铸造浇注系统设计
铸造浇注系统设计讲解

1)、入口处的连接 (与浇口
杯连接处)
采用圆角,一般要求入 口处圆角半径r≥d/4(d为 直浇道上口直径)。
这样可以减少气体的卷 入和避免尖角型砂被冲掉引 起冲砂缺陷。
2).直浇道的形状
• 直浇道的形状—上大下小的锥形即设计锥度 上大下小的锥形,
生产中减轻水平旋涡的措施
a 用大深度浇口杯 b 浇口杯底部安放筛网等
c 在浇口杯底部设置堤坝,形成垂直旋涡。
垂直旋涡的挡渣作用: 金属液沿斜壁流下, 由于流速的减低和流 向的改变,形成垂直 方向的旋流。
a)合理
b)不合理
• 在池形浇口杯中增设隔板和在浇口杯出口处又有 底坎,就能把浇包落入浇口杯中流股的紊乱搅拌
④ 缩短直-横浇道拐弯处的湍流区。
直浇道窝的作用
⑤ 浮出金属液中的气泡:最初注入型内的最初金 属液中,常带有一定量的气体,在直浇道窝内 可以浮出去。
直浇道窝结构设计
直浇道窝的直径应为直浇道下端直径的1.4-2倍,高度为横 浇道直径的2倍,直浇道与横浇道的连接也应做成圆角。
直浇道窝常做成半球形、圆锥台等形状。
主要作用是捕集、保留由渣关口。
要求横浇道平稳、缓慢地输送金属液,而低速流动又可减少充 填时对型腔时的冲击,利于渣粒在横浇道中上浮并滞留在其顶 部而不进入型腔。
1、横浇道中的液流分配
• 金属液从直浇道进入横浇道初期,以较大速度沿 长度方向向前运动,等到达横浇道末端冲击该处 型壁后,金属液的动能转变为势能,横浇道末端 附近液面升高,形成金属浪,并开始返回移动, 使横浇道内液面向直浇道方面逐渐升高,直到全 部充满。
• 计算浇注时间和浇注系统中的最小断面积,确定直 浇道的高度(如有浇口杯则从杯中液面高度算起)
第三章 浇注系统的设计与计算
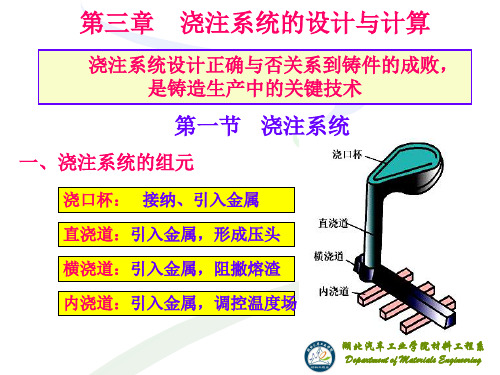
湖北汽车工业学院材料工程系 Department of Materials Engineering
复习题
1.浇注系统由哪些部分组成?分别说明各个组元的 作用? 2.比较顶注式和底注式浇注系统的优缺点。 3.比较封闭式和开放式浇注系统的优缺点。
4 . 如何提高横浇道的撇渣效果?
5. 内浇道在铸件浇铸中能够起到哪些重要作用? 6.确定内浇道位置要注意哪些具体问题? 湖北汽车工业学院材料工程系
配套措施:
1)浇口杯应足够大; 2)严格控制浇注时间。
湖北汽车工业学院材料工程系 Department of Materials Engineering
计算实例:
1、绘制模板布置简图
各层铸件内浇道的金属压力头: h1=100mm; h2=250mm; h3=350mm。
2、计算型内金属质量 m /kg
阶梯式的优缺点
兼有底注式和顶注式 的优点,充型平稳。 但结构复杂,设计和 计算较难。 用于高度大的中、大 型铸件。阶梯式或缝 隙式用于垂直分型无 箱挤压造型或金属型 铸造
湖北汽车工业学院材料工程系 Department of Materials Engineering
(二)按浇注系统各组元截面积的比例关系分
4、 选用浇口杯 根据铸型的浇注速度,使用4号浇口杯,铁液积存5.5 kg; 5、分别计算或由内浇道计算诺谟图查各层内浇道截面积: (流量系数取 μ=0.5) S1=70mm2 ; S2=45mm; S3=38mm2。 6、分直浇道截面积 ∑S内 =2×(70+45+38)=306mm2, S分直=1.2×S内=306×1.2=367mm2 分直浇道的截面尺寸: 上底宽11mm;下底宽22mm;高22mm 。 实际:S分直=363mm2。 7、 水平横浇道尺寸 S横=1.3×363 mm2=472 mm2。 选上底宽12.5mm;下底宽25mm;高25mm; 实际截面积469mm2。
精选铸造工艺学浇口设计
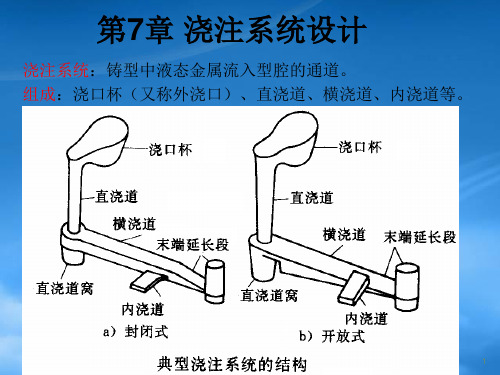
(1) 横浇道应呈充满状态:内浇道的截面、位置; (2) 流速应尽量低;
(3)横浇道与内浇道的位置关系要正确; a 内浇道距离直浇道应足够远,使渣团能上浮到吸动区上部。 b 有正确的横浇道末端延长段,以容纳初流金属液;吸收液流
动能使金属液平稳;防止液流折返。
27
c 封闭式浇注系统的内浇道应 位于横浇道的下部,且和横 浇道具有同一底面;开放式 浇注系统的内浇道应重叠在 横浇道之上,且搭接面积要 小,但大于内浇道横截面积 。
第7章 浇注系统设计
浇注系统:铸型中液态金属流入型腔的通道。 组成:浇口杯(又称外浇口)、直浇道、横浇道、内浇道等。
1
浇注基本要求: (1)内浇道设置符合铸件凝固原则和补缩方法; (2)在规定的浇注时间内充满型腔; (3)提供必要的充型压头,保证铸件轮廓、棱角清晰; (4)使金属液流动平稳,防止紊流、卷气、金属氧化; (5)具有良好的阻渣能力; (6)金属液进入时速度不可过高,避免飞溅、冲刷; (7)保证金属液面有足够的上升速度,避免夹砂结疤、浇
P = Pα+ρg·h (2)伯努利(E.Bernoulli)方程(能量守衡定律)
在封闭系统中移动的流体由三种不同的能量组成: 位能:用位于距离基准面以上h处的单位体积的流体来表
示(基准面位置任选)。EP=h(m)
压能:作用在单位体积流体上的压力来表示。
EP=p/ρ(m) p 质量压力(kg/m2)
ρ金属密度(kg/m3)
动能:用单位体积的流体以速度v移动时的动量来表示。
EK=v2/2g
定理:在一封闭系统中,单位质量流体所携带的总能量是
不变的,但其位能、压能、动能可以互换。
h1+p1/γ+V12/2g=h2+p2/γ+v22/2g 伯努利方程 (3)托里拆利(Torricelli)定理
第八章 浇注系统设计

Fmin
G 0.0443 H P
用上式计算浇注系统最小截面积时需仔细确定式中各因素的数值。
在计算的铸件确定以后,即已确定。铸件图上一般已标出了铸 件的重量(未标时根据铸件图可估算出铸件重量),再加上浇注系 统和冒口的重量即为G值。
影响µ值的因素很多,难于用数学计算方法确定,一般都按生产 经验和参考实验结果选定。对于航空铝、镁合金铸件所用的扩张式浇 注系统,其µ值可在0.3~0.7之间选取。实际铸造时可根据铸件合金种 类、浇注温度和铸件结构选择。
(1) 应在一定的浇注时间内,保证充满铸型 (2) 应能控制液体金属流入型腔的速度和方向 (3) 应能把混入金属液中的熔渣和气体挡在浇注系统里 (4) 应能控制铸件凝固时的温度分布
(5) 浇注系统结构应力求简单,简化造型,减少清理工作量和 液体金属的消耗。
(1)承接来自浇包的金属液,防止金属液飞溅和溢出,便于浇注;
H
p
P2 H 2C
用上式计算平均静压头有下列三种情况 (1) 采用底注式浇注系统时,因为P=C(图中(a)),所以有: HP=H-C/2 (2) 采用顶注式浇注系统时(图中(b)),因为P=0,所以有: HP=H (3) 采用中注式浇注系统时(图中(c)),HP可用上面的HM的计 算公式来计算。 HP=H-C/8
内浇道流量不均匀现象对铸件质量有显著影响: ① 对大型复杂铸件和薄壁铸件易出现浇不足和冷隔缺陷
② 在流量大的内浇道附近会引起局部过热、破坏原来所 预计的铸件凝固次序,使铸件产生氧化、缩松、缩孔
和裂纹等缺陷。பைடு நூலகம்
为了克服内浇道流量不均匀带来的弊病,通常采用如下方法
(1)尽可能将内浇道设置在横浇道的对称位置; (2)将横浇道断面设计成顺着液流方向逐渐缩小形式; (3)采用不同断面内浇道,缩小远离直浇道的内浇道断两积; (4)设置浇口窝等。
消失模铸造浇注系统设计

消失模铸造浇注系统设计浇注系统和浇注是获得高质量铸件的重要工序,浇注系统很关键,要经过反复试验,浇注系统可以用泡沫塑料板材来制造,但浇注系统最好是发泡成型,如果可能与模型成为一体,只有这样才能减少飞边,因为薄而复杂的浇注系统在操作过程中很容易损坏,所以使浇注系统简化很重要;浇注系统和浇注操作的目的是减少浇注时产生紊流的倾向,减轻金属液的氧化,防止产生冷隔、皱皮等缺陷,应用成功的浇口设计有很多类型,如顶注、底注、雨淋式浇注,压边浇口、牛浇口等;金属液的充型速度必频与模型热解的速度相同,浇注速度慢或出现断流的现象,都会引起严重的塌箱,金属液量一定要充分,以保持一定的金属静压头防止金属液前沿与熔融模型之间的空隙处发生他乡;铁或铝和氧的亲和性、铁或铝的吸气性以及模型结构对控制浇注的成功至关重要;浇注时泡沫塑料模型要发生一些列的变化,包括熔融、解聚、热解、聚合物裂解等,模型的热解产物会引起很多铸造缺陷,如铝合金中的气孔、缩松,铸件中的碳缺陷,以及铸钢件中的增碳等;金属液充型过程中,模型在约75℃时开始软化,164℃时溶熔,316℃时开始解聚,在580℃时开始分解,设计浇注系统和浇注过程中,要防止气体、干砂、模型的热解残留物卷入金属液中,减少模型热解残留物取决于浇注系统的设计、浇注速度、模型的几何形状尤其是模型的表面和体积之比、涂料、砂箱的排气、真空的使用、模型的密度及种类等;浇注系统的主要作用是用金属液充填型腔,同时必须不对铸型和金属两者产生部可接受的损坏,浇注系统能够在型内建立温度梯度、提供补给金属,以促进健全的铸件,浇注过程中,浇注系统内的金属流不仅要支撑铸型,还要通过浇注系统排除模型的热解产物,在涂料和干砂的充填、紧实的过程中,浇注系统还可用以支撑和搬运,浇注系统还要有一定的强度,便于操作并使模型某些部位可能加固,防止变形;浇注出铸件后,必须去掉浇注系统;浇注系统应该与铸件部重要的部位相连并且面积应尽量减小,一般情况下,面积越小,可增加浇注系统装配模型数量;消失模铸造工艺中多使用较大的浇口杯防止浇注过程中出现断流,能够快速而稳定地浇注,保持液态金属的静压头,浇口杯多采用合粘结剂的型砂制造;生产铸件时常用过滤网,它有助于防止浇注时直浇道的损坏,金属液的静压头必须超过金属与模型界面的压力,否则就会发生反喷,金属液压头越高,通常导致铸件的质量越好,铝合金铸件中采用中空直浇道和其它组元,有助于铝液的充型;1、消失模铸造浇注位置的确定确定浇注位置应考虑以下原则①尽量立浇、斜浇,避免大平面向上浇注,以保证金属有一定上1速度;②浇注位置应使金属与模型热解速度相同,防止浇注速度慢或出现断流现象,而引起塌箱、对流缺陷;③模型在砂箱中的位置应有利于干砂充填,尽量避免水平面和水平向下的盲孔;重要加工面处在下面或侧面,顶面最好是非加工面;⑤浇注位置还应有利于多层铸件的排列,在涂料和干砂充填紧实怕过程方便支撑和搬运,使模型某些部位可能加固,防止变形;2、消失模铸造浇注方式的确定浇注系统按金属液引入型腔的位置分为顶注、侧注、底注或几种方式综合使用;所有这些方法都能够生产出合格的铸件,顶注时充型所需的时间最短,因此需要浇注速度最快,以防止塌箱;侧注充型速度最慢,而底注介于两者之间,因为铝合金浇注时模型分解的速度很慢,型腔保持充满可避免塌箱,因此多采用顶注,但是这样难以控制金属液流,容易卷入热解残留物; 顶注系统:顶注充型所需时间最短,浇注快有利于防止塌箱;温度降低少,有利于防止浇不足和冷隔缺陷;工艺出品率高,顺序凝固补缩效果好,可以消除我铸铁件碳缺陷,因难控制金属液流,容易使EPS热解残留物卷入,增碳倾向降低;由于铝合金浇注时模型分解速度慢,型腔保持充满,可避免塌箱,一般薄壁件多采用顶注;侧浇注系统:液体金属从模型中间引入,一般在铸件最大投影面积部位引入,可缩短内浇道的距离;生产铸件的采用顶注和侧注,铸件上表面出现碳缺陷的机率低;但卷入铸件内部碳缺陷常常出现;底浇注系统:从底部模型引入金属液,上升平稳,充型速度慢,铸件上表面容易出现碳缺陷,尤其厚大件更为严重;因此应将厚大平面置于垂直方向而非水平方向;底注工艺最有利于金属充型,金属液前沿的分解产物在界面空隙中排出的同时,又能够支撑干砂型壁;一般厚大件应采取底注方式;阶梯式浇注系统:分两层或多层引入金属时采用中空直浇道,大部分金属从最上层内浇道引入金属,多层内浇道作用减弱;阶梯浇道引入容易引起冷隔缺陷;一般在高大铸件时采用;上述浇注方式在一定条件下能生产出合格的铸件;浇道比例和引入位置,采用的浇注系统原则①引入液体金属流,应使充型过程连续不断供应金属不断流,液体金属必须支撑干砂型壁,采用封闭式浇注系统最为有利;即内浇道断面最小;如内浇道:直浇道=1:1. 2-1. 4;②浇注系统的形式与传统工艺不同,不考虑复杂结构形式如常用的离心式、阻流式、牛角式等,尽量减少浇注系统组成,常没有横浇道只有直浇道和内浇道以缩短金属流动的距离;形状简单,方形长方形为主;③直浇道与铸件间距离即内浇道长度应保证充型过程不因温度升高而使模型变形;金属压头,应超过金属EPS界面气体压力,以防呛火;呛火是液体金属从直浇道反喷出来,中空直浇道和底注有利于避免反喷,同样适用于铸铝件;对EPS/EPMkIA共聚树脂模型更为突出,高的直浇道压头高容易导致良好的铸件质量和浇注时的安全;生产铸件时,采用顶注和侧注,铸件表面出现碳缺陷,但是由于卷入模型残留物,铸件的内部常常出现碳缺陷;底注能够减少内部的碳缺陷,但是在铸件的上表面容易出现碳缺陷,尤其是在厚大铸件的上表面,目此多将厚大平面置于垂直的而不是水平的方向;厚度介于3. 2-6. 4mm的铸件一般不会出现什么问题,但是对于壁厚较大的铸件,需要更多的内浇道隐入、更低的模型密度、代用模型材料、采用不同的涂料配方、抽真空浇注或其它的调整,以减少碳缺陷;3、内浇道尺寸大小的设计计算首先确定内浇道最小断面尺寸,再按一定比例确定在直浇道和横浇道;计算方法有2种:经验法:以传统砂型工艺为参考查表或经验公式计算后,适当调整,一般增大15%-20%即可;理论计算方法:如水力学计算公式,以球铁包括灰铁为例G:流经内浇道的液态重量kg铸造重+浇注系统重u:流量系数,可参考传统工艺查表,一般可按阻力偏小来取;如Hp:压头高度,根据模型在砂箱中位置确定;t:关键是浇注时间的选择,快速浇注是EPC工艺最大特点;按下式决定t:k1中小件用公式k1是修正系数,有负压时; K1取<1-般为左右;T=k1计算结果是一个参考值,通过浇注试验调整,有确切把握后可和模型联在一起发泡成型是有利的;4、消失模铸造浇注工艺浇注铝合金铸件时由于模型分解速度不快,浇注速度与铸铁件生产相比要低一些,因此,需要较大的内浇道和直浇道,生产铝合金件时的冷隔和皱皮缺陷是由于铝合金液中卷入了模型的热解残留物以及当今束流相遇是铝液的热量不足以充分熔融这些残留物的综合结果所致;底注工艺最有利于金属液充型,金属液以受控最好的方式在直浇道中下降,然后在铸型型腔内有规律地上,金属液前沿使分解产物在金属液与模型的界面空隙中逸出的同时,又能够支撑干砂型壁;一个浇注系统上能够组装多层模型,在浇注结束前金属液的静压头降低和流动的速度减小的情况下,一定要使每个铸型都充满,模型之间不要靠得太近,否则会使型内气压升高,浇注铸铁和铸钢件时,模型的热解的过程中产生大量高温气体,如果这些气体聚集在相邻两个模型间的区域内,模型会受到损坏,使干砂流入型腔内,产生严重的缺陷;如果把这些高温气体从型内排出,则可以解决这些问题;浇注时也可采用抽真空,抽真空能够排出砂箱内的气体,提高铸件表面的光洁度,阻止干砂流态化,改善薄壁铸件的充型性能,抽真空还能够排出浇注时产生的其它产物,真空系统中收集过多的这类产物会发生批爆炸,所以要求真空系统至少能够承受住1MPa的峰值压力;浇注温度的确定:由于模型气化是吸热反应,需要消耗液体金属的热量,浇注温度应高一些,虽然负压下浇注,充型能力大为提高,但从顺利排除EPS固、液相产物也要求温度高一些,特别是球铁件为减少残碳、皱皮等缺陷,温度偏高些对质量有利;一般推荐EPC工艺浇温比砂型高30-50℃,对铸铁件而言,最后浇注的铸件应高于136 0℃表1推荐的浇注温度范围:表l采用消失模铸造工艺时合金浇注温度负压的范围和时间的确定负压的作用:1 紧实干砂,防止冲砂和崩散、型壁移动尤其球铁更为重要;2 加快排气速度和排气量,降低界面气压,加快金属前沿推进速度提高充型能力,有利于减少铸件表面缺陷;3 提高复印性,铸件轮廓更清晰;4 密封下浇注,改善环境;负压大小范围:1根据合金种类,选定负压范围,见表2;表2 负压范围铸件凝固,形成外壳足以保持铸件时即可停止抽气,一般5min左右根据壁厚定为加快凝固冷却速度也可延长负压作用时间;铸件较小负压可选低些,重量大或一箱多铸可选高一些,顶注可选高一些,壁厚或瞬时发气量大也可选略高一些;浇注过程中,负压会发生变化,开始浇注后负压降低,达到最低值后,又开始回升,最后恢复到初始值,浇注过程负压下降最低点不应低于铸铁件l00-200mmHg,生产上最好控制在200mmHg以上,不允许出现正压状态,可通过阀门调节负压,保持在最低限以上;为避免浇注时喷灯效应,不应采用名冒口,而且直浇道是砂箱表面上唯一敞开处,仔细设计浇注系统,要力争减少型内不同方向的金属液的对流,在金属液流的前沿,常有一些模型热解残留物,在两股金属液对流时在交界面处会卷入这些残留物,因此,铸件截面尺寸的突然变化的部位也有类似的问题,设计浇注系统时,一定要懂得在金属液前沿积累的热解残留物一定要力争排除或减少;浇注操作EPC工艺中浇注时多使用较大的浇口杯防止浇注过程中出现断流而使铸型崩散,达到快速稳定浇注并保持静压头;浇口杯多采用砂型制造,生产铸件还常采用过滤网;它有助于防止浇注道的损坏并起滤渣的作用;消失模铸件在模型后退允许情况下,一般应尽快浇注;采用自动浇注机有利于稳定浇注速度,并能够在浇注时快速调整;而手工浇注不便控制,废品率比自动浇注时的要高一些;几种新的自动浇注方法已得到生产应用;如才用加压方法从铸件底部充型;采用真空技术将金属液吸入铸件中,其前景很好;。
[精彩]第三章 浇注系统的设计与计算
![[精彩]第三章 浇注系统的设计与计算](https://img.taocdn.com/s3/m/2c43a13b10a6f524ccbf85c8.png)
Department of Materials Engineering
计算
1、 奥赞(Osann)公式 —阻流(最小)截面积的计算 。 阻流(最小)组元指浇注系统中最小截 面积的浇道,一般为内浇道,即
m A阻= 2 gHp
H P H0 P
2
2C
湖北汽车工业学院材料工程系 Department of Materials Engineering
轻合金浇注系统中安装过滤网
湖北汽车工业学院材料工程系 Department of Materials Engineering
4、内浇道的设计
1) 内浇道的作用: 控制液态金属充型速度和流动方向、温度分布和凝固顺序。 2) 形状:扁平梯形、月牙形和三角形。 3) 位置的选择: 依据铸件所需凝固方式和流动特性考虑。 同时凝固: 对于壁厚均匀的铸件,拟采用多个内浇道分散引入; 对于不均匀的铸件,则从薄壁处引入。 顺序凝固: 从厚壁处引入金属液。
湖北汽车工业学院材料工程系 Department of Materials Engineering
5、确定内浇道位置的几个具体问题
结构复杂的铸件,壁厚差别大的补缩区域则按顺 序凝固从厚处引入;整个铸件按同时凝固方式采 用多个内浇道充型。 要求各内浇道的流量分布合理。 液流顺壁流入,不冲刷 型壁、型芯和铸型凸出部分。 避开铸件重要部位, 防止晶粒粗大。 造型、清理操作方便, 不阻碍铸件收缩。 湖北汽车工业学院材料工程系
(二)按浇注系统各组元截面积的比例关系分
1、封闭式浇注系统
∑A内< ∑A横<A直
一般为 ∑A内:∑A横:A直=1:1.1:1.15
特点:
挡渣力强,金属消耗少,易清理;
熔模铸造浇注系统计算
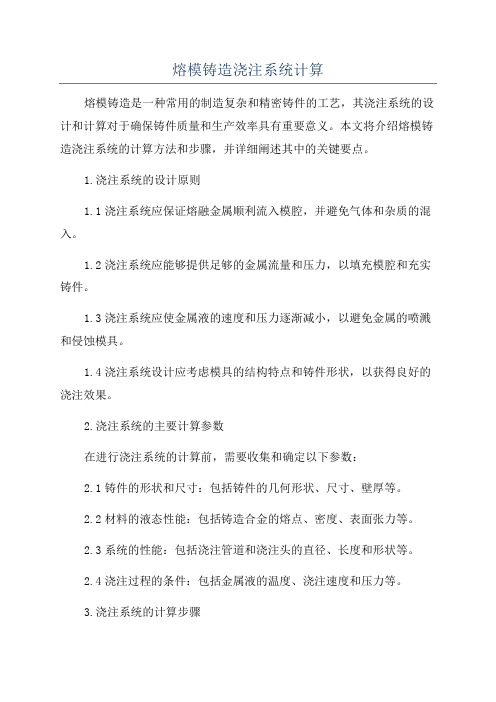
熔模铸造浇注系统计算熔模铸造是一种常用的制造复杂和精密铸件的工艺,其浇注系统的设计和计算对于确保铸件质量和生产效率具有重要意义。
本文将介绍熔模铸造浇注系统的计算方法和步骤,并详细阐述其中的关键要点。
1.浇注系统的设计原则1.1浇注系统应保证熔融金属顺利流入模腔,并避免气体和杂质的混入。
1.2浇注系统应能够提供足够的金属流量和压力,以填充模腔和充实铸件。
1.3浇注系统应使金属液的速度和压力逐渐减小,以避免金属的喷溅和侵蚀模具。
1.4浇注系统设计应考虑模具的结构特点和铸件形状,以获得良好的浇注效果。
2.浇注系统的主要计算参数在进行浇注系统的计算前,需要收集和确定以下参数:2.1铸件的形状和尺寸:包括铸件的几何形状、尺寸、壁厚等。
2.2材料的液态性能:包括铸造合金的熔点、密度、表面张力等。
2.3系统的性能:包括浇注管道和浇注头的直径、长度和形状等。
2.4浇注过程的条件:包括金属液的温度、浇注速度和压力等。
3.浇注系统的计算步骤根据以上参数和原则,进行浇注系统的计算,一般可分为以下几个步骤:3.1确定浇注管道和浇注头的几何参数:根据铸件的形状和尺寸,确定浇注管道和浇注头的直径、长度和形状。
通常,浇注管道和浇注头的直径会逐渐减小,以保证金属液的速度和压力逐渐降低。
3.2计算浇注头的流速和压力:根据材料的液态性能和浇注过程的条件,计算金属液在浇注头中的流速和压力。
这一步需要考虑金属液的粘度、密度以及浇注头的形状、长度等参数。
3.3计算浇注管道和浇注头的阻力:根据浇注管道和浇注头的形状和尺寸,计算流动的阻力。
这一步需要考虑流动的雷诺数、曼宁系数和摩擦因数等参数。
3.4确定浇注时间和浇注压力:根据铸件的尺寸和形状,计算金属液的流速和浇注时间,进而确定浇注压力。
通常,浇注时间应保证金属液充分填充模腔,并保持一定的冲刷效果。
4.浇注系统的优化完成上述计算后,可以进行浇注系统的优化,包括以下几个方面:4.1浇注管道的优化:可以通过改变浇注管道的形状和尺寸,减小阻力和压力损失,提高浇注效率。
铸造浇注系统设计-课件(1)
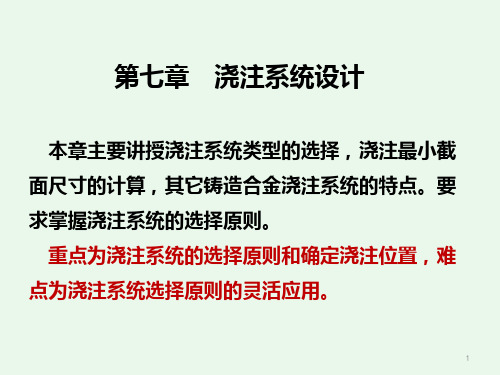
池盆形浇口杯
特点:挡渣作用明显,但是制作程序复杂,消耗 的金属较多 应用:主要用于中大型铸铁件。 结构:浇口盆 的深度应该大 于直浇道上端 直径的5倍。
12
浇口杯中应避免出现水平涡流
液态金属在平底的浇口杯中 流动 时易出现水平涡流。 流量分布不均匀造成流速方 向偏 斜。水平分速度对直浇 道中心线 偏斜,形成水平涡 流运动。在涡 流中心区形成 一个漏斗形充满空 气的等压 自由液面的空穴。容易 将空 气和渣子带入直浇道。
第七章 浇注系统设计
本章主要讲授浇注系统类型的选择,浇注最小截 面尺寸的计算,其它铸造合金浇注系统的特点。要 求掌握浇注系统的选择原则。
重点为浇注系统的选择原则和确定浇注位置,难 点为浇注系统选择原则的灵活应用。
1
概述
浇注系统:铸型中液态金属流入型腔的通道之总称 组成:浇口杯、直浇道、直浇道窝、横浇道、内浇道
2)采用纵向逆浇,设置底坎、挡板和闸门等; 3)采用特殊结构的浇口杯:拔塞式、浮塞式、铁隔 片式、闸门式等; 4)浇口杯与直浇道相连的边缘做成凸起状。
22
三、直浇道中的流动
直浇道的功用: 引导金属液进入横浇道、内绕道或直接导入型腔; 提供足够的压力头,使金属液克服各种流动阻力,
在规定时间内充满型腔。
型壁的多孔性、透气性和合金液的不相润湿性,给合金液的 运动以特殊边界条件
在充型过程中,合金液和铸型之间有着激烈的热作用、机 械作用和化学作用;合金液冲刷型壁,粘度增大,体积收 缩,吸收气体、使金属氧化等;
浇注过程是不稳定流动过程 ✓ 在型内合金液淹没了内浇道之后,随着合金液面上升,
充型的有效压力头渐渐变小 ✓ 型腔内气体的压力并非恒定 ✓ 浇注操作不可能保持浇口杯内液面的绝对稳定
铸造中浇注系统设计
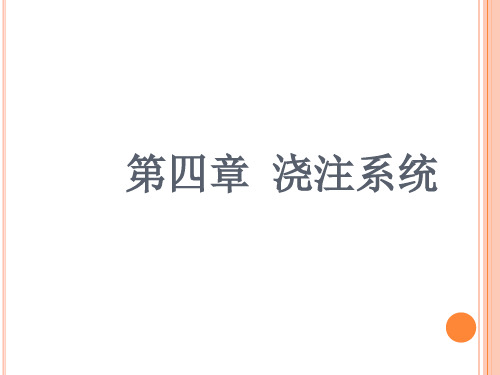
应用:
主要用于构造复杂旳多种黑色金属 铸件和易氧化旳有色金属铸件。
3、中间注入式浇注系统
对内浇道下列旳型腔部分为顶注 式;对内浇道以上旳型腔部分相 当于底注式。故它兼有顶注式和 底注式浇注系统旳优缺陷。因为 内浇道在分型面上开设,故极为 以便,广为应用。合用于高度不 大旳中档壁厚旳铸件。
轻易充斥,可降低薄壁 件浇不到、冷隔方面旳 缺陷
充型后上部温度高于底 部,有利于铸件自下而 上 旳顺序凝固和冒口旳 补缩
冒口尺寸小,节省金属
内浇道附近受热较轻
构造简朴,易于清除
缺陷:
易造成冲砂缺陷金属, 液下落过程中接触空气, 出现飞溅、氧化、 卷入 空气等现象,使充型不 平稳
易产生砂孔、铁豆、气 孔和氧化夹杂物缺陷, 大部分浇注时间,内浇 道工作在非淹没状态,
第四章 浇注系统
浇注系统旳作用:将液态金属引入铸型。
经典浇注系统旳构造 a)封闭式 b)开放式 1-浇口杯,2-直浇道,3-直浇道窝,4-横浇道,5-末端延长段,6-内浇道
对浇注系统旳基本要求
1.所拟定旳内浇道旳位置、方向和个数应符合铸件旳凝固原则或补缩 措施。
2.在要求旳浇注时间内充斥型腔。 3.提供必要旳充型压力头,确保铸件轮廓、棱角清楚。 4.使金属液流动平稳,防止严重紊流。预防卷入、吸收气体和使金属
过分氧化。 5.具有良好旳阻渣能力。 6.金属液进人型腔时线速度不可过高,防止飞溅、冲刷型壁或砂芯。 7.确保型内金属液面有足够旳上升速度,以免形成夹砂结疤、皱皮、
冷隔等缺陷。
第一节、浇注系统各单元旳作用:
1、浇口杯旳作用:①承接来自浇包旳金属液,预防金属液 飞溅和溢出,便于浇注;②减轻液流对型腔旳冲击、分离 渣滓和气泡,阻止其进入型腔;③增长充型压力头。
消失模铸造浇注系统设计

消失模铸造浇注系统设计1.选择浇注位置1)重要的加工平面应朝下或垂直放置;2)模样的大平面应垂直或倾斜放置;3)尽量将气化模截面积F与周长n之比最小的面朝上安放;4)尽量将气化模上具有开口部分(如空穴及凹槽等)朝上安放,便于填砂紧实;5)便于开设浇、冒系统和除渣排气通道;6)利于造型材料的填充,避免形成死角区;7)凝固原则,就是使截面的横截面积自下而上逐渐增大;8)浇注位置还应有利于多层铸件的排列,在涂料和干砂充填紧实的过程方便支撑和搬运,使模样某些部位加固,防止变形;9)模样在砂箱中的位置应有利于干砂充填,尽量避免水平面和水平向下的盲孔。
2.确定模样吃砂量原则:在保证铸型强度能承受住金属液冲刷和压挤力作用的前提下,吃砂量尽可能小。
表1 砂箱底部和侧面吃砂量的经验数据一箱浇注多件时,两气化模样之间的距离也可采用上述数据。
顶注的吃砂量应大些,控制在150~300mm之间。
3.选择浇注系统的形式a)顶注、 b)上注、 c)下1/3处浇注、d)阶梯浇注、 e)底注、 f)下雨淋浇注f)e)d)c)b)a)图1 浇注系统的形式对内在质量要求严格的中小件宜采用顶注,对结构复杂的大而薄的铸件宜采用底注, 下1/3处侧注及阶梯浇注系统是适用性最广、应用最多的浇注方式。
选用浇注系统时的依据: 1) 各种形式浇注系统的优缺点2) 合金本身的铸造工艺特性如流动性、易氧化性及收缩性等 3) 铸件的大小和壁厚4. 确定一箱多铸的铸件数量及模组的布置形式5. 内浇道设计(确定内浇口的截面总面积、位置和数量、内浇道的形状和尺寸)1) 内浇口截面总面积(1) 经验法 按传统砂型铸造内浇口设计,然后适当调整,一般增大15%~20%。
(2) 公式计算∑=PH t GF 31.0μ内式中:G —流经内浇道的液态金属重量(kg )(包括铸件重和浇注系统重量); μ—流量系数(可参考传统工艺查表)一般取0.3~0.4之间; P H —压头高度,根据模样在砂箱中位置确定;t —浇注时间,消失模采用快速浇注的方法,可按下式计算:对于中小型铸铁件:()G G K t t+=3对大型铸铁件:3G K t t =, t K 是修正值,一般取0.85左右。
浇注系统设计
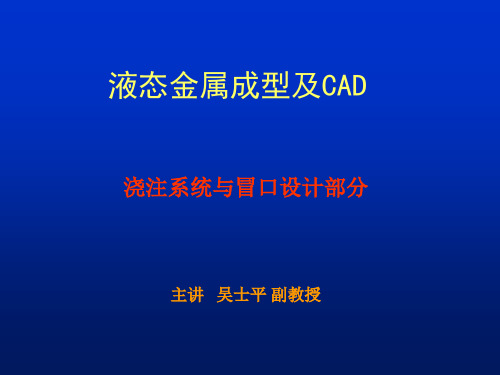
通常用最大相对流量偏差值K来评价内浇道中的 流量不均匀性。
K=(δmax-δmin)/(Qn-1) δmax—— 内浇道中最大流量 δmin—— 内浇道中最小流量 Q —— 系统中的总流量 n —— 内浇道的个数
(图3-2-29) 不同分布的内浇道中,最大流量偏 差与F损/F内的关系
由于内浇道在分型面上开设,就能方便地 按需作出布置,有利于控制金属液的流量分 布和铸型的热分布,对形状复杂的铸件十分 有利。这种浇注系统应用很普遍,适用于中 等重量、高度不大、中等壁厚的铸件。
4. 阶梯式浇注系统 金属液应该是先按底注方式又最下层内浇道引入
型腔,待金属液面接近第二层内浇道时,才有第二层 内浇道引金属液进入型腔,……如此类推,使金属液 由下面逐层按顺序充填型腔,最热的金属液经最高的 那层内浇道进入型腔顶部或顶冒口中,见图3-2-8。
应用:重量不大,不高和形状简单的薄壁或 中等壁厚的铸件。
顶注式浇注系统的其它形式: 雨淋式和压边浇口
2. 底注式浇注系统:
它是内浇道开设在型腔底侧或底下的浇 注系统。
优点:金属液充型平稳,液面逐渐升高, 可以避免冲击,飞溅和氧化及由此而形成的 铸件缺陷。型腔内气体容易逐渐排出。整个 浇注系统较快充满,有利于横浇道撇渣。
浇口杯分为漏斗形浇口杯和浇口盒
(一)、漏斗形浇口杯
漏斗形浇口杯撇渣效果差,但结构简单,节 约金属,多用于一般铸铁小件。(图3-2-10 a)
对于重要的件,常配合过滤网使用。(图3-210 b)
(二)、浇口盒
对于较大的铸件,为了能较好的初次撇渣和 控制流量以及均匀地供给金属,常采用浇口盒, 如图3-2-11 a 所示,金属也从侧面进入浇口杯时, 产生二支股流,一支股流在垂直面内运动,会耗 损能量,减小流量,但有利于渣和气泡上浮。
铸造工艺学浇注系统设计

铸造工艺学浇注系统设计一、引言铸造是制造业中非常重要的一种工艺。
在铸造的过程中,浇注系统设计是一个至关重要的环节。
浇注系统设计的好坏直接影响到铸件的质量和成本。
因此,本文将探讨铸造工艺学浇注系统设计的相关内容。
二、浇注系统的基本组成浇注系统是将熔化的金属倒入铸型中的设备。
一个完整的浇注系统通常由浇口、流道、浇道和进气系统组成。
下面将分别对这些组成部分进行介绍。
1. 浇口浇口是铸件与浇杆相连的部分。
浇口的设计要考虑到金属的流动性和气体的排出。
一般来说,浇口的形状应当为圆形或方形,尽量避免使用锥形或不规则形状的浇口。
2. 流道流道是将熔化金属从浇口引导到铸型中的管道。
流道的设计要保证金属可以顺利地流动,不产生气体团聚和金属氧化。
流道的截面积要逐渐增大,以确保金属流动的顺畅。
3. 浇道浇道是将熔化金属从炉中引导到浇口的管道。
浇道的设计要考虑金属流速和温度的均匀性。
一般来说,浇道的截面积要比流道大,以减少金属的回流和氧化。
4. 进气系统进气系统是将熔化金属中的气体排出的装置。
进气系统的设计要考虑金属的温度和粘度,保证气体可以顺利地排出,避免气泡和气孔的产生。
三、浇注系统设计要点1. 浇口位置浇口的位置要尽量选在铸件最厚部位的上方,保证金属可以顺利地充填整个铸型,并避免气体团聚。
此外,浇口的位置也要尽量避免对铸件表面造成损伤。
2. 流道和浇道设计流道和浇道的设计要满足金属流动的需要,保证金属可以顺利地流动并充填整个铸型。
流道和浇道的截面积要合理选择,使金属流速均匀,避免金属氧化和渣夹杂。
3. 进气系统设计进气系统的设计要保证气体可以顺利地排出,避免气泡和气孔的产生。
进气系统的位置要选择在最容易产生气孔的位置,如铸件表面和浇注系统连接处。
四、浇注系统设计实例分析以某种铸造工艺为例,介绍浇注系统设计的具体步骤和方法。
通过实例分析,展示浇口、流道、浇道和进气系统的设计原理和关键点。
五、结论本文从浇注系统的基本组成、设计要点以及实例分析等方面,探讨了铸造工艺学浇注系统设计的相关内容。
铸造工艺学第3章 浇注系统设计

适用于各类灰铸铁件及球铁件。
封
A杯>A直<A横<A内
阻流截面设在直浇道下端,或在横浇道中, 或在集渣包出口处,或在内浇道之前设置
闭 A杯>A直>A集渣包出 的阻流挡渣装置处。
开口
阻流截面之前封闭,其后开放,故既有利 于挡渣,又使充型平稳,兼有封闭式与开
放 A直>A阻<A横后<A 放式的优点。
式内
适用于各类铸铁件,在中小件上应用较多, 特别是在一箱多件时应用广泛。目前铸造
金属液进入横浇道后,起初以较大的速度沿着它 的长度方向往前流动,直到横浇道的末端处,并 冲击该处的型壁,使液流的动能变为位能,在横 浇道末端处附近的金属液面就升高,形成金属浪 并开始返回移动,直到退回的金属浪与从直浇道 流出的液流相遇后,横浇道中的液面将同时上升 到充满为止。
3.1.4 液态金属在横浇道中的流动情况
横浇道起挡 渣作用应 具备的条 件
横浇道必须呈充满状态
液流的流动速度宜低于渣 粒的悬浮速度 液流的紊流搅拌作用要尽 量小
应使夹杂物有足够的时间上浮到金属 液顶面,横浇道的顶面应高出内浇道 吸动区一定距离,末端应加长;
内浇道和横浇道应有正确 的相对位置。
3.1.4 液态金属在横浇道中的流动情况
提向横浇道挡渣能力的主 要途径是改变横浇道的结 构以增加流程中的阻力, 减慢金属液的流速,减少 紊流搅拌作用。常见的方 法有以下几种: 1) 缓流式浇注系统
图3-14 上台面铸件的倾斜浇注
3.3.2 浇注系统的计算
(二)阻流组元(或内浇道)截面积的计算及各组元 之间的比例关系的确定 阻流组元截面(简称阻流截面)的大小实际上反映了浇 注时间的长短。在一定的压头下阻流截面大,浇注时 间就短,所以阻流截面的大小对铸件质量的影响与浇 注时间长短的影响基本一致。生产中有各种确定阻流 截面尺寸的方法和实用的图、表,大多都是以水力学 原理为基础的,此处着重介绍水力学计算法。
浇注系统设计PPT课件

缓 冲 作 用
流 区
高 度 紊
弯 处 的
缩 短 拐
流浇改 头力局弯减 布量道善 损和部处少
分的内 失水阻的拐
•9
横浇道
主要功能:
1.稳流 2.挡渣(主要挡渣单元) 3.分配液流
结构形状:
圆形热损失最小、流动平稳,但工艺复杂; 一般采用:高/宽=1.2-1.•2
对浇注系统的基本要求
应在一定的浇注时间内,保证充满型腔。保证铸件轮 廓清晰,防止出现浇不足缺陷。
可以控制浇注速率和方向,尽可能使金属液平稳充型。 避免冲击、飞溅和漩涡发生,以免铸件产生氧化夹渣、 气孔和砂眼等缺陷。(夹渣 )
应能把混入金属液中的熔渣和气体挡在浇注系统里, 防止产生夹渣和气孔等缺陷。
•14
过滤装置
(1)过滤网(厚度为0.20.5的钢板冲制而成。
(2)过滤片(泡沫陶瓷过 滤)
(3)钢丝棉过滤(絮棉状 的细铁丝)
•15
浇注系统的类型
顶注式浇注系统 底注式浇注系统 中注式浇注系统 阶梯式浇注系统 缝隙式浇注系统
•16
备注
夹渣: 由于铸型具有一定的孔隙,金属液在充型过程中,往往 不能很好地贴附于管壁,此时可能将外界气体卷入液流, 形成气孔或引起金属液 氧化,形成氧化夹渣。
•12
内浇道流量分配
一般条件下,远离直浇道流量大。
浇不足,冷隔,过热 破坏凝固次序
氧化,缩松和裂纹
措施
尽可能将内浇道设置在横浇道的对称位置; 将横浇道断面设计成顺着液流方向逐渐缩小的形式;
设置浇口窝。
•13
内浇道的吸动作用
吸动作用越大,横浇道越难挡渣。
采用较高的横浇道和较低的内浇道
1.第一个内浇道不要离直浇道太近;最后一个内浇道 与横浇道末端要有一定的距离。 2.内浇道一般应置于横浇道的中部(中置式);轻合 金金属型铸造中,上置式的比较多用。 3.液态金属的导入位置是控制铸件凝固顺序的一个重 要措施。
第三章 浇注系统设计
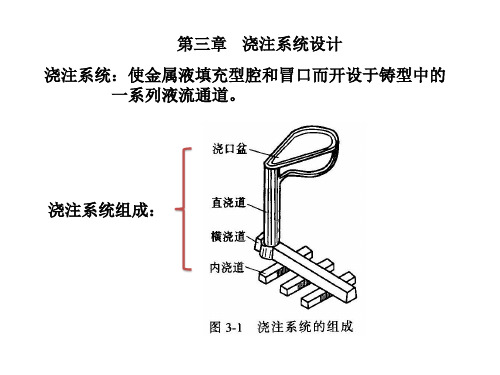
m Nnq
m —— 浇注金属质量(kg);N —— 同时浇注的浇包数; n —— 单个浇包的包孔数。
四、铸造非铁合金的浇注系统
特点:密度小、熔点低、热容量小而热导率大,且极 易氧化和液态吸气性强。 常见铸造缺陷:非金属夹杂、浇不到、冷隔、气孔、 缩孔、缩松及裂纹、变形等。
设计非铁合金浇注系统应注意: 非铁合金降温快,应快浇。 1)浇注温度不高,对 型砂的热作用较轻。
二、计算举例(浇注系统设计方法和步骤) 图3-19为灰铸铁件的垂直分型浇注系统的结构形 式,即模板布置简图。
1.绘制模板布置简图 模板布置来自于工艺设计方案和参照造型机标准模 板尺寸及合理吃砂量(图中A、B、C三个尺寸)等。据此 确定出各层铸件内浇道的金属压力头为: h1 =100mm; h2 =250mm; h3 =350mm。 2.计算型内金属质量m 每个铸件质量 2kg,共布置12件。铸件工艺出品率 (灰铁件)按70%估计,则型内金属质量(即铁液质量 数)为2×12 kg / 0.7 = 34.3 kg。
3.确定浇注时间和浇注速度q 造型机产率为300箱/h,节拍12s/型。据表3-8查出 浇注时间为8s。约用2s充满浇注系统,则充填单个型腔的 净浇注时间为6s。每个型腔的浇注速度应为2kg/6s≈0.33 kg/s。
4.选用浇口杯 根据铸型的浇注速度,参照表3-7,可查出浇口杯 尺寸。 如用手工浇注,使用4号浇口杯,铁液积存5.5kg; 如用自动浇注,使用2号浇口杯,铁液积存4kg。
A直: A横: A内=1:2:4
第二节
浇注系统组元中金属液的流动特性及组元设计
一、浇口杯(盆)
1.漏斗形浇口杯
特点:漏斗形浇口杯结构简 单,制作方便,其本身消耗 金属液少。 适用:小型铸件,在机器造 型中广泛使用。 杯底安放滤孔芯,可挡 渣并对金属液起缓冲作用。
- 1、下载文档前请自行甄别文档内容的完整性,平台不提供额外的编辑、内容补充、找答案等附加服务。
- 2、"仅部分预览"的文档,不可在线预览部分如存在完整性等问题,可反馈申请退款(可完整预览的文档不适用该条件!)。
- 3、如文档侵犯您的权益,请联系客服反馈,我们会尽快为您处理(人工客服工作时间:9:00-18:30)。
则:v2>v1, 可使P2<P1, 流体呈正压流动;
3、蛇形直浇道则使h1-2, 增 大,保 证 P2<P1 。 蛇形 直浇道时利用增加水力 损失改变直浇道压力分 布的一例,多用于有色 金属铸件和直浇道直接 接于型腔时。 4、直浇道尽量设在横、 内浇道的对称中心处, 以使金属液流程最短, 流量分布均匀。
原因:水平各向流量不均 衡造成流速方向的偏斜。
若忽略金属粘度的影响,视液态金属为理想流体, 浇口杯内液态金属应满足动量矩守衡:
Mvr=常量
式中:M 距离直浇道中心为r处的质点的质量 v M点的切线速度 r M点距离直浇道中心的距离。
漏斗形等压自由液面的形成:一旦出现水平旋涡, 越靠近中心,M质点的离心加速度越高,重力加速 度和离心加速度的合成加速度越接近于水平,根据 流体力学原理,等压面垂直于总加速度方向。等压 面逐步由水平过度到垂直,形成中空的大气压力表 面。 对铸件质量的影响:卷气、渣沿等压面进入型腔。
图 底坎和浇注方向对液流流向的影响
a) 纵向逆浇 b)纵向顺浇 c)侧向浇注
图 底坎和浇注方向对液流流向的影响 a) 纵向逆浇 b)纵向顺浇 c)侧向浇注
• 纵向顺浇方便浇注工作,不易产生垂直涡流,轻 质点夹杂物进入直浇道的可能性大;
• 纵向逆浇易形成垂直涡流,有助于夹杂物上浮。
• 侧向浇注形成垂直涡流的可能介于上述两者之间 ,液流从一侧流向直浇道,易形成水平涡流。
二、浇口杯中的流动
浇口杯分类:漏斗形浇口杯、池盆形浇口杯
漏斗形浇口杯
特点:结构简单,制作方便,容积小,消耗金属液少; 只能用来接纳和缓冲浇注的金属流股,挡渣能力小; 应用:主要用在小型铸铁件及铸钢件,广泛用于机器造 型。 结构:漏斗口的直径应该比直浇道大一倍以上。可用带 滤网的漏斗形浇口杯。
池盆形浇口杯
生产中减轻水平旋涡的措施 a 用大深度浇口杯 b 浇口杯底部安放筛网等
c 在浇口杯底部设置堤坝,形成垂直旋涡。
垂直旋涡的挡渣作用: 金属液沿斜壁流下, 由于流速的减低和流 向的改变,形成垂直 方向的旋流。
a)合理
b)不合理
• 在池形浇口杯中增设隔板和在浇口杯出口处又有 底坎,就能把浇包落入浇口杯中流股的紊乱搅拌 作用限制在浇注区范围内,且能急剧改变流股方 向,形成使轻质点杂质上浮的流向。
直浇道窝的作用
② 改善内浇道的流量分布:例如在S直:S横: 2S内= 1 : 2.5 : 5的实验条件下,无直浇道窝时,两相等 截面的内浇道的流量分配为:31.5%(近直浇道者) 和68.5%(远者);有直浇道窝时的流量分配为: 40.5%(近直浇道者)和59.5%(远者)。
直浇道窝的作用
③ 减小直-横浇道拐弯处的局部阻力系数和水力 压头损失。 ④ 缩短直-横浇道拐弯处的湍流区。
特点:挡渣作用明显,但是制作程序复杂,消耗 的金属较多 应用:主要用于中大型铸铁件。 结构:浇口盆 的深度应该大 于直浇道上端 直径的5倍。
浇口杯中应避免出现水平涡流
液态金属在平底的浇口杯中 流动 时易出现水平涡流。 流量分布不均匀造成流速方 向偏 斜。水平分速度对直浇 道中心线 偏斜,形成水平涡 流运动。在涡 流中心区形成 一个漏斗形充满空 气的等压 自由液面的空穴。容易 将空 气和渣子带入直浇道。
d 用拔塞等方法,使浇口杯内液面达到一定深度时
再向直浇道注入
• 即使带隔板和底坎(或凹坑)的浇口杯,也不能 完全阻挡浇注开始时液流带入的气体和夹杂物, 故浇注重要铸件时,常在浇注前用各种方法将直 浇道堵住,等浇口杯充满后再打开,并一直保持 浇口杯的液面高度。
浇口杯的结构设计
1) 浇口杯中金属液面的高度:H≥5d 直上 ,而且浇口 杯与直浇道要采用圆角连接, r>0.25d直上;
防止液流带入气体和冲砂,设计直浇道时应注意 以下几点: 1)、入口处的连接 (与浇口
杯连接处)
采用圆角,一般要求入 口处圆角半径r≥d/4(d为 直浇道上口直径)。 这样可以减少气体的卷 入和避免尖角型砂被冲掉引 起冲砂缺陷。
2).直浇道的形状
• 直浇道的形状—上大下小的锥形即设计锥度
上大下小的锥形, 有利于在直浇道中呈正 压流动,能防止吸气或 非充满状态而带气。
1、横浇道中的液流分配
• 金属液从直浇道进入横浇道初期,以较大速度沿 长度方向向前运动,等到达横浇道末端冲击该处 型壁后,金属液的动能转变为势能,横浇道末端 附近液面升高,形成金属浪,并开始返回移动, 使横浇道内液面向直浇道方面逐渐升高,直到全 部充满。
2.横浇道的挡渣作用
1)夹渣的上浮速度
式中:r-渣粒半径,cm;η-金属液粘度,0.024dyne.s/cm2; ρ液,ρ渣-金属液和夹渣的密度,g/cm3。
四、横浇道中的流动
横浇道:将金属液从直浇道导入内浇道的水平孔道
1、横浇道的作用 连接直浇道与内浇道 平稳而均匀的向内浇道分配洁净金属 储留最初浇入的含气和渣污的低温金属液并档渣 使金属液流平稳和减少产生氧化夹渣物。 主要作用是捕集、保留由浇道流入的夹杂物,所以又称“捕渣 器”,是浇注系统最后一道挡渣关口。 要求横浇道平稳、缓慢地输送金属液,而低速流动又可减少充 填时对型腔时的冲击,利于渣粒在横浇道中上浮并滞留在其顶 部而不进入型腔。
浇注系统的组成
浇注系统设计原则
使液态合金平稳充满铸型,不冲击型壁和型芯, 不产生涡流和喷溅,不卷入气体,并利于型腔内 的空气和其他气体排出型外,防止金属液过度氧 化及产生砂眼、冷豆、气孔。
阻挡夹杂物进入型腔,以免在铸件上形成渣孔。 调节铸型及铸件各部分温差,控制铸件的凝固顺序,
不阻碍铸件的收缩,减少铸件的变形和开裂倾向。
第七章
浇注系统设计
本章主要讲授浇注系统类型的选择,浇注最小截 面尺寸的计算,其它铸造合金浇注系统的特点。要 求掌握浇注系统的选择原则。 重点为浇注系统的选择原则和确定浇注位置,难 点为浇注系统选择原则的灵活应用。
概 述
浇注系统:铸型中液态金属流入型腔的通道之总称 组成:浇口杯、直浇道、直浇道窝、横浇道、内浇道 正确设计浇注系统使液态合金平稳合理的充满型 腔,对铸件品质影响很大,铸件废品中的30%是因浇注 系统不当引起。
直浇道的流动特点 (1)两种流态:充满和不充满。非充满状态易带气,但在 底注包浇注时或用阶梯浇注系统时采用。 (2)非充满直浇道中金属液以重力加速度做等加速运动, 流股必定向内收缩;流股内部与砂型表层气体之间无压力差, 气体不可能被吸入,而是被金属表面吸收和带走。 (3)直浇道入口形状影响金属流态。入口尖角时,增加流 动阻力和断面收缩率,常导致非充满式流动。要使直浇道呈 充满流态,要求入口处圆角半径r>d/4。 (4)水利学模拟实验与砂型中实际流动状况有差异。 (5)砂型中直浇道充满的理论条件。
S内 S直
1 z i
(hi hz ) 2 H
26
2)真空吸气理论
假设条件: ① 浇注系统是由不透气材料制成; ② 流体呈稳定流动,且为不可压缩流体; ③ 直浇道为等断面结构。 如图所示,选择直浇道的 出口2-2为分析的基准面,则 伯努利方程可写为:
其中,Z2=0,P2=Pa,整理得:
(1)液态金属在直浇道中的流动特点
直浇道入口处的形状影响液流分布:尖角连接时直 浇道内呈不充满流动;圆角连接时则为充满状态。
直浇道形状影响液流的内部压力:尖角连接时不充满, 而且流股呈渐缩形,直浇道上口有真空区存在。 有锥度的直浇道呈 充满状态,且呈正压 流动,从直浇道上的 小孔流水;而等断面 的直浇道虽然也呈充 满状态,但是却呈负 压流动,吸入气体;
2)采用纵向逆浇,设臵底坎、挡板和闸门等; 3) 采用特殊结构的浇口杯:拔塞式、浮塞式、铁隔 片式、闸门式等; 4)浇口杯与直浇道相连的边缘做成凸起状。
三、直浇道中的流动
直浇道的功用: 引导金属液进入横浇道、内绕道或直接导入型腔; 提供足够的压力头,使金属液克服各种流动阻力, 在规定时间内充满型腔。
影响水平旋涡的因素
浇口杯中金属流股的水平分速度越大,越容易形成水 平旋涡。而水平分速度的大小又与以下因素有关:
a 浇口杯内液面的深度:液面深度超过直浇道上端直
径的5倍时可基本消除水平旋涡。
b 浇注高度:浇包嘴离浇口杯越高,越容易产生水平
旋涡。
• c 浇注方向:逆向浇注较顺向浇注为佳。纵向逆浇不 易形成水平涡流,而纵向顺浇易将夹渣带入型腔;带 底坎时,侧向浇注时金属液可能绕过底坎从另一侧进 入直浇道形成呈湍流状态
多相流动
一般合金液总含有某些少量固相杂质、液相夹杂和 气泡,在充型过程中还可能析出晶粒及气体,故充型时 合金液属于多相流动
二、浇口杯中的流动
浇口杯作用:
用来承受来自浇包的金属液流并引入直浇道, 防止过浇而溢出; 避免流股直冲直浇道,减少液流对铸型的冲击 有一定的挡渣作用; 当砂箱高度低、压头不够时,又可用以增加金 属液的静压头。
由于是稳定流动,根据连续流动定律,有: F1V1=F2V2, F1=F2,V1=V2 则
因为Z1远远大于h1-2,所以,(P2-P1)/γ>0,P2 > P1 ,P2 =Pa,Pa > P1 。 因此,真空吸气理论的分析可以得出结论:在直浇道中有真空 度存在,流体经过浇注系统时要吸入气体。
直浇道结构设计
合金液流不应冲刷冷铁和芯撑。防止冷铁的激冷效 果降低及表面熔化,避免芯撑过早软化和熔化,造 成铸件壁厚变化
浇注系统设计原则
浇注系统尽可能结构简单紧凑,占砂箱面积小,体 积小,有利于减少冒口体积,节约合金和型砂,提 高砂箱利用率,方便造型、清理和浇注系统模样的 制造 使液态合金以最短的距离,最合适的时间充满型腔, 有足够的压力头,并保证金属液面在型腔内有必要 的上升速度等,以确保铸件的质量; 起一定的补缩作用,在内浇道凝固前补给部分液 态收缩