摇臂零件的工艺分析及夹具设计。
摇臂座工艺规程及夹具设计(全套图纸)-29页文档资料

目录1、“工艺规程及夹具设计”毕业设计指导书 (3)2、序言 (5)3、零件的分析 (6)4、工艺规程设计 (7)5、制订工艺路线 (8)6、工序Ⅰ粗铣Φ24mm底端面(40mm*32mm) (10)7、工序Ⅱ铣Ф24mm上端面 (12)8、工艺Ⅲ半精铣Ф24mm底端面 (14)9、工艺Ⅳ铣Ф18mm斜端面 (16)10、工序Ⅴ钻ø12.5mm孔 (17)mm)两端面 (19)11、工序Ⅵ、铣Ф34mm(24 +0.1012、工序Ⅶ、铣Ф28mm(16±0.20mm)两端面 (21)mm孔 (22)13、工序Ⅷ、钻、扩、铰ø20 +0.035mm孔 (24)14、工序Ⅸ、钻、扩、铰ø16 +0.03515、工序Ⅹ、去毛刺,检验 (26)16、夹具设计 (27)17、设计体会 (30)18、参考文献 (31)“工艺规程及夹具设计”毕业设计指导书一、毕业设计任务(一)设计题目:摇臂座工艺规程及夹具设计(二)、课题内容1、机械零件工艺规程及夹具设计:1)、重点研究和解决的问题--工艺过程方案及夹具方案的确定。
2)、设计工作量:每人完成①绘制加工零件图一张;②绘制工艺流程图一张;③编制工艺过程卡片一张;④编制工序卡片两张;⑤绘制指定夹具装配图两张;⑥绘制夹具零件(包括夹具体)图,共完成图纸工作量不少于A0两张。
⑦编写设计说明书一份约15000字。
二、设计步骤和方法毕业设计分实习、设计、答辩三阶段进行。
1、实习阶段:实习阶段的任务是调查研究,搜集资料。
提高确定工艺过程方案及夹具方案的感性认识;搜集现代制造工艺技术与传统工艺技术的联系与区别;生产类型与工装设计要求的关系。
实习时间为5周。
2、设计阶段:设计阶段的任务包括方案设计、图纸设计和编写技术文件等。
总设计时间为7周。
1)“工艺规程及夹具设计”题进度计划安排第一周借阅、熟悉资料,绘制零件图,对零件图进行工艺分析。
第二周编制工艺过程,绘制工艺流程图。
摇臂加工工艺规程及夹具设计
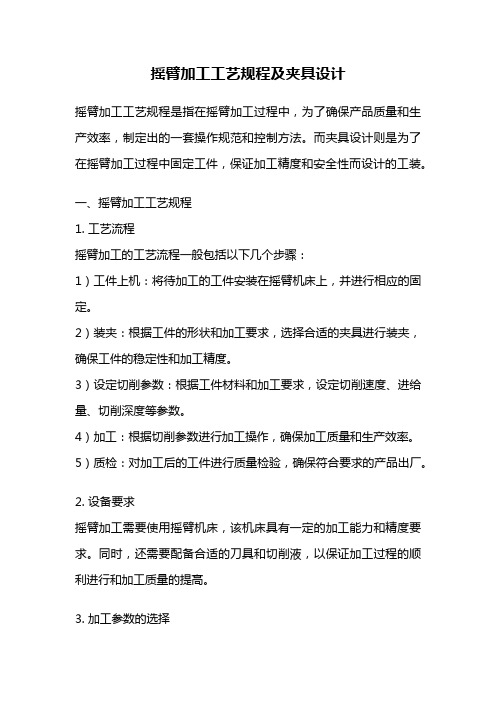
摇臂加工工艺规程及夹具设计摇臂加工工艺规程是指在摇臂加工过程中,为了确保产品质量和生产效率,制定出的一套操作规范和控制方法。
而夹具设计则是为了在摇臂加工过程中固定工件,保证加工精度和安全性而设计的工装。
一、摇臂加工工艺规程1. 工艺流程摇臂加工的工艺流程一般包括以下几个步骤:1)工件上机:将待加工的工件安装在摇臂机床上,并进行相应的固定。
2)装夹:根据工件的形状和加工要求,选择合适的夹具进行装夹,确保工件的稳定性和加工精度。
3)设定切削参数:根据工件材料和加工要求,设定切削速度、进给量、切削深度等参数。
4)加工:根据切削参数进行加工操作,确保加工质量和生产效率。
5)质检:对加工后的工件进行质量检验,确保符合要求的产品出厂。
2. 设备要求摇臂加工需要使用摇臂机床,该机床具有一定的加工能力和精度要求。
同时,还需要配备合适的刀具和切削液,以保证加工过程的顺利进行和加工质量的提高。
3. 加工参数的选择在摇臂加工中,选择合适的加工参数对于保证加工质量和提高生产效率至关重要。
加工参数包括切削速度、进给量、切削深度等。
不同的工件材料和形状需要选择不同的加工参数。
4. 质量控制摇臂加工过程中,需要进行质量控制,确保产品的加工精度和一致性。
质量控制包括加工过程中的监控和检验,以及对产品的最终质量进行评估和验证。
二、夹具设计1. 夹具的作用夹具在摇臂加工中起到固定工件的作用,保证加工过程中工件的稳定性和加工精度。
夹具设计的好坏直接影响到加工质量和生产效率。
2. 夹具的选择夹具的选择要根据工件的形状和加工要求来确定。
一般情况下,夹具应具备以下几个特点:1)稳定性:夹具要能够牢固地固定工件,确保加工过程中不发生移动或变形。
2)刚性:夹具要具备足够的刚性,以承受加工过程中的切削力和振动。
3)精度:夹具的设计要考虑到加工精度的要求,确保夹持工件的位置和角度精确。
4)易于操作:夹具设计要尽量简洁实用,便于操作和调整。
3. 夹具的设计原则夹具的设计应遵循以下原则:1)合理布局:夹具的各部件应布局合理,便于操作和调整。
新气门摇臂轴支座的机械加工工艺及夹具设计

新气门摇臂轴支座的机械加工工艺及夹具设计新气门摇臂轴支座的机械加工工艺及夹具设计新气门摇臂轴支座是一种汽车引擎部件,是连接气门和摇臂的重要支撑部位。
它的制造需要采用一定的机械加工工艺和相应的夹具设计,本文将对此进行探讨。
一、机械加工工艺1. 轴套加工首先需要进行的是轴套加工,这是因为轴套是与气门摇臂轴紧密配合的部件。
轴套的加工需要经过数道工序,其中包括车、铣、镗、插座螺纹等。
具体的步骤如下:(1)车削:采用车床将钢材进行加工成需要的形状和尺寸;(2)铣削:采用铣床对轴套进行平面加工,以保证其表面的光滑度和精度;(3)镗孔:采用数控加工中心进行孔径精度的控制,保证轴套与摇臂轴配合的紧密度;(4)插座螺纹:通过螺纹车床对轴套进行插座螺纹加工。
2. 支座加工在完成了轴套的加工后,需要对支座进行加工。
支座是固定在气门摇臂轴上的部件,其加工需要包含以下步骤:(1)车削:用车床将钢材进行加工成需要的形状和尺寸,如外形、凸台等;(2)锉削:用锉将支座的表面进行整形,以防止其表面存在毛刺或磨损;(3)钻孔:通过钻床进行定位孔和螺纹孔的加工。
3. 摇臂轴加工在完成了轴套和支座的加工后,需要进行摇臂轴的加工以保证其与轴套的精确配合,从而提高摇臂轴的实用性和寿命。
摇臂轴的加工需要包含以下步骤:(1)车削:采用车床将钢材进行加工成需要的形状和尺寸;(2)磨削:经过磨削,使摇臂轴的表面更加光滑、精确;(3)组合检测:通过检测手段,对摇臂轴、轴套和支座进行匹配测试,以保证精确配合。
二、夹具设计上述的机械加工工艺需要相应的夹具设计来实现。
夹具的设计需要考虑以下几个因素:1. 夹紧效果夹具的要求是能够紧密抱住工件,防止工件在加工过程中发生移动或扭曲变形。
因此,需要在设计过程中考虑工件的结构特点,精确的制定夹持力,确保夹具夹紧后不松动、不滑动。
2. 生产效率夹具设计应考虑向生产车间提供高效的加工条件。
夹具需要尽可能的实现快速、便捷的操作,以便提高生产效率和加工质量。
Z3050摇臂钻床回转盘的机械加工工艺规程及部分夹具设计

毕业设计Z3050摇臂钻床回转盘的机械加工工艺规程及部分夹具设计系、部:学生姓名:指导教师:职称专业:班级:完成时间:摘要本篇论文讲述的是Z3050摇臂钻床回转盘机械加工工艺及镗床夹具的设计,要求有实际生产指导意义。
首先,本论文讲述了一下设计Z3050摇臂钻床回转盘的作用和工艺分析。
然后,本论文就对Z3050摇臂钻床回转盘的生产纲领,生产类型等进行一些简单的介绍,主要提到回转盘的制造要求和工艺特点。
之后,论文开始进入具体的设计过程,先从总体上确立工艺规程的设计方案,确定毛坯的制造形式,定位基准的选择,零件表面加工方法的选择,加工顺序的安排,选择加工设备及刀具、夹具、量具,加工工序设计,夹具设计。
最后,是对此次设计进行总结,本书在编写过程中,得到了指导老师和同学的大力支持和热情的帮助,在此表示忠心的感谢。
关键词机床;定位;机床夹具;机械加工余量;基准ABSTRACTThis paper narration is the Z3050 radial drill drilling machine turn table machine-finishing craft and the boring lathe jig design, the request has the actual production guiding sense.First, the present paper narrated has designed the Z3050 radial drill drilling machine turn table the function and the craft analysis.Then, the present paper on carries on some simple introductions to the Z3050 radial drill drilling machine turn table function, mainly mentions the turn table the manufacture request and the craft characteristic.Afterwards, the paper starts to enter the concrete design process, as a whole establishes the technological process first the design proposal, definite semifinished materials manufacture form, localization datum choice, components face work method choice, processing order arrangement, selective treatment equipment and cutting tool, jig, measuring instrument, processing working procedure design, jig design.Finally, is carries on the summary to this design, this book in the compilation process, obtained has instructed teacher and schoolmate's vigorously support and the warm help, expressed loyal thanks.Key words machine tool ;allocation ;jig ;machining allowance ;benchmark目录摘要 (2)目录 (4)1. 回转盘的结构功用分析 (5)1.1 零件的作用 (5)1.2 零件的工艺分析 (5)2. 回转盘的生产纲领、生产类型和其他给定条件 (5)3. 工艺规程设计 (7)3.1 定位基准的选择 (7)3.2 零件表面加工方法的选择 (7)3.3 加工顺序的安排 (8)3.4 选择加工设备及刀具、夹具、量具 (10)3.5 加工工序设计 (10)3.5.1 工序四.粗刨方孔及端面,精刨方孔及Φ105端面,刨前用量的计算 (10)3.5.2 工序五.粗车的工序设计 (12)3.5.3 工序六.精车的工序设计 (16)3.5.4 工序七.铣削的工序设计 (18)3.5.5 工序八.钻4-Φ13,再刮4-Φ32孔 (19)3.5.6 工序九.镗孔 (20)3.6 时间定额的计算 (23)3.6.1 工序四的时间定额 (23)3.6.2 工序七的机动时间 (24)3.6.3 工序八的机动时间 (24)4.机床夹具设计 (25)5.总结 (27)参考文献 (28)致谢 (29)附录 (30)1 回转盘的结构功用分析1.1 零件的作用题目所给定的零件是Z3050摇臂钻床回转盘,它是钻床主轴上的一个重要零件,钻床主轴通过回转盘与钻头相连,回转盘与主轴用四个螺钉联接,实现钻床的正确联接。
摇臂加工工艺规程及夹具设计
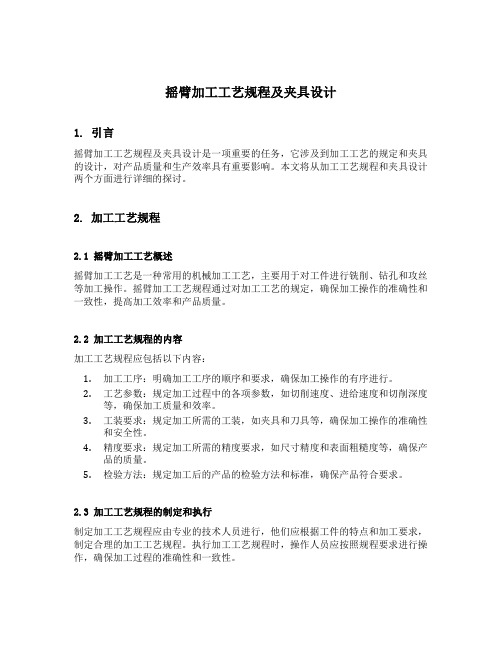
摇臂加工工艺规程及夹具设计1. 引言摇臂加工工艺规程及夹具设计是一项重要的任务,它涉及到加工工艺的规定和夹具的设计,对产品质量和生产效率具有重要影响。
本文将从加工工艺规程和夹具设计两个方面进行详细的探讨。
2. 加工工艺规程2.1 摇臂加工工艺概述摇臂加工工艺是一种常用的机械加工工艺,主要用于对工件进行铣削、钻孔和攻丝等加工操作。
摇臂加工工艺规程通过对加工工艺的规定,确保加工操作的准确性和一致性,提高加工效率和产品质量。
2.2 加工工艺规程的内容加工工艺规程应包括以下内容:1.加工工序:明确加工工序的顺序和要求,确保加工操作的有序进行。
2.工艺参数:规定加工过程中的各项参数,如切削速度、进给速度和切削深度等,确保加工质量和效率。
3.工装要求:规定加工所需的工装,如夹具和刀具等,确保加工操作的准确性和安全性。
4.精度要求:规定加工所需的精度要求,如尺寸精度和表面粗糙度等,确保产品的质量。
5.检验方法:规定加工后的产品的检验方法和标准,确保产品符合要求。
2.3 加工工艺规程的制定和执行制定加工工艺规程应由专业的技术人员进行,他们应根据工件的特点和加工要求,制定合理的加工工艺规程。
执行加工工艺规程时,操作人员应按照规程要求进行操作,确保加工过程的准确性和一致性。
3. 夹具设计3.1 夹具的作用和分类夹具是用于固定工件,使其能够稳定地进行加工操作的工具。
夹具的作用是提高加工效率和保证加工质量。
夹具根据其作用和结构可以分为以下几类:1.定位夹具:用于保证工件在加工过程中的位置准确。
2.紧固夹具:用于固定工件,保证其在加工过程中不移动。
3.装夹夹具:用于固定不规则形状的工件,保证其能够稳定地进行加工操作。
3.2 夹具设计的基本原则夹具设计应遵循以下基本原则:1.合理性原则:夹具的结构应合理,能够满足加工的需要。
2.稳定性原则:夹具应具有足够的稳定性,保证工件在加工过程中不移动。
3.易于操作原则:夹具的设计应便于操作,减少操作人员的劳动强度。
毕业设计-气门摇臂加工工艺及夹具设计

摘要机械加工行业作为一个传统而富有活力的行业,近几十年取得了突飞猛进的发展,在新经济时代,行业呈现新的发展趋势,由此对其它的质量,性能要求有了新的变化。
现在的机械加工行业发生着结构性变化,工艺工装的设计与改良已成为企业生存和发展的必要条件,工艺工装的设计与改良直接影响加工产品的质量与性能。
本文首先介绍了气门摇臂的加工方法和工艺分析,然后进行夹具设计。
此次设计是对气门摇臂的加工工艺和夹具设计,其零件为铸件,具有体积小,零件结构简单的特点,由于面比孔容易加工,在制定工艺规程时,就应该先加工面,再以面为基准来加工其它。
其中,各工序夹具都采用专用夹具,其机构设计简单,方便且能满足要求。
第一我们对产品(工件)的进行全面分析,确定了产品(工件)的毛坯设计,并附有生产工艺过程卡片以及工序卡片。
第二我们对数控加工工艺分析,主要是针对数控加工的内容,程序以及夹具的分析。
这次毕业设计是培养我独立分析与解决机械制造的实际课题的能力使我接受工程师的基本训练,并且使我在计算机绘图机编程、资料检索等方面得到锻炼与提高,同时也是对我三年大学所学知识的综合、全面运用和考查。
由于所掌握的知识和个人能力所限,设计尚有许多不足之处,恳请各位老师给予指导。
关键词:气门摇臂支座工艺分析工艺规程设计夹具设计气门摇臂加工工艺及夹具设计Xxxxxxx1.课题背景1.1 背景本设计所设计的零件是柴油机中摇臂结合部的气门摇臂,它是柴油机上气门控制系统的一个重要零件。
在内燃机中,每个气缸配备两个摇臂,摇臂穿于轴上,起作用在于:曲轴的旋转推动推杆上下运动,推杆推动轴上的摇臂做有规律的摆动,从而推动气门的开启与关闭,实现发动机的做功冲程。
其各部分尺寸在零件图中做详细标注。
柴油机是用柴油作燃料的内燃机。
柴油机属于压缩点火式发动机,它又常以主要发明者狄塞尔的名字被称为狄塞尔引擎。
柴油机在工作时,吸入柴油机气缸内的空气,因活塞的运动而受到较高程度的压缩,达到500~700℃的高温。
气门摇臂轴支座的机械加工工艺及夹具设计

1 绪论1.1本设计的内容及意义本次设计是在我们学完了大学的全部基础课,技术基础课以及专业课之后而进行。
这次设计目的在于使我们把这3年来所学的知识进行系统运用。
使我们对这3年来所学的知识进行进一步的巩固。
也是一次理论联系实际的训练。
通过本次设计使我们对设计加工的有了一次很大的提高,并使我们对以后的工作提供了一次宝贵的实践1.2课题背景知识1.2.1零件作用本设计所设计的零件是柴油机中摇臂结合部的气门摇臂轴支座,它是柴油机上气门控制系统的一个重要零件。
直径为18mm的孔和直径为16的孔用来装配摇臂轴,轴的两端各安装一进、排气气门摇臂。
直径为16mm的孔内装一个减压轴,用于降低汽缸内压力,便于启动柴油机。
两孔间距56mm,可以保证减压轴在摇臂上打开气门,实现减压。
两孔要求的表面粗糙度和位置精度较高,工作时会和轴相配合工作,起到支撑的作用,直径11的孔用M10的螺杆与汽缸盖相连,直径3的孔用来排油。
1.2.2柴油机相关知识介绍1.2.2.1柴油机历史法国出生的德裔工程师狄塞尔,在1897年研制成功可供实用的四冲程柴油机。
由于它明显地提高了热效率而引起人们的重视。
起初,柴油机用空气喷射燃料,附属装置庞大笨重,只用于固定作业。
二十世纪初,开始用于船舶,1905年制成第一台船用二冲程柴油机。
1922年,德国的博施发明机械喷射装置,逐渐替代了空气喷射。
二十世纪20年代后期出现了高速柴油机,并开始用于汽车。
到了50年代,一些结构性能更加完善的新型系列化、通用化的柴油机发展起来,从此柴油机进入了专业化大量生产阶段。
特别是在采用了废气涡轮增压技术以后,柴油机已成为现代动力机械中最重要的部分。
1.2.2.2 柴油机种类①按工作循环可分为四冲程和二冲程柴油机。
②按冷却方式可分为水冷和风冷柴油机。
③按进气方式可分为增压和非增压(自然吸气)柴油机。
④按转速可分为高速(大于1000转/分)、中速(300~1000转/分)和低速(小于300转/分)柴油机。
气门摇臂轴支座的机械加工工艺及夹具设计

气门摇臂轴支座的机械加工工艺及夹具设计工艺流程:1.材料准备:选择适合的材料,通常使用优质的合金钢材料。
将材料进行切割,确保尺寸大小符合需要。
2.粗加工:将切割好的原材料进行粗加工。
首先进行铣削工艺,使得材料的外形达到近似的形状。
然后进行车削工艺,将材料的尺寸进一步精确。
3.热处理:将粗加工好的材料进行热处理,以提高材料的硬度和耐磨性。
常见的热处理方法包括淬火、回火等。
4.精加工:经过热处理的材料再进行精加工。
主要包括车削、铣削、磨削等工艺,将材料的表面进行加工,使其更加平滑。
5.组装:将精加工好的零件进行组装,与其他部件连接起来,形成完整的气门摇臂轴支座。
注意在组装中要保持零件间的准确配合度。
夹具设计:夹具设计是为了在加工过程中稳定支撑和固定工件,使其能够准确地进行加工。
以下是气门摇臂轴支座夹具设计的一般步骤和注意事项。
1.确定夹具类型:根据气门摇臂轴支座的形状和加工要求,选择合适的夹具类型。
常用的夹具类型包括顶尖夹具、台站夹具、平板夹具等。
2.确定夹具夹持点:根据工件形状和加工要求,确定夹具夹持点的位置。
夹持点应能够保证工件的稳定,同时不影响加工工艺进行。
3.设计夹具结构:根据工件的形状和加工要求,设计夹具的结构。
夹具应具备稳定性、刚性和易操作性。
使用CAD软件进行绘制设计,并进行必要的强度计算。
4.确定夹具夹持力:根据工件的材料和加工要求,确定夹具夹持力的大小。
夹持力应能够保证工件在加工过程中不会发生位移和变形。
5.制造夹具:根据设计好的夹具图纸进行夹具的制造。
常用的制造工艺包括铣削、车削、线切割等。
6.调试夹具:制造完成后,对夹具进行调试,确保夹具的夹持力和稳定性符合要求。
总结:。
195柴油机摇臂轴座加工工艺及钻精镗Φ16孔的夹具设计

机械制造技术基础课程设计说明书设计题目:设计“摇臂轴座(195柴油机)”零件的加工工艺规程及“钻φ16的孔”工序的夹具设计专业班级;学生姓名:学生学号:指导教师:哈尔滨远东理工学院2013年 3 月 18 日机械制造技术基础课程设计任务书设计题目:设计“摇臂轴座(195柴油机)”零件的机械加工工艺规程及此零件“钻φ16的孔”工序的专用夹具设计内容:1.绘制零件图一张。
(要求计算机绘图)2.编制零件的加工工艺规程,并填写加工工艺过程卡及指定工序卡各一张。
3.设计指定工序的夹具,绘制夹具装配总图。
4.绘制夹具的非标零件图。
5.编写设计说明书一份。
班级:学生:指导教师:系主任:2013年3 月4 日序言机械制造技术基础课程设计是在学完了机械制造基础和大部分专业课,并进行了生产实习的基础上进行的又一个实践教学环节。
这次设计我们能综合运用机械制造基础中的基本理论,并结合生产实习中学到的实践知识,独立地分析和解决了零件机械制造工艺问题,在老师和同学的帮助下,我还对夹具,机床,刀具的的结构和工作原理有了更深的了解,不知不觉中我的图纸分析、结构设计能力都得到了提高,为今后的毕业设计及未来从事的工作打下了良好的基础。
在结束了《机械制造基础》及有关课程的学习后,通过本次的设计使我们所学的知识得到了巩固和加深,并培养了我们学会全面综合地运用所学知识,去分析和解决机械制造中的问题的能力。
由于能力有限,经验不足,设计中还有许多不足之处,希望老师多加指教。
一、零件的工艺分析及生产类型的确定1.零件的作用题目所给的零件是195柴油机摇臂轴支座,是柴油机的一个主要零件,.直径为16的孔用来装摇臂, 孔要求的表面粗糙度和位置精度不是很高,工作时与轴相配合工作,起支撑作用。
2.零件的工艺分析零件的材料为HT200,灰铸铁生产工艺简单,铸造性能优良,但塑性较差、脆性高,不适合磨削,为此以下是零件需要加工的表面以及加工表面之间的位置要求:φ的孔的平行度为0.1;(1)上下底面粗糙度均为6.3,底面与中心16φ的孔的(2)前端面粗糙度为3.2,后端面粗糙度6.3,前后端面与中心16垂直度为0.08;φ孔为10级精度,采用基孔制配合,粗糙度3.2;(3)中心16φ的孔的粗糙度12.5 。
摇臂支架夹具设计毕业设计

天津职业技术师范大学毕业设计(论文)题目摇臂支架制造工艺过程及工装设计班级姓名指导教师目录1 工件零件图 (2)1.1 零件图 (3)1.2零件技术要求分析 (3)2 毛坯 (4)2.1金属材料的分析 (4)2.2毛坯加工余量的确定 (5)3 加工方法的选择 (7)3.1 选前准备 (7)3.2 确定加工方法 (8)4 基准的选择和工艺路线 (9)4.1 粗基准选择 (9)4.2 精基准选择 (9)4.3 加工顺序 (10)4.4 工艺路线 (11)5 机床和刀具 (13)6 加工余量 (14)6.1 加工余量确定方法 (14)6.2 机械加工余量、工序尺寸及毛坯尺寸的确定 (14)6.2.1工序尺寸的确定方法 (14)6.2.2机械加工余量、毛坯尺寸的确定: (15)6.3 各工序的切削用量的选择 (16)7 工装设计 (25)7.1概述 (25)7.2工装夹具设计方案的确定 (25)7.2.1基准面的选择 (25)7.2.2定位方式及元器件选择 (26)7.2.3夹紧方式及元器件选择 (26)7.2.4装配方案 (26)7.2.5 夹具体总装图 (27)7.3主要零件设计的说明 (27)7.4工装夹具的装配要求 (28)7.5工装夹具的使用说明 (28)致谢 ............................................................ 错误!未定义书签。
参考文献 (29)摘要:运用所学知识,进行摇臂支架制造工艺过程的设计,达到熟练掌握运用所学课程的目的,为以后进一步深造做准备。
首先对零件图进行技术要求分析,并熟悉材料种类和用途,选出各表面的加工方法,确定加工余量和基准,安排加工顺序,选出所用的机床、刀具、夹具、量具,设计工装,并且编写出一套工艺规程和工艺卡片。
同时用AutoCAD绘出工程图和工装图。
关键词:摇臂支架工艺 AutoCAD1 工件零件图1.1 零件图叉架类零件包括拨叉、支架、连杆、杠杆等,它们多为铸件或锻件,结构形状变化较大,也较为复杂,机械加工的工序常不相同。
钻床夹具设计剖析

3.辅助装置
(1)钻套 从国家标准中选用。
(2)钻模板
4.夹具体
五、绘制夹具总图
二、定位方案与定位元件
1.确定定位方案
2.选用定位元件
三、夹紧方案及夹紧装置的设计
夹紧机构
四、夹具结构设计
1.定位装置
(1)销轴
(2)可调支承钉 可调支承钉在GB JB/T 8026.1-1999(六角头支承)中 选取M8×40-S。
(3)辅助螺旋支承
2.夹紧装置
(1)夹紧 选用M10螺纹以满足强度要求。 (2)开口垫圈
钻床夹具设计
一、明确设计任务
设计在摇臂钻床上加工杠杆臂零件上孔φ10
0.1 0
mm和
φ13mm的钻夹具。
1.杠杆臂零件图
2.杠杆臂加工工艺分析
(1)加工要求
(2) 加工工艺
该工件的结构形状比较不规则,臂部刚性不足,加 工孔φ10 mm位于悬臂结构处,且该孔精度和表面粗糙度 要求高,故工艺规程中分钻、扩、铰多个工序。由于该 工序中两个孔的位置关系为相互垂直,且不在同一个平 面里,要钻完一个孔后翻转90°再钻削另一个孔,因此 要设计成翻转式钻夹具。
气门摇臂轴支座加工工艺及夹具设计
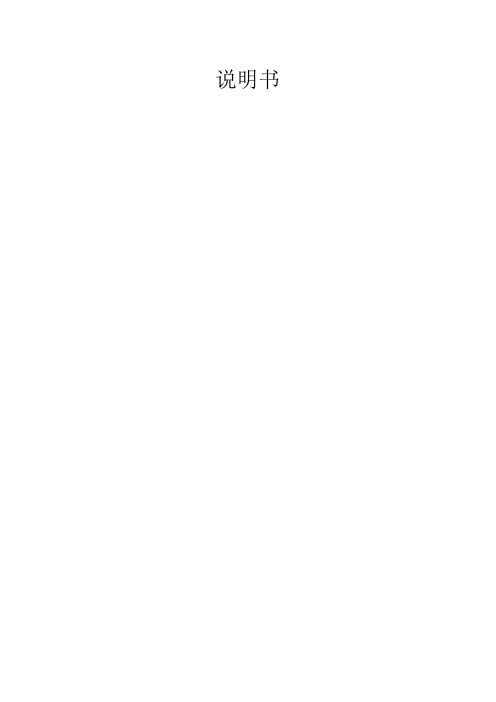
说明书任务书目录第一章、零件的工艺分析及生产类型的确定错误!未定义书签。
零件的分析...................................................................................... 错误!未定义书签。
(一) 零件的作用 ............................................................................ 错误!未定义书签。
(二) 零件的工艺分析 .................................................................... 错误!未定义书签。
(三) 零件的生产类型 (4)第二章、毛坯的选择与设计 51、确定毛坯种类 (5)2、确定铸件加工余量: (5)3、定毛坯尺寸 (6)4、毛坯图 (6)第三章、工艺规程的设计7(一)、选择定位基准: (7)(二)、零件表面加工方法的选择 (7)(三)制定工艺路线 (8)(四)工序设计 (12)(五)确定切削用量及工时定额的计算 (15)1、确定切削用量 (15)2、工时定额的确定18第四章夹具设计------------------------------------------144.1问题的提出-----------------------------------------144.2夹具的设计-----------------------------------------144.2.1 定位基准的选择-------------------------------144.2.2定位误差分析----------------------------------144.2.3夹紧装置的设计--------------------------------154.2.4切削力及夹紧力的计算--------------------------164.2.4.1切削力的计算----------------------------164.2.4.2夹紧力的确定----------------------------164.2.4.3液压缸的选择----------------------------174.2.5校验夹紧元件的强度----------------------------184.2.6液压控制回路的确定----------------------------194.2.6.1分析液压缸在夹具各工作过程的动作---------194.2.6.2液压回路的综合和整理---------------------204.2.7 夹具的使用及维护-----------------------------20第五章结论----------------------------------------------参考文献-------------------------------------------------致谢-----------------------------------------------------一零件的分析(一) 零件的作用参照p70(二)零件的工艺分析零件的材料为HT200,灰铸铁生产工艺简单,铸造性能优良,但塑性较差、脆性高,不适合磨削,为此以下是零件需要加工的表面以及加工表面之间的位置要求:1、22φ外圆的上端面以及与此孔相通的Φ11的通孔,粗糙度均为12.52、36mm 的下表面,粗糙度为6.3。
摇臂两斜孔钻夹具的设计与分析

由 公差 I T 1 2 级计算 ) 公差 0 . 3 a r m的 1 / 3 , 因此满足定位要求。 端
面定位 , 位移误差为零 。
3 _ 2 对刀误 差分析 使用钻模 加工孔产 生对刀误 差 的原 因 主要 有 以下 几点 : ( 1 ) 钻模板底孔定位元件 的尺寸差 D L 。( 2 ) 快换 钻套内外圈的同
轴度 e l 。 ( 3 ) 衬套 内外 圈的同轴度 e 2 。 ( 4 ) 快换钻套 与衬套 的最大 间隙 e 3 。 ( 5 ) 钻套 与刀具之间的最大间隙 x l 。 f 6 ) M具在钻套 中的
1 5 8 0 . 4 N。
3 . 4 钻套 的选用和设计
钻套 用来 引导钻头等孔加工刀具 ,提高刀具刚度并保 证 被加工孔与工件其他表面的相对位置 。 根据其结构和使用情况 分 为固定式 、 可换式 、 快换 式 、 和特殊钻套 , 前三种 已经标准化 。 本夹具在设计 时考虑到工件有钻底 孔和攻螺纹两道工序 。 所 用 选 用快换钻套并按 以下原则确定钻套 的尺寸及公差与配合 : ( 1 ) 在加 工 中, 钻套 与刀具会 产生摩擦 , 所 以钻 套必须 有 较高的耐磨性 。如钻套孔径 d ≤q b 2 6 m m, 用T 1 0 A钢制造 淬火
( 3 ) 钻 削钢件 时取 h = ( 0 . 7 — 1 . 5 ) d , 钻削铸铁 时排 屑空 间取
h = ( 0 . 3 — 0 . 7 ) d工件精度要求高时 , 可取 h = 0 , 本夹具 中工件为铸
Z3050×16立柱摇臂升降钻床壳体的加工工艺及夹具设计

毕业设计(论文)Z3050³16立柱摇臂升降钻床壳体的加工工艺及夹具设计专业名称:所在班级:学生姓名:指导老师:设计时间:2014年5月毕业设计任务书一.设计课题:Z3050³16立柱摇臂升降钻床壳体加工工艺及夹具设计。
二.设计任务书:1.壳体机加工工艺过程卡片 1张2.壳体机加工工序卡片 1套3.壳体产品图 1张4.壳体毛坯图 1张5.壳体夹具装配图 1张6.壳体夹具的主要零部件图 3—4张7.设计说明书 1份指导老师:2014年5月目录一.前言二.零件的分析三.零件的材料及毛坯种类的选择四.零件机加工时的主要问题五.基准的选择六.工艺路线的制定七.机械加工余量.工序尺寸.毛坯尺寸的确定八.加工设备的选定九.确定切削用量及基本工时十.专业夹具设计十一.参考文献十二.毕业设计总结前言在前面的实习过程中,我了解了一些产品的加工工艺过程,还见识了一些先进的机械加工设备和生产方法。
工艺是生产中最活跃的因素,既是构思和想法,又是实在的方法和手段。
工艺设计是生产加工中的核心内容之一。
本次设计要求编制一个中等复杂程度零件的机械加工工艺规程,按指导老师的指定设计其中一道工序的专用夹具,并撰写设计说明书。
本次设计是在我们学完了大学的全部基础课.技术基础课以及专业课之后,结束了毕业实习后进行的。
这是我们对三年大学所学各课程的一次深入的综合性的总复习,也是一次理论联系实际的训练。
就我个人而言,我希望能通过这次课程设计对自己未来将从事的工作进行一次适应性训练,从中锻炼自己分析问题,解决问题的能力,为今后参加祖国的现代化建设的下一个良好的基础。
当然,由于本人知识结构的不完善,欠缺实际生产工作经验,还缺少必要的工艺实验和现场调研,设计中尚存在许多不完善,不合理的地方,恳请各位老师批评指正。
零件的分析2.1 零件的作用分析题目所给定的零件是Z3050³16立柱摇臂升降钻床壳体(见附图)。
该零件为箱体类零件,它有六个外表面均需加工,孔系的加工精度高,此外,还需加工一系列的螺级孔。
气门摇臂轴支座零件数控加工工艺及夹具设计

北京联合大学毕业设计(论文)题目申报表
题目名称
气门摇臂轴支座零件数控加工工艺及夹具设计题ຫໍສະໝຸດ 性质工程设计题目类型
模拟
题目来源
自拟
毕设地点
校内
导师姓名
性别
年龄
职称
所在单位
所学专业
电话
课题简介:(主要内容、现有条件、时间安排、预期成果及表现形式。)
主要内容:
产量为10000台/年,1件/台,每日1班。零件材料为HT200。
(4)设计指定工序的专用夹具,绘制装配总图和主要零件图。
(5)撰写毕业设计说明书。
现有条件:工艺设计手册及机械绘图软件。
时间安排:
序号
设计(论文)各阶段任务
时间安排
1
明确设计要求,查阅文献,收集有关资料
第1周
2
撰写开题报告
第2周
3
零件的结构及工艺分析,填写工艺文件
工艺规程方案选择设计
第3-5周
4
夹具结构方案的设计及精度的校核
第6-7周
5
绘制夹具总图及零件图
第8-9周
6
编写设计说明书
第10-11周
7
答辩
第12周
预期成果及表现形式:
(1)零件图二维、三维各1张A3
(2)机械加工工艺卡片1套A3
(3)夹具总装图1张A0
(4)夹具主要部件图和零件图若干张
(5)毕业设计说明书1份
申报人姓名:日期:2012-11-16
审查人意见:签名:
(1)确定生产类型,对零件进行工艺分析,画二维、三维零件图。
(2)确定毛坯种类及制造方法;拟定零件的数控加工工艺过程;选择各工序的加工设备和工艺装备(刀具、量具、夹具、辅具);确定各工序加工余量和工序尺寸;计算各工序的切削用量和工时定额,进行技术经济分析;编制数控加工程序。
机械工艺夹具毕业设计156气门摇臂铣油槽夹具工艺设计设计
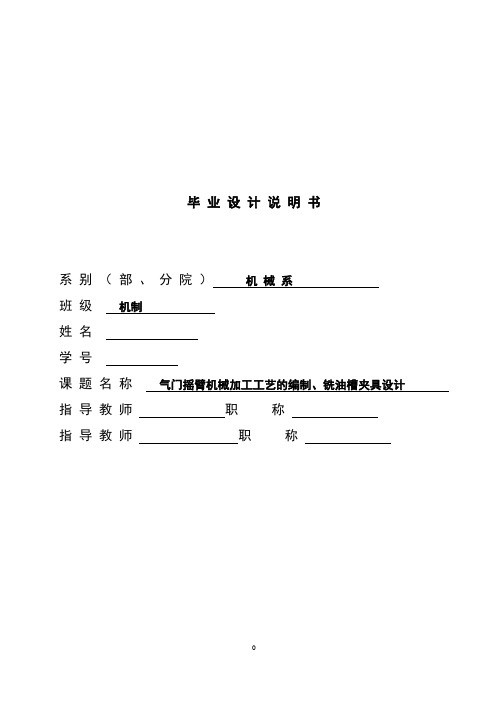
毕业设计说明书系别(部、分院)机械系班级机制姓名学号课题名称气门摇臂机械加工工艺的编制、铣油槽夹具设计指导教师职称指导教师职称目录一、毕业设计任务书二、毕业设计说明书(一)、绪论1.1本设计的内容及意义1.2课题背景知识(二)、零件的造型2.1零件造型软件介绍(三)、零件的工艺分析3.1零件的功用分析3.2零件的工艺分析(四)、零件工艺规程设计4.1确定毛坯的制造形式4.2定位基准的选择4.3拟定零件加工的工艺路线4.4机械加工余量、工序尺寸及毛坯尺寸的确定4.5确定切削用量及工时定额(五)、专用夹具设计5.1问题的提出5.2夹具设计(六)、存在的问题6.1存在的问题三、毕业设计小结与感悟四、参考文献五、致谢六、外文翻译(一)、绪论1.1本设计的内容及意义本次设计是在我们学完了大学的全部基础课,技术基础课以及专业课之后而进行的。
此次的设计是对大学期间所学各课程及相关的应用绘图软件的一次深入的全面的综合性的总复习,也是一次理论联系实际的训练。
其目的在于:1.巩固我们在大学里所学的知识,也是对以前所学知识的综合性的检验;2.增强我们查阅资料的能力,熟悉相关资料;3.树立正确的设计思想,掌握设计方法,培养我们的实际工作能力;4.通过对气门摇臂加工工艺的编制及油槽铣夹具的工装设计,使我们在机械制造工艺过程设计,工艺方案论证,机械加工余量计算,工艺尺寸的确定,编写技术文件及查阅技术文献等各个方面都得到了一次综合性的训练。
初步具备了一个中等复杂程度零件的工艺规程能力。
5.能根据被加工零件的技术要求,运用夹具设计的基本原理和方法,学会拟定夹具设计方案,完成夹具结构设计,初步具备设计出高效,省力,经济合理并能保证加工质量的专用夹具。
6.通过零件图,毛坯图,夹具装配图的绘制,使我们对于AutoCAD绘图软件的使用熟练程度进一步提高。
本次设计的主要内容为:首先应用AutoCAD绘图软件绘制气门摇臂的二维零件图,然后根据图纸的技术要求等确定零件的生产类型。
摇臂机械加工工艺及夹具设计(两套钻夹具设计)

摘要使用一般的夹具对摇臂的空进行加工时,鉴于摇臂的弯曲角度和孔的位置限制,不方便对摇臂进行夹紧固定加工。
为了更方便地对摇臂进行机械加工,我们必须要设计相对应的专用夹具。
通过对摇臂的结构的观察得出需设计出两个专门的摇臂钻床夹具对摇臂进行夹紧固定。
设计结果得知,在使用专门夹具夹紧摇臂加工时,能有效地对摇臂进行夹紧,并提高了孔的位置精度。
关键词:摇臂专用夹具位置精度谢谢您对文章的赏识!!!!AbstractThe use of general fixture on the rocker arm of the air processing, in view of the rocker arm bending angle and the hole position limit, not conveniently to the rocker arm for clamping and fixing process. In order to more easily to the rocker machining, we must design the corresponding fixture. Based on the observation that required rocker structure design of two specialized drill fixture on the rocker arm for clamping and fixing. Design results, in the use of special clamping fixture rocker processing, can effectively on rocker arm for gripping, and improve the position precision of the holes.Key words: rocker arm fixture Position accuracy目录一、前言 (3)二、零件的分析 (4)(一)零件的作用 (5)(二)零件的工艺分析 (5)三、确定毛坯图 (5)四、工艺规程设计 (5)(一)定位基准的选择 (6)(二)制订工艺路线 (6)(三)选择加工设备及刀具、夹具、量具 (6)(四)加工工序设计 (7)五、填写机械加工工艺过程卡和机械加工工艺卡 (13)六、夹具设计 (13)七、致谢词 (18)八、参考文献 (20)前言本次设计是为毕业答辩而准备的。
- 1、下载文档前请自行甄别文档内容的完整性,平台不提供额外的编辑、内容补充、找答案等附加服务。
- 2、"仅部分预览"的文档,不可在线预览部分如存在完整性等问题,可反馈申请退款(可完整预览的文档不适用该条件!)。
- 3、如文档侵犯您的权益,请联系客服反馈,我们会尽快为您处理(人工客服工作时间:9:00-18:30)。
目录1绪论 (1)2零件工艺性分析 (2)2.1零件的总体结构分析 (2)2.2零件的形状以及尺寸分析 (2)2.3零件技术条件分析 (3)2.3.1表面精度 (3)2.3.2表面间的位置精度 (3)2.4零件图尺寸标注分析以及基准的确定 (3)2.4.1选择定位基准的原则 (3)2.4.2摇臂定位基准的选择 (3)2.5零件的工艺性分析 (4)3加工工艺方案的确定 (5)3.1加工工艺方案的拟定 (5)3.2加工工艺方案的确定 (5)3.3重要工序的分析 (7)3.4工序的阶段划分 (7)3.4.1工序的划分 (7)3.4.2工序的安排 (7)4设备与工艺参数的选择及工艺文件的制定 (9)4.1毛坯的选择 (9)4.1.1毛坯的余量 (9)4.1.2毛坯的技术要求及说明 (9)4.2机床的选择 (9)4.3刀具材料的选择 (9)4.4冷却液的选择 (10)4.5工艺参数的选择 (11)4.5.1主轴转速的确定 (12)4.5.2进给速度的确定 (13)4.5.3切削时刀具材料应具备的性能 (15)4.5.4背吃刀具的确定 (15)4.6量具的选择 (15)4.7制定工艺文件 (16)4.8刀具卡 (17)5钻削 14mm孔的钻模设计 (18)5.1设计的准备 (19)5.2方案设计 (19)5.3确定装夹方案 (21)5.3.1 工件的夹紧 (21)5.3.2 斜楔夹紧机构 (25)6夹具的零部件设计 (28)6.1钻套的尺寸、公差、材料 (28)6.2钻模板设计 (29)6.3支脚设计 (29)6.4钻模夹具的误差分析 (29)6.5手柄的设计 (31)6.6夹具体的设计 (31)7夹具总体设计步骤 (33)7.1尺寸确定与工艺要求的标注 (36)7.2夹具构造特点及原理 (36)7.3夹具装配图 (36)结论 (37)致谢 (38)参考文献 (39)附录 (40)1 绪论随着社会生产和科学技术的不断发展,机械产品日趋精密、复杂,人们对机械产品的质量和生产率也提出了越来越高的要求。
尤其是航天、军事、造船等领域所需要的零件,精度要求越来越高,形状也越来越复杂,这些零件用普通机床和通用夹具是难以加工的。
数控机床是用数字化信号对机床的运动及其加工过程进行控制的机床,或者说是装备了数控系统的机床。
它是一种技术密集度及自动化程度很高的机电一体化加工设备是数控技术与机床相结合的产物。
数控加工则是根据被加工零件的图样和工艺要求,编制出以数码表示的程序,输入到机床的数控装置或控制计算机中,以控制工件和刀具的相对运动,使之加工出合格工件的一种加工方法。
在数控加工过程中,如果数控机床是硬件的话,数控工艺和数控程序就相当于软件,两者缺一不可。
数控加工工艺是伴随着数控机床的产生、发展而逐步完善的一种应用技术。
实现数控加工,编程是关键。
编程前必须要做好必要的准备工作,编程后还要进行必要的善后处理工作。
严格来说,数控编程也属于数控加工工艺的范畴。
对于一个零件的加工来说,首先进行工艺分析后,然后制定出工艺规程卡,也就是要按工艺规程顺序进行加工。
加工中除了需要机床、刀具、量具之外,还需要机床夹具。
它们是机床和工件之间的连接装置,使工件相对于机床或刀具获得正确的位置。
机床夹具的好坏将直接影响工件加工表面的位置精度,所以夹具设计是装配设计中一项重要的工作,是加工过程中最活跃的因素之一。
机床夹具包括通用夹具,专用夹具,可调整夹具和成组夹具,组合夹具和随行夹具,本篇设计的主要是立式钻床在钻削摇臂零件 14mm孔的专用夹具,它是针对某一工件某一工序的加工要求而专门设计和制造的夹具。
其特点是针对性强,没有通用性。
产品相对稳定,批量较大的生产中,常用各种专用夹具,可获得较高的生产效率和加工精度,同时降低了劳动强度,提高了机床的适用范围。
机床夹具设计涉及到多个领域的知识,涉及最多的是机械设计,机械设计本身受到各方面的限制,在一定的限制中要求有最合理的设计思想,最合理的设计结果,达到人们所渴望的要求,满足生产的需要。
设计要有创新还要易于实现,因此设计要从实际出发,围绕着实际的问题而进行。
2 零件工艺性分析2.1零件的总体结构分析从图2-1可以看出,摇臂是由铸铁经铣削、钻削等手段加工而成的零件。
总体看来,整体的精度要求并不是很高,零件的表面粗糙度的要求也不是很高。
图2-1摇臂零件2.2零件的形状以及尺寸分析零件左边孔的尺寸为φ20H7,并且加工出半径为2mm 的倒角,和一个锥度为1:8的锥孔,表面粗糙度无特殊要求,零件右边有一个为φ31H7的一个通孔,是后续加工孔的一个定向位置公差(垂直度)的基准孔,距φ31H7孔02.025.20-mm 处有一个垂直于φ31H7孔且公称尺寸为φ14mm 的孔,其表面粗糙度为6.3μm ,摇臂左右两端的前后平面、右端的左右两侧面及开口槽,都是该零件的加工内容,具体见图2-1所示。
2.3零件技术条件分析2.3.1表面精度总体看来摇臂的表面精度要求不是很高,整个零件的强度也不是很高。
端面粗糙度是该零件要求最高的可达到3.2μm,φ14mm 的孔粗糙度为6.5μm ,其余表面的粗糙度都是12.5μm 。
2.3.2表面间的位置精度在零件加工过程中φ31H7的孔中线为加工φ14mm 孔中线表面间的位置精度基准,与φ14mm 孔要保持一定的垂直度,垂直度误差不得超过0.15μm 。
2.4零件图尺寸标注分析以及基准的确定2.4.1选择定位基准的原则(1)尽量选择零件上的设计基准作为定位基准。
(2)当零件的定位基准与设计基准不能重合,且加工面与其设计基准又不能在一次安装内同时加工时,应认真分析零件图纸,确定该零件设计基准的设计功能,通过尺寸链的计算,严格规定定位基准与设计基准间的公差范围,确保加工精度。
(3)当在加工中心上无法同时完成包括设计基准在内的全部表面加工时,要考虑所选基准定位后,一次装夹能够完成全部关键精度部位的加工。
(4)定位基准的选择要保证完成尽可能多的加工内容。
(5)若批量加工时,零件定位基准应尽可能与建立工件坐标系的对刀基准(对刀后,工件坐标系原点与定位基准间的尺寸为定值)重合。
(6)必须多次安装时应遵循从基准统一原则。
2.4.2摇臂定位基准的选择如零件图2-1尺寸标注所示,中心线为工序基准,将摇臂左边φ20H7的孔确定后,以后的工序中孔的位置,成型面的位置都是以大圆端面为工序基准确定的,而孔的深度,沿轴线的两切面等都是以轴线为设计基准的。
以加工后工件的加工孔的定位尺寸为16±0.01mm 、02.025.20-mm ,被加工孔φ14mm 与φ20H7孔需要保持位置关系。
2.5零件的工艺性分析零件中主要是孔的加工和平面的加工,通过以上对零件的分析,加工φ14mm和φ31H7孔时工件与夹具所产生的总重力超过了150N,宜采用摇臂钻床或立式钻床,由于该工件是中批量生产,则采用立式钻床;为提高生产效率,在加工平面φ20H7的倒角及锥孔时,普通机床难以实现,宜采用用数控铣床或加工中心进行铣削加工,并辅以专用夹具进行加工。
3 加工工艺方案的确定3.1加工工艺方案的拟定由上面的零件结构分析可知:主要包括通孔、锥孔、倒角、平面、及开口槽。
以已加工表面为定位基准面,再综合其他精度要求和一些细节问题可以初步确定如下二个方案:方案一:铣摇臂左端下平面铣左端上平面钻φ20H7孔铣φ20H7孔倒角铣左端上平面铣1:8的锥孔铣右端下平面铣右端上平面右末端左右两平面粗铣开口槽精铣开口槽钻φ14mm中心孔钻φ14mm孔。
方案二:铣摇臂左右两端上端平面铣摇臂左右两端下平面铣1:8锥度钻φ31H7中心孔扩φ31H7孔粗镗φ31H7孔精镗φ31H7孔粗铣倒角精铣倒角粗铣右末端左右两平面精铣右末端左右两平面粗铣开口槽精铣开口槽钻φ14mm中心孔钻φ14mm孔。
3.2加工工艺方案的确定分析:在具有良好冷却系统的数控机床上,对于毛坯质量高、加工余量较小、加工精度要求不高或新产品试制等单件的零件,也可把粗、精加工合并进行,对于该零件,毛胚是铸造结构,平面几乎只有3mm左右的余量,所以在加工左右两端上下平面的时候,可把粗精加工放在一起;在零件开口槽、倒角、锥孔处,毛胚是封闭的,所以应在铣开口槽、倒角、锥度的时候,把粗精加工应划分成两道工序分别完成:钻削孔的时候,要先钻中心孔,以确定孔位置的准确性。
方案一的具体分析如下:第一次装夹:铣左端下平面,使之成为铣左端上平面的定位基准面。
刀具选择φ20mm 的端铣刀,在专用夹具上装夹,在数控铣床上加工。
第二次装夹:以铣后的下平面为定位基准面,铣左端上平面,再钻φ20H7孔,铣φ20H7孔倒角。
铣平面选用φ20mm的端铣刀,钻孔采用φ20mm麻花钻,倒角选用φ12mm的立铣刀,用专用夹具装夹,为减少装卸次数在加工中心上加工。
第三次装夹:铣右端下平面使之成为铣右端上平面的定位基准面。
刀具选择φ20mm 的端铣刀,用专用夹具装夹,在数控铣床上加工。
第四次装夹:以铣后的右端下面为定位基准面铣右端上平面。
刀具选择φ20mm的端铣刀,用专用夹具定位夹紧,在数控铣床上加工。
第五次装夹:铣摇臂左端1:8锥孔,用φ12mm的立铣刀,用专用夹具上定位夹紧,由于加工内容单一,机床选用数控铣床。
第六次装夹:铣右末端左右两个平面及开口槽,刀具选择φ12mm的立铣刀和φ6mm的立铣刀,在铣开口槽时要把粗精加工分开安排为两次工步,在专用夹具上装夹,为减少装夹次数,采取两次换刀,在加工中心上加工。
第七次装夹:钻削钻φ14mm孔的中心孔,选用A5mm的中心钻在专用夹具上定位装夹,机床选用立式钻床。
第八次装夹:钻φ14mm孔,选用φ14mm的麻花钻在专用夹具上定位装夹。
机床采用立式钻床。
优点:遵循了先面后孔的原则,在一定程度上也能提高生产率。
缺点:工序分布太散,没有必要先钻削的孔,再进行倒角,铣锥度,还有单独钻削的孔,定位更准确,同时加工的精度也更高方案二的具体分析:第一次装夹:铣摇臂左右端上平面,使之成为铣左右两端下平面的定位基准面。
刀具选择φ20mm的端铣刀,在专用夹具上装夹,在数控铣床上加工。
第二次装夹:以铣削后的上平面作为定位基准面,铣削摇臂左右端下平面,刀具选择φ20mm的端铣刀;铣摇臂左端1:8锥孔,用φ10mm的锥度铣刀;钻φ31H7中心孔,扩φ31H7孔,再粗镗φ31H7孔,最后精镗φ31H7孔,用的A5mm的中心钻、φ20mm的扩孔钻φ31mm的镗刀。
在专用夹具上装夹,为减少装卸次数采取5次换刀,在加工中心上加工。
第三次装夹:以摇臂左端下平面为定位基准面,铣C2的倒角,刀具选择φ12mm的球头铣刀,在专用的夹具上定位装夹,由于加工内容单一,故选择数控铣床进行加工。