钉齿滚筒式脱粒装置的设计
【完美升级版】家用小型玉米脱粒机的设计毕业论文设计
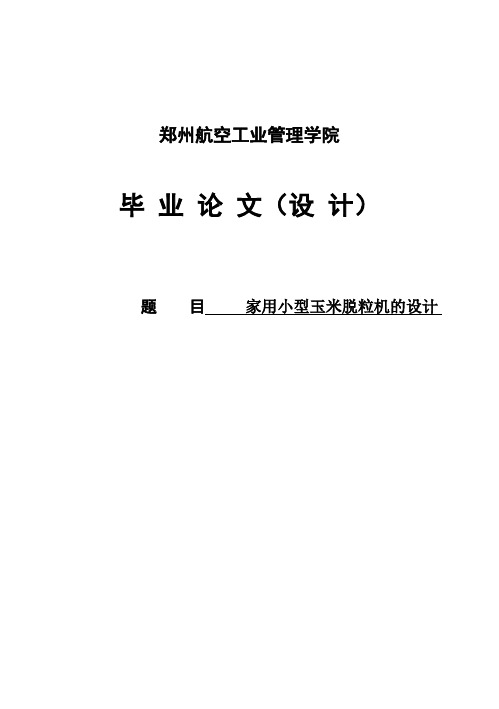
郑州航空工业管理学院毕业论文(设计)题目家用小型玉米脱粒机的设计毕业设计(论文)原创性声明和使用授权说明原创性声明本人郑重承诺:所呈交的毕业设计(论文),是我个人在指导教师的指导下进行的研究工作及取得的成果。
尽我所知,除文中特别加以标注和致谢的地方外,不包含其他人或组织已经发表或公布过的研究成果,也不包含我为获得及其它教育机构的学位或学历而使用过的材料。
对本研究提供过帮助和做出过贡献的个人或集体,均已在文中作了明确的说明并表示了谢意。
作者签名:日期: -指导教师签名:日期:使用授权说明本人完全了解大学关于收集、保存、使用毕业设计(论文)的规定,即:按照学校要求提交毕业设计(论文)的印刷本和电子版本;学校有权保存毕业设计(论文)的印刷本和电子版,并提供目录检索与阅览服务;学校可以采用影印、缩印、数字化或其它复制手段保存论文;在不以赢利为目的前提下,学校可以公布论文的部分或全部内容。
作者签名:日期:学位论文原创性声明本人郑重声明:所呈交的论文是本人在导师的指导下独立进行研究所取得的研究成果。
除了文中特别加以标注引用的内容外,本论文不包含任何其他个人或集体已经发表或撰写的成果作品。
对本文的研究做出重要贡献的个人和集体,均已在文中以明确方式标明。
本人完全意识到本声明的法律后果由本人承担。
作者签名:日期:年月日学位论文版权使用授权书本学位论文作者完全了解学校有关保留、使用学位论文的规定,同意学校保留并向国家有关部门或机构送交论文的复印件和电子版,允许论文被查阅和借阅。
本人授权大学可以将本学位论文的全部或部分内容编入有关数据库进行检索,可以采用影印、缩印或扫描等复制手段保存和汇编本学位论文。
涉密论文按学校规定处理。
作者签名:日期:年月日导师签名:日期:年月日指导教师评阅书指导教师评价:一、撰写(设计)过程1、学生在论文(设计)过程中的治学态度、工作精神□优□良□中□及格□不及格2、学生掌握专业知识、技能的扎实程度□优□良□中□及格□不及格3、学生综合运用所学知识和专业技能分析和解决问题的能力□优□良□中□及格□不及格4、研究方法的科学性;技术线路的可行性;设计方案的合理性□优□良□中□及格□不及格5、完成毕业论文(设计)期间的出勤情况□优□良□中□及格□不及格二、论文(设计)质量1、论文(设计)的整体结构是否符合撰写规范?□优□良□中□及格□不及格2、是否完成指定的论文(设计)任务(包括装订及附件)?□优□良□中□及格□不及格三、论文(设计)水平1、论文(设计)的理论意义或对解决实际问题的指导意义□优□良□中□及格□不及格2、论文的观念是否有新意?设计是否有创意?□优□良□中□及格□不及格3、论文(设计说明书)所体现的整体水平□优□良□中□及格□不及格建议成绩:□优□良□中□及格□不及格(在所选等级前的□内画“√”)指导教师:(签名)单位:(盖章)年月日评阅教师评阅书评阅教师评价:一、论文(设计)质量1、论文(设计)的整体结构是否符合撰写规范?□优□良□中□及格□不及格2、是否完成指定的论文(设计)任务(包括装订及附件)?□优□良□中□及格□不及格二、论文(设计)水平1、论文(设计)的理论意义或对解决实际问题的指导意义□优□良□中□及格□不及格2、论文的观念是否有新意?设计是否有创意?□优□良□中□及格□不及格3、论文(设计说明书)所体现的整体水平□优□良□中□及格□不及格建议成绩:□优□良□中□及格□不及格(在所选等级前的□内画“√”)评阅教师:(签名)单位:(盖章)年月日教研室(或答辩小组)及教学系意见教研室(或答辩小组)评价:一、答辩过程1、毕业论文(设计)的基本要点和见解的叙述情况□优□良□中□及格□不及格2、对答辩问题的反应、理解、表达情况□优□良□中□及格□不及格3、学生答辩过程中的精神状态□优□良□中□及格□不及格二、论文(设计)质量1、论文(设计)的整体结构是否符合撰写规范?□优□良□中□及格□不及格2、是否完成指定的论文(设计)任务(包括装订及附件)?□优□良□中□及格□不及格三、论文(设计)水平1、论文(设计)的理论意义或对解决实际问题的指导意义□优□良□中□及格□不及格2、论文的观念是否有新意?设计是否有创意?□优□良□中□及格□不及格3、论文(设计说明书)所体现的整体水平□优□良□中□及格□不及格评定成绩:□优□良□中□及格□不及格(在所选等级前的□内画“√”)教研室主任(或答辩小组组长):(签名)年月日教学系意见:系主任:(签名)年月日内容摘要从1785年苏格兰人安朱梅克( AndrewMeikle)发明第一个回转滚筒脱粒装置以来, 人们对玉米脱粒装置做了大量的试验和研究, 不断开发出新的玉米脱粒装置。
脱粒滚筒滚幅盘加工与拉伸模设计

脱粒滚筒滚幅盘加工与拉伸模设计张佳兴【摘要】脱粒装置是联合收获机的关键工作部件,其结构设计与制造工艺在很大程度上决定着联合收获机的工作性能.脱粒滚筒是脱粒装置核心部件,钉齿式脱粒滚筒主要包括滚筒轴、辐盘、齿杆和钉齿等部件.幅盘是钉齿式脱离滚筒的主要支撑件,其结构、强度、加工工艺性以及选材直接影响着脱离滚筒的使用可靠性.为此,通过对此盘类件的结构、性能及加工工艺分析,合理地设计幅盘拉伸模具,有效地利用激光切割机板材孔类切割的高效性和单点压力机气顶的双重作用,在保证加工质量的同时,最大限度地减少了模具投入和加工工序,降低了制造成本,产生了良好的经济效益.【期刊名称】《农机化研究》【年(卷),期】2011(033)012【总页数】4页(P67-70)【关键词】脱离滚筒;杠杆;幅盘;气顶【作者】张佳兴【作者单位】南通职业大学,江苏南通226007【正文语种】中文【中图分类】S225.30 引言联合收割机脱粒装置的主要性能指标有脱不净率、夹带率、破碎率、含杂率及功率消耗等。
钉齿滚筒式轴流全喂入脱粒装置是目前市场上使用量最大的脱粒结构,适用性广,能对小麦、水稻和大豆等多种作物进行脱粒和清选作业。
钉齿式脱粒滚筒的结构特点是:钉齿在齿杆上呈不等距排列,且进料口端比出料口端钉齿的排列间距小,可克服缠绕、堵塞、开锅、脱净率低、效率低及车损大的缺陷。
脱粒滚筒包括固定在滚筒轴上的若干辐板,辐板的外周面环形阵列有多个固定有钉齿的钉齿杆。
钉齿杆是脱粒滚筒工作时主要受力部件,辐板的强度及结构也就直接影响着脱粒滚筒工作性能的好坏。
因此,辐板在设计、选材和加工工艺等要优化考虑。
1 结构设计及选材本文以约翰.迪尔佳联收获机械有限公司生产的3060型联合收割机钉齿幅盘为例进行说明。
在设计结构时,考虑此盘类件是回转件,其回转时存在惯性离心力,同时为降低脱粒滚筒整体消耗功率,减小其质量,该件宜采用薄板类件加工。
如若采用焊接件制造,为提高其强度,势必用增加筋板加强。
3005_课程设计-谷物联合收获机脱粒工作部件的设计(喂入量5kg.s-双滚筒脱粒装置)

1.引言所谓双滚筒式脱粒装置,就是两个脱粒装置的组合。
它的第一滚筒为钉齿式,第 二滚筒为纹杆式。
脱粒时作物经第一滚筒脱出的成熟麦粒通过第一凹板分离后,未 脱下的较难脱的麦粒和茎杆进入第二滚筒,然后将麦粒完全脱净。
4LQ-2.5联合收割 机滚筒转速(转/分)的调整范围:钉齿:400/1330,纹杆:400-1200共八级,滚筒 与凹板间隙(毫米)调整范围,钉齿上侧间隙5,纹杆入口:0-60、出口:0-45。
由于 这些结构参数和运动参数选择的不恰当,脱粒过程中常常引起麦粒的破碎。
麦粒的 破碎率是衡量脱粒装置工作性能的重要指标。
因此,合理选择滚筒的速度和正确的 调整滚筒与凹板的间隙, 用正交法对4LQ-2.5联合收割机脱粒机构进引室内性能试验 是降低麦粒破碎率的必要措施。
2.理论介绍本次设计的是纹杆——钉齿双滚筒,第一个滚筒有喂入的谷物层均匀和拉薄作用, 进入第二滚筒谷物层较均薄,因而脱净率高,而破碎较低,但作物经二次脱粒,碎 秸草增加,清选工作负担大,因此功率消防大。
双滚筒装置对潮湿的作物适应性较 强。
双滚筒脱粒装置的第一滚筒大多采用钉齿式滚筒,第二个滚筒为纹杆式滚筒。
第一滚筒用钉齿式有利于抓取作物,脱粒能力强,第二滚筒 用纹杆式有利于提高分 离率,减少碎茎杆。
这种形式适用于收获稻麦。
配置双滚筒要注意保持作物脱粒工艺流程通畅。
要使第一滚筒脱出的作物秸杆 能顺利地喂入第二滚筒,中间设置过渡板,过渡板作用是保证正确的喂入第二个滚 筒,保证脱粒工作顺利的进行。
脱粒装置工作复杂,工作原理主要靠冲击,揉搓,梳刷等原理脱粒。
双滚筒脱粒装置采用前后两个脱粒滚筒,前脱粒滚筒为钉齿式,转速较低。
使 成熟饱满,易脱落的谷粒快速脱落下来,然后将未脱净的稻杆投入后齿杆脱粒滚筒, 使稿杆上剩余的较不易脱落的不十分成熟和不饱满的谷粒在较高速滚筒更强力的打 击落下来。
常用滚筒型式有圆柱形和圆锥形钉齿滚筒,滚筒圈有闭式也有开式:考虑结构简单,成本低且脱粒质量要求,选择圆柱形滚筒连同钉齿整体铸造。
玉米脱粒机毕业设计(毕业论文设计)
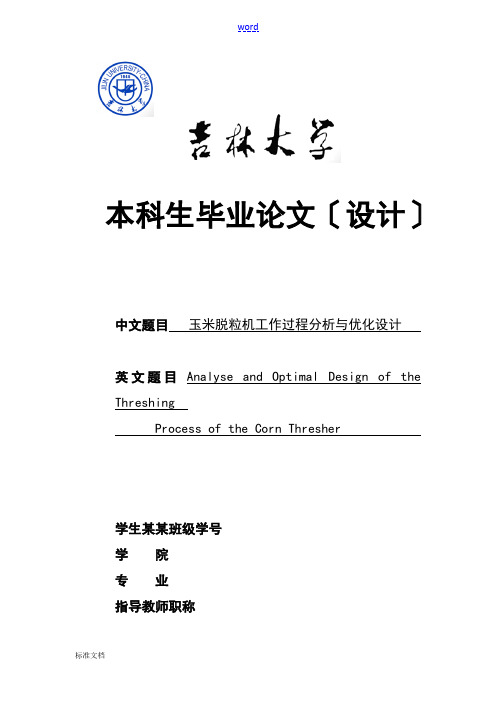
word本科生毕业论文〔设计〕中文题目玉米脱粒机工作过程分析与优化设计英文题目Analyse and Optimal Design of the ThreshingProcess of the Corn Thresher学生某某班级学号学院专业指导教师职称目录摘要IAbstractII第1章绪论11.1 研究背景与意义11.2 玉米脱粒机的种类与特点11.2.1 玉米脱粒机的表示方法11.2.2 各类玉米脱粒机的工作原理21.2.3 综合比拟各类玉米脱粒机41.3 国外玉米脱粒机的开展41.4 国内玉米脱粒机的开展51.5 存在的问题61.6 本文主要研究内容7第2章板齿玉米脱粒机总体结构与工作原理82.1 板齿脱粒机根本结构与工作过程82.2 板齿脱粒机工作原理82.3 本章小结9第3章板齿玉米脱粒机脱粒元件设计103.1 板齿设计103.1.1 板齿作用103.1.2 板齿样式与尺寸103.2 电动机设计113.2.1 板齿玉米脱粒机所需功率113.2.2 电机选择错误!未定义书签。
3.3 传动带的设计错误!未定义书签。
3.3.1 传动带的选取错误!未定义书签。
3.3.2 V带设计错误!未定义书签。
3.4 带轮设计错误!未定义书签。
3.4.1 带轮材料错误!未定义书签。
3.4.2 主动带轮设计错误!未定义书签。
3.4.3 从动带轮设计错误!未定义书签。
3.5 脱粒滚筒设计错误!未定义书签。
3.5.1 脱粒主轴作用错误!未定义书签。
3.5.2 阶梯轴设计错误!未定义书签。
3.5.3 脱粒滚筒设计错误!未定义书签。
3.5.4 阶梯轴的校核错误!未定义书签。
3.6 凹板设计错误!未定义书签。
3.6.1 凹板作用错误!未定义书签。
3.6.2 凹板类型错误!未定义书签。
3.6.3 凹板间隙错误!未定义书签。
3.6.4 凹板其他尺寸错误!未定义书签。
3.7 脱粒仓结构设计错误!未定义书签。
3.7.1 脱粒仓作用错误!未定义书签。
玉米脱粒机的设计
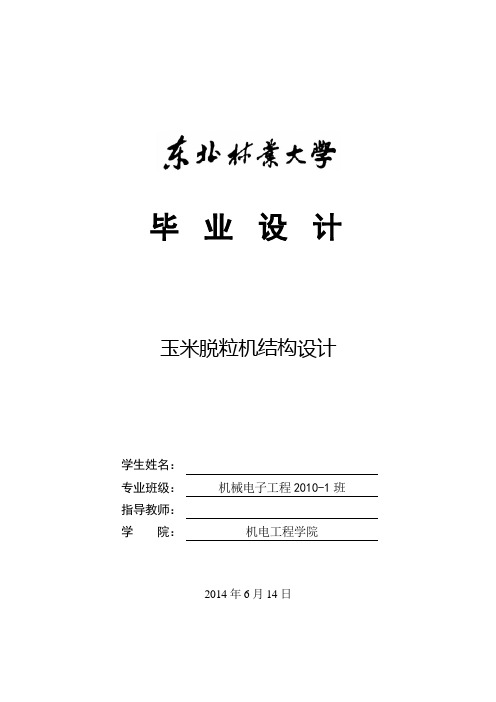
这里仅对玉米脱粒机进行结构设计,玉米脱粒是玉米脱皮后,经过一段时间的风干,然后将玉米粒和玉米芯分开,能完成这种动作的机器就是玉米脱粒机。为了降低农民脱粒劳动的强度、提高工作效率,所以设了计玉米脱粒机。该设计主要由入料口,筛网,钉齿滚筒及传动部件等组成。以电动机为动力源,动力由电动机输出,在通过传动带传递到钉齿滚筒上,脱粒滚筒配合筛网将玉米脱粒,玉米粒从筛网分离并输出到机器外。最后进行相关姓名:
专业班级:
机械电子工程2010-1班
指导教师:
学 院:
机电工程学院
2014年6月14日
玉米脱粒机结构设计
摘要
随着社会的进步,生活中的每一个角落都有机器的参与。农业是我国的基础经济、是国家发展的根本,机械化的普及,不仅使农业加强了农业化生产,同时也减轻了农民的劳动强度。如今我国北方大部分地区基本从种到收到入仓,都实现了机械化作业,更值得庆幸的是每种机械的开发和使用都有相当可观的市场,科技的创新更很好的开阔了市场。
关键词玉米脱粒机;钉齿滚筒;带轮;传动系统
Corn sheller Structure Design
Abstract
新型钉齿式大豆脱粒机的设计

2018 'w m'11’!遣I FU JIANt iliIA N N O N G J L蚵究与棵索新型钉齿式大豆脱粒机的设计赵晶晶(郑州工程技术学院机电与车辆工程学院河南郑州450000)摘要:针对大豆收获时含水率高,收获过程中大豆脱粒破损率高、脱不净等问题,设计了一种新型钉齿式 大豆脱粒机。
该机基于冲击脱粒的原理,采用低速螺旋排列的钉齿脱粒滚筒、冲孔式凹板结构。
与传统的钉齿 式脱粒滚筒相比,能提高大豆的脱净率,降低破损率,减小加工损失,提高经济效益。
关键词:大豆脱粒机;钉齿滚筒;冲孔式凹板中图分类号:S22文献标识码:A大豆是人们日常生活中必不可少的粮食作物之一。
目前我国大豆脱粒机械主要为钉齿式,钉齿以一定的速度对大豆进行冲击,从而实现脱粒。
然而当冲击作用超过一定的限度时,就会产生豆粒的破坏与损伤,因此合适的钉齿冲击力非常重要。
本文基于钉齿式大豆脱粒机冲击脱粒的原理,通过探讨钉齿的排列与安装方式,合理控制钉齿的冲击力,设计了一种新型钉齿式大豆脱粒机。
1钉齿式大豆脱粒机整机结构与工作原理1.1整机结构钉齿式大豆脱粒机主要由入料、脱粒、筛选和机架等4部分组成。
其总体结构如图1所示。
人料部分与大豆脱粒机的上盖相连、与钉齿滚筒部分的钉齿相切,是用10 m m厚的铁板制成。
脱粒部分是由钉齿滚筒、360°冲孔式凹板、半圆形上盖组成。
筛选部分主要由冲孔式凹板和溜板来完成,采用3 m m厚的 薄铁板制成。
机架部分由底部机架及支撑、上盖部 分及人料口、溜板等组成。
1.2主要技术参数1.上盖;2.轴承座;3.主轴;4.大带轮;5.传动带;6.电动机;7.小带轮;8.机架;9.圆盘;10.钉齿条;11.钉齿;12.螺栓;13.溜板;14.人料口;15.出料口。
新型钉齿式大豆脱粒机的主要技术参数如表1所示。
作者简介:赵晶晶(1989—),女,硕士,助教,研究方向:先进制造技术。
jS f — 38 —FUJIANNONGJI岬究与裸索_響卜!遣农机F U J IA N N O NG JI表1整机技术参数项目参数长X宽X高/(m m X nunXm m)1300x600x1000滚筒直径/m m270滚筒长度/m m900滚筒转速/(r/min)600钉齿线速度/(m/s)9.734脱粒间隙/m m15电动机型号为Y100L2-4,主要技术参数如表2所示。
农业机械及其自动化专业毕业论文--横向单轴流钉齿式滚筒脱粒装置

目录一.横向单轴流钉齿式滚筒脱粒装置的生产过程: ........................ - 1 - 二.横向单轴流钉齿式滚筒的特点:............................................... - 1 - 三.设计依据及生产对象:............................................................... - 1 - 四.横向单轴流钉齿式滚筒的设计:............................................... - 2 -4.1滚筒结构:............................................................................... - 2 -4.2带有螺旋形导向板的顶盖设计............................................... - 2 -4.3凹板的设计............................................................................... - 3 -4.4其他........................................................................................... - 3 -5.结论:............................................................................................... - 4 -6.参考文献:....................................................................................... - 5 -设计说明书一.横向单轴流钉齿式滚筒脱粒装置的生产过程:它由脱粒滚筒、栅格式凹板和顶盖等组成。
玉米脱粒机设计

TEL:18267419519
本课题是针对一种玉米脱粒机的结构设计,玉米脱粒机是玉米脱皮后,经过一段时间的风干,然后将玉米利用脱粒机使玉米和玉米芯分开,这种机械就是玉米脱粒机。它的工作原理是:玉米脱粒机在进行玉米脱粒时,利用钉齿滚筒回转运动的钉齿与栅格式凹板之间的间隙相配合,使玉米粒拖下(钉齿滚筒和栅格式凹板之间的揉搓作用,将玉米粒脱离玉米芯,并借助其他的机械机构将玉米粒和玉米芯分别从两个不同的出口排出机体之外,循环脱粒,不断的进行填入---脱粒---排出机体。玉米脱粒机主要组成部分:入料口、钉齿脱粒滚筒轴、栅格式凹板、机架等部分组成。有全套11张CAD图纸及完整设计说明书。
毕业设计(论文)主要内容和要求:玉米脱粒机是农作物玉米的脱粒机器,其主要功能是将玉米和玉米芯分开,达到玉米脱粒的功能。原始数据:玉米脱粒机主轴转速要求为650~750r/min,一次性可输入玉米的质量是10kg;主要内容和要求:根据玉米脱粒的工作流程,设计它的脱粒机构、传动结构以及它的筛选结构。
需毕业文正文全文及全套图纸可联系:
玉米脱粒机的传动装置和机架设计.
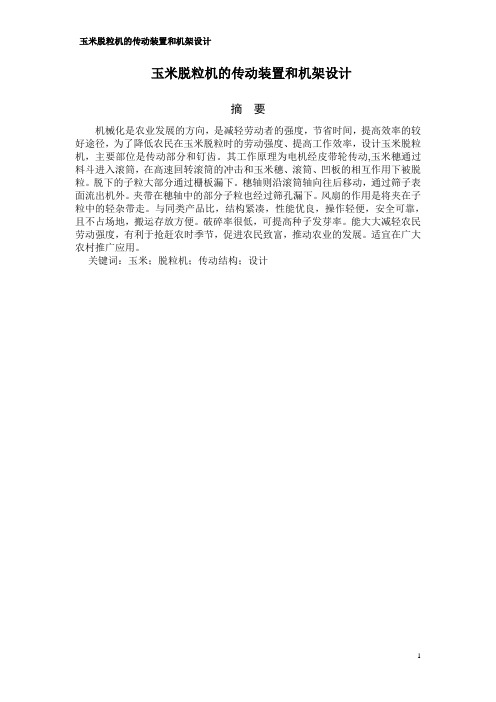
玉米脱粒机的传动装置和机架设计玉米脱粒机的传动装置和机架设计摘要机械化是农业发展的方向,是减轻劳动者的强度,节省时间,提高效率的较好途径,为了降低农民在玉米脱粒时的劳动强度、提高工作效率,设计玉米脱粒机,主要部位是传动部分和钉齿。
其工作原理为电机经皮带轮传动,玉米穗通过料斗进入滚筒,在高速回转滚筒的冲击和玉米穗、滚筒、凹板的相互作用下被脱粒。
脱下的子粒大部分通过栅板漏下。
穗轴则沿滚筒轴向往后移动,通过筛子表面流出机外。
夹带在穗轴中的部分子粒也经过筛孔漏下。
风扇的作用是将夹在子粒中的轻杂带走。
与同类产品比,结构紧凑,性能优良,操作轻便,安全可靠,且不占场地,搬运存放方便。
破碎率很低,可提高种子发芽率。
能大大减轻农民劳动强度,有利于抢赶农时季节,促进农民致富,推动农业的发展。
适宜在广大农村推广应用。
关键词:玉米;脱粒机;传动结构;设计1玉米脱粒机的传动装置和机架设计AbstractAgricultural mechanization is the direction of development, reduce the strength of the laborers is, save time, improve efficiency a better way, in order to reduce corn farmers in the labor intensity, threshing improve work efficiency, and design more corn, main part is the transmission part and nail teeth. The principle for the motor driving pulley, corn ear through the hopper into roller, at high speed rotary roller impact and corn ear, roller, concave board under the interaction was threshing. Take off the grain most through the grid board under the leakage. SuiZhou along the drum axle after the yearning mobile, through the sieve surface outflow cake layer. In parts of the SuiZhou carry grain have also been screen hole leakage. Fan is the role of the mixed in with fruit light away. With the similar product than, compact structure, good performance, convenient operation, safe and reliable, and do not take a site, carry convenience store. Broken rate is very low, can enhance seed germination rate. Can greatly reduce the farmer labor intensity, be helpful for snatches farming season, and to promote the peasant to become rich, promote the development of agriculture. Suitable for application in the rural areas.Keywords: corn; Threshers; Transmission structure; design2玉米脱粒机的传动装置和机架设计目录摘要 (1)abstract (2)1 引言 (5)1.1课题研究目的及意义 (5)1.2 国内外研究现状 (5)1.2.1 国外研究现状分析 (5)1.2.2 国内研究现状分析 (6)1.3 本课题研究内容 (7)2玉米脱粒机总体结构 (7)2.1入料部分 (7)2.2脱粒部分 (7)2.3筛选部分 (7)2.4机架部分 (8)2.5玉米脱粒机的总体设计 (8)3 玉米脱粒机的设计 (9)3.1 电动机的选择 (9)3.2 钉齿条上的钉齿转速 (9)3.3 钉齿滚筒的转速 (9)3.4 电动机的功率 (9)3.5 电动机的转速 (10)4带及带轮的设计 (11)4.1传动带的设计 (11)4.1.1 确定计算功率 (11)4.1.2 选择V带的型号 (12)4.1.3确定带轮的基准直径 (12)4.1.4 确定传动中心距和带长 (12)4.1.5 验算主动轮上的包角 (13)4.1.6 确定V带的根数 (13)4.1.7 确定带的初拉力 (14)4.1.8求V带传动作用在轴上的压力 (14)5 V 带带轮的设计 (14)3玉米脱粒机的传动装置和机架设计5.1带轮的材料选择 (14)5.2结构设计 (15)5.3 从动带轮的设计 (15)6 传动轴的设计 (16)6.1根据轴向定位的要求确定轴的各段直径和长度 (17)6.2 初步选择输出轴系 (17)6.3确定输出轴上的圆角半径r值 (18)6.4 按弯扭合成条件校核轴的强度 (18)6.4.1 作轴的简图 (18)6.4.2 求输出轴上的所受作用力的大小 (18)6.4.3钉齿条上的合力 (19)6.4.4轴上水平面内所受支反力如图 (19)6.4.5轴在垂直面内所受的支反力 (19)6.4.6 作弯矩图 (20)6.4.7作弯矩图 (21)6.4.8作当量弯矩图(弯矩、扭矩合成图 (21)6.5 校核轴的强度 (21)7 钉齿条的设计 (22)7.1 钉齿条的总体结构设计 (22)7.2 钉齿条及钉齿的设计 (23)7.3 钉齿的设计 (24)7.4 圆盘的设计 (24)8 栅格式凹板的设计 (25)9入料口及脱粒机上盖的设计 (26)10机架的设计 (27)11轴承座的设计 (28)12玉米脱粒机上的标准件的选择 (29)12.1玉米脱粒机上的螺栓的选择 (29)12.2钩头楔键的选择 (29)13 玉米脱粒机的维护 (29)13.1玉米脱粒机的技术保养 (30)13.2玉米脱粒机的保管 (30)结论 (30)致谢 (31)参考文献 (32)4玉米脱粒机的传动装置和机架设计1 引言1.1课题研究目的及意义玉米脱粒机用于对于晾干后的玉米穗进行脱粒。
毕业设计(论文)-制种玉米脱粒装置的设计

毕业设计(论⽂)-制种⽟⽶脱粒装置的设计机械电⽓⼯程学院本科毕业设计设计说明书题⽬:制种⽟⽶脱粒装置的设计院(系):专业:学号:姓名:指导教师:完成⽇期:制种⽟⽶脱粒装置的设计摘要:为解决传统制种⽟⽶脱粒机存在的脱净率低、破碎率⾼、对⽟⽶含⽔率适应性差的问题,现介绍⼀种利⽤打击和揉搓原理相结合的新型制种⽟⽶脱粒装置,该装置加⼊了带冠板齿和脱粒钉齿等机构,来满⾜制种⽟⽶脱粒的技术要求。
另外加⼊了间隙调节机构,增强了对不同含⽔率的⽟⽶脱粒作业的适应性。
该复合式制种⽟⽶脱粒装置降低了⽟⽶脱粒时的劳动强度,提⾼了作业效率。
关键词:制种⽟⽶;脱粒;带冠板齿;脱粒钉齿;设计Design of corn threshing deviceAbstract: in order to solve the existing in the traditional production of corn thresher threshing rate low, broken rate, poor adaptability to high water content in corn, this paper introduces a new use of combat and corn threshing device combining kneading principle, the device joined with crown plate gear and floating nail teeth and other institutions, to meet the corn threshing technical requirements. In addition to clearance adjusting mechanism, enhance the corn threshing operations with different water content adaptation. The hybrid seed corn threshing device of corn threshing and reduces the labor intensity, improve operational efficiency.Keywords:maize seed threshing teeth with crown plate; floating nail tooth design⽬录⼀、引⾔ (6)⼆、制种⽟⽶脱粒装置的总体设计 (7)1、研究内容 (7)2、⼯作原理 (7)3、⼯作过程 (7)4、主要机构 (8)4、1传动部分 (8)4、2⼊料⼝及脱粒滚筒上盖 (8)4、3 脱粒部分 (8)4、4控制部分 (9)4、5 机架部分 (9)4、6总体设计 (10)三、制种⽟⽶脱粒装置零部件的设计 (11)1、脱粒滚筒的设计 (11)1、1 滚筒转速 (11)1、2 滚筒直径 (11)1、3滚筒长度 (11)2、脱粒齿的设计 (12)2、1带冠板齿的设计 (12)2、2脱粒钉齿的设计 (13)2、3脱粒齿的排列 (13)3、栅格凹板的设计 (15)3、1栅格凹版 (15)3、2 间隙调节机构 (16)4 、脱粒滚筒主轴的设计 (16)4、1 根据轴向定位的要求确定轴的各段直径和长度 (17) 4、2 初步选择输出轴系 (18)4、3确定输出轴上的圆⾓半径r值 (18)4、4 作轴的结构图 (18)4、5 求输出轴上的所受作⽤⼒的⼤⼩ (18)4、6校核轴的强度 (19)5、带轮的参数设计 (19)5、1主动轮的选择 (19)5、2从动轮的结构设计 (20)5、2、1 带轮材料的选择 (20)5、2、2 V带的设计与计算 (21)5、2、3 带轮的结构设计 (22)6、⼊料搅龙的设计 (23)7、出料搅龙的设计 (23)8、机架的设计 (24)8、1 ⼊料⼝及脱粒机上盖的设计 (24)8、2机架的设计 (25)四、制种⽟⽶脱粒机装置上的标准件的选择 (26)1、轴承的选择 (26)2、螺栓的选择 (26)3、平键的选择 (27)五、制种⽟⽶脱粒装置的安全操作 (28)六、制种⽟⽶脱粒装置的维护 (29)1、制种⽟⽶脱粒装置的技术保养 (29)2、制种⽟⽶脱粒装置的保管 (29)七、结论 (30)⼋、参考⽂献 (31)九、致谢................................................................................................. 错误!未定义书签。
钉齿滚筒式脱粒装置的设计

面 的搓擦 作用 下脱 粒 。钉齿 凹板 为栅 格状 时 , 可能 会
有3 0 %~ 7 5 %的谷 粒 被分离 出来 ; 无 筛孔 时 , 则全 部 夹
在茎稿 中。
2 . 2 钉齿 的排 列及 滚筒 长度 、 直 径
J a n . 2 0 1 3
钉齿滚筒式脱粒装置 的设计
班 春 华
( 辽 宁省 农 业 机 械 化 研 究 所 , 沈阳 1 1 0 1 6 1 )
摘要 : 为 提 高脱 粒 装 置 的适 用 性 , 设 计 一款 结 构 简 单 、 体积小 、 质量 轻 、 造价低 、 性 能 稳 定 可 靠 的 钉 齿 滚 筒 式 脱 粒 装 置 。 介 绍 脱 粒 装 置 的 总体 设 计 思 路 及 工 作 原 理 , 探讨滚筒的钉齿排列 、 长 度 及 直径 确定 , 为 脱 粒 装 置 的研 制 应 用 提 供参 考 。 关键 词 : 脱 粒装 置 ; 钉齿 ; 设计 ; 直径 ; 凹 板
离 面积 .同时 也 阻挡 了谷 物在 凹板表 面 上 的运 动 速
获得所 需 谷粒 。 它是 提 高生 产率 , 改善 劳动 条件 , 确保
丰产 、 丰收 的重 要手 段 。我 国的脱 粒机 械 主要 有 人力 简易式 、 动 力半 复式 及大 中型 复式 3种 。在 我 国农业 机械 化逐 步发 展 的过程 中,脱粒 机仍 占重要 地 位 , 并 将在 品种 、 质量 上积 极发 展 。为适 应我 国农 业机 械 化 逐 步发 展 的要 求 , 在应 用传 统 技术 的基 础 上 , 对 部 分 部件 进 行改 进 创新 , 取 长补 短 , 设 计 了钉齿 滚 筒 式脱 粒装 置 。
钉齿滚筒式脱粒机的创新设计
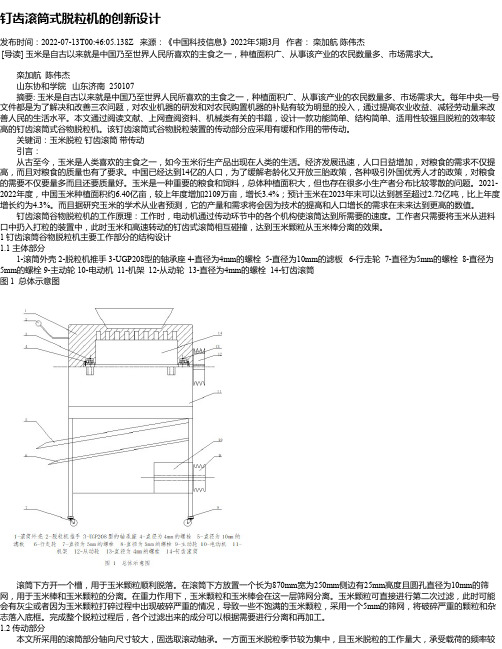
钉齿滚筒式脱粒机的创新设计发布时间:2022-07-13T00:46:05.138Z 来源:《中国科技信息》2022年5期3月作者:栾加航陈伟杰[导读] 玉米是自古以来就是中国乃至世界人民所喜欢的主食之一,种植面积广、从事该产业的农民数量多、市场需求大。
栾加航陈伟杰山东协和学院山东济南 250107摘要: 玉米是自古以来就是中国乃至世界人民所喜欢的主食之一,种植面积广、从事该产业的农民数量多、市场需求大。
每年中央一号文件都是为了解决和改善三农问题,对农业机器的研发和对农民购置机器的补贴有较为明显的投入,通过提高农业收益、减轻劳动量来改善人民的生活水平。
本文通过阅读文献、上网查阅资料、机械类有关的书籍,设计一款功能简单、结构简单、适用性较强且脱粒的效率较高的钉齿滚筒式谷物脱粒机。
该钉齿滚筒式谷物脱粒装置的传动部分应采用有缓和作用的带传动。
关键词:玉米脱粒钉齿滚筒带传动引言:从古至今,玉米是人类喜欢的主食之一,如今玉米衍生产品出现在人类的生活。
经济发展迅速,人口日益增加,对粮食的需求不仅提高,而且对粮食的质量也有了要求。
中国已经达到14亿的人口,为了缓解老龄化又开放三胎政策,各种吸引外国优秀人才的政策,对粮食的需要不仅要量多而且还要质量好。
玉米是一种重要的粮食和饲料,总体种植面积大,但也存在很多小生产者分布比较零散的问题。
2021-2022年度,中国玉米种植面积约6.40亿亩,较上年度增加2109万亩,增长3.4%;预计玉米在2023年末可以达到甚至超过2.72亿吨,比上年度增长约为4.3%。
而且据研究玉米的学术从业者预测,它的产量和需求将会因为技术的提高和人口增长的需求在未来达到更高的数值。
钉齿滚筒谷物脱粒机的工作原理:工作时,电动机通过传动环节中的各个机构使滚筒达到所需要的速度。
工作者只需要将玉米从进料口中扔入打粒的装置中,此时玉米和高速转动的钉齿式滚筒相互碰撞,达到玉米颗粒从玉米棒分离的效果。
- 1、下载文档前请自行甄别文档内容的完整性,平台不提供额外的编辑、内容补充、找答案等附加服务。
- 2、"仅部分预览"的文档,不可在线预览部分如存在完整性等问题,可反馈申请退款(可完整预览的文档不适用该条件!)。
- 3、如文档侵犯您的权益,请联系客服反馈,我们会尽快为您处理(人工客服工作时间:9:00-18:30)。
钉齿滚筒式脱粒装置的设计
脱粒机将割下的作物进行脱粒、分离和清选,以获得所需谷粒。
它是提高生产率,改善劳动条件,确保丰产、丰收的重要手段。
我国的脱粒机械主要有人力简易式、动力半复式及大中型复式3种。
在我国农业机械化逐步发展的过程中,脱粒机仍占重要地位,并将在品种、质量上积极发展。
为适应我国农业机械化逐步发展的要求,在应用传统技术的基础上,对部分部件进行改进创新,取长补短,设计了钉齿滚筒式脱粒装置。
1 钉齿滚筒式脱粒装置工作原理
脱离装置的特点是:抓取谷物能力强,不均匀喂入适应性好,适于潮湿作物以及水稻、大豆等作物脱粒;对装配要求高,成本高,稿草断碎多,凹板分离能力低,功率耗用较纹杆式高。
脱粒机工作时,谷物植株从脱粒总成的喂入口喂人,在电机带动脱粒总成中的脱粒滚筒及风扇转动的过程中,在脱粒滚筒钉齿的打击揉搓与摩擦作用下脱粒;脱粒后的谷物经筛板漏下,并沿溜板滑下;杂物由风机沿溜板斜向上吹出机体外,实现谷物与杂物的分离清选。
在此工作过程中,可通过调节调风板、风扇给风量来调节去杂能力。
如遇堵塞,可转动扳手打开底部筛板,利于清除堵塞物或残留物。
钉齿滚筒的脱粒原理为:作物被钉齿抓取后进入脱粒间隙,在钉齿打击及齿侧面、钉齿顶部与凹板弧面的搓擦作用下脱粒。
钉齿凹板为栅格状时,可能会有30%—75%的谷粒被分离出来;无筛孔时,则全部夹在茎稿中。
2钉齿滚筒式脱粒装置详细设计
钉齿滚筒式脱粒装置由钉齿滚筒和钉齿凹板组
成。
钉齿滚筒脱离装置的脱离性能与谷物喂入量、脱粒速度等有关。
钉齿滚筒脱离装置的凹板分离率比纹杆滚筒式小,这是由于凹板上有钉齿,减少了有效分离
面积,同时也阻挡了谷物在凹板表面上的运动速度。
钉齿滚筒的脱粒速度对谷物的破碎作用非常显著。
2.1 钉齿滚筒
钉齿按螺旋线成排固定在齿杆上。
脱粒机上常用的钉齿有板刀齿、楔齿和弓齿。
板刀齿薄而长,抓取和梳刷脱粒作用强,对喂人不均匀的厚层作物适应性好,打击脱粒的能力也比楔齿强。
由于其梳刷作用强,齿侧间隙又大,因此脱壳率较低,利于对水稻进行脱粒。
此外,由于其齿薄、侧隙大、齿重叠量小,因此功率消耗也比楔齿低。
楔齿基宽顶尖,纵断面几乎成正三角形,齿面向后弯曲,齿侧面斜度大,脱潮湿长秆作物时不易缠绕,且脱粒间隙的调整范围大。
在水稻脱粒时,弓齿的脱粒效果比刀齿好,凹板分离率较高,脱粒作用较柔和,破碎率和破壳率均较低。
经分析及试验,确定采用板刀齿。
板刀齿的工作面后倾角为10,20。
,大多用于双滚筒脱粒装置的第一滚筒上(后倾角大,脱草好,功率耗用较低)。
用板刀齿对水稻进行脱粒的试验表明:后倾角在0-37.50范围内变化时,谷粒损伤有所减轻,且功率耗用减少25%左右,但脱不净损失增加30%-50%:后倾角在在0,12.50范围内变化时,谷粒损失几乎没有增大。
2.2钉齿的排列及滚筒长度、直径
钉齿数量及排列对脱粒性能有很大影响。
在钉齿数量一定的情况下,若一个钉齿的运动轨迹内只有一个钉齿通过,则不仅生产率很低,而且滚筒必须很长。
因此,应尽量让若干个钉齿在同齿迹内回转。
为了确保工作均匀,钉齿应在同一齿迹内均匀分布,即按多头螺旋线来排列钉齿。
螺线导程的计算公式为:
t=Ma (1)式中:o为齿迹距,mm;M为齿杆数,常取6-12。
一般情况下,齿杆数为螺线头数k的整数倍,即每个齿迹有k个齿通过。
因此,增加k的数量,有利于
提高生产率。
但生产实践表明,k值也不宜过大。
相邻齿在齿杆上距离的计算公式为:
B=Malk (2)
滚筒长度计算公式为:
L=a(Z/k-1)+2?, (3)式中:口为齿迹距,多为25-50 mm:Z为滚筒上钉齿总数,根据经验数据确定:?L为钉齿距齿杆端顶的距离,根据结构需要确定。
滚筒直径计算公式为:
D=Ms/w+ 2h (4)
式中:为钉齿高度;s为距杆间距。
齿距一般为50-100 mm。
经计算分析,确定o=40 mm;k =4;M=12个:B=120 mm;Z=120个;AL=50mm; L=1260 mm;h=40 mm;s=600 mm。
钉齿在脱粒腔整个宽度内合理排列,且轨迹应均匀分布,以保证物料不会瞬间被推向一侧,有利于转子的动静平衡。
钉齿采用螺旋排列方式,因为该种形式能够充分发挥每个钉齿的作用,并且有利于秸秆杂质和籽粒的轴向移动,从而有利于提高脱净率,有效防止秸秆在脱粒滚筒上的缠绕。
2.3凹板
凹板有组合式和整体式之分。
组合式凹板的包角大多为1000。
钉齿排数一般为4-6排,只在对难度比较大的粳稻脱粒时,才用6排。
凹板上的齿距为B’=2a=80 mm。
头排或头二排齿较稀,B "=4a= 160 mm(前后排齿交错排列。
滚筒钉齿与凹板钉齿的最大重合度一般为30-50 mm,齿端和齿侧的最小间隙不小于3 mm(稻、麦)。
脱粒间隙最大时,上下钉齿可完全脱开,没有重合度。
凹板弧面与滚筒齿端面的间隙由大变小。
钉齿滚筒的功率耗用略高于纹杆滚筒。
小麦脱粒时的单位喂人量平均功率耗用为3.7-4.4 kW/(kg/s)。
凹板上每增多一排齿,就会增加5%-15%功率耗用。
但排数
多,功率波动较小。
齿侧间隙大的脱粒装置,其功率耗用可比齿侧间隙小的减少20%-30%。
钉齿滚筒式脱粒装置对不均匀喂人的适应性较好,功率波动小。
综合分析各方面的因素,确定最大功率为平均功率的1.5倍。
改变滚筒与凹板之间的间隙大小,能调整搓擦的作用强度。
3结论
在滚筒脱粒装置的工作过程中,脱粒功率消耗在整机功率消耗中占较大比重(在脱粒机上约占70%,在联合收获机上占40%以上)。
其运转稳定与否直接决定脱粒和分离作业的质量。
本机采用钉齿滚筒式结构设计,利用打击搓擦与摩擦原理进行脱粒,喂人方式为切向,具有结构简单、体积小、质量轻、造价低、便于搬运、性能稳定可靠的特点,且脱粒、清选可同时完成。
另外,其在满足脱粒要求的同时,能保持脱粒后小麦完好,破碎率<3%,脱净率>95%。
班春华(辽宁省农业机械化研究所)
相关附件
相关新闻
,
2014-10-21
, 稻麦脱粒装置脱出物分布模型的三维数字仿真
,
2014-06-16
, 脱粒装置的结构及工作性能分析
,
2014-10-08
, 烘干设备的设计制造
,
2014-06-27
, 全喂入式花生摘果机摘果滚筒改进设计方案,
2005-11-21
, 微生物厌氧发酵装置的设计与施工技术要点。