2_2_5t电动叉车新型传动系统的制动器设计_马乙
制动器的更换实训报告
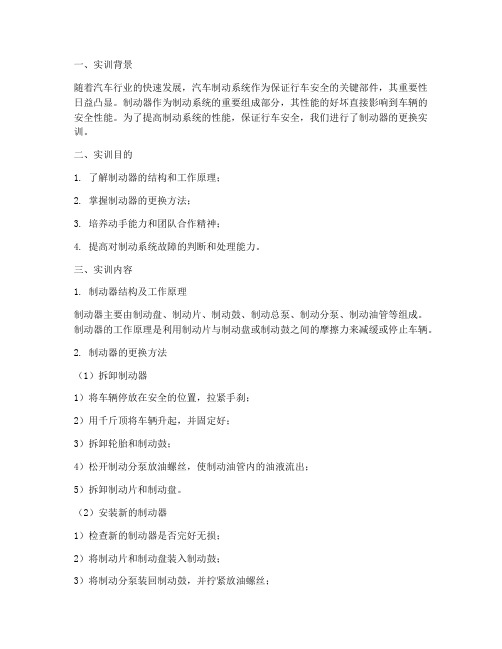
一、实训背景随着汽车行业的快速发展,汽车制动系统作为保证行车安全的关键部件,其重要性日益凸显。
制动器作为制动系统的重要组成部分,其性能的好坏直接影响到车辆的安全性能。
为了提高制动系统的性能,保证行车安全,我们进行了制动器的更换实训。
二、实训目的1. 了解制动器的结构和工作原理;2. 掌握制动器的更换方法;3. 培养动手能力和团队合作精神;4. 提高对制动系统故障的判断和处理能力。
三、实训内容1. 制动器结构及工作原理制动器主要由制动盘、制动片、制动鼓、制动总泵、制动分泵、制动油管等组成。
制动器的工作原理是利用制动片与制动盘或制动鼓之间的摩擦力来减缓或停止车辆。
2. 制动器的更换方法(1)拆卸制动器1)将车辆停放在安全的位置,拉紧手刹;2)用千斤顶将车辆升起,并固定好;3)拆卸轮胎和制动鼓;4)松开制动分泵放油螺丝,使制动油管内的油液流出;5)拆卸制动片和制动盘。
(2)安装新的制动器1)检查新的制动器是否完好无损;2)将制动片和制动盘装入制动鼓;3)将制动分泵装回制动鼓,并拧紧放油螺丝;4)将制动油管装回制动系统;5)将轮胎装回车辆,并拧紧螺栓;6)放下千斤顶,检查制动器是否安装牢固。
3. 制动器的调试1)检查制动系统油压是否正常;2)检查制动片与制动盘的间隙是否合适;3)检查制动踏板行程是否正常;4)进行制动性能测试,确保制动效果良好。
四、实训过程1. 实训准备(1)准备好实训所需的工具,如扳手、螺丝刀、千斤顶等;(2)准备好新的制动器及备品配件;(3)熟悉制动器的结构和工作原理。
2. 实训实施(1)按照制动器的拆卸方法,拆卸制动器;(2)按照制动器的安装方法,安装新的制动器;(3)进行制动器的调试。
3. 实训总结(1)实训过程中,严格按照操作规程进行,确保安全;(2)熟练掌握制动器的更换方法,提高动手能力;(3)培养团队合作精神,共同完成实训任务;(4)对制动系统故障的判断和处理能力得到提高。
叉车多盘湿式制动器冷却系统的设计

Ab ta t hsp p rpee t p sa da v na e f oki rc e rk s ou igo p rt na d d sg f sr c :T i a e rsnst e n d a tgso rltt k w t a e ,fc s no eai n eino y f f u b n o
1 湿 式 制 动器 特 点
湿 式制 动器工 作 性 能稳 定 ,不 需 要 经 常调 整 ,
使 用 寿命一般 为 干式 制 动器 的 3~ 5倍 ,使 用 超过 2年性能 不会 衰退 。其 主要 特 点如下 : 1 )制 动摩擦 片 在密 封 的油 浴 里工 作 ,摩 擦 片
两侧 的多 孔纤 维 面 能 确保 有 一 层 薄膜 油始 终 把摩
假 设周 围的环境 温度 为 t,进入 制动 器 的油 温 。
为 ,允许 流 出制动器 的 油温为 t,则制 动器 产 生 , : 的热量 一部 分 使 油 温 从 t 升 至 t,另 一 部 分 经 上 2 过制 动器 的表 面散发 到空气 中 ,即
Q =(2 t) v u t 一 1A 2 t 一 1 C Q+ (2 )
f l -l s d mu t d s e r k . u l co e l - i w tb a e y i k Ke wo d :f r l tt c y r s o ki r k;f l — l s d mut d s e r k ; fr i g c o i g r e c o i g f u u l c o e l - ik w tb a e o c n o l ;fe o l y i n n
叉车制动系统
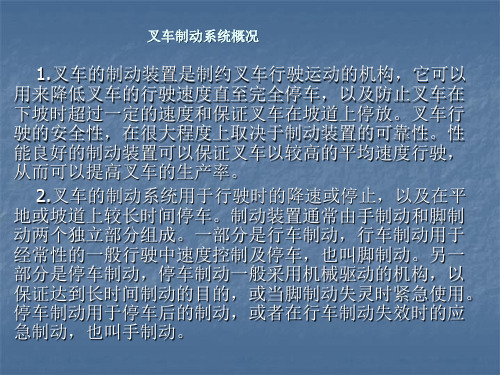
调节调整器
修理或更换 更换 修理或更换 调整 修理或更换 调节调整器 放气 按使用要求重调
制动液要求
1.高温性:具有优良的高温抗气阻性能; 2.低温性:具有优良的低温流动性能; 3.防腐性:良好的抗腐蚀性和防绣性能,以保护制动系统 中各种金属零部件在使用工程中不发生腐蚀; 4.水敏感性:在储存和使用过程中水分对制动液的性能影 响小; 5.橡胶皮碗适应性:具有优良的橡胶皮碗适应性能,以避 免橡胶皮碗在使用过程中过分溶胀或收缩而导致制动迟缓 或失灵; 6.热安定性、化学稳定性:遇热产生化学变化的可能性越 小越好; 7.润滑性:具有适当的润滑性,能对制动机构中的运动部 件起良好的润滑作用。
叉车制动系统概况
1.叉车的制动装置是制约叉车行驶运动的机构,它可以 用来降低叉车的行驶速度直至完全停车,以及防止叉车在 下坡时超过一定的速度和保证叉车在坡道上停放。叉车行 驶的安全性,在很大程度上取决于制动装置的可靠性。性 能良好的制动装置可以保证叉车以较高的平均速度行驶, 从而可以提高叉车的生产率。 2.叉车的制动系统用于行驶时的降速或停止,以及在平 地或坡道上较长时间停车。制动装置通常由手制动和脚制 动两个独立部分组成。一部分是行车制动,行车制动用于 经常性的一般行驶中速度控制及停车,也叫脚制动。另一 部分是停车制动,停车制动一般采用机械驱动的机构,以 保证达到长时间制动的目的,或当脚制动失灵时紧急使用。 停车制动用于停车后的制动,或者在行车制动失效时的应 急制动,也叫手制动。
谢谢!
叉车制动系统的主要故障及排除
现 象 故 障 原 因 排除方法
1 制动系统漏油
2 制动蹄间隙未调好 3 制动器过热 制动力不足
检查部件、管路及接头处密封 性
调节间隙调整器 检查是否间隙太小
叉车全方位智能刹车装置

Science and Technology & Innovation|科技与创新2024年第04期DOI:10.15913/ki.kjycx.2024.04.029叉车全方位智能刹车装置曹建国(大同市综合检验检测中心,山西大同037000)摘要:由于叉车操作的复杂性和环境的不确定性,安全问题一直是叉车使用过程中的重要关注点。
传统的叉车受限于现有的技术手段,不仅维护成本高、安全性能差,且与国家现行的绿色节能环保政策不相适应,因此,必须通过技术手段使叉车适应未来的发展。
通过借鉴汽车全车影像和雷达感应等现有的安全技术手段,经过系统研究和分析,引入适合叉车的传感器、控制器、执行器、可视化人工智能界面的相互联动来实现叉车的智能识别,从而提升使用的安全性和舒适感,有效避免叉车事故发生。
关键词:全车影像;雷达感应;智能识别;刹车装置中图分类号:TP277 文献标志码:A 文章编号:2095-6835(2024)04-0105-03叉车作为一种重要的物流设备,在仓储和物流行业及厂矿企业中扮演着重要的角色。
然而,由于叉车操作的复杂性和环境的不确定性,安全问题一直是叉车使用过程中的重要关注点。
据统计,2019—2022年底,共发生了162起叉车事故,其中有144人不幸死亡。
2022年,发生叉车事故42起,占特种设备事故总数的38.89%,死亡40人,占特种设备事故死亡总人数的39.6%;2021年,发生叉车事故42起,占特种设备事故总数的38.18%,死亡34人,占特种设备事故死亡总人数的34.34%;2020年,发生叉车事故33起,占特种设备事故总数的30.84%,死亡28人,占特种设备事故死亡总人数的26.42%;2019年,发生叉车事故45起,占特种设备事故总数的34.62%,死亡42人,占特种设备事故死亡总人数的35.29%。
这些数据说明,需要重视叉车搬运的安全问题。
不仅是企业,每一个操作叉车的人都需要时刻注意安全,遵守操作规程,保障自己和周围人员的安全。
220t电传动矿用自卸车全液压制动系统设计

^_.HydrostaticsandHydrodynamics’二::二I:二’二_土程机械_二i≥二:!i,■二?:i三二第39卷2∞8年3月:中南大学机电工程学院罗春雷赵遵平张友林;摘要:大型矿用自卸车作业效率高,运营成本低,具有中小型设备无法比拟的优势,因而广泛;;应用于大型露天矿山。
矿用自卸车载重量大、行驶速度高,对制动性能要求很高,而且电传动矿用自:;卸车的前后制动压力、流量差别较大,因此设计了新型全液压制动系统。
该系统采用带液控功能的双i!路踏板阀作为先导阀,继动阀作为主阀,组成双路工作制动系统,通过电磁阀液控踏板阀来实现紧急÷i制动,电磁阀液控后继动阀间接锁定后制动器来实现制动锁定;停车制动为弹簧施加、电磁阀控制液i;压解除,并设置单向阀、压力开关和速度传感器,防止停车制动器意外施加。
系统分为多条油路,并设;;置各自的隔离单向阀、蓄能器和油路调节器,保证系统在部分油路故障的情况下能够安全停车,即实?;现次级制动。
另外系统设置了多个压力开关,实现与推进互锁和压力低报警,并采用顺序阀液控踏板;÷阀,实现在制动压力低报警一段时间后自动施加所有制动器。
}关键词:电传动自卸车全液压制动次级制动矿用汽车220t矿用自卸车作业效率高,运营成本低,具有中小型设备无法比拟的优势,广泛应用于大型露天矿山【l】。
220t矿用自卸车自重达170t,满载后的总质量达到390t,而且其行走速度也达到48km/h,这就要求自卸车必须具有非常可靠的制动。
因此,本文通过参考国外相关产品,设计了全液压制动系统,来保障行车的安全性和制动的可靠性。
1制动工况分析矿用自卸车有机械传动和电传动两种方式,电传动是通过驱动电动机经行星减速器减速后驱动后轮,电动机直接安装在后桥内。
因此,国内外大型电传动矿用自卸车普遍采用前轮为轮速制动,后轮为枢速制动(制动器装在电动机的轴上),制动器一般采用全液压钳盘式制动器或者湿式制动器。
某型叉车动力制动系统的改进设计

制动阀不工作时,制动器中的高温液压油会经制动阀进入 散热器中进行散热冷却处理,降低了整个系统中液压油的 油温,提高了系统的安全性,可为类似制动制动系统改进 设计提供一定参考。■
CM&M 2021.04 29
4 结语
经改进的制动系统随时可以实现整车制动,可保证叉 车运行的安全性。系统中的液压油均可循环流动,液压油 不再被始终封闭在制动阀与制动器之间,不会因这一空间
只有当流向第一单向阀 7 的油液压力达到了第二单向 散热不畅而导致制动失效。制动阀与制动器之间的连接管
阀 8 的正向开启压力值,油液才会改由经第二单向阀 8 流 路既是制动管路,同时也是冲洗冷却管路。制动阀工作时,
液压泵 1 继续经蓄能器充液阀 2 为蓄能 10
器 3 充液。
2.2.2 充液—冲洗冷却过程
8
当蓄能器 3 内的高压油压力达到蓄
6
能器充液阀 2 设定的闭合压力值时,蓄
能器充液阀 2 由 P 口与 S 口连通改为 P 4
口与 N 口连通。此时系统若无制动需求,
制动阀 4 处于初始位置,其 A 口与 N1 口 2
该系统优先保证对蓄能器 3 的充液及整车制动。在初
始状态时,蓄能器 3 内的压力低于蓄能器充液阀 2 设定的
3 改进效果
开启压力值,蓄能器充液阀 2 的 P 口与 S 口连通。液压泵
测量充液阀 2 的进油口压力曲线,发现其最大压力在
1 经吸油过滤器 13 从液压油箱 10 中吸取油液,经蓄能器充 11.5 ~ 14MPa 之间,然后迅速回落至 0.5MPa 左右,如图 2。
口 P1 及压力报警开关 5 连接,其 N 口第一单向阀 7 及第二 单向阀 8 连接,T 口直接回液压油箱 10;制动阀 4 的回油
- 1、下载文档前请自行甄别文档内容的完整性,平台不提供额外的编辑、内容补充、找答案等附加服务。
- 2、"仅部分预览"的文档,不可在线预览部分如存在完整性等问题,可反馈申请退款(可完整预览的文档不适用该条件!)。
- 3、如文档侵犯您的权益,请联系客服反馈,我们会尽快为您处理(人工客服工作时间:9:00-18:30)。
F = P ×S 当活塞面积与摩擦片净面积一定时, 比压公式 可以简化为:
现代制造、 工艺装备 ·21· S 制动时, 电机即停止工作, 同时提供负制动, 所以当 q = P × Am 远远满足整机性 制动操纵系统压力为 6. 2 MPa 时, A m ≈ S m = 0 . 007 948 m2 , S = 0 . 001 491 5 m2 ∴ 对于此制动器: q = P × S Am 能、 人机工程要求。
电动叉车将逐渐成为市场发展的主力。 国内、 国际 电动叉车的动力控制系统已基本完成了直流向交流 的过渡, 因此高效的传动系统研发也要适当跟进 。 同时随着全球叉车制造技术的发展, 用户对整机的 纵向、 横向稳定性、 高位承载能力、 高性能动力源的 选用、 操纵舒适性等性能要求越来越高。 这就要求 整车具有前悬小、 电池容量大、 动力源选用交流电 机、 轮子半径小、 操纵者腿部空间大等特点。欧美国 家在电动叉车物料搬运行业应用交流技术已很广 泛, 在新型传动系统开发方面如双驱湿式驱动 、 整体 式湿式驱动电桥等研究比较多, 但在国内基本为空 白。目前国内主流厂商最新传动技术基本上是仿照 丰田、 力至优的干式制动的传动系统来开发产品 , 整 体技术虽相比 2005 年以前的产品提升了很多, 但 因受制于制动器技术, 传动系统技术还是落后于日 本、 欧洲等先进国家。 目前国内电动叉车传动系统 主要具有以下缺点: 驱动桥采用干式制动, 当使小轮
0
F k —作用在摩擦面上的回程弹簧的弹力 。 现采用 4 个圆柱压缩弹簧, 则: Fk = n × k × x = 4 × 7. 8 × 16. 6 = 518 N F = P0 × S - F k = 6 . 5 × 10 6 × 0 . 001 49 - 518 = 9 177 N R0 为摩擦面等效摩擦半径, R0 = =
= 1 490 mm2 8个 活塞行程 1. 6 mm( 理论计算 0. 9 mm 即可, 单个摩擦副按 0. 15 mm 计算, 试制时定分 摩擦副, 离间隙为 2. 05 mm) , 需流量 V: V 初始 = 2 × S × l =2 × 1 × 3. 14 × ( 0. 100 2 - 0. 090 2 ) → 4
× 1. 6 × 10 - 3 = 2 × 1. 49 × 10 - 3 × 1. 6 × 10 - 3 = 4. 77 mL V2. 05 = 2 × S × l
现代机械 2013 年第 6 期 1 F = P0 × S - F k = 2 × × 3. 14 × ( 0. 100 2 - 0. 090 2 ) → 4 式中: P —液压油的压强, 为 6. 5 MPa;
3 3 1 Dm - dm × 2 3 D m - d2 m
1 0 . 135 3 - 0 . 090 3 = 0. 057 × 3 0 . 135 2 - 0 . 090 2
× 10 - 3 = 2 × 1. 49 × 10 - 3 × 3 × 10 - 3 = 8. 95 mL 制动总泵如图 3 所示, 其内腔容积最大为 13. 6 mL, 但使用时考虑到安全因素, 将其额定最大使用 量设定到其总容量的 70% 即使用到 9. 52 mL, 此时 9. 52 mL > 8. 95 mL, 即液压系统的制动总泵容量满 足要求。 根据最新标准 GB / T18849 - 2008 规定, 整机踏 则假定制动踏板需 板操纵力建议不能超过 450 N, 输入力 450 N 才能实现整机制动有效, 又制动操纵 机构的杠杆比为 6 , 所以当踏板输出力为 450 N 时, 制动总泵的连杆输出力为 2 700 N, 根据系统内压强 处处相等的平衡关系从而可以确定由轮边制动负载 反馈液压系统压强为 6. 5 MPa。即当操纵液压系统 的压强为 6. 5 MPa 时, 操纵力为 450 N 且制动满足 要求。所以先假定制动液压系统压为 6. 5 MPa。 8 片摩 则对湿式制动器: 两边共有 10 片隔片, 擦片, 一共 16 个摩擦副。 摩擦片面积: Sm 1 2 = × π × ( D2 m - dm ) 4 = 1 × 3. 14 × ( 0. 135 2 - 0. 090 2 ) 4
现代机械 2013 年第 6 期
·18·
2 - 2. 5 t 电动叉车新型传动系统的制动器设计
马乙
( 安徽合力股份有限公司 技术中心 , 安徽 合肥 230601 )
摘要: 本文介绍了当前国内电动叉车传动系统因受制制动器技术而导致性能落后的现状 , 重点阐述了 2 - 2. 5 t 电动叉车湿式传动系统为突破制动器技术制肘 , 在反复论证基础上 , 通过逆向设计 , 正向验证的方法成功设 计出具有世界先进技术的产品过程 。 关键词 : 叉车 多盘式湿式制动器 行车制动 驻车制动 扭矩 3 中图分类号 : U482 , 文献标识码 : A 文章编号 : 1002 - 6886 ( 2013 ) 06 - 0018 - 05
0
引言
随着社会环保意识增强, 可靠性更高、 更清洁的
受轮辋的尺寸限制, 制动器外径较小, 导致制 子时, 且制动器寿命较短, 如采用大外 动力不能满足要求, 径的制动器时, 须将制动器外置轮辋外, 导致整车较 通过性不好。上述问题严重制约了整机实现性 宽, 能、 人机工程提高的潜在可能。 为此须研发与之匹 配的传动系统来突破制动器技术方面的制肘 。本文 重点阐述的就是一种突破目前因制动器制肘而研发 的 2 - 2. 5 t 电动叉车新型传动系统的设计与计算 ( 主要针对制动系统) 。
2
z—摩擦副数量: 外摩擦片 z1 + 内摩擦片 z2 - 1 K —考虑摩擦花键连接的摩擦阻力对压紧力影 响的修正系数。 表1
摩擦副数 K 2 0. 99 4 0. 98 6 0. 97 8 0. 96 10 16 20
0. 95 0. 925 0. 91
Z p = 16 以上, 查表取 K 值约为 0. 925 。 将以上数值代入( 1 ) 式得: T = 2 × μ × F × R0 × Z × K = 2 × 0 . 11 × 9 177 × 0 . 057 × 8 × 0 . 925 T = 852 N·m, T 总 = 852 × 6 = 5 109. 4 N·m F b = 17 618. 8 N( 轮胎 23 × 9 - 10 , r = 0. 29 m) 摩擦片厚度 1. 8 mm, 隔片厚度 2. 8 mm, 单边总 厚 21. 2 mm。 制动能力: Cb = = Fb × 100 % m ×g 17 618 . 8 × 100 % ( 4 300 + 2 500 ) × 9 . 8
2
行车制动系统设计
2. 1 工作原理见图 1 、 图2
则对行车湿式制动器, 行车制动活塞面积: S = = 行车湿式制动器内置在连接板 9 内, 连接板 9 内部采用 5 个通孔以保证内部贯通, 当制动油液在 由制动螺钉进入连接板 9 上的 外界压强的作用下, 油道时, 活塞 10 就开始克服弹簧 17 的拉力而快速 移动, 进而压紧摩擦片 13 、 隔片 14 , 因隔片 14 固定 在连接板 9 上, 当摩擦片 13 与隔片 14 压紧时,就 又止动齿轮 15 通过花 使止动齿轮 15 停止了转动, 键与半轴 18 联接在一起, 所以半轴 18 停止了转 动, 最终半轴 18 通行星轮 8 、 行星架 7 对输出半轴 19 进行了止动。 2. 2 液压系统设计与计算 在设计方案中, 为避免复杂的液压系统设计及 因复杂的液压系统装置应用带来高昂的生产成本 , = 1 × π × ( D2 - d 2 ) 4 1 × 3. 14 × ( 0. 100 2 - 0. 090 2 ) 4 1 × 3. 14 × 0. 001 9 = 0. 00 149 m2 4
现代制造、 工艺装备 ·19· 单独的液压控制阀 ) , 通过止动悬浮半轴的方式进 液压系统( 图 3 ) 选用人力助力提供机械能推动制动 其采用的自润滑、 自冷的技术在国、 内外均 行制动, 属首创设计。停车制动器采用鼓式制动, 装在一级 减速处, 有着所需制动力小, 结构较紧凑, 装配及维 修性较好的特点。 介质转变为液压能进而再实现机械能的液压系统 , 该系统中的液压动力机构为借用 1 - 3. 5T 叉车通用 型制动总泵( 图 4 ) 。
ห้องสมุดไป่ตู้
= 26 % 为了使摩擦片有足够的使用寿命, 压紧力 F 应 由足够大的摩擦面积来承受, 即单位面积上的压力 — — — 比压 q 不能过大, 有: q = F / Am 式中: A m — 摩擦片工作表面的当量面积, 即摩擦面
2 积扣除沟槽后的净面积( m ) 。
= 0. 007 95 m
能提供的制动力矩: T = 2 × μ × F × R0 × Z × K 其中: μ—摩擦副的摩擦系数取 0. 11 ; F —作用在摩擦面上的压紧力。 ( 1)
·20·
× 2. 05 × 10 - 3 = 2 × 1. 49 × 10 - 3 × 2. 05 × 10 - 3 = 6. 11 mL ( 考虑涂胶的原因, 取行程为 2. 05 ± 0. 1 , 等于 2. 15 mm, 则 V = 6. 4 mL) 摩擦片磨损一定程度需要更换, 此时为修理极 限, 要求摩擦片单片磨损的程度≤0. 25 , 单片最大的 摩损量≤0. 1 , 则单边最大摩损量: h = 0. 25 × 4 + 0. 1 × 4 + 1. 6 = 3 mm 即活塞最大行程 l 最大 = 3 mm, 需流量 V 最大 : V 最大 = 2 × S × l =2 × 1 × 3. 14 × ( 0. 100 2 - 0. 090 2 ) × 3→ 4
The Brake of Wet Drive System for 2 - 2. 5 t Electric Forklift
MA Yi Abstract: The document introduces the current domestic electric forklift drive system due to the technology of the brake and lead to poor performance,mainly focuses on the 22. 5 tons of electric forklift ’ s wet transmission system for the breakthrough technology of brake system’ s limits, on the basis of repeated proof , through reverse design, positive verification method successfully designed with the world advanced technology products process. Key words: forklift ; multifunction wet multidisk brake; service brake; paking brake; torque