电镀工艺(AQ水淬火)
电镀工艺简介

不良原因分析﹕ a:電鍍時電流密度過大﹐造成鍍層粗糙﹐不致密。 b:電鍍時電流在工件上的分布不均導致鍍層厚度不
均﹐影響整體膜層的耐蝕性。 對策﹕ a:調整電流密度和整平劑的用量。 b:調整陰陽極電極比或采用陰極移動法電鍍。
突點﹕
原因分析﹕ a:電鍍時陽極泥污染槽液。 b:槽液中有固體雜質。 對策﹕ a:增加陽極袋﹐加強陽極泥的過濾去除。 b:用棉芯進行循環過濾。
2.調整鍍液中濕潤劑的添加比例。
3.對槽液進行活性炭處理﹐消除有機雜質的 影響。
麻點產生的原因分析及對策﹕
• 麻點的產生原因﹕ a:油污的附著. b:鍍液緩沖劑不足。
對策﹕ a:加強前處理工序。 b:調整鍍液緩沖劑含量。
結合力不良﹕
原因分析﹕ a:前處理不良﹐脫脂未淨﹐脫模劑仍有殘留。 b﹕柔軟劑不足﹐使得鍍層內應力加大。 c:工件在鍍前活化不良﹐工件鍍前己有局部氧化現象。 d:電鍍過程中有停鍍現象。 改善對策﹕ a﹕加強前處理。 b:添加柔軟劑﹐減小鍍層內應力。 c:鍍前充分活化﹐除掉氧化膜。
•其主要特點是:
a:不用外加電壓﹐可在不導電的工件表面得到鍍
膜﹔ b:得到的是金屬與非金屬的合金鍍層﹐鍍膜的耐蝕
性和電子屏蔽性大大加強。 c:得到的鍍層的均勻性要比水電鍍優越。 d:對工件的形狀無要求﹐適合任何徑深比的工件電
鍍。
物理氣相沉積﹕
• 物理氣象沉積是一個物理沉膜過程﹐成膜過程不 發生化學反應。鍍層金屬在強電子束的撞擊下﹐ 轉變成氣態原子﹑分子狀態﹐然后在電場作用力 的牽引下﹐在工件表面沉積和附著﹐形成鍍膜。
壓鑄件最難處理的壓鑄不良﹕
壓鑄過程中產生的針孔和砂眼。 壓鑄件成形后金屬相分布不均。
在活化時﹐金屬相分布不均導致表面酸蝕不一致﹐產生凸 凹不平。
电镀工艺(AQ水淬火)分析

4.3 钢丝奥氏体化的过程 钢奥氏体化的过程分为4个基本的过程:奥氏体形核、奥氏体长大、 剩余渗碳体溶解和奥氏体成分均匀化。示意图如下:
Fe Fe3C a)A形核
未溶解Fe3C b)A长大
未溶解Fe3C c)残留Fe3C溶解
d)A均匀化
4.4 影响奥氏体化的因素 1、加热温度和保温时间 2、原始颗粒越细。形核越多,晶核长大速度越快,加速奥氏体 的形成过程。 3、钢中的碳含量越高,奥氏体化越快。
3.脱脂槽
*目的: ——获得均匀一致的表面色泽,使钢丝在炉内能均匀地接受辐射来的热 量。获得一致的机械性能。 ——涂上的皂液能控制钢丝在炉内的升温速度,控制钢丝在炉中的氧化 过程,易于酸洗。 *温度 温度最低85℃,较低的温度将影响脱脂液的流动,使钢丝不能有均匀 的涂层。钢丝的面缩率会大,强度偏低。 *浓度 钢丝表面的皂粉多少将影响钢丝在炉中的升温速度。皂粉太多,会导 致钢丝升温太快,有脱碳的可能。脱脂槽中的皂粉浓度由添加水的流量 控制。
6.酸洗
在酸洗过程中,我们必须除去钢丝加热过程中产生的所有氧化物。 一般来说,在盐酸溶液中会发生如下反应: FeO+2HCl=FeCl2+H2O Fe3O4+8Hcl=Fecl3+Fecl2+4 H2O Fe2O3+6Hcl=2Fecl3 +3 H2O
Fe(OH)2+2Hcl= FeCl2 +2 H2O Fe(OH)3+3Hcl=Fecl3 +3 H2O
4.奥氏体炉
4.6 炉温设定 炉温的分布可以有不同的设定,如桥式分布,但必须保证奥氏体化的转变, 并且要注意: *对炉氛控制 *保证最后一区的燃烧压力 *保证燃烧压力的稳定。 桥式温度分布能更好地保证炉子状态,炉子的设计也基于此:Z3到Z4, Z2到Z1。如果Z1压力太高,会破坏这种流动。桥式温度分布可以维持Z2、Z3 很高的压力,使气流正常流动,阻止炉两端的空气进入炉子。
电镀工艺
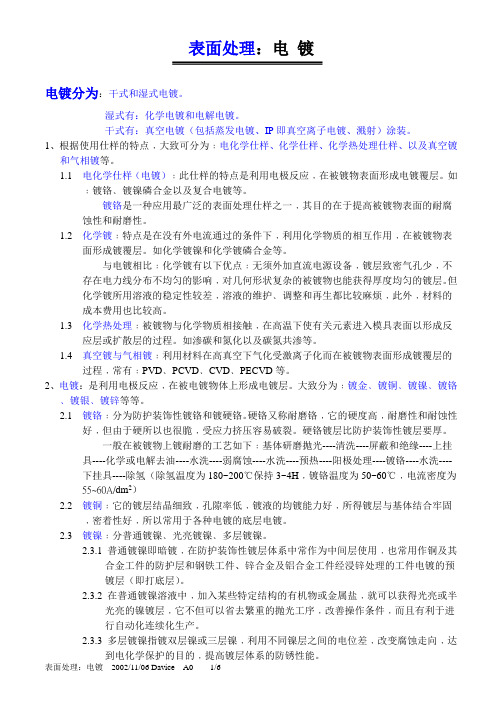
表面处理:电镀电镀分为:干式和湿式电镀。
湿式有:化学电镀和电解电镀。
干式有:真空电镀(包括蒸发电镀、IP即真空离子电镀、溅射)涂装。
1、根据使用仕样的特点﹐大致可分为﹕电化学仕样、化学仕样、化学热处理仕样、以及真空镀和气相镀等。
1.1 电化学仕样(电镀)﹕此仕样的特点是利用电极反应﹐在被镀物表面形成电镀覆层。
如﹕镀铬﹑镀镍磷合金以及复合电镀等。
镀铬是一种应用最广泛的表面处理仕样之一﹐其目的在于提高被镀物表面的耐腐蚀性和耐磨性。
1.2 化学镀﹕特点是在没有外电流通过的条件下﹐利用化学物质的相互作用﹐在被镀物表面形成镀覆层。
如化学镀镍和化学镀磷合金等。
与电镀相比﹕化学镀有以下优点﹕无须外加直流电源设备﹐镀层致密气孔少﹐不存在电力线分布不均匀的影响﹐对几何形状复杂的被镀物也能获得厚度均匀的镀层。
但化学镀所用溶液的稳定性较差﹐溶液的维护﹑调整和再生都比较麻烦﹐此外﹐材料的成本费用也比较高。
1.3 化学热处理﹕被镀物与化学物质相接触﹐在高温下使有关元素进入模具表面以形成反应层或扩散层的过程。
如渗碳和氮化以及碳氮共渗等。
1.4 真空镀与气相镀﹕利用材料在高真空下气化受激离子化而在被镀物表面形成镀覆层的过程﹐常有﹕PVD﹑PCVD﹑CVD﹑PECVD等。
2、电镀:是利用电极反应﹐在被电镀物体上形成电镀层。
大致分为﹕镀金﹑镀铜﹑镀镍﹑镀铬﹑镀银﹑镀锌等等。
2.1镀铬﹕分为防护装饰性镀铬和镀硬铬。
硬铬又称耐磨铬﹐它的硬度高﹐耐磨性和耐蚀性好﹐但由于硬所以也很脆﹐受应力挤压容易破裂。
硬铬镀层比防护装饰性镀层要厚。
一般在被镀物上镀耐磨的工艺如下﹕基体研磨抛光----清洗----屏蔽和绝缘----上挂具----化学或电解去油----水洗----弱腐蚀----水洗----预热----阳极处理----镀铬----水洗----下挂具----除氢(除氢温度为180~200℃保持3~4H﹐镀铬温度为50~60℃﹐电流密度为55~60A/dm2)2.2 镀铜﹕它的镀层结晶细致﹐孔隙率低﹐镀液的均镀能力好﹐所得镀层与基体结合牢固﹐密着性好﹐所以常用于各种电镀的底层电镀。
水电镀生产工艺
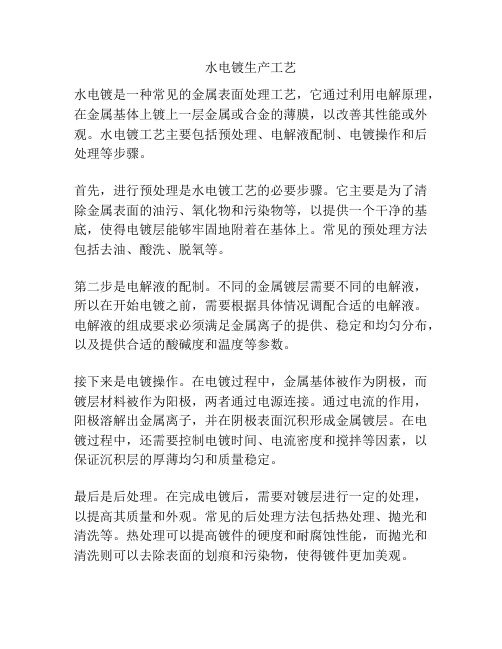
水电镀生产工艺水电镀是一种常见的金属表面处理工艺,它通过利用电解原理,在金属基体上镀上一层金属或合金的薄膜,以改善其性能或外观。
水电镀工艺主要包括预处理、电解液配制、电镀操作和后处理等步骤。
首先,进行预处理是水电镀工艺的必要步骤。
它主要是为了清除金属表面的油污、氧化物和污染物等,以提供一个干净的基底,使得电镀层能够牢固地附着在基体上。
常见的预处理方法包括去油、酸洗、脱氧等。
第二步是电解液的配制。
不同的金属镀层需要不同的电解液,所以在开始电镀之前,需要根据具体情况调配合适的电解液。
电解液的组成要求必须满足金属离子的提供、稳定和均匀分布,以及提供合适的酸碱度和温度等参数。
接下来是电镀操作。
在电镀过程中,金属基体被作为阴极,而镀层材料被作为阳极,两者通过电源连接。
通过电流的作用,阳极溶解出金属离子,并在阴极表面沉积形成金属镀层。
在电镀过程中,还需要控制电镀时间、电流密度和搅拌等因素,以保证沉积层的厚薄均匀和质量稳定。
最后是后处理。
在完成电镀后,需要对镀层进行一定的处理,以提高其质量和外观。
常见的后处理方法包括热处理、抛光和清洗等。
热处理可以提高镀件的硬度和耐腐蚀性能,而抛光和清洗则可以去除表面的划痕和污染物,使得镀件更加美观。
水电镀工艺具有生产工艺简单、成本低、镀层质量稳定等优点,因此在工业生产中得到广泛应用。
它可以增加金属的耐腐蚀性能、增加硬度、改善外观,并广泛应用于汽车、航空航天、电子、家具等行业。
同时,水电镀工艺也需注意环保问题,如合理利用电解液、控制废水排放、回收资源等,以减少对环境的影响。
总而言之,水电镀是一种重要的金属表面处理工艺,通过预处理、电解液配制、电镀操作和后处理等步骤,能够在金属基底上形成一层金属或合金的薄膜,以提高其性能或外观。
在实际应用中,需要合理控制各个环节,以确保镀层的质量和稳定性,同时也要注重环境保护,减少对环境的影响。
AQUA-QUENCH 251水溶性淬火剂

THIF-502水性淬火剂一、简介:本淬火剂为浅黄色透明液体,加有防锈、防腐、润湿、杀菌等多种添加剂制成,对水有逆溶性。
它克服了水冷却速度快,易使工件开裂,油品冷却速度慢,淬火效果差且易燃等缺点。
二、主要特点:1、 通过调整水溶液的浓度,可在很大范围内调整其冷却能力,可以得到近于水,或介于水油之间,以及相当于油或者更慢的冷却速度,以满足不同材料和工件的淬火要求。
2、无毒,无油烟,不燃烧,无火灾危险,使用安全,改善劳动环境,无环境污染。
3、淬硬层深,淬火硬度均匀,无软点,大大减小淬火变形和开裂的倾向,尤其适用于低、中碳钢感应及大件淬火。
4、对黑色金属及有色金属均无腐蚀,淬火工件光亮且有短期防锈作用,可不清洗直接回火。
5、不易老化,变质,使用寿命长。
6、带出量少,使用成本低,综合经济性好。
三、典型理化性能:恒鑫化工科技有限公司采用符合ISO9950标准的IVF 冷却速度测试仪测得不同浓度THIF-502水性淬火剂与水的冷却速度值对比如下表:同浓度的THIF-502水性淬火剂冷却能力可参见以下数据:40#钢,硬度单位HRC30CrMo钢,硬度单位HRC42rMo钢,硬度单位HRC低、中、高碳钢,大截面截面复杂性薄截面渗氮钢、碳氮共渗钢——————————————淬火烈度H 中、低碳低合金钢 5 2 0.9 0.7 0.5 0.3 0.2低渗透性钢盐水水快速油中速油常规油热油THIF-502THI®F-502冷却能力范围示意图五、适用范围:THIF-502水性淬火剂可用于锻钢、铸钢、铸铁以及冲压件等的淬火。
适用于开口式淬火槽、连续炉、淬火槽外设的多用炉及感应淬火炉等。
1、锻钢:小至一公斤大至几吨的低淬透性锻钢或高淬硬性合金锻钢均可采用THIF-502水性淬火剂淬火,所用浓度随合金成份而异,介于10%至30%不等。
2、铸钢:如同锻钢一样,单重悬殊,淬透性各异的铸钢和合金铸钢亦均可采用THIF-502水性淬火剂淬火,所用浓度随合金成份及铸件形体而异,介于10%至30%不等。
电镀前处理工艺概述以及配方
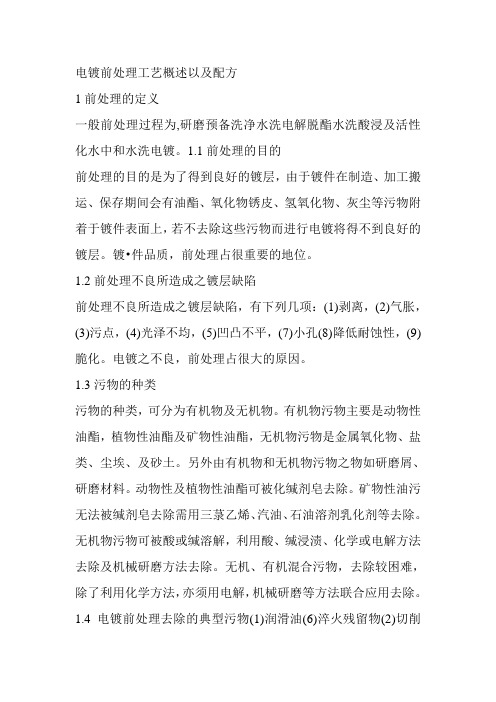
电镀前处理工艺概述以及配方1前处理的定义一般前处理过程为,研磨预备洗净水洗电解脱酯水洗酸浸及活性化水中和水洗电镀。
1.1前处理的目的前处理的目的是为了得到良好的镀层,由于镀件在制造、加工搬运、保存期间会有油酯、氧化物锈皮、氢氧化物、灰尘等污物附着于镀件表面上,若不去除这些污物而进行电镀将得不到良好的镀层。
镀•件品质,前处理占很重要的地位。
1.2前处理不良所造成之镀层缺陷前处理不良所造成之镀层缺陷,有下列几项:(1)剥离,(2)气胀,(3)污点,(4)光泽不均,(5)凹凸不平,(7)小孔(8)降低耐蚀性,(9)脆化。
电镀之不良,前处理占很大的原因。
1.3污物的种类污物的种类,可分为有机物及无机物。
有机物污物主要是动物性油酯,植物性油酯及矿物性油酯,无机物污物是金属氧化物、盐类、尘埃、及砂土。
另外由有机物和无机物污物之物如研磨屑、研磨材料。
动物性及植物性油酯可被化缄剂皂去除。
矿物性油污无法被缄剂皂去除需用三菉乙烯、汽油、石油溶剂乳化剂等去除。
无机物污物可被酸或缄溶解,利用酸、缄浸渍、化学或电解方法去除及机械研磨方法去除。
无机、有机混合污物,去除较困难,除了利用化学方法,亦须用电解,机械研磨等方法联合应用去除。
1.4电镀前处理去除的典型污物(1)润滑油(6)淬火残留物(2)切削油(7)热处理盐(3)研磨油(8)热处理盐(4)热斑(9)污迹(5)锈及腐蚀物(10)油漆及油墨1.5表面清洁测定表面清洁度测定,在工场最实用的方法是用水冲(water-beaktest),检查表面水是否均匀润湿,如果是均匀润湿则为清洁表面,反之则不清洁。
其它方法有,Nielsonmethod,Atomizertest,Fluoresentmethod,weightofresidualsoil,wip-ingmethod,residualpatlernmethod及Radioisotopetracertechnique。
1.6选择清洁方法及清洁材料之影响因素其影响因素有:(1)被清洁表面之特性(9)清洁剂的温度(2)被去除污物之特性(10)应用时间(3)清洁要求程度(11)经验(4)应用的方法(12)搅拌次数(5)水质(13)污染的程度(6)手续、另件、设备人员的安全(14)下一步处理(7)成本(15)废物之处理(8)清洁剂的浓度4镀铬之影响因素(l)CrO3浓度与导电度关系(2)温度兴导电度之关系(3)CrO3浓度与电流效率之关系(4)硫酸浓度之影响:浓度低时,低电流密度下电流效率高,反之电流效率低‥(5)三价铬的影响 1.三价铬很少时,沉积速率减媛。
电镀生产工艺流程
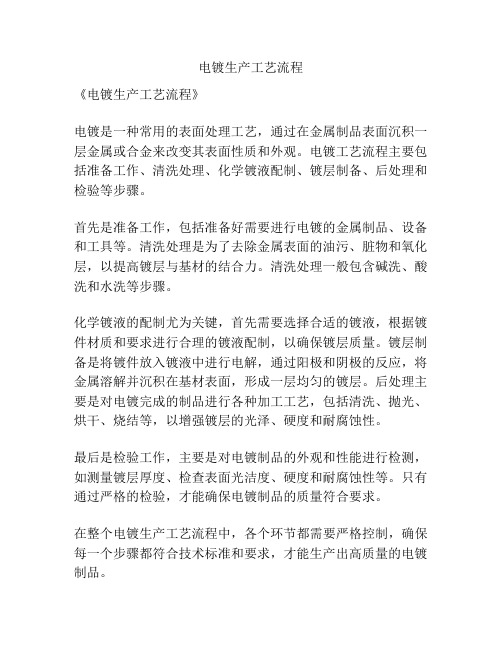
电镀生产工艺流程
《电镀生产工艺流程》
电镀是一种常用的表面处理工艺,通过在金属制品表面沉积一层金属或合金来改变其表面性质和外观。
电镀工艺流程主要包括准备工作、清洗处理、化学镀液配制、镀层制备、后处理和检验等步骤。
首先是准备工作,包括准备好需要进行电镀的金属制品、设备和工具等。
清洗处理是为了去除金属表面的油污、脏物和氧化层,以提高镀层与基材的结合力。
清洗处理一般包含碱洗、酸洗和水洗等步骤。
化学镀液的配制尤为关键,首先需要选择合适的镀液,根据镀件材质和要求进行合理的镀液配制,以确保镀层质量。
镀层制备是将镀件放入镀液中进行电解,通过阳极和阴极的反应,将金属溶解并沉积在基材表面,形成一层均匀的镀层。
后处理主要是对电镀完成的制品进行各种加工工艺,包括清洗、抛光、烘干、烧结等,以增强镀层的光泽、硬度和耐腐蚀性。
最后是检验工作,主要是对电镀制品的外观和性能进行检测,如测量镀层厚度、检查表面光洁度、硬度和耐腐蚀性等。
只有通过严格的检验,才能确保电镀制品的质量符合要求。
在整个电镀生产工艺流程中,各个环节都需要严格控制,确保每一个步骤都符合技术标准和要求,才能生产出高质量的电镀制品。
水电镀工艺流程

水电镀工艺流程水电镀是一种常见的金属表面处理工艺,通过电化学方法将金属离子沉积在工件表面,形成一层均匀、致密的金属镀层,以增强工件的耐腐蚀性和美观性。
水电镀工艺流程包括预处理、电镀、后处理等多个环节,下面将详细介绍水电镀的工艺流程。
1. 预处理。
在进行水电镀之前,需要对工件进行预处理,以确保镀层的附着力和质量。
预处理包括去油、除锈、清洗等步骤。
首先,将工件浸泡在去油溶剂中,去除表面的油污和污垢。
然后,采用化学方法或机械方法去除工件表面的氧化层和锈蚀,以保证金属表面的光洁度和清洁度。
最后,通过酸洗或碱洗等方式清洗工件表面,去除残留的杂质和化学物质,为后续的电镀工艺做好准备。
2. 电镀。
预处理完成后,工件进入电镀环节。
电镀过程中,工件作为阴极,放置在电解槽中,金属离子通过电解质溶液在工件表面沉积形成金属镀层。
首先,将含有金属离子的电解质溶液注入电解槽中,然后通过外加电流,使金属离子在工件表面还原成金属原子并沉积下来。
在电镀过程中,需要控制电流密度、温度、PH值等参数,以确保镀层的均匀性和致密性。
此外,还可以根据需要选择不同的金属材料进行电镀,如镍、铬、铜等,以满足工件的功能和装饰要求。
3. 后处理。
电镀完成后,需要对工件进行后处理,以提高镀层的光泽度和耐腐蚀性。
后处理包括清洗、抛光、封孔等步骤。
首先,将镀有金属层的工件进行清洗,去除电解质溶液残留和杂质,保证镀层的干净和光洁。
然后,通过机械抛光或化学抛光等方式,提高镀层的光泽度和表面质量。
最后,可以采用封孔处理,填充镀层中的微孔,提高镀层的致密性和耐腐蚀性。
4. 检测。
在整个水电镀工艺流程中,需要对工件和镀层进行检测,以确保产品质量和工艺稳定性。
检测包括镀层厚度、附着力、耐腐蚀性等指标的测试。
通过合适的检测设备和方法,对镀层进行定量和定性分析,及时发现和解决工艺问题,提高水电镀产品的质量和可靠性。
总结。
水电镀工艺流程包括预处理、电镀、后处理和检测等多个环节,每个环节都对最终镀层的质量和性能有重要影响。
电镀工艺技术介绍
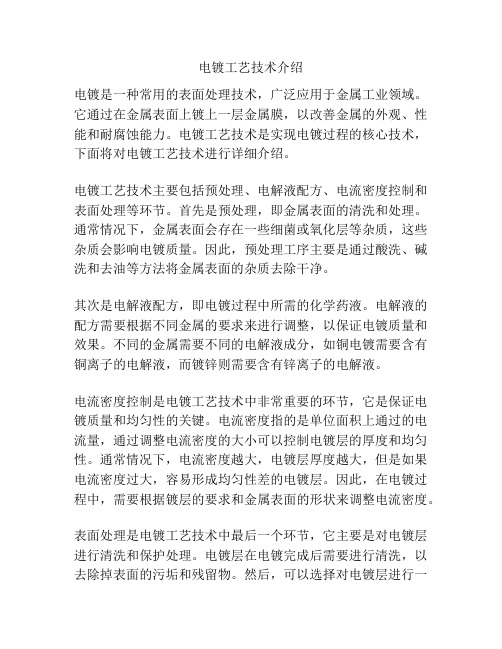
电镀工艺技术介绍电镀是一种常用的表面处理技术,广泛应用于金属工业领域。
它通过在金属表面上镀上一层金属膜,以改善金属的外观、性能和耐腐蚀能力。
电镀工艺技术是实现电镀过程的核心技术,下面将对电镀工艺技术进行详细介绍。
电镀工艺技术主要包括预处理、电解液配方、电流密度控制和表面处理等环节。
首先是预处理,即金属表面的清洗和处理。
通常情况下,金属表面会存在一些细菌或氧化层等杂质,这些杂质会影响电镀质量。
因此,预处理工序主要是通过酸洗、碱洗和去油等方法将金属表面的杂质去除干净。
其次是电解液配方,即电镀过程中所需的化学药液。
电解液的配方需要根据不同金属的要求来进行调整,以保证电镀质量和效果。
不同的金属需要不同的电解液成分,如铜电镀需要含有铜离子的电解液,而镀锌则需要含有锌离子的电解液。
电流密度控制是电镀工艺技术中非常重要的环节,它是保证电镀质量和均匀性的关键。
电流密度指的是单位面积上通过的电流量,通过调整电流密度的大小可以控制电镀层的厚度和均匀性。
通常情况下,电流密度越大,电镀层厚度越大,但是如果电流密度过大,容易形成均匀性差的电镀层。
因此,在电镀过程中,需要根据镀层的要求和金属表面的形状来调整电流密度。
表面处理是电镀工艺技术中最后一个环节,它主要是对电镀层进行清洗和保护处理。
电镀层在电镀完成后需要进行清洗,以去除掉表面的污垢和残留物。
然后,可以选择对电镀层进行一些保护处理,如添加一层有机膜或进行热处理,以增加电镀层的耐腐蚀性和耐磨性。
总之,电镀工艺技术是实现电镀过程的关键技术之一。
通过预处理、电解液配方、电流密度控制和表面处理等环节的合理操作,可以获得高质量、均匀的电镀层。
电镀工艺技术的不断发展和创新,为各行各业提供了更多的应用和发展空间。
电镀工艺流程及品质要求汇总

电镀工艺流程及品质要求一.电镀种类:1、一般水电镀:一般金属物的电镀,利用电化学作用,将防锈物或漂亮的有装饰颜色的化学物质,加在金属上面,使金属产品更有价值及防锈。
2、真空(铝)电镀:利用真空状态下,铝原子比较活泼的特性,加上静电的异性相吸原理,将铝原子的附在被加工物的表面,增加装饰性。
一般加工物体为非导电体的非金属材料,例如:玻璃、陶瓷、塑胶等制品。
3、真空镀钛(钯):(钛钯)等金属硬度较高,利用真空电镀原理,将钛金属溅镀在被加工物表面。
二.电镀工艺流程(一般):1、铁件:工件抛光→ 热浸除油→ 酸浸除锈→ 阴极电解除油→ 阳极电解除油→ 弱酸浸蚀→ 预镀铜→ 酸性光亮铜→ 镀表面→ 烤透明漆2、铝及铝合金件:工件抛光→ 超声波除蜡→ 化学抛光→ 锌置换→ 脱锌→ 锌置换→(镀表面、化学镍)烤透明漆3、锌和金件:工件抛光→ 热浸除油→ 超声波除蜡→ 阴极电解除油→ 活性酸→ 预镀铜→ 焦磷酸铜→ 酸性光亮铜→ 镀表面→ 烤透明漆4、用电镀铬的表面是金属铬,金属铬硬度很高(金属铬的布氏硬度是110HB、钛金属115HB 、铁50HB 、铜40HB 、锌35HB 、铝25HB 、铅5HB )不易被刮伤,所以电镀层表面不需再加保护处理;但其它色泽如镀青铜、古铜、镍、镍砂等非镀铬处理的表面,均需加一层透明漆保护。
三.工件品质注意事项:1、黑胚抛光需使用适当的模具,才不至于造成工件表面变形。
2、因为在电镀过程中,工件需浸水出水数次,所以必须考虑工件的进、排水状况,如果排水不良将造成吐酸现象。
3、工件若有经过焊接,则焊缝必需整个都焊实,不可漏掉,以免因为有漏缝处,产生毛细现象,含酸水造成吐酸现象。
4、工件若有凸出物,必需小心互相碰撞的问题,会造成伤害,要在包装加强。
5、若工件在电镀前无法抛光时,则需在粗胚加工前,还是原材料时就要先抛光再加工。
6、工件若有内外牙、抽牙或铆铜等在抛光或除色时需小心,以免被抛光受伤。
水电镀工艺流程分析
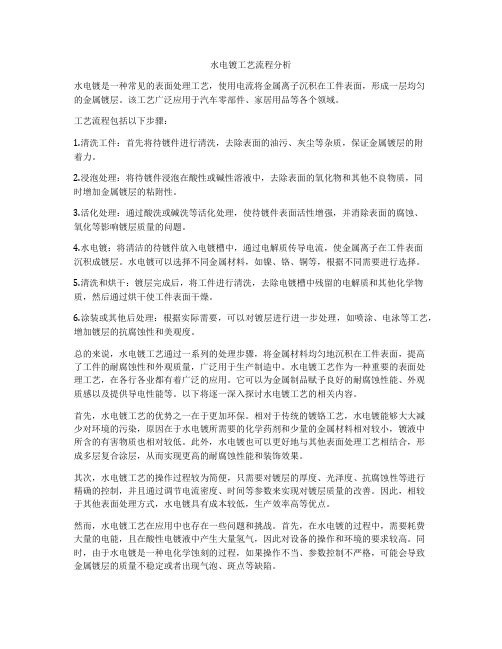
水电镀工艺流程分析水电镀是一种常见的表面处理工艺,使用电流将金属离子沉积在工件表面,形成一层均匀的金属镀层。
该工艺广泛应用于汽车零部件、家居用品等各个领域。
工艺流程包括以下步骤:1.清洗工件:首先将待镀件进行清洗,去除表面的油污、灰尘等杂质,保证金属镀层的附着力。
2.浸泡处理:将待镀件浸泡在酸性或碱性溶液中,去除表面的氧化物和其他不良物质,同时增加金属镀层的粘附性。
3.活化处理:通过酸洗或碱洗等活化处理,使待镀件表面活性增强,并消除表面的腐蚀、氧化等影响镀层质量的问题。
4.水电镀:将清洁的待镀件放入电镀槽中,通过电解质传导电流,使金属离子在工件表面沉积成镀层。
水电镀可以选择不同金属材料,如镍、铬、铜等,根据不同需要进行选择。
5.清洗和烘干:镀层完成后,将工件进行清洗,去除电镀槽中残留的电解质和其他化学物质,然后通过烘干使工件表面干燥。
6.涂装或其他后处理:根据实际需要,可以对镀层进行进一步处理,如喷涂、电泳等工艺,增加镀层的抗腐蚀性和美观度。
总的来说,水电镀工艺通过一系列的处理步骤,将金属材料均匀地沉积在工件表面,提高了工件的耐腐蚀性和外观质量,广泛用于生产制造中。
水电镀工艺作为一种重要的表面处理工艺,在各行各业都有着广泛的应用。
它可以为金属制品赋予良好的耐腐蚀性能、外观质感以及提供导电性能等。
以下将逐一深入探讨水电镀工艺的相关内容。
首先,水电镀工艺的优势之一在于更加环保。
相对于传统的镀铬工艺,水电镀能够大大减少对环境的污染,原因在于水电镀所需要的化学药剂和少量的金属材料相对较小,镀液中所含的有害物质也相对较低。
此外,水电镀也可以更好地与其他表面处理工艺相结合,形成多层复合涂层,从而实现更高的耐腐蚀性能和装饰效果。
其次,水电镀工艺的操作过程较为简便,只需要对镀层的厚度、光泽度、抗腐蚀性等进行精确的控制,并且通过调节电流密度、时间等参数来实现对镀层质量的改善。
因此,相较于其他表面处理方式,水电镀具有成本较低,生产效率高等优点。
电镀工艺详述

第一章电镀概论1 电镀定义电镀为电解镀金属法的简称。
电镀是将镀件(制品),浸于含有欲镀上金属离子的药水中并接通阴极,药水的另一端放置适当阳极(可溶性或不可溶性),通以直流电后,镀件的表面即析出一层金属薄膜的方法。
2 电镀基本五要素1)阴极:被镀物,指各种接插件端子。
2)阳极:若是可溶性阳极,则为欲镀金属。
若是不可溶性阳极,大部分为贵金属(白金,氧化铱)。
3)电镀药水:含有欲镀金属离子的电镀药水。
4)电镀槽:可承受、储存电镀药水的槽体,一般考虑强度,耐蚀,耐温等因素。
5)整流器:提供直流电源的设备。
3 电镀目的1)镀铜:打底用,增进电镀层附着能力,及抗蚀能力。
2)镀镍:打底用,增进抗蚀能力。
3)镀金:改善导电接触阻抗,增进信号传输。
4)镀钯镍:改善导电接触阻抗,增进信号传输,耐磨性比金佳。
5)镀锡:增进焊接能力,提升基材抗氧化能力。
4 电镀流程(一般铜合金底材如下,未含水洗工程)1)除油:通常同时使用碱性溶液除油或者电解除油。
2)活化:使用稀硫酸或相关的混合酸。
3)镀镍:使用硫酸镍系及氨基磺酸镍系。
4)镀钯镍:目前皆为氨系。
5)镀金:有金钴,金镍,金铁,一般使用金钴系最多。
6)镀锡:硫酸亚锡体系、甲基磺酸体系。
7)干燥:使用热风循环烘干。
8)封孔处理:采用溶液浸泡,提升抗氧化能力,有使用水溶型及溶剂型两种。
5 电镀药水组成1)纯水:总不纯物至少要低于5ppm。
2)金属盐:提供欲镀金属离子。
3)阳极解离助剂:增进及平衡阳极解离速率。
4)导电盐:增进药水导电度。
5)添加剂:有缓冲剂、光泽剂、平滑剂、柔软剂、湿润剂、抑制剂等等。
一般起到均匀镀层,提升亮度、结合力的效果。
6 电镀条件1)电流密度:单位电镀面积下所承受的电流,通常电流密度越高膜厚越厚,但是过高时镀层会烧焦粗燥。
2)电镀位置:镀件在药水中位置,与阳极相对位置,会影响膜厚分布。
3)搅拌状况:搅拌效果越好,电镀效率越高,有空气,水流,阴极摆动等搅拌方式。
钢丝水淬火说明

钢丝水淬火说明-CAL-FENGHAI.-(YICAI)-Company One1钢丝水淬火(AQ)工艺说明一工艺介绍AQ淬火是一种将钢丝在水(蒸汽)中冷却淬火的工艺。
钢丝从炉子中出来,得到完全的奥氏体。
如果冷却速度过快,一般得到坚硬的马氏体,根本无法拉拔。
在水中加入添加剂Aqua Quench 110后,AQ110能提高水的粘度,提高水的汽化温度,降低热传导率,使热的钢丝表面形成一层蒸汽膜。
钢丝和水不直接接触,钢丝在水中通过蒸汽膜与水进行热交换,实现钢丝的慢速冷却。
钢丝在任何时候都不能与水接触(如图)在转换未完成之前,钢丝必须被膜态沸腾产生的蒸汽膜所包围。
转变没有结束,钢丝与水接触会形成马氏体。
钢丝钢丝电镀钢丝的WAP一般分3个过程:(1)钢丝在第一个水槽(WT1)中冷却至650℃左右,在蒸汽膜破裂之前离开水槽1,组织为过冷奥氏体。
(2)钢丝在空气中冷却至620℃左右,开始发生过冷奥氏体向细珠光体/索氏体的转变;由于这个转变是个放热过程,所以钢丝温度会上升。
(3)为保证电镀钢丝的机械性能,钢丝又被引入第二个水槽(WT2)进行冷却,实现更多索式体转变。
钢丝在离开水槽2后转变基本全部完成。
经水浴后的钢丝组织以索式体为主,并伴有少量的铁素体。
相关参数:浴液温度:90±5℃出炉线温:930±20℃出水线温:610±30℃溶液浓度:--12±2%--安全限≥8%--浸液长度~3.2m钢丝浸入溶液深度10~15mm二操作事项在日常操作中1启动时,必须将溶液预热至85℃。
如果溶液温度过低,钢丝提供的热量不足以立即形成并保持蒸汽膜。
2只有在达到生产速度后钢丝方可浸入AQ溶液。
如果打低速时就将钢丝浸入溶液,由于浸没时间过长,蒸汽膜在钢丝离开溶液之前就破裂了3AQ流量不能过大,否则也会导致蒸汽膜破裂4为保证蒸汽膜的稳定性,蒸汽-水界面的表面张力必须满足一个最小值。
这意味着活性AQ浓度必须足够高。
电镀电镀基本工艺及各工序前处理作用

电镀电镀基本工艺及各工序前处理作用电镀是一种电化学过程﹐也是一种氧化还原过程。
电镀的基本过程是将零件浸在金属盐的溶液中作为阴极﹐金属板作为阳极﹐接直流电源后﹐在零件上沉积出所需的镀层。
例如﹕镀镍时﹐阴极为待镀零件﹐阳极为纯镍板﹐在阴阳极分别发生如下反应﹕阴极(镀件)﹕Ni2++2e→Ni(主反应)2H++e→H2↑(副反应)阳极(镍板)﹕Ni﹣2e→Ni2+(主反应)4OH-﹣4e→2H2O+O2+4e(副反应)不是所有的金属离子都能从水溶液中沉积出来﹐如果阴极上氢离子还原为氢的副反应占主要地位﹐则金属离子难以在阴极上析出。
根据实验﹐金属离子自水溶液中电沉积的可能性﹐可从元素周期表中得到一定的规律。
阳极分为可溶性阳极和不溶性阳极﹐大多数阳极为与镀层相对应的可溶性阳极﹐如﹕镀锌为锌阳极﹐镀银为银阳极﹐镀锡-铅合金使用锡-铅合金阳极。
但是少数电镀由于阳极溶解困难﹐使用不溶性阳极﹐如酸性镀金使用的是多为铂或钛阳极。
镀液主盐离子靠添加配制好的标准含金溶液来补充。
镀铬阳极使用纯铅﹐铅-锡合金﹐铅-锑合金等不溶性阳极。
电镀基本工艺及各工序的作用工艺流程(磨光→抛光)→上挂→脱脂除油→水洗→(电解抛光或化学抛光)→酸洗活化→(预镀)→电镀→水洗→(后处理)→水洗→乾燥→下挂→检验包装各工序的作用前处理﹕施镀前的所有工序称为前处理﹐其目的是修整工件表面﹐除掉工件表面的油脂﹐锈皮﹐氧化膜等﹐为后续镀层的沉积提供所需的电镀表面。
前处理主要影响到外观,结合力﹐据统计﹐60%的电镀不良品是由前处理不良造成﹐所以前处理在电镀工艺中占有相当重要的地位。
在电镀技朮发达的国家﹐非常重视前处理工序﹐前处理工序占整个电镀工艺的一半或以上﹐因而能得到表面状况很好的镀层和极大地降低不良率。
喷砂﹕除去零件表面的锈蚀﹐焊渣﹐积碳﹐旧油漆层﹐和其它干燥的油污﹔除去铸件﹐锻件或热处理后零件表面的型砂和氧化皮﹔除去零件表面的毛刺和和方向性磨痕﹔降低零件表明的粗糙度﹐以提高油漆和其它涂层的附著力﹔使零件呈漫反射的消光状态磨光﹕除掉零件表明的毛刺﹐锈蚀﹐划痕﹐焊缝﹐焊瘤﹐砂眼﹐氧化皮等各种宏观缺陷﹐以提高零件的平整度和电镀质量。
电镀工艺标准
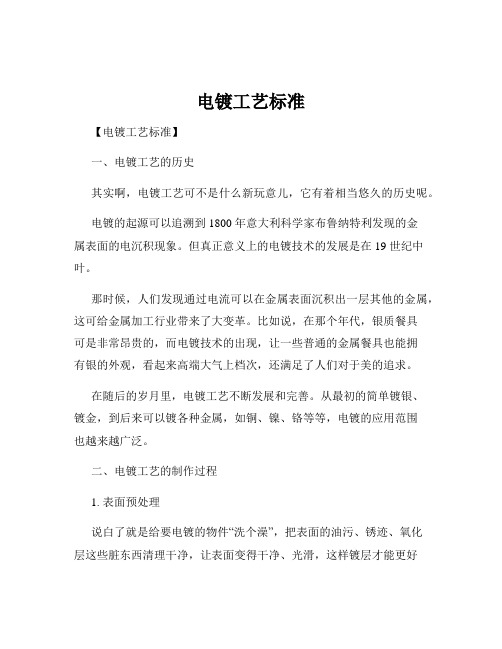
电镀工艺标准【电镀工艺标准】一、电镀工艺的历史其实啊,电镀工艺可不是什么新玩意儿,它有着相当悠久的历史呢。
电镀的起源可以追溯到 1800 年意大利科学家布鲁纳特利发现的金属表面的电沉积现象。
但真正意义上的电镀技术的发展是在 19 世纪中叶。
那时候,人们发现通过电流可以在金属表面沉积出一层其他的金属,这可给金属加工行业带来了大变革。
比如说,在那个年代,银质餐具可是非常昂贵的,而电镀技术的出现,让一些普通的金属餐具也能拥有银的外观,看起来高端大气上档次,还满足了人们对于美的追求。
在随后的岁月里,电镀工艺不断发展和完善。
从最初的简单镀银、镀金,到后来可以镀各种金属,如铜、镍、铬等等,电镀的应用范围也越来越广泛。
二、电镀工艺的制作过程1. 表面预处理说白了就是给要电镀的物件“洗个澡”,把表面的油污、锈迹、氧化层这些脏东西清理干净,让表面变得干净、光滑,这样镀层才能更好地附着上去。
这就好比我们要在墙上贴壁纸,如果墙面坑坑洼洼、满是灰尘,壁纸能贴牢吗?肯定不行!所以预处理很重要。
一般会用到化学方法,比如酸洗、碱洗,也可能会用到机械方法,像打磨、抛光。
2. 电镀液的配制这就像是给金属准备的“营养餐”。
电镀液的成分可是有讲究的,不同的金属电镀需要不同的配方。
比如镀铜,电镀液里就得有铜离子;镀镍,就得有镍离子。
而且,电镀液的酸碱度、温度、浓度等条件都得控制好,要不然镀出来的效果可就差强人意了。
3. 电镀操作这是最关键的一步啦。
把预处理好的物件放进电镀液里,然后通上电流。
电流就像是个“搬运工”,把电镀液里的金属离子搬到物件表面,形成一层均匀的镀层。
比如说,我们要给一个铁质的钥匙镀镍,把钥匙放进镍电镀液中,通上电流,镍离子就会在钥匙表面慢慢沉积,形成一层闪亮的镍镀层,让钥匙变得更加耐磨、耐腐蚀。
4. 后处理这是电镀的“收尾工作”。
镀完之后,要把物件清洗干净,去除表面残留的电镀液,还要进行一些检查和处理,确保镀层的质量。
电镀工艺(AQ水淬火)详解共42页

53、 伟 大 的 事 业,需 要决心 ,能力 ,组织 和责任 感。 ——易 卜 生 54、 唯 书 籍 不 朽。——乔 特
55、 为 中 华 之 崛起而 读书。 ——周 恩来
39、没有不老的誓言,没有不变的承 诺,踏 上旅途 ,义无 反顾。 40、对时间的价值没有没有深切认识 的人, 决不会 坚韧勤 勉。
谢谢!
51、 天 下 之 事 常成 于困约 ,而败 于奢靡 。——陆 游 52、 生 命 不 等 于是呼 吸,生 命是活 动。——卢 梭
- 1、下载文档前请自行甄别文档内容的完整性,平台不提供额外的编辑、内容补充、找答案等附加服务。
- 2、"仅部分预览"的文档,不可在线预览部分如存在完整性等问题,可反馈申请退款(可完整预览的文档不适用该条件!)。
- 3、如文档侵犯您的权益,请联系客服反馈,我们会尽快为您处理(人工客服工作时间:9:00-18:30)。
5.2 AQ水淬火的组织变化 AQ槽分成三部分,它们是:WT1、AIR、和WT2。钢丝在WT1中的 组织是过冷奥氏体,在空气段中开始由过冷奥氏体转变成为索氏体 (相变放出的热在空气后段时使钢丝又变红),在WT2中得到更多 的索氏体,在出WT2后钢丝组织转变的过程基本结束,最终得到以 索氏体为主的钢丝。冷却曲线如下图。
Fe+2Hcl= FeCl2 +H2 2Fecl3 +2H+=2 FeCl2 +2Hcl 2Fecl3 +Fe=3 FeCl2 酸洗是利用钢丝和盐酸反应生成的氢气来剥落氧化皮的。盐酸三份 之二的用量和钢丝反应,三份之一的用量和氧化皮反应。 Fe3+ + Fe → Fe2+ Fe3+有氧化性,对钢丝有腐蚀作用,所以浓度不能太高。因此溶液 中Fe2+高一些,能够抑制Fe3+与Fe 的反应。
6.酸洗
在酸洗过程中,我们必须除去钢丝加热过程中产生的所有氧化物。 一般来说,在盐酸溶液中会发生如下反应: FeO+2HCl=FeCl2+H2O Fe3O4+8Hcl=Fecl3+Fecl2+4 H2O Fe2O3+6Hcl=2Fecl3 +3 H2O
Fe(OH)2+2Hcl= FeCl2 +2 H2O Fe(OH)3+3Hcl=Fecl3 +3 H2O
5.4 调整的标准 一般调整时,先看强度在什么范围,若超出上标准限,则增加 WT1长度,若超出上工作限但没有超出上标准限时,增加空气 长度。增加WT1长度1cm,钢丝强度下降5MPa;增加AIR 长度 1cm,钢丝强度下降2MPa;增加WT2长度1cm,钢丝强度上升 5MPa。一般是只调整WT1和AIR的长度。
℃
时间
WT1:A
AIR:A+S
Q的目的是要得到要求的强度。当强度超出上标准时,增加空 气段长度,当强度超出上极限时,增加WT1的长度。 a)调整空气段降低强度的原理是:加长空气段的长度,则钢丝在 空气中的相变时间变长,钢丝上得到了更多的相变热,钢丝温度上 升得更多,由于WT2的长度没有发生变化,该段带走钢丝热量不变, 这样就减小了过冷度,所以强度下降。 b)调整WT1降低强度的原理是:加长WT1的长度,则钢丝在空气 中的相变点提前,时间变长,钢丝上得到了更多的相变热,使钢丝 温度上升得更多,由于WT2的长度没有发生变化,该段带走钢丝热 量不变,这样就减小了过冷度,所以强度下降。
2.放线
为了避免中拉钢丝在放线时绞丝,通过飞轮的张力带给予钢丝一定 的张力。钢丝的张力根据钢丝的直径来确定,不同的直径控制相应的张 力。因此,每次更换直径后要调整放线张力。
2.放线
1、张力太大: *导线孔易磨损 *会造成钢丝在炉中有延伸 ――电镀钢丝直径变细,湿拉钢丝破断拉力不够 ――湿拉拉拔会形成中心毛刺 *分线梳磨损 *炉中断丝 *接断丝困难 2、张力太小: *钢丝跳出放线工字轮而断丝。 *炉中绞丝 ――加热不均匀 ――面缩率偏高,湿拉不正常断丝 ――铁素体溶解不完全 ――抗拉强度低,散差大 *损坏氧化皮 ――脱碳 ――炉内氧化皮堆积
6.酸洗
酸洗质量的判断: 生产中,用手掌外侧轻触酸洗水冲洗后钢丝,不沾染黑色表示酸洗质量较 好;有擦不掉的黑色,表示过酸洗;能擦掉的黑色表示酸洗不够。
洗酸器: 洗酸器是酸槽洗的一个组成部分,能洗去空气中的酸雾。无论生产线启动或 停止,必须保证常开。
4.奥氏体炉
4.5 DV值 我们的炉子是气体加热辐射炉,热量的传输取决于钢丝的吸热系 数。为了保证奥氏体化均匀一致,得到一致速度的加热,不同的直 径用不同的收线速度来达到。我们保证同样单位的表面积的钢丝通 过炉子。表面积和直径成正比,因此,我们根据燃气炉的功率得到 炉子常数(furnace constant)=D*V。 虽然加热和钢丝表面积有关,但还和钢丝的体积有关,因而虽然 在相同的DV值下,不同直径和不同含碳量的钢丝的加热功率(炉温 设定)还是有不同。
电镀工艺(AQ水淬火)
放线
脱脂 奥氏体炉 AQ水淬火 水冷却 串连水冲洗 镀锌槽 串连水冲洗
皂浸
串连水冲洗 收线
热水洗
酸洗
热扩散
串连水冲洗
水冷却槽
镀铜
磷酸浸
1.简介
中拉钢丝需根据帘线成品的要求,经过热处理来获得一定的强度。热处理的 目的: ――重新具有拉拔性能 ――得到最佳的金相组织 ――得到经湿拉后想要的抗拉强度 热处理分为两个步骤:奥氏体化和淬火。拉拔前,钢的组织由不同方向分布 的渗碳体的晶粒组成,之间的间隙(晶界)由杂乱分布的Fe3C填充。 在拉拔过程中,钢丝的良好结构会被破坏,晶粒被拉长,断裂。钢丝硬度增 加,延展性变差,无法进一步拉拔。经过炉子升温使晶粒重新形成渗碳体。 在炉子中,被破坏的Fe3C重新融合;在淬火槽中,Fe3C重新排列。 钢帘线最重要的性能之一是钢帘线与橡胶的粘合力。我们通过黄铜镀层加强 与橡胶的粘合力。同时,黄铜在湿拉过程中能起润滑作用。不同的客户使用 不同的胶料,由此我们设计不同的镀层:铜含量和镀层重量。
4.3 钢丝奥氏体化的过程 钢奥氏体化的过程分为4个基本的过程:奥氏体形核、奥氏体长大、 剩余渗碳体溶解和奥氏体成分均匀化。示意图如下:
Fe Fe3C a)A形核
未溶解Fe3C b)A长大
未溶解Fe3C c)残留Fe3C溶解
d)A均匀化
4.4 影响奥氏体化的因素 1、加热温度和保温时间 2、原始颗粒越细。形核越多,晶核长大速度越快,加速奥氏体 的形成过程。 3、钢中的碳含量越高,奥氏体化越快。
3.脱脂槽
*目的: ——获得均匀一致的表面色泽,使钢丝在炉内能均匀地接受辐射来的热 量。获得一致的机械性能。 ——涂上的皂液能控制钢丝在炉内的升温速度,控制钢丝在炉中的氧化 过程,易于酸洗。 *温度 温度最低85℃,较低的温度将影响脱脂液的流动,使钢丝不能有均匀 的涂层。钢丝的面缩率会大,强度偏低。 *浓度 钢丝表面的皂粉多少将影响钢丝在炉中的升温速度。皂粉太多,会导 致钢丝升温太快,有脱碳的可能。脱脂槽中的皂粉浓度由添加水的流量 控制。
3.脱脂槽
*添加水 ——补偿蒸发 ——钢丝带出的水 ——不断溢流溶液,控制硼砂和皂粉的浓度 *抽气装置 抽气装置必须始终工作,抽气口要保持清洁。抽气风机的过滤器要 保持清洁。如被污垢堵塞将影响抽气效果。过滤器的压差如大于100mm 水柱,则需更换滤网。
4.奥氏体炉
4.1钢是一种混合物,主要由铁和碳两种元素组成。碳以渗碳体存在 (Fe3C)。钢丝的抗拉强度主要由 Fe3C的数量和分布决定 Fe3C的厚度和相互之间的距离决定。
4.奥氏体炉
4.8面缩率和晶粒度 面缩率是能衡量奥氏体化的较快的参数,通过拉伸试验得到。面缩率指 标不是标准,因为面缩率的值还取决于盘条质量和拉拔工艺。面缩 率的测量必须在24小时以内,否则会产生时效(ageing),数值会 偏高。 • 如果面缩率值偏高,说明钢丝温度太低,保温时间太短,晶粒太小。 碳没有完全溶解,有残留碳化物。 可能的原因:钢丝碰炉底、交叉、缠绕、钢丝光亮等。现象:炉出口钢 丝暗,小的晶粒度抗拉强度太低,湿拉会中心毛刺。 • 如果面缩率值偏低,说明钢丝温度太高,晶粒增长速度慢,单个奥 氏体晶粒太大。钢丝的延展性差、有脱碳的风险,钢丝过氧化。
4.奥氏体炉
4.2 钢丝结构的转变 钢的组织由不同方向分布的渗碳体的晶粒组成,之间的间隙(晶 界)由杂乱分布的Fe3C填充。 在拉拔过程中,钢丝的良好结构会被破坏,晶粒被拉长,断裂。 经过燃气炉加热,使晶粒重新形成渗碳体。在炉子中,被破坏的 Fe3C重新融合;在淬火槽中, Fe3C重新排列。 温度超过723(取决于钢丝成分及加热速度)钢丝会奥氏体化。碳 原子渗透到间隙里去,需要一定的时间,也即我们要时钢丝加热到 更高的温度。完美的奥氏体化要尽可能的均匀,需要有很好的温度 及足够的时间让碳原子扩散。但如果钢丝停留在炉子时间太长,晶 粒会长得很大。 燃气炉共有四个区,钢丝在炉子第三区要达到940-950,第四区 提供一个扩散(溶解)的时间,也即第四区只是保温作用,不应该 是加热的过程,通过第四区的燃烧压力大小来判断。
4.奥氏体炉
4.4 炉温设定 如何是一个理想的炉温分布呢,钢丝在炉中可以分为几个阶段: Z1:在Z1形成保护性的氧化皮(Fe3O4),颜色更暗,吸热更快。理论上, 当离开Z1时已达到转变温度,>723。 Z2:在理想情况下,该区应该提供所有的热量来使得α-铁向β-铁转变,珠 光体向奥氏体转变。在整个转变过程中,钢丝温度在20-30之间,是等温转变, 热量提供给组织结构的转变。 Z3:钢丝被加热到最终温度940左右。实际上转变从Z2后半部分开始,可能会 持续到Z3,因此,在很好的情况下,钢丝温度在900左右。 Z4:理想情况下,Z4是保温区,同时也能提供一定的时间让如光亮钢丝等吸 热慢的钢丝达到所需的温度。 炉子各区温度等于设定温度,尤其最后区的温度和燃烧压力。最后区的实 际温度必须等于设定的980℃(±3℃),燃烧嘴只需打开一半,同时燃烧压 力必须较低,小于150cm水柱。因为钢丝在前面区已充分受热,在最后区仅 需补充钢丝损失的热量(保温)。
4.奥氏体炉
4.7 炉气氛 燃烧产物跟所用的燃气有关,如液化石油气LPG,天然气NG。燃气中甲烷含 量高,热值高,氢含量高,热值低。 在我们的炉子中必须防止游离氧,否则氧化物形成会不受控。为了防止游离 氧,炉子内部为小的正压,同时具有稍微的还原性气氛。 炉子的第一区可以稍微的氧化性气氛,使得钢丝表面迅速形成Fe3O4,我们需 要 Fe3O4在进一步加热时防止脱碳。从第一区到第四区,CO的含量应逐渐提 高,防止钢丝中的C和CO2反应,形成脱碳(脱碳钢丝比正常钢丝软,内层硬, 外层软,湿拉会堵塞模孔,镀层剥落)。CO含量太高,燃烧压力会很高,炉 子压力不是很理想,奥氏体化不完全。
6.酸洗
钢丝在奥氏体化和热处理时会形成氧化物,还有皂粉和硼砂的固化物,会影 响镀层与钢丝的结合力,影响湿拉拉拔。酸洗就是把氧化物和气体固化物去 除的过程。正如脱脂是热处理的预先处理,酸洗是镀层的预处理。好的酸洗 过程,要溶解所有的氧化物,不溶解钢基,并且酸洗残留物不停留在钢丝表 面。酸洗很重要,不好的酸洗会造成不好的镀层,会造成大量的废品。