8月 3 1 日大 修 投 产, 至 今 已安 全 运 行 9年 零 1个 月 。 高 炉 炉 腹 及
2 影响 7号高炉冷却壁 寿命 的主要因素
2 . 1 高炉 冷却 系统设计 特 点
2 . 1 . 1 冷 却 系统基 本情 况 新 钢 7号 高炉 采用 了炉 腹及 以上 部 位 均为 镶砖
以上部分 为镶砖 冷却 壁 的砖 壁 合一 薄炉 衬设 计 , 工业水循 环冷却 , 高 温 区未设铜 冷 却壁 。高炉 大
修 投 产 9年 以 来 , 克 服 了原燃 料 质 量差 , 入 炉 有 害元素高 , 炉 况顺 行 较 差 和 渣 皮 频 繁 脱 落 等 不 利
冷却壁的砖壁合一薄炉衬设计 , 高炉采用全冷却壁 结构 , 共设 1 5段 5 5 0块 冷却 壁 , 各 段 冷 却 壁 根 据 其
第3 4卷第 1 期
2 0 1 4 年 2 月
高炉铜冷却壁破损的原因分析与防治

高炉铜冷却壁破损的原因分析与防治高炉铜冷却壁是高炉内部的关键设备,用于冷却高温高炉炉壁和延长高炉的使用寿命。
由于高炉工作环境的恶劣以及高炉操作不当,铜冷却壁往往容易发生破损。
本文将分析造成高炉铜冷却壁破损的原因,并提出相应的防治措施。
造成高炉铜冷却壁破损的原因主要有以下几点:高炉工作环境的高温和高压容易导致铜冷却壁的热应力过大,从而引发裂纹和破损。
高炉内部温度可达到1500℃以上,冷却壁长时间暴露在高温下,无法承受强大的热应力,随着时间的推移,冷却壁逐渐产生裂纹,最终导致破损。
高炉操作不当也是导致铜冷却壁破损的重要原因。
如果高炉操作不规范,比如控制不准确的喷吹速率、不合理的风口位置和进料方式等,都会导致炉内温度和压力的不稳定,进而给冷却壁带来冲击和振动,从而增加了冷却壁出现破损的风险。
渣铁质量的不稳定也会对铜冷却壁造成损害。
高炉冶炼过程中,渣铁质量的不稳定性会导致冷却壁受到腐蚀和侵蚀,从而削弱冷却壁的强度和耐用性。
特别是高硅、高硫和高镁渣铁,对冷却壁的损害更为严重。
高炉运行的振动和冲击也是导致铜冷却壁破损的一个重要原因。
高炉操作过程中产生的振动和冲击会对铜冷却壁产生较大的压力,长时间下来会导致冷却壁的疲劳破裂,从而造成冷却壁的破损。
加强高炉操作规范性。
操作人员需要进行严格的培训,熟悉高炉操作规程,确保操作准确无误。
特别是要关注冷却壁的温度、压力和震动情况,并采取相应的措施进行调整和修复,保持冷却壁的良好工作状态。
优化高炉冶炼工艺。
对于渣铁质量的不稳定性,可以通过在炉内加入稳定剂和改变冶炼工艺,并对渣铁进行预处理,降低对冷却壁的腐蚀和侵蚀。
对于长期高温和高压环境下的铜冷却壁,可以采取增强材料的方式。
使用具有较好耐高温特性的高硅铜材料,或者在冷却壁表面喷涂耐磨涂层,提高冷却壁的耐用性和抗腐蚀能力。
定期检查和维护冷却壁。
定期对冷却壁进行检查,及时发现和修复裂纹和破损部位,确保冷却壁的正常工作。
还可以定期对冷却壁进行清洗和防腐处理,延长冷却壁的使用寿命。
涟钢七高炉强化与长寿
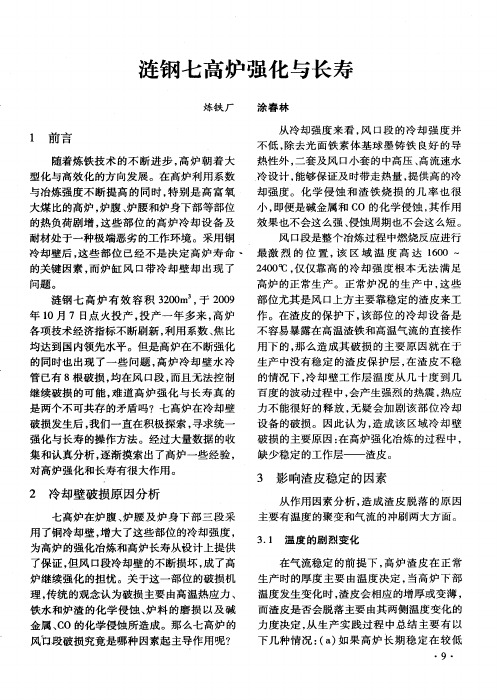
大煤 比的高 炉 , 腹 、 炉 炉腰 和炉 身下 部 等部 位 的热 负荷 剧增 , 些 部 位 的 高 炉冷 却 设 备 及 这
耐材 处 于一种 极端 恶 劣 的工 作 环境 。采用铜
冷却 壁后 , 些 部 位 已经 不是 决 定 高 炉 寿命 、 最 激 烈 的 位 置 , 区 域 温 度 高 达 10 ~ 这 该 60
.
理 , 统 的观 念认 为破 损 主要 由高温 热应 力 、 传
铁水 和炉 渣 的化 学 侵 蚀 、 炉料 的磨 损 以及 碱
金属 、O 的化 学 侵蚀 所造 成 。那 么七高 炉 的 C 风臼: 损究 竟是 哪种 因素起 主导作 用 呢? 段破
9 .
的炉 温水平 , 渣皮会 相应 的增 厚 , 在提高 炉温 的过程 中 , 如果 遇到 温度急剧 升高 , 尤其 当遇 到净焦 时 , 皮一般 就会脱 落 , 渣 这种 情况 主要
了保证 , 风 口段冷 却 壁 的不断 损坏 , 了高 但 成
炉继 续强 化 的担忧 。关 于这 正 常 高
生 产时 的厚 度 主 要 由温度 决 定 , 当高 炉 下 部 温 度发 生变 化 时 , 皮会相 应 的增厚 或 变薄 , 渣 而 渣皮 是 否会脱 落 主要 由其两 侧温 度变 化 的 力 度决 定 , 生产 实 践 过 程 中 总结 主要 有 以 从 下 几种 情 况 : a 如果 高炉 长期 稳 定 在 较 低 ()
主 要有 温度 的聚 变 和气 流 的 冲刷 两大 方 面 。
3 1 温 度 的剧 烈变化 .
2 冷却壁破损原 因分析
七 高 炉在 炉腹 、 腰 及 炉 身 下 部 三 段 采 炉
榆钢高炉护炉实践

差整体呈下降趋势 , 热流强度基本稳定实现受控 , 高炉护炉达到安全运行 的 目的。
关键词 : 高炉 ; 炉体状况 ; 护炉
中 图分 类 号 :F 7 . T 56 7 文 献 标识 码 : A
1 引 言
榆钢 1 、样 撑2 高炉容积为 4 0m , 2 。分别于 20 年 04
目前 炉缸 也 有 较 为 严 重 的 侵 蚀 现象 , 段 6 、 二 #
2 #2# 4 、5 冷却 壁水 温 差 相 对 较 高 ,4 已改 为 管道 泵 2#
1 3
图 1 榆 钢 高 炉 炉 底 、 缸 结 构 图 炉
第 二 段配 置 24 2m 长度 的冷却 壁 , 9 m 在此 高炉 炉 缸安 全运 行 的 “ 害 ” 位 设 置超 长 的 冷却 壁 , 要 部 对
m h最 高是 3段 1 , 流强度 2 2 Jm h , 组 热 128k/ 。・ ( 见表 3 。 ) 目前炉 缸存 在 不 同 程 度 的侵 蚀 , 部水 温差 时 局 有 波动 , 二段 1# 1# 1 # 却 壁 水 温 差相 对 较 高 , 3 、4 、5 冷 1# 1# 3 、5 已改 为管 道 泵 强 制 冷却 ,4 改 为高 压 水 冷 1# 却, 目前冷却 壁 热 流 强 度 分 别 为 3 6 Jm h 799k/ 、
乐观 。
表 2 2 高炉 炉 体 冷 却 壁 破 损 分布 情 况 样
高 炉冷 却 壁 破 损 的主 要 原 因是 炉 况 稳 定 性 不
层粘 土保 护砖 。
好, 滑尺、 崩料频繁 , 煤气利用率不高 , 并且受钟式炉 顶 限制 , 气 流分 布 不稳 定 , 缘气 流 比较 旺盛 , 煤 边 冷
( 酒钢集 团公司 榆钢公司炼铁分厂 , 甘肃 榆中 70 0 ) 3 0 0
高炉风口大量破损原因分析
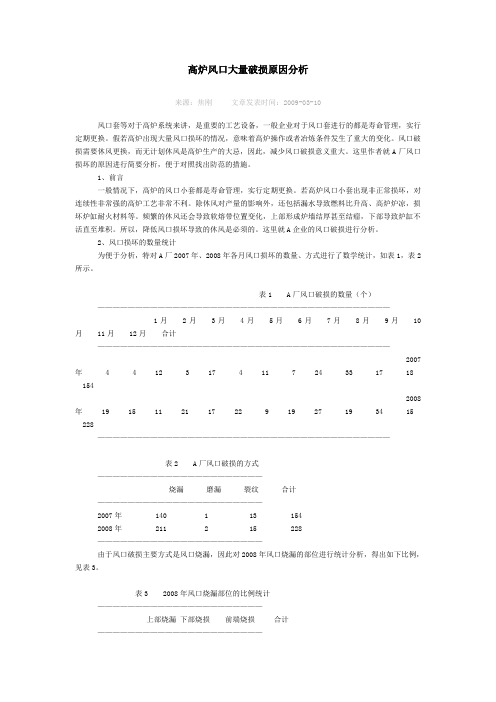
高炉风口大量破损原因分析来源:焦刚文章发表时间:2009-03-10风口套等对于高炉系统来讲,是重要的工艺设备,一般企业对于风口套进行的都是寿命管理,实行定期更换。
假若高炉出现大量风口损坏的情况,意味着高炉操作或者冶炼条件发生了重大的变化。
风口破损需要休风更换,而无计划休风是高炉生产的大忌,因此,减少风口破损意义重大。
这里作者就A厂风口损坏的原因进行简要分析,便于对照找出防范的措施。
1、前言一般情况下,高炉的风口小套都是寿命管理,实行定期更换。
若高炉风口小套出现非正常损坏,对连续性非常强的高炉工艺非常不利。
除休风对产量的影响外,还包括漏水导致燃料比升高、高炉炉凉,损坏炉缸耐火材料等。
频繁的休风还会导致软熔带位置变化,上部形成炉墙结厚甚至结瘤,下部导致炉缸不活直至堆积。
所以,降低风口损坏导致的休风是必须的。
这里就A企业的风口破损进行分析。
2、风口损坏的数量统计为便于分析,特对A厂2007年、2008年各月风口损坏的数量、方式进行了数学统计,如表1,表2所示。
表1 A厂风口破损的数量(个)———————————————————————————————————————1月2月3月4月5月6月7月8月9月10月11月12月合计———————————————————————————————————————2007年 4 4 12 3 17 4 11 7 24 33 17 18 1542008年19 15 11 21 17 22 9 19 27 19 34 15 228———————————————————————————————————————表2 A厂风口破损的方式——————————————————————烧漏磨漏裂纹合计——————————————————————2007年140 1 13 1542008年211 2 15 228——————————————————————由于风口破损主要方式是风口烧漏,因此对2008年风口烧漏的部位进行统计分析,得出如下比例,见表3。
高炉冷却壁维护技术

高炉冷却壁维护技术
随着高炉的冶炼强度的不断提高,高炉的冷却壁频繁破坏,影响生产,分析认为高炉冷却壁破坏原因主要有:
1)冷却壁结构不合理。
冷却壁属于大断面尺寸铸件,铸造时内外凝固冷却不一致,存在较大的残余应力。
冷却壁的表面和中心的热延伸率不同,冷热差过大,会产生裂纹。
2)冷却壁材质问题。
浇铸球墨铸铁冷却壁,球化不彻底时,连续的石墨存在,成为高炉煤气进入金属内部的通道,导致氧化反应。
造成冷却壁损坏。
3)高炉钢壳焊接质量差。
炉皮与螺栓垫板及冷却壁水管建的焊缝,存在裂纹、气泡等获变形开裂,会引起煤气串动,是冷却壁损坏。
4)冷却强度不够。
冷却水管表面积与冷却壁表面积之比过小,达不到高炉的冷却要求,会造成冷却壁破损。
5)进水温度高。
进水温度决定炉墙渣皮厚度及能否快速形成保护性渣皮,会影响冷却壁。
6)高炉冶炼。
由于冶炼强度及富氧燃烧,对冷却壁的要求提高;高炉冶炼的强化需要边缘气流,而边缘气流过度发展,容易引起渣皮过薄,导致冷却壁局部过热;炉况顺行度差时,容易造成渣皮不稳且脱落;炉内温度波动大,温度超过800℃,冷却壁材质容易氧化和塑性形变,应稳定炉况;热洗炉时,可以洗去炉墙的结厚和防止边缘气流不稳定,当回造成炉内冷却壁热负荷过高,烧损炉体;风口套和装料制度不当时,不能将燃烧区推向炉缸中心,只是高炉边缘过度发展,冷却壁温度升高,侵蚀冷却壁,造成冷却壁早损。
国内韶钢对1-2#、4-5#高炉冷却壁出现裂纹用气刨开后填焊,在烧损冷却壁部位增设铜冷却棒,更换炉壳、灌浆造衬等操作,维护了高炉的安全生产,并把高炉冶炼因素作为主要原因,用于日常高炉冷却壁的破坏防止,取得了较好的效果。
- 1、下载文档前请自行甄别文档内容的完整性,平台不提供额外的编辑、内容补充、找答案等附加服务。
- 2、"仅部分预览"的文档,不可在线预览部分如存在完整性等问题,可反馈申请退款(可完整预览的文档不适用该条件!)。
- 3、如文档侵犯您的权益,请联系客服反馈,我们会尽快为您处理(人工客服工作时间:9:00-18:30)。
摘要立足8年炉龄的中天钢铁7号高炉,采取一定长寿技术和管理措施,对中天钢铁7号高炉炉役后期在强化冶炼与高炉长寿方面所做的工作进行了总结分析,通过采用精料、加钛矿护炉、优化操作制度以及合理维护等操作技术措施,7号高炉在炉役后期实现了稳定顺行生产,延长了高炉寿命,单位炉容产铁量超过10000 t/m3,各项技术经济指标不断改善。
关键词高炉长寿炉役后期中天钢铁7号高炉始建于2011年,于12月16日顺利开炉,容积850m3,20个风口送风,炉前东西场两边各一铁口,炉缸使用的是北京瑞尔非金属材料有限公司提供的大块单元式风口组合砖,整体式陶瓷杯壁(带密闭隔热夹层),双向错台的陶瓷杯垫砖,见图1。
上料系统采用斜桥小车上料,无料钟旋转溜槽多环布料;炉前东西出铁场均采用摆动沟罐位,冲渣系统采用环保底滤法,保证高炉出尽渣铁;高炉本体冷却采用工业水开路循环;鼓风机AV50—14,热风炉为顶然式,送风采用两烧一送原则。
截止2020年2月份已连续正常生产八年多时间,期间无特殊炉况发生,通过操作维护和加强炉体监护工作高炉投产八年来无冷却壁烧损,打破了高炉炼铁生产过程中发生冷却壁烧损的历史,创造了“中天骄傲”。
高炉利用系数已达3.8t/(m3·d)以上,燃料比520kg/t以下。
截止目前,7号高炉在一代炉龄无大、中修情况下单位炉容产铁量突破1.06万吨,参照目前高炉长寿标准,7号高炉已经成功跨入世界钢铁企业长寿高炉行列,并且在全国同等立级高炉中多项技术经济指标名列前茅,尽管已处于炉役后期,仍然保持着稳定高产的生产状态。
其中多年来主要经济指标如表1所示。
由表中可以看出7号高炉各项指标在稳定不断进步。
2020年因新型冠状肺炎疫情的影响,公司决定7号高炉2月3日降料面停炉,为后续开炉快速达产于3月5日开始炉内扒料,通过测量观察风口以上冷却壁镶砖基本还保留,炉缸除了东西铁口橡角区侵蚀到碳砖表面,其它侧壁区域陶瓷杯完整存在,见图2。
停炉时风口组合砖状况至停炉时所有风口无变形,上翘现象;停炉时陶瓷杯壁砖的状况铁口中心线以上位置,陶瓷杯壁砖侵蚀最大位置,剩余杯壁厚度200mm,包括铁口上方的二层陶瓷杯壁砖。
停炉时陶瓷杯垫状的状况由于停炉前高炉运行良好,高炉本体各处温度平稳,按照熔损计算,炉底陶瓷杯垫砖侵蚀度低,因此本次停炉后不准备对炉缸底部进行处理,辩证的说明高炉炉缸没有安全隐患,高炉还可延续生产。
1 操作制度1.1 送风制度风量:2200-2350m3/min,风温:1180-1200℃之间,压力:330-335kPa,顶压:185-190kPa;富氧率:3.4-5.5%左右,毛煤比:175-185kg/t之间,其中煤粉挥发份控制在19±1.5%;风口小套按长度可分470mm和500mm两种,斜度上可分为直风口和斜5°风口,正常情况下使用斜5°风口。
1.2 布料制度正常生产料批分为29.2t和35.5t,即矿石分为两车制和三车制;正常料线1.5m,布料采取正角度。
7号高炉炉料结构为当前国内主流形式:烧结矿+球团矿+块矿,正常生产烧结矿比例波动在65-75%之间,球团和块矿波动范围在10-20%之间,熟料率≥80%。
1.3 造渣制度炉渣二元碱度控制在1.13±0.5,因渣中铝含量较高,最高时在19-20%之间,为确保渣铁流动性二元碱度按下限控制,同时添加蛇纹石保证炉渣中镁铝比在60±5%。
1.4 热制度正常生产时,[Si]:0.28~0.35%,上下两炉间的波动两<0.1%,[S]:0.02~0.04%,铁水物理热≥1480℃,原燃料好的时候,可以控制在中下限,原燃料差的时候维持在中上限,确保炉缸的活跃性。
2 生产过程控制2.1 合理的布料制度7号高炉煤气流控制主要以中心气流为主边缘III煤气流适中分布模式,下部通过调整、优化风口进风面积和改变小套长度来适应原燃料质量的变化,保证气流顺畅,高炉中心气流明显,边缘气流适中,此种情况下煤气利用率较高,均值在47%左右。
由7号高炉2015年以来布料制度调整可以看出(见表2),为适应不同冶炼强度,需要不同煤气流分布形式与之相适应。
7号高炉实践证明,在当前原燃料水平条件下,能以发展中心气流为主,适度调整边缘气流,以提高高炉的使用寿命,实现高冶炼强度下的生产。
2.2 适宜的热制度高炉生产需要长期稳定顺行,而炉缸活性犹如高炉的心脏一般,维护着高炉生产的动态平衡,而炉缸内液态渣铁流入并流出的顺畅程度是表示炉缸活性的重要内容。
从生产角度出发,影响炉缸活性的因素大致有三个:(1)焦炭所提供“透气-透液通道”的数量;(2)渣铁流动性能;(3)风口回旋区的位置。
连接炉缸活性和热制度的纽带就是渣铁流动性能。
良好的炉缸活性状态需要有良好的渣铁流动性能,而良好的炉渣流动性能需要合理稳定的热制度,而合理稳定的热制度则是高炉操作者日常工作的主要内容[1]。
2.2.1 中钢7号高炉热制度的控制所谓热制度的控制,也就是对炉温的控制,即对铁水物理热和化学热的把握。
从生产角度出发,制定相应的最低值、波动值和绝对值。
其中最低值是保证高炉正常生产的底线,一般不允许出现比最低值还低的情况。
而波动值的确定要综合考虑原燃料情况、设备状态、操作水平等因素的影响。
总的来说,原燃料条件好,波动值应控制较小范围,原燃料条件差,波动值需要控制较大范围。
同样,波动值范围小,说明高炉生产炉况稳定;波动值范围大,表明炉况顺行情况不理想。
绝对值则是高炉正常生产需要保持的状态,取决于最低值和波动值。
若高炉接受的铁水物理热最低值为1480℃,波动值为20℃,那绝对值应为1500℃。
具体到高炉操作,那么控制炉温的方法应有以下三个操作要点:(1)负荷是稳定炉温的基础;(2)料速是检测炉温的标准;(3)燃料比是控制炉温的手段。
2.2.2 低硅冶炼推动高炉进行低硅冶炼可以有效地降低高炉的燃料消耗。
高炉炉温控制是根据高炉自身炉容、运行条件决定,在此基础上确定铁水物理热水平,在确保炉缸热充沛的情况下,高炉可以通过降低铁水硅含量,达到降低燃料消耗的目的。
由于高炉炉缸热储备充足,加之高顶压、高风温等条件,本身就适合于高炉进行低硅冶炼,近年来850m3高炉低硅冶炼施行情况见图3。
2.1 合理的布料制度7号高炉煤气流控制主要以中心气流为主边缘III煤气流适中分布模式,下部通过调整、优化风口进风面积和改变小套长度来适应原燃料质量的变化,保证气流顺畅,高炉中心气流明显,边缘气流适中,此种情况下煤气利用率较高,均值在47%左右。
由7号高炉2015年以来布料制度调整可以看出(见表2),为适应不同冶炼强度,需要不同煤气流分布形式与之相适应。
7号高炉实践证明,在当前原燃料水平条件下,能以发展中心气流为主,适度调整边缘气流,以提高高炉的使用寿命,实现高冶炼强度下的生产。
2.2 适宜的热制度高炉生产需要长期稳定顺行,而炉缸活性犹如高炉的心脏一般,维护着高炉生产的动态平衡,而炉缸内液态渣铁流入并流出的顺畅程度是表示炉缸活性的重要内容。
从生产角度出发,影响炉缸活性的因素大致有三个:(1)焦炭所提供“透气-透液通道”的数量;(2)渣铁流动性能;(3)风口回旋区的位置。
连接炉缸活性和热制度的纽带就是渣铁流动性能。
良好的炉缸活性状态需要有良好的渣铁流动性能,而良好的炉渣流动性能需要合理稳定的热制度,而合理稳定的热制度则是高炉操作者日常工作的主要内容[1]。
2.2.1 中钢7号高炉热制度的控制所谓热制度的控制,也就是对炉温的控制,即对铁水物理热和化学热的把握。
从生产角度出发,制定相应的最低值、波动值和绝对值。
其中最低值是保证高炉正常生产的底线,一般不允许出现比最低值还低的情况。
而波动值的确定要综合考虑原燃料情况、设备状态、操作水平等因素的影响。
总的来说,原燃料条件好,波动值应控制较小范围,原燃料条件差,波动值需要控制较大范围。
同样,波动值范围小,说明高炉生产炉况稳定;波动值范围大,表明炉况顺行情况不理想。
绝对值则是高炉正常生产需要保持的状态,取决于最低值和波动值。
若高炉接受的铁水物理热最低值为1480℃,波动值为20℃,那绝对值应为1500℃。
具体到高炉操作,那么控制炉温的方法应有以下三个操作要点:(1)负荷是稳定炉温的基础;(2)料速是检测炉温的标准;(3)燃料比是控制炉温的手段。
2.2.2 低硅冶炼推动高炉进行低硅冶炼可以有效地降低高炉的燃料消耗。
高炉炉温控制是根据高炉自身炉容、运行条件决定,在此基础上确定铁水物理热水平,在确保炉缸热充沛的情况下,高炉可以通过降低铁水硅含量,达到降低燃料消耗的目的。
由于高炉炉缸热储备充足,加之高顶压、高风温等条件,本身就适合于高炉进行低硅冶炼,近年来850m3高炉低硅冶炼施行情况见图3。
2.3.2 水质控制为了减轻高炉冷却器结垢,保证冷却强度,每天对高炉软水水质进行了化验分析,严格控制软水指标,PH值必须在3%~5%,避免了经常酸洗对冷却器的侵蚀,起到了延长冷却设备寿命的作用。
2.4 炉前出铁管理根据7号高炉的生产实践,确定维持合理的铁口深度2.3~2.5m左右,这既可有效地控制出铁时间,又可满足高炉生产的主要。
随着炉龄的增加,炉底砖衬被侵蚀,实际铁水面下降,将铁口角度调整到10~11°,达到了出净渣铁和维护好铁口的目的。
2.4.1 出铁时间确定合理的出铁时间,对维护炉缸、炉底有利。
出铁时间太短,意味着铁水流速增大,铁水环流会加重对炉缸砖衬的侵蚀。
此外,出铁时间太短容易造成铁水跑大流,既不安全,也不利于铁口维护。
因此,应适当控制渣铁流速,使高炉熔渣及铁水匀速排放,保持高炉炉缸内渣铁液面相对稳定,以减小铁水环流对炉缸砖衬的侵蚀[4]。
根据7号高炉的时间,出铁时间维持在70~75min左右可保证渣铁及时排放,为炉况稳定创造条件。
调整开口机钻头直径大小直接关系着出铁时间长短,使用不同直径的钻头可控制出铁时间。
2012年以来,7号高炉所用的钻头直径有φ70mm和φ50mm二种,可根据炉况不同的铁口深度选用不同直径的钻头,以保证合适的出铁时间。
2.4.2 加强炉前作业管理高炉铁口的工作状态对炉内的稳定顺行起着至关重要的作用,保证按时出净渣铁,避免炉内憋压而影响高炉的稳定顺行,而冶炼强度的提高必然使得铁口工作压力的增加,为稳定铁口合格率,为炉况的稳定顺行创造有利条件,制定了相应的炉前作业标准,规范炉前操作,提升炉前工的操作水平,每次堵口后对设备运行状况进行点检,发现问题及时汇报,及时解决,尽可能避免因设备问题影响炉前的出铁节奏。
加强对打泥量的管理,保证铁口泥套的完整,减少跑泥导致铁口深度的波动影响出铁节奏,铁口深度维持在2.4±0.1m,根据渣铁生成量以及出铁时间选择合适的开口钻头,每次出铁时间控制在70min左右,日均出铁次数控制在15炉次左右,有利于炉缸的长寿。