机械制造工艺基础第三版周世权课后答案
机械制造工艺基础(周世权田文峰罗云华著)华中科技大学出版社课后答案第四章王建伟方飞龙
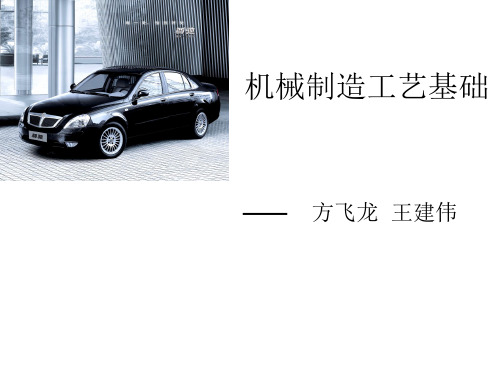
4.3.2 粗车45钢轴外圆,毛坯直径dw=86mm,粗车 后直径 dm=80mm,被加工外圆表面长度lw=50mm,切 入、切出长度l1=l2=3mm,切削用量 vc=120m/min , f=0.2mm/r,ap=3mm,试求基本工艺时间tm。
答:车削行程长度l=l1+l2+lw=50+3+3mm=56mm;
5.4.1 对7级精度的斜齿圆柱齿轮、蜗轮、扇形 齿轮、多联齿轮和内齿轮,各采用什么方法加工比 较合适?
答:斜齿圆柱齿轮采用滚齿,蜗轮采用滚齿法;扇形齿轮、多联齿 轮采用插齿法;内齿轮采用插齿法或拉齿法。
5.4.2 对齿面淬硬和齿面不淬硬的6级精度直齿圆 柱齿轮,其齿形的精加工面应采取什么方法?
答:对没有淬硬的6级精度直齿圆柱齿轮可以进行剃齿,从而达到 需要的精度。而对淬硬了的可以采用珩齿,以消除淬火后的氧化皮和 轻微磕碰而产生的齿面毛刺与压痕.
切屑是怎样形成的?常见的切屑有几种?
答:(1)金属切削过程实际就是切屑的形成过程。被切削金属层受到 刀具的挤压作用,产生弹性变形。随着切削的继续进行,刀具继续给被 切金属层施加压力,金属内部的应力和应变也随之变大;当应变达到材 料的屈服极限时,被切削金属层产生塑性变形。此时切削仍在进行, 金 属内部应力与应变继续变大,当应力达到材料断裂强度极限时,被切金 属层就会断裂而形成切屑。此时,金属内部应力迅速下降,又重新开始 弹性变形—塑性变形—断裂变形的循环,产生新的切屑。
答:平面铣刀主要有圆柱铣刀和端面铣刀两种,前者轴线平行于被加
工表面,后者轴线垂直于被加工表面。由于铣刀的刀齿都是相同的,所 以可以用一个刀齿的特点来说明整个铣刀的特点。而每个刀齿都相当于 一把车刀,因此铣刀的结构特点与车刀几乎相同。
机械制造基础第三版课后答案.doc
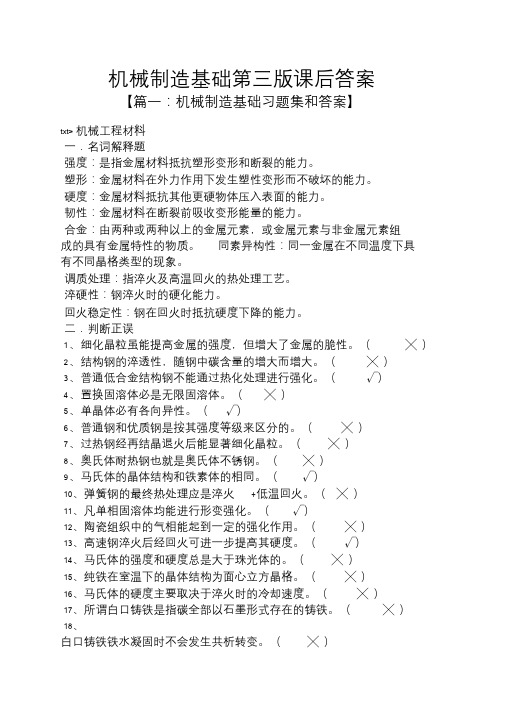
机械制造基础第三版课后答案【篇一:机械制造基础习题集和答案】txt> 机械工程材料一.名词解释题强度:是指金属材料抵抗塑形变形和断裂的能力。
塑形:金属材料在外力作用下发生塑性变形而不破坏的能力。
硬度:金属材料抵抗其他更硬物体压入表面的能力。
韧性:金属材料在断裂前吸收变形能量的能力。
合金:由两种或两种以上的金属元素,或金属元素与非金属元素组成的具有金属特性的物质。
同素异构性:同一金属在不同温度下具有不同晶格类型的现象。
调质处理:指淬火及高温回火的热处理工艺。
淬硬性:钢淬火时的硬化能力。
回火稳定性:钢在回火时抵抗硬度下降的能力。
二.判断正误1、细化晶粒虽能提高金属的强度,但增大了金属的脆性。
(╳)2、结构钢的淬透性,随钢中碳含量的增大而增大。
(╳)3、普通低合金结构钢不能通过热化处理进行强化。
(√)4、置换固溶体必是无限固溶体。
(╳)5、单晶体必有各向异性。
(√)6、普通钢和优质钢是按其强度等级来区分的。
(╳)7、过热钢经再结晶退火后能显著细化晶粒。
(╳)8、奥氏体耐热钢也就是奥氏体不锈钢。
(╳)9、马氏体的晶体结构和铁素体的相同。
(√)10、弹簧钢的最终热处理应是淬火+低温回火。
(╳)11、凡单相固溶体均能进行形变强化。
(√)12、陶瓷组织中的气相能起到一定的强化作用。
(╳)13、高速钢淬火后经回火可进一步提高其硬度。
(√)14、马氏体的强度和硬度总是大于珠光体的。
(╳)15、纯铁在室温下的晶体结构为面心立方晶格。
(╳)16、马氏体的硬度主要取决于淬火时的冷却速度。
(╳)17、所谓白口铸铁是指碳全部以石墨形式存在的铸铁。
(╳)18、白口铸铁铁水凝固时不会发生共析转变。
(╳)19、铸件可用再结晶退火细化晶粒。
(√)20、冷热加工所形成的纤维组织都能使金属出现各向异性。
(√)21、奥氏体的塑性比铁素体的高。
(√)22、白口铸铁在室温下的相组成都为铁素体和渗碳体。
(√)23、过共析钢的平衡组织中没有铁素体相。
机械制造工程原理(第三版)课后答案

第1章 金属切削基本要素习 题1-1 用母线、导线概念,试述与车削端平面相对应的平面成形原理和相应的机床加工方法。
解:成形原理:圆端平面可视为母线A 1绕导线B 2旋转而成。
如图1(a )加工方法有两种:(1) 轨迹法:作轨迹运动形成母线A 1,A 1绕导线B 2运动形成(A 1、B 2为两个独立的运动)。
如图1(b )(2) 成形法:采用宽刀刃,只需一个成形运动B 2。
如图1(c )(a ) (b ) (c )图1-1平面成形原理和相应的机床加工方法 1-3 用°=45r κ的车刀加工外圆柱面,加工前工件直径为Φ62,加工后直径为Φ54,主轴转速n = 240 r/min ,刀具的进给速度v f =96mm/min ,试计算C v 、f 、a p 、h D 、b D 、A D 。
解:3.146224046.72(/min)10001000C dn v m π××=== 96/2400.4(/)f mm r ==()/24()p w m a d d mm =−=sin 0.4sin 450.283()D r h f mm κ==×=o/sin 4/sin 45 5.657()D p r b a mm κ===o20.44 1.6()D p A f a mm =×=×=o1-5 画出下列标注角度的车床切断刀的车刀图:o 100=γ,o 60=α,o 20=′α,o 90=r κ,o 2=′r κ,o 0=s λ。
解:(参照教材P113页图3-4,第二行,第二个图)根据刀具几何参数定义,在切削刃上选定点A ,切削速度C V 矢量垂直于纸面,基面过A 点平行于纸面为r P 。
切削平面过A 点,垂直于纸面并与切削刃(粗线P 分)相切为s P ,按正交方法可得到主剖面0P 。
如图1-5图1-51-10 按照以下刀具材料、工件材料、加工条件进行相应刀具材料的合理选择刀具材料:YG3X ,YG8,YT5,YT30,W18Gr4V工件材料及切削条件:①粗铣铸铁箱体平面;②精镗铸铁箱体孔;③齿轮加工的滚齿工序;④45钢棒料的粗加工;⑤精车40Cr 工件外圆。
机械制造工艺基础(周世权田文峰罗云华著)华中科技大学出版社课后答案第三章王建伟方飞龙

3.2.11 产生焊接应力与变形的原因是什么?焊接过程中和焊 后,焊缝区纵向受力是否一样?清除和防止焊接应力有哪些 措施?
答:焊接过程的加热和冷却受到周围冷金属的约束,不能自由膨胀和收缩。当约 束很大时,则会产生残余应力,无残余变形。当约束很小时,既产生残余应 力,又产生残余变形。 采取以下措施可以防止或消除焊接应力: (1)焊接不要有密集交叉,截面和长度也要尽可能小,以减少焊接局部 加热,从而减少焊接应力。 (2)采取合理的焊接顺序,使焊缝能够自由收缩,以减少应力。 (3)采用小线能量,多层焊,也可减少焊接应力。 (4)焊前预热可以减少工件温差,也能减少残余应力。 (5)当焊缝还处于较高温度时,锤击焊缝使金属伸长,也能减少焊接残余 应力。 (6)焊后进行消除应力的退火可消除残余应力。
答:焊接接头的不完整性称为焊接缺陷,主要有焊接裂纹,未焊透,夹渣, 气孔和焊缝外观缺陷等。其中危害最大的是焊接裂缝和气孔。
3.3.5 点焊的热源是什么?为什么会有接触电阻?接触电 阻对点焊熔核的形成有什么影响?怎样控制接触电阻的 大小?
答:点焊是用圆柱电极压紧工件,通过电流流过工件产热获得焊点。 工件无为金属,金属有自身的电阻。接触电阻小时,吸热少而散热快,导 致熔核偏向电阻大的一方,形成熔核偏移。可以采用特殊电极或工艺垫片 来改变接触电阻。
图1
图2
图3
3.3.5 点焊的热源是什么?为什么会有接触电阻?接触电 阻对点焊熔核的形成有什么影响?怎样控制接触电阻的大小?
答:点焊是用圆柱电极压紧工件,通过电流流过工件产热获得焊点。工件无为金 属,金属有自身的电阻。接触电阻小时,吸热少而散热快,导致熔核偏向电 阻大的一方,形成熔核偏移。可以采用特殊电极或工艺垫片来改变接触电阻。
决定腹板与上下翼板的焊缝位置选择焊接方法画出各条焊缝接头形式并制定各条焊缝和焊接次序图356焊接工艺设计腹板与上下翼板的焊缝位置应选在腹板上的耳板与翼板交接处图中510的位置采用手弧焊焊接顺序如图中数字所示各焊缝接头形式如下
机械制造技术基础(第三版)第五章课后题答案
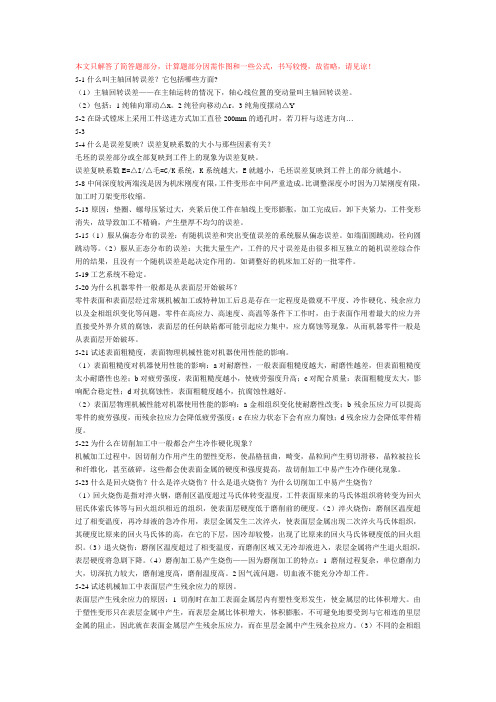
本文只解答了简答题部分,计算题部分因需作图和一些公式,书写较慢,故省略,请见谅!5-1什么叫主轴回转误差?它包括哪些方面?(1)主轴回转误差——在主轴运转的情况下,轴心线位置的变动量叫主轴回转误差。
(2)包括:1纯轴向窜动△x。
2纯径向移动△r。
3纯角度摆动△Y5-2在卧式镗床上采用工件送进方式加工直径200mm的通孔时,若刀杆与送进方向…5-35-4什么是误差复映?误差复映系数的大小与那些因素有关?毛坯的误差部分或全部复映到工件上的现象为误差复映。
误差复映系数E=△I/△毛=C/K系统,K系统越大,E就越小,毛坯误差复映到工件上的部分就越小。
5-8中间深度较两端浅是因为机床刚度有限,工件变形在中间严重造成。
比调整深度小时因为刀架刚度有限,加工时刀架变形收缩。
5-13原因:垫圈、螺母压紧过大,夹紧后使工件在轴线上变形膨胀,加工完成后,卸下夹紧力,工件变形消失,故导致加工不精确,产生壁厚不均匀的误差。
5-15(1)服从偏态分布的误差:有随机误差和突出变值误差的系统服从偏态误差。
如端面圆跳动,径向圆跳动等。
(2)服从正态分布的误差:大批大量生产,工件的尺寸误差是由很多相互独立的随机误差综合作用的结果,且没有一个随机误差是起决定作用的。
如调整好的机床加工好的一批零件。
5-19工艺系统不稳定。
5-20为什么机器零件一般都是从表面层开始破坏?零件表面和表面层经过常规机械加工或特种加工后总是存在一定程度是微观不平度、冷作硬化、残余应力以及金相组织变化等问题,零件在高应力、高速度、高温等条件下工作时,由于表面作用着最大的应力并直接受外界介质的腐蚀,表面层的任何缺陷都可能引起应力集中,应力腐蚀等现象,从而机器零件一般是从表面层开始破坏。
5-21试述表面粗糙度,表面物理机械性能对机器使用性能的影响。
(1)表面粗糙度对机器使用性能的影响:a对耐磨性,一般表面粗糙度越大,耐磨性越差,但表面粗糙度太小耐磨性也差;b对疲劳强度,表面粗糙度越小,使疲劳强度升高;c对配合质量:表面粗糙度太大,影响配合稳定性;d对抗腐蚀性,表面粗糙度越小,抗腐蚀性越好。
机械制造工艺学第三版习题册参考答案
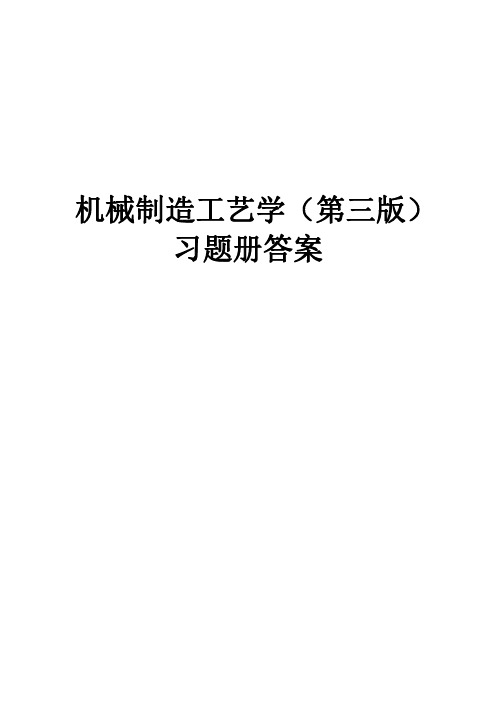
机械制造工艺学(第三版)习题册答案目录模块一机械制造基础知识 (1)任务1认识常见金属切削机床的型号 (1)任务2认识常见金属切削机床及刀具 (2)任务3选择零件毛坯 (5)任务4选择零件的热处理方法 (7)模块二典型表面机械加工方法的选择 (11)任务1外圆表面机械加工方法的选择 (11)任务2认识常见金属切削机床及刀具 (13)任务3平面机械加工方法的选择 (15)任务4成型表面机械加工方法的选择 (19)任务5螺纹表面机械加工方法的选择 (21)模块三机械加工质量与控制 (24)任务1认识机械加工精度 (24)任务2典型表面常见的加工误差与控制 (25)任务3加工误差的统计分析 (28)任务4选择保证加工精度的方法 (30)任务5表面质量的控制 (31)模块四机械加工工艺规程的制定 (34)任务1制定零件机械加工工艺过程 (34)任务2认识机械加工工艺规程 (36)任务3编制机械加工工艺过程卡 (37)任务4编制机械加工工序卡 (44)模块五典型零件的加工工艺分析 (53)任务1轴类零件的加工工艺分析 (53)任务2套类零件的加工工艺分析 (56)任务3箱体零件的加工工艺分析 (59)任务4圆柱齿轮零件的加工工艺分析 (61)模块六复杂零件加工工艺分析 (64)任务1曲轴零件的加工工艺分析 (64)任务2卧式车床丝杠的加工工艺分析 (65)任务3深孔零件加工工艺分析 (67)任务4连杆零件的加工工艺分析 (69)模块七机械装配工艺 (72)任务1认识装配工作 (72)任务2编制机械装配工艺规程 (73)任务3认识装配尺寸链 (75)任务4选择保证装配精度的方法 (76)模块八先进制造技术 (81)任务1认识超精密加工 (81)任务2认识高速加工 (82)任务3认识增材制造技术 (82)模块一机械制造基础知识任务1认识常见金属切削机床的型号一、填空题(将正确答案填写在横线上)1.尺寸精度2.车床磨床铣床3.通用专门化4.汉语拼音字母5./6.类代号7.数控车床8.阿拉伯数字阿拉伯数字9.折算10.主参数11.联动轴数复合二、判断题(正确的,在括号内打“√”;错误的,在括号内打“×”)1.√2.√3.×4.√5.√6.√7.√8.√9.×10.×11.√12.√13.√14.√15.×三、选择题(将正确答案的序号填写在括号内)1.A2.C3.D4.A5.B6.A7.D8.A四、解释下列机床型号的含义1.答:CQ6140B表示工件最大回转直径为400mm的经第二次重大改进的轻型卧式车床。
机械制造技术基础(第三版)第六章课后题答案

6-1什么是生产过程,工艺过程和工艺规程?(1)生产过程——将原材料转变为成品的过程。
(2)工艺过程——在生产过程中,凡是改变生产对象的形状、尺寸、位置和性质等,使其成为成品或半成品的过程称为工艺过程。
(3)工艺规程——把合理工艺过程的有关内容写成工艺文件的形式,用以指导生产,这些工艺文件称为工艺规程。
6-2何谓工序、工步、走刀?(1)工序是指一个(或一组)工人,在一台机床上(或一个工作地点),对同一工件(或同时对几个工件)所连续完成的那部分工艺过程。
(2)工步是在加工表面不变,加工工具不变,切削用量不变的条件下所连续完成的那部分工序。
(3)走刀又叫工作行程,是加工工具在加工表面上加工一次所完成的工步。
6-3零件获得尺寸精度、形状精度、位置精度的方法有哪些?(1)零件获得尺寸精度的方法:试切法、定尺寸刀具法、调整法、自动控制法。
(2)零件获得形状精度的方法:轨迹法、成形法、展成法。
(3)零件获得位置精度的方法:找正法、装夹法。
6-4不同生产类型的工艺过程的特点:p222-223表6-4.6-5试述工艺规程的设计原则、设计内容、设计步骤。
(1)工艺规程的设计原则:1所设计的工艺规程应能保证机器零件的加工质量(或机器的装配质量),达到设计图样上规定的各项技术要求。
2应使工艺过程具有较高的生产率,使产品尽快投放市场。
3设法降低制造成本。
4注意减轻劳动工人的劳动强度、保证生产安全。
(2)工艺规程的设计内容及步骤:1分析研究产品的零件图及装配图。
2确定毛坯。
3拟定工艺路线,选择定位基准。
4确定各工序所采用的设备。
5确定各工序所采用的刀具、夹具、量具和辅助工具。
6确定各主要工序的技术技术要求及检验方法。
7确定各工序的加工余量,计算工序尺寸和公差。
8确定切削用量。
9确定工时定额。
10技术经济分析。
11填写工艺文件。
6-6拟定工艺路线需完成那些工作?拟定工艺路线须完成的工作:1确定加工方法。
2安排加工顺序。
3确定夹紧方法。
- 1、下载文档前请自行甄别文档内容的完整性,平台不提供额外的编辑、内容补充、找答案等附加服务。
- 2、"仅部分预览"的文档,不可在线预览部分如存在完整性等问题,可反馈申请退款(可完整预览的文档不适用该条件!)。
- 3、如文档侵犯您的权益,请联系客服反馈,我们会尽快为您处理(人工客服工作时间:9:00-18:30)。
3.2.11 产生焊接应力与变形的原因是什么?焊接过程中和焊后,焊缝区 纵向受力是否一样?清除和防止焊接应力有哪些措施?
答:焊接过程的加热和冷却受到周围冷金属的约束,不能自由膨胀和收 缩。当约束很大时,则会产生残余应力,无残余变形。当约束很小时, 既产生残余应力,又产生残余变形。 采取以下措施可以防止或消除焊接应力: (1)焊接不要有密集交叉,截面和长度也要尽可能小,以减少焊接局 部加热,从而减少焊接应力。 (2)采取合理的焊接顺序,使焊缝能够自由收缩,以减少应力。 (3)采用小线能量,多层焊,也可减少焊接应力。 (4)焊前预热可以减少工件温差,也能减少残余应力。 (5)当焊缝还处于较高温度时,锤击焊缝使金属伸长,也能减少焊接 残余应力。
1.4.2在方便铸造和易于获得合格铸件的条件下,图1-62所示铸件构造
有何值得改进之处?怎样改进?
构造改进如图所示:
悬臂部分改为工字梁。
1.5.4 某铸件壁厚有5mm,20mm,52mm三种,要求铸件各处的抗拉强度 都能达到150MPa,若选用HT150牌号的灰铸铁浇注,能否满足其性能要 求?
答:由表中数据可得: HT150 175(2.5~10mm)
145 (10~20mm) 130 (20~30mm) 120 (30~50mm) 因铸件在壁厚20mm,52mm处无法承受150MPa强度,所以不满足性能要 求。
2.1.1 锡在20℃、钨在1100 ℃变形,各属于哪种变形?为什么(锡的熔点 为232 ℃,钨的熔点为3380 ℃)? 答:按照绝对温度计算。绝对温度零点是-237 ℃。
2.4.9 试述图2-60所示冲压件的生产过程。
1.先从板材上冲裁出上图形状。
2.再在图示位置冲掉两个圆孔。
3.最后沿着图示虚线位置折弯。
3.2.6 常见焊接缺陷有哪几种?其中对焊接接头性能危害最 大的为哪几种?
答:焊接接头的不完整性称为焊接缺陷,主要有焊接裂纹,未焊透,夹 渣,气孔和焊缝外观缺陷等。其中危害最大的是焊接裂缝和气孔。
2.应有一定的拔模斜度,便于拔模;
3.应设计得更厚,不然金属容易冷却, 不易充满模膛;
4.应为非机械加工面,模锻的尺寸精度 高和表面粗糙度底,所示处不用于配合。
2.4.4 用Φ50冲孔模具来生产Φ50落料件能否保证冲压件的精度?为什么?
答:不能。冲孔模的设计以凸模为基准,考虑到磨损,凸模取合乎公差要求的 最大值,因而,使用冲孔模,来生产落料件,尺寸偏大。
• 应用范围:压力铸造广泛应用于汽车,拖拉机,仪器仪表,医疗器械等 制造行业中;低压铸造常用来生产汽缸体,汽缸盖,活塞,曲轴箱,壳 体等高质量铝合金,镁合金铸件,有时用于生产铜合金,铸铁件。挤压 铸造适合于生产各种力学性能要求高,气密性好的后壁铸件,如汽车铝 轮毂,发动机铝活塞,铝缸体,制动器铝铸件等,不适合生产结构复杂 的铸件。
1.1.4 某工厂铸造一批哑铃,常出现如图1-59所示的明缩 孔,有什么措施可以防止,并使铸件的清理 工作量最小?
冒口 缩 孔
冷铁
▪答:可采用顺序凝固,使铸件按 规定方向从一部分到另一部分逐渐
凝固。在铸件可能出现缩孔的厚大 部位安放冒口。或在铸件远离浇冒
口的部位增设冷铁,加快该处的冷
却速度,使厚壁凸台反而最先凝固,
锡在20℃变形属于热变形,其T再=0.4×(232+237)K <(237+20)K; 钨在1100 ℃变形属于冷变形,其T再=0.4×(3380+237)K>(1100+237)K。 2.2.3 如何确定模锻件分模面的位置?
答:按照以下原则确定分模面的位置
1) 要保证模锻件能从模膛中取出。
2) 按选定的分模面制成的锻模后,应使上、下两模沿分模面的模膛轮廓一致,以 便在安装锻模和生产中容易发现错模现象,及时调整锻模的位置。
冷裂外形常穿过晶粒,呈连续直线状。裂缝细小,宽度均匀,断 口表面干净光滑,具有金属光泽或微氧化色。 (2)铸件结构不合理,合金的收缩大,型(芯)砂退让性差以及铸 造工艺不合理均可能引起热裂,刚和铁中的硫,磷降低了刚和铁的 韧性,使热裂的倾向大大提高。
1.2.2 确定如图所示铸件的铸造工艺方案,要求如下: (1)按单件小批生产条件分析最佳方案; (2)按所选方案绘制浇注位置,分型面,分模面。
3) 最好把分模面选在模膛深度最浅的位置处,使金属很容易充满模膛,便于取出 锻件,有利于锻模的制造。
4) 选定的分模面应使零件上所加的敷料最少。
5) 最好使分模面为一个平面,使上、下锻模的膛深度基本一致,差别不宜过大, 以便于制造锻模。
不合理的地方如图:
1.应设计为圆角,减小金属流动时的摩 擦阻力和使金属液充分的填满模膛;
从而实现自下而上的顺序凝固。如 图所示
1.1.5 某厂自行设计了一批如图所示的铸铁铁槽型梁。铸后立即进行了机 械加工使用一段时间后,在梁的长度方向上发生了弯曲变形。 (1) 该梁壁厚均匀,为什么还会变形?判断梁的变形方向。 (2) 有何铸造工艺措施能减少变形? (3) 为防止铸件变形,请改进槽型梁结构。
2.4.5 用Φ250×1.5板料能否一次拉深成直径为Φ50的拉深件?应采取哪些措 施才能保证正常生产?如果为多次拉深,请设计每次拉深系数。
答:不能一次拉深成型,应采用多次拉深,为保证材料有足够的塑性,一两 次拉深之后应安排工序间的退火处理,再着,多次拉深中,拉深系数应一次比一次 大。
各次拉深系数,m1=0.5,m2=0.625,m3=0.64(m=m1×m2×m3=0.2) 。
采用型芯三箱造型,或使用型芯二箱造型:
上 下
1.3.2 试比较压力铸造,低压铸造,挤压铸造三种方法的异同点及应 用范围。
• 异同点:压力铸造是动型提供压力,最后从动型中顶出铸件;低压铸造 是压缩空气提供压力,铸件由浇口进行补缩,不要冒口;挤压铸造的压 力很小,外力不直接作用在工件上,没有塑性变形组织。
答:1.因为该铸件有应力是不稳定的,将自发的通过变形来减小内应 力,趋于稳定状态。向下凹。
2.采用同时凝固以便冷却均匀,或用“反变形”工艺。 3.采用如下图所示结构。或增加外圆角,减小热节。
1.1.11 某铸件时常产生裂纹缺陷,如何区分其性质?如果属于热裂 纹,应该从那些方面寻找原因?
(1)热裂常发生在 铸件的拐角处,截面厚度突变处等应力集中的部位 或铸件最后凝固区的缩孔附近或尾部。裂纹往往沿晶界产生和发展, 外形曲折,不规则,裂缝较宽,裂口表面氧化较严重。