海洋环境下热喷涂锌、铝及其合金涂层防腐蚀机理研究概况
锌铝合金涂层与有机涂层耐盐雾腐蚀性对比

锌铝合金涂层与有机涂层耐盐雾腐蚀性对比摘要研究了锌铝合金涂层与有机涂层的耐盐雾性能,在防腐涂层体系中,锌铝合金涂层的耐盐雾防腐性能好于有机涂层;而在防腐防污涂层体系中由于防污漆含有铜,锌铝涂层与铜离子可形成原电池加速腐蚀,锌铝合金涂层的防腐性能差于有机涂层体系。
宋雪曙(上海振华重工集团股份有限公司涂装技术应用研究所,上海200125)关键词:热喷涂;锌铝合金;有机涂层;耐盐雾;防腐;防污1引言金属锌、铝的电化学电位比铁低,在电化学防腐体系中发挥着重要的作用。
现在广泛应用的喷锌、喷铝及各种富锌漆对铁基体都有良好的电化学保护和屏蔽保护作用,其耐盐雾腐蚀性能高于只有屏蔽保护作用的纯有机涂层,可用于海洋环境中的长效重防腐蚀涂层体系。
采用热喷涂锌、铝及其合金涂层对钢铁构件和构筑物进行长效防护早在20世纪20年代就己开始应用。
随着经济的发展,人类在海洋中建造了无数固定与活动的海上钢铁构筑物,如舰船、风力发电、海底管线、栈桥码头、海上石油平台等,从20世纪中叶开始,世界各国在不同的海域对热喷涂锌铝及其合金涂层海洋环境下长期防护性能进行了很多现场挂片暴露试验和实际应用。
国内外的大量长期现场试验证明,热喷涂锌铝及其合金涂层对于海洋环境下的钢铁构筑物具有优良的长效防护性能,锌具有优良的电化学保护性,铝具有比锌更好的化学稳定性,锌铝合金既保留了锌的电保护特点,又具有铝的化学稳定性能。
特别是经过适当有机涂料封闭的喷锌、铝、锌铝合金的复合涂层对处于海洋大气和浪花飞溅区的海洋平台等海上钢铁设施是一种保护性较好的长效防腐方案。
2热喷涂技术2.1热喷涂技术原理热喷涂是借助某种热源(火焰或电能)将欲喷涂的金属材料(线材或粉末)熔化,利用压缩空气将金属熔滴雾化,高速喷射到经粗化处理的工件基体表面,熔滴在撞击到工件表面的瞬间冷凝而形成金属涂层。
涂层的组织结构是由互相镶嵌、重叠的无数变形微粒机械地结合在一起,并含有一定数量的孔隙结构。
电弧喷涂锌铝合金涂层的防腐机理和应用现状
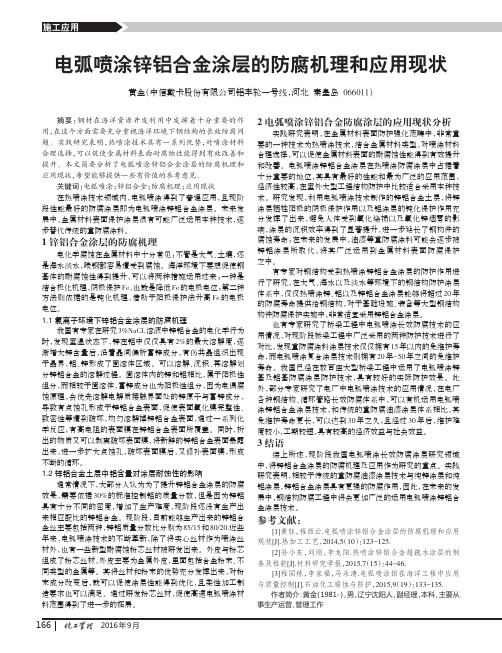
2016年9月电弧喷涂锌铝合金涂层的防腐机理和应用现状黄金(中信戴卡股份有限公司铝车轮一号线,河北秦皇岛066011)摘要:钢材在海洋资源开发利用中发挥着十分重要的作用,在这个方面需要充分重视海洋环境下钢结构的长效防腐问题。
实践研究表明,热喷涂技术具有一系列优势,对喷涂材料合理选择,可以促使金属材料表面耐腐蚀性能得到有效改善和提升。
本文简要分析了电弧喷涂锌铝合金涂层的防腐机理和应用现状,希望能够提供一些有价值的参考意见。
关键词:电弧喷涂;锌铝合金;防腐机理;应用现状在热喷涂技术领域内,电弧喷涂得到了普遍应用,且现阶段性能最好的防腐涂层即为电弧喷涂锌铝合金涂层。
未来发展中,金属材料表面保护涂层很有可能广泛运用本种技术,逐步替代传统的重防腐涂料。
1锌铝合金涂层的防腐机理电化学腐蚀在金属材料中十分常见;不管是大气、土壤,还是海水淡水,碳钢都容易遭受到腐蚀。
海洋环境下要想促使钢基体的耐腐蚀性得到提升,可以将两种措施运用过来;一种是结合极化机理,阴极保护Fe,也就是降低Fe的电极电位;第二种方法则依据的是钝化机理,借助于阳极保护法升高Fe的电极电位。
1.1氯离子环境下锌铝合金涂层的防腐机理我国有专家在研究3%NaCL溶液中锌铝合金的电化学行为时,发现室温状态下,锌在铝中仅仅具有2%的最大溶解度,逐渐增大锌含量后,沿着晶间偏析富锌成分,有伪共晶组织出现于晶界,铝、锌形成了固溶体区域。
可以溶解、沉积、再溶解划分锌铝合金的溶解过程。
固溶体内的锌和铝相比,属于阳极性组分,而相较于固溶体,富锌成分也为阳极性组分,因为电偶腐蚀原理,会优先溶解电解质接触界面处的锌原子与富锌成分,导致有点蚀孔形成于锌铝合金表面,促使表面氧化膜完整性、致密性等遭到破坏,均匀溶解掉锌铝合金表面,通过一系列化学反应,有高电阻的表面膜在锌铝合金表面所覆盖。
同时,析出的物质又可以剥离破坏表面膜,将新鲜的锌铝合金表面暴露出来,进一步扩大点蚀孔,破坏表面膜后,又修补表面膜,形成不断的循环。
海洋环境下热喷涂锌_铝及其合金涂层防腐蚀机理研究概况
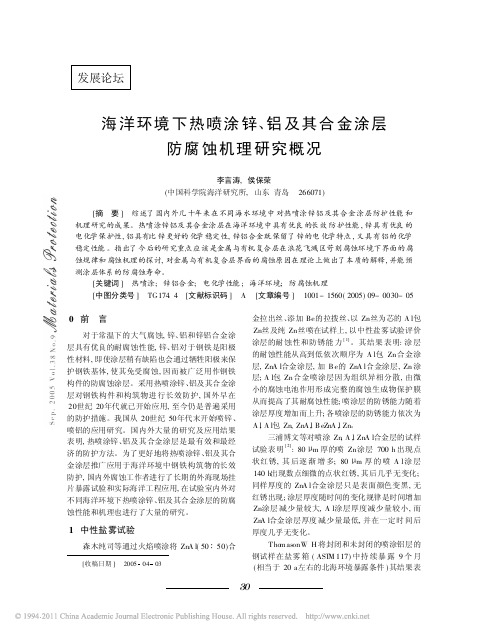
Shaw B A 等在钢基体和聚四氟乙烯基体分别 喷涂了 Zn, A ,l Zn 15%A l合金和 Zn 15%A l伪合 金 4种涂层, 将他们浸入人工海水 ( ASTMD I 141 75) 中, 监测涂层电位随时间的变化 [ 12 ] 。火焰喷铝 涂层的腐蚀电位与基体材料无关, 10 d后稳定在 - 800 50 mV ( vs SCE) 左右。暴露 30 a喷铝涂层 没有发生孔蚀。火焰喷锌涂层的腐蚀电位也与基 体材料无关, 几天后稳定于 - 1. 0 ~ - 1. 2 V 范围 内。锌铝合金及伪合金涂层的腐蚀电位与纯锌涂 层相同, 一周后稳定于 - 1. 02 V左右。
铃 木隆 三 等 测量 了 Zn, A l 及 ( 5% ~ 30% ) A l Zn合 金 喷涂 层 在 3% N aC l 溶 液 中 的 腐蚀 行 为 [ 13] 。认为不同铝含量的锌铝合金涂层自然腐蚀 电位及其随时间的变化与锌涂层非常接近, 与铝涂 层相差较大 ( - 50~ - 100 mV ) 。锌铝合金的自然 腐蚀电位随铝含量的增加而变正。
[关键词 ] 热喷涂; 锌铝合金; 电化学性能; 海洋环境; 防腐蚀机理 [中图分类号 ] TG174. 4 [文献标识码 ] A [文章编号 ] 1001- 1560( 2005) 09- 0030- 05
0前 言
对于常温下的大气腐蚀, 锌、铝和锌铝合金涂 层具有优良的耐腐蚀性能, 锌、铝对于钢铁是阳极 性材料, 即使涂层稍有缺陷也会通过牺牲阳极来保 护钢铁基体, 使其免受腐蚀, 因而被广泛用作钢铁 构件的防腐蚀涂层。采用热喷涂锌、铝及其合金涂 层对钢铁构件和构筑物进 行长效防护, 国外早在 20世纪 20年代就已开始应用, 至今仍是普遍采用 的防护措施。我国从 20世纪 50年代末开始喷锌、 喷铝的应用研究。国内外大量的研究及应用结果 表明, 热喷涂锌、铝及其合金涂层是最有效和最经 济的防护方法。为了更好地将热喷涂锌、铝及其合 金涂层推广应用于海洋环境中钢铁构筑物的长效 防护, 国内外腐蚀工作者进行了长期的外海现场挂 片暴露试验和实际海洋工程应用, 在试验室内外对 不同海洋环境下热喷涂锌、铝及其合金涂层的防腐 蚀性能和机理也进行了大量的研究。
铝合金在海洋环境中的防腐蚀技术研究进展
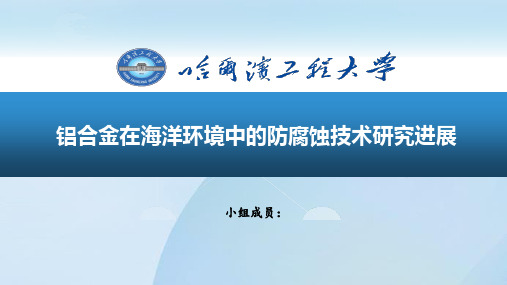
小组成员:
☞ 主要内容 :
1
背景介绍
2
铝合金在海洋环境中防腐蚀技术概述
3
铝合金微弧氧化膜表面原位生长LDH的研究
4
参考文献
1
背景介绍
随着海洋资源开发和国际战略新格局的显现,海洋工程用高性能结构材料 的研发已成为材料研究的热点问题之一。铝合金因具有密度低、比强度高等优 点被广泛应用于船舶和海洋工程领域。然而铝合金本身的硬度低、耐磨性较差
传统的有机涂料防护方式对于抑制铝合金涂层下点蚀的能力十分有限,通常需 要配合阳极氧化、微弧氧化或化学转化处理等来提高铝合金基体防护性能。
3
铝合金微弧氧化膜表面原位生长LDH的研究
研究背景
• 铝合金微弧氧化膜表面存在一定微孔和微裂纹,通常需封孔处理。 • 层状双金属氢氧化物(layer double hydroxide,LDH),水滑石类化合物 主 体由两种金属氢氧化物构成,其结构的灵活性和多样性赋予其优异的吸附性、 离子交换及耐腐蚀性能。
实验结果—低频阻抗模值随时间变化曲线
低频阻抗模值可以用来评 价膜层对基底材料的防护 性能,图中可以看出浸泡 过程中微弧氧化膜经NiAlLDH处理后低频模值有较 明显提高。
3
铝合金微弧氧化膜表面原位生长LDH的研究
实验结果—盐雾试验
MAO
MAO+ NiAl-LDH
0h
720h
1094h
3
铝合金微弧氧化膜表面原位生长LDH的研究
3
铝合金微弧氧化膜表面原位生长LDH的研究
实验结果—动电位极化曲线
微弧氧化铝合金表面NiAl-LDH 的生长抑制了阳极反应和阴极 反应,腐蚀电位正移,icorr 减 小,说明NiAl-LDH的生长提高 其耐蚀性,且随NiAl-LDH的生 长耐蚀性逐渐提高。 Nhomakorabea3
电弧喷涂锌铝合金涂层的防腐机理和应用现状

[ 2 】舒亮 , 包 志 坚 ,张爱 青 。一种 2 - ( 2 -噻吩基 )乙醇对
0 引言
电弧 喷 涂是 一 种较 为 常用 的热 喷 涂技 术 , 随 着 科学 技术 的不 断进 步 , 热喷 涂技 术也 取得 了一 定的 改进 与完善 , 并得 到 了越来越 广泛 的应用 , 其在 实际应用 过程 中表 现 出了不可替 代
王金 辉 ( 中信 戴卡 股份 有 限公 司 , 河北 秦 皇 岛 0 6 6 0 0 0 )
摘要 : 锌 铝合金 涂层是一种应用十分 广泛的防腐 手段 , 在金 属材 料表 面喷 涂锌 铝合 金涂层 , 可以对金属材料 实施有 效 的保护 , 能 够预 防金属材 料的腐蚀 , 从 而有利于延 长金属材 料的使用寿命 , 也有 利于减少金属 材料 的维护与保养成本。 电弧喷涂是一种较为 常用的热喷涂技术, 电弧喷涂锌 铝合金涂层是现 阶段防腐性能最 好的涂层之 一, 在我 国有 着 良好的发展 前景与广 阔的发展 空间。 本篇论文 中, 笔者主要 对 电弧喷涂锌铝合金涂层 的防腐机理进行 了 探 讨, 并分析 了电弧喷涂锌铝合金 涂层 的应用现状 , 以供 参考 。 关键 词 : 电弧喷涂 ; 锌 铝合金 涂层 ; 防腐机 理
金涂 层 中含有 锌 、 铝 以及微 量 的稀土 元素 , 相 比较 于常 规热 镀
锌, 热镀锌铝 合金涂 层的耐 大气腐蚀 特性较好 , 且 涂敷性 较好 ,
因此能够 使涂 层、 合金 层之 间的结 合长期保 持稳定 。
上接3 1 页( 文 章 题 目 :优 势 通 道 识 别 综 合 评 价 指 l 电弧喷 涂 锌铝合 金 涂层 的 防腐机 理 标体 系 在油 井 生产 管理 的 应用 ) 对 于金 属材料 来 说 , 最为 常见 的一种腐 蚀类 型便 是 电化
热喷涂高铝含量Zn-Al合金涂层热带岛礁大气环境腐蚀行为研究
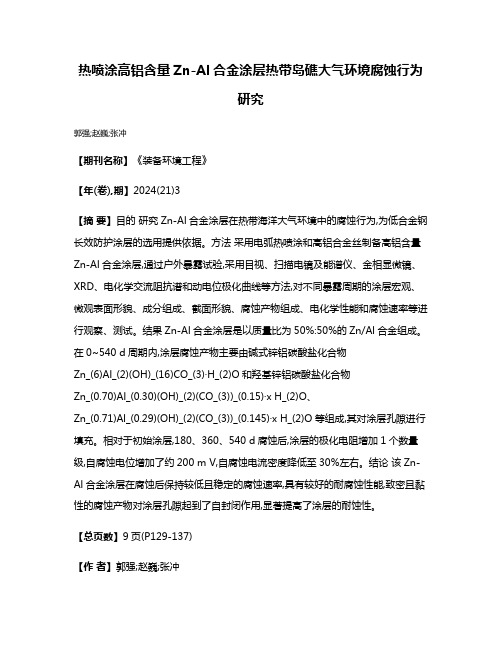
热喷涂高铝含量Zn-Al合金涂层热带岛礁大气环境腐蚀行为研究郭强;赵巍;张冲【期刊名称】《装备环境工程》【年(卷),期】2024(21)3【摘要】目的研究Zn-Al合金涂层在热带海洋大气环境中的腐蚀行为,为低合金钢长效防护涂层的选用提供依据。
方法采用电弧热喷涂和高铝合金丝制备高铝含量Zn-Al合金涂层,通过户外暴露试验,采用目视、扫描电镜及能谱仪、金相显微镜、XRD、电化学交流阻抗谱和动电位极化曲线等方法,对不同暴露周期的涂层宏观、微观表面形貌、成分组成、截面形貌、腐蚀产物组成、电化学性能和腐蚀速率等进行观察、测试。
结果Zn-Al合金涂层是以质量比为50%:50%的Zn/Al合金组成。
在0~540 d周期内,涂层腐蚀产物主要由碱式锌铝碳酸盐化合物Zn_(6)Al_(2)(OH)_(16)CO_(3)·H_(2)O和羟基锌铝碳酸盐化合物Zn_(0.70)Al_(0.30)(OH)_(2)(CO_(3))_(0.15)·x H_(2)O、Zn_(0.71)Al_(0.29)(OH)_(2)(CO_(3))_(0.145)·x H_(2)O等组成,其对涂层孔隙进行填充。
相对于初始涂层,180、360、540 d腐蚀后,涂层的极化电阻增加1个数量级,自腐蚀电位增加了约200 m V,自腐蚀电流密度降低至30%左右。
结论该Zn-Al合金涂层在腐蚀后保持较低且稳定的腐蚀速率,具有较好的耐腐蚀性能,致密且黏性的腐蚀产物对涂层孔隙起到了自封闭作用,显著提高了涂层的耐蚀性。
【总页数】9页(P129-137)【作者】郭强;赵巍;张冲【作者单位】北京机械设备研究所;空军装备部驻北京地区第一军事代表室【正文语种】中文【中图分类】TG172【相关文献】1.热喷涂高铝含量锌铝涂层的耐腐蚀性能研究2.2A97 铝锂合金热带海洋大气环境腐蚀行为3.2A97铝锂合金典型防护涂层热带海洋大气环境腐蚀老化行为4.Al含量对Zn-Al合金涂层电化学腐蚀行为的影响因版权原因,仅展示原文概要,查看原文内容请购买。
ZnAl牺牲阳极涂层模拟低温海洋环境的腐蚀行为研究的开题报告

ZnAl牺牲阳极涂层模拟低温海洋环境的腐蚀行为研
究的开题报告
1. 研究背景
海洋环境中,金属材料可能遭受严重的腐蚀,导致其寿命缩短并降低性能。
因此,了解和预测金属材料在海洋环境中的腐蚀行为对于制定有效的防止腐蚀措施至关重要。
牺牲阳极涂层是一种有效的防止腐蚀方法,但其在低温海洋环境中的应用和腐蚀行为尚未得到充分研究。
2. 研究目的
本研究旨在探究ZnAl牺牲阳极涂层在模拟低温海洋环境中的腐蚀行为,并分析其防腐蚀性能和腐蚀机制,为金属材料在低温海洋环境中的防腐蚀提供参考。
3. 研究内容
3.1 实验设计
在控制温度、盐度等参数的条件下,采用模拟海洋环境的方法进行腐蚀实验,观察ZnAl牺牲阳极涂层在不同时间段内的腐蚀情况。
3.2 实验步骤
(1)制备ZnAl牺牲阳极涂层试样;
(2)将试样置于模拟海洋环境中,进行腐蚀实验;
(3)每隔一段时间取出试样,观察其腐蚀情况;
(4)对实验结果进行分析,并基于实验结果探究腐蚀机制。
3.3 预期结果
预计ZnAl牺牲阳极涂层在低温海洋环境中的防腐蚀性能较好,随着腐蚀时间的增加,腐蚀程度会逐渐增加。
同时,本研究还将探究腐蚀机制,为制定有效的防腐蚀措施提供理论支持。
4. 研究意义
本研究将探究ZnAl牺牲阳极涂层在低温海洋环境中的腐蚀行为,为金属材料在海洋环境中的腐蚀控制提供实验数据和理论基础。
对于优化海洋工程、海洋运输等领域的金属材料的使用、设计和维护具有重要的现实意义和应用价值。
新型防腐蚀涂层在海洋工程中的应用研究
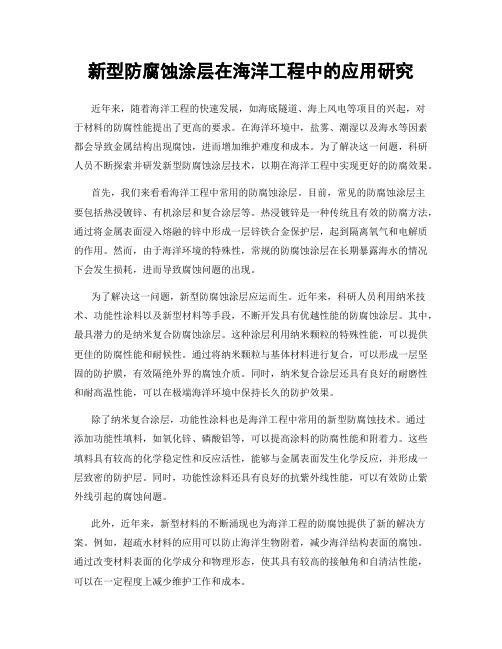
新型防腐蚀涂层在海洋工程中的应用研究近年来,随着海洋工程的快速发展,如海底隧道、海上风电等项目的兴起,对于材料的防腐性能提出了更高的要求。
在海洋环境中,盐雾、潮湿以及海水等因素都会导致金属结构出现腐蚀,进而增加维护难度和成本。
为了解决这一问题,科研人员不断探索并研发新型防腐蚀涂层技术,以期在海洋工程中实现更好的防腐效果。
首先,我们来看看海洋工程中常用的防腐蚀涂层。
目前,常见的防腐蚀涂层主要包括热浸镀锌、有机涂层和复合涂层等。
热浸镀锌是一种传统且有效的防腐方法,通过将金属表面浸入熔融的锌中形成一层锌铁合金保护层,起到隔离氧气和电解质的作用。
然而,由于海洋环境的特殊性,常规的防腐蚀涂层在长期暴露海水的情况下会发生损耗,进而导致腐蚀问题的出现。
为了解决这一问题,新型防腐蚀涂层应运而生。
近年来,科研人员利用纳米技术、功能性涂料以及新型材料等手段,不断开发具有优越性能的防腐蚀涂层。
其中,最具潜力的是纳米复合防腐蚀涂层。
这种涂层利用纳米颗粒的特殊性能,可以提供更佳的防腐性能和耐候性。
通过将纳米颗粒与基体材料进行复合,可以形成一层坚固的防护膜,有效隔绝外界的腐蚀介质。
同时,纳米复合涂层还具有良好的耐磨性和耐高温性能,可以在极端海洋环境中保持长久的防护效果。
除了纳米复合涂层,功能性涂料也是海洋工程中常用的新型防腐蚀技术。
通过添加功能性填料,如氧化锌、磷酸铝等,可以提高涂料的防腐性能和附着力。
这些填料具有较高的化学稳定性和反应活性,能够与金属表面发生化学反应,并形成一层致密的防护层。
同时,功能性涂料还具有良好的抗紫外线性能,可以有效防止紫外线引起的腐蚀问题。
此外,近年来,新型材料的不断涌现也为海洋工程的防腐蚀提供了新的解决方案。
例如,超疏水材料的应用可以防止海洋生物附着,减少海洋结构表面的腐蚀。
通过改变材料表面的化学成分和物理形态,使其具有较高的接触角和自清洁性能,可以在一定程度上减少维护工作和成本。
综上所述,新型防腐蚀涂层在海洋工程中的应用研究十分重要。
海洋平台的腐蚀及防腐技术

海洋平台的腐蚀及防腐技术化学化工学院装控131 杨哲 1304310125摘要:概括了海洋平台不同区域的腐蚀环境和腐蚀规律,对海洋平台重防腐涂料的选择要求及配套体系进行简要叙述。
针对海洋平台的长效防腐防护要求,介绍了几种具有长效的防腐材料和防腐技术特点,包括海洋平台热喷涂长效防腐蚀技术、锌加保护技术、海洋平台桩腿防腐套包缚技术等,为我国对海洋平台长效防腐防护技术的研究提供参考。
关键词:海洋平台;防腐;热喷涂;锌加技术;防腐套Abstract:This paper summarizes the corrosion environment and rules of the differentzones in offshore platforms, also briefly introduces the requirements and systems of the anticorrosion coating .According to the long-term anticorrosion requirements in offshore platforms, the paper introduces several long-term anticorrosion technology, including thermal spraying, adding zinc protection and anticorrosion technology with platform legs wrapped etc,which will provide some references to the research of the long-term anticorrosion technology in offshore platforms.Key words:Offshore platform;anticorrosion; Thermal spraying; Adding zinc technology; Anticorrosion wrap海洋平台是一种海上大型工程结构物。
16Mn钢热浸镀ZnAl合金镀层在海水中应力腐蚀行为研究
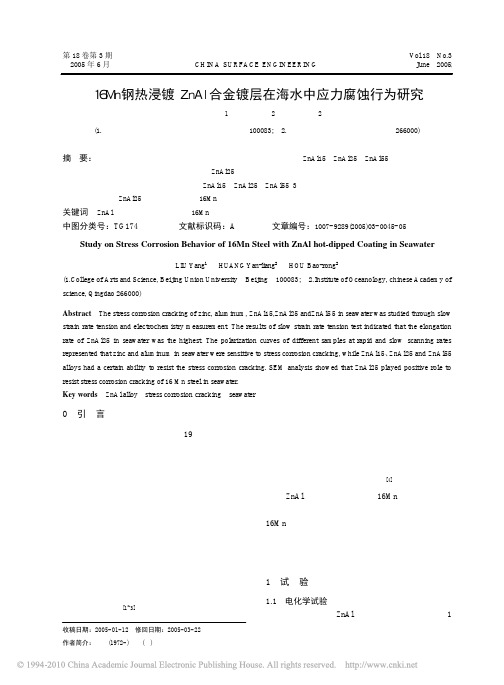
中 国 表 面 工程
刘 洋,等:C1H6MINnA钢S热U浸RF镀ACZEnAElN合G金IN镀E层ER在IN海G水中应力腐蚀行为研究
Vol.18 No.3 June 20045
16Mn 钢热浸镀 ZnAl 合金镀层在海水中应力腐蚀行为研究
刘 洋 1,黄彦良 2,侯保荣 2
2.6 97.4 0.075×10-3
15 <85
<10-6
25 <75
<10-6
55 <45
<10-4
<10-4
1.2 慢应变速率拉伸试验 利用慢应变速率试验技术来确定各种合金镀
层的应力腐蚀敏感性。试验中拉伸试验采用的材料 是镀有 ZnAl 合金的 16Mn 钢,16Mn 钢的化学成分 和机械性能如表 3 和表 4 所示,镀层的主要成分如 表 1 所示。慢应变速率拉伸机为西德产 K- S- M021 试验机,拉伸试样如图 2 所示。试验机横梁运动速 度为 2.5×10-5 mm/s,拉伸的应变速率为 1.66×10-6 s-1,所有试样的初始载荷均为 50 kg。
成分 含量/(g/kg)
溶液中含量/(mol/kg)
表 2 海水成份
Table 2 NaCl 24.7
The composition of seawater
MgCl2·6H2O
Na2SO4·10H2O
13
9.0
0.478Na+
0.064Mg 2+
0.550Cl-
H2O 954 0.028SO4 2-
100 mV 的电位阴极极化 5 min,再进行极化曲线的 测量。
表 1 ZnAl 合金电极成份(w/%)
海洋环境热喷涂铝复合涂层保护机理分析

d e td t a ddt 3 h e e = n f rt pc alr fc aig iae h ta i wi le k y ra o o y ia fiu e o o tn y s , , l Ke r s au n y wo d : ] mi mn; t  ̄ , p yn h ' a s m Jg; c mp st o t g; p oe t n; mai ee vrn n ml o o i c ai e n rtci o rn n i me t o
a d L ̄e- n ' rRmn n tss ln t h f c feti l n lp tc in o l miu c mp st o tn Re ut n s a e t .ao g wi t eef to l r l h e v o me tot r e to fau n m o o i c aig o e s l i- s
维普资讯
第 3 5卷 第 6 期 2 0 年 6月 02
材
料
保
护
V 3 N0 6 5
MAT ER【 S P AL ROTE CH 0N
Jn 0 2 u .20
海 洋 环 境 热 喷 涂 铝 复合 涂 层 保 护 机 理 分 析
响 , 出酸 度 影 响 是 常 见保 护 失 效 的 主 要 原 因 得
[ 关键词 ] 铝 ; 热喷潦 ; 复合潦层 ; 保护 海洋环境 [ 中图分类 号] T 7 G144 [ 献标 识码 ] ^ 文 [ 文章编号 ] 10 一1 0 20 )6 0 1 —0 0 l 5 (02 0 — 0 4 2 6
i f r i r u t dte ef to i i ls i zt f o ) l miu y A m e a c .1 2 A f n o or s n p d c n h f c f rd t O tb l ai n n p 1 au n m b C i p d n e R , 7 ]N o c o o o a e a y 2 a i o  ̄ MR,
模拟深海环境中热喷涂铝涂层破损后的腐蚀行为

模拟深海环境中热喷涂铝涂层破损后的腐蚀行为S.Paul【摘要】热喷涂铝涂层(TSA)已经在海上应用了数十年,它们在减轻海水中钢结构的腐蚀的有效性也已经被证明多年.然而,很少会有工作报告TSA受损时的性能.而且,深海中受损TSA的性能数据几乎是不存在的.本文设法了解并解决这个知识缺口,研究并报道模拟深海环境中受损的TSA的腐蚀性能.钻取样品面积的3%使基体碳钢暴露,整体样品放置于5℃,50MPa的高压釜中30天,釜内充满人造海水模拟5000m水压.试验后,检查试样的结果表明,在裸露的钢表面形成了石灰质沉淀,并没有明显的钢被腐蚀的产物.石灰质沉淀详细的微观结构表征证实有轻微钙基材料的镁基保护层的形成.因此,我们可以得出这样的结论:在深海环境下,即使TSA损坏依旧可以保护碳钢.【期刊名称】《热喷涂技术》【年(卷),期】2017(009)002【总页数】7页(P48-53,58)【关键词】热喷涂铝涂层;深海环境【作者】S.Paul【作者单位】英国剑桥【正文语种】中文【中图分类】TG174.4热喷涂铝涂层(TSA)对海水中钢结构提供长期的腐蚀保护[1-2]。
它的低腐蚀率加上其作为一个均匀分布的阳极的能力,使它非常适合这样的应用[3-5]。
铝作为阳极为海水中的碳钢提供保护,使得任何裸露的钢都形成了石灰质沉淀[6]。
沉淀有效的减少了阴极面积,从而降低腐蚀速率[7]。
在实验室和现场的长期研究中,海洋环境中的TSA保护钢的性能已被广泛的研究[2/8-10]。
众所周知,TSA在常温和高温下有能力对钢结构提供一定程度的阴极保护,即使TSA损坏时也是如此[5-7]。
同时也探索了它对没有阴极保护的海水中的钢结构的行为[5]。
此外,海水中石灰质沉淀的形成机理也一直在研究[4/9-11]。
例如温度,pH值和海水中存在的各种离子等参数的影响已经被研究。
尽管在这个方面已经有一些论文发表,但是到目前为止,石灰质沉淀的形成的探究集中在环境压力暴露方面,特别是环境温度上。
金属材料的海洋腐蚀与防护(第7章)铝及铝合金在海洋环境中的腐蚀
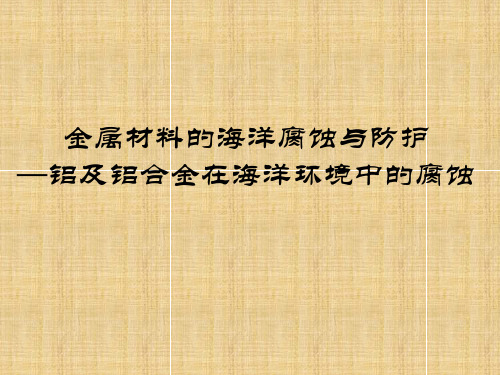
第一节 概述
• 通常铝的氧化膜的形成有几个阶段: • 第一阶段,非晶型氢氧化铝Al(OH)3; • 第二阶段,单铝水化物或正菱型—水软铝石
γ—AlO(OH)或γ—Al2O3·3H2O; • 第三阶段,3个结晶水的单楔型贝叶石β-
Al2O3·3H2O。
第一节 概述
• 氢氧化铝在一般条件下是胶状类物质,不 能抵御水和潮湿空气的腐蚀,而晶体氧化 铝能使金属表面有效钝化,使之不受腐蚀。 但海水中的氯离子,能破坏铝表面的钝化 膜,引起材料的点蚀等。
第三节 铝及铝合金在潮差区的腐蚀
一、工业纯铝和锻铝 • 工业纯铝L4M、L3M在海水潮差区的耐蚀性
较差,锻铝LD2CS的耐蚀性较差,如图7-5、 7-6.
第三节 铝及铝合金在潮差区的腐蚀
二、防锈铝 • 防锈铝LF2Y2、LF6M(BL)、LF11M、LF21M、
180YS在海水潮差区的耐蚀性较好。
第二节 铝及铝合金在全浸区的腐蚀
• 两种材料在青岛进行了16a的暴露试验, 16a时点蚀深度明显增大。与防锈铝的点蚀 深度相当,之所以会发生这种情况同包铝 层有关。
第二节 铝及铝合金在全浸区的腐蚀
• 包铝层(纯铝)的腐蚀电位比基体负100mV 以上,包铝层与基体形成电偶,在腐蚀过 程中,包铝层作为阳极,基体作为阴极, 基体得到保护,包铝层一旦腐蚀完,基体 由于失去了阴极保护腐蚀变得严重。
第二节 铝及铝合金在全浸区的腐蚀
• 表7-6列出了不同表面状态的3种防锈铝和锻 铝在舟山海域全浸区的暴露结果。
第二节 铝及铝合金在全浸区的腐蚀
• 表7-7列出了不同表面状态的180YS和LF3M 在青岛、厦门和榆林海域全浸区的暴露试 验结果。从表中可以看出,不同表面状态 对防锈铝合金海水腐蚀行为可产生不同程 度的影响。其影响的程度受到海水介质对 铝合金腐蚀苛刻性的制约。
研究海上风电设备腐蚀机理及现状

研究海上风电设备腐蚀机理及现状标题:研究海上风电设备腐蚀机理及现状导言:海上风电作为一种新兴的清洁能源发电方式,已在全球范围内得到广泛应用。
然而,由于海洋环境的特殊性,海上风电设备面临着严峻的腐蚀问题。
本文将深入探讨海上风电设备腐蚀机理,并总结现有腐蚀控制技术和未来的发展方向。
一、腐蚀机理1.1 介电腐蚀介电腐蚀是海上风电设备腐蚀的主要机理之一。
在海洋环境中,风力涡轮机塔筒、转子叶片等金属部件容易发生介电腐蚀,导致金属表面出现氧化、溶解和脱落等问题。
1.2 填隙腐蚀填隙腐蚀是另一种常见的海上风电设备腐蚀机理。
由于海水在风力涡轮机设备的密封接口、焊缝和螺栓孔等处会聚集,形成填隙环境,使金属表面容易受到腐蚀破坏。
1.3 微生物腐蚀微生物腐蚀是海洋环境中一种常见的风电设备腐蚀机理。
海洋中的微生物可以通过代谢产生化学物质,对金属表面产生腐蚀作用,加速金属的氧化和溶解。
二、腐蚀控制技术现状2.1 金属涂层技术金属涂层技术是一种常用的腐蚀控制技术,可以通过在金属表面形成一层保护膜来防止腐蚀。
目前,热浸镀锌、热喷涂和电镀等技术在海上风电设备上得到广泛应用。
2.2 阳极保护技术阳极保护技术利用金属阳极或外加电流,使金属表面形成一层保护膜,从而抑制腐蚀的发生。
海上风电设备中常见的阳极保护技术包括牺牲阳极和印流阳极。
2.3 轻金属合金技术轻金属合金技术被广泛应用于海上风电设备的金属部件中,通过合金化改变金属的化学成分和微观结构,提高其抗腐蚀性能。
铝合金、镁合金和钛合金等被认为是具有良好抗腐蚀性能的轻金属合金。
三、未来发展方向3.1 新型涂层技术新型涂层技术将成为未来海上风电设备腐蚀控制的重要发展方向。
纳米涂层、多层涂层和复合涂层等技术不仅可以提高涂层的耐腐蚀性能,还可以改善涂层的耐磨性和耐久性。
3.2 生物防污技术生物防污技术可以减少海上风电设备表面的海藻、藤壶、贻贝等生物附着,从而减少腐蚀的发生。
超声波清洗、抗生物膜涂层和生物防污剂等技术正在被研发和应用。
海洋环境下热喷涂铝基涂层的生物腐蚀行为研究
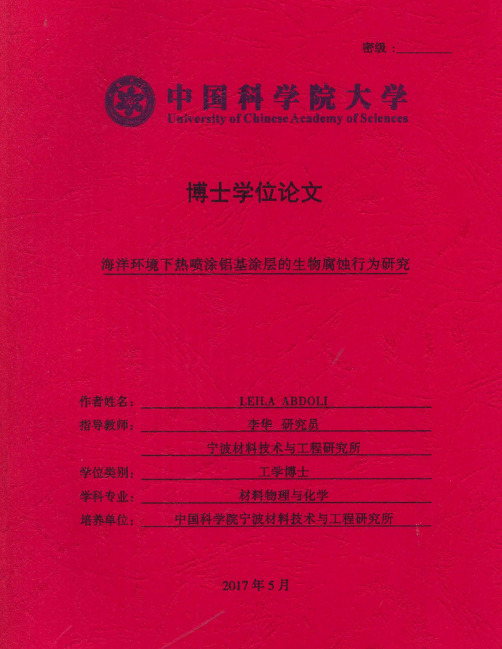
密级:博士学位论文海洋环境下热喷涂铝基涂层的生物腐蚀行为研究作者姓名:LEILA ABDOLI指导教师: 李华研究员宁波材料技术与工程研究所学位类别: 工学博士学科专业: 材料物理与化学培养单位: 宁波材料技术与工程研究所2016 年 11 月BIOCORROSION BEHAVIORS OF THERMAL SPRAYED BAS-ED COATINGALUMINUMSEAWATERSSYNTHETICINByLEILA ABDOLIA dissertation submitted toUniversity of Chinese Academy of Sciencesin partial fulfillment of the requirementfor the degree ofDoctor of Philosophy (Ph.D.)Ningbo Institute of Materials Technology and EngineeringChinese Academy of SciencesNovember, 2016摘要海洋环境中,金属材料表面发生化学或/和电化学腐蚀是长期困扰海上设施的问题之一,而腐蚀介质中微生物的存在使这一问题更加复杂化。
对大多数金属材料而言,比如海洋环境中常用的不锈钢316L,贴附在其表面的微生物的活动会破坏它们的机械、物理和化学性能。
近年来,众多研究人员试图通过优化海洋涂层来防止海洋生物污损和腐蚀。
热喷涂无机涂层已经被成功用于海洋设施表面,并实现了免维护、长期有效服役。
涂层表面的微生物膜的形成必然会影响涂层的抗腐蚀性能。
目前为止,热喷涂涂层的海洋生物腐蚀机制鲜有报道。
本课题选取不锈钢316L和热喷涂铝基涂层作为典型海洋材料来研究细菌在涂层表面的贴附行为。
此外,还进一步探索pH、温度、培养时间、表面形貌和水动力条件等不同环境因素的影响。
本课题共包括4个紧密相关的研究内容。
热浸镀锌及锌铝合金镀层在模拟海洋大气环境中腐蚀行为的电化学研究
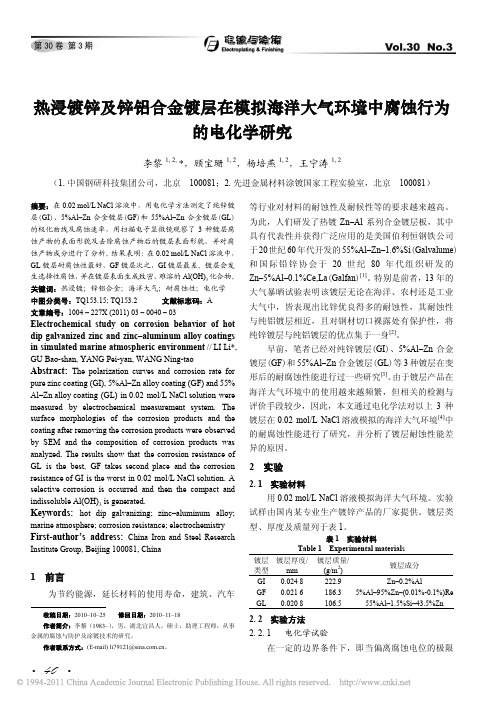
analyzed. The results show that the corrosion resistance of
GL is the best, GF takes second place and the corrosion
resistance of GI is the worst in 0.02 mol/L NaCl solution. A
层(GI)、5%Al–Zn 合金镀层(GF)和 55%Al–Zn 合金镀层(GL)
的极化曲线及腐蚀速率,用扫描电子显微镜观察了 3 种镀层腐
蚀产物的表面形貌及去除腐蚀产物后的镀层表面形貌,并对腐
蚀产物成分进行了分析。结果表明:在 0.02 mol/L NaCl 溶液中,
GL 镀层耐腐蚀性最好,GF 镀层次之,GI 镀层最差。镀层会发
热浸镀锌及锌铝合金镀层在模拟海洋大气环境中腐蚀行为 的电化学研究
李黎 1, 2, *,顾宝珊 1, 2,杨培燕 1, 2,王宁涛 1, 2
(1.中国钢研科技集团公司,北京 100081;2.先进金属材料涂镀国家工程实验室,北京 100081)
摘要:在 0.02 mol/L NaCl 溶液中,用电化学方法测定了纯锌镀
surface morphologies of the corrosion products and the
coating after removing the corrosion products were observed
by SEM and the composition of corrosion products was
pure zinc coating (GI), 5%Al–Zn alloy coating (GF) and 55%
金属喷涂层在海水中的腐蚀研究
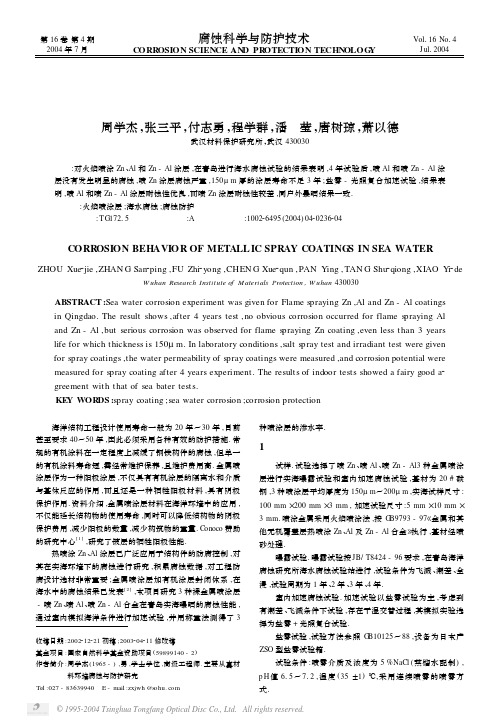
Zn
fart hing lime worms ,multiple t hick and loose red rusts.
tide range
Al
bestrewed by barnacles ,oysters and green algae surface. Wit hout significant corrosion
收稿日期 :2002212221 初稿 ;2003204211 修改稿 基金项目 :国家自然科学基金资助项目 (59899140 - 2) 作者简介 :周学杰 (1965 - ) ,男 ,学士学位 ,高级工程师. 主要从事材
料环境腐蚀与防护研究 Tel :027 - 83639940 E - mail :zxjwh @sohu. com
测量喷涂层孔隙率的试验. 方法参 见 ASTMD1653 79. 将待测涂层的分离膜固定在渗水的杯口上 ,并一起放在 干燥的气氛中 ,每隔 24 小时称重一次 ,直至失重达到恒定. 试验条件 ,恒温 25 ℃,渗透杯内外湿度差为 70RH ,对不同膜 厚的喷 Zn 、喷 Al 、喷 Zn - Al 游离膜进行测试.
第 16 卷 第 2004 年 7
4期 月
CO RROS IO N
腐蚀科学与防护技术
SCIENCE AND PROTECTION
- 1、下载文档前请自行甄别文档内容的完整性,平台不提供额外的编辑、内容补充、找答案等附加服务。
- 2、"仅部分预览"的文档,不可在线预览部分如存在完整性等问题,可反馈申请退款(可完整预览的文档不适用该条件!)。
- 3、如文档侵犯您的权益,请联系客服反馈,我们会尽快为您处理(人工客服工作时间:9:00-18:30)。
P等将火焰喷涂和电弧喷涂的铝涂
层浸渍于常温(8℃)和高温(60℃)的天然海水 中,发现在暴露最初的两周内涂层电位不稳定,变 化没有规律,直至4周后才达到稳定电位;没有空
于…940
一1 200
白区的火焰喷铝涂层的自由腐蚀电位在常温下位
980
mV(Ag/AgCl)之间,随着涂层表
面温度的上升,涂层的自由腐蚀电位变得更负,涂 层的自由腐蚀电位在80℃海水中暴露初期可低至 mV,2个月后,增加至相对稳定的一1
涂层均呈现最佳的防锈能力。封孔处理的各种喷 涂层的防锈能力为:铝涂层>锌铝合金涂层>锌涂 层。 胡传忻等按照GB 6458—86对火焰喷涂与电 弧喷涂锌铝涂层及封闭后涂层(封闭剂为OH:厚 浆型环氧煤沥青防腐漆)的防腐蚀性能进行了评 价∞J,试验结果为: (1)火焰喷涂铝试样8 h后表面出现不均匀 深褐色斑点,24 h开始增多,48 h后试样表面呈灰 褐色,264 h表面未见红斑; (2)火焰喷涂锌试样24 h后表面出现不均 匀白锈,48 h后逐渐增多,72 h后近边缘处出现浅 黄色透迹,144 h后中间也出现锈点,264 h基本不 扩展; (3)电弧喷涂铝试样8 h后表面出现均匀浅 灰褐色,随着时间的延长,无明显变化,264 h表面 未出现红锈; (4)电弧喷涂铝试样+封闭剂264 h表面完 好; (5)电弧喷涂锌试样+封闭剂24 h后出现 一处气孔,72 h出现一个鼓泡(约5 mm),96 h后 气孔中流出白色锈迹,264 h表面均出现气泡。 迁野文三使用火焰喷涂zn,AI,ZnAI合金涂层 的试样,经环氧树脂和硅树脂封闭后按JIS 进行了3
稳定性能。指出了今后的研究重点应该是金属与有机复合层在浪花飞溅区苛刻腐蚀环境下界面的腐 蚀规律和腐蚀机理的探讨,对金属与有机复合层界面的腐蚀原因在理论上做出了本质的解释,并能预 测涂层体系的防腐蚀寿命。
[关键词]
热喷涂;锌铝合金;电化学性能;海洋环境;防腐蚀机理
A[文章编号] 1001—1560(2005)09—0030—05
000 Z-237
H等将有64 mm宽空白区的喷涂试样
在试验室内进行了两年的浸渍暴露试验,结果表 明,如果有一种良好的电解质存在且所喷涂金属层 面积比合适,那么阴极保护对整个空白区都是有效 的‘7|。
Steffens H
D在研究火焰喷涂层阴极保护的过
程中观察到火焰喷铝涂层自由腐蚀电位为
一900
mV(VS SCE),将部分表面喷涂铝覆盖层的
(I)根据喷涂层重量变化观察未封闭的喷锌 涂层的腐蚀状况可分为初期增重、失重较少、失重 激增和重量几乎不变4个阶段。未封闭的喷铝涂 层和喷锌铝合金涂层的腐蚀状况可分为初期增重 至轻微失重、增重较少和重量几乎不变3个阶段。 防腐蚀性能为铝涂层>锌铝涂层>锌涂层; (2)喷锌涂层的耐蚀性优于热浸锌层及无机 富锌漆;
万方数据
海洋环境下热喷涂锌、铝及其合金涂层防腐蚀机理研究概况
高电位为一712 mV(VS SCE)和一715 mV(VS SCE),这时,电流从封闭和未封闭喷铝涂层试样流 向裸钢,试样的电流分别为3.0 mA(600 mA/m2) 和3.6 mA(700 mA/m2),使大部分钢表面很快极 化。硅封闭的喷铝涂层试样比未封闭试样产生的 电流小。随着暴露时间的增加,这些试样的电位逐 渐负移至一850 mV和一907 mV。钢表面的阴极电 流逐渐下降,同时未封闭的涂层产生的电位更负。 因此,由于涂层破损而暴露的钢表面从周围的火焰 喷铝涂层(包括封闭和未封闭的)得到阴极保 护‘引。 当试验温度降低时,增加了海水中的溶解氧, 使喷铝涂层的电位立刻正移,不过仍处于保护范 围,所以喷铝涂层在较热温度的海水环境要比较冷 的海水环境提供更好的阴极保护。
mV。 000
A等在钢基体和聚四氟乙烯基体分别
将铝和铝镁涂层阴极极化到一1
mV所需
喷涂了zn,A1,zn一15%Al合金和zn.15%Al伪合 金4种涂层,将他们浸入人工海水(ASTMDI.141— 75)中,监测涂层电位随时间的变化¨2|。火焰喷铝 涂层的腐蚀电位与基体材料无关,10 d后稳定在
一800-4-50
妒痧痧驴移移抄匈
8发展论坛2 钐、:蓉》、:2孑、、:2护-、:2予-、驴、护圆
海洋环境下热喷涂锌、铝及其合金涂层 防腐蚀机理研究概况
李言涛。侯保荣 (中国科学院海洋研究所,山东青岛266071) [摘 要] 综述了国内外几十年来在不同海水环境中对热喷涂锌铝及其合金涂层防护性能和
机理研究的成果。热喷涂锌铝及其合金涂层在海洋环境中具有优良的长效防护性能,锌具有优良的 电化学保护性,铝具有比锌更好的化学稳定性,锌铝合金既保留了锌的电化学特点,又具有铝的化学
厚度几乎无变化。
Thomason W
H将封闭和未封闭的喷涂铝层的
钢试样在盐雾箱(ASTMll7)中持续暴露9个月 (相当于20 a左右的北海环境暴露条件)其结果表
万方数据
海洋环境下热喷涂锌、铝及其合金涂层防腐蚀机理研究概况
明旧J:带有硅树脂封闭层的试样没有腐蚀的迹象, 但未封闭的喷铝涂层遭到了明显的破坏,但涂层下 的钢基体只受到轻微的破损;大部分破损出现在暴 露后期,如果在使用中涂层出现这类破损,那么将 会有时间维修涂层。同时未封闭的涂层能为飞溅 区环境中的钢表面提供保护。 植野军二等进行了封孔处理的zn,AI,ZnAl合 金喷涂层的盐雾试验H J。3种封孔剂对涂层的封 闭增长能力依次为:硅树脂>环氧树脂>聚四氟乙
(3)封闭处理的喷涂层与未封闭喷涂层的腐 蚀状况相比,封闭提高了喷涂层的防腐蚀性能; (4)用硅树脂封闭的喷铝涂层具有最佳的防 腐蚀性能。 因此,中性盐雾试验主要是对不同的锌铝喷涂 层的耐腐蚀性能进行了评价,其中硅树脂封闭的喷
铝涂层的耐腐蚀性能最好。
2浸渍试验
Spinder
烯树脂。使用硅树脂封孔处理的喷涂层不管何种
Fischer K
李守本等测量了zn一4.5%A1,Zn一15%A1,Zn一 30%Al,zn.55%Al和添加稀土元素的zn一55%Al 合金线材火焰喷涂涂层在天然海水的自然腐蚀电 位¨6|:随着合金中铝含量的增加,电位逐渐变正, 其中铝含量较低的zn一15%Al合金涂层的电位与 纯锌涂层相近,在一0.95一一1.02 V(VS SCE)之 间;铝含量较高的zn一55%Al合金涂层电位最正, 在一0.81~一0.94 V之间;喷涂试样电位总的变 化趋势是随时间的推移而变负,然后趋向平稳。 因此,利用浸渍试验主要是对不同的锌铝喷涂 层的耐海水腐蚀性能和阴极保护性能进行评价,喷 锌涂层可对钢铁基体提供良好的阴极保护,喷铝涂 层也对钢铁基体有一定的阴极保护作用,喷锌铝合 金涂层随着合金中铝含量的增加,电位逐渐变正,电 弧喷铝涂层对钢铁的保护能力不如火焰喷铝涂层。
试样在海水中浸泡60 d后,发现喷铝涂层对未喷 涂部分(或破损部位)提供了间接保护,其保护是 充分的,但比喷锌涂层差。同时研究了涂层的均一 性,并发现试样的电位是一致的,火焰喷涂铝覆盖
层提供了较长的使用寿命,不过一旦涂层受到破
坏,铝涂层提供的阴极保护将受到限制伸o。
Magone
M等观察到用金属丝喷涂的铝涂层,
0|。
h试验旧o,试验结果为:
中山直美等将喷锌和喷铝涂层的试样浸泡于 50℃、3%NaCl溶液中,观察到锌涂层的腐蚀减量几 乎随时间增加而直线上升,而铝涂层在形成铝氧化 膜后腐蚀基本停止了,喷铝涂层在盐水中的自然腐 蚀电位及铝表面氧化膜的形成与溶液的pH值、cl一 浓度和温度有关,但是在向溶液中充气使氧含量充 足时,上述因素不再影响喷铝涂层的腐蚀行为¨1|。 Thomason将两块封闭和两块未封闭的喷铝涂 层试样悬垂于ASTM海水中,试样刚浸人海水时最
金拉出丝、添加Be的拉拨丝、以zn丝为芯的A1包 zn丝及纯zn丝喷在试样上,以中性盐雾试验评价 涂层的耐蚀性和防锈能力¨J。其结果表明:涂层 的耐蚀性能从高到低依次顺序为Al包zn合金涂 层,ZnAl合金涂层,加Be的ZnAl合金涂层,zn涂 层;A1包zn合金喷涂层因为组织异相分散,由微 小的腐蚀电池作用形成完整的腐蚀生成物保护膜 从而提高了其耐腐蚀性能;喷涂层的防锈能力随着 涂层厚度增加而上升;各喷涂层的防锈能力依次为 Al,Al包Zn,ZnAl,BeZnAl,Zn。 三浦博文等对喷涂zn,A1,ZnAl合金层的试样 试验表明旧J:80¨m厚的喷zn涂层700 h出现点 状红锈,其后逐渐增多;80 txm厚的喷Al涂层
[中图分类号]TGl74.4[文献标识码]
0前言
对于常温下的大气腐蚀,锌、铝和锌铝合金涂 层具有优良的耐腐蚀性能,锌、铝对于钢铁是阳极 性材料,即使涂层稍有缺陷也会通过牺牲阳极来保 护钢铁基体,使其免受腐蚀,因而被广泛用作钢铁 构件的防腐蚀涂层。采用热喷涂锌、铝及其合金涂 层对钢铁构件和构筑物进行长效防护,国外早在 20世纪20年代就已开始应用,至今仍是普遍采用 的防护措施。我国从20世纪50年代末开始喷锌、 喷铝的应用研究。国内外大量的研究及应用结果 表明,热喷涂锌、铝及其合金涂层是最有效和最经 济的防护方法。为了更好地将热喷涂锌、铝及其合 金涂层推广应用于海洋环境中钢铁构筑物的长效 防护,国内外腐蚀工作者进行了长期的外海现场挂 片暴露试验和实际海洋工程应用,在试验室内外对 不同海洋环境下热喷涂锌、铝及其合金涂层的防腐 蚀性能和机理也进行了大量的研究。
Shaw B
白区和无空白区的电弧喷铝涂层,在60℃海水中 的腐蚀电位分别为一880 mV和一1
050
mV,而相
应的火焰喷涂层的腐蚀电位分别为一975 mV和
一1 010
mV;有空白区的电弧喷铝涂层试样的高极
化率表明,电弧喷铝涂层对钢铁的保护能力不如火 焰喷铝涂层¨4I。
Gartlaቤተ መጻሕፍቲ ባይዱd P
O将火焰喷涂的锌涂层、铝涂层以
及电弧喷涂的Al-5%Mg合金涂层试样浸入天然
海水中¨5|,锌涂层电位很快稳定于约一1