煤中硫分对水泥易烧性的影响
氧化镁、碱、氯、硫和微量元素对烧成及水泥品质的影响
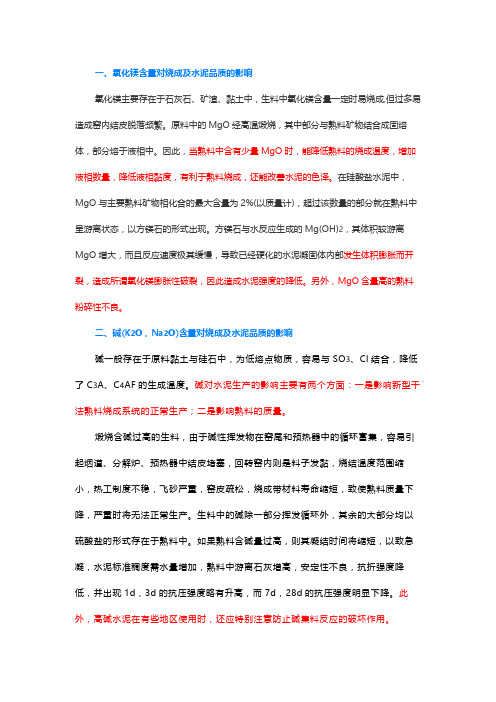
一、氧化镁含量对烧成及水泥品质的影响氧化镁主要存在于石灰石、矿渣、黏土中,生料中氧化镁含量一定时易烧成,但过多易造成窑内结皮脱落频繁。
原料中的MgO经高温煅烧,其中部分与熟料矿物结合成固熔体,部分熔于液相中。
因此,当熟料中含有少量MgO时,能降低熟料的烧成温度,增加液相数量,降低液相黏度,有利于熟料烧成,还能改善水泥的色泽。
在硅酸盐水泥中,MgO与主要熟料矿物相化合的最大含量为2%(以质量计),超过该数量的部分就在熟料中呈游离状态,以方镁石的形式出现。
方镁石与水反应生成的Mg(OH)2,其体积较游离MgO增大,而且反应速度极其缓慢,导致已经硬化的水泥凝固体内部发生体积膨胀而开裂,造成所谓氧化镁膨胀性破裂,因此造成水泥强度的降低。
另外,MgO含量高的熟料粉碎性不良。
二、碱(K2O,Na2O)含量对烧成及水泥品质的影响碱一般存在于原料黏土与硅石中,为低熔点物质,容易与SO3、Cl结合,降低了C3A、C4AF的生成温度。
碱对水泥生产的影响主要有两个方面:一是影响新型干法熟料烧成系统的正常生产;二是影响熟料的质量。
煅烧含碱过高的生料,由于碱性挥发物在窑尾和预热器中的循环富集,容易引起烟道、分解炉、预热器中结皮堵塞,回转窑内则是料子发黏,烧结温度范围缩小,热工制度不稳,飞砂严重,窑皮疏松,烧成带材料寿命缩短,致使熟料质量下降,严重时将无法正常生产。
生料中的碱除一部分挥发循环外,其余的大部分均以硫酸盐的形式存在于熟料中。
如果熟料含碱量过高,则其凝结时间将缩短,以致急凝,水泥标准稠度需水量增加,熟料中游离石灰增高,安定性不良,抗折强度降低,并出现1d,3d的抗压强度略有升高,而7d,28d的抗压强度明显下降。
此外,高碱水泥在有些地区使用时,还应特别注意防止碱集料反应的破坏作用。
三、氯含量对烧成及水泥品质的影响氯主要存在于石灰石、矿渣与燃料中,是低熔点物质,易和碱结合,成为旋风筒堵塞的原因。
氯在烧成系统中主要生成CaCl2或氯化碱,其挥发性特别高,在窑内几乎全部再次挥发,形成氯、碱循环富集,致使预热器生料中氯化物的含量提高近百倍,引起预热器结皮堵塞。
硫对铝酸盐水泥物相组成和浇注料性能的影响

是 由燃 煤造成 的 j。文献 [7]报道 ,在硅 酸盐 水泥 的生 产 过程 中 ,煤燃 烧放 出的 SO:能与 水泥 生 料反 应生 成 硫铝 酸钙 (3CaO·3A1 0 ·CaSO ,即 C S)而得 到 固 定 ,降低 SO:排放 。在铝酸盐水 泥 的生产 过 程 中 ,煤 中 的硫 能否与水 泥生料反应 生成 c s,对铝 酸盐水泥结 合浇 注料 的施 工性能有何 影响 ,目前还 未见报道 。
表 1 原料的化学组成
用 s4 Pioneer X射线荧光仪对煅烧矾土和水泥进 行化学组成分析,采用 CS-206型碳硫仪进行全硫分析。
用 x’Pert Pro X射线衍射仪对水泥熟料进行物 相分 析 ,用 Nova Nano SEM 400扫 描 电子 显 微 镜 并 结
张 业 范 :男 ,1978年 生 ,博 士 研 究生 。
E—mail:yefanzhang@ 163.corn
通讯作者 :李楠 ,男 ,1938年 生 ,教授 。
E—mail linan@ wust.edu.cn
Байду номын сангаас收稿 日期 :2015—07—07
54 NAIHUO CAILIAO/耐火材料 201 6/1 http://www.nhc1.com.cn
摘 要 :为 了研 究煤 中的硫 含 量对铝 酸 盐水泥 的物相 组 成和 浇 注料 性 能 的影 响 ,选取 以不 同硫 含 量 的煤 为 燃料 煅烧的两种不同硫含量的 CA一50铝酸盐水泥为研 究对象,分析 了煤 中硫含量的增加对水泥熟料物相组成的影 响 ,并 用碳硫 仪 、XRD、SEM 和 EDS分析 了原料和 熟料 中硫 的含 量和存 在 形式 ,比较 了两种铝 酸 盐水 泥结合 浇 注 料的性能。结果表明:煤 中硫含 量的增加导致水泥 中硫铝酸钙含量的增加 ,进 而影响浇注料 中水泥的水化过 程 ,推迟 了水化产物产生大量沉淀的时间,降低 了最高放热温度 ,提 高了24 h养护后 的耐压强度。 关键 词 :铝 酸 盐水 泥 ;二氧 化硫 ;硫铝 酸钙 ;煤
配料中硫、碱成分对煅烧的影响及控制

①影响燧烧过程的正常运行。
碱与硫的单独影响是,当熟料中碱的总量或S03超过熟料重量的1%时,过量的碱(K、Na)会影响窑后烟室的结皮;过量的硫会引起窑内结圈。
当熟料中S03含量在1%左右时,会有利于改善生料易烧性,并提高熟料强度,但要以硫的含量增加不降低饱和比为前提。
考虑硫碱比对生产的影响就更复杂。
在预分解窑中,保持硫碱比值的恒定是动态的。
由于物料在窑内停留时间特别短,热负荷又小,碱(K、Na)很容易随熟料带走,而硫化物仍在窑内挥发循环,此时由于碱的缺乏,在窑的后部会形成结皮的恶性循环。
如果窑的燃烧温度高,或火焰直扫到物料上,这种循环更会加剧,直到结皮或预热器堵塞发生。
而一旦在窑的低温区域,这些硫化物还要释放出来,使生成的熟料中S03变高。
硫在窑内的循环与富集机理是:窑内的硫化物主要形式是S02,它在窑内的来源是燃料中硫的氧化及硫酸盐的分解,理论上S02低温下可氧化成S03,但实际上99%的气态硫化物将是S02,这样形成的S02几乎都被旋风预热器中的K20、Na20和CaO所结合,当大量CaS04在烧成区域再度挥发,并在窑尾和四、五级预热器形成硫循环结皮时,碱性硫酸盐的低挥发性将使它们存在于熟料中,这种循环严重时将引发预热器结瘤和堵塞出现。
②不合理的硫碱比值会影响熟料质量及易烧性。
熟料中因S03过量会阻止C3S的形成。
成为形成黄心料的另一种原因。
熟料的褐色核心一般都认为是窑内的还原气氛所致,但是由于形成高贝利特和硫酸盐浓缩减少了熟料的渗透性,阻止了冷却期间亚铁(Fe2+)氧化成三价铁(Fe?+),这就成为黄心料出现的另一条途径,这本身又是由窑喂料的化学成分变化和硫化物在窑内的低挥发性所造成的。
褐色熟料的不良结果就是热耗增加、降低易磨性、损失水泥强度和造成水泥快凝。
2、生料配料中的硫碱含量应控制在什么范围?生料配料中的硫碱控制范围建议如下。
①热生料中S03应小于3%,S03和Cl-的总和应小于4%,其中Ck含量对硫碱的比值影响很大,因为碱先是与氯化合为氯化碱/剩余的碱与硫结合成为硫碱化物。
硫对水泥熟料煅烧的影响(上)
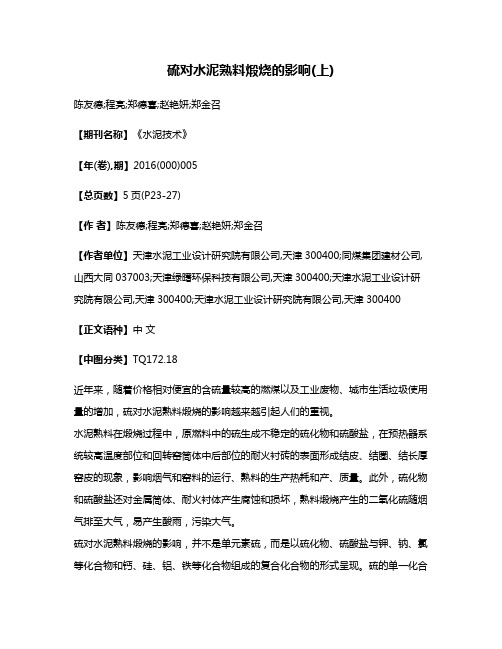
硫对水泥熟料煅烧的影响(上)陈友德;程亮;郑德喜;赵艳妍;郑金召【期刊名称】《水泥技术》【年(卷),期】2016(000)005【总页数】5页(P23-27)【作者】陈友德;程亮;郑德喜;赵艳妍;郑金召【作者单位】天津水泥工业设计研究院有限公司,天津300400;同煤集团建材公司,山西大同037003;天津绿曙环保科技有限公司,天津300400;天津水泥工业设计研究院有限公司,天津300400;天津水泥工业设计研究院有限公司,天津300400【正文语种】中文【中图分类】TQ172.18近年来,随着价格相对便宜的含硫量较高的燃煤以及工业废物、城市生活垃圾使用量的增加,硫对水泥熟料煅烧的影响越来越引起人们的重视。
水泥熟料在煅烧过程中,原燃料中的硫生成不稳定的硫化物和硫酸盐,在预热器系统较高温度部位和回转窑筒体中后部位的耐火衬砖的表面形成结皮、结圈、结长厚窑皮的现象,影响烟气和窑料的运行、熟料的生产热耗和产、质量。
此外,硫化物和硫酸盐还对金属筒体、耐火衬体产生腐蚀和损坏,熟料煅烧产生的二氧化硫随烟气排至大气,易产生酸雨,污染大气。
硫对水泥熟料煅烧的影响,并不是单元素硫,而是以硫化物、硫酸盐与钾、钠、氯等化合物和钙、硅、铝、铁等化合物组成的复合化合物的形式呈现。
硫的单一化合物的熔融温度大致从1 200℃开始至1 550℃结束。
此外,在高温还原工况下,硫酸盐大量吸热后与未完全燃烧的碳作用,生成二氧化硫,随烟气后逸与窑料中的氧化钾、氧化钠、氧化钙等氧化物作用,生成熔融的硫酸盐并随窑料运行,在此过程中形成熟料成分。
上述情况表明,硫的化合物在系统内相互作用,在不同温度的固、熔、气态之间转换,循环富集,对熟料煅烧产生影响。
烧成系统内与硫有关的化合物、复合化合物的循环富集介绍如下。
1.1 物料熔融温度水泥熟料煅烧过程中,主要矿物仅为4种,但其化合物约有数十种,一些易在窑内循环的低熔融化合物的熔融温度如下:(1)碱、氯、硫等化合物的熔融温度碱、氯、硫化合物的熔融温度因实验状况不同,温度稍有差异,这是由实验条件的差异所造成的。
煤对水泥熟料的影响 (2)
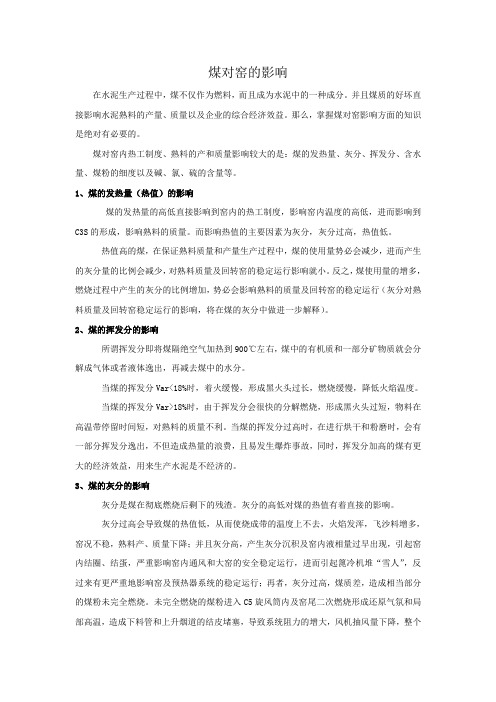
煤对窑的影响在水泥生产过程中,煤不仅作为燃料,而且成为水泥中的一种成分。
并且煤质的好坏直接影响水泥熟料的产量、质量以及企业的综合经济效益。
那么,掌握煤对窑影响方面的知识是绝对有必要的。
煤对窑内热工制度、熟料的产和质量影响较大的是:煤的发热量、灰分、挥发分、含水量、煤粉的细度以及碱、氯、硫的含量等。
1、煤的发热量(热值)的影响煤的发热量的高低直接影响到窑内的热工制度,影响窑内温度的高低,进而影响到C3S的形成,影响熟料的质量。
而影响热值的主要因素为灰分,灰分过高,热值低。
热值高的煤,在保证熟料质量和产量生产过程中,煤的使用量势必会减少,进而产生的灰分量的比例会减少,对熟料质量及回转窑的稳定运行影响就小。
反之,煤使用量的增多,燃烧过程中产生的灰分的比例增加,势必会影响熟料的质量及回转窑的稳定运行(灰分对熟料质量及回转窑稳定运行的影响,将在煤的灰分中做进一步解释)。
2、煤的挥发分的影响所谓挥发分即将煤隔绝空气加热到900℃左右,煤中的有机质和一部分矿物质就会分解成气体或者液体逸出,再减去煤中的水分。
当煤的挥发分Var<18%时,着火缓慢,形成黑火头过长,燃烧缓慢,降低火焰温度。
当煤的挥发分Var>18%时,由于挥发分会很快的分解燃烧,形成黑火头过短,物料在高温带停留时间短,对熟料的质量不利。
当煤的挥发分过高时,在进行烘干和粉磨时,会有一部分挥发分逸出,不但造成热量的浪费,且易发生爆炸事故,同时,挥发分加高的煤有更大的经济效益,用来生产水泥是不经济的。
3、煤的灰分的影响灰分是煤在彻底燃烧后剩下的残渣。
灰分的高低对煤的热值有着直接的影响。
灰分过高会导致煤的热值低,从而使烧成带的温度上不去,火焰发浑,飞沙料增多,窑况不稳,熟料产、质量下降;并且灰分高,产生灰分沉积及窑内液相量过早出现,引起窑内结圈、结蛋,严重影响窑内通风和大窑的安全稳定运行,进而引起篦冷机堆“雪人”,反过来有更严重地影响窑及预热器系统的稳定运行;再者,灰分过高,煤质差,造成相当部分的煤粉未完全燃烧。
燃煤的工业分析中各成分对燃烧的影响
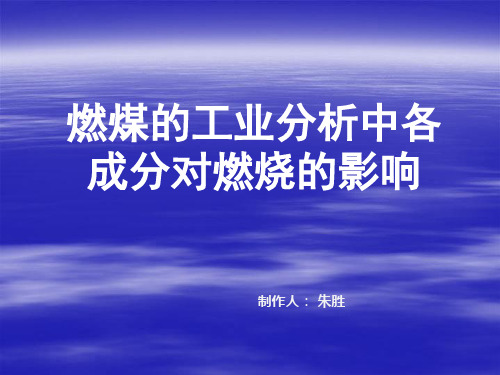
燃料中的硫化铁加剧磨煤部件的磨损
灰熔点(ST) 灰分在熔融状态下粘结在锅炉受热面上造成结渣,危及锅
炉运行的安全性和经济性。 对于固态排渣炉, ST< 1350℃ 可能结渣
煤的分类
我国煤的主要分类指标 干燥无灰基挥发分Vdaf含量 可分为三大类:褐煤( Vdaf含量>37% )、烟煤 ( Vdaf含量>10% )、无烟煤( Vdaf含量≤10% ) 为实现能源的综合利用,考虑各种工艺(炼焦、 燃烧、气化或液化等)对煤质的要求,每一类煤 还要进一步划分为小类
煤灰成分沾污指数
煤灰和飞灰烧结强度:直观的沾污判别指数
煤的常规特性对锅炉工作的影响
煤中V对锅炉工作的影响
挥发分 V V的含量代表了煤的地质年龄,地质年龄越短,煤的碳化程 度越浅,V含量越多 V含量越多(C含量越少),V中含O量亦多,其中的可燃 成分相应减少,这时,煤的热值低 V含量越多,煤的着火温度低,易着火燃烧
与燃尽困难; M、A 高,q2、q3、q4、q6 增加,热效率下降
M、A 高,过热器易超温
M、A 高,受热面腐蚀、堵灰、结渣及磨损加重 M、A 高,煤粉制备困难或增加能耗
煤的常规特性对锅炉工作的影响
煤中S、ST对锅炉工作的影响
硫分 S 可燃硫的热值低,含量少,对煤的着火、燃烧无明显影响 高、低温腐蚀;易造成受热面的堵灰 形成酸雨,污染环境
燃煤的工业分析中各 成分对燃烧的影响
制作人: 朱胜
煤的常规特性
煤灰的熔融特性
高温下煤灰的熔融性 用灰熔点表示,煤灰的角锥法确定
变形温度 DT(原t1)
软化温度 ST(原t2) 流动温度 FT(原t3) 温度间隔200-400℃,称为长渣 温度间隔100-200℃,称为短渣 判断锅炉运行中是否会结渣的主要因素之一。
脱硫粉煤灰对混凝土的影响及对策
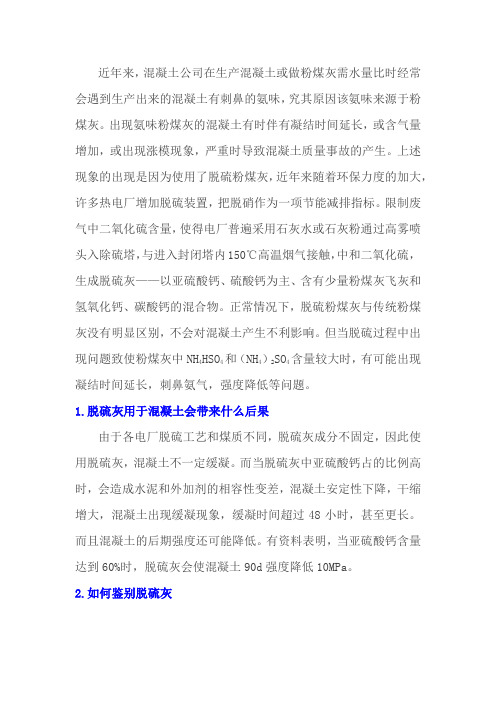
近年来,混凝土公司在生产混凝土或做粉煤灰需水量比时经常会遇到生产出来的混凝土有刺鼻的氨味,究其原因该氨味来源于粉煤灰。
出现氨味粉煤灰的混凝土有时伴有凝结时间延长,或含气量增加,或出现涨模现象,严重时导致混凝土质量事故的产生。
上述现象的出现是因为使用了脱硫粉煤灰,近年来随着环保力度的加大,许多热电厂增加脱硫装置,把脱硝作为一项节能减排指标。
限制废气中二氧化硫含量,使得电厂普遍采用石灰水或石灰粉通过高雾喷头入除硫塔,与进入封闭塔内150℃高温烟气接触,中和二氧化硫,生成脱硫灰——以亚硫酸钙、硫酸钙为主、含有少量粉煤灰飞灰和氢氧化钙、碳酸钙的混合物。
正常情况下,脱硫粉煤灰与传统粉煤灰没有明显区别,不会对混凝土产生不利影响。
但当脱硫过程中出现问题致使粉煤灰中NH4HSO4和(NH4)2SO4含量较大时,有可能出现凝结时间延长,刺鼻氨气,强度降低等问题。
1.脱硫灰用于混凝土会带来什么后果由于各电厂脱硫工艺和煤质不同,脱硫灰成分不固定,因此使用脱硫灰,混凝土不一定缓凝。
而当脱硫灰中亚硫酸钙占的比例高时,会造成水泥和外加剂的相容性变差,混凝土安定性下降,干缩增大,混凝土出现缓凝现象,缓凝时间超过48小时,甚至更长。
而且混凝土的后期强度还可能降低。
有资料表明,当亚硫酸钙含量达到60%时,脱硫灰会使混凝土90d强度降低10MPa。
2.如何鉴别脱硫灰此种方法适用于混凝土生产企业,操作方便快捷,可定性鉴别脱硫灰(脱硫石膏)中是否含有亚硫酸钙。
为安全起见,建议检测时放出刺激性气味的“粉煤灰”谨慎对待,进行相关试验后再使用。
4.脱硫灰造成混凝土结构缓凝的对策使用脱硫灰的混凝土如果缓凝超过48小时,后期强度可能会降低(粉煤灰中亚硫酸钙含量不同,对强度影响也不同),若是墙、柱结构,建议拆除返工,因为墙、柱不仅要承受本层荷载,还要承受上部各层的荷载。
28d后强度不合格加固费用更高。
若脱硫灰掺量很小,混凝土缓凝时间又不长,工程可待混凝土养护到600℃·d时,采用回弹等非破坏检测鉴定是否需要加固处理。
熟料煅烧过程原煤使用控制

熟料燃烧过程原煤使用控制高硫煤一、高硫煤对熟料燃烧的影响1、熟料质量下降由于煤中的含硫量高,在烧成过程中液相会提前出现,而且液相量大大增加,在这种情况下如果生料中Fe2O3.AI2O3含量不合理,C3S形成过快,部分C2S 尚未来得及吸收CaO形成C3S便被包裹在C3S晶体中,导致熟料中C3S含量偏低,同时较高的S03存在势必争夺部分CaO而形成CaS04,使熟料的实际饱和比降低若配料时再按常规计算,则保证生成C3S的CaO量就显得相对不足。
致使熟料中C3S含量进一步偏低,导致熟料强度的降低,同时当S03含量较高时,容易与熟料中的C3A,反应形成易于膨胀的单硫型水化硫铝酸钙(CaO∙AI2O3∙CaSO4∙31H2O)造成水泥熟料强度的降低。
由于高硫煤的燃点高,易燃性差,燃尽率低的特点,将会出现分解炉燃烧不完全的情况,分解炉缩口及出口结皮较多,减小了系统通风量,造成了尾煤不完全燃烧,窑内因通风量减小而产生还原气氛,使Fe2O3还原成FeO也会液相提前出现,物料容易在窑内结大球和产生黄心料,为确保尾煤的完全燃烧,除加强对系统结皮的清理外,还应适当加大窑内通风。
2、窑尾结皮在使用高硫煤以前,由于原材料中有害元素偏高,在熟料中硫碱比过高后,以S03为主的有害元素在窑尾大量富集生成CaS04和K3Na(S04)2等矿物,形成大量比较坚硬结皮。
3、窑前飞砂料和篦冷机"雪人〃由于硫碱比例增加,窑系统内S03相对过剩降低了液相黏度和液相表面张力,使熟料颗粒结构疏松,物料在窑内难以形成较大颗粒,产生大量细粉料。
另外由于窑尾结皮严重,窑内通风严重受阻,造成严重的短焰急烧,熟料表面液相黏度小,难以将物料黏结成粒也使得飞砂料大量增加。
同时飞砂料的形成后,在严重的短焰急烧造成窑前温度很高的情况下,易形成"雪人〃。
4、熟料产量下降为了确保熟料质量合格,减少黄心料,欠烧料,窑操只能用降低窑产量燃烧的方法。
探究硫对硅酸盐水泥熟料烧成过程的影响规律
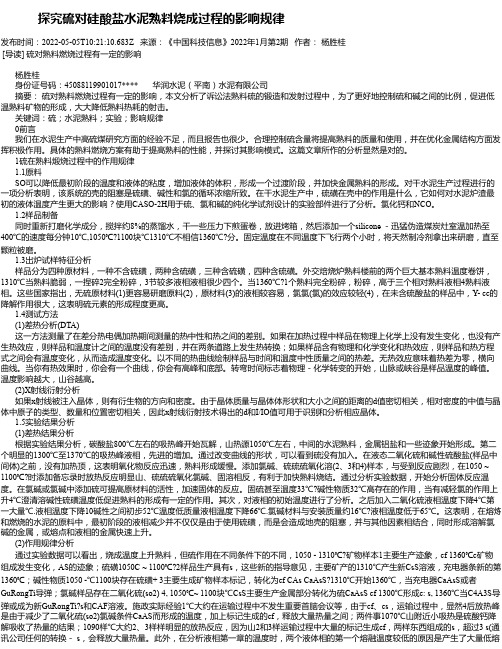
探究硫对硅酸盐水泥熟料烧成过程的影响规律发布时间:2022-05-05T10:21:10.683Z 来源:《中国科技信息》2022年1月第2期作者:杨胜桂[导读] 硫对熟料燃烧过程有一定的影响杨胜桂身份证号码:45088119901017**** 华润水泥(平南)水泥有限公司摘要:硫对熟料燃烧过程有一定的影响,本文分析了诉讼法熟料硫的锻造和发射过程中,为了更好地控制硫和碱之间的比例,促进低温熟料矿物的形成,大大降低熟料热耗的射击。
关键词:硫;水泥熟料;实验;影响规律0前言我们在水泥生产中高硫煤研究方面的经验不足,而且报告也很少。
合理控制硫含量将提高熟料的质量和使用,并在优化金属结构方面发挥积极作用。
具体的熟料燃烧方案有助于提高熟料的性能,并探讨其影响模式。
这篇文章所作的分析显然是对的。
1硫在熟料煅烧过程中的作用规律1.1原料SO可以降低最初阶段的温度和液体的粘度,增加液体的体积,形成一个过渡阶段,并加快金属熟料的形成。
对干水泥生产过程进行的一项分析表明,该系统的壳的阻塞是硫磺、碱性和氯的循环浓缩所致。
在干水泥生产中,硫磺在壳中的作用是什么,它如何对水泥炉渣最初的液体温度产生更大的影响?使用CASO-2H用于硫、氯和碱的纯化学试剂设计的实验部件进行了分析。
氯化钙和NCO。
1.2样品制备同时重新打磨化学成分,搅拌约8%的蒸馏水,干一些压力下煎蛋卷,放进烤箱,然后添加一个silicone -迅猛伪造煤炭灶室温加热至400℃的速度每分钟10℃,1050℃?1100块℃1310℃不相信1360℃?分。
固定温度在不同温度下飞行两个小时,将天然制冷剂拿出来研磨,直至颗粒被磨。
1.3出炉试样特征分析样品分为四种原材料,一种不含硫磺,两种含硫磺,三种含硫磺,四种含硫磺。
外交焙烧炉熟料楼前的两个巨大基本熟料温度卷饼,1310℃当熟料脆弱,一捏碎2完全粉碎,3节较多液相液相很少四个。
当1360℃?1个熟料完全粉碎,粉碎,高于三个相对熟料液相4熟料液相。
硫对水泥熟料煅烧的影响(下)
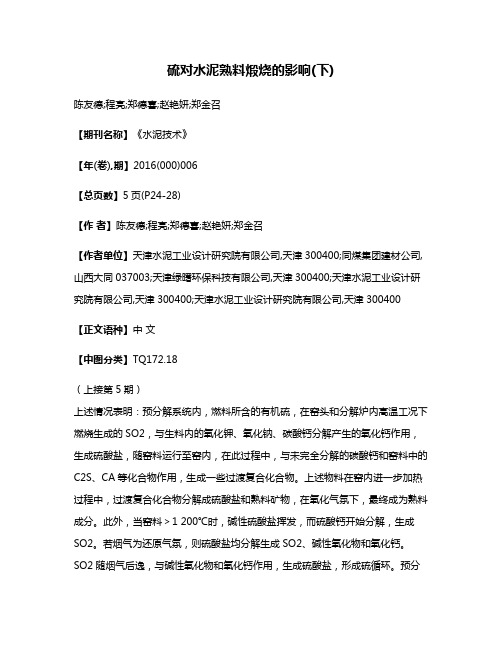
硫对水泥熟料煅烧的影响(下)陈友德;程亮;郑德喜;赵艳妍;郑金召【期刊名称】《水泥技术》【年(卷),期】2016(000)006【总页数】5页(P24-28)【作者】陈友德;程亮;郑德喜;赵艳妍;郑金召【作者单位】天津水泥工业设计研究院有限公司,天津300400;同煤集团建材公司,山西大同037003;天津绿曙环保科技有限公司,天津300400;天津水泥工业设计研究院有限公司,天津300400;天津水泥工业设计研究院有限公司,天津300400【正文语种】中文【中图分类】TQ172.18(上接第5期)上述情况表明:预分解系统内,燃料所含的有机硫,在窑头和分解炉内高温工况下燃烧生成的SO2,与生料内的氧化钾、氧化钠、碳酸钙分解产生的氧化钙作用,生成硫酸盐,随窑料运行至窑内,在此过程中,与未完全分解的碳酸钙和窑料中的C2S、CA等化合物作用,生成一些过渡复合化合物。
上述物料在窑内进一步加热过程中,过渡复合化合物分解成硫酸盐和熟料矿物,在氧化气氛下,最终成为熟料成分。
此外,当窑料>1 200℃时,碱性硫酸盐挥发,而硫酸钙开始分解,生成SO2。
若烟气为还原气氛,则硫酸盐均分解生成SO2、碱性氧化物和氧化钙。
SO2随烟气后逸,与碱性氧化物和氧化钙作用,生成硫酸盐,形成硫循环。
预分解窑系统内,原燃料燃烧产生的硫循环见图7。
(2)燃料中的硫进入熟料的量煤粉在预分解系统内燃烧后,所含的硫全部进入熟料中,单位熟料中SO3含量(g/kg)计算公式如下:式中:A——烧成热耗,kJ/kgB——煤粉热值,kJ/kgS——燃料中的硫含量,%3.1 减少入窑原燃料中的硫、氯、碱的含量硫对熟料煅烧和装备损坏的影响均与碱、氯形成的化合物和复合化合物有关,减缓的措施是尽可能减少进入系统的生料和燃料中的硫、氯、碱的含量。
国外某耐火材料公司,为减少结皮对生产和耐火材料的影响,通过长期的现场结皮料分析,提出熟料内Cl、SO2、R2O值与结皮趋势(见表7),表明碱、硫、氯含量越多,越易结皮堵塞。
关于硫对硅酸盐水泥熟料烧成过程的影响规律研究

关于硫对硅酸盐水泥熟料烧成过程的影响规律研究摘要:水泥工业随着优质资源的不断减少,现阶段已经逐渐的朝着利用低质燃料的方向进行发展,但是因为如今水泥的生产工艺水平比较低,所以实际可以适应水泥生产的煤种范围还是比较狭窄,在我国多数新型干法水泥厂中,一般都使用低硫含量烟煤。
如果在水泥生产中可以应用高硫煤,这样和其他行业之间的竞争就可以得到缓解,本文论述现在水泥生产中高硫煤的研究现状,并探在硅酸盐水泥熟料烧制中硫的影响。
关键词:硅酸盐;高硫煤;熟料烧制引言:在人类社会的发展过程中,资源和人口以及环境是一直都是需要面对的难题,现今广大的科技人员和各国政府,都十分关注实际社会的可持续发展问题,同时,材料生产和环境的协调性之间的研究,直接影响着社会的可持续发展。
一、在水泥生产中高硫煤应用研究的现状最早使用煤粉当做燃料的设备就是水泥窑,这个时候也是研究煤的起步阶段,最近这些年来,为了更好的去利用廉价的燃料,并将水泥的成本降低,使环境得到保护,我们国家的水泥研究者和生产者已经相继开展了很多研究工作。
在我们国家,很早就已经有了水泥立窑生产中利用高硫煤的相关报道,但是在实际立窑的时候,利用高硫煤作为主要燃料,十分容易出现结大块或挂边结窑的情况,而且在很多熟料这中的很高,强度不断下降,最终水泥十分容易出现快凝等问题。
所以很多立窑厂烧制水泥的时候,并不敢自己单独去利用高硫煤,一般为了降低成本都会就地取材,或者使用一些比较劣质的高硫煤,但是针对这样的方法来说,预期效果只能在预均化条件比较好的情况下达到,如果预均化条件并不是十分好的时候,使用优劣搭配这样的方法会导致配热出现不稳定的情况,尤其配料的难度比较大,实际进行立窑煅烧的时候操作起来也十分困难,最终导致熟料质量存在较大波动的情况。
在水泥熟料实际烧制的时候,高硫煤有着很好的降温和加速阿利特形成的作用,同时在控制不当的时候,也会出现结皮堵塞等情况。
最近这些年来,水泥的生产方法在不断的进行着演变。
水泥烧失量高的原因和影响

烧失量又称灼减量,即将样品在950±25℃的高温炉中灼烧所排出的结晶水,碳酸盐分解出的C02,硫酸盐分解出的S02,以及有机杂质被排除后物量的损失与低价硫、铁等元素氧化成高价的代数和。
烧失量的变化会引起熟料和水泥一些控制指标的变化,同时也会引起荧光分析结果与化学分析结果对比发生偏差。
1烧失量变化对熟料的影响熟料烧失量是衡量熟料质量好坏的一个重要指标,烧失量高说明窑内物料化学反应不完全,还有一部分碳酸钙或煤粒没有分解或燃尽,更有一部分碳酸钙虽已分解,但来不及继续完成熟料。
由此可以分析熟料烧失量过高的原因有:①分解率过低;②煤质转差,有害成份过高;③煤粉质量控制指标合格率不高;④喷煤管位置过低;⑤喷煤管性能下降。
煨烧过程中应根据烧成温度、窑尾温度、系统负压、废气分析等参数结合判断窑内状况变化,及时调整生料和煤投料量。
当然稳定的生料成份是煨烧高质量熟料的前提,首先要保证出磨生料的合格率在目标控制范围。
如果煤粒没有燃烧完全,造成熟料烧失量偏高,不仅增加了煤耗,而且会影响粉磨后的水泥质量。
高烧失量熟料将直接影响到熟料的性能,主要影响值有熟料标准稠度、强度、凝结时间。
大多数熟料烧失量会随f-Cao升高而增加,所以将烧失量作为一项控制指标,虽然此值在生产过程中,相对比较稳定,但仍需进行检测,可以第一时间指导生产,促进熟料质量的稳定和改善。
2烧失量变化对水泥的影响控制水泥中的烧失量,实际上就是限制石膏和混合材的渗入量,以保证水泥质量。
要控制水泥烧失量首先要控制熟料的烧失量,保证熟料质量,毕竟熟料占比例最大。
虽然混合材配料量比例不大,但烧失量比较高,烧失量变化比较大,因此,石膏和混合材的渗入量是影响水泥烧失量变化的主要原因。
石灰石、石膏的水份和烧失量的变化,以及混合材配料秤传感器上落入物料、皮带重量变化、跑边等因素,导致某些混合材多配或少配,从而引起烧失量发生变化。
3粉煤灰烧失量变化对水泥的影响粉煤灰是热力发电厂将燃烧后的残渣,具有品质稳定,成本低,活性好,烧失量低,可以降低水泥的水化热,推迟水化热的峰值等优点被水泥厂广泛利用。
硫对硅酸盐水泥熟料烧成过程的影响规律研究
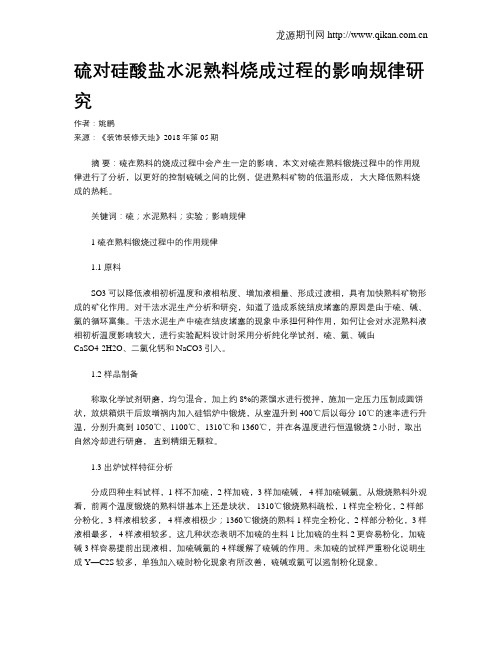
硫对硅酸盐水泥熟料烧成过程的影响规律研究作者:姚鹏来源:《装饰装修天地》2018年第05期摘要:硫在熟料的烧成过程中会产生一定的影响,本文对硫在熟料锻烧过程中的作用规律进行了分析,以更好的控制硫碱之间的比例,促进熟料矿物的低温形成,大大降低熟料烧成的热耗。
关键词:硫;水泥熟料;实验;影响规律1 硫在熟料锻烧过程中的作用规律1.1 原料SO3可以降低液相初析温度和液相粘度、增加液相量、形成过渡相,具有加快熟料矿物形成的矿化作用。
对干法水泥生产分析和研究,知道了造成系统结皮堵塞的原因是由于硫、碱、氯的循环富集。
干法水泥生产中硫在结皮堵塞的现象中承担何种作用,如何让会对水泥熟料液相初析温度影响较大,进行实验配料设计时采用分析纯化学试剂,硫、氯、碱由CaSO4·2H2O、二氯化钙和NaCO3引入。
1.2 样品制备称取化学试剂研磨,均匀混合,加上约8%的蒸馏水进行搅拌,施加一定压力压制成圆饼状,放烘箱烘干后放增祸内加入硅铝炉中锻烧,从室温升到400℃后以每分10℃的速率进行升温,分别升高到1050℃、1100℃、1310℃和1360℃,并在各温度进行恒温锻烧2小时,取出自然冷却进行研磨,直到精细无颗粒。
1.3 出炉试样特征分析分成四种生料试样,1样不加硫,2样加硫,3样加硫碱, 4样加硫碱氯。
从煅烧熟料外观看,前两个温度锻烧的熟料饼基本上还是块状, 1310℃锻烧熟料疏松,1样完全粉化,2样部分粉化,3样液相较多, 4样液相极少;1360℃锻烧的熟料1样完全粉化,2样部分粉化,3样液相最多, 4样液相较多。
这几种状态表明不加硫的生料1比加硫的生料2更容易粉化,加硫碱3样容易提前出现液相,加硫碱氯的4样缓解了硫碱的作用。
未加硫的试样严重粉化说明生成Y—C2S较多,单独加入硫时粉化现象有所改善,硫碱或氯可以遏制粉化现象。
1.4 测试方法(1)差热分析(DTA)。
该方法是通过差热电偶对热中性体与被测试样在加热过程中的温差进行测定。
硫碱成分对水泥生产及质量有何影响

1、碱成分对水泥质量有什么危害?众所周知,碱不论以何种形式存在,都会对水泥生产与质量带来如下不利。
①使水泥快凝、早强,碱含量偏高时,可提高早期强度,但降低28天强度,易出现急凝、安定性不合格等现象。
②K2O、Na2O含量高的水泥易与碱活性骨料发生碱-骨料反应而造成混凝土破坏性膨胀,即俗称的“混凝土癌症”。
③过量的碱(K、Na)在生产中易造成窑内结圈、预热器及窑尾结皮堵塞,特别是影响窑后烟室的结皮。
2、硫成分在生料及煤中超量会对生产及质量有何不利?虽然以生料的灼烧基,或以熟料为基准,SO3仅占0.1%~2%,碱总量小于1%,但它们对窑的正常运转以及对水泥、混凝土质量的影响是不可忽视的。
①影响煅烧工艺的正常运行:过量的硫易引起窑内结圈。
为满足低碱规定,特别是生产低碱水泥,煅烧时会因SO3过量而阻止熟料中C3S的形成。
②不合理的硫碱比会影响熟料质量及易烧性。
③熟料中的SO3越高,在水泥磨中的易磨性越差,并限制了石膏的加入量,继而又影响水泥凝结时间。
④影响水泥及混凝土强度:SO3较高时,有利于增加28天强度;最佳的SO3量可使一天的砂浆强度最大化,对后期强度或在升高温度下的最大强度也有利。
对于细度越粗、C3A和碱含量越高的水泥,需要更多的SO3,有利于强度;含有减水剂的混凝土也需要更高的SO3。
⑤形成的硫化物会对设备装置腐蚀,特别是导致对烟气管道严重腐蚀。
3、硫的循环及硫碱比对生产的影响机理是什么?①来自燃料中硫的氧化及硫酸盐分解而成的硫化物主要形式是SO2,它们在窑内遇高温挥发,在预热器中降温后又凝集的过程就是硫在窑内的循环。
理论上,SO2低温下可氧化成SO3,但实际上99%的气态硫化物将是SO2,它们几乎都与预热器中的K2O、Na2O和CaO结合,并在烧成区再度挥发,又到窑尾和四、五级预热器形成硫循环结皮,不易挥发的碱性硫酸盐才存在于熟料中,这种循环最终将引发预热器结皮或堵塞出现。
②碱在熟料中的赋存状态取决于硫碱的摩尔比:SG=SO3/(1.292Na2O+0.85K2O)当SG<1时,除形成K2SO4和Na2SO4外,K2O还和C2S形成不规则圆形KC23S12颗粒及残留较多的f-CaO;Na2O和C3A形成暗色长条状NC8A3。
水泥生料含硫对硅酸盐水泥熟料质量的影响
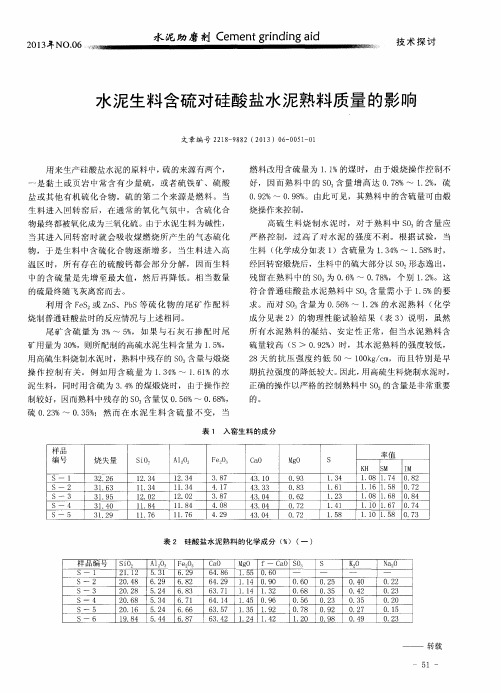
N a 2 0
0 . 2 2 O . 2 3 0 . 2 O O . 1 5 0 . 2 3
S一 2 S一 3 S一 4 S一 5 S一 6
2 O . 4 8 2 O . 2 8 2 O . 6 8 2 O . 1 6 1 9 . 8 4
物 ,于是 生料 巾含硫 化合 物逐渐 增 多,当生料 进入 高 温 区时 ,所有 存在 的硫酸 钙都会 部分 分解 ,因而 生料 中的含硫 量 是先 增至最 大值 ,然 后再 降低 。相 当数 量 的硫最 终随飞灰离窑而去。
严 格控 制,过 高 了对 水泥 的 强度 不利 。根据 试验 ,当
是黏 土或 页岩 中常含 有少 量硫 ,或 者硫 铁矿 、硫 酸
盐 或其 他有机 硫 化合物 。硫 的第 二个 来源 是燃料 。 当
生料进 入 回转窑 后,在通 常 的氧 化气 氛 中,含硫 化合 物最 终都被 氧化成为三氧化硫 。由于水泥生料为碱性 ,
当其 进入 回转 窑 时就会 吸收煤燃 烧所产 生 的气态 硫化
3 . 87
C a O
4 3 . 1 O 4 3 . 3 3
4 3. 0 4
M g O
O . 9 3 0 . 8 3
0. 6 2
S
K H S M I M
1 . 3 4 1 . 6 1
1 . 23
1 . 0 8 1 . 7 4 0 . 8 2 1 . 1 6 1 . 5 8 O . 7 2
1 . 4 1
1 .5 8
1 . 1 O 1 . 6 7 0 . 7 4
1.1 O 1 .5 8 O.7 3
表 2 硅 酸 盐 水 泥 熟 料 的化 学 成 分 ( % )( 一) 样 品 编 号 S i O 2
浅谈混合煤中硫对熟料煅烧的影响及解决措施
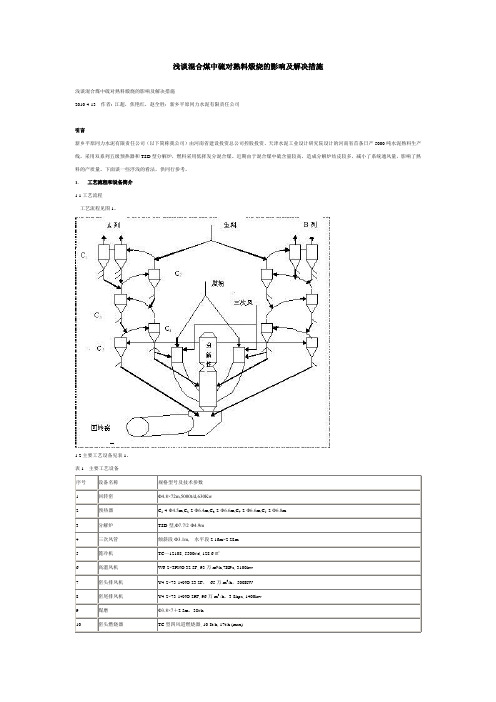
浅谈混合煤中硫对熟料煅烧的影响及解决措施浅谈混合煤中硫对熟料煅烧的影响及解决措施2010-4-13作者: 江超,焦艳红,赵全胜:新乡平原同力水泥有限责任公司引言新乡平原同力水泥有限责任公司(以下简称我公司)由河南省建设投资总公司控股投资、天津水泥工业设计研究院设计的河南省首条日产5000吨水泥熟料生产线,采用双系列五级预热器和TSD型分解炉,燃料采用低挥发分混合煤。
近期由于混合煤中硫含量较高,造成分解炉结皮较多,减小了系统通风量,影响了熟料的产质量。
下面谈一些浮浅的看法,供同行参考。
1. 工艺流程和设备简介1.1工艺流程工艺流程见图1。
1.2主要工艺设备见表1。
表1 主要工艺设备2.混合煤中硫含量高对煅烧的影响2.1我公司煤质的特点⑴原煤的供应商较多(少时有3家、最多时有7~8家)。
⑵结合我公司的特殊地理环境及生产要求,为了降低成本,允许各个供应商在满足我公司原煤各项质量指标要求的前提条件下对原煤进行搭配调整。
⑶煤质因来源不同而差异较大。
我公司所用混合煤从工业分析结果看差别不大,但实际煤质存在较大的差异。
因为在经济利益的驱动下,有的供应商会掺加一些价格低廉的高硫煤。
虽然进厂混合煤全硫含量都在1.5﹪左右,但可能由含硫量差别不大的3种煤组成,也可能由含硫为0.3﹪~0.5﹪与3.5﹪~4.0﹪的煤与其他煤按比例混合而成(在煤的工业分析中分析不出来各种原煤的实际比例)。
这会导致混合煤中一部分煤的硫含量偏高。
这部分高硫煤对煅烧的影响一般不被重视。
人们在评价煤质时往往只看其热值高低,挥发分、灰分含量多少,而忽视其均匀程度。
我公司质检部对各个供应商的进厂原煤现场取样、化验,再根据化验结果确定比例进行搭配、均化。
但前段时间堆取料机出现故障,只能人工移动布料机并用铲车取煤,一定程度上影响了均化效果。
2.2高硫煤对煅烧的影响2.2.1分解炉结皮严重、硫碱比失调2007年底分解炉出口负压升高(最大时达到-1.7KPa)、三次风压高达-1.1 KPa 。
挥发性组分碱、氯、硫对熟料烧成的影响

挥发性组分碱,氯,硫对熟料煅烧的影响碱,氯,硫主要来源于原料和燃煤之中,它们在熟料的煅烧过程中表现为有利和不利的两个方面:一方面是微量的碱氯硫的存在可以降低最低共熔点温度,增加液相量,降低液相粘度,起助熔作用,促进C3S的形成。
另一方面是含量太高产生不利的影响,危害熟料质量。
1.挥发性组分的挥发凝聚循环(1).挥发凝聚循环。
碱氯硫化合物在熟料煅烧过程中,先后分解,气化和挥发,并随窑内气流由低温区窑尾系统逸散。
在温度降低到一定程度时挥发性组分中的一部分凝聚,聚集。
粘附于生料颗粒表面并随生料重又返回高温区,然后再度挥发凝聚,如此循环过程称作挥发凝聚循环。
在挥发凝聚循环中,随生料和燃料带入的碱氯硫所造成的凝聚循环称内循环。
随窑内气流及所含粉尘离开窑系统的挥发性组分,在利用窑尾废气余热烘干生料和煤粉的系统中,部分又凝聚于生料或煤粉中,收尘装置收集的粉尘也含有一部分挥发性组分,这些挥发性组分或混入生料中,或单独喂入窑内,这些就构成了挥发性组分的外循环。
(2).挥发凝聚循环的危害及防范措施。
危害主要是窑尾烟室,缩口,下料溜子及五级筒内壁结皮,堵塞,熟料结大块和窑内结圈。
防范措施主要是限制原燃材料中的碱氯硫含量.生料中K2O+Na2O小于1.0%,CL控制在0.015~0.020%.生料中SO3控制在0.4%~0.7%。
2.较高碱含量对熟料煅烧和质量的影响 (1)破坏熟料矿物C3S,C2S. C3A 的形成 (2)影响液相粘度。
(3)水泥结块,快凝。
(4)水泥制品性能变坏 。
碱(K2O,Na2O)使熟料液相粘度提高,因此常使煅烧温度提高,但碱的存在又使C3S和C3A等矿物水化加速,造成水泥凝结快,早强较高而28d强度却有所降低。
如果采用含硫煤或在高碱熟料煅烧过程中加入一定SO3,使之达到适宜的硫酸盐化程度,则可减轻碱的不良作用,但即使如此,熟料强度仍然是下降的。
硫对水泥熟料煅烧的影响(下)
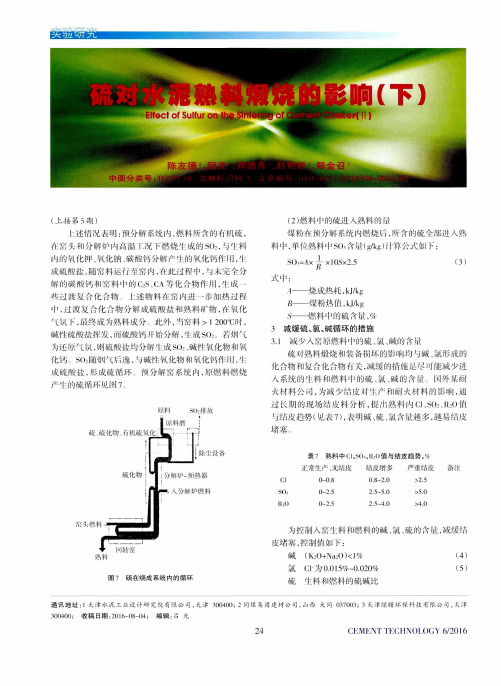
采取 决措 施 ( 8 )
堵怅 J . 必须 合 怵 t 分折结皮
} I } 仃 欠, 多的 ’ j 硫、 瞅 『 氽、
I I T J ' ( 常l L { J 现 系统 心 水 进 行 分忻 ' Z : 】 l
_ j 寸 存时 的
埘 次 8
仃火
的 热物 料
| _ 0 I 蛇 ( K ! ( ) + a 0) <1 %
z
. 减 缓
( 4)
熟 图 7 硫在 烧 成 系 统 内 的循 环
熟 - ( . : 1 为0 . ( ) l 5 %~ 0 . 0 2 ( ) % 料f ¨ 燃 料 的硫 碱 比
( 5 Байду номын сангаас
硫
通讯 地址 : l天津 水 泥 工 业 设 计 研 究 院 有 限公 司 ( ) 4 ( ) ( ) ; 收 稿 日期 : 2 0 1 6 - 0 8 — 0 4; 编辑 : 吕 光
【 ) I X音 ×l O S x 2 . 5
,J
( 3)
』 f i l :
1 — — 烧 成热 耗 , k J / k g
— —
【 l l , 过渡 介 化合物 分晰成硫酸盐和熟料矿物 , 存 化
— —
煤粉热 f I f f = , k J / k g
燃 料・ I 的 硫 , %
Z
4
勿
f
I
l
L
( 上接 第 5 期)
( 2 ) 燃料 t f I 佝硫进 入 I 粒 I . 的 艟 粉( i i @ i 分解 系统 I J 、 】 燃烧 后 . 昕 的 硫 全 进 入热 料r 『 l f ’ 熟 料r 1 - ) 含 g / k g ) 汁钟 : 公 『 』 【 1 下:
脱硫灰对水泥熟料煅烧的影响及对策
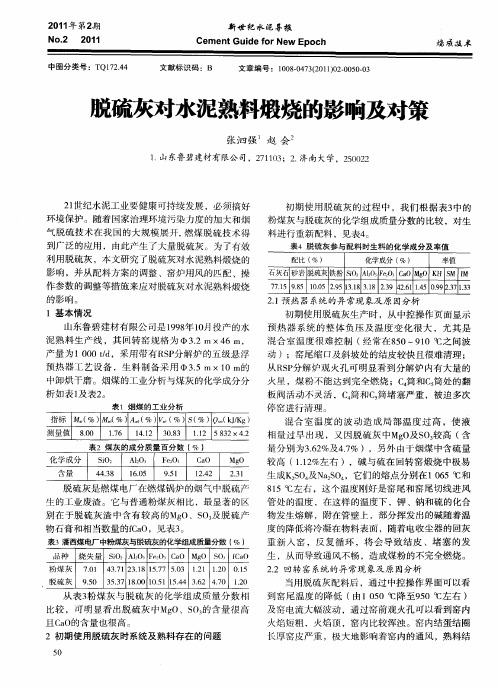
表 2 煤 灰 的成 分 质 量 百 分 数 ( ) % 化 学 成 分
含 量
S0 i:
4- 43 8
A23 l O
1.5 6 0
F 23 e 0
9 1 . 5
C0 a
1.2 24
Mg O
23 .1
2 1 年 第2 01 期
No. 2 1 2 0 1
新 世 纪水 泥导报
C me t i ef r w p c e n d Gu o Ne E o h
文 献 标识 码 :B 文章 编 号 : 10 —4 32 1)20 5 —3 0 807 (0 0 —0 00 1
初期 使用脱 硫 灰生 产时 ,从 中控操 作 页面显 示
预 热 器 系 统 的 整 体 负 压及 温度 变化 很 大 ,尤 其 是
混 合 室温 度很 难 控 制 ( 常 在 80~9 0 q之 间波 经 5 1 c
动 );窑尾 缩 口及斜 坡处 的结皮 较快 且很难 清理 ;
从RP S 分解 炉观 火孔 可 明显 看到 分解 炉 内有 大量 的
当用脱 硫灰 配料 后 ,通 过 中控操 作 界面可 以看
到 窑尾 温度 的 降低 ( 10 0℃降至 9 0℃左 右 ) 由 5 5
从 表 3 煤 灰 与脱 硫 灰 的化 学 组 成 质量 分 数相 粉 比较 ,可 明显 看 出脱 硫 灰 中Mg O、S O 的含 量很 高 且CO a 的含 量也很 高 。 2初期 使用脱 硫灰 时 系统及 熟料 存在 的问题
较 高 ( .2 11%左 右 ),碱 与硫在 回转窑 煅烧 中极易
生成 KS aS 0 及N 0 ,它们 的熔点 分别 在 10 5℃和 6