图形刻蚀技术
精选图形刻蚀技术
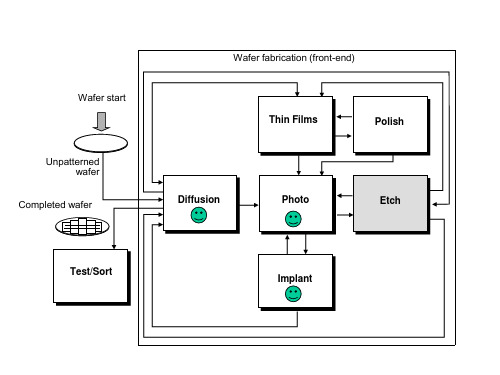
7.1.2 刻蚀中的质量问题:图形畸变:曝光时间、显影时间、刻蚀速度浮胶:粘附、前烘时间、曝光时间、 显影时间、刻蚀速度、腐蚀液毛刺和钻蚀:清洁、显影时间、腐蚀液针孔:膜厚不足、曝光不足、清洁、掩膜版小岛:曝光、清洁、湿法显影、掩膜版湿法腐蚀工艺的特点:速度快,成本底,精度不高。
问题:常见的刻蚀对象:SiO2、Si3N4、Poly-Si、磷硅玻璃、铝或铝合金、衬底材料等即:金属刻蚀、介质刻蚀、硅(半导体)刻蚀
Etch Bias、 Undercut 、 Slope and Overetch
选择比:SEf=被刻蚀材料的刻蚀速率Er=掩蔽层材料的刻蚀速率
对刻蚀的基本要求:图形的高保真:横向腐蚀和各向异性腐蚀刻蚀剖面:选择比:光刻胶和不同材料的腐蚀速度关键尺寸(CD)控制均匀性:小线条和大硅片清洁:残渣沾污损伤:
改变气体温度
刻蚀腔中气体的温度高时刻蚀剖面要好,但刻蚀效果要好,但刻蚀速率几乎不变
改变ac偏压
AC偏压变化时,刻蚀体现不出差别
改变dc偏压
DC偏压大时刻蚀效果要好,刻蚀速率几乎不变
改变等离子体刻蚀速率的线性部分
等离子体刻蚀速率的线性系数与刻蚀速率成线性
改变刻蚀腔压强时的刻蚀剖面
See Table 11.3
InGaAs刻蚀仿真
刻蚀前结构
PIN结构。10um厚的本征InP衬底,在衬底上生长3um厚的掺杂Si浓度为2×1018的InP层(N+),然后再淀积3um厚的Si掺杂4×1016的n-,InGaAs,InGaAs中In的组分为0.53。上层淀积1um厚的InP,掺杂为2×1018(P+)。刻蚀阻挡层采用Si3N4,厚度1um。
Chemical Versus Physical
Dry Plasma Etching
光刻与刻蚀工艺

1、涂胶
第十六页,共118页。
1、涂胶
❖涂胶目的 ❖在硅片表面形成厚度均匀、附着性强、并
且没有(méi yǒu)缺陷的光刻胶薄膜。 ❖怎样才能让光刻胶粘的牢一些?
第十七页,共118页。
可以(kěyǐ)开始涂胶了……
❖ 怎么涂? ❖旋转涂胶法:把胶滴在硅片,然后使硅片
高速旋转,液态胶在旋转中因离心力作用 (zuòyòng)由轴心沿径向(移动)飞溅出去, 但粘附在硅表面的胶受粘附力的作用 (zuòyòng)而留下。在旋转过程中胶所含的 溶剂不断挥发,故可得到一层均匀的胶膜 ❖ 怎样才算涂的好?
❖一个英制等级100的洁净室相当于公制等级
第八页,共118页。
洁净室(4)
❖ 对一般的IC制造区 域,需要等级100的洁 净室,约比一般室内 空气低4个数量级。
❖ 在图形(túxíng)曝 光的工作区域,则需 要等级10或1的洁净室。
第九页,共118页。
lithography
❖Introduction ❖光刻 ❖洁净室 ❖工艺流程(ɡōnɡ yì liú chénɡ) ❖光刻机 ❖光刻胶 ❖掩膜版
第十四页,共118页。
resist substrate
maБайду номын сангаасk
negative tone
光刻工艺(gōngyì)过程
❖ 涂胶 coating ❖ 前烘 prebaking ❖ 曝光(bào guāng) exposure ❖ 显影 development ❖ 坚膜 postbake ❖ 刻蚀 etch ❖ 去胶 strip ❖ 检验 inspection
第二十八页,共118页。
❖显4、影之显后影的(x检iǎ查n yǐng)(Development)
光刻与刻蚀工艺
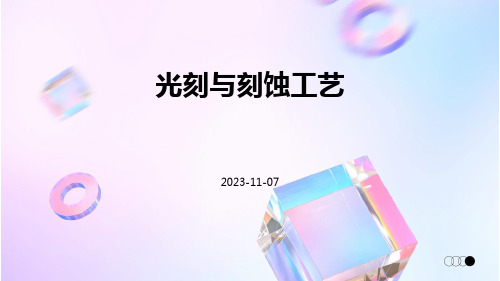
涂胶/显影技术
01
02
03
涂胶
在晶圆表面涂上一层光敏 胶,以保护非曝光区域并 提高图像对比度。
显影
用适当的溶剂去除曝光区 域的光敏胶,以形成所需 的图案。
控制胶厚
保持胶厚均匀,以避免图 像的扭曲和失真。
烘烤与曝光技术
烘烤
通过加热去除晶圆表面的湿气,以提高光敏胶的灵敏度和图像质 量。
曝光
将掩模图像投影到光敏胶上,通过光化学反应将图像转移到晶圆 上。
非接触式光刻
投影式非接触
利用光学系统将掩膜板上的图像投影到光刻胶涂层上,优点是无需直接接触,缺点是难度较高,需要精确的控 制系统。
电子束光刻
利用电子束在光刻胶上直接曝光,优点是分辨率高、无需掩膜板,缺点是生产效率低。
投影式光刻
接触式投影
掩膜板与光刻胶涂层之间保持接触,通过投影系统将图像投影到光刻胶上,优点是操作简单、高效, 缺点是图像质量可能受到掩膜板损伤和光刻胶污染的影响。
要点二
损伤控制
是指在刻蚀过程中避免对材料产生损伤。对于某些特殊 材料,如脆性材料,损伤控制尤为重要。如果刻蚀过程 中产生过多损伤,可能会导致材料性能下降甚至破裂。
感谢您的观看
THANKS
光刻工艺的基本步骤
涂胶
将光刻胶涂敷在硅片表面,以形成 光刻胶层。
烘烤
通过烘烤使光刻胶层干燥并固化。
曝光
将掩膜版上的图形对准硅片上的光 刻胶层,并使用曝光设备将图形转 移到光刻胶上。
显影
使用显影液将曝光后的光刻胶进行 化学处理,使图形更加清晰地展现 出来。
光刻工艺的重要性
光刻工艺是半导体制造中的关键环节,直接影响芯片的制造 质量和性能。
第八章光刻与刻蚀工艺模板

第八章光刻与刻蚀工艺模板光刻与刻蚀工艺是现代集成电路制造中的重要工艺环节之一、光刻技术用于在硅片上制作电路图形,而刻蚀技术则用于去除不需要的材料,以形成所需的电路结构。
本章将介绍光刻与刻蚀工艺的基本原理及常见的工艺模板。
一、光刻工艺模板在光刻工艺中,需要使用光刻胶作为图形保护层,以及光罩作为图形的模板。
光刻模板通常由硅片或光刻胶制成,可以通过不同的工艺步骤来实现具体的图形需求。
1.硅片模板硅片模板是一种常见的光刻工艺模板,它的制作过程相对简单。
首先,将一块纯净的硅片进行氧化处理,形成硅的氧化层。
然后,在氧化层上通过光刻技术制作所需的图形。
最后,使用化学刻蚀方法去除不需要的硅的氧化层,就可以得到所需的硅片模板。
硅片模板具有较好的精度和可靠性,能够满足微纳加工的要求。
然而,硅片模板制作过程复杂,成本较高。
2.光刻胶模板光刻胶模板是利用光刻胶作为模板材料的一种工艺模板。
光刻胶是一种感光性的聚合物材料,可以在光照的作用下发生化学反应。
在光刻工艺中,首先将光刻胶涂覆在硅片上,然后通过光刻曝光将所需的图形转移到光刻胶上。
接下来,使用化学方法或溶剂去除不需要的光刻胶,就可以得到所需的光刻胶模板。
光刻胶模板制作过程简单,成本较低。
同时,光刻胶模板的精度较高,可以满足微纳加工的要求。
然而,光刻胶模板的使用寿命较短,通常只能使用几次。
在刻蚀工艺中,需要使用刻蚀胶作为图形保护层,以及刻蚀模板作为图形的模板。
刻蚀模板通常由硅片或光刻胶制成,可以通过不同的工艺步骤来实现具体的图形需求。
1.硅片模板硅片模板在刻蚀工艺中的制作方法与光刻工艺类似。
首先,在硅片上通过光刻技术制作所需的图形,然后使用化学刻蚀方法去除不需要的硅材料,就可以得到所需的刻蚀模板。
硅片模板具有较高的精度和可靠性,可以满足微纳加工的要求。
然而,硅片模板制作过程复杂,成本较高。
2.光刻胶模板光刻胶模板在刻蚀工艺中的制作方法与光刻工艺类似。
首先,将光刻胶涂覆在硅片上,然后通过光刻曝光将所需的图形转移到光刻胶上。
集成电路工艺:刻蚀

1. 引 言
1.1刻蚀的概念
刻蚀:它是半导体制造工艺,微电子IC制造工 艺以及微纳制造工艺中的一种相当重要的步骤。 是与光刻相联系的图形化(pattern)处理的一 种主要工艺。所谓刻蚀,实际上狭义理解就是 光刻腐蚀,先通过光刻将光刻胶进行光刻曝光 处理,然后通过其它方式实现腐蚀处理掉所需 除去的部分。随着微制造工艺的发展;广义上 来讲,刻蚀成了通过溶液、反应离子其它机 械方式来剥离、去除材料的一种统称,成为微 加工制造的一种普适叫法。
4.2常用材料的湿法刻蚀
1.二氧化硅湿法刻蚀 采用氢氟酸溶液加以进行。因为二氧化硅可与室
温的氢氟酸溶液进行反应,但却不会蚀刻硅基材 及多晶硅。反应式如下:
SiO2 + 6HF= H2[SiF6] + 2H2O 由于氢氟酸对二氧化硅的蚀刻速率相当高,在制
程上很难控制,因此在实际应用上都是使用稀释 后的氢氟酸溶液,或是添加氟化铵(NH4F)作 为缓冲剂的混合液,来进行二氧化硅的蚀刻。
下层的Ti ➢ 金属铝的刻蚀步骤多,工艺复杂
4. 湿法刻蚀
4.1 湿法刻蚀的原理
湿法刻蚀是将被刻蚀材料浸泡在腐蚀液内进行腐蚀 的技术
这是各向同性的刻蚀方法,利用化学反应过程去除 待刻蚀区域的薄膜材料
湿法刻蚀,又称湿化学腐蚀法。半导体制造业一开 始,湿法腐蚀就与硅片制造联系在一起。现在湿法 腐蚀大部分被干法刻蚀代替,但在漂去氧化硅、除 去残留物、表层剥离以及大尺寸的图形腐蚀应用方 面起着重要作用。尤其适合将多晶硅、氧化物、氮 化物、金属与Ⅲ-Ⅴ族化合物等作整片的腐蚀。
干法刻蚀是各向异性刻蚀,用物理和化学方法, 能实现图形的精确转移,是集成电路刻蚀工艺的 主流技术。
各向同性刻蚀:侧向与纵向腐蚀速度相同 各向异性刻蚀:侧向腐蚀速度远远小于纵向腐蚀
半导体行业之刻蚀工艺

1.负载效应等离子体图形化刻蚀过程中,刻蚀图形将影响刻蚀速率和刻蚀轮廓,称为负载效应。
负载效应有两种:宏观负载效应和微观负载效应。
宏观负载效应具有较大开口面积的晶圆刻蚀速率与较小开口面积的晶圆刻蚀速率不同,这种晶圆对晶圆的刻蚀速率差异就是宏观负载效应,这主要影响批量刻蚀,但对单片晶圆影响不大。
微观负载效应对于接触窗和金属层间接触窗孔的刻蚀,较小窗孔的刻蚀速率比大窗孔慢。
这就是微观负载效应(见下图(a)),产生该效应的原因是刻蚀等离子体气体难以穿过较小的窗孔,而且刻蚀的副产品也难以扩散出去。
减少工艺压力可以降低微观负载效应。
当压力较低时,平均自由程较长,刻蚀气体较易穿过微小的窗孔而接触到要被刻蚀的薄膜,从而比较容易从微小的窗孔中把刻蚀副产品去除。
由于光刻胶会溅镀沉积在侧壁上,所以图形隔离区域的刻蚀轮廓比密集区域宽,这是由于隔离图形区域缺少由邻近图形散射离子造成的侧壁离子轰击。
下图(b)说明了微观负载效应轮廓。
2.过刻蚀效应当刻蚀薄膜时(包括多晶硅、电介质以及金属刻蚀),晶圆内的刻蚀速率和薄膜厚度并不完全均匀。
因此当大部分薄膜被刻蚀移除后,留下的少部分薄膜必须移除。
移除剩余薄膜的过程称为过刻蚀,过刻蚀前的过程称为主刻蚀。
在过刻蚀中,被刻蚀薄膜和衬底材料之间的选择性要足够高才能避免损失过多的衬底材料。
在主刻蚀中,如果主刻蚀与过刻蚀使用不同的刻蚀条件,则能够改善过刻蚀中被刻薄膜和衬底材料之间的选择性,等离子体刻蚀中的光学终点侦测器可以自动停止主刻蚀而引发过刻蚀,这是因为当主刻蚀中的刻蚀剂开始刻蚀衬底薄膜时,等离子体中的成分就会发生变化。
如在多晶硅栅刻蚀中(见下图),主刻蚀不需要考虑二氧化硅的选择性。
当某些区域的多晶硅被刻蚀时,氯等离子体开始刻蚀二氧化硅,氧的辐射信号强度就会增强,从而发出一个停止主刻蚀而切换到过刻蚀的信号。
下图说明了主刻蚀和过刻蚀过程。
问题:对于一个IC芯片,多晶硅的厚度为3000A,薄膜的非均匀性为1.5%。
刻蚀工艺介绍

刻蚀前后对比照片
Metal刻蚀前后:
ITO刻蚀前后:
主要工艺参数
1 刻蚀液浓度 刻蚀液的浓度对刻蚀效果影响较大,所以 我们主要通过:来料检验、首片确认、定 期更换的方法来保证。 温度越高刻蚀效率越高,但是温度过高工 艺方面波动较大,只要通过设备自带温控 器和点检确认。 刻蚀流片的速度与刻蚀速率密切相关 喷淋流量的大小决定了基板表面药液置换 速度的快慢,流量控制可保证基板表面药 液浓度均匀。 过刻量即测蚀量,适当增加测试量可有效 控制刻蚀中的点状不良
辛小刚
刻蚀原理刻蚀不良原因分析
刻蚀原理介绍
刻蚀是用一定比例的酸液把玻璃上未受光刻胶保护的 Metal/ITO膜通过化学反应去除掉 膜通过化学反应去除掉, Metal/ITO膜通过化学反应去除掉,最终形成制程所需 要的图形。 要的图形。
刻蚀种类
目前我司的刻蚀种类主要分两种: 1、Metal刻蚀 刻蚀液主要成分:磷酸、硝酸、醋酸、水。 Metal:合金金属 2、ITO刻蚀 刻蚀液主要成分:盐酸、硝酸、水。 ITO:氧化铟锡(混合物)
刻蚀原理介绍主要工艺参数刻蚀液更换频率的管控刻蚀不良的产生原因单击此处编辑母版标题样式单击此处编辑母版标题样式刻蚀工艺介绍辛小刚刻蚀原理介绍刻蚀主要工艺参数刻蚀液更换频率的管控刻蚀不良原因分析刻蚀是用一定比例的酸液把玻璃上未受光刻胶保护的metalito膜通过化学反应去除掉最终形成制程所需要的图形
刻蚀工艺介绍
2
刻蚀温度
3
刻蚀速度
4
喷淋流量
5
过刻量
刻蚀液更换频率的管控
作业数量管控: 作业数量管控: 每天对生产数量及时记录,达到规定作业片数 及时更换。 作业时间管控: 作业时间管控: 由于药液的挥发,所以如果在规定更换时间未 达到相应的生产片数药液也需更换。 首片和抽检管控: 首片和抽检管控: 作业时需先进行首片确认,且在作业过程中每 批次进行抽检(时间间隔约25min)。
干法刻蚀
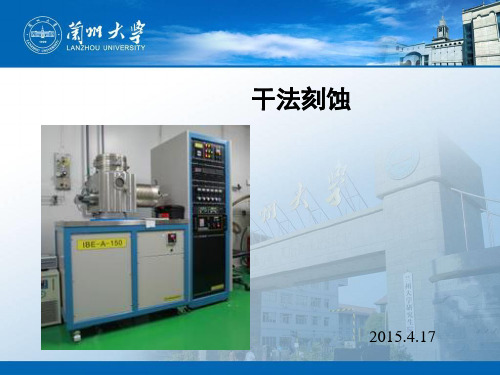
2
干法刻蚀技术的分类
物理化学刻蚀:
物理和化学混合作用的机理可以理解为离子轰击改善化学刻蚀作用。加入离子 撞击的作用:一是将待蚀刻物质表面的原子键结破坏,以加速蚀刻速率;二是 将再沉积于待蚀刻物质表面的产物或聚合物打掉,以便待蚀刻物质表面能再与 反应蚀刻气体接触
3
典型的干法刻蚀模式及原理
离子束刻蚀(IBE):
3
典型的干法刻蚀模式及原理
电感耦合等离子体刻蚀(ICP):
ICP系统有2个独立的射频电源 RF1和RF2,一个接到反应室外 的电感线圈,另一个接反应室 内的电极。给反应室外的线圈 加压时,反应室内产生交变的 电磁场,当电场达一定程度时, 气体产生放电现象,进入等离 子态,交变的电磁场使等离子 体中电子路径改变,增加等离 子体密度
3
典型的干法刻蚀模式及原理
GaAs刻蚀
GaN刻蚀
3
典型的干法刻蚀模式及原理
RIE与ICP比较:
RIE 离子密度低( ~109 ~1010/cm3) 离子密度与离子能量不能分别控 制 离子能量低,刻蚀速率低 低压下刻蚀速率低 DC Bias损伤大 ICP 离子密度高(>1011/cm3)(刻蚀速率 高) 离子密度由ICP功率控制,离子能 量由RF功率控制 在低离子能量下可控离子流量达 到高刻蚀速率 低压下由于高离子流量从而维持 高刻蚀速率 DC Bias损伤小
干法刻蚀
2015.4.17
1
2 3
刻蚀技术中的术语
干法刻蚀技术的分类
典型的干法刻蚀模式及原理
4
干法刻蚀技术的应用
1
刻蚀技术中的术语
刻蚀
用物理的、化学的或同时使用化学和物理的方 法,有选择地把没有被抗蚀剂掩蔽的那一部分 材料去除,从而得到和抗蚀剂完全一致的图形
刻蚀
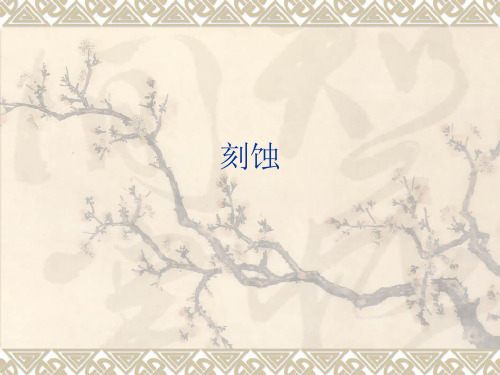
铜 CuCl2挥发性较弱,一般不用化学方式进行
主要是采用物理高能粒子的轰击方式,将其
去除
钨的回蚀: 采用氟化物等离子体(例如:CF4、NF3、SF6
等),进行反应离子刻蚀,将覆盖于介电层 表面的钨去掉,只留下介电层导电孔内的钨, 此过程又称为钨的回蚀。
终点检测
由于干法刻蚀选择比较差些,过度刻蚀会造
ion etching):通过活性离子对衬底的物理轰击 和化学反应双重作用刻蚀,
离子轰击加上自由基反应 具有溅射刻蚀和等离子刻蚀两者的优点
各向异性
选择性较好
目前,RIE已成为超大规模集成电路VLSI工
艺中应用最广泛的主流刻蚀技术
三种常见干法刻蚀方法的比较
等离子体刻蚀 刻蚀速率 选择性 刻蚀分布 终点控制 从高到低 很好 各向同性 时间或观察 溅射刻蚀 较低 较差 反应离子刻蚀 较高,可控 适中,可控
(1)等离子体引起损伤 原因:等离子体内具有一定能量的离子、电子 和处于激发状态的分子,对晶片表面的轰击会 产生机械损伤等。 形式:俘获界面电荷,材料缺陷迁移到主体材 料中等。
影响:
改变敏感器件的性质,如肖特基二极管的整流能
力降低; 在氧化层接触孔的刻蚀过程中,高分子聚合物的 淀积,会引起高的接触电阻; 在刻蚀过程中形成的挥发性物质会引起产品电学 性能的改变,影响稳定性等。
②
③ ④
特点 可实现各向异性的刻蚀,图形保真性高,有 很好的线宽尺寸控制,分辨率可在1µm以下 的精细图形加工的主要刻蚀方法; 刻蚀速率有较好控制,刻蚀均匀性好:片内, 片间以及批次间都可以保持较好的均匀性; 刻蚀选择性比湿法刻蚀差,要注意刻蚀终点 的监测。 设备复杂,成本高。
干法刻蚀的方法
(第六章)刻蚀知识讲解
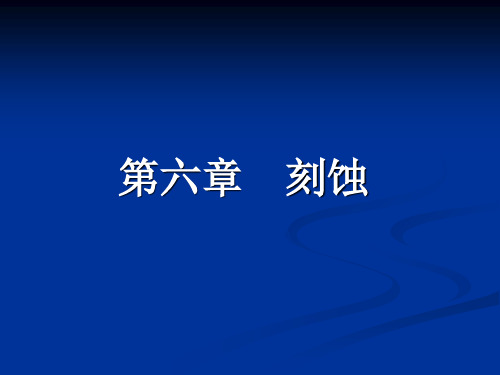
干法刻蚀的缺点(与湿法腐蚀比) 1. 对下层材料的刻蚀选择比较差 2. 等离子体诱导损伤 3. 设备昂贵
干法刻蚀过程
1. 刻蚀气体进入反应腔 2. RF电场使反应气体分解电离 3. 高能电子、离子、原子、自由基等结合产生等离子体 4. 反应正离子轰击表面-各向异性刻蚀(物理刻蚀) 5. 反应正离子吸附表面 6. 反应元素(自由基和反应原子团)和表面膜的表面反
= ΔTsio2/ΔT胶
(a)0时刻
(b)t1时刻
5. 均匀性 刻蚀均匀性是指刻蚀速率在整个硅片或整批硅片上 的一致性情况。非均匀性刻蚀会产生额外的过刻蚀。
ARDE效应-微负载效应:Aspect Ratio Dependence Etching
Emax:最大刻蚀速率 Emin:最小刻蚀速率 Eave:平均刻蚀速率
(b) Substrate after etch
6.1 引 言
刻蚀的工艺目的: 把光刻胶图形精确地转移到硅片上,最后达到复制 掩膜版图形的目的。它是在硅片上复制图形的最后 主要图形转移工艺。
刻蚀工艺分类:干法刻蚀和湿法刻蚀
✓ 干法刻蚀:把要刻蚀的硅片放在具有反应气体的等 离子体真空腔中去除表面层材料的工艺过程。亚微 米
硅槽
湿法刻蚀是各向同性腐蚀, 干法刻蚀有各向同性腐蚀,也
不能实现图形的精确转移, 有各向异性腐蚀。各向异性腐
一般用于特征尺寸较大的
蚀能实现图形的精确转移,是
情况(≥3μm) 。
集成电路刻蚀工艺的主流技术。
3. 刻蚀偏差
刻蚀偏差是指刻蚀以后线宽或关键尺寸的变化 刻蚀偏差=Wa-Wb
Wb
Wa
Bias
✓ 湿法刻蚀:把要腐蚀的硅片放在化学腐蚀液里去除 表面层材料的工艺过程。大于3微米
第二章干法刻蚀的介绍
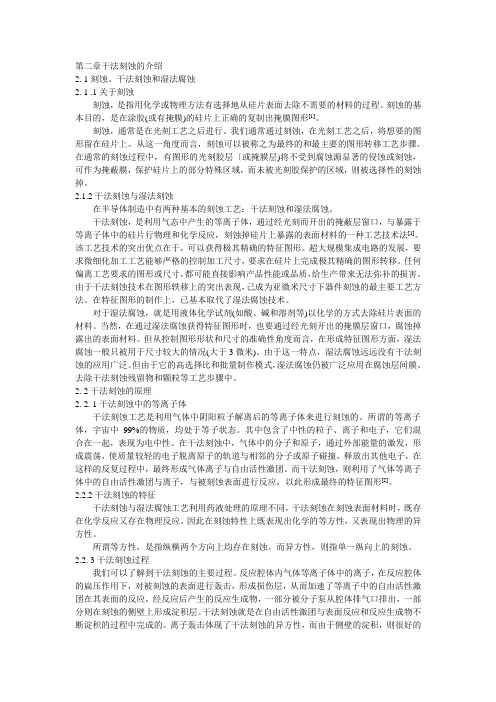
第二章干法刻蚀的介绍2. 1刻蚀、干法刻蚀和湿法腐蚀2. 1 .1关于刻蚀刻蚀,是指用化学或物理方法有选择地从硅片表面去除不需要的材料的过程。
刻蚀的基本目的,是在涂胶(或有掩膜)的硅片上正确的复制出掩膜图形[1]。
刻蚀,通常是在光刻工艺之后进行。
我们通常通过刻蚀,在光刻工艺之后,将想要的图形留在硅片上。
从这一角度而言,刻蚀可以被称之为最终的和最主要的图形转移工艺步骤。
在通常的刻蚀过程中,有图形的光刻胶层〔或掩膜层)将不受到腐蚀源显著的侵蚀或刻蚀,可作为掩蔽膜,保护硅片上的部分特殊区域,而未被光刻胶保护的区域,则被选择性的刻蚀掉。
2.1.2干法刻蚀与湿法刻蚀在半导体制造中有两种基本的刻蚀工艺:干法刻蚀和湿法腐蚀。
干法刻蚀,是利用气态中产生的等离子体,通过经光刻而开出的掩蔽层窗口,与暴露于等离子体中的硅片行物理和化学反应,刻蚀掉硅片上暴露的表面材料的一种工艺技术法[1]。
该工艺技术的突出优点在于,可以获得极其精确的特征图形。
超大规模集成电路的发展,要求微细化加工工艺能够严格的控制加工尺寸,要求在硅片上完成极其精确的图形转移。
任何偏离工艺要求的图形或尺寸,都可能直接影响产品性能或品质,给生产带来无法弥补的损害。
由于干法刻蚀技术在图形轶移上的突出表现,己成为亚微米尺寸下器件刻蚀的最主要工艺方法。
在特征图形的制作上,已基本取代了湿法腐蚀技术。
对于湿法腐蚀,就是用液体化学试剂(如酸、碱和溶剂等)以化学的方式去除硅片表面的材料。
当然,在通过湿法腐蚀获得特征图形时,也要通过经光刻开出的掩膜层窗口,腐蚀掉露出的表面材料。
但从控制图形形状和尺寸的准确性角度而言,在形成特征图形方面,湿法腐蚀一般只被用于尺寸较大的情况(大于3微米)。
由于这一特点,湿法腐蚀远远没有干法刻蚀的应用广泛。
但由于它的高选择比和批量制作模式,湿法腐蚀仍被广泛应用在腐蚀层间膜、去除干法刻蚀残留物和颗粒等工艺步骤中。
2. 2干法刻蚀的原理2. 2. 1干法刻蚀中的等离子体干法刻蚀工艺是利用气体中阴阳粒子解离后的等离子体来进行刻蚀的。
刻蚀

11.5 离子铣
离子铣刻蚀又称为离子束溅射刻蚀。 一、离子溅射刻蚀机理 入射离子以高速撞击固体表面,当传递给固体原子的能量 超过其结合能(几到几十电子伏特)时,固体原子就会脱离其 晶格位置而被溅射出来。这是一种纯粹的物理过程。 一次溅射:入射离子直接将晶格位置上的原子碰撞出来。 二次溅射:被入射离子碰撞出来的晶格原子,若具有足够 的能量时,可将其它晶格原子碰撞出来。
刻蚀硅基材料时的刻蚀气体有 CF4、C2F6 和 SF6 等。其中 最常用的是 CF4 。
CF4 本身不会并直接刻蚀硅。等离子体中的高能电子撞击 CF4 分子使之裂解成 CF3 、CF2 、C 和 F,这些都是具有极强 化学反应性的原子团。
CF4 等离子体对 Si 和 SiO2 有很高的刻蚀选择比,室温下 可高达 50,所以很适合刻蚀 SiO2 上的 多晶 Si 。
10-2 ~ 10-4 Torr ,加工室气压为 10-5 ~ 10-7 Torr 。
(2) 离子源与加工室一体的,如射频型,气压为 10-2 Torr。
三、离子束溅射刻蚀的特点 优点 1、入射离子有很强的方向性,为各向异性刻蚀,无侧向 钻蚀,刻蚀分辨率高; 2、能刻蚀任何材料,一次能刻蚀多层材料; 3、刻蚀在高真空中进行,刻蚀过程不易受污染。
化学刻蚀 电解刻蚀
离子铣刻蚀(物理作用) 等离子体刻蚀(化学作用) 反应离子刻蚀(物理化学作用)
与湿法化学刻蚀相比,干法刻蚀对温度不那么敏感,工艺 重复性好;有一定的各向异性;等离子体中的颗粒比腐蚀液中 的少得多;产生的化学废物也少得多。
11.1 湿法刻蚀
湿法刻蚀是一种纯粹的化学反应过程。 优点 1、应用范围广,适用于几乎所有材料; 2、选择比大,易于光刻胶的掩蔽和刻蚀终点的控制; 3、操作简单,成本低,适宜于大批量加工。
刻蚀技术

湿法刻蚀
选择性刻蚀---常用溶液 选择性刻蚀---常用溶液(续) ---
常用的湿法刻蚀液: 常用的湿法刻蚀液:KOH+异丙脂+水 +异丙脂+
许多先进电子器件的组成都是由一种薄膜材料淀积到另一层材料 上。需要选择性刻蚀制备各层之间的电接触孔。 需要选择性刻蚀制备各层之间的电接触孔。
有时需要一定程度的定向刻蚀中半导体衬底上腐蚀很深的图案。 有时需要一定程度的定向刻蚀中半导体衬底上腐蚀很深的图案。
有时利用沟槽来做高集成度IC器件的彼此隔离。 有时利用沟槽来做高集成度 器件的彼此隔离。 器件的彼此隔离
电子科学与技术系
湿法腐蚀
对Al的腐蚀 的腐蚀
湿法腐蚀广泛用于对铝连线的腐蚀。 湿法腐蚀广泛用于对铝连线的腐蚀。
Ai是多晶体,湿法腐蚀生产的联系边缘参差不齐。 是多晶体,湿法腐蚀生产的联系边缘参差不齐。 是多晶体
常用20%的乙酸+ %的磷酸+ %的硝酸。 常用 %的乙酸+77%的磷酸+3%的硝酸。
硅工艺中的铝互连不是纯铝,其中的杂质挥发性不及基体材料, 硅工艺中的铝互连不是纯铝,其中的杂质挥发性不及基体材料, 搀杂的铜、硅很难除去。 搀杂的铜、硅很难除去。 2011-12-1 15
与暴露的膜发生化学反应生成可溶解的副产物
从硅片表面移去反应生成物
三个步骤都必须发生,最慢的一步称为速率限制步骤, 三个步骤都必须发生,最慢的一步称为速率限制步骤,决 定刻蚀速率。 定刻蚀速率。
2011-12-1 9
电子科学与技术系
湿法刻蚀
被腐蚀的膜并非直接溶解于刻蚀剂中。 被腐蚀的膜并非直接溶解于刻蚀剂中。必须将被腐蚀的材 料从固态转化为气态或液态。 料从固态转化为气态或液态。 这种气体将形成气泡从而阻止新的腐蚀剂向硅片表面移动。 这种气体将形成气泡从而阻止新的腐蚀剂向硅片表面移动。 由于气泡的发生不能被预测,问题尤其严重。 由于气泡的发生不能被预测,问题尤其严重。 为帮助新鲜的腐蚀剂化学药液移动到硅片表面, 为帮助新鲜的腐蚀剂化学药液移动到硅片表面,在湿法刻 蚀化学槽中的搅拌将减少硅片表面鼓泡的附着力。 蚀化学槽中的搅拌将减少硅片表面鼓泡的附着力。 由于除去所有腐蚀产物很困难,即使不产生鼓泡, 由于除去所有腐蚀产物很困难,即使不产生鼓泡,小的几 何特征尺寸图形也可能腐蚀得很慢。 何特征尺寸图形也可能腐蚀得很慢。
图形化衬底(PSS)刻蚀设备工艺研究进展
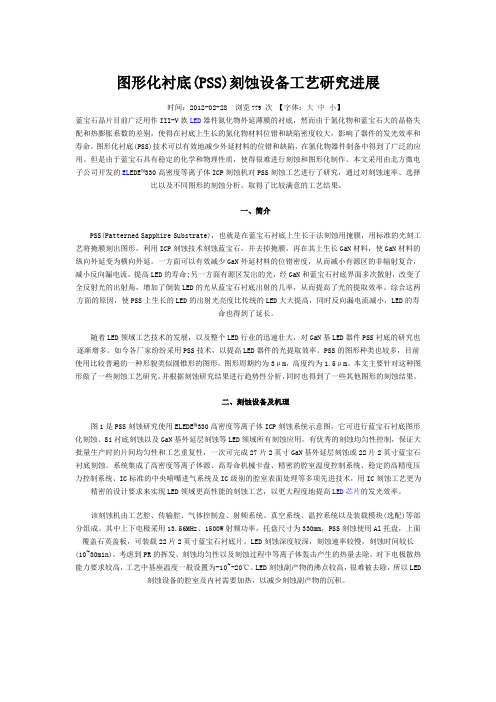
图形化衬底(PSS)刻蚀设备工艺研究进展时间:2012-02-28 浏览779次【字体:大中小】蓝宝石晶片目前广泛用作III-V族LED器件氮化物外延薄膜的衬底,然而由于氮化物和蓝宝石大的晶格失配和热膨胀系数的差别,使得在衬底上生长的氮化物材料位错和缺陷密度较大,影响了器件的发光效率和寿命。
图形化衬底(PSS)技术可以有效地减少外延材料的位错和缺陷,在氮化物器件制备中得到了广泛的应用。
但是由于蓝宝石具有稳定的化学和物理性质,使得很难进行刻蚀和图形化制作。
本文采用由北方微电子公司开发的EL EDE™330高密度等离子体ICP刻蚀机对PSS刻蚀工艺进行了研究,通过对刻蚀速率、选择比以及不同图形的刻蚀分析,取得了比较满意的工艺结果。
一、简介PSS(Patterned Sapphire Substrate),也就是在蓝宝石衬底上生长干法刻蚀用掩膜,用标准的光刻工艺将掩膜刻出图形,利用ICP刻蚀技术刻蚀蓝宝石,并去掉掩膜,再在其上生长GaN材料,使GaN材料的纵向外延变为横向外延。
一方面可以有效减少GaN外延材料的位错密度,从而减小有源区的非辐射复合,减小反向漏电流,提高LED的寿命;另一方面有源区发出的光,经GaN和蓝宝石衬底界面多次散射,改变了全反射光的出射角,增加了倒装LED的光从蓝宝石衬底出射的几率,从而提高了光的提取效率。
综合这两方面的原因,使PSS上生长的LED的出射光亮度比传统的LED大大提高,同时反向漏电流减小,LED的寿命也得到了延长。
随着LED领域工艺技术的发展,以及整个LED行业的迅速壮大,对GaN基LED器件PSS衬底的研究也逐渐增多。
如今各厂家纷纷采用PSS技术,以提高LED器件的光提取效率。
PSS的图形种类也较多,目前使用比较普遍的一种形貌类似圆锥形的图形,图形周期约为3μm,高度约为1.5μm。
本文主要针对这种图形做了一些刻蚀工艺研究,并根据刻蚀研究结果进行趋势性分析,同时也得到了一些其他图形的刻蚀结果。
刻蚀技术.ppt
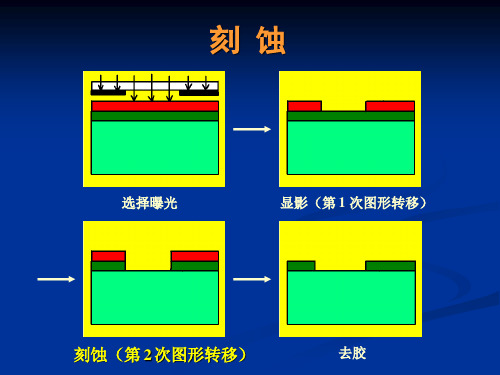
(2) 离子源与加工室一体的,如射频型,气压为 10-2 Torr。
工作原理(以射频型为例)
射频发生器
Vb
C
Va
接地电极(阳极) 等离子体区(亮区) 电位降区(暗区)
浮空电极(阴极)
典型工艺条件 射频频率:13.56 MHz
RF electrode
Wafers
Gas in Reaction chamber
Wafers
RF generator
Quartz boat
Vacuum pump
典型工艺条件 射频频率:13.56 MHz
射频功率:300 ~ 600 W
工作气体: O2(去胶) F 基(刻蚀 Si、Poly-Si、Si3N4 等) F 基 + H2(刻蚀 SiO2 等)
2 干法刻蚀基本分类
等离子体刻蚀(化学作用) 反应离子刻蚀(物理化学作用) 离子铣刻蚀(物理作用)
3等离子体刻蚀
一、等离子体刻蚀机理
在低温等离子体中 ,除了含有电子和离子外,还含有大量 处于 激发态的游离基 和 化学性质活泼的中性原子团。正是利用 游离基和中性原子团与被刻蚀材料之间的化学反应 ,来达到刻 蚀的目的 。对硅基材料的基本刻蚀原理 是用 “ 硅--卤 ” 键代 替 “ 硅--硅 ” 键 ,从而产生挥发性的硅卤化合物。
0 ,这时靶原子
可获得最大能量,即 Emax E0 。所以为获得最好的溅射效果,
应选择入射离子使其质量尽可能接近靶原子。
2、要求入射离子对被刻蚀材料的影响尽量小 3、容易获得 例如,若要对 SiO2 进行溅射加工,根据要求 2 与要求 3 , 入射离子应在较为容易获得的惰性气体离子 Ar+、Kr+ 和 Xe+ 中选择,又因 Si 原子和 O2 分子的原子量分别是 28 和 32,而 Ar+、Kr+ 和 Xe+的原子量分别是 40、84 和 131,所以采用 Ar+ 离子的效果是最好的。
刻蚀工艺
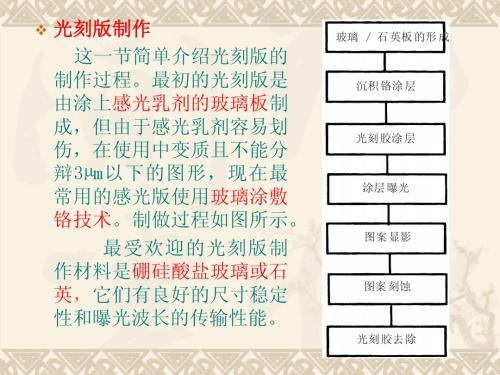
光刻胶的去除 刻蚀工艺完成后,作为刻蚀阻挡层的光刻胶 已经完成任务,必须从表面去掉。传统的方法 是用湿法化学工艺去除,尽管有一些问题,湿 法去除在前线工艺还是经常采用的一种方法 (特别是硅片表面和MOS栅极暴露并易于受到等 离子体中氧气离子的损伤)。 另一种是干法的等离子体去除,在后线工 艺中经常采用(此时硅片和MOS栅极已经被绝缘 和金属层覆盖)。 湿法去除有许多不同的化学品被由于去除工 艺,其选择依据是晶圆表层、产品考虑、光刻 胶极性和光刻胶的状态(见下图)。
2、要求入射离子对被刻蚀材料的影响尽量小。 、要求入射离子对被刻蚀材料的影响尽量小。 3、容易获得。 、容易获得。 例如, 进行溅射加工, 例如,若要对 SiO2 进行溅射加工,根据要求 2 与要求 3 , 入射离子应在较为容易获得的惰性气体离子 Ar+ 、Kr+ 和 Xe+ 中选择, 中选择,又因 Si 原子和 O2 分子的原子量分别是 28 和 32 ,而 Ar+ 、Kr+ 和 Xe+ 的原子量分别是 40、84 和 131,所以采用 、 , Ar+ 离子的效果是最好的。 离子的效果是最好的。
光刻版制作 这一节简单介绍光刻版的 制作过程。最初的光刻版是 由涂上感光乳剂的玻璃板制 成,但由于感光乳剂容易划 伤,在使用中变质且不能分 辩3µm以下的图形,现在最 常用的感光版使用玻璃涂敷 铬技术。制做过程如图所示。 最受欢迎的光刻版制 作材料是硼硅酸盐玻璃或石 英,它们有良好的尺寸稳定 性和曝光波长的传输性能。
少一个电子的氟原子
离子的形成
选择离子的原则: 选择离子的原则: 1、质量 、 质量为 M2 的靶原子从质量为 M1 的入射离子所获得的能量 为:
4M1M2 E= E0 2 (M1 + M2 )
刻蚀技术

IBE刻蚀特点
方向性好,各向异性,陡直度高 分辨率高,可达到0.01μm 不受刻蚀材料限制(金属or化合物,无机物or
有机物,绝缘体or半导体均可) 刻蚀过程中可改变离子束入射角θ来控制图形 轮廓 加工过程中,损伤比较严重 加工精度不容易控制
离子束刻蚀速率影响因素
A.被刻蚀材料种类 B.离子能量 C .离子束流密度 D.离子束入射角度
一个RIE的工艺包括以下六个步骤: 分离:气体由等离子体分离为可化学反应的元素; 扩散:这些元素扩散并吸附到硅片表面; 表面扩散:到达表面后,四处移动; 反应:与硅片表面的膜发生反应; 解吸:反应的生成物解吸,离开硅片表面; 排放:排放出反应腔。
RIE的优点: A.可以容易地开始和结束, B.对硅片上温度的微小变化不是那么敏感 C.等离子体刻蚀有很高的各向异性
IBE相关刻蚀数据
离子能量:350eV
离子能量:300eV
由于IBE刻蚀对材料无选择性,对于那 些无法或者难以通过化学研磨、电介研磨 难以减薄的材料,可以的通过IBE来进行减 薄。另外,由于离子束能逐层剥离原子层, 所以具有的微分析样品能力,并且可以用 来进行精密加工。
反应离子束刻蚀(RIBE)
例如在刻铝过程中发生如下反应: 2Al+3Cl2→2AlCl3 Cl2在刻蚀开始时较多,在刻蚀过程中因 与铝反应而减少,在刻蚀结束时又增加,因 此监控, Cl2的变化,就有如图4 的记录。如 果监控反应生成物AlCl3就得到如图5所示曲 线,因为在刻蚀开始时没有AlCl3,在刻蚀过 程中产生,刻蚀终点时又消失。
/ 2nT
为激光波长,n为被刻蚀层的折射率,
T为一个周期
光学发射光谱法是通过检测刻蚀过程 中刻蚀剂物质或刻蚀生成物质的发射光谱 强度的相对变化来判断刻蚀终点。 在等离子体中,电子被激发到较高的 能量状态,当电子回落到原来状态时就会 发出光,并且每一种原子、分子、离子或 原子团具有唯一属于它们自己的光波长。 我们要把需要的光送到光电二极管,把光 信号转变成电信号,信号强度的变化就反 映了相应该波长的物质相对变化。
- 1、下载文档前请自行甄别文档内容的完整性,平台不提供额外的编辑、内容补充、找答案等附加服务。
- 2、"仅部分预览"的文档,不可在线预览部分如存在完整性等问题,可反馈申请退款(可完整预览的文档不适用该条件!)。
- 3、如文档侵犯您的权益,请联系客服反馈,我们会尽快为您处理(人工客服工作时间:9:00-18:30)。
第7章:图形刻蚀技术(Chapter 11)•问题:-常见的刻蚀对象:SiO 2> Si 3N 4> Poly-Si>磷 硅玻璃、铝或铝合金、衬底材料等-即:金属刻蚀、介质刻蚀、硅(半导体)刻 蚀Photoresist Photoresistmask maskFilm ProtectedfilmPhotoresistmask to be etchedFilm to beetched (b) Substrate after etch(a) Photoresist-patterned substrateResistLayer to be etched SubsUateReactive Ion plasma sictiing (RlE)图4-21不同腐蚀工艺的结果:〈左面}湿法腐蚀(髙各向同性〉、 C 中间)干法刻曲方向性}和佑恥干法刻述(爲方向性)I high pressure \^low pressureWet etchingAisohrpic(dq^endungcnequipTErt &ponjnrlers) T^perfEteh SdeMallHxtile WtEtdiIsctn ic(c^endh^cnequipTErt &pEranrters)SliccnTtendiEtch Bias、Undercut、Slope and OveretchW b| H一Wa—丨f ◄—Bias;Resist :FilmSubstrateUndercutMaskChrome<-Lithographybias ArrayFigure 11.1 Typical isotropic etch process showing the etchbias.选择比:sE尸被刻蚀材料的刻蚀速率E产掩蔽层材料的刻蚀速率E rE rNitride•对刻蚀的基本要求:-图形的咼保真:横向腐蚀和各向异性腐蚀-刻蚀剖面:-选择比:光刻胶和不同材料的腐蚀速度-关键尺寸(CD)控制-均匀性:小线条和大硅片-清洁:残渣沾污-损伤:• 7.1.湿法腐蚀:即,化学腐蚀(S11.1) -8.1.1腐蚀液:-SiO2:HF:NH4F:H2O=3毫升:6克:10毫升(36° C)-Al:H2PO4> 70-80 ° C、乙醇稀释-Si3N4:H2PO4>H2PO4: HNO3=3: 1 ( SiC>2膜) HF (Cr膜)-其它定向腐蚀(P265~263)etching in KOH, isopropyl alcohol, and water. The upper photo shows a 50-mm-deep etch. The lower photographs are of 80-mm-deep trenches etched at 10 mm pitch on (110) and 107 off (110) (ctfter Bean, ©1978 IEEE).盒-7.1.2刻蚀中的质量问题:-图形畸变:曝光时间、显影时间、刻蚀速度-浮胶:粘附、前烘时间、曝光时间、显影时间、刻蚀速度、腐蚀液-毛刺和钻蚀:清洁、显影时间、腐蚀液-针孔:膜厚不足、曝光不足、清洁、掩膜版-小岛:曝光、清洁、湿法显影、掩膜版-湿法腐蚀工艺的特点:速度快,成本底,精度不高。
•7.2.干法腐蚀:即,等离子刻蚀• Section 11.3 (重点阅读)-7.2.1.原理和特点:-是一种物理-化学刻蚀;-是一种选择性很强的刻蚀-在低压中进行,污染小-与去胶工艺同时进行-表面损伤置入等离子场中的分子因等离子能量的激励生成了性的游离基分子、原子,以这些活性游离基分子、原子引起的化学反应,形成挥发性产物,而使被蚀物剥离去掉。
活性游离基分子、原子不受电场影响,因而各向同性。
Reactive High ion density etching plasma Plasma etching l I IPressure (torr)Figure 11.2 Types of etch processes on a chamber pressure scale.I101 io-1 10-3 10-5 w Ion milling 才装置:<JTi_L M *曲予区腑L 蠶内閒 siProcess gases-F基刻蚀原理:(Si。
?为例)CF4 -等离子激发.A 2F+CF2 (游离基)• SiO2+4F-SiF4+2O• SiO2+2CF2>SiF4+2COCl基…Figure 11.8 Proposed mechanism of plasma etching of siliconin CF#・ A l - to 5-a(om-lhick SiF v layer forms on the surface ・ A silicon atom on the upper level is bonded to two fluorine atoms. An additional flu or inc atom may remove the silicon as SiF 2. Much more likely, however, is that additional (III) fluorine atoms bond to the silicon atom until SiF 4 forms anddesorbs (after Manos and Flanun, reprinted by permission, Academic Press)./Sl \\ / 1/ /Sl \/Sl \(II)◎RF generator:1) Etchant gases: enter chamber (Gas deliver Electric fieldEtch process chamberExhaustIsotropic etchSubstrate唸么么么么么么么么么么么么么么么么么么么么7) Desorption ofby-productsBy-productso2) Dissociation ofreactants byelectric fields4) Reactive +ionsbombard surfaceAnisotropicetch九oo3) Recombination ofO electrons with atoms.creates plasma5) Adsorption of 6) Surface reactions of reactiveions radicals and surface filon surface8) By-productremovalCD-氧的作用:加快-氢的作用:减慢-高分子生成:刻蚀速度、选择性-反应气体:CF4> CHF3、CF6SOLID ETCH GAS ETCH PRODUCT Si. SiO2a Si3N4CF中SF6, NF3SiF4Si 0*12, CCIgF? SiCI2r SiCI4Al BGig. CCI4, SiCI4, ci2AICI31 AI2CI6 Organic Solids °2 co, co2l H£O°2 + CF4 C0P C02, HF Refractory Metals {W, Ta, Mo...)See Table 11.3120Figure 11.11 Etch rate of Si and SiO 2 in (A) CF 4/O 2 plasma (after Mogab et al.9 reprinted by permission, AIP)、and (B) CF 4/H 2 plasma (after Ephrath and Petrillo, reprinted by permission of the publisher, The Electrochemical Society Inc.).10080Resist (PMMA 2041)604020Pressure - 25 mTorrFlow rate - 40 ccm150 (B)10 20 30 40 Percent hydrogen (CF 4 + H 2 mixture)InGaAs刻蚀仿真刻蚀前结构PIN结构。
10um厚的本征InP衬底,在衬底上生长3urri厚的掺杂Si浓度为2X 1018的InP层(N+),然后再淀积厚的Si掺杂4X1016的n_,lnGaAs, InGaAs中In的组分为0.53。
上层淀积lum厚的InP,掺杂为2X IO18 (P+) o刻蚀阻挡层采用Si3N4,厚度lumo等离子体刻蚀中可以改变的参数及默认值各参数的意义:[PRESSURE=<n>] #定义等离子体刻蚀机反应腔的压强[TGAS=<n>] #定义等离子体刻蚀机反应腔中气体的温度[TION=<n>] #定义等离子体刻蚀机反应腔中离子的温度[VPDC=<n>] #等离子体外壳的DC偏压[VPAC=<n>] #等离子外壳和电珠之间的AC电压[LSHDC=<n>] #外壳的平均厚度[LSHAC=<n>] #外壳厚度的AC组成[FREQ=<n>] # AC电流的频率[NPARTICLES=<n>] #用蒙托卡诺计算来自等离子体的离子流的颗粒数[MGAS=<n>] #气体原子的原子质量[MION=<n>] #等离子体离子的原子量[(CHILD 丄ANGM|COLLISION|LINEAR|CO NSTANT)] #计算等离子体外壳的电压降的模型,默认为CONSTANT[MAX.IONFLUX=<n>] [IONFLUX.THR=vn>][K.l=<n>] #定义等离子体刻蚀速率的线性系数[K.F] #定义化学流相关的等离子刻蚀速率[K.D] #定义淀积流量相关的等离子体刻蚀速率刻蚀腔压强越大,刻蚀速率变小.刻蚀效果也变差。
这从离子的能量一角度分布中也可以得出结论 SU O L S 改变刻蚀腔压强 ATHENA WERLAY AlltNAff\tRlAY Dala from multiple files Data from multiple files MierGCiS 妇旳 &_p RORJU3 旳 U_p _ph5niw_p ir»j««6^_pherTi6i_p mgoaa _phsma_p 1.£tf 37S 511 lO<str 50如 100 sir 8410HicrorfS改变气体温度ATHEf^A OVERLAYData from multiple 1iles-10 — •8-6 ・2 n0aFt5_ptosme*Jg95j2CO.5lf in 护8_ptairiiaJ93a_3CO alt 「旷25』忖巧.d 〔0 5lr 10 14 16 Microns刻蚀腔中气体的温度高时刻蚀剖面要好,但影响较小改变离子温度离子温度低时刻蚀效果要好,AWENA OVERLAYDala from muliiple filesSUOP5“ --------- X in0&38_pisce»ri6(Jion_etO.2trin0a38_K<&eiriGi_t>oajcO3<trX x in 阿2占他命in 的”屮时。