(2)板料冲压方法及主要工序小结
板料冲压工艺

板料冲压工艺板料冲压是指用冲模使板料经分离或成形得到制件的工艺方法,它通常是在室温下进行,所以又称为冷冲压,简称冲压。
1、板料冲压的特点及应用冲压用原材料必须具有足够的塑性,广泛应用的金属材料有低碳钢、高塑性合金钢、铝、铜及其合金等;非金属材料有石棉板、硬橡皮、绝缘纸、纤维板等。
他广泛应用于汽车、拖拉机、航空、电器、仪表、国防等工业部门。
板料冲压具有以下特点:(1)冲压件的尺寸精度高,表面质量好,互换性好,一般不需切削加工即可直接使用,且质量稳定。
(2)可压制形状复杂的零件,且材料的利用率高、产品的重量轻、强度和刚度较高。
(3)冲压生产生产率高,操作简单,其工艺过程易于实现机械化和自动化,成本低。
(4)冲压用模具结构复杂,精度要求高,制造费用高。
冲压只有在大批量生产时,才能显示其优越性。
(5)冲压件的质量为一克至几十千克,尺寸为一毫米至几米。
2、冲压设备(1)剪床剪床的用途是把板料切成一定宽度的条料,以供下一步冲压工序之用。
(2)冲床冲床将完成除剪切以外的其他冲压工作。
右图为单柱式冲床的外形及其传动简图。
电动机5带动飞轮4转动,当踩下踏板6时,离合器3使飞轮与曲轴2连接,因而曲轴随飞轮一起转动,通过连杆8带动滑块7作上下运动,从而进行冲压工作。
当松开踏板时,离合器脱开,曲轴不随飞轮转动,同时制动闸1使曲轴停止转动,并使滑块7停在上面位置3、冲压模具(1)简单冲模简单冲模在冲床一次行程中只完成一道工序,见右图。
凸模1用压板6固定在上模板3上,通过模柄5与冲床滑块连接。
凹模2用压板7固定在下模板4上。
操作时,条料沿两导料板9之间送进,碰到挡料销10停止。
冲下部分落入凹模孔。
此时,条料夹住凸模一起返回,被卸料板8推下。
重复上述动作,完成连续冲压。
导柱12和导套11组成的导向机构可保证凸模、凹模的合模准确性。
简单冲模结构简单,容易制造,价格低廉,维修方便,生产率低,适用于小批量生产。
(2)连续冲模连续冲模在冲床一次行程中,按着一定顺序,在模具的不同位置上,同时完成数道冲压工序,见右图。
板料冲压

(6) 修整 是利用修整模沿冲裁件外缘或内孔刮削一薄层 金属,去掉剪裂带和毛刺,提高冲裁件的尺寸精度 和表面精度。
2. 变形工序
—— 是使坯料的一部分相对于另一部分产生
位移而不破坏的工序。
如:拉深,弯曲,翻边,胀形等。
(1) 弯曲 ——是将坯料的一部分相对于另一部分弯曲成 一定角度的冲压加工方法。被弯材料可是板料、型 材或管料。
可采用加强筋措施 以薄材代替厚材。
3. 冲压件的精度和表面质量
在满足需要的前提下,尽量降低精度要求,而且 一般不要超过原材料的表面质量。
4.
简化工艺、节约材料
(1) 采用冲—焊结构
用于复杂冲压件,可分别冲 压成几个简单件,然后焊接 成整体,简化工艺
(2) 采用冲口工艺 ——可以减少组合件数量
(3)在不改变使用性能的前提下,简化拉深件结构, 可减少工序并节约材料。
落料和冲孔的区别在于: 落料:冲落部分为成品,周边是废料; 冲孔:是为了获得带孔的冲裁件,冲落部分为 废料。
(1) 冲裁分离过程
冲裁时板料的变形和分离过程对冲裁件质量有 很大的影响。其过程可分为三个阶段。
弹性变形阶段→塑性变形阶段→断裂分离阶段
冲裁出的工件断面分为四个特征区,分别为圆 角带(塌角)、光亮带、剪裂带和毛刺。
板厚越大,m取 值应越大。
设计落料模时,取凹模作为设计基准,然后根 据间隙确定凸模尺寸。设计冲孔模时,取凸模作为 设计基准,然后根据间隙确定凹模尺寸。
(3) 凸凹模刃口尺寸的确定
落料件尺寸会随凹模刃口磨损而增大,因此,加
工凹模刃口时取落料件公差范围的最小尺寸;
冲孔件尺寸会随凸模刃口磨损而减小,因此,加
压边圈——防止工件起皱 压边力不能太 大,一般为 2~3MPa。
板料冲压知识点总结

板料冲压知识点总结一、板料冲压的基本原理板料冲压是一种利用模具对金属板料进行加工成型的工艺方法,它通过对金属板料施加压力,使其产生塑性变形,从而得到所需的形状和尺寸。
在板料冲压的过程中,金属板料会经历拉伸、挤压、弯曲等变形,因此需要设计合适的模具来完成这些变形过程。
板料冲压的基本原理包括以下几个方面:1. 材料选择:板料冲压所使用的金属材料通常包括冷轧钢板、热轧钢板、不锈钢板、铝合金板等。
在选择材料时需要考虑其机械性能、成本、加工性能等因素。
2. 模具设计:模具是板料冲压的关键,它影响着成型件的形状精度、表面质量及加工效率。
模具设计需要考虑材料的选择、结构的设计、工艺的优化等因素。
3. 冲压工艺:冲压工艺包括冲程、冲次、冲压速度、冲压压力等参数的选择。
通过优化冲压工艺可以有效控制成型件的形状和尺寸精度。
4. 设备选型:板料冲压过程需要使用冲床、模具、送料装置等设备。
选择合适的设备可以提高加工效率,并保证成型件的质量。
二、板料冲压的工艺流程板料冲压的工艺流程通常包括以下几个步骤:1. 材料准备:选择合适的金属板料,并进行切割、清洗等准备工作。
2. 模具设计:根据成型件的要求设计模具,包括上模、下模、模具座等部件。
3. 冲压工艺设计:确定冲程、冲次、冲压速度等工艺参数,进行工艺计算及优化。
4. 模具加工:制作模具并进行调试,保证其精度和可靠性。
5. 材料送料:将切好的板料通过送料装置送入冲床内,准备开始冲压。
6. 冲压成型:通过冲床对金属板料进行塑性变形,得到所需的形状。
7. 成品处理:对冲压成型后的零件进行去毛刺、喷漆等处理,提高表面质量。
8. 质量检验:检验成型零件的形状和尺寸精度,确保其符合要求。
9. 成品包装:对合格的成品进行包装、标识等处理,准备发货或存储。
三、板料冲压常见问题及解决方法在板料冲压加工过程中,常常会出现一些问题,如变形不良、裂纹、气泡等。
以下是一些常见问题及解决方法:1. 变形不良:板料在冲压过程中出现变形不良的现象,可以采取调整冲床参数、优化模具结构等方法解决。
板材冲压(一)
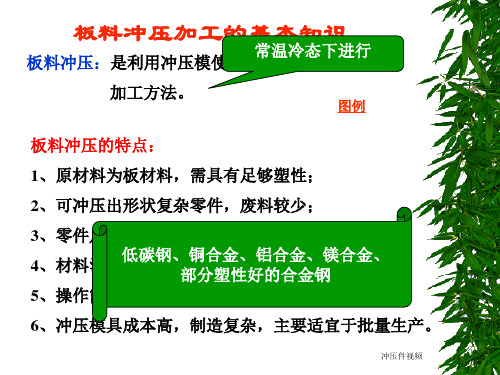
外力
由于凸模与凹模之间有一定的距离,使得板料在受 到凸模与凹模正压力作用的同时还受到弯矩的作用, 板料的变形不可能是纯剪切,还要产生有害的弯曲变
形。
板料的弯曲变形对模具刃口的侧面产生挤压作用,
反过来,凸模与凹模刃口的侧面对板料产生反挤作用,
形成对板料剪切面的侧压力
2、冲裁时变形区的应力状态
冲裁时板料最大的塑性变形集中在以凸模与凹模刃口连线为中 线的纺锤形区域内。
冲裁工艺及模具
冲压件视频
板料冲压加工的基本知识
图例
一、冲模及冲压设备
1、冲模 2、冲压设备 二、冲压基本工序 (一)、落料 落料是在平板的毛坯上沿封闭轮廓进行 冲裁,余下的就是废料。落料常用于制备工 序件。 (二)、冲孔 冲孔是以落料件或其他成型件为工序件, 完成各种形状孔的冲孔冲裁加工。
冲模 冲床设备
落料、冲孔视频
图a表示初始冲裁时的变形区由刃口向板料 中心逐渐扩大,截面呈纺锤形。材料的塑性 越好、硬化指数大,则纺锤形变形区的宽度 将越大。
图b表示变形区随着凸模切入板料深度的增
加面逐渐缩小,但仍保持纺锤形。其周围己 变形的材料比初始冲裁时己被严重加工硬化 了,因此冲裁断面存在加工硬化现象。
2、冲裁时变形区的应力状态
板料冲压

板料的冲压成形
一、何谓冲压成形
板料冲压成形是利用冲模使板料产生分离或变形的加工方法,板料冲压 的坯料厚度一般小于4mm,通常是在常温下进行的,所以又叫冷冲压。
二、工艺分类
分离工序: 落料、冲孔、切断 变形工序:拉深、弯曲
三、板料冲压的特点
1、操作简单,加工效率高; 2、一般不需再进行切削加工,因而节约材料,节约能源消耗; 3、加工质量高,基本不需要后序加工; 4、对工人技术要求低; 5、灵活性差。
YQ32系列四柱液压机
拉深加工产品示例
1)拉深变形过程
使坯料在凸模的作用下压入凹模, 获得空心体零件的冲压工序。
h d d
Dd h 2
拉深过程示意图
2)拉深废品 ① 拉裂(拉穿) ② 起皱
3)拉深模设计及工艺特点 ① 凸凹模的工作部分必须具有一定 的圆角; r凹=(5~10)t r凸=(0.7-1)t ② 凸凹模间隙要合理 Z =(1.1-1.2)t ③ 控制拉深系数(m)
形状零件的工序。
弯曲过程示意图
1)弯曲的变形特点 ① 变形区域主要在圆角部位; ② 外层金属受拉应力,内层金属受压应力。 2)弯曲缺陷 弯裂 回弹 a)设计补偿角 b)对工件进行退火 c)设计加强筋
3)弯曲工艺特点 ①弯曲半径 r≥rmin=(0.25-1)t ;
② 毛刺应位于内侧;
③ 弯曲线应尽量与坯料纤维方向垂直;
3)液态模锻
原理:将液态金属直接注入模膛,施以静压力,使熔融
或半熔融态金属在压力下结晶凝固,并产生少量塑性变形。
特点:
与铸造比:无须浇注系统,节约金属;组织比压铸件细密。 与锻造比:成形压力小及能耗少2/3~~3/4;组织比一般模锻件差。
板料的冲压工艺

(3)间隙合适 )
裂纹重合一线,冲裁力、卸料力、 间隙合适—上、下裂纹重合一线,冲裁力、卸料力、推件 力适中,模具寿命足够,零件尺寸几乎与模具一样。 力适中,模具寿命足够,零件尺寸几乎与模具一样。 较小的间隙有利于提高冲裁件的质量。 较小的间隙有利于提高冲裁件的质量。 有利于提高冲裁件的质量 较大的间隙则有利于提高模具的寿命。 较大的间隙则有利于提高模具的寿命。 则有利于提高模具的寿命 间隙合理模具有足够长的寿命, 间隙合理模具有足够长的寿命,零件的 模具有足够长的寿命 尺寸几乎与模具一致。 尺寸几乎与模具一致。 冲裁模合理间隙值见表8-1 冲裁模合理间隙值见表
10
光亮带:塑性变形过程中凸模 或凹模)挤压切入材料, 凸模( ② 光亮带:塑性变形过程中凸模(或凹模)挤压切入材料,使其 受到剪切和挤压应力的作用而形成。表面光滑,断面质量最好。 受到剪切和挤压应力的作用而形成。表面光滑,断面质量最好。 剪裂(断裂) 由于刃口处的微裂纹 拉应力作用下不断扩 刃口处的微裂纹在 ③ 剪裂(断裂)带:由于刃口处的微裂纹在拉应力作用下不断扩 展断裂而形成。表面粗糙,略带斜度。 展断裂而形成。表面粗糙,略带斜度。 毛刺:微裂纹出现时产生,冲头继续下行时被拉长。 ④ 毛刺:微裂纹出现时产生,冲头继续下行时被拉长。
第八章 板料的冲压工艺
板料冲压:是利用装在冲床上的冲模对金属板料 板料冲压:是利用装在冲床上的冲模对金属板料 冲床上的冲模 加压,使之产生变形 分离, 变形或 加压,使之产生变形或分离,从而获得零件或毛坯 的加工方法。 的加工方法。 板料冲压通常在室温下进行,故又称冷冲压 冷冲压。 板料冲压通常在室温下进行,故又称冷冲压。 当板料厚度超过8∼10 mm 时,需采用热冲压。 需采用热冲压 热冲压。 当板料厚度超过 ∼
板料冲压
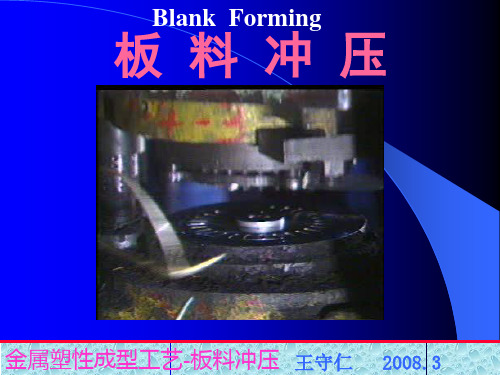
冲模在工作过程中必然有磨损,落料件尺寸会 随凹模刃口的磨损而增大,而冲孔件尺寸则随凸模 的磨损而减小。为了保证零件的尺寸要求,并提高 模具的使用寿命:
落料时凹模刃口的尺寸应靠近落料件公差范围 内的最小尺寸;冲孔时,选取凸模刃口的尺寸靠近 孔的公差范围内的最大尺寸。
金属塑性成型工艺-板料冲压 王守仁 2008.3
金属塑性成型工艺-板料冲压 王守仁 2008.3
金属塑性成型工艺-板料冲压 王守仁 2008.3
外缘修整模的凸凹模间隙,单边取0.001~0.01 mm。也可以采用负间隙修整,即凸模刃口尺寸大 于凹模刃口尺寸的修整工艺。
三、切断
切断是指用剪刃或冲模将板料沿不封闭轮廓进 行分离的工序。
剪刃安装在剪床上,把大板料剪切成一定宽度 的条料,供下一步冲压工序用。而冲模是安装在冲 床上,用以制取形状简单、精度要求不高的平板件。
特征与材料(板料材料)塑性的关系:
断面质量受冲裁条件的不同而不同,如: 刃口间隙,刃口形状,锋利程度,冲裁力、 润滑条件,板料质量(表面质量),板料种 类(性能)。
冲压生产要求冲裁件有较大的光亮带, 尺量减少断裂带区域的宽度。
材料塑性愈好,光亮带愈大,断裂带愈 小,同时,圆角毛刺亦增大。
金属塑性成型工艺-板料冲压 王守仁 2008.3
当单边间隙Z增大到材料厚度的15%-20%时, 卸料力为0。
金属塑性成型工艺-板料冲压 王守仁 2008.3
冲裁间隙对冲压的影响 D、间隙对模具寿命的影响
由于工件与凸、凹模侧壁之间有磨擦的存在, 间隙小,磨擦大,模具寿命短。冲裁过程中,凸模 与被冲孔之闻,凹模与落料件之阀均有摩擦,而且闻 隙越小,摩擦越严重。所以过小的间隙对模具寿命 极为不利,而较大的间隙可使凸模与凹模的侧面与 材料间的摩擦减小,井能减缓间隙不均匀的影响,从 而提高模具的寿命。
板料冲压

第三章板料冲压板料冲压:利用冲模在压力机上使板料分离或变形,从而获得冲压件的加工方法称为板料冲压。
板料冲压的坯料厚度一般小于4mm,通常在常温下冲压,故又称为冷冲压,简称冲压。
板料厚度超过8~10mm时,才用热冲压。
原材料:具有塑性的金属材料,如低碳钢、奥氏体不锈钢、铜或铝及其合金等,也可以是非金属材料,如胶木、云母、纤维板、皮革等。
板料冲压的特点:(1)冲压生产操作简单,生产率高,易于实现机械化和自动化。
(2)冲压件的尺寸精确,表面光洁,质量稳定,互换性好,一般不再进行机械加工,即可作为零件使用。
(3)金属薄板经过冲压塑性变形获得一定几何形状,并产生冷变形强化,使冲压件具有质量轻、强度高和刚性好的优点。
(4)冲模是冲压生产的主要工艺装备,其结构复杂,精度要求高,制造费用相对较高,故冲压适合在大批量生产条件下采用。
一、冲压设备主要有剪床和冲床两大类。
剪床是完成剪切工序,为冲压生产准备原料的主要设备。
冲床是进行冲压加工的主要设备,按其床身结构不同,有开式和闭式两类冲床。
按其传动方式不同,有机械式冲床与液压压力机两大类。
图8-26所示为开式机械式冲床的工作原理及传动示意图。
冲床的主要技术参数是以公称压力来表示的,公称压力(kN)是以冲床滑块在下止点前工作位置所能承受的最大工作压力来表示的。
我国常用开式冲床的规格为63~2000kN,闭式冲床的规格为1000~5000kN。
二、冲压工序冲压基本工序可分为落料、冲孔、切断等分离工序,和拉深、弯曲等变形工序两大类。
(一)分离工序它是使板料的一部分与另一部分分离的加工工序。
(1)切断:使板料按不封闭轮廓线分离的工序叫切断;(2)落料:是从板料上冲出一定外形的零件或坯料,冲下部分是成品。
(3)冲孔:是在板料上冲出孔,冲下部分是废料。
冲孔和落料又统称为冲裁。
1、冲裁变形过程冲裁可分为普通冲裁和精密冲裁。
普通冲裁的刃口必须锋利,凸模和凹模之间留有间隙,板料的冲裁过程可分为三个阶段,如图8-27所示:(1)弹性变形阶段(2)塑性变形阶段(3)剪裂分离阶段板料冲裁时的应力应变十分复杂,除剪切应力应变外,还有拉伸、弯曲和挤压等应力应变,如图8-28所示。
冲压的基本工序及应用特点

冲压的基本工序及应用特点冲压是一种通过应用外力将板材或其他材料加工成所需形状的工艺。
它包含了多个基本工序,其中最常见的有剪切、冲孔、拉伸和弯曲。
这些基本工序的应用特点如下:1. 剪切:剪切是将板材按照规定的线条切割成所需形状的工序。
它常采用带刃口的模具,通过对板材施加剪切力,将板材分离成两部分。
剪切工序的特点是切削速度快,成本低,适用于大批量生产。
2. 冲孔:冲孔是通过模具,在板材上制作出所需形状的孔洞。
冲孔工序通常使用冲孔机进行,通过运动的冲头对板材施加冲击,使板材上形成一个或多个孔洞。
冲孔工序的特点是生产效率高,成本低,能够进行高精度的冲孔。
3. 拉伸:拉伸是将板材拉伸至所需形状的工序。
它常用于制作薄壁杯状、碗状或盖板等形状复杂的零件。
拉伸工序通常使用模具,通过对板材施加拉伸力,使板材从某一局部区域开始逐渐变形,最终形成所需形状。
拉伸工序的特点是能够制作出形状复杂的零件,但对板材的材质和厚度有一定要求。
4. 弯曲:弯曲是将板材按照规定角度弯曲成所需形状的工序。
它通过施加相应的弯曲力使得板材围绕模具的弯曲线进行变形。
弯曲工序的特点是生产周期短,成本低,能够制作出不同半径和角度的弯曲零件。
冲压工艺具有以下应用特点:1. 生产效率高:冲压工艺适用于大批量生产,具有高效率、高精度、高一致性的特点。
冲压设备可以实现自动化生产,提高生产效率和降低劳动力成本。
2. 产品质量稳定:冲压工艺可以精确控制零件的尺寸和形状,具有较高的产品质量稳定性。
通过合理设计模具和工装,可以有效避免零件变形和表面缺陷等质量问题。
3. 材料利用率高:冲压工艺通过对原材料的切割、冲孔、拉伸和弯曲等加工,可以最大限度地降低材料的浪费,提高材料的利用率。
4. 灵活性强:冲压工艺可以适应不同的材料和工件形状,具有较高的生产灵活性。
通过更换模具和工装,可以在短时间内实现不同产品的生产。
5. 适用于多种材料:冲压工艺适用于金属材料和非金属材料,包括钢板、铝板、不锈钢板、铜板、塑料板等。
冲压工艺
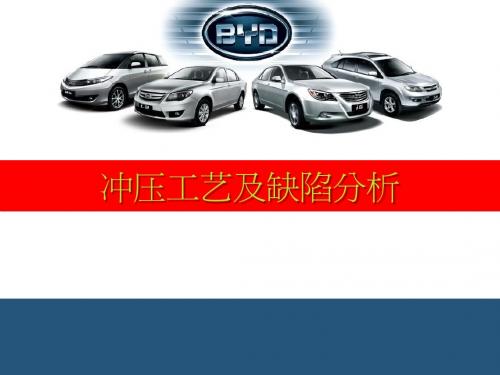
设备
冲压设备 • 机械压力机 • 液压机
冲压材料
• 板材 • 带材 • 管材及其他型材
冲压零件
冲压模具
材料
模具
• 冲压加工的主要工艺装备 • 冲压件质量与模具关系最大
冲压概述
3.冲压加工特点
• • • • • • • • 产品尺寸稳定,重量轻,刚度好 表面质量和精度较好 操作简单,易于实现自动化 生产效率高 适于大批量生产 大批量生产时加工费用较低 依赖设备与模具 投产周期较长,初始投入大
工序名 称
代号
切角 翻孔 扣合 落料 弯曲 分离 CT BU HEM BL BE SEP
二、冲压工序
1.分离工序
板料在外力作用下沿一定的轮廓线分离而获得一定形状、 尺寸和切断面质量的成品和半成品。
分离条件:变形材料内部的应力超过强度极限σb。
二、冲压工序
1.1落料
用冲模沿封闭曲线冲切,冲下部分是零件。用于制造各种 形状的平板零件。
六、缺陷及分析 (2)变形
压料板与凹模型面配合不好;间隙过大等 凹模或凸模缺损; 定位销造成(放偏或走料)
(3)表面划伤
操作时有拖、拉等现象; 板料在剪切过程中划伤等;
六、缺陷及分析 (4)尺寸不符
上料不到位; 定位装置损坏或松动,位置窜动等
(5)少孔
冲头折断; 冲头长度不够; 行程不到位。
冲压工艺及缺陷分析
目录
一 二 三 四 五 六 冲压概述 冲压工序 冲压模具 冲压设备
冲压材料
缺陷及分析
一、冲压概述
1.什么是冲压?
利用安装在压力机上的模具对材料施加压力,使其产生分 离或塑性变形,从而获得一定几何形状和尺寸精度的机械 零件或制品的一种压力加工方法。 冲压通常在常温下进行,主要用于金属板料成型加工,故 又称为冷冲压。
冲压加工的基本工序
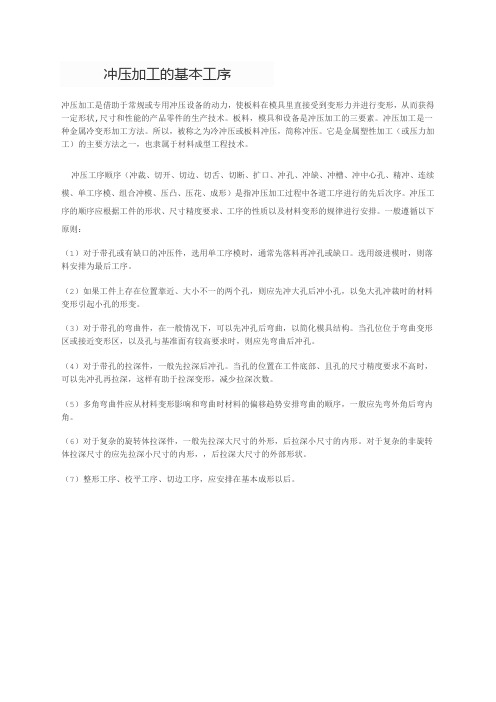
冲压加工的基本工序冲压加工是借助于常规或专用冲压设备的动力,使板料在模具里直接受到变形力并进行变形,从而获得一定形状,尺寸和性能的产品零件的生产技术。
板料,模具和设备是冲压加工的三要素。
冲压加工是一种金属冷变形加工方法。
所以,被称之为冷冲压或板料冲压,简称冲压。
它是金属塑性加工(或压力加工)的主要方法之一,也隶属于材料成型工程技术。
冲压工序顺序(冲裁、切开、切边、切舌、切断、扩口、冲孔、冲缺、冲槽、冲中心孔、精冲、连续模、单工序模、组合冲模、压凸、压花、成形)是指冲压加工过程中各道工序进行的先后次序。
冲压工序的顺序应根据工件的形状、尺寸精度要求、工序的性质以及材料变形的规律进行安排。
一般遵循以下原则:(1)对于带孔或有缺口的冲压件,选用单工序模时,通常先落料再冲孔或缺口。
选用级进模时,则落料安排为最后工序。
(2)如果工件上存在位置靠近、大小不一的两个孔,则应先冲大孔后冲小孔,以免大孔冲裁时的材料变形引起小孔的形变。
(3)对于带孔的弯曲件,在一般情况下,可以先冲孔后弯曲,以简化模具结构。
当孔位位于弯曲变形区或接近变形区,以及孔与基准面有较高要求时,则应先弯曲后冲孔。
(4)对于带孔的拉深件,一般先拉深后冲孔。
当孔的位置在工件底部、且孔的尺寸精度要求不高时,可以先冲孔再拉深,这样有助于拉深变形,减少拉深次数。
(5)多角弯曲件应从材料变形影响和弯曲时材料的偏移趋势安排弯曲的顺序,一般应先弯外角后弯内角。
(6)对于复杂的旋转体拉深件,一般先拉深大尺寸的外形,后拉深小尺寸的内形。
对于复杂的非旋转体拉深尺寸的应先拉深小尺寸的内形,,后拉深大尺寸的外部形状。
(7)整形工序、校平工序、切边工序,应安排在基本成形以后。
工序简图特点:1.落料:将板料沿封闭轮廓分离,切下部分是产品,我们一般称之为“平面下料”,这种模具一般很简单,新人只要学会拆模装模,就能够搞定这套模具2.冲孔:将板材沿封闭轮廓线分离,切下部分是废料3.切断:将板材沿不封闭的轮廓分离4.切边:将产品边缘多余的材料冲切下来5.剖切:将已冲压成型的半成品切开为两个或多个产品,我们一般称为“一出二6.切舌:沿不封闭轮廓,将部分板材切开并使其向下弯或者上弯,我们一般称为“刺破”内容来源网络,由深圳机械展收集整理!更多相关内容,就在深圳机械展!。
第三章 板料冲压
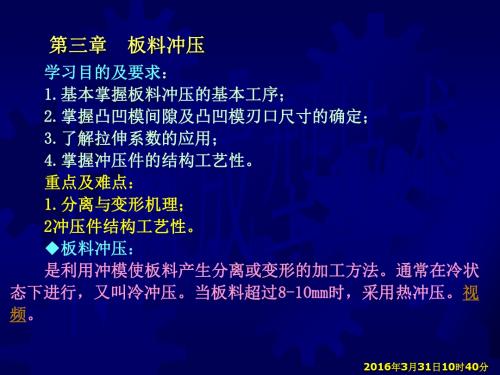
二、连续冲模 它是在冲床的一次冲程中,在模具的不同部位同时完成数道 工序的模具。- 冲孔和落料同时进行。 ◆生产率高,要求定位精度高。
2016年3月31日10时40分
三、复合冲模 它是在冲床的一次冲程中,在模具的同一部位同时完成数道 工序模具。特点是模具中有一个凸凹模- 落料和冲孔同时进行。 精度高,模具复杂。
2016年3月31日10时40分
◆变形特点: 1)底部金属一般不变形,只传递拉力,厚度基本不变; 2)环形部分金属,切向受压应力,径向受拉应力>屈服应力; 3)形成的直壁本身受轴向拉力,厚度有所减小; 4)过度圆角处被拉薄得最严重。 2、拉深中的废品 拉穿:拉应力超过材料强度极限时。 起皱:间隙过大。动画演示。
2016年3月31日10时40分
◆板料冲压的特点: 优点: 1)可以冲出形状复杂的零件,且废料少; 2)产品由足够高的精度和较低的表面粗糙度,互换性好; 3)能获得重量轻、材料消耗少、强度和刚度均较高的零件; 4)冲压操作简单,工艺过程便于机械化和自动化,生产率高 。故零件成本低。 缺点: 冲模制造复杂、成本较高,只适用于大批量生产。 ◆板料冲压的原材料:应具有足够的塑性。 常用材料有: 低碳钢、铜合金、铝合金、镁合金及塑性好的合金钢。形状 上分板料、条料及带料等。
2016年3月31日10时40分
3、旋压 有些空心的回转体件还可用旋压方法来制造。旋压是在专用 旋压机(数控)上进行。视频。 ◆特点: 不需要复杂的冲模,变形力小,但 生产率较低。一般用于中小批生产,某 些厚板和大型容器。
2016年3月31日10时40分
二、弯曲 弯曲是将坯料弯成具有一定角度和曲率的变形工序。动画演 示1、2、3、4。 ◆弯曲部分的内侧受压,而外侧受拉伸。拉应力> 抗拉强度 时造成破裂。板料越厚,内弯曲r越小,则拉应力越大,越容易弯 裂。 为防止弯裂应要注意: 1.弯曲角要大于最小弯曲半径。 rmin=(0.25~1)δ 2.要注意材料的纤维方向。尽可能使弯曲线与板料纤维组织 垂直。 3.使模具角度比成品角度小一个回弹角。弯曲结束后,由于 弹性变形的恢复,使被弯曲的角度增大,回弹。一般0-10º 。
板料冲压的基本工序
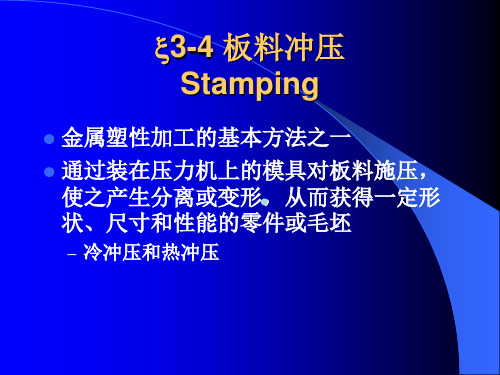
(2)胀形 Bulging:胀形是利用局部变形使 半成品部分内径胀大的冲压成形工艺
(3)起伏Raising, Embossing:利用 局部变形使坯料压 制出各种形状的凸 起或凹陷的冲压工 艺,多用于薄板零 件上制出筋条、文 字、花纹等。
作业:
1、冲孔和落料有何异同?如何 确定凸模和凹模的尺寸?
–影响因素:材料的力学性能、板料厚度、弯曲形状、 相对弯曲半径以及弯曲力的大小等。
–措施:
利用回弹规律,在设计弯曲模时,使模具角度与工件角度 差一个回弹角。
校正
3.拉深 Drawing
利用模具将已落料的平面板坯压制成各 种开口空心零件,或将已制成的开口空 心件毛坯,制成其他形状空心零件的一 种变形工艺,又称拉延。
凹模圆角半径Rd =(5~20)t 凸模圆角半径RP≤Rd
–控制凸模和凹模之间的间隙C= (1.1~1.5)t
–采用有压边圈进行拉深
–采用润滑,以降低拉深件壁部的拉应 力,提高模具寿命。
4. 成形 Forming
使板料或半成品改变局部形状的工序。
(1)翻边 Flanging:将工件的内孔或外缘 翻成竖立边缘的冲压工序 。
生产率高,操作简便,成本低,工艺过程易实 现机械化和自动化;
可利用加工硬化提高零件的力学性能 冲压模具结构较复杂,加工精度要求高,制造
费用大,因此板料冲压加工适用于大批量生产。
板料冲压的原材料及应用
原材料:必须具有足够的塑性
– 金属板料:低碳钢、高塑性的合金钢、不锈 钢、铜、铝、镁及其合金等。
2、弯曲时,易产生什么缺陷或 废品?如何防止?
3、拉深时常见的废品有哪些? 如何防止?
利用模具或其它工具将坯料一部分相对另一部 分弯曲成一定的角度和圆弧的变形工序。
金属工艺学-板料冲压

落料凹模和冲孔凸模尺寸
落料凹模基本尺寸应取 工件尺寸公差范围内的 较小的尺寸。
冲孔凸模基本尺寸应取 工件尺寸公差范围内的 较大尺寸。
二、修整 (1)外缘修整:修整冲裁件外形 (2)内孔修整:修整冲裁件内孔
三、切断
4.冲裁件的排样 排样方式:有搭边排样、无搭边排样
第二节 变形工序
变形工序是使坯料一部分相对于另一部分产 生位移而不破裂的工序。
(4)当凸、凹模采用配制加工时,刃口尺寸的制 造公差一般为冲裁件公差的1/4~1/3。
如果凸、凹模分别加工时,其制造公差之和应 小于或等于最大与最小间隙之差的绝对值,即: (δ凹+δ凸)≤│Zmax -Zmin│。
(5)刃口尺寸计算要根据模具制造特点,冲裁件 的形状简单时,其模具采用分别加工法计算, 冲裁件形状复杂时,其模具用配制法计算。
弯曲边高
带孔弯曲件
3)弯曲带孔零件时,为避免孔的变形,孔的位置 如图所示,L>(1.5~2)s
4)当L过小时,可在弯曲线上冲工艺孔,如对零件孔 的精度要求较高,则应弯曲后再冲孔。
3.对拉伸件的要求
1)外形应简单、对称; 2)应尽量避免直径小而深度过深; 3)底部与侧壁、凸缘与侧壁应有足够的圆角;
2、材料的利用率高,一般可达70—80%;
3、适应性强,金属及非金属均可用冲压方法加工 ,零件可大可小。
4、生产率高,每分钟可冲压小件数千件,易实 现机械化和自动化。
5、模具结构复杂、制造成本高。
三、冲压的基本工序
基本工序
分离工序 变形工序
剪切 冲裁 切口 修边 剖切
弯曲 拉伸 翻边 成形
落料 冲孔
1、拉深过程
拉深中常见的缺陷
1)拉穿
第八章 板料的冲压工艺
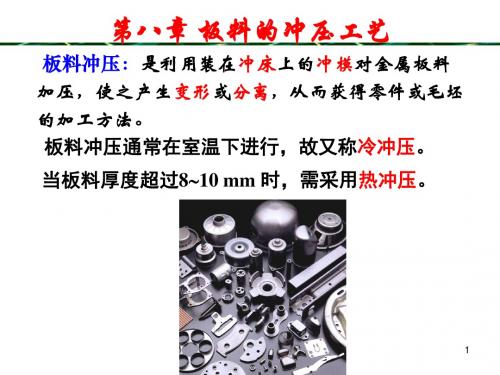
54
4. 冲裁力的计算
冲裁时材料对模具的最大抗力称为冲裁力。 冲裁力大小与板料的材质、厚度及冲裁件周边的长度有关。 普通平刃口冲裁模冲裁力的计算方法如下:
冲裁力是选择压力机的主要依据,也是设计模具所必须的依据。
P=KL
式中
P──冲裁力,N; L──冲裁件周长,mm;
──板料厚度,mm;
31
2. 拉深中常见的废品及防止措施
拉深后,筒形件壁部的厚度与硬度都会发生变化。 筒壁愈靠上,切向压缩愈大,壁部愈厚,变形量愈大, 加工硬化现象严重,硬度愈高。 筒壁的底部靠近圆角处,几乎没有切向压缩,变形程度 小,加工硬化现象小,材料的屈服点低,壁厚变薄。
(1) 拉裂
拉伸件最危险部位——直壁与底部过渡圆角处; 拉应力>材料强度极限时——拉裂 拉深时,极限变形程度就是以不拉裂为前提 的。
第二节 变形工序
第三节 冲模的分类和构造 第四节 冲压工艺过程的制定
6
第一节 分离工序
分离工序——是使坯料的一部分与另一部分相互 分离的工序。如落料、冲孔、切断、精冲等。
一、 落料及冲孔
落料及冲孔(统称冲裁)是使坯料按封闭 轮廓分离的工序。 落料是被分离的部分为成品,而周边是 废料; 冲孔是被分离的部分为废料, 而周边是成品;
① 一般冲裁:精度为IT10~IT11,Ra:12.5~3.2; ② 精密冲裁:IT8~IT9,Ra:3.2~0.20。
25
精冲的工作原理:
精冲时,齿圈压板2将板料3压紧在凹模5表面,V形齿压入材料, 使坯料径向受到压缩,当凸模下压时,板料处于凸模 1的下压力、 齿圈压板2的压边力及顶板4的反压力的共同作用下,此外由于凸、 凹模的间隙很小,坯料处于强烈的三向压应力状态,提高了材料的 塑性,抑制了剪切过程中裂纹的产生,使冲裁过程以接近于纯剪切 的变形方式进行。
- 1、下载文档前请自行甄别文档内容的完整性,平台不提供额外的编辑、内容补充、找答案等附加服务。
- 2、"仅部分预览"的文档,不可在线预览部分如存在完整性等问题,可反馈申请退款(可完整预览的文档不适用该条件!)。
- 3、如文档侵犯您的权益,请联系客服反馈,我们会尽快为您处理(人工客服工作时间:9:00-18:30)。
翻边
使平板柸件上的空或外圆获得内外凸缘的变形工序。
冲模:专用翻边模
11
成形
利用局部变形是柸料货半成品改变形状的工序。
冲模:专用成形模
冲模:冲孔模
4
修整
利用修整模沿冲压件外缘或内孔刮去一薄层金属,以提高冲裁件的加工精度和降低剪断表面粗糙度的冲压方法。
冲模:专用修整模
5
切断
指用剪刃货冲模讲板料沿不封闭轮廓进行分离的工序。
设备:冲床
以制取形状简单、精密要求不高的平板零件
6
精密冲裁
用压边圈是板料冲裁区处于静压作用下,抑制剪裂纹的发生,事先塑料变形分离的冲裁方法。
冲模:冲裁模
大中型工厂使用的冲裁模多数设计出压边圈
7
切口
将材料沿不封闭的曲线部分地方离开,其分离部分的材料发生弯曲。
8
拉深
通过模具把板料加工成空心体或对已初拉成形的空心体进行继续拉深成形工序。
冲模:拉深模
大体可分为旋转体、矩形和复杂形状零件
9
弯曲
柸料的一部分相对于另一部分弯曲成一定角度工序。
冲模:专用弯曲模
板料冲压方法及主要工序小结
序号
方法工序
含义
设备及冲模
适用范围
典型冲压件
1
板料冲压
利用冲模使板料产生分离和变形,以获得零件的加工方法。
设备:剪床、冲床
冲模:专用板料冲压模具
应用于汽车、飞机、农业械化、仪表电器、轻工和日用品等工业部门。
2
落料
3
冲孔
是为了得到带有孔的冲压件。