电路板自动测试系统
ATS_自动测试系统_及ATE技术
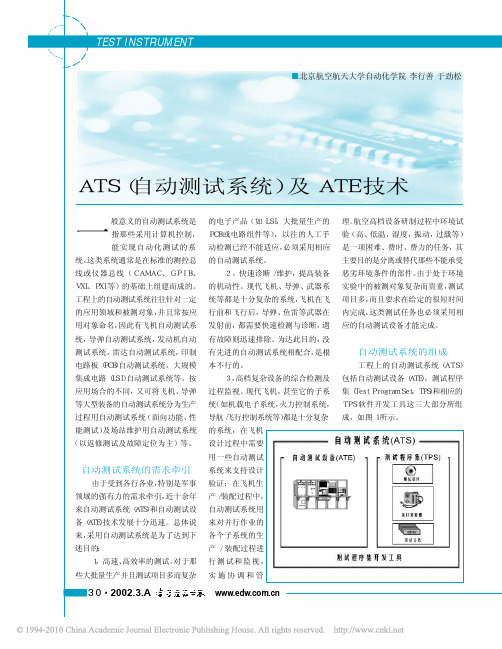
■北京航空航天大学自动化学院 李行善 于劲松ATS(自动测试系统)及ATE技术一 图1 自动测试系统的组成2002.3.A2002.3.A ATE是指测试硬件和它自己的操作系统软件。
ATE硬件本身可以像便携式设备那样小,也可以是由多个机柜所组成,总重量达上千公斤的设备。
为适应飞机、舰船或机动前线部队的应用,ATE往往是一些加固了的商用设备。
即使是非前线环境(如维修站或修理厂)应用的ATE,也几乎完全由商用现成设备(CommercialOff-The-Shelf Equipment, COTS)组成。
ATE的心脏是计算机,该计算机用来控制复杂的测试仪器如数字电压表,波形分析仪,信号发生器及开关组件等。
这些设备在测试软件的控制下运行, 以提供被测对象中的电路或部件所要求的激励,然后测量在不同的引脚、端口或连接点的响应,从而确定该被测对象是否具有规范中的规定的功能或性能。
ATE有着自己的操作系统,以实现内部事务的管理,如自测试,自校准等,跟踪预防维护需求及测试过程排序,并存储和检索相应的技术手册内容。
ATE的典型特征是其功能上的灵活性,例如用一台ATE可以测试多种不同类型的电子设备。
从部件测试角度,ATE可用来实现对两类黑盒子的测试,即:①现场可更换单元(LRUs, Line Replaceable Units)或武器可更换组件(WRAs,WeaponsReplaceable Assemblies);②车间可更换单元(SRUs, Shop ReplaceableAssemblies)。
测试程序集(TPS)是与被测对象及其测试要求密切相关的。
典型的测试程序集由三部分组成:①测试程序软件; ②测试接口适配器,包括接口装置、保持/紧固件及电缆;③被测对象测试所需的各种文件。
测试软件ATEATE及开关组件等,加入的地方,响应信号。
个部件。
口,连接UUT到应的接口设备,完成UUT到ATE并且为ATE具。
境, 包括①ATE和UUTATE研制和TPS以及人工智能在自动测试系统中的应用;从集中型的ATS正向着分布式的集成诊断测试系统发展。
某电路板自动测试系统的设计与实现

HUA a , HE L — n , T AN Z o h a S n imi g I u —u
a c mp ihe o d efc s a d i p o e e te ce y g e t c o ls s g o fe t , n m r v st s f inc r al i y. K e o ds vru li tume t daa a qusto s ra o mu c to y w r : it a nsr n ; t c ii n; e lc m i i nia in
强 电信 号 的 通 断 。
针对手动测试 的低效率 和低 可靠性 , 计 了一套 自动测 试 设 系统 , 使用夹具信号连接 目标 电路板与转接板 , 在测试 中只要 夹 具信 号到位 , 便能保证 目标 电路板 与转接 板 的准 确连 接。转 接 板 的输 入输出都通 过 N 公 司 的 6 2 I 2 1和 6 1 55两块 P I 卡与 C板 P C机相连 , C端软件 的控制 信号 通过 转接 板 的继 电器和 光 电 P 隔离器模拟实 际开关 的通 断 , 并通过 串 口读写获 取 目标 电路 板
维普资讯
某 电路 板 自动 测 试 系统 的 设 计 与 实现
・ 5・ 1
某 电路 板 自动测试 系统 的设计 与实现
华 山 , 黎 明 ,田作 华 何
( 海 交 通 大 学 自动 化 系 ,: 上 j海 204 ) 0 2 0
摘 要 : 对 某 电路 板 手 动 测 试 的缺 点 , 计 了一 套 自动 测 试 系统 。该 系 统 基 于 L b IW 虚 拟 仪 器 软 件 平 台 , 过 N 公 司 针 设 aV E 通 I 的61 5 5和 62 2 1数 据 采 集卡 进 行 输 入 输 出采 集 与控 制 , 将 目标 电路 板 信 号 通 过 夹 具信 号 引 入 自主 设 计 的 转 接 板 , 并 实现 目 标 电路 板 的 各 项 动 作 , 得 了 良好 的效 果 , 大提 高 了测 试 效 率 。 取 大 关键词 : 拟仪 器 ; 据 采集 ; 虚 数 串口通 信 中 图 分 类 号 :P 7 T 24 文 献 标 识 码 : B 文 章 编 号 :0 0—8 2 ( 0 8 0 0 1 0 10 8 9 20 )7— 0 5— 2
一种PCB自动测试系统的设计

萎 榘
遁 裁
V 13 N . o. 0 o3
Sp2 2 e . 01
JC I HENG ANLU ONG DI T XU N
一
种 P B 自动 测 试 系统 的 设 计 C
李金 宝 李贵娇 张浩然 薛海英
( 北方 通用 电子集 团有 限公 司微 电子部 苏 州 2 5 6 ) 1 1 3
内测 试 的 功 能 。
关键 词
P B 自动 测试 C
路 内测试
六 线测试 法
线 、 心 控 制模 块 、 内测 试模 块 、 核 路 多路 开 关矩 阵
及针床 组成 。系统整体 结构 如图 l 所示 。 系统 工
在 电子产 品的开 发 、 生产及 维修 中 , 常要对 通 作过程 如下 : 由 P 先 C机通 过 U B总 线 给 核心 控 S
六 个触 针与测试装置连接起来 , 以这 种方法 称为 所 “ 六线 测 试法 ” 。采 用 六线 测 试法 进行 测 量 。 可 以达 到较高 的测量精 度 , 常采用 的一种方 法。 是经 3 2 二 极管 的测试 。
内测试模块进行信号幅度与偏移量的调节, 然后 传给核心控制模块 , 核心控制模块进行 A D转换 /
电路板 进行 测试 。简单 的电路板 可 以用手 工方法
来检 测 。随着 电子 工 业 和科 学技 术 的飞 速 发展 ,
制模块发送测试命令 , 核心控制模块根据命令进
行 D A转 换 , 出合适 的模 拟 电压 激 励信 号 , / 发 施 加 给路 内测试模 块 , 过 路 内测 试模 块 的八 条测 通 试总线 传 至多路 开关矩 阵 。多路开关 矩阵 与针床
ATE测试原理范文

ATE测试原理范文ATE(Automatic Test Equipment,自动测试设备)是一种用于自动测试和诊断电子元器件、电路板和电子设备的装置,广泛应用于电子制造业。
ATE测试原理是指在ATE系统中进行测试和诊断的基本原理和方法。
本文将从ATE测试的基本流程、测试原理和常见的测试技术等方面进行阐述,介绍ATE测试原理。
在ATE测试中,基本的测试流程通常包括以下几个步骤:1.测试准备:包括测试系统的初始化、测试程序的加载和设备的连接等。
2.测试信号发生:根据测试需求生成测试信号,例如时钟信号、电源信号等,用于驱动被测设备。
3.测量信号采集:采集被测设备在测试信号作用下的响应信号,如输出电压、电流等。
4.数据分析和判断:通过对采集到的信号进行分析和判断,判断被测设备是否符合规格要求。
5.测试结果输出:根据测试判断的结果,输出测试报告或控制设备进行优化和调整。
1.测试目标和测试方法选择:在ATE系统中,根据被测设备的特点和测试需求,选择合适的测试目标和测试方法。
例如,对于数字电路的测试,常采用逻辑测试方法,对模拟电路则采用参数测试方法。
2.测试信号的发生和采集:在ATE系统中,需要根据被测设备的特点生成相应的测试信号,并采集被测设备在测试信号作用下的响应信号。
这一过程通常通过信号发生器和信号采集模块实现。
3.数据分析和判断:在ATE系统中,根据采集到的信号,通过数据分析和判断,判断被测设备是否符合规格要求。
这一过程通常通过数字信号处理和模拟信号处理技术来实现。
4.测试结果输出和记录:根据测试判断的结果,通过输出测试报告或记录测试数据等方式,将测试结果输出。
1.功能测试:用于测试被测设备各个功能模块是否正常工作。
通过输入各种不同的信号,观察输出是否符合预期结果。
2.电气参数测试:用于测试被测设备的电气特性参数,如电压、电流、功率等。
通过对被测设备的输入和输出信号进行测量和分析,判断其电气参数是否在规格范围内。
自动测试系统
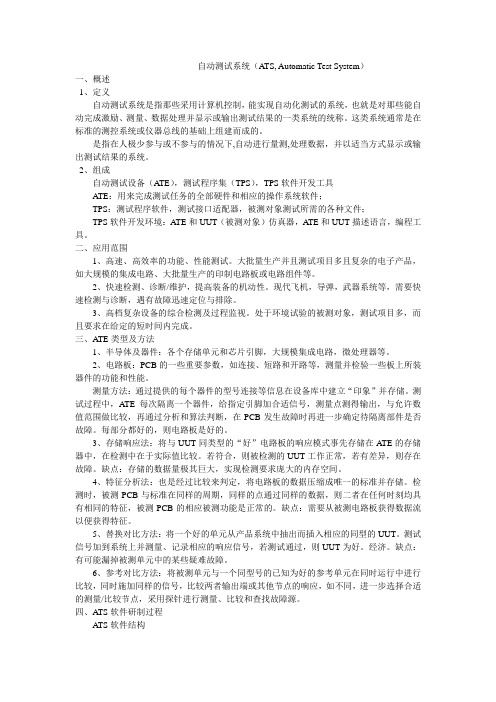
自动测试系统(A TS, Automatic Test System)一、概述1、定义自动测试系统是指那些采用计算机控制,能实现自动化测试的系统,也就是对那些能自动完成激励、测量、数据处理并显示或输出测试结果的一类系统的统称。
这类系统通常是在标准的测控系统或仪器总线的基础上组建而成的。
是指在人极少参与或不参与的情况下,自动进行量测,处理数据,并以适当方式显示或输出测试结果的系统。
2、组成自动测试设备(A TE),测试程序集(TPS),TPS软件开发工具A TE:用来完成测试任务的全部硬件和相应的操作系统软件;TPS:测试程序软件,测试接口适配器,被测对象测试所需的各种文件;TPS软件开发环境:A TE和UUT(被测对象)仿真器,A TE和UUT描述语言,编程工具。
二、应用范围1、高速、高效率的功能、性能测试。
大批量生产并且测试项目多且复杂的电子产品,如大规模的集成电路、大批量生产的印制电路板或电路组件等。
2、快速检测、诊断/维护,提高装备的机动性。
现代飞机,导弹,武器系统等,需要快速检测与诊断,遇有故障迅速定位与排除。
3、高档复杂设备的综合检测及过程监视。
处于环境试验的被测对象,测试项目多,而且要求在给定的短时间内完成。
三、A TE类型及方法1、半导体及器件:各个存储单元和芯片引脚,大规模集成电路,微处理器等。
2、电路板:PCB的一些重要参数,如连接、短路和开路等,测量并检验一些板上所装器件的功能和性能。
测量方法:通过提供的每个器件的型号连接等信息在设备库中建立“印象”并存储。
测试过程中,A TE每次隔离一个器件,给指定引脚加合适信号,测量点测得输出,与允许数值范围做比较,再通过分析和算法判断,在PCB发生故障时再进一步确定待隔离部件是否故障。
每部分都好的,则电路板是好的。
3、存储响应法:将与UUT同类型的“好”电路板的响应模式事先存储在A TE的存储器中,在检测中在于实际值比较。
若符合,则被检测的UUT工作正常,若有差异,则存在故障。
一种PCB自动分板及自动测试设备

新产品开发
一种 PCB 自动分板及自动测试设备
方贵本,李 锋
(南宁富桂精密工业有限公司,广西 南宁 530000)
摘 要:以一种印刷电路板(PCB)生产线改造为例,分析对比改造前后该 PCB 生产线分板及测试的工艺流程。结合该 PCB 来料连板的特点以及技术要求,给出了此种 PCB 生产线自动分板及自动测试的总体设计方案。实际生产表明,该自 动分板及自动测试的设计结构简单合理,自动化程度高,减少生产安全隐患,节约人工成本的同时,提高生产效率。 关键词:PCB;自动;分板;测试
11
3 2 1
图 3 PCB 自动分板及自动测试设备总体组成
设备经过改造后,实现生产过程自动化。基本工 艺流程:批量 PCB6 连板来料放入集装箱内,推板机 1 分片对产品自动送料— ——机械手 4 自动取放料——— 分板冲床 5 自动冲压 分板———机 械手 4 自动 取放 料———交叉传送机 7 送料———2# 六轴取放料机械手 8 取放料— ——自动扫描、测试———良品或不良品分别 收集于 1#tray 或 2#tray 内,整个过程全自动生产[2]。在 实践生产中,整线自动化节省人力达 22 人/天。
12
11
16
图 4 推板机结构图组成
4 进料输送机
进料输送机如图 5 所示,包含:1# 进料轨道 21、 1# 有料感应器 22、2# 进料轨道 23、2# 有料感应器 24、回弹组件 25、定位组件 26、宽度调节螺杆 27、固 定组件 28.其工作原理:推板机出来的 PCB 6 连板, 进入 1# 进料轨道,当 2# 感应器 24 检测没又有料 时,PCB 板再进入到 2# 进料轨道末端,感应检测到 物料,回弹模组 25 回拉,定位组件 26 把 PCB 板夹紧 定位。等待 1# 机械手抓取。第二片 PCB 板进入 1# 进 料轨道 21 上方等待。当 1# 号机械手把第一片 PCB 板抓走后,第二片板迅速补位到 2# 进料轨道上方。
ATE自动化测试系统是什么_ATE自动化测试系统介绍
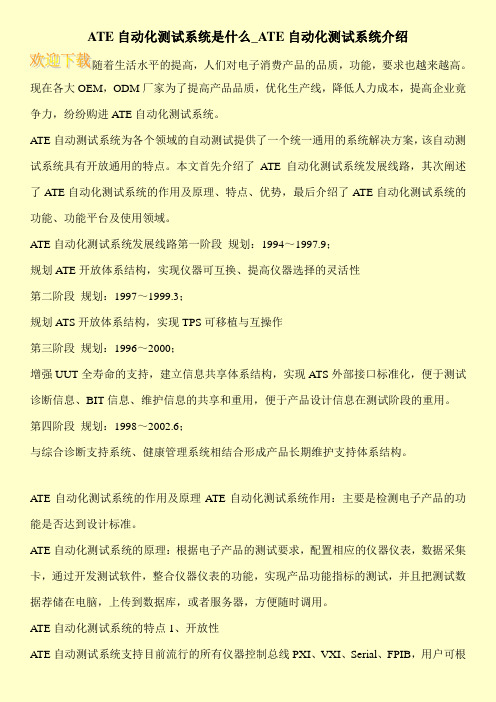
ATE自动化测试系统是什么_ATE自动化测试系统介绍随着生活水平的提高,人们对电子消费产品的品质,功能,要求也越来越高。
现在各大OEM,ODM厂家为了提高产品品质,优化生产线,降低人力成本,提高企业竟争力,纷纷购进ATE自动化测试系统。
ATE自动测试系统为各个领域的自动测试提供了一个统一通用的系统解决方案,该自动测试系统具有开放通用的特点。
本文首先介绍了ATE自动化测试系统发展线路,其次阐述了ATE自动化测试系统的作用及原理、特点、优势,最后介绍了ATE自动化测试系统的功能、功能平台及使用领域。
ATE自动化测试系统发展线路第一阶段规划:1994~1997.9;规划ATE开放体系结构,实现仪器可互换、提高仪器选择的灵活性第二阶段规划:1997~1999.3;规划ATS开放体系结构,实现TPS可移植与互操作第三阶段规划:1996~2000;增强UUT全寿命的支持,建立信息共享体系结构,实现ATS外部接口标准化,便于测试诊断信息、BIT信息、维护信息的共享和重用,便于产品设计信息在测试阶段的重用。
第四阶段规划:1998~2002.6;与综合诊断支持系统、健康管理系统相结合形成产品长期维护支持体系结构。
ATE自动化测试系统的作用及原理ATE自动化测试系统作用:主要是检测电子产品的功能是否达到设计标准。
ATE自动化测试系统的原理:根据电子产品的测试要求,配置相应的仪器仪表,数据采集卡,通过开发测试软件,整合仪器仪表的功能,实现产品功能指标的测试,并且把测试数据荐储在电脑,上传到数据库,或者服务器,方便随时调用。
ATE自动化测试系统的特点1、开放性ATE自动测试系统支持目前流行的所有仪器控制总线PXI、VXI、Serial、FPIB,用户可根。
基于自动测试系统的数字电路板测试与故障诊断
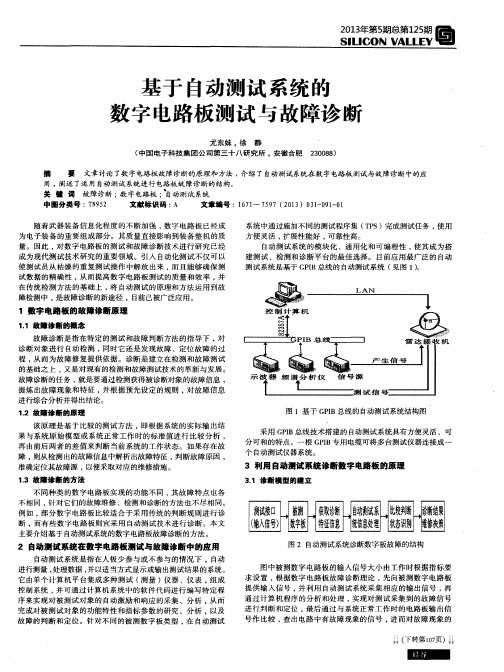
个 自动 测试 仪器 系统 。
3 利 用 自动测试 系 统诊 断 数字 电路板 的 原理
( 输 入 信 号 ) I l 数 字 板 l } 特 征 信 息 } l 统 信 息 处 理 I l 状 态 识 别 I l 维 修 决 策
图 2 自动测 试 系统诊 断数 字板 故 障 的结构
测 试 接 口 L l 被 测 I l J 获 取 诊 断 U 自 枷 憾 系 l _ J 比 较 判 断 U 诊 断 结 果
用 ,阐述 了运 用 自动 测试 系统 进行 电路 板故 障 诊 断的 结构 。 关 键 词 故障诊 断 ; 数 字 电路板 ; ’ 自动测 试 系统 中 图分 类号 : T N 9 5 2 文 献标 识码 : h 文 章编 号 : 1 6 7 1 —7 5 9 7( 2 O 1 3 )0 3 1 — 0 9 1 — 0 1 系统 中通 过 施加 不 同的测 试 程序 集 ( T P S) 完 成测 试任 务 , 使用 方便 灵活 , 扩展性 能好 , 可靠 性 高。 自动 测试 系 统 的模 块 化 、通 用 化 和可 编 程 性 , 使 其 成 为搭 建 测 试 、检测 和 诊 断平 台 的最 佳选 择 。 目前 应 用最 广 泛 的 自动 测 试 系统 是 基于 G P I B总 线 的 自动 测试 系统 ( 见图 1 ) 。
2 0 1 3 年第 5 期总第 1 2 5 期
基于 自动测试 系统 的 数 字 电路板测试 与故 障诊 断
ATE测试原理与维护

ATE测试原理与维护ATE(Automatic Test Equipment)是自动测试设备的缩写,是一种自动化测试设备,用于对电子器件、PCB电路板、集成电路芯片等进行功能、性能及可靠性测试。
下面将详细介绍ATE测试原理与维护。
一、ATE测试原理:1. 信号发生器(Signal Generator):用于产生各种不同频率、振幅和波形的电信号,用于测试被测器件的频率响应。
2. 信号采集器(Signal Analyzer):用于对被测器件的输出信号进行采样和分析,可以测量信号的频率、振幅、相位等参数。
3. 数据采集及控制器(Data Acquisition and Controller):用于采集、处理和分析被测器件的数据,同时可以控制其他测试设备的运行。
4. 电源供应器(Power Supply):提供各种电压和电流以供被测器件正常工作。
5. 环境控制器(Environment Controller):用于对被测器件环境进行控制,例如温度和湿度。
整个ATE测试过程包括以下几个步骤:1.设置测试条件:根据被测器件的规格和要求,设置测试参数,如输入电压和电流范围、工作频率等。
2.连接被测器件:使用适当的连接线将被测器件与ATE设备连接。
3.发送信号:通过信号发生器产生测试信号,送入被测器件。
4.采集数据:信号采集器对被测器件的输出信号进行采样,并将数据传送到数据采集及控制器进行处理和分析。
5.分析数据:数据采集及控制器对采集到的数据进行分析,通过算法和预设的规则判断被测器件的性能和可靠性是否符合要求。
6.生成报告:根据测试结果生成测试报告,包括被测器件的各项测试数据和结果。
二、ATE测试维护:ATE设备的维护对于测试结果的准确性和工作效率的提高至关重要,主要包括以下几个方面:1.定期校准:ATE设备需要定期进行校准,以保证测试结果的准确性。
校准包括对信号发生器、信号采集器和数据采集及控制器的参数进行检查和调整。
aoi自动光学检测机工作原理

aoi自动光学检测机工作原理AOI自动光学检测机是一种高精度、高效率的检测设备,广泛应用于电子、半导体、汽车等行业中。
其工作原理是通过光学成像技术和图像处理算法,对印刷电路板(PCB)、芯片等进行非接触式的自动检测。
一、 AOI自动光学检测机的基本构成AOI自动光学检测机主要由以下几个部分组成:1. 光源系统:提供光源,照亮被测试物体。
2. 成像系统:将被测试物体的图像转换为数字信号。
3. 图像处理系统:对数字信号进行处理和分析,提取出需要的信息。
4. 控制系统:控制整个设备的运行。
5. 传输系统:将被测试物体从一个位置传输到另一个位置。
二、 AOI自动光学检测机的工作流程AOI自动光学检测机的工作流程如下:1. 准备工作:在测试前需要对设备进行预热和校准,确保设备正常运行。
2. 加载PCB或芯片:将待测试的PCB或芯片放置于传输带上,并通过传输带将其送入设备内部。
3. 光源照射:在进入成像系统前,被测试物体会先经过光源系统的照射,使其表面得到充分的照明。
4. 成像:被测试物体经过光源照射后,进入成像系统。
成像系统利用透镜、CCD等元件将被测试物体的图像转换为数字信号,并传送到图像处理系统中。
5. 图像处理:图像处理系统对数字信号进行处理和分析,提取出需要的信息。
这些信息可能包括线路连接情况、元器件位置、焊点质量等。
6. 判定:根据预设的检测标准和算法,对提取出来的信息进行判定。
如果检测结果符合要求,则将其发送到下一步操作;否则将其标记为不良品并发送到设备外部进行处理。
7. 卸载PCB或芯片:检测完成后,将PCB或芯片从传输带上卸载,并送至下一步操作或退出设备。
三、 AOI自动光学检测机的优势1. 高精度:AOI自动光学检测机采用高精度成像技术和图像处理算法,能够对PCB、芯片等进行高精度、高速度的自动检测。
2. 高效率:AOI自动光学检测机能够实现非接触式的自动检测,避免了传统手工检测的繁琐和低效率。
基于虚拟仪器的多功能电路板检测系统的实现

1 系统构架
本文介绍的测试 目标 电路板是某冰柜的核心控制系统 。 目 标 电路板上集成 了对 冰柜进行控制所需要的各种按钮 、 开关 、 负
标 电路板读取其特定的状态信号来进行判断 。状态信息通过 目 标 电路板 自带 的 I I 口, C接 经协 议转换设 备转换 成为 R 22串 S3 口数据输入到计算机进行检 测结果 的判定。另一方 面 , 检测程 序需要控制电路板夹具 , 待测的硬件 信号引入 到数据采集板 将
se d l mp o e t e ts f ce c . ta i i r v h e te in y y i Ke r s L b i d w / VI P - 5 5 P I6 2 ; t p ig mo o y wo d : a W n o s C ; CI 1 ; C 一2 1 se p n t r 6
数据采集卡 , 它具有 2路的模拟输 出 , 1 6路模拟输入 ,4路数字 2
I /O。
量 , 以对 电路板 测 步骤都是 采用人工 的方法 , 这样 的检测 方法既 耗时 , 也不能保证检测 的正确性 , 以需要引入 自动检测 系统 。 所
电路板 自动功能检测 系统完成对电路板所有主要功能 的检
接 口。它拥有 3 2路数 字输入 以及 3 2路漏 极数 字输 出, 8通 每 道成一组。N C-2 1 N 公司推出的 M系列低价 位多功能 I I 2 是 I P 6
测 。作为电路板检测流水 线的最后 一个步骤 , 这个检测 系统 的 检测的正确和可靠程度很大程度决定了 出厂的电路板产 品的质
HUANG i Ru ,HE L — n , T AN u —u imig I Z oh a
基于PXI总线的电路板级功能测试系统

摘要 : 本文研 究了一种 P X I 总线 的数字 电路板 板级 自动测试 系统 , 该方法针 对传统 的测试 方法速度低 的 问题 , 提 出了应用速 度 高达 1 3 2 M b y t e / s的 P X I 总线进 行通讯 的测试方案 ; 针对传 统 的测试 方法可靠 性、 可 维护性 的问题 , 提 出 了应用 N I 高速稳 定的板卡的测试方案 。 文章 首先说明 自动测试系统架构 、 组成及原理 , 在 此基 础上根据 实际项 目的要求 , 针 对系统的硬 件设计、
c o m p o s i t i o n a n d p r i n c i p l e a r e a n a l y z e d .A n d o n t h i S b a s i S ,a c c o r d i n g t o t h e s y s t e m h a r d w a r e d e s i g n a n d u ni v e r s a l t e s t i n t e r f a c e ,i n t e g r a t e d s o f t w a r e d e v e l o p m e n t a n d o t h e r a r e a s w e r e i 1 l u s t r a t e d a n d e x p l a i n e d i n
《电路板自动光照检测系统的设计与实现》

《电路板自动光照检测系统的设计与实现》一、引言随着现代电子制造业的快速发展,电路板的检测技术也在不断进步。
电路板自动光照检测系统作为一种高效、精确的检测手段,在电子制造领域得到了广泛应用。
本文将详细介绍电路板自动光照检测系统的设计与实现过程,包括系统设计的目的、意义、相关领域的研究现状以及本文的研究内容和方法。
二、系统设计目的与意义电路板自动光照检测系统的主要目的是实现电路板的快速、准确检测,提高生产效率和产品质量。
该系统的设计具有以下意义:1. 提高检测效率:通过自动化检测,减少人工检测的时间和人力成本,提高生产效率。
2. 提升检测精度:采用高精度光照检测技术,实现对电路板缺陷的精确识别。
3. 降低生产成本:通过自动化检测,减少因人为因素导致的误检、漏检,降低生产成本。
三、相关领域研究现状目前,电路板检测技术主要包括视觉检测、红外检测、X射线检测等。
其中,视觉检测技术因其成本低、操作简便等优点,在电路板检测领域得到了广泛应用。
然而,传统的视觉检测方法往往需要人工操作,存在检测效率低、误检率高等问题。
因此,研究一种高效、精确的自动光照检测系统具有重要意义。
四、系统设计电路板自动光照检测系统主要包括硬件和软件两部分。
硬件部分包括光源、镜头、相机、电路板传送装置等;软件部分包括图像处理算法、控制系统等。
1. 硬件设计硬件设计主要包括光源、镜头、相机的选择以及电路板传送装置的设计。
其中,光源的选择对检测结果的影响较大,需要根据电路板的特性和检测需求选择合适的光源。
镜头和相机的选择需要考虑其分辨率、成像质量等因素。
电路板传送装置的设计需要保证电路板的稳定传输,以便进行准确的检测。
2. 软件设计软件设计主要包括图像处理算法和控制系统。
图像处理算法是该系统的核心部分,需要实现对电路板图像的采集、处理、分析等功能。
控制系统则需要实现对硬件设备的控制,以及与上位机的通信等功能。
五、系统实现1. 图像处理算法实现图像处理算法主要包括图像采集、预处理、特征提取、缺陷识别等步骤。
pcb的ets流程

PCB的ETS流程一、什么是ETSETS(Engineering Test System)是一种在PCB(Printed Circuit Board,印刷电路板)制造过程中使用的测试系统。
它用于验证PCB的电气性能和功能是否符合设计要求,帮助发现可能存在的问题和缺陷。
二、ETS流程概述ETS流程是指在PCB制造过程中进行的工序,通过一系列的测试和检查,确保PCB 的质量和性能符合预期。
下面将详细介绍ETS流程的各个环节和步骤。
2.1 电气测试前的准备工作在进行ETS之前,需要进行一些准备工作。
2.1.1 制定测试方案根据PCB的设计要求和功能需求,制定测试方案,确定测试的内容和方法。
2.1.2 确定测试设备和工具根据测试方案,确定所需的测试设备和工具,包括测试仪器、夹具、控制系统等。
2.1.3 准备测试文件和程序准备好测试文件和程序,用于控制测试设备和记录测试结果。
2.2 电气测试流程ETS的核心环节是电气测试流程,主要包括以下几个步骤。
2.2.1 板前准备在进行电气测试之前,需要进行一些准备工作,包括对PCB进行目视检查,确保没有明显的质量问题;检查测试设备和工具的正常运行;设置测试环境,包括温度、湿度等。
2.2.2 测试准备将PCB安装到测试夹具上,连接测试设备,准备进行电气测试。
在测试准备阶段,需要根据测试方案设置各种参数,如电流、电压、频率等。
2.2.3 电气测试进行电气测试,包括静态测试和动态测试。
静态测试主要是对PCB进行电阻、电容、电感等参数的测量;动态测试主要是对PCB进行信号的输入和输出测试,检查电路的正常工作情况。
2.2.4 测试结果分析和记录根据测试结果,进行分析和判断,判断PCB是否符合设计要求。
同时将测试结果记录下来,用于后续的分析和改进。
2.3 电气测试后的处理工作在完成电气测试后,还需要进行一些处理工作。
2.3.1 分析测试结果对测试结果进行分析,找出PCB存在的问题和缺陷,确定改进方向。
印刷电路板生产用自动光学检测系统

。
焊接 点直径不 足 10 i 或Nk 20 i 5 mt t T 0 mt _ t 焊接掩模开 窗孔的 圆周超过
35 T 7 l ml
确保焊接掩模开窗孔 的圆周不超过 30 l。 5 T ml
有机锡焊的保护涂 层 ( 镍金表面涂上 一层超过 0 m 厚的金箔 m 5 O P 或镍 金表面涂料 ( S) 金箔厚度不超过 0 ) 热空气焊 球已均匀调整 ( .mm 。 5 H
7g 1 5i n/ 8
、
5 三点屈 曲测试:三点屈曲测试采用 10 m 跨距 . 0r a 的测试电路板 。中间部分须承受每分钟 9 5 m 的偏转 .r 4a 力 (e et n。即使偏转力高达 2 m df co ) l i 5 m,焊接面并无断
( 国国家 导体 美 半 公司 供 臣衄 稿)
… 。
⑤ 爱 …
维普资讯
印刷 电路板 生产 用 自动 光 学检 测 系统
T os nNir yr 安捷伦 科技 有 限公 司 h rt emee e
过近 1 年的努力 ,自动光学检测系统 ( O )最终 0 A I
印刷 电路 应选用未经指定焊接掩 模 ( MD ,因为其性 能 比已经 指定焊接 掩模 (MD NS ) s ) 更优胜 。确保焊接 掩模开窗孔的 圆周不 超过 35 i。 7 l ml
板
焊接掩模开 窗孔 的圆周超过 3 5 i 7 l ml 镍金表面涂上一层超过 0 衄 厚 的金箔 . 5
方形孔不超过 2 0 2 0m 0x0 ̄ 方形孔不超过 2 5 2 5m 7 x7 B 化学蚀刻 厚度超过 15 m或不足 10 m 2g 0p
~
焊剂
第三类 (ye ) ( 2 至 4 微米的粒子大小) 或更幼小 Tp 3 即 5 5
PCB电路板通电前自动化检测平台设计

PCB电路板通电前自动化检测平台设计设计一个PCB电路板通电前的自动化检测平台可以通过以下步骤进行:1.确定需求和目标:首先,确定需要检测的参数和指标,例如电阻、电容、电压、电流、短路、开路等。
然后,确立设计的目标,例如提高检测的效率、降低误判率等。
2.确定检测设备:选择合适的测试设备来进行自动化检测。
例如,可以选择多用途测试仪器,如万用表、逻辑分析仪、示波器等,或者选择专业的测试设备,如电阻测试仪、电容测试仪、红外检测仪等。
根据需求和目标,选择相应的设备。
3.设计测试夹具:根据电路板的设计和尺寸,设计适用的测试夹具来保持电路板的稳定性并连接测试设备和电路板。
测试夹具应该具有多个接口,以便同时测试多个参数。
4. 开发自动化检测软件:根据需求和目标,开发适用于自动化检测的软件。
软件应能够读取测试设备的数据,并进行数据分析和处理。
例如,可以使用Python等编程语言来编写测试程序,根据测试仪器的控制指令自动进行测试,提取测试结果并进行分析。
5.确定测试流程:确定合适的测试流程,包括测试的步骤和顺序。
例如,首先对电路板进行可见故障的检测,如焊接问题、元件损坏等;然后进行电阻、电容、电压等参数的测试;最后进行短路、开路等故障的检测。
测试流程应根据实际情况进行优化,以提高检测效率和准确性。
6.进行实际测试:将设计好的测试夹具连接到测试设备和待测的电路板上,运行自动化检测软件,进行实际的测试。
记录测试结果,包括通过和不通过的项目,并生成测试报告。
7.优化和改进:根据测试结果和反馈,对自动化检测平台进行优化和改进。
可以调整测试流程、修改测试夹具、改进软件功能等。
通过以上步骤,设计一个PCB电路板通电前的自动化检测平台,可以提高检测效率和准确性,减少人力成本,并加快产品的上市时间。
同时,测试结果的一致性也能得到保证,有助于提高产品的品质和可靠性。
自动测试系统

3.2自动测试系统3.2.1自动测试系统的组成通常把以计算机为核心,在程控指令的控制下,能自动完成某种测试任务而组合起来的测量仪器和其它设备的有机整体称为自动测试系统,简称(Automatic Test System)[1]。
通过应用ATS可以降低设备的维护时间,设备的性能,提高其工作效率,降低成本,并且具有高速度、高精度、能、多参数和宽测量范围等众多优点。
自动测试系统由自动测试设备(ATE, Automatic Test Equipment)、测试程序集(TPSs, Test Program Sets)和测试环境(TE, Test Environment)三个部分组成。
其中自动测试设备ATE是整个测试系统的硬件平台,它是一种通过计算机控制进行器件、电路板和子系统测试的设备。
通过计算机编程取代人的手工操作,自动地完成测试。
ATE的核心是计算机,它包括所有的硬件设备和相应的操作系统软件。
ATS采用ATE来控制复杂的测试仪器,例如:数字电压表、信号发生器和开关组件等。
这些设备在测试软件的控制下运行,提供被测对象的电路或部件所要求的激励,然后测量在不同的引脚、端口或连接点的响应,从而确定该被测对象是否具有规范中规定的功能或性能[2]。
典型的TPS由测试程序软件、测试接口适配器(包括接口装置、固件及电缆)和被测对象测试文档三部分组成。
测试环境可包括ATS结构说明、程序设计和测试描述语言、编译器、开发工具、描述UUT ( Unit Under Test)设计需求的标准格式和开发TPS软件的测试策略信息。
在自动测试系统中,测试资源定义为系统所使用的自动测试设备和信号调理适配器的相关信息[3]。
其中自动测试设备是测试系统中完成激励信号产生和响应信号采集的主要设备,是测试资源的核心。
信号调理适配器的功能就是实现将通过接口连接件引出的ATE的信号管脚和UUT的信号管脚对应连接起来,并实现一定的信号调理,如电压的转换。
- 1、下载文档前请自行甄别文档内容的完整性,平台不提供额外的编辑、内容补充、找答案等附加服务。
- 2、"仅部分预览"的文档,不可在线预览部分如存在完整性等问题,可反馈申请退款(可完整预览的文档不适用该条件!)。
- 3、如文档侵犯您的权益,请联系客服反馈,我们会尽快为您处理(人工客服工作时间:9:00-18:30)。
电路板自动测试系统简介
一.概述
随着电子技术及印制板制造技术的发展,现代电子产品日趋复杂,印制电路板的密度日趋增加,随之而来的是印制板的检测及修理也愈加困难。
为了提高印制电路板的检测及维修的自动化程度,国际上从七十年代开始,进行印制板自动测试系统的研制。
经过二十多年的发展,各种印制板自动测试系统层出不穷。
目前,印制电路板自动测试技术发展迅速,印制板在线测试系统(ATE)广泛应用于印制板光板及各种产品的印制电路板的生产、检测和维修等。
ATE的测试方法可分接触式测试和非接触式测试两大类。
其中接触式测试分为在线测试、功能测试、BIST和边界扫描测试等;非接触式测试又可分为非向量测试、自动视觉测试、红外热图象测试、X射线和激光测试。
随着计算机技术及VXI总线技术的应用,各种建立在VXI测试平台上的印制电路板的ATE和功能测试也得到迅速发展。
由之而来对测试过程中所需要的工装(夹具)不断提出要求,于是电路板测试仪(又称电子测试工装)应运而生。
二.工作原理
1、印制电路板手动测试治具介绍:
手动电路板测试治具是指:通过针床、手动测试治具、印制板插脚、输入/输出接口,向被测电路板施加控制信号及输入信号,并实时读取被测电路板的输出信号,通过一系列的数据分析处理,进而判断被测电路板的性能(或功能)正确与否。
由于用户的测试要求、测试对象各不相同,其具体的性能(或功能)测试原理及测试方法也各不相同。
它需要量体裁衣,单台定制才
能满足用户的要求。
例如:某日资录象机专业企业——录象机主板功能测试工装
㈠、要求
1)检测录象机主板的功能是否正确(录象、放象、倒带、暂停、向录象机输入生产编号、录入时钟等)
2)测试设备:计算机(RS232接口)、音频发生器、电源供给系统、录象机、音频接收器、电视机、示波器等。
㈡、试框图(检测录象机的主板)
㈢、工作原理
将计算机通过接口和录象机主板相连,因此可读写设置主板的时间、出厂编号和制式等…。
音频信号送入工装CN1,打开电源供电系统。
同时将工装的音频相关信号CN5接至音频接收器;并将工装上的相关波形测试点CN6接至示波器;同时在电视机上监测其录象机的放像功能的正确性。
2、印制电路板自动功能测试介绍:
自动测试系统的广泛适用性是因为自动测试系统的设计不是针对单一的测试对象进行的,而是将印制电路板的功能测试进行抽象和分类,印制电路板测试(这里是抽象的印制电路板)过程可分为信号的输入和信号的输出:
信号的输入分为: 能源信号;信息信号;控制信号;
信号的输出同样分为: 能源信号;信息信号;控制信号;
以上三种信号按信号性质可分为:周期信号;非周期信号;直流信号。
基于以上的信号分类,印制电路板的测试过程可简单归纳为激励和响应的过程,即在印制电路板的测试过程中,在适当的时刻在适当的节点施加适当的激励,然后在适当的时刻在适当的节点检测响应并作出判断,判断此响应是否与预期的响应一致,若一致则判为正确(或合格)若不一致则判为不正确(或不合格)。
由此可以清楚的看出此过程是一个清晰的程序过程,此程序过程最适合于计算机完成。
此种方法的优点是显而易见的:简洁、有效、快速、可靠。
自动测试系统与传统手工测试比较最突出的优点;在于手工测试方法在测试时由于投资、人员培训等原因造成测试结果的不确定性是固有的。
而自动测试系统可将不确定性降至最低。
㈠、方案框图: 印制电路板自动测试系统框图
㈡、所用到的测试仪器:
1、 工业控制机;
2、 中继控制器(将所用到的相关硬件有机的结合起来);
3、开关矩阵(根据用户所须的测试通道和测量范围选定,能扩展);
4、数字存储示波器
分辨率:100MHz 采样点:8位;
50MHz 采样点:12位;
3.125MHz 采样点:14位;
195KHz 采样点:16位;
采样速率:100MHz 10ns;
50MHz 20ns
灵敏度:200mV~80V(满刻度)
阻抗:1Mohm/30pF
耦合:AC/DC
带宽:DC~50MHz
存储深度:0~128K字节
5、任意波形发生器
分辨率:14位;
采样速率:0.01Hz~50MHz
存储深度:1~256K 字节
带宽:DC~2MHz
阻抗:50Ohm
耦合:DC
输出幅度:-12V~+12V
输出步骤:8192步
输出波形:方波、三角波、正玄波、DC、用户自定义
对称:1~99%
6、频率计20Hz~10MHz
7、数字多用表可测量温度、压力、功率、电流、电压等电工量。
8、逻辑分析仪
通道:24
门限电平:-1~+3V变化
触发输入:任意通道均可作为触发输入;
外部时钟:1个(最大25M Hz)
带宽:30MHz
阻抗:100Kom
最大输入电压:输入通过470Kohm电阻耦合,-5V~50V输入
采样速率:100Msa/s
存储深度:128K/每通道
触发方式:单次、普通、自动等
耦合:DC
三、方案的成熟性
此方案已成熟的应用于某日资专业电视机企业。
应用于HDTV (高清晰数字彩色电视)的全线测试。
配置按每条生产线2台共计4条成产线。
同时备份2套已备生产量调节之用。
四、方案的经济性(国内著名家电企业)
基本情况;专业家电生产(电冰箱、空调、洗衣机、微波炉……),10条生产线。
不同品种要制作2-6台功能测试工装,每品种使用寿命为(磨损及品种淘汰)6-18个月,每年耗资约100-150万元(RMB);每条生产线需配备约4名专业测试工装操作人员,每名操作人员须不停的培训新工装的使用方法和熟悉测试流程,因为测试结果需要操作人员判断正确与否。
每台测试工装从设计到制作调试完成,全部要从头做起耗时、耗人、耗金钱。
随着时间的推移,工装堆积如山。
不同的工装尺寸外观千奇百怪,管理保养各不相同,维护及管理麻烦多多。
采用自动测试系统方案每条生产线配备2台,初期采购价格约为10万元(RMB)/台,当年的采购成本仅高于当年传统方案的采购成本30%,从第二年起针对不同品种仅需配备标准针床,每品种每台仅需500-1000元(RMB)。
当年采购数量即使达到200台套,也不过10-20万元(RMB)。
节约采购成本90%-95%,专职测试人员减少50%。
由于方法的标准化和规范化,测试工装的设计和编程可由设计部门直接完成。
生产部门仅需完成日常维护责任。
责任清晰。
由于测试结果的判断由电脑完成,对生产线的操作员工的培训大大化简,要求大大下降,甚至无需专业人员。
标准针床的规格尺寸一致,便于存放和管理。
此方案明确体现了好快多省的原则。
北京晨芒电子技术有限公司
日期:2004-3-3
附录
自动测试系统在山东松下映像产业有限公司现场图片。