电弧喷涂锌铝涂层耐腐蚀实验报告
电弧喷涂锌铝合金涂层的防腐机理和应用现状
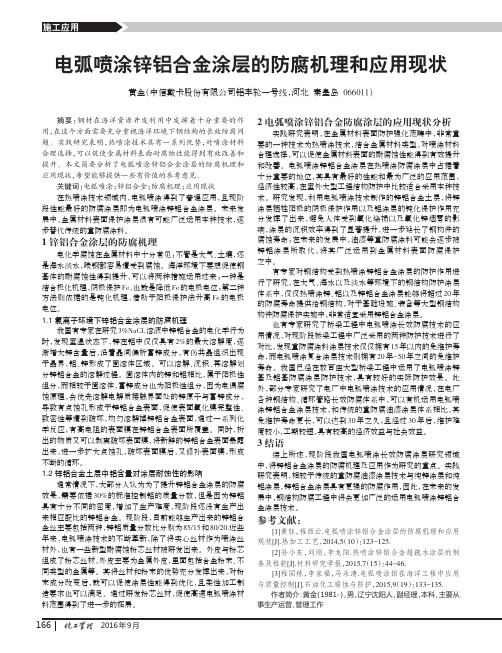
2016年9月电弧喷涂锌铝合金涂层的防腐机理和应用现状黄金(中信戴卡股份有限公司铝车轮一号线,河北秦皇岛066011)摘要:钢材在海洋资源开发利用中发挥着十分重要的作用,在这个方面需要充分重视海洋环境下钢结构的长效防腐问题。
实践研究表明,热喷涂技术具有一系列优势,对喷涂材料合理选择,可以促使金属材料表面耐腐蚀性能得到有效改善和提升。
本文简要分析了电弧喷涂锌铝合金涂层的防腐机理和应用现状,希望能够提供一些有价值的参考意见。
关键词:电弧喷涂;锌铝合金;防腐机理;应用现状在热喷涂技术领域内,电弧喷涂得到了普遍应用,且现阶段性能最好的防腐涂层即为电弧喷涂锌铝合金涂层。
未来发展中,金属材料表面保护涂层很有可能广泛运用本种技术,逐步替代传统的重防腐涂料。
1锌铝合金涂层的防腐机理电化学腐蚀在金属材料中十分常见;不管是大气、土壤,还是海水淡水,碳钢都容易遭受到腐蚀。
海洋环境下要想促使钢基体的耐腐蚀性得到提升,可以将两种措施运用过来;一种是结合极化机理,阴极保护Fe,也就是降低Fe的电极电位;第二种方法则依据的是钝化机理,借助于阳极保护法升高Fe的电极电位。
1.1氯离子环境下锌铝合金涂层的防腐机理我国有专家在研究3%NaCL溶液中锌铝合金的电化学行为时,发现室温状态下,锌在铝中仅仅具有2%的最大溶解度,逐渐增大锌含量后,沿着晶间偏析富锌成分,有伪共晶组织出现于晶界,铝、锌形成了固溶体区域。
可以溶解、沉积、再溶解划分锌铝合金的溶解过程。
固溶体内的锌和铝相比,属于阳极性组分,而相较于固溶体,富锌成分也为阳极性组分,因为电偶腐蚀原理,会优先溶解电解质接触界面处的锌原子与富锌成分,导致有点蚀孔形成于锌铝合金表面,促使表面氧化膜完整性、致密性等遭到破坏,均匀溶解掉锌铝合金表面,通过一系列化学反应,有高电阻的表面膜在锌铝合金表面所覆盖。
同时,析出的物质又可以剥离破坏表面膜,将新鲜的锌铝合金表面暴露出来,进一步扩大点蚀孔,破坏表面膜后,又修补表面膜,形成不断的循环。
电弧喷涂Zn-Al在油罐长效防腐中的应用研究

热喷涂层与有机涂层复合实现油罐长效防腐的研究1 本项目的目的意义金属材料的腐蚀遍及国民经济的各个领域,给国家带来了重大的经济损失。
腐蚀是从材料的表面开始的,因此很久以来人们就采用各种方法在钢铁表面形成各种保护层,以使易腐蚀的基体与外部腐蚀环境隔离。
最常用的防腐方法有涂料、金属镀层、热浸Zn 或Al 涂层以及使用耐腐蚀的金属和非金属材料等。
鉴于此,原油储罐主要采用的抗腐蚀技术措施是:涂装有机底漆,连接Zn块作为牺牲阳极,重点部件换用不锈钢材料等。
采取这些措施后,对于储罐防腐蚀有一定的效果,但油田使用后的腐蚀问题仍然相当严重。
油罐不同部位的腐蚀状况不同:水层与底泥层段钢板坑蚀穿孔,是原油储罐失效的最常见形式。
主要原因是该层段积聚了水中含有大量的富氧离子,成为较强的电解质溶液,产生化学腐蚀;加上油中固体杂质和油罐腐蚀产物大量沉积于罐底,它们与油罐罐底有不同的电极电位,这就形成了腐蚀电池,产生了电化学腐蚀。
加强对原油储罐腐蚀防护的研究,开发新型高效、经济合理的防腐技术,以减少泄漏事故的发生显得尤为重要,并且日益引起石油领域的关注。
2 热喷涂防腐的技术现状热喷涂技术自上世纪30 年代开始在防腐方面应用。
由于其对大型钢结构件有较好的现场施工性,工艺简单,防腐效果优异,可获得较厚的涂层,并可预计涂层的寿命,很快得到广泛重视,正日益取代油漆和热浸、电镀。
经过几十年的应用证明,热喷涂技术是钢铁结构件长效防腐的最好方法,这个结论已得到世界许多国家的政府和工业界所认可。
英国标准BS 5493:1977《钢铁结构防腐蚀保护层的使用规程》中指出,只有喷Zn、Al涂层才能保证在各种工业及海洋环境中维持20年而无需维护;美国焊接学会进行的19年腐蚀试验及LaQue腐蚀中心的34年海洋环境使用性能报告也有力地说明了在各种不利的环境下,Zn、Al 涂层长效防护的有效性。
目前用于防腐蚀的热喷涂技术主要有火焰喷涂和电弧喷涂两种。
国外在上世纪70年代后期逐渐成熟的电弧喷涂工艺具有速度快、喷涂效率高、能源利用率高、涂层性能好、施工周期短、现场施工方便等明显优越性,在钢铁构件长效防腐中应用广泛。
Zn(OH)2、Al(OH)3对锌、铝镀层腐蚀行为的影响的开题报告

Zn(OH)2、Al(OH)3对锌、铝镀层腐蚀行为的影响的开题报告题目:Zn(OH)2、Al(OH)3对锌、铝镀层腐蚀行为的影响摘要:本研究主要研究Zn(OH)2、Al(OH)3对锌、铝镀层腐蚀行为的影响。
通过利用多种表面分析技术来研究涂覆有Zn(OH)2、Al(OH)3的锌、铝镀层的腐蚀性能及微观形貌。
实验结果表明,涂覆了Zn(OH)2、Al(OH)3的锌、铝镀层比未经涂覆处理的锌、铝镀层具有更好的耐腐蚀性能。
同时,Zn(OH)2、Al(OH)3的使用对于减缓锌、铝镀层的腐蚀速率和减少腐蚀产物的形成有着显著的效果。
关键词:锌、铝镀层;Zn(OH)2、Al(OH)3;耐腐蚀性能;腐蚀产物一、研究背景锌和铝是常见的金属材料,广泛应用于制造工业和日常用品中。
锌、铝材料的耐腐蚀性是决定其使用寿命的关键因素之一。
然而,在特定工作条件下,锌、铝材料表面可能会发生腐蚀现象,导致减少其使用寿命和性能,因此有必要对其进行防腐处理。
Zn(OH)2、Al(OH)3是一种常用的防腐涂层材料,在许多工业中被广泛应用,可以有效防止金属表面的腐蚀。
然而,在实际应用中,锌、铝镀层的腐蚀防护效果与涂覆层的质量有直接关系。
因此,对于Zn(OH)2、Al(OH)3对锌、铝镀层腐蚀行为的影响研究具有重要的意义。
二、研究目的本研究旨在探究Zn(OH)2、Al(OH)3防腐涂层对于锌、铝镀层的腐蚀行为的影响,并研究其防腐效果的机理。
通过多种表面分析技术,研究不同涂覆层下锌、铝镀层的耐腐蚀性能、微观形貌以及腐蚀产物的组成。
三、研究方法1.材料制备锌、铝材料是由商业化供应商提供的,涂覆Zn(OH)2、Al(OH)3的锌、铝镀层由溶液法制备,溶液中的活性成分为ZnO、AlO(OH)等。
2.涂布及实验过程涂布方法采用浸涂法和喷涂法。
在涂布处理后,样品将进行腐蚀测试,腐蚀测试将在盐水溶液中进行,测试过程中将记录锌、铝材料及其涂覆层的质量减少情况,同时使用SEM/EDX、XRD等表面分析技术分析腐蚀产物和微观形貌以及腐蚀机理。
电弧喷涂锌铝合金涂层的防腐机理和应用现状

[ 2 】舒亮 , 包 志 坚 ,张爱 青 。一种 2 - ( 2 -噻吩基 )乙醇对
0 引言
电弧 喷 涂是 一 种较 为 常用 的热 喷 涂技 术 , 随 着 科学 技术 的不 断进 步 , 热喷 涂技 术也 取得 了一 定的 改进 与完善 , 并得 到 了越来越 广泛 的应用 , 其在 实际应用 过程 中表 现 出了不可替 代
王金 辉 ( 中信 戴卡 股份 有 限公 司 , 河北 秦 皇 岛 0 6 6 0 0 0 )
摘要 : 锌 铝合金 涂层是一种应用十分 广泛的防腐 手段 , 在金 属材 料表 面喷 涂锌 铝合 金涂层 , 可以对金属材料 实施有 效 的保护 , 能 够预 防金属材 料的腐蚀 , 从 而有利于延 长金属材 料的使用寿命 , 也有 利于减少金属 材料 的维护与保养成本。 电弧喷涂是一种较为 常用的热喷涂技术, 电弧喷涂锌 铝合金涂层是现 阶段防腐性能最 好的涂层之 一, 在我 国有 着 良好的发展 前景与广 阔的发展 空间。 本篇论文 中, 笔者主要 对 电弧喷涂锌铝合金涂层 的防腐机理进行 了 探 讨, 并分析 了电弧喷涂锌铝合金 涂层 的应用现状 , 以供 参考 。 关键 词 : 电弧喷涂 ; 锌 铝合金 涂层 ; 防腐机 理
金涂 层 中含有 锌 、 铝 以及微 量 的稀土 元素 , 相 比较 于常 规热 镀
锌, 热镀锌铝 合金涂 层的耐 大气腐蚀 特性较好 , 且 涂敷性 较好 ,
因此能够 使涂 层、 合金 层之 间的结 合长期保 持稳定 。
上接3 1 页( 文 章 题 目 :优 势 通 道 识 别 综 合 评 价 指 l 电弧喷 涂 锌铝合 金 涂层 的 防腐机 理 标体 系 在油 井 生产 管理 的 应用 ) 对 于金 属材料 来 说 , 最为 常见 的一种腐 蚀类 型便 是 电化
Zn-Al和Al-RE热喷涂涂层的耐蚀性研究

G P的 5 。因此 , D % 随着 经 济 的发展 , 效地 阻 止 或 效 和 最 经 济 的 方 法 。 为 对 比研 究 热 喷 涂 z — 1 有 n A 和
延缓钢结构腐蚀越来越迫切 。
A 一 E涂 层 的耐 蚀 性 , 者 考 察 了 两种 涂 层 在 铜 加 1R 笔
热 喷涂 锌 、 涂 层 自 2 世 纪 2 年 代 首 次 在 英 速 醋 酸 盐 雾 试 验 中 的 腐 蚀 行 为 并 探 讨 了其 腐 蚀 防 铝 0 0 国应 用 以来 , 到 了世 界 各 国 的高 度 重 视 并 沿 用 至 护 机 理 得
第7 卷
第6 期
装 备 环 境 工 程
E I ME T E V R N N A E G N E I G QU P N N I O ME T L N I E R N
2 1年 1月 00 2
Z — 和 AlR n AI — E热喷涂涂层 的耐蚀性研 究
梁义 , 魏世丞 刘毅 王玉江 徐滨士 , , ,
r s e tv l e p c ie y.Th ir tu t r e m c osr c u e ofZn— 1a d —RE o tngsbe o e a fe o r i n — n A1— A c a i f r nd a tr c roso we e a l z d b s a i g e e r ni r na y e y c nn n lcto c
Ke o ds Zn A1 o t g;A1 RE c ai g;CAS yw r : — ai c n 一 o t n S;c ro i nr ssa c o so e itn e
钢结 构 的腐蚀 与 防护 一直 备受 世界 各 国的关 注 今 16 3J , 。我 国从 2 世 纪 5 年 代 末 开 始 热 喷 涂 锌 、 0 0 铝
FBE、玻璃钢、电弧喷涂防腐层罐道耐磨试验报告

FBE、玻璃钢、电弧喷涂防腐层罐道耐磨试验报告
目的:本试验通过磨损试验的结果评定涂层的使用寿命。
试验方法:采用称重法来实现耐磨性能的评定。
称重法采
用试样在试验前后质量之差值来表示耐磨性能的评定方法,由于两试样间的磨损所引起的磨损量,可以采用精度达万
分之一克的DTG160分析天平上,称量出试样试验前后质量
之差来获得。
试验标准:GB/T 1768-2006 色漆和清漆耐磨性的测定旋
转橡胶砂轮法。
评判依据:MT/T5017-2011煤矿井筒装备防腐蚀技术规范
1、附录A,表A.1(热喷锌、铝)长效防腐涂层,涂层总
厚度≥250μm使用年限20年以上;
2、附录B,表B.2井筒装备常用的玻璃钢复合材料,涂层
厚度4mm使用年限20年以上。
试验结果:
1、矿用环氧树脂涂层(FBE)磨损失重0.036mg;
2、罐道用玻璃钢外覆材料磨损失重0.088mg;
3、电弧喷涂长效防腐涂层磨损失重0.143mg.
试验分析:玻璃钢耐磨损也是电弧喷涂长效防腐涂层的两
倍以上,但因玻璃钢涂层厚与钢材的膨胀比不同、挠度系
数也不同,玻璃钢使用的是不饱和聚酯树脂,与钢芯的结
合能力远不如环氧树脂,所以玻璃钢层容易出再脱壳现象,影响其使用寿命。
按电弧喷涂长效防腐涂层厚度≥250μm使用年限20年
计算,矿用环氧树脂涂层(FBE)厚度≥350μm使用年限为111年,保守使用也在40~50年。
超音速电弧喷涂锌铝合金涂层的制备及在海水中的腐蚀行为研究

超音速电弧喷涂锌铝合金涂层的制备及在海水中的腐蚀行为研究梁国;魏伟;王玉纯;贾传宝;张婧;常德春【摘要】This paper introduces the process and technology of preparing Zn-Al alloy coating by supersonic velocity arc spraying. The coating was tested by electrochemical methods. The results show Zn-Al coating play a sacrificial anode role in corrosion process, and there is passive film in the surface of Zn-Al coating after immersing. So the base alloys are effectively protected.%本文介绍了超音速电弧喷涂技术制备锌铝合金涂层的过程和工艺,对涂层进行了电化学测试。
结果表明合金涂层可以起到牺牲阳极的作用,同时浸泡一段时间之后合金涂层表面可以生成钝化膜。
锌铝涂层可以保护钢铁基体不被腐蚀。
【期刊名称】《全面腐蚀控制》【年(卷),期】2014(000)009【总页数】3页(P55-56,81)【关键词】超音速电弧喷涂;锌铝合金;腐蚀【作者】梁国;魏伟;王玉纯;贾传宝;张婧;常德春【作者单位】中国人民解放军济南军区72502部队,山东济南250330;中国人民解放军济南军区72502部队,山东济南250330;中国人民解放军济南军区72502部队,山东济南250330;山东省科学院海洋仪器仪表研究所,山东青岛266001;山东省科学院海洋仪器仪表研究所,山东青岛266001;中国海洋大学化学化工学院,山东青岛266100【正文语种】中文【中图分类】TG174.44近年来,国家积极推进海洋强国建设,不断提高海洋资源开发能力,发展海洋经济。
6061铝合金表面电弧喷涂纯铝涂层的研究
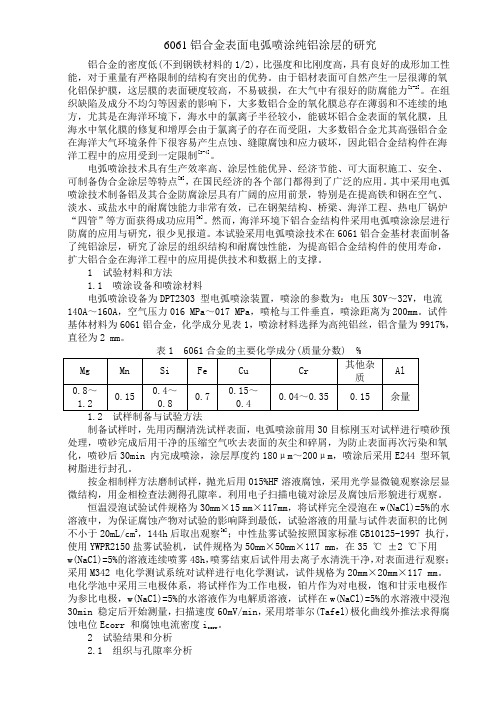
6061铝合金表面电弧喷涂纯铝涂层的研究铝合金的密度低(不到钢铁材料的1/2),比强度和比刚度高,具有良好的成形加工性能,对于重量有严格限制的结构有突出的优势。
由于铝材表面可自然产生一层很薄的氧化铝保护膜,这层膜的表面硬度较高,不易破损,在大气中有很好的防腐能力[1-2]。
在组织缺陷及成分不均匀等因素的影响下,大多数铝合金的氧化膜总存在薄弱和不连续的地方,尤其是在海洋环境下,海水中的氯离子半径较小,能破坏铝合金表面的氧化膜,且海水中氧化膜的修复和增厚会由于氯离子的存在而受阻,大多数铝合金尤其高强铝合金在海洋大气环境条件下很容易产生点蚀、缝隙腐蚀和应力破坏,因此铝合金结构件在海洋工程中的应用受到一定限制[3-4]。
电弧喷涂技术具有生产效率高、涂层性能优异、经济节能、可大面积施工、安全、可制备伪合金涂层等特点[5],在国民经济的各个部门都得到了广泛的应用。
其中采用电弧喷涂技术制备铝及其合金防腐涂层具有广阔的应用前景,特别是在提高铁和钢在空气、淡水、或盐水中的耐腐蚀能力非常有效,已在钢架结构、桥梁、海洋工程、热电厂锅炉“四管”等方面获得成功应用[6]。
然而,海洋环境下铝合金结构件采用电弧喷涂涂层进行防腐的应用与研究,很少见报道。
本试验采用电弧喷涂技术在6061铝合金基材表面制备了纯铝涂层,研究了涂层的组织结构和耐腐蚀性能,为提高铝合金结构件的使用寿命,扩大铝合金在海洋工程中的应用提供技术和数据上的支撑。
1 试验材料和方法1.1 喷涂设备和喷涂材料电弧喷涂设备为DPT2303 型电弧喷涂装置,喷涂的参数为:电压30V~32V,电流140A~160A,空气压力016 MPa~017 MPa,喷枪与工件垂直,喷涂距离为200mm。
试件基体材料为6061铝合金,化学成分见表1,喷涂材料选择为高纯铝丝,铝含量为9917%,直径为2 mm。
表1 6061合金的主要化学成分(质量分数) %制备试样时,先用丙酮清洗试样表面,电弧喷涂前用30目棕刚玉对试样进行喷砂预处理,喷砂完成后用干净的压缩空气吹去表面的灰尘和碎屑,为防止表面再次污染和氧化,喷砂后30min 内完成喷涂,涂层厚度约180μm~200μm,喷涂后采用E244 型环氧树脂进行封孔。
实验室电镀锌实验报告(3篇)

第1篇一、实验目的1. 了解电镀锌的基本原理和工艺流程。
2. 掌握电镀锌的实验操作方法和注意事项。
3. 熟悉赫尔槽的结构特点和使用方法。
4. 分析电镀锌过程中影响镀层质量的因素。
二、实验原理电镀锌是一种利用电解原理在金属表面镀上一层锌的工艺。
在电镀过程中,锌离子在阴极上得到电子还原成锌原子,沉积在工件表面形成镀层。
赫尔槽是一种用于电镀工艺试验的仪器,通过调节阴极与阳极的距离,使电流密度在阴极上形成梯度分布,从而研究镀液组分、添加剂、电流密度等因素对镀层质量的影响。
三、实验仪器与材料1. 仪器:赫尔槽、直流稳压电源、计时器、温度计、电极夹具、样品架、pH计、电导率仪等。
2. 材料:锌板、锌酸盐镀锌溶液、纯水、电解液、添加剂等。
四、实验步骤1. 准备赫尔槽:将赫尔槽清洗干净,并用纯水冲洗干净,确保无杂质。
2. 配制镀锌溶液:根据实验要求,配制一定浓度的锌酸盐镀锌溶液,并加入适量的添加剂。
3. 测量溶液参数:使用pH计和电导率仪测量镀锌溶液的pH值和电导率,确保溶液符合实验要求。
4. 安装电极:将锌板作为阴极,将纯锌作为阳极,分别固定在电极夹具上,放入赫尔槽中。
5. 接通电源:将直流稳压电源的正极连接到阳极,负极连接到阴极,调节电流密度。
6. 电镀过程:打开电源,开始电镀过程,记录电镀时间。
7. 停止电镀:电镀达到预定时间后,关闭电源,取出锌板。
8. 清洗样品:用纯水冲洗锌板,去除表面残留的镀液。
9. 测量镀层厚度:使用厚度计测量镀层厚度。
10. 分析结果:根据实验数据,分析镀层质量。
五、实验结果与分析1. 镀层厚度:根据实验数据,镀层厚度在0.05-0.1mm之间,符合实验要求。
2. 镀层外观:镀层表面光滑,颜色均匀,无明显缺陷。
3. 镀层结合力:通过划痕试验,镀层与基体结合良好,无脱落现象。
4. 镀层耐腐蚀性能:将镀层样品放置在中性盐雾试验箱中,经24小时试验后,镀层表面无明显腐蚀现象。
六、实验结论1. 电镀锌是一种简单、高效的金属表面处理方法,具有良好的镀层质量和耐腐蚀性能。
镁合金表面电弧喷涂铝锌工艺及涂层性能的研究的开题报告
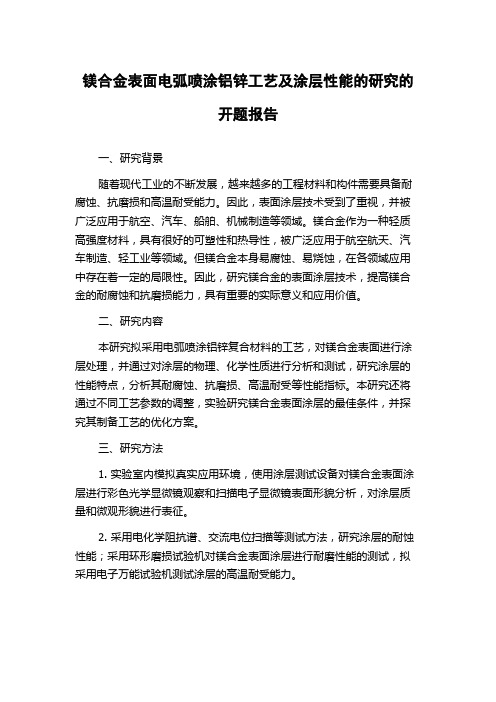
镁合金表面电弧喷涂铝锌工艺及涂层性能的研究的开题报告一、研究背景随着现代工业的不断发展,越来越多的工程材料和构件需要具备耐腐蚀、抗磨损和高温耐受能力。
因此,表面涂层技术受到了重视,并被广泛应用于航空、汽车、船舶、机械制造等领域。
镁合金作为一种轻质高强度材料,具有很好的可塑性和热导性,被广泛应用于航空航天、汽车制造、轻工业等领域。
但镁合金本身易腐蚀、易烧蚀,在各领域应用中存在着一定的局限性。
因此,研究镁合金的表面涂层技术,提高镁合金的耐腐蚀和抗磨损能力,具有重要的实际意义和应用价值。
二、研究内容本研究拟采用电弧喷涂铝锌复合材料的工艺,对镁合金表面进行涂层处理,并通过对涂层的物理、化学性质进行分析和测试,研究涂层的性能特点,分析其耐腐蚀、抗磨损、高温耐受等性能指标。
本研究还将通过不同工艺参数的调整,实验研究镁合金表面涂层的最佳条件,并探究其制备工艺的优化方案。
三、研究方法1. 实验室内模拟真实应用环境,使用涂层测试设备对镁合金表面涂层进行彩色光学显微镜观察和扫描电子显微镜表面形貌分析,对涂层质量和微观形貌进行表征。
2. 采用电化学阻抗谱、交流电位扫描等测试方法,研究涂层的耐蚀性能;采用环形磨损试验机对镁合金表面涂层进行耐磨性能的测试,拟采用电子万能试验机测试涂层的高温耐受能力。
3. 通过变化涂层工艺参数,如电极材料、电流密度、气氛气体等进行试验,确定电弧喷涂铝锌工艺的最佳参数,并分析涂层制备工艺的因素对镁合金涂层质量的影响。
四、研究意义本研究将探究电弧喷涂铝锌复合材料在镁合金表面涂层中的应用和性能,为提高镁合金的耐腐蚀、抗磨损和高温耐受性能,推广镁合金在航空、汽车、机械制造等领域的应用提供实用技术解决方案。
同时,本研究还将为电弧喷涂技术在表面涂层领域的应用提供经验和参考,具有一定的学术价值和认识价值。
电弧喷涂铝基涂层耐腐蚀性能
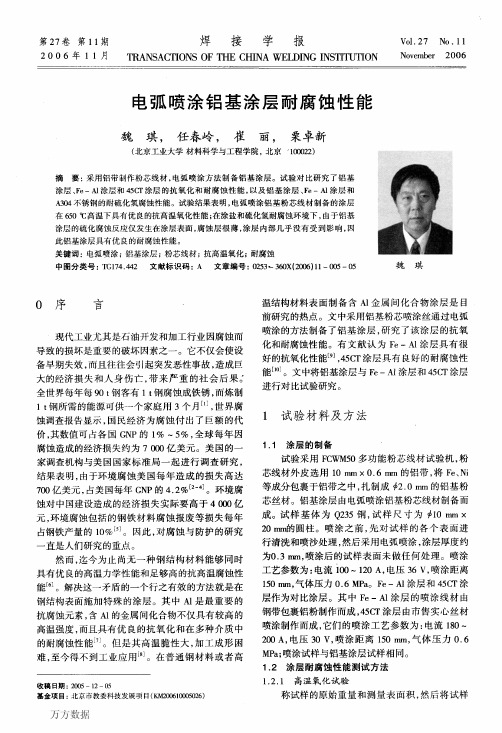
150 I姗,气体压力0.6 MPa。Fe—Al涂层和45cT涂
层作为对比涂层。其中Fe—Al涂层的喷涂线材由 钢带包裹铝粉制作而成,45CT涂层由市售实心丝材 喷涂制作而成,它们的喷涂工艺参数为:电流180~ 200 A,电压30 V,喷涂距离150 mm,气体压力0.6 MPa;喷涂试样与铝基涂层试样相同。 1.2涂层耐腐蚀性能测试方法 1.2.1高温氧化试验
1试验材料及方法
1.1涂层的制备 试验采用FCWM50多功能粉芯线材试验机,粉
芯线材外皮选用10ⅡⅡn×0.6 n硼的铝带,将Fe、Ni
等成分包裹于铝带之中,扎制成乒2.o rm的铝基粉
芯丝材。铝基涂层由电弧喷涂铝基粉芯线材制备而 成。试样基体为Q235钢,试样尺寸为≠10 n瑚×
20一的圆柱。喷涂之前,先对试样的各个表面进
基涂层氧化后生成了Al,Fe,Ni之间的化合物,A12 03 以及少量的Fe20,和Fe。
图3为Fe一灿涂层和铝基涂层氧化后表面 SEM形貌。由图3a来看图中主要为疏松的针状组 织,经分析为Fe20,。由图3b来看主要由片状的A 区域和脊状的B区域组成,经分析片状结构为亚稳 态0一A12 03,脊状结构为稳态a.A12 03,这两种结构的
600℃时的硫化氢腐蚀动力学曲线。由图7可知, A304不锈钢的硫化氢腐蚀动力学瞳线呈二次函数 增长,在600℃,经12 h硫化氢腐蚀后,腐蚀产物从 基体上剥落下来,说明其耐硫化氢腐蚀性能很差。 Fe一灿涂层和铝基涂层的硫化氢腐蚀动力学曲线 均为对数函数,曲线变化较缓,涂层均对基材具有一 定的保护作用。从图7可以看出,铝基涂层腐蚀增 重最低,抗硫化氢腐蚀性能最好。
电弧喷涂锌铝复合涂层耐蚀性能研究

防腐保温技术
电弧 喷 涂 锌 铝 复 合涂 层 耐 蚀 性 能研 究
方 华 彭立涛 董 光 张晓健
( .大庆石 油学院 , 1 黑龙江 大庆 13 1 ; 6 3 8
13 1 ) 6 3 8 2 .大庆 钻探 工程公司钻技一公 司, 黑龙江大庆
关键词 电弧喷 涂
锌铝 涂 层
增重 法
腐蚀
封 闭涂 层
复合 涂层
S u y o r o i n Re it nc t d n Co r so ss a e
o c S r y n n nd Alm i um m p st a i g fAr p a i g Zi c a u n Co o ie Co tn s
1 前 言
金 属 锌和铝 由于具有 牺牲 阳极 作 用所 以成 为常
式中 , V 为增重腐蚀 速率 ,/ m h ; 为 g ( ・ ) W 腐蚀后试件的重量 ,ቤተ መጻሕፍቲ ባይዱ 为腐蚀前的重量 , ; 为 g w。 gS
试件暴 露 在 腐 蚀 介 质 中 的 表 面 积 , t 腐 蚀 时 m ;为
非 工作 面 , 留工作 面积 为 1 m 。 预 4c
表 l 电弧 喷涂 锌、 铝涂层 的平均厚 度
V =( 一W0 / t W2 ) s・ …… …… ( ) 1
平 均厚度
10±1 6 5
1041 9 5 -
2
方 华等 : 电弧喷 涂锌铝 复合 涂层 耐蚀性 能研 究 带有 锌铝涂 层试 件刷 涂封 闭漆 时醇酸树 脂涂层 中 的传 质 过 程 。对 于 表 面涂 刷 封 闭 涂层 的 电 极 J
Fo g Hu 1, Pe t o , D n un n h n a oa n a ng Li 1 ogG a g a dZ ag ̄a i t a jr
电弧喷涂锌铝涂层耐腐蚀实验报告

电弧喷涂锌铝涂层耐腐蚀实验报告一、实验背景水工钢闸门是水电站、水库、水闸、船闸等水工建筑物中控制水位的重要水工钢构件,其制造量约为500万吨,保有量十分巨大。
水工钢闸门由于长期浸水,在阴暗潮湿、干湿交替、高速水流、风浪、水生物腐蚀等恶劣环境下工作,经多年运行后很容易被腐蚀,出现绣皮泛起、局部绣坑密布,导致整个结构强度削弱,降低了钢闸门的承载能力,还要消耗大量的人力、物力、财力。
Zn-13A1涂层具有良好的耐腐蚀性能,以高速电弧喷涂方式将之喷到水工钢闸门表面可以有效防止表面腐蚀。
二、实验目的本实验针对内陆水库及水电站工程,模拟其水工钢闸门的运行环境,研究Zn-13A1涂层对水工钢闸门的保护程度及对比分析不同保护涂层(Zn跟Zn-13A1)对防腐蚀能力的优劣程度。
三、实验器材NaCl溶液,Q235钢板,棕刚玉砂,喷砂机,高性能电弧喷涂设备,超声清洗机,电子天平,防腐涂料,交流阻抗测试仪,M273 型电位仪,5208 型锁相放大器焊机,铜导线等。
四、实验过程1、制备浸泡液:质量分数为5%的NaCl溶液。
2、加工试样,将Q235钢板加工成72片尺寸为12 mm*12mm*3mm的试样,将之分为九组,每组8片。
3、采用颗粒度为14~18#的棕刚玉砂对前六组试样表面进行喷砂处理。
喷砂操作时,压缩空气的工作压力为0.6 MPa,喷砂距离为150~200 mm,喷砂角度为70°~80°。
4、使用TLAS-III 型高性能电弧喷涂设备制备Zn-13A1涂层,电压45V,电流120A;制备Zn涂层,电压40V,电流120A。
5、丙酮超声清洗3min后烘干,将54片试样沉重,并记录,剩余的18个试样用于随时观察腐蚀情况。
6、将清洗过的试样画出工作界面:10mm*10mm;试样多余的部分用防腐涂料密封,露出10mm*10mm的工作界面。
同时将做电化学测试的试样焊接铜导线,以便测试其极化曲线和阻抗。
7、将全部处理好的试样放入浸泡液中,按照GBT19746-2005《金属和合金的腐蚀盐溶液周浸试验》标准进行全浸泡试验。
电弧喷涂铝涂层海洋飞溅区腐蚀模拟试验研究

关键词 : 涂层 铝
腐蚀
海 洋 飞溅 区 电 弧 喷 涂 文 献标 识 码 : A 文 章编 号 :37 05 2 1)2- 06 C 10 — 1X{00 0 0 1 一 l 1 5
中 图分类 号 :G 7.4 T 1 42 4
随着海 洋石 油工 业 的迅速 发展 , 上石 油生 产 海
收稿 日期 :09— 9— 8 修稿 日期 :0 9~1 —1 。 20 0 2 ; 20 1 7 作者简介 : 李春玲 (9 4一) 女 , 18 , 中国石油大学 ( 华东 ) 材料 图 1 海 洋飞溅区腐蚀模拟试验 装置
工程 系在读 硕士研究 生。
第 2期
李春玲等 .电弧喷涂铝 涂层 海洋飞溅 区腐蚀模 拟试 验研究 表 1 试样 的拟合参数 及相关系数
试验 装置 由飞溅 系 统 、 温加 热系 统 、 风 系 恒 通 统 和挂 片系统 四部 分 组 成 。海 洋 飞 溅 区腐蚀 环境 的主要特 点是 海水 飞溅 、 水充 分充 气 、 含 量大 、 海 盐 t 3照强烈 和无 海 生 物 污 损 等 。该 试 验 装 置 能够 J
规模逐步扩大 , 为海上 石油生产基 地 的钻 采平 作 台, 服役环境恶劣且维修困难。海洋飞溅区是海洋 环境中一般钢铁材料遭受腐蚀最严重的区域 ¨ 。 ’ 目前 , 研究金属材料在海洋飞溅 区腐蚀的主要手段 是现场暴露试验 , 但是现场暴露试验存在研究周期 长 和试 样 管 理 困 难 等 不 足 - 。干 湿 交 替 试 验 、 3 J 盐
重精度为 0 1 g . 。腐蚀试 验前采用 M 9 m 3 8型腐蚀 电化学测试 系统测量 涂层和 2 0号钢 的 自腐蚀 电 位, 比电极为饱和甘汞电极 , 蚀介质是 质量分 参 腐
耐熔融锌、铝腐蚀涂层的分析

山东科技大学硕士学位论文5涂层耐熔锌、熔铝腐蚀性能结果与分析有因在空气中实施喷涂而发生大面积的氧化,这在显微组织分析中也得到了验证。
(2)显微组织分析图5.2末腐蚀Mo涂层显微组织Fig.5.2MicroslructurcofuncorrodedMolybdenumcoating从Mo涂层电子探针背散射图像(图5.2)中可以看出,涂层基体中的层与层之间以及涂层与打底层之间结合都非常好,孔隙率和氧化物夹杂等缺陷也很少,涂层基体中几乎不存在呈片状分布的氧化物夹杂。
涂层在宏观上看不具有喷涂层的典型结构(见图5.2些奎型垫查堂堡主堂垡堕壅!鳖星堕堕壁:鳖塑堕塾丝墼竺墨兰坌堑(a,b,c)),但在高倍率下可以显著观察到涂层中存在着微小的层状叠加,微裂纹非常小,仅限于在微小的层中,很少有大的显微裂纹存在(见图5.2(d,e,f))。
从整体来看Mo层的喷涂熔化状态良好。
5.1.2Fe.Al涂层分析本课题中采用了两种方法来制备Fe.Al金属间化合物层:一种是通过电弧喷涂纯Al层并进行高温扩散来获得Fe一越金属间化合物层,即渗铝层:另一种是采用电弧喷涂Al丝/Fe—Cr丝获得伪合金涂层,然后进行原位扩散处理获得Fe-Cr-A1金属间化合物涂层。
5.1.2.1渗铝层分析渗铝层由以下几部分组成:如果扩散不充分,表面层有可能存在一层纯铝层,再往里依次为FeAl3、Fe2A15、FeAl2、FeAI、Fe3AI等化合物层,而以Fe2A15为主要形式。
这是因为FeAl3和FeAl2不够稳定,FeAl3在600*(2以下会分解为Fe2A15和Fe2A17两相混合物:而铝含量为13.9~20%的铁铝合金缓冷后成为具有FeAl3型的有序超结构pl固溶体;而铝含量为20~36%的铁铝合金,冷却后则成为具有FeAI型的有序超结构p2固溶体。
在基体与渗层之间是一层柱状晶粒区,而在FeAI化合物区有一层疏松多孔区,存在一部分孔洞,在整个渗层上不规则分布着针状A14c。
电弧喷涂Zn-Al伪合金涂层耐腐蚀性能研究进展

电弧喷涂Zn-Al伪合金涂层耐腐蚀性能研究进展
张敏;丁玉萍;王淞;刘施峰
【期刊名称】《表面技术》
【年(卷),期】2024(53)10
【摘要】通过在钢基体表面制备涂层可以很好地延长钢铁材料的服役时间,减少因腐蚀造成的重大事故和人员伤亡。
相较于传统的纯Zn涂层、纯Al涂层以及Zn-Al合金涂层,Zn-Al伪合金涂层能够为基体材料提供长久有效的腐蚀防护,在钢铁材料的腐蚀防护中具有巨大的应用潜力。
简述了Zn-Al伪合金涂层电弧喷涂制备工艺的特点;介绍了Zn、Al、Zn-Al合金及Zn-Al伪合金涂层在模拟海洋环境下的腐蚀防护原理;在此基础上从组分、喷涂工艺参数(喷涂距离、喷涂电流和喷涂电压)、元素掺杂(Mg、Si及Re)及后处理工艺(封孔、激光重熔)等角度,论述了其对Zn-Al 伪合金涂层耐蚀性的影响;讨论了Zn-Al伪合金涂层防腐体系在桥梁、海洋钢结构件、地下运输管道中的应用现状;最后总结了目前研究工作中存在的挑战,提出了电弧喷涂Zn-Al伪合金涂层尚需深入研究的重点问题,为提高钢铁材料使用寿命提供了参考。
【总页数】15页(P1-15)
【作者】张敏;丁玉萍;王淞;刘施峰
【作者单位】重庆大学材料科学与工程学院
【正文语种】中文
【中图分类】TG174.4
【相关文献】
1.高速电弧喷涂Zn-Al和Zn-Al-Mg-RE涂层在模拟海洋环境中的耐腐蚀性能
2.电弧喷涂Zn-Al伪合金涂层电化学腐蚀性能研究
3.电弧喷涂工艺参数对Zn-Al伪合金制模涂层性能的影响
4.Mg和RE对电弧喷涂Zn-Al合金涂层耐腐蚀性能的影响
因版权原因,仅展示原文概要,查看原文内容请购买。
铝合金的防腐实验报告

一、实验目的随着科技的发展和工业生产的需要,铝合金因其轻质、高强度、耐腐蚀等优异性能在各个领域得到了广泛应用。
然而,铝合金在实际使用过程中易受到各种环境因素的影响,如氧化、腐蚀等,从而影响其使用寿命和性能。
本实验旨在研究铝合金的防腐性能,探讨不同防腐措施对铝合金耐腐蚀性的影响,为铝合金在各类环境中的应用提供理论依据。
二、实验材料与方法1. 实验材料(1)铝合金板材:材料牌号为6061,厚度为2mm。
(2)实验药剂:磷酸、硝酸、氢氧化钠、硫酸、盐酸等。
(3)实验设备:电化学工作站、中性盐雾试验箱、超声波清洗机、电子天平等。
2. 实验方法(1)腐蚀试验将铝合金板材分为四组,分别进行以下处理:A组:不做任何处理,作为对照组。
B组:进行阳极氧化处理,阳极氧化电压为20V,处理时间为2小时。
C组:进行电镀处理,镀层为锌,镀层厚度为5μm。
D组:进行表面涂层处理,涂层材料为氟碳漆,涂层厚度为50μm。
将处理后的铝合金板材置于中性盐雾试验箱中,进行盐雾腐蚀试验,试验时间为720小时。
(2)重量损失法在腐蚀试验结束后,取出铝合金板材,用超声波清洗机清洗,去除表面的盐雾和腐蚀产物。
使用电子天平称量腐蚀前后铝合金板材的重量,计算重量损失率。
(3)金相分析对腐蚀后的铝合金板材进行金相分析,观察腐蚀形态和腐蚀产物。
三、实验结果与分析1. 腐蚀试验结果表1 腐蚀试验结果组别重量损失率(%)A组 4.20B组 1.50C组 0.80D组 0.30由表1可知,经过不同防腐处理后,铝合金板材的重量损失率明显降低。
其中,D 组(表面涂层处理)的重量损失率最低,说明表面涂层处理对铝合金的防腐性能有显著提高。
2. 金相分析结果表2 金相分析结果组别腐蚀形态A组全面腐蚀B组局部腐蚀C组局部腐蚀D组无明显腐蚀由表2可知,经过不同防腐处理后,铝合金板材的腐蚀形态有所不同。
其中,D组(表面涂层处理)的腐蚀形态无明显腐蚀,说明表面涂层处理能够有效防止铝合金板材的腐蚀。
喷锌防腐项目报告

喷锌防腐项目报告
(一)采用喷砂除锈法进行表面预处理
1.原理:借助压缩空气驱动砂粒,通过专用喷砂枪嘴以较高的速度使砂粒喷射到钢结构表面上去。
由于高速砂粒的冲击和摩擦,从而达到除锈和清理表面的目的。
处理后的闸门表面清洁干燥,露出灰白色金属光泽,并且具有益定的粗糙度,有利于镀锌层与闸门表面的良好结合。
2.工艺要求:
(1)水工钢结构在涂装之前必须进行表面处理。
(2)水工钢结构表面在喷射处理之前,必须仔细的清洁焊渣、飞溅等附着物,并清洁基体金属表面可见的油脂及其它污物。
(3)压缩空气必须经过冷却装置及油水分离器处理,保证空气干燥、清洁,气罐要定期进行排污和清理。
(4)砂质要坚硬、有棱角、干燥、无泥土和其它杂质,砂粒粒径控制在0.5mm<d<2mm,即中粗砂为宜。
- 1、下载文档前请自行甄别文档内容的完整性,平台不提供额外的编辑、内容补充、找答案等附加服务。
- 2、"仅部分预览"的文档,不可在线预览部分如存在完整性等问题,可反馈申请退款(可完整预览的文档不适用该条件!)。
- 3、如文档侵犯您的权益,请联系客服反馈,我们会尽快为您处理(人工客服工作时间:9:00-18:30)。
电弧喷涂锌铝涂层耐腐蚀实验报告
一、实验背景
水工钢闸门是水电站、水库、水闸、船闸等水工建筑物中控制水位的重要水工钢构件,其制造量约为500万吨,保有量十分巨大。
水工钢闸门由于长期浸水,在阴暗潮湿、干湿交替、高速水流、风浪、水生物腐蚀等恶劣环境下工作,经多年运行后很容易被腐蚀,出现绣皮泛起、局部绣坑密布,导致整个结构强度削弱,降低了钢闸门的承载能力,还要消耗大量的人力、物力、财力。
Zn-13A1涂层具有良好的耐腐蚀性能,以高速电弧喷涂方式将之喷到水工钢闸门表面可以有效防止表面腐蚀。
二、实验目的
本实验针对内陆水库及水电站工程,模拟其水工钢闸门的运行环境,研究Zn-13A1涂层对水工钢闸门的保护程度及对比分析不同保护涂层(Zn跟Zn-13A1)对防腐蚀能力的优劣程度。
三、实验器材
NaCl溶液,Q235钢板,棕刚玉砂,喷砂机,高性能电弧喷涂设备,超声清洗机,电子天平,防腐涂料,交流阻抗测试仪,M273 型电位仪,5208 型锁相放大器焊机,铜导线等。
四、实验过程
1、制备浸泡液:质量分数为5%的NaCl溶液。
2、加工试样,将Q235钢板加工成72片尺寸为12 mm*12mm*3mm的试样,将之分为九组,每组8片。
3、采用颗粒度为14~18#的棕刚玉砂对前六组试样表面进行喷砂处理。
喷砂操作时,压缩空气的工作压力为0.6 MPa,喷砂距离为150~200 mm,喷砂角度为70°~80°。
4、使用TLAS-III 型高性能电弧喷涂设备制备Zn-13A1涂层,电压45V,电流120A;制备Zn涂层,电压40V,电流120A。
5、丙酮超声清洗3min后烘干,将54片试样沉重,并记录,剩余的18个试样用于随时观察腐蚀情况。
6、将清洗过的试样画出工作界面:10mm*10mm;试样多余的部分用防腐涂料密封,露出10mm*10mm的工作界面。
同时将做电化学测试的试样焊接铜导线,以便测试其极化曲线和阻抗。
7、将全部处理好的试样放入浸泡液中,按照GBT19746-2005《金属和合金的腐蚀盐溶液周浸试验》标准进行全浸泡试验。
8、每组试验在浸泡液中浸泡120h(5d),240h(10d),360h(15d),480h(20d),600h (25d),720h(30d)之后将之进行表面清洗,清洗方法为:清水冲掉表面盐分,然后超声
清洗3min烘干。
然后进行a表面观察和扫描电镜观察,并记录观察结果;b取出表面的防腐涂料,称量腐蚀之后的重量,并记录;c测量锈蚀的计划曲线;d测量锈蚀的阻抗值。
9、绘制失重率的时变曲线,计算腐蚀速率,对计划曲线和阻抗曲谱进行分析,分析试验待测涂层的防腐性能。
四、实验结果与讨论
1、扫描电镜观察
腐蚀完毕后丙酮超声清洗3min,烘干后进行扫描电镜观察如图所示,图1为腐蚀3天后3种试样表面腐蚀坑内腐蚀产物的微观形貌。
无涂层试样已经被严重腐蚀,表面结构疏松,附着力差。
纯Zn涂层表面存在细小针状、取向不同的腐蚀产物,但由于针状腐蚀产物的数量较少,对腐蚀介质的阻碍能力较弱。
Zn-13Al涂层的腐蚀坑内存在大量细小的针状腐蚀产物,对腐蚀介质具有较强的阻碍能力。
图2为涂层出现第一锈点时的表面形貌图,经3天腐蚀实验之后,无涂层试样出现第一锈点,局部存在轻微鼓泡现象;12天时,纯Zn涂层表面出现较多的锈点,并有鼓泡和开裂现象,涂层明显鼓起,附着力很差,防护性能基本丧失;26天时,Zn-13Al涂层表面出现少量锈点,也出现了鼓包和开裂现象,其特征与纯Zn的形貌特征类似。
(a)无涂层(b)Zn涂层(c)Zn-13Al涂层
图1 腐蚀3d后的表面形貌
(a)无涂层(b)Zn涂层(c)Zn-13Al涂层
图2对应第一锈点出现时的表面形貌
2、计算失重
取出表面的防腐涂料,称量腐蚀之后的重量,记录如下,图3为全浸泡腐蚀试验中涂层
图3 涂层试样单位面积的质量损失随时间的变化曲线
3、涂层耐腐蚀性能检测
图4为在浓度为5%的NaCl溶液中,Zn-13Al涂层与基体的自腐蚀电位E与时间t的曲线。
分析可知,Zn-13Al涂层自腐蚀电位一直低于基体,从电化学的角度来讲,Zn-13Al涂层在电解质溶液中发生电化学腐蚀时,可实现牺牲阳极(涂层),保护阴极(基体)的功能。
在浸泡初期,Zn-13Al涂层自腐蚀电位快速提升,并逐渐趋于稳定,这表明在涂层表面形成了保护膜。
图4 Zn-13Al涂层与基体(Q235钢)的自腐蚀电位E与时间t关系曲线图5为Zn-13Al涂层浸泡1 h、20 h、500 h之后的极化曲线。
分析可知,涂层浸泡(1h 与
20 h)之后,出现较为明显的钝化现象,表明在涂层表层,形成了钝化膜(Al(OH)3)。
Zn-13Al 涂层腐蚀电位稳步增加,其电流密度显著降低,这表明涂层具有较好的耐腐蚀性。
浸泡500 h 之后,该涂层处于溶解阶段。
这表明Zn-13Al涂层颗粒较细,涂层较均匀,孔隙率较小,获得致密的组织结构,达到减少腐蚀通道的目的。
腐蚀反应进行到一定程度之后,因腐蚀产物堵塞,Cl-1难以利用涂层表面缺陷进入到涂层;其自封闭效果更为明显。
这有效提升了其腐蚀产物层的稳定性,进而使Zn-13Al涂层获得良好的耐腐蚀性能。
图5 不同时间Zn-13Al涂层的极化曲线
五、结论与展望
1、Zn-13Al涂层形成细小致密、稳定的针状腐蚀产物,可以有效填补涂层中的孔隙,切断腐蚀介质的快速通道,具有良好的自封闭性。
2、Zn-13Al涂层腐蚀电位低,腐蚀电流密度小,具有良好的阴极保护能力和耐蚀性能。
3、Zn-13Al涂层的耐蚀性能优于纯锌涂层,腐蚀形貌宏观表现为均匀腐蚀。
4、利用电弧喷涂方式将Zn-13Al涂层喷到水工钢闸门表面,可以有效提高水工钢闸门耐蚀性,延长其寿命,较小不必要的人力、物力与财力。