混凝土离析的原因
混凝土离析
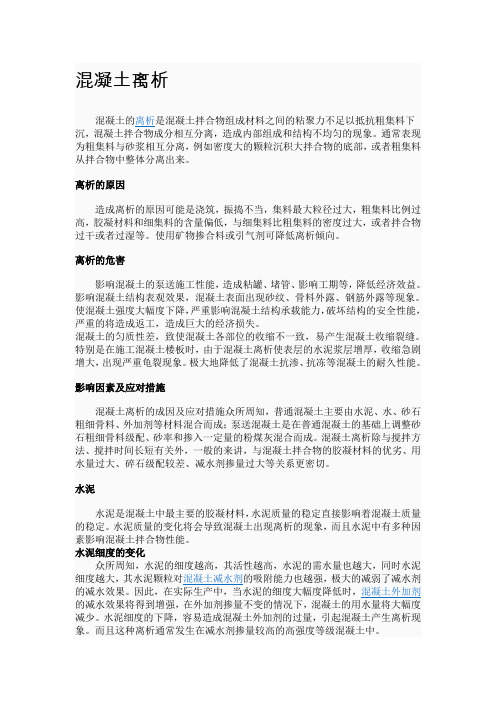
混凝土离析混凝土的离析是混凝土拌合物组成材料之间的粘聚力不足以抵抗粗集料下沉,混凝土拌合物成分相互分离,造成内部组成和结构不均匀的现象。
通常表现为粗集料与砂浆相互分离,例如密度大的颗粒沉积大拌合物的底部,或者粗集料从拌合物中整体分离出来。
离析的原因造成离析的原因可能是浇筑,振捣不当,集料最大粒径过大,粗集料比例过高,胶凝材料和细集料的含量偏低,与细集料比粗集料的密度过大,或者拌合物过干或者过湿等。
使用矿物掺合料或引气剂可降低离析倾向。
离析的危害影响混凝土的泵送施工性能,造成粘罐、堵管、影响工期等,降低经济效益。
影响混凝土结构表观效果,混凝土表面出现砂纹、骨料外露、钢筋外露等现象。
使混凝土强度大幅度下降,严重影响混凝土结构承载能力,破坏结构的安全性能,严重的将造成返工,造成巨大的经济损失。
混凝土的匀质性差,致使混凝土各部位的收缩不一致,易产生混凝土收缩裂缝。
特别是在施工混凝土楼板时,由于混凝土离析使表层的水泥浆层增厚,收缩急剧增大,出现严重龟裂现象。
极大地降低了混凝土抗渗、抗冻等混凝土的耐久性能。
影响因素及应对措施混凝土离析的成因及应对措施众所周知,普通混凝土主要由水泥、水、砂石粗细骨料、外加剂等材料混合而成;泵送混凝土是在普通混凝土的基础上调整砂石粗细骨料级配、砂率和掺入一定量的粉煤灰混合而成。
混凝土离析除与搅拌方法、搅拌时间长短有关外,一般的来讲,与混凝土拌合物的胶凝材料的优劣、用水量过大、碎石级配较差、减水剂掺量过大等关系更密切。
水泥水泥是混凝土中最主要的胶凝材料,水泥质量的稳定直接影响着混凝土质量的稳定。
水泥质量的变化将会导致混凝土出现离析的现象,而且水泥中有多种因素影响混凝土拌合物性能。
水泥细度的变化众所周知,水泥的细度越高,其活性越高,水泥的需水量也越大,同时水泥细度越大,其水泥颗粒对混凝土减水剂的吸附能力也越强,极大的减弱了减水剂的减水效果。
因此,在实际生产中,当水泥的细度大幅度降低时,混凝土外加剂的减水效果将得到增强,在外加剂掺量不变的情况下,混凝土的用水量将大幅度减少。
混凝土离析的原因和预防

混凝土离析的原因和预防混凝土离析的原因和预防摘要:对混凝土离析原因的分析并有针对性的采取预防措施从而保证混凝土质量。
关键词:混凝土离析原因分析预防措施。
混凝土离析的原因:一是原材料的质量和配合比欠妥;二是操作方法不正确(包括搅拌、运输、浇筑和振捣)。
实践证明混凝土离析多是由于操作不当造成的。
混凝土离析对混凝土的强度、耐久性和匀质性都会造成影响同时也给混凝土浇筑入模和振捣带来不便是造成混凝土蜂窝麻面的主要原因也是造成混凝土不均匀收缩的内在原因。
分层、离析和泌水是混凝土和易性不佳的典型现象。
分层是离析造成的结果泌水是离析的一种表现形式。
混凝土的离析是指各组分分离形成不均匀和失去连续性的现象这是由构成混合料的各种固体颗粒大小和密度不同引起的构件形状和操作方法的差异会使它们之间产生不同的运动产生不同的位移。
例如柱子和墙体等竖直构件往往粗骨料下沉水泥浆上浮上下强度不一造成上弱下强而上部下是与水平构件(梁、板接头的部位或是施工缝部位、节点弯矩所在部位在结构上形成薄弱环节对结构的整体性造成不利影响。
现将预防混凝土离析的措施介绍如下:一、把好搅拌关为了获得质量优良的混凝土要正确选择搅拌机并且制定搅拌制度也就是搅拌时间、投料顺序、进料容量等。
在实践中最容易忽略的是搅拌时间的控制。
搅拌时间过短拌和不均匀会降低混凝土的和易性;搅拌时间过长不仅会影响搅拌机的生产效率也会降低水泥浆的胶凝性使混凝土的和易性降低。
混凝土搅拌时间不应小于规定的最短时间在操作时机手如果没有钟表可以搅拌机的转数为准。
必须使水泥砂浆中没有结块的水泥团和砂浆团使水泥砂浆完全包裹住石子。
因为骨料是干涩无流动性的水泥砂浆作为润滑剂可使混凝土具有流动性和可塑性减小骨料颗粒间的相对阻力。
二、把好装车关混凝土由搅拌机装入手推车或料斗时应尽量使搅拌机的出料板仅位于装载器的中间并使出料板可以调整倾斜度以防止“石窝”和“砂窝”的出现(图1)。
三、把好运输关用手推车、吊斗、料斗或漏斗运输混凝土时应防止振动道路要平坦吊运要平稳要走最短路线用最短时间运输。
混凝土离析原因及危害
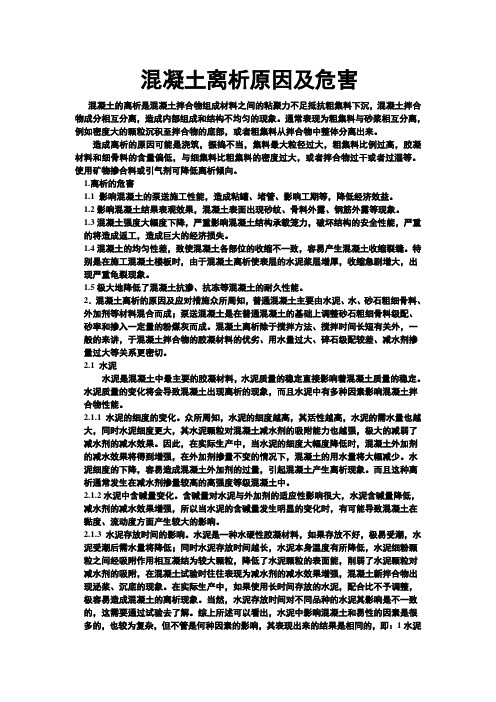
混凝土离析原因及危害混凝土的离析是混凝土拌合物组成材料之间的粘聚力不足抵抗粗集料下沉,混凝土拌合物成分相互分离,造成内部组成和结构不均匀的现象。
通常表现为粗集料与砂浆相互分离,例如密度大的颗粒沉积至拌合物的底部,或者粗集料从拌合物中整体分离出来。
造成离析的原因可能是浇筑,振捣不当,集料最大粒径过大,粗集料比例过高,胶凝材料和细骨料的含量偏低,与细集料比粗集料的密度过大,或者拌合物过干或者过湿等。
使用矿物掺合料或引气剂可降低离析倾向。
1.离析的危害1.1 影响混凝土的泵送施工性能,造成粘罐、堵管、影响工期等,降低经济效益。
1.2影响混凝土结果表观效果,混凝土表面出现砂纹、骨料外露、钢筋外露等现象。
1.3混凝土强度大幅度下降,严重影响混凝土结构承载笼力,破坏结构的安全性能,严重的将造成返工,造成巨大的经济损失。
1.4混凝土的均匀性差,致使混凝土各部位的收缩不一致,容易产生混凝土收缩裂缝。
特别是在施工混凝土楼板时,由于混凝土离析使表层的水泥浆层增厚,收缩急剧增大,出现严重龟裂现象。
1.5极大地降低了混凝土抗渗、抗冻等混凝土的耐久性能。
2.混凝土离析的原因及应对措施众所周知,普通混凝土主要由水泥、水、砂石粗细骨料、外加剂等材料混合而成;泵送混凝土是在普通混凝土的基础上调整砂石粗细骨料级配、砂率和掺入一定量的粉煤灰而成。
混凝土离析除于搅拌方法、搅拌时间长短有关外,一般的来讲,于混凝土拌合物的胶凝材料的优劣、用水量过大、碎石级配较差、减水剂掺量过大等关系更密切。
2.1 水泥水泥是混凝土中最主要的胶凝材料,水泥质量的稳定直接影响着混凝土质量的稳定。
水泥质量的变化将会导致混凝土出现离析的现象,而且水泥中有多种因素影响混凝土拌合物性能。
2.1.1 水泥的细度的变化。
众所周知,水泥的细度越高,其活性越高,水泥的需水量也越大,同时水泥细度更大,其水泥颗粒对混凝土减水剂的吸附能力也越强,极大的减弱了减水剂的减水效果。
因此,在实际生产中,当水泥的细度大幅度降低时,混凝土外加剂的减水效果将得到增强,在外加剂掺量不变的情况下,混凝土的用水量将大幅减少。
混凝土离析原因及危害
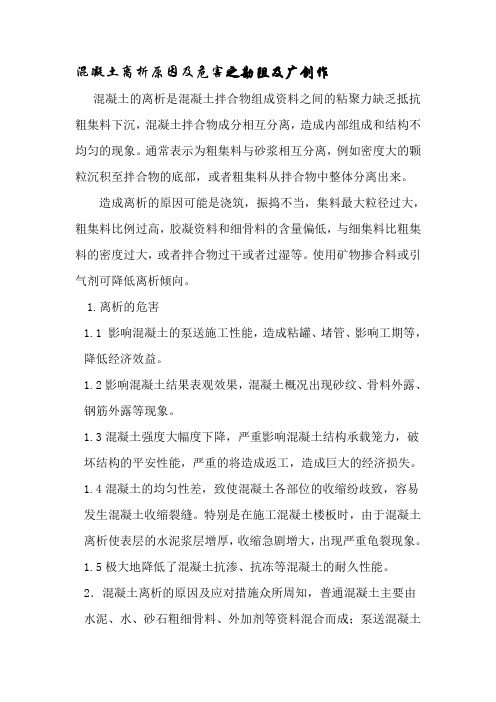
混凝土离析原因及危害之勘阻及广创作混凝土的离析是混凝土拌合物组成资料之间的粘聚力缺乏抵抗粗集料下沉,混凝土拌合物成分相互分离,造成内部组成和结构不均匀的现象。
通常表示为粗集料与砂浆相互分离,例如密度大的颗粒沉积至拌合物的底部,或者粗集料从拌合物中整体分离出来。
造成离析的原因可能是浇筑,振捣不当,集料最大粒径过大,粗集料比例过高,胶凝资料和细骨料的含量偏低,与细集料比粗集料的密度过大,或者拌合物过干或者过湿等。
使用矿物掺合料或引气剂可降低离析倾向。
1.离析的危害1.1 影响混凝土的泵送施工性能,造成粘罐、堵管、影响工期等,降低经济效益。
1.2影响混凝土结果表观效果,混凝土概况出现砂纹、骨料外露、钢筋外露等现象。
1.3混凝土强度大幅度下降,严重影响混凝土结构承载笼力,破坏结构的平安性能,严重的将造成返工,造成巨大的经济损失。
1.4混凝土的均匀性差,致使混凝土各部位的收缩纷歧致,容易发生混凝土收缩裂缝。
特别是在施工混凝土楼板时,由于混凝土离析使表层的水泥浆层增厚,收缩急剧增大,出现严重龟裂现象。
1.5极大地降低了混凝土抗渗、抗冻等混凝土的耐久性能。
2.混凝土离析的原因及应对措施众所周知,普通混凝土主要由水泥、水、砂石粗细骨料、外加剂等资料混合而成;泵送混凝土是在普通混凝土的基础上调整砂石粗细骨料级配、砂率和掺入一定量的粉煤灰而成。
混凝土离析除于搅拌方法、搅拌时间长短有关外,一般的来讲,于混凝土拌合物的胶凝资料的优劣、用水量过大、碎石级配较差、减水剂掺量过大等关系更密切。
2.1 水泥水泥是混凝土中最主要的胶凝资料,水泥质量的稳定直接影响着混凝土质量的稳定。
水泥质量的变更将会导致混凝土出现离析的现象,而且水泥中有多种因素影响混凝土拌合物性能。
2.1.1 水泥的细度的变更。
众所周知,水泥的细度越高,其活性越高,水泥的需水量也越大,同时水泥细度更大,其水泥颗粒对混凝土减水剂的吸附能力也越强,极大的减弱了减水剂的减水效果。
混凝土离析的原因及补救方法
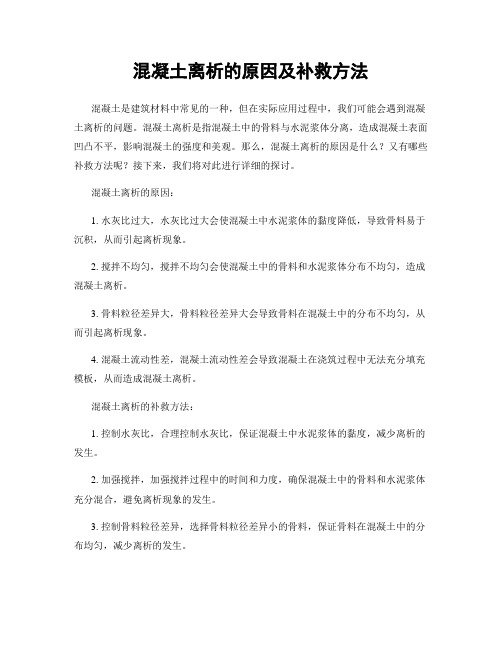
混凝土离析的原因及补救方法混凝土是建筑材料中常见的一种,但在实际应用过程中,我们可能会遇到混凝土离析的问题。
混凝土离析是指混凝土中的骨料与水泥浆体分离,造成混凝土表面凹凸不平,影响混凝土的强度和美观。
那么,混凝土离析的原因是什么?又有哪些补救方法呢?接下来,我们将对此进行详细的探讨。
混凝土离析的原因:1. 水灰比过大,水灰比过大会使混凝土中水泥浆体的黏度降低,导致骨料易于沉积,从而引起离析现象。
2. 搅拌不均匀,搅拌不均匀会使混凝土中的骨料和水泥浆体分布不均匀,造成混凝土离析。
3. 骨料粒径差异大,骨料粒径差异大会导致骨料在混凝土中的分布不均匀,从而引起离析现象。
4. 混凝土流动性差,混凝土流动性差会导致混凝土在浇筑过程中无法充分填充模板,从而造成混凝土离析。
混凝土离析的补救方法:1. 控制水灰比,合理控制水灰比,保证混凝土中水泥浆体的黏度,减少离析的发生。
2. 加强搅拌,加强搅拌过程中的时间和力度,确保混凝土中的骨料和水泥浆体充分混合,避免离析现象的发生。
3. 控制骨料粒径差异,选择骨料粒径差异小的骨料,保证骨料在混凝土中的分布均匀,减少离析的发生。
4. 使用外加剂,在混凝土中添加流动性好的外加剂,提高混凝土的流动性,避免离析现象的发生。
5. 注意施工操作,在混凝土浇筑过程中,注意控制浇筑速度和振捣方式,确保混凝土充分填充模板,避免离析的发生。
总结:混凝土离析是混凝土施工中常见的问题,其原因主要包括水灰比过大、搅拌不均匀、骨料粒径差异大、混凝土流动性差等。
针对这些原因,我们可以通过控制水灰比、加强搅拌、控制骨料粒径差异、使用外加剂、注意施工操作等补救方法来减少混凝土离析的发生,保证混凝土施工质量。
希望本文的内容能够对大家有所帮助,谢谢阅读!。
混凝土离析原因及危害
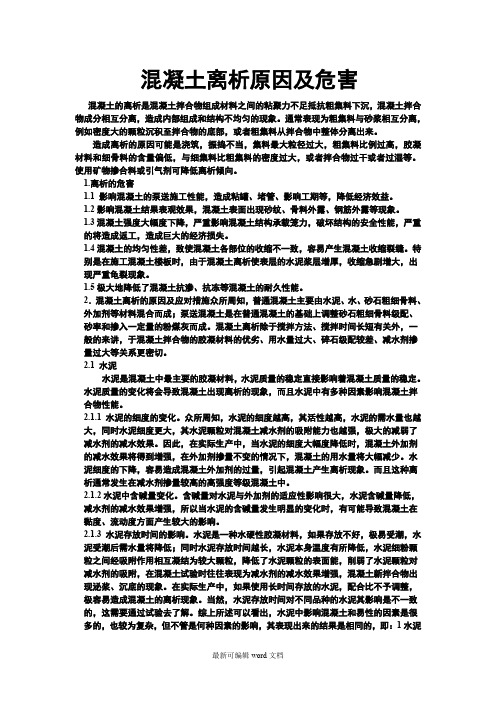
混凝土离析原因及危害混凝土的离析是混凝土拌合物组成材料之间的粘聚力不足抵抗粗集料下沉,混凝土拌合物成分相互分离,造成内部组成和结构不均匀的现象。
通常表现为粗集料与砂浆相互分离,例如密度大的颗粒沉积至拌合物的底部,或者粗集料从拌合物中整体分离出来。
造成离析的原因可能是浇筑,振捣不当,集料最大粒径过大,粗集料比例过高,胶凝材料和细骨料的含量偏低,与细集料比粗集料的密度过大,或者拌合物过干或者过湿等。
使用矿物掺合料或引气剂可降低离析倾向。
1.离析的危害1.1 影响混凝土的泵送施工性能,造成粘罐、堵管、影响工期等,降低经济效益。
1.2影响混凝土结果表观效果,混凝土表面出现砂纹、骨料外露、钢筋外露等现象。
1.3混凝土强度大幅度下降,严重影响混凝土结构承载笼力,破坏结构的安全性能,严重的将造成返工,造成巨大的经济损失。
1.4混凝土的均匀性差,致使混凝土各部位的收缩不一致,容易产生混凝土收缩裂缝。
特别是在施工混凝土楼板时,由于混凝土离析使表层的水泥浆层增厚,收缩急剧增大,出现严重龟裂现象。
1.5极大地降低了混凝土抗渗、抗冻等混凝土的耐久性能。
2.混凝土离析的原因及应对措施众所周知,普通混凝土主要由水泥、水、砂石粗细骨料、外加剂等材料混合而成;泵送混凝土是在普通混凝土的基础上调整砂石粗细骨料级配、砂率和掺入一定量的粉煤灰而成。
混凝土离析除于搅拌方法、搅拌时间长短有关外,一般的来讲,于混凝土拌合物的胶凝材料的优劣、用水量过大、碎石级配较差、减水剂掺量过大等关系更密切。
2.1 水泥水泥是混凝土中最主要的胶凝材料,水泥质量的稳定直接影响着混凝土质量的稳定。
水泥质量的变化将会导致混凝土出现离析的现象,而且水泥中有多种因素影响混凝土拌合物性能。
2.1.1 水泥的细度的变化。
众所周知,水泥的细度越高,其活性越高,水泥的需水量也越大,同时水泥细度更大,其水泥颗粒对混凝土减水剂的吸附能力也越强,极大的减弱了减水剂的减水效果。
因此,在实际生产中,当水泥的细度大幅度降低时,混凝土外加剂的减水效果将得到增强,在外加剂掺量不变的情况下,混凝土的用水量将大幅减少。
混凝土离析原因及危害
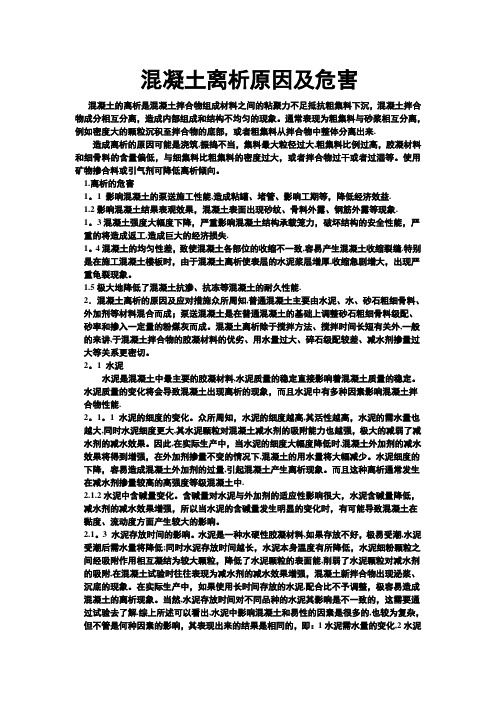
混凝土离析原因及危害混凝土的离析是混凝土拌合物组成材料之间的粘聚力不足抵抗粗集料下沉,混凝土拌合物成分相互分离,造成内部组成和结构不均匀的现象。
通常表现为粗集料与砂浆相互分离,例如密度大的颗粒沉积至拌合物的底部,或者粗集料从拌合物中整体分离出来.造成离析的原因可能是浇筑,振捣不当,集料最大粒径过大,粗集料比例过高,胶凝材料和细骨料的含量偏低,与细集料比粗集料的密度过大,或者拌合物过干或者过湿等。
使用矿物掺合料或引气剂可降低离析倾向。
1.离析的危害1。
1 影响混凝土的泵送施工性能,造成粘罐、堵管、影响工期等,降低经济效益.1.2影响混凝土结果表观效果,混凝土表面出现砂纹、骨料外露、钢筋外露等现象.1。
3混凝土强度大幅度下降,严重影响混凝土结构承载笼力,破坏结构的安全性能,严重的将造成返工,造成巨大的经济损失.1。
4混凝土的均匀性差,致使混凝土各部位的收缩不一致,容易产生混凝土收缩裂缝.特别是在施工混凝土楼板时,由于混凝土离析使表层的水泥浆层增厚,收缩急剧增大,出现严重龟裂现象。
1.5极大地降低了混凝土抗渗、抗冻等混凝土的耐久性能.2.混凝土离析的原因及应对措施众所周知,普通混凝土主要由水泥、水、砂石粗细骨料、外加剂等材料混合而成;泵送混凝土是在普通混凝土的基础上调整砂石粗细骨料级配、砂率和掺入一定量的粉煤灰而成。
混凝土离析除于搅拌方法、搅拌时间长短有关外,一般的来讲,于混凝土拌合物的胶凝材料的优劣、用水量过大、碎石级配较差、减水剂掺量过大等关系更密切。
2。
1 水泥水泥是混凝土中最主要的胶凝材料,水泥质量的稳定直接影响着混凝土质量的稳定。
水泥质量的变化将会导致混凝土出现离析的现象,而且水泥中有多种因素影响混凝土拌合物性能.2。
1。
1 水泥的细度的变化。
众所周知,水泥的细度越高,其活性越高,水泥的需水量也越大,同时水泥细度更大,其水泥颗粒对混凝土减水剂的吸附能力也越强,极大的减弱了减水剂的减水效果。
因此,在实际生产中,当水泥的细度大幅度降低时,混凝土外加剂的减水效果将得到增强,在外加剂掺量不变的情况下,混凝土的用水量将大幅减少。
混凝土离析原因及危害

混凝土离析原因及危害之邯郸勺丸创作混凝土的离析是混凝土拌合物组成资料之间的粘聚力缺乏抵抗粗集料下沉,混凝土拌合物成分相互别离,造成内部组成和结构不均匀的现象.通常表示为粗集料与砂浆相互别离,例如密度大的颗粒沉积至拌合物的底部,或者粗集料从拌合物中整体别离出来.造成离析的原因可能是浇筑,振捣不当,集料最大粒径过大,粗集料比例过高,胶凝资料和细骨料的含量偏低,与细集料比粗集料的密度过大,或者拌合物过干或者过湿等.使用矿物掺合料或引气剂可降低离析倾向.1.离析的危害1.1 影响混凝土的泵送施工性能,造成粘罐、堵管、影响工期等,降低经济效益.1.2影响混凝土结果表不雅效果,混凝土概略出现砂纹、骨料外露、钢筋外露等现象.1.3混凝土强度大幅度下降,严重影响混凝土结构承载笼力,破坏结构的平安性能,严重的将造成返工,造成巨大的经济损失.1.4混凝土的均匀性差,致使混凝土各部位的收缩不一致,容易产生混凝土收缩裂缝.特别是在施工混凝土楼板时,由于混凝土离析使表层的水泥浆层增厚,收缩急剧增大,出现严重龟裂现象. 1.5极大地降低了混凝土抗渗、抗冻等混凝土的耐久性能. 2.混凝土离析的原因及应对措施众所周知,普通混凝土主要由水泥、水、砂石粗细骨料、外加剂等资料混合而成;泵送混凝土是在普通混凝土的基础上调整砂石粗细骨料级配、砂率和掺入一定量的粉煤灰而成.混凝土离析除于搅拌办法、搅拌时间长短有关外,一般的来讲,于混凝土拌合物的胶凝资料的优劣、用水量过大、碎石级配较差、减水剂掺量过大等关系更密切.2.1 水泥水泥是混凝土中最主要的胶凝资料,水泥质量的稳定直接影响着混凝土质量的稳定.水泥质量的变更将会导致混凝土出现离析的现象,并且水泥中有多种因素影响混凝土拌合物性能.2.1.1 水泥的细度的变更.众所周知,水泥的细度越高,其活性越高,水泥的需水量也越大,同时水泥细度更大,其水泥颗粒对混凝土减水剂的吸附能力也越强,极大的减弱了减水剂的减水效果.因此,在实际生产中,当水泥的细度大幅度降低时,混凝土外加剂的减水效果将得到增强,在外加剂掺量不变的情况下,混凝土的用水量将大幅减少.水泥细度的下降,容易造成混凝土外加剂的过量,引起混凝土产生离析现象.并且这种离析通常产生在减水剂掺量较高的高强度等级混凝土中.2.1.2水泥中含碱量变更.含碱量对水泥与外加剂的适应性影响很大,水泥含碱量降低,减水剂的减水效果增强,所以当水泥的含碱量产生明显的变更时,有可能导致混凝土在黏度、流动度方面产生较大的影响.2.1.3 水泥存放时间的影响.水泥是一种水硬性胶凝资料,如果存放欠好,极易受潮,水泥受潮后需水量将降低;同时水泥存放时间越长,水泥自己温度有所降低,水泥细粉颗粒之间经吸附作用相互凝结为较大颗粒,降低了水泥颗粒的概略能,削弱了水泥颗粒对减水剂的吸附,在混凝土试验时往往表示为减水剂的减水效果增强,混凝土新拌合物出现泌浆、沉底的现象.在实际生产中,如果使用长时间存放的水泥,配合比不予调整,极容易造成混凝土的离析现象.当然,水泥存放时间对不合品种的水泥其影响是不一致的,这需要通过试验去了解.综上所述可以看出,水泥中影响混凝土和易性的因素是很多的,也较为庞杂,但不管是何种因素的影响,其表示出来的结果是相同的,即:1水泥需水量的变更,2水泥与外加剂的适应性变更.因此,如果是因为水泥的原因导致混凝土的离析,一般的都可以采纳以下措施解决:1水泥进场后,必须按要求试验项目进行检测,特别注意水泥的需水量情况,发明需水量异常时,及时做水泥与现使用的外加剂的适应性试验.需要时重新做混凝土配合比试验.2在包管混凝土水灰比不变的前提下(基天性包管混凝土的28d强度),适当的调整减水剂的用量.3在包管强度的基础上,改用粉煤灰等掺合料的用量较大的配合比进行生产(商品混凝土公司具备相同强度等级的不合配比),这必须以试验为基础.4用Ⅰ、Ⅱ粉煤灰等少量取代水泥,将能很好的控制混凝土的离析现象,改良混凝土的和易性.2.2外加剂混凝土中使用的外加剂,大多是由减水剂同其他产品如引气剂、缓凝剂、保塑性等复合而成的多功效产品,是泵送混凝土不成或缺的重要资料,外加剂的掺入极大地改良混凝土拌合物的性能,但外加剂使用不当将可能导致混凝土的离析.1如果混凝土减水剂的掺量过大,减水率过高,单方混凝土的用水量减少,有可能使减水剂在搅拌机内没有充分阐扬作用,而在混凝土运输过程中不竭的产生作用,导致使混凝土到现场的塌落度大于出机时的塌落度.这种情况极易造成混凝土的严重离析.并且表示在高强度等级的混凝土中,对混凝土的危害极大.2外加剂中缓凝组分、保塑组分掺量过大,特别磷酸盐或糖类过量,也容易造成混凝土出现离析现象.当由于外加剂的原因造成混凝土的离析时,可以从以下几方面进行调整:1适当调整配合比,降低减水剂的用量;2在混凝土外加剂中复合一定量的增稠剂;3在外加剂中复合一定量的引气剂,可增强混凝土的粘聚性,提高混凝土的抗离析性;4在混凝土试配时,应使混凝土在静态的条件下有20~30mm的塌落度损失(1h),在实际生产中混凝土不容易出现离析现象.2.3 粉煤灰粉煤灰是混凝土的重要的掺合料之一,虽然用量很少,但在混凝土中掺入适量粉煤灰能极大改良混凝土和易性、密实性及强度性能.优质的粉煤灰细度在20~8规模内,是配制混凝土的理想资料,能取代10%~30%的水泥用量,极大的降低了混凝土生产成本.若粉煤灰质量动摇较大,增加了混凝土质量控制的难度,有时会造成混凝土出现离析的情况.1当粉煤灰的质量突然变好时(如细度从19%变成4%),粉煤灰的需水量降低很大,容易造成混凝土出现突然离析的现象;2同样当粉煤灰的质量突然变差时(如细度从19%变成38%),由于粉煤灰的很大一部分重量已失去胶结料的功效,因而外加剂相对胶结料掺量实际上已经提高了,所以会出现混凝土的离析现象对于粉煤灰应采纳如下措施:1加强检测,最好能对每车进场的粉煤灰进行检测,对不合格的资料坚决不克不及进场,起到预防作用.2调整粉煤灰的用量,选用掺量较低的配合比进行生产.3当粉煤灰质量较好情况,可适当的减少用水量,加强搅拌.或选用外加剂掺量较低的配合比进行生产.2.4砂、石骨料砂石料是混凝土中用量最大的资料,砂石料的质量直接影响混凝土的质量,砂石质量的动摇容易造成混凝土的离析,并且其造成离析的原因是多方面的.1碎石粒径增大、级配变差、单一级配都容易造成混凝土的离析现象.2砂子中得含石(粒径大于9.75mm的颗粒)量过大、特别是含片状石屑量过大将严重影响混凝土的和易性,导致混凝土的严重离析.3砂石的含水率过高(特别是砂子含水率过高,大于10%),将使混凝土的质量难以控制,容易出现混凝土离析现象.由于砂子中含水过大,砂子含水处在过饱和状态,当混凝土拌合料在搅拌机中搅拌时,砂子表层毛细管中得含水不克不及够及时的释放出来,因此在搅拌时容易使拌合水用量过大,同时混凝土在运输过程中,骨料毛细管中的水不竭的往外释放,破坏了骨料与水泥浆的粘结,造成混凝土的离析泌水.4砂石的含泥量过大将使水泥浆同骨料的粘结力降低,水泥浆对骨料的包裹能力下降,导致骨料的别离,引起混凝土离析现象.对于骨料的原因导致混凝土离析的现象,可以采纳以下措施进行调整.1为避免因骨料的问题造成混凝土的离析问题,首先应以预防为主,严格骨料进场检查制度,包管骨料的质量.2针对以上原因的第1条原因,可适当的提高砂率来调整混凝土配合比,解决离析问题.3对于因骨料中含片状石屑过大造成的离析问题,单靠调整砂率是不克不及解决问题的,应提高混凝土胶结资料(特别是掺合料的用量),同时调整外加剂用量.4对于应骨料含水率问题造成的混凝土离析问题应采纳延长搅拌时间的手段来解决.提高粉煤灰等掺合料的用量对控制这类离析现象也很有效果.2.5其他.以上阐发了许多有关混凝土离析的原因,但造成混凝土离析的原因远不止这些,如水泥用量、水泥及掺合料品种、计量等问题都是引起混凝土离析的原因.在平时任务中,应注意积累,加强细节的办理,遇到问题及时解决.。
自密实混凝土离析的原因

自密实混凝土离析的原因自密实混凝土离析是指混凝土在浇筑或养护过程中出现的颗粒分离现象。
混凝土作为一种常用的建筑材料,在工程中承担着重要的结构和承载功能。
然而,由于多种因素的影响,混凝土在施工或使用过程中可能会出现离析现象,影响其力学性能和使用寿命。
混凝土的离析主要包括水分离析和颗粒离析两种情况。
水分离析是指混凝土中水分与水泥浆体分离,形成水集聚现象。
这种现象通常发生在混凝土浇筑后,由于浇筑中的振动或流动,较轻的颗粒和水分被甩离,而较重的颗粒则沉积在底部。
导致水分离析的原因主要有以下几点:1. 水胶比过高:水胶比是指水与水泥的质量比,直接影响混凝土的流动性和凝结性。
如果水胶比过高,混凝土中的水分较多,容易发生离析现象。
2. 施工振动不均匀:在混凝土浇筑过程中,振动是为了排除混凝土中的气泡和使其密实。
如果振动不均匀,部分区域的混凝土就会发生离析。
3. 浇筑速度过快:如果混凝土浇筑速度过快,就会导致浇筑面上的水分和较轻颗粒在振动中分离出来。
而颗粒离析是指混凝土中的骨料和水泥分离,造成颗粒的集聚现象。
这种现象通常在混凝土的表面或较干燥的部分发生,导致混凝土表面粗糙、质地不均匀。
颗粒离析的原因主要有以下几点:1. 骨料过粗或过细:骨料的粒径对混凝土的流动性和凝结性有直接影响。
如果骨料过粗或过细,容易发生颗粒离析。
2. 施工振动不当:振动是为了排除混凝土中的气泡,使其更加密实。
如果振动不当,就会导致骨料的分离和集聚。
3. 水胶比过低:水胶比过低会导致混凝土凝结不良,骨料与水泥难以黏结,容易发生颗粒离析。
为了减少混凝土的离析现象,可以采取以下措施:1. 控制水胶比:合理控制水胶比可以增加混凝土的流动性和凝结性,减少水分离析的可能性。
2. 均匀振动:在混凝土的浇筑和振动过程中,要保证振动均匀,避免出现局部振动不足或过度的情况。
3. 合理选择骨料:选择合适的骨料粒径,避免过粗或过细的骨料导致颗粒离析。
4. 控制浇筑速度:合理控制混凝土的浇筑速度,避免过快的浇筑速度导致水分和颗粒的离析。
混凝土塌落度及泌水离析问题的原因及解决方法

混凝土塌落度及了泌水离析问题的原因及解决方法一、泵送混凝土塌落度损失、坍落度不稳定问题的原因及解决方法1 产生原因(1) 混凝土外加剂与水泥适应性不好引起混凝土塌落度损失快。
(2) 混凝土外加剂掺量不够,缓凝、保塑效果不理想。
(3) 天气炎热,某些外加剂在高温下失效;水分蒸发快;气泡外溢造成新拌混凝土塌落度损失快。
(4) 初始混凝土塌落度太小,单位用水量太少。
(5) 工地现场与搅拌站协调不好,使罐车压车、塞车时间太长,导致混凝土塌落度损失过大。
(6)混凝土搅拌称量系统计量误差大,不稳定。
(7)粗、细骨料含水率变化。
(8)水泥混仓存放,混合使用。
2 解决途径(1) 调整混凝土外加剂配方,使其与水泥相适应。
施工前,务必做混凝土外加剂与水泥适应性试验。
(2) 调整砼配合比,提高或降低砂率、用水量,将混凝土初始塌落度调整到200mm以上。
(3) 掺加适量粉煤灰,代替部分水泥。
(4) 适量加大混凝土外加剂掺量, 外加剂中调整缓凝成份(尤其在温度比平常气温高得多时)。
(5) 防止水分蒸发过快、气泡外溢过快。
(6) 选用矿渣水泥或火山灰质水泥。
(7) 改善混凝土运输车的保水、降温装置。
(8) 计量设备的精度应满足有关规定,并具有法定计量部门签发的有效合格证,加强自检,确保计量准确。
(9) 加强骨料含水率的检测,变化时,及时调整配合比。
(10)进库水泥应按生产厂家、品种和标号分别贮存、使用。
3 总结经验针对泵送混凝土特别是泵送混凝土以及水下灌注桩基混凝土坍落度损失的问题。
通过学习摸索试验总结出了一套结合实际情况解决问题的办法。
如沟通外加剂厂家改善和调整外加剂中的缓凝成份;调整混凝土的施工时间,尽量避免不在高温情况下施工;在施工便道路况差路途远的情况下采用外加剂的二次投料;使用大掺量粉煤灰混凝土配合比施工等。
使混凝土坍落度损失这一棘手问题,得到较大缓解。
无论何种原因导致的坍落度变小造成无法泵送或是满足不了施工要求的坍落度的情况我们都能用外加剂进行调节使之达到所需坍落度,杜绝随意加水增大坍落度的不良习惯从根本上确定了混凝土的质量!二、混凝土易出现泌水、离析问题的原因及解决方法1 产生原因(1) 水泥细度大时易泌水,水泥中C3A含量低易泌水,水泥标准稠度用水量小易泌水。
混凝土离析原因及危害
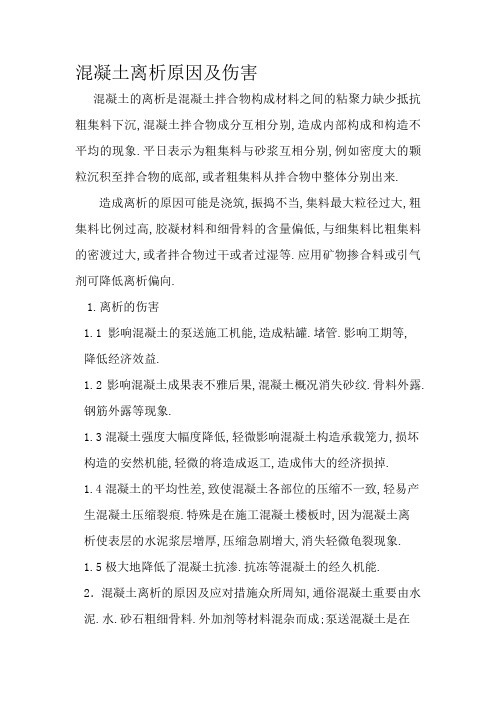
混凝土离析原因及伤害混凝土的离析是混凝土拌合物构成材料之间的粘聚力缺少抵抗粗集料下沉,混凝土拌合物成分互相分别,造成内部构成和构造不平均的现象.平日表示为粗集料与砂浆互相分别,例如密度大的颗粒沉积至拌合物的底部,或者粗集料从拌合物中整体分别出来.造成离析的原因可能是浇筑,振捣不当,集料最大粒径过大,粗集料比例过高,胶凝材料和细骨料的含量偏低,与细集料比粗集料的密渡过大,或者拌合物过干或者过湿等.应用矿物掺合料或引气剂可降低离析偏向.1.离析的伤害1.1 影响混凝土的泵送施工机能,造成粘罐.堵管.影响工期等,降低经济效益.1.2影响混凝土成果表不雅后果,混凝土概况消失砂纹.骨料外露.钢筋外露等现象.1.3混凝土强度大幅度降低,轻微影响混凝土构造承载笼力,损坏构造的安然机能,轻微的将造成返工,造成伟大的经济损掉.1.4混凝土的平均性差,致使混凝土各部位的压缩不一致,轻易产生混凝土压缩裂痕.特殊是在施工混凝土楼板时,因为混凝土离析使表层的水泥浆层增厚,压缩急剧增大,消失轻微龟裂现象.1.5极大地降低了混凝土抗渗.抗冻等混凝土的经久机能.2.混凝土离析的原因及应对措施众所周知,通俗混凝土重要由水泥.水.砂石粗细骨料.外加剂等材料混杂而成;泵送混凝土是在通俗混凝土的基本上调剂砂石粗细骨料级配.砂率和掺入必定量的粉煤灰而成.混凝土离析除于搅拌办法.搅拌时光长短有关外,一般的来讲,于混凝土拌合物的胶凝材料的好坏.用水量过大.碎石级配较差.减水剂掺量过大等关系更亲密.2.1 水泥水泥是混凝土中最重要的胶凝材料,水泥质量的稳固直接影响着混凝土质量的稳固.水泥质量的变更将会导致混凝土消失离析的现象,并且水泥中有多种身分影响混凝土拌合物机能.水泥的细度的变更.众所周知,水泥的细度越高,其活性越高,水泥的需水量也越大,同时水泥细度更大,其水泥颗粒对混凝土减水剂的吸附才能也越强,极大的减弱了减水剂的减水后果.是以,在现实临盆中,当水泥的细度大幅度降低时,混凝土外加剂的减水后果将得到加强,在外加剂掺量不变的情形下,混凝土的用水量将大幅削减.水泥细度的降低,轻易造成混凝土外加剂的过量,引起混凝土产生离析现象.并且这种离析平日产生在减水剂掺量较高的高强度等级混凝土中.水泥中含碱量变更.含碱量对水泥与外加剂的顺应性影响很大,水泥含碱量降低,减水剂的减水后果加强,所以当水泥的含碱量产生显著的变更时,有可能导致混凝土在黏度.流淌度方面产生较大的影响.水泥存放时光的影响.水泥是一种水硬性胶凝材料,假如存放不好,极易受潮,水泥受潮后需水量将降低;同时水泥存放时光越长,水泥本身温度有所降低,水泥细粉颗粒之间经吸附感化互相凝聚为较大颗粒,降低了水泥颗粒的概况能,减弱了水泥颗粒对减水剂的吸附,在混凝土实验时往往表示为减水剂的减水后果加强,混凝土新拌合物消失泌浆.沉底的现象.在现实临盆中,假如应用长时光存放的水泥,合营比不予调剂,极轻易造成混凝土的离析现象.当然,水泥存放时光对不合品种的水泥其影响是不一致的,这须要经由过程实验去懂得.综上所述可以看出,水泥中影响混凝土和易性的身分是很多的,也较为庞杂,但不管是何种身分的影响,其表示出来的成果是雷同的,即:1水泥需水量的变更,2水泥与外加剂的顺应性变更.是以,假如是因为水泥的原因导致混凝土的离析,一般的都可以采纳以下措施解决:1水泥出场后,必须按请求实验项目进行检测,特殊留意水泥的需水量情形,发明需水量平常时,实时做水泥与现应用的外加剂的顺应性实验.须要时从新做混凝土合营比实验.2在包管混凝土水灰比不变的前提下(基本性包管混凝土的28d强度),恰当的调剂减水剂的用量.3在包管强度的基本上,改用粉煤灰等掺合料的用量较大的合营比进行临盆(商品混凝土公司具备雷同强度等级的不合配比),这必须以实验为基本.4用Ⅰ.Ⅱ粉煤灰等少量代替水泥,将能很好的掌握混凝土的离析现象,改良混凝土的和易性.混凝土中应用的外加剂,大多是由减水剂同其他产品如引气剂.缓凝剂.保塑性等复合而成的多功效产品,是泵送混凝土不成或缺的重要材料,外加剂的掺入极大地改良混凝土拌合物的机能,但外加剂应用不当将可能导致混凝土的离析.1假如混凝土减水剂的掺量过大,减水率过高,单方混凝土的用水量削减,有可能使减水剂在搅拌机内没有充分施展感化,而在混凝土运输进程中不竭的产生感化,导致使混凝土到现场的塌落度大于出机时的塌落度.这种情形极易造成混凝土的轻微离析.并且表示在高强度等级的混凝土中,对混凝土的伤害极大.2外加剂中缓凝组分.保塑组分掺量过大,特殊磷酸盐或糖类过量,也轻易造成混凝土消失离析现象.当因为外加剂的原因造成混凝土的离析时,可以从以下几方面进行调剂:1恰当调剂合营比,降低减水剂的用量;2在混凝土外加剂中复合必定量的增稠剂;3在外加剂中复合必定量的引气剂,可加强混凝土的粘聚性,进步混凝土的抗离析性;4在混凝土试配时,应使混凝土在静态的前提下有20~30mm的塌落度损掉(1h),在现实临盆中混凝土不轻易消失离析现象.2.3 粉煤灰粉煤灰是混凝土的重要的掺合料之一,固然用量很少,但在混凝土中掺入适量粉煤灰能极大改良混凝土和易性.密实性及强度机能.优质的粉煤灰细度在20~8规模内,是配制混凝土的幻想材料,能代替10%~30%的水泥用量,极大的降低了混凝土临盆成本.若粉煤灰质量摇动较大,增长了混凝土质量掌握的难度,有时会造成混凝土消失离析的情形.1当粉煤灰的质量忽然变好时(如细度从19%变成4%),粉煤灰的需水量降低很大,轻易造成混凝土消失忽然离析的现象;2同样当粉煤灰的质量忽然变差时(如细度从19%变成38%),因为粉煤灰的很大一部分重量已掉去胶结料的功效,因而外加剂相对胶结料掺量现实上已经进步了,所以会消失混凝土的离析现象对于粉煤灰应采纳如下措施:1加强检测,最好能对每车出场的粉煤灰进行检测,对不合格的材料果断不克不及出场,起到预防感化.2调剂粉煤灰的用量,选用掺量较低的合营比进行临盆.3当粉煤灰质量较好情形,可恰当的削减用水量,加强搅拌.或选用外加剂掺量较低的合营比进行临盆.2.4砂.石骨料砂石料是混凝土顶用量最大的材料,砂石料的质量直接影响混凝土的质量,砂石质量的摇动轻易造成混凝土的离析,并且其造成离析的原因是多方面的.1碎石粒径增大.级配变差.单一级配都轻易造成混凝土的离析现象.2砂子中得含石(粒径大于9.75mm的颗粒)量过大.特殊是含片状石屑量过大将轻微影响混凝土的和易性,导致混凝土的轻微离析.3砂石的含水率过高(特殊是砂子含水率过高,大于10%),将使混凝土的质量难以掌握,轻易消失混凝土离析现象.因为砂子中含水过大,砂子含水处在过饱和状况,当混凝土拌合料在搅拌机中搅拌时,砂子表层毛细管中得含水不克不及够实时的释放出来,是以在搅拌时轻易使拌合水用量过大,同时混凝土在运输进程中,骨料毛细管中的水不竭的往外释放,损坏了骨料与水泥浆的粘结,造成混凝土的离析泌水.4砂石的含泥量过大将使水泥浆同骨料的粘结力降低,水泥浆对骨料的包裹才能降低,导致骨料的分别,引起混凝土离析现象.对于骨料的原因导致混凝土离析的现象,可以采纳以下措施进行调剂.1为防止因骨料的问题造成混凝土的离析问题,起首应以预防为主,严厉骨料出场检讨轨制,包管骨料的质量.2针对以上原因的第1条原因,可恰当的进步砂率来调剂混凝土合营比,解决离析问题.3对于因骨估中含片状石屑过大造成的离析问题,单靠调剂砂率是不克不及解决问题的,应进步混凝土胶结材料(特殊是掺合料的用量),同时调剂外加剂用量.4对于应骨料含水率问题造成的混凝土离析问题应采纳延伸搅拌时光的手腕来解决.进步粉煤灰等掺合料的用量对掌握这类离析现象也很有后果.2.5其他.以上剖析了很多有关混凝土离析的原因,但造成混凝土离析的原因远不止这些,如水泥用量.水泥及掺合料品种.计量等问题都是引起混凝土离析的原因.在日常平凡工作中,应留意积聚,加强细节的治理,碰到问题实时解决.。
混凝土离析原因及危害
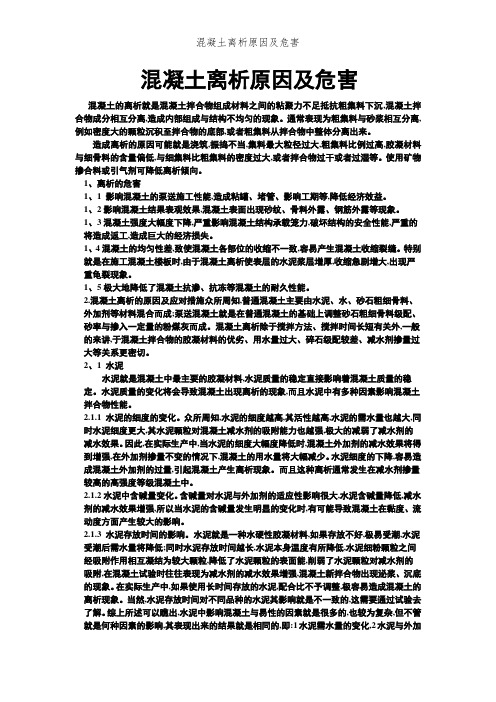
混凝土离析原因及危害混凝土的离析就是混凝土拌合物组成材料之间的粘聚力不足抵抗粗集料下沉,混凝土拌合物成分相互分离,造成内部组成与结构不均匀的现象。
通常表现为粗集料与砂浆相互分离,例如密度大的颗粒沉积至拌合物的底部,或者粗集料从拌合物中整体分离出来。
造成离析的原因可能就是浇筑,振捣不当,集料最大粒径过大,粗集料比例过高,胶凝材料与细骨料的含量偏低,与细集料比粗集料的密度过大,或者拌合物过干或者过湿等。
使用矿物掺合料或引气剂可降低离析倾向。
1、离析的危害1、1 影响混凝土的泵送施工性能,造成粘罐、堵管、影响工期等,降低经济效益。
1、2影响混凝土结果表观效果,混凝土表面出现砂纹、骨料外露、钢筋外露等现象。
1、3混凝土强度大幅度下降,严重影响混凝土结构承载笼力,破坏结构的安全性能,严重的将造成返工,造成巨大的经济损失。
1、4混凝土的均匀性差,致使混凝土各部位的收缩不一致,容易产生混凝土收缩裂缝。
特别就是在施工混凝土楼板时,由于混凝土离析使表层的水泥浆层增厚,收缩急剧增大,出现严重龟裂现象。
1、5极大地降低了混凝土抗渗、抗冻等混凝土的耐久性能。
2.混凝土离析的原因及应对措施众所周知,普通混凝土主要由水泥、水、砂石粗细骨料、外加剂等材料混合而成;泵送混凝土就是在普通混凝土的基础上调整砂石粗细骨料级配、砂率与掺入一定量的粉煤灰而成。
混凝土离析除于搅拌方法、搅拌时间长短有关外,一般的来讲,于混凝土拌合物的胶凝材料的优劣、用水量过大、碎石级配较差、减水剂掺量过大等关系更密切。
2、1 水泥水泥就是混凝土中最主要的胶凝材料,水泥质量的稳定直接影响着混凝土质量的稳定。
水泥质量的变化将会导致混凝土出现离析的现象,而且水泥中有多种因素影响混凝土拌合物性能。
2.1.1 水泥的细度的变化。
众所周知,水泥的细度越高,其活性越高,水泥的需水量也越大,同时水泥细度更大,其水泥颗粒对混凝土减水剂的吸附能力也越强,极大的减弱了减水剂的减水效果。
混凝土离析性能评估标准
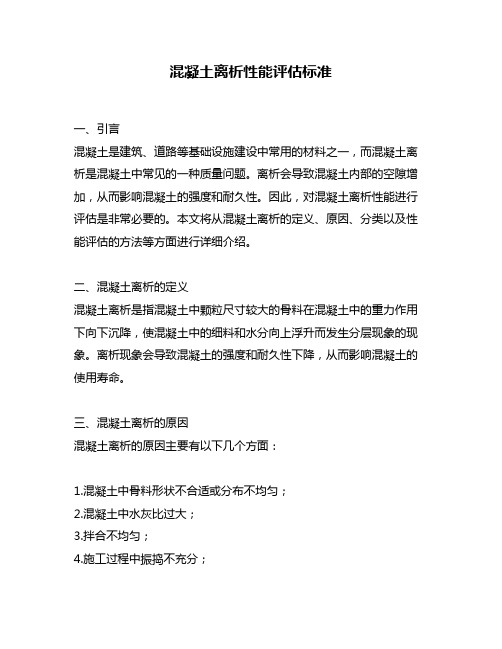
混凝土离析性能评估标准一、引言混凝土是建筑、道路等基础设施建设中常用的材料之一,而混凝土离析是混凝土中常见的一种质量问题。
离析会导致混凝土内部的空隙增加,从而影响混凝土的强度和耐久性。
因此,对混凝土离析性能进行评估是非常必要的。
本文将从混凝土离析的定义、原因、分类以及性能评估的方法等方面进行详细介绍。
二、混凝土离析的定义混凝土离析是指混凝土中颗粒尺寸较大的骨料在混凝土中的重力作用下向下沉降,使混凝土中的细料和水分向上浮升而发生分层现象的现象。
离析现象会导致混凝土的强度和耐久性下降,从而影响混凝土的使用寿命。
三、混凝土离析的原因混凝土离析的原因主要有以下几个方面:1.混凝土中骨料形状不合适或分布不均匀;2.混凝土中水灰比过大;3.拌合不均匀;4.施工过程中振捣不充分;5.温度变化引起的收缩和膨胀;6.混凝土养护不当;7.过度流动性。
四、混凝土离析的分类根据混凝土中骨料的尺寸和密度不同,混凝土离析可以分为以下几种类型:1.重力离析:混凝土中骨料的密度大于混凝土中水浆的密度,骨料会向下沉降,使水浆向上浮升。
2.浮力离析:混凝土中骨料的密度小于混凝土中水浆的密度,骨料会向上浮升,使水浆向下沉降。
3.干缩离析:混凝土中水分蒸发后,混凝土表面变干,使水分向表面移动,造成表面上的混凝土与底部混凝土之间出现空隙,发生干缩离析。
4.温度离析:混凝土在不同温度下收缩和膨胀的速度不同,使混凝土发生分层现象。
五、混凝土离析性能评估的方法混凝土离析性能评估的方法主要包括以下几个方面:1.观察法:通过肉眼观察混凝土表面是否有分层现象,对混凝土离析情况进行初步判断。
2.水浸法:将混凝土样品浸泡在水中,观察是否有细料浮出,从而判断混凝土是否发生离析。
3.压实法:将混凝土样品进行压实,观察是否有分层现象,从而判断混凝土离析情况。
4.超声波检测法:利用超声波探测仪对混凝土进行检测,测量混凝土中声速的变化,从而判断混凝土的离析情况。
混凝土离析原因及危害
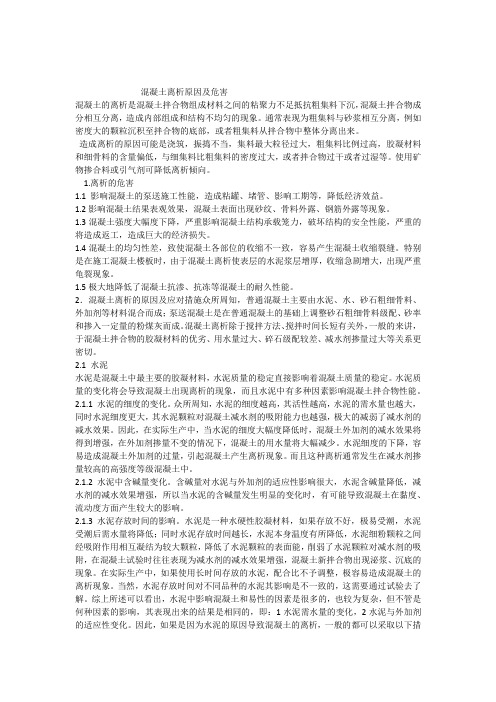
混凝土离析原因及危害混凝土的离析是混凝土拌合物组成材料之间的粘聚力不足抵抗粗集料下沉,混凝土拌合物成分相互分离,造成内部组成和结构不均匀的现象。
通常表现为粗集料与砂浆相互分离,例如密度大的颗粒沉积至拌合物的底部,或者粗集料从拌合物中整体分离出来。
造成离析的原因可能是浇筑,振捣不当,集料最大粒径过大,粗集料比例过高,胶凝材料和细骨料的含量偏低,与细集料比粗集料的密度过大,或者拌合物过干或者过湿等。
使用矿物掺合料或引气剂可降低离析倾向。
1.离析的危害1.1 影响混凝土的泵送施工性能,造成粘罐、堵管、影响工期等,降低经济效益。
1.2影响混凝土结果表观效果,混凝土表面出现砂纹、骨料外露、钢筋外露等现象。
1.3混凝土强度大幅度下降,严重影响混凝土结构承载笼力,破坏结构的安全性能,严重的将造成返工,造成巨大的经济损失。
1.4混凝土的均匀性差,致使混凝土各部位的收缩不一致,容易产生混凝土收缩裂缝。
特别是在施工混凝土楼板时,由于混凝土离析使表层的水泥浆层增厚,收缩急剧增大,出现严重龟裂现象。
1.5极大地降低了混凝土抗渗、抗冻等混凝土的耐久性能。
2.混凝土离析的原因及应对措施众所周知,普通混凝土主要由水泥、水、砂石粗细骨料、外加剂等材料混合而成;泵送混凝土是在普通混凝土的基础上调整砂石粗细骨料级配、砂率和掺入一定量的粉煤灰而成。
混凝土离析除于搅拌方法、搅拌时间长短有关外,一般的来讲,于混凝土拌合物的胶凝材料的优劣、用水量过大、碎石级配较差、减水剂掺量过大等关系更密切。
2.1 水泥水泥是混凝土中最主要的胶凝材料,水泥质量的稳定直接影响着混凝土质量的稳定。
水泥质量的变化将会导致混凝土出现离析的现象,而且水泥中有多种因素影响混凝土拌合物性能。
2.1.1 水泥的细度的变化。
众所周知,水泥的细度越高,其活性越高,水泥的需水量也越大,同时水泥细度更大,其水泥颗粒对混凝土减水剂的吸附能力也越强,极大的减弱了减水剂的减水效果。
因此,在实际生产中,当水泥的细度大幅度降低时,混凝土外加剂的减水效果将得到增强,在外加剂掺量不变的情况下,混凝土的用水量将大幅减少。
混凝土离析原因及危害

混凝土离析原因及危害混凝土离析原因及危害混凝土离析原因及危害混凝土离析原因及危害混凝土的离析是混凝土拌合物组成材料之间的粘聚力不足抵抗粗集料下沉混凝土的离析是混凝土拌合物组成材料之间的粘聚力不足抵抗粗集料下沉混凝土的离析是混凝土拌合物组成材料之间的粘聚力不足抵抗粗集料下沉混凝土的离析是混凝土拌合物组成材料之间的粘聚力不足抵抗粗集料下沉,,,,混凝土拌合混凝土拌合混凝土拌合混凝土拌合物成分相互分离物成分相互分离物成分相互分离物成分相互分离,,,,造成内部组成和结构不均匀的现象造成内部组成和结构不均匀的现象造成内部组成和结构不均匀的现象造成内部组成和结构不均匀的现象。
通常表现为粗集料与砂浆相互分离通常表现为粗集料与砂浆相互分离通常表现为粗集料与砂浆相互分离通常表现为粗集料与砂浆相互分离,,,,例如密度大的颗粒沉积例如密度大的颗粒沉积例如密度大的颗粒沉积例如密度大的颗粒沉积至至至至拌合物的底部拌合物的底部拌合物的底部拌合物的底部,,,,或者粗集料从拌合物中整体分离出来或者粗集料从拌合物中整体分离出来或者粗集料从拌合物中整体分离出来或者粗集料从拌合物中整体分离出来。
造成离析的原因可能是浇筑造成离析的原因可能是浇筑造成离析的原因可能是浇筑造成离析的原因可能是浇筑,,,,振捣不当振捣不当振捣不当振捣不当,,,,集料最大粒径过大集料最大粒径过大集料最大粒径过大集料最大粒径过大,,,,粗集料比例过高粗集料比例过高粗集料比例过高粗集料比例过高,,,,胶凝胶凝胶凝胶凝材料和细骨料的含量偏低材料和细骨料的含量偏低材料和细骨料的含量偏低材料和细骨料的含量偏低,,,,与细集料比粗集料的密度过大与细集料比粗集料的密度过大与细集料比粗集料的密度过大与细集料比粗集料的密度过大,,,,或者拌合物过干或者过湿等或者拌合物过干或者过湿等或者拌合物过干或者过湿等或者拌合物过干或者过湿等。
使用使用使用使用矿物掺合料或引气剂可降低离析倾向矿物掺合料或引气剂可降低离析倾向矿物掺合料或引气剂可降低离析倾向矿物掺合料或引气剂可降低离析倾向。
混凝土离析原因
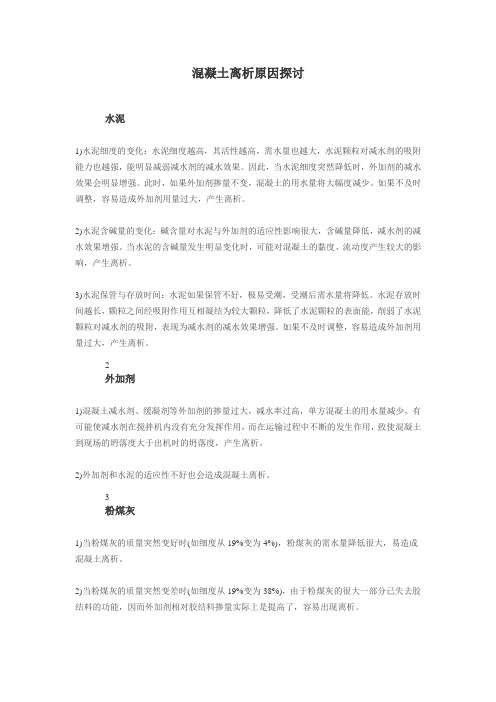
混凝土离析原因探讨水泥1)水泥细度的变化:水泥细度越高,其活性越高,需水量也越大,水泥颗粒对减水剂的吸附能力也越强,能明显减弱减水剂的减水效果。
因此,当水泥细度突然降低时,外加剂的减水效果会明显增强。
此时,如果外加剂掺量不变,混凝土的用水量将大幅度减少。
如果不及时调整,容易造成外加剂用量过大,产生离析。
2)水泥含碱量的变化:碱含量对水泥与外加剂的适应性影响很大,含碱量降低,减水剂的减水效果增强。
当水泥的含碱量发生明显变化时,可能对混凝土的黏度、流动度产生较大的影响,产生离析。
3)水泥保管与存放时间:水泥如果保管不好,极易受潮,受潮后需水量将降低。
水泥存放时间越长,颗粒之间经吸附作用互相凝结为较大颗粒,降低了水泥颗粒的表面能,削弱了水泥颗粒对减水剂的吸附,表现为减水剂的减水效果增强。
如果不及时调整,容易造成外加剂用量过大,产生离析。
2外加剂1)混凝土减水剂、缓凝剂等外加剂的掺量过大,减水率过高,单方混凝土的用水量减少,有可能使减水剂在搅拌机内没有充分发挥作用,而在运输过程中不断的发生作用,致使混凝土到现场的坍落度大于出机时的坍落度,产生离析。
2)外加剂和水泥的适应性不好也会造成混凝土离析。
3粉煤灰1)当粉煤灰的质量突然变好时(如细度从19%变为4%),粉煤灰的需水量降低很大,易造成混凝土离析。
2)当粉煤灰的质量突然变差时(如细度从19%变为38%),由于粉煤灰的很大一部分已失去胶结料的功能,因而外加剂相对胶结料掺量实际上是提高了,容易出现离析。
粉煤灰是混凝土重要的掺和料之一,能极大改善混凝土和易性、密实性及强度性能。
如果粉煤灰质量波动较大,则混凝土质量控制的难度增大,容易产生离析。
4骨料骨料是混凝土中用量最大的材料,其质量直接影响混凝土的质量。
骨料质量的波动很容易造成混凝土的离析。
1)碎石质量不好。
碎石粒径增大、级配变差、级配单一,都容易造成混凝土的离析现象。
2)砂子质量不好。
砂子中石头多、含水过高、片状石屑量过大将影响混凝土的和易性,产生离析。
什么是混凝土的离析现象
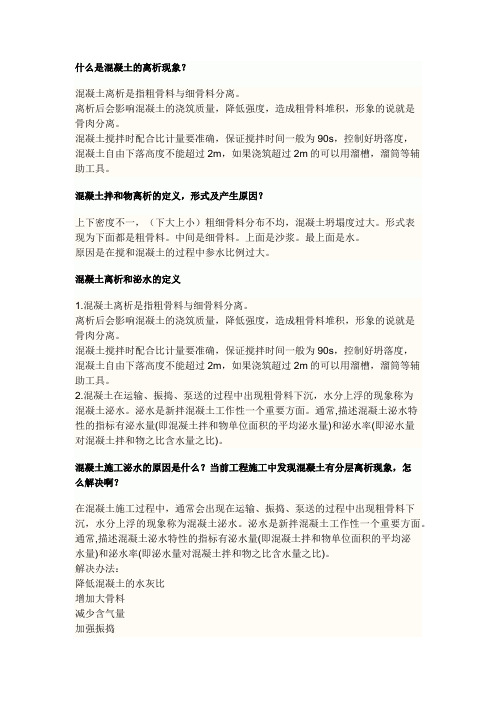
什么是混凝土的离析现象?混凝土离析是指粗骨料与细骨料分离。
离析后会影响混凝土的浇筑质量,降低强度,造成粗骨料堆积,形象的说就是骨肉分离。
混凝土搅拌时配合比计量要准确,保证搅拌时间一般为90s,控制好坍落度,混凝土自由下落高度不能超过2m,如果浇筑超过2m的可以用溜槽,溜筒等辅助工具。
混凝土拌和物离析的定义,形式及产生原因?上下密度不一,(下大上小)粗细骨料分布不均,混凝土坍塌度过大。
形式表现为下面都是粗骨料。
中间是细骨料。
上面是沙浆。
最上面是水。
原因是在搅和混凝土的过程中参水比例过大。
混凝土离析和泌水的定义1.混凝土离析是指粗骨料与细骨料分离。
离析后会影响混凝土的浇筑质量,降低强度,造成粗骨料堆积,形象的说就是骨肉分离。
混凝土搅拌时配合比计量要准确,保证搅拌时间一般为90s,控制好坍落度,混凝土自由下落高度不能超过2m,如果浇筑超过2m的可以用溜槽,溜筒等辅助工具。
2.混凝土在运输、振捣、泵送的过程中出现粗骨料下沉,水分上浮的现象称为混凝土泌水。
泌水是新拌混凝土工作性一个重要方面。
通常,描述混凝土泌水特性的指标有泌水量(即混凝土拌和物单位面积的平均泌水量)和泌水率(即泌水量对混凝土拌和物之比含水量之比)。
混凝土施工泌水的原因是什么?当前工程施工中发现混凝土有分层离析现象,怎么解决啊?在混凝土施工过程中,通常会出现在运输、振捣、泵送的过程中出现粗骨料下沉,水分上浮的现象称为混凝土泌水。
泌水是新拌混凝土工作性一个重要方面。
通常,描述混凝土泌水特性的指标有泌水量(即混凝土拌和物单位面积的平均泌水量)和泌水率(即泌水量对混凝土拌和物之比含水量之比)。
解决办法:降低混凝土的水灰比增加大骨料减少含气量加强振捣混凝土泌水什么原因?水泥与外加剂适应性不好,如何解决、?石子的颗粒级配是和1-3的石子,请高手解答水泥与外加剂适应性不好,是要外加剂厂家来人调的,这个不是问题。
混凝土泌水,这个首先你可以做一下外加剂的压力泌水和常压泌水试验,看看是不是外加剂的问题,如果不是那,你就要检查自己的配合比了,看看砂率够不够了,骨料级配合不合适,骨料吸水率,适当的减少一点水泥浆,这个泌水如果不是外加剂的问题多数就是砂率,或者矿物掺合料的掺量了,你可以试试,主要是我不知道你所说的泌水是混凝土在什么状态上出现的泌水。
混凝土离析的概念分析
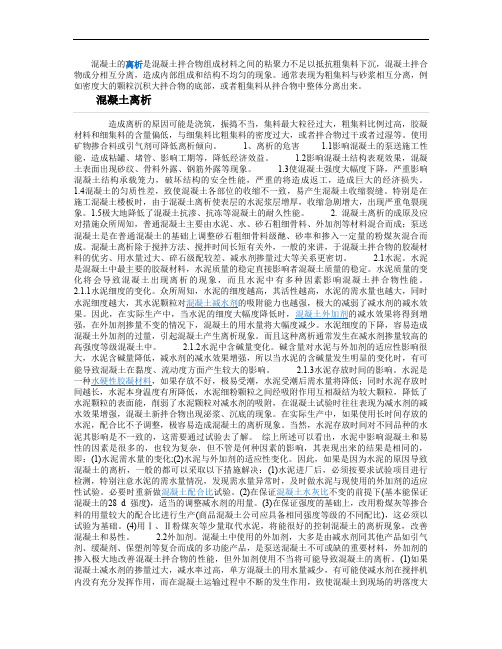
混凝土的离析是混凝土拌合物组成材料之间的粘聚力不足以抵抗粗集料下沉,混凝土拌合物成分相互分离,造成内部组成和结构不均匀的现象。
通常表现为粗集料与砂浆相互分离,例如密度大的颗粒沉积大拌合物的底部,或者粗集料从拌合物中整体分离出来。
混凝土离析造成离析的原因可能是浇筑,振捣不当,集料最大粒径过大,粗集料比例过高,胶凝材料和细集料的含量偏低,与细集料比粗集料的密度过大,或者拌合物过干或者过湿等。
使用矿物掺合料或引气剂可降低离析倾向。
1、离析的危害 1.1影响混凝土的泵送施工性能,造成粘罐、堵管、影响工期等,降低经济效益。
1.2影响混凝土结构表观效果,混凝土表面出现砂纹、骨料外露、钢筋外露等现象。
1.3使混凝土强度大幅度下降,严重影响混凝土结构承载笼力,破坏结构的安全性能,严重的将造成返工,造成巨大的经济损失。
1.4混凝土的匀质性差,致使混凝土各部位的收缩不一致,易产生混凝土收缩裂缝。
特别是在施工混凝土楼板时,由于混凝土离析使表层的水泥浆层增厚,收缩急剧增大,出现严重龟裂现象。
1.5极大地降低了混凝土抗渗、抗冻等混凝土的耐久性能。
2. 混凝土离析的成原及应对措施众所周知,普通混凝土主要由水泥、水、砂石粗细骨料、外加剂等材料混合而成;泵送混凝土是在普通混凝土的基础上调整砂石粗细骨料级酏、砂率和掺入一定量的粉煤灰混合而成。
混凝土离析除于搅拌方法、搅拌时间长短有关外,一般的来讲,于混凝土拌合物的胶凝材料的优劣、用水量过大、碎石级配较差、减水剂掺量过大等关系更密切。
2.1水泥。
水泥是混凝土中最主要的胶凝材料,水泥质量的稳定直接影响者混凝土质量的稳定。
水泥质量的变化将会导致混凝土出现离析的现象,而且水泥中有多种因素影响混凝土拌合物性能。
2.1.1水泥细度的变化。
众所周知,水泥的细度越高,其活性越高,水泥的需水量也越大,同时水泥细度越大,其水泥颗粒对混凝土减水剂的吸附能力也越强,极大的减弱了减水剂的减水效果。
因此,在实际生产中,当水泥的细度大幅度降低时,混凝土外加剂的减水效果将得到增强,在外加剂掺量不变的情况下,混凝土的用水量将大幅度减少。
- 1、下载文档前请自行甄别文档内容的完整性,平台不提供额外的编辑、内容补充、找答案等附加服务。
- 2、"仅部分预览"的文档,不可在线预览部分如存在完整性等问题,可反馈申请退款(可完整预览的文档不适用该条件!)。
- 3、如文档侵犯您的权益,请联系客服反馈,我们会尽快为您处理(人工客服工作时间:9:00-18:30)。
混凝土离析的原因
混凝土离析是指在混凝土生产、运输、浇筑、养护等过程中,其中的水分与固体颗粒分离的现象。
离析使得混凝土的均匀性和强度得以降低,严重时甚至导致混凝土的失效。
混凝土离析的原因很多,主要可以归结为以下几个方面:
1.混凝土配合比不合理:混凝土的配合比直接影响着混凝土的均匀性和离析倾向。
如果水灰比过大、水胶比过小或者使用堆积密实的骨料等,都会导致混凝土离析的发生。
2.混凝土搅拌不均匀:在混凝土的搅拌过程中,如果搅拌时间过短或搅拌不均匀,会使得混凝土中的水分与固体颗粒分离,从而发生离析。
3.浇筑方式不当:浇筑方式直接影响着混凝土的均匀性。
如果浇筑速度过快、高度过大或浇筑工艺不合理等,都容易导致混凝土离析。
4.温度和湿度变化:混凝土在养护过程中,如果受到温度和湿度的变化,会引起混凝土内部的应力变化,从而导致混凝土离析。
5.骨料形状和颗粒大小:混凝土中的骨料是混凝土结构的主要组成部分,其形状和颗粒大小对混凝土离析的程度也有直接的影响。
如果骨料形状不均匀、颗粒大小差异大,都会增加混凝土离析的可能性。
6.水质和掺用材料:水质和掺用材料的质量也会对混凝土的离析产生影响。
如果使用水质较差的水源或者掺杂了劣质的添加剂等,都会增加混凝土离析的可能性。
针对混凝土离析的问题,可以采取以下一些措施进行预防和解决:
1.合理设计配合比:根据混凝土所在的环境和使用要求,合理设计混
凝土的配合比,保证水灰比、水胶比和骨料的比例等参数满足要求,减少
离析的发生。
2.优化搅拌工艺:在混凝土的搅拌过程中,要保证搅拌时间充分,并
采用适当的搅拌设备,确保混凝土均匀搅拌,减少离析现象。
3.控制浇筑速度和高度:在进行混凝土浇筑时,要控制浇筑速度,保
证浇筑高度适中,避免过快或过高造成的离析。
4.加强养护措施:在混凝土浇筑后,要及时进行养护,保持适宜的温
度和湿度,减少混凝土内部应力变化,防止离析的发生。
5.选择适合的骨料和掺合材料:选择形状均匀、颗粒大小合理的骨料,并保证水质的优良,合理选择和使用掺合材料,减少离析的风险。
总之,混凝土离析是一个复杂的问题,其原因多种多样,需要综合考
虑各种因素并采取相应的措施进行预防和解决。
只有在每个环节细致入微
的把控好,才能保证混凝土的质量和结构的稳定性。